Comment Hayco développe des brosses à dents ultrasoniques pour les marques les plus réputées au monde
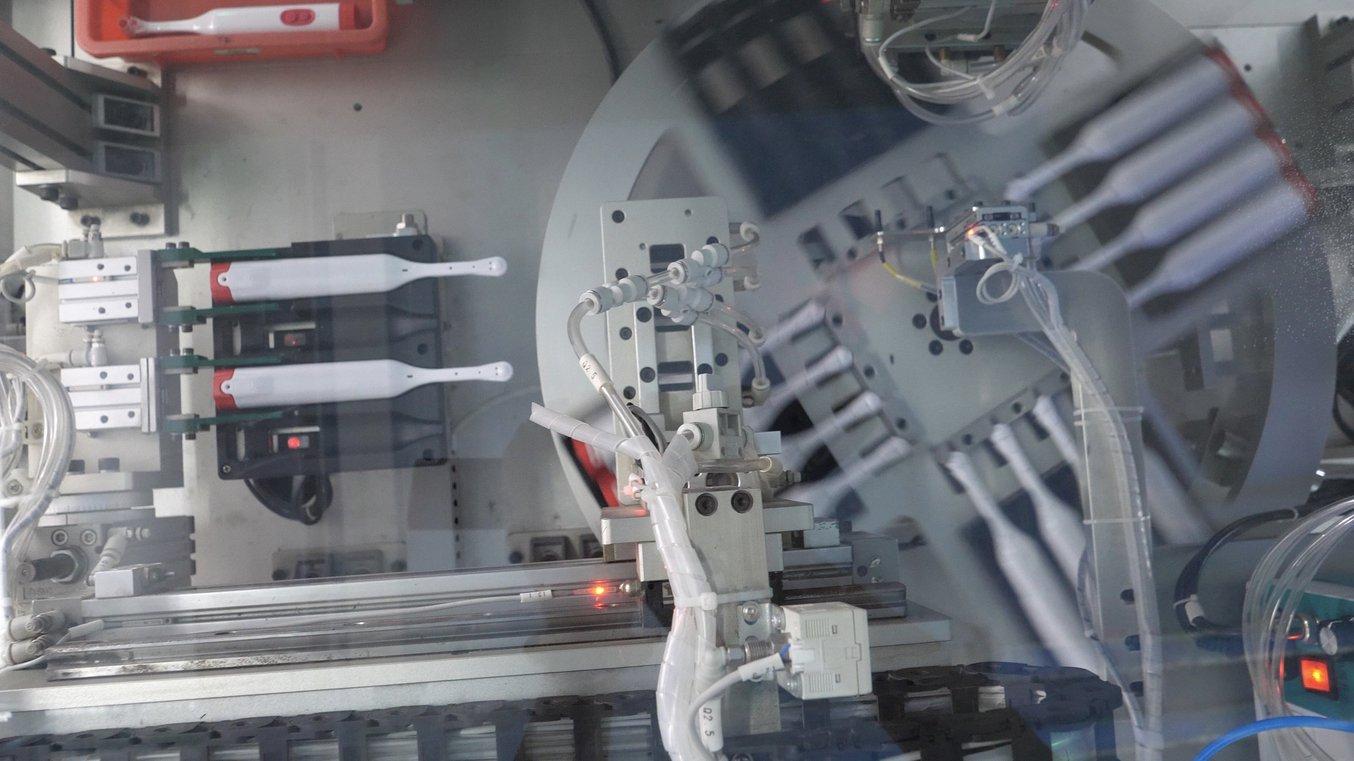
En 1892, l'entrepreneur australien William E. Hay a fondé la South Australian Brush Company, dont les balais et les brosses se sont rapidement fait connaître en Australie-Méridionale. Puis en 1983, Donald Hay, le petit-fils de William, a pu assister à l'ascension économique de l'Asie, et a décidé de créer une nouvelle société à Hong Kong, appelée Hayco.
En se concentrant sur la fabrication de brosses qui a fait la réputation de la famille, Hayco a ouvert une usine de moulage par injection à Shenzhen, en Chine. Elle a poursuivi sa croissance rapide avec une équipe de 6000 personnes et de multiples usines en Chine et en République dominicaine.
Depuis sa création, Hayco a travaillé avec de nombreuses marques renommées dans la fabrication de produits d'entretien ménager en plastique. S'appuyant sur son expérience dans la fabrication de brosses, Hayco conçoit et produit depuis plus de 18 ans des brosses à dents électriques de qualité supérieure pour les grandes marques de soins bucco-dentaires, notamment Philips et Church & Dwight, et expédie actuellement plus de 20 millions de brosses à dents électriques par an sur les marchés mondiaux.
Lisez la suite pour savoir comment l'équipe d'ingénieurs de Hayco utilise la fabrication additive pour développer de nouveaux produits et créer des prototypes précis et biocompatibles avant de passer à la production.
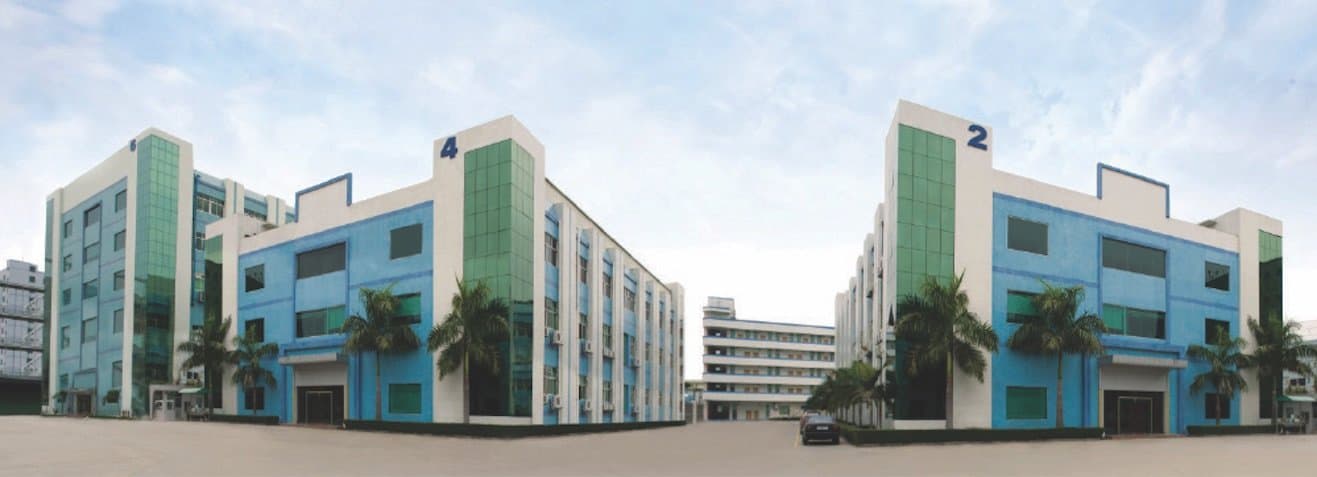
Usine de fabrication de Hayco à Shenzhen, Chine
Les premiers utilisateurs de la fabrication additive
Forte d'une longue tradition d'innovation dans le domaine de la fabrication et de la conception, Hayco a adopté très tôt l'impression 3D. Elle utilise des imprimantes 3D à dépôt de fil fondu (FDM) et à frittage sélectif par laser (SLS) depuis le début des années 90. Lorsque Hoss Vong – aujourd'hui directeur principal de l'équipe de recherche – a rejoint Hayco en 2000, il a commencé à utiliser l'impression 3D pour le prototypage de nombreux produits en plastique, notamment des brosses à dents à ultrasons.
« À l'époque, le prototypage rapide par impression 3D était très différent d'aujourd'hui. Les machines que nous avions étaient de qualité industrielle. Elles étaient volumineuses, nécessitaient une formation poussée et étaient très coûteuses à l'achat et à l'entretien », a déclaré M. Vong.
Trouver les bons matériaux pour les différents composants
Lors de la conception d'une nouvelle brosse à dents, chaque composant a des exigences différentes qui influencent le choix des méthodes et des matériaux de prototypage. Par exemple, le boîtier doit être lisse et robuste, le châssis doit être résistant mais aussi très précis pour accueillir toute l'électronique et, surtout, la tête de la brosse doit être fabriquée dans un matériau biocompatible pour permettre des tests consommateurs.
Le choix du matériau est particulièrement important dans l'évaluation des caractéristiques dynamiques et vibratoires du produit ; la rigidité et la densité doivent être aussi proches que possible du produit final.
« Nous avons obtenu d'excellents résultats en utilisant la gamme de matériaux de Formlabs pour reproduire fidèlement les performances du produit final », a déclaré M. Vong.
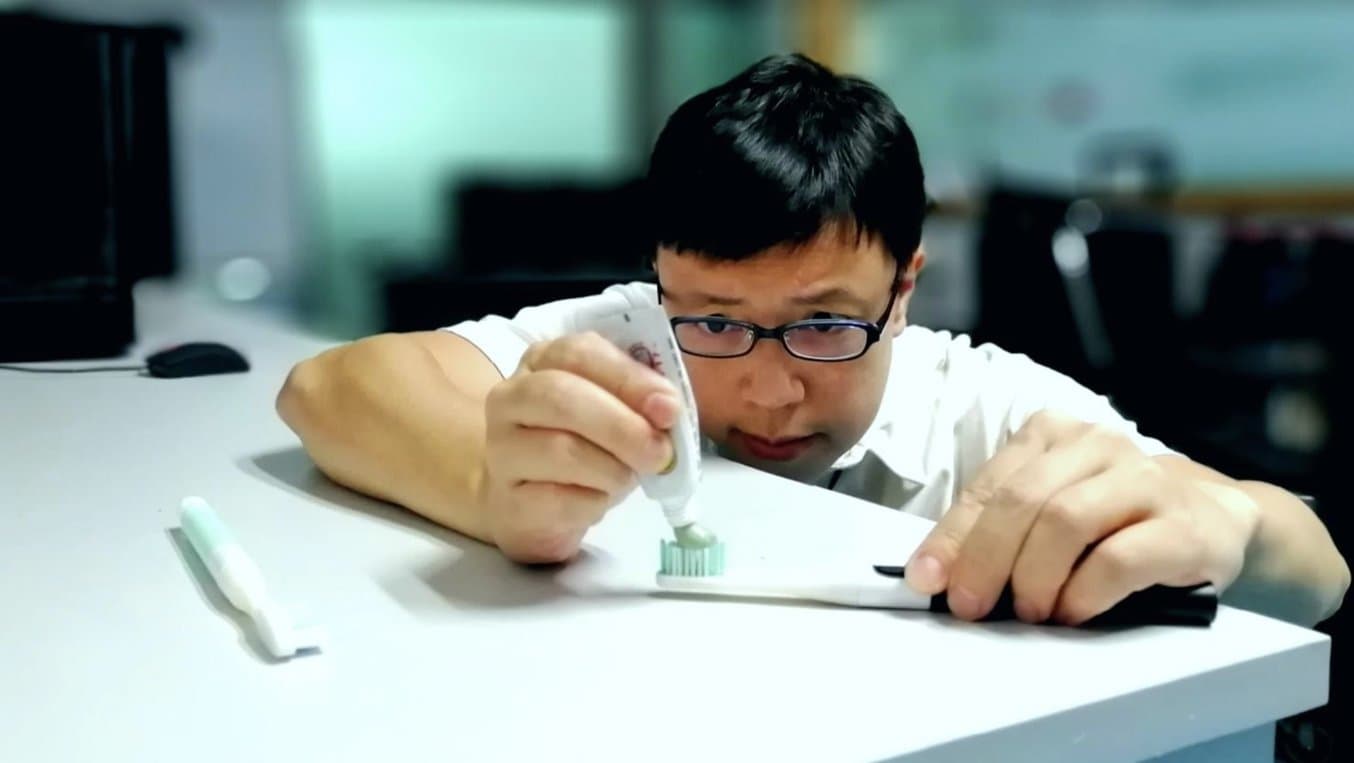
Hoss Vong testant un prototype de brosse à dents. La tête de la brosse est imprimée en 3D avec un matériau biocompatible pour qu'elle puisse être testée.
Par expérience, M. Vong savait que la technologie d'impression 3D la plus adaptée à cette application était la stéréolithographie, mais il n'était pas facile de trouver une imprimante offrant la sélection de matériaux dont il avait besoin. « Vous pouvez bien sûr toujours trouver des résines tierces bon marché, mais nous ne les utilisons jamais pour des raisons de sécurité et de qualité », a déclaré M. Vong.
Après avoir effectué ses recherches, M. Vong a décidé d'acheter une imprimante 3D de Formlabs, qui offre un large choix de matériaux pour le prototypage et pour les applications nécessitant une biocompatibilité.
« Nous utilisons beaucoup les résines standard de Formlabs, et lorsque nous devons effectuer des tests auprès des consommateurs, nous utilisons Dental SG Resin, qui est biocompatible et imprime des détails précis », a déclaré M. Vong.
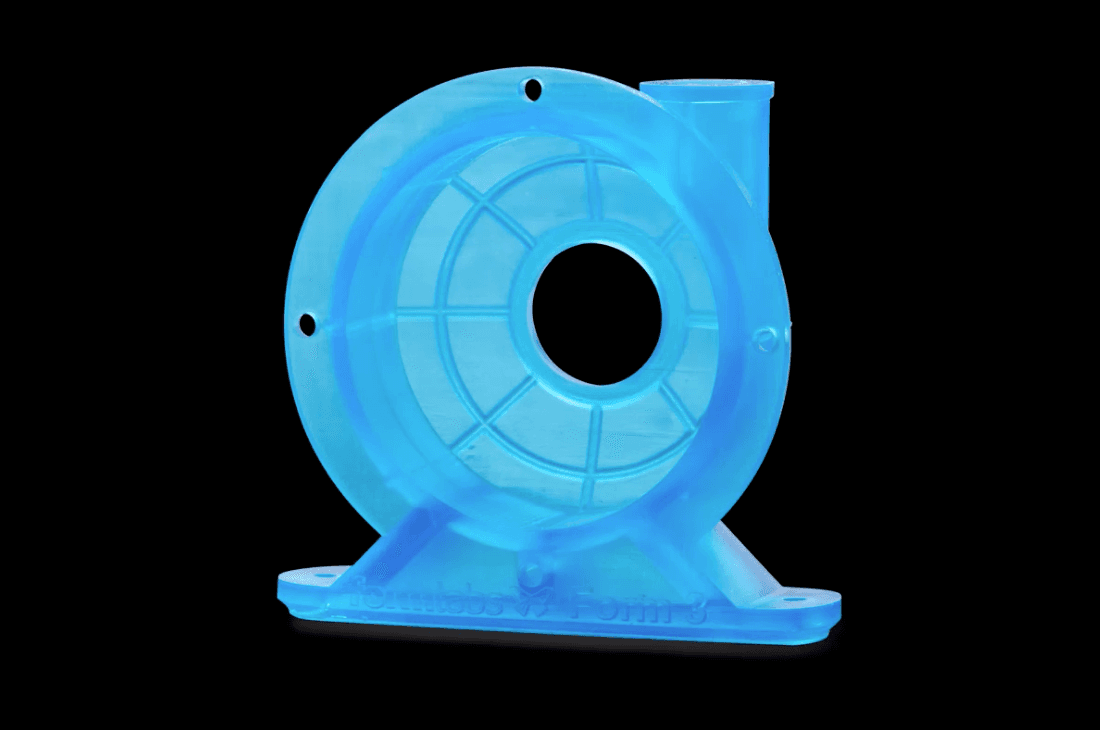
Commander un échantillon gratuit
Touchez et constatez par vous-même la qualité de l’impression 3D SLA. Nous vous enverrons un échantillon gratuit imprimé en 3D.
Donner à tous les ingénieurs les moyens d'utiliser l'impression 3D
« La Form 2 a été à la hauteur des critiques positives que j'ai lues avant d'acheter nos premières imprimantes à Formlabs. Ces imprimantes se sont révélées très fiables, et Formlabs m'a offert une sélection de matériaux à tester. En outre, contrairement à de nombreuses autres imprimantes de qualité industrielle que nous possédions, son utilisation est très intuitive. Nos imprimantes 3D ne sont plus limitées à quelques ingénieurs qualifiés ; chacun peut les utiliser pour ses projets, ce que nous encourageons vivement. Ainsi, lorsque la Form 3 est sortie, nous en avons immédiatement précommandé deux pour répondre à notre demande croissante de prototypage. Nous avons maintenant un total de six imprimantes SLA de Formlabs », a déclaré M. Vong.
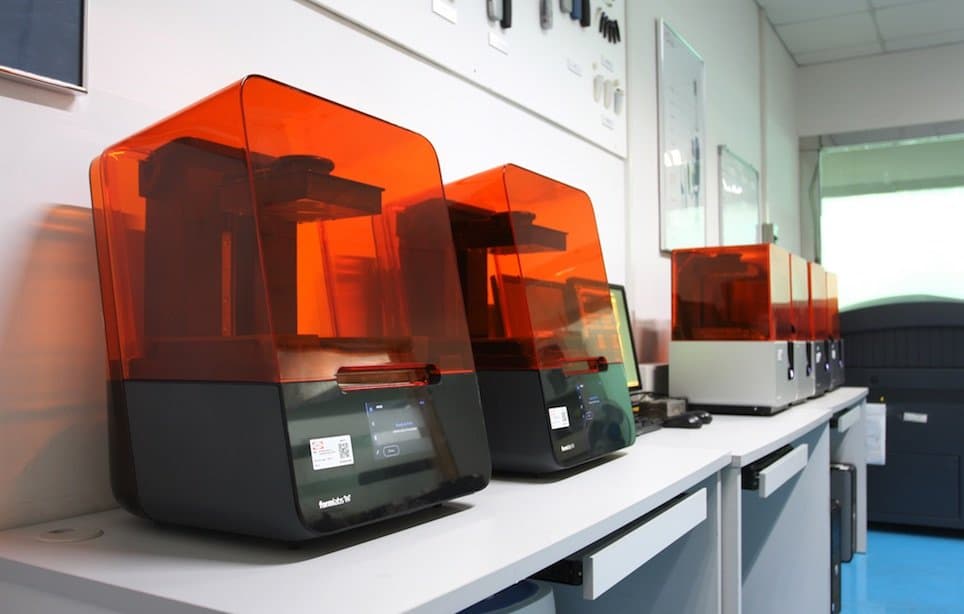
Hayco utilise actuellement six imprimantes SLA de Formlabs dans ses ateliers d'impression 3D. En raison de leur facilité d'utilisation, les imprimantes 3D ne sont plus limitées à quelques ingénieurs qualifiés : tout le monde est encouragé à les utiliser pour ses projets.
Selon M. Vong, les économies réalisées avec les imprimantes 3D de Formlabs sont de l'ordre de 35 % par rapport aux autres technologies d'impression, notamment avec la technologie Low Force Stereolithography (LFS)™ de la Form 3.
« Nous constatons que les autres technologies d'impression impriment beaucoup plus de supports que la Form 3 – dans certains cas jusqu'à 60 % de plus – ce qui augmente rapidement nos coûts lorsque nous avons de nombreuses itérations pour de nombreux produits », a déclaré M. Vong.
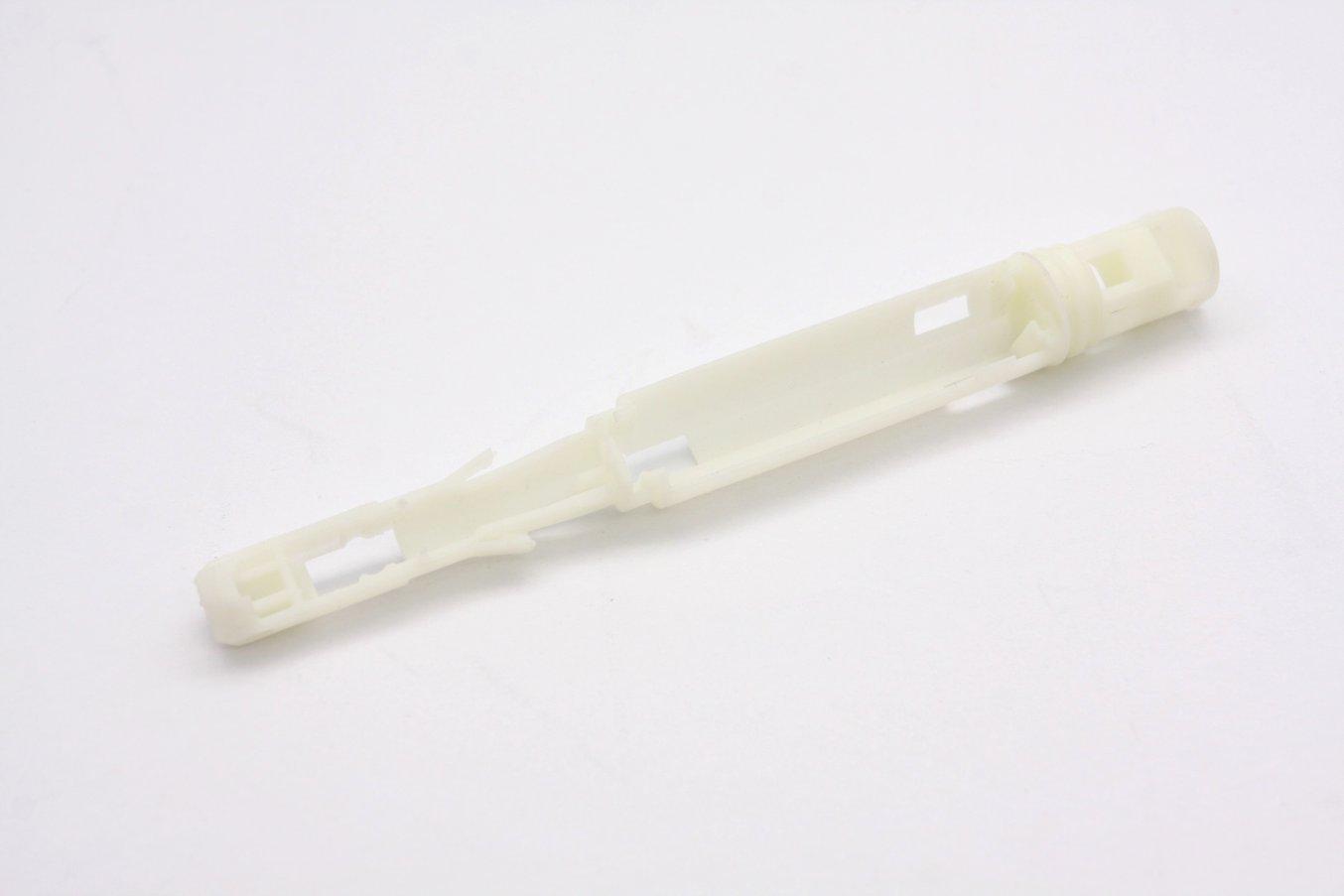
Un châssis de brosse à dents électrique imprimé en 3D avec White Resin sur la Form 3.
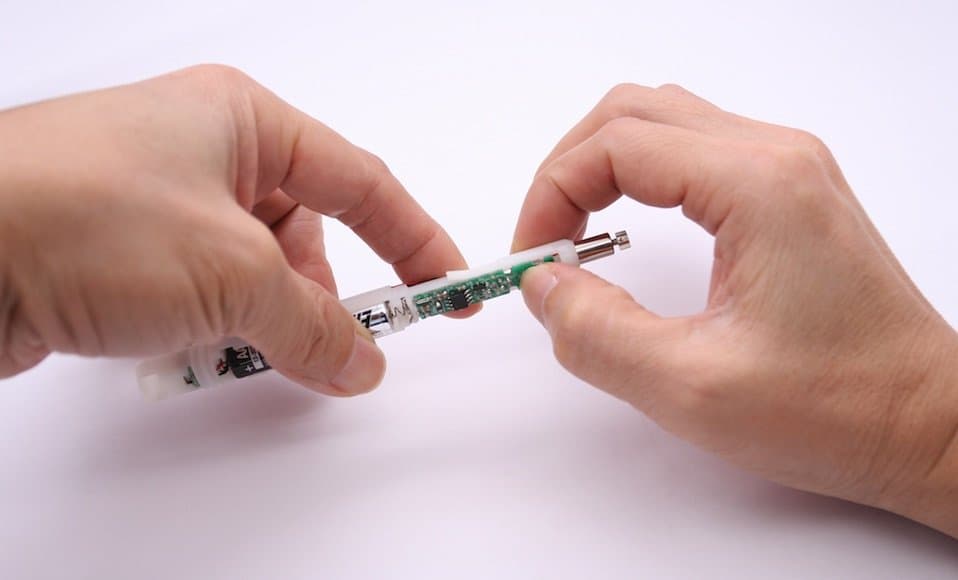
Les prototypes de châssis des brosses à dents électriques doivent être robustes et très précis pour pouvoir accueillir toute l'électronique.
Créer des prototypes sans outillage de moulage par injection rapide
« Prenons l'exemple du développement des boutons de la brosse à dents électrique : il y a quelques années, sans outil d'injection rapide pour produire de véritables pièces moulées en plastique, nous ne pouvions jamais être sûrs à 100 % du fonctionnement du ressort en plastique », a déclaré M. Vong.
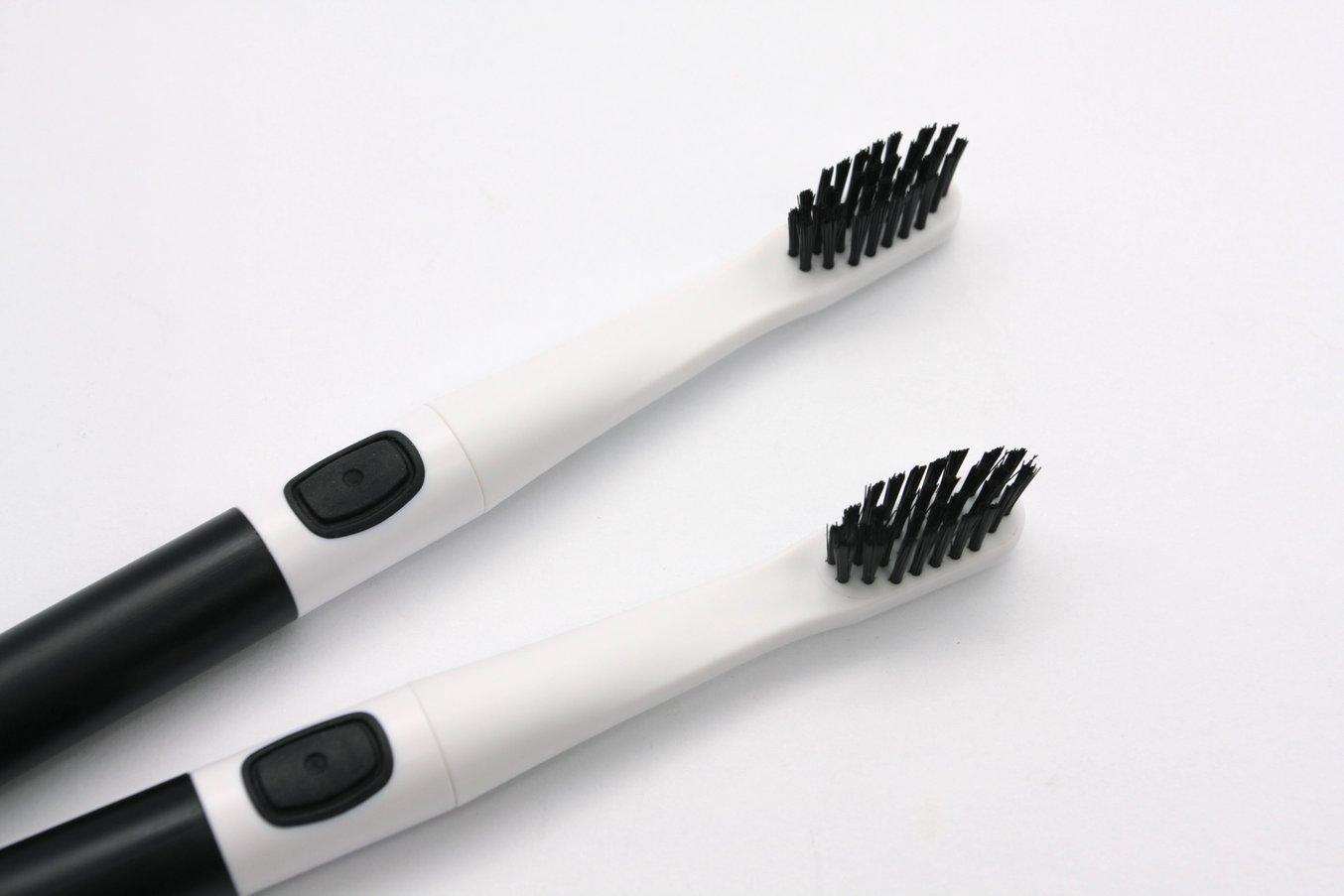
Un prototype de brosse à dents électrique imprimé sur la Form 3 avec White Resin (en bas), et le produit plastique final réalisé par moulage par injection (en haut).
« Nous utilisons désormais l'imprimante Form 3 et Tough 2000 Resin pour certains de nos prototypes. Les impressions sont très similaires à celles du POM (polyoxyméthylène) moulé par injection. Grâce à cela, nous sommes non seulement en mesure de construire un prototype à des fins de démonstration, mais aussi de tester différents modèles pour comparer leurs fonctionnalités, et d'optimiser les dimensions en quelques heures si nécessaire », a déclaré M. Vong.
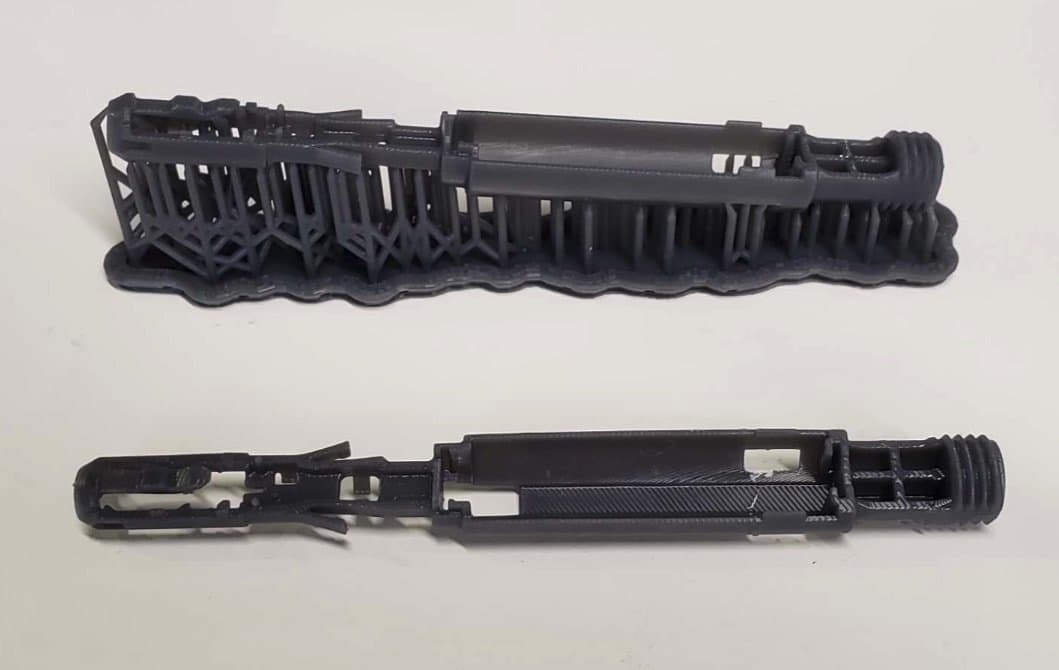
Le prototype de châssis de brosse à dents électrique imprimé avec la résine technique Tough 2000 Resin de Formlabs.
Les prochaines étapes pour Hayco
Les soins bucco-dentaires sont un secteur prometteur pour Hayco, un secteur où elle peut s'imposer grâce à son expertise en matière de touffetage, de moulage et d'assemblages électroniques et mécaniques, ainsi qu'à ses tests très poussés. La technologie d'impression 3D de Formlabs permet à Hayco de développer des produits pour le marché en pleine croissance de l'Asie-Pacifique, en s'appuyant sur son expérience dans la fabrication de brosses.
« Nous continuerons à investir dans les technologies d'impression 3D, comme nous le faisons depuis 20 ans. Nous travaillons actuellement sur des inserts en métal fritté au laser pour la fabrication de moules. Nous produisons déjà des pièces qu'il serait pratiquement impossible de fabriquer autrement », a déclaré M. Vong.
« Nous avons trouvé en Formlabs un excellent partenaire, et nous attendons avec impatience leurs prochains développements pour étendre les possibilités offertes par leurs matériaux », a déclaré M. Vong.
Curieux d'essayer nos matériaux d'ingénierie ? Examinez et testez par vous-même la qualité de nos matériaux Formlabs pour trouver celui qui répond à vos besoins.