Uno sguardo all'interno di Google ATAP: superare le sfide di pre-produzione grazie alla stampa 3D
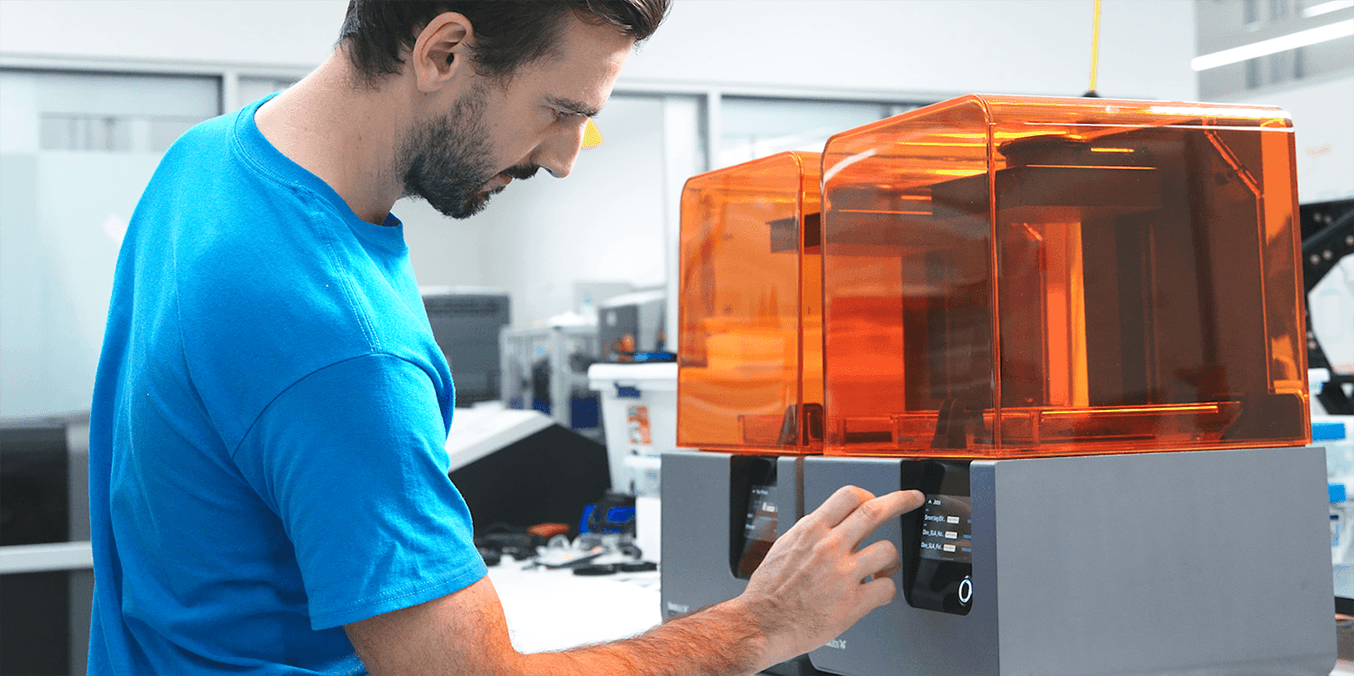
Il laboratorio Google Advanced Technology and Projects (ATAP) è stato creato per essere un centro di ricerca unico nel suo genere, in grado di dare vita a progetti hardware. Il laboratorio offre uno sguardo sul futuro dei prodotti e della produzione, ma utilizza approcci di risoluzione dei problemi che qualsiasi azienda può implementare subito: da una mentalità iterativa in ogni fase dello sviluppo a un set di strumenti tecnologici che consente soluzioni agili e creative.
In un caso, l'approccio del team ha portato a un'innovazione di processo, che ha permesso di aggirare la complessa catena di fornitura della fase di validazione pre-produzione di un dispositivo indossabile sovrastampato. Utilizzando la High Temp Resin di Formlabs, un materiale per la stampa 3D con un'elevata stabilità termica, hanno colmato il divario tra prototipazione e produzione, riducendo dell'85% i tempi di realizzazione di un componente cruciale, con un risparmio di oltre 100 000 $.
Guarda il video per scoprire come Google ATAP ha usato la produzione additiva per colmare il divario tra prototipazione e produzione, utilizzando le stampanti 3D di Formlabs e la High Temp Resin per risolvere una sfida di pre-produzione di un dispositivo indossabile sovrastampato complesso.
"Non stiamo studiando solo come saranno i prodotti in futuro, ma anche come sarà la produzione. La produzione additiva è davvero un elemento importante di questo processo ed è molto legata a numerosi progetti su cui stiamo lavorando" spiega Bryan Allen, tecnologo di progettazione di Google ATAP, specializzato nella stampa 3D e nelle tecnologie di fabbricazione avanzate.
"Sono davvero entusiasta quando riusciamo a identificare qualche nuovo sviluppo nella stampa 3D, un materiale o un processo innovativo, e poi applicarlo ai progetti in maniera inedita, così da poter realizzare qualcosa in modo più efficiente, più veloce, migliore o più piacevole dal punto di vista estetico."
Dentro al caso di studio: una sfida di pre-produzione
Il team era bloccato. Si trovava nella fase di pre-produzione, durante il processo di sovrastampaggio di un dispositivo indossabile, e doveva ottenere risultati in maniera più rapida. Il processo era nuovo, la catena di fornitura era complessa e dovevano superare questo passaggio prima di poter spedire.
"L'elettronica veniva sovrastampata due volte, perciò avevamo a disposizione un oggetto flessibile e impermeabile, che potevamo usare in un dispositivo indossabile" spiega David Beardsley, manager del negozio di modelli per il laboratorio Google ATAP.
Il sovrastampaggio è un processo di fabbricazione comune. Nel caso di una parte sovrastampata senza elettronica, una fabbrica può realizzare migliaia di articoli al costo di pochi centesimi per parte o assemblaggio. Tuttavia, il team ATAP stava eseguendo un secondo sovrastampaggio su un sottoinsieme elettronico sovrastampato, un circuito stampato (ingl. "printed circuit board assembly", PCBA) con elettronica complessa proveniente da un altro stabilimento; perciò i materiali di partenza erano costosi e i tempi di realizzazione del prodotto finale dipendevano dalla rapidità con cui la prima fabbrica poteva produrre e consegnare gli articoli.
Il sovrastampaggio è un processo di stampaggio a iniezione che richiede tipicamente la messa a punto iniziale dell'attrezzatura in fabbrica per le nuove parti, note come primi articoli. Questi prodotti potrebbero essere troppo pieni, troppo vuoti o avere problemi estetici, dato che i parametri di stampaggio devono essere calibrati. Durante la risoluzione dei problemi, gli ingegneri di produzione si assicurano che gli arresti della macchina e i livelli di pressione siano corretti, e che tutti i parametri di stampaggio siano impostati correttamente.
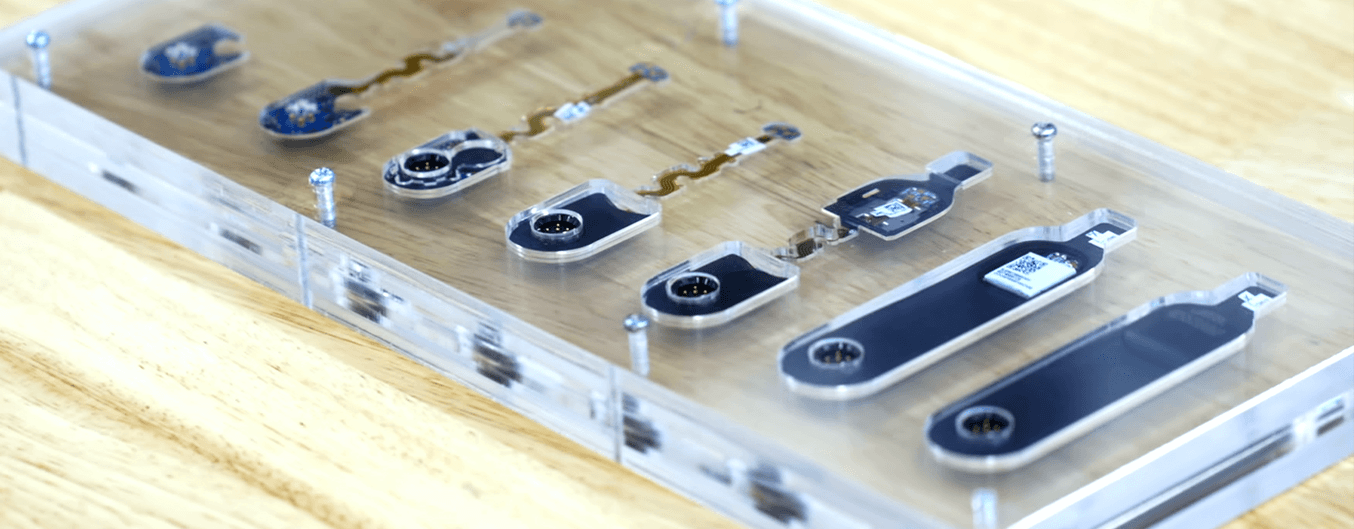
Il dispositivo indossabile al principio è un circuito stampato popolato di componenti. Viene quindi incapsulato in un sistema di stampaggio a bassa pressione, che lo trasforma in un blocco di plastica. Questo circuito stampato e un cavo flessibile formano il sottoinsieme elettronico che viene poi sovrastampato in un ibrido di uretano termoplastico (TPU) e gomma di silicone. Il circuito viene quindi sottoposto al passaggio di sovrastampaggio finale.
Quando si apprestava a iniziare la pre-produzione, il team ha capito che il costo dei primi articoli sarebbe stato molto più alto rispetto a una tipica parte stampata a iniezione. Quello che non avevano previsto era il collo di bottiglia della catena di fornitura: ci sono volute tre settimane per ottenere i sottoinsiemi elettronici sovrastampati di cui avevano bisogno per eseguire questi test. Beardsley doveva accorciare i tempi per aumentare i livelli di produzione e spedire i prodotti.
"Potresti aver bisogno di centinaia o migliaia di prodotti per calibrare gli strumenti. Il problema è che se usi componenti elettronici con vere schede al loro interno e le invii per eseguire il sovrastampaggio, devi tenere conto dell'intera catena di fornitura" spiega Beardsley.
"Si tratta di soldi e tempo sprecato solo per cercare di impostare lo strumento. Come facciamo a provare che il prodotto funziona se non riusciamo neanche a inserirvi dei componenti elettronici funzionanti?"
Dovevano trovare un processo e un materiale che potesse sostituire il circuito stampato. Questo prodotto doveva essere accurato dal punto di vista dimensionale e rappresentare l'esatta geometria del sottoinsieme reale, in modo che il riempimento potesse essere caratterizzato, e sufficientemente robusto da consentire allo strumento di chiudersi al pezzo senza rompersi o deflettersi, con conseguenti sbavature eccessive.
"Sapevamo di dover utilizzare un materiale in grado di resistere a migliaia di chili di pressione e temperature superiori ai 250 °C" spiega Beardsley. "Avevamo bisogno di alta resistenza alle temperature e alto tasso di rigidità."
Beardsley contattò Allen per chiedere il suo aiuto, e insieme idearono un piano.
“Sapevamo di dover utilizzare un materiale in grado di resistere a migliaia di chili di pressione e temperature superiori ai 250 °C. Avevamo bisogno di alta resistenza alle temperature e alto tasso di rigidità.”
David Beardsley, Google ATAP
La soluzione: parti surrogate stampate in 3D con la High Temp Resin
I parametri erano stretti. Allen decise di provare a stampare in 3D dei sostitutivi, o parti surrogate, in High Temp Resin sulla stampante 3D stereolitografica (SLA) Form 2. Sapeva che avrebbe spinto al limite il materiale: le parti finali sarebbero state iniettate a 270 °C a una pressione di 27 000 psi, ossia all'estremità superiore della temperatura di distorsione termica (ingl. "heat deflection temperature", HDT) pubblicata per la High Temp Resin.
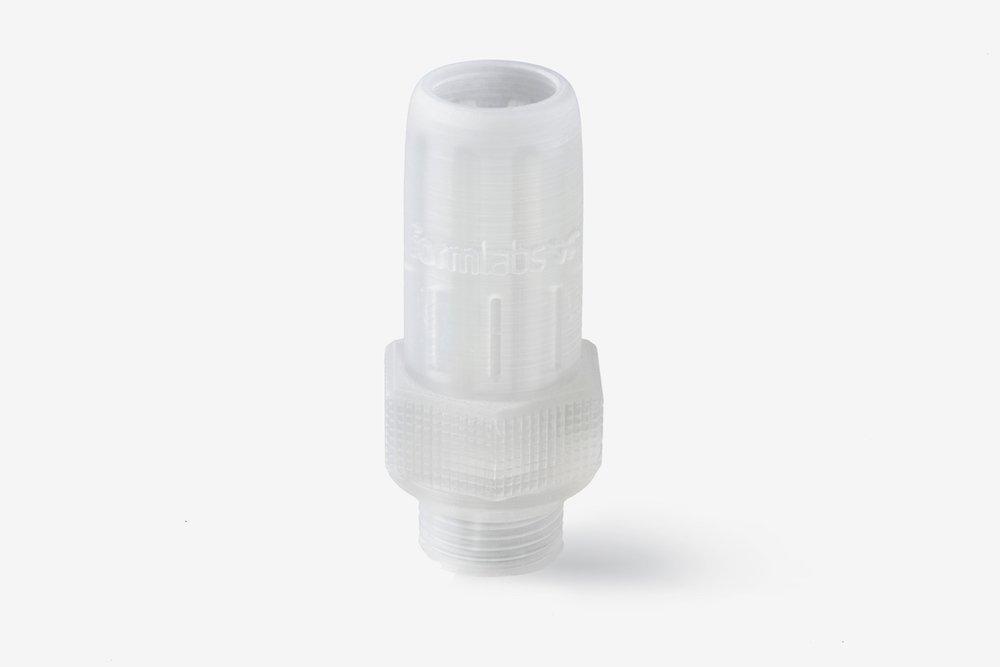
Richiedi un campione
Scopri l'ultima formulazione e molte altre applicazioni di questo materiale per la stampa 3D resistente al calore, oppure richiedi un campione gratuito.
Richiedi un campione gratuito"Per poter ottenere i dettagli di piccole dimensioni e le valvole di cui necessitavamo, avevamo bisogno di quella risoluzione. È stata proprio la combinazione di risoluzione e resistenza alle alte temperature che ci ha permesso di utilizzare la Form 2 per questa operazione" spiega Allen. "Siamo in grado di selezionare molte altre tecnologie di fabbricazione, ma avere l'opzione di realizzare queste parti è davvero importante per il nostro laboratorio."
"Siamo in grado di selezionare molte altre tecnologie di fabbricazione, ma avere l'opzione di realizzare queste parti è davvero importante per il nostro laboratorio."
Bryan Allen, Google ATAP
Il team si è messo subito al lavoro, stampando durante la notte alcune parti da testare.
"Non avevamo abbastanza tempo per modificare i modelli CAD. Ho aperto il file, l'ho esportato come STL e l'ho caricato nel software PreForm. Una volta ottenuto il primo lotto di validazione, abbiamo iniziato a prendere velocità. Abbiamo realizzato 200 parti nel primo ciclo e poi altre 100" racconta Allen.
PreForm è il software di preparazione della stampa gratuito di Formlabs, che può essere utilizzato per disporre le parti in lotti sulla piattaforma di stampa. Una volta presa velocità, Allen ha stampato 250 inserti in lotti da 10, che hanno richiesto circa quattro ore ciascuno, così il team è stato in grado di produrre centinaia di parti nel corso di un fine settimana.
Allen ha posizionato dei supporti sulle parti in High Temp Resin, in modo che i segni lasciati dai supporti fossero solo sulle parti che si chiudono, non sulle superfici di stampaggio. In questo modo le parti non richiedevano ulteriori operazioni di levigazione o finitura oltre a un normale ciclo di lavaggio e polimerizzazione post-stampa prima dell'uso.
Le parti stampate in 3D hanno funzionato perfettamente come sostituti dei sottoinsiemi elettronici. Il processo ha ridotto il tempo di realizzazione degli inserti con circuito stampato da tre settimane a tre giorni, e il costo per unità è sceso da 100 $ a 0,80 $.
"Ci ha permesso di intercettare il processo in una fase più avanzata e quindi evitare una serie di passaggi iniziali. In questo modo, tre o quattro fasi precedenti sono state eliminate. Abbiamo risparmiato un sacco di tempo" spiega Beardsley.
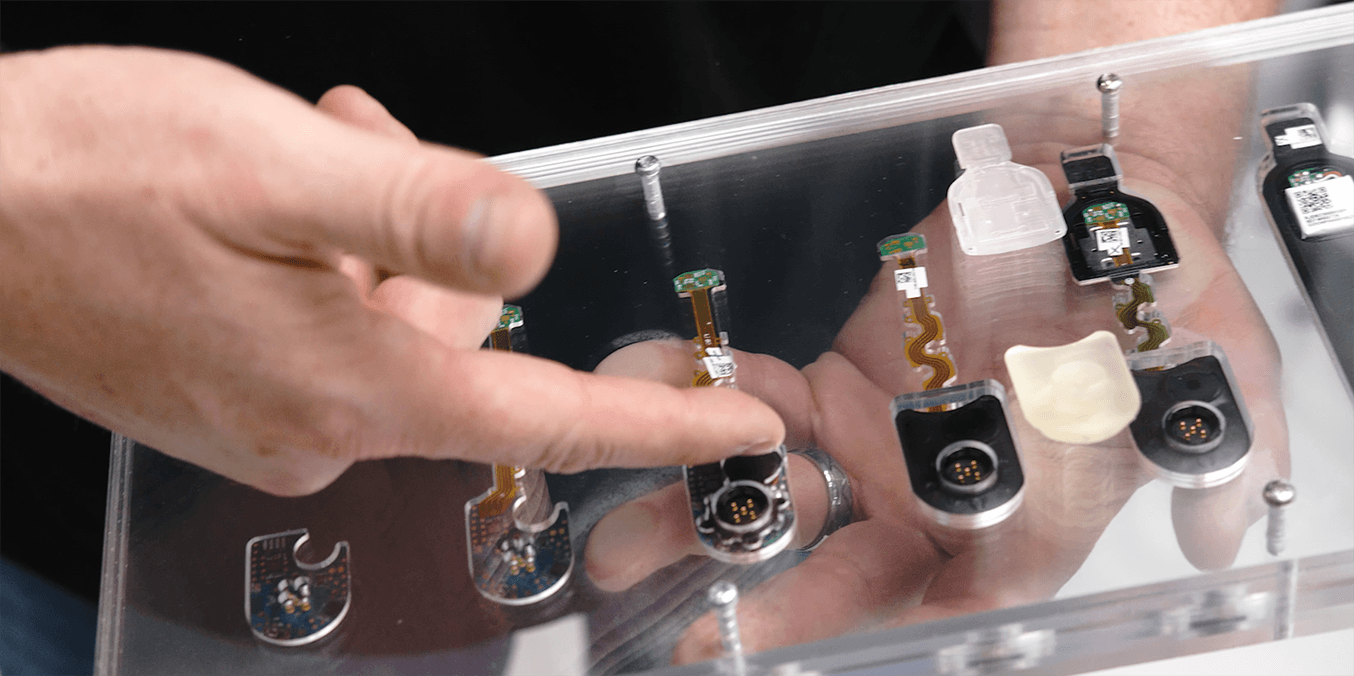
David Beardsley spiega come sono riusciti a "intercettare il processo", eliminando quattro fasi di produzione e permettendo al team di concentrarsi sulla composizione rapida nella fase finale di sovrastampaggio. Le parti surrogate stampate in 3D hanno consentito di aggirare la complessa catena di fornitura e hanno ridotto i tempi di realizzazione delle parti inserto da tre settimane a tre giorni.
"Il fatto che siamo stati in grado di chiudere lo strumento su materiale stampato in 3D e usarlo con l'iniezione ad alta pressione, senza nemmeno una sbavatura, è un po' straordinario. Se non avessimo avuto la Form 2, non ci saremmo riusciti."
David Beardsley, Google ATAP
Poiché la produzione delle parti stampate aveva un costo accessibile, il team ha potuto fornire più unità di quanto la fabbrica avesse stimato di aver bisogno, consentendo quindi di eseguire diverse prove, fino a quando non sono stati ottenuti risultati soddisfacenti.
"Il fatto che siamo stati in grado di chiudere lo strumento su materiale stampato in 3D e usarlo con l'iniezione ad alta pressione, senza nemmeno una sbavatura, è un po' straordinario. Se non avessimo avuto la Form 2, non ci saremmo riusciti" spiega Beardsley.
"Quando siamo passati a un ciclo completo del prodotto, eravamo sicuri che avrebbe funzionato" racconta Allen.
L'articolo in breve: che risultato ha ottenuto Google ATAP? Grazie alla stampante 3D SLA Form 2 e la High Temp Resin di Formlabs, il team è riuscito a:
-
Stampare in 3D degli inserti surrogati utilizzando la High Temp Resin, che ha resistito al sovrastampaggio con uretano termoplastico (TPU) iniettato a oltre 250 °C e 27 000 psi.
-
Risparmiare circa 100 000 $ in sottoinsiemi elettronici sprecati; la cifra è superiore se si tiene conto anche della manodopera evitata.
-
Eludere una complessa catena di fornitura e accorciare il ciclo di test di validazione pre-produzione per gli inserti con circuito stampato da tre settimane a tre giorni.
"Quando siamo passati a un ciclo completo del prodotto, eravamo sicuri che avrebbe funzionato."
Bryan Allen, Google ATAP
Tre lezioni da trarre dall'esperienza di Google ATAP nell'applicazione della stampa 3D alla produzione
Anche se il processo di produzione del dispositivo indossabile trattato in questo caso di studio era unico, il modo in cui il team ha affrontato il problema, ha utilizzato la tecnologia per risolverlo e il loro approccio alla stampa 3D possono essere preziosi per aziende di tutte le dimensioni. Prendi ispirazione da queste tre riflessioni tratte dalla nostra conversazione con Bryan Allen, tecnologo di progettazione, e David Beardsley, manager del negozio di modelli, presso Google ATAP.
Considera ogni fase di sviluppo, dalla prototipazione alla spedizione del prodotto, con una mentalità iterativa.
"Una delle cose davvero uniche del nostro modo di lavorare è che consideriamo l'intero processo di produzione come un procedimento di prototipazione, in cui eseguiamo cicli di prototipi in ogni fase della produzione, piuttosto che dividerlo nelle classiche fasi (prototipazione, catena di fornitura, lancio del prodotto). In sostanza, si tratta di applicare un approccio di progettazione e iterazione lungo l'intero processo piuttosto che solo all'inizio" spiega Allen.
"Applicando la prototipazione a ogni piccolo passo del percorso, possono venire alla luce eventuali problemi che è meglio affrontare il prima possibile, così da evitare che diventino molto più grandi in fasi avanzate di produzione" spiega Beardsley.
Non tenere le tecnologie in compartimenti stagni: considera ogni macchina come parte del tuo set di strumenti per la risoluzione dei problemi che ti aiutano a trovare la soluzione migliore per ogni sfida.
"Non proviamo mai a sostituire un intero processo. Cerchiamo sempre di scoprire quali sono i punti di forza di ciascun macchinario. Ossia quella funzione che svolge meglio di qualunque altro strumento e come possiamo sfruttare questa caratteristica a nostro vantaggio. Non essendo così legati a un singolo processo o a una macchina specifica ci permette di vedere i meriti per molti materiali e processi diversi, e quindi applicarli di conseguenza" spiega Allen.
"Consideriamo la stampa 3D uno strumento come altri tra quelli a nostra disposizione, a cui possiamo aggiungere CNC, stampaggio e tutti i processi di fabbricazione più tradizionali. Migliora la nostra capacità di riflettere su come applichiamo queste nuove tecnologie alla realizzazione dei prodotti."
La stampante 3D Form 2 è tra gli strumenti che ingegneri e progettisti del laboratorio di Google ATAP utilizzano per risolvere problemi complessi e realizzare progetti hardware ambiziosi.
Inizia risolvendo un problema.
"Ci sono ancora così tanti limiti di progettazione delle parti. Ai laboratori che vogliono iniziare ad applicare la produzione additiva nei loro processi, consigliamo di scegliere un problema specifico che rappresenta solo una parte. Non cercate di stampare lo strumento completo: provate a stampare un inserto. Scegliete un pezzo, risolvete il problema di produzione e imparate da questa esperienza" spiega Allen.
Scopri di più sulla Form 2, materiali ingegneristici e applicazioni
La Form 2 e la High Temp Resin sono tra gli strumenti che aiutano ingegneri e progettisti del laboratorio di Google ATAP a risolvere problemi complessi e realizzare progetti hardware ambiziosi.
"Molte grandi aziende pensano che una macchina costosa permetterà di risolvere qualsiasi problema. Noi abbiamo strumenti di questo tipo, ma in realtà la Form 2 è quella che si rivela più utile" spiega Beardsley. "Precisione, velocità, finitura, la capacità di ottenere subito una parte completata: è davvero straordinario."
Scopri la Form 2 e la raccolta di resine ingegneristiche di Formlabs, oppure richiedi un campione gratuito stampato in High Temp Resin o altri materiali per toccare con mano la qualità della stampa 3D.
Leggi il nostro whitepaper Realizzazione di stampi con la stampa 3D per imparare nuove tecniche di applicazione della stampa 3D alla prototipazione e la produzione.