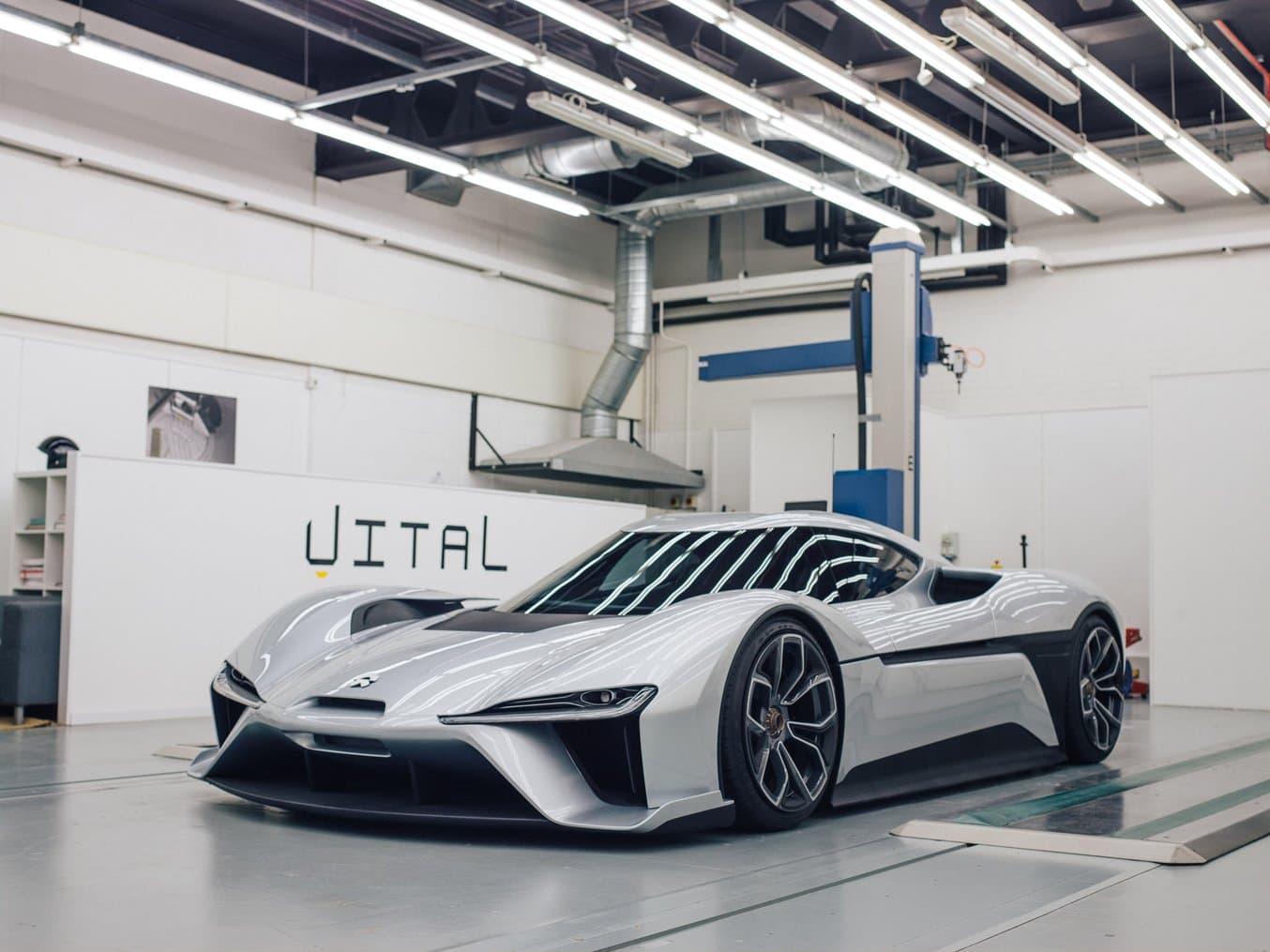
아직은 대리점에서 3D 프린팅된 자동차를 구매할 수는 없지만 3D 프린팅은 수년 동안 자동차 개발 프로세스의 중요한 부분이었습니다. 그러나 최근에는 3D 프린팅 사용 사례가 제조 전반에 걸쳐 발판을 마련하기 시작했습니다.
3D 프린팅은 공급망에 막대한 가치를 추가하여 광범위한 생산 응용 분야를 열 수 있습니다. 이 기술은 공장 현장에서 프로세스를 지원하기 위해 사내에서 적층 제조를 가져올 수 있는 회사와 함께 더욱 실행 가능하고 저렴하게 성장하고 있습니다. 새롭고 탄력 있는 재료는 최종 파트를 대신할 수 있고 (대량) 맞춤화 기회와 성능이 우수한 고정밀 기능의 3D 프린트물을 생산할 수 있는 기회를 열어주고 있지만 이는 시작에 불과합니다.
이어지는 내용에서 3D 프린팅이 디자인에서 제조에 이르기까지 자동차 산업 전반에 걸쳐 혁신을 주도하는 9가지 주요 방법을 알아보보세요.
자동차 디자인 및 프로토타이핑을 위한 3D 프린팅
프로토타이핑은 역사적으로 자동차 산업에서 3D 프린팅의 가장 일반적인 사용 사례였습니다. 3D 프린팅으로 프로토타이핑 속도가 크게 증가한 덕분에 신속 프로토타이핑은 사실상 3D 프린팅의 동의어가 되었으며 이 기술은 제품 개발 프로세스를 혁신했습니다.
3D 프린팅을 사용하면 자동차 디자이너가 간단한 내부 요소에서 대시보드 또는 전체 자동차의 축척 모델에 이르기까지 물리적 파트 또는 어셈블리의 프로토타입을 신속하게 제작할 수 있습니다. 기업은 신속 프로토타이핑을 통해 아이디어를 설득력 있는 컨셉 증명으로 전환할 수 있습니다. 그런 다음 이러한 컨셉을 최종 결과와 거의 일치하는 충실도 높은 프로토타입으로 개발할 수 있으며 궁극적으로 일련의 검증 단계를 통해 제품 대량 생산에 이르게 됩니다.
프로토타이핑은 많은 반복을 거치기 때문에 시간과 비용이 많이 듭니다. 3D 프린팅을 사용하면 기존 제조 방법보다 훨씬 저렴한 비용으로 매우 설득력 있고 전형적이며 기능적인 프로토타입을 하루 안에 만들 수 있습니다. 데스크톱 3D 프린터를 사용하면 엔지니어링 팀과 디자인 팀이 반복 주기를 늘릴 수 있는 기술을 사내로 가져올 수 있습니다. 그 결과 아이디어와 최종 제품 사이의 거리를 단축되어 전체 제품 개발 워크플로를 강화할 수 있습니다.
1. 3D 프린팅을 이용한 당일 자동차 프로토타입 제작
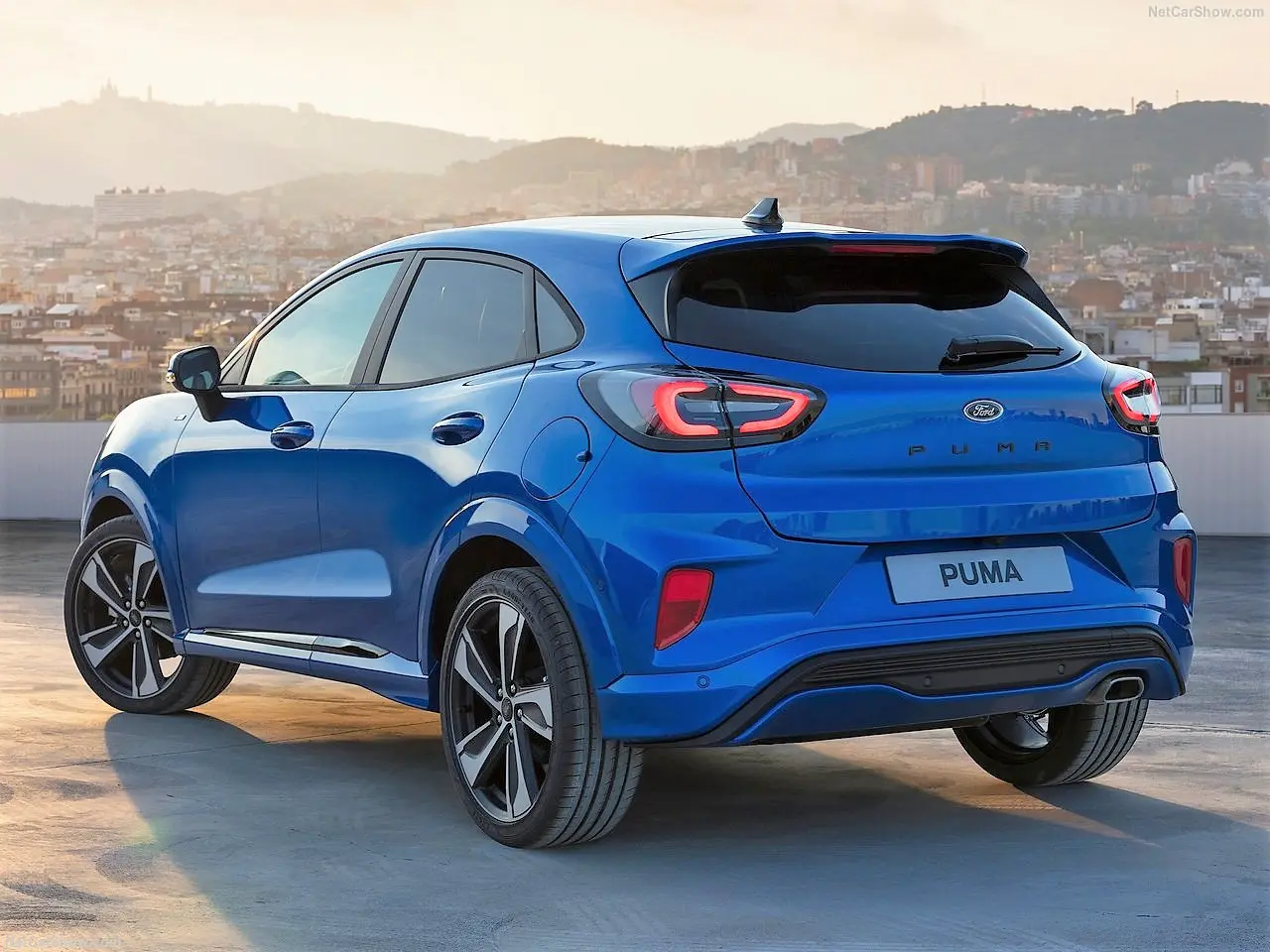
포드의 디자이너는 Formlabs 3D 프린터로 단 몇 시간 만에 포트 퓨마 뒷면의 레터링 프로토타입을 제작했습니다.
독일 메르케니히에 있는 포드의 신속 테크놀로지 센터(Rapid Technology Center)에서는 다양한 3D 프린팅 기술로 짧은 처리 시간에 프로토타입을 제작합니다. 엔지니어와 디자이너는 리드 타임이 몇 주나 되는 작업을 작업장에 보내는 대신 몇 시간 만에 디자인을 손에 쥐고 있을 수 있습니다.
디자이너는 신속 테크놀로지 센터에서 당일 프로토타입을 제작하여 단 몇 시간 만에 여러 디자인을 반복할 수 있습니다. 물리적 프로토타입을 제작하면 디지털 모델보다 이점을 얻을 수 있다고 포드의 적층 제조 전문가인 브루노 알베스는 이야기합니다.
예를 들어, Formlabs 3D 프린터로 포드 퓨미 뒷면의 레터링 프로토타입을 제작하면 디자이너가 다양한 조명 조건에서 선과 그림자가 어떻게 나타나는지 확인할 수 있습니다. 알베스는 "프린터는 아주 빠르고 이런 종류의 레터링에 매우 효과적이어서 디자이너에게 반복할 수 있는 옵션을 제공할 수 있습니다."라며"카티아나 다른 소프트웨어에서도 확인할 수 있고 조명을 시뮬레이션할 수 있지만 자동차에 레터링을 넣어 느끼고 만지고 반사되는 모습을 전부 확인하는 것과는 다릅니다."
포드 모터 컴퍼니(Ford Motor Co.)의 브루노 알베스와 브로제(Brose)의 크리스티안 클라일라인(Christian Kleylein)이 진행하는 웨비나를 시청하며 3D 프린팅이 자동차 거대 기업의 혁신에 어떻게 힘을 실어주고 있는지 자세히 알아보세요.
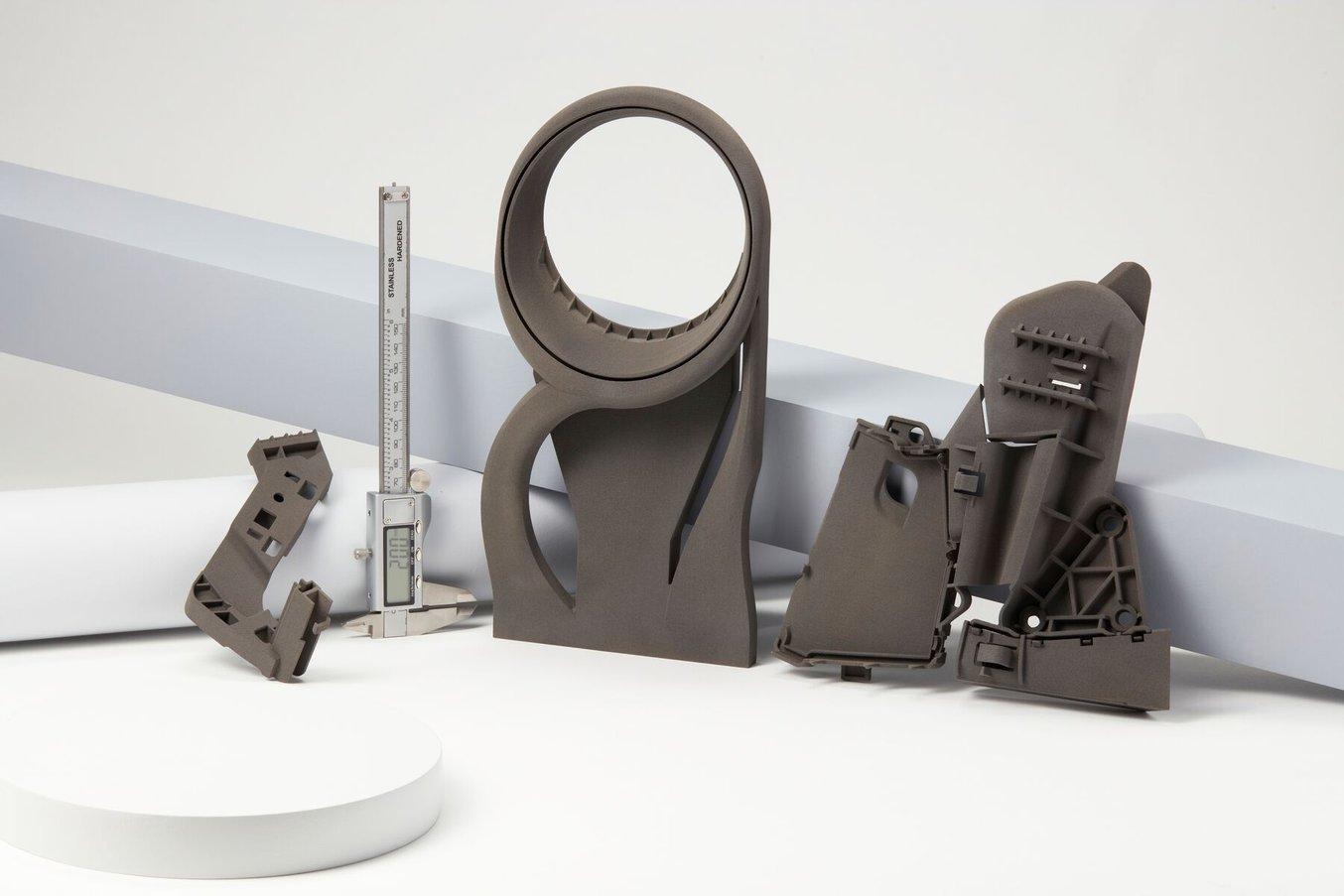
포드와 브로제의 대화: 두 자동차 거물과 함께 다뤄본 대규모 3D 프린팅
이 웨비나에서는 최상위 가족 소유 자동차 공급업체 중 가장 큰 브로제의 기술자인 크리스티안 클라일라인과 포드의 적층 제조 전문가인 브루노 알베스가 디자인에서 제조에 이르기까지 자동차 산업 전반에 걸쳐 3D 프린팅이 혁신을 주도하고 있는 모습을 공유해드립니다.
2. 3D 프린팅으로 자동차 부품 경량화
IGESTEK는 플라스틱 및 복합 재료를 사용하는 경량 솔루션 개발을 전문으로 하는 스페인의 자동차 공급업체입니다. 그들의 팀은 형상 확인용 컨셉 설계 단계부터 기능적 프로토타입 구현용 세부 설계 단계에 이르기까지 제품 개발 프로세스 전반에 걸쳐 3D 프린팅을 사용합니다. 또한 플라스틱 사출금형용 인서트 또는 복합재용 열성형 도구 제조 같은 신속 툴링에도 3D 프린팅을 사용합니다.
토폴로지 최적화는 경량화 분야에서 인기를 끌고 있는 주제입니다. IGESTEK는 Autodesk Fusion 360을 사용하여 매개변수 목록을 기반으로 여러 솔루션을 생성합니다.
하나의 서스펜션 마운트를 제작하기 위해, 팀은 현재 시중의 솔루션보다 40% 더 가벼운 패키지로 최고의 성능을 얻기 위해 제너레이티브 지오메트리에 기반한 금속 3D 프린팅과 더 가벼운 복합재를 결합하는 다중 재료 아키텍처를 개발했습니다. 해당 파트의 프로토타입은 훨씬 더 빠른 반복 및 테스트를 위해 여러 디자인을 동시에 프로토타이핑할 수 있을 만큼 충분히 큰 Form 3L에서 제작되었습니다.
IGESTEK의 사례에서 이 응용 분야에 관한 자세한 내용과 IGESTEK이 자동차 부품을 경량화하는 두 가지 다른 방법을 알아보세요.
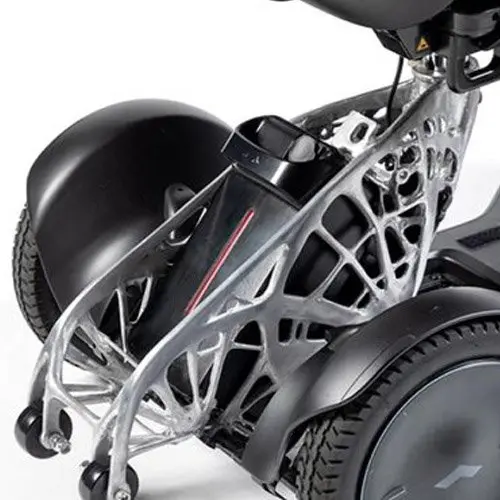
3D 프린팅 경량 파트 생산에 사용되는 제너레이티브 디자인 소개
이 웨비나에서는 Formlabs 제품 마케팅 책임자인 제니퍼 밀른이 가벼운 브래킷 제작을 다루는 Fusion 360의 단계별 자습서를 비롯하여 기계 파트 설계에 적용할 수 있는 방식으로 제너레이티브 디자인이 무엇인지 설명하여 간략한 개요를 제공해드립니다.
3. 3D 프린팅으로 컨셉카에 생명을 불어넣다
바이탈 오토(Vital Auto)는 Volvo, Nissan, Lotus, McLaren, Geely, TATA 등과 같은 주요 자동차 브랜드와 협력하는 영국의 산업 디자인 스튜디오입니다. OEM(주문자 상표 부착 생산자) 업체는 스스로 실험할 시간이 없을 때 바이탈 오토에 와서 아이디어, 초기 스케치, 도면 또는 기술 사양을 완전히 실현된 물리적 형태로 바꿉니다.
“우리는 처음부터 3D 프린팅을 사용해 왔습니다. 비용 절감뿐만 아니라 고객에게 디자인과 아이디어를 훨씬 다양하게 제공하기 위해 그 기술을 제조 공정에 도입하고 싶었습니다” 적층 제조를 담당하는 설계 엔지니어인 앤서니 바니코트(Anthony Barnicott)의 이야기 입니다.
현재 바니코트는 14대의 대형 용융 적충 모델링 방식(FDM) 프린터, 3대의 Formlabs Form 3L 대형 포맷 광경화성 수지 조형 방식(SLA) 3D 프린터, 5대의 Fuse 1 선택적 레이저 소결 방식(SLS) 3D 프린터을 갖추고 전체 3D 프린팅 부서를 운영하고 있습니다. 바니코트는 “용량 측면에서, 모든 프린터를 첫날부터 24시간 연중무휴로 100% 가동했습니다. 우리는 컨셉과 디자인의 모든 영역에서 이들 프린터를 사용합니다. 일반적으로 생산 기반 파트에는 Fuse 1을 사용하고 컨셉 기반 파트에는 Form 3L을 사용합니다"라고 밝혔습니다.
3D 프린팅은 작업팀이 향상된 제품을 신속히 제작하는 데 도움이 될 뿐만 아니라 새로운 비즈니스를 유치하는 데에도 도움이 됩니다. 그들은 많은 고객들이 최신 첨단 소재를 사용한 구성품 제작을 원하기 때문에 최신 기술을 원하고 해당 기술에 의존한다는 것을 알게 되었습니다.
바니코트는 “지난 10년 동안 이뤄온 기술과 3D 프린팅의 발전은 놀랍습니다. 제가 처음에 소량의 틈새 차량 생산을 시작했을 때는 오늘날 우리가 생산하는 일부 제품들이 쉽게 접근할 수 없었던 품목들이었습니다. 지금은 이들 파트를 생산할 수 있을 뿐만 아니라 매우 경제적으로 신속히 생산하는 것이 가능해졌습니다”라고 합니다.
바이탈 오토 팀의 심층 대담에서 3D 프린팅 파트를 사용하는 특정 응용 분야에 관한 더 깊은 통찰력을 얻어보세요.
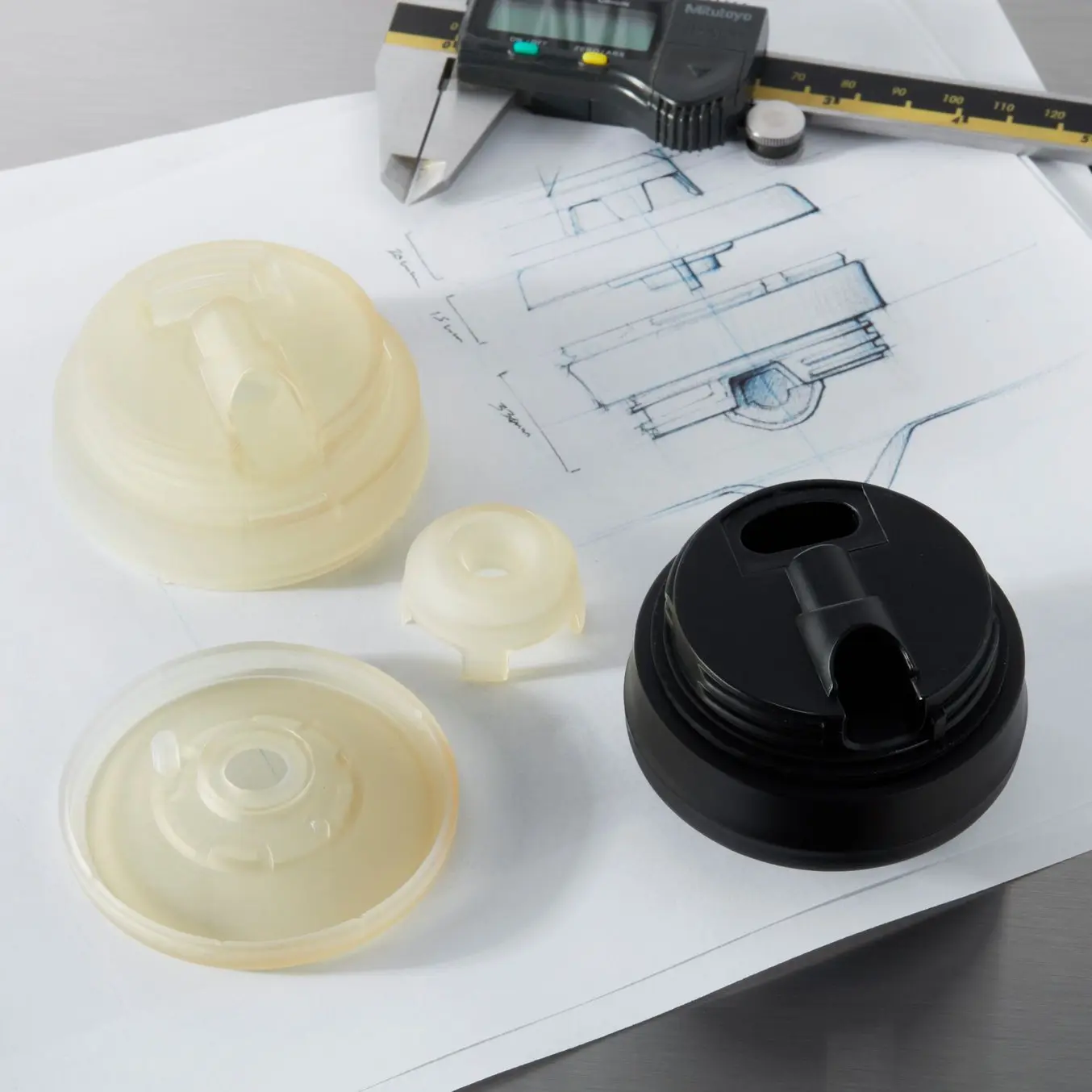
제품 개발을 위한 신속 프로토타이핑 안내서
이 가이드에서는 신속 프로토타이핑의 제품 개발 프로세스와 응용 분야, 오늘날 제품 개발 팀에서 사용할 수 있는 신속 프로토타이핑 도구는 무엇인지 알아봅니다.
자동차 제조 분야의 3D 프린팅
3D 프린터와 고성능 재료의 급속한 발전 덕분에 적층 제조는 이제 극한 환경의 문제에 대처할 수 있는 파트 생산의 해결책이 되었습니다.
3D 프린팅을 제조에 활용하면 간접비를 줄이고 맞춤형 지그 및 고정 장치와 같은 제조 보조 도구로 효율성을 높이고 사출 성형 또는 열성형과 같은 기존 제조 공정에 사용할 수 있는 신속한 툴링을 소량으로 진행할 수 있습니다.
3D 프린팅 최종 사용 파트는 또한 다른 생산 수단을 사용했을 때 특히 지나치게 비싸고 느린 자동차 산업, 애프터마켓, 맞춤형 또는 교체 부품과 같은 응용 분야에서 점점 보편화되고 있습니다.
4. 자동차 파트용 3D 프린팅 금형과 다이
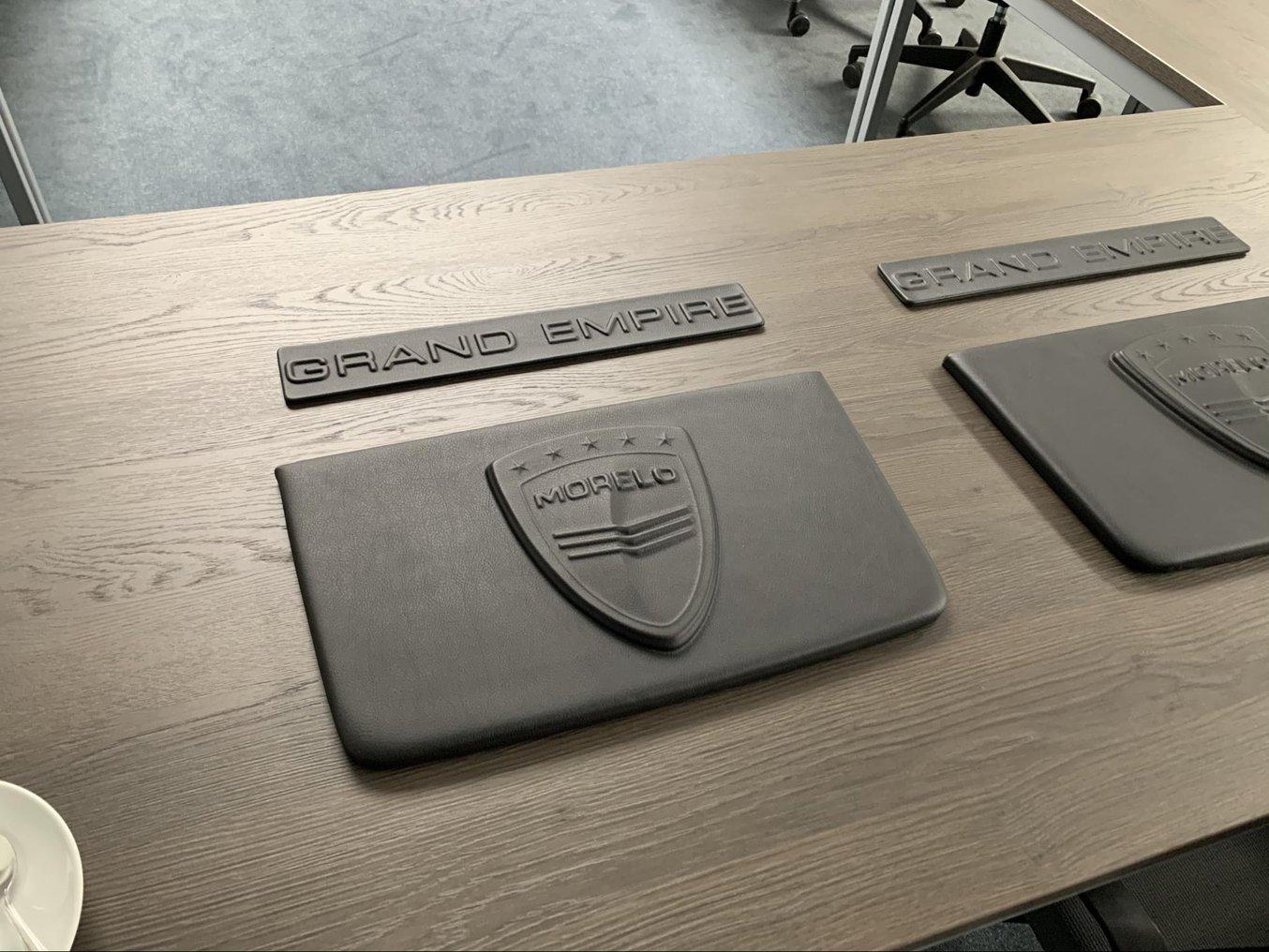
마크라 프로(Makra Pro)는 3D 프린팅 다이로 가죽을 트리밍하는 새로운 기술을 개발했습니다.
마크라 프로는 적층 제조 서비스 제공업체로 성형하기가 까다로울 수 있는 고급 자동차용 인기 트리밍 재료인 가죽의 형태를 만드는 새로운 프로세스를 개발했습니다. 고급 자동차, 오토바이, 캠핑카 제조업체를 포함한 일부 고객과 협력하여 실제 가죽을 성형하고 엠보싱 효과를 내는 방법을 테스트했습니다.
Form 3에서 프린팅한 몰드를 사용하는 마크라 프로의 기술은 늘어난 가죽 패널 전체에 압력을 균등하게 분산시키는 데 확장 폼을 사용합니다. 폼이 굳으면서 가죽이 다이에 압착되어 형태를 갖추게 됩니다.
완성된 가죽 파트는 예를 들어 자동차의 도어 패널 위에 씌우거나 차량의 시트 커버에 부착할 수 있습니다. 한정판 고급 자동차를 튜닝하는 것으로 잘 알려진 한 회사는 벽 또는 천장 패널에 이러한 성형 가죽 부품을 사용하여 멋스러움을 더합니다.
마크라 프로의 심층 사례를 읽어보거나 백서를 다운로드하여 사출 성형, 열성형 등을 포함한 보다 빠른 툴링 응용 분야를 알아보세요.
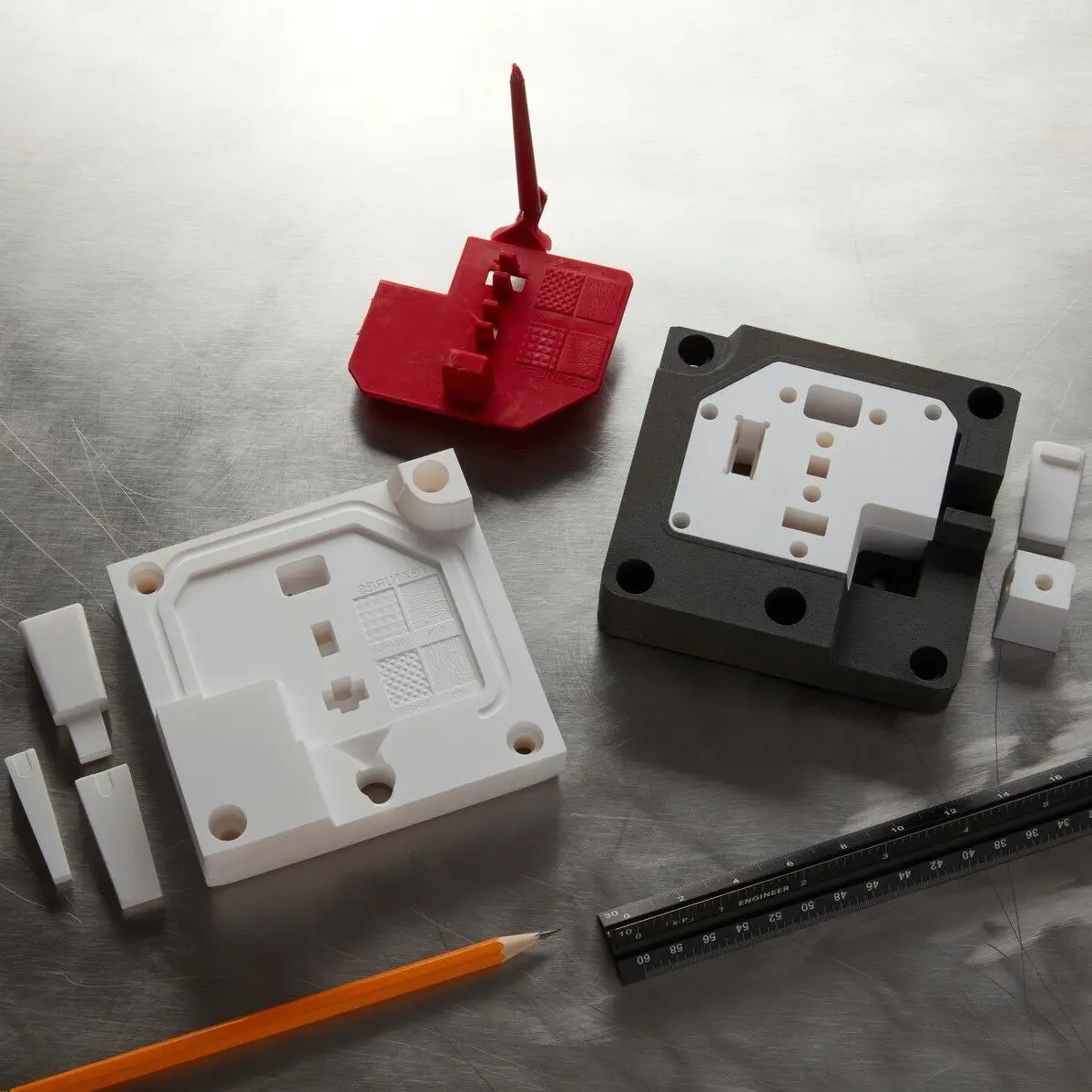
5. 3D 프린팅 제조 보조 도구
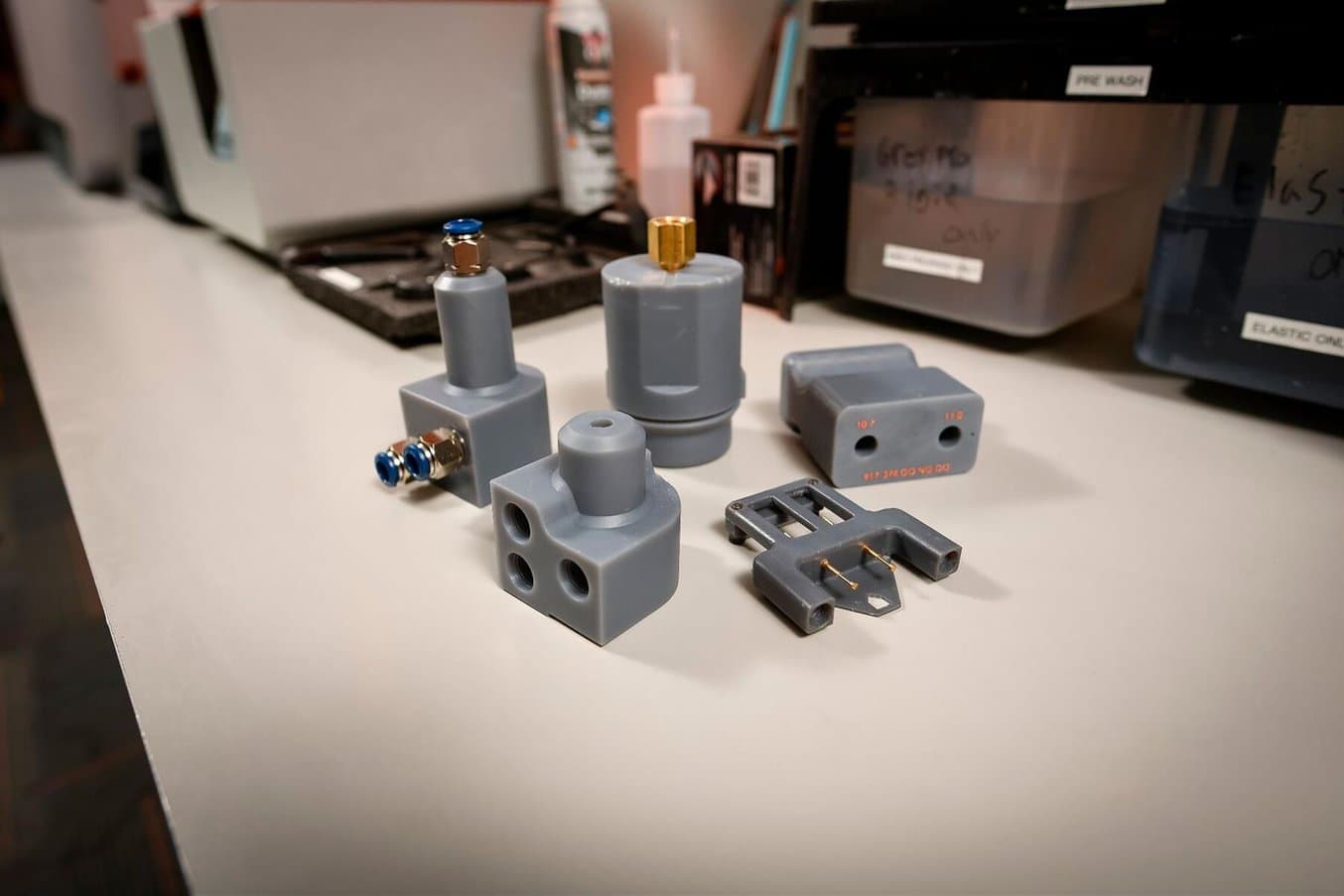
도먼 프로덕츠(Dorman Products)는 +/- 0.05mm까지 정확한 Gray Resin으로 go/no-go 테스트 지그를 생산합니다.
도먼 프로덕츠는 수백 종의 서로 다른 차량에 사용되며 그 수가 100,000개를 훌쩍 뛰어 넘는 파트 데이터베이스를 디자인하고 관리합니다. 기계 설계 팀 관리자인 에릭 트라이슨(Eric Tryson)은 "역사적으로 우리는 매년 4,000~5,000개의 부품을 새로 출시했습니다."라고 합니다.
적층 제조 책임자인 크리스 알리바흐(Chris Allebach)는 애프터마켓 공급업체의 운영에서 발생하는 물류 자체의 문제 외에도 도먼사의 제품 설계 및 제조 팀은 특히 민첩해야 한다고 합니다. “OEM에는 단일 파트를 설계하는 팀이 있으며 때로는 새 차가 나오기 2년 전에 시작하기도 합니다. 우리는 교체용 파트를 신뢰할 수 있는 동시에 시장에 신속하게 출시할 수 있는 방법을 찾아야 합니다.”
3D 프린터를 워크플로에 통합하기 전에는 맞춤형 테스트 설비가 없다보니 신속하게 개발하기가 어려웠습니다. 기계 가공은 접근하기 어려울 정도로 고가이며 시간이 많이 필요했습니다.
알리바흐는 “이제 3D 프린터로 제품 프로토타입과 테스트용 고정구, 게이지를 함께 개발하므로 최종 디자인을 결정할 때 테스트할 고정구도 얻을 수 있습니다. 우리는 가능한 한 적극적으로 대응하고 있습니다.”라고 합니다.
10년 전 도먼사가 첫 번째 FDM 3D 프린터를 구매한 이후, 알리바흐와 트라이슨은 프린터를 꾸준히 추가하여 기존 장치의 용량을 지속적으로 늘리고 대형 포맷 Form 3L을 포함하여 Formlabs SLA 프린터에서 전체 재료 라이브러리를 활용했습니다.
트라이슨은 “저희는 [첫 번째 3D 프린터]에 투자한 비용을 2개월 내에 회수할 수 있었습니다. Formlabs 프린터의 비용을 정당화해보거나 ROI를 계산해보면 2년이 아니라 단 몇 개월 만에 수익을 정당화할 수 있음을 확인할 수 있습니다. 이런 점 덕분에 3D 프린팅에 대한 투자가 가치 투자라는 우리의 리더십에 확신을 가질 수 있습니다."라며 확신했습니다.
도먼 프로덕츠는 다른 몇몇 응용 분야에도 3D 프린팅을 사용하고 있습니다. 저희 블로그 글에서 확인해보세요..
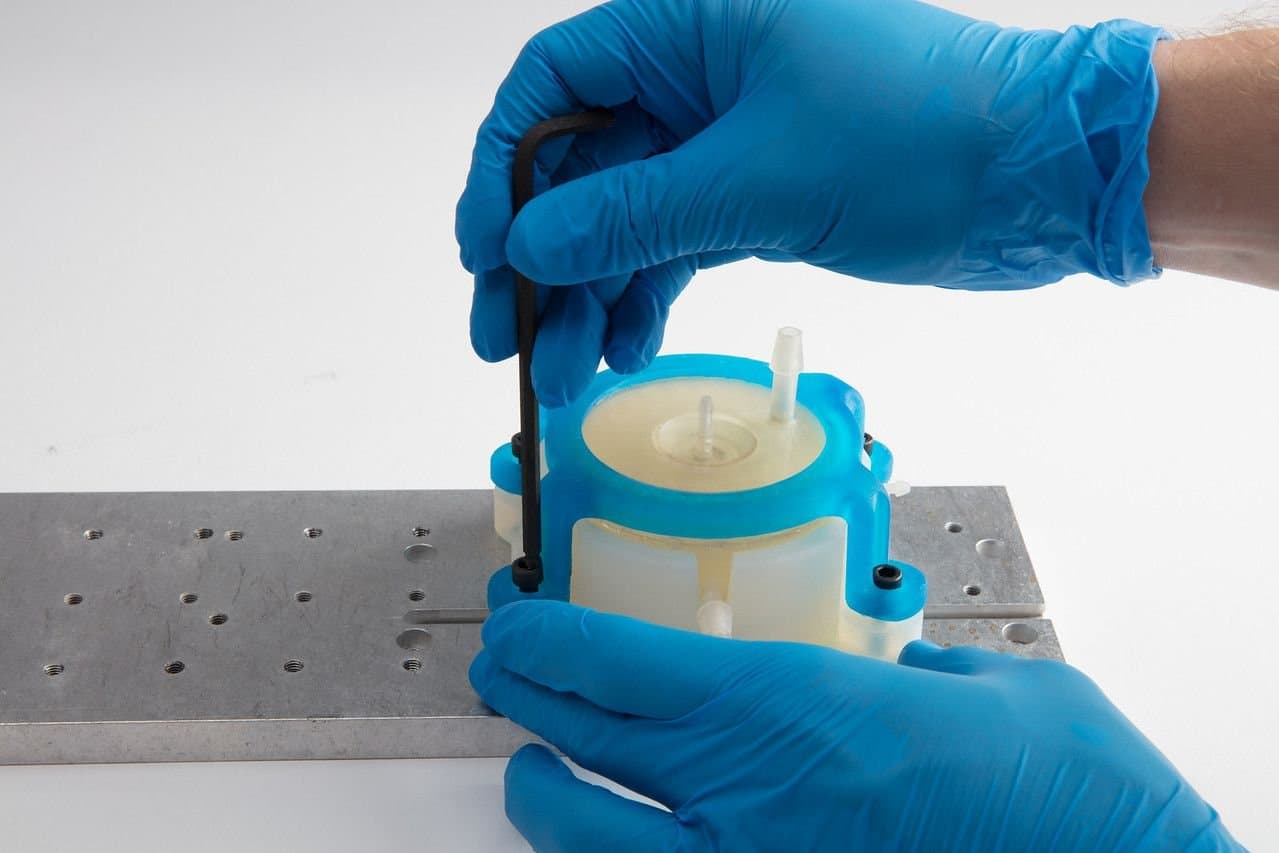
3D 프린팅으로 지그 및 고정구 설계
우수한 품질을 유지하면서 생산 속도를 극대화하는 것은 제조업체의 성공에 핵심적인 역할을 합니다. 지그와 고정구는 제조 및 조립 프로세스를 보다 간단하고 안정적이며 효율적으로 만들어 사이클 타임을 줄이는 동시에 작업자의 안전을 향상시키는 데 사용됩니다.
6. 3D 프린팅으로 제작하는 최종 사용 애프터마켓 파트
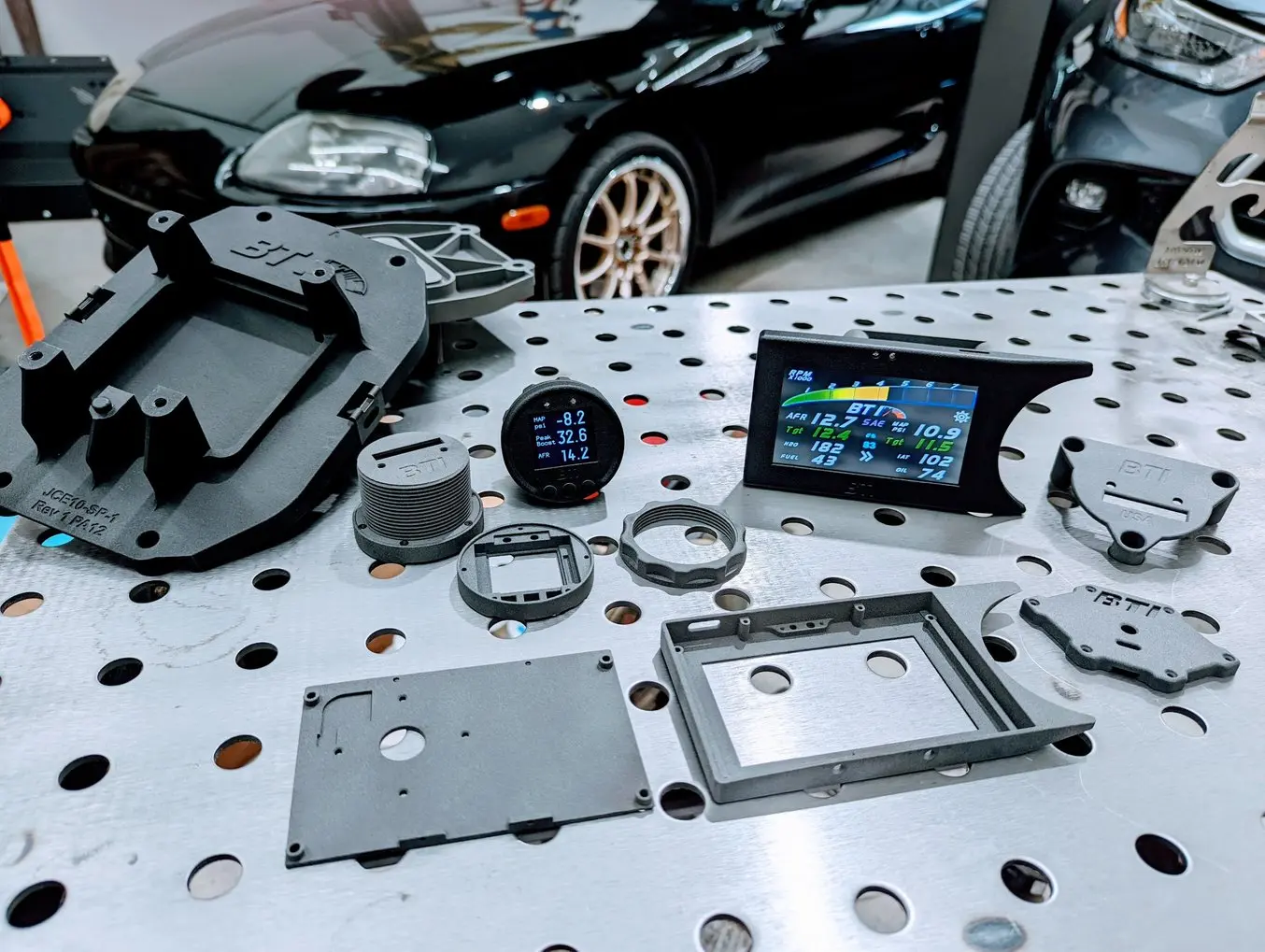
BTI Gauges는 고성능 자동차용 원격 측정 디스플레이를 설계합니다.
수많은 성공적인 비즈니스가 그렇듯 BTI 게이지는 시장의 틈새에서 시작했습니다. 설립자이자 소유주인 브랜든 토크미트(Brandon Talkmitt)는 고성능 자동차의 원격 측정 디스플레이를 맞춤형으로 제작하고 싶었습니다.
토크미트는 앞 유리가 여러 화면과 주의를 산만하게 하는 판독값으로 뒤덮이지 않도록 여러 성능 메트릭이 포함된 게이지를 찾아보았지만 실패했습니다. 그래서 그는 3D 프린터에서 게이지의 외부 케이싱을 프로토타이핑하고 직접 테스트하여 케이싱을 자동차 및 오븐 내부의 고열 환경에 노출시키고 여러 자동차 모델을 보완하도록 디자인을 수정하는 데서 시작했습니다.
1990년대 스타일의 일본 경주용 자동차, 람보르기니, 닷지 바이퍼스 및 기타 고성능 차량을 운전하는 고객들은 즉시 그의 제품에 관심을 표현했습니다.
토크미트는 값비싼 플라스틱 파우더 베드 융합 3D 프린터, 레진 3D 프린터, 저렴한 소형 SLS 옵션을 포함한 다른 3D 프린팅 옵션을 평가하기 시작했습니다. 그러나 50만 달러 가격표가 붙은 일부 제품과 기타 제품의 복잡한 재료 구매 프로세스 사이에는 사용 가능한 옵션이 없었습니다. Fuse 1을 알기 전까지는 말입니다. 토크미트는 “샘플을 받았을 때 '세상에, 내 파트가 이렇게 생겼으면 좋겠다'고 생각했어요. 그래서 몇 가지 테스트를 실행하고 어떤 종류의 열을 견딜 수 있는지 확인했습니다. 마무리 및 페인팅 프로세스를 수행했고 모든 것이 잘 되었죠.”라고 회고합니다.
지난 2년의 공급망 문제 기간 동안 BTI Gauges는 터치스크린 디스플레이와 9개 제품 라인에 필요한 기타 구성 요소 몇 가지가 부족해지는 문제에 직면했습니다. 라인에 필요한 기타 구성 요소의 몇 가지가 부족했습니다. Fuse 1으로 인하우스 3D 프린팅을 도입하니 새로운 툴링에 수천 달러를 지출하거나 지금은 구식이 된 제품의 백로그를 처리하지 않고도 즉시 새로운 디자인으로 전환할 수 있었습니다.
토크미트는 “그 모든 플라스틱 사이에서 어떻게 할 수 없었을 때 Fuse 1을 사용하면 즉석에서 변경할 수 있었습니다. 파일을 변경하는 데 30분이 걸렸습니다. Fuse 1 없이는 지금 당장 어떻게 할 수 없었을 것입니다.”라고 합니다.
BTI Guages에 대한 심층 스토리에서 최종 용도 애프터마켓 부품 생산에 대해 자세히 알아보세요.
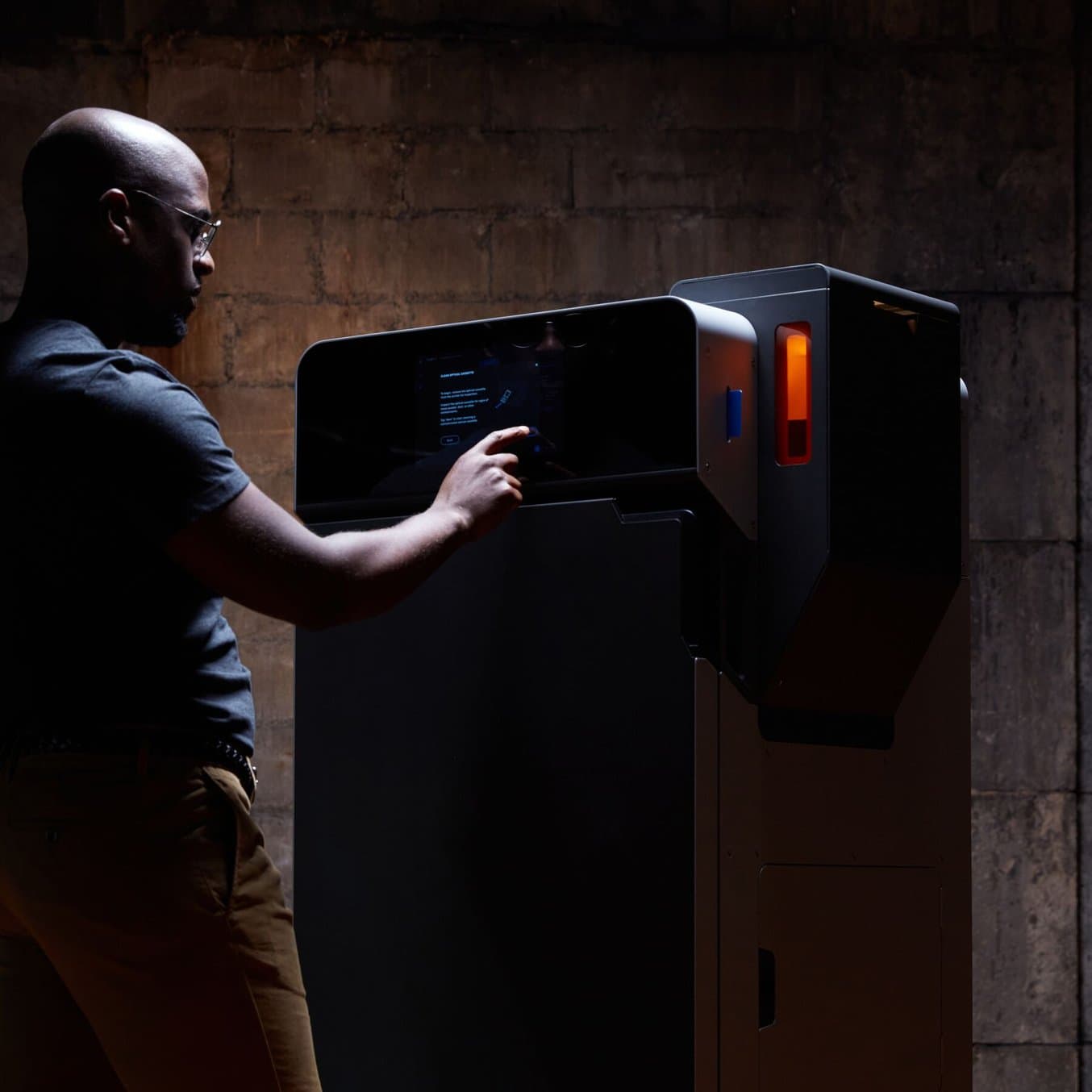
아웃소싱 vs. 인하우스 제작: 인하우스 SLS 3D 프린팅 도입은 언제쯤 합리적인 선택이 될 수 있나?
이 백서에서는 SLS 3D 프린터를 사내에 도입하는 것과 SLS 파트를 대행 업체에 아웃소싱하는 것의 가치 제안을 비교하여 평가해보려고 합니다.
경주용 자동차 및 오토바이용 3D 프린팅
3D 프린팅은 도구가 필요 없는 제조 공정으로 모터스포츠에 적합하며 소량 생산 및 맞춤형 제조를 신속하고 비용 효율적으로 수행할 수 있는 강력한 도구입니다. 툴링 시간과 비용을 제거함으로써 제품을 신속하게 수정하고 시장 출시 시간을 단축할 수 있는 유연성을 제공합니다. 설계 자유도를 높이고 제품을 맞춤화할 수 있는 기능을 제공하며 추가 비용 없이 격자 같은 복잡한 모양을 제작할 수 있습니다.
인하우스 3D 프린팅을 사용하면 모터스포츠 팀이 더 빠르게 개발하고, IP를 안전하게 유지하고, 더 많은 아이디어를 테스트하고, 궁극적으로는 경쟁에서 이길 수 있습니다.
7. 3D 프린팅된 반복 설계로 엔진 성능 개선
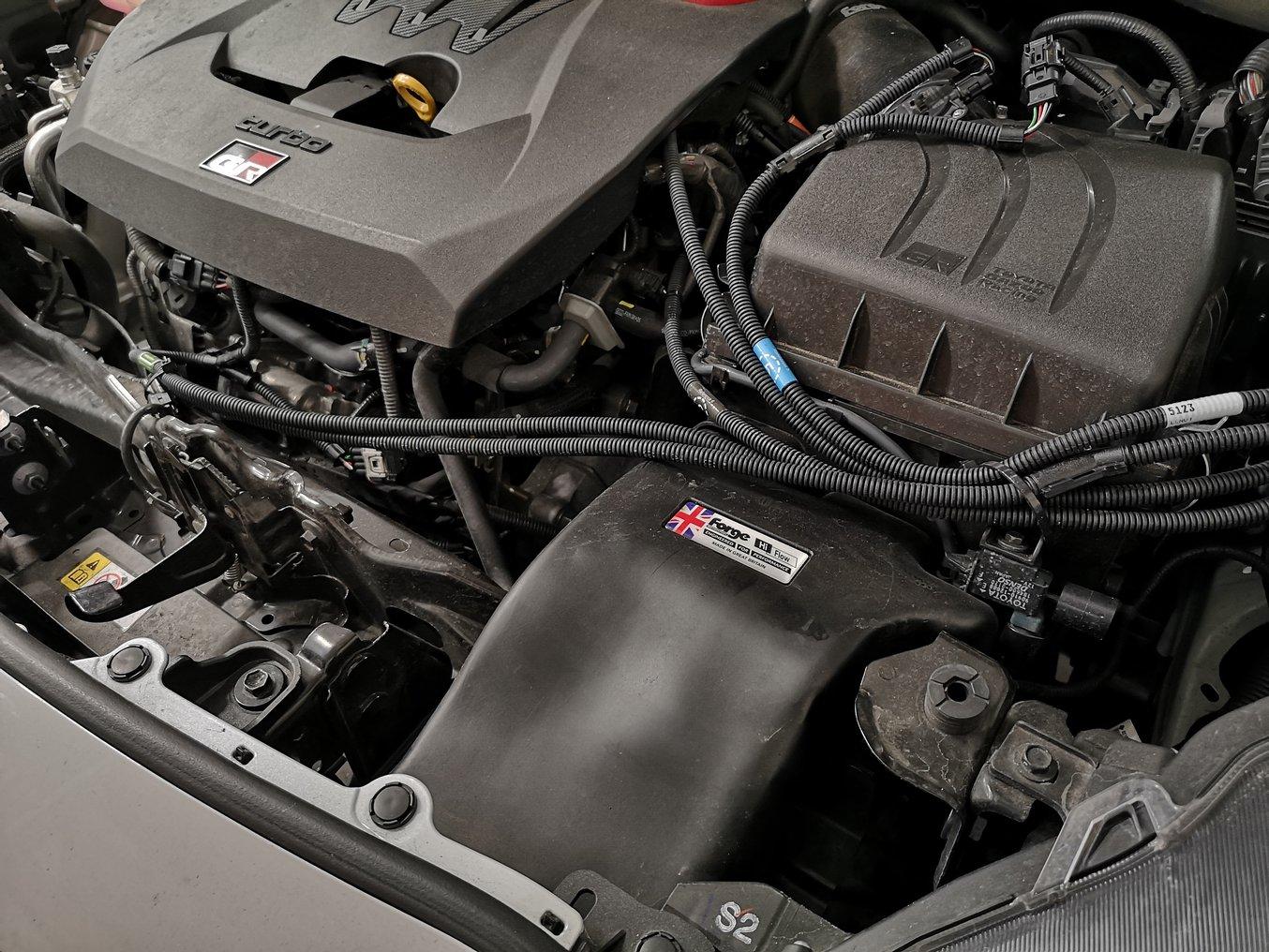
포지 모터스포츠(Forge Motorsport)의 재설계 덕트는 흡기 온도를 6° C까지 낮췄습니다.
고성능 자동차용 애프터마켓 파트를 젲가하는 포지 모터스포츠는 파트 프로토타입 제작에 3D 프린팅을 이용합니다. 토요타 야리스(Toyota Yaris) GR이 출시되었을 때 포지의 엔지니어들은 에어박스 개구부를 옮기고 파트의 전체 크기를 늘려 흡입구 덕트 설계를 개선할 수 있는 몇 가지 기회를 발견했습니다. 그렇게 하면 엔진 성능을 예측하기 어렵게 만드는 흡기 온도(IAT)의 변동을 줄이는 동시에 전반적인 평균 온도를 낮출 수 있을 것 같았습니다.
그들은 3D 스캐닝으로 OEM 부품을 리버스 엔지니어링하고 솔리드웍스(SOLIDWORKS)에서 가상으로 설계를 변경하여 공기 흐름을 시뮬레이션할 수 있었습니다. 실행 가능한 3D 모델을 제작하고 나서 그들은 빠르게 프린팅되는 Draft Resin으로 프로토타입을 만들었고 프로토타입으로 에어박스 개구부의 새 위치가 의도한 대로 작동하고 파트의 전체 크기가 다른 구성 요소나 케이블을 방해하지 않는다는 것을 확인했습니다. 기본 핏을 확인하고 나서 강력하고 충격에 강한 소재인 Tough 1500 Resin으로 파트를 다시 프린팅하고 최종 파트와 유사하도록 검은색으로 칠한 다음 고객에게 보내 테스트했습니다.
고객은 5개월 동안 자신의 야리스 GR에서 3D 프린팅된 파트를 사용했으며, 그 동안 트랙과 오르막길을 포함한 다양한 조건에서 성능에 대한 데이터를 수집했습니다. 재고 파트의 IAT는 42~45°C 사이에서 변화했으며, 레이스 도중 상당한 변화가 관찰되었습니다. Tough 1500 Resin으로 프린팅한 재설계 파트를 사용한 고객은 35~36 °C 사이에서 IAT를 측정했습니다. 예상대로 재설계된 파트는 전체 IAT가 낮고 변동이 줄었습니다. 이 데이터를 손에 쥐고 자신의 파트가 OEM 설계보다 개선되었다는 확신을 가지게 된 포지사는 탄소 섬유로 최종 생산 파트를 제조하기 시작했습니다.
3D 스캐닝을 사용한 리버스 엔지니어링 워크플로에 대한 자세한 내용은 포지 모터스포츠 및 Peel3D와 함께 하는 웨비나를 시청하세요.

포지 모터스포츠의 사례로 보는 자동차 산업의 3D 스캐닝과 3D 프린팅
Formlabs, Solid Print3D 및 peel 3d에서 제공하는 이 웨비나에서는 밸브, 인터쿨러 및 액추에이터와 같은 애프터마켓 자동차 산업을 위한 성능 업그레이드를 제조하는 포지 모터스포츠와 이야기를 나눕니다.
8. 포뮬러 자동차용 탄소 섬유 몰딩 및 3D 프린팅 최종 사용 부품
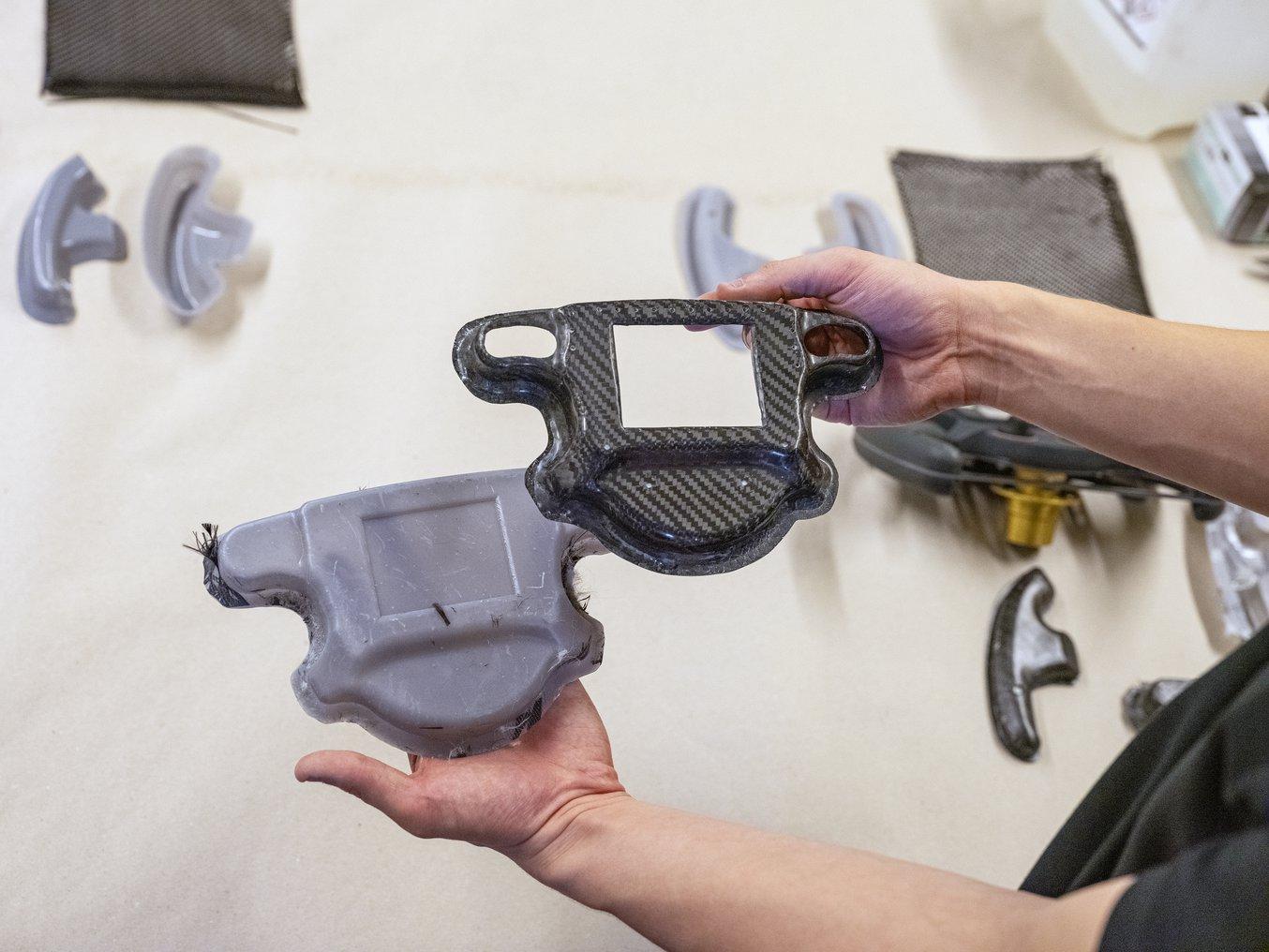
사내에서 금형을 3D 프린팅하게 된 TU Berlin의 경쟁 팀은 이 탄소 섬유 부품의 비용과 리드 타임을 크게 줄일 수 있었습니다.
매년 개최되는 포뮬러 스튜던트(Formula Student)는 전 세계 학생팀이 포뮬러 스타일의 자동차를 만들고 경주를 벌이는 공학 설계 대회입니다. 포뮬러 학생팀 TU 베를린(FaSTTUBe)은 가장 큰 그룹 중 하나로, 80~90명의 학생들이 2005년부터 매년 새로운 경주용 자동차를 개발하고 있습니다. 해당 팀은 Form 3 SLA 3D 프린터를 제작 도구로 채택하여 다른 방법을 사용했다면 엄청난 비용이 들었을 시간 및 비용을 절감하며 탄소 섬유 부품을 저렴하게 제작할 수 있었습니다.
복합재용 3D 프린팅 금형을 통해 팀은 스티어링 휠 섀시 같은 핵심 파트를 설계할 때 훨씬 더 큰 유연성, 리드 타임 단축 및 비용 절감을 할 수 있었습니다. 이 파트의 금형을 가공하려면 값비싼 특수 도구를 소싱해야 했고, 성형 파트를 아웃소싱하려면 몇 주가 걸리고 비용은 거의 1,000유로에 달했습니다. 대신 인하우스로 금형을 3D 프린팅하고 수작업으로 라미네이팅하는 데 드는 비용은 단돈 10유로, 작업 시간은 1.5시간입니다.
또한 이 팀은 3D 프린팅을 사용하여 디자인 프로토타입, 경량 부품, 최종 사용 파트 제작까지 하고 있습니다. 그들의 스토리에서 이러한 응용 분야에 관한 자세한 내용을 확인해보세요.
3D 프린팅 기술은 FaSTTUBe 팀에 유연성, 자유로운 설계 가능성, 비용 절감 효과를 가져다주었습니다. 또한 학생들은 프로젝트 과정에서 프로토타입, 툴링 및 최종 사용 부품을 제작하는 경험을 쌓을 수 있었습니다. 이러한 능력은 학생들이 후일 직장 생활을 할 때도 그대로 유지되며 모든 엔지니어링 분야에서 두각을 나타낼 수 있는 귀중한 경험이 됩니다.
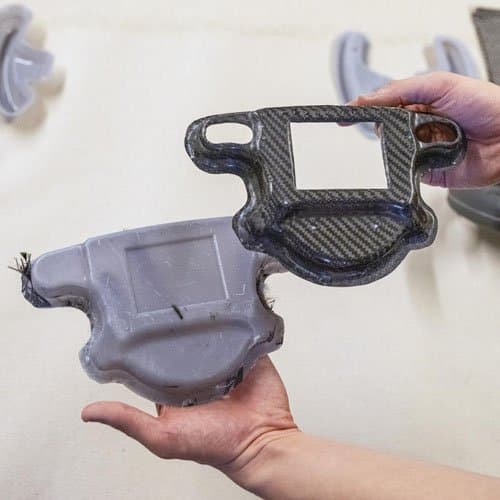
3D 프린팅 금형을 사용한 탄소 섬유 파트 제작
탄소 섬유 파트 제작에 사용되는 프리프레그 및 핸드 라미네이팅 방법에 관한 단계별 지침과 복합 금형 설계 지침을 확인하려면 본 백서를 다운로드하세요.
9. 3D 프린팅 예비 엔진 부품
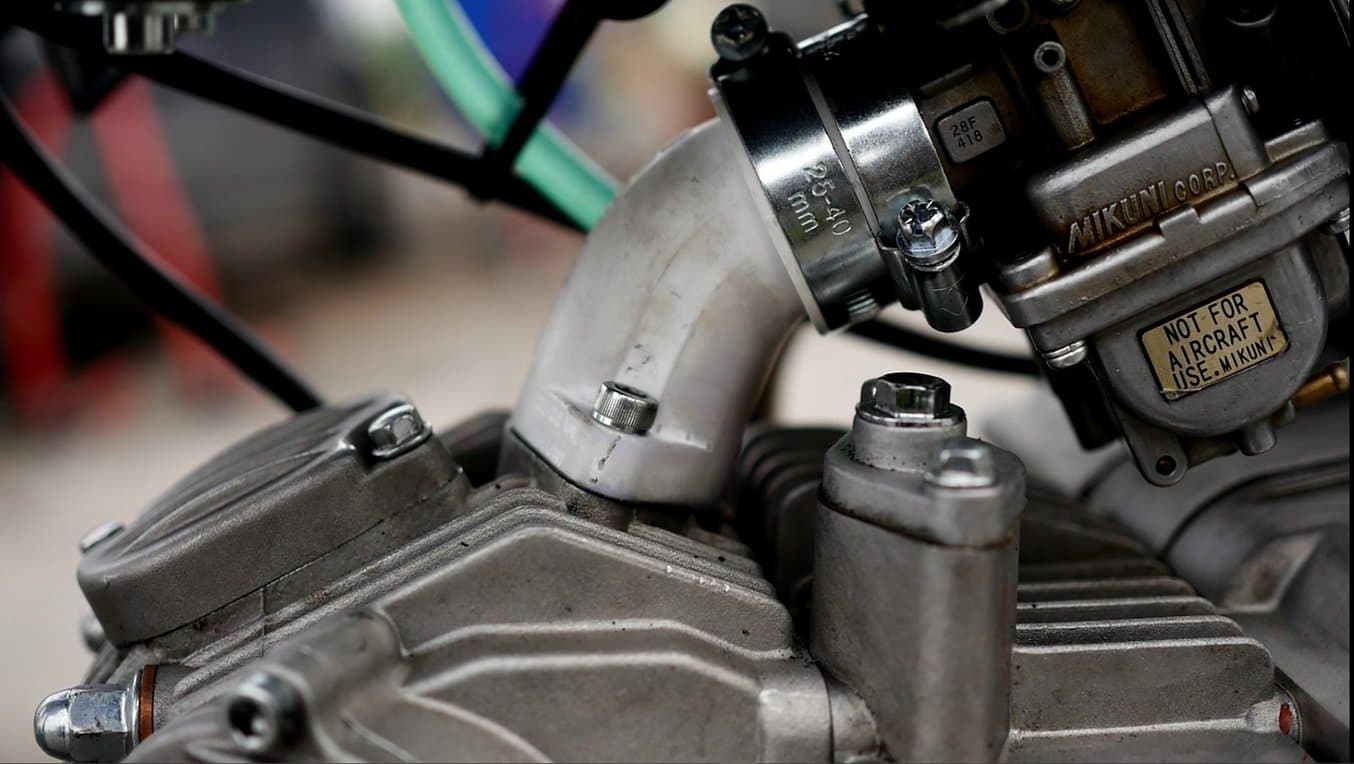
Rigid 10K Resin으로 프린팅한 흡기 매니폴드는 원래 알루미늄 파트보다 레이스 후 온도가 낮았습니다.
안드레아 피라치지(Andrea Pirazzini)는 2012년부터 오토바이를 타고 있습니다. 그는 자신의 자전거에 장착할 기능적이고 안전한 3D 프린팅 흡기 매니폴드를 설계하고 제작하는 데 도전하고 싶었습니다. 과거에 FDM 프린팅 기술을 시도했지만, 파트가 밀폐되지 않고 엔진의 기능을 손상시켜 원하는 결과를 얻지 못했습니다.
프로젝트를 전개해나가기 위해 피라치지는 3D 스캐닝과 Autodesk Fusion 360 소프트웨어를 사용하여 설계를 리버스 엔지니어링했습니다. 프레임과 기화기가 있는 4행정 엔진(2밸브) 엔진을 스캔하여 매니폴드의 크기를 정확하게 결정한 다음 최적의 위치에 배치하는 데 도움이 되었습니다. CAD 소프트웨어를 사용하여 헤드 흡입구의 직경을 기화기와 정렬하여 단차와 압력 강하 또는 난류를 피할 수 있었습니다.
새로운 매니폴드 디자인은 100μm 레이어 높이에서 Rigid 10K Resin으로 Form 3에서 프린팅하여 눈에 보이는 레이어 라인 없이 매끄러운 표면을 얻었습니다. 마무리로 피라치니는 고전적인 수성 사포를 사용하여 표면을 매끄럽게 만들었습니다. 방수를 위해 외부와 내부를 처리해야 하는 FDM 매니폴드와는 달리 SLA 프린팅을 이용하면 견고하고 방수가 되는 파트를 얻을 수 있습니다.
피라치니가 Form 3로 프린팅한 매니폴드는 고온과 저온을 완벽하게 견뎌냈으며 여전히 그의 피트 바이크에 장착되어 있습니다. 열화상 카메라를 사용한 덕분에 피라치니는 Rigid 10K Resin의 열 성능이 훨씬 더 낫다는 사실을 발견했습니다. 냉각 핀이 있는 3D 프린팅 매니폴드는 기존 알루미늄 매니폴드에 비해 섭씨 40~50도 더 낮은 온도를 기록했습니다. 게다가 섭씨 33도 안팎의 외부 온도에서 20~25분 정도 레이스를 펼친 뒤 화상 걱정 없이 매니폴드를 만질 수 있었습니다.
이 프로젝트는 성공했을 뿐만 아니라 엔진의 기능도 개선했습니다. 피라치니가 원래 디자인에 적용한 몇 가지 개선 사항을 기반으로 엔진은 표준 가공 매니폴드에 비해 더 많은 마력(약 1 HP, 거의 10% 증가)을 사용하면서 챔피언십 규칙에 의해 부과된 제한을 벗어나지는 않았습니다.
세부적인 사례 연구에서 피라치니가 프로젝트를 개발한 방법에 관해 알아보세요.
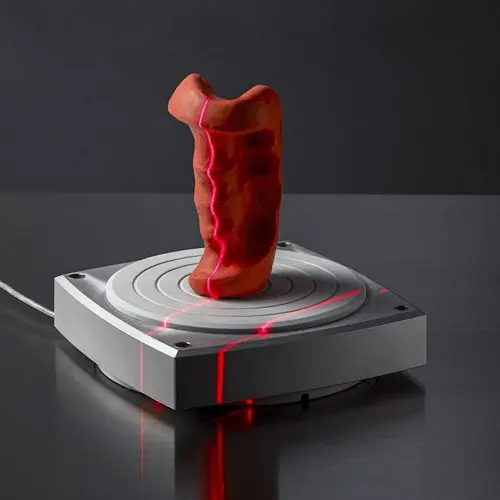
리버스 엔지니어링에 사용되는 3D 스캐닝과 3D 프린팅과 기타 응용 분야
3D 스캐닝 및 3D 프린팅 워크플로는 복제 및 복원, 리버스 엔지니어링, 계측 등에 적용할 수 있습니다.백서를 다운로드하여 이러한 애플리케이션을 살펴보고 시작하는 방법을 알아보세요.
보너스: 3D 프린팅 자동차
2010년대 초 3D 프린팅 과대 광고 속에서 전체 3D 프린팅 자동차를 포함하여 규모가 크고 복잡한 어셈블리를 3D 프린팅하게 되자 대중 매체에서 흥분하기 시작했습니다. 그러나 "완전한" 3D 프린팅 자동차를 가장 많이 지지했던 지지자조차도 엔진이나 기타 전기 기계 어셈블리가 아닌 섀시, 차체 및 시트와 같은 구조 및 트림 구성 요소를 프린팅하는 데만 중점을 두었습니다.
로컬 모터스(Local Motors) 및 EDAG를 비롯한 일부 회사는 2010년대 중반에 SEMA와 같은 무역 행사에서 대중에게 공개하기 위해 섀시와 차체를 3D 프린팅한 완전한 컨셉카를 제작했습니다. 그러나 이러한 프로젝트 중 어느 것도 연속 생산에 도달하지는 못했습니다.
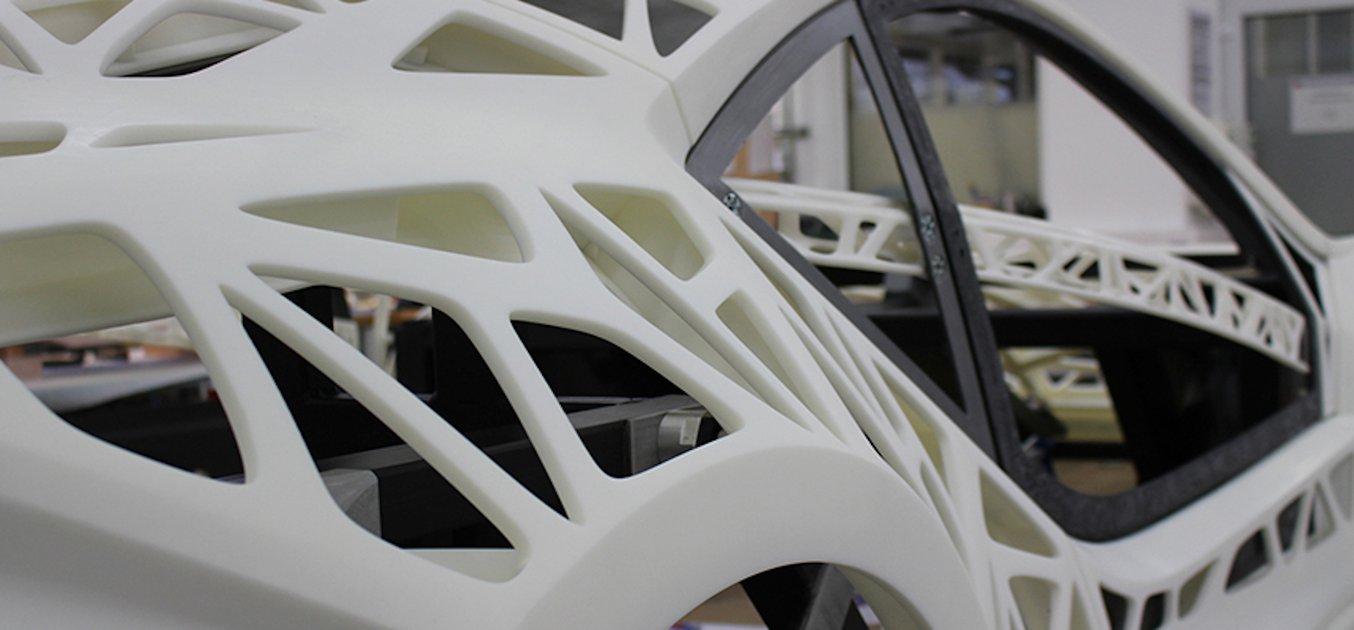
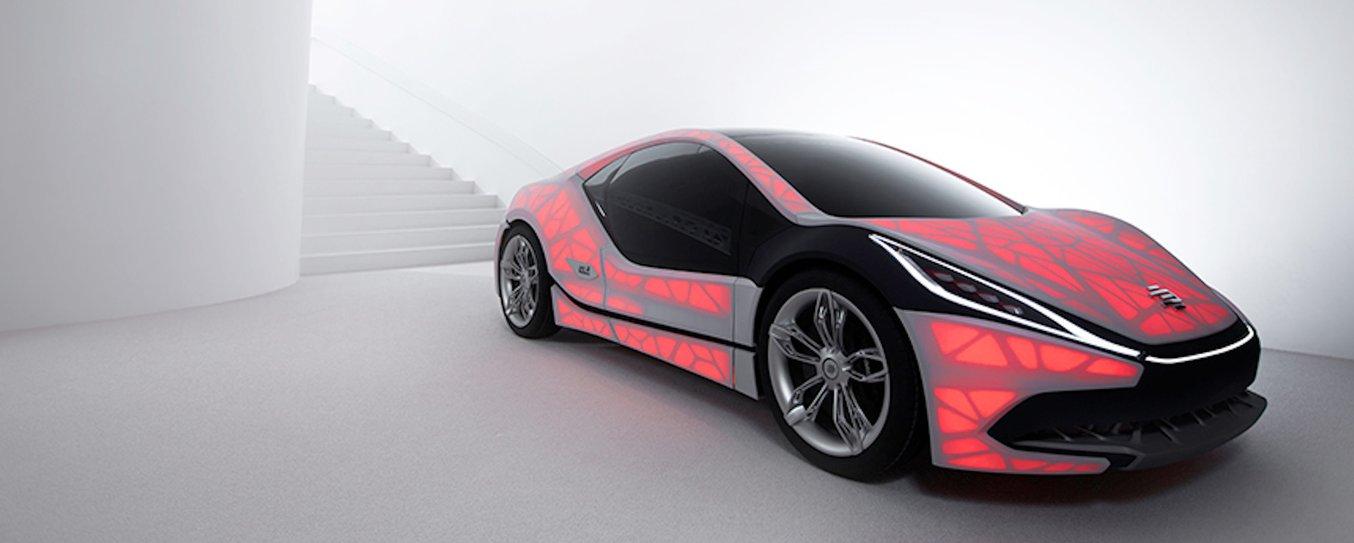
내후성 외에도 EDAG의 Light Cocoon 커버는 디자인과 개인화 측면에서 절대적인 자유를 제공합니다.(출처: EDAG)
현재 연속 생산에 가장 가까이 다가간 프로젝트와 회사는 Divergent 3D와 XEV인 것 같습니다.
Divergent 3D는 제너레이티브 디자인과 3D 프린팅을 결합하여 자동차 파트 제조업체를 위해 맞춤형 파트를 만듭니다. 구성 요소를 설계하면 회사의 금속 3D 프린터를 사용하여 제조합니다. 그들의 첫 공개 프로젝트는 Czinger 21C 하이퍼카이며 애스턴 마틴(Aston Martin)을 비롯한 주요 OEM의 공급업체이기도 합니다.
스펙트럼의 다른 쪽 끝에서 이탈리아 회사 XEV가 개발한 YoYo는 현재 고객에게 배송되는 최초의 "매스 마켓" 3D 프린팅 전기 자동차일 수 있습니다. YoYo는 섀시, 시트, 앞 유리를 제외하고도 눈에 보이는 모든 부분이 3D 프린팅으로 제작되었습니다. 3D 프린팅의 광범위한 사용 덕분에 이 회사는 파트 수를 2,000개에서 57개로 줄여 무게가 450kg에 불과한 가벼운 디자인을 만들었습니다.
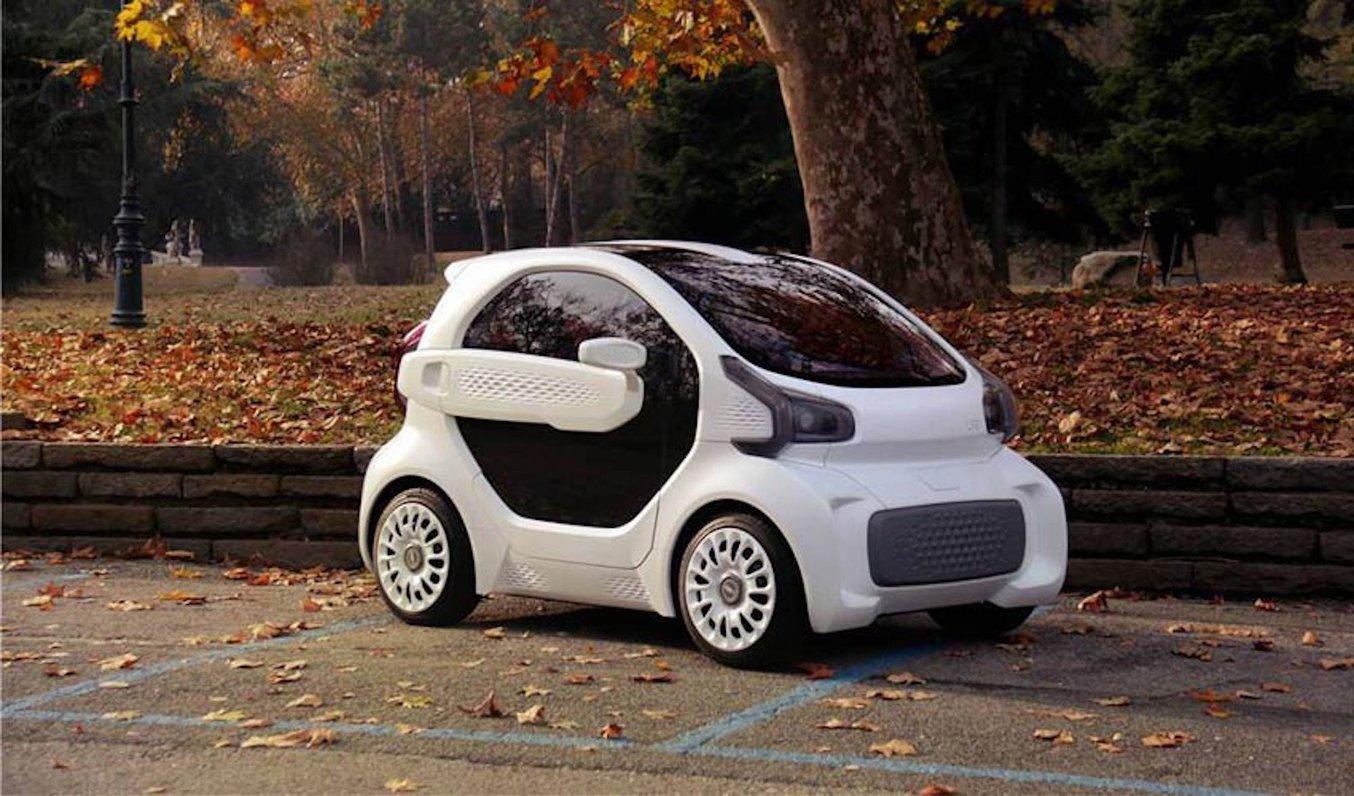
YoYo는 현재 고객에게 배송되는 최초의 "매스 마켓" 3D 프린팅 전기 자동차입니다.
자동차 분야의 3D 프린팅에 대해 자세히 알아보기
이 모든 사례를 통해 살펴본 바와 같이 3D 프린팅이 시장 출시 시간을 단축하고 차량 성능을 개선하기 위해 창의적으로 활용할 때 공급업체, OEM 및 소비자에게 상당한 이점을 제공한다는 것이 이미 반복적으로 입증되었습니다. 경우에 따라 3D 프린팅 기술은 경계를 허물고 설계 및 생산에서 완전히 새로운 가능성에 도달하는 데 도움이 됩니다. 다른 경우에는 기술이 생산 비용을 낮추고 시간을 절약합니다.
3D 프린팅의 가치와 현실에 대한 이해가 업계 전반에 걸쳐 계속 확산되고 기술 및 사용 가능한 재료 기반이 더욱 다양해짐에 따라 적층 기술은 전 세계 차량을 설계, 제작 및 유지 관리하는 방식을 지속적으로 재구성할 것입니다.