La resina elettrostaticamente sicura colma il divario tra la prototipazione e la produzione della Fuse Sift
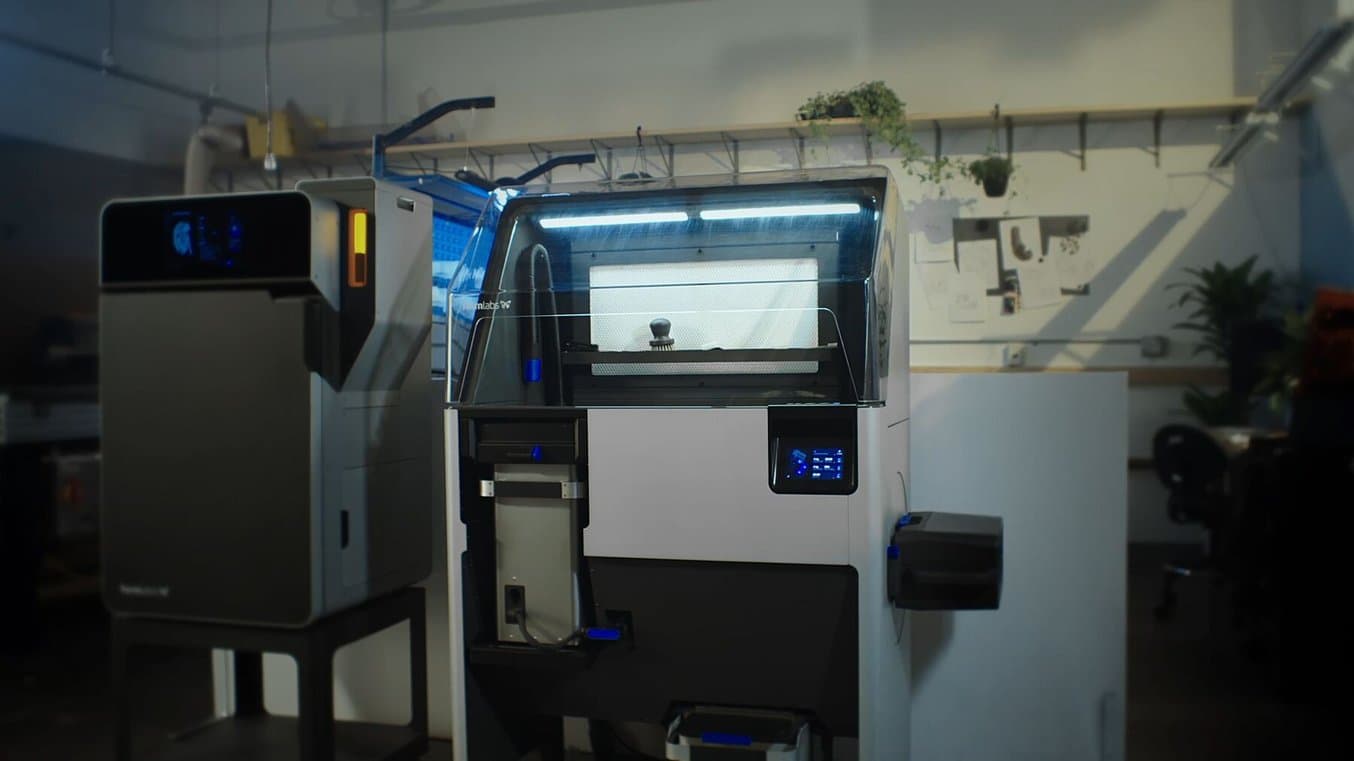
La Fuse 1 è la migliore soluzione di sinterizzazione laser selettiva (SLS) sul mercato, ma il percorso per arrivare alla produzione di massa è stato lungo. Creare la Fuse Sift, la macchina per la post-elaborazione e il riciclaggio delle polveri che semplifica il flusso di lavoro SLS, ha rappresentato una nuova sfida per il team di ingegneri di Formlabs. Per ottenere il risultato sperato sono state necessarie strategie e soluzioni uniche.
La progettazione delle parti per il sistema di contenimento della polvere nella fase finale di prototipazione della Fuse Sift ha presentato una sfida particolare. I sottosistemi di contenimento della polvere servivano a dissipare l'elettricità statica generata dalle particelle di polvere in rapido movimento, ma non dovevano avere costi proibitivi o tempistiche di realizzazione lunghe.
Scopri come il team di sviluppo è riuscito a prototipare le parti della Fuse Sift con una resina elettrostaticamente sicura, riuscendo così a spedire i prototipi ai beta tester.
Sviluppare un flusso di lavoro SLS completo
Nel 2019 Formlabs aveva un prototipo di stampante SLS potente, ma, senza un sistema di post-elaborazione di alta qualità, la stampante non poteva essere considerata una soluzione industriale. La maggior parte dei clienti stampa parti per uso finale in ambienti professionali e di produzione, perciò è di vitale importanza contenere le particelle di polveri sottili, per mantenere un'area di lavoro sicura e pulita.
Per far fronte a questa preoccupazione, il team della Fuse 1 si è dedicato alla Fuse Sift, una postazione di recupero e riciclaggio della polvere che estrae le parti dalla stampante Fuse 1. L'obiettivo della Fuse Sift era creare una soluzione completa e semplificare il flusso di lavoro della stampa SLS. Nel 2019, sia la Fuse 1 che i prototipi della Fuse Sift erano quasi pronti per il beta test esterno, ma il controllo della polvere del prototipo della Fuse Sift non era pronto per il lancio.
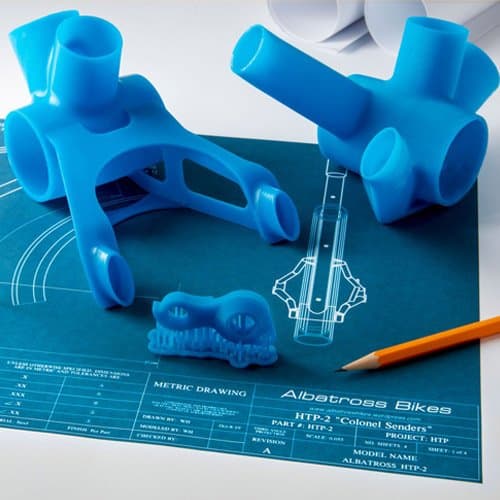
Come avere successo con la prototipazione rapida e la stampa 3D
Questo e-book affronta sei casi di studio concreti di aziende che puntano sulla stampa 3D per innovare e migliorare i processi tradizionale.
Al completamento della stampa, l'utente rimuove la camera di stampa dalla stampante Fuse 1 e la inserisce nella Fuse Sift, dove le parti finite vengono separate dalla polvere compattata non sintetizzata. L'aria viene fatta passare attraverso un filtro HEPA sul retro della superficie di lavoro coperta, per mantenere la pressione negativa nell'area di stampa e ridurre il rischio che la polvere fuoriesca dalla macchina. La polvere compattata non sintetizzata della camera di stampa viene setacciata e conservata in un serbatoio. Qui viene miscelata, nelle giuste proporzioni, con la polvere fresca, per ricaricare le cartucce di polvere per la stampa.
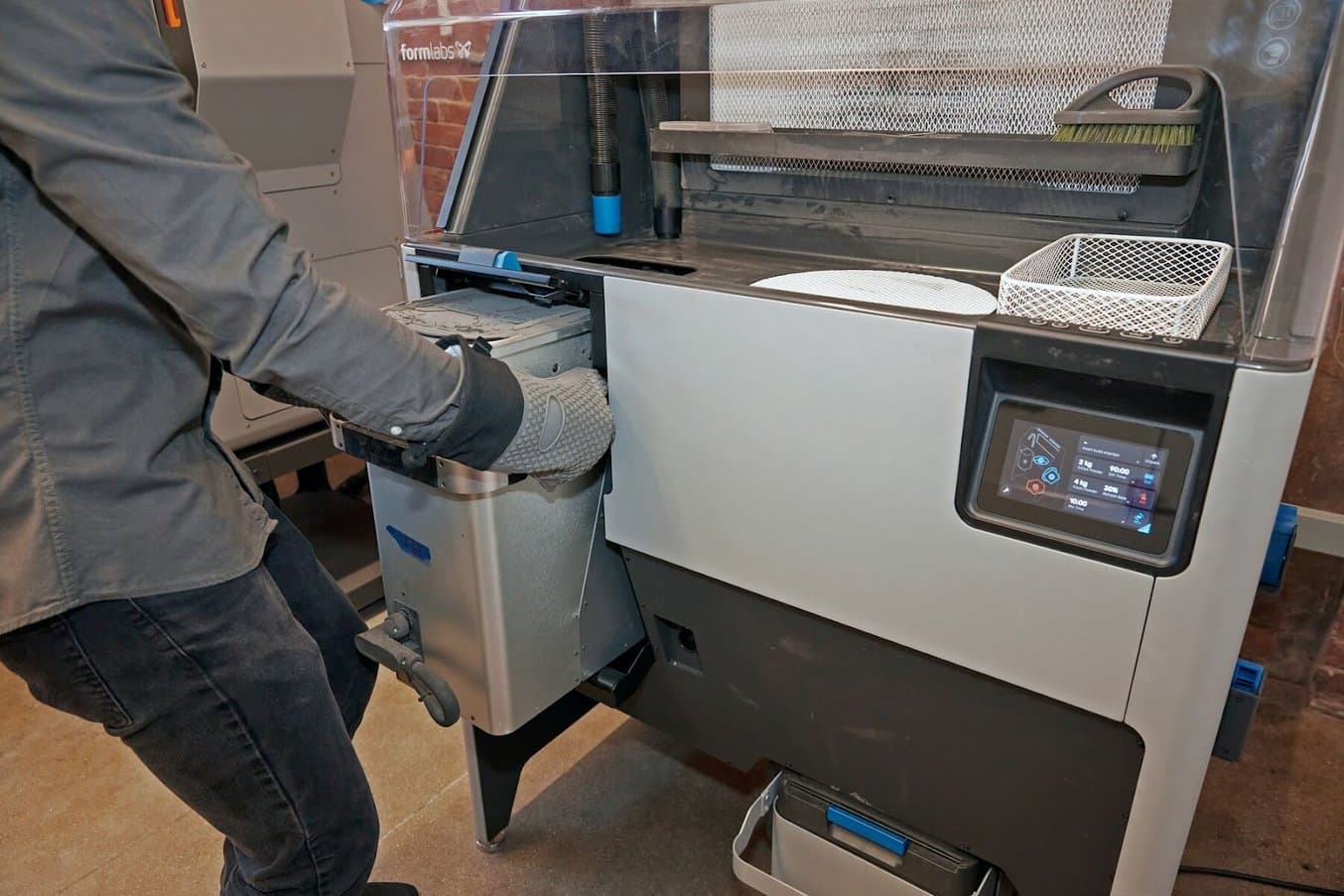
Problemi di controllo e monitoraggio della polvere
"Ci siamo concentrati a lungo sul filtro HEPA, che riusciva a rimuovere la polvere dal coperchio, ma rimaneva ancora questo strato di polvere sul piano d'appoggio, e abbiamo cercato di capire da dove uscisse. Ho fatto un paio di video che mostrano che, durante la dosatura, una valanga di polvere di nylon microscopica vola fuori dalla cartuccia. Dopo una settimana la Fuse Sift, le cartucce e il piano d'appoggio sono coperti di polvere", racconta Larry Cheung, capo ingegnere meccanico del team della Fuse Sift.
Il team ha preso in considerazione alcune opzioni, come un coperchio o un rivestimento che racchiudesse sia il sistema di dosaggio che la nuova cartuccia. Ma, poiché la cartuccia deve essere costantemente pesata durante il dosaggio per garantire la miscela ottimale di polvere fresca e usata, qualsiasi cosa a contatto con la cartuccia ne influenzerebbe il sistema di peso e sarebbe quindi da scartare.
"Abbiamo pensato, dato che avevamo già un aspirapolvere, che potevamo usarlo per tenere tutto pulito. Così abbiamo iniziato a testare un prototipo con un divisore a Y che collega i tubi dalla superficie di lavoro e dalla porta di dosaggio all'aspirapolvere. Per vedere se funzionava, l'abbiamo stampato in Draft Resin e l'abbiamo avvolto nel nastro di rame", racconta Cheung.
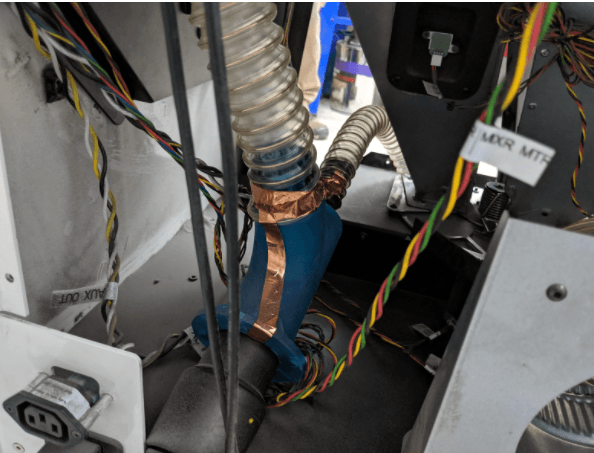
Primo prototipo di divisore a Y in Draft Resin con nastro di rame
Nonostante fosse una soluzione temporanea, il nastro di rame assicurava l'importante funzione di dissipare la carica elettrostatica causata dalla polvere di nylon che si spostava nel tubo. Dissipare efficacemente questa carica è importante per prevenire eventuali scariche elettrostatiche che metterebbero a rischio i componenti elettronici nella Fuse Sift e potrebbero diventare una fonte di ignizione per la polvere di nylon combustibile nel sistema.
Larry Cheung
"Se vengono utilizzati componenti non dissipativi, è possibile percepire e perfino vedere scosse elettrostatiche quando si fa passare una tonnellata di polvere nel sistema a una velocità elevata. Perciò l'elettrostaticità è un problema reale. Tutti i nostri sottosistemi hanno la messa a terra, e non possiamo permettere che una scarica elettrostatica li attraversi."
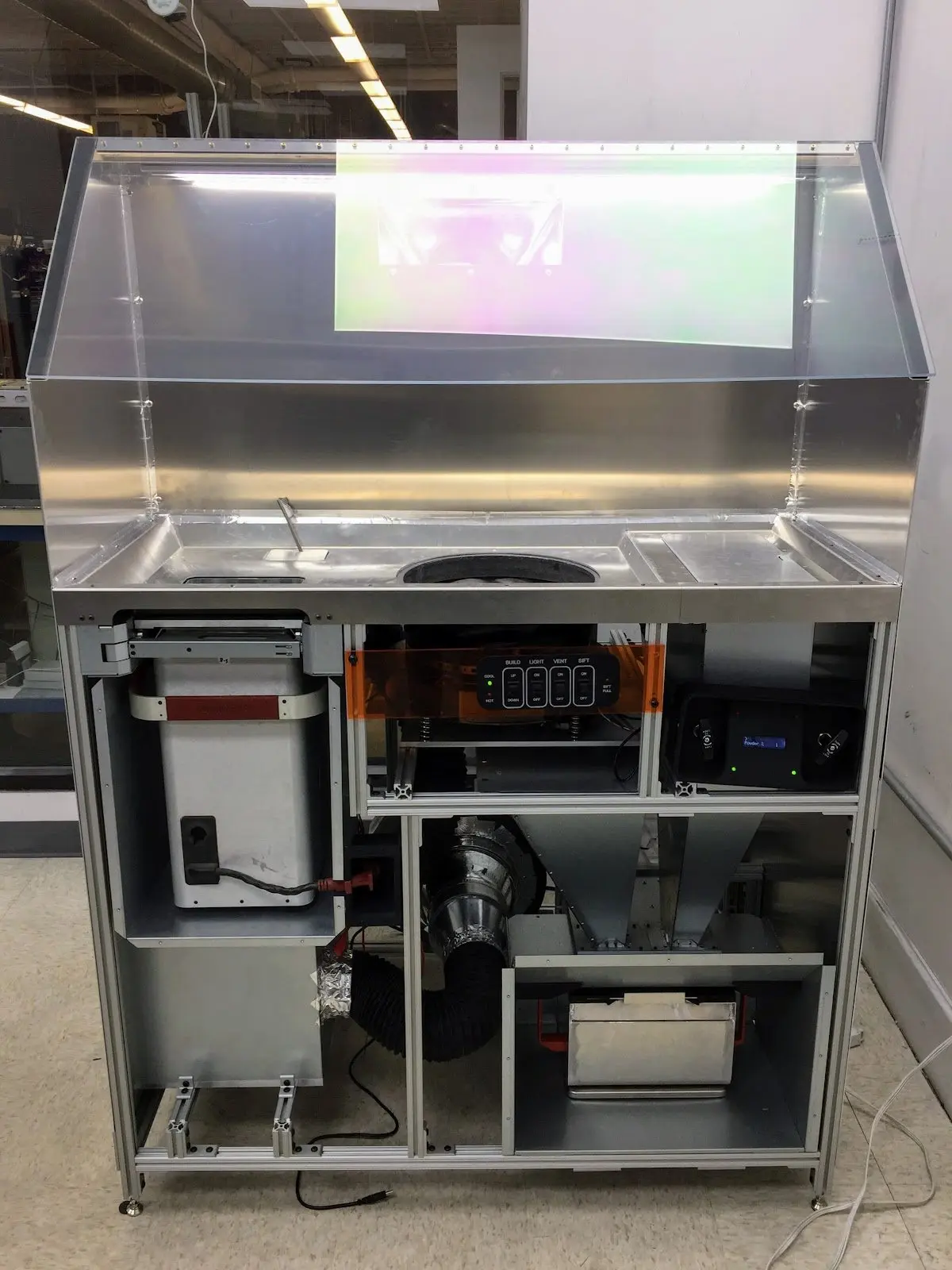
Uno dei primi prototipi della Fuse Sift.
Le correnti elettriche statiche non monitorate sono una fonte di preoccupazione per ogni produttore, con svariate implicazioni, tra cui la sicurezza del personale e l'esigenza di proteggere i dipendenti da scosse elettriche pericolose durante l'uso dell'attrezzatura, o la preoccupazione di determinare da dove provengono le scosse, se da componenti elettrici o dell'elettricità statica. Se non si riesce a individuare la fonte di un corto circuito, intere linee di prodotti possono subire danni, con costi per i produttori in termini di tempo e denaro.
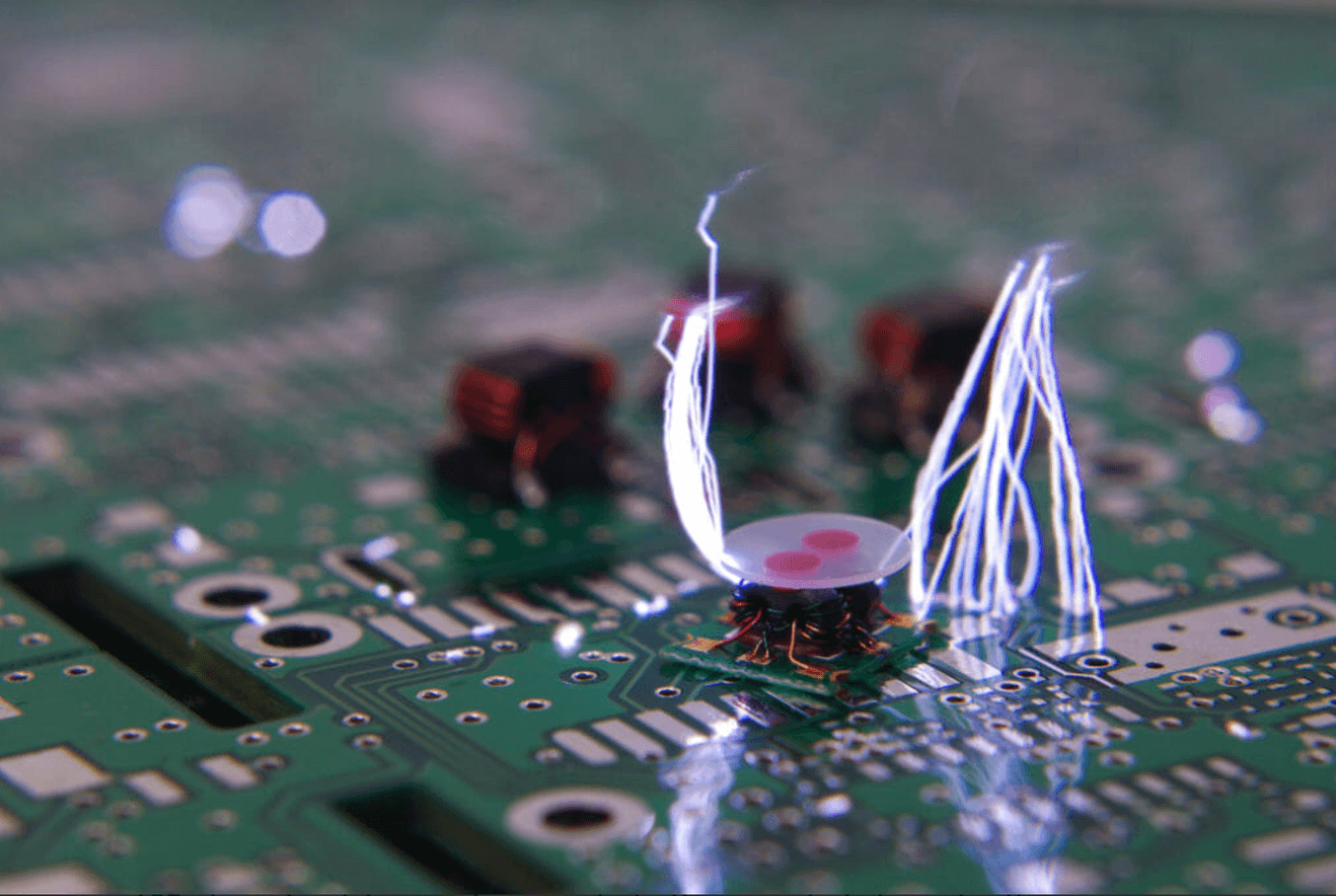
Scosse statiche che distruggono un circuito stampato.
In alcuni casi, come quello del cliente di Formlabs HAVEN, cariche elettrostatiche incontrollate possono provocare corto circuiti elettrici nei prodotti finali, il che significa che i clienti ricevono un prodotto inutilizzabile fin da subito. HAVEN ha utilizzato l'ESD Resin per creare maschere e staffaggi elettrostaticamente sicuri nella linea di assemblaggio e controllare le scariche elettrostatiche.
Ci sono quattro tipi di materiali correlati alla scarica elettrostatica:
-
I conduttivi (ad es. il metallo) consentono agli elettroni di attraversare liberamente la propria superficie, motivo per cui le attrezzature per i componenti elettrici sono spesso ricavate dal metallo.
-
I dissipativi (ad es. l'ESD Resin o altre plastiche elettrostaticamente sicure) permettono agli elettroni di muoversi verso un punto di messa a terra a una velocità minore rispetto ai metalli.
-
I materiali antistatici inibiscono la carica triboelettrica, o la carica elettrica che si crea dallo sfregamento o dal contatto con un altro materiale.
-
Gli isolanti impediscono o limitano il flusso di elettroni attraverso la loro superficie, il che significa che le cariche elettriche possono formarsi e restare lì per lunghi periodi di tempo, causando spesso danni ai circuiti elettrici con cui sono a contatto.
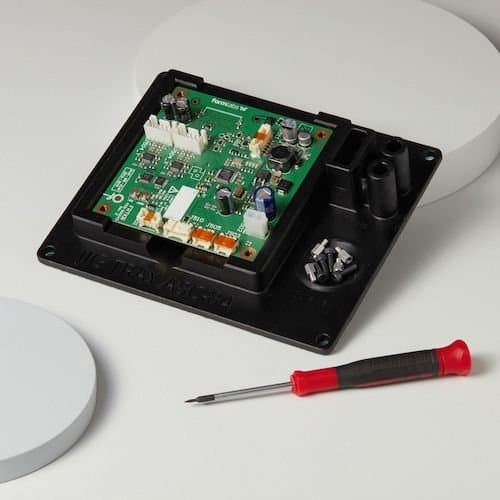
Come la stampa 3D con l'ESD Resin semplifica la produzione di componenti elettronici
Scopri dal capo ingegnere di HAVEN Indoor Air Quality, Phil Tsao, in che modo hanno usato l'ESD Resin per ridurre fino al 90% i costi e i tempi di realizzazione dei fissaggi di produzione elettrostaticamente sicuri.
Flussi di lavoro tradizionali elettrostaticamente sicuri
Di solito, le parti per uso finale per applicazioni elettrostaticamente sicure sono realizzate in metallo o in plastiche staticamente dissipative. La saldatura, la colata o la lavorazione sono tutte opzioni per l'esternalizzazione di parti metalliche con costi e implicazioni variabili. Tuttavia, durante la fase di prototipazione può essere difficile e costoso progettare, creare e montare le parti metalliche personalizzate, che potrebbero essere rese obsolete nella successiva iterazione.
"Abbiamo contattato alcuni fornitori esperti in piegatura e saldatura di tubi per avere un'idea dei costi e dei tempi di realizzazione di questa parte per la produzione a breve e a lungo termine. Tutti i preventivi ci hanno mostrato che era estremamente costosa da produrre, tra i 40 e i 50 dollari per ciascuna parte, anche per quantità da produzione di massa, il che era molto di più di quanto anticipato, e ci sarebbero volute settimane per averle. A causa dei vincoli temporali e dei costi, esternalizzare la realizzazione di queste parti per i nostri prototipi non era un'opzione conveniente. Perciò poterli produrre noi in-house e averli immediatamente a disposizione è stata davvero una svolta", afferma Cheung.
Oltre ad avvolgere una parte stampata in Draft Resin con un nastro di rame, il team ha provato a usare spray antistatici e un processo di rivestimento a immersione per ricoprire la parte in resina stereolitografica con un materiale statico dissipativo. Il problema con questo approccio era che i rivestimenti statici dissipativi non erano particolarmente resistenti all'usura e risultava difficile ottenere il rivestimento uniforme necessario per una prestazione affidabile. Per fortuna, al team della Fuse Sift era giunta voce che la soluzione poteva essere vicina.
Una soluzione nei paraggi
"Abbiamo sentito in giro che il team dei materiali stava lavorando a una resina elettrostaticamente sicura, così abbiamo contattato Kathy [Bui] (responsabile di prodotto, settore ingegneria) per vedere se potevamo stampare un paio di parti per i prototipi della Fuse Sift", racconta Cheung.
"Dato che molti dei nostri clienti realizzano design di prodotto e opere di ingegneria con le nostre resine, ci viene spesso richiesta la sicurezza elettrostatica, e questo è servito da base per lo sviluppo dell'ESD Resin. Uno degli aspetti migliori di Formlabs è che, siccome facciamo la nostra progettazione in-house, spesso abbiamo le stesse esigenze dei clienti riguardo ai nostri prodotti. Quando Larry ha descritto le sfide che il team della Fuse Sift stava affrontando, abbiamo capito che era proprio la situazione per cui avevamo progettato l'ESD Resin, quindi abbiamo colto al volo l'opportunità di mettere in pratica ciò che predichiamo", afferma Bui.
L'ESD Resin del team dei materiali non poteva arrivare in un momento migliore. I prototipi della Fuse 1 erano pronti a essere sottoposti ai beta tester esterni, e con loro doveva esserci il prototipo della Fuse Sift. Non c'era tempo di aspettare le parti da un fornitore di rivestimenti o attrezzature esterno, quindi la capacità di stampare quelle parti in-house era essenziale per rispettare i tempi del beta test.
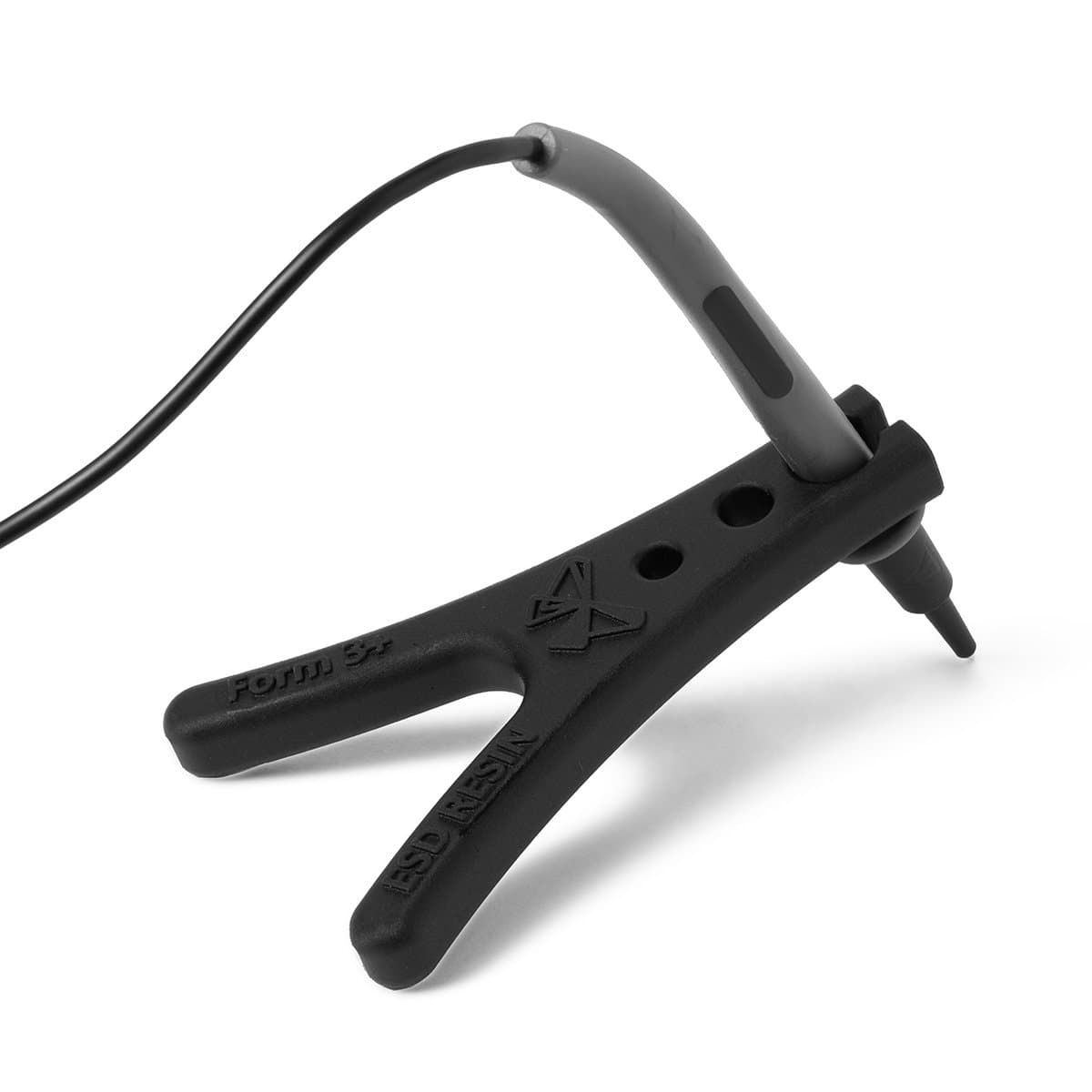
Richiedi un campione gratuito
Vuoi testare personalmente l'ESD Resin? Richiedi il nostro supporto per sonde da multimetro stampato in 3D, gratuito ed elettrostaticamente sicuro, per il tuo banco di lavorazione dei componenti elettrici. Testane la resistività superficiale per convalidarne la sicurezza elettrostatica.
Le parti in ESD Resin permettono di completare nove prototipi
Il team ha stampato nove prototipi nel materiale che è stato poi distribuito con il nome di ESD Resin. Le parti sono state approvate sulla base dei prototipi finiti della Fuse Sift, successivamente inviati a potenziali terzisti e utilizzati per beta test interni ed esterni. Usando un misuratore di resistività superficiale, il team ha scoperto che le parti stampate in ESD Resin erano dissipative statiche e perfette per i tubi attraversati da grandi quantità di polvere di nylon.
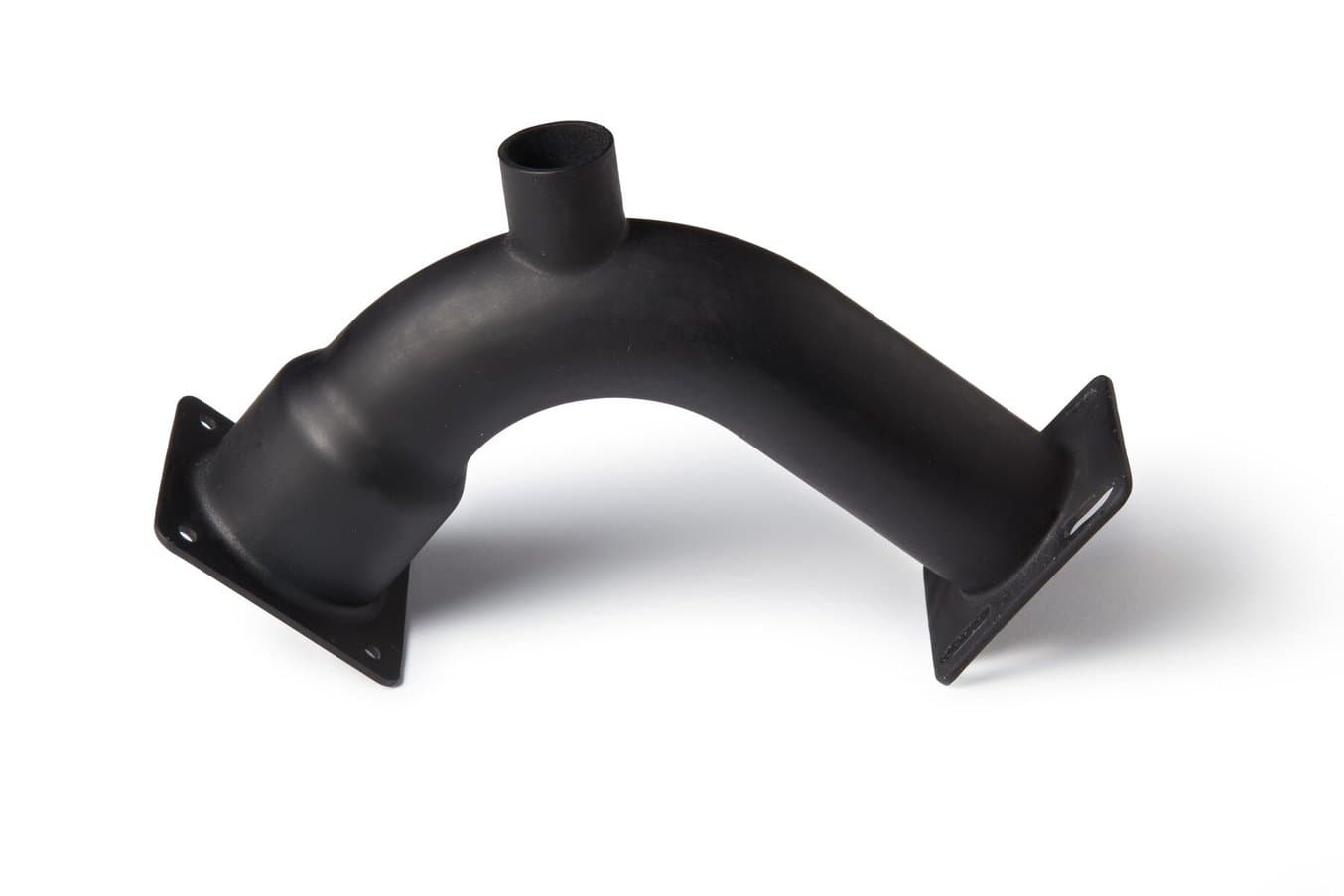
Il tubo finale della Fuse Sift in ESD Resin
"Usare l'ESD Resin ci ha permesso di colmare il divario tra prototipazione e produzione. La stampa 3D è il modo più veloce per realizzare il prototipo di una parte come questa, ma non potevamo approvare in sicurezza il concetto del divisore e dei tubi senza una soluzione elettrostaticamente sicura. L'ESD Resin ci ha consentito di progettare e convalidare in-house il nostro concetto, risparmiando centinaia, se non migliaia, di dollari in strumentazione o in parti esternalizzate", afferma Cheung.
Usare l'ESD Resin di Formlabs ha permesso ai team della Fuse 1 e dalla Fuse Sift di accorciare la strada verso la produzione, evitando i costi elevati e i lunghi tempi di lavorazione associati all'esternalizzazione di parti elettrostaticamente sicure. Per un produttore di hardware, avere gli strumenti per creare parti elettrostaticamente sicure in-house significa poter lanciare il proprio prodotto più velocemente e con meno rischi.
"Se non lo avessimo stampato internamente, ci sarebbero volute due settimane e forse duemila dollari per averlo. Sapere che potevamo produrlo noi, soprattutto quando dovevamo rispettare una scadenza con i terzisti, ci ha permesso di avere una pianificazione migliore", sostiene Cheung.