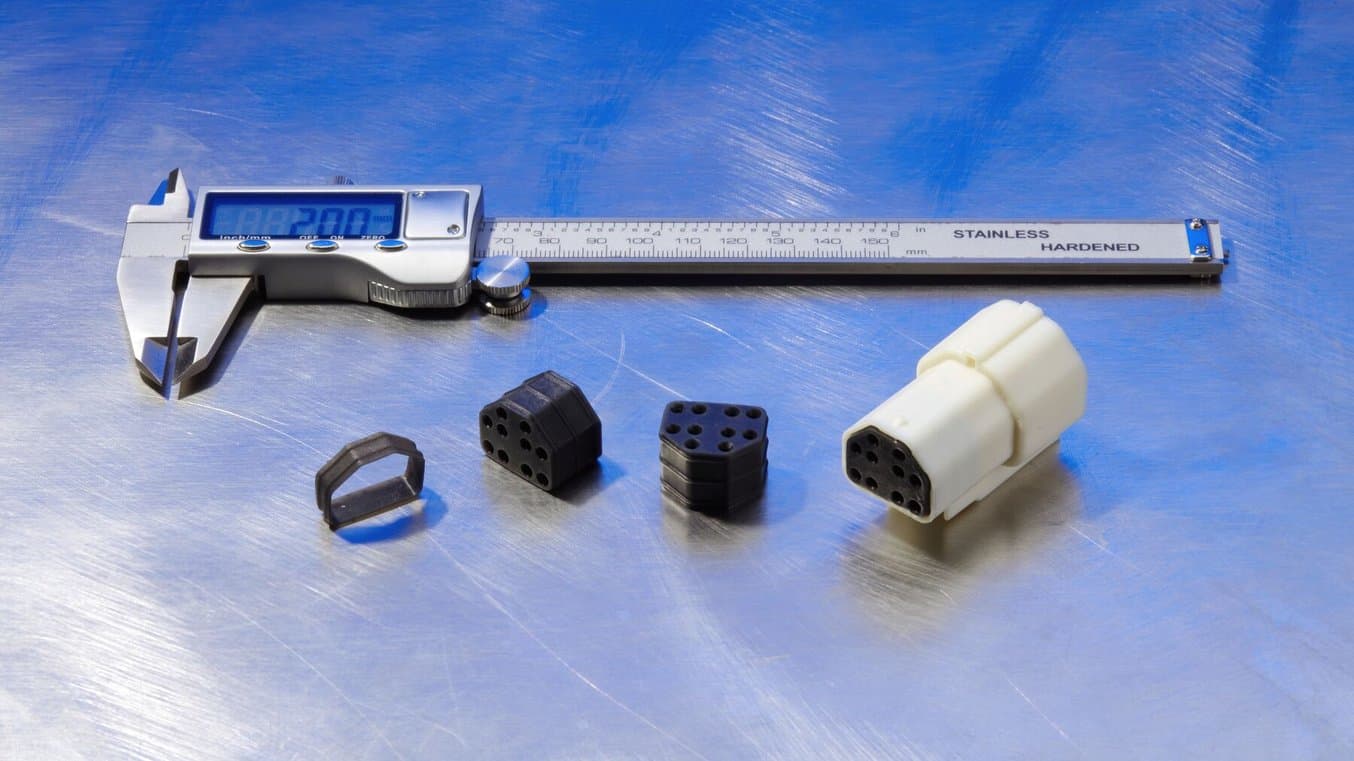
Guarnizioni di HGM Automotive Electronics stampate in 3D in Silicone 40A Resin.
HGM Automotive Electronics è un'azienda produttrice specializzata nella progettazione e fornitura di sistemi elettronici all'avanguardia per il mercato automobilistico post-vendita.
Guy Cardwell, direttore del dipartimento di ricerca e sviluppo di HGM Automotive Electronics, ha dichiarato che una delle principali sfide affrontate dall'azienda è la difficoltà nel reperire le parti per la manutenzione o il restauro dei motori. Infatti, molti dei veicoli che richiedono questi interventi sono auto d'epoca. I connettori e altri componenti elettrici originali sono diventati più difficili da trovare perché la loro produzione è stata interrotta.
L'azienda ha quindi scelto di usare la stampa 3D per la prototipazione e la produzione in volumi ridotti, che è l'opzione ideale per fabbricare le parti in-house e su richiesta. Tuttavia, si trovano a operare in un settore regolamentato in cui è necessario rispettare requisiti specifici, come l'indice di protezione da agenti esterni (IP) e la resistenza agli agenti chimici. La scelta del materiale è quindi molto importante. Il materiale più comune utilizzato per le guarnizioni automobilistiche è in genere il silicone morbido, ma le opzioni per produrlo sono estremamente limitate. Se da una parte lo stampaggio a iniezione ha costi proibitivi per la produzione in volumi ridotti, dall'altra la colata di silicone è un metodo che richiede tempi molto lunghi.
Con l'introduzione della Silicone 40A Resin, il primo materiale accessibile per la stampa 3D in silicone al 100% per parti morbide, flessibili e resistenti, Cardwell è sicuro di aver trovato "il materiale perfetto". Attraverso rigorosi test chimici e meccanici, HGM Automotive Electronics ha dimostrato che il nuovo materiale possiede eccellenti proprietà meccaniche e resistenza alle sostanze chimiche che lo rendono ideale per parti automobilistiche per utilizzo finale. L'azienda ha inoltre partecipato al programma beta per i nuovi materiali e ha utilizzato la nuova resina per la prototipazione, ma il suo obiettivo principale è ora quello di iniziare a impiegarlo nella produzione di parti per utilizzo finale in volumi ridotti.
"La Silicone 40A Resin è semplicemente perfetta. La somiglianza con il materiale originale del fornitore è davvero incredibile."
Guy Cardwell, direttore del dipartimento di ricerca e sviluppo presso HGM Automotive Electronics
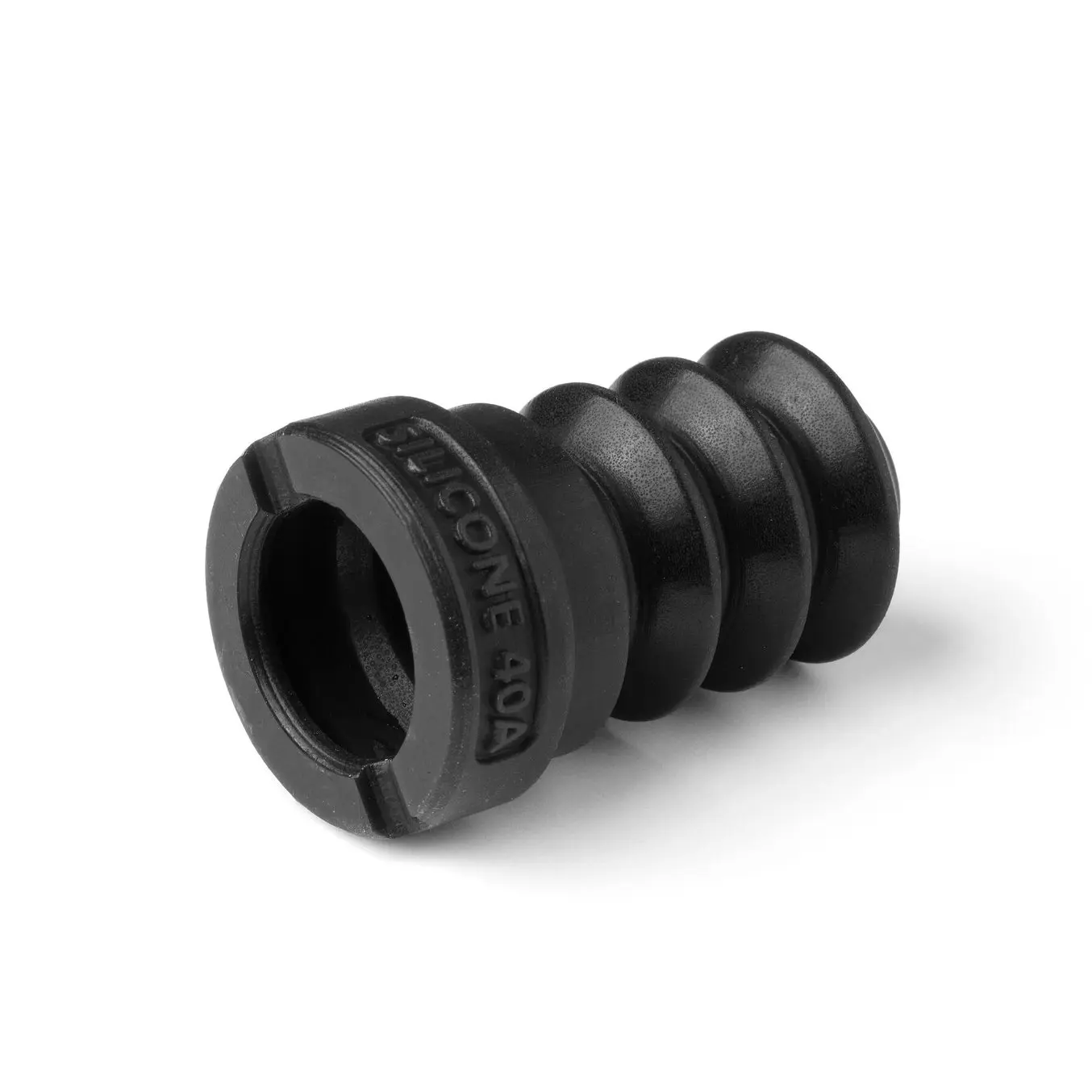
Richiedi un campione gratuito
Guarda e tocca con mano la qualità di Formlabs. Saremo lieti di inviare presso la tua azienda un campione gratuito in Silicone 40A Resin.
Progettazione migliorata delle guarnizioni con la Silicone 40A Resin
Metodo di confronto | Vantaggi della stampa 3D con la Silicone 40A Resin |
---|---|
Stampaggio a iniezione esternalizzato | Tempo di realizzazione ridotto del 90% Costi ridotti del 98% |
Colata di silicone in-house | Realizzazione di geometrie complesse con alta risoluzione dei dettagli Riduzione di manodopera, rischi di errori e tempo di realizzazione Ripetibile e scalabile da 10 a 1000 unità di produzione |
Dopo il successo ottenuto con i connettori elettrici prodotti, HGM Automotive ha iniziato a sperimentare con le guarnizioni personalizzate. Questi componenti sono difficili da reperire sul mercato e i pochi disponibili sono spesso di qualità molto scarsa. Le difficoltà legate allo sviluppo di guarnizioni personalizzate per connettori derivano dalla mancanza di un materiale elastomerico flessibile idoneo. Per produrre le parti, l'azienda poteva produrre uno stampo a iniezione e utilizzarlo con un uretano molto morbido. L'aspetto negativo era però il costo iniziale dello stampo, compreso tra i 6000 e i 10 000 dollari. Questo costo sarebbe giustificato per la produzione di 10 000 parti, ma il volume reale richiesto va dalle 100 alle 1000 parti all'anno. Inoltre, una volta realizzato lo stampo, è quasi impossibile modificarne il design. Ciò rappresenta un ostacolo soprattutto per le guarnizioni dei connettori, che tendono ad avere una geometria complessa. "Si riduce tutto a una questione di costi e flessibilità", afferma Cardwell.
Tempo di realizzazione | Costo | |
---|---|---|
Stampaggio a iniezione esternalizzato | 3-4 settimane | 10 000 $ per le attrezzature 0,5 $ per parte |
Stampa 3D in-house con la Silicone 40A Resin | 6 ore per 25 parti | 1-2 $ per parte |
Per un volume di produzione di 100 guarnizioni, HGM Automotive ha ridotto i costi del 98% e il tempo di realizzazione del 90%.
In passato, l'azienda stampava le guarnizioni per i connettori con l'Elastic 50A Resin di Formlabs. Questo materiale è morbido e flessibile, ma non lo era abbastanza per ottenere prestazioni ottimali. Cardwell ha inoltre aggiunto che, poiché i connettori vengono assemblati manualmente, gli addetti ai cablaggi impiegano due o tre volte più tempo per assemblare un connettore prodotto con un materiale più duro come l'uretano rispetto a una guarnizione in silicone, "semplicemente perché è un materiale che richiede uno sforzo maggiore".
Un'altra opzione era quella di utilizzare un normale silicone da colata, una soluzione già utilizzata dall'azienda per altre parti. Tuttavia, questo specifico connettore è progettato per includere nove cavi che passano attraverso la guarnizione, perciò il suo design è molto complicato. I suoi fori e la geometria renderebbero difficile il rilascio dallo stampo, e nel complesso presenta un livello di dettaglio che richiede la precisione della stampa 3D.
"La colata è un'opzione possibile, ma bisogna prestare moltissima attenzione [alle geometrie intricate]. Inoltre è un processo molto lungo. Avere la possibilità di stampare in 3D in lotti è davvero un lusso rispetto a qualsiasi altro processo."
Guy Cardwell, direttore del dipartimento di ricerca e sviluppo presso HGM Automotive Electronics
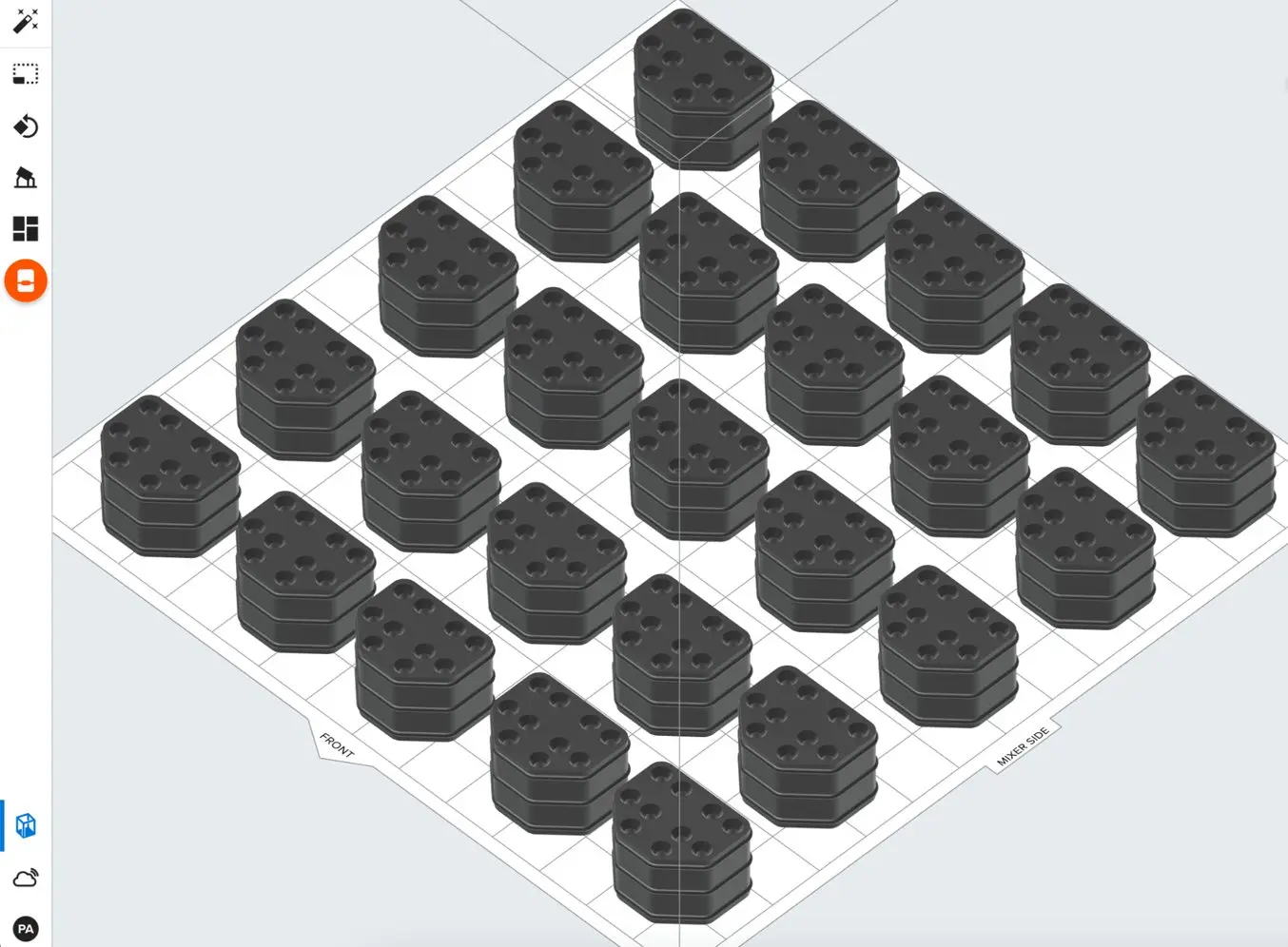
File CAD delle guarnizioni di HGM Automotive Electronics caricato nel software PreForm. Nove cavi passano attraverso la guarnizione, che ha uno spessore di circa 1 cm. Per via della geometria intricata e dei dettagli di piccole dimensioni, la realizzazione di strumenti per lo stampaggio a iniezione o la colata di silicone è complicata. I 25 connettori vengono stampati in quattro ore e 30 minuti sulla Form 3+.
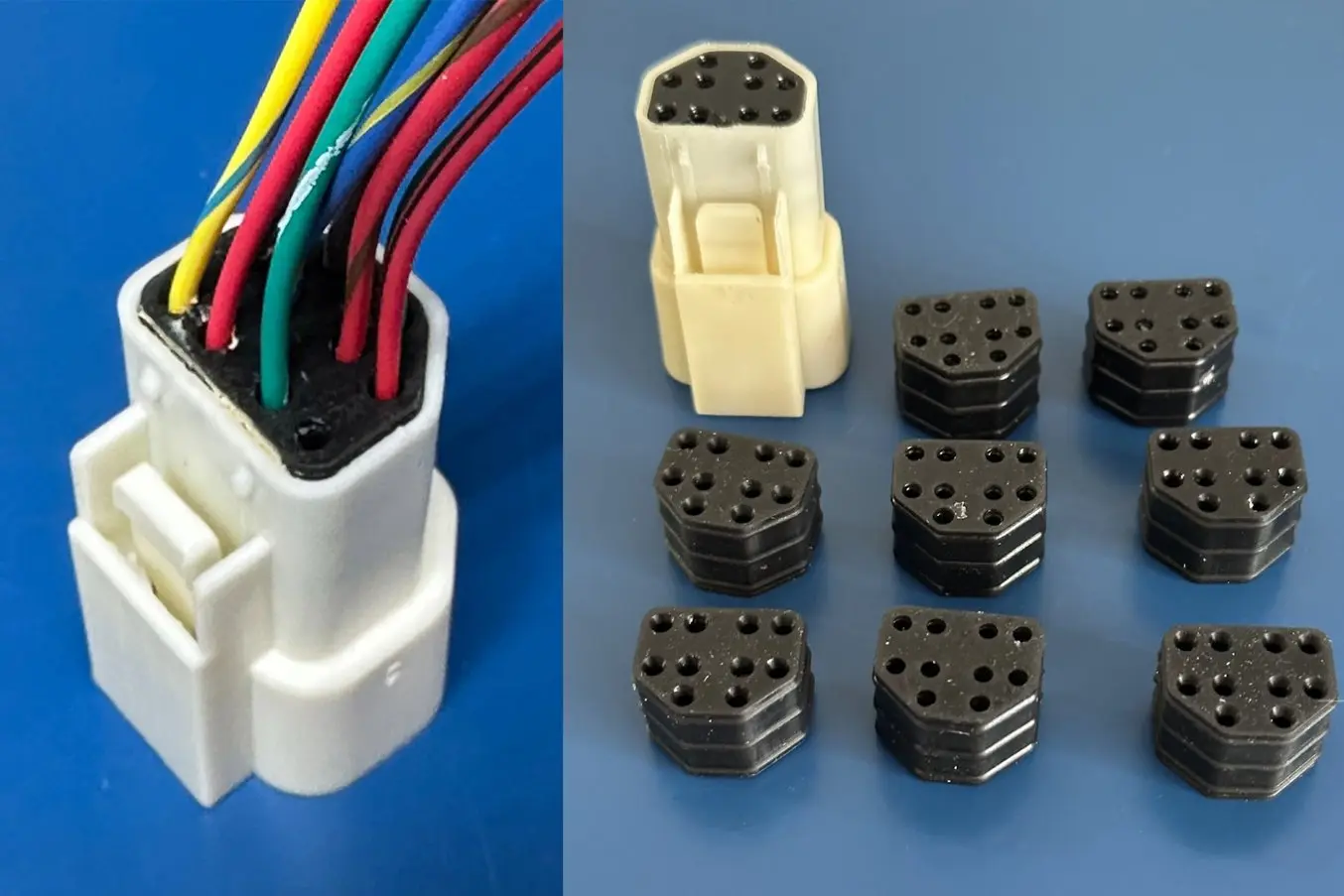
Guarnizioni per connettori stampate e assemblate con un alloggiamento e componenti elettronici.
"È il materiale perfetto perché è estremamente simile al materiale di produzione originale."
Guy Cardwell, direttore del dipartimento di ricerca e sviluppo presso HGM Automotive Electronics
La Silicone 40A Resin consente a HGM di eseguire in-house i processi di produzione in volumi ridotti e ha il vantaggio aggiuntivo di poter essere utilizzata in svariati modi diversi. Il team ha già pensato ad altri utilizzi oltre alla produzione di guarnizioni per connettori. I punti di forza di questo nuovo materiale sono la sua somiglianza al materiale di produzione originale e le sue proprietà di elasticità, flessibilità e resistenza alla lacerazione, ideali per le applicazioni di HGM Automotive Electronics.
"La Silicone 40A Resin offre la flessibilità necessaria per ottenere design che in passato potevano essere realizzati solo tramite un lungo e costoso processo di stampaggio. Inoltre, ci consente di esplorare nuovi mercati e fabbricare prodotti fino a oggi considerati troppo costosi o complessi. Altre soluzioni di stampa 3D consentono di stampare alcuni tipi di materiali elastici, ma solo la combinazione di Silicone 40A Resin e stampanti SLA di Formlabs ci ha permesso di creare guarnizioni morbide con la stessa qualità e resistenza di una parte realizzata tramite stampaggio a iniezione in silicone o poliuretano termoplastico."
Guy Cardwell, direttore del dipartimento di ricerca e sviluppo presso HGM Automotive Electronics
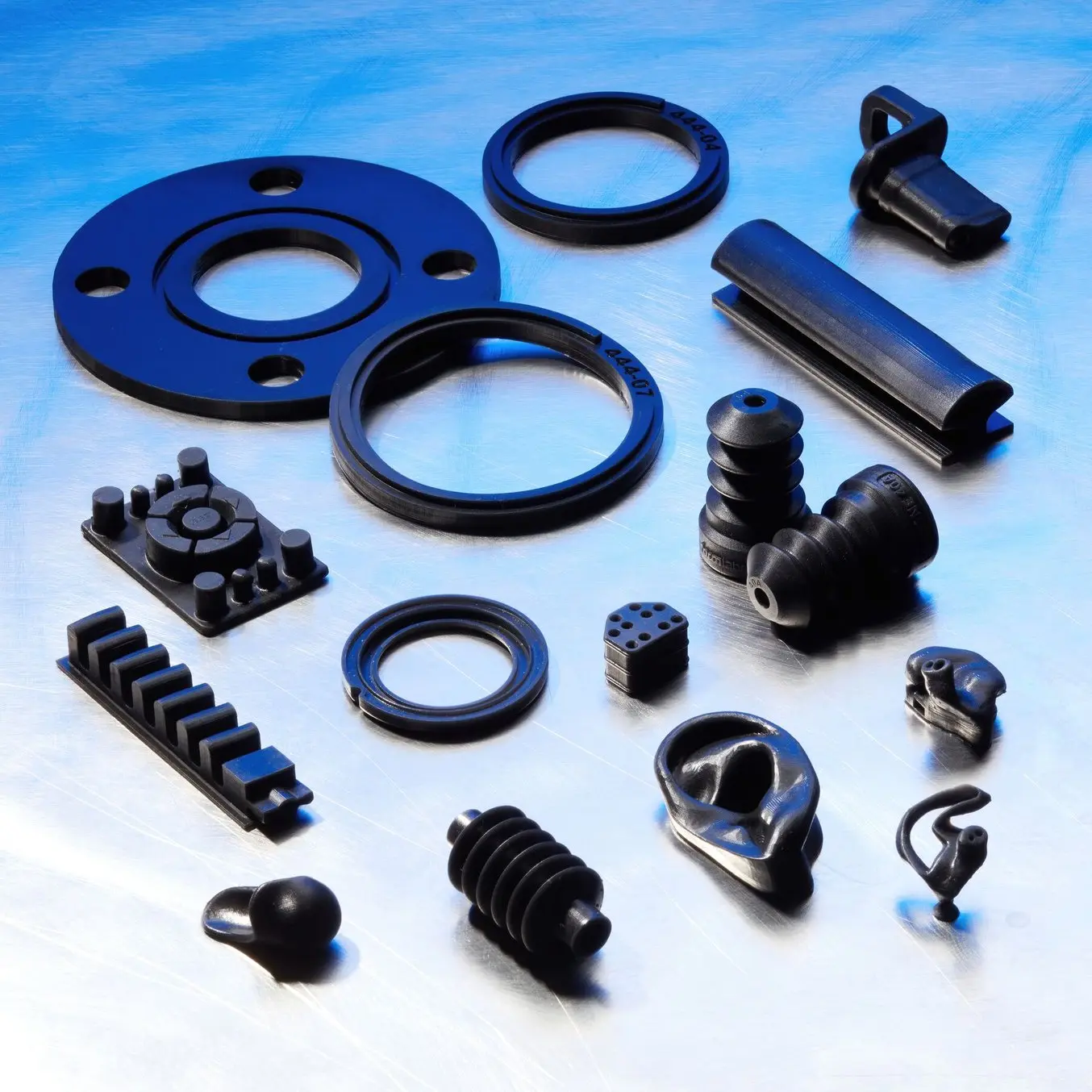
Presentazione della Silicone 40A Resin
In questo webinar, il nostro team specializzato in stampa 3D ti illustrerà i vantaggi e le applicazioni principali della Silicone 40A Resin, nonché le relative proprietà del materiale e il workflow associato.
Dai test al successo: la Silicone 40A Resin soddisfa requisiti industriali di temperatura e resistenza alle sostanze chimiche
"La Silicone 40A Resin possiede tutte le proprietà necessarie per questa applicazione in termini di flessibilità e lavorabilità. Fino a questa fase di test, la resistenza alle sostanze chimiche è risultata in linea con quella prevista per un silicone da colata o stampato a iniezione utilizzato in questa applicazione."
Guy Cardwell, direttore del dipartimento di ricerca e sviluppo presso HGM Automotive Electronics
Le applicazioni automobilistiche sono spesso soggette a condizioni che richiedono guarnizioni impermeabili, in grado di resistere a profondità comprese tra uno e due o tre metri, a seconda dell'applicazione. Inoltre, i loro requisiti di resistenza alle sostanze chimiche riguardano tutti i principali fluidi automobilistici standard, tra cui acqua, olio e liquido di trasmissione. Per testare le parti, Cardwell ha stampato diversi campioni e li ha sottoposti a test funzionali nel vano motore della sua auto. I campioni stampati in silicone sono stati lasciati nel vano motore in normali condizioni operative per più di sei settimane per testare la resistenza al calore e alle sostanze chimiche.
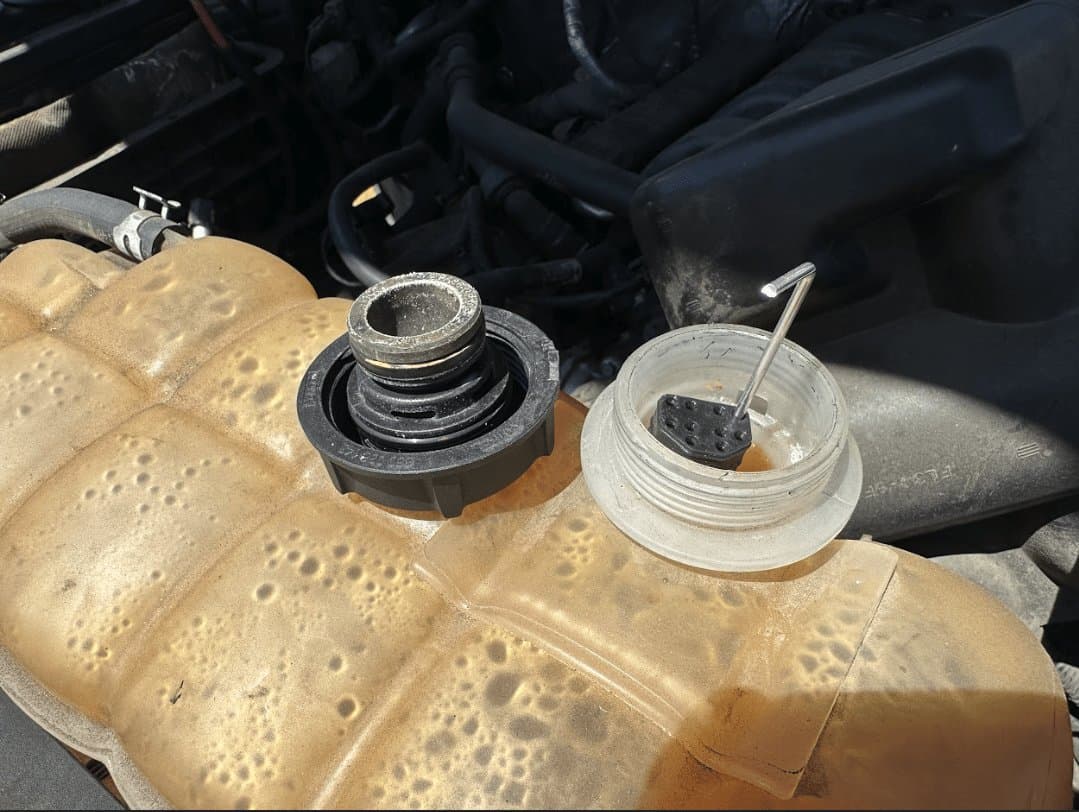
Guarnizioni stampate in 3D in Silicone 40A Resin testate sul campo da HGM Automotive Electronics all'interno del serbatoio di liquido refrigerante di un motore di automobile.
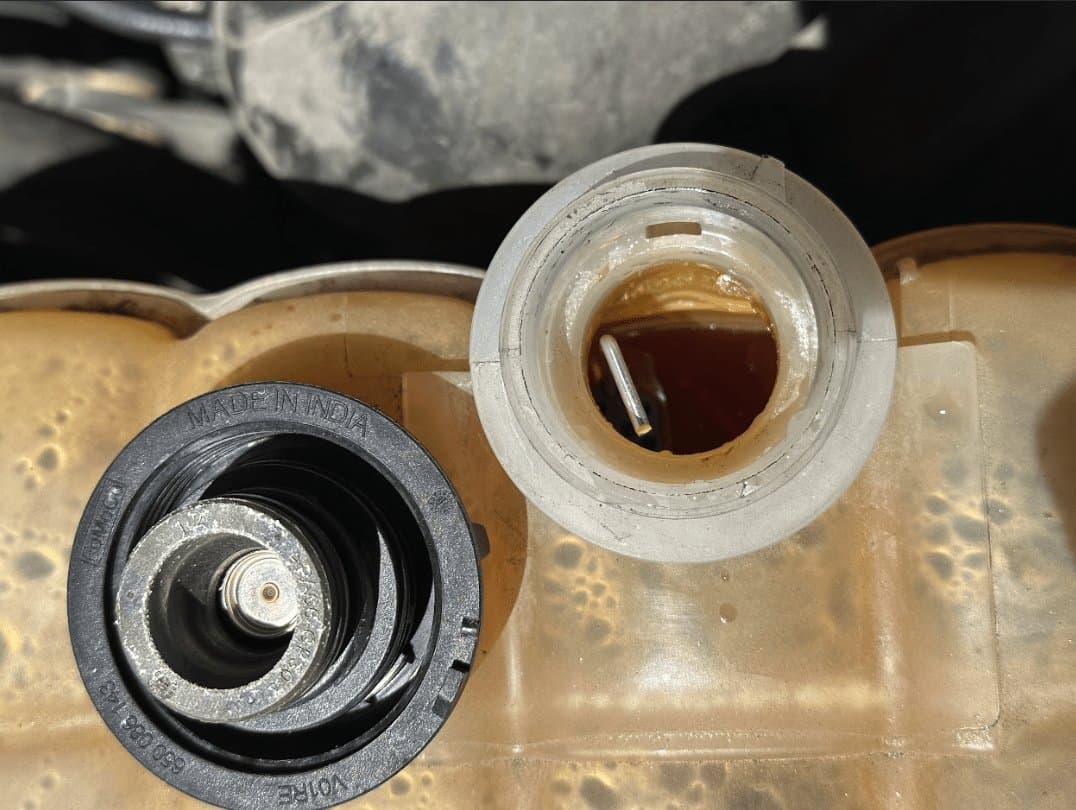
"Le abbiamo lasciate esposte ai diversi fluidi all'interno del motore e sottoposte a cicli termici. Abbiamo eseguito test con acqua e test statici con liquido di trasmissione e antigelo", spiega Cardwell. "La sostanza a cui le guarnizioni riescono a impedire l'ingresso in maniera più efficace è l'acqua", aggiunge. Dopo sei settimane di cicli termici ed esposizioni a vari fluidi, Cardwell ha confermato l'impermeabilità e la resistenza al calore della Silicone 40A Resin. La temperatura dei componenti elettronici automobilistici oscilla tra i -40 °C e i 105 °C. La Silicone 40A Resin, con una temperatura di transizione vetrosa (Tg) di -107 °C e una resistenza a temperature comprese tra i -25 °C e i 125 °C, risponde perfettamente ai requisiti di resistenza termica. "Ho proseguito i test sul materiale con la certezza che avrebbe avuto un comportamento simile a un silicone stampato a iniezione dello stesso tipo", ed è stato proprio così. Le proprietà della Silicone 40A Resin erano perfettamente in linea con le sue aspettative per un materiale per utilizzo finale, il che l'ha resa un'aggiunta perfetta al suo arsenale.
Dopo gli intensivi test sul campo, il team di HGM è rimasto completamente soddisfatto della nuova resina in silicone al 100% e della sua idoneità a tutti i requisiti. Per questo verrà utilizzata nella produzione di parti per utilizzo finale, ovvero le guarnizioni per connettori, con una stima di 500-1000 unità prodotte all'anno. Cardwell sta progettando di ampliare ulteriormente le possibilità di utilizzo di questa resina e aggiunge: "Solamente tra i connettori ci sono almeno quattro prodotti per cui potremmo prenderla in considerazione".
Innovazioni future di HGM Electronics
La Silicone 40A Resin ha fornito a HGM Electronics la flessibilità di sviluppare design che in passato potevano essere realizzati solo tramite processi lunghi e costosi, nonché la possibilità di esplorare nuovi mercati.
"Mi ricordo che quando ho distribuito [alcuni campioni] ai dipendenti dell'azienda sono rimasti tutti a bocca aperta! È davvero un materiale sorprendente. E non riesci a farti un'idea delle possibili applicazioni future finché non lo provi in prima persona. A quel punto diventa tutto più chiaro. Il mio lavoro con i connettori andrà avanti, ma ci sono molte altre cose che possiamo fare con questo materiale. Su questo non ho alcun dubbio."
Guy Cardwell, direttore del dipartimento di ricerca e sviluppo presso HGM Automotive Electronics
Tra i progetti futuri, Cardwell sogna il giorno in cui potrà dire ai suoi clienti che è finalmente in grado di produrre parti personalizzate in gomma morbida. Nello specifico, sta valutando di sviluppare diversi tipi di guarnizioni personalizzate e nuovi isolanti elettrici in silicone, come quelli raffigurati di seguito.

Isolanti per candele stampati in 3D con la Silicone 40A Resin.
"Non posso prevedere cosa farò in futuro con i siliconi stampati in 3D, ma non vedo l'ora di scoprirlo."
Guy Cardwell, direttore del dipartimento di ricerca e sviluppo presso HGM Automotive Electronics