Résolution de problèmes dans l’atelier : aides à la fabrication chez Productive Plastics
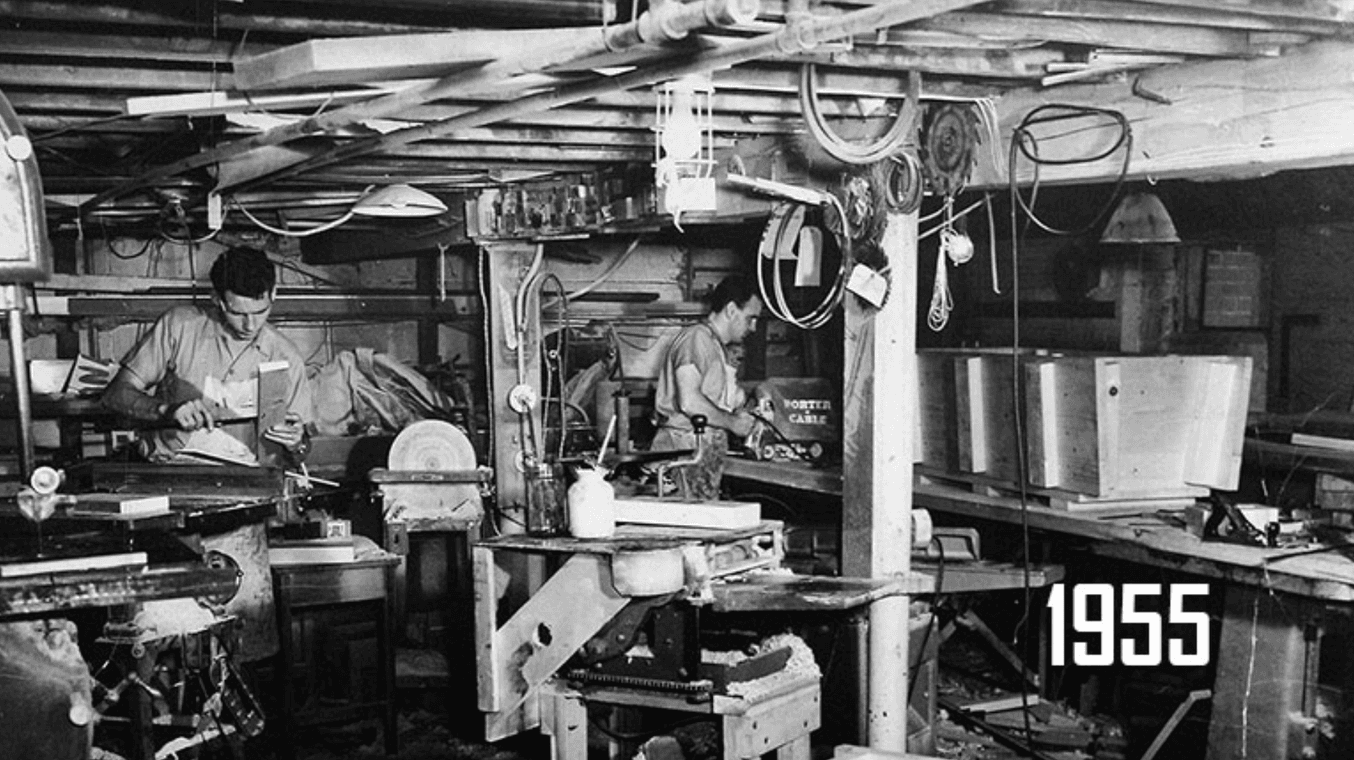
Productive Plastics existe depuis 1955 et fournit des pièces thermoformées de haute qualité pour les secteurs médicaux, ferroviaires, électroniques et automobiles, entre autres.
Productive Plastics, entreprise de thermoformage industriel, voit tout en grand : les machines sont imposantes, les clients sont de grandes sociétés et les volumes de production sont élevés. L’entreprise peut avoir à gérer des commandes de centaines de grands boîtiers pour des sociétés de dispositifs médicaux du classement Fortune 500 ou de milliers de composants d’accoudoirs pour des trains.
Les pièces demandées par les clients changent constamment, mais les machines et la main-d’œuvre de Productive Plastics restent les mêmes. L’entreprise a donc dû optimiser chacun de ses processus pour qu’ils puissent s’adapter à de nouvelles géométries et de nouveaux types de pièces. Elle a ainsi créé une large gamme d’aides à la fabrication sur l’imprimante 3D à frittage sélectif par laser (SLS) Fuse 1.
Dans l’atelier de fabrication Productive Plastics
Le thermoformage est un procédé de fabrication qui consiste à chauffer et à mouler des feuilles de plastique dans la forme souhaitée. De nombreuses méthodes différentes existent, les plus populaires étant le formage sous vide, le formage sous pression ou le formage avec des forces mécaniques Productive Plastics dispose de six cellules de fabrication, de sorte que plusieurs projets peuvent être menés de front. Chaque cellule est équipée d’une thermoformeuse industrielle, d’une fraiseuse CNC, d’une zone d’assemblage et d’un système informatique permettant d’organiser et de contrôler les opérations.
Ces six cellules fonctionnent en continu et enchaînent les commandes sans interruption. Dustin Johnson, ingénieur en outillage, identifie et conçoit les aides à la fabrication nécessaires à chaque commande. Une tâche peut nécessiter un guide de perçage pour aider les techniciens à assembler deux pièces avec précision, tandis qu’une autre peut nécessiter une pièce de rechange sur une machine cassée.
« La Fuse 1 était notre première imprimante 3D. Avant de l’acquérir, nous devions parfois usiner du bois pour créer des socles, sous-traiter la fabrication de fixations personnalisées à des sociétés de moulage par injection ou tout simplement renoncer à une aide à la fabrication et estimer l’espacement », explique M. Johnson.
L’utilisation de la Fuse 1 a permis de réduire les coûts, d’améliorer la productivité et d’éviter les arrêts ou retards. M. Johnson a même commencé à concevoir des alternatives imprimées en 3D destinées à une utilisation finale pour les assemblages des clients. « Nous pouvons bien mieux contrôler les délais de fabrication en interne. Il est beaucoup plus simple d’appuyer sur le bouton Imprimer que de demander une pièce au client ou à un fournisseur externe. Et plus nous pouvons faire de choses en interne, plus nous améliorons la rentabilité », explique Kyle Davidson, directeur des ventes et du marketing chez Productive Plastics.
Réduire les coûts avec des gabarits et fixations en interne
Productive Plastics est spécialisé dans le thermoformage de forte épaisseur et utilise souvent des feuilles épaisses d’un alliage PVC/acrylique tel que le Kydex pour les composants finaux produits. Ces feuilles sont assez peu onéreuses, mais éviter le gaspillage en alignant correctement la taille des pinces, les pièces et les paramètres de moulage peut permettre à la société, et à ses clients d’économiser des milliers de dollars.
Pour une pièce intérieure spécifique d’un wagon, les paramètres de moulage faisaient que les pinces étaient trop éloignées du moule. Une distance de 0,25 pouce (environ 0,6 cm) devait être maintenue entre le moule et le cadre de serrage d’une façon ou d’une autre, que ce soit en utilisant une fixation pour assurer cet espacement ou en choisissant une feuille plastique plus grande.
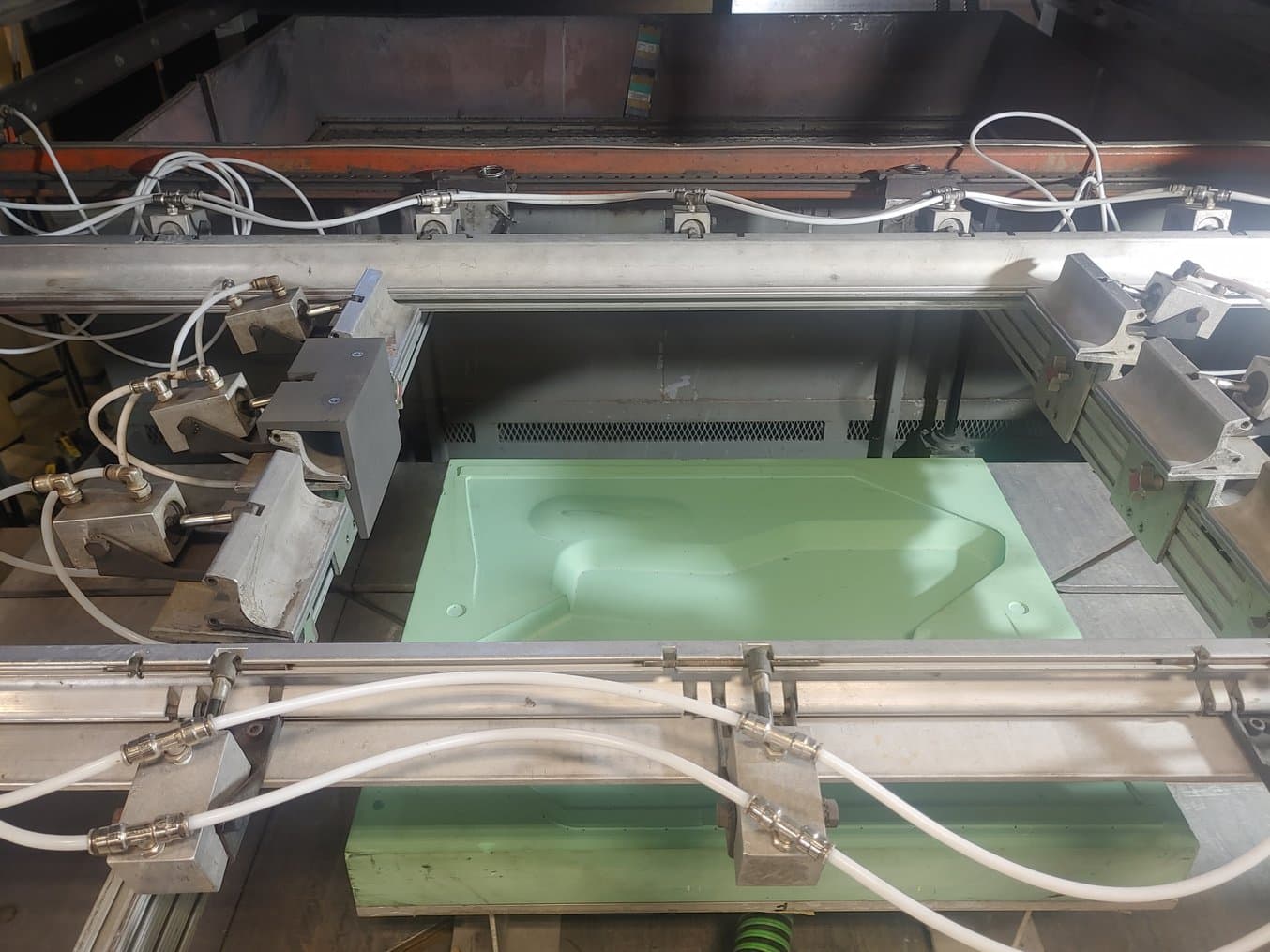
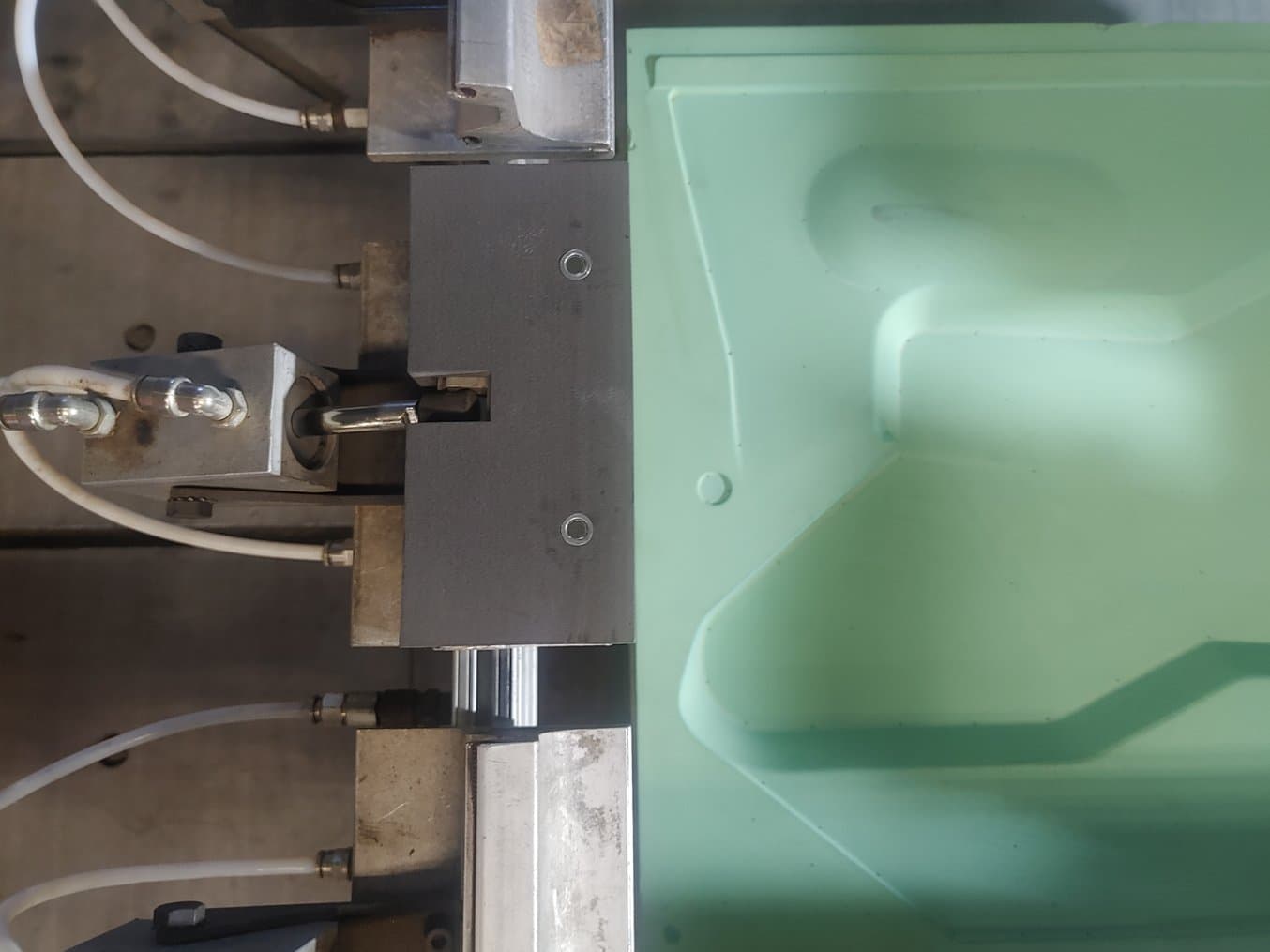
La fixation de serrage (pièce gris clair) assure l’espacement correct entre le moule (vert clair) et le cadre de serrage (structure métallique).
Une feuille plus grande aurait été plus lourde, entraînant un coût par pièce plus élevé et plus de déchets, mais faire produire des pinces personnalisées par une société externe aurait prolongé le délai de réalisation de deux à trois semaines. L’impression 3D en interne de fixations de serrage personnalisées a permis à Productive Plastics d’utiliser des feuilles de la taille optimale, ce qui permet d’économiser de l’argent et de réduire les déchets, tout en évitant des retards de production.
"Utiliser exactement la bonne taille de feuille permet de réduire les coûts pour le client. Grâce à l’impression 3D, nous pouvons personnaliser les largeurs de façon très précise avec des pinces personnalisées. En une seule journée, nous avons pu finaliser l’impression et lancer la production."
Kyle Davidson
Continuer à produire avec des pièces de rechange
Avec autant de clients et de commandes à livrer dans les temps, rien n’arrête la production. Sauf, bien sûr, une panne de la thermoformeuse sous vide. Lorsque la roue de la pompe d’une machine a cassé, l’équipe était censée attendre six à huit semaines pour recevoir une pièce de rechange. « Une société de thermoformage ne peut pas travailler sans pompe à vide. Nous ne pouvons pas fermer une cellule entière pendant six semaines, nous avions donc besoin d’une solution provisoire », explique M. Davidson.
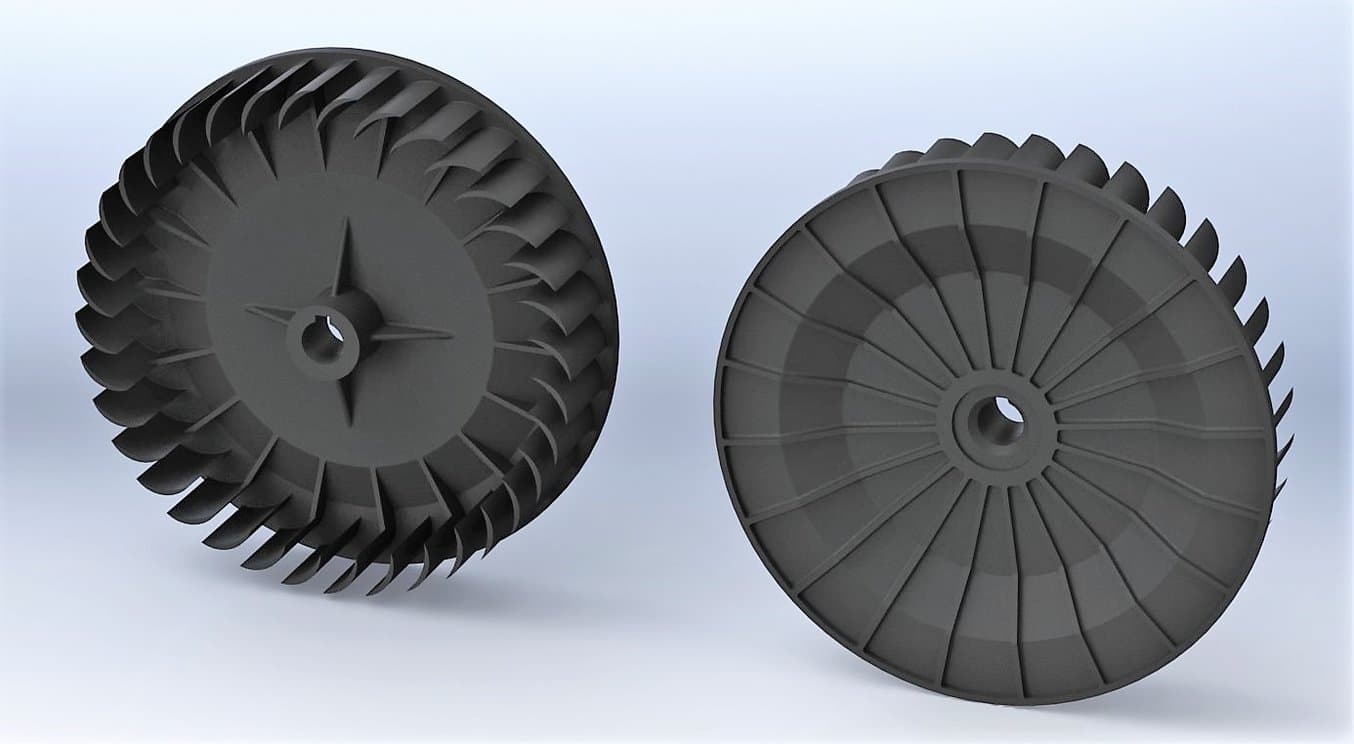
Le fichier 3D de la pièce de rechange dans Solidworks. Les deux côtés présentent des zones positives et négatives ainsi qu’un alésage central, ce qui élimine les technologies utilisant des structures de support, telles que les potentielles solutions FDM et SLA.
Ils ont conçu deux itérations de roue de remplacement dans Solidworks, puis les ont imprimées sur une Fuse 1 pendant la nuit en utilisant Nylon 12 Powder. La roue a immédiatement fonctionné, en s’ajustant parfaitement dans la pompe à vide existante, ce qui a permis de relancer la cellule. Le lit de poudre autoportant de l’impression 3D SLS a permis de réaliser une pièce à double face avec un alésage central sans supports à retirer ou à post-traiter. La roue était prête à être immédiatement installée sur la machine existante.
"Attendre une pièce de rechange nous aurait contraints à fermer la cellule pendant des semaines. Cela aurait engendré des pertes d’environ 30 000 $, donc cette pièce de remplacement provisoire à elle seule a quasiment remboursé l’imprimante."
Kyle Davidson
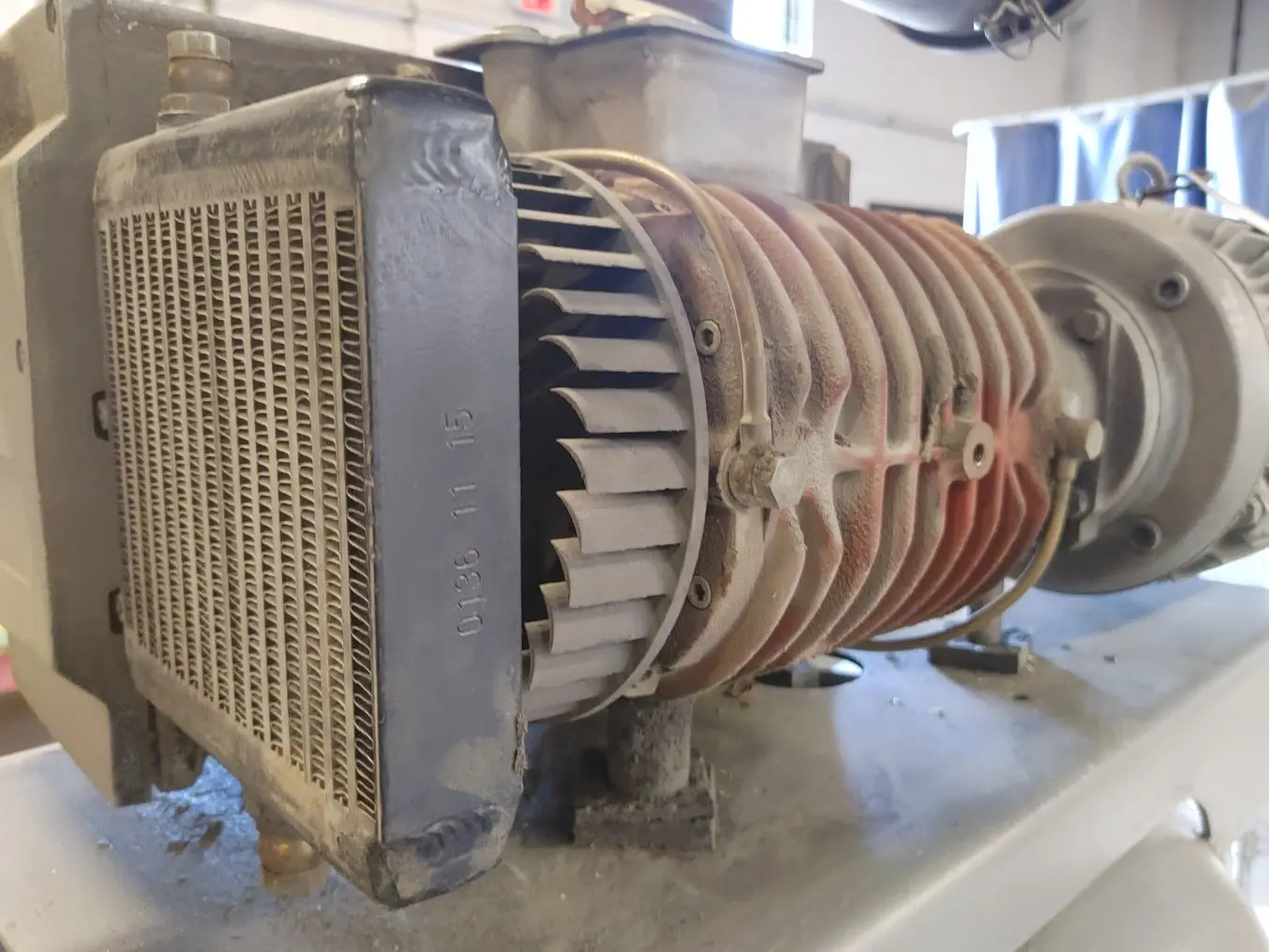
Gros plan (à droite) et vue agrandie (à gauche) de la roue imprimée en 3D, qui s’intègre parfaitement dans la pompe à vide industrielle pour le thermoformage.
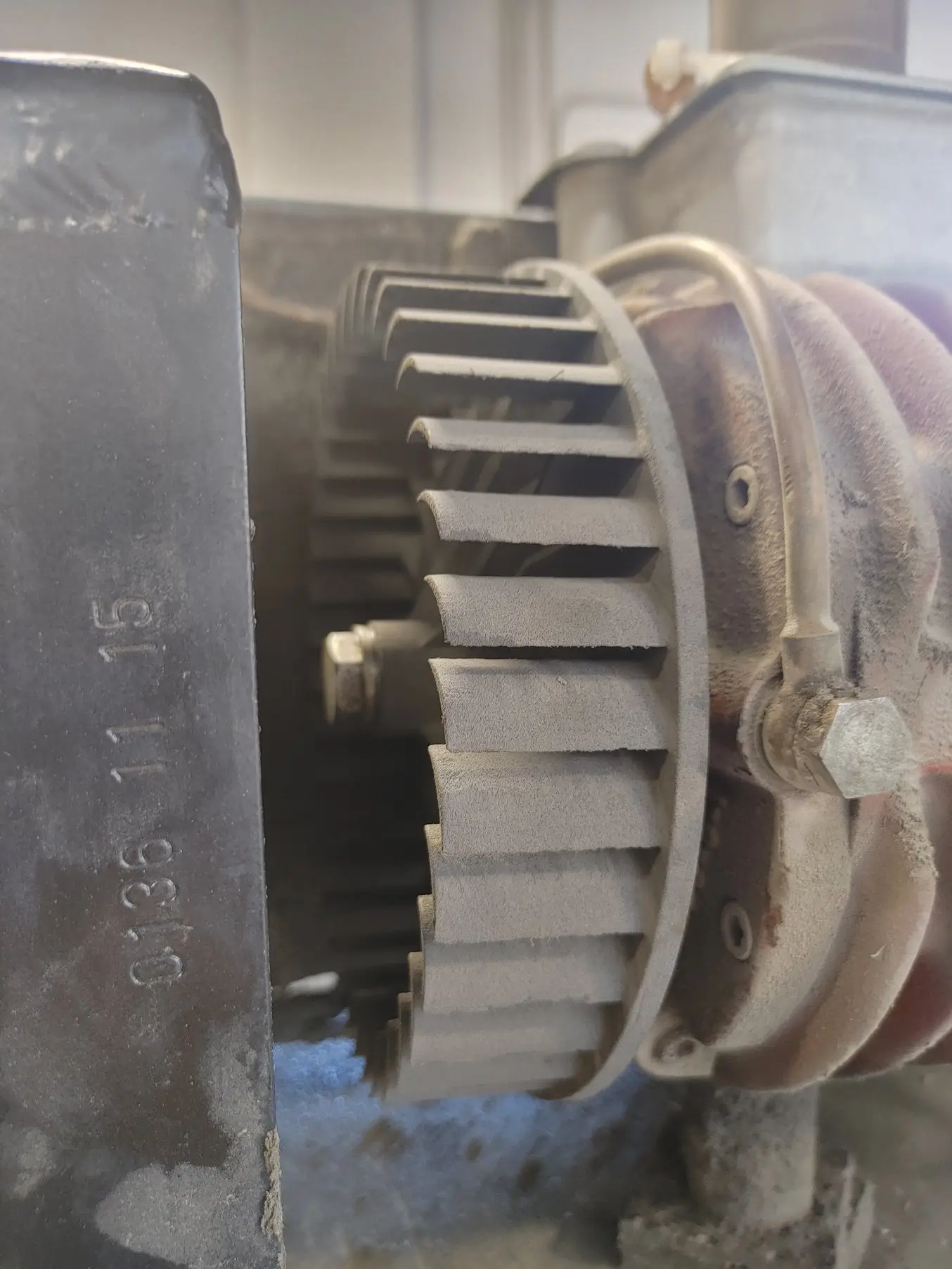
Gagner beaucoup de temps, quelques secondes à la fois
Les pièces subissent souvent des processus secondaires, tels que l’assemblage ou la finition, après leur formage. Ces processus secondaires nécessitent des outils et des manipulations spécialisés, comme le masquage à la main pour la peinture. Pour cette pièce, les techniciens recouvraient de ruban adhésif une surface cuivrée, puis indiquaient manuellement au pochoir l’endroit où le cuivre se terminait afin que la peinture puisse recouvrir le reste de la pièce. Cette délimitation n’était pas très précise, et les erreurs, les rayures sur le cuivre ou les deuxièmes tentatives étaient fréquentes. Au contraire, avec un ou deux pochoirs imprimés en 3D, les opérateurs peuvent découper rapidement et efficacement.
« Même si l’on n’économise que 10 à 15 secondes par pièce, cela se traduit par des économies significatives sur l’ensemble du cycle de vie du produit », explique M. Johnson. « Nous avions l’habitude de sculpter du bois pour faire cela à la main, mais c’était difficile et chronophage. Une pièce imprimée en 3D ne coûte que quelques dollars, et cela se fait facilement d’une main. »
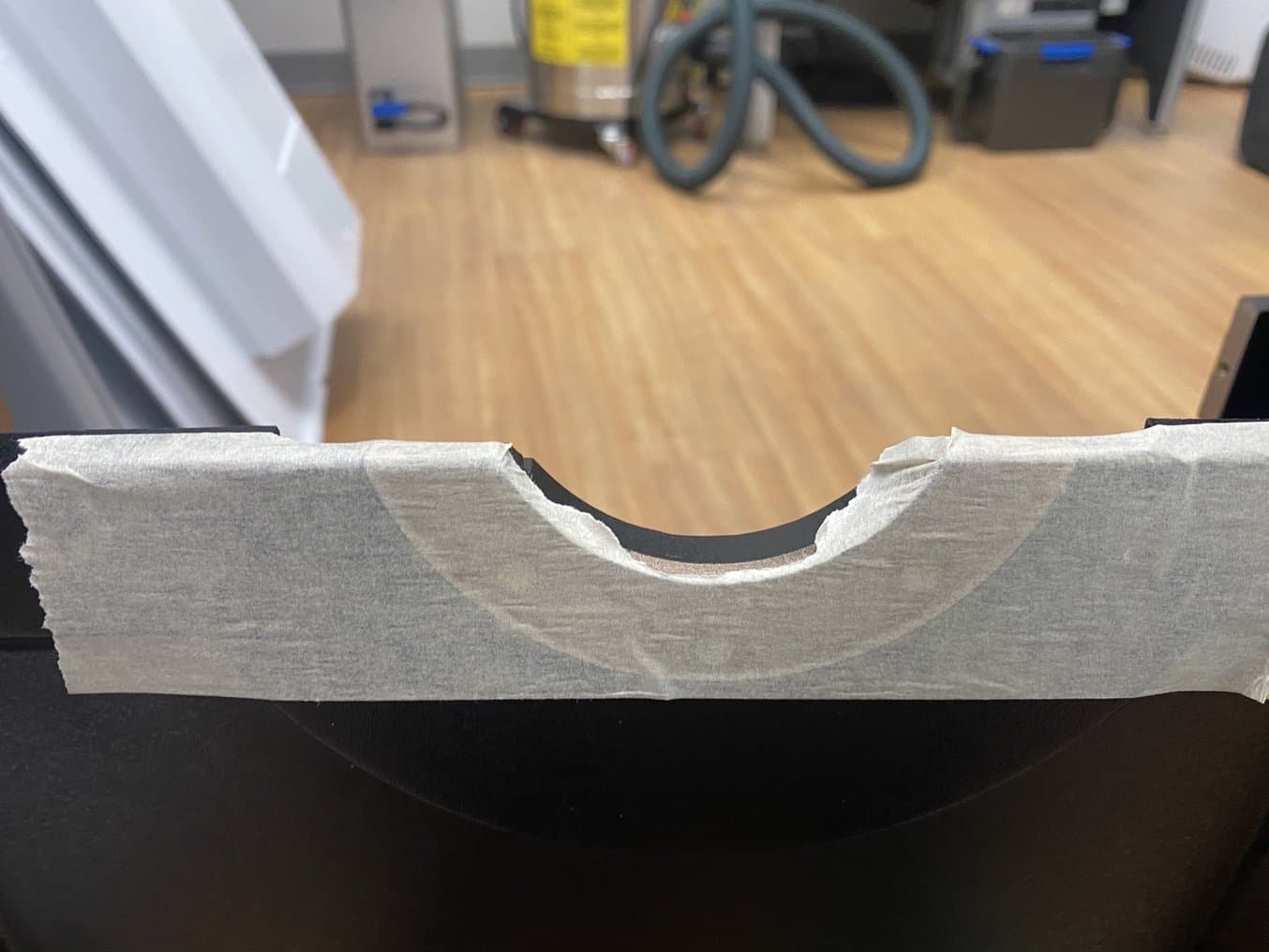
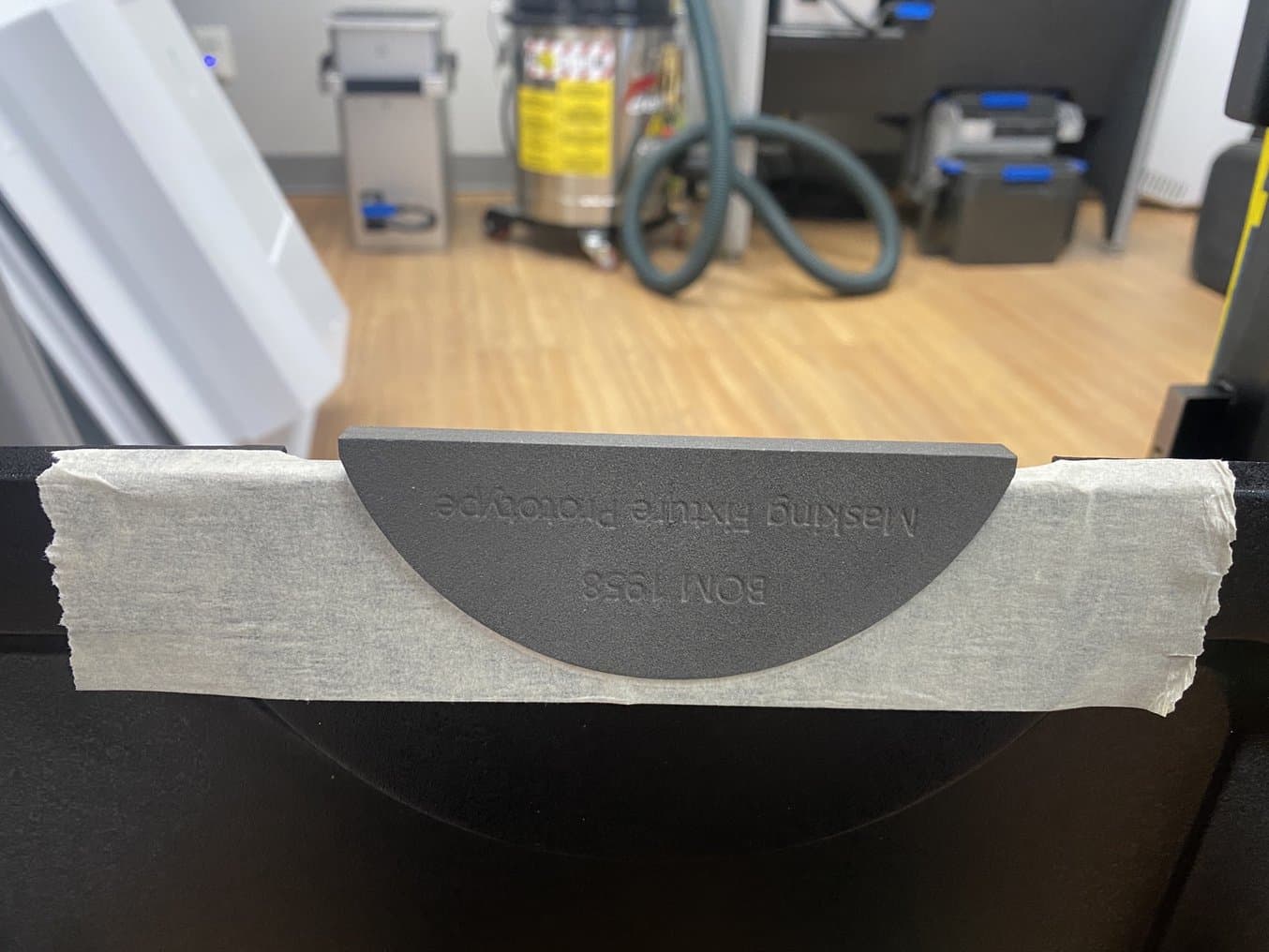
Pendant la première étape, le ruban adhésif recouvre une grande partie de la pièce. Pendant la deuxième, la pièce imprimée en 3D sert de pochoir autour duquel un technicien découpera le reste du ruban adhésif, de sorte que la partie revêtue reste exempte de peinture, tandis que le reste de la surface est peint en noir.
Améliorer la communication client pour éviter les surprises
Lors de la conception du processus, Productive Plastics travaille avec ses clients pour développer la pièce, le processus de thermoformage et le type de blocs qui sont fixés aux pièces dans un assemblage secondaire. Ces blocs, nécessaires pour l’intégrité structurelle ou les éléments de l’assemblage fonctionnel, doivent s’adapter parfaitement à la feuille thermoformée. Des centaines ou des milliers de blocs étant nécessaires, la moindre erreur peut être très coûteuse.
L’équipe avait l’habitude d’esquisser un dessin des blocs, avec les dimensions et les tolérances nécessaires, mais il est difficile de représenter des surfaces inclinées sur un dessin en deux dimensions. Les blocs avaient donc souvent une taille ou une forme incorrecte. Les blocs arrivaient juste avant que le thermoformage ne soit lancé, et lorsque l’erreur était découverte, l’ensemble du projet s’arrêtait net. Au contraire, les capacités de production en interne avec la Fuse 1 garantissent que chaque client crée des ensembles de blocs parfaitement adaptés.
« Nous avons besoin de milliers de ces blocs, donc même si le diamètre est légèrement incorrect sur un simple bloc, c’est un gaspillage énorme et nous ne pouvons pas terminer le projet. Envoyer aux clients un produit physique ne nous coûte que quelques dollars et évite de produire des milliers de pièces incorrectes », explique M. Johnson.
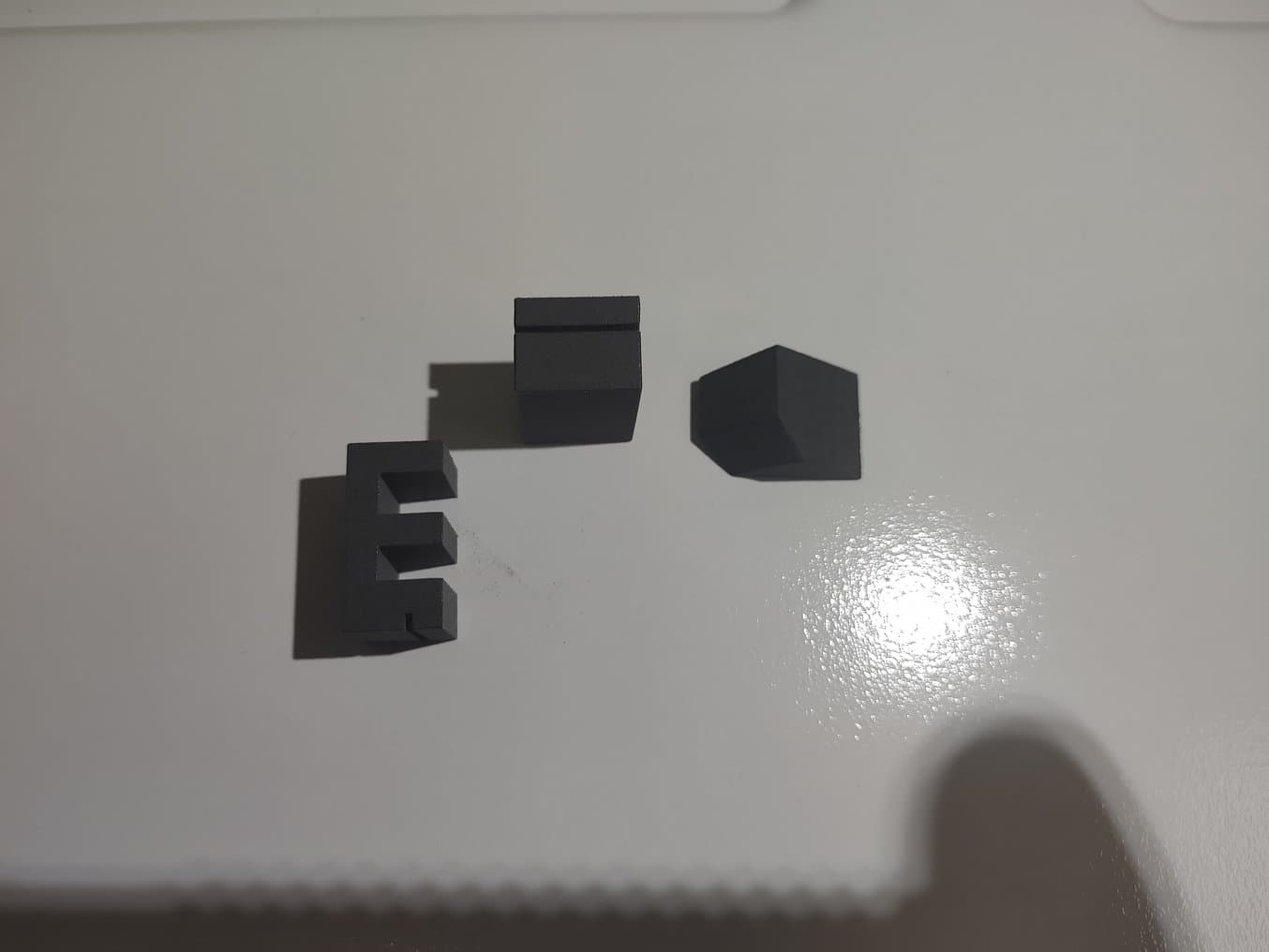
Les blocs personnalisés imprimés en 3D sont utilisés au moment de l’assemblage fonctionnel d’une pièce thermoformée. Un bloc incorrect peut stopper net tout le cycle de production.
Améliorer l’efficacité de chaque cellule
Entre le volume de commandes, la variété des pièces et le nombre d’étapes de chaque processus, l’activité est intense chez Productive Plastics. Tout ce qui peut faciliter la communication entre les différents services a un impact énorme sur l’efficacité de l’équipe.
Chaque cellule utilise un système de surveillance informatique qui assure le suivi des commandes, des manuels des machines, du registre d’aides à la fabrication et des pièces. Bien qu’ils aient essayé de faire passer leurs systèmes informatiques sur des tablettes, il n’y avait pas de moyen facile de garder les tablettes facilement accessibles et mobiles à la fois. Les boîtiers de protection de qualité industrielle des tablettes ne pouvaient pas s’adapter à un support standard, de sorte qu’elles étaient souvent laissées sur une étagère ou sur un poste de travail encombré. M. Johnson a réussi à démonter un support de téléphone classique et à en faire l’ingénierie inverse. Il a ainsi conçu quelque chose de plus grand, capable de s’accrocher au boîtier industriel de la tablette et de se fixer solidement sur un panneau de bois.
« Cela nous a permis de nous assurer que les tablettes restent mobiles, tout en étant facilement accessibles au meilleur endroit pour nos opérateurs. Nous n’avons rien trouvé sur le marché pour moins de 300 dollars, mais je les ai imprimés pour 30 dollars sur la Fuse 1, et nous en avons monté quelques-uns dans chaque cellule », explique M. Johnson.
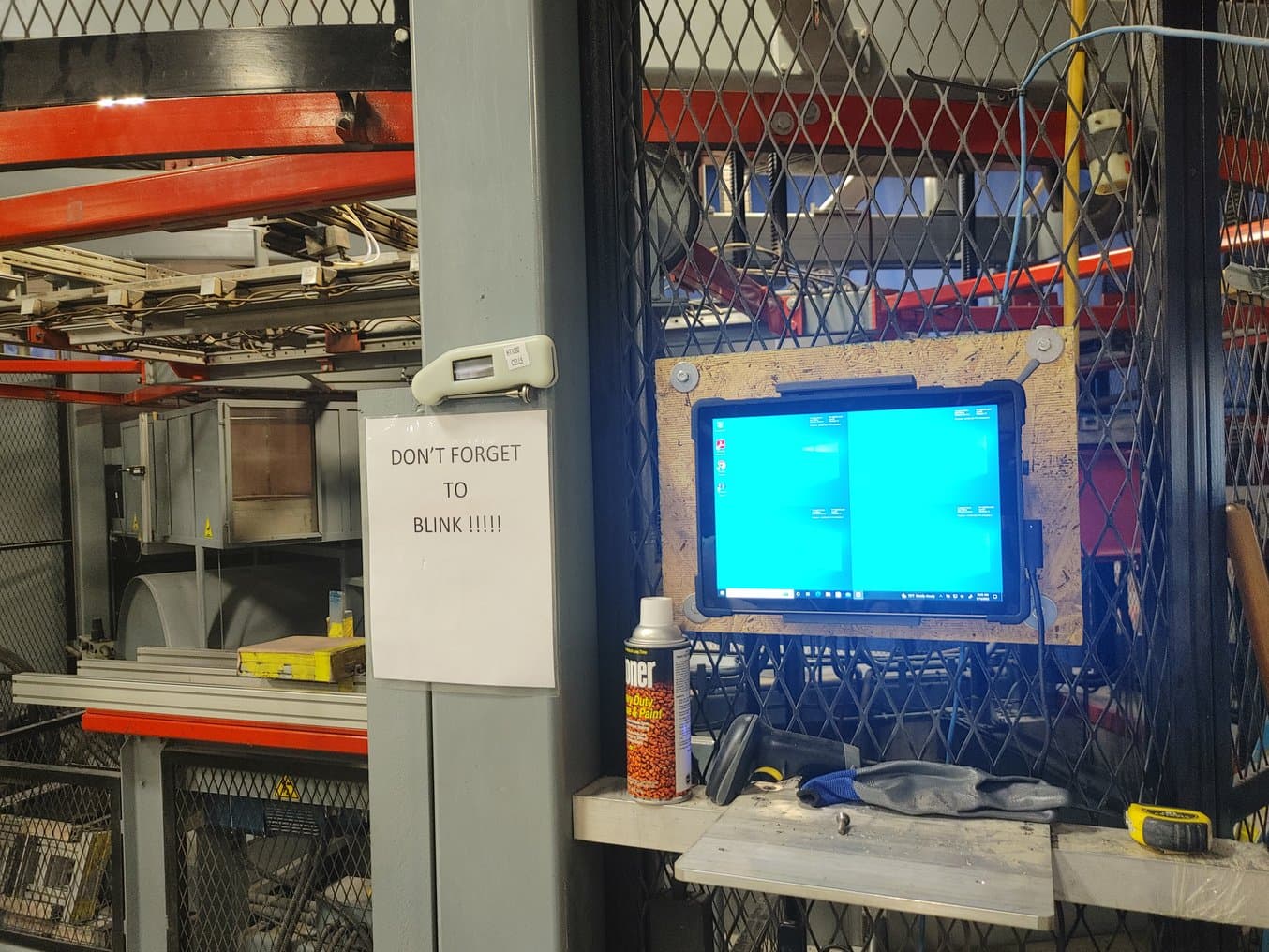
Le support de tablette conçu sur mesure permet de la fixer sur le mur et de la détacher pour se déplacer avec elle dans la cellule.
Assurer une production à plein régime
Une fois le processus initial de thermoformage terminé, les opérateurs effectuent les processus secondaires nécessaires, qu’il s’agisse de fixer des blocs à la pièce pour l’assemblage, de découper la pièce ou de la préparer d’une autre façon pour le client. Lorsque les blocs sont attachés à la pièce moulée, Productive Plastics garantit une tolérance de 0,03 pouce (environ 0,76 mm). Une méthode de mesure était donc nécessaire pour vérifier que chaque bloc était parfaitement attaché.
L’équipe renonçait aux guides et mesurait à vue de nez, ou utilisait des blocs de bois collés puis usinés aux bonnes dimensions. Les deux méthodes étaient fastidieuses, ralentissaient le processus et entraînaient des erreurs qu’il fallait corriger. M. Johnson a pu concevoir un gabarit de positionnement qui indique précisément l’endroit où fixer les blocs sur la pièce thermoformée, ce qui permet aux opérateurs de fixer correctement les blocs en quelques secondes.
« Nous avons plusieurs ensembles de gabarits utilisés en parallèle, ce qui nous permet de maintenir une production à plein régime. Ils nous ont permis d’améliorer la précision du positionnement des blocs et de récupérer le temps autrefois passé à rogner ou à usiner les blocs », explique M. Davidson.
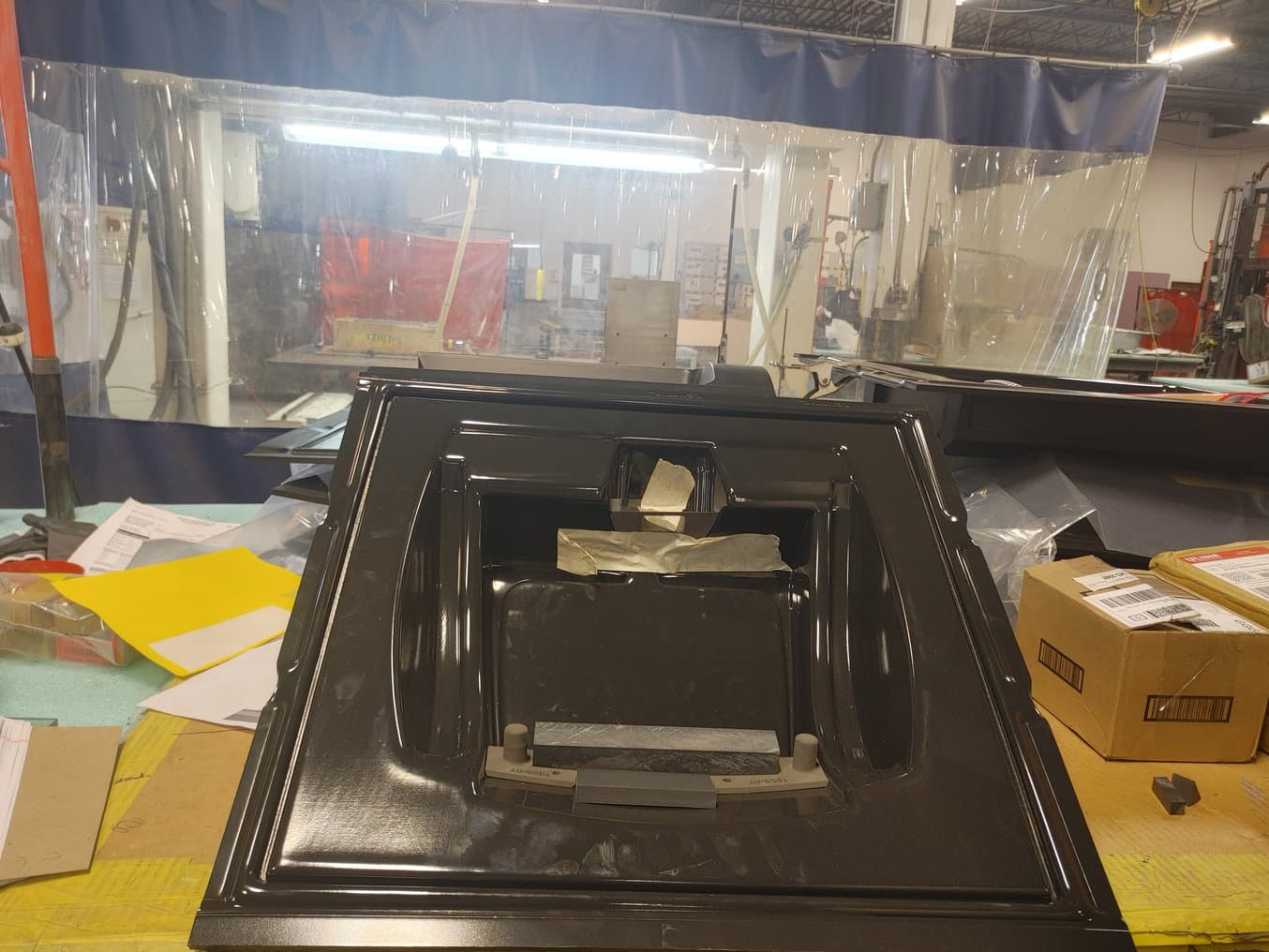
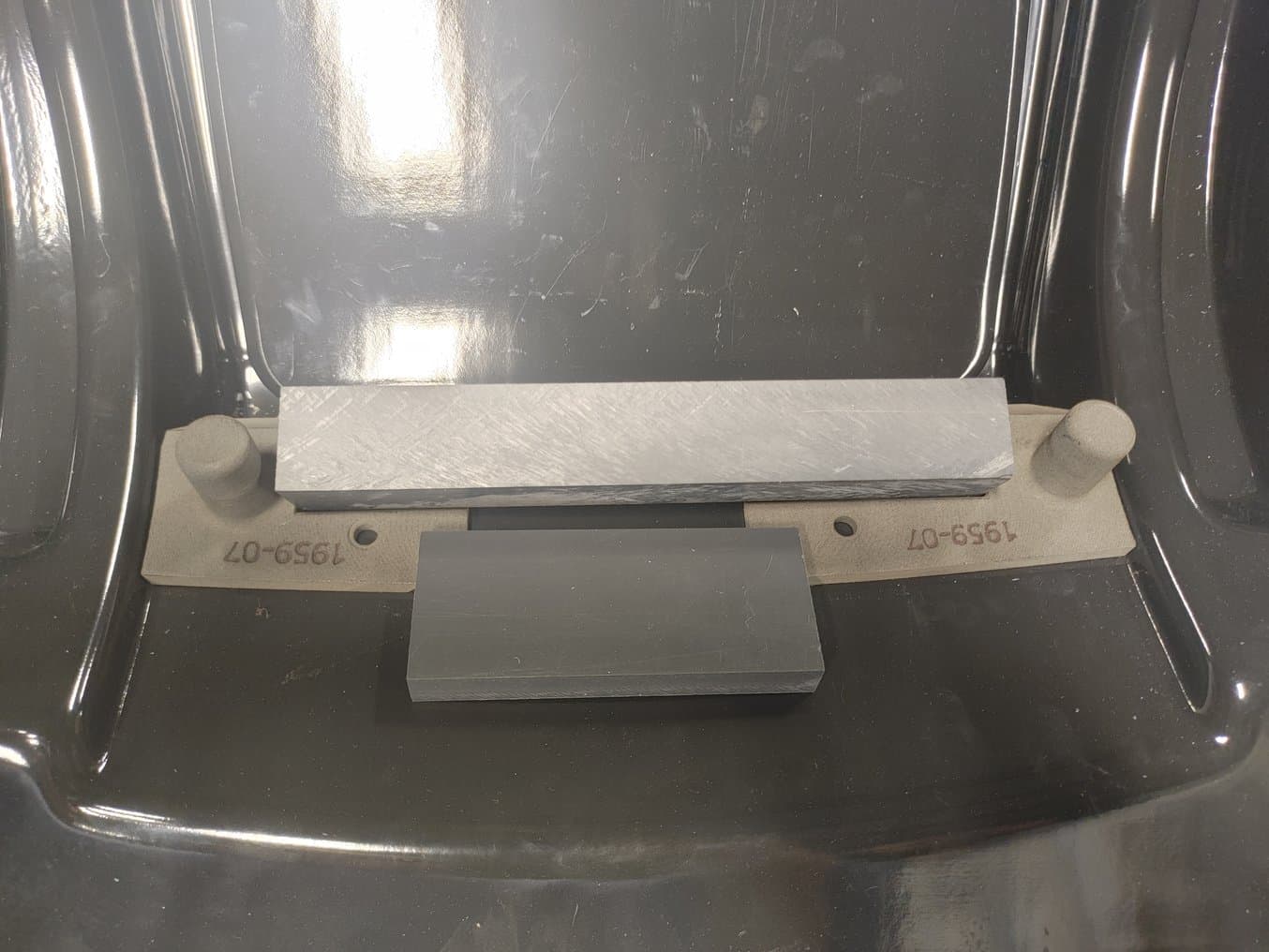
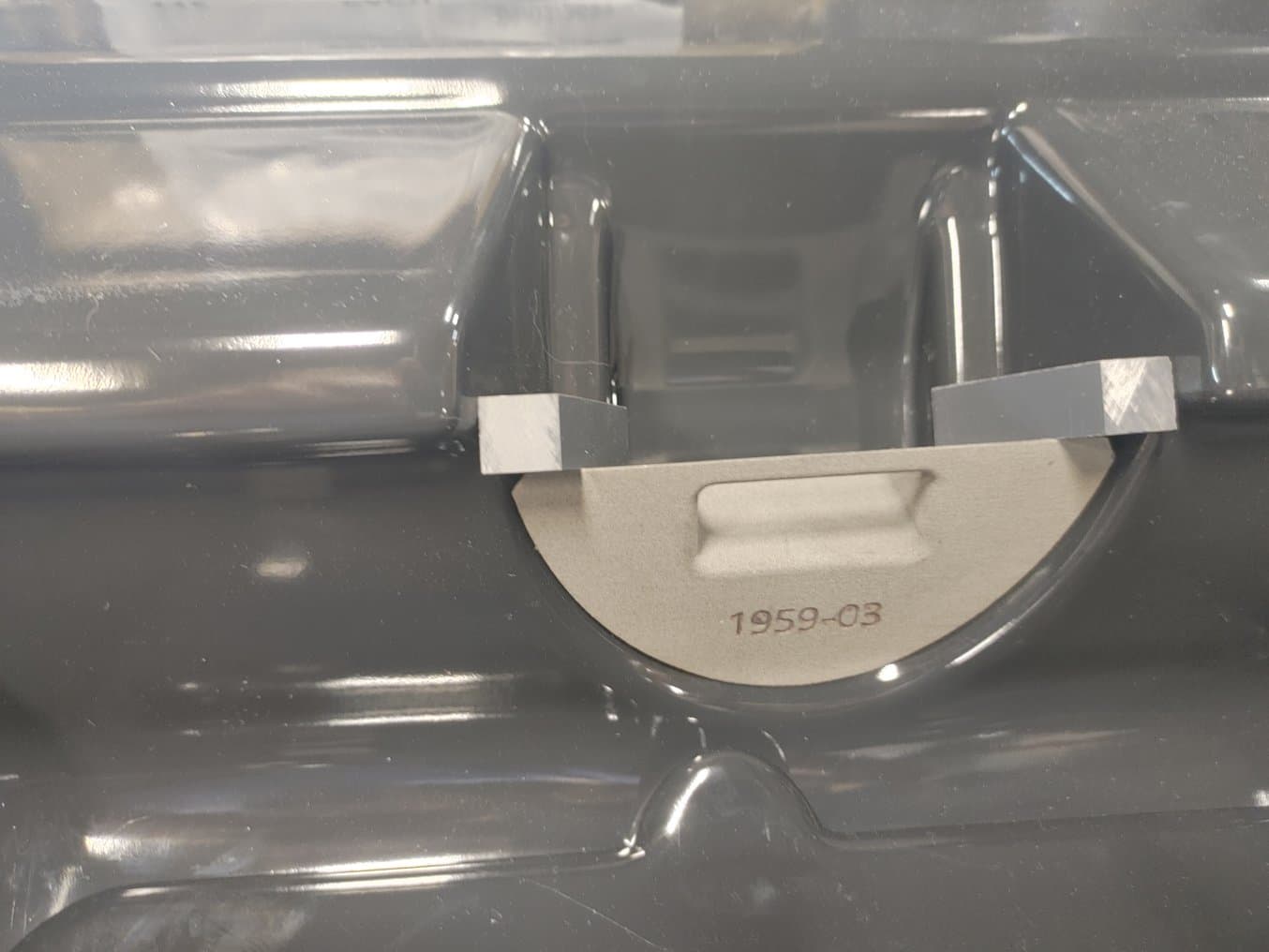
Deux blocs (longue barre argentée et barre gris foncé plus courte) doivent être attachés au boîtier de dispositif médical (pièce moulée noire, photo de gauche). Les deux gabarits de positionnement (pièces gris clair avec des boutons à gauche et à droite) indiquent précisément à l’opérateur où les fixer, ce qui permet de gagner du temps et assure un positionnement correct.
Autres utilisations finales avec Nylon 12 Powder
Lorsque Productive Plastics a rencontré des difficultés à se procurer un composant spécifique lors des retards de la chaîne d’approvisionnement l’année dernière, M. Johnson a décidé de tester l’impression 3D d’un petit composant qu’ils reçoivent en général d’un mouleur par injection. Le composant s’insère dans une machine utilisée dans des établissements de soin pour couvrir toute ouverture lorsqu’elle n’est pas connectée à des perfusions intraveineuses ou autres systèmes de distribution de fluides. En utilisant Nylon 12 sur la Fuse 1, M. Johnson a pu parfaitement recréer le composant moulé par injection, et bien qu’une validation réglementaire spécifique soit nécessaire pour l’utiliser dans un établissement médical, l’équipe a pu le présenter au client comme une alternative viable en cas de problème d’approvisionnement.
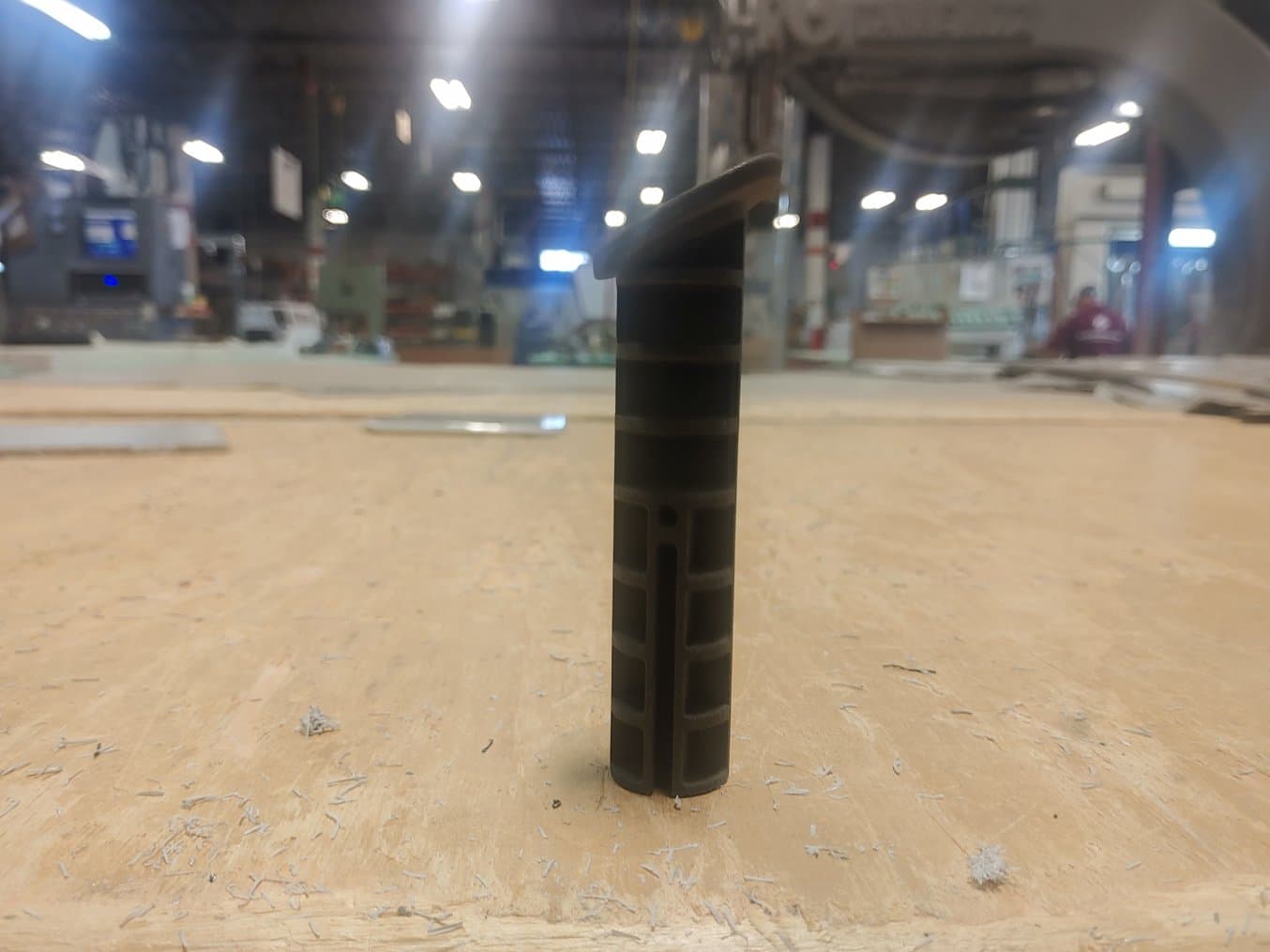
Le bouchon imprimé en Nylon 12 Powder sur la Fuse 1 est une alternative fabriquée en interne à un composant moulé par injection.
Créer une bibliothèque numérique d’aides à la fabrication pour l’avenir
Lorsque les commandes clients sont moulées par centaines et milliers de pièces, les petits détails font la différence. Si l’équipe d’assemblage peut gagner 10 secondes par pièce en utilisant un gabarit de positionnement pour attacher les blocs, ou si une machine peut continuer à fonctionner grâce à une pièce de rechange imprimée en 3D, les opérations sont optimisées et plus efficaces. L’utilisation de la Fuse 1 et de Nylon 12 Powder permet à M. Johnson non seulement de corriger les problèmes, mais aussi d’améliorer préventivement les processus. Ces avantages profitent aux clients, le coût des pièces étant moindre, et contribuent également à leur satisfaction générale.
« Les opérateurs viennent me voir en disant qu’ils ont cassé une pièce ou en demandant si quelque chose peut être amélioré, et j’y travaille avec l’imprimante. J’ai gagné énormément de temps », déclare M. Johnson. L’équipe a pu améliorer la productivité globale en travaillant de manière proactive sur des points de l’atelier où des goulots d’étranglement ou des réparations pourraient ralentir les processus. Bien qu’elle soit leur première imprimante 3D, la Fuse 1 a offert à Productive Plastics de toutes nouvelles possibilités de production.