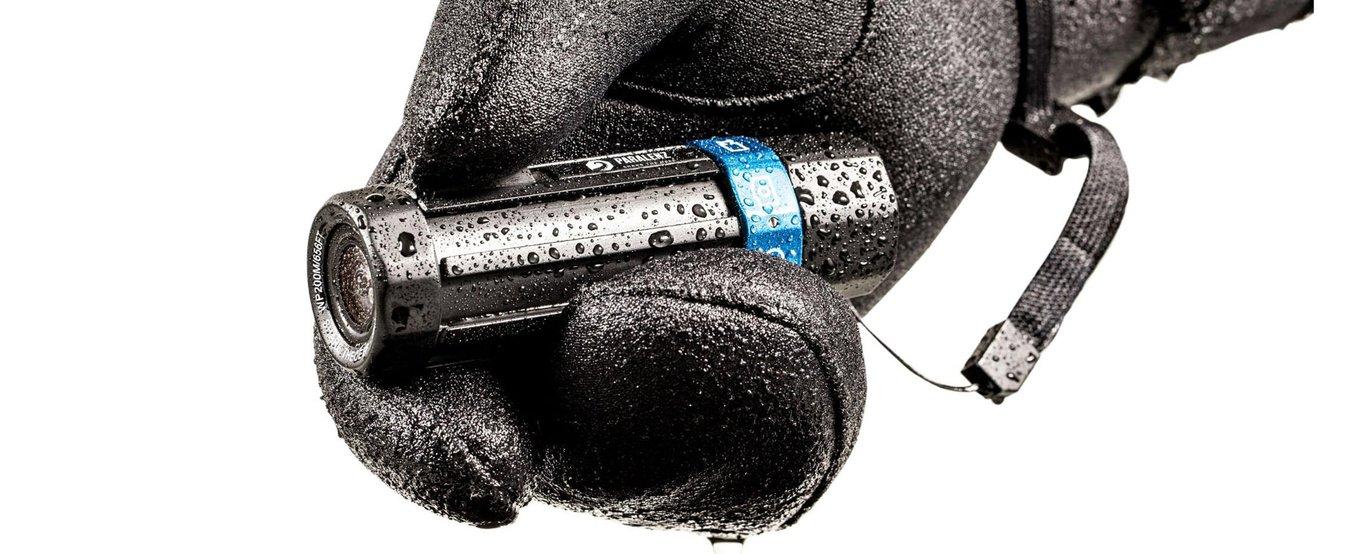
Michael Trøst et son équipe participent au développement produit et au conseil depuis plus de 15 ans. Lorsque leur collègue Martin, un plongeur avide, a constaté le gouffre qui existait entre les caméras polyvalentes et les caméras de plongée haut de gamme, ils ont décidé d’explorer cette opportunité.
Cela a mené à des mois de recherche, de développement et plusieurs itérations. À l’aide d’une imprimante 3D SLA Form 2, l’équipe a créé des prototypes incroyables qui sont comparables au produit final par leur aspect et leur fonctionnement, mais qui ont en plus résisté à des profondeurs de 150 m et aux essais dans l’eau salée.
Consultez notre guide détaillé pour en savoir plus sur le prototypage rapide via l'impression 3D : ses processus, ses applications et ses outils.
Guide Ultime du Prototypage Rapide pour le Développement Produit
En utilisant ces prototypes pour créer leur matériel de marketing, ils ont recouru au financement participatif pour recruter un groupe de bêta-testeurs dévoués, et amassé 468 470 $ de la part de 1153 participants. Mais il y avait encore un défi à relever : gérer la fabrication de la caméra en Asie.
Alors que l’équipe s'apprête à envoyer ses unités tests, nous avons rencontré Michael pour en savoir plus sur l’odyssée de la caméra de plongée Paralenz du prototypage à la production.
Un aperçu de la conception et du développement à Paralenz présentant des prototypes de la caméra de plongée entièrement imprimés en 3D et ses accessoires créés à l’aide de la Form 2.
Comment vous est venue l’idée de développer une caméra de plongée pour une profondeur de plus de 200 mètres ?
Nous avons fondé notre société en 2000 et nous avions pour principale activité la publicité, les effets spéciaux pour les films et les films en stop-motion. Nous avons progressivement ajouté la numérisation 3D, le CNC et l’impression 3D. Je me rappelle que nous avions acheté notre première imprimante 3D il y a 15 années. Depuis, nous avons évolué petit à petit dans l’ingénierie, et aujourd’hui nos ingénieurs et concepteurs contribuent au développement des produits.
Mon collègue Martin a eu l’idée de développer une caméra de plongée pour combler le vide sur le marché. Le choix se faisait entre une GoPro ou autre caméra polyvalente, qui ne sont pas vraiment conçues pour la plongée, et les caméras de plongée haut de gamme, très onéreuses, dotées d’un boîtier d’aluminium, de lampes, etc. Martin voulait trouver un moyen plus simple et abordable de filmer ses propres plongées.
Comment avez-vous obtenu des prototypes aussi réalistes ?
Dès leur sortie de l’imprimante, les pièces sont nettoyées, poncées et peintes. C’est une question de pratique. L’objectif est fabriqué par coulage : nous avons d’abord imprimé un modèle master en 3D, puis fabriqué un moule de silicone pour y couler la pièce. Les logos sont imprimés sur une imprimante à jet d’encre pouvant s’adapter aux grandes pièces. La Form 2 nous a aidés à gagner des heures de travail, parce que les pièces sont prêtes à la finition directement à la sortie de la machine. Les modèles FDM prennent trois fois plus de temps pour obtenir un beau résultat final, et quand il y a beaucoup de pièces vous ne pouvez pratiquement pas obtenir deux modèles avec le même rendu, quelle que soit la charge de travail.

Découvrez les tenants et aboutissants du post-traitement en lisant nos tutoriels (en anglais) sur l'apprêt, la peinture, and l'assemblage des pièces imprimées en SLA.
Comment ces prototypes très fidèles vous ont-ils aidés pour la fabrication ?
Lorsque nous avons eu les premières réunions avec toutes les différentes entreprises chinoises impliquées dans la fabrication, nous avons imprimé des prototypes pour leur montrer le produit qu’il fallait obtenir. Pour ceux qui devaient fabriquer une pièce qui s’enclenche sur une autre, nous avons imprimé les pièces de référence pour les guider dans la fabrication. Ils ont désormais des pièces réelles sous la main, pas seulement des modèles 3D.
Parfois, des erreurs inattendues surviennent suite à un problème de communication, surtout lorsqu’il s’agit de détails hautement techniques. Et ces erreurs sont très coûteuses. Même la plus minime des erreurs peut retarder le développement d’une semaine, voire de plusieurs semaines pour les erreurs critiques. Pour cette caméra, 17 fournisseurs différents fabriquent pour nous des pièces personnalisées, et donc il est essentiel que nous soyons tous synchronisés. Présenter des pièces réelles au début aide les gens à comprendre ce qu’il faut faire.

Nous envisageons d’acheter une autre Form 2 et de l’installer en Chine pour gagner du temps pour nos futurs produits. Nous avons un collègue qui vit en Chine à qui nous pourrons envoyer les fichiers. Cela nous permettra d’avoir les pièces imprimées en quelques heures non seulement dans nos bureaux mais aussi sur place, et ainsi de les montrer directement aux fabricants. Actuellement, l’expédition de pièces de notre bureau vers la Chine prend 2 à 5 jours selon le forfait choisi pour le transport, et donc cet achat accélèrera les choses.
En quoi l’impression 3D a-t-elle été utile pour votre processus de développement ?
Nous utilisons l’impression 3D dans toutes nos activités. Nous réalisons beaucoup de prototypes, toujours à l’avance. Nous avons commencé par parler avec de nombreux plongeurs et par trier les informations collectées. Cela nous a permis d’identifier les fonctionnalités les plus importantes à leurs yeux et ainsi de réduire la liste des exigences pour n’inclure à notre produit que les fonctionnalités indispensables.
Nous avons d’abord réalisé trois ou quatre conceptions de base avant d’en choisir une. Ensuite, nous avons mené beaucoup de tests sur les dimensions, imprimé des modèles en quatre tailles différentes pour évaluer le volume, le poids et la manipulation, et nous avons demandé aux plongeurs de nous faire part de leur préférence. Nous avons créé de nombreuses versions d'un bouton, et les avons testées soigneusement avant de choisir celle qui fonctionnait le mieux. Dans l’ensemble, nous avons réalisé sept ou huit conceptions différentes que nous avons toutes imprimées.
À ce stade, nous avons schématisé toutes les pièces. Avec un produit si compact il y a peu de liberté de conception, et nous avons donc passé beaucoup de temps à optimiser la conception, tout en vérifiant qu’elle remplissait bien les fonctions voulues. Lorsque nous sommes passés au développement des pièces internes, nous avons dû apporter beaucoup de changements. La batterie est aujourd’hui un peu plus petite que ce qu’elle était au début puisque nous avons changé le capteur, l’objectif et certaines autres pièces. Il y a beaucoup de va-et-vient dans ce processus. Nous avons imprimé en 3D tous les changements apportés à la caméra, itérant 20 à 25 boîtiers sur la Form 2 en seulement quelques mois.

Finalement, nous avons réalisé les prototypes finaux que nous avons peints, testés et utilisés également dans la vidéo de campagne. Pour la campagne sur Kickstarter, si nous n’avions pas ce prototype en main, ou un produit physique qui ressemble à la caméra réelle, il aurait été impossible d’amasser les fonds.
En plus de l’accélération des itérations pendant le développement, l’utilisation de la Form 2 nous a aidés à réaliser d’importantes économies d’argent. Nous avons l’habitude de consacrer un budget pour les modèles SLA, et sur ce projet seul, nous aurions dû dépenser 15 000 $ sur les pièces SLA. La Form 2 et ses matériaux coûtent ensemble moins du tiers de cette somme, et donc notre retour sur investissement a déjà été garanti plusieurs fois.
Comment la Form 2 a-t-elle influencé votre productivité ?
Avant d’acheter la Form 2, nous lancions trois machines pour s’assurer qu’au moins l’une d’entre elle fonctionnerait correctement. Les pièces n'étaient jamais prêtes au moment voulu en raison des défaillances de la machine. La Form 2 est la première imprimante 3D en laquelle nous pouvons avoir confiance. Jusqu’à maintenant, nous n’avons eu qu’un échec d’impression sur plus de 200 impressions. Nous l’utilisons chaque jour, souvent plusieurs fois, et l’imprimante fonctionne en continu sur différents projets, des fichiers numérisés en 3D aux grandes pièces, sans oublier les petites pièces aux détails minutieux. Elle fonctionne désormais parfaitement. Pour nous, l’essentiel est que nous sommes rassurés quant à la réussite de l’impression. Nos autres machines requièrent en outre beaucoup de maintenance, nous devons les nettoyer et les démonter très souvent. La Form 2 est simple à utiliser, une imprimante 3D presque parfaite si j’ose dire.
Il y a également moins de soucis de pièces mal ajustées, ce qui était un problème récurrent avec les autres imprimantes. Si vous fabriquez un objet arrondi en CAO, il sera arrondi dans la réalité. S’il est réparti en plusieurs pièces, celles-ci s’emboîtent parfaitement, et même le filetage s’enclenche. Nous concevons pour la fabrication, et donc il est essentiel que notre outil de prototypage puisse émuler le procédé de fabrication qui sera finalement adopté, tout en nous évitant de modifier les pièces à la dernière minute. Nos pièces sont schématisées en gardant en tête la fabrication, qu’elles soient destinées à être extrudées d’aluminium, meulées ou moulées par injection. Nous avons testé la forme et l’ajustement de toutes les pièces. Ainsi, nous pouvons passer à la fabrication avec assurance.
Nous avons même soumis les prototypes à des tests de pression et des tests réels en plongée sous-marine. Si notre prototype a pu résister à cette profondeur, alors le produit final résistera sans souci. Les impressions 3D ont été testées à 150 m (492 pieds) sans aucun problème, et avec le produit final en aluminium usiné, nous avons pu atteindre 400 m (1312 pieds).
L’impression 3D de bureau facilite-t-elle le développement de matériel ?
La Form 2 est une machine fantastique qui nous fait gagner beaucoup de temps. Avant, nous devions exécuter beaucoup de tâches manuellement ou par l’usinage CNC, qui exigeaient des compétences supplémentaires. Maintenant, notre travail est plus facile. Ceci dit, même si vous disposez du bon outil, vous avez toujours à faire une conception de qualité. Il faut avoir la bonne idée et main-d'œuvre pour modéliser les pièces de votre produit. Mais cette technologie simplifie et accélère votre travail, parce que vous n’avez pas à apprendre à manipuler la machine d’usinage CNC ou d’autres outils.
Mieux encore, elle est tellement simple que même les enfants peuvent l’utiliser. Nous avons d’ailleurs collaboré avec des écoles pour apprendre aux étudiants la modélisation 3D. Certains étudiants nous ont surpris par leurs compétences : en seulement quelques mois, ils étaient parvenu à réaliser des choses que nous croyons impossibles jusqu’alors.
Quelles sont les prochaines étapes, maintenant que vous êtes en phase de production ?
Nous avons presque terminé la production du premier lot de nos unités tests, que nous envisageons d’expédier avant la fin de l’année, mais nous sommes toujours en train de développer certains accessoires, notamment un visionneur à la troisième personne que nous prototypons également sur la Form 2. Son principe de fonctionnement ressemble à celui d’un selfie-stick, mais avec pontons (dispositifs de flottaison) pour qu’il puisse flotter derrière le plongeur.

Aujourd’hui, 250 bêta-testeurs sont enregistrés dans 37 pays. Nous comptons lancer une production de caméras à expédier dans le monde entier pour les tester dans une variété d’environnements et types d’utilisations. Nous avons eu des commandes par tous types de plongeurs : plongeurs de grottes de la Finlande et du Mexique, plongeurs libres de la Belgique et de la Floride, plongeurs techniques d’Australie et du Canada, et pêcheurs à lances d’Hawaï et de l’Afrique. Nous avons même eu des commandes en Antarctique et en Alaska. Nous rassemblerons les retours pour découvrir toutes les erreurs susceptibles d’être présentes sur un produit de première génération avant de lancer la production du produit final en février.