Optimisation des pièces, des processus et des produits grâce à la fabrication additive
La production justifie l'optimisation, mais le chemin pour y parvenir dépend grandement du contexte et des objectifs. Dans cet article, nous examinons les contextes dans lesquels les fabricants et les ingénieurs utilisent la fabrication additive et les techniques qu'ils emploient dans plusieurs domaines.
Se pose tout d'abord la question de ce qu'il faut optimiser. De façon générale, un ingénieur ou un fabricant peuvent considérer l'optimisation à trois niveaux :
- Au niveau de la pièce
- Au niveau du processus
- Au niveau du produit
Les points à considérer sont évidemment différents pour chacun de ces niveaux, mais les calculs d'optimisation reposent tous sur le même ensemble de ressources : le temps, les matériaux, la main d'œuvre et la qualité. Ce sont ces facteurs essentiels qui conditionnent le coût et déterminent les marges relatives à une pièce, un processus ou un produit.
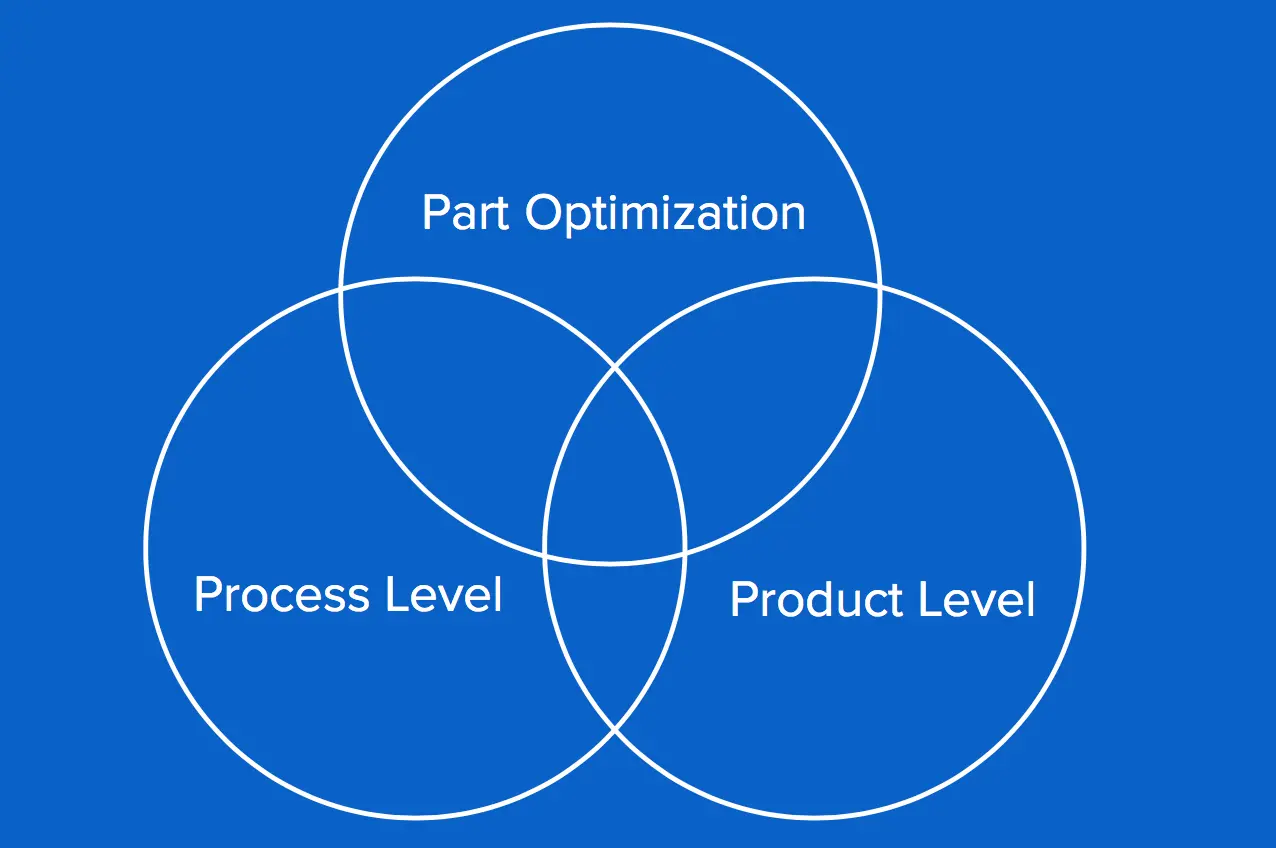
Optimisation au niveau de la pièce
L'optimisation au niveau de la pièce est certainement la plus familière aux ingénieurs : comment développer une forme de pièce qui satisfasse les exigences de conception et de performances, tout en minimisant le temps et le coût de la fabrication d'une telle pièce ? Les autres critères d'optimisation de la pièce sont souvent la facilité d'entretien et d'assemblage, la réduction du poids et la durabilité sous les contraintes et les déformations.
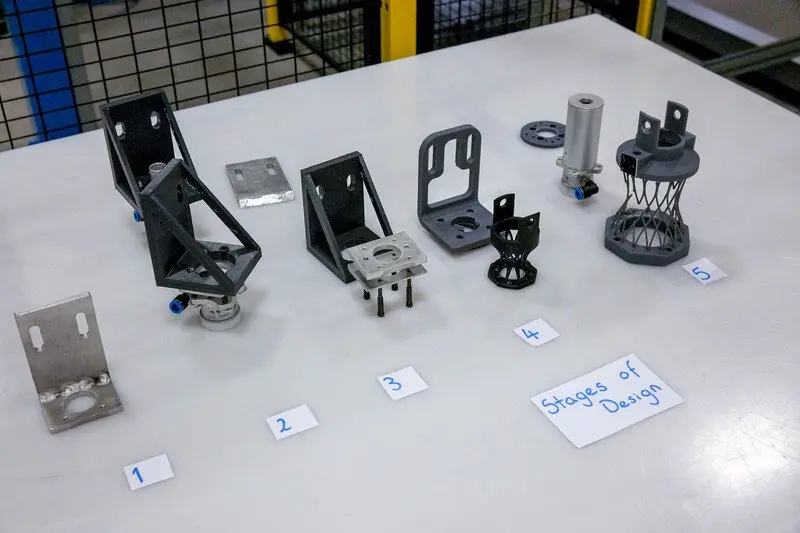
Le processus d'optimisation d'une pièce de fixation d'une pince robotique à ARMC a comporté cinq étapes.
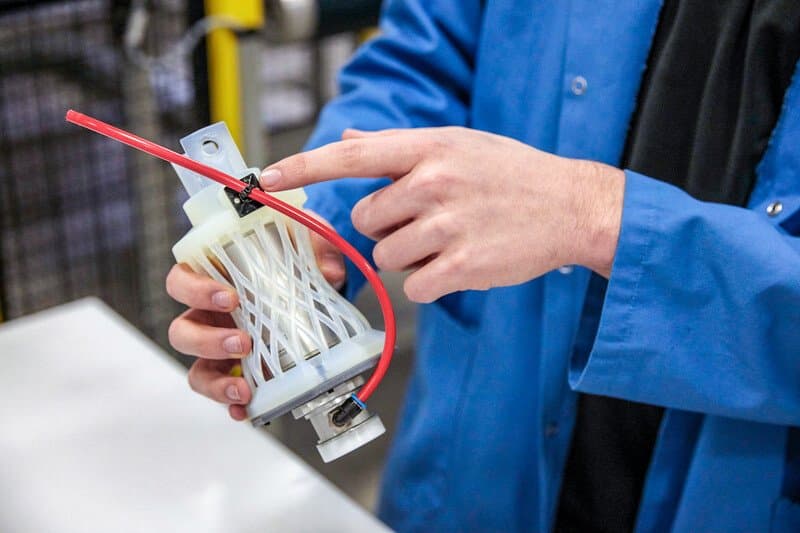
Cette pièce a finalement été produite par impression 3D par stéréolithographie (SLA).
Cet exemple d'attache d'une pince robotique d'AMRC illustre parfaitement l'optimisation au niveau d'une pièce. Les ingénieurs ont étudié les matériaux disponibles et les contraintes imposées par le processus de fabrication par impression 3D pour concevoir une pièce qui optimise à la fois son usage et sa fabricabilité.
En ce qui concerne les pièces en polymères, la fabrication additive permet de nouvelles formes et des gains de fonctionnalité et d'efficacité du matériau.
Conception en vue de la conformité et des exigences de poids et de flexibilité
Les structures en treillis sont courantes pour des pièces imprimées en 3D, et il y a une bonne raison à cela. Contrairement aux processus de moulage ou d'usinage, il est très simple et rentable de fabriquer des pièces avec des éléments négatifs, tels que des trous, des fentes et des conduits de connexion, et, dans une large mesure, indépendamment de leurs dimensions et leur inclinaison. Ces éléments négatifs réduisent la quantité requise de matériau pour la pièce et le temps de fabrication. De plus, ils maintiennent l'intégrité structurelle et les performances de la pièce, voire même les renforcent.
Pour les matériaux flexible ou semi-rigides, les structures en treillis peuvent améliorer la capacité de la pièce à absorber les contraintes et les déformations, sur des plages étendues d'angle et de pression, dépassant les exigences de conformité lorsqu'il le faut, et présentant une résistance à la compression ou à la flexion sur d'autres zones.
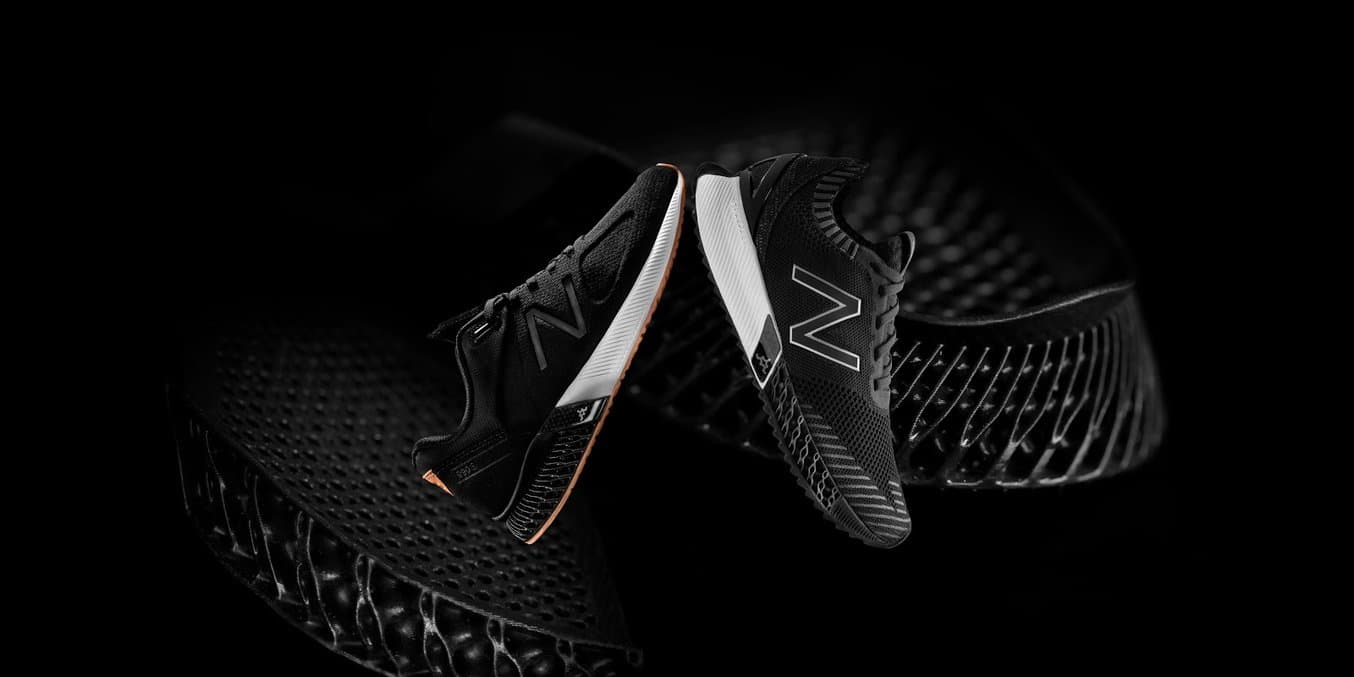
Deux produits récemment lancés par New Balance utilisent cette structure en treillis imprimée en 3D pour l'absorption des chocs avec retour élastique, pour une quantité de matériau et un poids moindres que ceux d'un produit fabriqué traditionnellement.
Optimisation au niveau du processus
L'optimisation au niveau du processus concerne moins les spécificités d'une pièce donnée, mais plutôt la façon dont le travail quotidien peut être amélioré en termes d'économie de coûts, de gain de temps ou pour favoriser le rendement et la qualité.
Un des domaines où l'impression 3D contribue à l'optimisation du processus est celui des porte-pièces, des fixations et des outils spéciaux pour des opérations de fabrication. Souvent les sociétés se servent d'imprimantes 3D en interne pour « re-verticaliser », c'est-à-dire remplacer les commandes coûteuses à des sous-traitants, les surcoûts dues aux commandes minimum et les délais entre l'atelier du sous-traitant et l'installation de ces pièces sur le lieu de production.
Internalisation / Re-verticalisation :
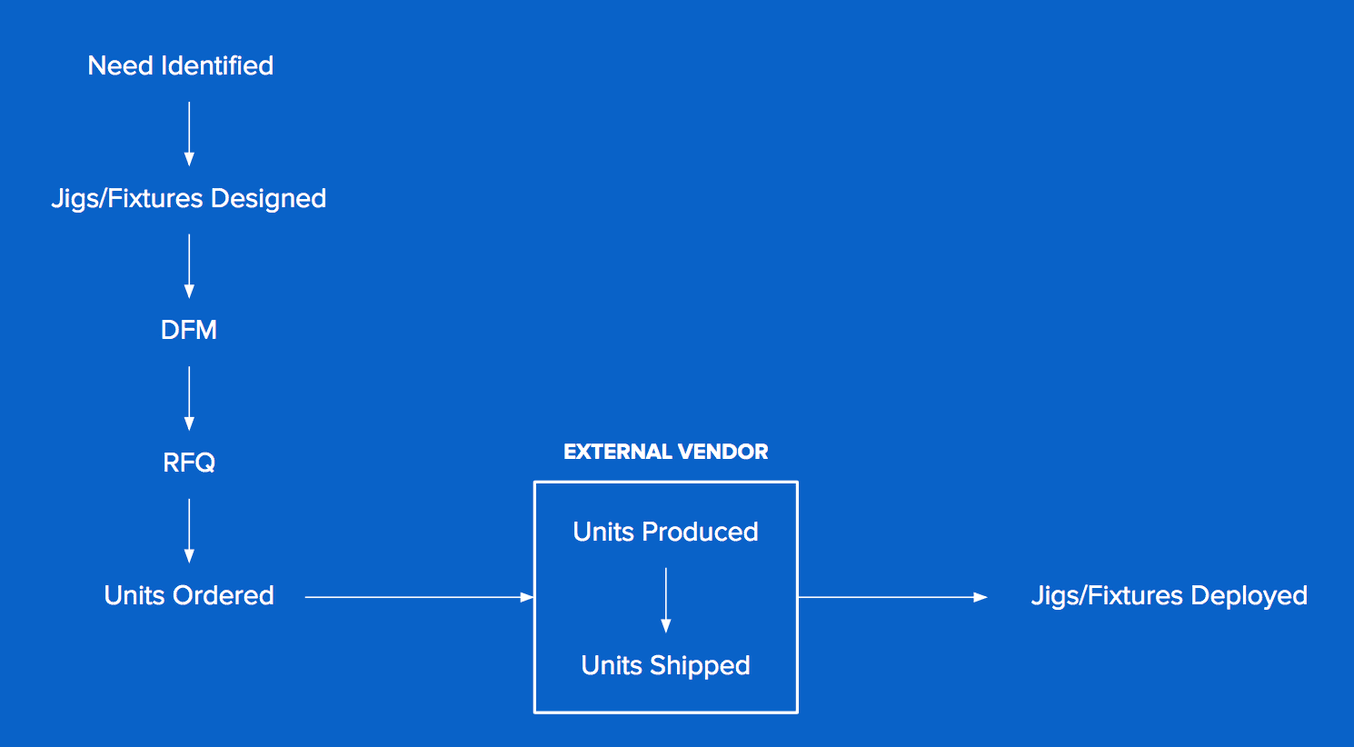
La sous-traitance d'un processus traditionnel de fabrication par usinage de porte-pièce et de fixation requiert une démarche de DFM (conception en vue de la fabrication). Il comporte souvent des minimum de quantité commandée pour qu'il soit rentable et des délais de fabrication se comptant en jours ou en semaines.
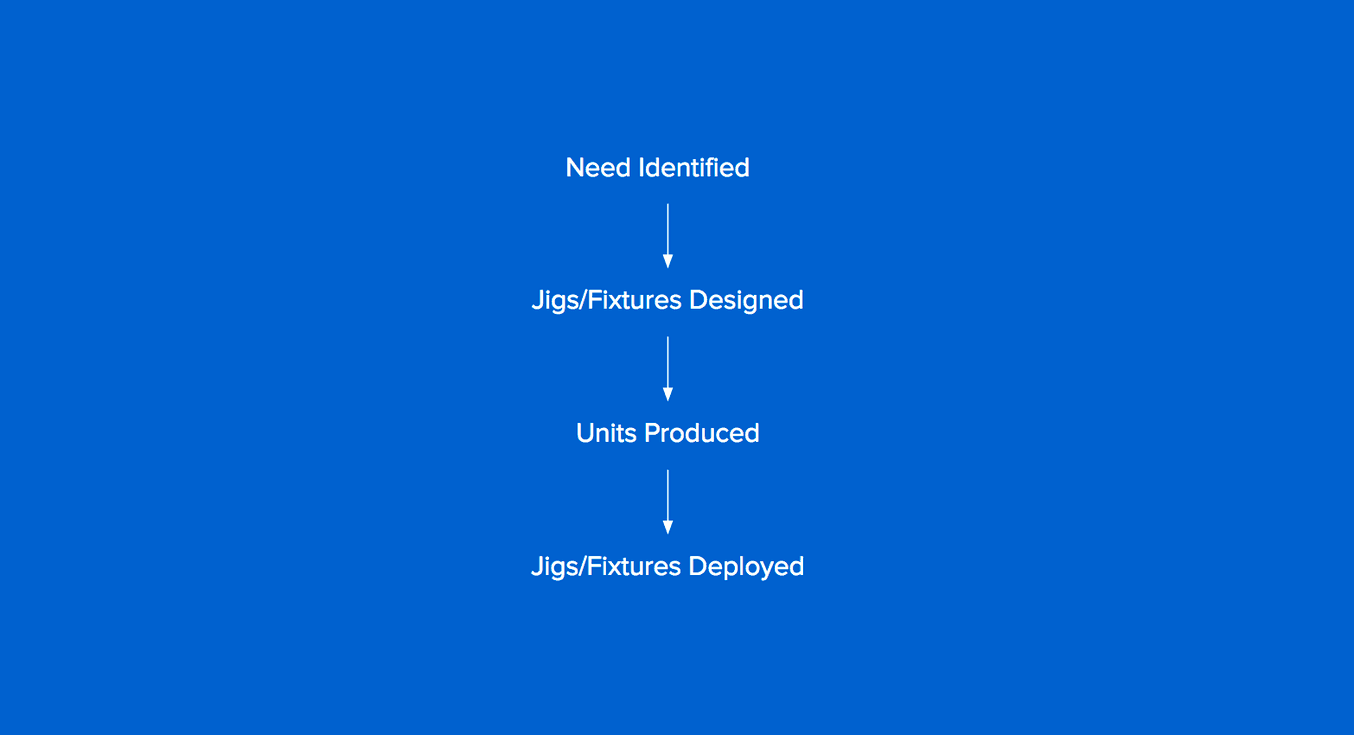
La fabrication additive permet un processus de production de porte-pièces et de fixations en interne et réduit grandement les étapes entre l'identification d'un besoin et la mise en place de la solution au niveau de l'usine.
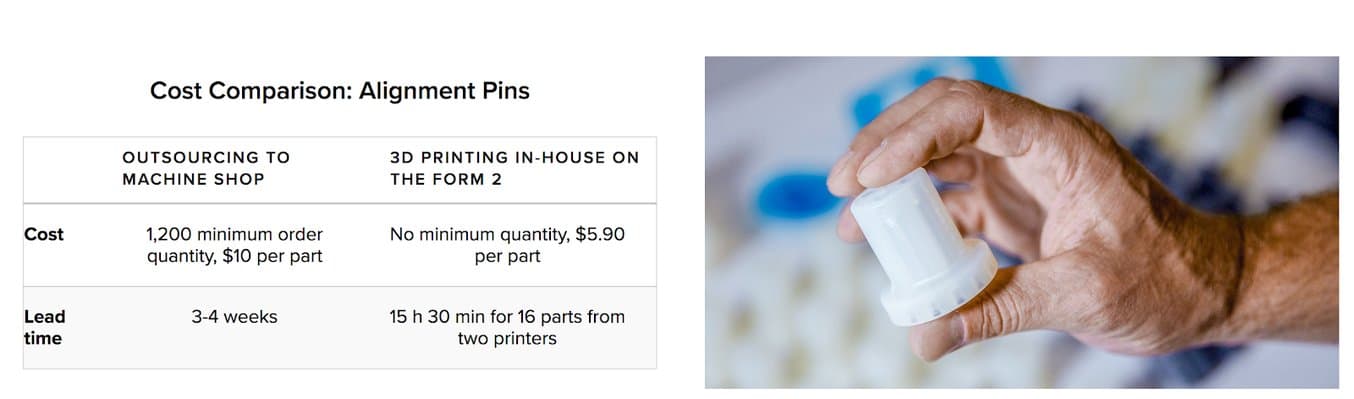
L'utilisation de l'impression 3D en interne pour la re-verticalisation a aidé Ashel Furnitures dans son usine de production d'étagères à gagner du temps et réduire les coûts sur la fabrication de porte-pièces, de fixations et d'outils, comme cette cheville d'alignement.
L'accessibilité conduit à l'innovation
Une optimisation majeure du processus de travail se produit lorsque des modifications d'un processus de plus bas niveau (comme l'internalisation de la fabrication de porte-pièces et de fixations) conduit à des expériences et déclenche des innovations qui auraient été difficiles à planifier, ce qui arrive pourtant fréquemment lorsque des techniques de fabrication automatisées comme l'impression 3D sont mises à disposition des ingénieurs.
Dans le passé, les imprimantes 3D de haute qualité étaient coûteuses et requéraient des techniciens qualifiés, c'est pourquoi la plupart des sociétés ont développé cette technique avec une approche top-down.
Approche top-down :
- Imprimantes 3D dans un centre local d'impression.
- Machines industrielles de grande capacité.
- Utilisées par des techniciens experts et dédiés qui conseillent sur l'introduction de l'impression 3D.
- Des projets complètement planifiés et autorisés avant leur démarrage.
- Dépenses en capital et coûts opérationnels élevés.
Le coût des imprimantes 3D ayant diminué et leur accessibilité s'étant accrue, une approche bottom-up de l'usage de cette technique a émergé.
Approche bottom-up :
- Des imprimantes 3D réparties dans toute l'entreprise.
- Des appareils de bureau, peu coûteux et accessibles.
- Mise en œuvre par les utilisateurs eux-mêmes, experts de leurs propres processus.
- Les projets sont menés comme des expériences à faible risques.
- Dépenses en capital et coûts opérationnels faibles.
- Changement culturel : les employés sont encouragés à innover au fur et à mesure de l'intégration de l'impression 3D.
« J’avais besoin d’appareils pour lesquels il soit facile de former les collègues et qui leur permettent de réussir, de sorte qu’ils aient envie de les réutiliser. Parmi les petites imprimantes SLA que j’ai utilisées, la Form 2 est la première qui m’a paru pouvoir changer la donne. La machine en elle-même est très facile d’utilisation, » explique Cocking. « Le logiciel est très intuitif, les ingénieurs le comprennent très rapidement. Il leur a été facile de comprendre les bases et à partir de là, ils ont appris par eux-mêmes et ont mené leurs propres expériences de fabrication additive. Nous avons actuellement un peu plus de 100 ingénieurs formés pour utiliser le parc de Form 2. »
L'Advanced Manufacturing Research Centre (AMRC) de l’université de Sheffield
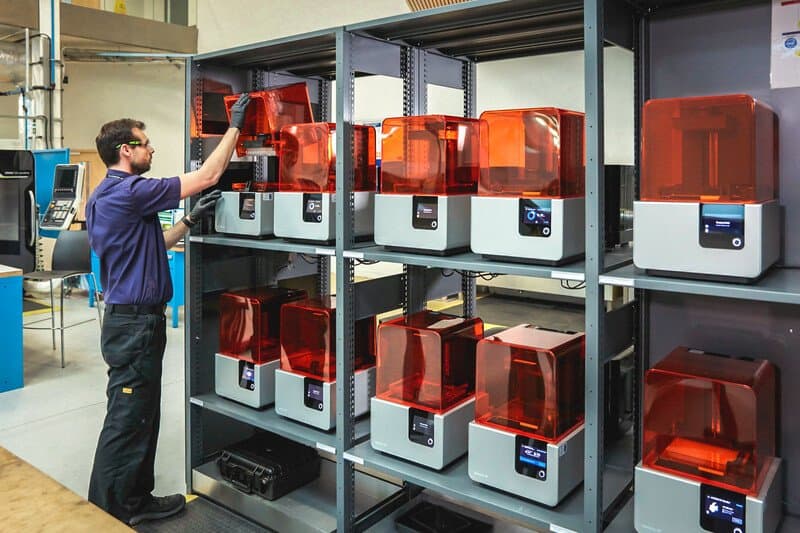
Plus de 100 ingénieurs de l'AMRC utilisent le parc de Form 2 de Formlabs.
Optimisation au niveau du produit
L'optimisation au niveau du produit diffère de celles du niveau pièce et processus parce qu'elle concerne plus souvent la mise en place ou le prototypage de nouveaux modèles commerciaux que la création de nouveaux produits.
L'impression 3D aide les sociétés à éliminer les risques liés aux nouveaux concepts comme la personnalisation de masse en supprimant les besoins d'outillage lourd, impliquant des coûts et des délais de production élevés. Avec l'impression directe, les sociétés sont libres d'essayer en permanence de nouvelles formes, de nouveaux mécanismes et de proposer des produits en matériaux solides qui conviennent à leur usage final.
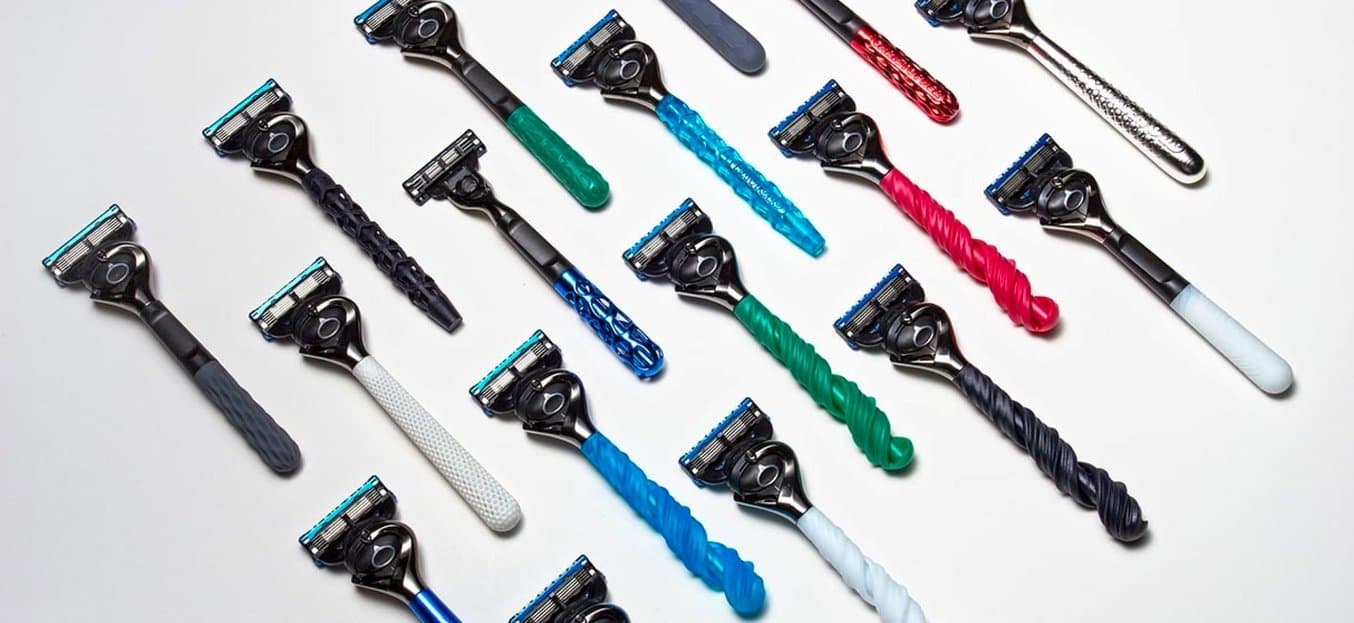
Par exemple, Gillette a utilisé l'impression 3D directe pour leur initiative Razor Maker, qui donne aux clients un large choix de combinaisons de couleurs et de motif pour leur rasoir et leur permet même de personnaliser le manche avec des noms. Produire rentablement des produits sur demande, même si le lot ne contient qu'une seule pièce, serait totalement impossible avec les techniques de fabrication traditionnelles.
Des efforts similaires de personnalisation ou de production sur mesure sont en cours dans le domaines des orthèses, des écouteurs et des composants automobiles. Dans tous ces exemples, les produits personnalisés ou sur mesure permettent d'optimiser l'adéquation d'un produit aux personnes, à leurs goûts ou à leurs caractéristiques physiques. Ainsi les marques peuvent proposer à leurs clients exactement ce qu'ils souhaitent et quand il le souhaitent.
Élargir accessibilité
Les techniques d'impression 3D sont disponibles depuis les années 80, mais les opportunités d'optimisation s'accroissent rapidement avec le développement par les sociétés de nouveaux matériaux, d'outils de calcul et de structures opérationnelles.
Les avancées en impression de haute résolution à bas coût rendent ces techniques abordables pour des entreprises de toute taille et réduisent l'écart entre le concept et sa mise en œuvre. Consultez cet article pour en savoir plus sur la dernière génération d'imprimante SLA et la capacité d'innovation que donne le procédé LFS aux ingénieurs chaque jour.
Demander un échantillon gratuit imprimé sur la Form 3