Des pièces imprimées en 3D hautes performances pour la F1 et d’autres secteurs
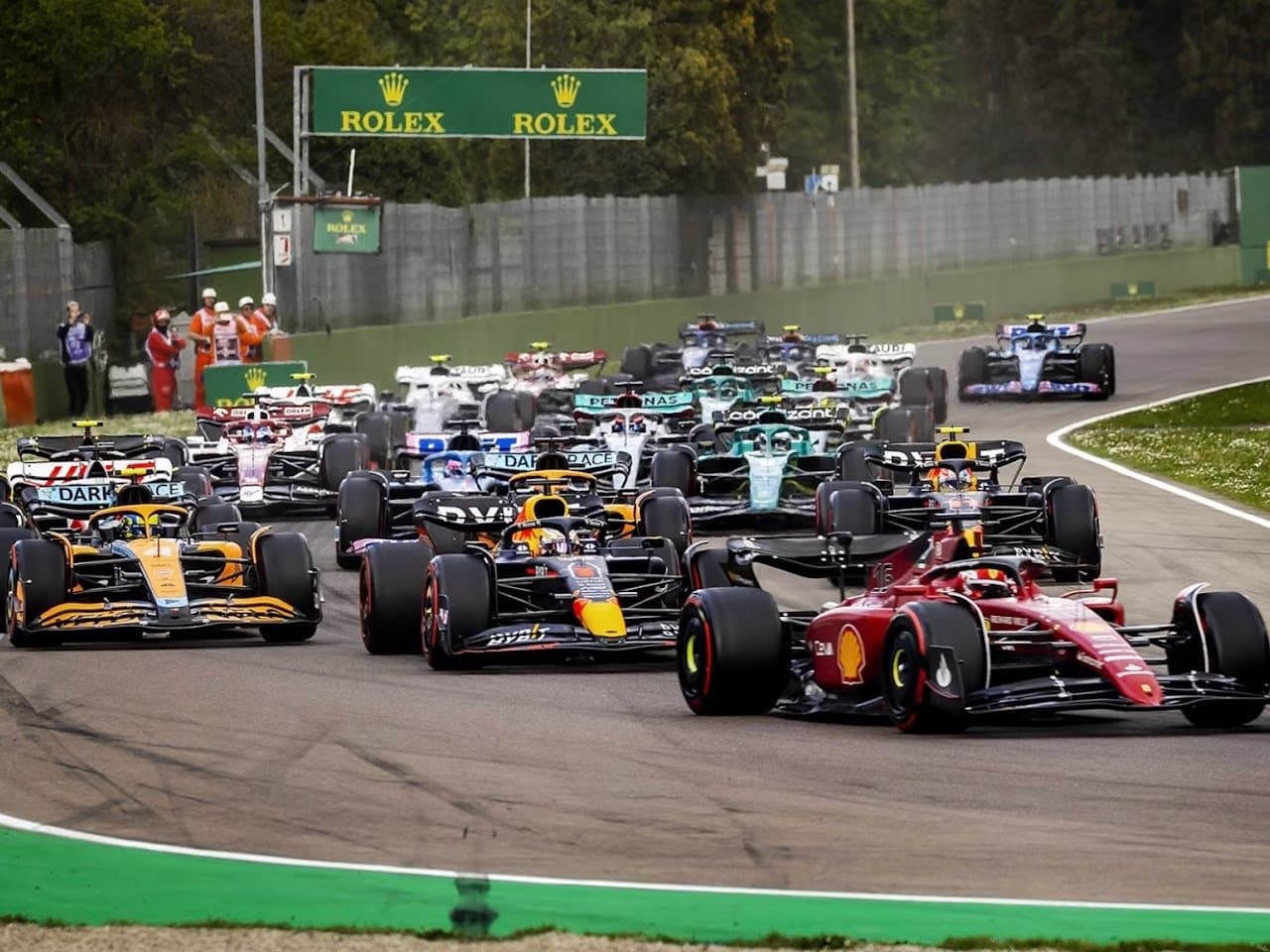
Photo de Formula1.com
Alors qu’une attention grandissante est accordée aux grandes écuries de sports automobiles comme la Formule 1, la rapidité et la puissance de chaque véhicule font l’objet d’une pression croissante. Les équipes de F1 emploient déjà certains des esprits les plus brillants du secteur de l’ingénierie. Il arrive néanmoins que même ces équipes de pointe se tournent vers des experts externes pour gagner encore un peu en puissance.
L’un de ces experts est Mackart Additive, un prestataire d’ingénierie et de production industrielle situé dans le Staffordshire, au cœur du Royaume-Uni. Comptant plus de deux décennies d’expérience dans les domaines de l’ingénierie de conception et de la fabrication additive, Mackart a su repousser les limites de l’impression 3D au-delà des paramètres traditionnels du prototypage rapide. Environ 80 % des projets actuels de Mackart impliquent des équipes de F1. Ces clients recherchent constamment des améliorations supplémentaires pour optimiser la légèreté, la puissance, la fiabilité et l’aérodynamisme de leurs voitures. L’équipe de M. McCarthy excelle dans l’impression 3D d’outils complexes pour les composants en plastique renforcé de fibre de carbone (CFRP, Carbon Fiber Reinforced Plastic), qui établissent de nouvelles normes jusqu’alors inconcevables.
Tirant parti de neuf imprimantes stéréolithographiques (SLA) de la série Form 3 et de la Form Auto, ainsi que d’imprimantes utilisant le dépôt de fil fondu (FDM) et des composites, Mackart produit des outils pour les pièces en fibre de carbone et en silicone, ainsi que des composants finaux imprimés en 3D. En collaboration avec Solid Print3D, partenaire officiel de Formlabs, la société Mackart s’est développée et a atteint un volume de production conséquent.
"Nous ne considérons pas l’impression 3D comme un outil de prototypage rapide. Il s’agit d’un procédé de fabrication efficace."
Steven McCarthy, Directeur général et fondateur, Mackart
L’impression 3D d’outils complexes pour les pièces en fibre de carbone
Si M. McCarthy a commencé dans le domaine de l’ingénierie aérospatiale, Mackart s’est associée depuis ses débuts en 2016 à des acteurs dans des secteurs très différents, des fabricants d’équipements de plomberie aux géants internationaux des sports automobiles.
L’un des matériaux les plus couramment employés dans le monde de la compétition automobile et qui s’est plus récemment imposé dans le secteur automobile grand public est la fibre de carbone. Les composants en fibre de carbone peuvent supporter les hautes températures caractéristiques des circuits de course, tout en offrant des propriétés inégalées au niveau du ratio force/poids, ce qui permet d’augmenter les performances de chaque aspect d’une voiture de course.
Les pièces en fibre de carbone sont généralement fabriquées à l’aide de feuilles de tissu de carbone pré-imprégné comportant le volume adéquat de résine non polymérisée. Ces feuilles pré-imprégnées sont ensuite laminées dans le moule ou sur celui-ci, puis polymérisées en autoclave avec de la chaleur et de la pression.
Traditionnellement, chaque moule est usiné à partir de métal afin de supporter la chaleur et la pression de l’autoclave. Ce procédé soustractif comporte plusieurs inconvénients : il peut gaspiller des ressources, être lent et coûteux, et empêcher les itérations du processus de conception. À mesure que les matériaux et les équipements d’impression 3D se sont développés, l’impression 3D est devenue une option viable pour créer des outils rigides destinés à ces applications.
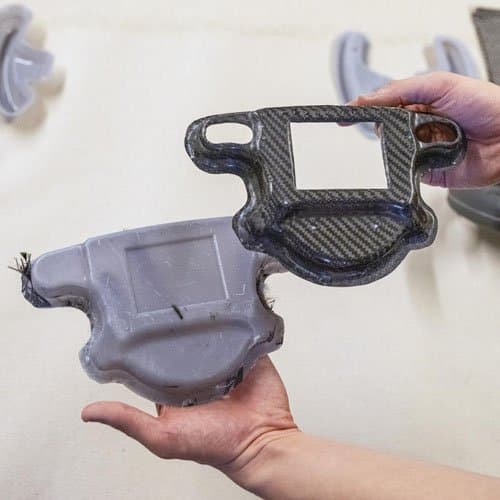
La fabrication de pièces en fibre de carbone avec des moules imprimés en 3D
Téléchargez ce livre blanc pour obtenir des instructions de conception de moules ainsi que des guides étape par étape concernant les méthodes de pré-imprégnation et de laminage manuel pour créer des pièces en fibre de carbone.
Des technologies combinées pour créer des outils pour les pièces en fibre de carbone
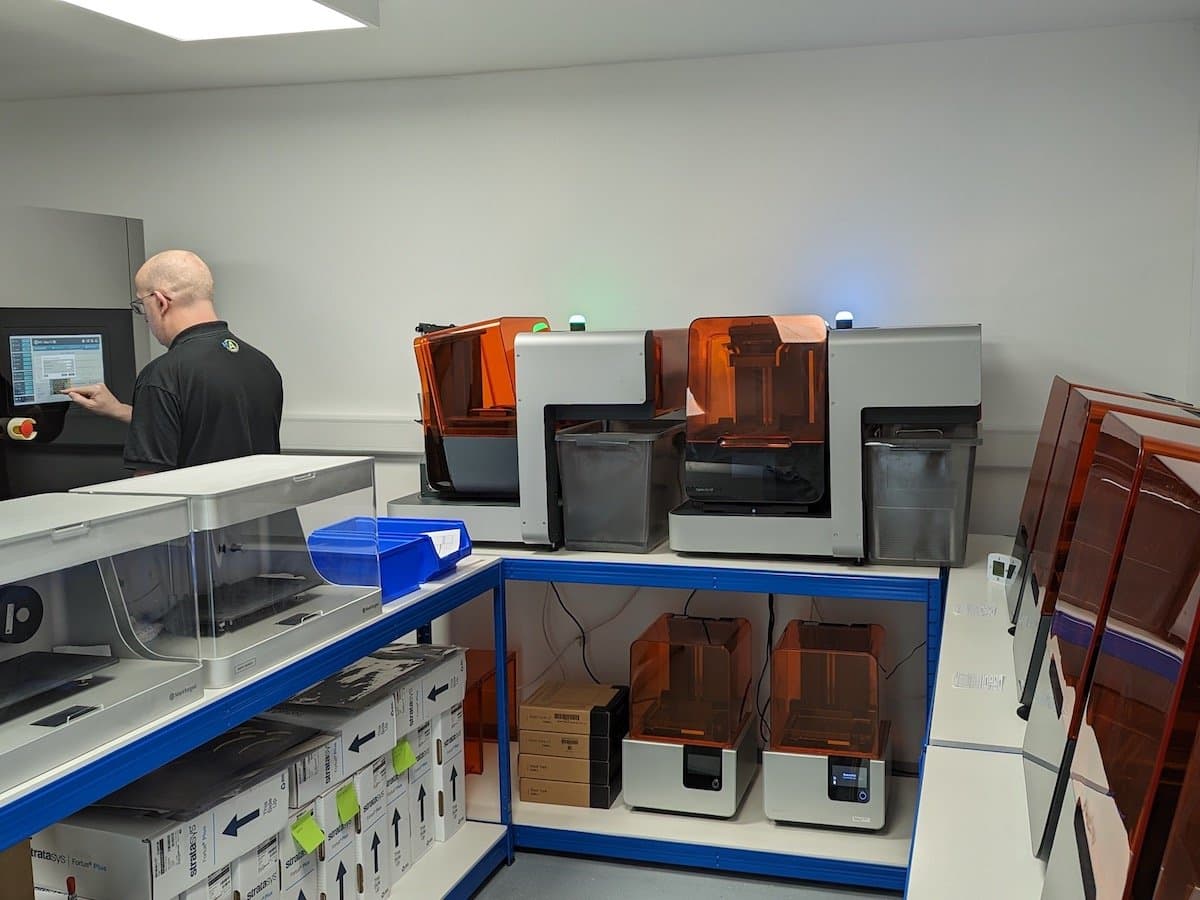
Le laboratoire d’impression 3D de Mackart Additive combine plusieurs technologies et procédés, dont deux extensions Form Auto, afin de créer des pièces avancées destinées à une vaste gamme d’applications industrielles.
La clé du succès lors de la création d’outils industriels réside dans l’optimisation de la conception et de l’orientation des impressions, des paramètres que l’équipe de Mackart maîtrise à la perfection. Elle conçoit et fabrique des mandrins et des moules complexes pour fibre de carbone à l’aide d’une combinaison de matériaux et de technologies d’impression 3D différents, chacun étant choisi pour ses caractéristiques spécifiques.
Après avoir initialement utilisé Grey Resin, puis Grey Pro, l’équipe a commencé à tester Rigid 4000 Resin et Rigid 10K Resin. Elle a alors découvert que la finition de surface lisse et la rigidité donnaient des résultats optimaux pour les pièces finales en fibre de carbone. « Nous avons essayé des outils d’impression uniques avec Rigid 4000 Resin et les résultats étaient excellents. Nous les avons inspectés à l’aide de métrologie laser et, du point de vue des dimensions, les résultats étaient phénoménaux. Dans certains cas, nous avons constaté des déviations de l’ordre du micron par rapport à la géométrie CAO nominale », a indiqué M. McCarthy.
L’équipe produit souvent des outils de grande taille en les divisant en pièces plus petites, puis en les assemblant à l’aide d’éléments de fixation soigneusement conçus. « Pour les outils de grande taille qui dépassent les volumes d’impression de l’imprimante, nous incorporons souvent des joints à brides pour permettre l’assemblage. Nous pouvons produire des assemblages comportant trois ou quatre composants pour réaliser des outils mesurant presque 450 mm de long », explique M. McCarthy.
Comparaison des technologies : outils pour les pièces en fibre de carbone
Délai de production | Avantages | Inconvénients | |
---|---|---|---|
Outils imprimés en 3D | 1 semaine | Liberté de conception Contrôle sur le délai de production/la chaîne logistique Solution rentable pour les faibles volumes | Doit prendre en compte la croissance thermique Dimensions limitées Nombre de tractions moins élevé par pièce |
Outils fabriqués selon un processus traditionnel | 3 à 4 semaines | Milliers de tractions Durabilité Dimensions | Délais de production longs Conception limitée |
La définition des paramètres et l’optimisation du processus
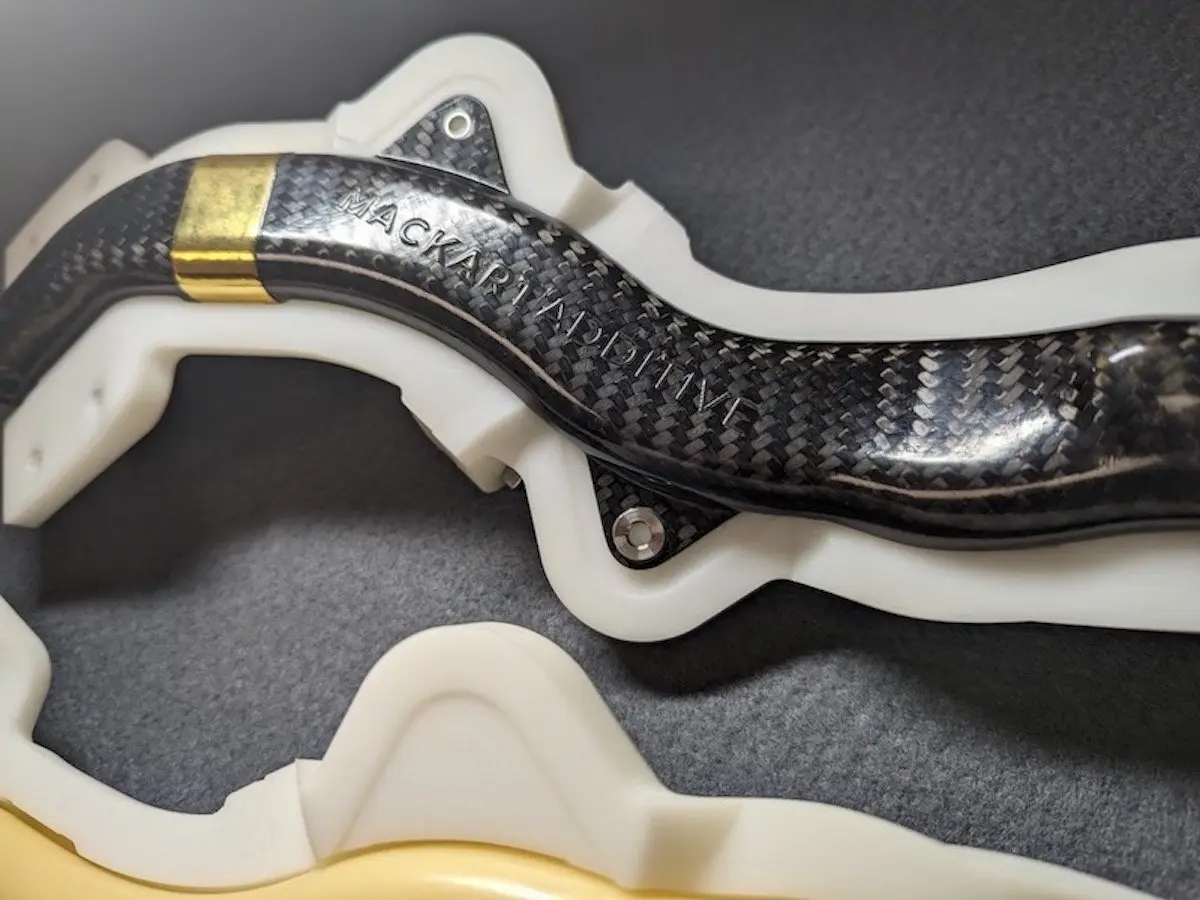
Ce composant de conduit en fibre de carbone a été produit à l’aide d’outils rapides imprimés en 3D, dont une coque extérieure imprimée avec la Form 3+ en Rigid 10K Resin et un outil de moulage de mandrin interne imprimé sur une imprimante 3D SLA à cuve profonde de grande taille.
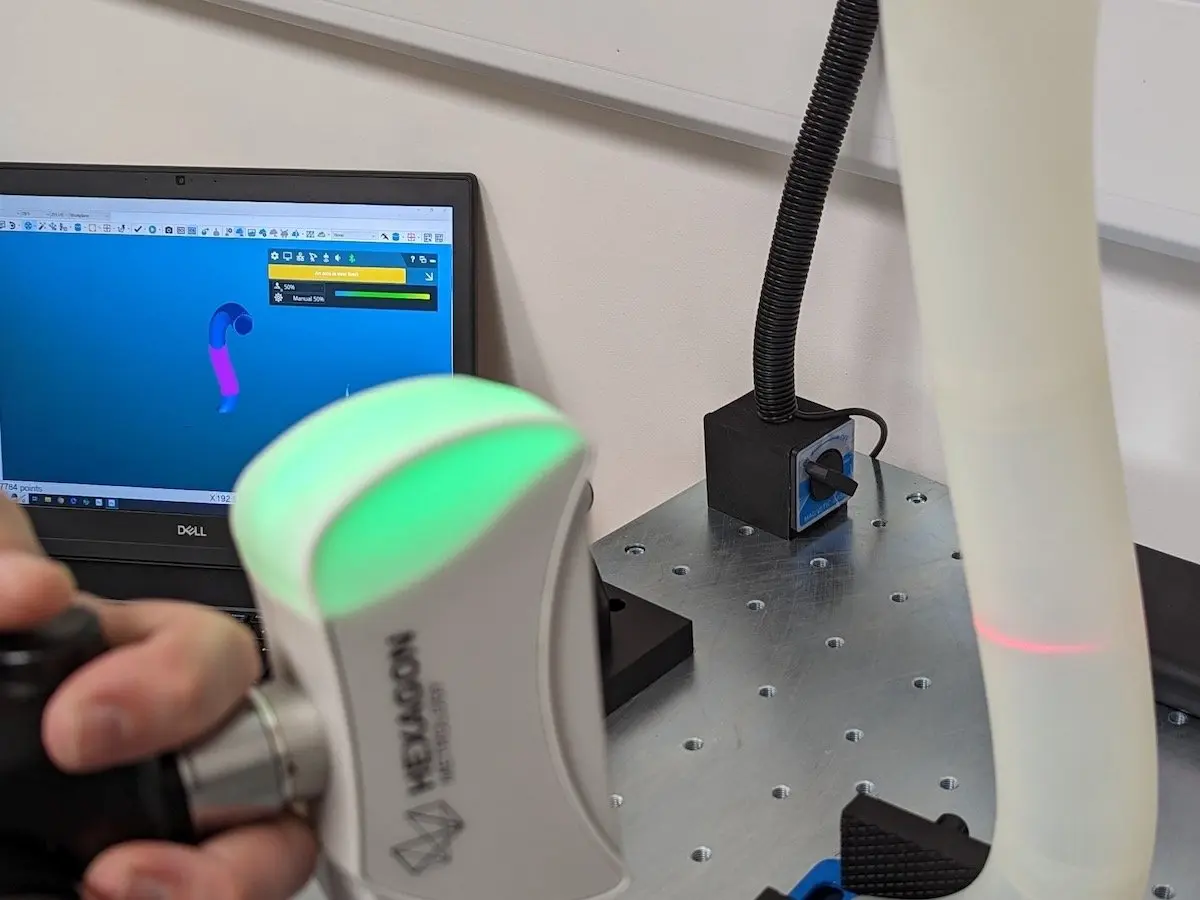
M. McCarthy effectue une numérisation 3D d’un mandrin imprimé dans la Form 3 avec Durable Resin. Il sera utilisé dans un processus avec fibre de carbone pour créer un conduit d’acheminement de l’air pour la F1.
Lors du processus de polymérisation en autoclave, les températures peuvent dépasser la température de transition vitreuse du matériau de l’outil. Toutefois, l’équipe a constaté que Rigid 10K Resin obtient de bonnes performances : le matériau ne se dégrade pas et ne perd pas en précision dimensionnelle après une utilisation répétée. « Rigid 10K Resin est un matériau plus résistant et il fournit une finition de surface un peu meilleure. Il s’agit en fait d’une excellente alternative à l’aluminium », déclare M. McCarthy. Afin d’optimiser la surface pour les interactions avec les feuilles en fibre de carbone, l’équipe de Mackart apprête légèrement la surface des pièces du moule en Rigid 10K Resin afin de retirer les particules de verre découlant de la conversion photopolymère unique de Rigid 10K Resin pendant l’impression.
L’équipe a également défini ses facteurs de compensations pour le fluage du matériau lors du processus en autoclave, afin que la pièce en fibre de carbone qui en résulte réponde au seuil de tolérance. « Ce n’est pas très compliqué, nous pouvons correspondre parfaitement à la fourchette de tolérance. Pour les outils de plus grande taille, il s’agit de quelques points de pourcentage », affirme M. McCarthy.
Traditionnellement, des mandrins solubles sont employés pour la forme interne des composants en fibre de carbone complexes, tels que les conduits et les tubes. Toutefois, pour les composants de plus petite taille (qui tiennent dans le volume d’impression de l’imprimante), il est possible de produire des mandrins extractibles, ce qui évite la complexité et l’investissement temporel associés à la solution soluble traditionnelle produite par FDM. Mackart a utilisé Durable Resin pour cette application et a obtenu d’excellentes performances. Pour les mandrins extractibles de plus grande taille qui dépassent le volume d’impression de l’imprimante, Mackart utilise son processus SLA de cuve profonde interne.
Chaque détail compte
La fabrication additive est idéale pour un secteur comme les sports automobiles, où chaque changement supplémentaire dans le design, même de l’ordre du micron, est susceptible de faire gagner une seconde ou de permettre la dernière accélération avant la lignée d’arrivée. La circulation de l’air autour de la voiture et à travers celle-ci est d’une importance capitale.
« L’impression 3D offre une excellente solution pour les sports automobiles en permettant de libérer la géométrie des limites des méthodes soustractives traditionnelles. L’espace à l’intérieur d’une voiture de course est critique. À cet égard, cette liberté de géométrie permet aux équipes d’optimiser l’aérodynamisme dans son ensemble. Sans la possibilité de manipuler et d’intégrer des composants rigides en fibre de carbone sans compromis (les pièces en fibre de carbone fabriquées avec les outils imprimés), les gains en termes de performances réalisés lors des dernières saisons de course pourraient ne pas avoir été possibles. La capacité de produire des outils qui libèrent ce potentiel découle de l’adoption d’outils imprimés en 3D, optimisés par une technique de conception soigneusement développée », explique M. McCarthy.
Par le passé, la fabrication de géométries relativement complexes en fibre de carbone à l’aide de méthodes d’outils soustractives traditionnelles nécessitait l’incorporation de matériau sacrificiel ou « superflu » dans le composant pour permettre « l’ébarbage » lors de la phase d’installation finale. La précision et la stabilité des moules imprimés en 3D ont grandement diminué le besoin pour ce surplus de matériau. « Il est désormais attendu d’avoir "bon" du premier coup et nous parvenons régulièrement à ce résultat avec les composants finaux en fibre de carbone. Notre talent est de créer des géométries avancées d’une grande précision », avance M. McCarthy.
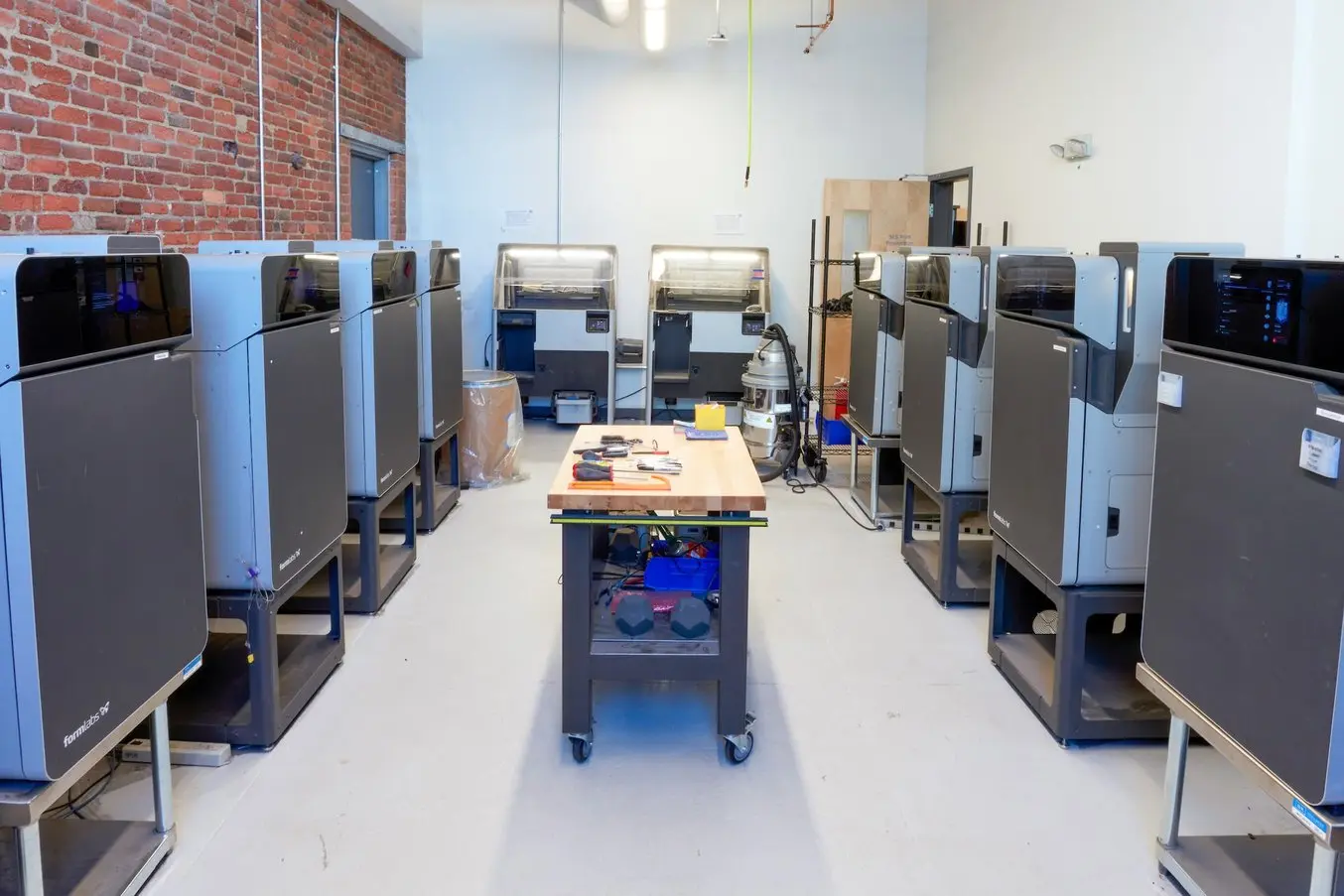
Gestion des parcs d'imprimantes 3D
La gestion de plusieurs imprimantes SLA et SLS ne doit pas forcément être compliquée : n'importe quelle entreprise peut mettre en place un parc d'imprimantes SLA et SLS en seulement un jour ou deux. En examinant quatre scénarios différents, ce guide vous aidera à mettre en place un flux de travail efficace pour n'importe quel volume ou type de pièce.
Les trois-huit avec la Form Auto
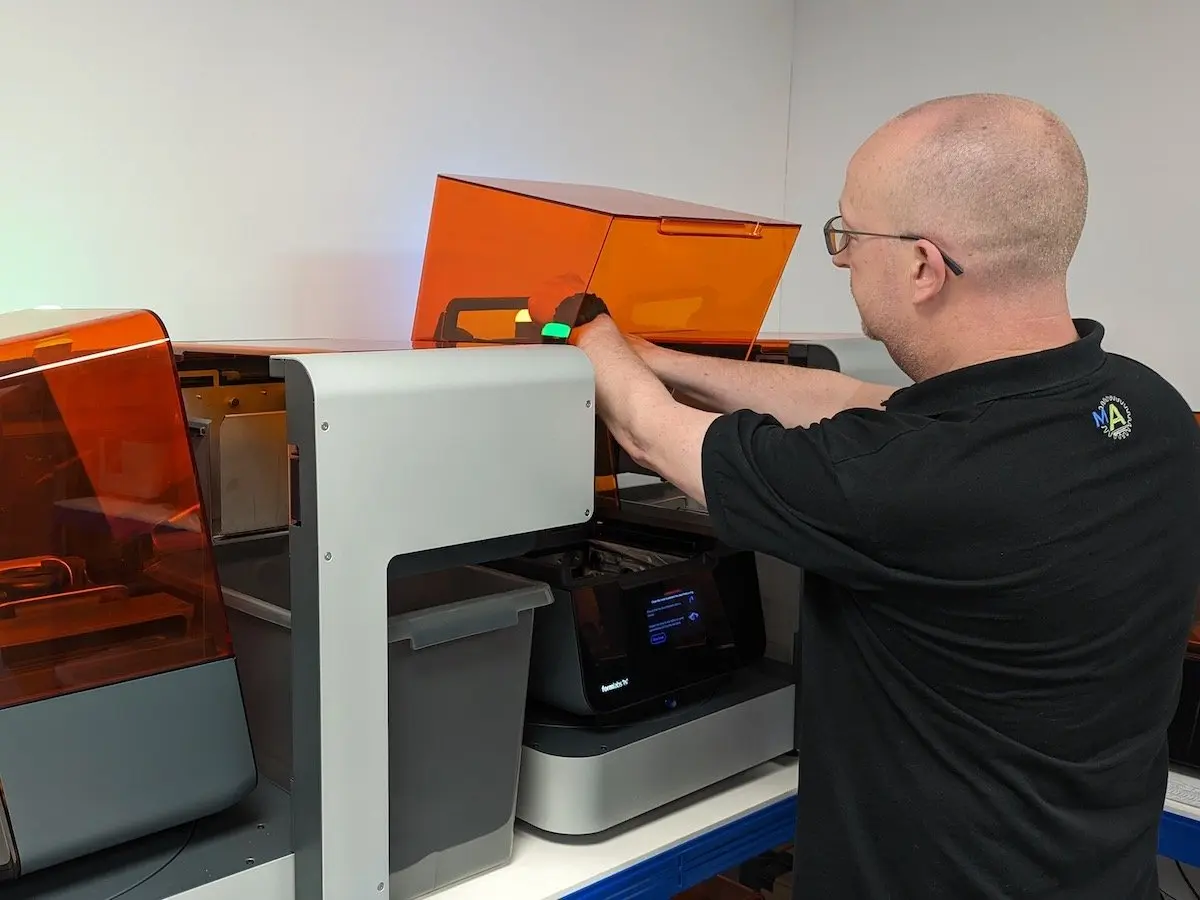
La Form Auto peut être fixée à une imprimante Form 3 ou Form 3+ existante, ce qui permet aux laboratoires de développer leur installation matérielle progressivement, à mesure que leur activité se développe.
Mackart a adopté l’écosystème d’automatisation Formlabs à un stade précoce. La société a commencé à utiliser la Form Auto au début de 2023 et optimise depuis son flux de travail automatisé. « Nous avons une opportunité pour optimiser la capacité. L’avantage de la Form Auto est qu’il est possible de poursuivre le travail la nuit », déclare M. McCarthy.
Une Form Auto a été fixée à deux des neuf imprimantes Form 3+ de Mackart et fonctionne en continu, y compris la nuit et les week-ends, pour continuer à imprimer même lorsque l’équipe a terminé de travailler.
« Avec la Form Auto, il est possible de travailler la nuit et le week-end, sans prévoir de rotations, ni modifier les plateformes de fabrication. Le processus fonctionne très bien. Il est adapté aux composants de petite taille et la production par lots de taille moyenne inclut jusqu’à 1000 pièces et plus ».
Steven McCarthy, Directeur général et fondateur, Mackart
L’équipe de Mackart travaille en permanence sur différents projets. Même si elle demeure impliquée dans le travail de certaines des pièces plus récentes et complexes, la Form Auto peut gérer beaucoup de tâches répétitives et réduire le temps d’arrêt de l’imprimante. « Notre délai de production a été réduit et la productivité a augmenté », conclut M. McCarthy.
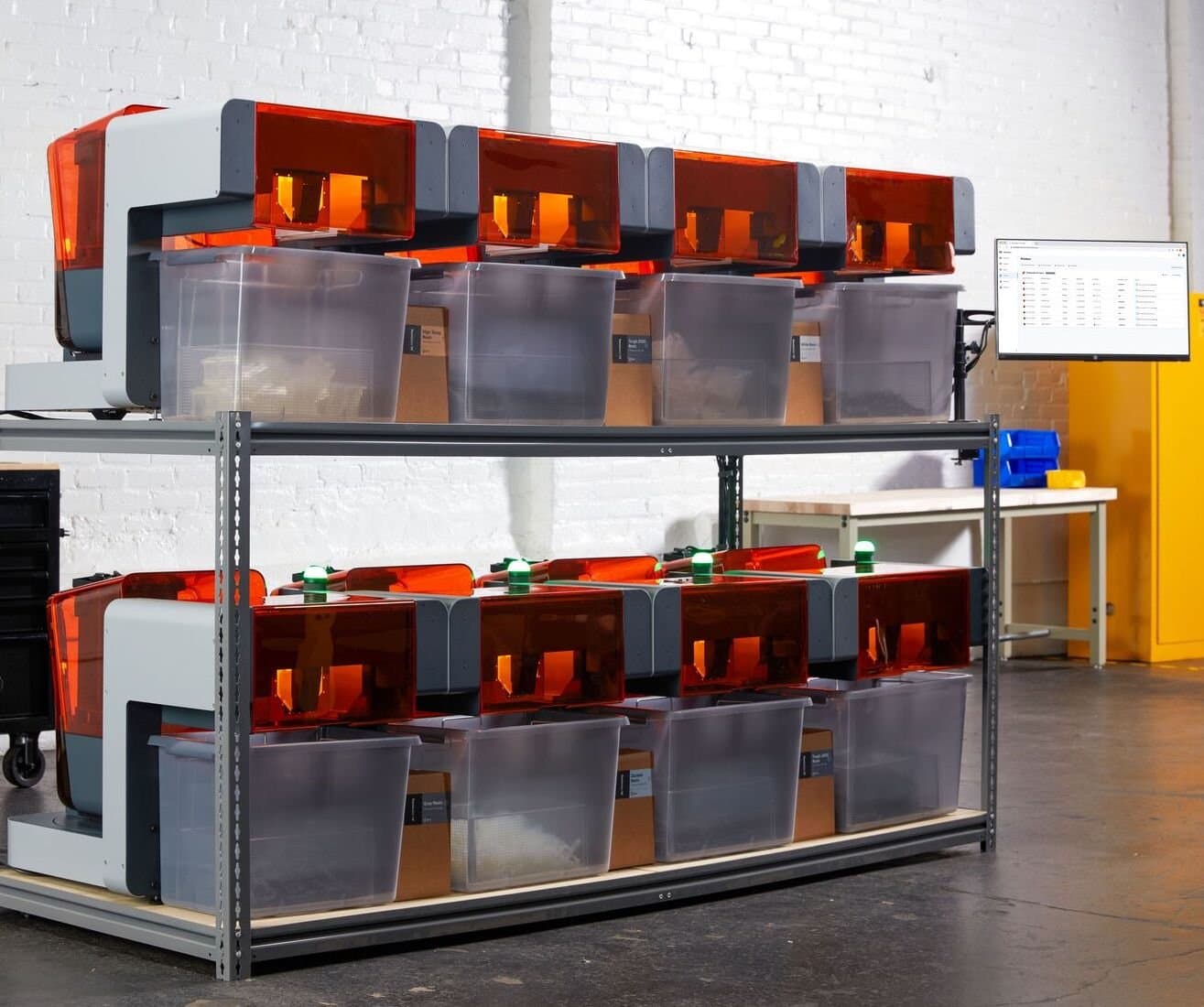
Présentation de l’écosystème d’automatisation Formlabs
Découvrez l’écosystème d’automatisation Formlabs : produisez des pièces en continu 24/7, augmentez votre rendement et automatisez votre parc d’imprimantes 3D.
Des économies de plus de 10 000 £ sur les pièces de voitures de collection
Certaines de ces tâches répétées concernent de petites pièces qui doivent être produites en volumes élevés, telles que les pièces de voitures de collection. Typiquement, ces pièces auraient été moulées par injection. Cependant, beaucoup de ces outils sont tombés dans l’oubli et les derniers stocks sont épuisés. Cette situation a amené un client à demander de l’aide à Mackart.
Ces pièces pouvaient auparavant coûter 0,20 £ à l’unité lorsqu’elles étaient disponibles. L’impression 3D multiplie le prix de ces pièces environ 5 à 10 fois, mais économise les coûts des nouveaux outils, de la production minimale par moulage par injection, des frais d’installation, ainsi que de l’incapacité à amortir ces coûts de production de façon viable pour chaque composant individuel.
Le composant imprimé en 3D offre désormais une solution tout à fait viable. « En imprimant ces pièces en 3D, on enlève de l’équation l’amortissement du coût de toute la production par moulage par injection. Nous concevons par rétro-ingénierie ce dont les clients ont besoin et ils peuvent acheter une seule unité, sans débourser plus de 10 000 £ pour acheter un nouvel outil de moulage par injection et payer les coûts de tous les autres procédés associés. Ils ont ensuite une opportunité d’approvisionnement illimitée pour les quantités dont ils ont besoin », souligne M. McCarthy.
Dans le secteur automobile, avoir besoin d’un seul élément ou même d’un faible volume peut revenir très cher, ce qui fait de la restauration et de la maintenance d’une voiture de collection un passe-temps de luxe. Avec l’impression 3D, Mackart peut offrir des remises aux clients en fonction de la quantité. « Il s’agit d’une solution économique bien plus flexible et c’est là que la Form Auto fait la différence. Elle est livrée prête à l’emploi, elle requiert peu d’entretien et on peut imprimer 1000 pièces, en ajoutant simplement une nouvelle cartouche de résine de temps à autre », dit M. McCarthy.
Mackart cherche désormais à augmenter la capacité
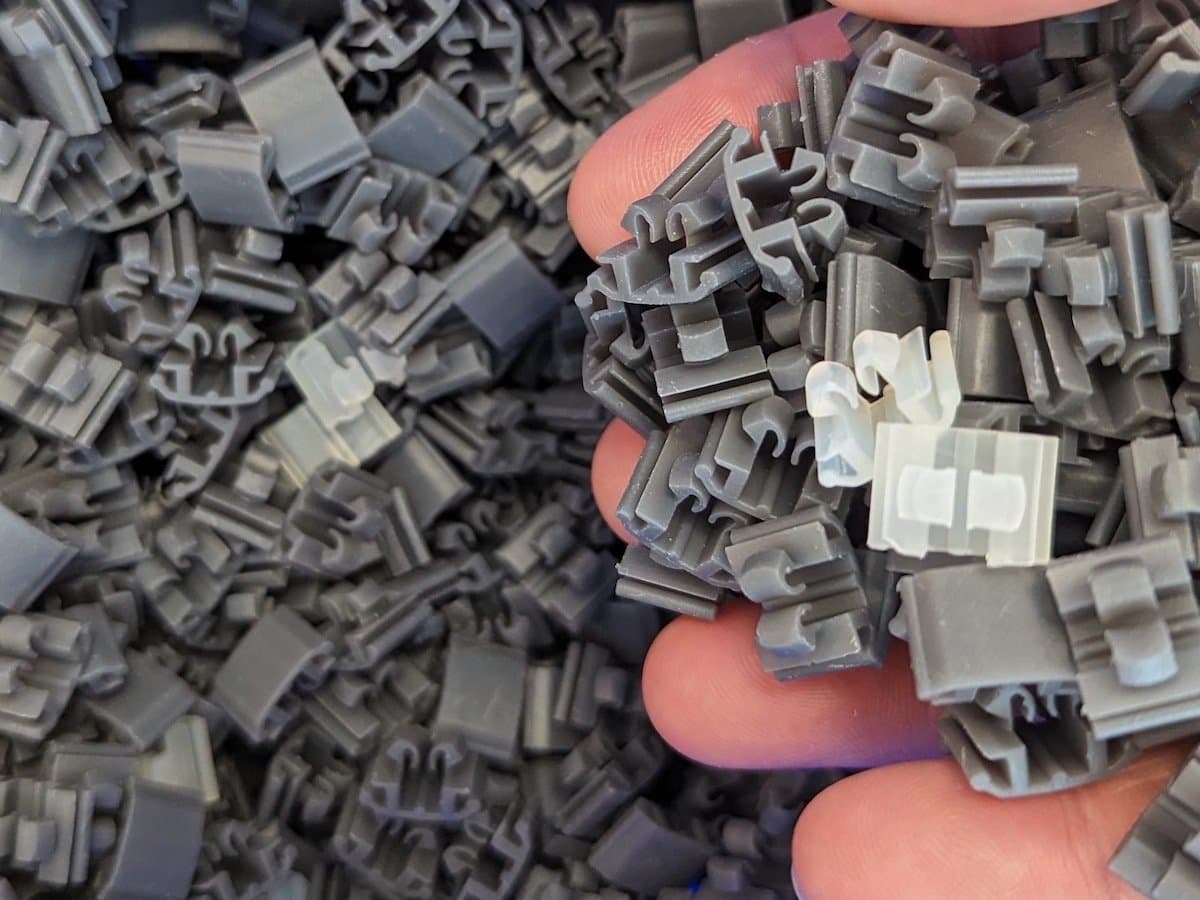
La Form Auto excelle dans l’art d’aider Mackart à fabriquer des centaines ou des milliers de petites pièces, comme ces clips pour le marché des voitures de collection.
Mackart a pris le temps d’optimiser ses processus afin de produire des conceptions de haute qualité pour ses clients dans de nombreux secteurs différents. La société y est parvenue en s’appuyant sur un ensemble de technologies complémentaires et en tirant parti des différents matériaux et méthodes d’impression 3D dans les cas appropriés.
L’adoption de la Form Auto a augmenté sa capacité et a permis d’étendre sa semaine de production aux trois-huit, sans personnel. Pour la suite, M. McCarthy a la certitude qu’à mesure que la demande augmente, Mackart peut utiliser son parc d’imprimantes 3D pour conquérir de nouveaux secteurs et aborder de nouvelles applications sans se départir de la précision et des performances qui ont fait de la société un partenaire de confiance pour certaines des plus grandes équipes de F1 au monde.
Remerciements spéciaux à notre revendeur partenaire au Royaume-Uni, Solid Print3D, qui conseille et soutient Mackart en lui fournissant des solutions d’impression 3D Formlabs. Pour en savoir plus sur les applications de l’impression 3D dans le secteur automobile, consultez notre page de ressources ou contactez notre équipe pour discuter de votre application spécifique.