Comment Tessy Plastics réduit les arrêts de production avec la Fuse 1
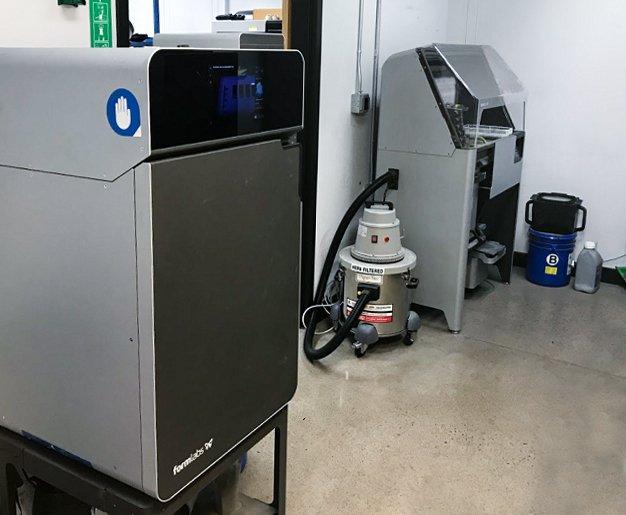
Tessy Plastics est un sous-traitant pour la fabrication de produits sur mesure en plastique moulé par injection, travaillant pour des entreprises médicales, pharmaceutiques, de diagnostic et de produits de consommation. Brian Anderson, ingénieur en recherche et développement chez Tessy Plastics, est un expert de l’utilisation de la fabrication additive pour l’amélioration des résultats à l’atelier. Chaque semaine il doit trouver de nouvelles solutions à tout type de problèmes apparaissant à l’atelier, allant du remplacement de pièces d’appareils à la création d’outils et d’accessoires sur mesure. Son travail est de garantir que les délais des clients de Tessy seront respectés, quel que soit le problème.
Récemment, Brian a pu ajouter la Fuse 1, imprimante 3D à frittage sélectif par laser (SLS), à son parc d’imprimantes 3D et d’autres outils de fabrication. Tessy Plastics a fait l’acquisition de sa première imprimante 3D SLS et voici comment il l’a utilisée.
Fabrication additive chez Tessy Plastics
« La première chose que nous avons essayée a été d’éprouver la résistance à la rupture des pièces en nylon. Elles sont vraiment solides ! »
Brian Anderson
Tessy met à disposition de son équipe un parc interne d’imprimantes 3D d’une grande variété. Il compte deux imprimantes à dépôt de filament fondu (FDM), un appareil Stratasys J750 PolyJet et deux imprimantes stéréolithographiques (SLA) Formlabs. Plusieurs départements font appel à cet ensemble d’imprimantes, chacune étant utilisée selon différents besoins.
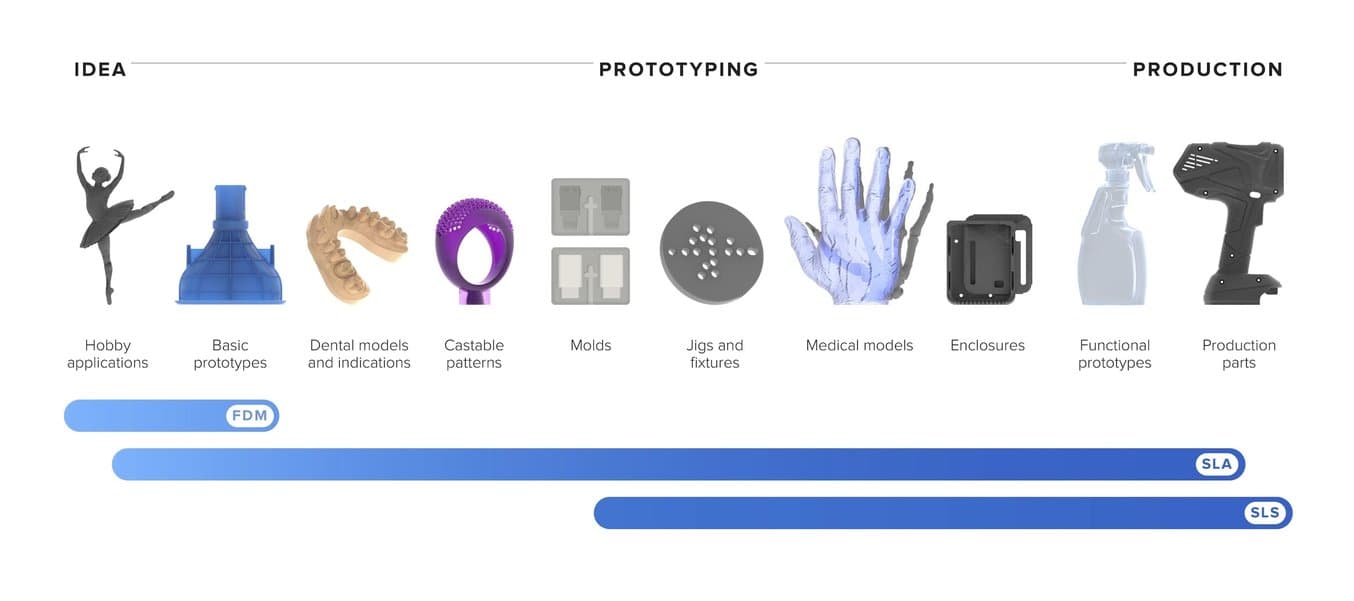
Comment utiliser différentes imprimantes 3D en tandem.
Cette année, l’équipe a pu disposer en interne de sa première imprimante à poudre de nylon : la Fuse 1. L’objectif de cet appareil est de réaliser des pièces de rechange fonctionnelles de qualité lorsque des appareils sont endommagés, ce qui augmente leur disponibilité et permet de continuer la production. Brian a également utilisé la Fuse 1 pour réaliser des prototypes fonctionnels prêts pour la production afin de résoudre des problèmes spécifiques auxquels ses imprimantes SLA, FDM et Polyjet ne pouvaient répondre.
Réaliser des pièces finales par impression 3D SLS
Brian pensait que disposer en interne de l’imprimante SLS Fuse 1 « leur donnerait plus de chances de trouver la meilleure solution aux problèmes qu’ils rencontraient », du fait de la polyvalence de l’impression SLS et de la grande qualité des pièces produites en nylon. Le nylon et ses composites sont des thermoplastiques de haute qualité, dont les propriétés mécaniques ont été éprouvées et sont comparables à celles de pièces réalisées selon des méthodes de fabrication conventionnelles comme le moulage par injection.
Lorsque des pièces imprimées par SLS sont sous-traitées, l’équipe n’a finalement qu’un seul essai à faire pour s’assurer que leurs modèles sont corrects. Le modèle est conçu et envoyé à l’impression. Il revient plusieurs semaines plus tard, ce qui ne laisse plus guère de place à des modifications éventuelles. Grâce à la Fuse 1, il est possible d’en imprimer plusieurs et d’optimiser le modèle dans un délai de quelques jours seulement, ce qui permet d’obtenir un meilleur produit fini qu’en passant par la sous-traitance.
Voyons maintenant les problèmes que Brian a pu contourner avec sa Fuse 1.
Poulie de courroie de distribution standard
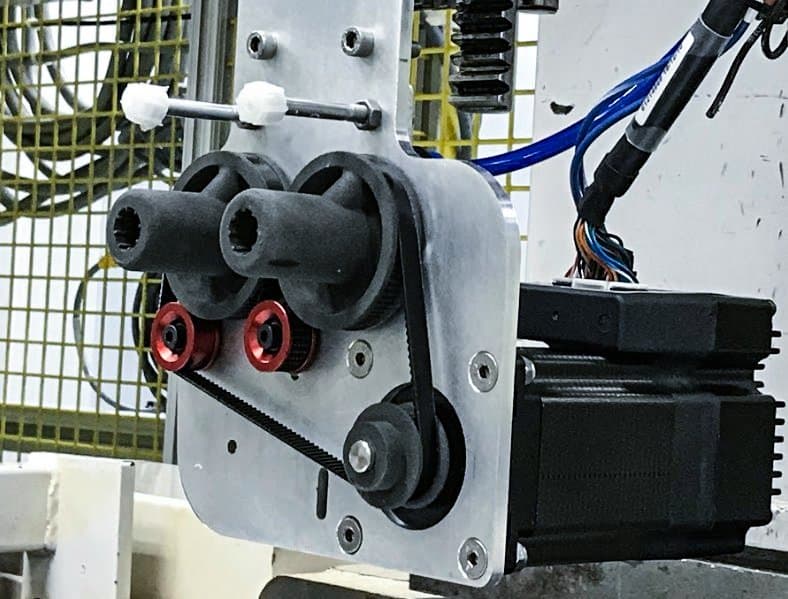
« La précision et la durabilité de la poulie ont été impressionnantes. »
À mi-chemin de la réalisation d’un prototype demandé par un client, celui-ci a modifié le modèle de façon importante. Il aurait été nécessaire de faire un nouveau moule de la pièce en raison du changement de forme requis, ce qui aurait induit un délai dans la production de la pièce.
Au lieu de refaire un moule, Tessy a imprimé avec la Fuse 1 un nouveau système de poulies pour l’appareil de moulage. Après trois semaines d’utilisation, les poulies imprimées en 3D paraissent neuves et fonctionnent comme telles. En utilisant les poulies fabriquées avec la Fuse 1 comme pièces finales, Tessy a pu produire rapidement des milliers de pièces pour son client au lieu d’arrêter la production et d’attendre qu’un nouveau moule soit fabriqué.
« Les poulies sur mesure imprimées la semaine dernière fonctionnent bien en production. Elles présentent des nervures très fines sur la face interne de l’outil d’aspiration, qui tiennent bien au dévissage du noyau des pièces moulées. »
Brian Anderson
Outils pour raccords
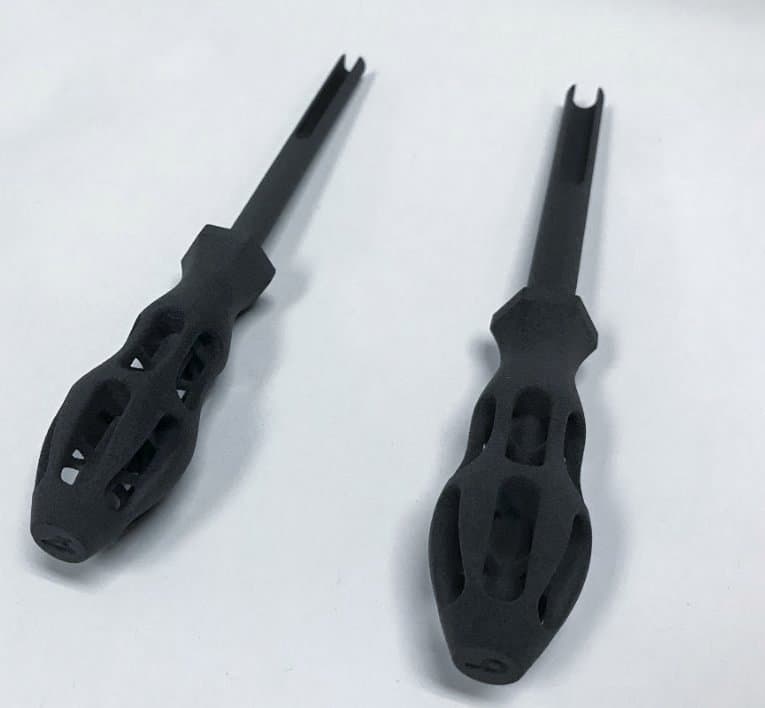
Outils pour raccords sur mesure, imprimés avec la Fuse 1.
Au niveau du moulage, des douzaines de raccords pneumatiques à emboitement sont utilisés sur différents appareils. L’insertion des tubes dans les raccords est bien souvent difficile et des pièces peuvent être endommagées lorsque l’opération est effectuée à la main ou avec un tournevis.
Un tournevis de raccordement a été réalisé pour retirer les tubes en caoutchouc des raccords. La solidité des pièces fabriquées par SLS permet de réaliser des outils sur mesure et de les utiliser directement à l’atelier quelques jours après leur conception. Brian a ainsi pu étudier un problème survenu à l’atelier, proposer une solution et imprimer plusieurs types d’outils de raccordement pour l’équipe de production.
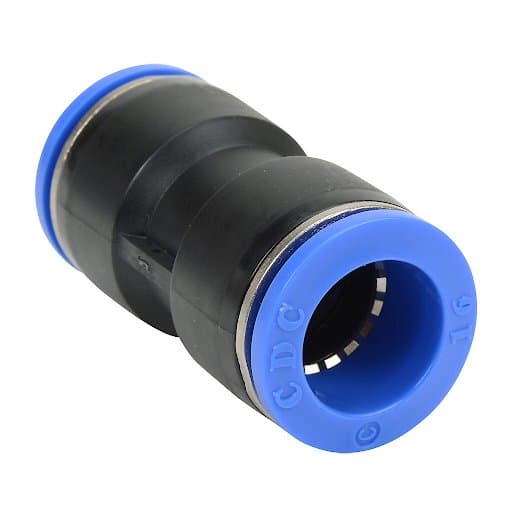
Exemple de raccord pneumatique à emboitement.
L’outil spécial facilite l’insertion et l’extraction des tubes en caoutchouc, diminue le risque d’endommager les raccords, dont le remplacement coûte entre 17 et 25 € chacun. Le coût par pièce imprimée sur la Fuse 1 étant faible, il devient plus rentable de réaliser des outils que de remplacer des pièces à chaque fois qu’un raccord est abimé. Cette économie indirecte résultant de la réduction du nombre de raccords à remplacer est également attribuable à la Fuse 1.
Le coût par pièce le plus bas en impression 3D
« Nous pensons que l’investissement dans la Fuse 1 en vaut la peine. »
Brian Anderson
La Fuse 1 apporte à des entreprises comme Tessy toute la puissance du procédé SLS industriel, sous forme d’un système compact et de prix abordable, pouvant produire des pièces en nylon prêtes pour la production. La plupart des entreprises ont eu des expériences de sous-traitance de pièces en nylon imprimées en 3D, mais n’ont jamais eu la possibilité de les imprimer en interne à un prix abordable.
L’un des facteurs entrant dans l’évaluation du RSI de la Fuse 1 par Tessy est la réduction du temps d’arrêt des machines de production. La capacité à imprimer des pièces de rechange en nylon haute performance se traduit par la réduction des arrêts machines qui peuvent paralyser la production. Par exemple, il a été possible de réaliser des millions de kits de test COVID en attendant des pièces de rechange, ce qui a contribué à justifier le RSI de l’adoption par Tessy de l’impression SLS en interne. Proposée à un prix bien inférieur aux 170 000 € (200 000 $) que coûtent généralement les systèmes SLS industriels, l’imprimante Fuse 1 vise à générer un RSI pour des entreprises dont les budgets sont plus réduits et plus réalistes.
Comparaison de la Fuse 1 aux autres imprimantes Formlabs
Selon Brian, les imprimantes 3D telles que la Form 2 utilisées en interne peuvent se rentabiliser immédiatement en fonction du projet. « Le prix de vente de la Form 2 était si bas que nous avons pu en acheter deux pour un projet donné et elles ont été rentabilisées dès le premier mois. » Brian considère que la Fuse 1 représente un investissement à plus long terme que la Form 2, mais qu’elle peut facilement être rentabilisée.
« Nous considérons que la Fuse 1 est différente de la Form 2. Nous ne vendons pas les pièces qu’elle produit. Elle nous sert à réaliser des pièces fonctionnelles, utilisées directement, en développement de produits ou pour l’outillage. C’est un investissement sur trois ans et nous pensons qu’il en vaut vraiment la peine. » Le fait que le coût unitaire des pièces imprimées avec la Fuse 1 soit le plus bas sur l’ensemble des imprimantes 3D de Tessy Plastics y contribue également. Toujours selon Brian, « le coût des pièces est vraiment bas. Lorsqu’on la compare à nos autres imprimantes 3D, il s’avère que la Fuse 1 est celle qui produit des pièces de coût unitaire le plus faible.
En savoir plus : L’imprimante SLS Fuse 1
« La Fuse 1 est un « couteau suisse » en production. »
Brian Anderson
Voici quelques exemples des pièces que Tessy a imprimées sur la Fuse 1. « Nous avons imprimé quelques ensembles de carénages de rechange pour ventilateur, un tournevis limiteur de couple, un outil pour bras robotique et un bloc avec plusieurs filetages imprimés. Nous avons essayé la Fuse 1 sur des applications très diverses. »
Formlabs est vraiment heureux de proposer l’imprimante 3D SLS Fuse 1, qui permet à des entreprises de toute taille de réduire les coûts de sous-traitance et les délais de réalisation. L’impression 3D SLS est très appréciée des ingénieurs parce qu’elle permet d’imprimer des pièces fonctionnelles solides, sans supports. Mais cette technologie a longtemps été coûteuse et difficile à utiliser. Disposer de la puissance du SLS à l’atelier permet à des ingénieurs comme Brian Anderson de résoudre tous les problèmes qui se présentent à eux.
Soyez parmi les premiers à recevoir ce qui représente la nouvelle référence en matière d’impression 3D industrielle.
Plus d’informations sur Tessy Plastics : Société fondée en 1973, Tessy Plastics est un fabricant sous-traitant au niveau mondial, dont le siège se trouve à Skaneateles, NY. Elle est spécialisée dans le moulage par injection et les solutions d’assemblage automatisé sur mesure. Nous possédons également des installations dans l’État de New-York, en Pennsylvanie et en Chine. Toutes nos installations sont conformes aux normes FDA/GMP. Leur surface totale dépasse les 160 000 m2, dont environ 14 600 sont des salles propres ISO 7 et 8, dédiées à la fabrication. Grâce à nos équipes d’ingénierie et de recherche et développement totales, nos produits sont de qualité supérieure et peuvent rapidement être mis sur le marché. Travaillant pour des entreprises médicales, pharmaceutiques, de diagnostic et de produits de consommation, nous disposons d’une expertise sur un grand éventail de produits. Nous pouvons traiter des projets de conception et développement de produit, de prototypage rapide, de conception et réalisation d’outils et de dispositifs médicaux automatisés, ainsi que d’assemblages complexes de produits médicaux ou de consommation.