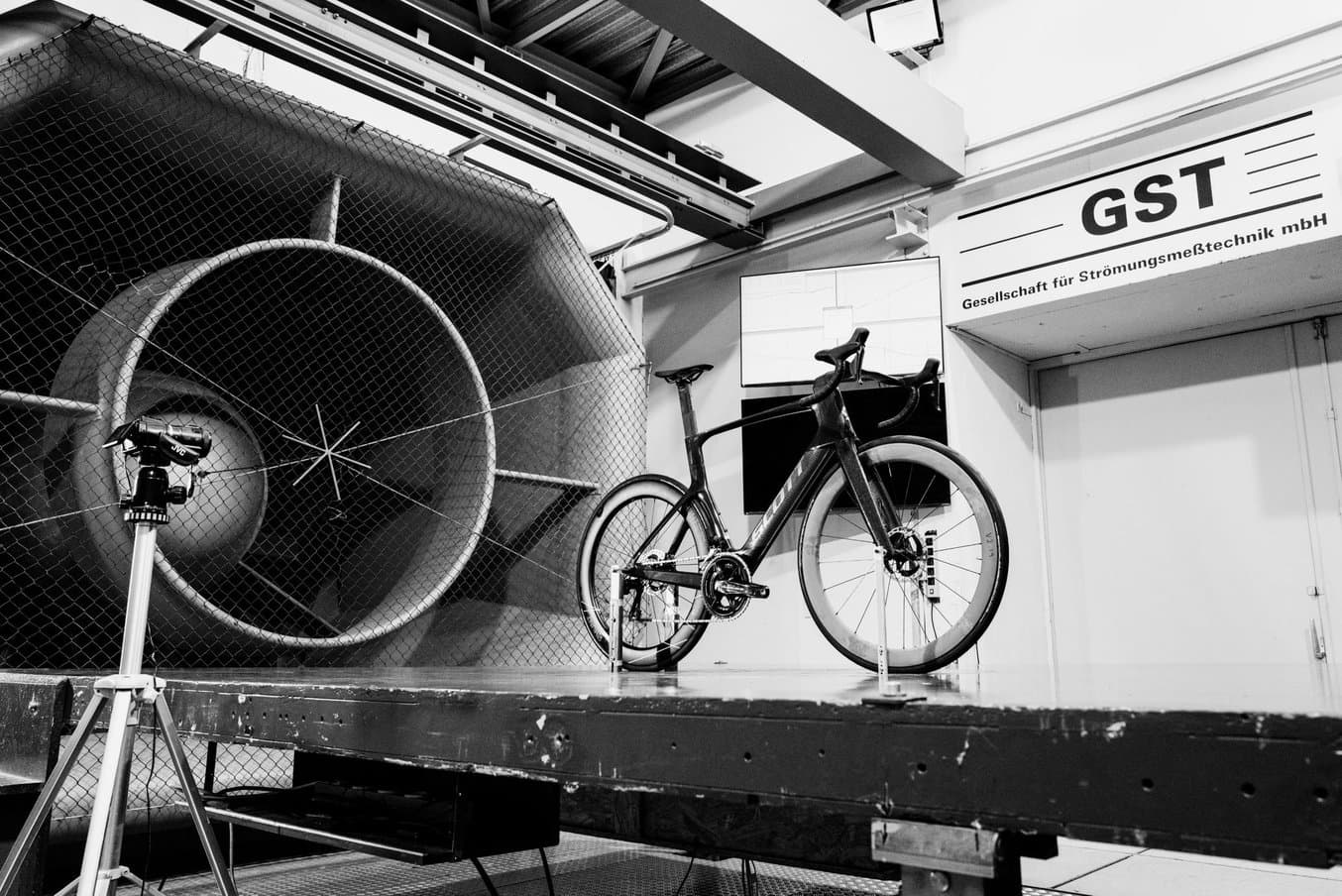
Hunt Bike Wheels testa i profili dei cerchi delle sue bici nella galleria del vento di Friedrichshafen, nella Germania meridionale.
In tutto il mondo, un numero sempre più elevato di persone si sta avvicinando al ciclismo, che sia per andare al lavoro, esplorare la natura, allenarsi o gareggiare. Per le aziende produttrici di biciclette è quindi fondamentale stare al passo con gli sviluppi tecnologici e le tendenze in continua evoluzione. The Rider Firm è l'azienda che gestisce il marchio Hunt Bike Wheels, leader mondiale nella vendita al dettaglio di biciclette, nonché altri brand specializzati in attrezzature, componenti e bici all'avanguardia, come Privateer Bikes, Cairn Cycles e Dissent 133.
Per raggiungere l'obiettivo di produrre bici e componenti ad alte prestazioni ma dal prezzo accessibile, The Rider Firm deve poter contare su un processo di sviluppo più agile ed efficiente dei marchi di biciclette tradizionali con budget più elevati. L'adozione della stampa 3D in-house, con l'acquisto della stampante 3D SLA di grande formato Form 3L, è stata l'ultima iniziativa dell'azienda per dare impulso all'innovazione e ridefinire il proprio workflow.
Nonostante il maggiore centro di produzione per il settore del ciclismo si trovi a Taiwan, il processo di sviluppo del prodotto di The Rider Firm si svolge nel Regno Unito, luogo di nascita dell'azienda, dove il team sfrutta la Form 3L per la maggior parte del lavoro, soprattutto per la prototipazione. Dan Hicks, ingegnere di sviluppo presso Privateer Bikes, e Patrick Brown, ingegnere progettista presso Hunt Bike Wheels, ci hanno svelato alcuni aspetti interessanti del loro workflow, raccontandoci come la Form 3L supporta i team ingegneristici nella creazione di nuovi prodotti e nella costante ricerca di innovazione.
Hunt Bike Wheels: stampa 3D di prototipi funzionali di cerchi in scala reale per test in galleria del vento
La scelta del nome "Hunt Bike Wheels" non è stata casuale: "hunt" in inglese significa "andare a caccia" ed è un riferimento alla costante ricerca da parte dell'azienda dei più piccoli dettagli che completino il prodotto. L'instancabile team ingegneristico mette in campo tutta la propria esperienza per creare ruote che offrono prestazioni eccezionali su vari tipi di terreni. Attraverso rigorosi processi di ricerca e sviluppo e test, il team punta a migliorare velocità, stabilità ed efficienza ottimizzando l'aerodinamica delle ruote. I cosiddetti guadagni marginali sono il fattore più determinante nel ciclismo professionistico. La differenza di resistenza aerodinamica tra una coppia di ruote e l'altra può essere minima, tra il 2% e il 5% a 45 chilometri all'ora, ma quei pochi secondi possono fare la differenza tra il primo e il decimo posto in classifica.
Patrick Brown ci ha illustrato il processo di sviluppo delle ruote. Questo inizia con la progettazione da parte del team ingegneristico di diversi profili di cerchi, che vengono poi testati tramite fluidodinamica computazionale (CFD), ovvero una galleria del vento virtuale. Le analisi CFD consentono al team di identificare i profili di cerchi con le prestazioni migliori, che verranno in seguito testati in contesti reali tramite prototipi stampati in 3D.
Per la nuova coppia di ruote LIMITLESS, il team ha testato circa 45 profili di cerchi diversi tramite analisi CFD e ha identificato quelli con la più bassa resistenza aerodinamica e le migliori caratteristiche di resistenza al vento trasversale. Nei test si sono in particolare distinte quattro ruote anteriori e tre ruote posteriori, che il team ha stampato in 3D e testato nella galleria del vento di Friedrichshafen, nella Germania meridionale.
Grazie al grande volume di stampa della Form 3L, è stato possibile stampare ogni ruota in cinque o sei sezioni, a seconda del numero di fori dei raggi usati in ciascuna sezione, e posizionare nella piattaforma di stampa quattro sezioni alla volta. Dopo la polimerizzazione post-stampa e la post-elaborazione, le parti stampate sono state incollate tra loro con resina epossidica e assemblate con mozzi, raggi e pneumatici per creare prototipi funzionali.
In merito all'utilizzo della Grey Pro Resin, Patrick Brown afferma che le ruote stampate in 3D con questo materiale "sono un po' morbide, ma capaci di assorbire circa il 65% della tensione di una coppia di ruote in fibra di carbonio. Si possono ottenere in modo abbastanza immediato prototipi realistici, di qualità adeguata al test in galleria del vento".
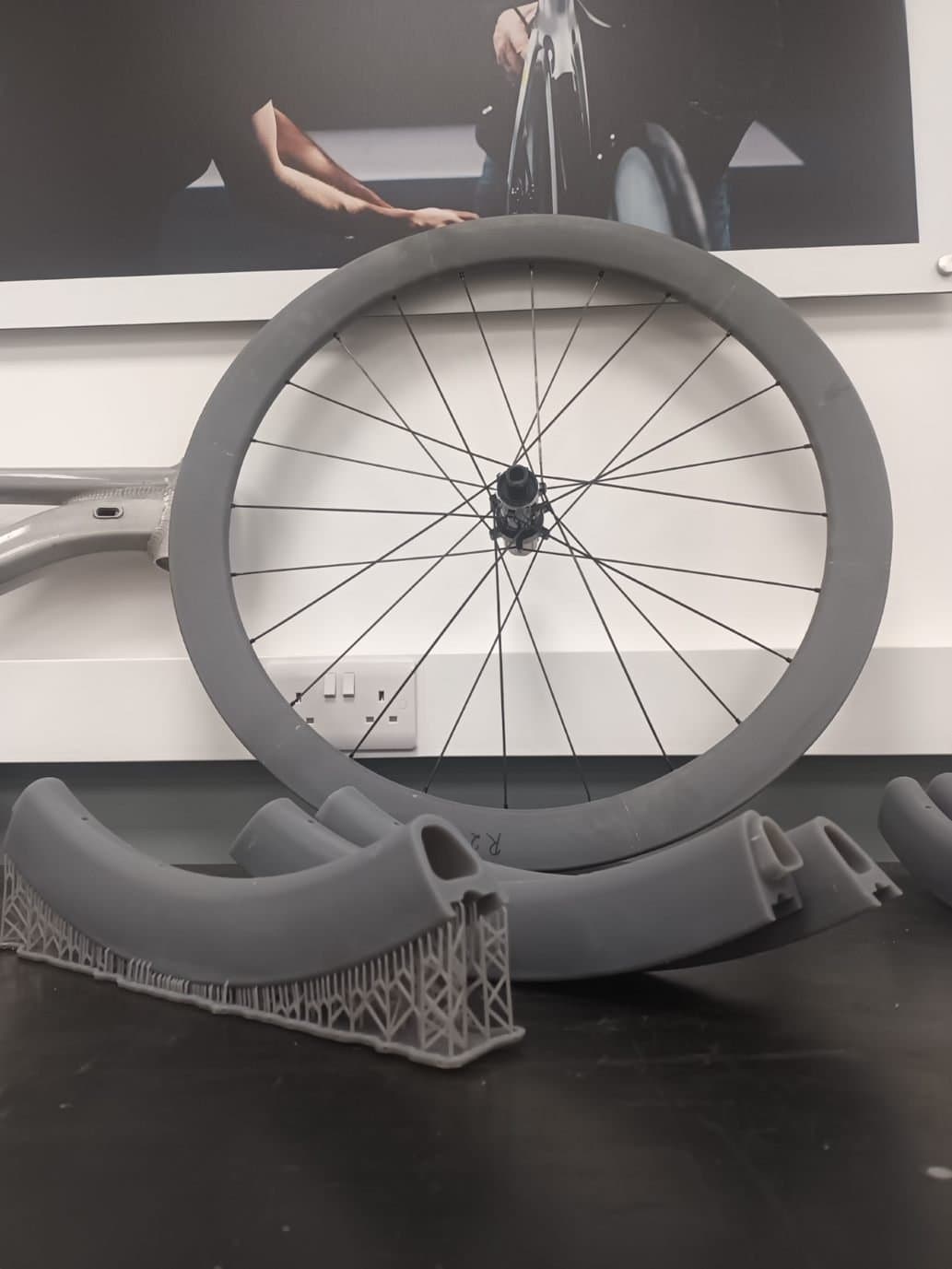
La Grey Pro Resin è un ottimo materiale per la prototipazione, poiché è in grado di assorbire circa il 65% della tensione di una coppia di ruote in fibra di carbonio.
In passato, Hunt Bike Wheels avrebbe affidato la stampa 3D delle varie sezioni di ruota a un'azienda esterna, con numerosi svantaggi. Innanzitutto, il team ingegneristico avrebbe dovuto spedire i profili delle ruote finalizzati con due o tre mesi di anticipo, con conseguente rallentamento del processo e riduzione della flessibilità. Ma adesso che utilizzano la Form 3L, ammette Brown, per il loro ultimo progetto "sono riusciti a stampare gli ultimi pezzi poco prima [di lasciare l'ufficio]", ovvero hanno potuto eseguire iterazioni fino all'ultimo minuto. Inoltre, le parti esternalizzate non erano abbastanza resistenti da consentire il gonfiaggio dello pneumatico fino alla giusta pressione e le crepe presenti su alcune parti rendevano queste ultime inadatte ai test.
"Ora posso eseguire simulazioni molto più lunghe e continuare a sviluppare nuovi profili. Avere questa flessibilità in-house è un grande vantaggio per noi."
Patrick Brown, ingegnere progettista presso Hunt Bike Wheels
"È importante riuscire a gonfiare gli pneumatici fino alla pressione che consente loro di assumere la giusta forma sulla ruota. Per noi è davvero essenziale non solo che le stampe siano precise da un punto di vista geometrico, ma che abbiano anche la giusta resistenza per ottenere il profilo aerodinamico adatto nel complesso". Durante il processo di sviluppo, la Grey Pro Resin ha soddisfatto questi rigidi requisiti, rivelandosi un materiale di grande precisione geometrica e dalla straordinaria capacità di resistere fino a tre bar e mezzo di pressione esercitata dagli pneumatici. Brown ha inoltre sottolineato che l'eccellente finitura superficiale conferita dalla Grey Pro Resin è stata un elemento fondamentale durante i test per l'aerodinamica.
"[Nella galleria del vento] le ruote girano su un rullo a 45 chilometri all'ora."
Patrick Brown, ingegnere progettista presso Hunt Bike Wheels
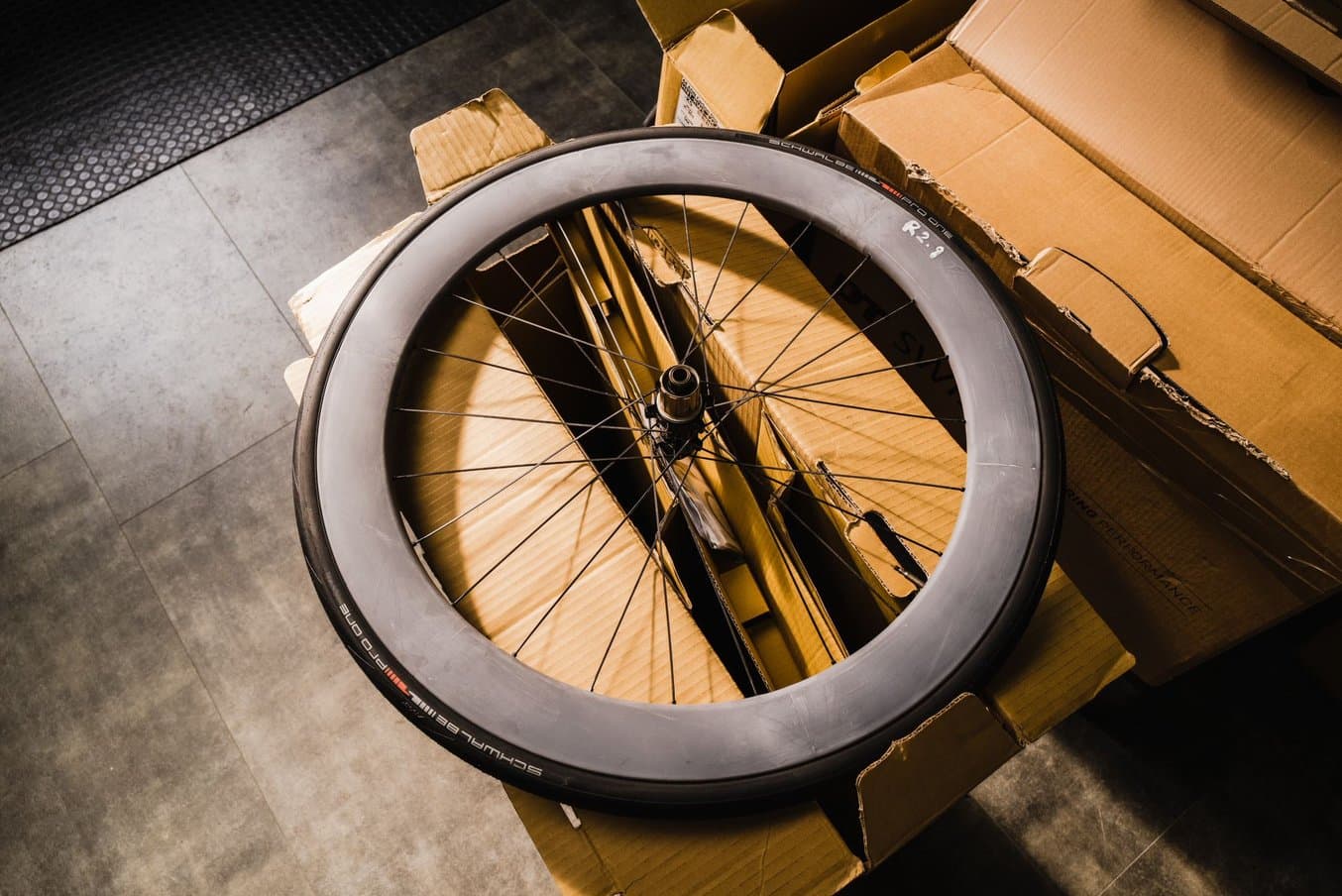
L'eccellente finitura superficiale conferita dalla Grey Pro Resin è stata un elemento fondamentale durante i test per l'aerodinamica.
La stampa 3D in-house consente inoltre al team ingegneristico di eseguire più iterazioni, diminuendo al contempo i costi. Quando esternalizzava questo processo, Hunt Bike Wheels spendeva oltre 2000 € per un solo prototipo di cerchio. Grazie alla Form 3L, questi costi sono stati ridotti a circa 200 €, con un risparmio del 90%.
"Ciò ci consente di portare alla galleria del vento un maggior numero di ruote, in modo da convalidare studi di CFD con svariati prototipi. Possiamo anche saltare tre o quattro cicli di iterazione del prodotto per ottenerne uno di qualità. Adesso sappiamo che ogni nuovo prodotto che lanciamo sarà sempre di qualità eccezionale", afferma Hicks.
Oggi, la Form 3L è una parte essenziale del modello aziendale di The Rider Firm poiché consente all'azienda di essere sempre un passo avanti alla concorrenza. "Gestendo la prototipazione in modo intelligente e le operazioni aziendali in maniera efficiente, siamo in grado di offrire ruote con le stesse prestazioni aerodinamiche di aziende più grandi, ma a metà prezzo", afferma Hicks.
Privateer Bikes: telai di bici completi e prototipazione rapida per superare i limiti
Il team ingegneristico di Privateer Bikes utilizza la Form 3L per un'ampia gamma di applicazioni di prototipazione, inclusi telai di bici completi ed elementi di protezione del telaio.
Nell'ambito della progettazione di una nuova serie di bici, il team ingegneristico di Privateer Bikes ha stampato telai completi e alcune delle sezioni più complesse del telaio in varie misure. Ciò gli ha permesso di inserire componenti all'interno del telaio, ad esempio cuscinetti e forcelle di sospensione incastrati a pressione, per garantire la fattibilità ed eseguire un secondo controllo sui giochi per diverse dimensioni di telaio. "Possiamo controllare i giochi, l'assemblaggio, l'aderenza dei componenti o se si verificano urti quando si muovono le sospensioni."
Inoltre, la stampa del telaio completo ha permesso alla persona responsabile della grafica in-house di verniciare la parte con uno spray per provare le idee di decorazione e realizzare decalcomanie per la nuova serie. I telai sono stati stampati in 3D con la Grey Pro Resin in molteplici piccole parti, successivamente assemblate e incollate tra loro. Una volta completate queste operazioni, la bici può essere sottoposta a una certa quantità di sollecitazioni ed "è possibile maneggiare le parti senza troppi problemi."
"La stampa 3D è stata molto utile, perché ci ha permesso di avere del materiale su cui lavorare", afferma Hicks, che aggiunge: "Per i team di marketing è comodo avere qualcosa di tangibile, perché consente di presentare e promuovere molto meglio il design finale".
Hicks sottolinea che la Form 3L è stata particolarmente vantaggiosa per la prototipazione di elementi di protezione del telaio personalizzati per le loro bici. La catena di una mountain bike sbatte spesso contro i foderi orizzontali, il che può generare anche parecchio rumore e potenzialmente danneggiare il telaio. Per questo motivo, il team ha sviluppato elementi di protezione del telaio personalizzati in gomma che aderiscono ai foderi orizzontali.
Di norma, il team non ha la possibilità di realizzare prototipi di questo tipo di parti, ma invia piuttosto il design al fornitore taiwanese, che realizza l'attrezzatura di produzione e spedisce un campione della parte finale. Questo processo richiede normalmente dai tre ai quattro mesi e costa circa 3000-4000 €. In questo modo, sarebbe stato difficile apportare piccole modifiche, eseguire iterazioni e ottimizzare le parti, dal momento che qualsiasi cambiamento del design avrebbe richiesto la realizzazione di nuova attrezzatura, con conseguenti costi aggiuntivi.
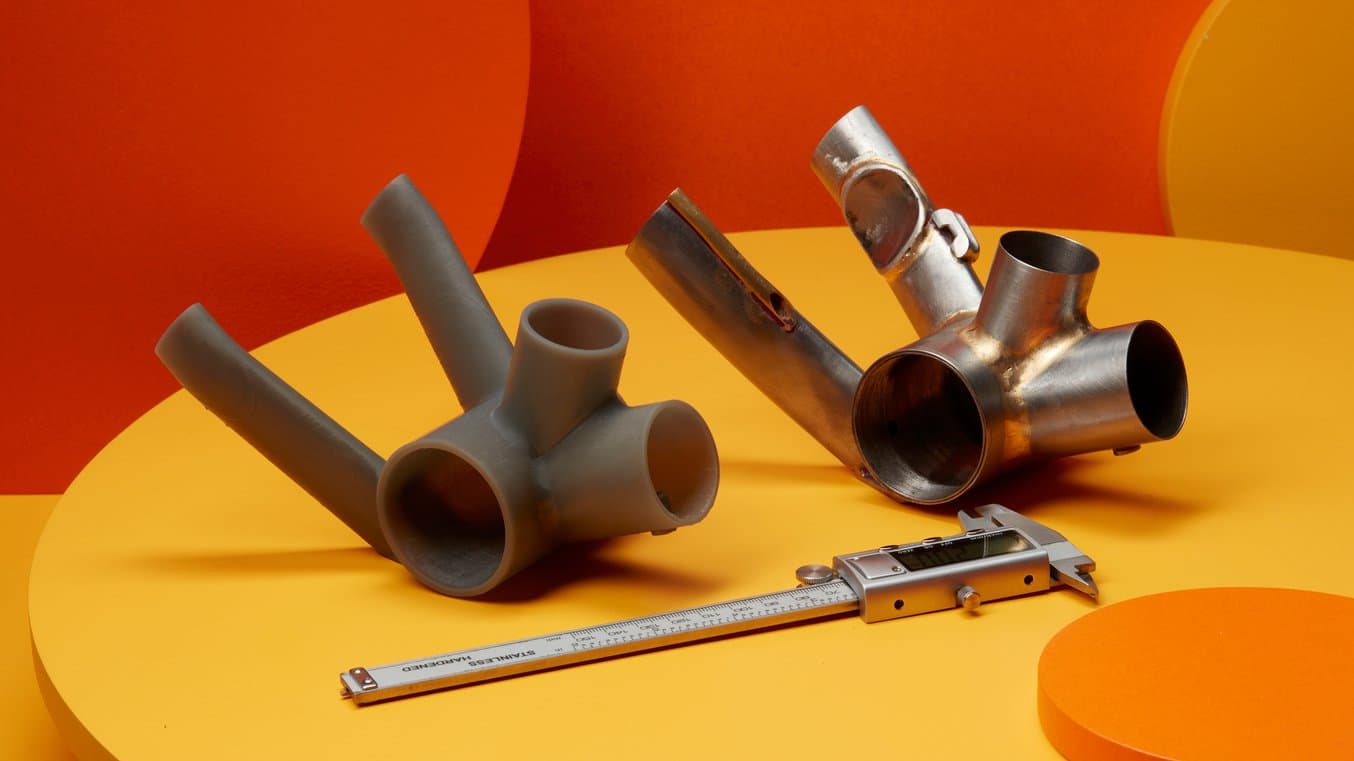
Prototipazione rapida: come scegliere i processi e i materiali più adatti
In questo webinar scoprirai come creare modelli concettuali e prototipi funzionali più rapidamente che mai e come eseguire revisioni rapide dei design basandoti su test in condizioni reali.
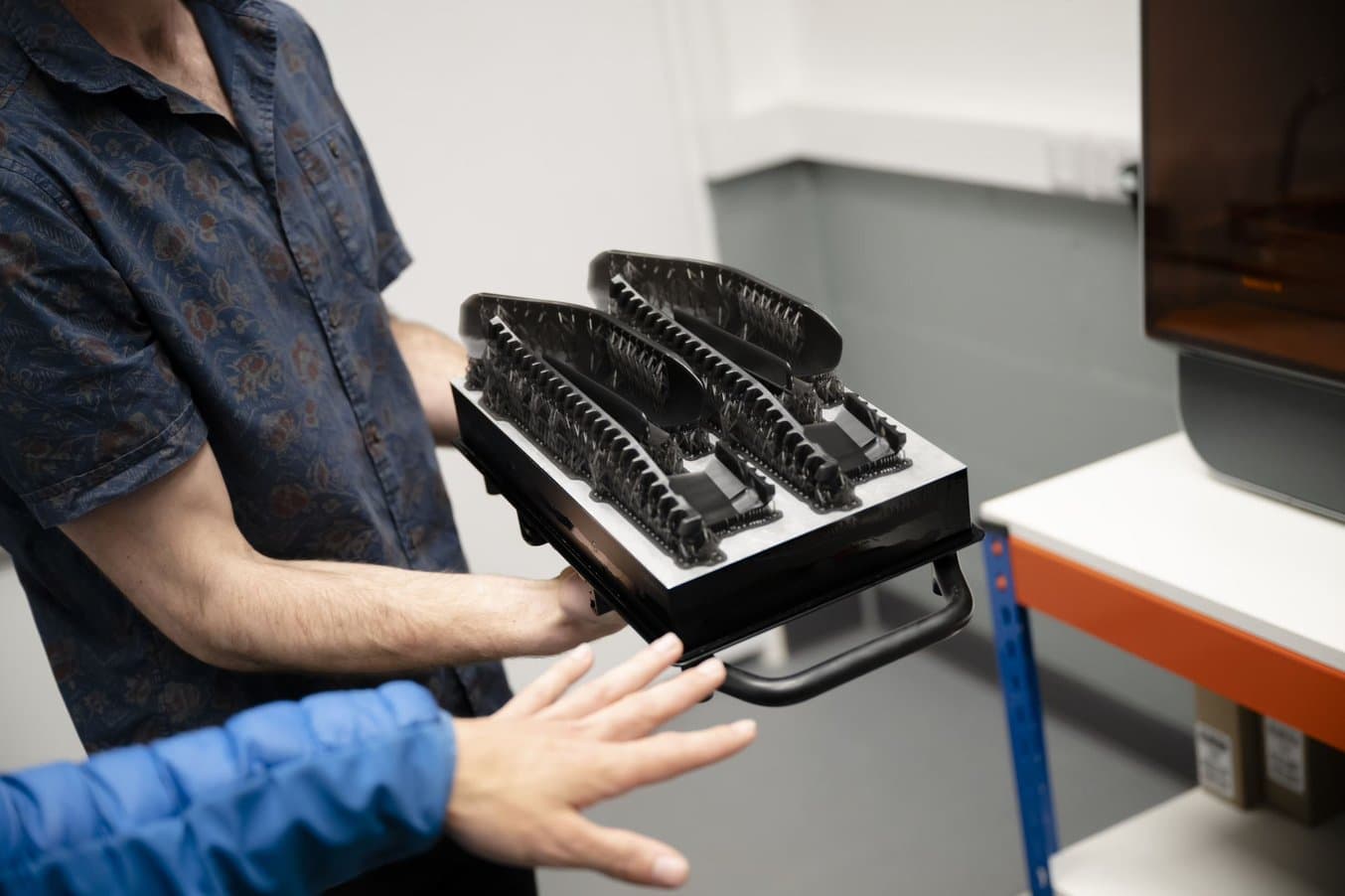
La Form 3L si è rivelata un eccellente strumento per la stampa dei prototipi degli elementi di protezione del telaio con la Flexible 80A Resin.
Grazie alla stampa 3D, il team ingegneristico di Privateer Bikes è in grado di stampare tre o quattro design alla volta e realizzare prototipi molto velocemente. "Cambiare il design non ci costa nulla. Ciò significa che quando inviamo un file di produzione all'azienda di manifattura, possiamo iniziare subito a realizzarlo", afferma Hicks. Specifica inoltre che questo processo ha permesso all'azienda di guadagnare circa sei mesi nella realizzazione del progetto e di risparmiare approssimativamente 4000-5000 € per l'attrezzatura di produzione.
"Quando inviamo un file di produzione all'azienda di manifattura, possiamo iniziare subito a realizzarlo."
Dan Hicks, ingegnere dello sviluppo presso Privateer Bikes
Il materiale scelto per questa particolare applicazione è stato la Flexible 80A Resin, che "è all'incirca della giusta durezza" e quindi ideale per i prototipi funzionali che vengono direttamente inseriti nelle bici per i test. Il team ha testato questi elementi di protezione sulle bici per svariati mesi, esaminando i punti in cui la catena continuava a sbattere e a fare rumore ed eseguendo iterazioni sulla base di questi risultati.
"Possiamo realizzare gran parte del design per la fabbricazione: quando hai la possibilità di guardare la parte da vicino e immaginare le linee di divisione dell'attrezzatura e il possibile funzionamento, è tutto molto più semplice."
Dan Hicks, ingegnere dello sviluppo presso Privateer Bikes
Risposta rapida alle tendenze in evoluzione grazie alla stampa 3D
"Ogni persona vive la bici in modo diverso e non sappiamo come il settore cambierà da qui a due anni. Oggi però abbiamo un vantaggio competitivo che ci permette di adattarsi rapidamente alle tendenze in continua evoluzione, passando velocemente a prodotti nuovi."
Dan Hicks, ingegnere dello sviluppo presso Privateer Bikes
Nel prossimo futuro, The Rider Firm mira a produrre più biciclette elettriche e relativi componenti. Queste bici richiedono progettazioni più complesse; Hicks sottolinea che "più componenti devi inserire, più il processo è difficile" e che la stampa 3D consentirà all'azienda di realizzare prototipi di tutte le configurazioni necessarie.
Ogni persona vive la bici in modo diverso e The Rider Firm è curiosa di scoprire come il settore cambierà nel futuro. Con la Form 3L a sua disposizione, l'azienda è ora in grado di adattarsi rapidamente alle tendenze in evoluzione, senza mai smettere di impegnarsi per dare impulso all'innovazione.