Optimisez vos projets en utilisant ensemble les technologies FDM et SLA
L'impression par dépôt de fil fondu (FDM) et la stéréolithographie (SLA) sont les deux procédés d'impression 3D les plus populaires sur le marché. Chaque procédé présente ses avantages et ses forces propres, avec des différences concernent la qualité d'impression, les matériaux, les applications, le processus de travail, la vitesse, les coûts, etc.
Un procédé peut être mieux adapté à la fabrication de certaines pièces que l'autre, en fonction de l'application. Pourquoi ne pas pas combiner les deux procédés pour obtenir le meilleur de chacun ?
Dans ce post, nous découvrons comment trois utilisateurs ont vu la complémentarité des procédés FDM et SLA et l'ont exploitée pour optimiser leurs projets.
Choisir entre niveau de détail et taille d'impression pour un modèle réduit de montagnes russes
Voilà presque dix ans que Matt Schmotzer joue avec l'impression 3D. Actuellement, il fabrique des montagnes russes miniatures. Il a déjà réalisé trois modèles qui fonctionnent parfaitement, avec les rails et des assemblages de trains très détaillés. Matt exploite les deux procédés FDM et SLA, en jouant sur les atouts de chacun pour créer finalement un modèle plus fonctionnel. Il a récemment emmené ses modèles pour les présenter aux étudiants d'écoles d'ingénieurs.
Les modèles les plus ambitieux de Matt comportent plus de 700 éléments de poutres. Les poutres internes sont plates et collées à un échafaudage en bois avec des colles de marque Loctite.Comme le niveau de détail des poutres n'est pas vraiment important, Matt a préféré imprimer rapidement la majorité d'entre elles par FDM. L'impression par FDM permet d'utiliser un nombre presque illimité de couleurs, libérant la créativité de Matt lors de l'assemblage final.
Les trains aussi posent des défis très spécifiques. Les modèles de trains sont imprimés sur des appareils SLA, parce que les petites pièces de 3,8 x 7,6 cm doivent être réalistes. Pour ces pièces, Matt a choisi Grey Pro Resin sur son imprimante Formlabs. Les imprimantes SLA excellent à la fabrication de pièces finies de grande qualité et les modèles de train doivent être aussi réalistes que possible, jusqu'aux minuscules poignées sur les portes.
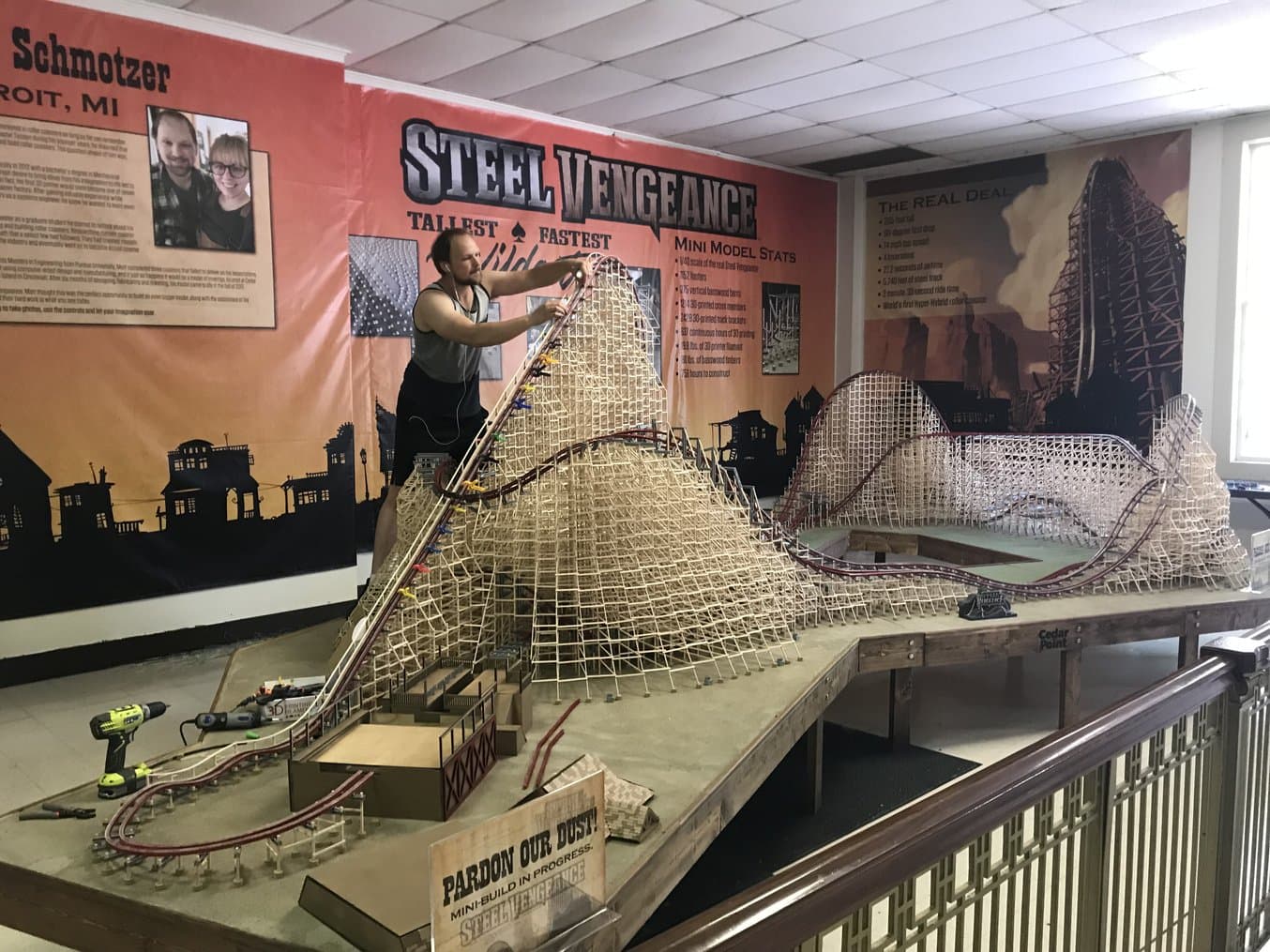
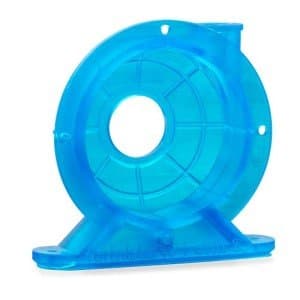
Demander un échantillon gratuit
Examinez et ressentez par vous-même la qualité Formlabs. Nous vous enverrons un échantillon gratuit imprimé en 3D.
Demander un échantillon gratuitUn prestataire de services d'impression aide ses clients à atteindre les objectifs de leur projet
Christina Perla a fondé Makelab, un bureau de prestations de services d'impression 3D, à Brooklyn, New York, il y a plus de deux ans. Makelab n'est pas un simple parc d'imprimantes, c'est un bureau de conseil qui aide ses clients à atteindre les objectifs de leur projet.
MakeLab travaille avec les deux procédés FDM et SLA, et oriente ses clients vers celui qui correspond le mieux à leurs besoins. Actuellement, l'activité de l'entreprise se répartit pour moitié entre impressions FDM et SLA. Makelab propose toute la gamme de résines Formlabs. En 2018, High Temp Resin a été la plus populaire.
« Parce que nous sommes prestataires de services, notre rôle auprès du client dans le processus de conception s'arrête à l'impression 3D. Nous considérons la SLA comme un procédé plus élaboré, proposé aux côtés du procédé FDM. Nous avons proposé les résines Formlabs dès les débuts de Makelab. Nous avons toujours reconnu leur valeur et celle qu'elles apportent aux clients. »
Christina Perla
Christina reconnait qu'elle a tendance à préférer l'impression SLA, mais que l'impression FDM fonctionne bien pour de grosses quantités et lorsque la taille des pièces dépassent les volumes d'impression de la plupart des imprimantes SLA. Christina favorise aussi l'impression FDM lorsque la pièce sert à la démonstration de faisabilité de base en interne. Makelab imprimera en SLA des pièces destinées à une réunion d'investisseurs, à un argumentaire en direction du client ou aux présentations finales pour approbation de projets.
Christina trouve qu'il est utile de choisir une marque d'imprimante 3D pour chaque procédé, et d'investir dans l'écosystème de l'entreprise. Cela lui permet de maitriser l'impression sur un appareil donné, de proposer les meilleures impressions possibles et de cultiver une relation avec les marques des imprimantes si jamais elle a besoin d'assistance.
« Ne vous dispersez pas, et choisissez une marque pour chaque [procédé], puis travaillez au sein de ces écosystèmes.Assurez-vous également que chacune des entreprises auxquelles vous achetez les imprimantes offrent une assistance de qualité. Avec simplement deux équipes d'assistance, deux numéros de téléphones et deux ensembles de pièces de rechange, tout se passe bien. »
Christina Perla
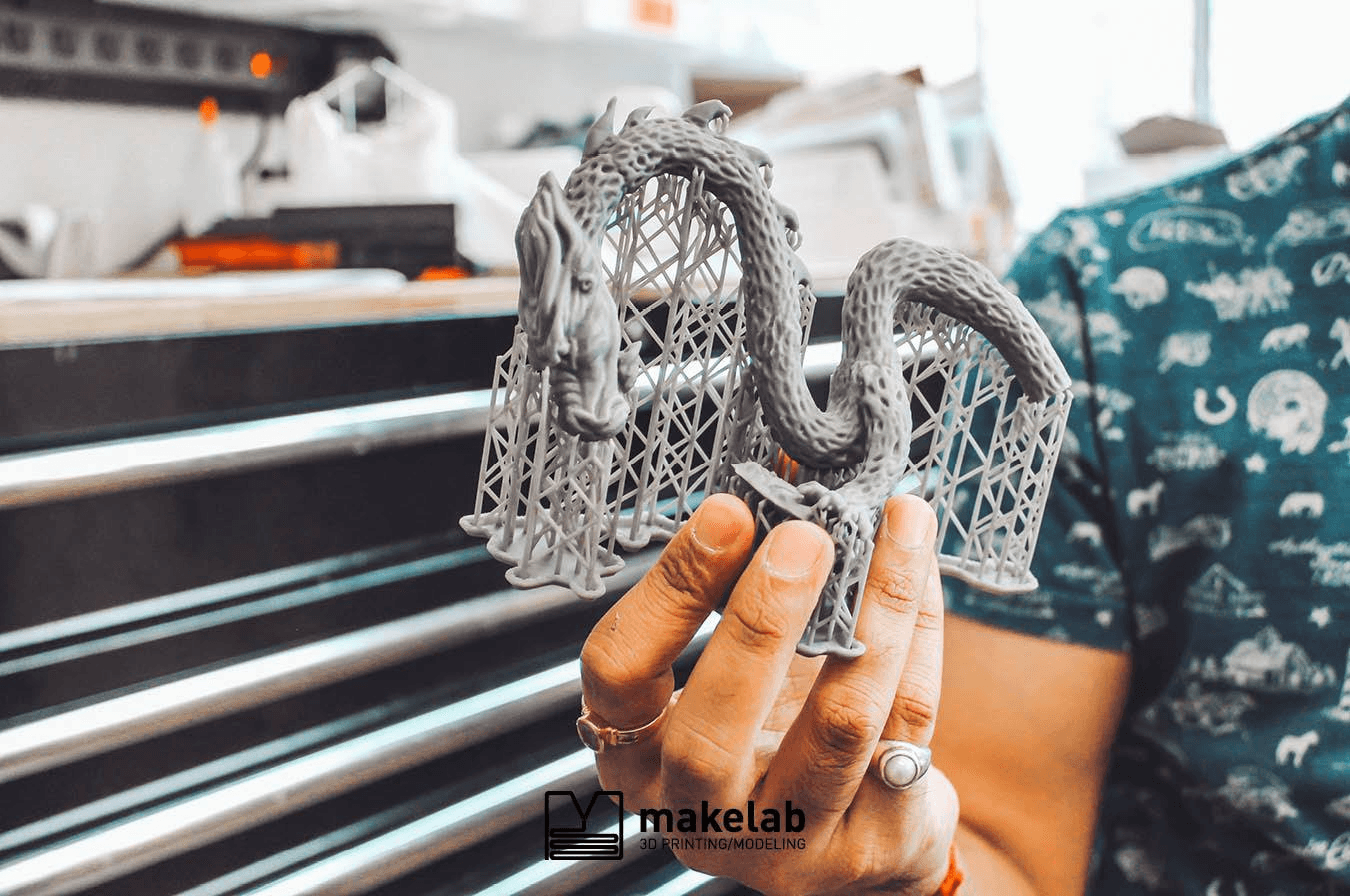
Choix des matériaux souples pour la réalisation du « troisième pouce »
Dani Clode est la créatrice du projet « troisième pouce », en collaboration avec le Laboratoire de plasticité de l'Institut de neurosciences cognitives à l'University College de Londres. Ce pouce prothèse est contrôlé par le pied de l'utilisateur. Il étend de façon importante les capacités d'une main humaine. Le but ultime de ce projet est d'étudier et d'améliorer l'ergonomie et le contrôle des appareils de prothèse.
Un aspect intéressant du projet est que le pouce combine des composants imprimés par SLA et par FDM. La pièce qui constitue le poignet est imprimé en Grey Resin de Formlabs, donnant un matériau solide, mais qui reste léger et poli, et s'adapte bien aux formes anatomiques humaines. Dani a essayé d'imprimer cette pièce sur un appareil à frittage sélectif par laser (SLS), mais elle est revenue à l'impression SLA avec Grey Resin. Dani s'est habituée à ce matériau qu'elle a utilisé depuis ses débuts en prototypage avec l'impression 3D.
Le pouce lui-même est imprimé par FDM, avec les bouts de doigts en Elastic Resin de Formlabs. Dani combine délicatement de nombreuses impressions tant pour le pouce que pour le poignet, choisissant le meilleur matériau pour chacune.En essayant chacun des procédés, Dani a pu trouver comment faire se compléter les procédés FDM et SLA, permettant la réalisation d'un projet qui n'aurait pas vu le jour sinon.
« Le pouce lui-même est imprimé par FDM en polyuréthane thermoplastique, avec une faible densité d'impression. Le matériau FDM flex est difficile mais il reste la meilleure option pour fabriquer le pouce pour le moment. Il est léger et solide. Les bouts de doigts sont imprimés avec Elastic Resin de Formlabs, parce que j'avais besoin d'un matériau souple et à haute résolution, pouvant être de faible épaisseur et bien garder sa forme et son adhérence. J'apprécie également qu'il puisse se fixer facilement aux autres matériaux que j'utilise, contrairement au silicone. Le procédé SLA est le seul à pouvoir imprimer correctement les conduits internes compliqués permettant le contrôle du pouce.
Dani Clode
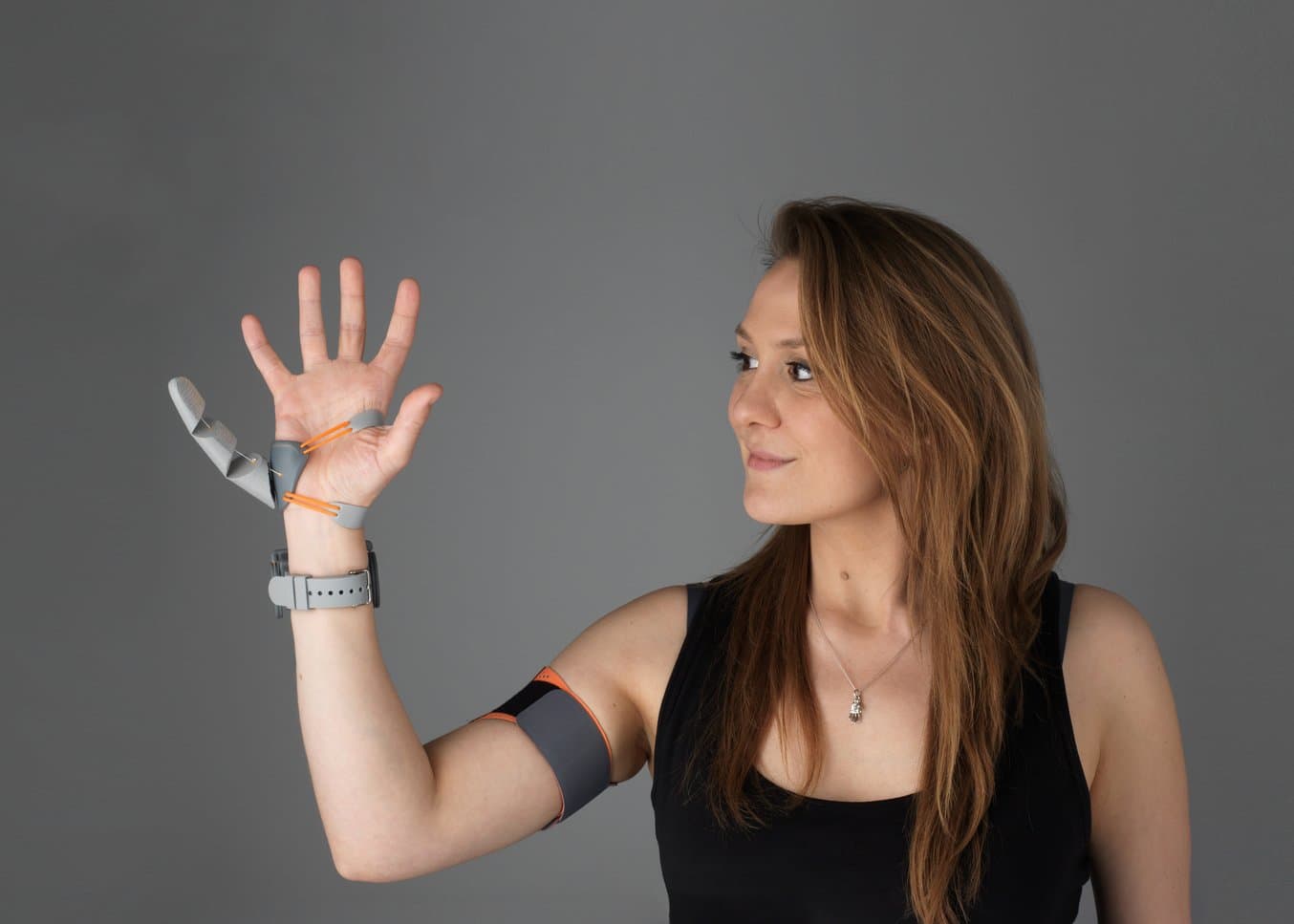
Si vous travaillez sur des projets intéressants, rendus possibles par la combinaison des deux procédés, faites-le nous savoir sur les réseaux sociaux en ajoutant à vos posts le tag @Formlabs !