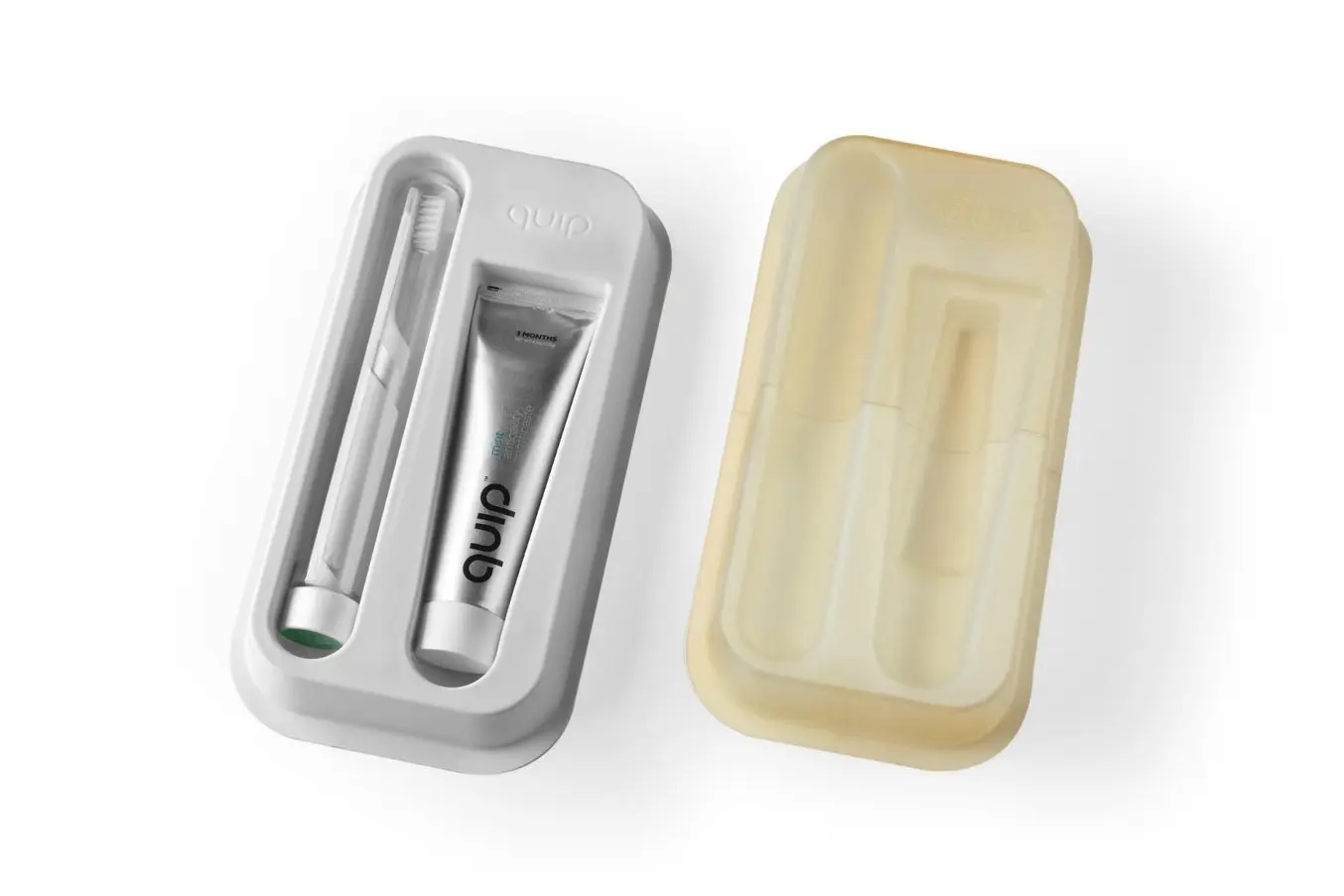
Aujourd’hui, plusieurs commodités que nous utilisons au quotidien sont obtenues par formage sous vide. Sans ce procédé de fabrication polyvalent, les dispositifs médicaux essentiels, l’emballage de la nourriture et même les voitures auraient l’air très différent.
Continuez à lire pour découvrir comment le faible coût et l’efficacité du formage sous vide en font une option très intéressante pour les fabricants industriels, les artisans indépendants et les simples bricoleurs.
Ce guide vous propose une introduction détaillée au formage sous vide comprenant :
-
Un aperçu du procédé de formage sous vide.
-
Comment créer des moules pour le formage sous vide.
-
Les avantages et les limites du formage sous vide.
-
Comment le formage sous vide est utilisé par les entreprises et les créateurs indépendants.
-
Une brève étude de cas sur le formage sous vide et l’impression 3D.
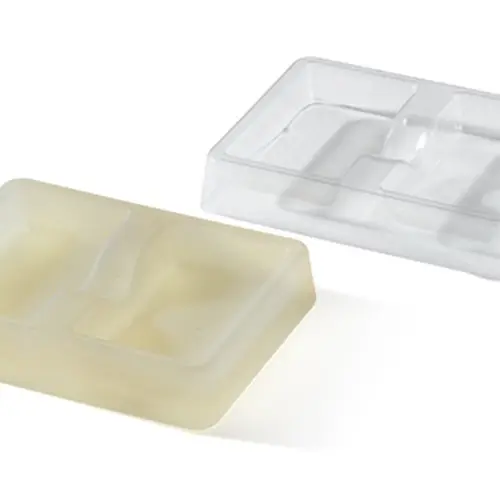
Le formage sous vide à l’aide de moules imprimés en 3D
Téléchargez notre livre blanc pour apprendre comment créer rapidement des moules complexes grâce à l’impression 3D et pour obtenir des conseils et des recommandations à suivre lors de la préparation des pièces de moule.
Qu’est-ce que le formage sous vide ?
Le formage sous vide est un procédé de fabrication utilisé pour former des matières plastiques. Lors du processus de formage sous vide, une feuille de plastique est chauffée puis plaquée sur un moule par aspiration.
Le formage sous vide entre dans une large gamme d’applications de fabrication telles que les petites pièces sur mesure réalisées sur une imprimante de bureau ou des pièces volumineuses fabriquées sur des machines industrielles automatisées.
Quelles sont les différences entre le formage sous vide, le thermoformage et le formage sous pression ?
Le thermoformage est un procédé de fabrication au cours duquel une feuille de plastique est chauffée afin de la rendre souple, puis formée ou profilée à l’aide d’un moule et enfin, ébarbée pour créer une pièce ou un produit fini. Le formage sous vide et le formage sous pression sont deux des types de thermoformage les plus populaires. La principale différence entre le formage sous vide et les autres procédés de thermoformage réside dans les méthodes utilisées pour former les pièces et dans le nombre et le type de moules utilisés.
Le formage sous vide est la méthode la plus simple de thermoformage du plastique. Il nécessite un moule et une pression négative pour obtenir la géométrie de la pièce désirée. Ce processus est idéal pour les pièces qui ne nécessitent des surfaces précises que d’un seul côté, comme par exemple les emballages pour la nourriture ou les appareils électroniques.
Il existe deux grands types de moule : le moule mâle ou positif, qui est convexe, et le moule femelle ou négatif, qui est concave. Pour les moules mâles, la feuille de plastique est déposée sur le moule pour épouser les dimensions intérieures de la pièce en plastique. Pour les moules femelles, la feuille de thermoplastique est placée à l’intérieur du moule pour former avec précision les dimensions extérieures de la pièce.
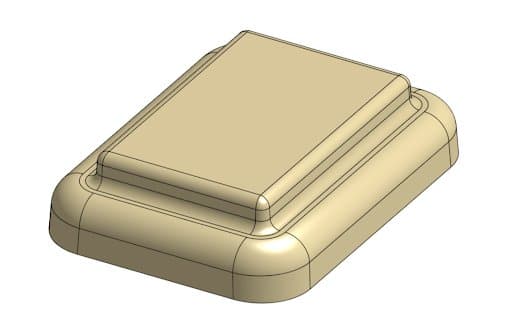
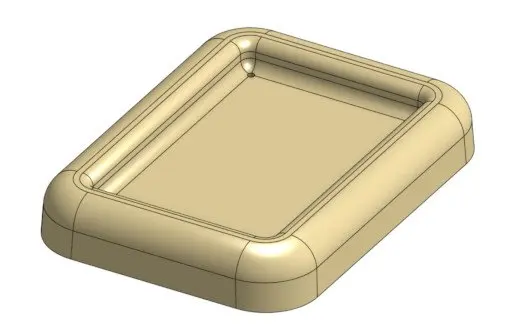
Dans le formage sous pression, une feuille de plastique chauffé est pressée (d’où le nom) entre deux moules au lieu d’être plaquée sur un seul moule par succion. Le formage sous pression est idéal pour fabriquer des pièces en plastique qui doivent présenter une forme très précise sur leurs deux côtés et/ou qui nécessitent une pression plus élevée (elles doivent pénétrer plus loin ou plus profondément dans le moule), telles que les boîtiers d’appareils qui doivent présenter un bel aspect esthétique extérieur et une précision intérieure élevée.
Comment fonctionne le formage sous vide ?
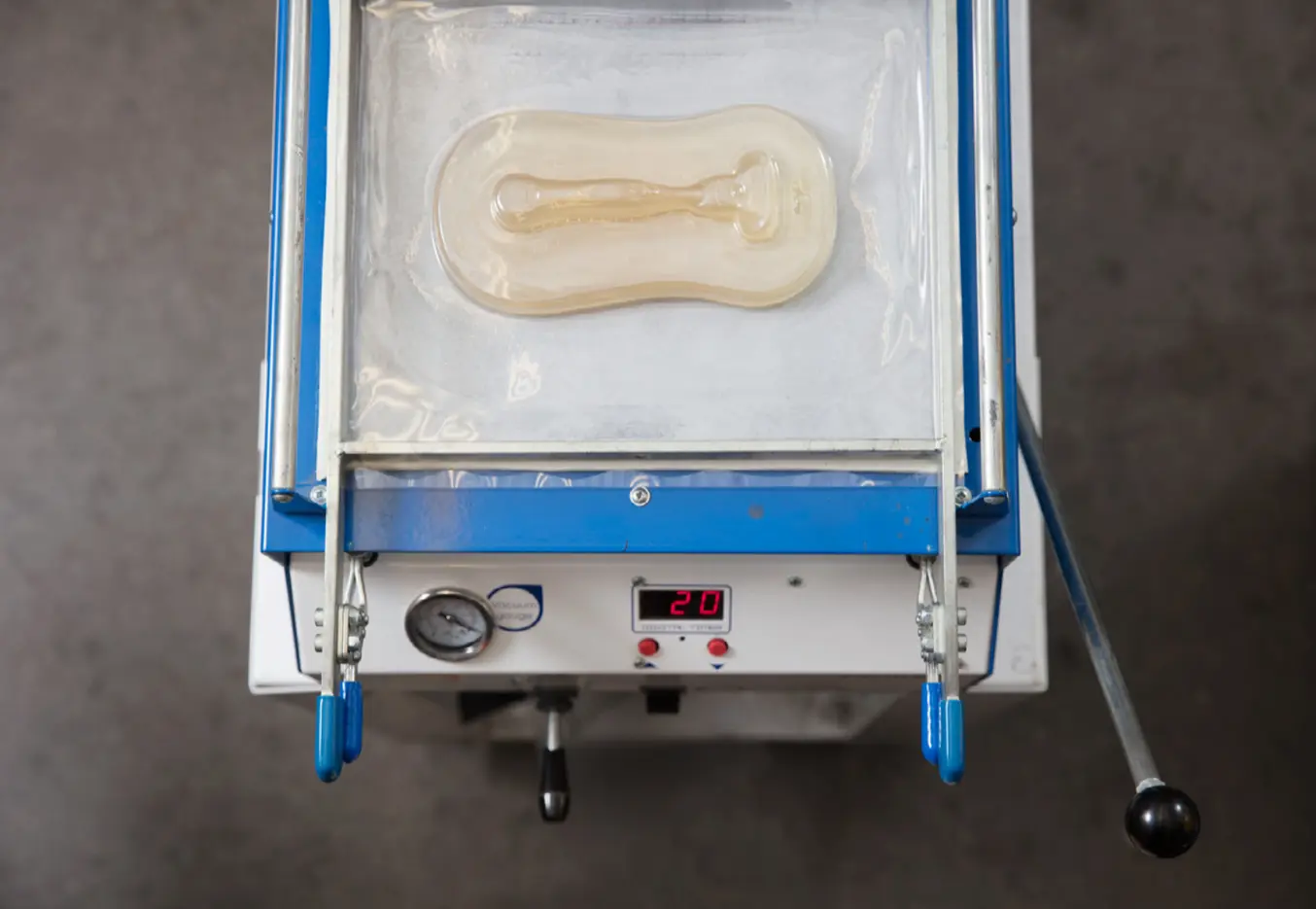
Les étapes successives du procédé de formage sous vide sont les suivantes :
-
Pince : Une feuille de plastique est placée dans un cadre ouvert et serrée en place.
-
Chaleur : la feuille de plastique est assouplie à l’aide d’une source de chaleur jusqu’à ce qu’elle atteigne la température de formage adéquate et devienne pliable.
-
Vide : le cadre maintenant la feuille de plastique chauffée et pliable est abaissé sur un moule et la feuille est plaquée contre celui-ci grâce à un vidé créé de l’autre côté du moule. Les moules femelles (ou convexes) doivent être percés de minuscules trous dans les éléments en creux pour que le vide puisse faire épouser efficacement la forme désirée à la feuille thermoplastique.
-
Refroidissement : une fois le plastique formé autour du moule ou à l’intérieur de celui-ci, il doit être refroidi. Pour les pièces de taille importante, des ventilateurs et/ou une vaporisation de brume sont parfois utilisés pour accélérer cette étape du cycle de production.
-
Détachement : quand le plastique a refroidi, il peut être séparé du moule et détaché du cadre.
-
Découpe : la pièce moulée doit encore être débarrassée de l’excès de matière et ses arêtes peuvent devoir être chanfreinées, poncées ou polies.
Le formage sous vide est un procédé relativement rapide dont les étapes de chauffage et de mise sous vide ne prennent généralement que quelques minutes. Cependant, en fonction de la taille et de la complexité des pièces à réaliser, le refroidissement, la finition et la création des moules peuvent prendre considérablement plus de temps.
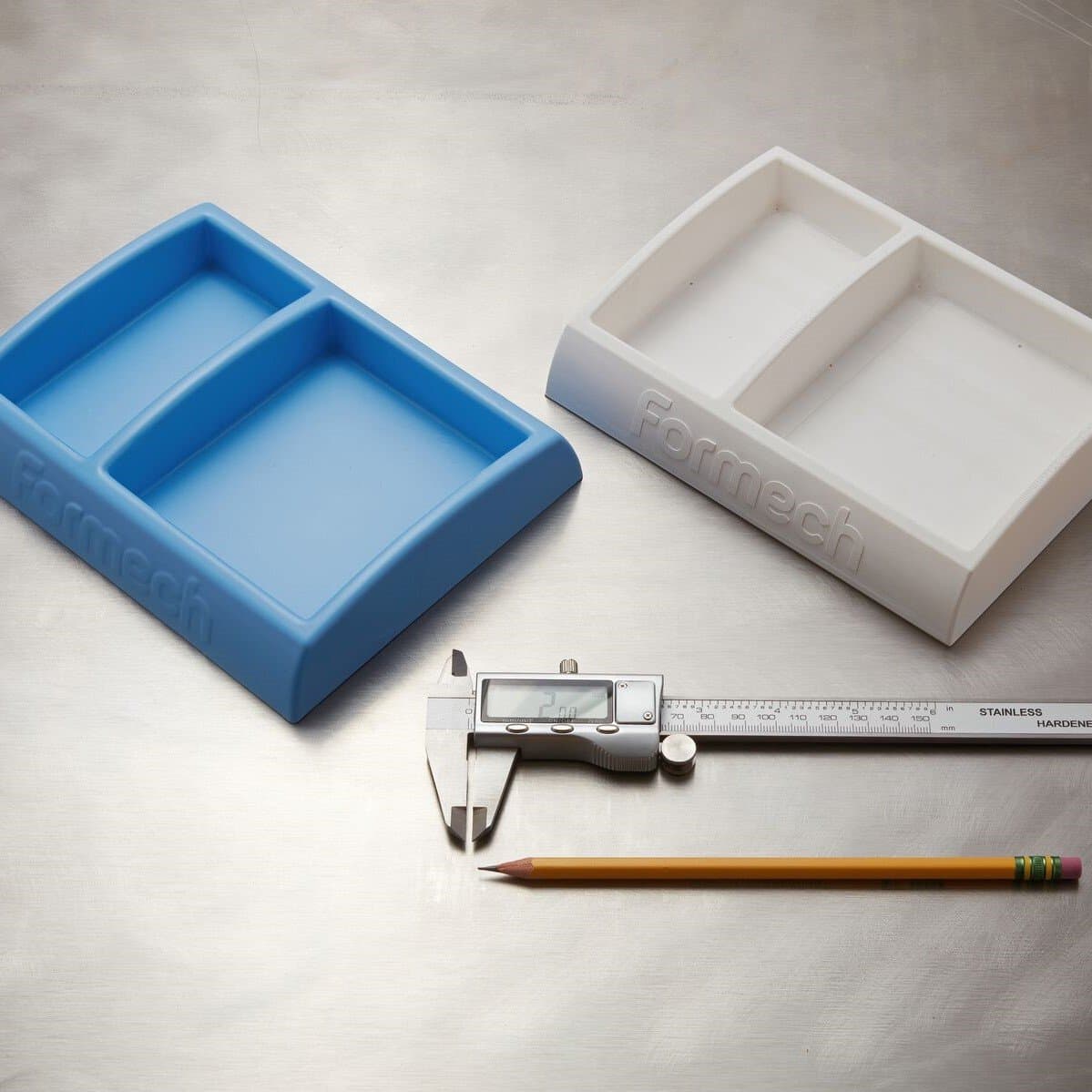
Le thermoformage avec des moules imprimés en 3D : un guide pratique
Accélérez le développement de produits, réduisez les coûts et les délais, et créez facilement des produits personnalisés ou de petites séries en combinant l'outillage rapide imprimé en 3D et le thermoformage.
Les avantages et les inconvénients du formage sous vide
De nombreux fabricants, concepteurs et autres professionnels préfèrent le formage sous vide car il offre une souplesse dans la forme des modèles pour un coût relativement faible comparé aux autres méthodes de fabrication. Voici une liste non exhaustive des avantages du formage sous vide :
Faible coût
Le formage sous vide est généralement plus abordable que les autres méthodes de fabrication telles que le moulage par injection de plastique, surtout pour les productions en petite série (de 250 à 300 unités par an). Le faible coût du formage sous vide est dû en majeure partie aux coûts d’outillage et de prototypage inférieurs qu’il nécessite. En fonction de la superficie de la pièce à réaliser et des dimensions du cadre de bridage, l’outillage pour un moulage par injection peut coûter deux à trois fois plus cher que pour la même pièce réalisée par thermoformage ou formage sous vide du plastique.
Temps de production
Le formage sous vide permet un cycle de production plus court que les autres méthodes de fabrication traditionnelles car l’outillage qu’il nécessite peut être réalisé plus rapidement. Le cycle de production de l’outillage pour un formage sous vide est généralement deux fois plus court que pour outiller un moulage par injection. Quand des imprimantes 3D sont utilisées pour créer les moules, le temps de production peut être encore plus court. En améliorant l’efficacité du processus de production, le formage sous vide permet aux entreprises de commercialiser de nouveaux modèles plus rapidement.
Flexibilité
Le formage sous vide donne aux concepteurs et aux fabricants la flexibilité nécessaire pour tester de nouveaux modèles et réaliser des prototypes sans entraîner de frais ou de délais exorbitants. Les moules peuvent être réalisés en bois, aluminium, mousse structurelle ou en plastique imprimé en 3D pour pouvoir être remplacés et/ou modifiés plus facilement qu’avec les autres procédés de fabrication.
À la fin des années soixante-dix et au début des années quatre-vingts, Dick Teal a eu recours au formage sous vide pour tester des prototypes de pièces pour motoneiges John Deere, principalement parce que cette méthode nécessitait un outillage peu onéreux. Dans ce livre, John Deere Snowmobiles: Development, Production, Competition and Evolution, 1971–1983 », les auteurs expliquent que « des pièces moins chères et un investissement moindre dans l’outillage de production ont créé une situation gagnant-gagnant. »
Le formage sous vide permet également aux concepteurs de proposer un plus vaste choix de couleurs et de personnalisations aux consommateurs. Ceci donne à de nombreuses entreprises la liberté d’offrir à leurs clients des modèles uniques et de réaliser des produits personnalisés tels que des appareils dentaires pour un prix abordable.
Utilisation de matériaux stériles et de qualité alimentaire
Les fabricants utilisent souvent le formage sous vide pour produire des contenants de qualité alimentaire et des pièces pour l’industrie médicale car ce procédé est compatible avec des plastiques stérilisables ou résistants aux contaminants. Par exemple, le polyéthylène haute densité (PEHD) entre souvent dans le formage sous vide de contenants alimentaires.
La résistance du PEHD aux composés acides fait aussi de lui un matériau adéquat pour le formage sous vide de contenants de produits nettoyants. Les plastiques de qualité médicale sont utilisés en formage sous vide pour créer des pièces capables de résister aux processus de stérilisation et de répondre à des normes médicales et/ou pharmaceutiques très strictes.
Limites du formage sous vide
Même si le formage sous vide comporte un certain nombre d’avantages, il a également ses limites. Il ne se prête qu’à des pièces présentant des parois relativement fines et des géométries simples. Les pièces finies peuvent ne pas avoir une épaisseur de paroi constante et les pièces concaves comportant des creux profonds sont difficiles à produire quand elles sont réalisées par formage sous vide.
De plus, même si le formage sous vide est souvent le choix le plus rentable pour des productions en petite à moyenne série, d’autres procédés de fabrication du plastique peuvent être meilleur marché pour les productions en très grande série.
Applications du formage sous vide
De nos jours, il serait bien difficile de passer une seule journée sans entrer en contact avec au moins une pièce réalisée par formage sous vide. Ce procédé de fabrication est utilisé pour produire toute une diversité de pièces dans de larges pans de l’industrie. En voici quelques exemples :
Automobile et transports
Les fabricants utilisent le formage sous vide pour créer une large gamme de pièces pour voitures, bus, bateaux et avions. Dans les voitures, toutes les pièces en plastique, des pare-chocs aux tapis de sol et même les revêtements de coffre sont fabriqués par formage sous vide.
Regardez la plus grande machine rotative de formage sous vide au monde en action.
Le formage sous vide permet aux fabricants de voitures de différencier leur production en termes de couleur ou de niveau d’équipement et donne aux concepteurs la possibilité de tester de nouveaux prototypes en cours de développement.
Industrie
Les fabricants utilisent aussi le formage sous vide pour produire toutes sortes de caisses industrielles et d’emballages profilés pour des machines.
Découvrez comment les panneaux ou les enseignes lumineuses en acrylique sont fabriqués par formage sous vide.
Le formage sous vide est un procédé de fabrication tout indiqué pour les pièces devant être placées en extérieur ou entrer en contact avec une source de chaleur parce que les industriels peuvent utiliser toute une palette de matériaux ignifugés ou résistants aux UV. Par exemple le polychlorure de vinyle (PVC) respectant la norme d’inflammabilité UL 94 V-0 ou l’acrylique traitée anti-UV (PMMA) peuvent tous deux être formés sous vide.
Emballages et présentoirs
Quand vous achetez un produit dans un présentoir en plastique dont il épouse parfaitement la forme, il y a de fortes chances pour que ce présentoir ait été réalisé par formage sous vide. Les rasoirs, brosses à dents, appareils électroniques et les produits de maquillage ou d’entretien sont souvent vendus dans un emballage formé sous vide.
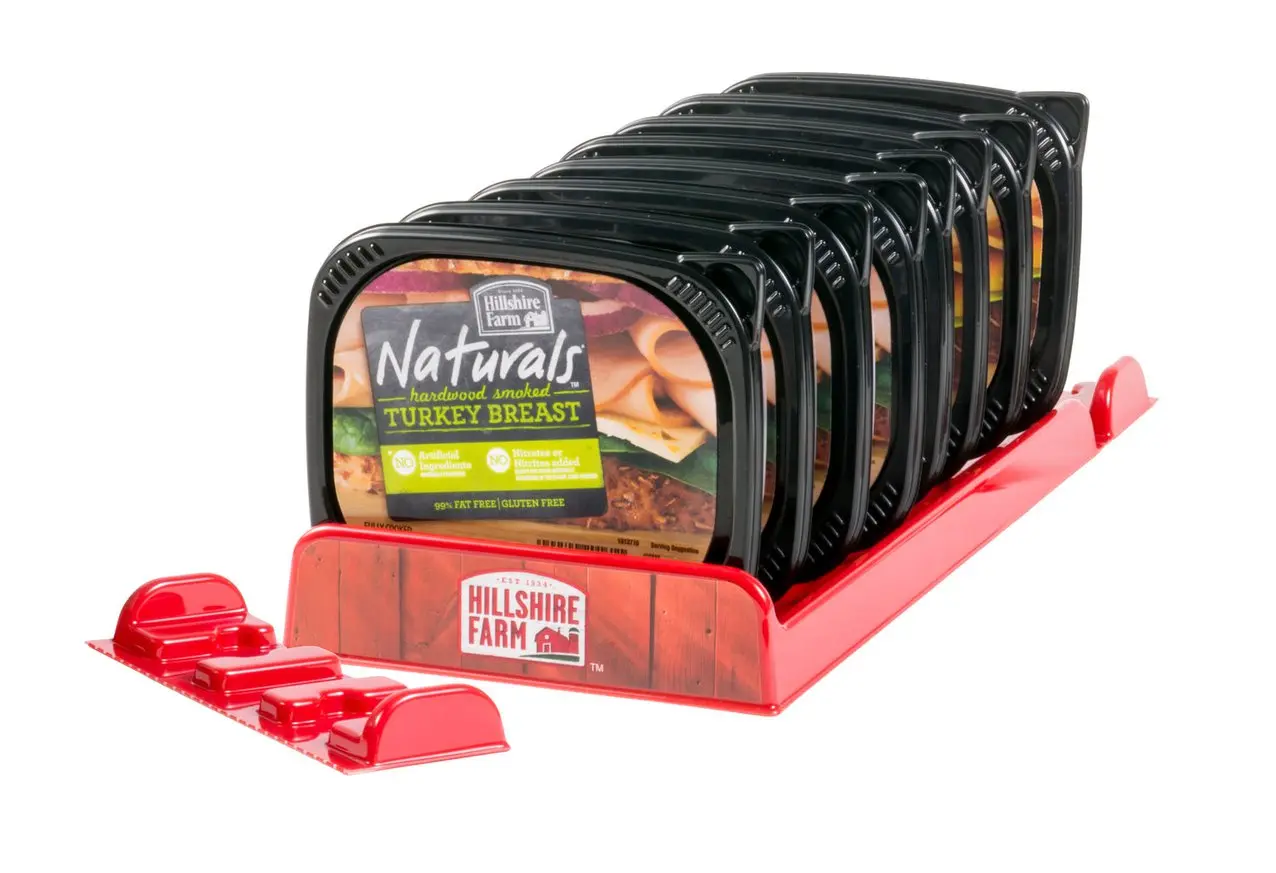
Ce présentoir a été fabriqué par formage sous vide. (source)
En outre, les affichages promotionnels, les affichages sur le lieu de vente (PLV) et les présentoirs de tête de gondole sont, eux aussi, souvent fabriqués par formage sous vide.
Emballages alimentaires
Le formage sous vide est souvent utilisé pour l’emballage alimentaire parce qu’il est compatible avec le plastique de qualité alimentaire et peut produire des pièces faciles à stériliser.
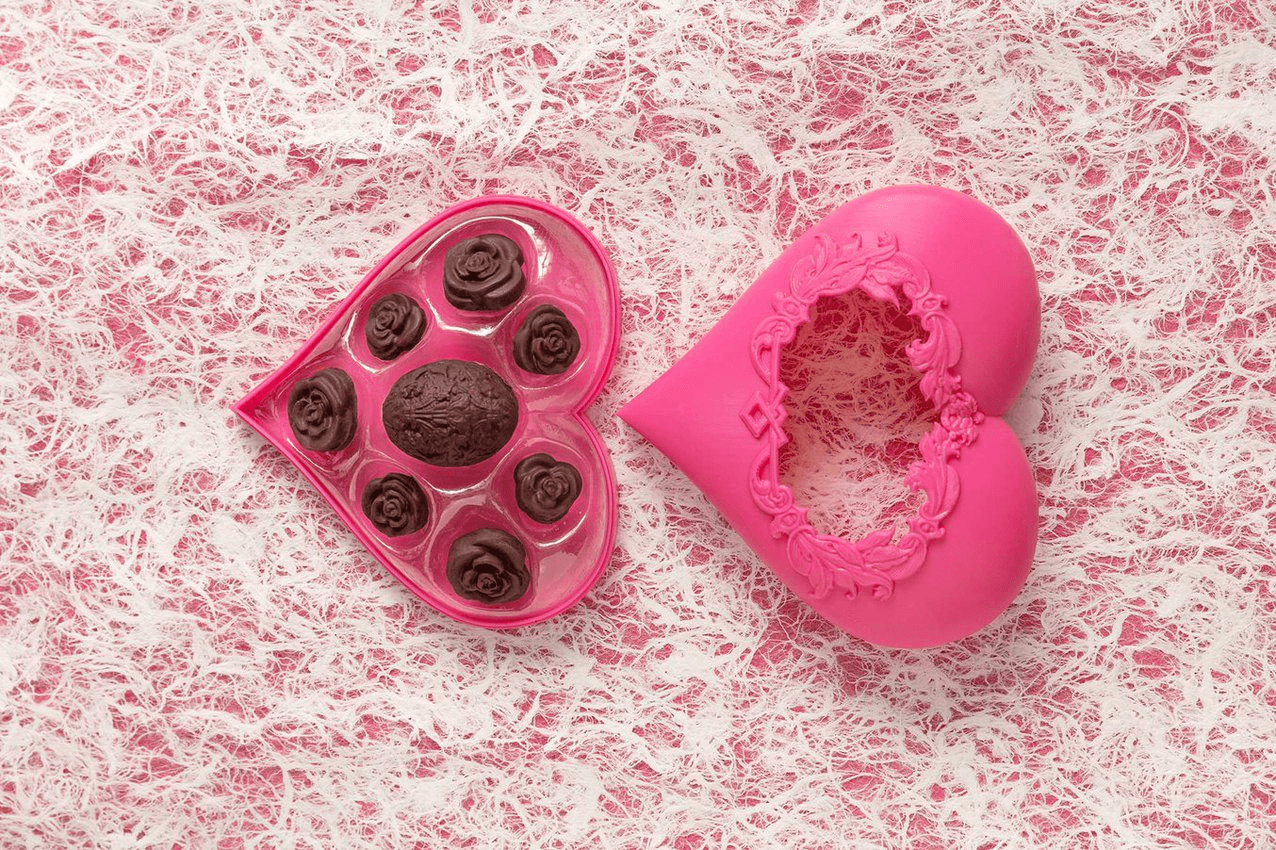
Ces chocolats ont été coulés dans des moules formés sous vide et sont présentées dans un support translucide formé sous vide. Lisez notre guide pour apprendre comment créer des moules à chocolat par impression 3D.
Les emballages de fruits, les supports pour œufs en plastique, et les barquettes de biscuits sont souvent formés sous vide.
Produits de consommation
La liste des produits de consommation réalisés par formage sous vide est pour ainsi dire interminable. Les fabricants peuvent créer des produits tels que des jouets pour enfants, des articles de voyage et de décoration à l’aide du formage sous vide.
Regardez cette vidéo pour découvrir comment les valises rigides sont formées sous vide.
Médical
Les pièces médicales et les composants qui doivent recevoir un traitement antimicrobien ou être résistants aux contaminants sont souvent fabriqués par formage sous vide.
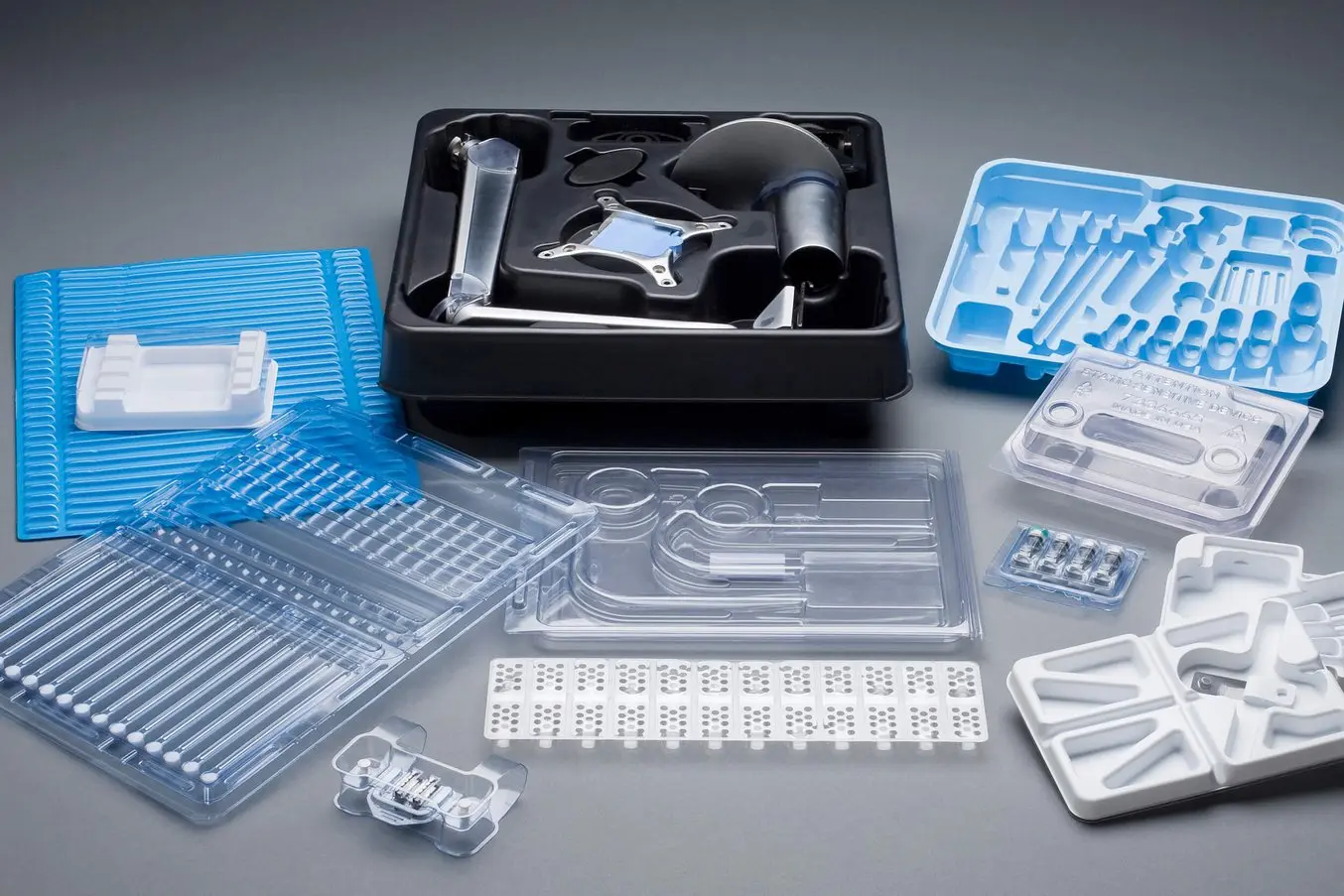
Ces plateaux formés sous vide abritent des composants médicaux. (source)
Ceci comprend les emballages médicaux, les blisters pharmaceutiques dans lesquels sont emballés les pilules, des composants de lit médicalisé et des pièces extérieures de scanner médical et d’appareil d’imagerie par résonance magnétique.
Pièces sur mesure et effets spéciaux
Le formage sous vide intervient dans divers secteurs pour créer des pièces sur mesure et uniques telles que des accessoires pour effets spéciaux.
Regardez cette vidéo dans laquelle Adam Savage explique comment fonctionne le formage sous vide et où il crée un accessoire sur mesure.
Types de thermoformeuses sous vide
Les thermoformeuses sous vide varient grandement en taille, en coût, en complexité et en fonctionnalités, ce qui veut dire que les créateurs indépendants, les bricoleurs et les fabricants professionnels de tous les niveaux peuvent trouver la machine qui leur convient. Les différentes tailles de thermoformeuses sous vide vont des modèles de bureau qui coûtent quelques centaines de dollars aux machines industrielles qui en valent des milliers.
Voici quelques exemples de la diversité des thermoformeuses sous vide :
Les thermoformeuses sous vide industrielles, telles que celles produites par Formech, Ridat ou Belovac, sont idéales pour les applications commerciales et la fabrication de pièces de grande envergure.
Les thermoformeuses sous vide de bureau, telles que la Mayku FormBox qui utilise un aspirateur ménager standard pour créer le vide d’air, sont parfaites pour les petites entreprises et les professionnels travaillant de chez eux.
Les machines de formage sous vide à réaliser soi-même peuvent aussi être efficaces, et le processus de fabrication même de la machine constitue un projet éducatif parfait pour les enfants et les adolescents.
Quand vous utilisez une machine de formage sous vide, pensez à toujours respecter les instructions d’utilisation du fabricant, à porter l’équipement de sécurité adéquat et à n’utiliser la machine que dans un environnement bien aéré.
Matériaux adaptés au formage sous vide
Une large gamme de thermoplastiques sont compatibles avec la fabrication par formage sous vide. Voici quelques-uns des plastiques les plus largement utilisés :
-
Acrylique (PMMA)
-
Acrylonitrile butadiène styrène (ABS)
-
Polycarbonate (PC)
-
Polyéthylène (PE)
-
Polytéréphtalate d’éthylène-glycol (PETG)
-
Polypropylène (PP)
-
Polystyrène (PS)
-
Polychlorure de vinyle (PVC)
Comment réaliser des moules de thermoformage
Les concepteurs et les fabricants ont plusieurs options à leur disposition pour réaliser l’outillage nécessaire à une production par formage sous vide. La flexibilité est un gros avantage du formage sous vide en tant que méthode de fabrication et chaque type de procédé de fabrication de moule possède ses propres avantages et limites. Voici quelques-uns des procédés les plus répandus :
Moules imprimés en 3D
De nombreuses entreprises ont recours à l'impression 3D pour créer des moules de formage sous vide, car elle permet un temps de production plus court et des coûts moindres, surtout pour les séries limitées, les pièces sur mesure et les modèles de prototypes. L'impression 3D offre également une liberté de conception inégalée pour créer des moules complexes et travaillés.
Lisez notre guide de conception détaillé pour créer des moules de formage sous vide imprimés en 3D ou téléchargez notre livre blanc pour en savoir plus sur le thermoformage rapide de petites séries avec des moules imprimés en 3D.
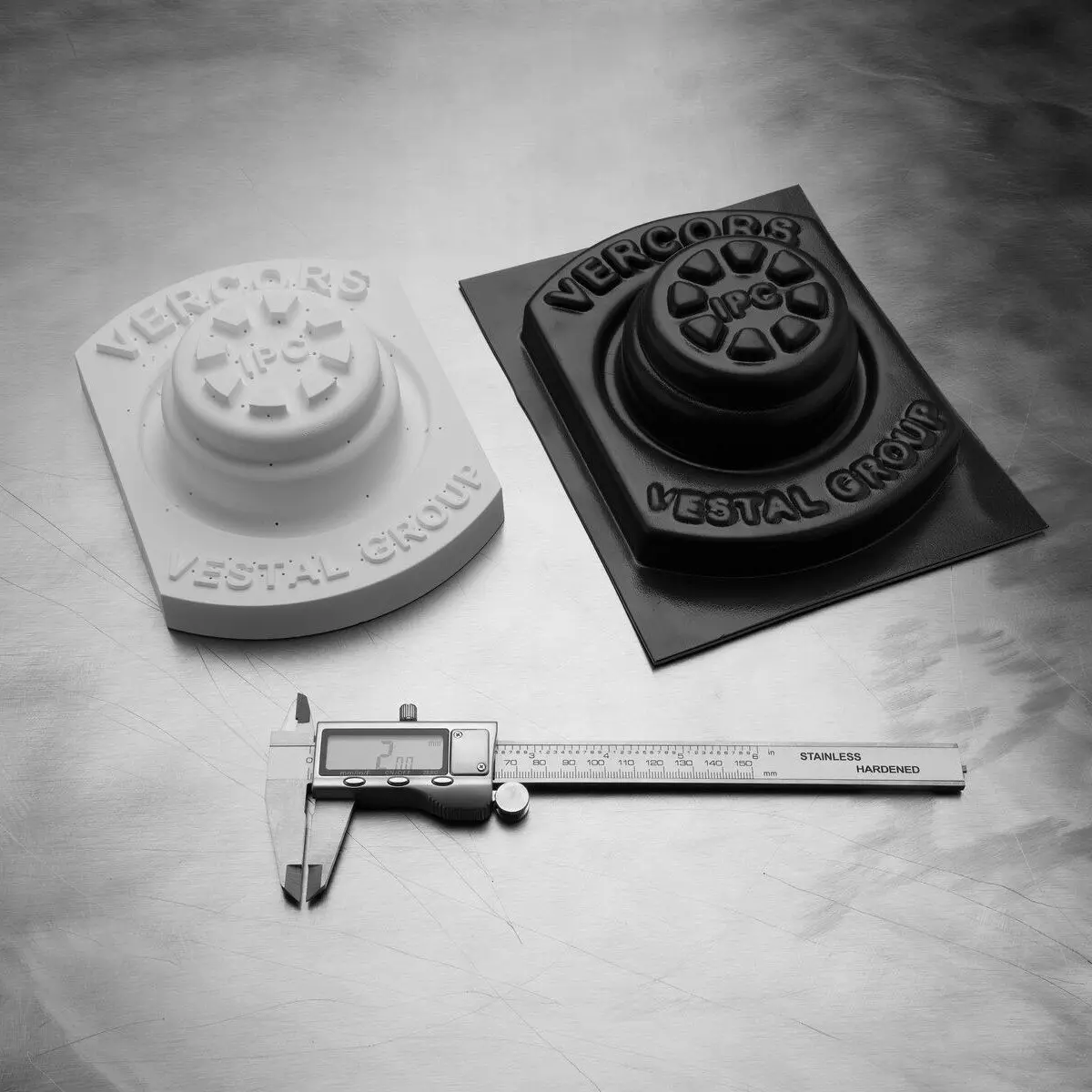
Le thermoformage rapide de petites séries avec des moules imprimés en 3D
Téléchargez notre livre blanc pour apprendre comment créer rapidement des moules complexes grâce à l’impression 3D et pour obtenir des conseils et des recommandations à suivre lors de la préparation des pièces de moule.
Moules de formage sous vide en argile à modeler
Les bricoleurs, artisans et concepteurs qui veulent sculpter un prototype rapide peuvent utiliser l’argile à modeler pour créer un moule de formage sous vide. Cependant, il est à noter que les moules réalisés en argile à modeler ont une espérance de vie d’à peine quelques utilisations. La chaleur appliquée lors du formage sous vide peut causer l’apparition de fissures dans le moule en argile et sa destruction rapide.
En outre, il est important de donner aux moules en argile tout le temps nécessaire à leur refroidissement avant de les utiliser pour le formage sous vide. Toute l’humidité présente dans l’argile doit être complètement évaporée ou éliminée par cuisson pour qu’elle n’obstrue pas le vide ou endommage l’équipement de mise sous vide.
Moules de formage sous vide en bois
Les moules en bois ont une longévité considérablement plus élevée que celle des moules en argile et peuvent résister à plusieurs centaines, voire plusieurs milliers de moulages avant de se détériorer. Les concepteurs indépendants et les lignes de production commerciales utilisent l’un comme l’autre des moules en bois pour créer leurs produits. Opter pour du bois dur tel que le chêne peut encore augmenter la durée de vie du moule. Les moules en bois sont la solution idéale pour les moules épais comportant un minimum de détails fins.
La limite de ce type de moule est qu’il se dilate et se contracte légèrement lors du processus de formage sous vide. À terme, ceci peut causer l’apparition de fissures ou d’échardes dans le moule ou bien sa déformation. Malgré tout, le bois reste un excellent choix de matériau pour bon nombre de modèles et il est facile de sculpter cette matière à l’aide de quelques outils de travail du bois basiques.
Moules en aluminium coulé
Les moules en aluminium sont plus chers et prennent plus de temps à produire (le délai de production peut aller de deux semaines à deux mois) que les autres options d’outillage. Pour cette raison, les moules en aluminium usiné ou coulé ne sont pas fréquemment utilisés pour les petites séries ou les prototypes, mais bien plus souvent pour les productions de masse. Les thermoformeuses sous vide industrielles utilisent souvent un outillage en aluminium car ces moules sont considérés comme ayant l’une des durées de vie les plus longues de toutes les options d’outillage disponibles pour le formage sous vide.
Moules en mousse structurelle
Les moules en mousse structurelle peuvent être une alternative bon marché aux moules en aluminium coulé tout en offrant une durabilité comparable. Les pièces en mousse structurelle sont plus légères que celles en aluminium coulé, ce qui peut représenter un avantage non négligeable sur certaines lignes de production.
Étude de cas : à la pointe de l’innovation avec le formage sous vide et l’impression 3D
Ashford Orthodontics, le plus grand laboratoire spécialisé en orthodontie du Royaume-Uni, est un pionnier en fabrication de dispositifs dentaires car ses procédés associent l’impression 3D au formage sous vide. En utilisant de pair ces méthodes de fabrication, ses spécialistes ont raccourci leur cycle de production global par rapport à la concurrence et ont permis aux cliniciens d’offrir un traitement plus rapidement et de manière plus fluide aux patients.
Ashford Orthodontics est capable de fournir des appareils de maintien orthodontique et autres dispositifs aux cliniciens à peine 48 heures après la réception des scans numériques grâce à son cycle de production en continu savamment orchestré. Quand le laboratoire reçoit une nouvelle commande, il analyse les scans numériques, modélise les mouvements des dents dans un logiciel CAO dentaire, puis envoie le résultat à son parc impressionnant d’imprimantes 3D pour une impression du jour au lendemain. Le jour suivant, la réplique imprimée de la dentition du patient est utilisée comme moule pour le formage sous vide de plaques occlusales et d’appareils de maintien translucides.
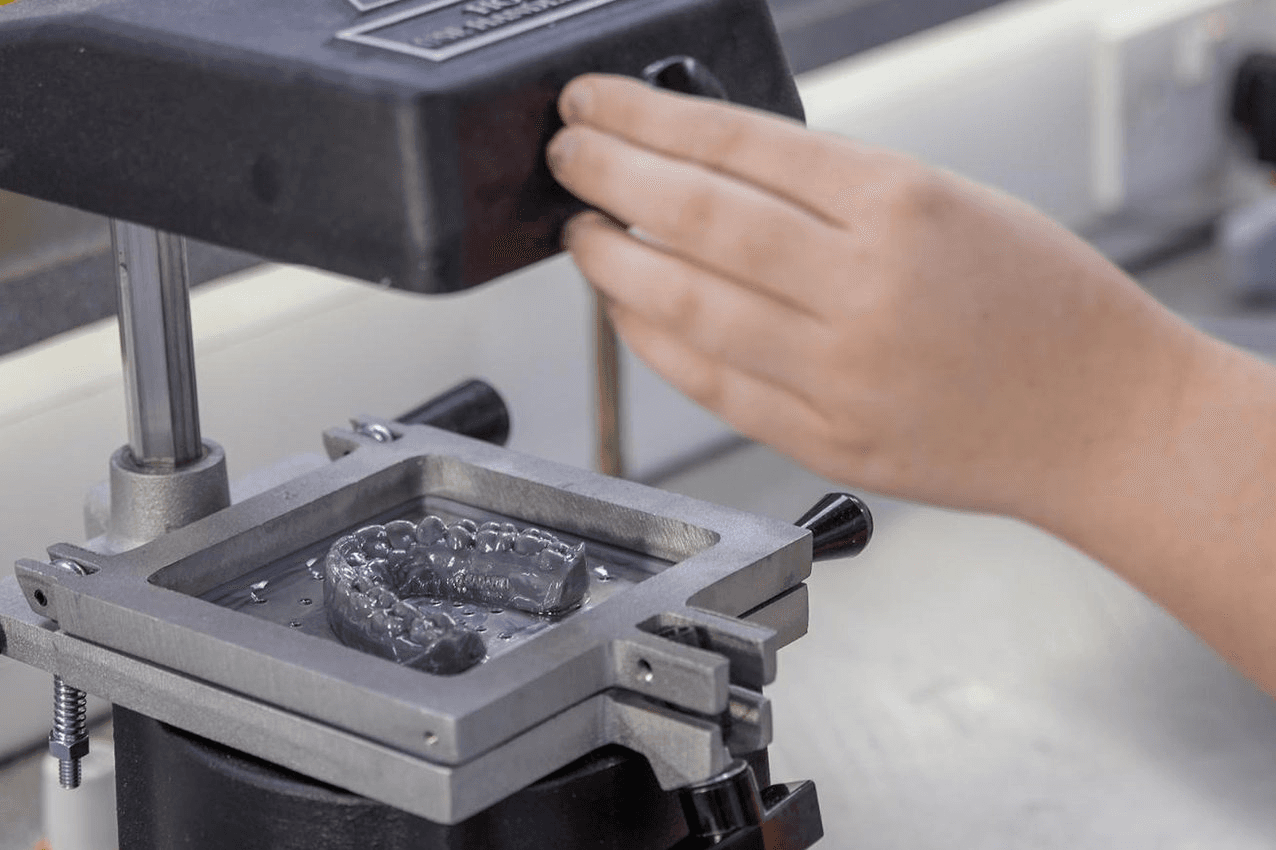
Un technicien de chez Ashford Orthodontics utilise une thermoformeuse sous vide pour produire un appareil de maintien translucide.
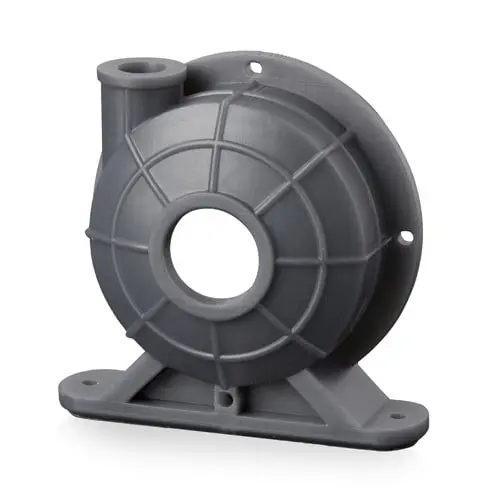
Commander un échantillon gratuit
Examinez et constatez par vous-même la qualité Formlabs. Nous enverrons un échantillon gratuit à votre bureau.
Démarrer avec l'impression 3D de moules de formage sous vide
En combinant des moules imprimés en 3D avec le formage sous vide, vous pouvez améliorer le processus de production en augmentant la flexibilité, l'agilité, l'évolutivité et la rentabilité. Grâce au formage sous vide et aux moules imprimés en 3D, validez votre conception et vos matériaux avant de passer à la production en série, et produisez des pièces personnalisées ou des séries limitées de pièces finales.
Téléchargez notre livre blanc pour en savoir plus sur les directives de conception, les flux de travail détaillés, les conditions du processus de thermoformage et des études de cas réelles impliquant des moules de formage sous vide imprimés en 3D.