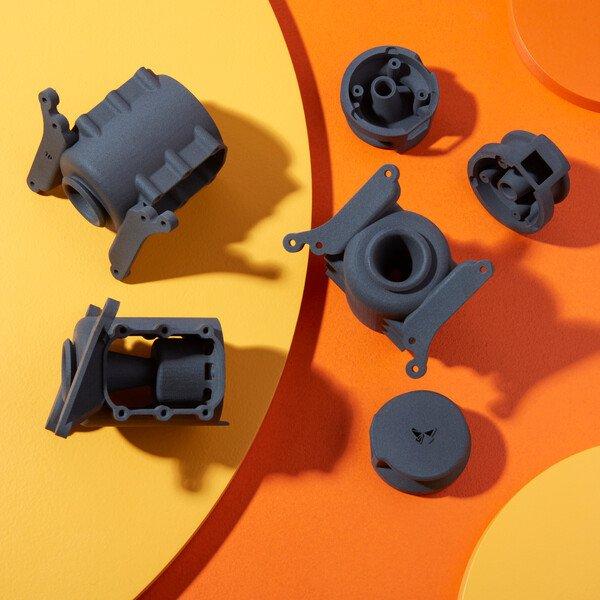
Parti per uso finale stampate con la Fuse 1
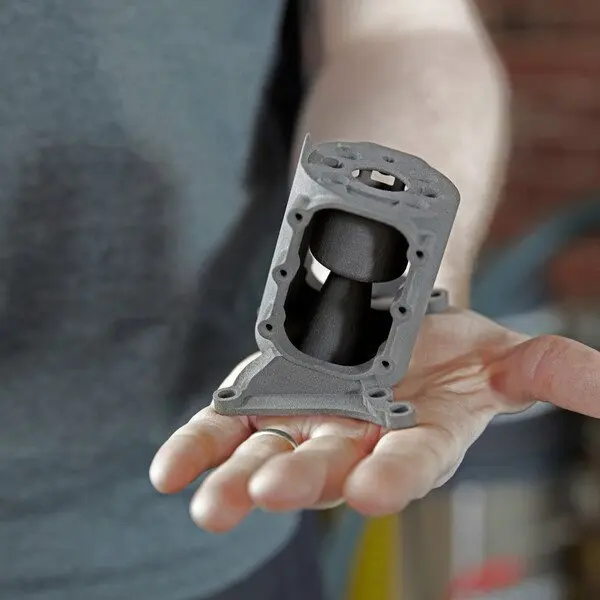
Uno spurgo per sensore IR stampato sulla Fuse 1 con la Nylon 12 Powder
Costruire la Fuse 1 è stata una vera sfida a livello ingegneristico. Includere delle prestazioni di livello industriale in una stampante 3D a sinterizzazione laser selettiva (SLS) desktop compatta e a un prezzo accessibile ha richiesto anni di lavoro di ingegneria e progettazione.
Uno degli strumenti usati dagli ingegneri Formlabs per realizzare i prototipi della parti è stata proprio la Fuse 1. Ma l’uso della stampa 3D non si è limitato alla prototipazione. Oggi, ogni unità Fuse 1 spedita ai clienti contiene diverse parti di produzione stampate direttamente sulla Fuse 1 utilizzando la Nylon 12 Powder.
L'utilizzo della stampante SLS Fuse 1 per la prototipazione e la creazione di parti per uso finale ha comportato principalmente tre vantaggi, come ci racconta Seth Berg, l'ingegnere responsabile dello sviluppo della Fuse 1:
- Libertà di progettazione nel creare parti complesse senza strutture di supporto interne.
- Accorciamento della catena di fornitura mediante la prototipazione e la creazione in-house di parti per uso finale.
- Eliminazione dell’esternalizzazione e creazione di una soluzione conveniente per la produzione di piccoli lotti con un materiale in Nylon 12 collaudato e versatile.
Prototipazione SLS e produzione in-house: stampa di uno spurgo per sensore IR
Seth Berg parla della stampa di parti per uso finale con la Fuse 1
Quando gli utenti installano la loro nuova stampante Fuse 1 e l'unità di post-elaborazione Fuse Sift, forse non sanno che ben cinque parti sono state stampate utilizzando una Fuse 1. Di queste cinque parti, lo spurgo del sensore IR è l’esempio perfetto di una parte che si può produrre in piccoli lotti con la stampa 3D SLS in-house.
Uno dei maggiori ostacoli durante la creazione della Fuse 1 è stata la misurazione e il bilanciamento della temperatura interna della camera di stampa. Verso la fine del processo di produzione della Fuse 1, Berg sapeva che il suo team doveva affrontare uno degli ostacoli più importanti: era necessario uno spurgo del sensore IR personalizzato per regolare correttamente il calore all'interno del vano di stampa. Vista l’importanza della precisione della temperatura all'interno del vano di stampa, il team prevedeva di dover creare decine di prototipi per poter trovare lo spurgo del sensore IR giusto e la prospettiva di esternalizzare o utilizzare lo stampaggio a iniezione non era l'ideale a causa del numero di prototipi richiesti. Quindi il team ha deciso di usare la versione beta della Fuse 1 con la Nylon 12 Powder sia per prototipare che per produrre le parti. "Avevamo bisogno di una tecnologia di stampa 3D che non ci vincolasse nella geometria e non posizionasse supporti sulle superfici dove volevamo un flusso d'aria libero. Per questo la stampa SLS era davvero l'unica opzione di stampa 3D che avrebbe potuto funzionare", racconta Berg.
Il team ha quindi iniziato a lavorare utilizzando le prime unità di produzione della Fuse 1 per progettare, testare e infine produrre parti personalizzate su larga scala in modo da poter introdurre la Fuse 1 sul mercato. Con il passare del tempo hanno iniziato a creare più parti: maniglie degli sportelli, manici per il sensore, maniglie per la Fuse Sift, tutte in-house con la versione beta della Fuse 1. Oggi tutte le unità di Fuse 1 vendute contengono diverse parti di produzione stampate direttamente su una Fuse 1. “Abbiamo testato queste parti in modo molto rigoroso. Abbiamo circa 50 stampanti nella sede centrale che lavorano ininterrottamente per stampare queste parti. Le abbiamo testate per un'applicazione di stampa reale per migliaia e migliaia di ore", ha affermato Berg.
Dopo decine di prototipi per lo spurgo del sensore IR, il team ha scelto il design finale. Sono passati in maniera molto fluida dalla prototipazione alla produzione di piccoli lotti sulle stesse stampanti Fuse 1. Con migliaia di parti stampate ogni settimana, la linea di produzione Fuse 1 è stata un'ulteriore conferma che l’apparecchio era pronto per essere lanciato sul mercato. Berg racconta: "In Formlabs, pensiamo all'accessibilità dei prodotti sia dal punto di vista del prezzo, creando prodotti a prezzi accessibili, ma anche dal punto di vista della manutenzione. La cosa peggiore è arrivare in laboratorio al mattino e vedere che la stampa non è riuscita. Vedere la Fuse 1 in azione sia per la prototipazione che come macchinario di produzione a tempo pieno è stato veramente gratificante”.
Grazie all’ampia capacità di carico della Fuse 1, la camera di stampa è in grado di contenere 12 spurghi per il sensore IR per ciclo di stampa. Per le parti più piccole come la maniglia del sensore IR, si arriva a 60 parti per ciclo di stampa. Sebbene la stampa 3D in-house non abbia ancora senso per la produzione di massa di milioni di parti, l’uso di diversi apparecchi in contemporanea è un’ottima soluzione per lotti di piccole e medie dimensioni. La stampa di ciascuna maniglia del sensore IR richiede 22 g di polvere e il costo è di 2 $ per parte. Lo spurgo del sensore IR principale richiede 70 g di polvere, al costo di circa 7 $ per parte.
Secondo Berg, "avere la Fuse 1 in-house ci ha aiutato a creare uno spurgo per il sensore IR migliore, perché siamo stati in grado di eseguire iterazioni più rapide e di provare più design, passando poi direttamente alla produzione utilizzando lo stesso materiale". Ciò significa che il team non ha dovuto modificare le tolleranze tra prototipazione e produzione.
Seth Berg
Avere la Fuse 1 in-house ci ha aiutato a creare uno spurgo per il sensore IR migliore, perché siamo stati in grado di eseguire iterazioni più rapide e di provare più design, passando poi direttamente alla produzione utilizzando lo stesso materiale.
Secondo Berg, senza la Fuse 1 il team avrebbe dovuto continuare a esternalizzare la stampa SLS di queste parti. Berg ha poi aggiunto: "Se non avessimo avuto la Fuse 1 in-house, avremmo esternalizzato le parti SLS a un servizio esterno, che sarebbe stato più costoso, e avremmo impiegato più tempo per avere le parti. Con la Fuse 1 stampiamo in-house parti SLS per uso finale di qualità industriale a una frazione del prezzo e del tempo”.
Berg ha affermato che nel suo team “sono convinti che le parti funzioneranno bene in questa applicazione e che ogni Fuse 1 che distribuiremo avrà parti stampate con la Fuse 1”. Lo spurgo del sensore IR, la maniglia del sensore, la maniglia della porta e il coperchio del magnete di interblocco sono stati tutti resi possibili dalla Fuse 1.
La Nylon 12 Powder per parti per uso finale
Il primo materiale che Formlabs ha lanciato per la Fuse 1 è la Nylon 12 Powder, un materiale estremamente versatile, adatto sia alla realizzazione di prototipi funzionali, sia alla produzione di assemblaggi complessi e parti per utilizzo finale resistenti e con un’elevata stabilità ambientale.
Anche se ci sono altri processi di stampa 3D che possono essere utilizzati per parti per uso finale, la stampa SLS offre un insieme di proprietà che hanno reso più vantaggiosa la stampa di parti per la Fuse 1. Innanzitutto, le parti SLS tendono a durare più a lungo, soprattutto se maneggiate o utilizzate ogni giorno. Rispetto ai materiali per stereolitografia, le parti in Nylon 12 Powder offrono una maggiore vita utile, meno attrito e più resistenza all'usura, ai prodotti chimici e ai raggi UV. “Esistono molti tipi diversi di parti per uso finale, ma quasi tutte devono essere robuste e resistenti sia alla temperatura che agli urti. Il nylon è il materiale che rappresenta al meglio tutte queste proprietà. Quindi se hai in mente un’applicazione per la quale vorresti stampare una parte e usarla, il nylon è quasi sicuramente una buona opzione”, ha affermato Berg.
Una caratteristica della stampa SLS a polvere che è particolarmente importante per la creazione di uno spurgo personalizzato per il sensore IR è stata la possibilità di stampare parti senza supporti interni. Con altri processi di stampa 3D, le fessure e le aperture interne richiederebbero strutture di supporto e le parti devono essere progettate tenendolo presente. La stampa SLS elimina questo problema, consentendo di creare e utilizzare parti complesse con tempi di post-produzione drasticamente ridotti.
Infine, la Nylon 12 Powder consente alla Fuse 1 di stampare con fino al 70% di polvere riciclata. Questo è un enorme vantaggio sia per la prototipazione che per la produzione con la Fuse 1, in quanto permette ai team di ingegneri di sfruttare al massimo ogni grammo di polvere acquistata. Per il team di Berg questo è uno dei motivi principali per cui la Fuse 1 si è rivelata un'opzione di produzione competitiva, e affermano che "tutte le parti stampate e installate sulla Fuse 1 sono stampate con il 70% di polvere riutilizzata. Questo è uno dei segreti che la rende un’opzione di produzione in-house competitiva a livello di costi.” Berg ci ha detto inoltre “e non abbiamo utilizzato la polvere riciclata solo per i prototipi. Nella linea di produzione della Fuse 1 stampiamo tutte le parti con il 70% di polvere riciclata, comprese le parti per uso finale”.
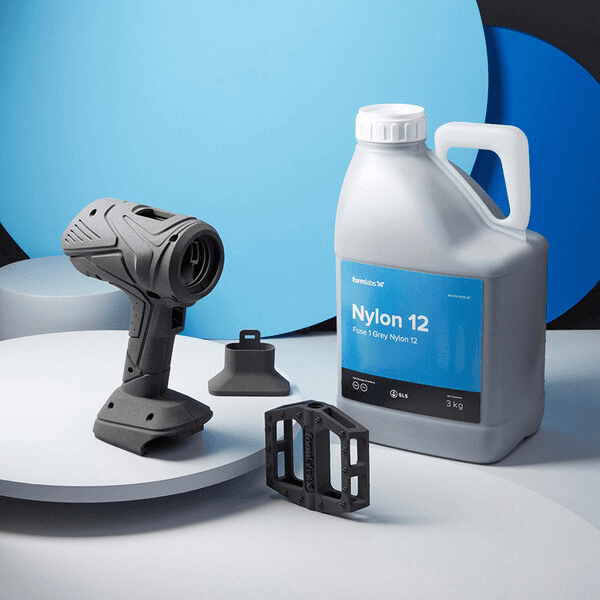
Nylon 12 Powder
La Nylon 12 Powder è un materiale estremamente versatile, adatto sia alla realizzazione di prototipi funzionali, sia alla produzione di assemblaggi complessi e parti per utilizzo finale resistenti e con un’elevata stabilità ambientale. Abbiamo creato un articolo con tutte le domande più frequenti.
La Fuse 1: spedizioni avviate
Formlabs è nota per la progettazione di workflow di produzione additiva in grado di consentire alle aziende di tutte le dimensioni di accedere alla stampa 3D di qualità industriale. La Fuse 1 e la Fuse Sift permettono alle aziende di avere il controllo completo sul design di prodotto, di stampare in-house parti in nylon pronte alla produzione, di incrementare il rendimento e di integrare nei propri laboratori la stampa 3D SLS di qualità industriale. E tutto questo a un prezzo davvero accessibile. Tutti questi vantaggi, la versatilità della Nylon 12 Powder e i benefici specifici della stampa 3D SLS sono stati di grande aiuto per Berg e il team di ingegneri Formlabs durante la creazione della Fuse 1.
Vuoi vedere da vicino le parti per uso finale stampate con la Fuse 1? Richiedi un campione gratuito.