Located in the Bilbao region in Spain, IGESTEK is a leading company specializing in the development of lightweight solutions for the automotive industry using plastics and composite materials.
The company develops and integrates different hybrid processing techniques to manufacture composite components, which can then be implemented by Tier 1 automotive suppliers and original equipment manufacturers (OEMs) to produce parts for high-end cars and motorcycles.
IGESTEK’s team uses 3D printing throughout the product development process, from the conceptual design phase to verify geometries to the detailed design phase for the realization of functional prototypes. They also use 3D printing to manufacture rapid tooling, such as inserts for plastic injection molds or thermoforming tools for composites.
Read on to learn how IGESTEK improves the speed of development, reduces costs, and ensures an agile response to possible problems that may arise.
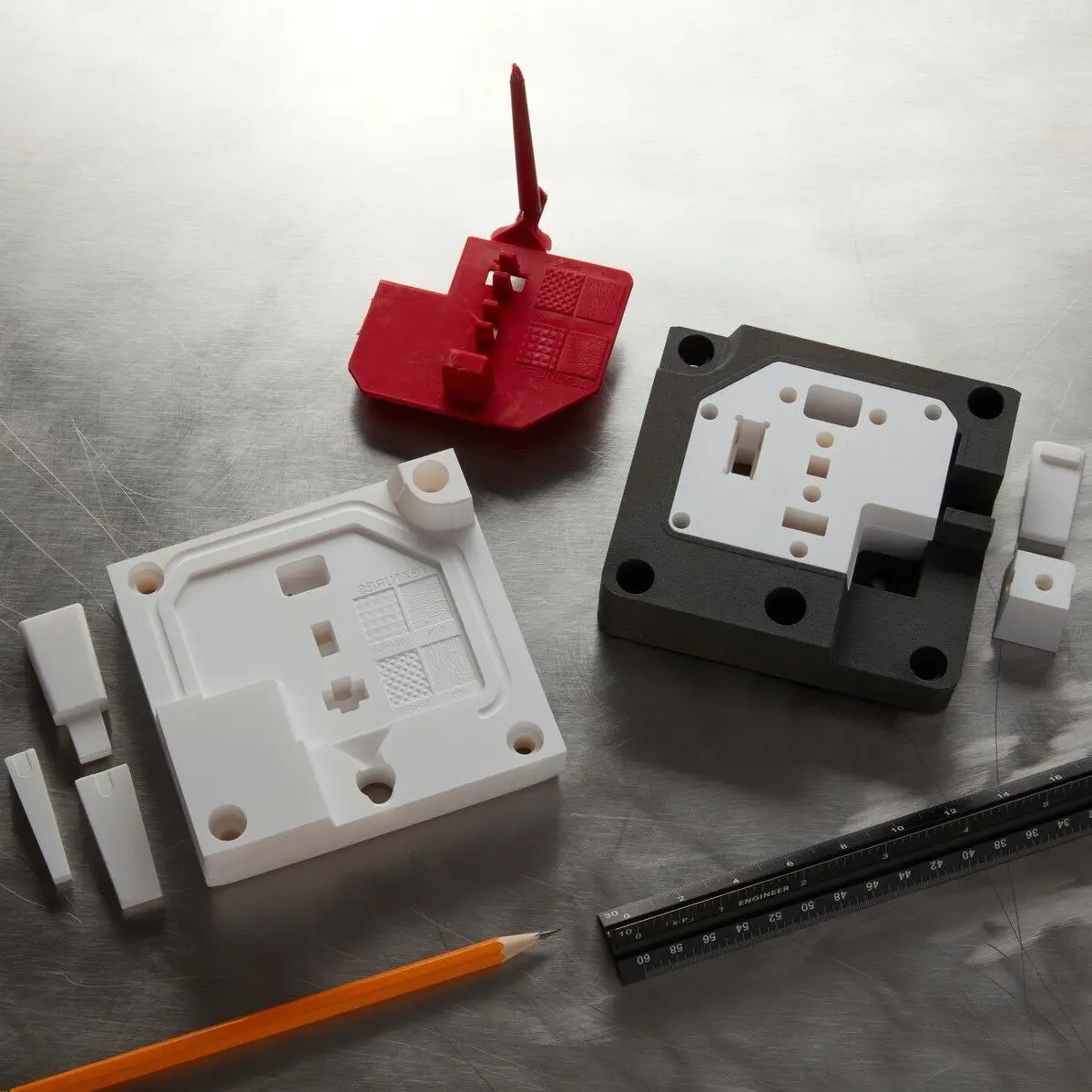
Guide to Rapid Tooling
In this white paper, learn how to combine rapid tooling with traditional manufacturing processes like injection molding, thermoforming, or casting.
Iterating a Generative Designed Car Component on the Form 3L
One of IGESTEK’s latest innovative projects is a Suspension Shock Absorber Support (Top Mount). These components are part of a car’s suspension system that aim to reduce the vibrations produced by the rolling of the vehicle to improve comfort for the passengers.
The shock absorber support was developed with Autodesk’s Fusion 360 generative design software, which provided multiple solutions based on a limited series of requirements.
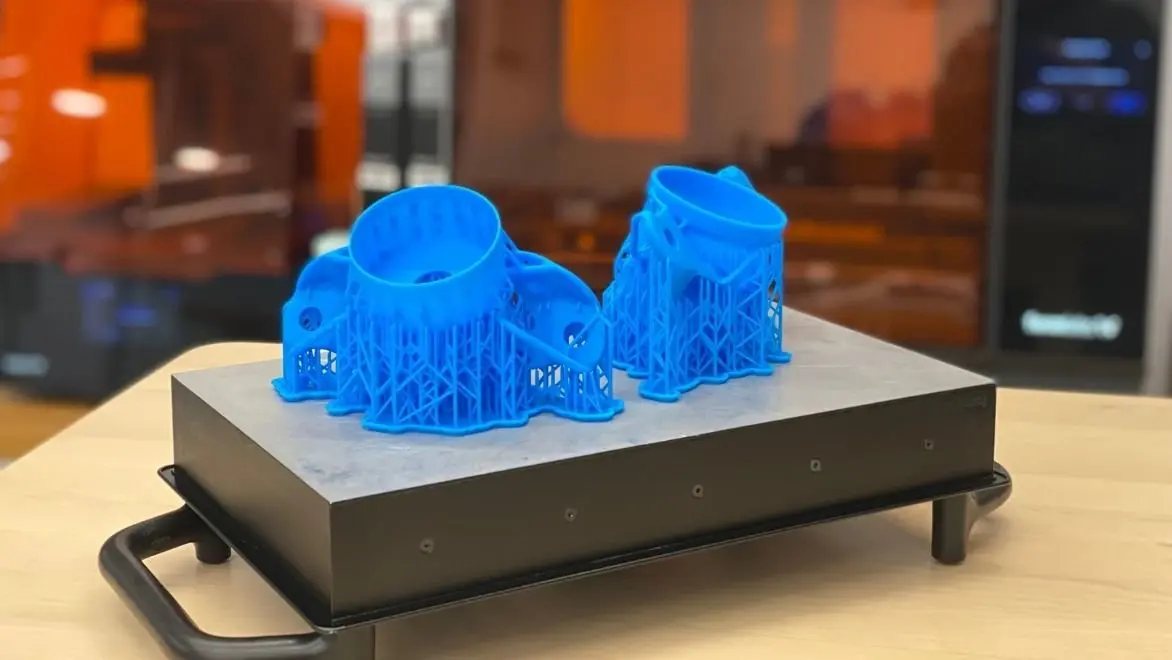
The large build volume of the Form 3L empowered IGESTEK to print multiple iterations of the component at the same time.
The team then 3D printed the most promising designs on their Form 3L large-format stereolithography (SLA) 3D printer in-house to validate the geometry, leveraging its large build volume to print up to three different iterations at the same time. SLA 3D printing made it feasible to realize the complex geometries obtained through generative design and validate assembly and kinematic processes with functional prototypes without investing in expensive tooling.
The end result of the R&D process was a multi-material architecture that combines metal 3D printing based on generative geometries and lighter composite materials to offer the best performance, in a 40% lighter package than current solutions on the market.
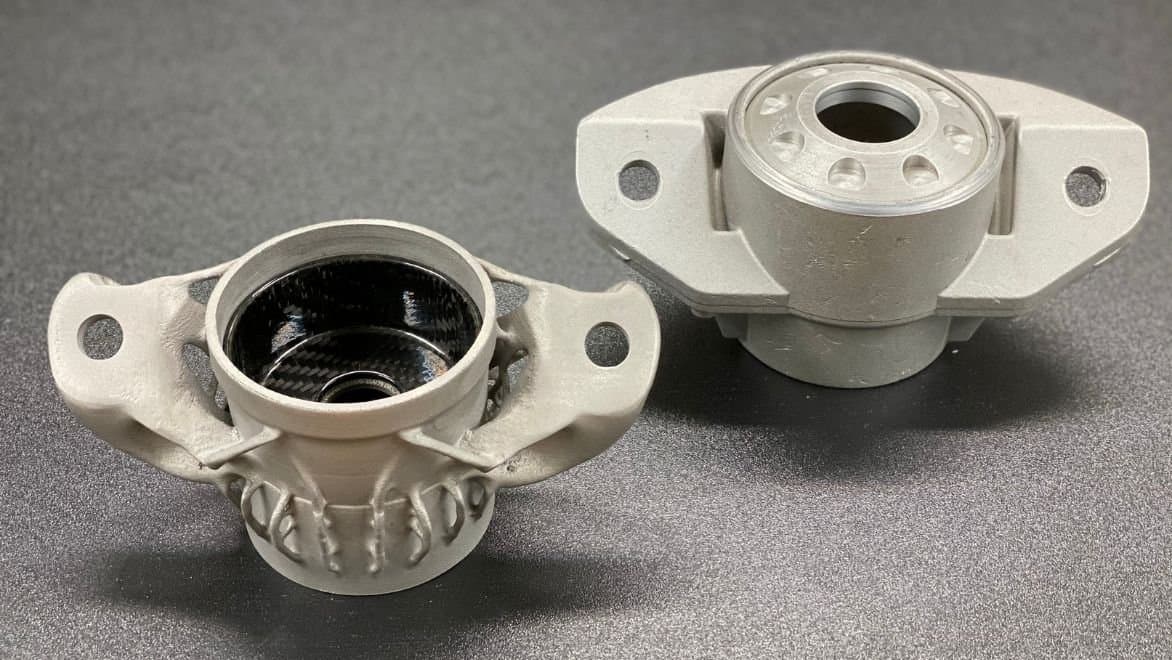
The end result, built using a combination of metal 3D printing and composite materials.
Using Diverse SLA 3D Printing Materials to Create a Thermoforming Tool
IGESTEK’s team also uses 3D printing beyond prototyping, to produce rapid tooling for producing composite parts, such as thermoforming carbon prepregs.
“Formlabs resins, such as Rigid 10K and High Temp are quite useful for engineering purposes. We usually work with composite compression thermoforming technologies. To work with a press, the tool needs to be stiff and heat-resistant, because you're using pressure [to form the composite parts] and also high temperature, usually 180 degrees or 200 degrees,” said Nerea Romero, Innovation Manager at IGESTEK.
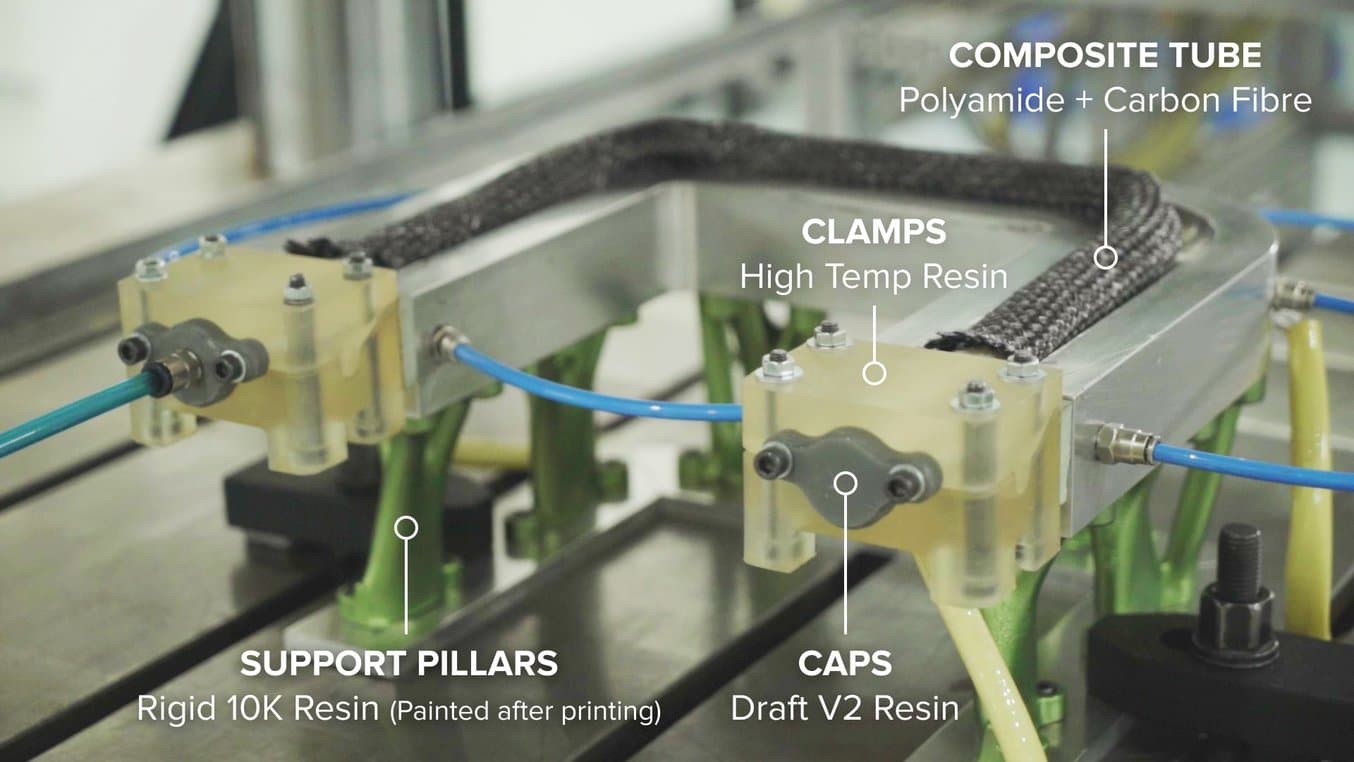
This thermoforming rig for composite tubes was built using a variety of 3D printed parts.
One recent example is a tool that the team developed to manufacture composite tubes. They used Rigid 10K Resin to produce the support pillars of the rig that required high stiffness, High Temp Resin to produce the clamps that needed to withstand high temperature and air pressure, and Draft Resin to quickly produce end caps for the tool.
“[If we didn’t have access to 3D printing], we’d have to produce it with metal, which obviously takes more time and is more expensive. With 3D printing, we have the quick answer for what we are researching. If something doesn't work, we can just print another prototype and improve it," said Romero.
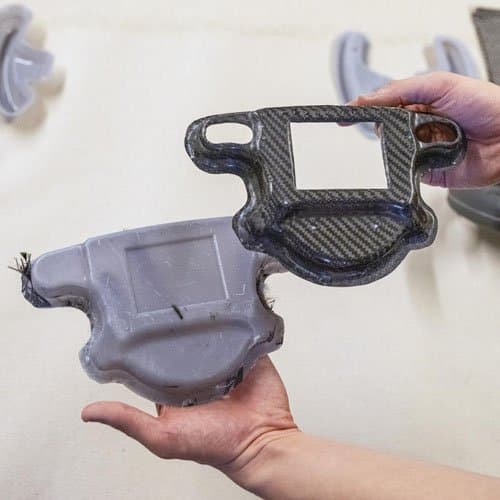
Carbon Fiber Parts Manufacturing With 3D Printed Molds
Download this white paper for composite mold design guidelines and step-by-step guides to the prepreg and hand laminating methods to create carbon fiber parts.
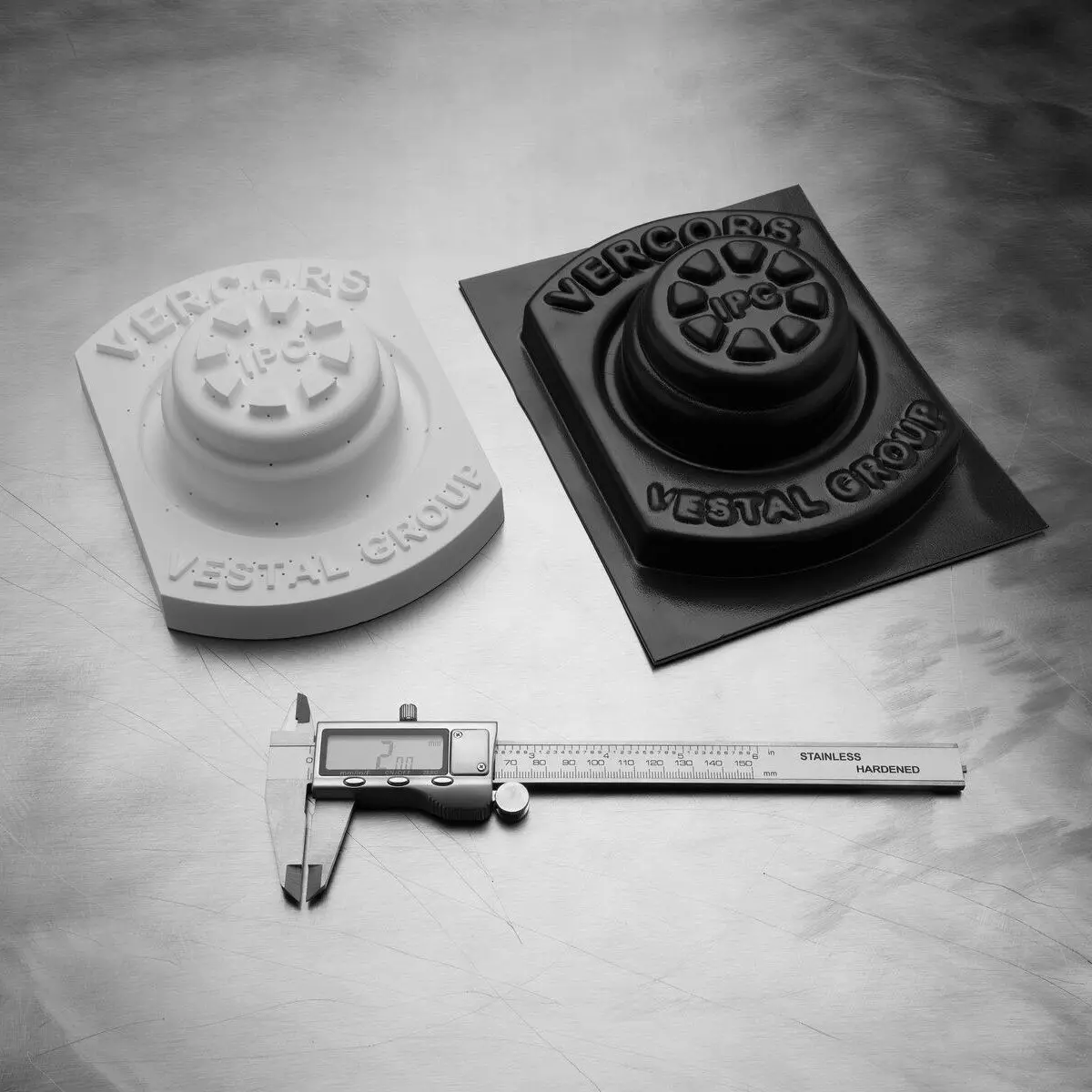
Low-Volume Rapid Thermoforming With 3D Printed Molds
Download our white paper to see how to create complex molds with 3D printing fast and learn about tips and guidelines that you’ll want to follow when preparing your mold parts.
Injection Molding With 3D Printed Mold Inserts
IGESTEK’s team also uses 3D printing to create mold inserts for injection molding plastic parts. Traditionally, they’d machine these inserts out of aluminum and steel—in-house for simple parts and outsourced for more complex molds—but this incurs high costs and long lead times, especially for one-off or low-volume prototypes.
With a recent example of an injection mold insert for manufacturing a component for the exterior cover of a car, 3D printing allowed the team to reduce costs and lead time to less than a third of the original.
Injection Mold Insert | 3D Printed | Machined Metal |
---|---|---|
Cost | 300€ | 1000€ |
Lead time | 10 hours | 30 hours |
The mold has two cavities: one cavity is made of a metal insert and the other cavity is a custom 3D printed insert that contains the negative of the design. For prototyping, this is ideal, because the team can easily change the 3D printed inserts and test different iterations rapidly.
“For the prototype phase, you only need a few components that will be assembled with other components to test the symmetry of everything. With 20 or 50 components, it's enough to prove what you're doing works," said Romero.
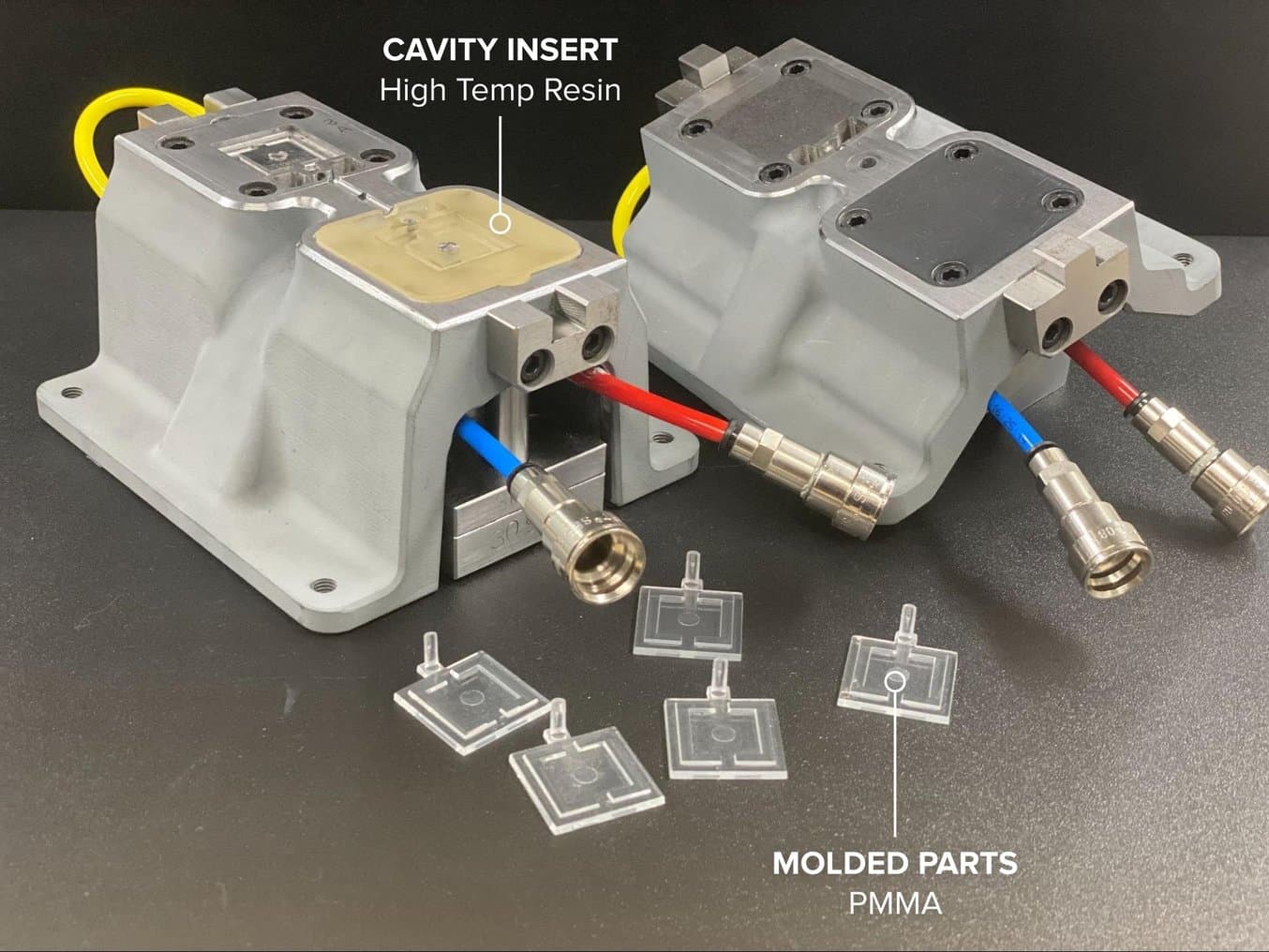
Injection molding setup for a PMMA car component, using mold insert printed in High Temp Resin.
The number of molded parts that can be obtained with a 3D printed insert depends mainly on three factors: molding material, injection system, and molding process parameters.
“It depends a lot on what type of material you're using for the injection molding or for the composite. Because for injection molding, for instance, if you're using plastic, which is reinforced with fibers, it's much more aggressive than conventional materials. So, [the insert] will be damaged earlier. Maybe you can obtain 20 components, but if you want to produce more, you just need to exchange the inserts to continue producing," said Romero.
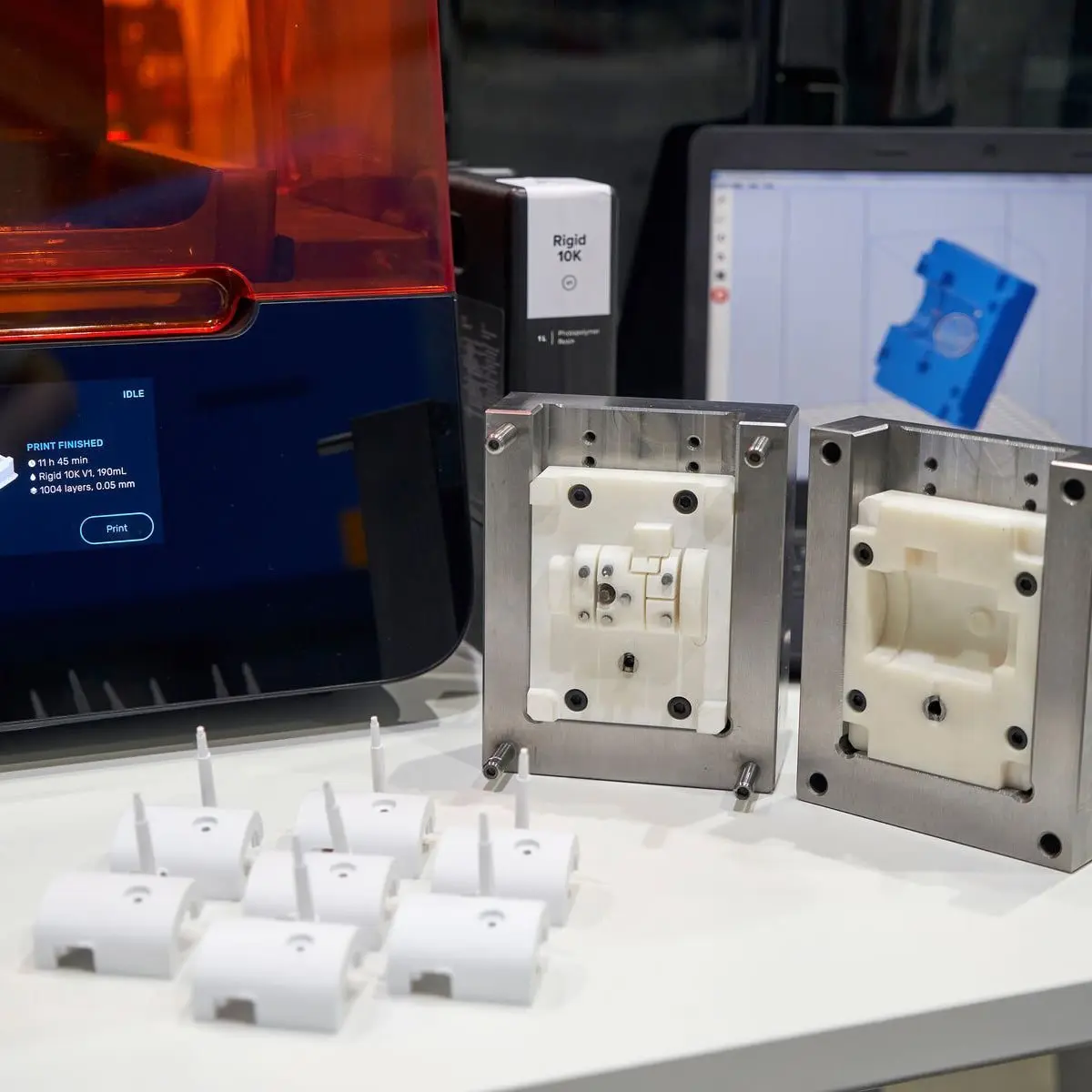
Low-Volume Rapid Injection Molding With 3D Printed Molds
Download our white paper for guidelines for using 3D printed molds in the injection molding process to lower costs and lead time and see real-life case studies with Braskem, Holimaker, and Novus Applications.
Moving Onto the Next Big Project
As IGESTEK’s team continues to innovate, they’re already thinking about how they can push the boundaries of what’s possible with 3D printing in their next projects.
Some of their next projects include creating large-scale thermoforming tooling, leveraging the build volume of their Form 3L, and experimenting with other materials like Flexible 80A Resin and Elastic 50A Resin that bring new capabilities to tooling.