Situato nel cuore del settore automobilistico del Regno Unito, Vital Auto è uno studio di design industriale con una notevole esperienza nel design di auto. La clientela illustre dell'azienda comprende molti dei più importanti produttori di automobili, come Volvo, Nissan, Lotus, McLaren, Geely, TATA e altri.
"In genere, i clienti si rivolgono a noi per cercare di superare i limiti di ciò che è fattibile con la tecnologia disponibile", ha dichiarato Shay Moradi, vicepresidente del dipartimento di innovazione e tecnologia esperienziale di Vital. Quando i produttori non hanno tempo a disposizione per la sperimentazione, si affidano a Vital Auto per trasformare idee, schizzi iniziali, disegni o specifiche tecniche in una forma fisica realizzata interamente.
Continua a leggere per scoprire come Vital Auto crea prototipi estremamente fedeli e concept car, eseguendo rapidamente diverse iterazioni utilizzando una serie di strumenti avanzati, tra cui una vasta flotta di stampanti Form 3L e Fuse 1.
Realizzazione di una concept car
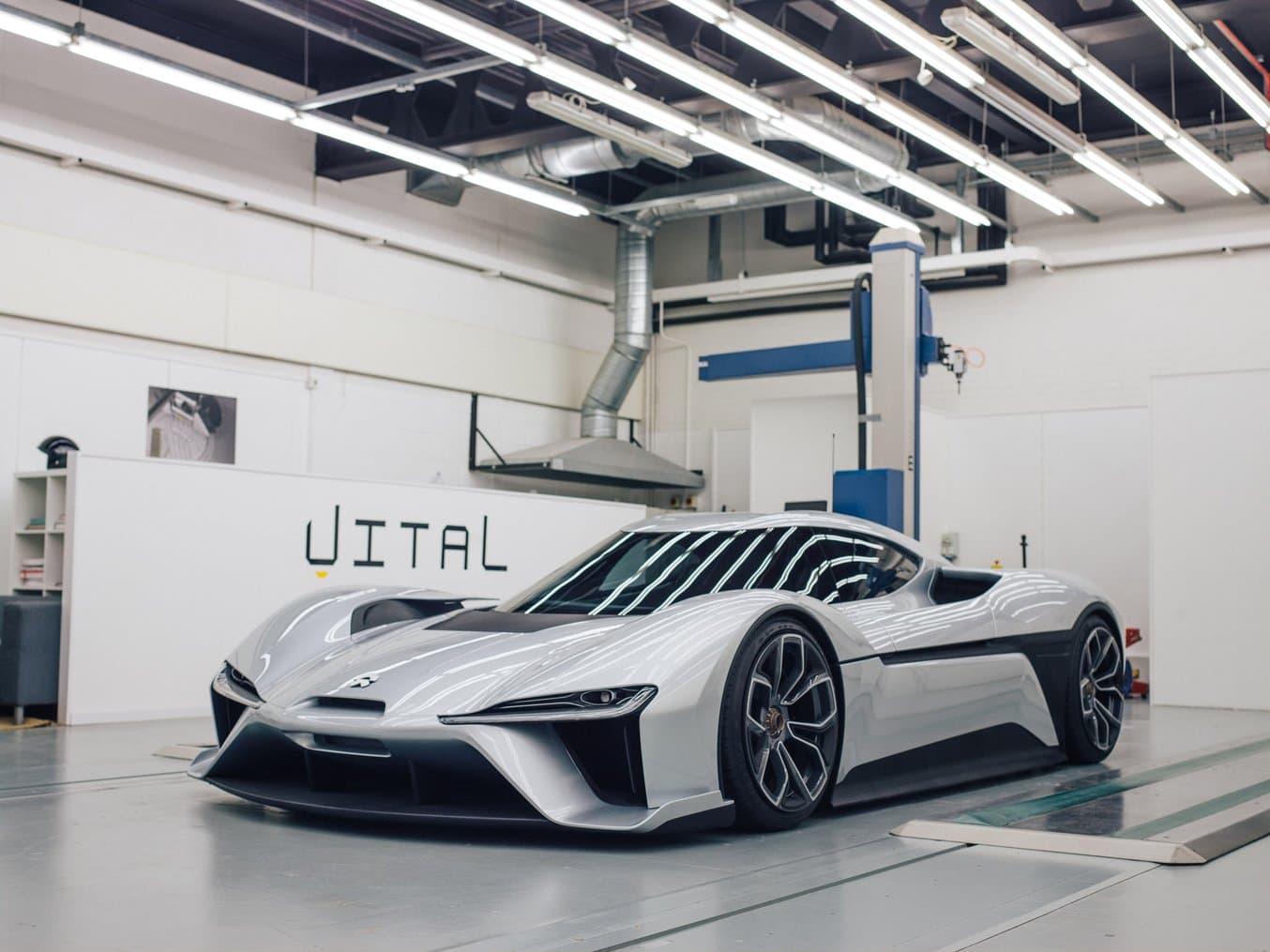
Vital Auto è stata fondata nel 2015 da tre amici che hanno lasciato il lavoro e hanno deciso di aprire un'attività; giustamente in un garage. Uno dei primi incarichi dell'azienda è stato per la realizzazione della concept supercar NIO EP9, che ha subito indirizzato il team verso la produzione di prototipi di veicoli estremamente realistici e altamente fedeli.
A seconda delle richieste del cliente, il team parte da un semplice schizzo su carta per arrivare a un veicolo già progettato. Sviluppa le auto partendo da un foglio bianco, progetta il telaio, tutti gli elementi interni ed esterni, aperture e chiusure, e le parti interattive. Un progetto può durare da tre a 12 mesi, impegnando da cinque a 30 persone per un singolo concept.
In questo lasso di tempo, un'auto da esposizione viene sottoposta a una dozzina di iterazioni del design di base e, all'interno di queste, si susseguono ulteriori iterazioni di componenti più piccoli, fino a quando il design non soddisfa pienamente le aspettative del cliente.
"Nel nostro settore è giusto considerare le proprietà virtuali come un mezzo per valutare un prodotto prima che arrivi sul mercato. Tuttavia, ritengo che esisterà sempre uno spazio anche per gli oggetti prodotti fisicamente. Non c'è niente che possa battere la sensazione di tenere in mano un prodotto che abbia il giusto peso, le giuste proporzioni, ma anche la dinamica di come l'ambiente fisico cambi la percezione dell'oggetto fisico", ha aggiunto Moradi.
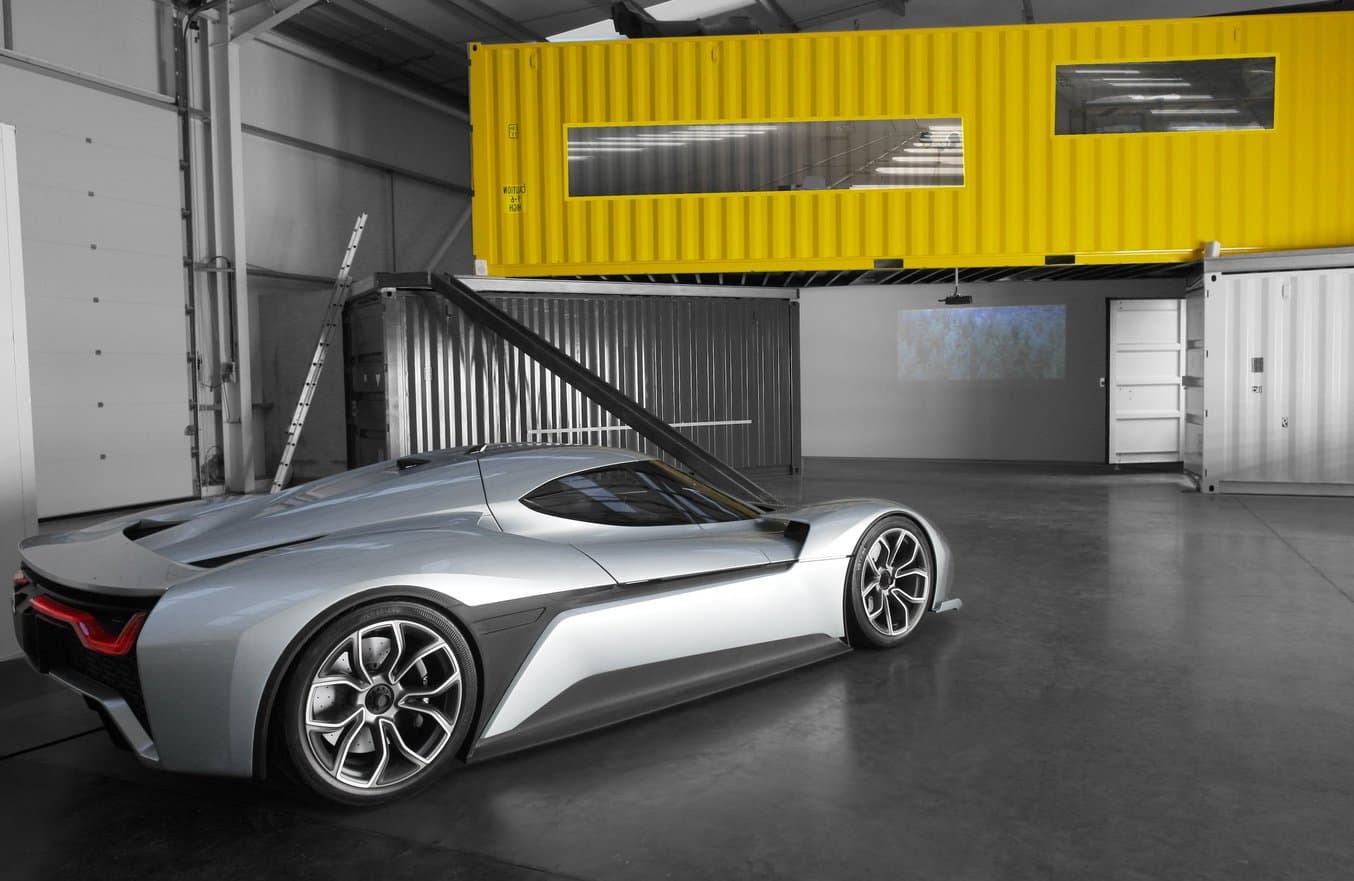
"Molti dei nostri clienti vengono da noi con un'idea nuova, innovativa, qualcosa che non è mai stato realizzato. Per cui, ogni giorno ci troviamo ad affrontare nuove sfide, e sono infinite", ha affermato Anthony Barnicott, ingegnere di progettazione, responsabile della produzione additiva. "Queste sfide ci portano a chiederci come fare a produrre un tale numero di parti in questo lasso di tempo, come creare un prodotto sostenibile oppure come poter realizzare una parte che abbia un peso specifico e raggiungendo ugualmente una particolare prestazione."
Benché le auto da esposizione tradizionali vengano realizzate solitamente solo con argilla fresata, il team ricorre anche alla fresatura CNC a tre e cinque assi, alla formatura a mano, alla modellazione manuale dell'argilla e ai materiali compositi in vetroresina. Tuttavia, questi processi tradizionali non sono ideali per produrre parti personalizzate necessarie per concept una tantum.
"Utilizziamo la stampa 3D sin dal primo giorno. Volevamo introdurla nel nostro processo di produzione, non solo per ridurne i costi, ma anche per offrire ai clienti maggiore diversità per i loro design e le loro idee", ha detto Barnicott.
Al momento Barnicott gestisce un intero reparto per la stampa 3D, che comprende dieci stampanti FDM di grande formato, tre stampanti SLA Form 3L di Formlabs, sempre di grande formato, e cinque stampanti SLS Fuse 1.
"In termini di capacità, tutte le stampanti hanno funzionato al 100%, 24 ore su 24, 7 giorni su 7, praticamente dal primo giorno. Le utilizziamo per tutte le aree dei nostri concept e design. Generalmente usiamo le Fuse 1 per le parti che si basano sulla produzione e le Form 3L per la parti basate sul concept", ha affermato Barnicott.
Produzione di design complessi con diversi materiali con la Form 3L
"Utilizziamo le Form 3L per tutte le finiture superficiali di classe A, come ad esempio, in un contesto automobilistico, un interno in cui siano presenti parti che non vengono rifinite con pelle o Alcantara o, in generale, con un tessuto. I materiali di Formlabs producono una finitura bella e liscia con cui possono lavorare i verniciatori. In questo modo, possiamo usare le parti appena stampate direttamente su un veicolo", ha detto Barnicott.
"Quello che mi interessa maggiormente degli apparecchi Form 3L è la loro versatilità, la capacità di fare un cambio di materiale in meno di cinque minuti. La variabilità dei materiali, da quelli morbidi e flessibili a quelli rigidi, per noi non ha prezzo", ha proseguito.
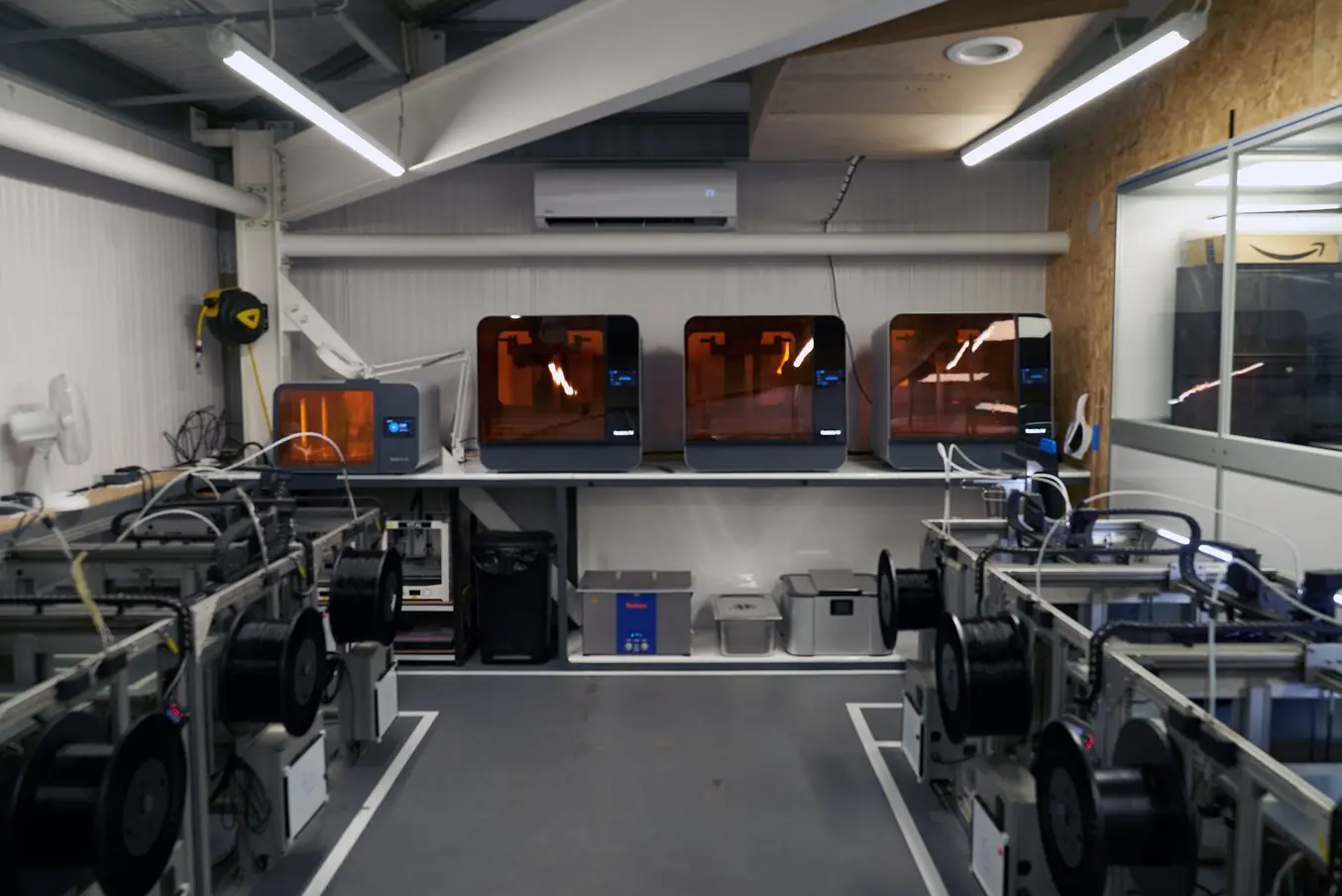
Il team usa le Form 3L con molteplici materiali per una vasta gamma di applicazioni, ad esempio:
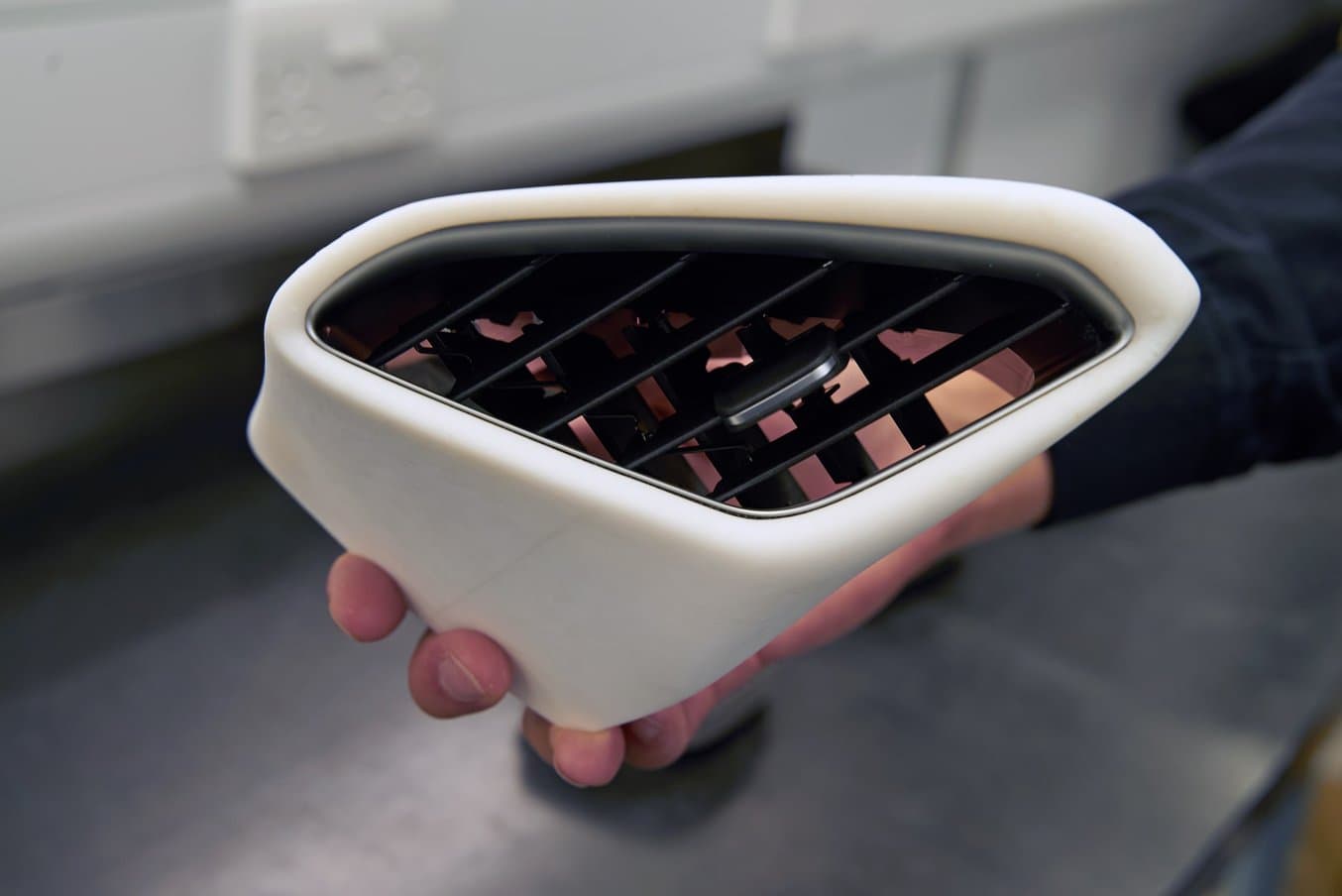
Sfiati
"La nostra azienda affronta frequentemente una sfida: i clienti si rivolgono a noi con un prodotto proprietario che desiderano inserire nel proprio design. Una volta, un cliente ci ha presentato una presa d'aria brevettata per un altro veicolo che desiderava includere nei propri interni. Abbiamo usato la scansione 3D per riprodurre digitalmente questa parte e poi abbiamo creato una superficie esterna. L'abbiamo prima prodotta con la Draft Resin per provare il design e permettere al cliente di controllarlo. Successivamente, siamo passati alla White Resin per produrre una parte pronta per la produzione."
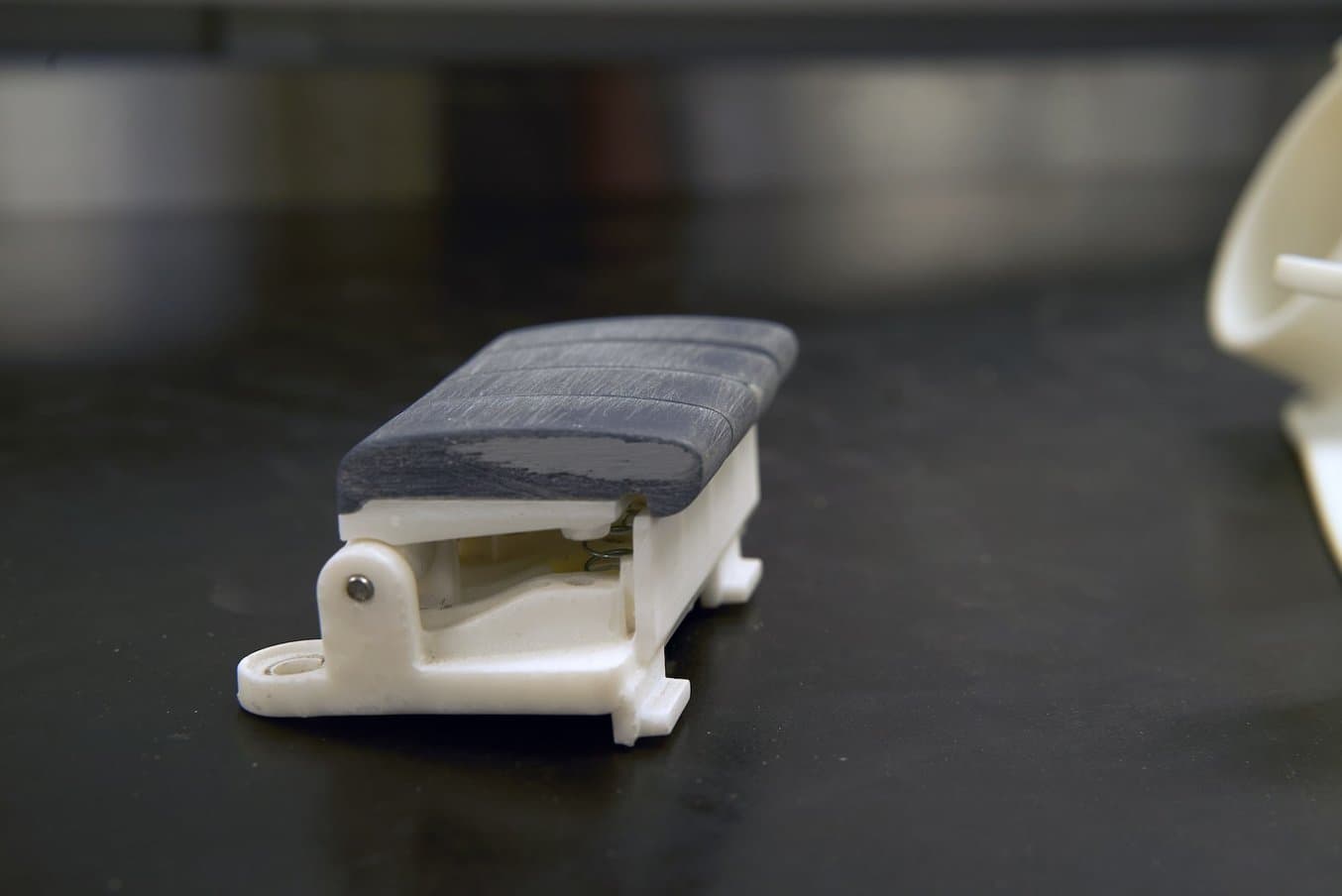
Pacchetti di interruttori
"Quando si lavora con design estremamente intricati, come piccoli pacchetti di interruttori, è possibile utilizzare più materiali per ottenere un prodotto meccanico che non solo funzioni correttamente, ma che possa anche essere utilizzato nella realtà. [Per questi pacchetti di interruttori], abbiamo combinato i materiali più duri, come la Tough 2000 Resin per la parte superiore, con quelli più leggeri ed economici per le parti interne."
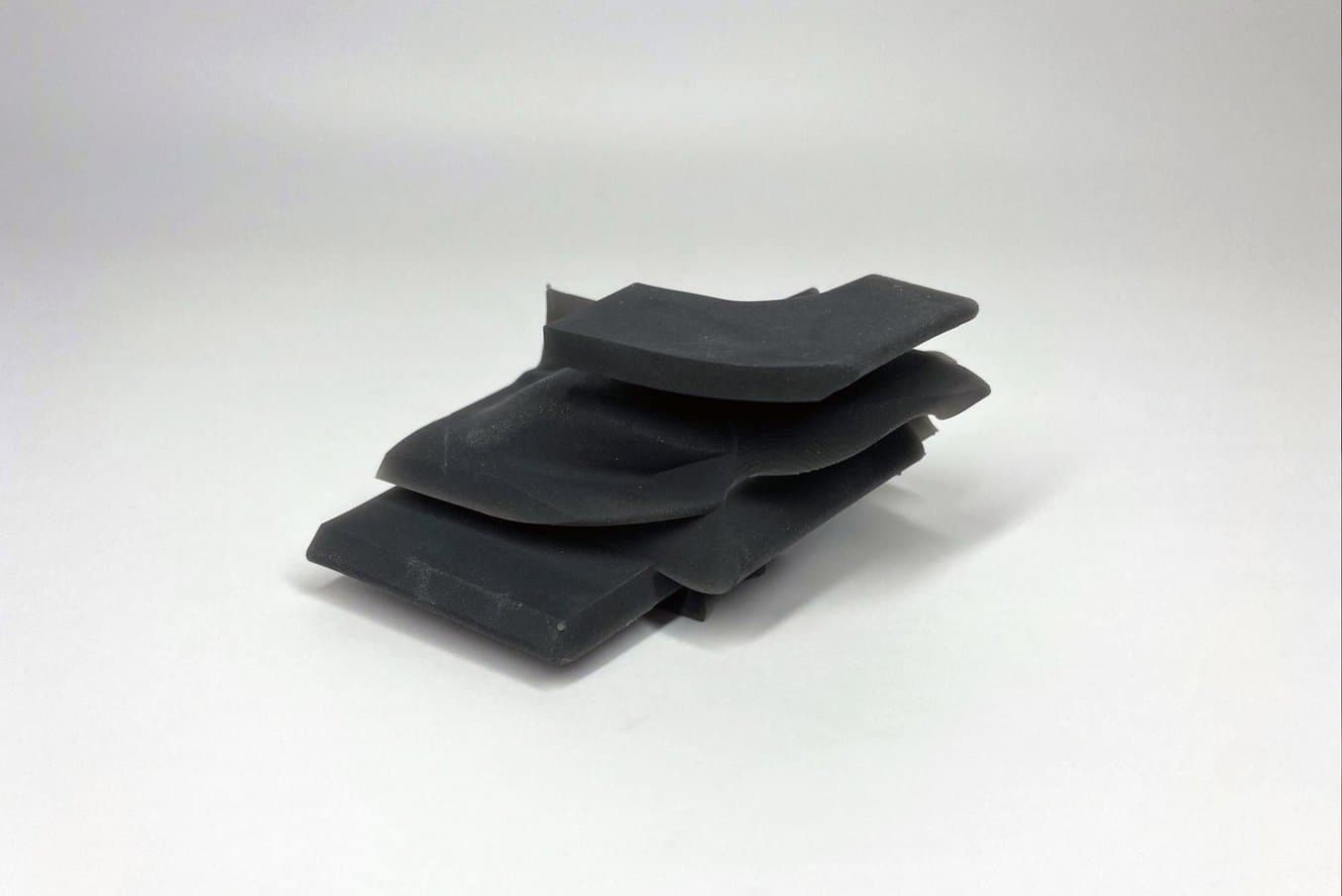
Guarnizioni per le portiere
"In genere, le guarnizioni per portiere destinate ad applicazioni automobilistiche hanno un costo di produzione notevole. Per realizzarle non esiste altro modo che lo stampaggio per estrusione. La procedura comporta non solo un costo elevatissimo per le attrezzature, ma anche tempi di consegna molto lunghi. A questo proposito, abbiamo provato uno degli ultimi materiali offerti da Formlabs, la Flexible 80A Resin. Con la Form 3L abbiamo prodotto sezioni di questa guarnizione in una notte per testarne le varie geometrie. Il risultato è stato stampato con uno scarto di 50 micron rispetto al design reale."
La Form 3L permette al team di produrre parecchie iterazioni di parti, in genere entro 24 ore. L'azienda ha acquistato tre macchine per poter produrre fino a tre diverse iterazioni di una parte contemporaneamente, anche usando tre materiali differenti. In questo modo, si può far risparmiare il cliente o, in alternativa, gli si può offrire un valore aggiunto presentando più varianti di design a parità di prezzo.
“Uno degli aspetti più belli della produzione additiva è la riduzione dei tempi. Quindi cosa si può fare con il tempo che si è guadagnato? Pensiamo di estendere lo spazio di possibilità immaginando delle alternative, aggiungendo altri cicli di iterazione nel processo", ha detto Moradi.
"Senza le Form 3L non saremmo in grado di produrre molti dei nostri prodotti. Grazie ad alcune delle tecniche di produzione più avanzate, come la lavorazione meccanica CNC a sette assi, saremmo in grado di produrre queste parti, ma a un costo troppo esorbitante", ha affermato Barnicott.
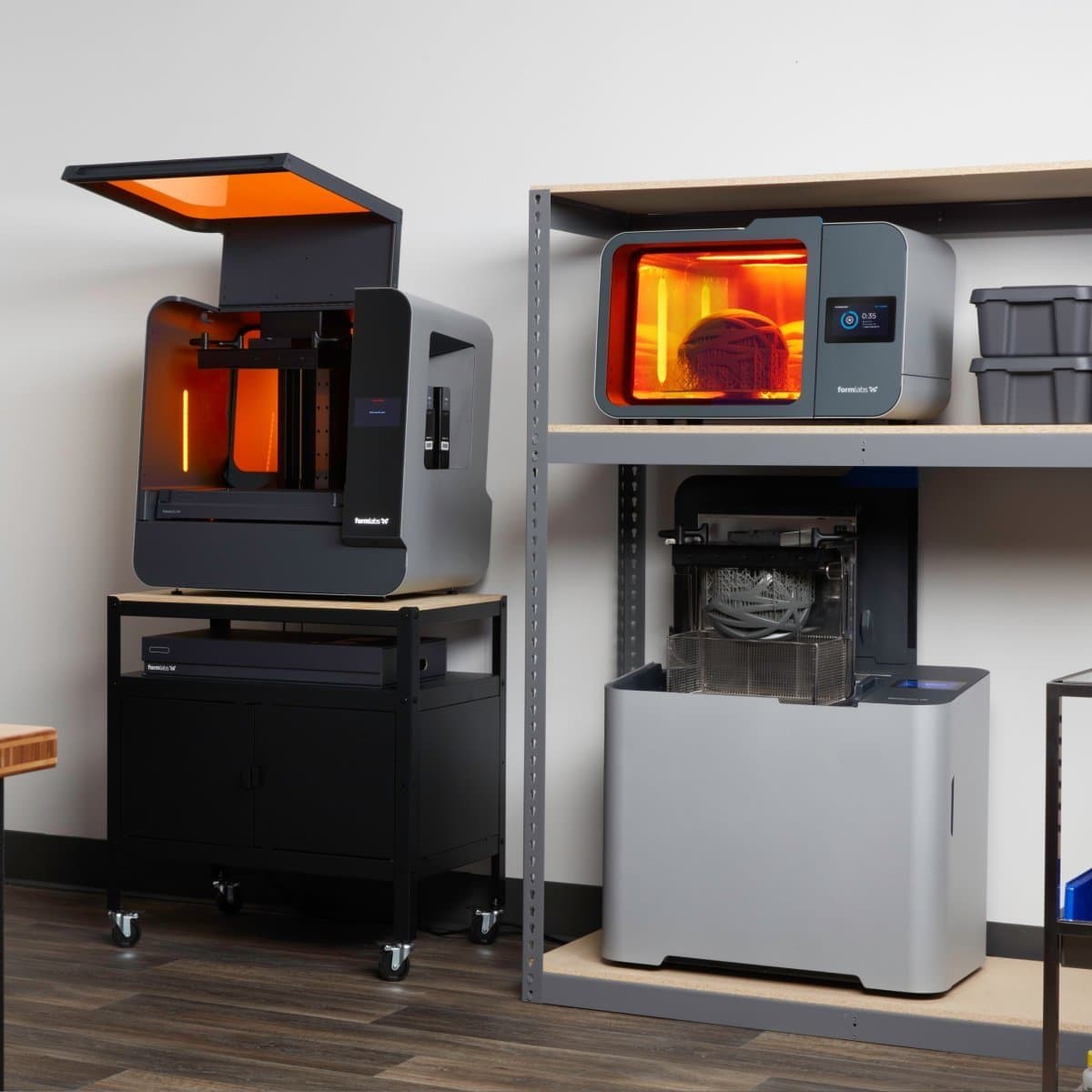
Dimostrazione dell'ecosistema Form 3L
Vuoi scoprire di più sugli ecosistemi Form 3L e Form 3BL e sugli apparecchi per la post-elaborazione di grande formato? In questa dimostrazione, Kyle e Chris spiegheranno come navigare nel workflow completo della Form 3L, compresa la post-elaborazione.
Integrazione della lavorazione meccanica CNC per le parti meccaniche con la Fuse 1
"È stato con la Fuse 1 che abbiamo iniziato a sperimentare con la tecnologia SLS. Essendo un'azienda piccola, pensavamo che non saremmo mai stati in grado di avere questa tecnologia sul posto. Adesso non abbiamo solo una Fuse 1, ma ne abbiamo ben cinque in azienda. Questi apparecchi ci consentono di produrre molto velocemente parti meccaniche strutturali, non solo per i test, ma anche per applicazioni fisiche nella maggior parte dei nostri concept. Questo processo solitamente si sarebbe svolto con la lavorazione meccanica CNC, dentro o fuori dall'azienda, a seconda della geometria, e avremmo dovuto aspettare da due a quattro giorni per poter avere le parti. La Fuse 1 ci consente di fare tutto sul posto e di avere di solito le parti in meno di 24 ore", ha affermato Barnicott.
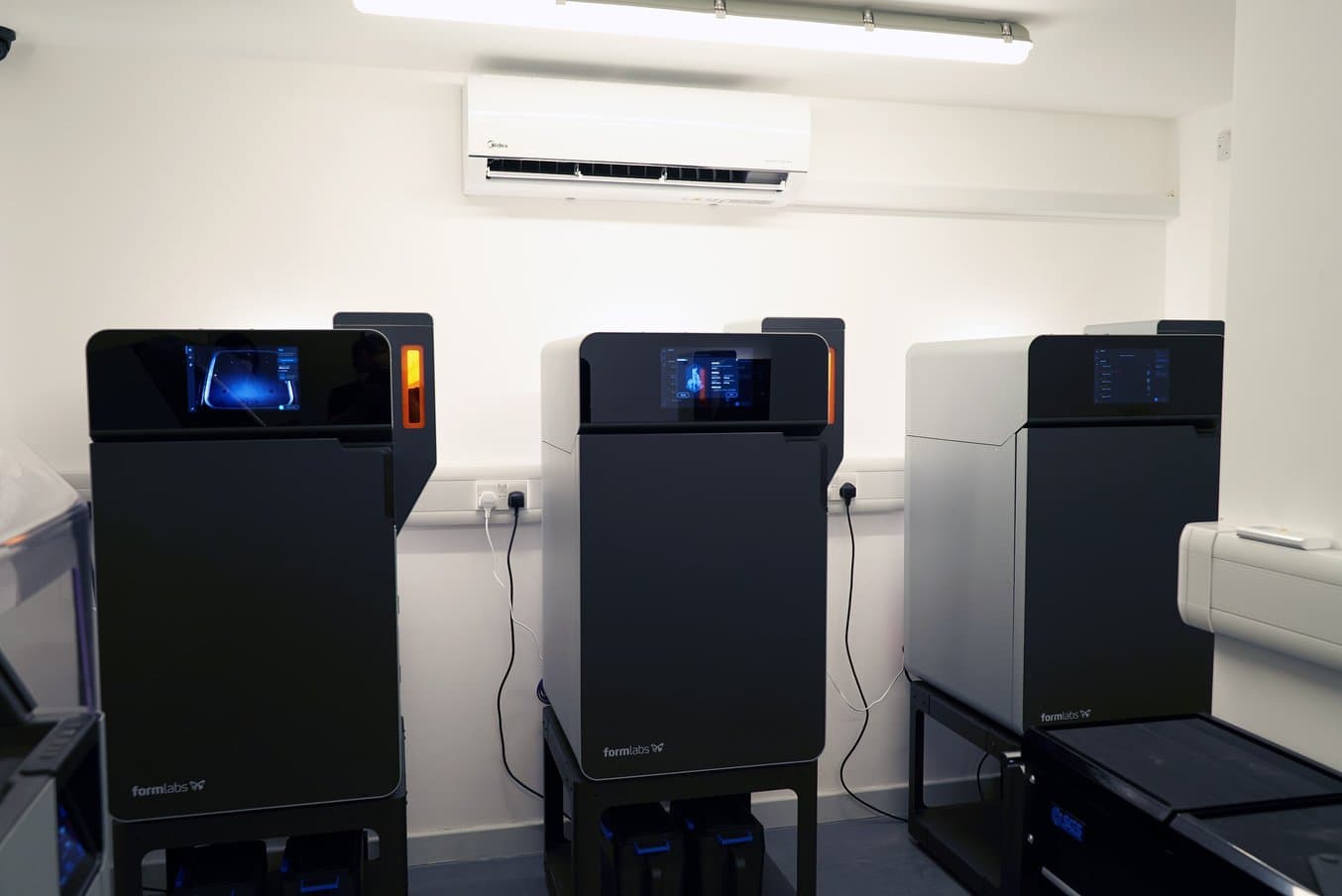
Il team utilizza le Fuse 1 soprattutto per le parti meccaniche, come le cerniere, gli interni delle maniglie e gli interni delle portiere, e per le applicazioni strutturali. Le parti si possono utilizzare da subito, sin dopo la stampa, con rifiniture minime. Alcune delle applicazioni nelle quali il team ha utilizzato le Fuse 1 comprendono:
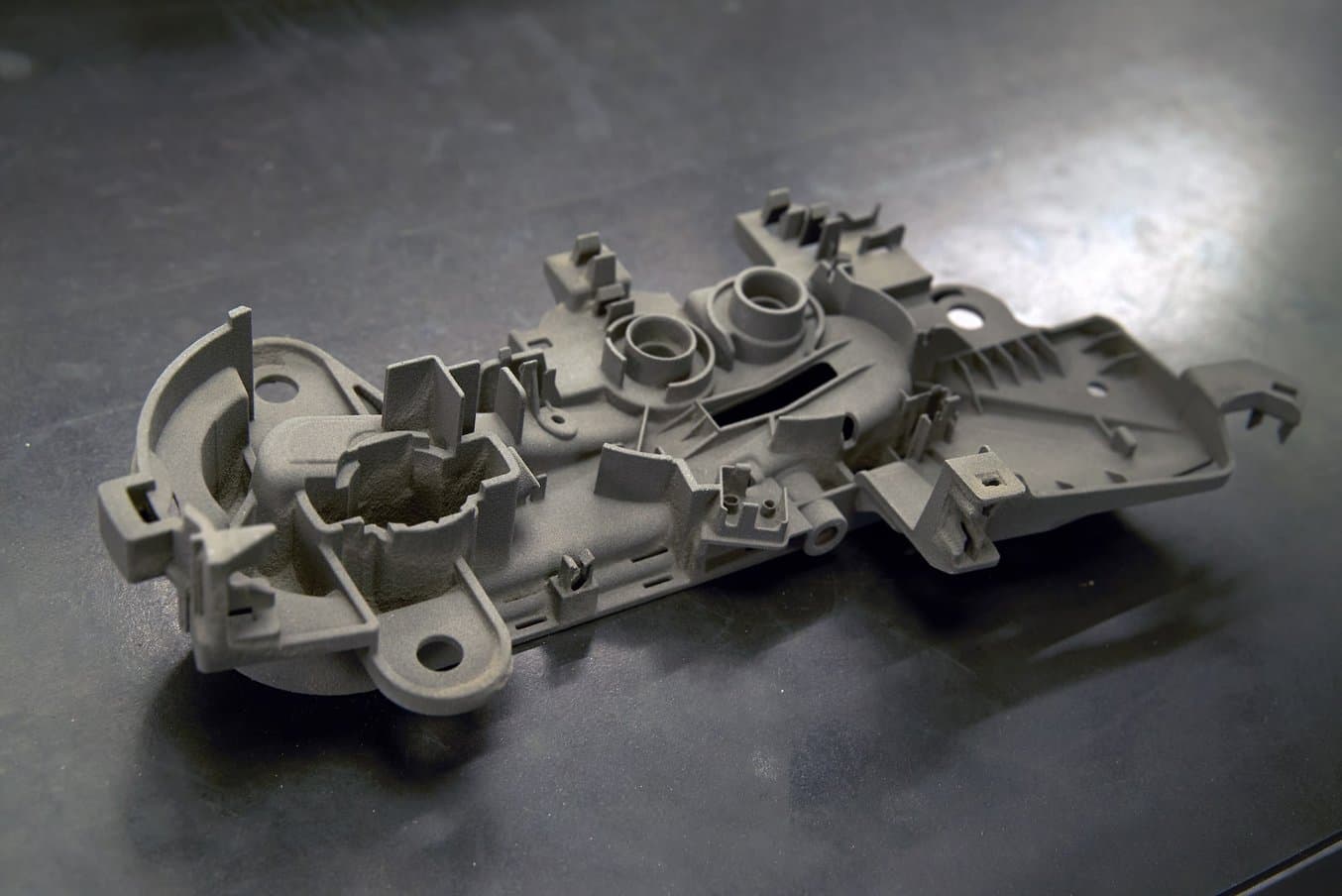
Condotti dell'aria
“Molte parti per gli interni delle automobili possono essere incredibilmente difficili da produrre senza seguire il tradizionale percorso dello stampaggio a iniezione. Si tratta di componenti come i condotti interni dell'aria e le bocchette di ventilazione, elementi che non si vedono mai, ma che hanno un costo elevato per la produzione. Per realizzarli, utilizziamo la Fuse 1. Ci permette di essere molto più versatili con i design che inseriamo nel veicolo, evitando i costi ingenti che comporterebbero normalmente."
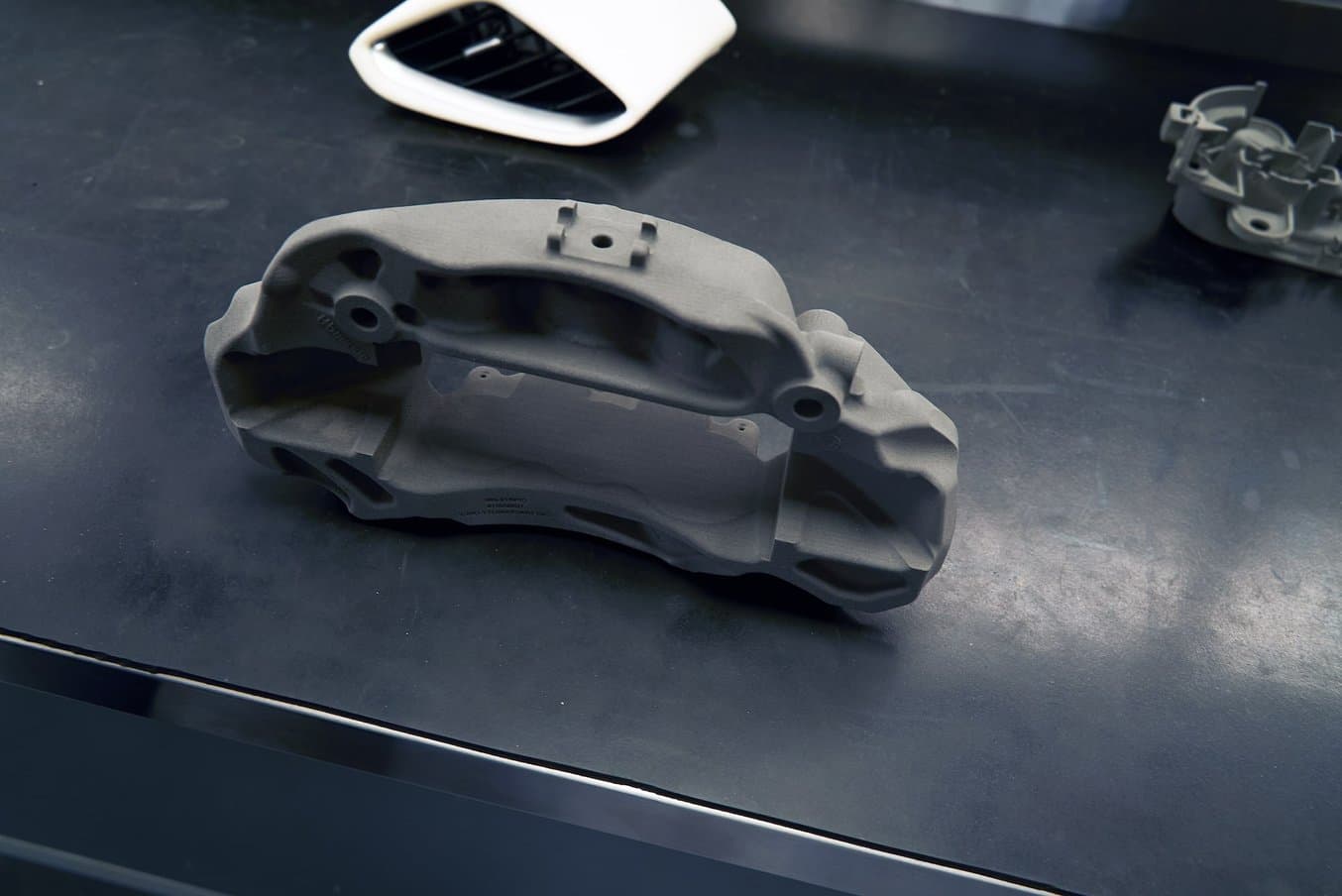
Pinze dei freni
"A volte realizziamo parti sulle quali il cliente vuole semplicemente vedere che aspetto avrebbe il loro marchio su questi componenti. Perciò dobbiamo produrli in tempi piuttosto brevi, per poter applicare il logo. Per produrre queste parti, come le pinze dei freni, utilizziamo la Fuse 1, che ci permette di inserire il logo in aree diverse delle pinze e con colori diversi. Il cliente può così valutare le varie opzioni disponibili."
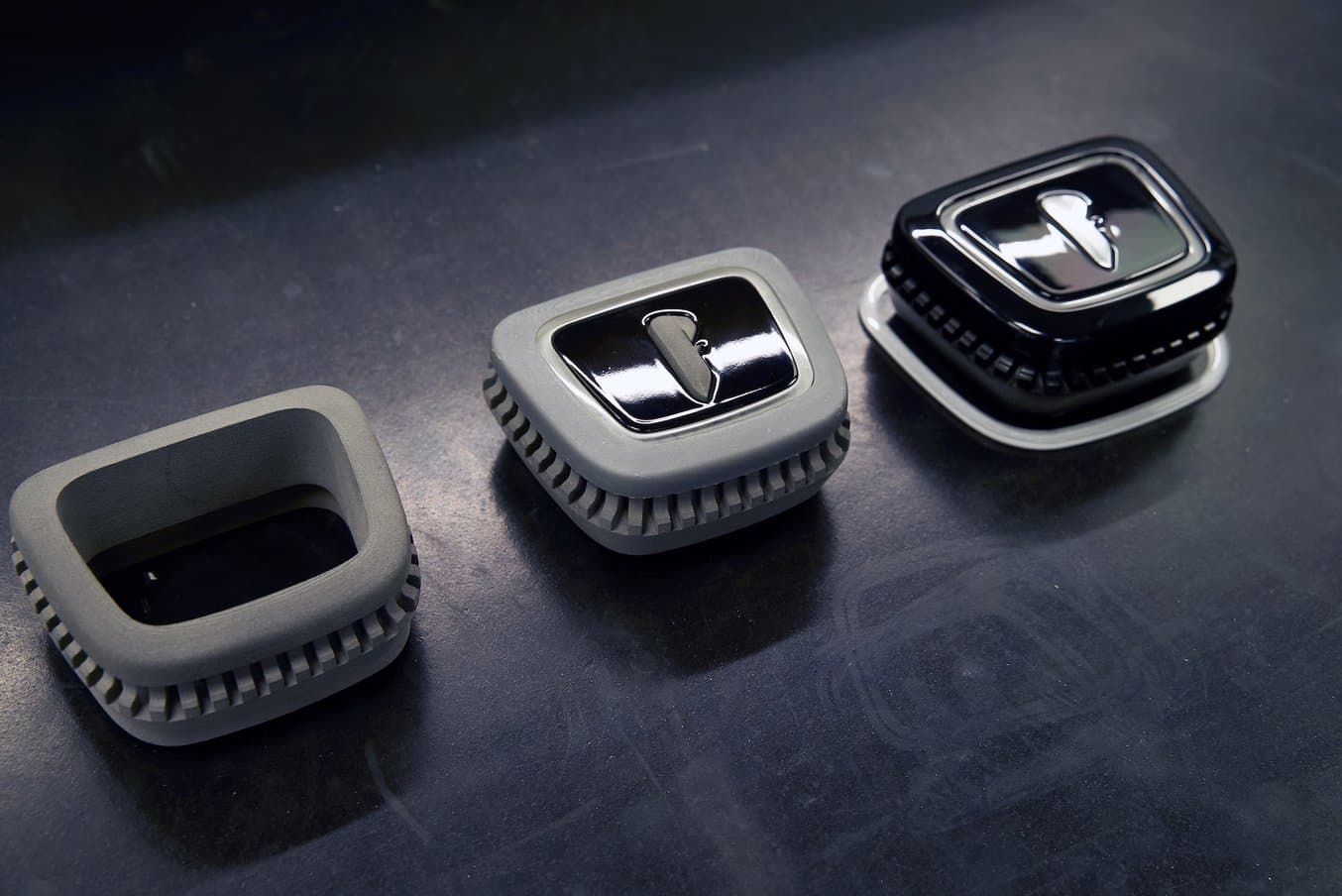
Concept interattivo per una supercar
"La stampa 3D ci ha permesso di combinare i materiali SLA con quelli SLS per realizzare diverse iterazioni di design in un progetto specifico. Questo metodo ci consente di produrre rapidamente più iterazioni, associando entrambi i processi, utilizzandoli per le loro proprietà specifiche, per ottenere un design finale. Può trattarsi di qualsiasi cosa, dalle parti meccaniche a quelle trasparenti, per verificarne la qualità ottica e la resa."
Sebbene si dica spesso che la produzione additiva sostituirà quella sottrattiva, il team di Vital Auto riconosce i vantaggi di combinare tra loro diverse tecnologie per sfruttarne i punti di forza.
"Usiamo entrambe le tecniche in maniera combinata. Per molte parti usiamo la produzione sottrattiva e poi quella additiva per realizzare i dettagli. Così possiamo produrre molti dei nostri modelli concettuali con un costo ridotto", ha spiegato Barnicott.
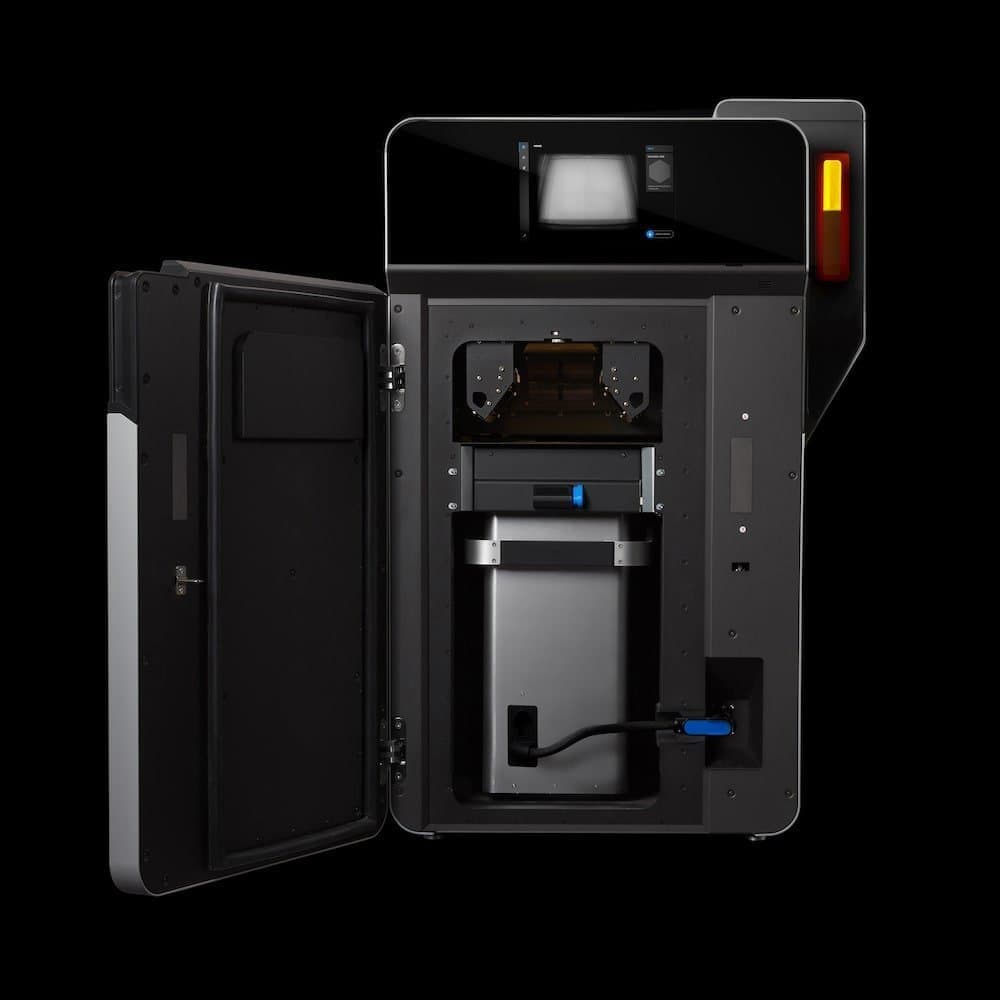
Dimostrazione di prodotto della Fuse 1
Guarda la nostra dimostrazione di prodotto per un’introduzione alla Fuse 1 e alla stampa 3D SLS svolta dagli esperti di Formlabs.
Realizzazione di concept car estremamente fedeli con la stampa 3D
"I progressi della tecnologia e della stampa 3D avvenuti negli ultimi 10 anni sono stati fenomenali. Quando ho iniziato a produrre veicoli di nicchia in quantità limitate, alcuni dei prodotti che realizziamo oggi sarebbero stati letteralmente inaccessibili. Invece adesso non solo sono in grado di produrre queste parti, ma riesco anche a produrle a costi contenuti e molto rapidamente", ha dichiarato Barnicott.
La stampa 3D non solo aiuta il team a creare prodotti migliori più velocemente, ma anche ad aumentare gli ordini. Molti dei clienti si rivolgono a loro perché vogliono avere accesso alle ultime tecnologie e vogliono che i loro componenti vengano realizzati con materiali all'avanguardia.
"Ci sono cose che non si possono più classificare come tecnologie emergenti. La stampa 3D è una di queste. È così avanzata che tutto quello che produciamo può essere utilizzato nella fase finale della presentazione, grazie a tutti i livelli di produzione che usiamo. La stampa 3D non è più una novità: ormai è parte integrante del nostro lavoro", ha detto Moradi.