Produire des prototypes de haute précision pour les montres mécaniques grâce à l’impression 3D
Les montres et leurs mouvements sont des appareils de mesure précis qui doivent à la fois être beaux et adaptés au goût des clients. L’association de ces deux conditions n’est pas toujours chose aisée.
Petra Möller, directrice de la gestion de produit chez Sinn Spezialuhren, et son équipe sont régulièrement confrontés au défi de devoir concrétiser les concepts de produits. Pour cela, ils ont récemment commencé à utiliser l’imprimante 3D stéréolithographique (SLA) Form 3 pour créer des prototypes de leurs modèles de montre.
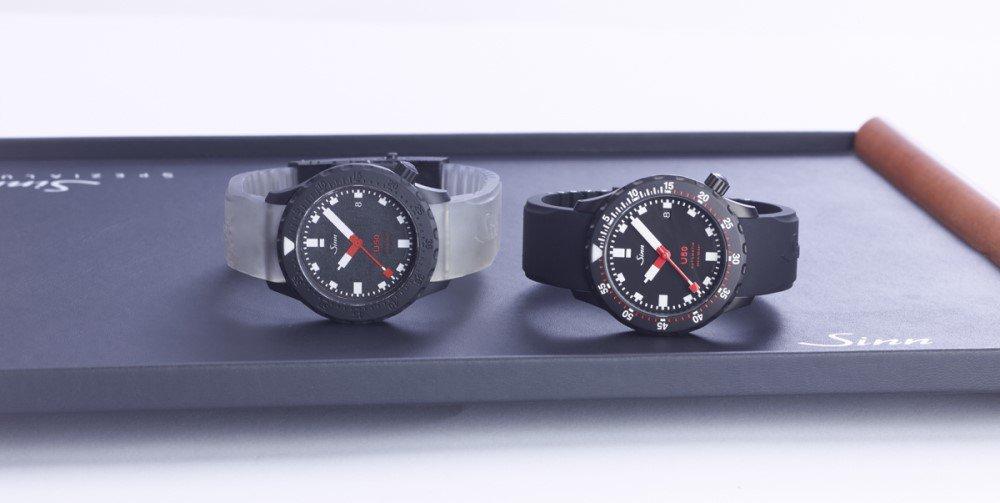
Prototype de montre imprimé en 3D à l’aide de la Form 3, à côté du produit fini.
Depuis près de 60 ans, Sinn Spezialuhren est synonyme de montres mécaniques riches en fonctionnalités. Sa gamme de produits s’étend des montres aviateurs aux montres de plongée, en passant par des chronographes et des chronomètres de mission portés par des pilotes, des plongeurs et l’unité tactique d’élite GSG 9 de la police fédérale allemande. Au cours du processus de développement, la conception d’une montre est fortement influencée par sa fonctionnalité prévue, qui constitue souvent un défi pour l’équipe.
Améliorer le développement de produits avec l’impression de prototypes en 3D
Nils Hunder travaille au sein de l’équipe de Petra Möller sur le développement et la conception de boîtiers, de mouvements et de bracelets de montres. Le travail de cette équipe consiste à faire progresser le développement des produits jusqu’à la production en série et de collaborer avec l’ensemble des services.
Les pièces de montres sont souvent petites, avec des détails fins qui affectent sensiblement l’apparence et la fonctionnalité d’un dispositif d’horlogerie. Certaines des questions essentielles au cours du processus de développement consistent à déterminer si les proportions de la montre sont correctes, à quoi ressemble la forme du boîtier sur le bras ou la meilleure façon d’attacher le bracelet au boîtier.
Souvent, les dessins des produits, informatisés ou faits à la main, ne communiquent pas de manière optimale la réalité du produit fini sur le bras. Pour que le développement du produit soit un succès, il est extrêmement utile de créer des prototypes avant que la montre ne soit produite en masse.
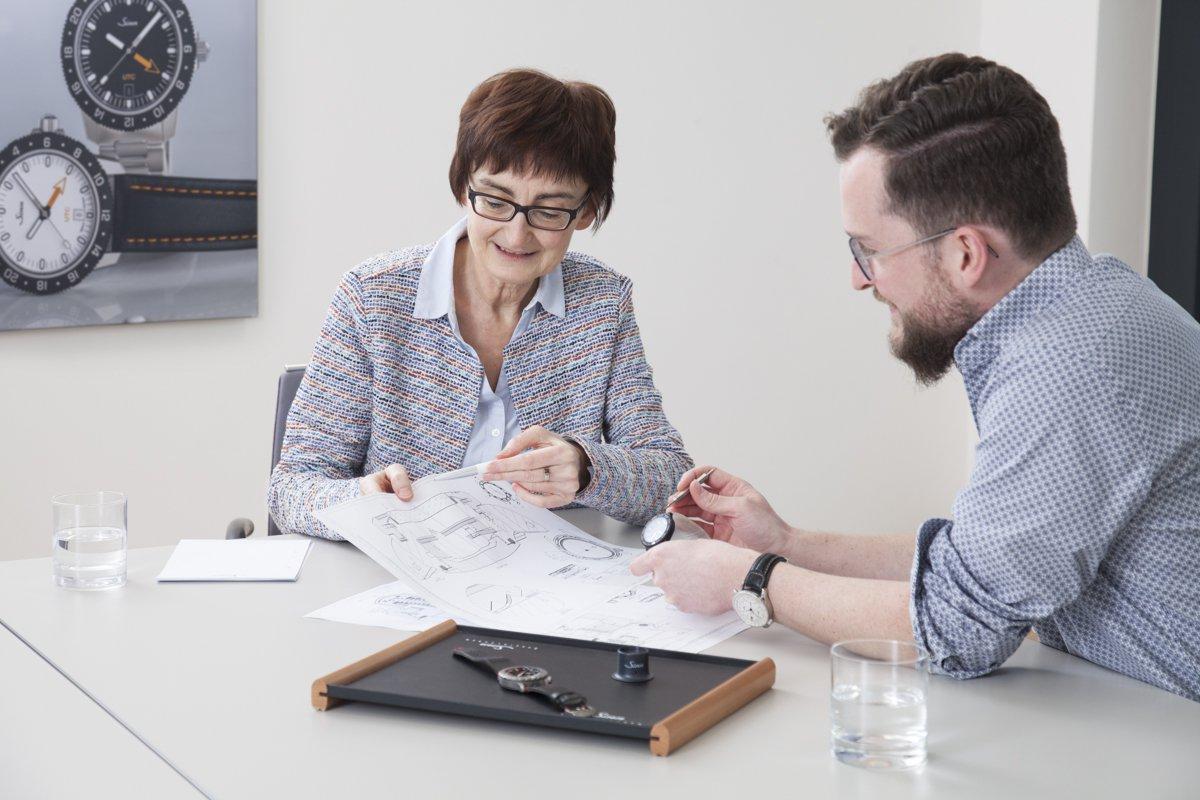
Petra Möller et Nils Hunder comparant les dessins techniques avec un modèle de montre imprimé en 3D.
« L’utilisation précoce de prototypes réduit au minimum le gaspillage de moyens et les développements mal orientés. »
Petra Möller, directrice de la gestion de produit
Jusqu’à présent, Sinn commanditait la production des prototypes à un fournisseur de services externe. Au début, les modèles de montre étaient imprimés en 3D SLA à partir d’une résine synthétique qui était très délicate et se cassait facilement. Ce n’était pas le matériau adéquat pour des modèles qui doivent également être portés au poignet afin d’en apprécier le style et le ressenti. L’équipe est ensuite passée à l’impression 3D à l’aide d’imprimantes 3D FDM (dépôt de fil fondu) et d’un matériau cireux. Cependant, ceux-ci devaient quand même être moulés en aluminium, ce qui était très fastidieux et coûteux. « Par le passé, les prototypes étaient utilisés bien plus tard dans le processus de développement. Tout était déjà fini à ce stade et, avant d’appuyer sur le bouton de démarrage de la machine à commande numérique, nous jetions un dernier coup d’œil à la montre », indique Hunder.
La volonté de l’équipe d’introduire l’impression 3D en interne fait que Hunder a passé beaucoup de temps à suivre Formlabs. Il s’est montré enthousiaste au sujet de l’aspect lisse de la qualité de la surface obtenue grâce aux imprimantes 3D SLA, même si la Form 1 et la Form 2 ne l’ont pas complètement convaincu de leur valeur ajoutée. Comme il est souvent nécessaire d’utiliser des structures de support avec la technologie SLA, l’équipe s’est longtemps demandé si une imprimante FDM avec des structures de support lavables et une surface plus rugueuse ne serait pas un meilleur choix. En fin de compte, c’est la qualité de la surface et les structures de support facilement amovibles de la Form 3 qui ont convaincu Petra Möller et Nils Hunder d’acquérir cette machine, ainsi que les outils de post-traitement Form Wash et Form Cure. Depuis, leur nouvelle imprimante Low Force Stereolithography (LFS) est régulièrement utilisée pour le développement de prototypes.
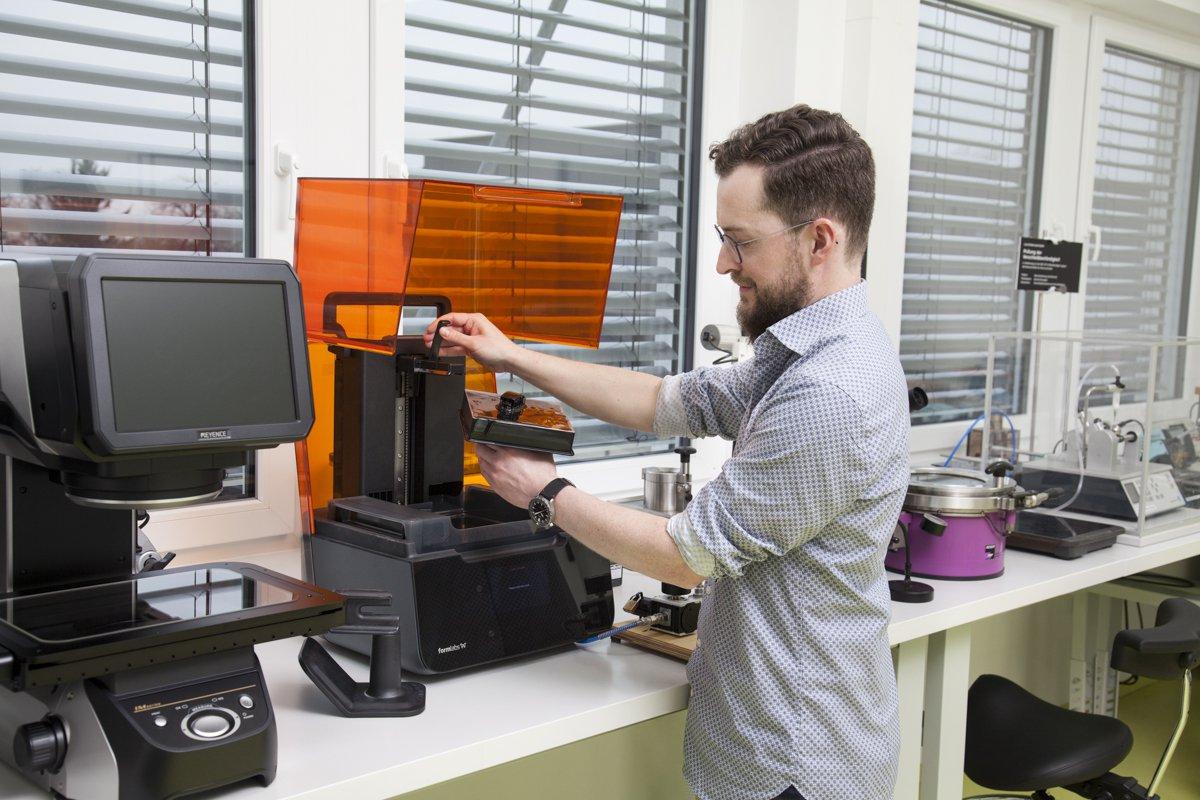
Nils Hunder utilisant la Form 3
Des prototypes de haute précision imprimés en 3D pendant la nuit
Grâce au laser haute précision de la Form 3, des détails fins tels que des gravures ou des stries sur la couronne du boîtier de la montre peuvent être imprimés. Le matériau que l’équipe préfère est Black Resin, pour l’impression des boîtiers de montre. Les détails ressortent mieux avec une épaisseur de couche de 25 microns. Quasiment aucun post-traitement n’est nécessaire et le boîtier peut subir une finition de surface ultérieurement, en étant par exemple peint à l’aérographe pour obtenir la couleur désirée.
« Nous utilisons principalement la Form 3 au cours du processus de conception afin de voir les premières ébauches le plus rapidement possible et de savoir à quoi ressemble la montre en termes de proportions, ainsi que de tester son ressenti sur le poignet. »
Nils Hunder, ingénierie et développement de produits
L’équipe a découvert que l’utilisation de la Form Wash et le lavage adéquat des pièces imprimées dans de l’éther monométhylique de tripropylène-glycol (TPM), suivi d’un rinçage dans de l’alcool isopropylique, étaient essentiels. Les bracelets possèdent de fins canaux qui peuvent se boucher et retenir la résine à l’intérieur lors de la post-polymérisation si les modèles n’ont pas subi un lavage minutieux.
Mis à part ce détail, la mise en place de l’impression 3D chez Sinn Spezialuhren a été un jeu d’enfant. L’impression 3D est désormais utilisée au cours des phases initiales du développement des prototypes et des modèles. Les modèles sont souvent imprimés pendant la nuit afin que les ajustements et les nouvelles itérations puissent être faites très tôt.
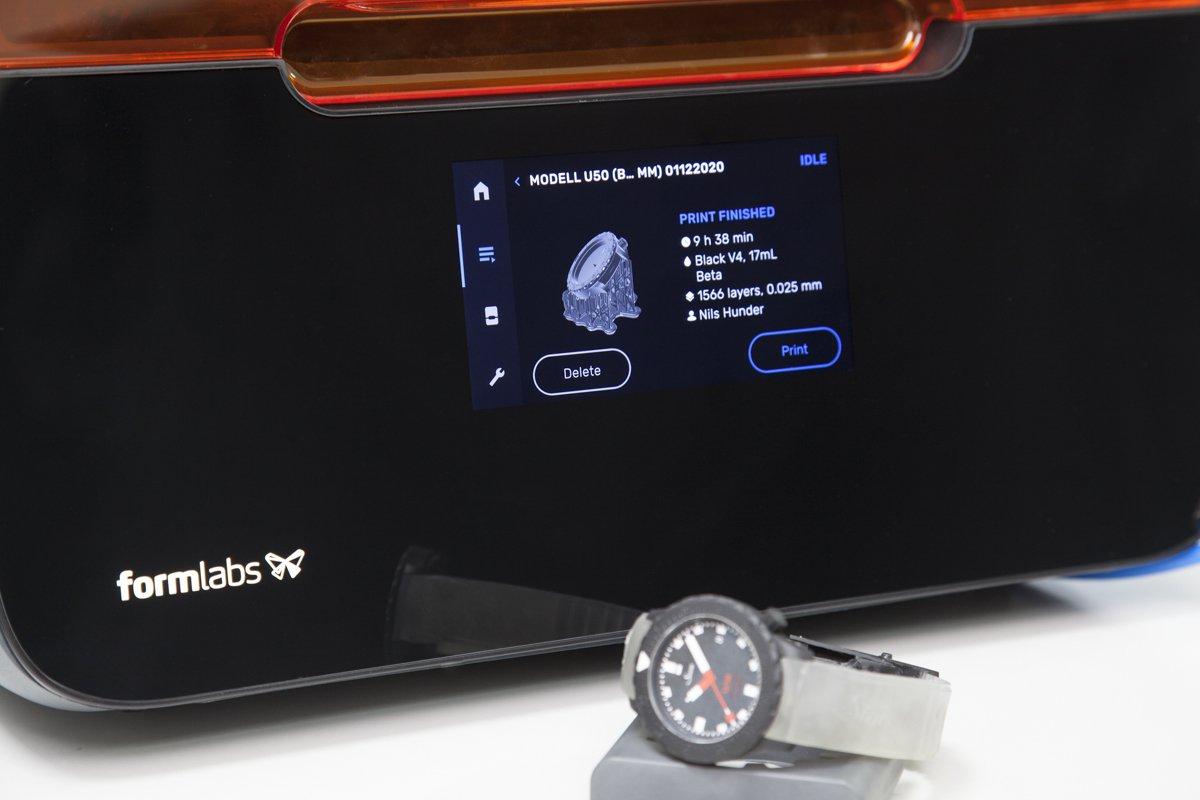
Le prototype d’une montre devant la Form 3.
Grâce à la gamme en constante évolution de matériaux pour les imprimantes 3D de Formlabs, l’équipe se voit souvent suggérer de nouvelles idées à tester en prototypage. Par exemple, le nouveau matériau Flexible 80A Resin possède une dureté similaire à celle du silicone utilisé pour les véritables bracelets de montre. C’est pourquoi l’équipe de Sinn a déjà utilisé ce matériau pour imprimer en 3D des prototypes de type silicone.
Impression 3D rapide et rentable d’outils de fabrication pour l’horlogerie
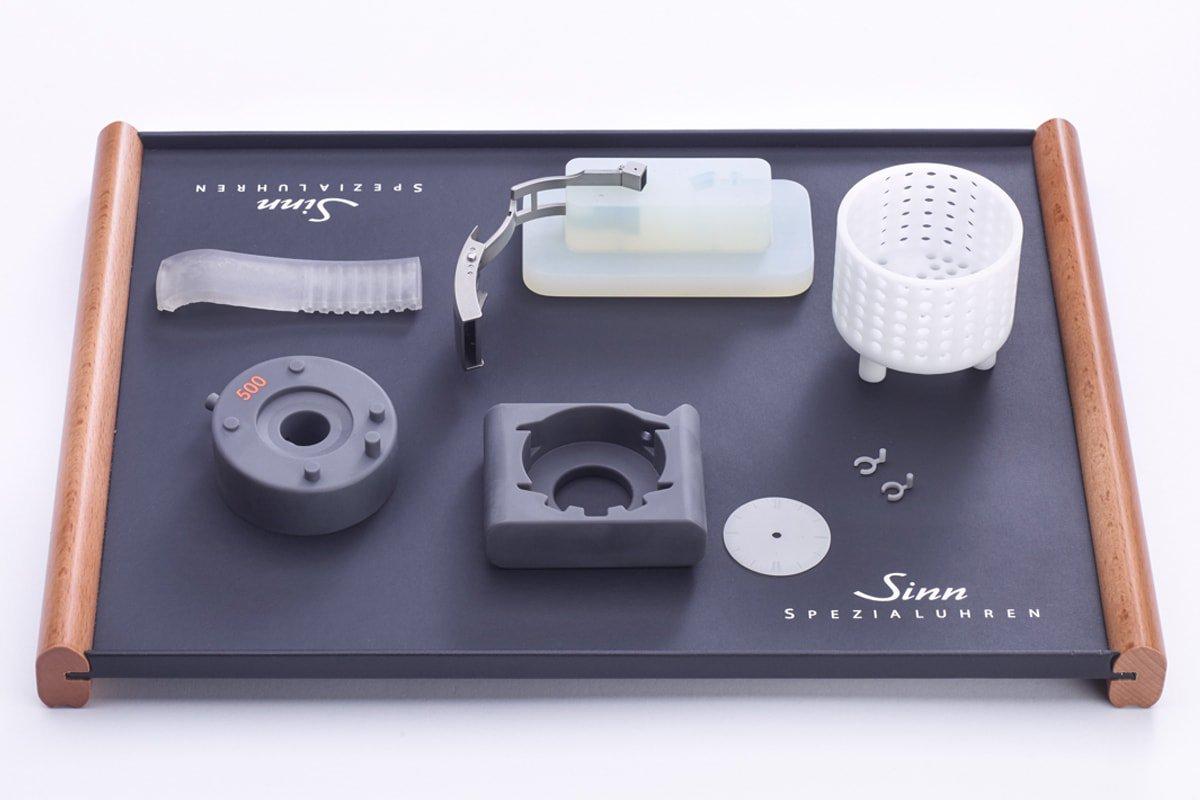
Prototypes de pièces de montre, de fixations et d’équipements de test imprimés en 3D avec la Form 3.
Après l’achat de sa première imprimante 3D, l’équipe de Sinn a rapidement découvert d’autres applications intéressantes pour la machine, en plus du prototypage. La polyvalence de la Form 3 et sa capacité à produire des impressions de qualité de façon régulière se prêtent à différentes applications tout au long du développement de produits et de la production.
Lisez notre article suivant pour découvrir comment l’entreprise a exploité l’impression 3D pour produire des outils de fabrication, tels que des supports, des fixations et des équipements de test.