Impression 3D et galvanoplastie dans le cadre d'expériences scientifiques
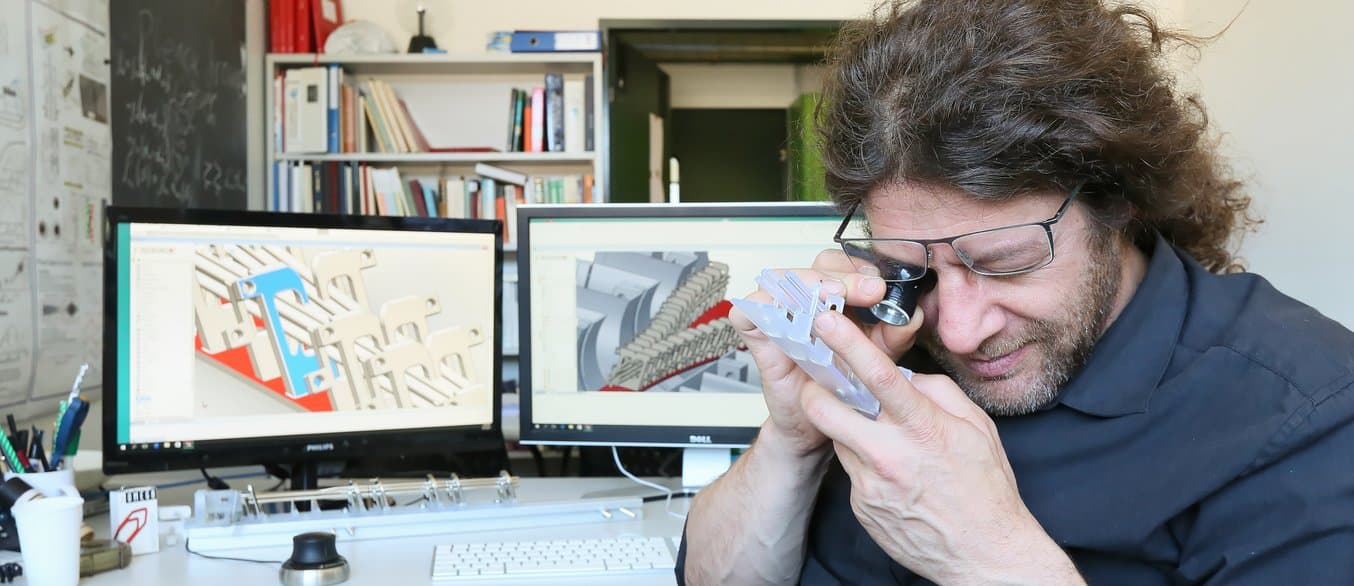
Andreas Osterwalder appelle son bureau le « musée ». Ce qui ressemble à une collection de petites machines est constitué de pièces imprimées en 3D puis partiellement traitées par galvanoplastie, que le scientifique a réalisées pour mener ses expériences à l'École polytechnique fédérale de Lausanne (EPFL), en Suisse.
Ces dispositifs expérimentaux, comme le séparateur de faisceau d'Osterwalder, réalisent des fonctions extrêmement complexes. Transformer une piste de recherche en une expérience peut facilement prendre des mois ou même des années. Une difficulté courante est de fabriquer des composants spécifiques sur mesure.
Avec l'aide d'une entreprise de galvanoplastie spécialisée dans le prototypage rapide, Osterwalder a trouvé une méthode lui permettant de réaliser rapidement et à moindre coût des pièces pour ses expériences pointues, grâce à l'impression 3D et la galvanoplastie.

Le sujet de recherche d'Osterwalder fait partie d'un domaine apparu récemment, appelé « chimie à basses températures ».
Des molécules ou des atomes entrant en collision provoquent des réactions chimiques. La majeure partie des réactions chimiques importantes pour les humains se passent à la température ambiante ou au-delà. Mais des collisions se produisent également à des températures beaucoup plus basses, même s'il n'y a alors pratiquement pas de mouvement.
L'objectif des recherches d'Osterwalder est d'étudier la chimie au zéro absolu, -273,15 °C, et de comprendre les aspects les plus élémentaires des interactions moléculaires se produisant dans ces conditions.
Afin d'observer les molécules et de les contrôler à une température aussi basse, les scientifiques doivent pouvoir en contrôler complètement le déplacement.
« Imaginez un jet d'eau : le faisceau de molécules se trouve dans le vide et, dans ces conditions, nous pouvons commencer à contrôler la direction dans laquelle est dirigé le jet », explique Osterwalder, qui a réalisé un séparateur de faisceau macroscopique pour cette expérience.
Première étape vers des dispositifs expérimentaux imprimés en 3D
Un chercheur peut produire un schéma technique complexe en très peu de temps, mais fabriquer le dispositif expérimental relève de l'ingénierie de précision, utilisant des méthodes traditionnelles telles que l'usinage classique ou CNC, et cette fabrication requiert généralement plusieurs mois. Osterwalder souhaitait trouver une méthode plus rapide et plus économique pour passer de l'idée à l'expérience.
Il a entendu parler de l'impression 3D pour la première fois vers 2009, mais la précision des procédés alors disponibles FDM (dépôt de filament fondu), SLA (stéréolithographie) et frittage, n'était pas suffisante ou leur coût trop élevé.
La stéréolithographie est une technologie d'impression 3D qui utilise un laser pour polymériser de la résine liquide et créer un produit fini imprimé. Plus d'informations sur le .
Avec l'imprimante 3D Form 2 qu'Osterwalder a acheté en 2015, à sa sortie, lui a apporté toute satisfaction. « L'impression 3D SLA est une simple question de résolution », constate Osterwalder. « C'est ce qui m'a permis de me concentrer sur la création de structures complexes, que l'imprimante va reproduire pratiquement à l'identique. »
Un séparateur de faisceau fabriqué en quelques jours au lieu de plusieurs mois
Le séparateur de faisceau, imprimé en 3D et traité par galvanoplastie, permet à Osterwalder de diviser en deux un faisceau de molécules en phase gazeuse, sans toucher aux molécules. La structure en métal sert à produire des champs électriques puissants, en appliquant des tensions de l'ordre de 10 000 volts. Ces champs génèrent des forces qui agissent sur les molécules. Ces dispositifs sont faciles à réaliser pour la lumière, en utilisant par exemple un verre partiellement réfléchissant, mais ils sont bien plus difficiles à réaliser lorsqu'il s'agit de molécules.

Grâce à l'impression 3D et à la galvanoplastie, Osterwalder a pu réduire le temps de production de ce montage expérimental de plusieurs mois à moins d'une semaine. Osterwalder a passé quelques jours à concevoir le séparateur de faisceau et seulement 36 heures pour l'imprimer en 3D dans son laboratoire. Le placage au nickel de la structure par galvanoplastie n'a pris qu'une journée supplémentaire. Finalement, c'est l'aller-retour des pièces imprimées entre le laboratoire et l'entreprise de galvanoplastie qui a pris le plus de temps dans tout le processus.
Galvanoplastie de pièces imprimées en 3D
Les pièces galvanisées sont présentes partout, des robinets à eau aux grilles de calandre automobile. Elles sont recouvertes par électrolyse de chrome, d'argent ou d'autres métaux de grande qualité, pour améliorer l'aspect et les propriétés du matériau, comme la résistance à l'usure et la conductivité électrique.
En revanche, la galvanoplastie appliquée aux plastiques reste très difficile. Les plastiques ne conduisent généralement pas l'électricité, ce qui est fondamental dans le procédé de galvanoplastie. Un traitement chimique préalable peut résoudre ce problème, mais, jusqu'au début des années 2000, il n'a pu s'appliquer avec succès qu'à certains plastiques, dont l'ABS. Osterwalder a alors sollicité les conseils d'une entreprise suisse, Galvotec.
« J'ai voulu relever le défi d'appliquer la galvanoplastie à d'autres matériaux » raconte Rico Schuhmacher, fondateur de Galvotec. « J'ai réalisé de multiples recherches et expériences avec différents matériaux plastiques. Un an plus tard, en 2012, j'ai décidé de fonder mon entreprise de galvanoplastie appliquée aux plastiques. »
Il n'existe dans le monde que quelques entreprises de galvanoplastie, spécialisées dans le prototypage rapide, et Galvotec est la seule en Suisse. « Les pièces de M. Osterwalder devaient être partiellement recouvertes de métal. Cela signifie que certaines surfaces devaient subir l'électrolyse et d'autres non. C'est à l'aide de masques que nous y sommes parvenus », explique Schuhmacher. « Un autre défi était d'empêcher le contact entre deux surfaces. Nous avons donc dû traiter ces pièces séparément. »

Le scientifique est convaincu que l'association des techniques d'impression 3D et de la galvanoplastie peut être étendue à la réalisation d'expériences jusque-là impossibles.
Consultez l'article de recherche publié récemment par Osterwalder et Gordon pour savoir comment la galvanoplastie de pièces en plastique imprimées en 3D peut ouvrir d'innombrables pistes de recherche.
Osterwalder ne pense pas qu'à l'avenir ces avantages soient limités à son domaine de recherche spécifique. Pour lui, en fait la question n'est pas de savoir quoi faire avec un séparateur de faisceau imprimé en 3D, mais bien de savoir comment le reproduire pour d'autres expériences.
« Dans la plupart des domaines de recherche, la reproduction exacte de la même expérience est cruciale pour sa vérification et les recherches ultérieures. L'impression 3D pourrait nous permettre de réaliser un système adaptable, fait de briques comme celles du LEGO, dans lesquelles chaque pièce est imprimée en 3D et peut être reproduite », explique encore Osterwalder. Dans cette perspective, les instituts et les laboratoires de recherche du monde entier auraient alors la possibilité de mener et reproduire des expériences grâce au simple transfert d'un fichier STL.
Exploitation de l'impression 3D dans le domaine de la recherche
Le séparateur de faisceau d'Osterwalder vous a inspiré ? Comment utiliser l'impression 3D comme outil de pointe pour la recherche et enseignement.