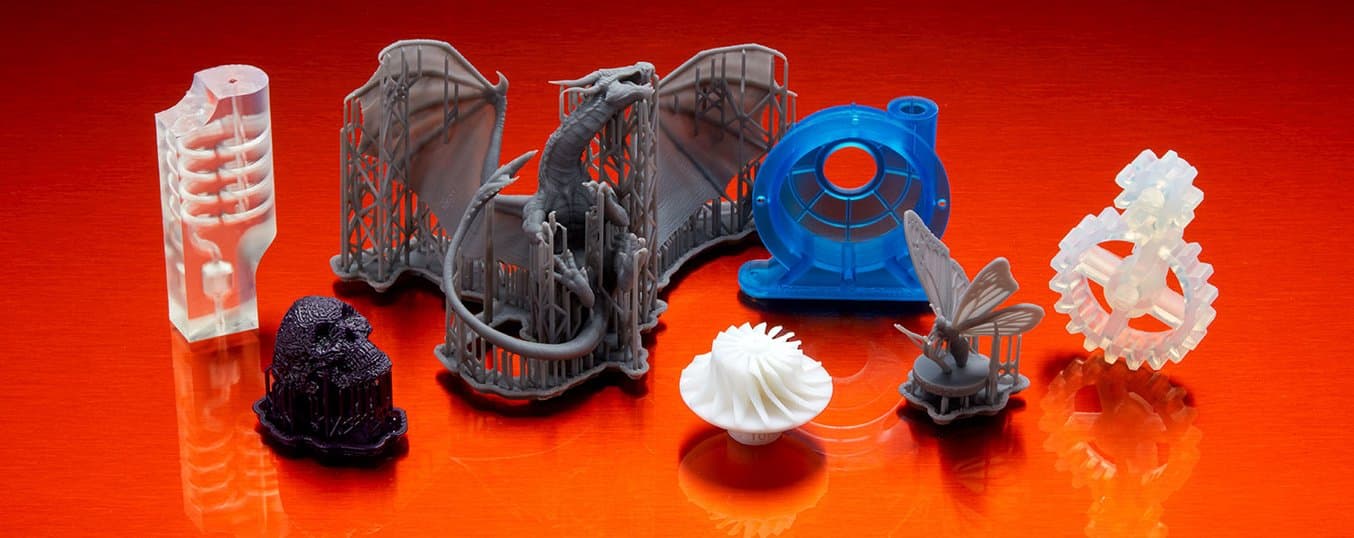
Quando ad aprile abbiamo annunciato il lancio della Form 3 e della Form 3L, abbiamo spiegato perché abbiamo riprogettato la stampa 3D stereolitografica nella nuova tecnologia Low Force Stereolithography (LFS)™. La stampa 3D LFS si serve di un serbatoio resina flessibile per ridurre in modo significativo le forze di distacco durante la stampa e di una Light Processing Unit (LPU); il nostro motore della parte ottica progettato su misura - per realizzare stampe uniformi e precise.
In questo post, esploreremo assieme come la stampa 3D LFS ha un impatto diretto su qualità e rendimento di stampa grazie a miglioramenti importanti in quattro categorie: dettaglio di superficie, finitura superficiale, strutture di supporto e precisione delle parti.
Stampa modelli dettagliati come non mai
La Form 3 e la Form 3L contengono un motore della parte ottica personalizzato, la Light Processing Unit (LPU). A seguito di numerosi miglioramenti, la LPU ottiene un punto laser nitido e pulito. Il fascio laser attraversa un filtro spaziale che cattura i fasci di luce in eccesso, una serie di specchi assicurano che il fascio cada sempre perpendicolarmente rispetto al piano di stampa.
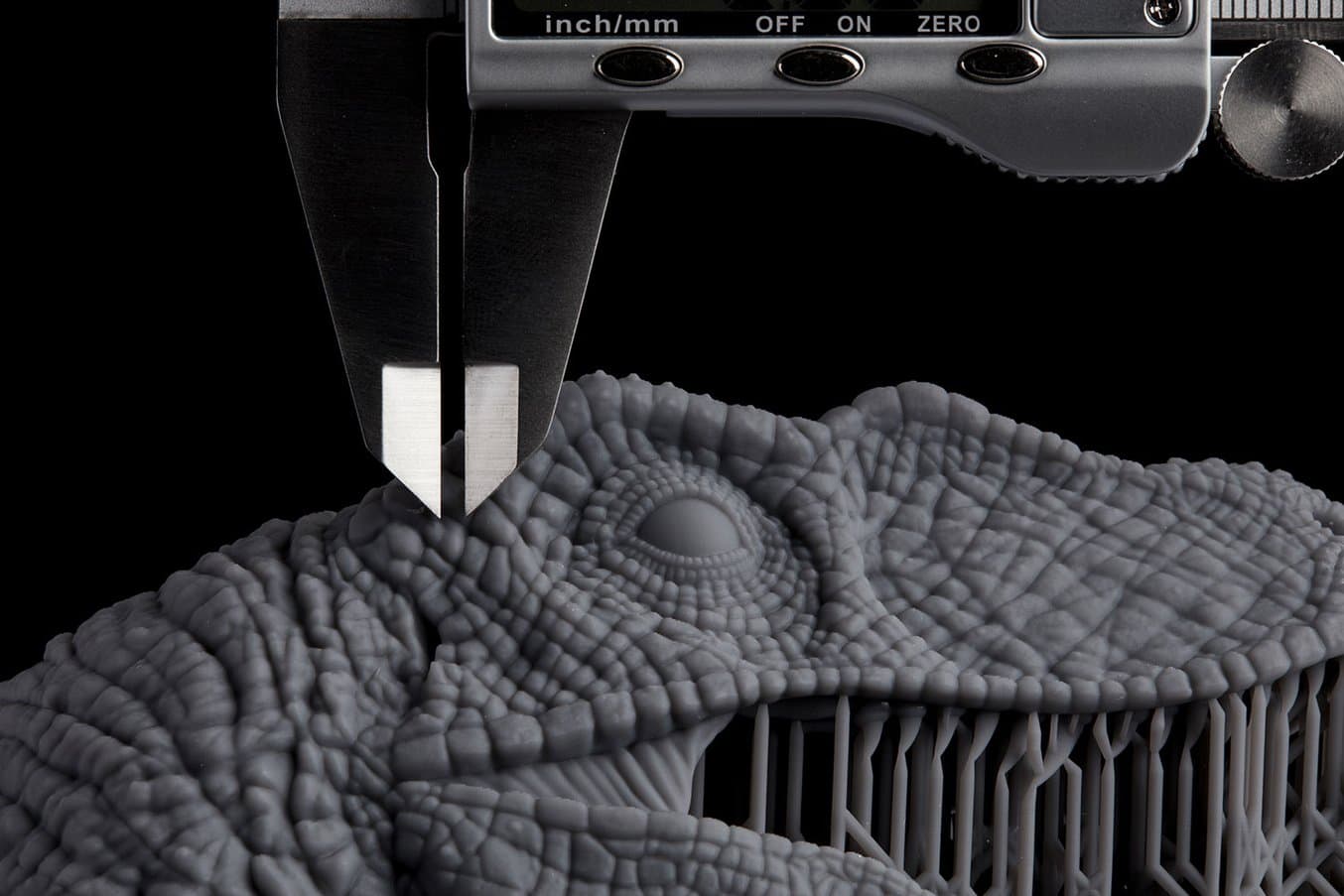
Il percorso lineare del laser assicura che dettagli minuti quali fori, lettere goffrate e piccole rifiniture vengano stampati con bordi nitidi. La Low Force Stereolithography stampa parti con un dettaglio di superficie impressionante e con dettagli minuti, in precedenza impossibili da ottenere sul desktop.
"Una delle cose più entusiasmanti della Form 3 è assistere a dove ci porta il processo di stampa a forza ridotta in termini di qualità di stampa e finitura. Siamo entusiasti di poter andare oltre i limiti di particolari veramente minuscoli. Sono entusiasta dei piccoli dettagli che vengono riprodotti nei modelli. È davvero straordinario."
—Sean Buxton, ingegnere meccanico senior, Ximedica
Finitura di superficie liscia, anche a una risoluzione di stampa di 100 micron
In definitiva, la finitura superficiale della parte stampata in 3D è il risultato di una buona registrazione degli strati, ovvero con quanta precisione ciascuno strato è allineato con quello precedente. Quando vi è una buona registrazione degli strati, le linee fra uno strato e l'altro diventano pressoché invisibili. Ne consegue una riduzione della ruvidità superficiale che, in definitiva, comporta una finitura liscia e, per i materiali trasparenti, parti più traslucide.
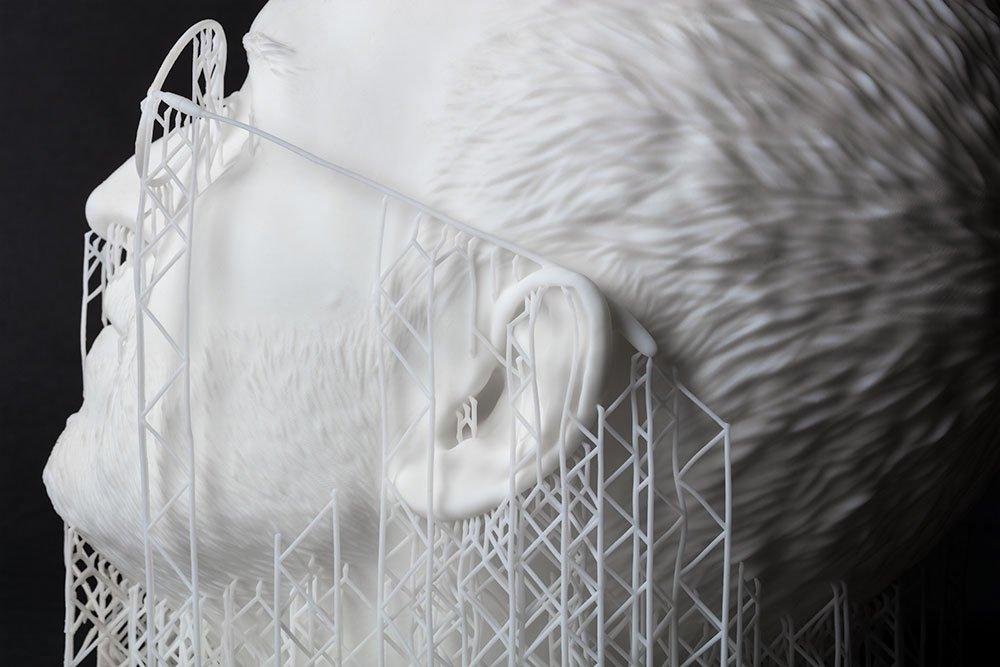
Poiché ciascuno strato di resina viene polimerizzato, si crea un legame fra la parte stampata e il serbatoio. Il processo di distacco rompe questo legame consentendo alla parte di spostarsi verso l'alto e allo strato successivo di essere stampato. Nella maggior parte delle stampanti 3D stereolitografiche invertite, questa separazione esercita una grande pressione sulla parte, il che può portare a superfici ruvide (punto che la Form 2 tiene in considerazione prestando molta attenzione alla calibrazione).
Nella stampa 3D Low Force Stereolithography (LFS), il film di rivestimento flessibile alla base del serbatoio resina si stacca delicatamente quando la piattaforma di stampa tira la parte verso l'alto. Questo riduce in modo significativo lo sforzo esercitato sulla parte (test interni mostrano una riduzione delle forze di distacco dieci volte maggiore rispetto alla Form 2), consentendo un deciso cambiamento per quanto riguarda finitura superficiale e nitidezza della parte.
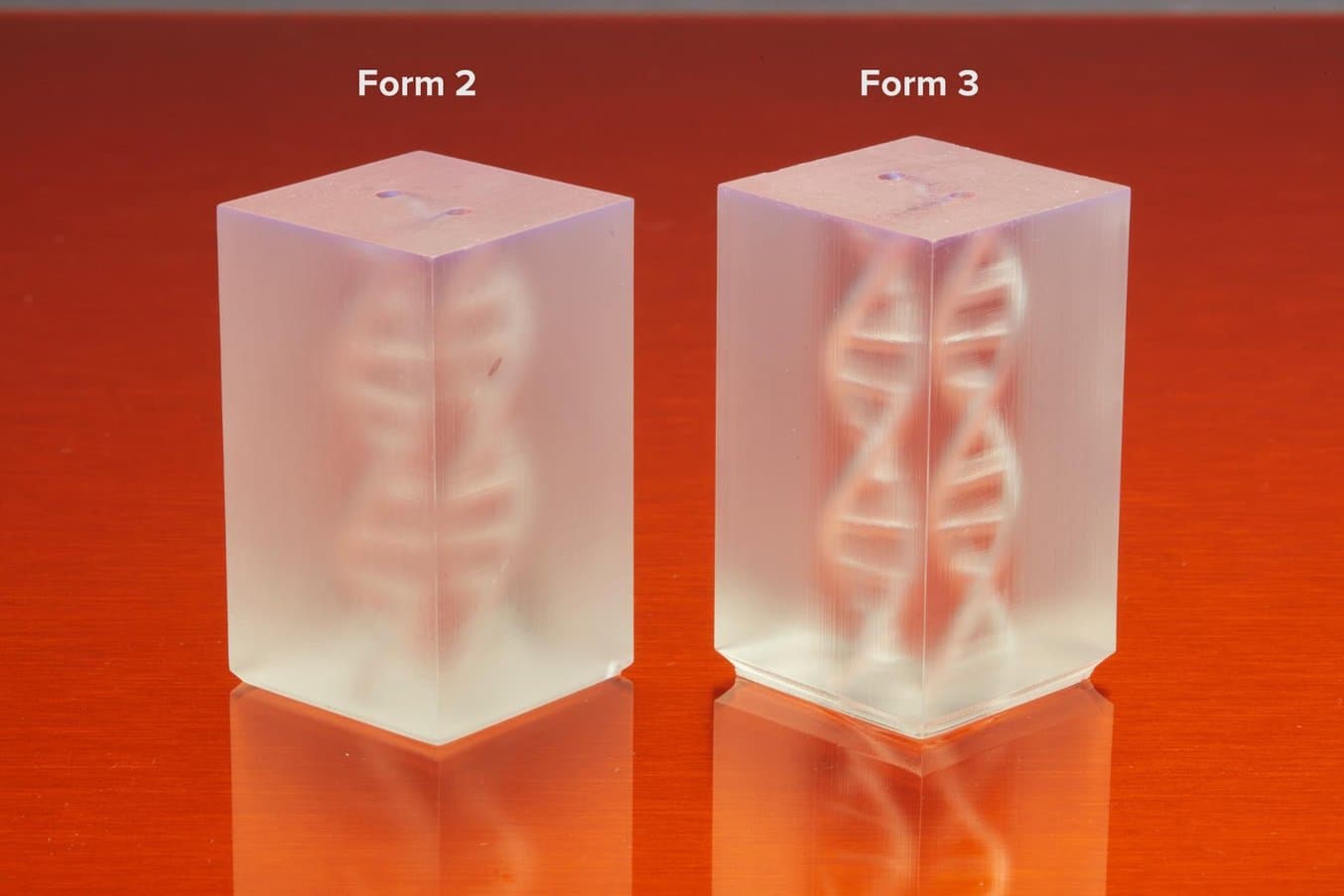
"Quello che ci ha inizialmente colpito della Form 3 è stato la qualità delle stampe. La prima stampa che abbiamo realizzato ha dato un risultato incredibile. Gli strati della struttura erano praticamente invisibili. Storicamente Hypertherm produce gioielleria. Quando dico gioielleria, intendo finiture estremamente accurate, bordi levigati e lucenti, tanti dettagli. Per quanto riguarda i nostri processi di controllo siamo davvero minuziosi nel cercare di avvicinarci il più possibile alla perfezione.
Per noi una soluzione di stampa 3D che offra una finitura di qualità e che richieda meno post-elaborazione è importante. Si tratta di meno lavoro manuale: meno dobbiamo usare un taglierino di precisione o della carta abrasiva, meglio per noi. Essere in grado di stampare con quel livello di finitura superficiale è importante per gli assemblaggi funzionali."
—Aaron Noyes e Dan Harrington, operatori di prototipazione senior, Hypertherm
Supporti leggerissimi per un rendimento migliore
In un recente questionario relativo alla finitura delle parti compilato da utenti Form 2, il 47% ha indicato che la rimozione dei supporti era il maggior punto dolente e il 62% ha menzionato che i supporti sono l'elemento chiave per migliorare il processo di finitura.
Per la maggior parte delle tecnologie di stampa 3D, la post-elaborazione, incluse la rimozione delle strutture di supporto, la levigazione e la finitura delle parti, è un'operazione dispendiosa a livello di tempo e limita il rendimento. I segni lasciati dai supporti hanno un impatto negativo sulla finitura superficiale.
Nuovi, leggerissimi supporti tengono in considerazione questa insoddisfazione comune. Queste nuove strutture di supporto usano punti di contatto minuscoli per consentire una semplice rimozione, lasciando pochissimi segni. Presentano inoltre un intreccio più robusto, di modo che quando la parte viene rimossa dai supporti, questi tendono a staccarsi in un'unica struttura.
Questo porta a uno spreco di materiale quattro volte inferiore, che a sua volta significa meno tempo impiegato nella post-elaborazione e meno necessità di un'ulteriore levigazione. Per il grafico sottostante, le parti sono state stampate con una densità dei punti di contatto di 0,8 mm e una dimensione dei punti di contatto di 0,6 mm per la Form 2, e una densità dei punti di contatto di 0,5 mm e una dimensione dei punti di contatto di 0,3 mm per la Form 3 e sono state fotografate con un ingrandimento di 38x.
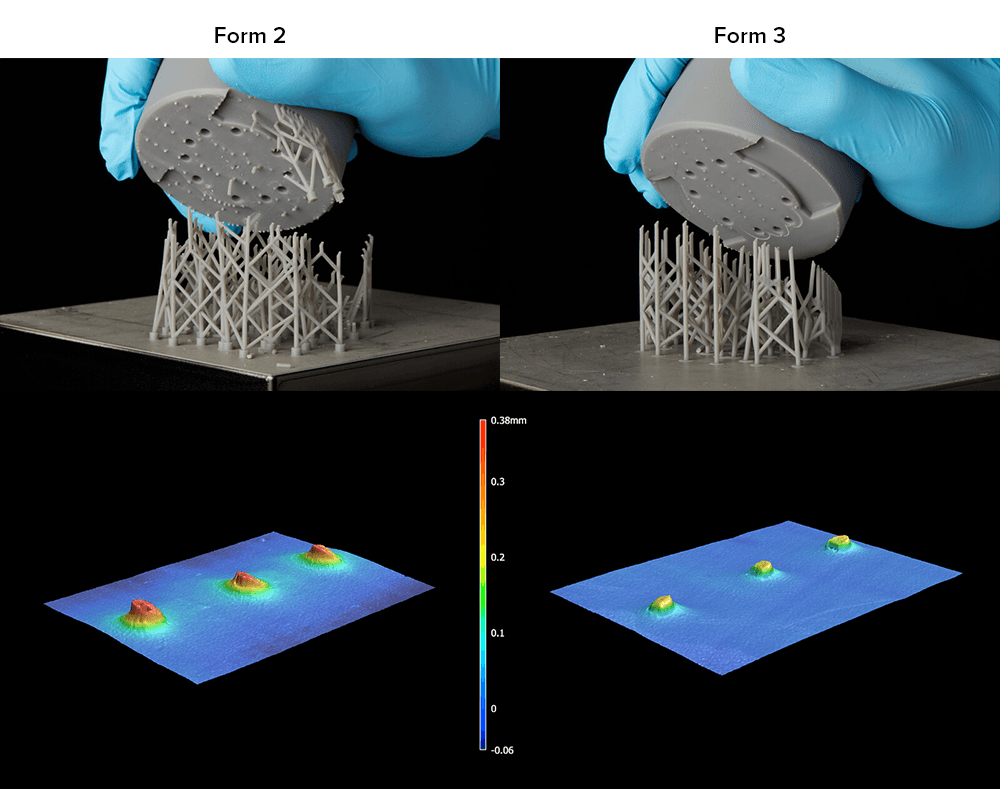
"Il perfezionamento dei supporti leggeri che si rompono facilmente rappresenta un cambio radicale. Non esistono parole per descrivere la prima volta che si prende in mano una parte, la si tira e questa si stacca perfettamente dai supporti senza che resti alcun residuo. Questo elimina lo stress di costruire e pulire le parti e ci consente di concentrarci sul design e la creazione."
—Justen England, direttore generale, Delve
Stampa precisa e riproducibile
L'ottica della Form 3 è racchiusa completamente in una Light Processing Unit (LPU) progettata su misura. All'interno di questo modulo dell'ottica, il fascio laser viene fatto passare attraverso un filtro spaziale che cattura i fasci di luce in eccesso assicurando così un punto laser pulito. Il laser viene poi direzionato in basso verso un singolo galvanometro che lo posiziona sull'asse Y, successivamente verso uno specchio parabolico e dopo ancora verso uno specchio parabolico che lo raddrizza prima di farlo uscire dalla finestra della LPU direttamente sotto alla superficie della stampante.
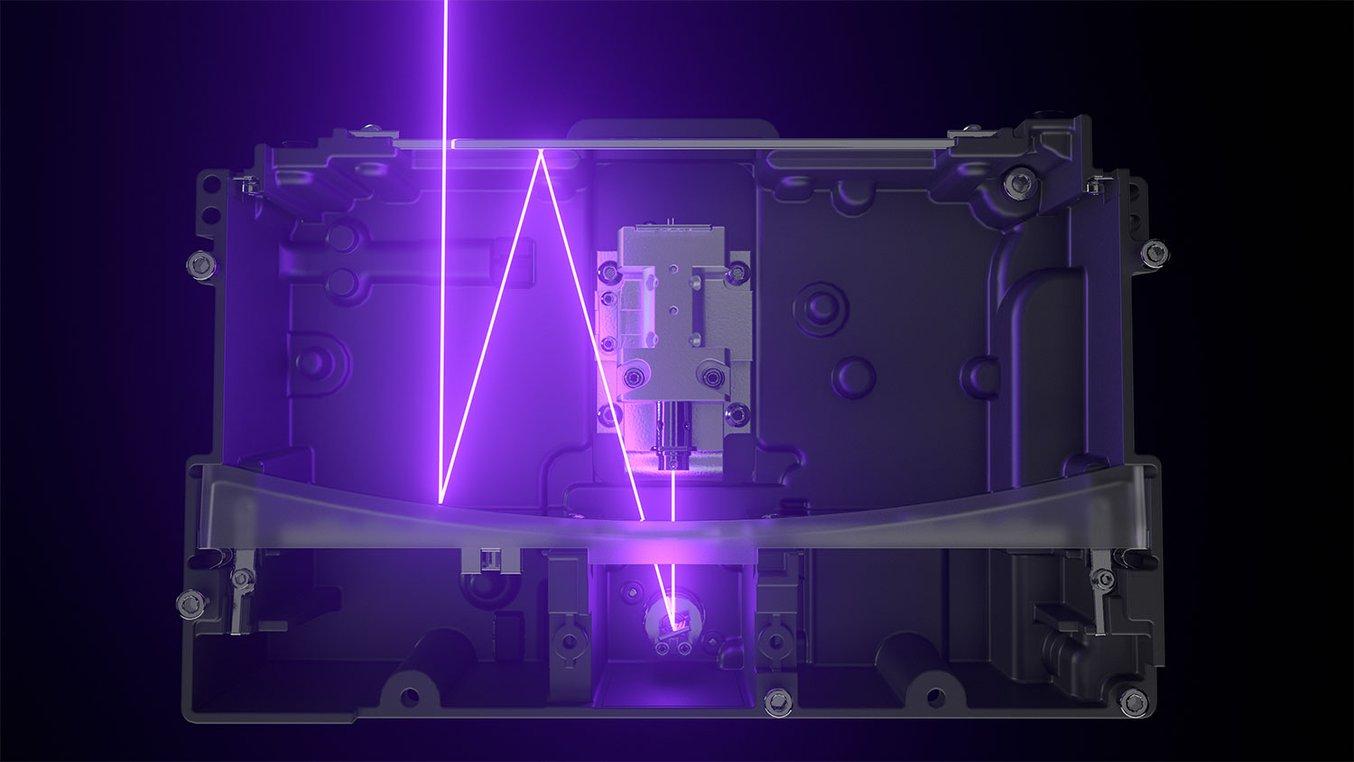
Un motore passo-passo conduce la LPU in direzione X con un movimento uniforme di scansione lineare. In combinazione con il percorso luminoso perpendicolare del laser, questo crea quella che noi chiamiamo illuminazione lineare. Questo procedimento di scansione lineare fornisce una risoluzione XY di 25 micron uniforme e affidabile nel tempo.
Questa risoluzione XY di 25 micron descrive la precisione con cui la stampante è in grado di lavorare sul piano XY: il laser muove piccoli "passi" da 25 micron in direzione X. La dimensione di 85 micron del punto laser è fondamentalmente la dimensione della punta di un pennello. A causa del costante processo di scansione lineare, la Form 3 è in grado di realizzare in modo consistente parti con una risoluzione XY di 25 micron. (È stato difficile stabilire questo numero con la Form 2 a causa delle differenze del procedimento di stampa.)
Tieni d'occhio l'uscita a breve di un approfondito studio di precisione di parti stampate con la Form 3.
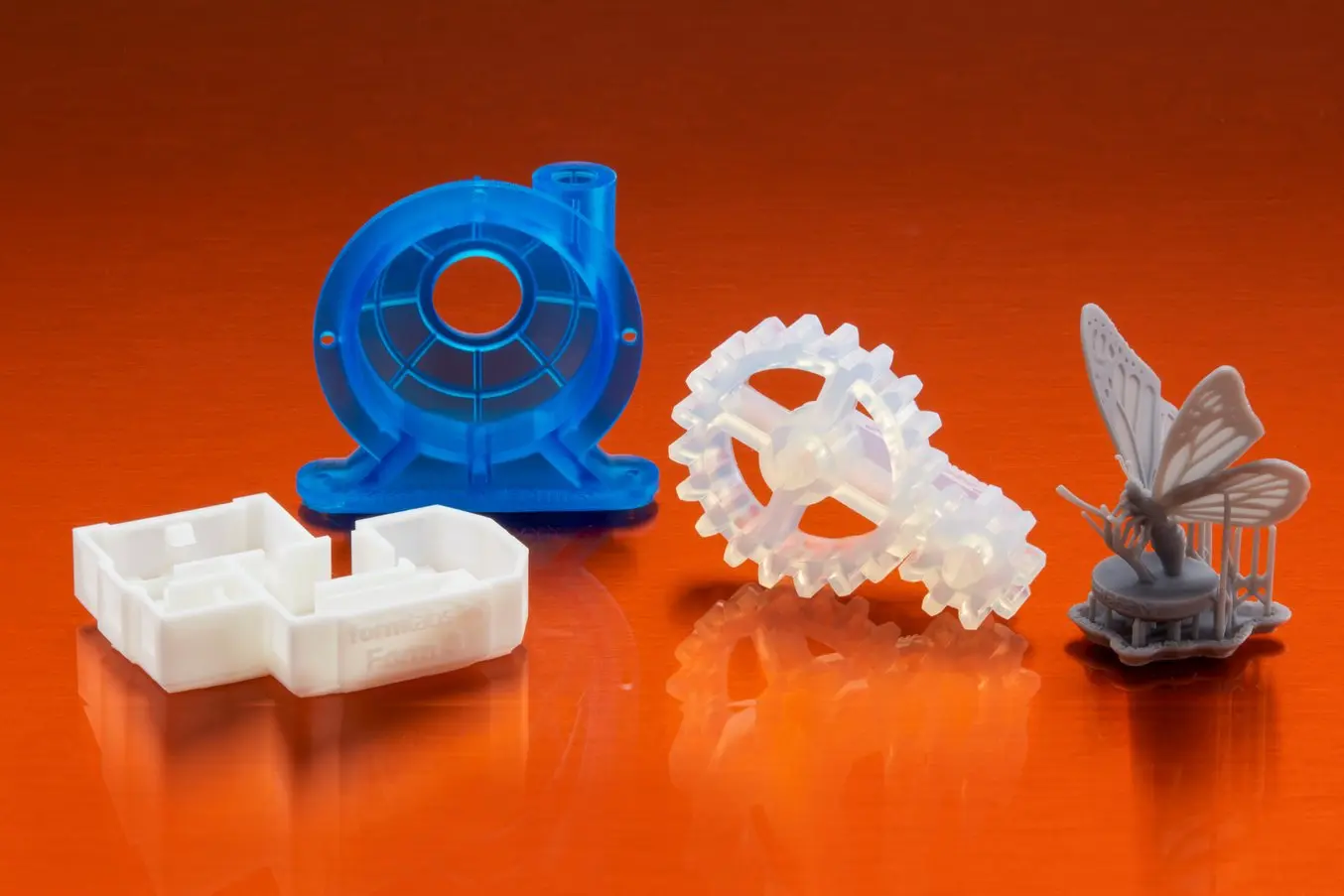
Richiedi un campione gratuito
Guarda e tocca con mano la precisione di Formlabs. Saremo lieti di inviare presso la tua azienda un campione gratuito stampato in 3D.
Richiedi un campione gratuitoLa stampa 3D industriale di nuova generazione
Formlabs ha spianato il cammino per fornire alle aziende gli strumenti per una produzione di alta qualità. La Form 3, costruita con tecnologia Low Force Stereolithography (LFS), è il passo successivo verso l'universalizzazione della stampa 3D di livello industriale per il desktop e per la prima volta nella storia porta la fabbricazione professionale in house.
Ordina subito la tua Form 3 Compara modelli SLA di Formlabs