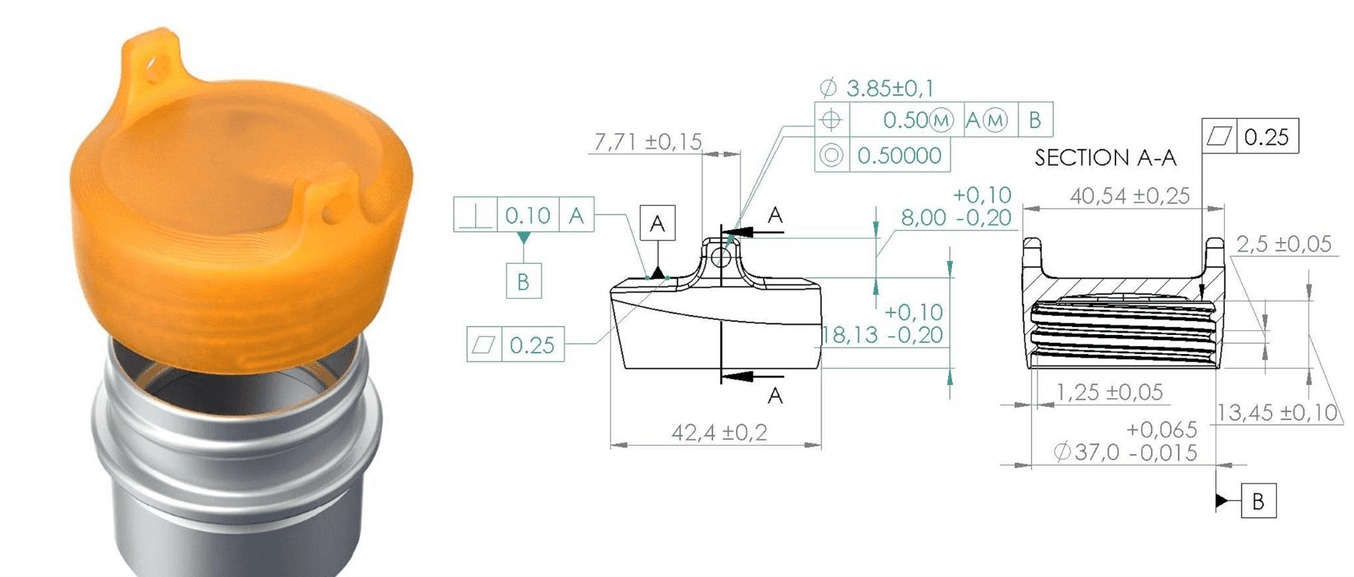
Les objets fabriqués diffèrent en taille et dimensions du modèle CAO initial en raisons des variations qui apparaissent pendant les processus de fabrication. Pour contrôler ces variations et pouvoir communiquer à leur sujet, les ingénieurs et les fabricants se servent d'un langage symbolique, appelé GD&T (Système de cotations et de tolérances géométriques).
Ce langage indique aux partenaires de fabrication ou aux inspecteurs les variations acceptables de l'assemblage du produit, et normalise les modes de mesure de ces variations.
Ce guide présente le système GD&T, qui vise à faciliter la communication relative à la conception dans les secteurs de la production industrielle tant traditionnelle que numérique.
À lire pour en savoir plus :
- Les principes de base du GD&T
- Les divers symboles de définition des tolérances
- Une étude de cas présentant comment le GD&T est utilisé dans Solidworks et une application réelle
Limites des tolérances avant l'apparition du GD&T
Avant l'adoption du GD&T, les caractéristiques de fabrication étaient spécifiées par des zones X-Y. Par exemple, pour le perçage d'un trou de montage, celui-ci devait se trouver dans une zone X-Y déterminée.
Une spécification précise de la tolérance devrait cependant définir la position du trou relativement à sa position souhaitée, la zone d'acceptation étant un cercle. La définition des tolérances X-Y laisse une zone qui aurait produit un faux négatif à l'inspection : l'alésage ne se trouve pas complètement à l'intérieur de la zone carrée définie par X-Y, alors qu'il le serait si la zone était définie comme le cercle circonscrit.
Stanley Parker, un ingénieur qui développait des armes navales pendant la Seconde guerre mondiale, avait remarqué cette erreur en 1940. Poussé par la nécessité d'une production rentable respectant les délais, il élabora un nouveau système, qu'il décrivit dans plusieurs publications. Après avoir démontré que cette méthode était meilleure, le nouveau système est devenu une norme militaire dans les années 50.
Actuellement, la norme GD&T est définie par l'American Society of Mechanical Engineers (ASME Y14.5-2018) aux États-Unis et par la norme ISO 1101-2017 pour tous les autres pays. Il concerne surtout la géométrie globale du produit, d'autres normes décrivant des caractéristiques particulières comme la rugosité de la surface, la texture ou les filetages.
Pourquoi mettre en place des processus GD&T ?
Qu'il s'agisse d'assemblages fonctionnels, de produits composés de plusieurs pièces ou de pièces à fonctions complexes, il est essentiel que tous ces composants fonctionnent correctement ensemble. Tous les ajustements et caractéristiques doivent être spécifiés de façon à minimiser leurs effets sur le processus de fabrication et les investissements qu'ils peuvent entrainer, tout en garantissant la fonctionnalité du produit. Multiplier par deux le niveau de tolérance peut doubler les coûts, voire plus, en raison de l'augmentation du nombre de rejets et des modifications d'outillage. C'est le système GD&T qui permet aux développeurs et aux inspecteurs d'optimiser la fonctionnalité sans augmenter les coûts.
L'avantage le plus important du système GD&T est qu'il décrit l'intention de conception plutôt que la géométrie exacte qui en résulte, de la même façon qu'un vecteur ou une formule sont une représentation plutôt qu'une description d'un objet réel.
Par exemple, la tolérance d'un élément placé à 90° par rapport à une surface peut être définie par sa perpendicularité par rapport à cette surface. Cela définira deux plans espacés l'un de l'autre, entre lesquels le plan central de l'élément doit se trouver. Ou encore, pour percer un trou, il est plus intéressant de définir la tolérance en termes d'alignement par rapport à d'autres éléments.
Décrire la géométrie d'un produit par rapport à la fonctionnalité recherchée et la méthode de fabrication est bien plus simple que de la décrire par ses dimensions linéaires. Cela représente aussi un outil de communication avec les fabricants, les clients ainsi que les inspecteurs contrôle qualité.
Lorsqu'il est bien appliqué, le GD&T permet même d'appliquer la Maitrise statistique des procédés (SPC en anglais), qui réduit les taux de rejet, les échecs d'assemblage et le travail de contrôle qualité, ce qui épargne des ressources substantielles aux entreprises. Il en résulte que plusieurs départements peuvent aussi travailler davantage en parallèle parce qu'ils disposent d'une vision et d'un langage communs de ce qu'ils veulent réaliser.
Comment fonctionne le GD&T ?
Les dessins techniques doivent montrer les dimensions de toutes les parties de la pièce. À côté des dimensions, il faut spécifier une valeur de tolérance, avec ses limites maximum et minimum acceptables. La tolérance est la différence entre la limite maximum et la limite minimum. Par exemple, pour une table dont la hauteur acceptable se situe entre 750 et 780 mm, la tolérance sera de 30 mm.
Cependant cette tolérance implique qu'une table qui aurait une hauteur de 750 mm d'un côté et de 780 mm de l'autre serait acceptable, alors que sa surface présenterait des irrégularités d'une amplitude de 30 mm. Donc, pour spécifier correctement la tolérance acceptable pour ce produit, il nous faut communiquer l'intention de conception par un symbole qui indique que la surface de la table doit être plane. C'est pourquoi il faut ajouter une tolérance de planéité à la tolérance globale portant sur la hauteur.
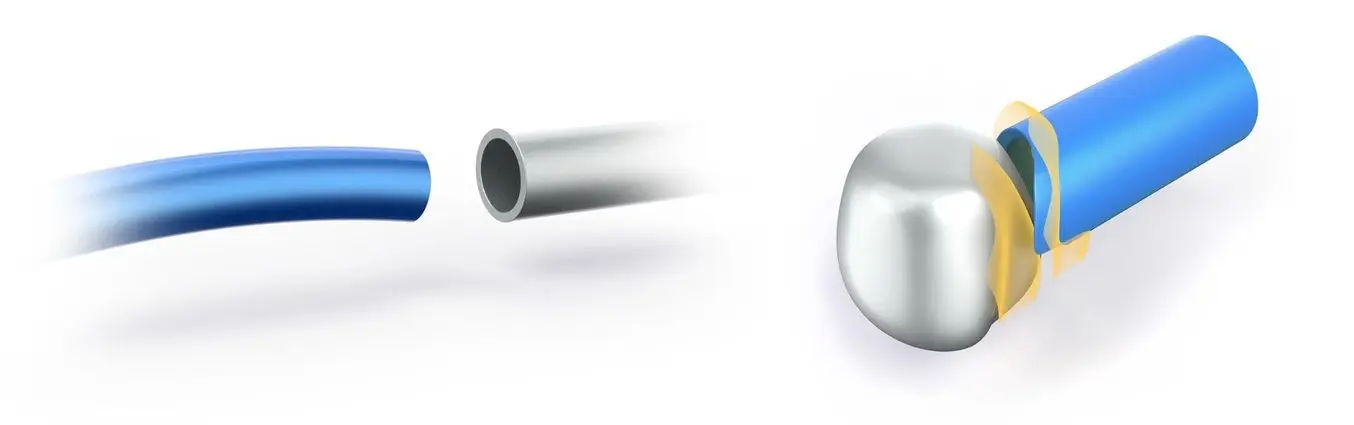
Des pièces présentant des variations non prévisibles et des formes complexes demandent des règles de GD&T plus compliquées qu'une tolérance spécifiée par plus ou moins.
De façon similaire, un cylindre avec un diamètre de tolérance ne rentrera pas obligatoirement dans l'alésage prévu s'il est légèrement courbé pendant sa fabrication. Il faut donc en contrôler la rectitude, ce qui sera difficile avec une tolérance spécifiée par plus ou moins. Ou un tube qui doit s'adapter parfaitement à une surface complexe pour y être soudé doit être contrôlé à l'aide d'un profil de surface.
Le GD&T établit une bibliothèque de symboles qui décrivent les intentions de conception, que nous allons présenter dans la section suivante.
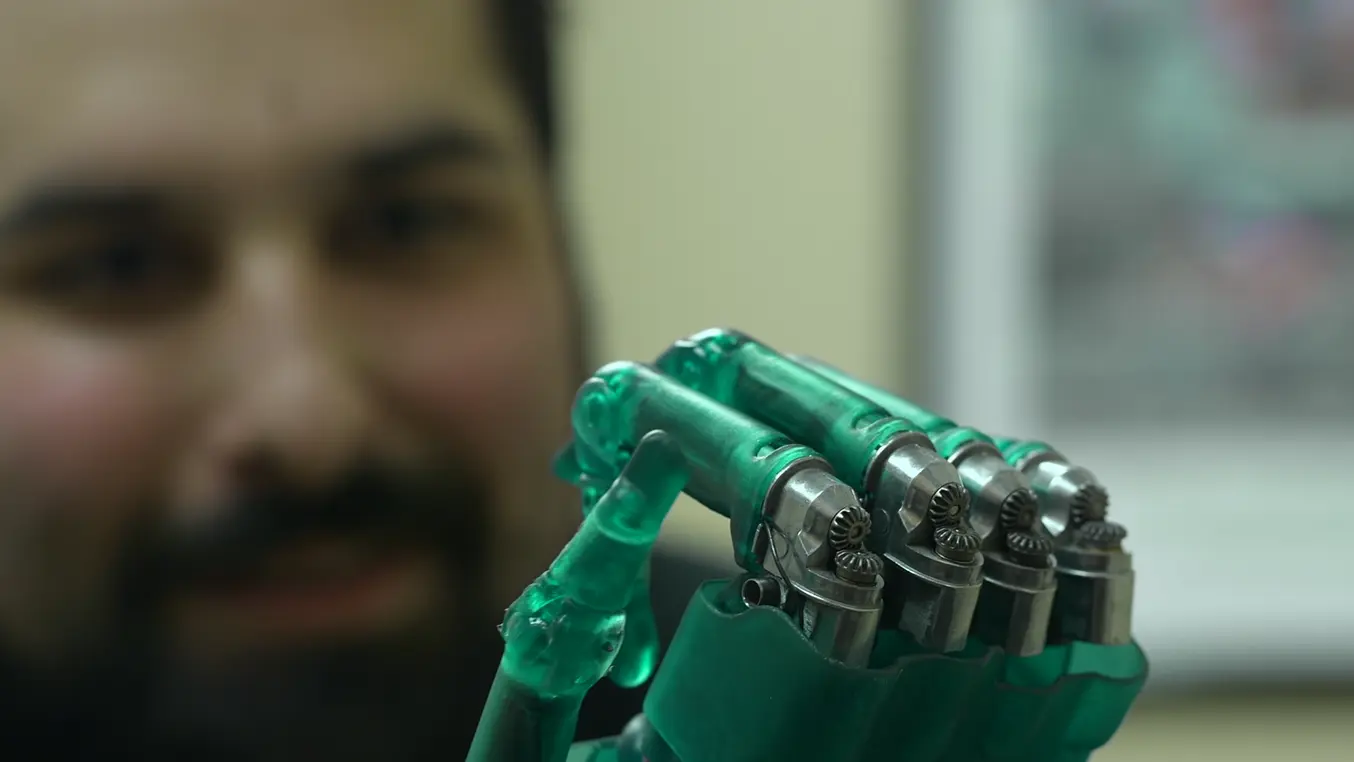
Un assemblage dynamique tel qu'une prothèse de main, requiert une définition précise des tolérances.
L'art de cette définition réside dans la façon de communiquer uniquement les variations correctes pour chacun des éléments caractéristiques, afin de maximiser le taux d'acceptation du produit dans le cadre des limites des processus de fabrication, en fonction de l'usage et de l'aspect visuel requis pour la pièce
Dans le système métrique, il existe des niveaux de qualité de tolérance (IT), qui permettent également de spécifier les tolérances au moyen de symboles. Le symbole 40H11 par exemple signifie qu'il s'agit d'un alésage de diamètre 40 mm avec un ajustement tournant avec jeu. Le fabricant n'a plus qu'à consulter le tableau de base des alésages pour connaitre exactement la valeur de la tolérance.
En plus des tolérances par élément, les ingénieurs doivent aussi tenir compte des effets au niveau du système. Par exemple, quand une pièce est produite avec ses dimensions au maximum de leurs valeurs acceptables, les exigences relatives au poids et à l'épaisseur des parois du produit sont-elles encore respectées ? Cette caractéristique est appelée Condition du maximum de matière (MMC), et sa contrepartie est la Condition du minimum de matière (LMC).
Les tolérances sont également superposables. Si nous réalisons un maillon d'une chaine, pour lequel chaque alésage a une tolérance positive de 0,1 mm et chaque arbre une tolérance négative de 0,1 mm, cela signifie que nous acceptons donc une différence de 20 mm pour 100 maillons. Lorsqu'il faut positionner des éléments répétitifs, comme un motif de perforations, il vaut mieux positionner d'abord le motif puis donner les distances entre eux, plutôt que de référencer chaque élément par rapport à un coin ou un plan fixes de la pièce.
Ces normes ne concernent pas seulement les concepteurs et les ingénieurs. Elles servent aussi aux inspecteurs contrôle qualité en leur donnant des informations sur la manière de mesurer les dimensions et les tolérances. L'usage d'outils spécifiques, tels que des micromètres numériques et des pieds à coulisse, des jauges de hauteur, des marbres à dresser, des indicateurs à cadran et une machine à mesure tridimensionnelle (MMT) est également important pendant la tolérance.
Lorsque la pièce est définie et dimensionnée, sa géométrie existe dans un espace conceptuel appelé cadre de références (DRF, pour Datum Reference Frame). Il est comparable au système des coordonnées à l'origine d'un espace de modélisation 3D. Une référence est un point, une ligne ou un plan, définis dans le DRF, constituant le point d'origine de la mesure. Il faut s'assurer que les fonctions de référence sont pertinentes par rapport aux fonctionnalités de la pièce. À moins que vous cherchiez à faire correspondre les caractéristiques d'une pièce à celles des autres dans un assemblage, il est possible de n'utiliser qu'une seule référence. Il faut toujours vérifier que la référence primaire est bien placée pour permettre de déduire les autres mesures à partir d'elle, par exemple sur un endroit de la pièce qui ne risque pas de présenter trop de variations imprévisibles.
Recommandations relatives aux tolérances GD&T
Un dessin technique doit reproduire le produit de façon précise, sans ajouter de complexité ou de restrictions inutiles. Il est utile de tenir compte des recommandations suivantes :
-
Le plus important dans un dessin est sa clarté, peut-être même plus que sa précision et son exhaustivité. Pour améliorer la clarté du dessin, il vaut mieux placer les dimensions et les tolérances en dehors des limites de la pièce et au bout de lignes visibles sur des profils réels, n'employer qu'un seul sens de lecture, bien évoquer la fonction de la pièce, grouper les dimensions ou les échelonner, et bien utiliser l'espace libre.
-
Toujours concevoir les tolérances les plus souples pour maintenir les coûts au plus bas.
-
Employer une tolérance globale qui s'applique à toutes les dimensions de la pièce et sera indiquée en bas du dessin. Des tolérances spécifiques plus ajustées ou moins ajustées pourront être indiquées sur le dessin et elles annuleront et remplaceront les valeurs globales.
-
Décidez en premier lieu des tolérances des éléments fonctionnels et leurs interrelations, puis passer au reste de la pièce.
-
Dès que cela est possible, laissez le travail de GD&T aux experts en fabrication et ne décrivez pas de procédés de fabrication dans le dessin technique.
-
Ne précisez pas lorsqu'un angle est de 90° parce que c'est la valeur par défaut.
-
Sauf contre indication, les dimensions et les tolérances sont valables à 20 °C / 101,3 kPa.
Les symboles des tolérances
Le GD&T est basé sur des fonctions, chacune d'entre elles étant spécifiée au moyen de contrôles. On distingue cinq groupes de contrôles :
-
Les contrôles de forme, qui spécifient la formes des éléments, notamment :
-
La rectitude se partage entre rectitude d'élément linéaire et rectitude d'axe.
-
La planéité qualifie la rectitude dans de multiples dimensions. Elle est mesurée en référence aux points les plus hauts et les plus bas d'une surface.
-
La circularité (ou rotondité) peut être décrite comme la rectitude courbée en un cercle.
-
La cylindricité est simplement la planéité courbée dans un cylindre. Elle comprend la rectitude, la circularité et la conicité, ce qui la rend coûteuse à inspecter.
-
-
Les contrôles de profil définissent la zone de tolérance tridimensionnelle autour d'une surface :
-
Le profil de ligne compare une section bidimensionnelle à une forme idéale. La zone de tolérance est définie par deux courbes décalées, sauf contre indication.
-
Le profil de surface génère deux surfaces décalées entre lesquelles doit se trouver l'élément. Ce contrôle est complexe et doit être réalisé à l'aide d'une machine à mesure tridimensionnelle (MMT).
-
-
Les contrôles d'orientation concernent les dimensions définies par un angle, notamment :
-
L'inclinaison caractérise l'angle d'un plan par rapport à une référence. L'élément doit se trouver entre deux plans de référence espacés de la valeur de la tolérance.
-
La perpendicularité caractérise un élément plan à 90° par rapport à un plan de référence. La surface doit être comprise entre deux plans de référence distants de la valeur de la tolérance.
-
Le parallélisme représente la rectitude à une distance donnée. Le parallélisme d'axes peut se définir comme une zone de tolérance cylindrique, en plaçant le symbole du diamètre devant la valeur de tolérance.
-
-
Les contrôles de position définissent l'emplacement de l'élément par des dimensions linéaires :
-
Le positionnement définit l'emplacement des éléments les uns par rapport aux autres ou par rapport à des références. C'est le contrôle le plus utilisé.
-
La coaxialité compare la position de l'axe d'un élément par rapport à un axe de référence.
-
La symétrie assure que des parties non cylindriques sont identiques de part et d'autre d'un plan de référence. C'est un contrôle complexe, généralement effectué à l'aide d'une MMT.
-
-
Les contrôles de battement définissent pour un élément particulier la valeur admise de variation par rapport aux références :
-
Le battement circulaire est utilisé lorsqu'il faut prendre en compte différentes erreurs, comme pour des pièces d'un assemblage de roulement à billes. L'inspection fait tourner la pièce autour d'un axe pour mesurer les variations ou les « oscillations » autour de l'axe de rotation.
-
Le battement total est mesuré à plusieurs points de la surface. Il ne décrit pas uniquement le battement d'un élément mais celui de l'ensemble d'une surface. Cela permet le contrôle de la rectitude, du profil, de l'inclinaison et d'autres variations.
-
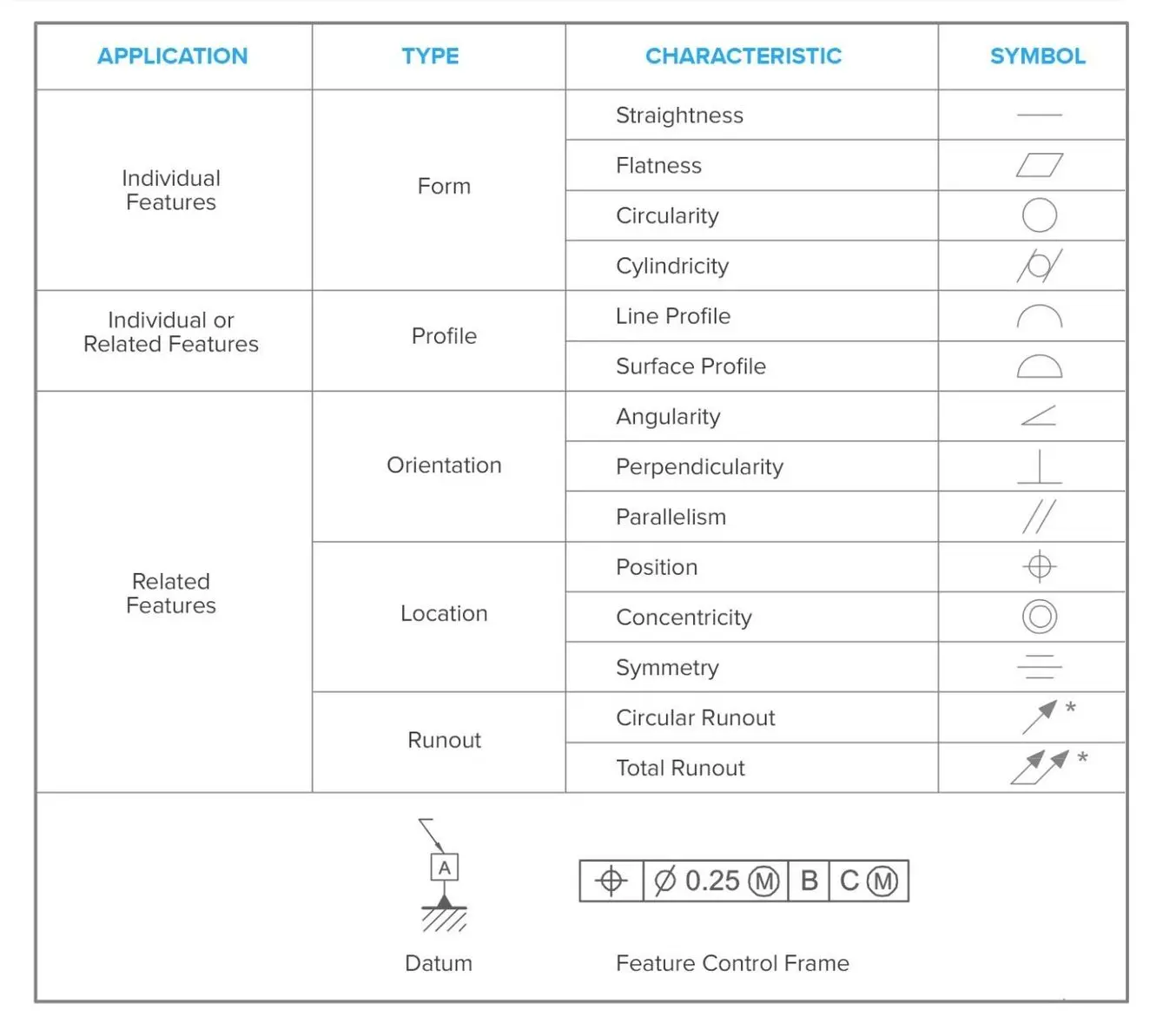
Les normes ANSI et ISO utilisent ces symboles communs des tolérances.
Cadre de tolérance d'un élément
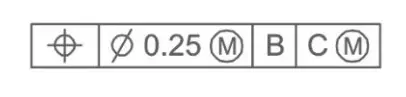
Dans ce cadre sont notées toutes les tolérances à appliquer au dessin. La case la plus à gauche indique la caractéristique géométrique. Dans l'exemple ci-dessus, c'est la tolérance de position, mais cela pourrait être tout autre symbole. Le premier symbole de la deuxième case indique la forme de la zone de tolérance. Dans cet exemple, c'est un diamètre et non une dimension linéaire. Le nombre indique la valeur de tolérance admise.
À côté de cette case, se trouvent des cases distinctes correspondant à chaque élément de référence de la tolérance. Ici, la position sera mesurée par rapport aux références B et C. À côté de la tolérance ou de la référence, on peut trouver une lettre entourée d'un cercle, le modificateur d'élément.
Les options sont les suivantes :
-
M : signifie que la tolérance s'applique à la MMC (Condition du maximum de matière)
-
L : signifie que la tolérance s'applique à la LMC (Condition du minimum de matière)
-
U : signifie que les tolérances ne sont pas les mêmes de chaque côté ; c'est-à-dire qu'une tolérance de 1 mm peut être de -0,20 d'un côté et + 0,80 de l'autre.
-
P : signifie que la tolérance est mesurée dans une Zone de tolérance projetée à une distance spécifiée de la référence.
-
Il n'existe pas de symbole particulier pour spécifier la tolérance indépendamment de la taille de la pièce (RFS pour Regardless of Feature Size).
Dans cet exemple, si la pièce est en dehors de la MMC, un bonus de tolérance peut lui être attribué proportionnellement à l'écart à la MMC. Ainsi, si une pièce est à 90 % de la MMC, la tolérance sera aussi diminuée de 10 %.
Tolérances en impression 3D
De nombreux concepteurs et ingénieurs utilisent l'impression 3D au cours du prototypage et du développement des produits, afin de réaliser des prototypes et des pièces sur mesure rentables, qui sinon exigeraient des investissements importants.
Les méthodes du tolérance pour les outils de fabrication traditionnelle et en impression 3D différent parce que cette dernière est un procédé unique automatisé. Imposer des tolérances serrées peut demander plus de travail au moment de la conception, mais se traduira par des économies de coûts et de temps substantielles lors du prototypage et de la production.
L'impression 3D SLA sur une imprimante comme la Form 3 de Formlabs permet une exactitude et une précision de haut niveau, et propose une large gamme de matériaux techniques, depuis des résines utilisables à haute température pour réaliser des moules, à celles qui supportent des contraintes et des déformations importantes ou résistent à l'usure. Téléchargez notre livre blanc « Ajustement mécanique : Optimisation de la conception d’assemblages imprimés en 3D » pour connaitre les tolérances recommandées à la conception pour les matériaux Tough Resin et Durable Resin.
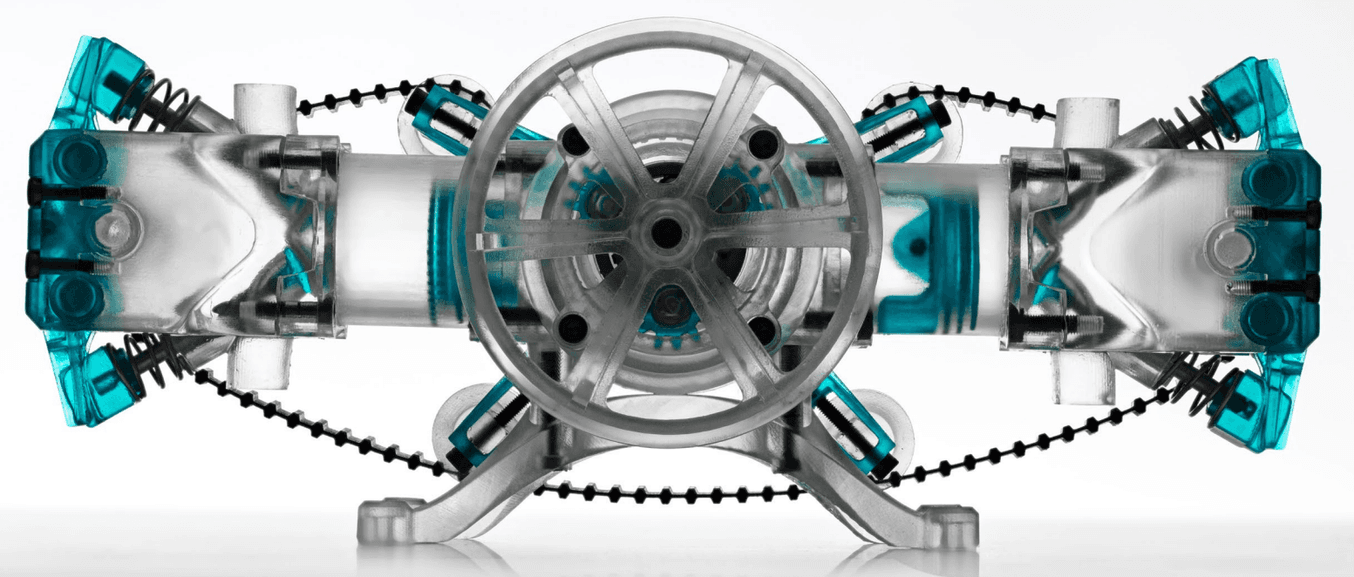
Grâce à l'impression 3D, les ingénieurs et les concepteurs de produits peuvent réaliser en interne des pièces et des prototypes d'assemblages complexes et faire des économies de coûts et de temps à chacune des phases du développement de produits.
Étude de cas relative au GD&T
La plupart des outils GD&T destinés à l'ingénierie mécanique, comme SolidWorks, Autodesk Fusion 360, AutoCAD, SolidEdge, FreeCAD, CATIA, NX, Creo et Inventor proposent un système intégré GD&T pour réaliser des mises en plan ou dessins techniques. Cependant, les concepteurs doivent toujours positionner les tolérances manuellement, en tenant compte des écarts éventuels qui apparaissent pendant les processus de fabrication. Dans cette étude de cas, nous montrons un exemple de GD&T utilisé dans SolidWorks.
Ce projet vise à produire 50 000 capsules de bouteille par moulage par injection. Nous voulons contrôler la façon dont la capsule s'ajuste à la bouteille et la force nécessaire. Il faut donc spécifier correctement les tolérances. Nous voulons éviter que des capsules soient d'un diamètre extérieur plus large que celui de la bouteille, ou que d'autres soient trop petites et empêchent un bon ajustement tournant.
Le filetage de la bouteille a un diamètre extérieur de 36,95 +/- 0,010 mm. Cela signifie que le diamètre intérieur de la capsule doit se trouver entre les limites 36,985 et 37,065 mm, la valeur moyenne étant 37,0 mm.
La capsule doit aussi comporter un alésage particulier pour s'attacher à un axe, situé en dessous d'une surface plane, pour que la bouteille puisse s'ouvrir d'une seule main, tout en restant suspendue en dessous d'une surface d'un logement de stockage. Cet axe est une pièce en inox d'un fabricant OEM, de 4 mm de diamètre avec une tolérance de 0,13 mm (0.005 in.). Pour que l'ajustement soit glissant et juste, nous avons besoin d'un emmanchement en force avec une surcote dans l'intervalle -0,0375 et 0,0125 mm. L'intervalle de tolérance du diamètre de l'alésage est ici de 3,99 à 4,01 mm pour permettre un emmanchement en force pour toutes les tailles de l'axe. C'est un intervalle tellement petit que nous avons décidé de fixer la spécification de l'alésage à 3,85 mm et de le percer à 4,00 mm exactement, ce qui contrôle aussi la coaxialité des deux alésages.
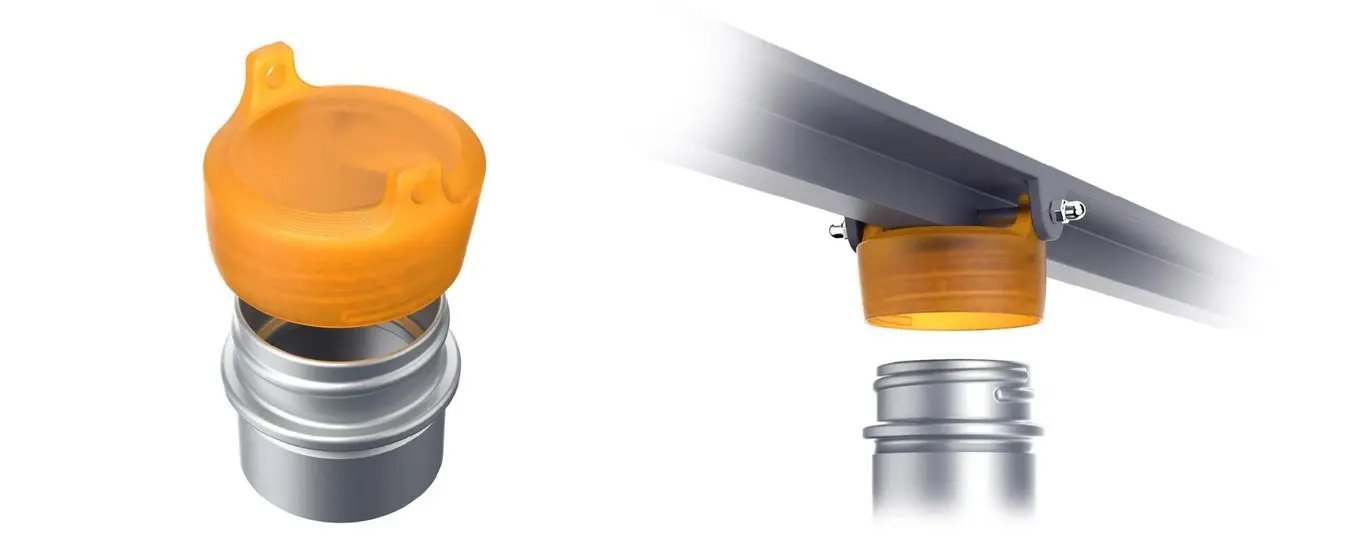
Cette capsule présente de multiples éléments d'assemblage et sa fabrication requiert des cotations et des tolérances géométriques.
Pour contrôler correctement ses dimensions, nous avons besoin d'une référence. Une référence doit permettre de représenter des éléments d'assemblage et la fonction de l'objet. Elle doit en outre être stable, reproductible et accessible. Ce qui est important dans ce cas précis, c'est que la capsule et le goulot s'assemblent bien. C'est pourquoi nous avons choisi la surface cylindrique interne de la capsule comme référence primaire. La fonction secondaire est l'assemblage avec la surface de montage, et nous avons donc choisi le sommet plat de la capsule comme référence secondaire.
Après avoir pris ces décisions, la tolérance du GD&T de SolidWorks se passe comme suit : Indiquer les références dans DimXpert > Schéma de cotation automatique et sélectionner l'option Géométrique et non l'option Plus/Moins pour la tolérance. Sélectionnez ensuite les références et les fonctions à contrôler par rapport aux références. Après avoir terminé le schéma de cotation, ajoutez les tolérances géométriques et les symboles GD&T individuellement. Le logiciel génère automatiquement les dimensions pour les fonctions dimensionnelles, comme les alésages et les bossages. Assurez-vous de bien sélectionner « Bilatérale » ou « Limite » pour les types de tolérance dont les limites plus et moins ne sont pas égales.
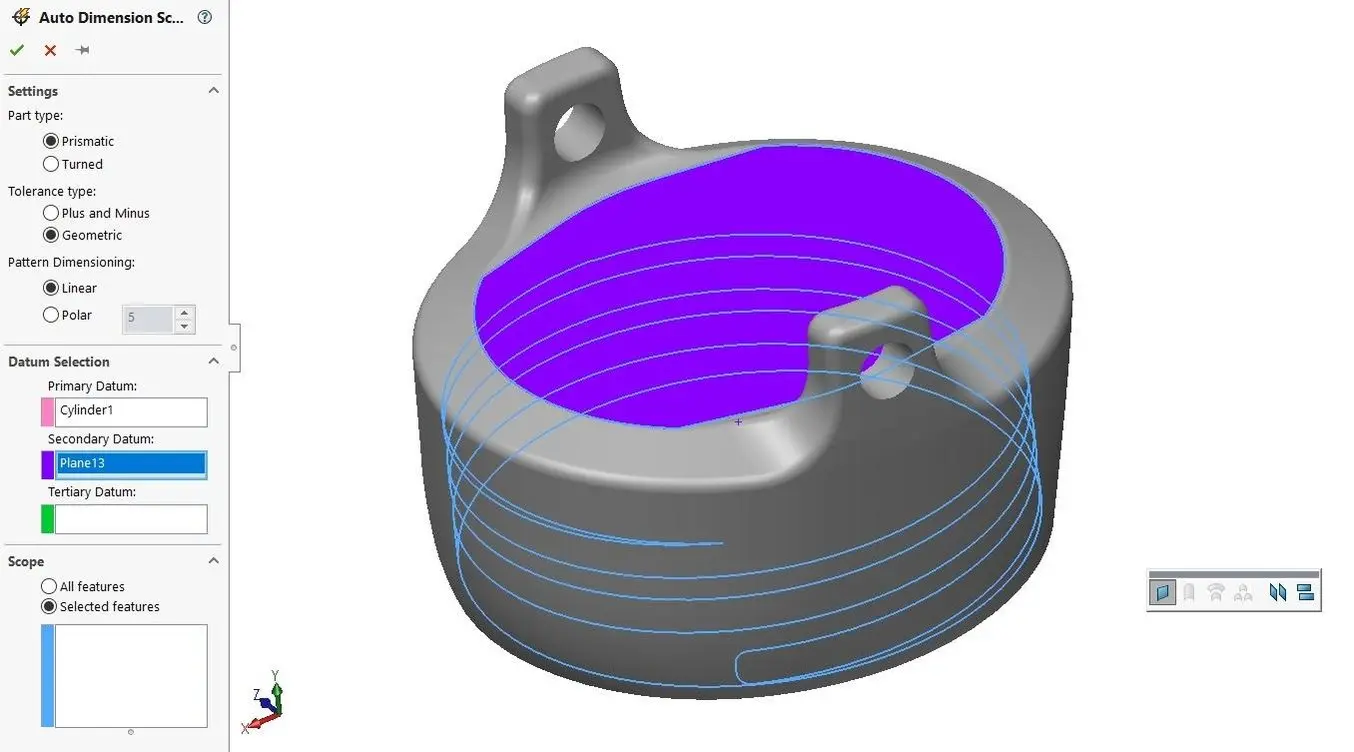
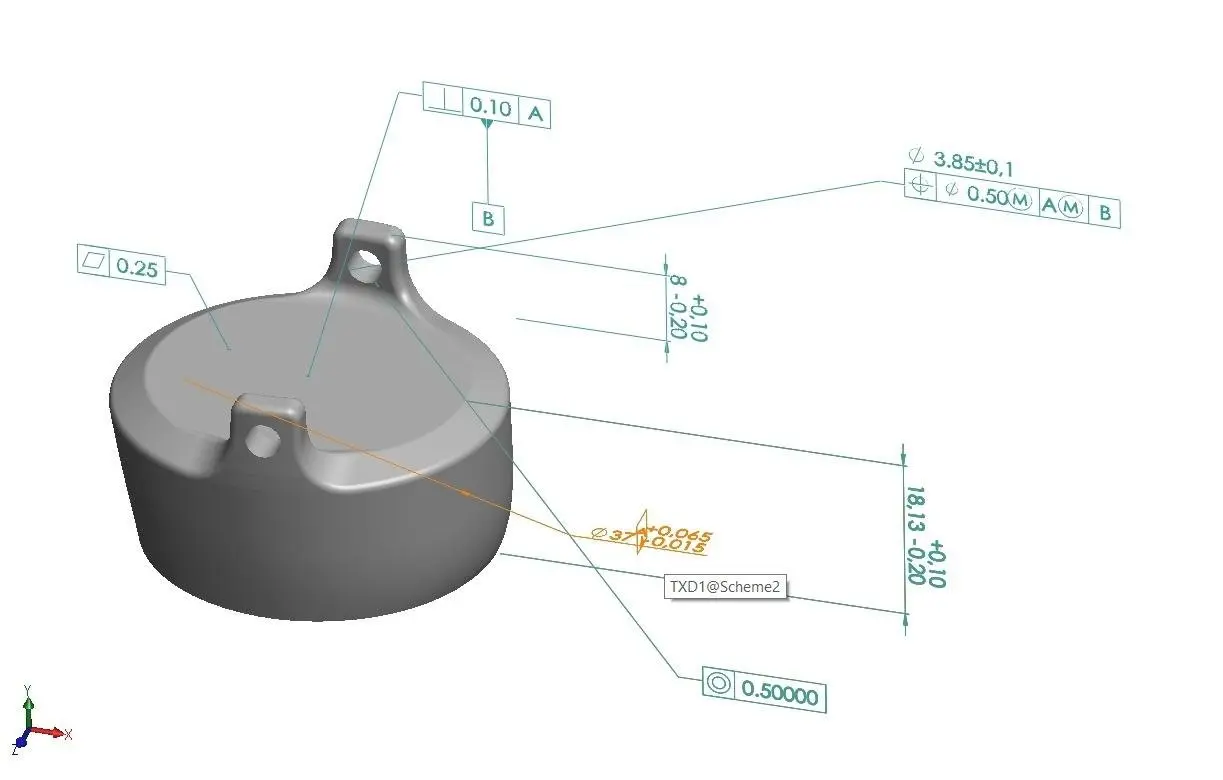
Sélection des références et des fonctions pour les tolérances géométriques dans SolidWorks.
Pour importer ces tolérances dans une mise en plan technique, vérifiez d'abord dans FeatureManager quels sont les plans utilisés dans le dossier « Annotations ». Lorsque vous importez les vues à partir de ces plans dans une mise en plan, vérifiez « Importer les annotations » et « Annotations DimXpert ». Une vue en coupe adéquate ajoute beaucoup à la clarté de la mise en plan.
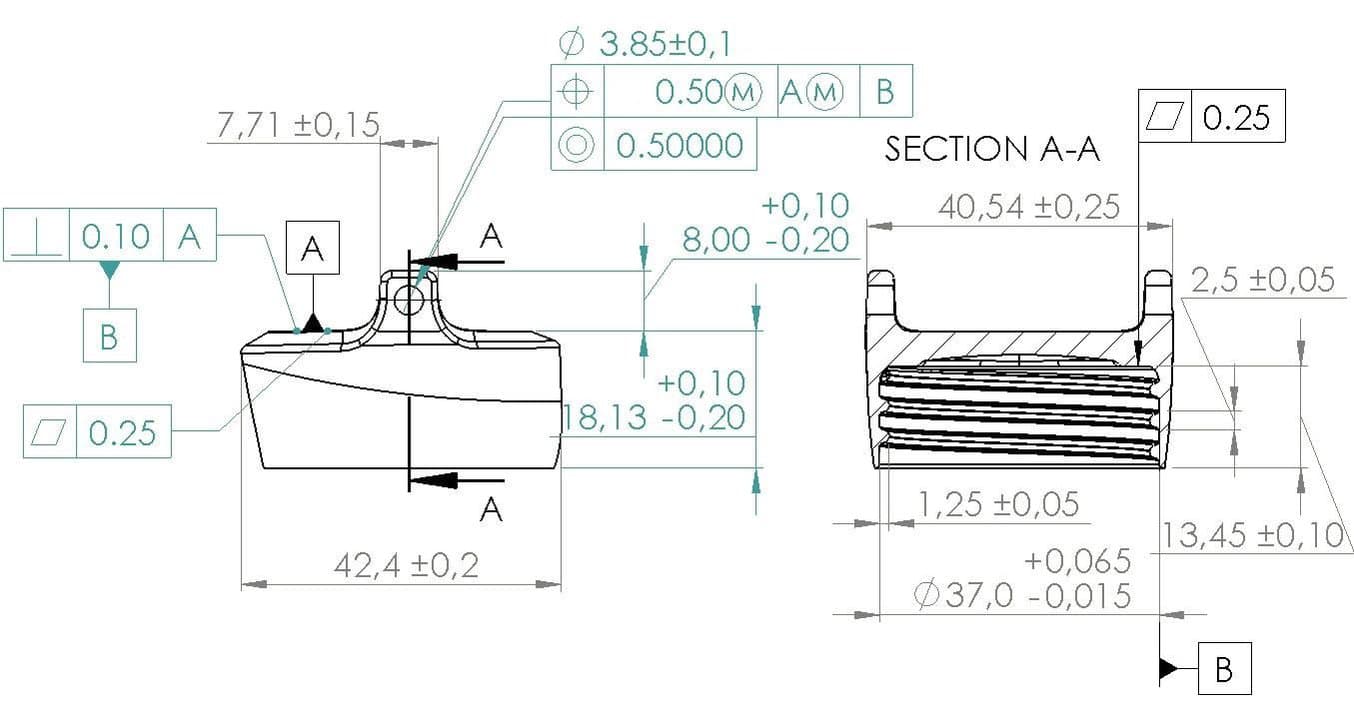
Une mise en plan pour la production avec des tolérances adéquates.
Prototyper et fabriquer rapidement des pièces grâce à l'impression 3D
Dans ce guide, nous avons décrit le système de cotations et de tolérances géométriques (GD&T), qui apporte d'énormes avantages aux concepteurs et aux ingénieurs travaillant sur des produits complexes, dont les dimensions doivent être strictement contrôlées. Nous avons constaté que le GD&T décrit non seulement des cotes linéaires mais aussi l'intention de conception, ce qui clarifie la communication entre les concepteurs et les différents acteurs du projet.
Grâce à une douzaine de symboles, la fonction de référence et le cadre des tolérances seulement, il est possible de d'enrichir considérablement les mises en plan pour la production, et d'assurer que les ajustements resteront homogènes sur l'ensemble des assemblages du produit. Le GD&T incite aussi les développeurs à réfléchir aux façons de définir les tolérances acceptables en fonction du processus de fabrication, qui entraine différents écarts en fonctins des caractéristiques de la technique utilisée.
Pour avancer sur le chemin prometteur de l'industrie 4.0, des entreprises des secteurs de l'aérospatiale, de la défense, des biens de consommation et médical adoptent des outils numériques de fabrication industrielle. L'impression 3D est un catalyseur de l'efficacité, parce qu'elle apporte aux acteurs concernés, de l'ingénieur de production à l'opérateur des machines-outils, les outils permettant de raccourcir la chaine logistique, d'améliorer la production et de mettre les produits plus rapidement sur le marché, économisant ainsi des centaines de milliers de dollars et des semaines, voire des mois, sur l'ensemble du processus.
En savoir plus sur la manière dont les fabricants leaders du secteur se servent l'impression 3D pour réduire les coûts et les temps de réalisation, de la conception à la production.