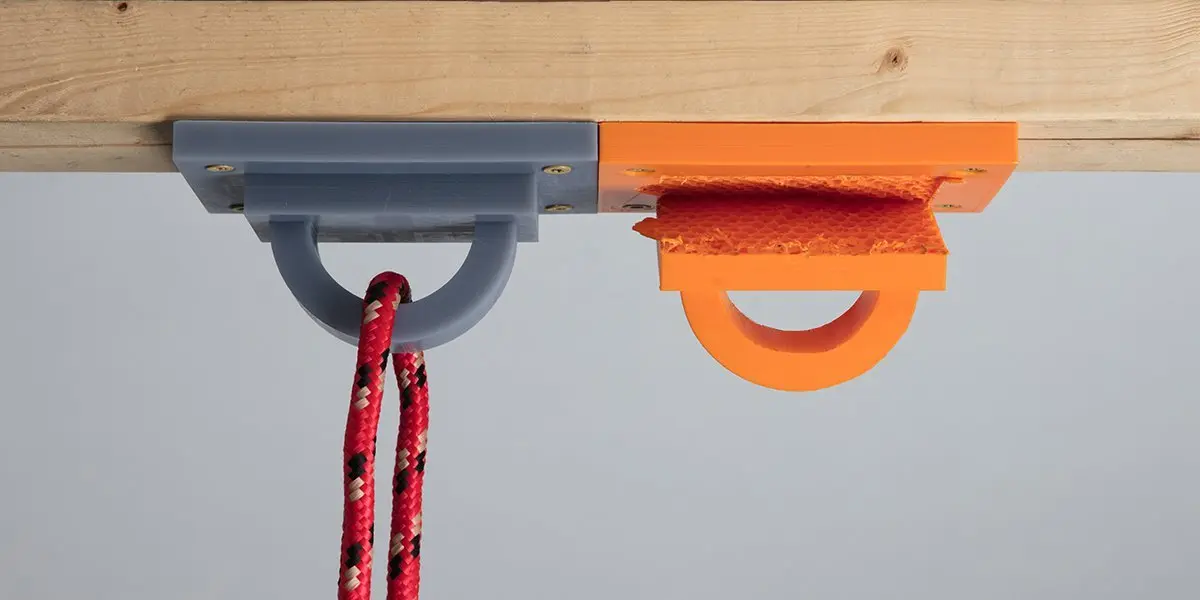
Il faut prendre en compte plusieurs aspects lors de la préparation d'un objet pour l'imprimer en 3D. L'un d'entre eux est l'orientation de l'objet sur la plateforme de fabrication : La surface d'adhérence est-elle suffisante, les surplombs non soutenus sont-ils minimisés, y a-t-il suffisamment de place entre les objets ?
En plus de tout cela, il faut également considérer l'anisotropie, surtout si la pièce doit supporter des contraintes importantes.
Dans ce contexte, l'anisotropie se définit comme des propriétés physiques variant selon la direction. Par exemple, un objet imprimé en 3D peut présenter des différences d'allongements à la rupture ou encore de rigidité selon les axes X, Y et Z.
Les concepts d'isotropie et d'anisotropie sont souvent abordés en impression 3D, mais dans certains cas les hypothèses sont faites sur la base de généralisations.
Elles ne seront souvent envisagées que pour des imprimantes à dépôt de filament fondu (FDM), qui fondent des polymères et les solidifient sous la forme de la pièce finale, et font des raccourcis intuitifs pour étendre cette définition de l'anisotropie structurelle à d'autres techniques d'impression, telles que l' impression 3D par stéréolithographie.
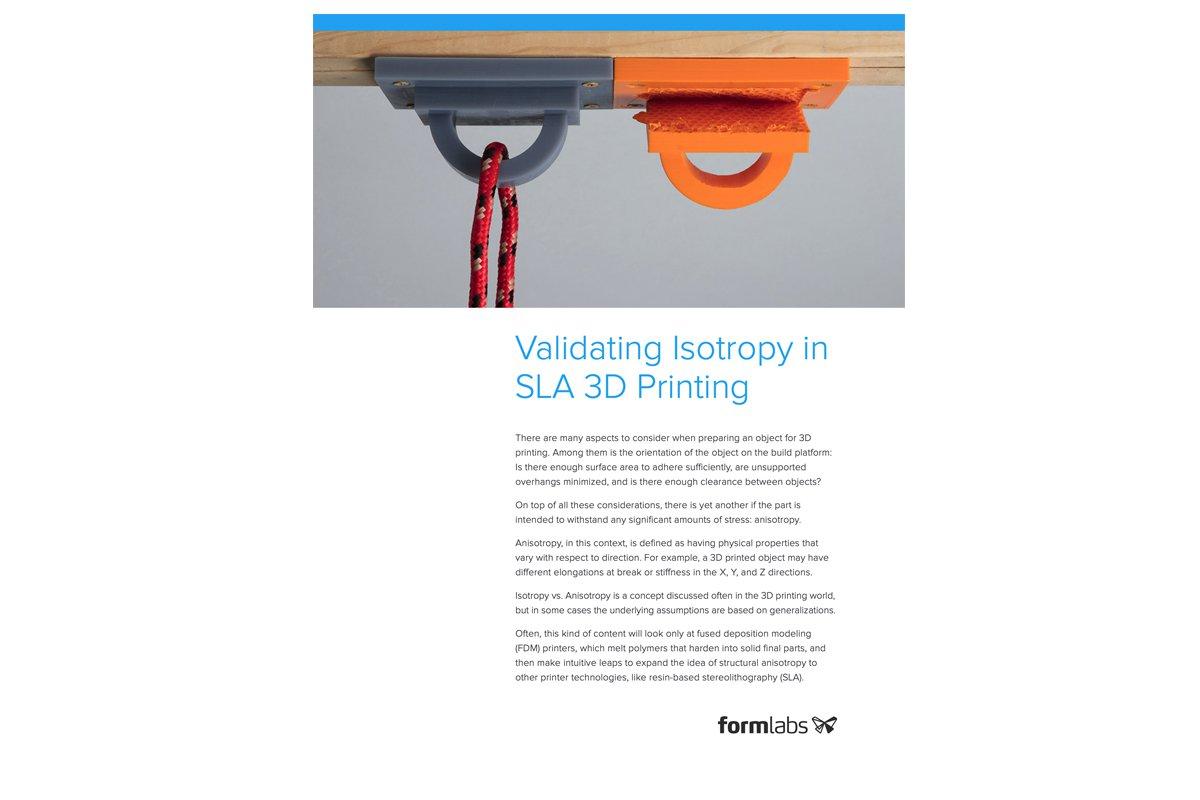
Validation de l'isotropie en impression 3D SLA
Pas assez de temps pour tout lire maintenant ? Téléchargez un PDF de cet article.
Télécharger le PDFPourquoi les impressions FDM sont anisotropes
Les imprimantes 3D fabriquent les pièces couche par couche, mais elles utilisent des méthodes différentes pour le faire. Cela a des effets importants sur la composition moléculaire des pièces produites par chacune des méthodes.
Par exemple, le procédé FDM fond des couches de plastique les unes sur les autres. L'adhérence est alors créée mécaniquement (et non chimiquement). Comme le démontre cette expérience, les surfaces des couches FDM n'adhèrent pas complètement les unes aux autres. Même quand la couche précédente est partiellement fondue, les couches environnantes n'adhèrent que partiellement entre elles.
C'est pourquoi les objets imprimés par FDM présentent des propriétés mécaniques différentes selon la direction d'impact de la contrainte mécanique appliquée, et qu'ils sont moins denses que les mêmes objets produits par d'autres méthodes, telles que le moulage par injection. C'est aussi la raison pour laquelle il est difficile de produire des objets étanches par impression FDM : Les impressions FDM sont pleines de cavités et de trous microscopiques.
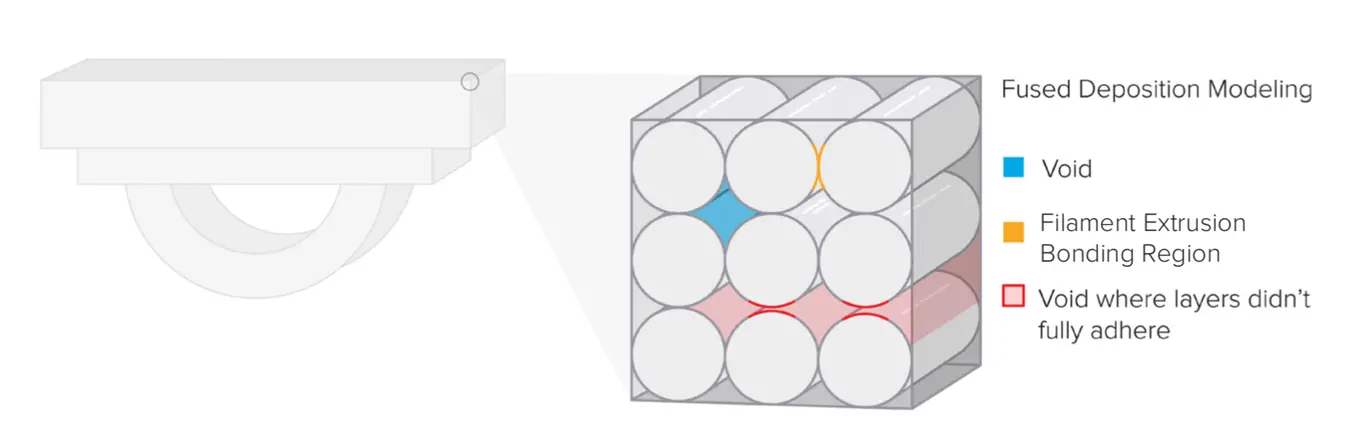
Les imprimantes 3D FDM forment des couches par dépôt de lignes de PLA ou d'ABS. Ce procédé fait que les couches ne sont pas liées entre elles aussi fortement que les lignes (extrusion du filament) elles-mêmes. Il se forme des cavités entre les lignes de forme ronde et il est possible que les couches n'adhèrent pas complètement les unes aux autres.
Lorsqu'on examine cet arrangement au niveau moléculaire, on constate une différence nette entre les forces à l'intérieur de chaque couche et les forces qui maintiennent les couches ensemble : Chaque ligne de PLA ou d'ABS déposée est composée de chaînes de polymères très imbriquées, qui se maintiennent ensemble très fortement. Elles sont donc bien solides, dures et rigides.
Lorsque de nouvelles lignes sont déposées au-dessus ou sur le côté d'une ligne, il est extrêmement difficile, voire impossible, d'obtenir la même imbrication entre chaque ligne, ce qui produit des jonctions dans les zones de liaison entre les fibres qui sont bien moins solide et rigides.
Cela signifie qu'étant donné un motif particulier de dépôt de lignes, la pièce sera plus solide dans la direction de la ligne déposée, et moins solide les long des axes qui sont d'abord constitués par ces zones de liaison entre les fibres, à savoir les deux axes orthogonaux à l'axe de la ligne.
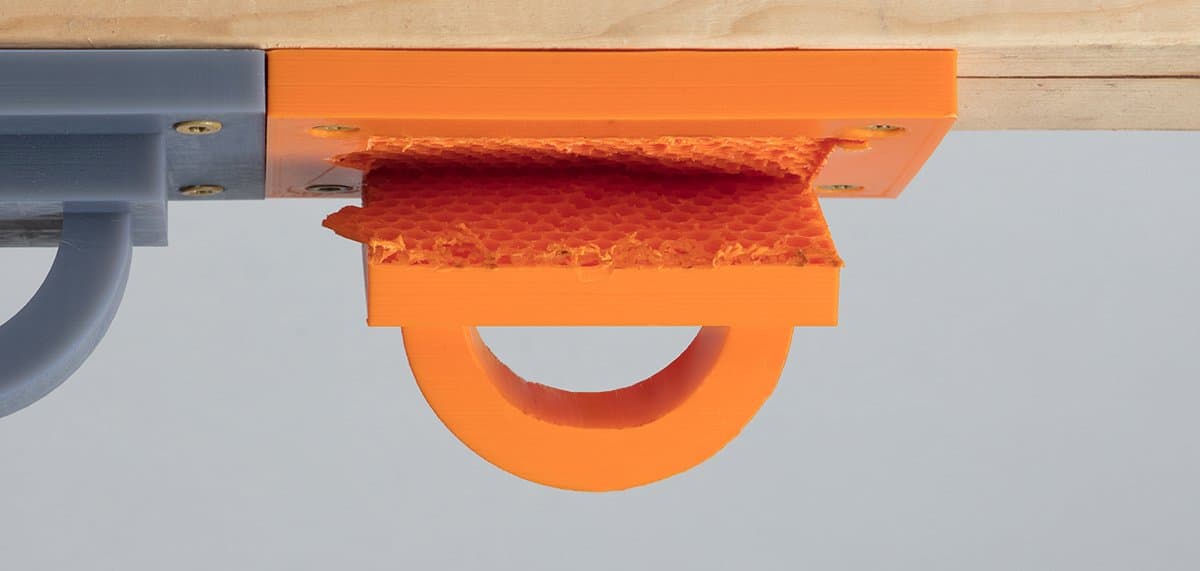
Les impressions FDM sont anisotropes. Lorsque un poids est appliqué, les impressions FDM peuvent ne pas le supporter si elles ne sont pas orientées correctement ou modélisées de façon à prendre en compte cette anisotropie.
En bref, les pièces FDM ne présentent pas la même solidité dans toutes les directions et ne peuvent être isotropes. Cela signifie que leur orientation est à prendre en compte lors de la conception et l'impression de pièces supportant des charges.
Pourquoi les impressions SLA sont-elles isotropes ? Théorie
En impression 3D SLA avec des résines, il n'existe aucune différence entre les liaisons chimiques qui constituent les couches individuelles, et les forces qui maintiennent les couches ensemble.
À la formation de chaque couche, les monomères de la résine forment des liaisons covalentes qui confèrent une forte cohésion latérale, mais la réaction de polymérisation n'est pas complète. Le processus d'impression est modulé de façon à ce que la couche reste dans un état intermédiaire de la réaction, appelé « état brut ».
Une différence très importante entre cet état brut et l'état de polymérisation complète est qu'il subsiste des groupes polymérisables à la surface de la couche avec lesquels les couches suivantes peuvent établir des liaisons covalentes.
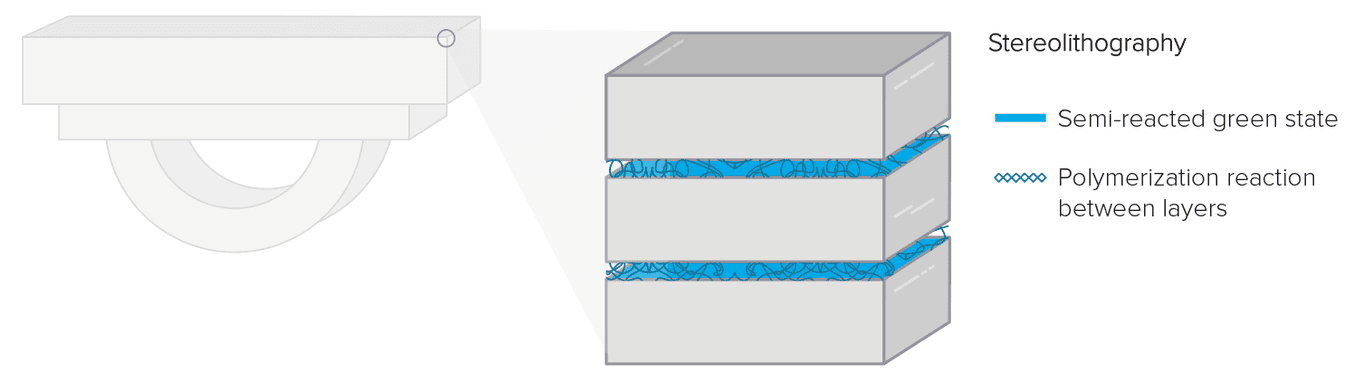
Dans les impressions SLA, il n'y a plus de différence au niveau moléculaire entre l'axe Z et le plan XY en termes de liaisons chimiques : chaque pièce continue fabriquée par une imprimante stéréolithographique constitue un réseau continu de polymères.
Pendant la polymérisation de la couche suivante, la réaction va concerner les groupes de la couche précédente, formant ainsi des liaisons covalentes non seulement latéralement mais aussi avec la couche précédente. Cette réticulation est propre à tous les procédés stéréolithographiques.
Cela signifie qu'il y a peu ou pas de différence au niveau moléculaire entre l'axe Z et le plan XY en termes de liaisons chimiques : chaque pièce continue fabriquée par une imprimante stéréolithographique est une seule molécule. Comme les lignes SLA sont complètement liées à leurs voisines, il n'y a pas non plus de cavités ou de microfissures typiques des impressions FDM. Ces pièces imprimées sont étanches et complètement denses.
Les pièces imprimées par SLA préparées de la sorte pour tout usage pratique sont isotropes.
La théorie est bonne, les données pratiques encore meilleures
À quoi cela ressemble-t-il en pratique ? Si votre pièce imprimée en SLA doit subir des contraintes, faut-il vous inquiéter de son orientation ? Nous avons décidé de mettre la théorie en pratique en utilisant une Form 2, de Clear Resin et notre banc d'essai de résistance à la traction.
Nous l'avons utilisé pour mesurer les différences de résistance maximum et de module de Young entre des impressions en SLA et en FDM.
Pour obtenir des mesures dans tout le spectre angulaire, nous avons imprimé des éprouvettes de traction ASTM de type IV, à 15 degrés d'intervalle, de 0 (plate par rapport au plan XY) à 90 degrés (droite vers le haut et vers le bas). Chaque ensemble d'éprouvettes a été lavé dans de l'alcool isopropylique, post-polymérisé puis placé dans le banc d'essai de traction.
Les éprouvettes ont été étirées à vitesse constante jusqu'à la rupture, et leurs forces de réaction ont été enregistrées. À partir de ces données, il est possible de tirer une foule de propriétés des matériaux, les plus pertinentes étant la résistance maximum et le module de Young.
Contrainte maximum
La contrainte maximum est la traction constante la plus haute que l'éprouvette peut supporter avant la rupture. C'est ce que signifie ce qu'on entend généralement par un matériau « solide ».
Il est facile voir comment la contrainte maximum peut servir de mesure de l'anisotropie : une pièce avec des liaisons chimiques faibles entre les couches présentera une résistance réduite lorsque les forces de traction s'exerceront perpendiculairement au plan XY.
C'est en fait exactement ce qui s'est passé dans l' expérience précédente sur des impressions FDM, pour lesquelles la résistance à la déformation selon l'axe Z d'une pièce était d'environ 55 % celle selon l'axe X.
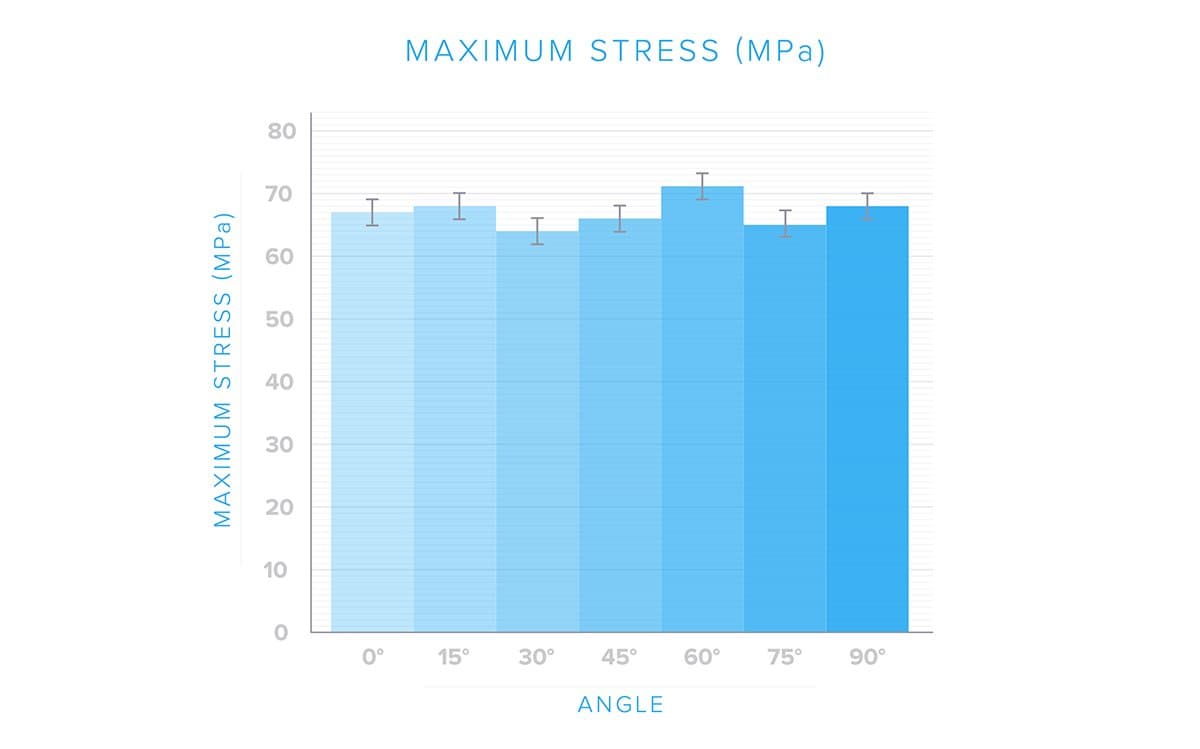
La contrainte maximum reste constante quelles que soient les directions. Cela signifie que la pièce est isotrope en ce qui concerne la résistance à la rupture par traction.
Si les pièces SLA étaient anisotropes, nous nous serions attendus à observer une décroissance de la contrainte maximum lorsque l'angle approcherait 90 degrés.
Pour valider ces résultats, nous avons également enregistré les valeurs du modules de Young dans les différents directions.
Modules de Young
Le module de Young est une mesure de la rigidité et une indication de la flexibilité d'un objet. Il est particulièrement important pour les ingénieurs qui doivent prendre des décisions de conception sur la base des contraintes et des déformations, pour une application particulière.
Comme pour la résistance à la déformation, il est probable que des liaisons plus faibles entre les couches fassent décroître le module de Young, ce qui en fait une autre mesure pertinente de l'isotropie des pièces imprimées par SLA.
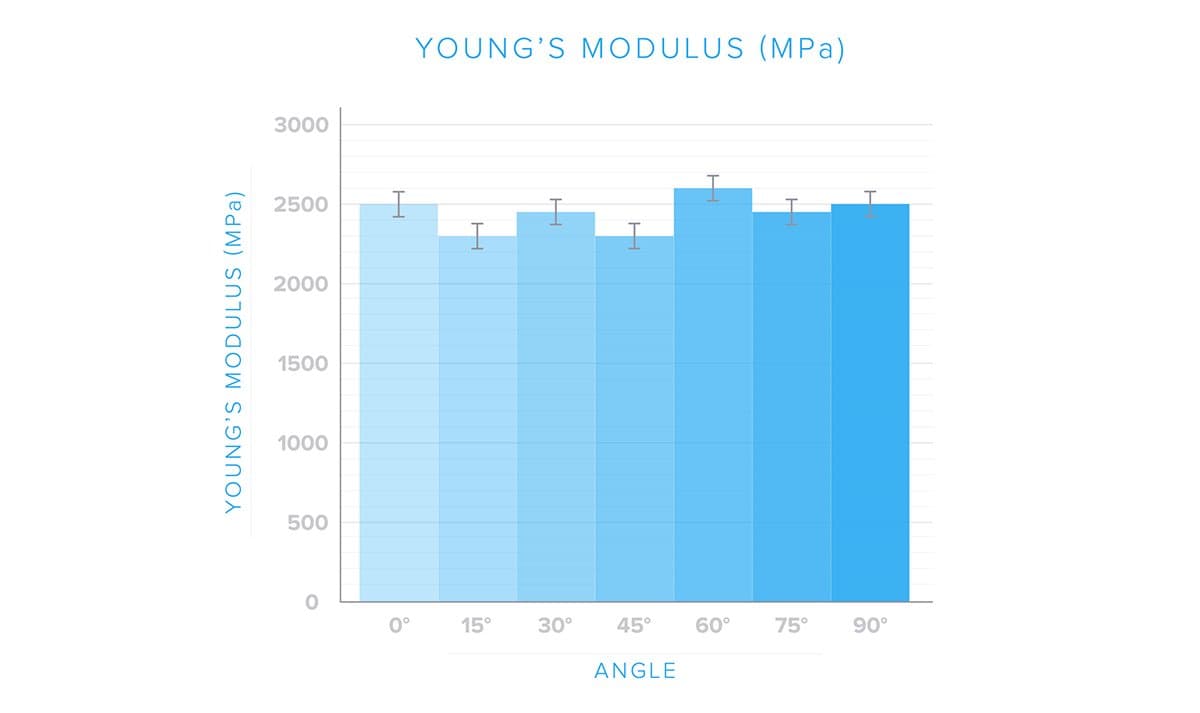
De la même façon que pour la résistance maximum, le module de Young reste pratiquement constant dans toutes les directions. Le module de Young est donc également isotrope par rapport aux directions de fabrication.
Comme prévu, les données de module de Young se rassemblent autour d'une ligne horizontale, indiquant là encore que l'orientation de l'impression par SLA n'a pas d'effet sur les propriétés du matériau, et confirmant l'hypothèse selon laquelle les pièces imprimées par SLA sont bien isotropes.
Le verdict : Les pièces imprimées par stéréolithographie sont isotropes
Plusieurs preuves pour une même conclusion : Les imprimante 3D SLA produisent des pièces qui sont aussi solides et dures selon l'axe Z que selon les axes X et Y, quelle que soit la façon dont vous les découpez (et vous les imprimez) en couche. C'est pourquoi l'impression 3D par SLA est idéale pour les applications d'ingénierie pour lesquelles les propriétés des matériaux ont de l'importance.
Consultez notre page Matériaux pour en savoir plus sur les résines Formlabs, et demandez un échantillon gratuit pour vous rendre compte par vous-même de leur qualité.