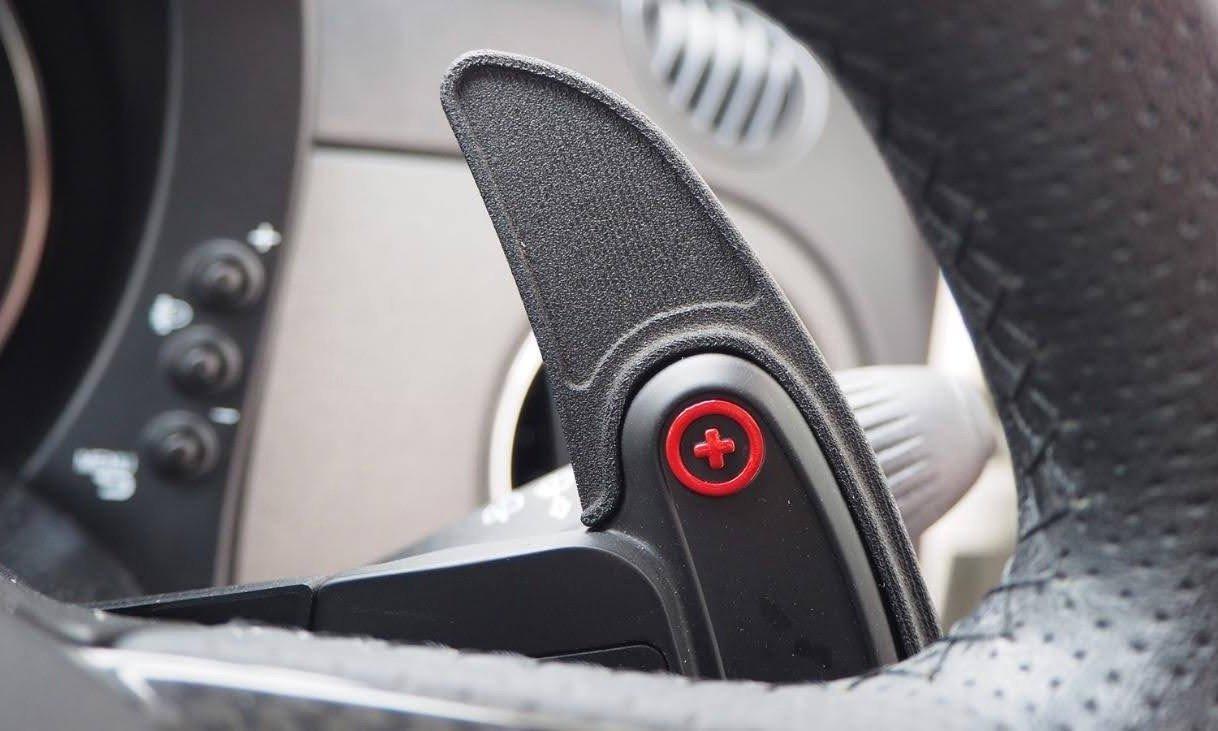
Le Japon est au centre de l'innovation automobile depuis des décennies. Les principes de la production allégée, qui trouvent leur origine dans la philosophie des constructeurs automobiles japonais, tout comme le Kaizen ou l'amélioration continue, sont enseignés dans le monde entier dans le cadre de formations continues destinées aux cadres et sont présentés comme des protocoles fondamentaux pour tous les types de production. L'esprit d'innovation et de développement continu qui a démarré chez ces grands équipementiers est également très présent chez le fabricant japonais de pièces détachées automobiles Codetech CAM.
Codetech s'est taillé une place dans le secteur automobile japonais concurrentiel en fournissant des solutions de rechange pour les voitures importées. Bien que la base de clientèle soit restreinte, les amateurs de voitures importées ont des préférences marquées, et la demande de personnalisation et d'ajouts de luxe est en hausse.
Codetech répond à cette demande en créant un modèle de fabricabilité réactif et agile basé sur des pièces imprimées en 3D de haute performance. En utilisant les technologies de la stéréolithographie (SLA) et du frittage sélectif par laser (SLS), Codetech a été en mesure de fournir à ses clients des solutions qui améliorent leur expérience de conduite ainsi que l'esthétique de leur voiture importée. « Avec une bonne compréhension des besoins des clients et des possibilités techniques pour y répondre, il existe d'innombrables possibilités de créer des produits intéressants », déclare Masato Uchida, responsable du laboratoire de design chez Codetech.
Trouver la faille dans le marché des voitures importées
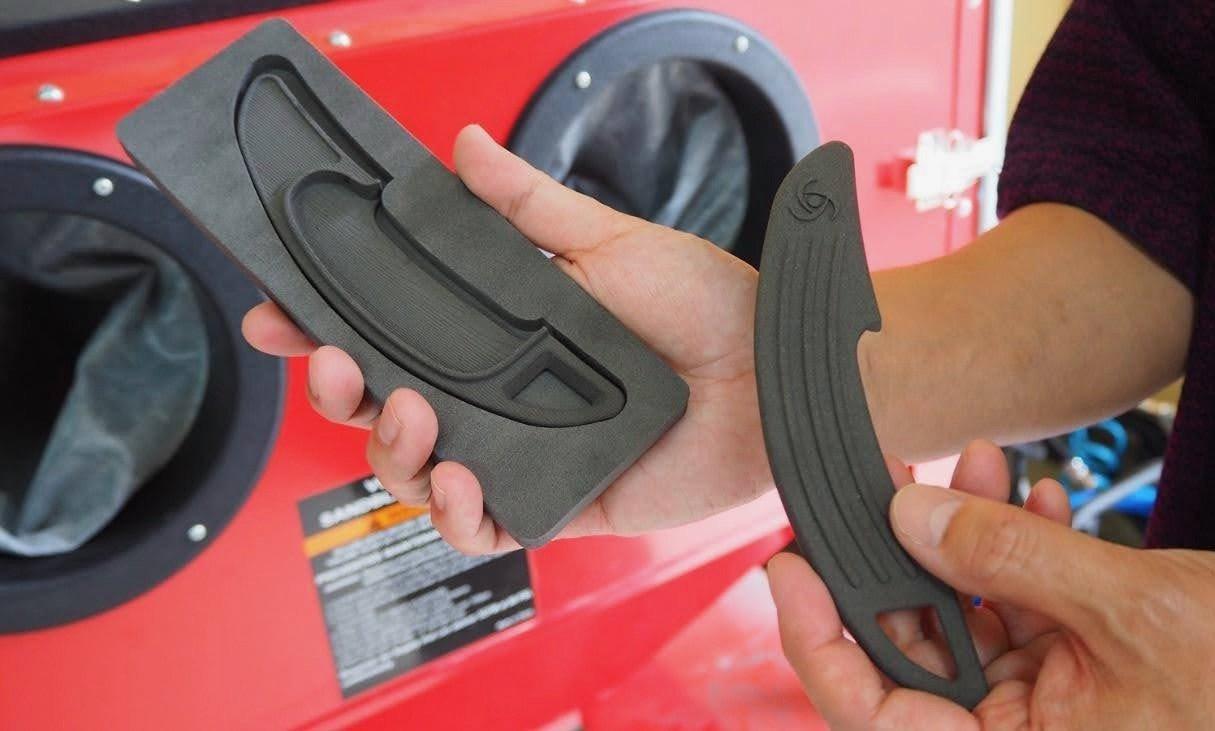
Cette extension de palettes de changement de vitesse Core-OBJ est un produit populaire de CodeTech. Elle permet de rallonger les palettes de changement de vitesse d'origine d'Abarth et offre une taille et une texture plus agréables pour les doigts.
Les constructeurs automobiles japonais, comme Toyota, Honda et Nissan, contrôlent la grande majorité des parts de marché au Japon, mais les marques européennes comme BMW ou Volkswagen sont considérées par un petit groupe de consommateurs comme des articles de luxe. Ces propriétaires de voitures veulent des accessoires personnalisés et des pièces de rechange, mais il est pratiquement impossible de trouver des fabricants de pièces automobiles qui couvrent un large éventail de marques de fabricants d'équipements d'origine (OEM).
Les systèmes logiciels automobiles devenant de plus en plus sophistiqués, il est de plus en plus difficile de trouver ces pièces de rechange. Les composants électriques sont souvent mis à jour au fur et à mesure que les systèmes logiciels évoluent avec chaque nouveau modèle de voiture, ce qui rend les pièces de rechange obsolètes.
CodeTech est en mesure de s'imposer là où d'autres fabricants de pièces de rechange ne le peuvent pas, car l'entreprise mise sur une méthode de fabrication plus flexible : l'impression 3D.
L'impression 3D au service de la rétro-ingénierie
Les procédés de fabrication traditionnels de l'industrie automobile, tels que le moulage par injection, l'usinage CNC, le moulage par soufflage ou le moulage au sable, sont des méthodes efficaces de production de masse pour les équipementiers. Pour les fabricants de pièces de rechange, qui doivent procéder à une rétro-ingénierie des composants afin de les ajuster ou de les reproduire, ces méthodes rendent impossible une fabrication rentable.
Dès le début, l'équipe de CodeTech savait qu'elle devrait utiliser une méthode de fabrication plus flexible et moins coûteuse afin de produire de manière cohérente et rentable des pièces compatibles avec les voitures importées produites en masse.
Uchida et l'équipe de Design Lab ont commencé avec l'imprimante 3D SLA Form 1, puis ont ajouté les imprimantes Form 2, Form 3, et maintenant l'imprimante SLS Fuse 1+ 30W. Cela a permis à l'équipe d'augmenter sa capacité pour répondre à la demande croissante de sa petite clientèle. Lorsque l'équipe reçoit une demande de nouvelle pièce, elle peut procéder à la rétro-ingénierie du composant d'origine grâce au scan 3D et à la conception CAO. Une fois que M. Uchida dispose du fichier, il peut l'imprimer immédiatement et livrer une pièce finale qui a été fabriquée sans qu'il soit nécessaire de recourir à des outils coûteux. « Ce que j'aime dans la Fuse 1, c'est que je peux imprimer un produit presque fini dès le début », explique M. Uchida.
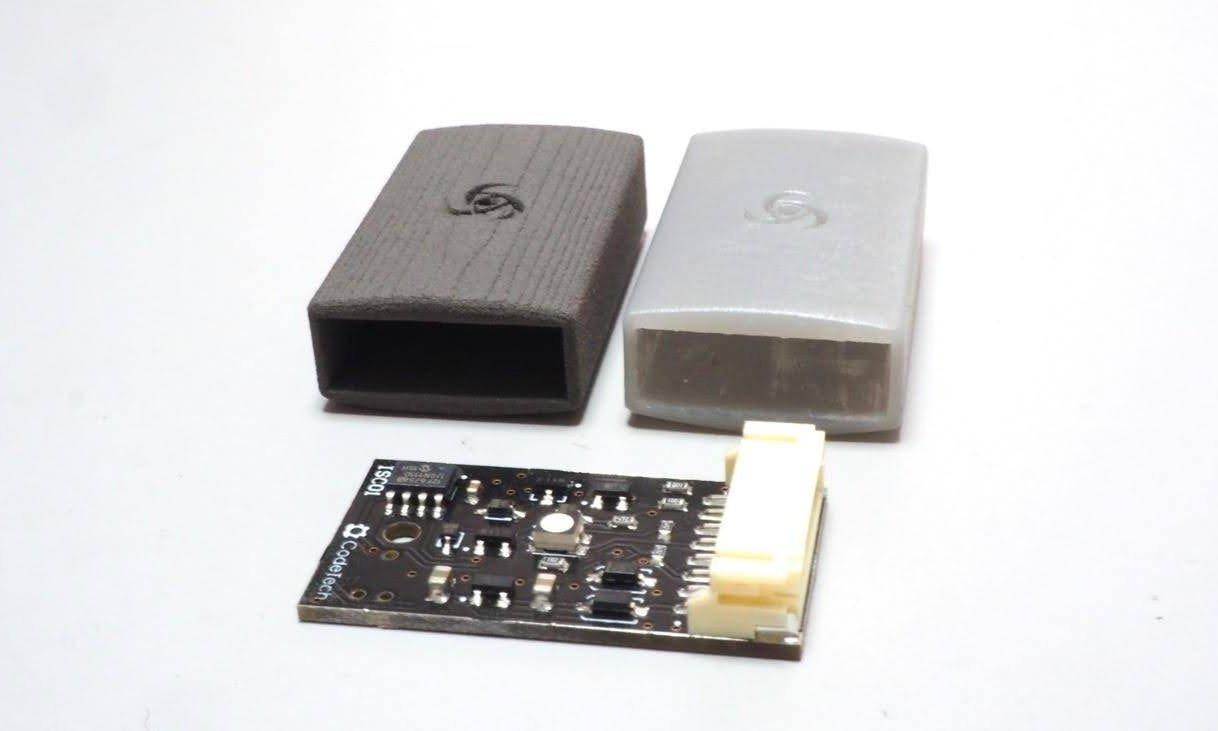
Ces boîtiers électroniques ont été rapidement prototypés sur une imprimante Form 3 SLA avec Draft Resin, puis imprimés en tant que pièce complète sur l'imprimante SLS Fuse 1+ 30W.
La viabilité commerciale des pièces imprimées en 3D par SLS a été validée lors d'une récente exposition automobile. Ces boîtiers électroniques ont rapidement été prototypés sur une imprimante SLA Form 3 avec Draft Resin, puis imprimés en tant que pièce d'utilisation finale sur une imprimante SLS Fuse 1+ 30W. Lors de l'exposition, il a reçu des retours positifs inattendus : les gens voulaient savoir quand le produit serait disponible à l'achat. M. Uchida est retourné au laboratoire de conception et a mis en production la Fuse 1+ 30W avec Nylon 12 Powder.
« Le salon a pu avoir lieu uniquement parce que j'ai pu créer un produit presque fini avec la Fuse 1 directement après le modelage. Je trouve que cette vitesse est nécessaire et qu'elle s'ajuste à la durée dans laquelle nous vivons. »
Masato Uchida, responsable du laboratoire de conception chez CodeTech
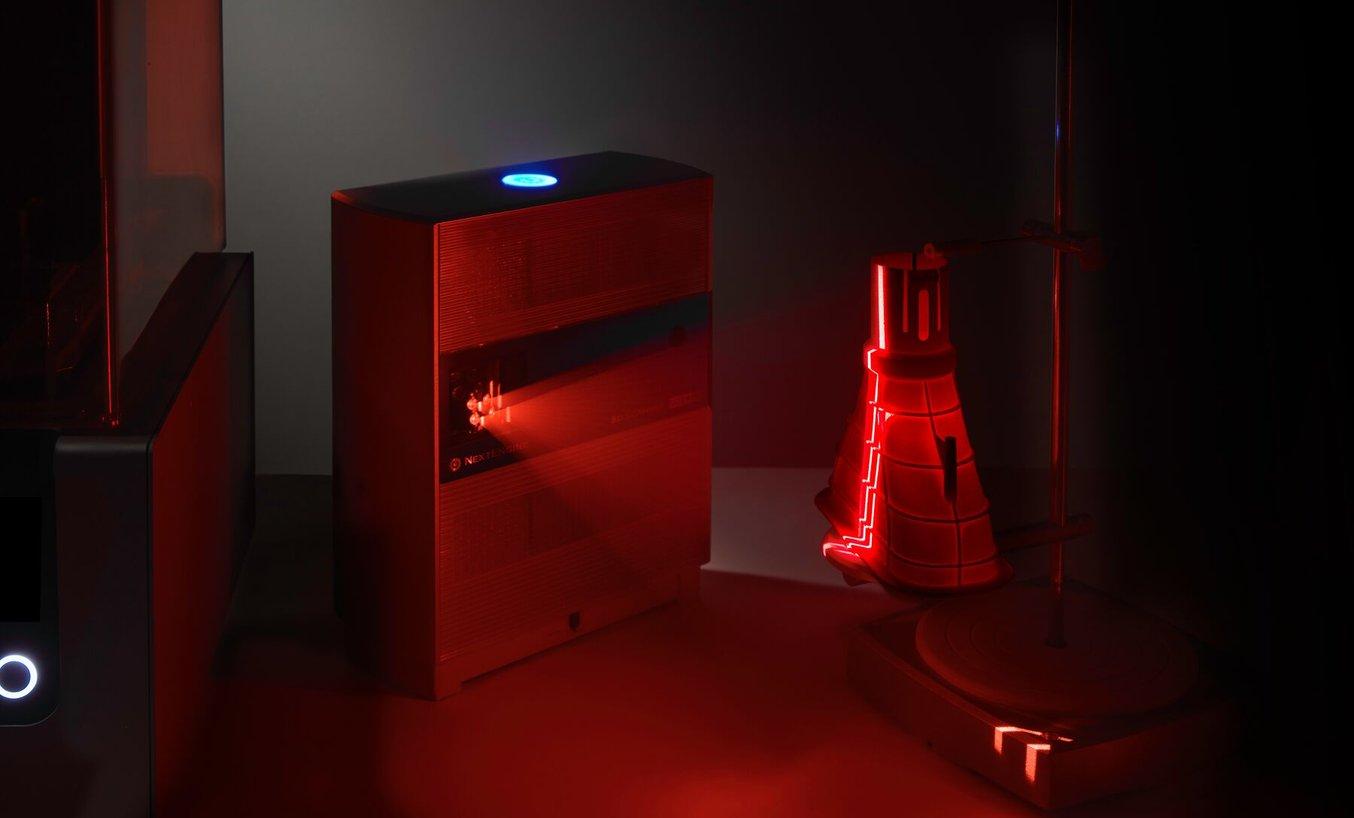
Numérisation et impression 3D pour la rétro-ingénierie et d’autres applications
La numérisation 3D et l’impression 3D sont utilisables, entre autres, en reproduction, en restauration, en rétro-ingénierie, en métrologie, et bien plus. Téléchargez notre livre blanc pour découvrir ces applications et vous lancer.
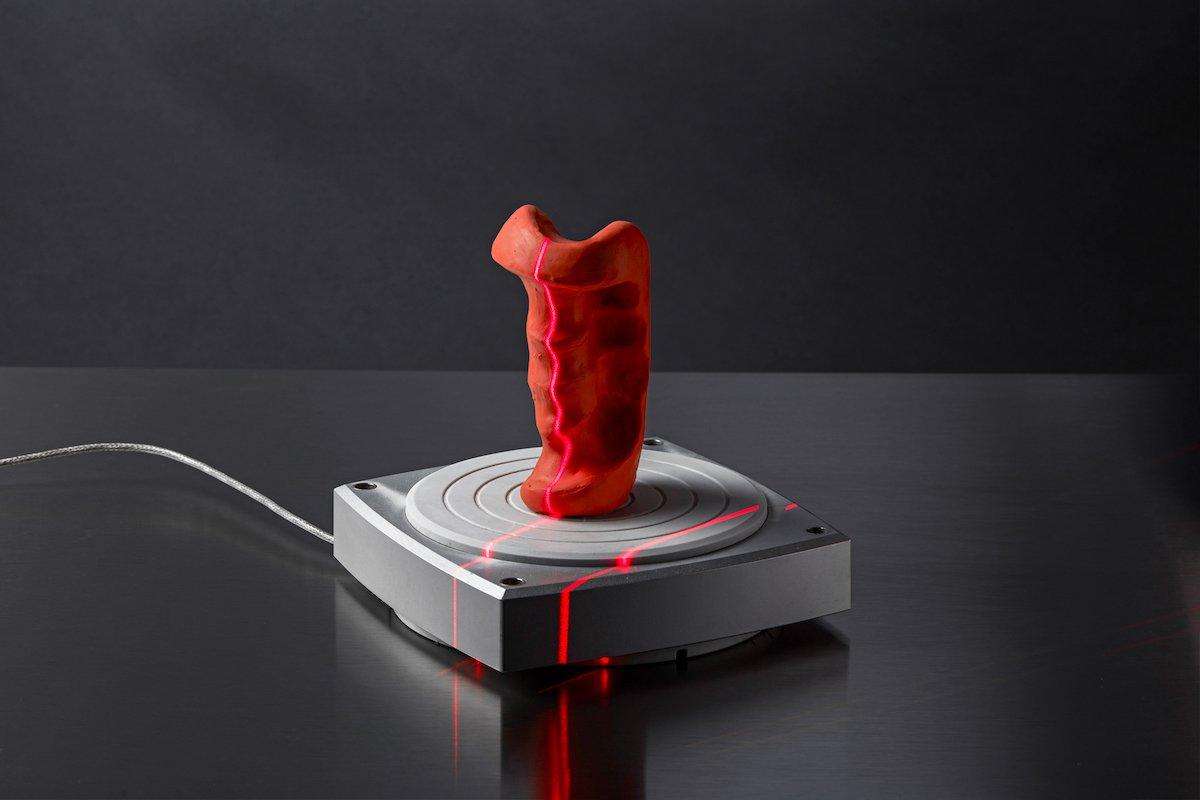
De la numérisation 3D à l’impression 3D : rétro-ingénierie rapide pour la restauration de machines, les gabarits d’assemblage et les produits d’après-vente
Regardez ce webinaire et découvrez comment utiliser la numérisation 3D pour améliorer la conception et la production des pièces en la combinant à la rétro-ingénierie CAO et à l’impression 3D.
Approvisionnement flexible et commandes en ligne
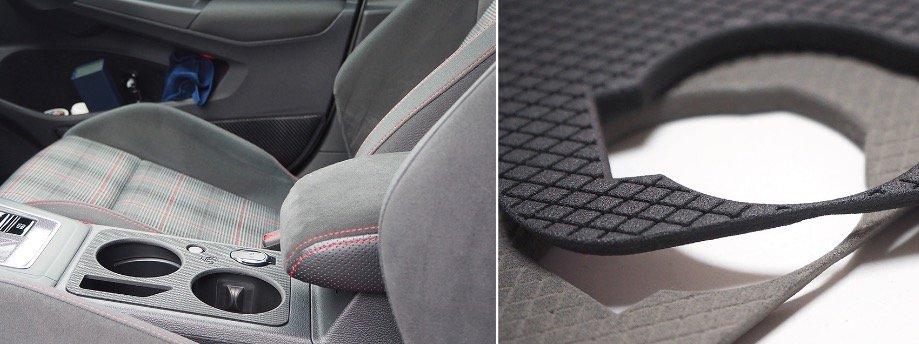
Les porte-gobelets de la Volkswagen Golf 8 sont sablés puis finis avec un revêtement en uréthane noir mat (à gauche). Le bord fin du support (à droite sur la photo) serait impossible à réaliser avec des méthodes de fabrication conventionnelles ; l'impression 3D interne permet de créer des pièces avec des tolérances aussi étroites et des détails aussi fins.
Le fait de disposer d'un inventaire numérique et de processus de production par impression 3D permet également à CodeTech de réagir rapidement aux changements de la demande et l'empêche d'avoir à constituer d'importants stocks physiques. En concevant et en produisant des pièces uniques qui sont ensuite utilisées pour la publicité en ligne, CodeTech peut estimer la demande avant de se lancer dans la production. L'équipe peut travailler de manière plus flexible et plus efficace et éviter de dépenser des ressources pour des produits qui ne se vendent pas. Lorsque la demande est là, ils peuvent modifier leur flux de travail de production pour y répondre immédiatement.
Dans le cas d'un porte-gobelet conçu pour la console centrale d'un véhicule Volkswagen, CodeTech a d'abord publié de la publicité pour le produit, puis a adapté son processus de production en conséquence. M. Uchida imprime 25 porte-gobelets par chambre de construction ; grâce à l'algorithme d'agencement de la série Fuse et au recyclage des poudres, une telle production en petites séries est possible. Le design du porte-gobelet a immédiatement rencontré un grand succès, car ses bords extérieurs fins s'adaptent parfaitement à une console VW existante, mais seraient trop fins pour être fabriqués selon des procédés conventionnels. C'est un cas où la fabrication additive ne se contente pas de reproduire des pièces, mais les améliore.
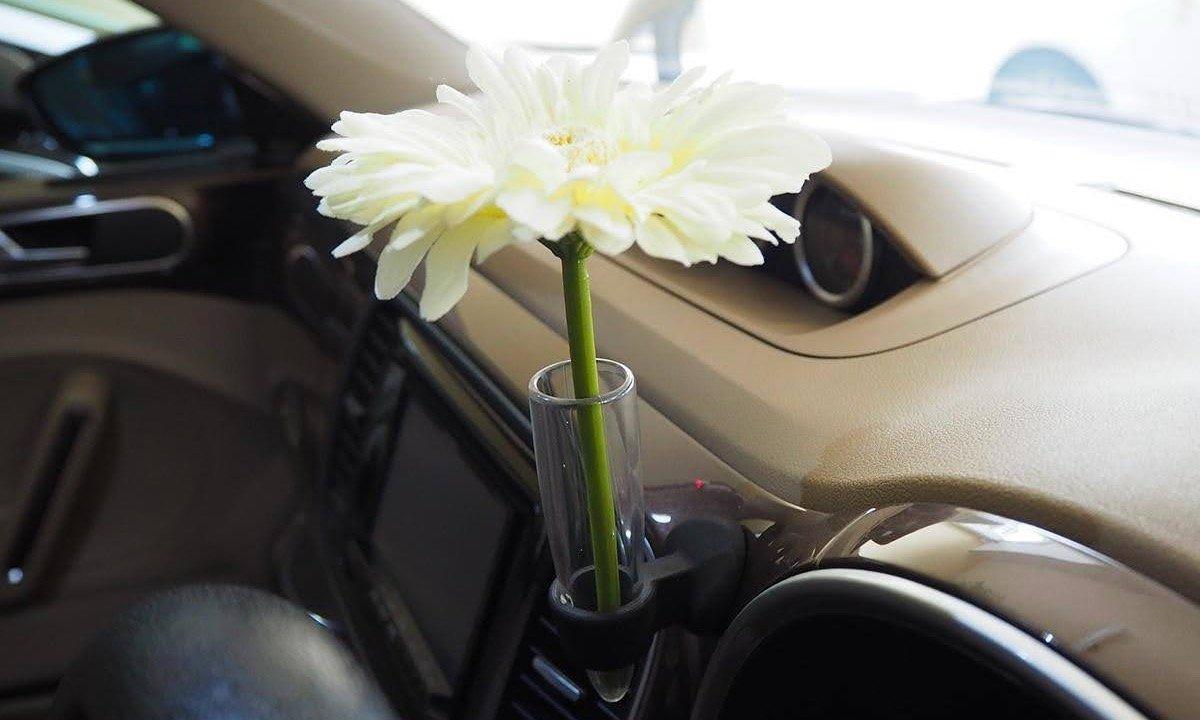
Des pièces de rechange peuvent aider à la personnalisation, comme cette fixation de vase à fleurs avec une fixation imprimée en 3D.
Pour rendre les pièces SLS d'utilisation finale comme celles-ci encore plus attrayantes pour les consommateurs, l'équipe du laboratoire de conception utilise des techniques de post-traitement avancées pour lisser la surface des pièces en nylon. Les porte-gobelets ont été dépoudrés dans une Fuse Sift, sablées, puis finies avec une couche d'uréthane noir mat, ce qui leur permet de s'ajuster parfaitement aux finitions intérieures de la Volkswagen.
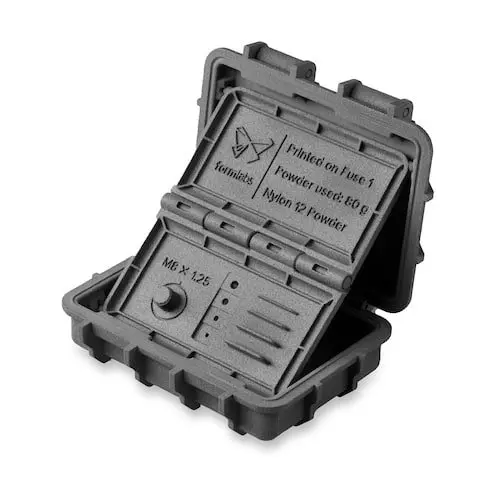
Commander un échantillon SLS gratuit
Examinez et constatez par vous-même la qualité Formlabs. Nous vous enverrons un échantillon gratuit imprimé sur la Fuse 1+ 30W à votre bureau.
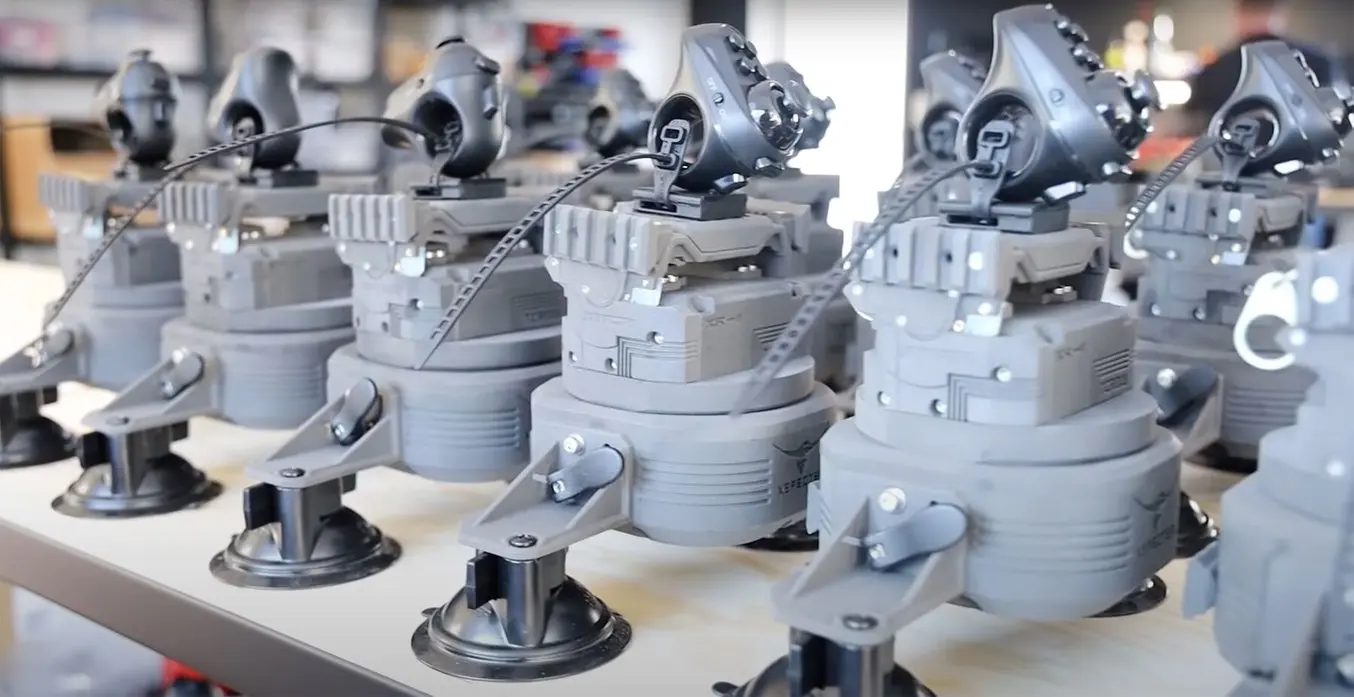
Le SLS pour la production finale
L'impression 3D pour la production finale n'est pas seulement accessible : elle est aussi plus abordable, plus agile et plus évolutive que jamais grâce à l'écosystème SLS Fuse. Explorez notre page dédiée à la production SLS pour comparer les différentes méthodes de fabrication, consulter les tarifs des poudres en vrac et découvrir comment 15 fabricants exploitent actuellement les imprimantes de la série Fuse.
Progresser grâce à la fabrication additive
M. Uchida et ses collègues de CodeTech se sont engagés à continuer d'innover et à développer des produits capables de répondre à l'évolution constante des demandes des consommateurs. En s'appuyant sur les imprimantes Formlabs, que M. Uchida trouve « intuitives et faciles à utiliser », l'équipe de CodeTech peut créer un procédé de fabrication flexible et réactif. La production sur demande de pièces finales avec la Fuse 1+ 30W permet à l'entreprise d'éviter de consacrer de l'argent et du temps à une fabrication traditionnelle coûteuse ou à la maintenance de volumes importants de produits physiques.
Pour en savoir plus sur l'impression 3D dans le secteur automobile, explorez nos applications automobiles et nos études de cas. Pour savoir comment l'impression 3D SLA ou SLS peut profiter à votre flux de travail, contactez nos experts automobiles.