Guide du moulage par compression, du prototypage à la production de masse
Le moulage par compression est un procédé de fabrication polyvalent utilisé par les entreprises de production petites et grandes pour créer toute une diversité de pièces allant de gros composants aéronautiques à des tétines pour biberon.
Dans ce guide, nous vous présentons une introduction au moulage par compression, ses avantages et ses applications. Ensuite, nous démontrerons comment tout un chacun peut utiliser ce procédé pour tous les volumes de production, de la création de prototypes à la production de masse.
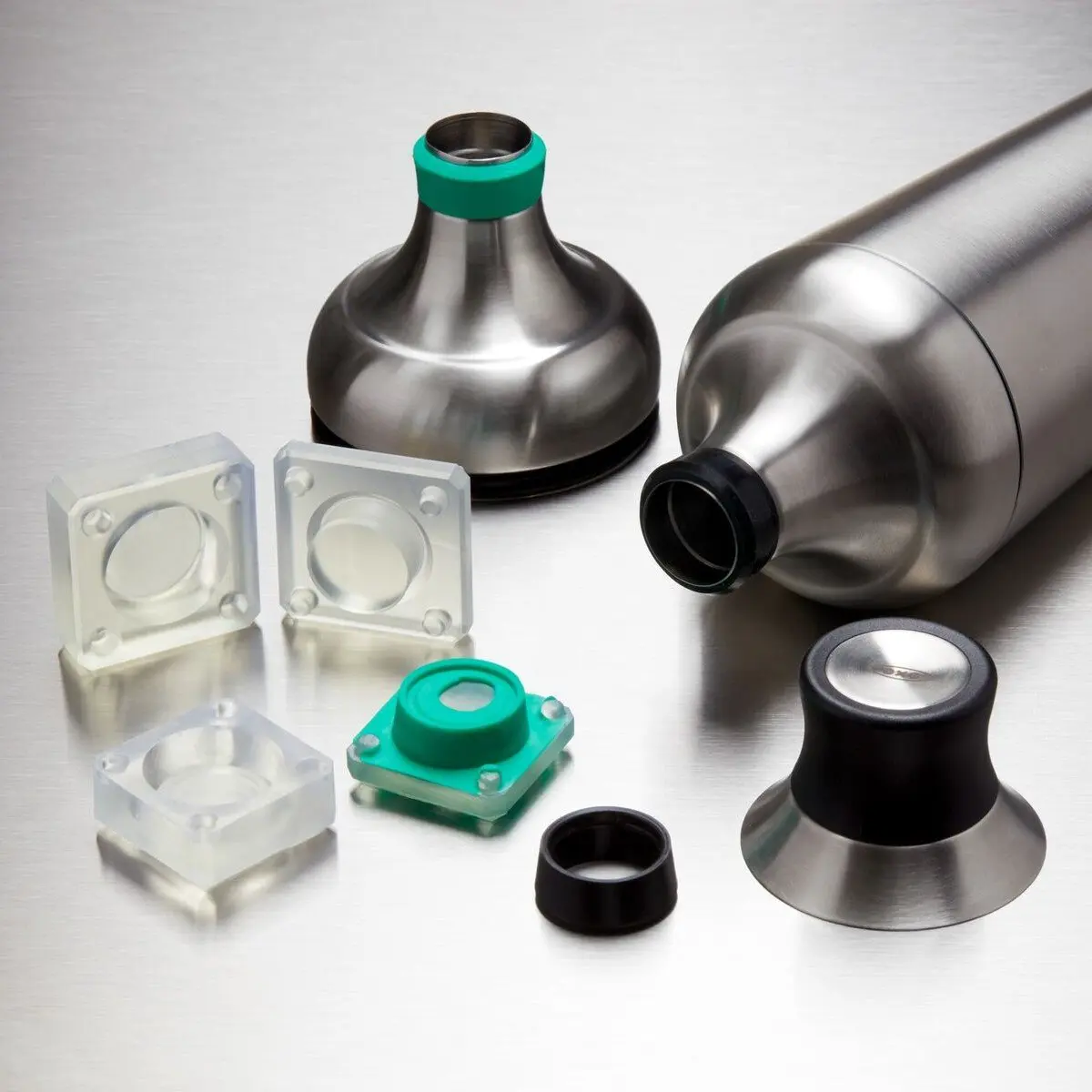
Production de pièces en silicone avec des outils imprimés en 3D
Téléchargez ce rapport et suivez le guide étape par étape sur l'impression 3D d'outillage pour la production de pièces en silicone, avec des meilleures pratiques pour la conception des moules et des études de cas.
Qu’est-ce que le moulage par compression ?
Le moulage par compression est un procédé de fabrication lors duquel une quantité précise de matériau à mouler généralement préchauffé (habituellement appelé la charge) est comprimée à l’aide de deux moules chauffés pour lui donner la forme désirée.
Comment fonctionne le moulage par compression ?
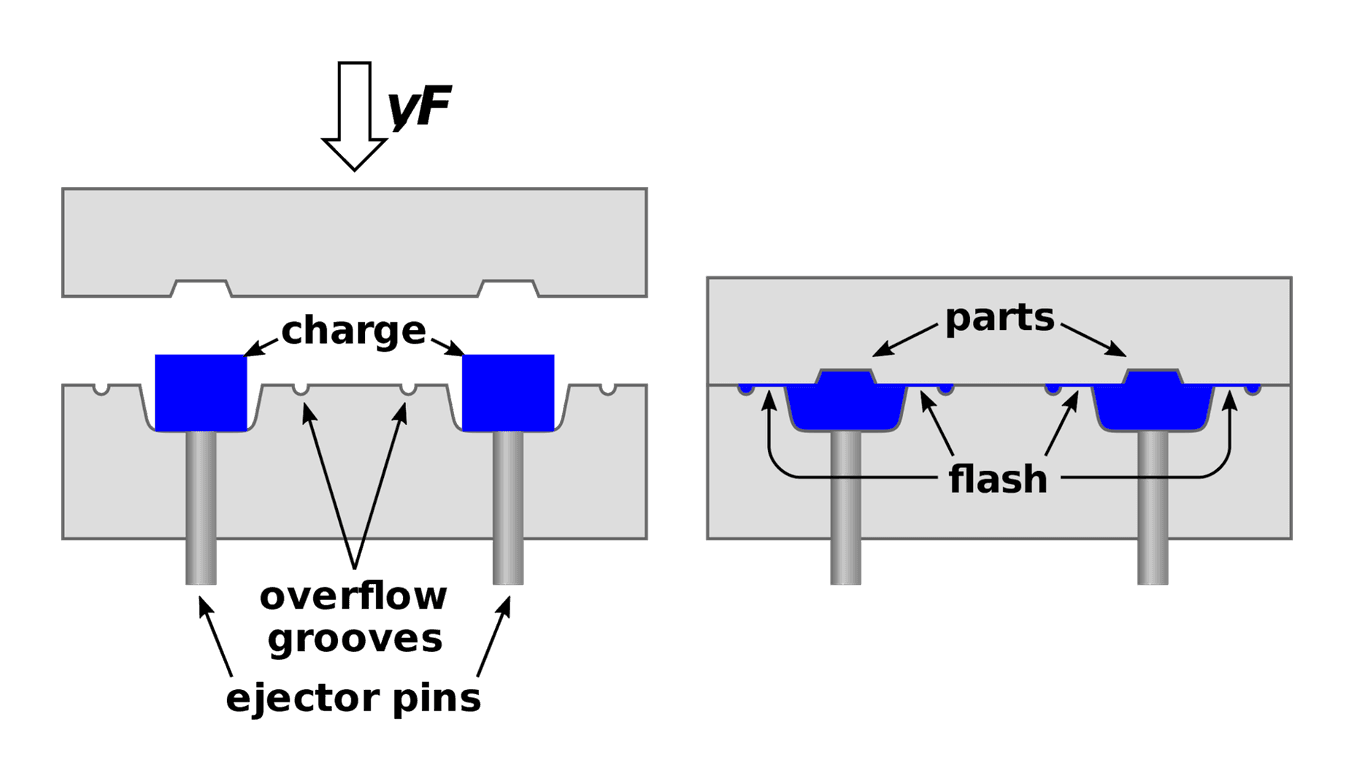
Un diagramme simplifié illustrant le procédé de moulage par compression. (source de l’image)
Les étapes successives du processus de moulage par compression sont les suivantes :
-
Création du moule : l’outillage peut être produit de plusieurs manières, dont l’usinage, le coulage sous pression ou l’impression 3D.
-
Préparation de la machine : en fonction de la machine ou de l’équipement utilisé, ceci peut inclure le nettoyage du moule, l’activation de la source de chaleur et d’autres procédés d’installation.
-
Préparation de la charge : sélectionnez le type de matériau désiré et mesurez la quantité de matériau nécessaire. Si la charge est trop importante, l’excès de matériau débordera du moule et formera une bavure qu’il faudra éliminer manuellement.
-
Insertion de la charge : placez la charge au centre du fond du moule.
-
Compression de la pièce : fermez le moule supérieur, appliquez une pression et attendez que la pièce se forme. De nombreux fabricants utilisent de la chaleur durant le processus de compression, ce qui ramollit la matière première et peut accélérer la production.
-
Démoulage de la pièce : séparez la pièce réalisée de son moule.
-
Nettoyage de la pièce : les bavures de résine autour des arêtes doivent être éliminées manuellement et la pièce peut devoir être nettoyée avant son assemblage final.
Moulage par compression ou Moulage par injection
Ces deux techniques de moulage sont très ressemblantes mais elles ont tout de même une différence de taille. Dans le moulage par compression, les moules viennent se refermer autour de la charge. Dans le moulage par injection, la charge est injectée dans la cavité formée par un moule déjà fermé.
De nos jours, les fabricants recourent fréquemment au moulage par compression et par injection, mais pour réaliser des types de pièce différents. Le moulage par injection est généralement un meilleur choix pour les pièces complexes, alors que le moulage par compression est une excellente solution pour les modèles relativement simples, dont les formes basiques de très grande taille qui ne peuvent être produites par filage.
Le moulage par injection comporte une durée de cycle plus courte que le moulage par compression, il est donc plus rapide et plus rentable quand il s’agit de produire un grand nombre de pièces. Cependant, le moulage par compression est une méthode de production à basse pression, ce qui implique un coût d’outillage souvent plus faible. La quantité de matière gaspillée est aussi très faible lors de la compression, ce qui représente un avantage quand on met en œuvre des matériaux onéreux.
En règle générale, le moulage par injection est plus adapté aux volumes de production élevés, alors que le moulage par compression se justifie plus pour les productions en petite à moyenne série.
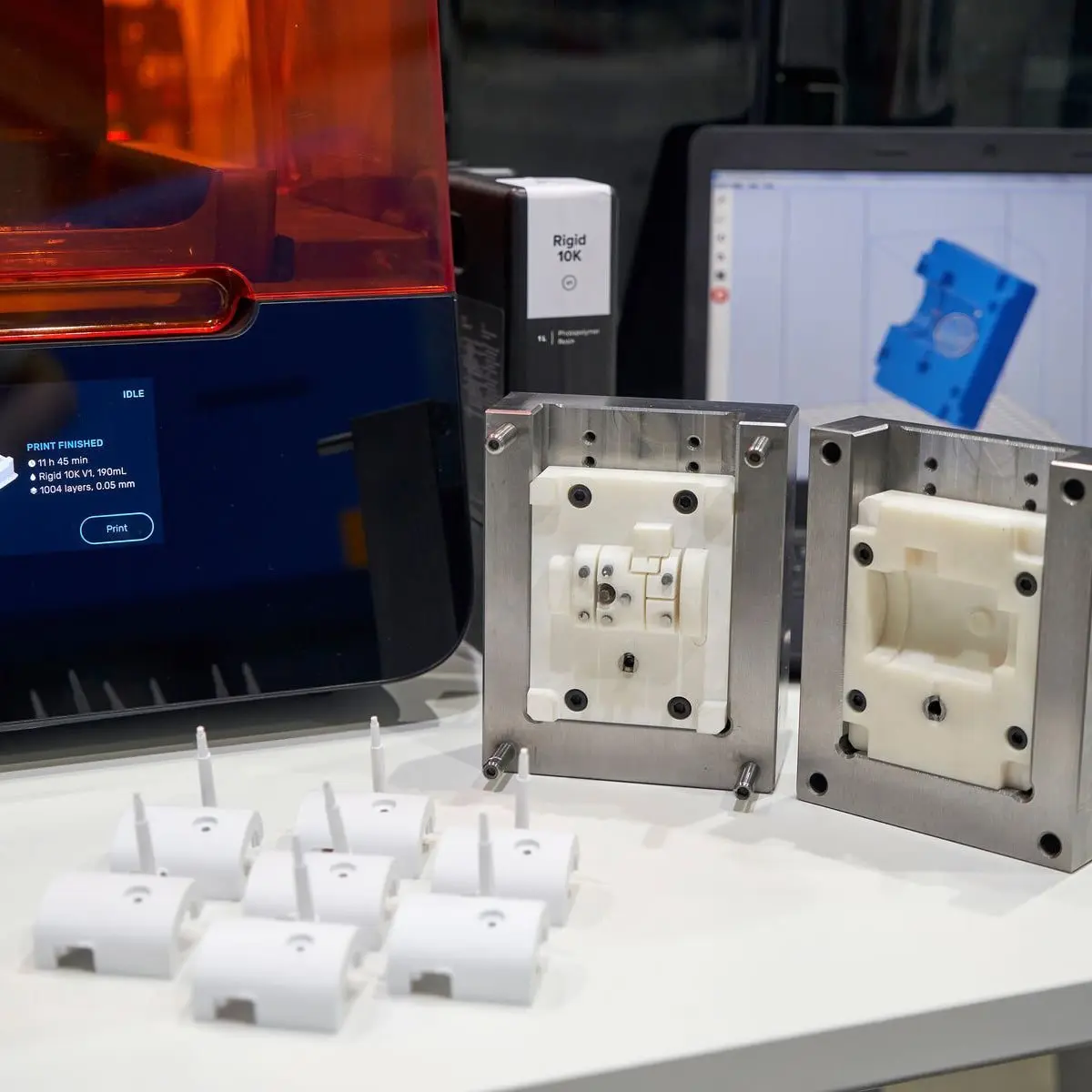
Le moulage par injection rapide de petites séries avec des moules imprimés en 3D
Téléchargez ce livre blanc pour savoir comment utiliser des moules imprimés en 3D pour le processus de moulage par injection, et ainsi réduire les coûts et les délais de production. Vous y trouverez des études de cas réels, réalisées chez Braskem, Holimaker et Novus Applications.
Les avantages et les inconvénients du moulage par compression
Maintenant que nous avons exposé les différences entre le moulage par compression et le moulage par injection, penchons-nous sur les avantages et les limites spécifiques au procédé de fabrication qui nous intéresse.
La rentabilité
Le moulage par compression est souvent le procédé de fabrication le plus rentable quand il s’agit de produire des pièces simples de grande taille et généralement planes. Le modèle peut comporter des courbures et des structures creuses dans une certaine mesure, mais les angles aigus et les nervures profondes peuvent être difficilement réalisables avec le moulage par compression. En raison des faibles pressions appliquées, les coûts d’outillage sont raisonnables et les moules disposent généralement d’une bonne longévité avant de se déformer ou de devoir être remplacés. Pour compenser le coût généré par la durée de cycle importante du moulage par compression, les fabricants peuvent utiliser un moule à cavités multiples pour produire plusieurs pièces en un seul cycle.
La solidité des pièces produites
Le moulage par compression produit des pièces solides dépourvues de soufflures et de plan de joint. La stabilité structurelle des pièces moulées par compression est très élevée. Le moulage par compression est aussi utilisé pour fabriquer des pièces en matériaux composites, ce qui veut dire que des pièces et des produits durables et résistants à la corrosion peuvent facilement être obtenus grâce à cette méthode.
La souplesse de conception
Le moulage par compression est aussi un excellent outil de fabrication pour les ingénieurs et les développeurs de produits. Par exemple, le prototypage peut être effectué à moindres frais grâce au moulage par compression. Les moules à compression de forme simple peuvent être conçus avec un logiciel CAO, imprimés en 3D, puis servir à former divers types de matériaux à l’aide d’un simple étau d’établi. Au cours de cette publication, vous découvrirez par exemple comment OXO réalise son prototypage.
Les limites
Même si le moulage par compression comporte de nombreux avantages, il a aussi ses limites. Il ne se prête pas bien à la fabrication de pièces complexes telles que celles comprenant des angles très aigus ou de très petits détails. La durée de cycle, qui peut être de plusieurs minutes, est longue par rapport aux méthodes de moulage à volume élevé. Le moulage par injection, par exemple, comporte souvent une durée de cycle d’à peine quelques secondes.
Le coût en main-d’œuvre associé au moulage par compression peut aussi être relativement élevé en raison de l’importante durée de cycle qui entraîne une augmentation des heures travaillées. Les jets et les bavures présents sur les pièces moulées par compression doivent être éliminés manuellement, ce qui prend plus de temps et génère du rebut. Toutes ces limites mises à part, le moulage par compression reste une méthode de fabrication importante utilisée dans la fabrication d’une vaste gamme de produits que nous utilisons au quotidien.
Les applications du moulage par compression
Le moulage par compression se prête à une foule d’applications. Voici quelques-uns des nombreux produits contenant des pièces moulées par compression avec lesquels nous interagissons tous les jours :
-
Pièces de véhicule : de nombreuses pièces volumineuses comme des panneaux pour voiture, tracteurs et autres véhicules sont moulées par compression. Bien des pièces en plastique présentes dans l’habitacle ou dans le compartiment moteur des véhicules peuvent aussi être moulées par compression.
-
Périphériques de jeu et d’ordinateur : des composants pour manettes de jeu vidéo, claviers et autres peuvent être moulés par compression.
-
Matériel de cuisine : de nombreux articles de cuisine, ustensiles et appareils électroménagers comportent des pièces qui sont moulées par injection. Les pièces de vaisselle telles que les bols, les tasses, les assiettes et autres sont souvent fabriquées grâce au moulage par compression, surtout quand elles sont faites en mélamine.
-
Composants électriques : le moulage par compression intervient souvent dans la fabrication des prises électriques, interrupteurs, façades et appareils de mesure.
-
Pièces pour dispositifs médicaux et dentaires : de nombreuses pièces en plastique et en silicone utilisées dans le secteur médical sont moulées par compression, dont les bouchons de seringue et les respirateurs.
Ustensiles de cuisine fabriqués à l’aide du moulage par compression.
Types de machines de moulage par compression
La taille des machines de moulage par compression va des machines industrielles de grande taille aux petites machines faites maison. Tout comme les pièces qu’elles produisent, les machines de moulage par compression sont aussi variées que les ingénieurs et les concepteurs qui les créent. Regardons quelques exemples de cette diversité dans la prochaine section.
Machines de moulage par compression hydraulique industrielles
Les énormes machines industrielles de moulage par compression se prêtent le mieux à la productions de pièces commerciales volumineuses.
Des systèmes de levage hydraulique permettent d’obtenir un haut niveau de pression pour la production et la fabrication de pièces volumineuses et uniformes pendant que l’opérateur supervise le processus sur un panneau de contrôle séparé.
Presses d’atelier
Des machines de compression d’atelier plus petites sont idéales pour la fabrication de pièces et de produits de petite à moyenne taille. Les presses d’atelier Beckwood ont une empreinte au sol plus faible que les grandes machines de compression industrielles, mais conviennent toutefois à la production en grande série. Plusieurs points d’accès offrent une flexibilité aux ingénieurs pour en extraire facilement les pièces moulées et éliminer les jets, et leur encombrement réduit facilite leur intégration dans des entrepôts ou locaux de production de petite taille.
Machines de moulage par compression à froid (sans chaleur)
Pour rappel, le moulage par compression peut être réalisé avec ou sans apport de chaleur. Ceci s’applique à toutes les tailles de machine de moulage par compression. Certains fabricants utilisent même une machine de compression à froid, mais chauffent la charge ou la matière première avant de la placer dans le moule. On peut contrôler la manière dont un produit fini se polymérise et raccourcir les cycles de production en apportant de la chaleur à des moments spécifiques.
Machines de moulage par compression par voie humide
Les machines de moulage par compression par voie humide sont utilisées pour imprégner un canevas solide de résine, d’époxy et d’autres substances liquides.
La compression par voie humide est devenue un procédé de fabrication courant pour réaliser des pièces et des composants de voiture résistants. BMW et d’autres grands groupes ont intégré des machines de moulage par compression par voie humide dans leurs lignes de production.
Appareils de moulage par compression faits maison
Le moulage par compression est aussi un outil parfait pour les concepteurs travaillant de chez eux et les bricoleurs. Des matériaux souples tels que l’uréthane peuvent être moulés par compression en appliquant une pression relativement faible. Même des moules complexes peuvent être fabriqués facilement à l’aide d’une imprimante 3D et d’un logiciel CAO. Pour bien des petits projets, la compression nécessaire peut être atteinte à l’aide d’un simple étau d’établi ou par un système de leviers.
Matériaux pour le moulage par compression
Les thermoplastiques ainsi que les plastiques thermodurcissables sont compatibles avec le moulage par compression. Les matériaux thermoplastiques sont des types de plastique qui deviennent souples et pliables quand ils sont chauffés, et qui durcissent quand ils sont refroidis. Les thermoplastiques peuvent être chauffés et refroidis (ou reformés) de nombreuses fois.
Les matériaux thermodurcissables, pour leur part, comprennent les plastiques et autres polymères dont la polymérisation est irréversible quand ils sont exposés à la chaleur, ce qui veut dire qu’ils ne peuvent être moulés ou formés qu’une fois. Le procédé de moulage par compression provoque des modifications au niveau chimique des plastiques thermodurcissables qui ne peuvent être ni annulées, ni répétées.
Voici les matériaux les plus couramment utilisés pour le moulage par compression :
-
Phthalate de diallyle (DAP)
-
Époxy
-
Polyéthylène haute densité (PEHD)
-
Mélamine
-
Polyamides et polyimides (PA et PI)
-
Polyétheréthercétone (PEEK)
-
Polyuréthane (PU)
-
Polysulfure de phénylène (PPS)
-
Phénoplastes (PF)
-
Polytétrafluoroéthylène (PTFE)
-
Silicone
-
Urée-formaldéhyde (UF)
-
Uréthane
Comment créer des moules pour le moulage par compression
En fonction du matériau ou de la charge à mouler par compression, plusieurs choix sont possibles pour créer le moule. La clé du processus est que le moule doit pouvoir résister au processus de moulage par compression, donc s’il y a un apport de chaleur, il faudra créer des moules capables de subir des changements de température abrupts. Les moules devront aussi pouvoir résister à la pression appliquée lors de la compression.
Coulage sous pression
Parmi d’autres méthodes de fabrication, le coulage sous pression est l’une des méthodes les plus courantes pour créer des moules destinés au moulage par compression. Le coulage sous pression reste l’un des meilleurs choix car il produit des pièces métalliques solides à un coût plus avantageux que les autres méthodes de fabrication. Il est à noter que les matrices pour le coulage sous pression sont souvent usinées par CNC et ces deux méthodes de fabrication vont souvent de pair.
Usinage CNC
L’usinage CNC est un choix optimal pour des moules de compression plus détaillés. La composante informatique de l’usinage CNC donne aux ingénieurs plus de contrôle sur la conception. Cependant, la création de l’outillage pour cette méthode peut coûter cher. Certains fabricants recourent à une combinaison de coulage sous pression suivie d’un usinage CNC pour produire des moules de manière plus rentable.
Impression 3D
L’outillage pour le moulage par compression peut aussi être réalisé par impression 3D. S’il faut prototyper des pièces de petite taille, l’impression 3D peut devenir la méthode la plus rapide et la moins onéreuse pour créer les moules. Plusieurs itérations peuvent être réalisées rapidement avec un logiciel CAO, réimprimées, puis testées. L'impression 3D est le plus souvent utilisée pour les moules de compression destinés à des applications sans chaleur.
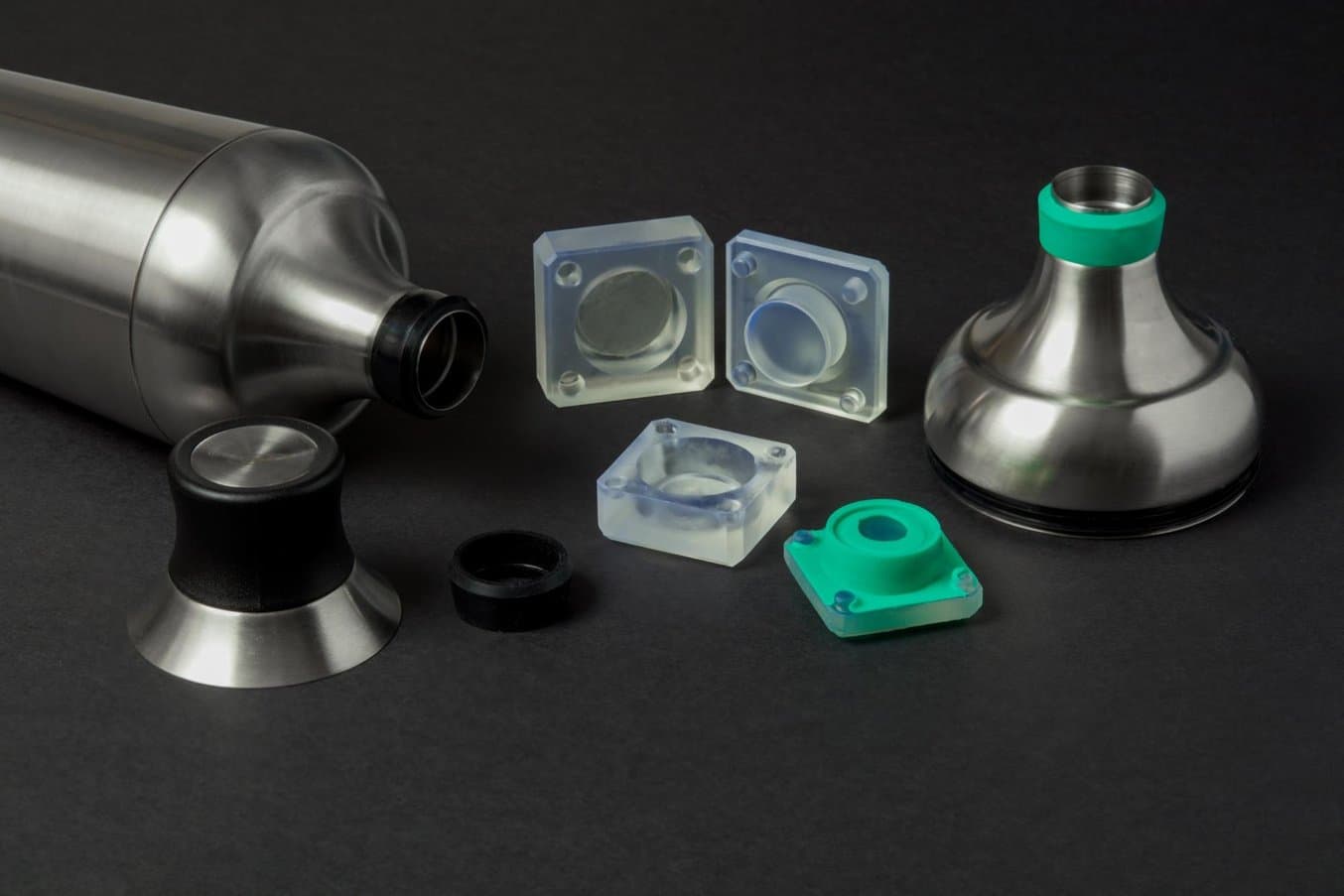
L’impression 3D est une méthode rapide et bon marché pour créer des moules destinés au moulage par compression.
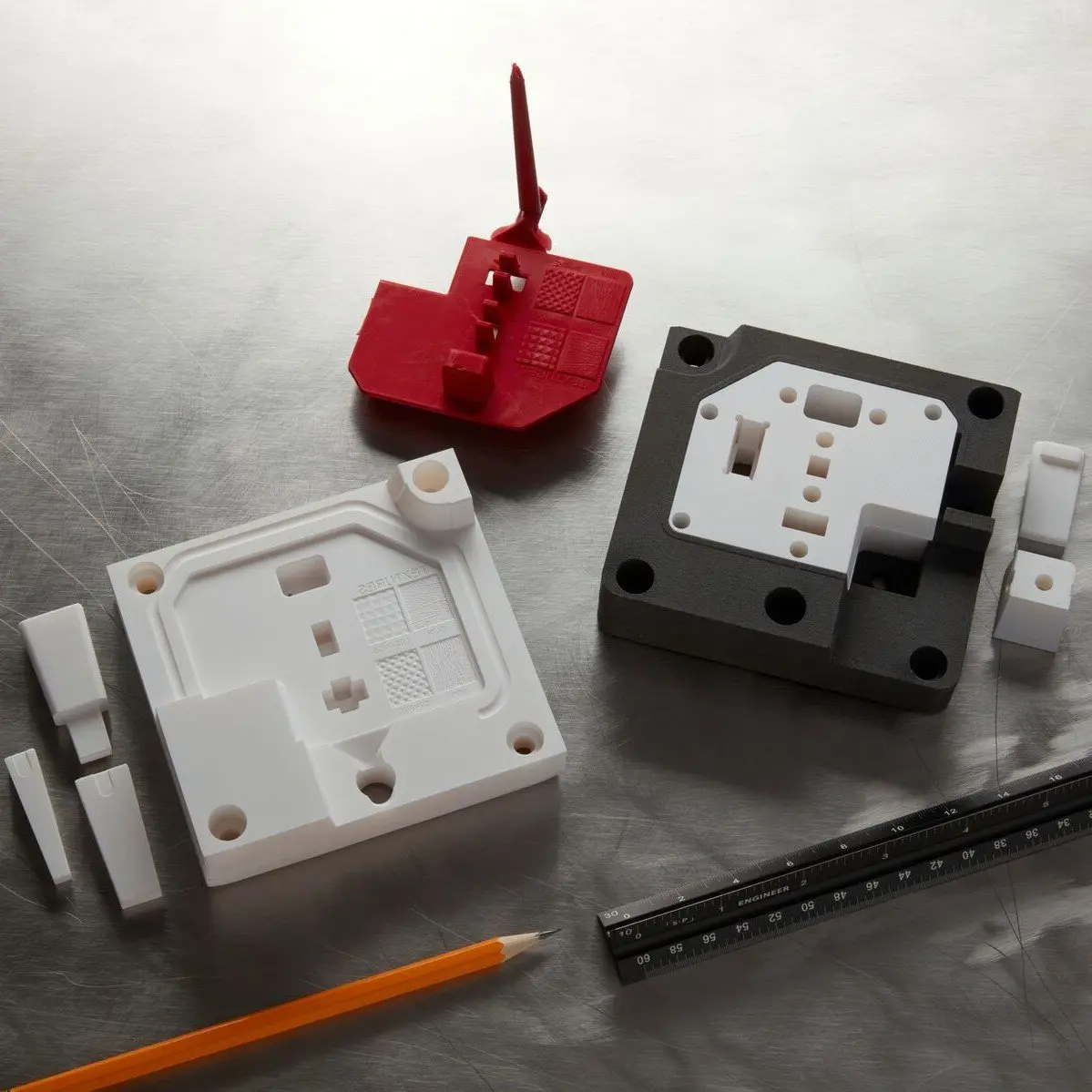
Guide de l'outillage rapide
Dans ce livre blanc, apprenez comment combiner l'outillage rapide imprimé en 3D avec des procédés de fabrication traditionnels tels que le moulage par injection, le formage sous vide ou la fonderie.
Comment OXO a utilisé le moulage par compression pour son prototypage
Basée aux États-Unis, OXO créé des objets pratiques et ergonomiques pour la vie quotidienne, notamment des ustensiles de cuisine devenus emblématiques. Leurs concepteurs de produits utilisent l’impression 3D par stéréolithographie pour évaluer la forme et la fonctionnalité des prototypes, mais des méthodes hybrides sont essentielles pour créer les parties souples, comme les joints.
Les ingénieurs d’OXO devaient fournir un prototype fonctionnel de joint de shaker avec un sceau étanche entre les pièces. Après de nombreux essais avec les différents silicones disponibles, ils ont estimé que le moulage par compression de la pâte silicone en deux produits Castaldo Quick-Sil était idéale pour créer un prototype étanche simulant les caractéristiques du joint industriel. En fait, le moule de compression du prototype était lui-même une bonne représentation de la conception des moules et des méthodes utilisées dans la production industrielle de joints.
Les ingénieurs d’OXO ont utilisé leur imprimante 3D SLA Formlabs pour créer leurs moules avec Clear Resin. Une fois les moules lavés et polymérisés, ils ont été préparés pour le moulage par compression. Un agent démoulant a été appliqué sur les surfaces internes. Ensuite, la pâte silicone a été préparée et placée dans le fond du moule.

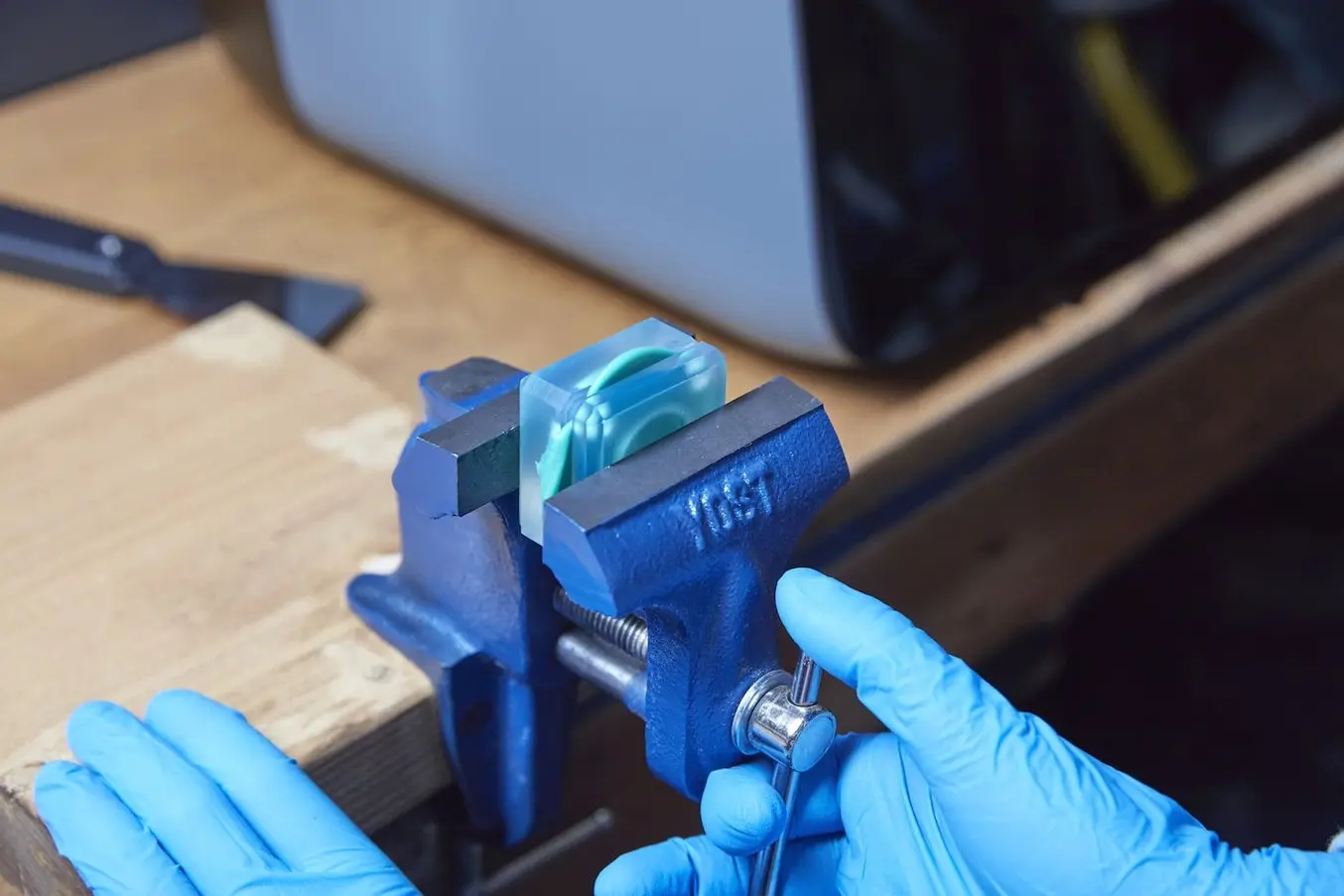
À gauche : Le composé silicone est placé dans le moule imprimé en 3D. À droite : Le moule est comprimé à l’aide d’un étau d’établi.
Ensuite, le moule supérieur a été mis en place et les ingénieurs ont pu appliquer le niveau de pression désiré en comprimant les deux moules dans un étau d’établi. La pièce ayant été complètement polymérisée, elle a été retirée du moule et ébavurée. Libre à vous d’adapter ce processus à vos propres fins à l’aide du guide étape par étape de notre livre blanc.
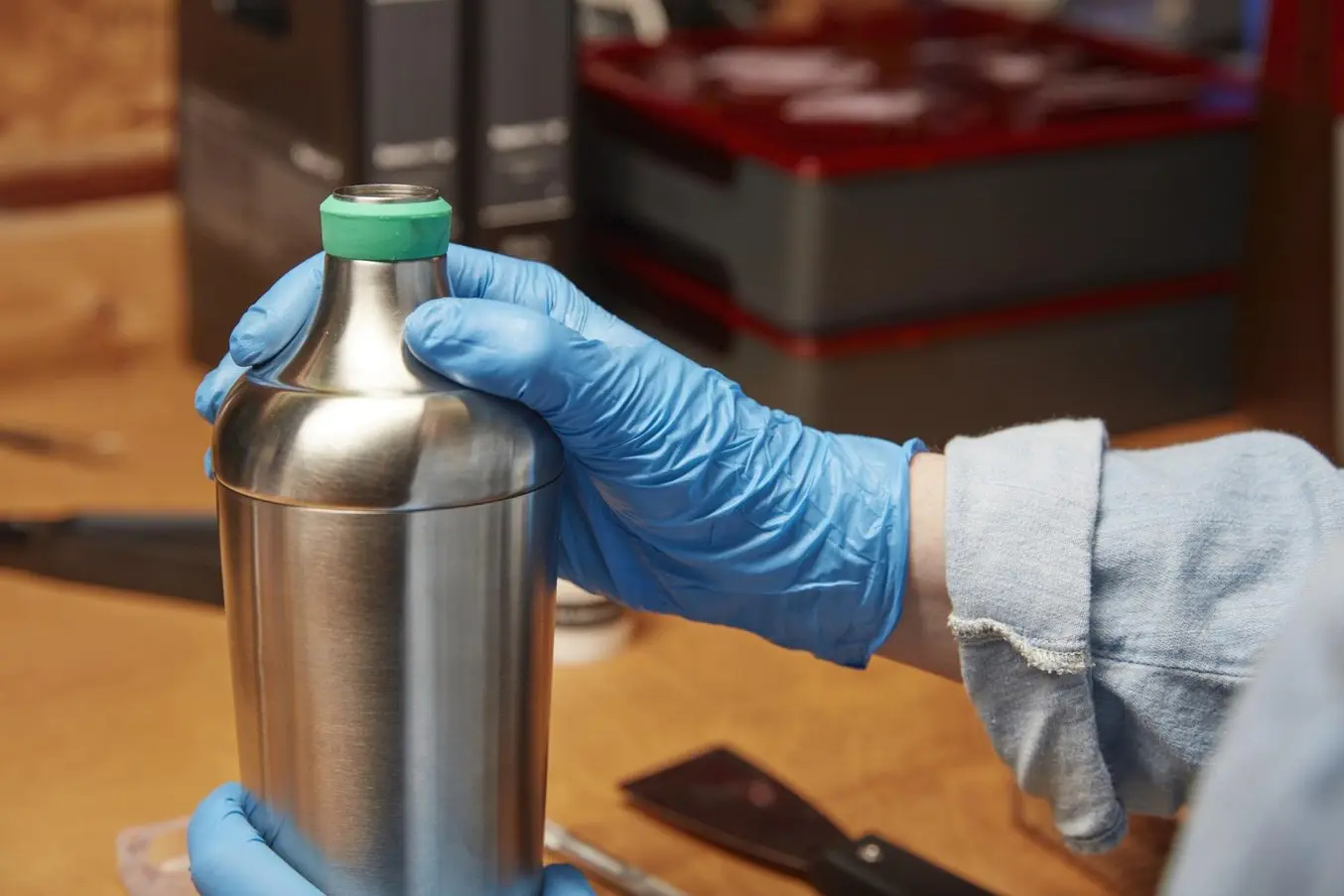
Le prototype fonctionnel final du joint de shaker.
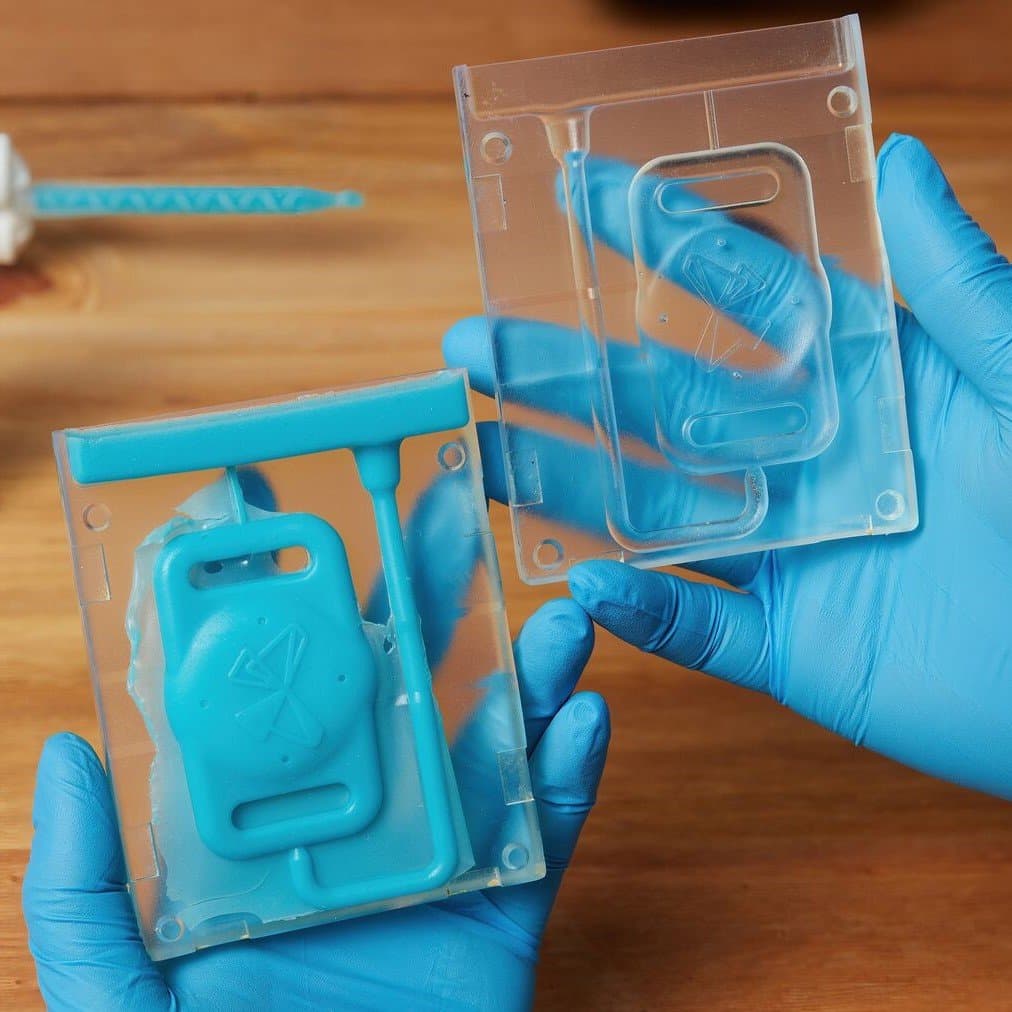
Comment produire des pièces en silicone avec des outils imprimés en 3D
Dans ce webinaire, vous découvrirez un exemple détaillé de surmoule d'injection imprimé avec Clear Resin de Formlabs. Nous abordons également la manière de sélectionner un type de moule pour votre application, ainsi que la compatibilité silicone-résine et d'autres bonnes pratiques en matière de moulage de silicone.
Le moulage par compression, le moulage par injection, le formage sous vide et le moulage du silicone par impression 3D
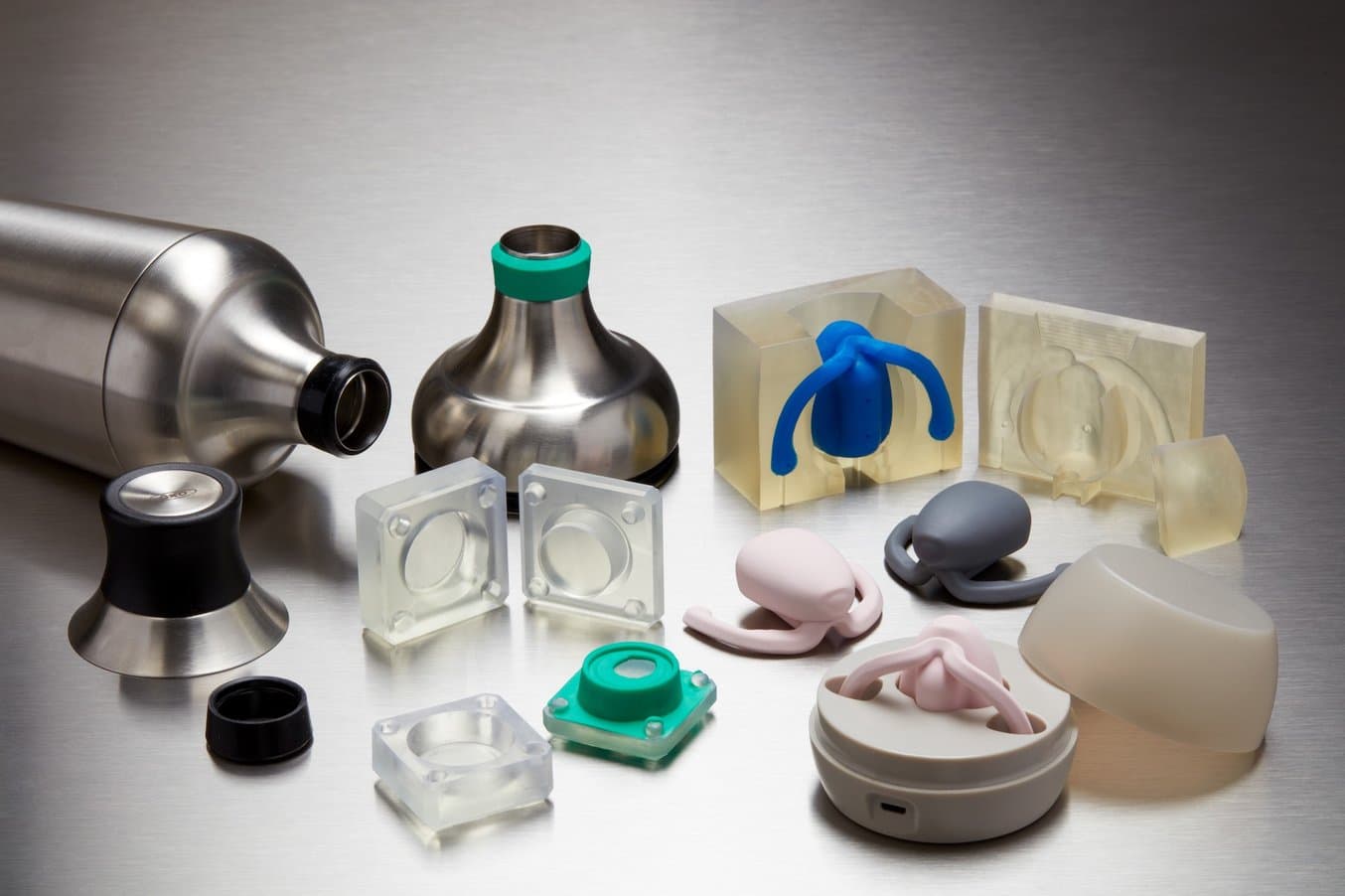
Si vous êtes intéressé par le processus de travail étape par étape pour créer des moules par impression 3D, regardez nos webinaires de formation gratuits et téléchargez gratuitement nos livres blancs :
-
Regardez notre webinaire pour obtenir les bases de la conception de moule et apprendre comment elles s’appliquent aux moules imprimés en 3D, ainsi que découvrir des exemples concrets de moulage de prototype et de moules imprimés en 3D actuellement en production.
-
Téléchargez notre livre blanc et suivez le guide étape par étape sur l'impression 3D d'outillage pour la production de pièces en silicone, avec des meilleures pratiques pour la conception des moules et des études de cas.
-
Téléchargez notre livre blanc pour découvrir trois stratégies de réalisation de moules pour le prototypage et la production : le moulage par injection, le thermoformage et le coulage d’élastomères.