Comment Vertiball fabrique des prototypes fiables reproduisant des pièces moulées par injection
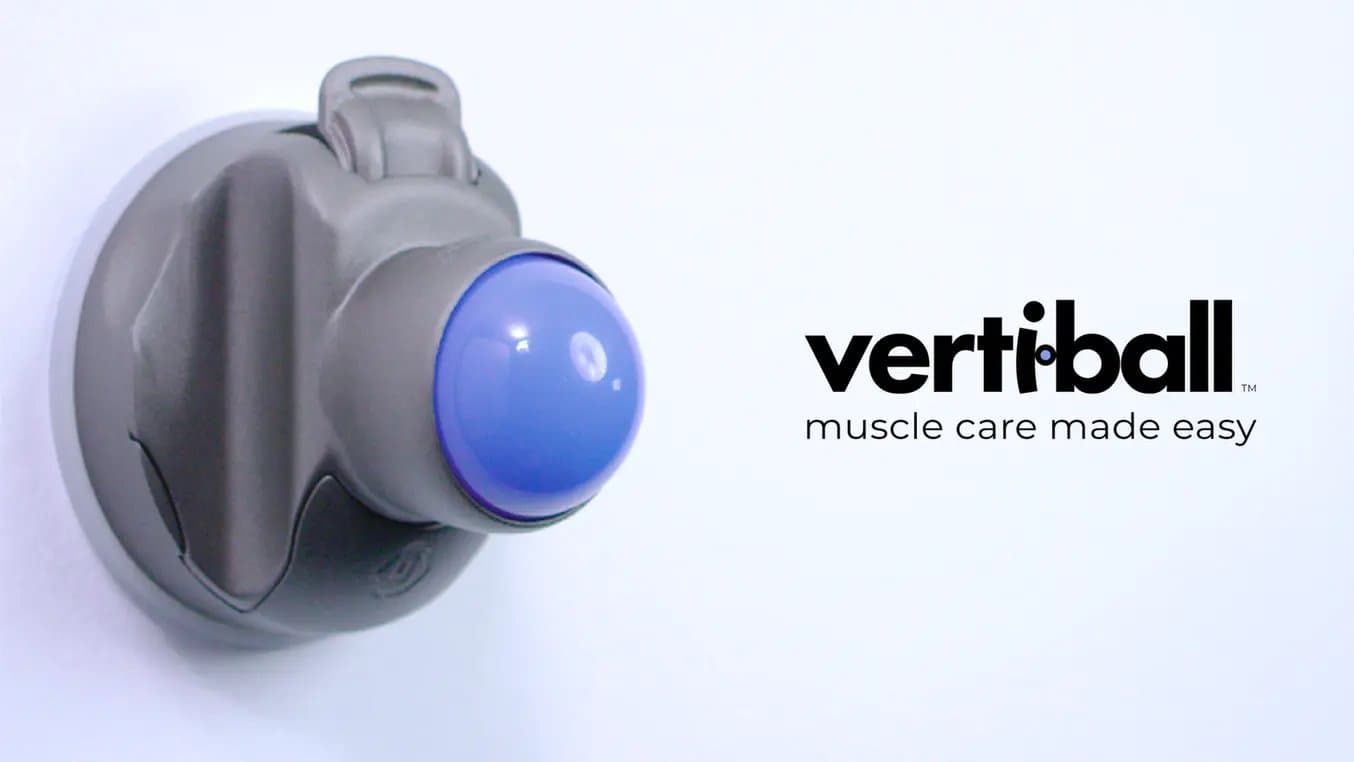
Le fondateur et PDG de Vertiball, Curtis Kennedy, a entrepris de changer la façon dont les douleurs musculaires et dorsales sont traitées. Ayant lui-même souffert de douleurs au dos, Curtis a testé de nombreuses thérapies à domicile recommandées par les médecins, notamment le massage des zones douloureuses avec une balle de tennis. Pour Curtis – et pour beaucoup d'autres personnes cherchant à soulager leur douleur et à éviter les blessures – masser une zone spécifique du dos en étant allongé sur une balle de tennis n'est pas une méthode facile à maîtriser.
Curtis a donc imaginé un moyen de monter une boule sur une surface verticale, permettant aux utilisateurs de se concentrer sur la zone exacte qui nécessite un massage thérapeutique. L'innovation clé de Vertiball est son système de support mobile breveté,™ une ventouse de qualité industrielle qui peut se fixer sur des surfaces lisses non poreuses comme les cloisons peintes, le métal ou le bois. L'avant de l'appareil contient une boule de massage en rotation libre qui glisse et se verrouille sur le mécanisme de base. L'appareil est petit et portable, ce qui permet aux utilisateurs de l'emporter du vestiaire de la salle de sport à leur propre salon.
« Je sais que Vertiball a la capacité de changer la façon dont nous traitons les douleurs dorsales et musculaires [et de donner] à ses utilisateurs la possibilité de contrôler leur douleur et de trouver le soulagement qu'ils recherchent. »
Curtis Kennedy, PDG de Vertiball
Actuellement, les ingénieurs de Vertiball utilisent Autodesk Fusion 360 pour développer leurs concepts produits et en faire des modèles CAO, puis ils utilisent leur imprimante 3D stéréolithographique (SLA) Form 3 pour prototyper et valider ces concepts. Cependant, il a fallu beaucoup d'essais et d'erreurs pour aboutir à ce processus de prototypage.
La découverte d'un processus de travail SLA fiable
Curtis a commencé à concevoir Vertiball alors qu'il étudiait à l'Université du Nouveau-Brunswick, en utilisant les outils qui étaient à la disposition des étudiants sur le campus. Il a commencé à créer des prototypes à l'aide d'imprimantes 3D à dépôt de fil fondu (FDM). Cependant, alors que Curtis pensait être arrivé à une conception finale, il s'est avéré que les échantillons moulés par injection qu'il avait commandés présentaient des problèmes d'assemblage. Il s'est rendu compte que des composants critiques de son prototype manquaient de précision, en raison du rétrécissement subi pendant le processus d'impression FDM.
Étant donné que Vertiball est un produit final, sa conception est en réalité assez exigeante. Comme le dispositif est conçu pour un usage quotidien, les utilisateurs actionneront le mécanisme de verrouillage des centaines, voire des milliers de fois. De plus, le produit comprend du plastique moulé par injection qui s'adapte à du matériel métallique, les composants avant et arrière doivent glisser l'un sur l'autre sans se fissurer, et la bille doit pouvoir tourner librement avec une faible friction. Pour ces raisons, l'équipe a choisi le polyamide 6, un matériau durable à faible friction, pour fabriquer les pièces moulées finales.
Pour Curtis, il ne faisait aucun doute qu'il lui fallait des prototypes imprimés très précis qui reproduisaient la précision et la finition de surface des pièces moulées par injection. Dans un premier temps, Curtis a demandé à Formlabs de lui fournir un échantillon personnalisé en Durable Resin afin de tester une conception modifiée. En tenant sa pièce imprimée en 3D SLA dans ses mains, il a pu se décider pour une conception finale qui pourrait être envoyée à un fabricant de moulage par injection. Plus tard, son équipe a investi dans sa propre imprimante Form 3.
« La Form 3 est essentielle dans notre flux de travail, car c'est la seule imprimante 3D que nous possédons qui peut imprimer avec la précision dimensionnelle nécessaire pour tester correctement les nouveaux prototypes et les comparer à la fonctionnalité qui serait obtenue par le moulage par injection plastique. »
Curtis Kennedy
En ce qui concerne le choix du logiciel CAO, Curtis et son équipe ont suivi un processus similaire. Ils ont fini par trouver un logiciel CAO que tous les concepteurs appréciaient. Selon Curtis, « après avoir utilisé divers autres programmes CAO, nous avons trouvé que Fusion 360 répondait le mieux à nos besoins. L'interface utilisateur est optimisée pour être intuitive, et lorsque nous l'avons comparée à d'autres programmes de modélisation 3D, nous avons constaté qu'elle était beaucoup plus simple à utiliser. »
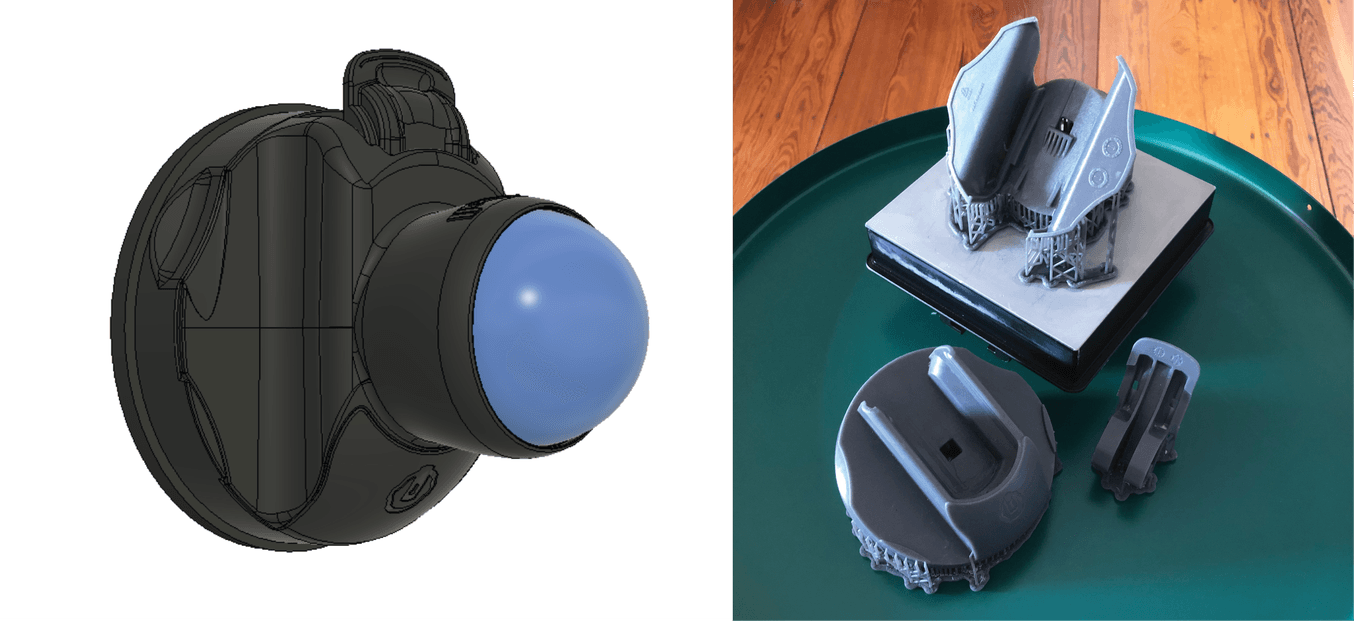
La conception de Vertiball dans Fusion 360, puis imprimée avec la Form 3.
Fusion 360 permet également aux concepteurs de Vertiball de visualiser les performances de leur produit dans des conditions réalistes. Ils utilisent l'environnement de simulation Fusion 360 pour effectuer des analyses de contraintes sur des pièces soumises à des charges spécifiques, afin de pouvoir modifier et optimiser les zones du modèle qui ne répondent pas encore à leurs attentes. Bien qu'une grande partie de leur conception itérative se fasse en simulation, l'équipe reste convaincue que les prototypes physiques sont essentiels. « Une nouvelle conception peut sembler géniale sur l'ordinateur, mais la seule façon d'en être certain est de la tester. Une fois que nous avons validé la fonctionnalité théorique d'une conception par simulation, nous passons directement au prototypage en utilisant la Form 3. »
Le produit phare de Vertiball a été financé avec succès sur Kickstarter en 2019, où les fondateurs ont reçu huit fois la somme qu'ils espéraient récolter. Ils reçoivent encore des critiques élogieuses sur leur produit de la part de kinésithérapeutes et d'athlètes professionnels, dont les joueurs de la NFL CeeDee Lamb et Minkah Fitzpatrick. Curtis et son équipe continuent également d'innover en matière de produits de soulagement musculaire qui répondent à la devise de leur entreprise : « Si nous pouvons nous sentir au top, nous pouvons être au top. »
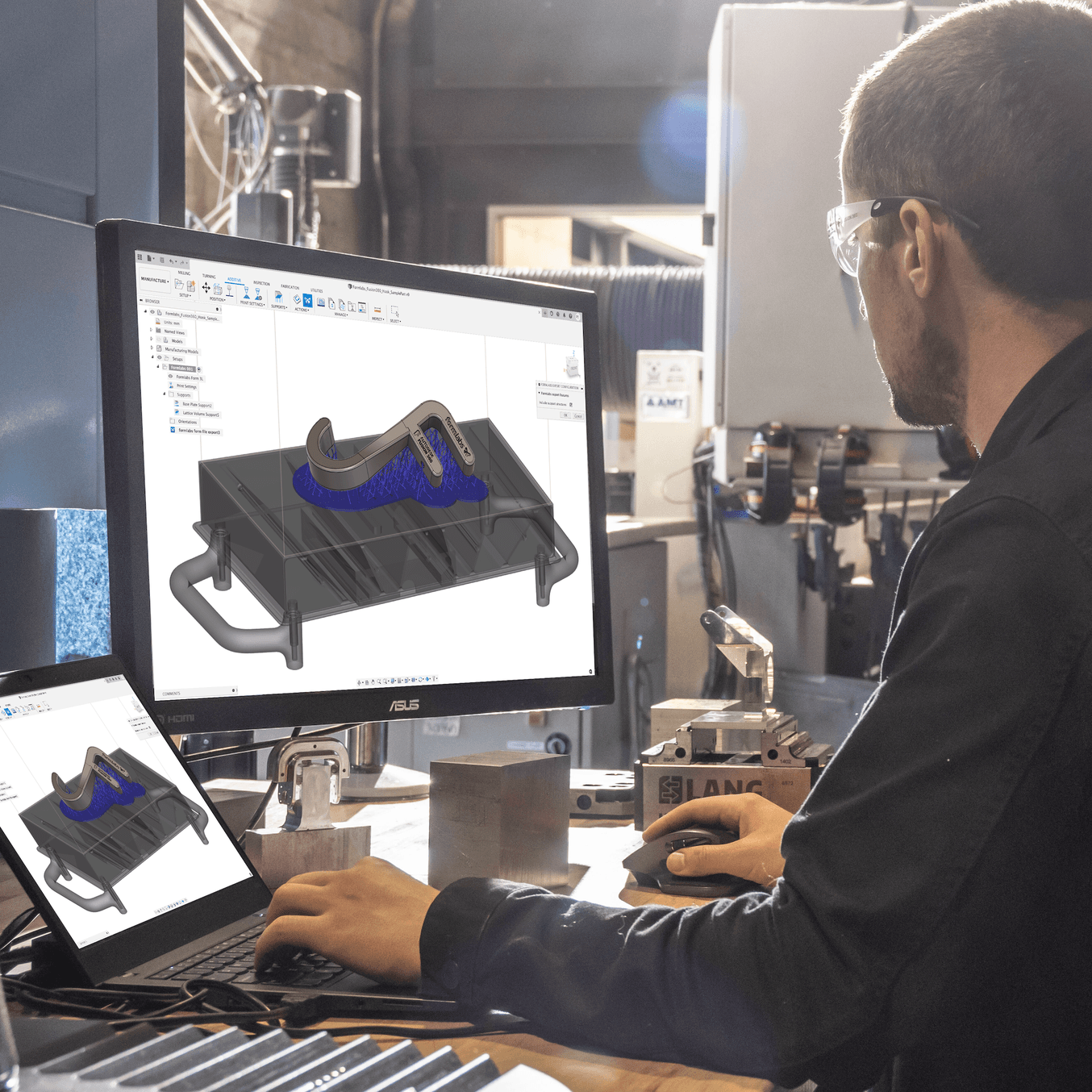
Intégration de Formlabs avec Fusion 360
Formlabs et AutodeskFusion 360 se sont associés pour optimiser vos procédures numériques grâce à un nouveau logiciel CAO intégrant l’impression 3D.Visitez notre centre d'intégration pour découvrir les toutes dernières fonctionnalités de Fusion 360 pour l'impression SLA, lire d'autres témoignages d'utilisateurs et télécharger notre guide de conception.