Concevez, innovez et fabriquez n'importe où avec la Fuse 1 et Fusion 360
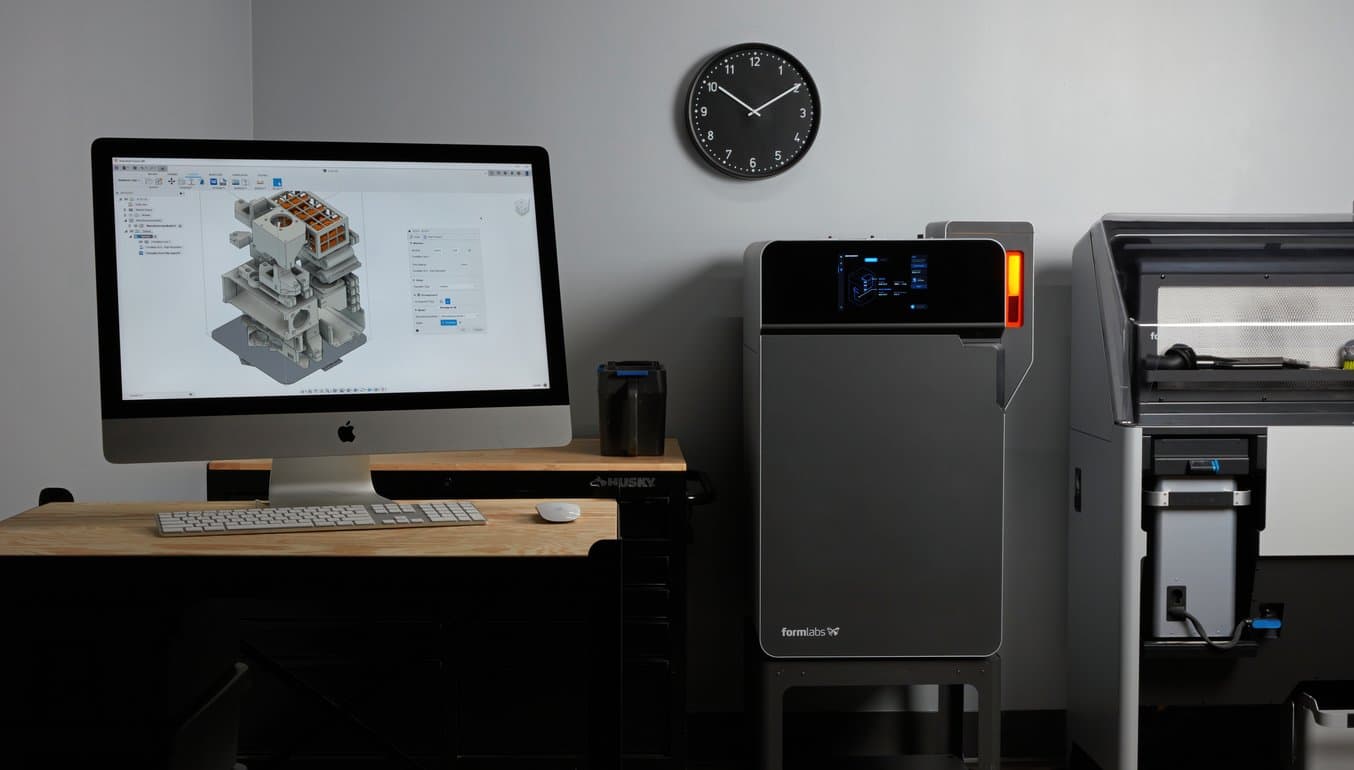
Formlabs et Autodesk se sont à nouveau associés pour intégrer l'imprimante SLS Fuse 1 à la suite d'outils CAO pour l'impression 3D de Fusion 360. Dans le prolongement de notre collaboration lancée en mai 2021, Fusion 360 supporte désormais toutes les imprimantes 3D Formlabs, offrant ainsi un ensemble d'outils complet et accessible qui permet de concevoir, d'innover et de fabriquer des pièces d'utilisation finale dans un seul logiciel.
La mise à jour de notre intégration logiciel comprend de nouvelles fonctionnalités qui réduisent le nombre d'étapes entre la conception et le produit fini. L'interface graphique permet aux utilisateurs de visualiser et d'agencer les pièces dans la chambre de fabrication de la Fuse 1, ou d'agencer automatiquement plusieurs pièces à une vitesse incroyable. Les tableaux de bord de conception personnalisables offrent une grande répétabilité et un accès facile à vos flux de production les plus couramment utilisés. Les équipes bénéficient désormais d'un contrôle de version plus fiable leur permettant d'exporter directement un fichier FORM depuis Fusion 360 (l'exportation directe vers PreForm sera bientôt disponible).
Les ingénieurs de Formlabs et d'Autodesk sont constamment à l'écoute de nos utilisateurs pour répondre à leurs préoccupations et construire des outils flexibles qui leur permettent d'innover où qu'ils soient. En associant la puissante plateforme CAO d'Autodesk à la technologie SLS professionnelle de Formlabs, nous voulons offrir aux concepteurs de produits, aux ingénieurs et aux chefs d'entreprise des méthodes de fabrication accessibles. Dans les récits suivants, vous découvrirez deux utilisateurs de Fuse 1 et de Fusion 360 qui utilisent ces outils pour réduire les coûts, itérer rapidement et fabriquer des solutions sur mesure pour leurs clients.
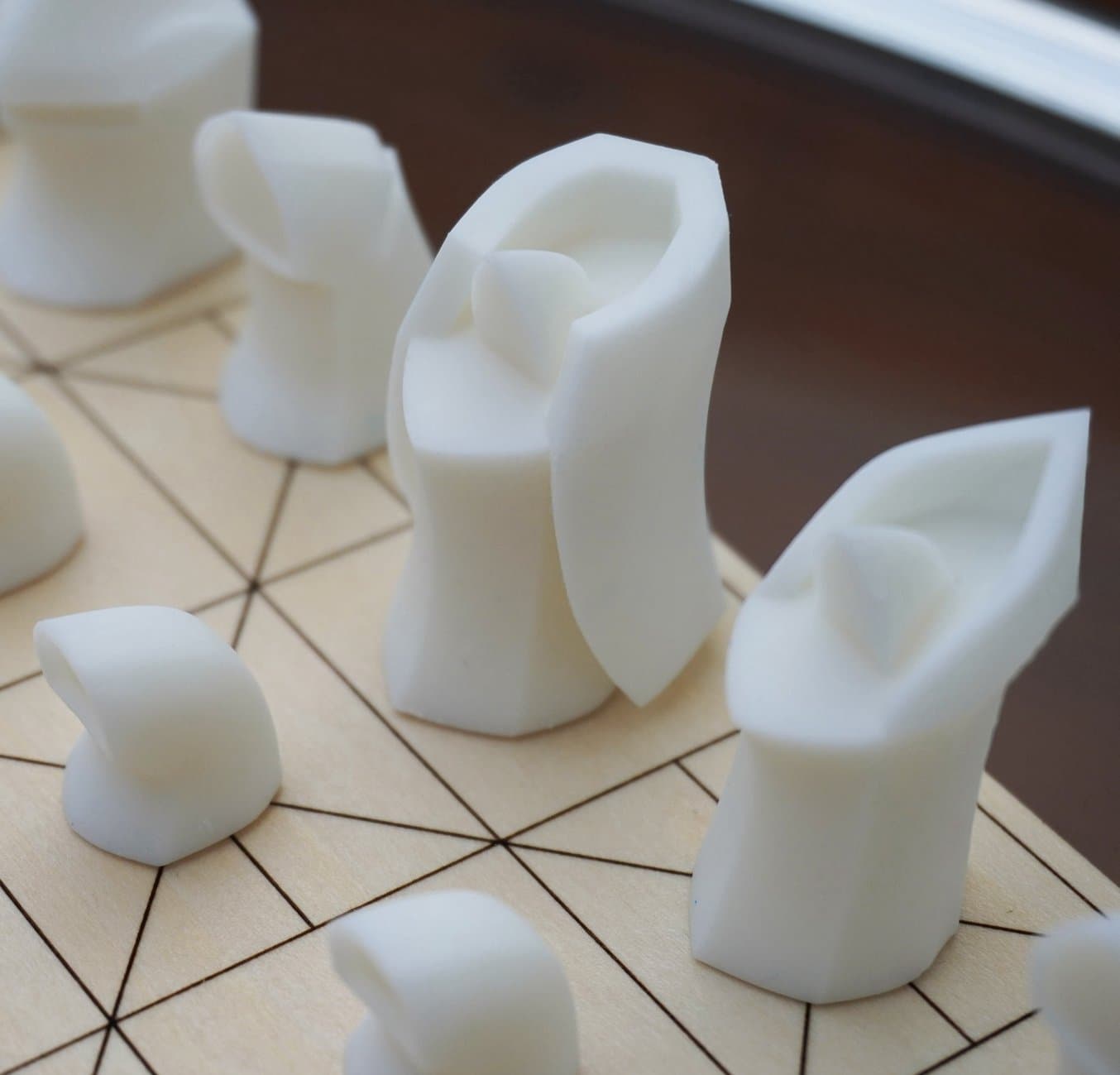
Intégration de Formlabs et de Fusion 360
Formlabs et Fusion 360 d'Autodesk se sont associés pour optimiser vos procédures numériques grâce à un nouveau logiciel CAO intégrant l’impression 3D.Visitez notre centre d'intégration pour découvrir les toutes dernières fonctionnalités de Fusion 360 pour l'impression SLA et SLS, lire d'autres témoignages d'utilisateurs et télécharger notre guide de conception. (En photo : jeu d'échecs de Will Qiu)
KUHMUTE : fabriquer des produits de micromobilité
Peter Deppe et Scott Spitler ont fondé KUHMUTE en 2018, alors que les trottinettes électriques commençaient seulement à devenir populaires. Ils ont compris les avantages qu'offraient les trottinettes électriques pour le transport, mais ont également constaté des problèmes d'organisation et de sécurité dans leur ville natale de Flint, dans le Michigan. Ils ont donc développé la station de recharge universelle KUHMUTE pour ces véhicules. Grâce à l'impression 3D, ils ont également rendu leurs stations de recharge compatibles avec les fauteuils roulants, les vélos électriques et les robots de livraison pour répondre aux divers besoins ressentis par les utilisateurs en fonction de leurs capacités physiques ou de la distance de leur trajet.
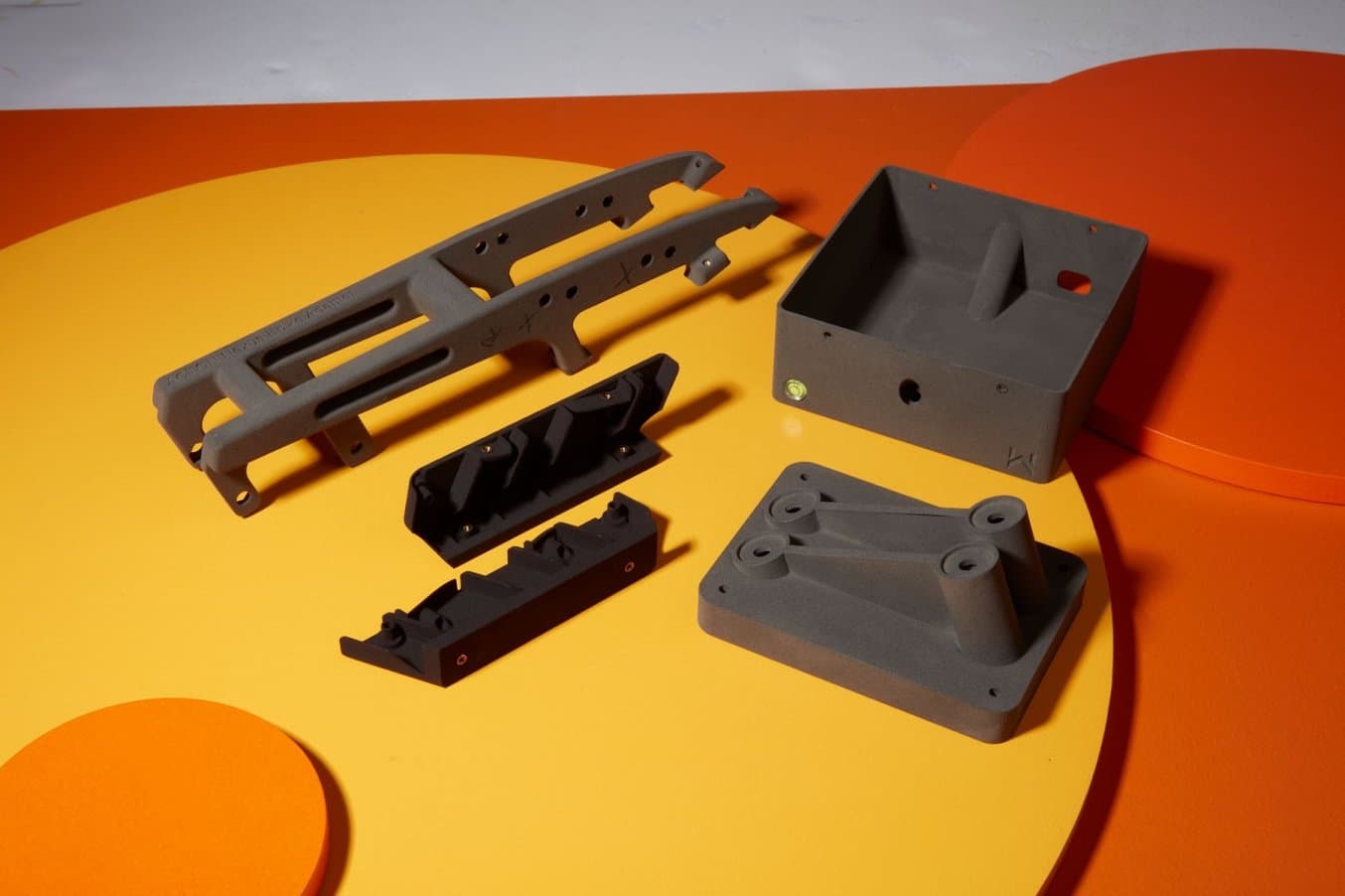
KHUMUTE utilise des pièces en nylon SLS imprimées avec la Fuse 1 pour le prototypage et la production finale.
De nombreux composants fonctionnels de la station de recharge sont imprimés avec la Fuse 1. L'adaptateur de véhicule est également imprimé en 3D avec de la poudre de nylon SLS : c'est ce dispositif qui s'adapte à chaque véhicule et qui permet à tout conducteur d'utiliser les stations de recharge KUHMUTE.
Comme beaucoup de startups, l'équipe a commencé à travailler sur cette technologie dans l'appartement d'un collègue, et a commencé à imprimer en 3D avec une machine FDM. L'équipe a rapidement réalisé qu'elle avait besoin de pièces plus précises et plus lisses pour ses prototypes d'assemblages mécaniques. Ils ont été impressionnés par la qualité d'impression de la Form 3, et les interfaces utilisateur intuitives des imprimantes et des logiciels Formlabs leur ont tout de suite plu. Ils ont acheté leur première Fuse 1 l'année dernière, et ont rapidement commencé à utiliser les poudres de nylon SLS pour fabriquer des pièces d'utilisation finale.
« L'impression 3D nous a notamment permis de fabriquer nous-mêmes la plupart des pièces en interne, ce qui constitue pour nous un véritable avantage concurrentiel. Nous sommes capables d'innover plus rapidement et d'offrir plus d'options de mobilité dans les communautés urbaines, ce que nous pensons être nécessaire. »
Peter Deppe, cofondateur et PDG de KUHMUTE
L'équipe tire parti des imprimantes SLA et SLS Formlabs qui offrent une vaste gamme de matériaux (allant de Clear Resin jusqu'aux poudres de nylon), ainsi que de l'outil de conception multifonctionnel Fusion 360. Fusion 360 est utilisé pour presque toutes les tâches de conception, qui incluent notamment la conception de produits, la visualisation, les rendus de conception graphique pour leur site web, et même la conception des icônes de l'application KUHMUTE. Fusion 360 s'intègre particulièrement bien à EAGLE, ce qui leur permet d'importer un modèle 3D de circuit imprimé, puis de concevoir des boîtiers autour de celui-ci.
Si vous utilisez des véhicules de micromobilité électriques (en gros, tous les véhicules électriques plus petits qu'une voiture), surveillez de près les stations de recharge KUHMUTE qui devraient apparaître partout dans les villes américaines.
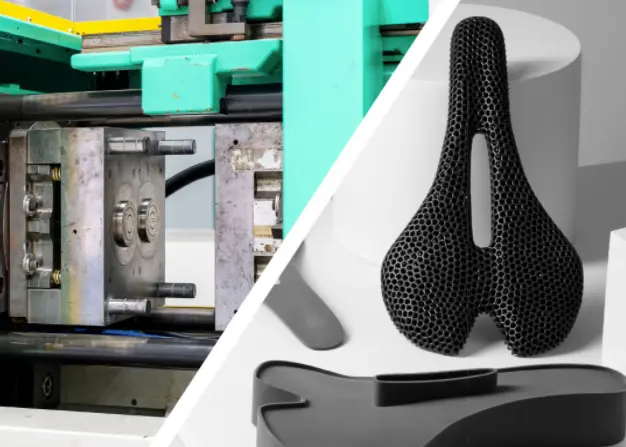
Impression 3D SLS ou moulage par injection : quand remplacer le moulage de pièces par l'impression 3D ?
Dans ce livre blanc, nous traiterons du moulage par injection, de ses avantages et de ses inconvénients, et nous présenterons l'impression 3D SLS ainsi que les applications pour lesquelles elle peut être utilisée.
Partial Hand Solution : fabrication de prothèses spécifiques aux patients
Matt Mikosz, fondateur de Partial Hand Solutions, a consacré sa carrière à faire progresser la fabrication de prothèses pour des patients amputés de tous âges. Matt propose des solutions fonctionnelles pour toutes les personnes – qu'il s'agisse de soldats ou d'enfants – ayant subi une amputation partielle de la main ou du doigt, ou souffrant d'autres problèmes de membres. Mais une question se pose toujours : comment fabriquer une prothèse durable et personnalisée à un prix abordable ?
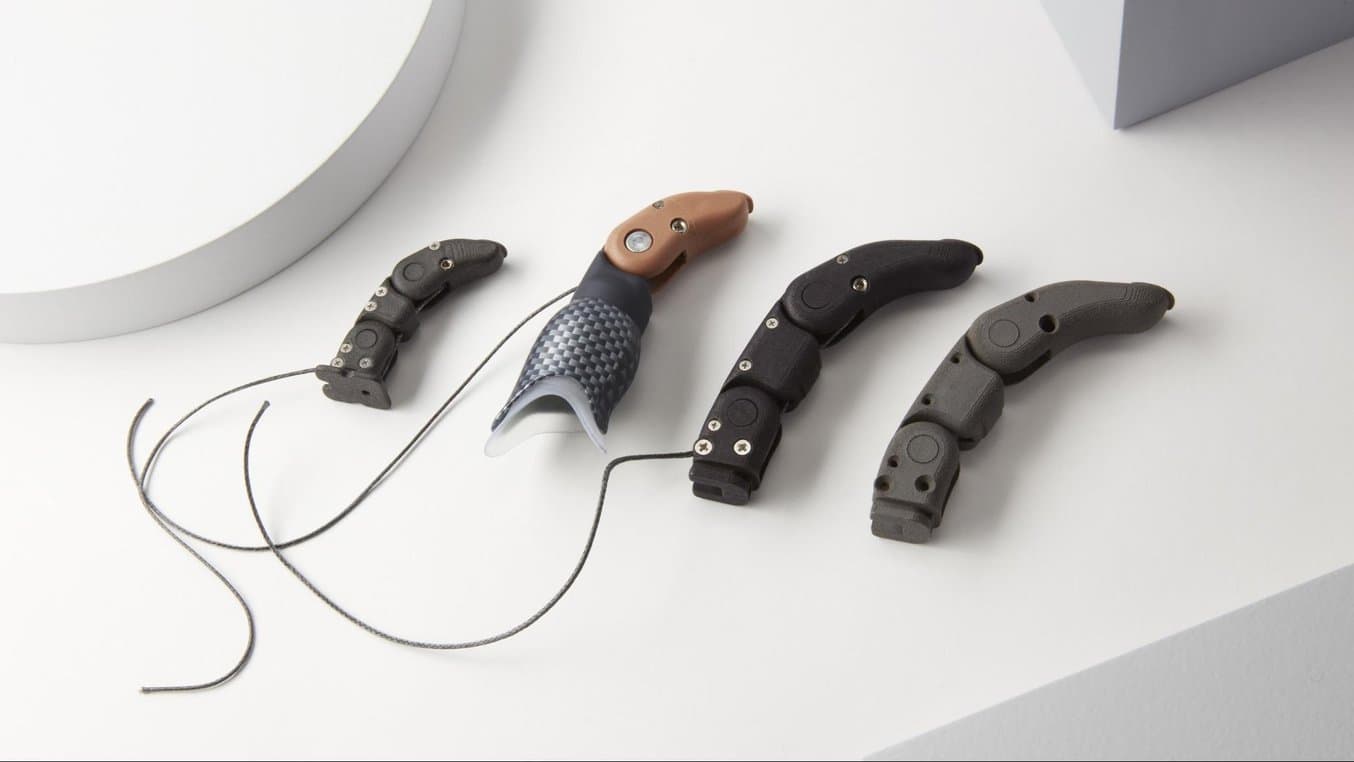
Les prothèses de doigts avec des joints articulés conçues par Partial Hand Solutions sont imprimées avec la Fuse 1.
Autrefois, Matt sous-traitait souvent la fabrication de moules d'injection ou de pièces usinées. Cependant, ces pièces prenaient souvent jusqu'à deux semaines pour arriver par la poste, ce qui laissait peu de temps et de possibilités pour transformer des pièces génériques en pièces sur mesure. Après avoir adopté le flux de travail Fuse 1, il a constaté que les pièces imprimées avec des poudres de nylon SLS lui permettaient d'itérer rapidement ses conceptions et de proposer plus rapidement des produits hautement personnalisés à ses clients.
« [L'impression 3D] a eu un impact considérable sur mon activité. Lorsque j'ai créé mon entreprise il y a 14 ans, je payais quelqu'un pour fabriquer des prototypes et cela me coûtait très cher. Je devais m'assurer que ma conception était très proche du produit final pour ne pas avoir à réaliser plusieurs prototypes et augmenter les coûts. Le fait de disposer de Fusion 360 et de la Fuse 1 m'a permis de réaliser des prototypes aussi souvent que nécessaire, à un coût bien moindre. »
Matthew Mikosz, fondateur de Partial Hand Solutions
Matt utilise Fusion 360 pour concevoir ses prothèses sur mesure. Il collabore fréquemment à distance avec des cliniciens à l'aide des outils de collaboration de Fusion 360 afin de les impliquer dans le processus de développement des dispositifs qu'il fabrique pour les patients. Une fois la conception terminée, il peut télécharger un fichier STL ou FORM, imprimer la prothèse avec la Fuse 1 et l'envoyer au patient pour qu'il l'essaie. Après que la conception a été approuvée, il peut également donner une finition personnalisée aux prothèses. Son laboratoire est équipé pour polir, teindre et ajouter des motifs hydrographiques sur les impressions 3D, ce qui permet à Matt d'obtenir des résultats magnifiques et d'atteindre le but recherché : améliorer la mobilité et la qualité de vie des patients.
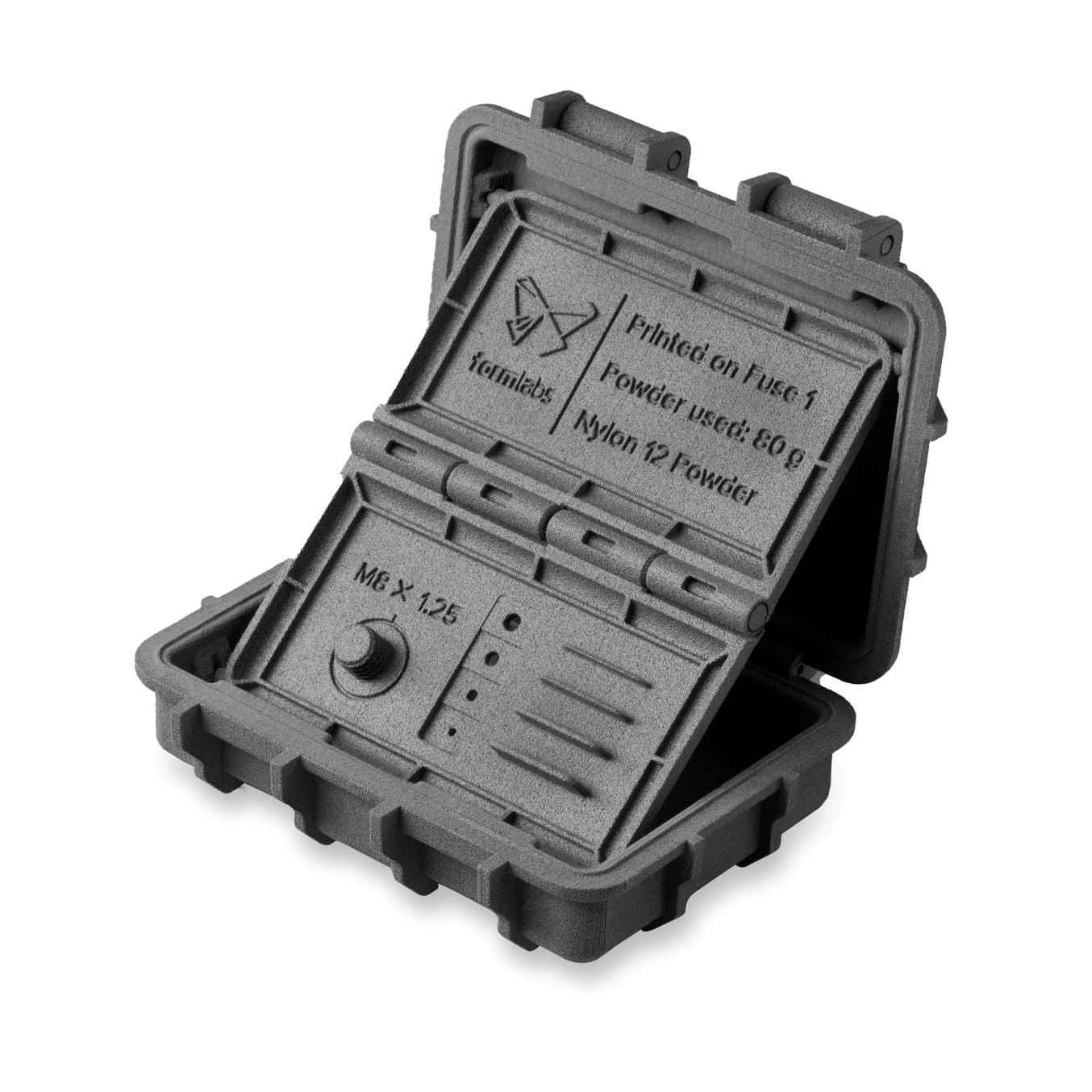
Commander un échantillon gratuit
Vous voulez constater par vous-même la résistance, la durabilité et la finition de surface d'une pièce imprimée avec la Fuse 1 ? Commandez un échantillon gratuit imprimé avec Nylon 11 Powder ou Nylon 12 Powder.