Brose, proveedor de piezas automovilísticas a escala global, recurre a la impresión 3D SLS para producir piezas de uso final para coches
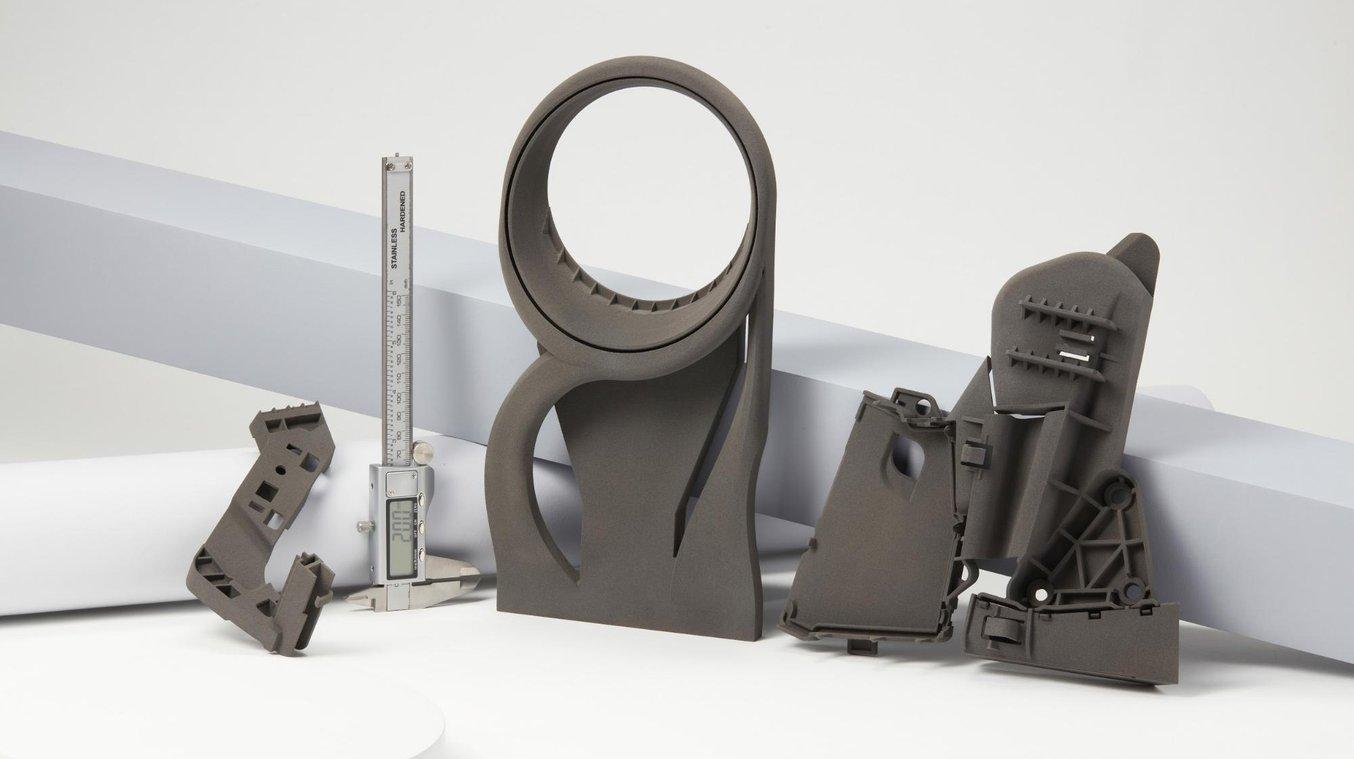
Si has estado en un coche, es muy probable que hayas interactuado con uno de los productos de Brose. Con 25 000 empleados en 24 países, esta empresa familiar es uno de los mayores proveedores automovilísticos de primer nivel y colabora con más de 80 marcas automovilísticas, más de 40 proveedores y 50 fabricantes de bicicletas eléctricas.
Muchos de los nuevos vehículos que se fabrican en todo el mundo incluyen como mínimo un producto de Brose, entre los que se encuentran diversos componentes y sistemas mecatrónicos como estructuras de asientos, piezas de las puertas y diversos motores y mecanismos eléctricos.
Al ser una de las empresas más innovadoras de Alemania, Brose se encuentra en una posición privilegiada para integrar la fabricación aditiva en sus productos y en su proceso de trabajo para la fabricación. Utiliza varias tecnologías para elaborar prototipos, herramientas y fijaciones y su siguiente objetivo es pasar a la producción en serie. La última incorporación a su parque de impresoras, la Fuse 1, es la primera impresora 3D industrial de sinterizado selectivo por láser (SLS) de Formlabs y una de las herramientas que ayudará a hacer realidad su meta.
Sigue leyendo para conocer la experiencia que ha tenido con la nueva máquina Christian Kleylein, técnico de fabricación aditiva de polímeros en serie de Brose, y cómo la empresa planea usar la impresión 3D para llevar a cabo la fabricación en serie.
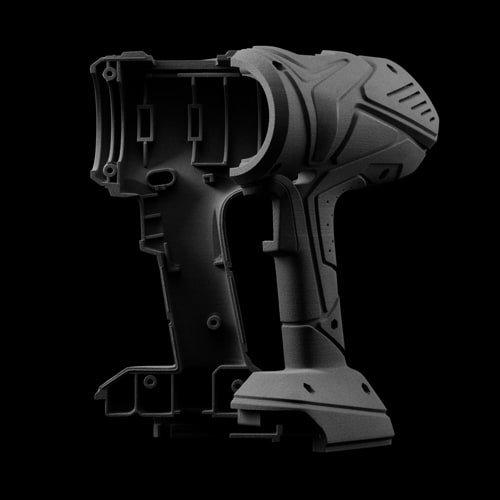
Introducción a la impresión 3D por sinterizado selectivo por láser (SLS)
¿Estás buscando una impresora 3D capaz de crear piezas resistentes y funcionales? Descarga nuestro libro blanco para aprender cómo funciona la impresión SLS y por qué es un proceso de impresión 3D popular para crear prototipos funcionales y productos de uso final.
La Fuse 1 en un entorno industrial
La fabricación aditiva es una de las nuevas capacidades clave de Brose. Su centro de fabricación aditiva en Alemania en un taller completo para la creación de prototipos, para el desarrollo de procesos y materiales y para la valoración, que produce piezas para todo el mundo.
Todo empezó hace más de diez años con su primera impresora 3D de modelado por deposición fundida (FDM), pero desde entonces la empresa ha expandido sus capacidades para abarcar casi todos los procesos de fabricación aditiva del mercado: estereolitografía (SLA), procesos de inyección de material, sinterizado selectivo por láser y una gran parque de impresoras 3D de metal.
El parque de impresoras de Brose cuenta con varios sistemas de impresión SLS, desde pequeñas máquinas de escritorio hasta las impresoras industriales tradicionales de mayor tamaño. Su experiencia con la tecnología es muy amplia y fue una de las primeras empresas de Europa en hacerse con la Fuse 1.
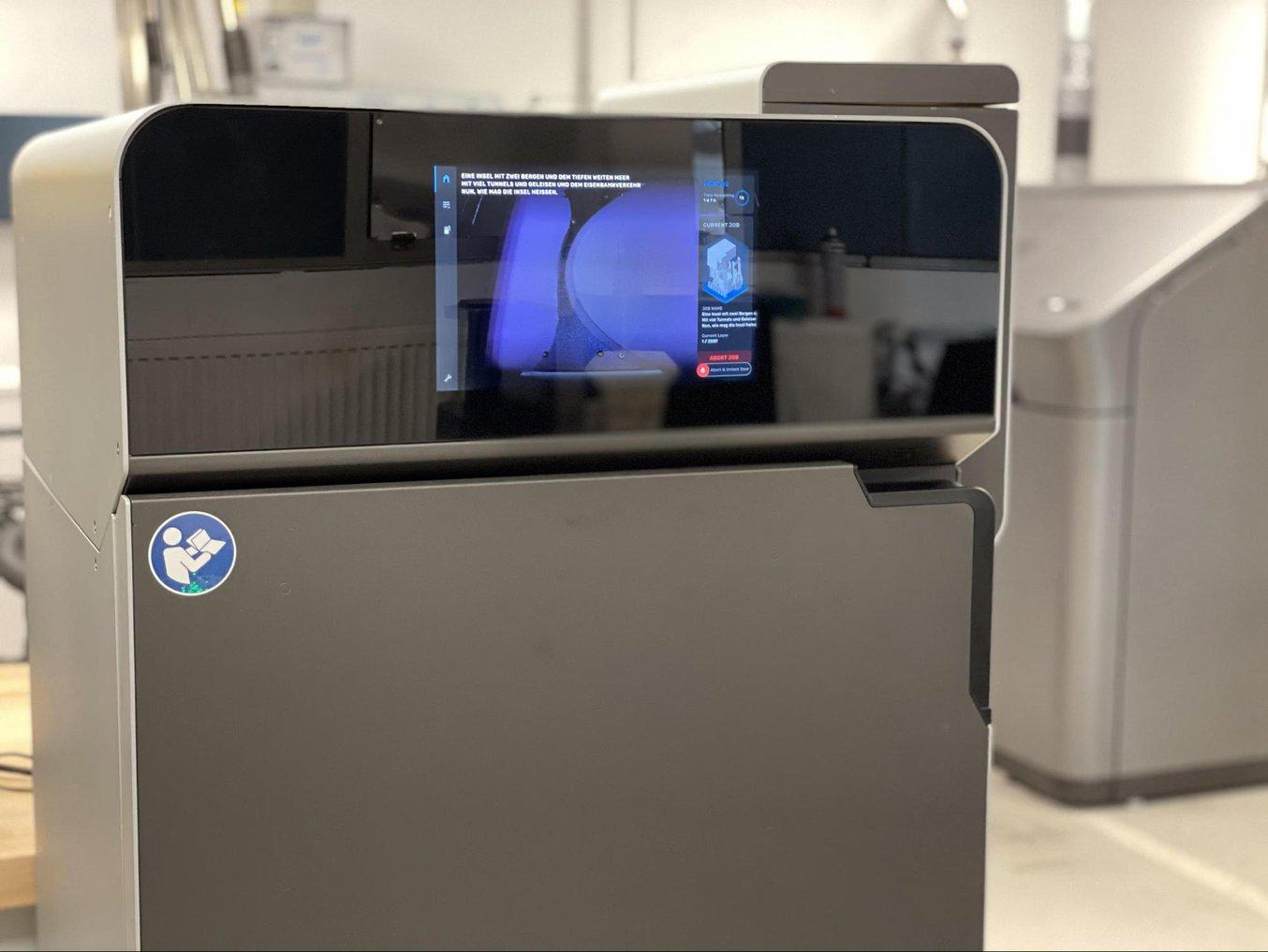
El centro de fabricación aditiva de Brose está equipado con casi todos los procesos de impresión 3D del mercado, incluida la incorporación más reciente, la Fuse 1.
Preparar y poner en marcha una máquina más grande puede llegar a requerir una semana, pero a Kleylein el proceso de preparación de la Fuse 1 le resultó sencillo.
"Es muy fácil prepararla. Si se tiene una sala cerrada con aire acondicionado, básicamente está todo listo. No requiere mucho espacio, lo que es muy positivo. Y no requiere ninguna calibración significativa; todo lo que hace falta es asegurarse de que permanece nivelada. Se enchufa, se inicia el proceso de configuración y se realiza la impresión en el mismo día de la entrega", nos dijo Kleylein.
"La curva de aprendizaje es sencilla. Es probable que tu primera impresión ya sea un éxito. Y después, puedes empezar a ajustar y a conocer en profundidad la máquina".
Christian Kleylein
"Hemos probado la Fuse muy a fondo. Hemos estado imprimiendo muchas de las piezas con el grosor mínimo y también con diseños muy largos y delgados. Al realizar ensayos con las piezas, vimos que incluso cuando las dimensiones de las mismas no eran las correctas, la desviación se producía siempre de la misma forma. Por eso, una vez que se ha optimizado el proceso, al final se obtienen piezas con una gran precisión dimensional", nos contó Kleylein.
El equipo ha realizado muchas impresiones en la Fuse 1 para poner a prueba sus límites, desde impresiones cortas de unas 12 horas a cámaras de impresión totalmente llenas con más de 1000 piezas pequeñas que tardaron cuatro días.
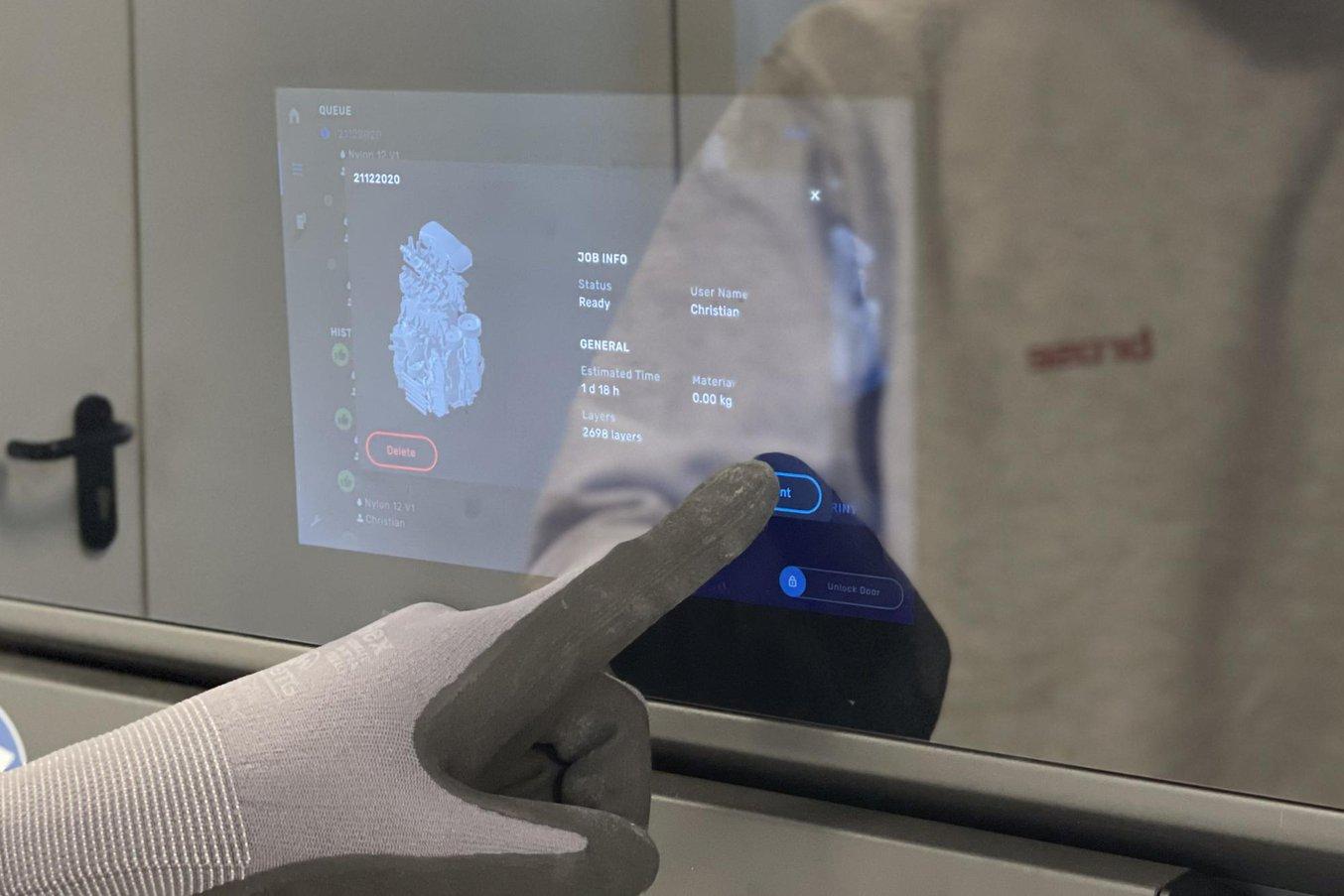
El sinterizado selectivo por láser no necesita estructuras de soporte porque el polvo sin sinterizar rodea las piezas durante la impresión. Es posible disponer múltiples piezas para que estén juntas durante la impresión y maximizar el espacio de impresión disponible.
"El acabado de la superficie es muy bonito y liso. Se ven muy pocas capas, de modo que se pueden usar las piezas justo después de sacarlas de la impresora y rociarlas con aire comprimido para quitarles el poco polvo que quede. Se pueden imprimir detalles muy finos. Por ejemplo, si se imprimen engranajes, se obtienen piezas redondas muy buenas", nos dijo Kleylein.
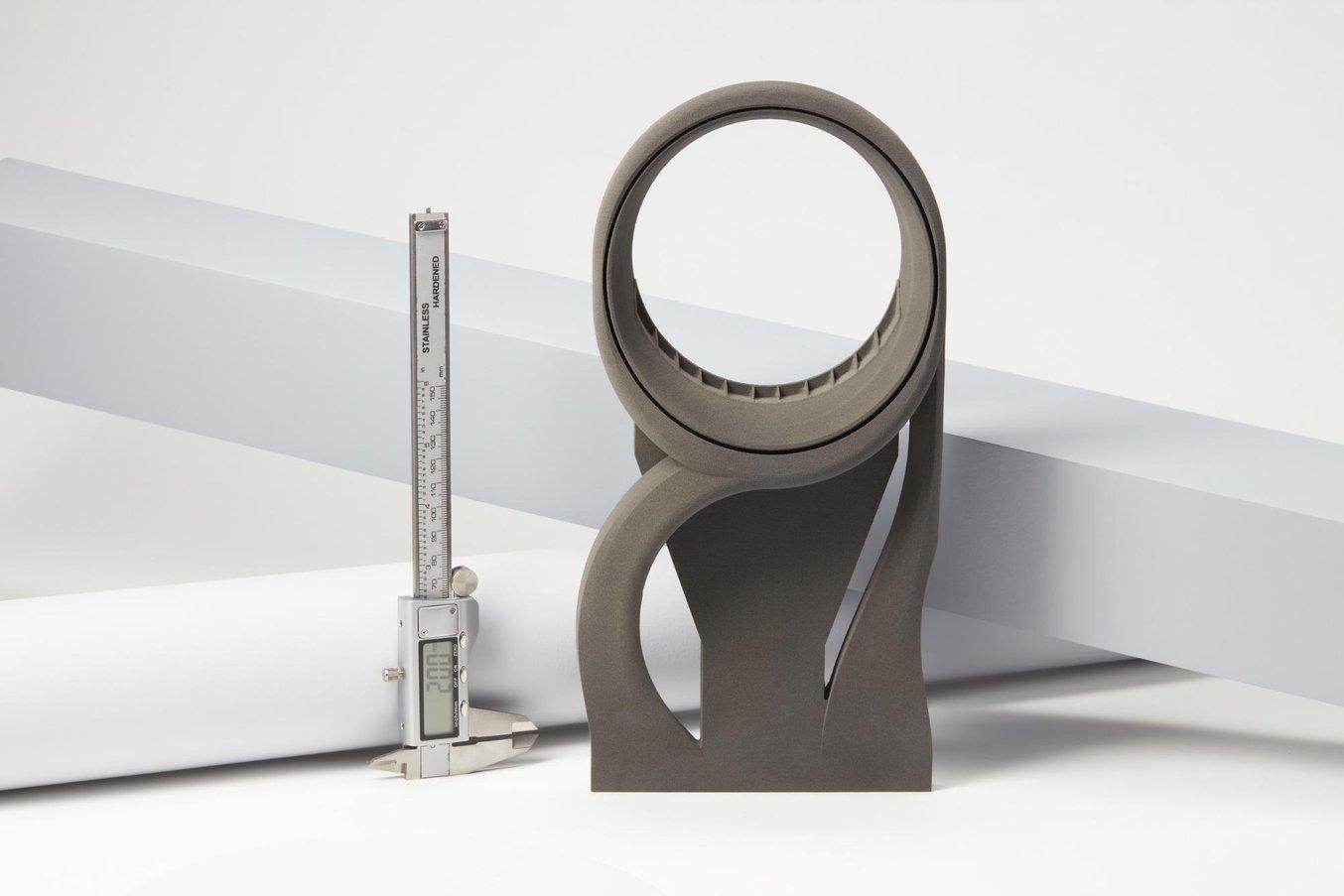
Un dispositivo de testeo de final de línea para máquinas de Brose durante el montaje.
Con la Fuse 1, Formlabs pretende eliminar la diferencia entre las impresoras SLS industriales tradicionales e impresoras de formato más pequeño y bajo coste, ofreciendo una alta calidad en un espacio reducido y un proceso de trabajo completo y simplificado por un precio menor que el de los sistemas de SLS industriales tradicionales.
"Es más comparable a las impresoras industriales que a una de las máquinas de escritorio. Ya que hay láseres de fibra, Formlabs ha desarrollado su propio sistema de escáner óptimo y el rayo láser se desvía de la forma adecuada", dijo Kleylein.
"Es una máquina. No parece un juguete, sino que da la impresión de ser una herramienta de trabajo en condiciones. Si abres la puerta, parece industrial y todo funciona. En el equipo de testeo están muy contentos. Se puede usar en un entorno industrial con mucha facilidad".
Christian Kleylein
Cabría pensar que las impresoras grandes son más adecuadas para piezas automovilísticas, pero Kleylein descubrió que el volumen de impresión de la Fuse 1 es suficiente para la mayoría de los diseños.
"El 80 % de las piezas que imprimimos tienen más o menos el tamaño de un puño como mucho. Por eso, podemos imprimirlas todas con la Fuse 1. Hay algunas piezas que quedan en medio en cuanto a tamaño y el resto es bastante grande", nos dijo Kleylein.
"La velocidad de impresión es buena, probablemente irá más rápida después de la optimización. Pero como punto de partida, tienes una buena velocidad de impresión y el espacio de impresión adecuado para aplicaciones definidas", dijo Kleylein.
La Fuse 1 también viene con la Fuse Sift, una estación de posacabado todo en uno que combina la extracción de las piezas, la recuperación del polvo, el almacenamiento y la mezcla en un único dispositivo sin anclajes.
"Anteriormente, con determinadas máquinas, el equipo de posacabado era un extra. Eso es algo que la gente ha diseñado por su cuenta, incluso el mezclado. La Fuse Sift es un buen sistema integrado. Con todos esos ventiladores para extraer el polvo, el equipo restrictivo de seguridad personal se puede reducir al mínimo. Filtra el polvo, por lo que todo lo que sea demasiado grande para pasar por el tamiz se puede recoger para reciclarlo. El polvo se mezcla aquí y tienes la libertad de definir tu propio índice de renovación. Si necesitas ciertas propiedades, se puede imprimir con un 100 % de polvo nuevo o con un 100 % de polvo usado. "Se coloca en el mezclador y el polvo queda bien dispersado", dijo Kleylein.
Kleylein comprobó que producir piezas de SLS con la Fuse 1 suele ser un proceso poco intensivo, que requiere solo un tiempo y esfuerzo limitados para preparar la nueva impresión, realizar el mantenimiento de la impresora y posacabar las piezas.
"Se puede situar en un taller pequeño, para tener a una persona que dedique solo una cuarta parte de su tiempo a dirigir el taller. El software gratuito es bueno y el proceso de impresión es comparable al de las impresoras grandes, por lo que es rápido de preparar", afirmó Kleylein.
"Es sencillo y está muy bien pensado. Se puede reiniciar la impresora en menos de 30 minutos".
Christian Kleylein
"Es una de esas máquinas que tiene una gran capacidad para trabajar en paralelo con otras. Es muy planificable y podemos mantenerla en marcha de forma continua. Poder imprimir las 24 horas es una gran ventaja. No tenemos tiempo de inactividad, solo lo hay si la impresora no está lo bastante llena y se detiene en el fin de semana, "dijo Kleylein.
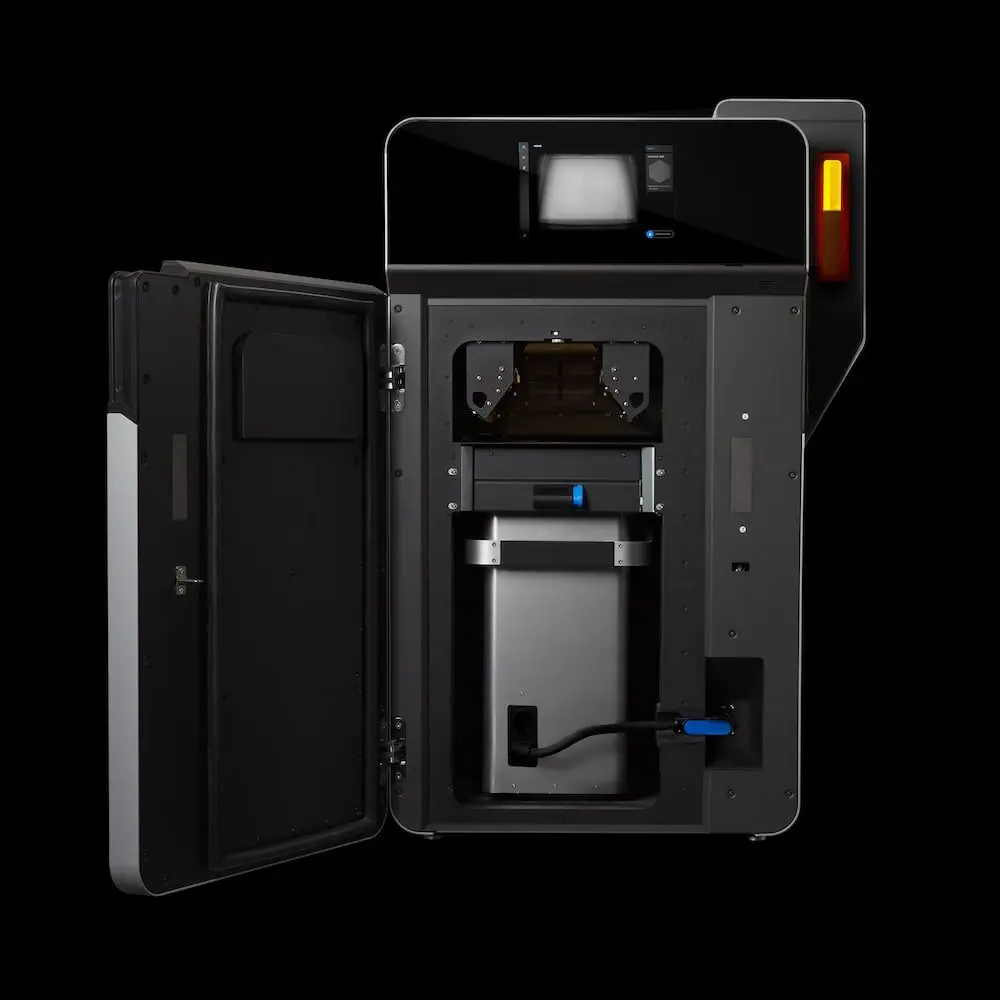
Demostración de producto de la Fuse 1
Ve nuestra demostración del producto para aprender más sobre el funcionamiento de la Fuse 1 y la impresión 3D SLS de la mano de expertos de Formlabs.
SLS para aplicaciones de uso final: Recambios y piezas para productos de fin de vida útil
Para empezar, Brose planea utilizar la Fuse 1 para crear prototipos funcionales que se beneficien de la producción rápida y del material que se usa, el Nylon 12, que ofrece propiedades parecidas a las de sus actuales materiales de producción. Sin embargo, el equipo de Kleylein ya está validando piezas y creando casos para las primeras aplicaciones de uso final. Los principales candidatos para ello son piezas de recambio y piezas para productos de fin de vida útil.
Aunque un modelo de vehículo deje de fabricarse, los proveedores automovilísticos siguen teniendo la obligación de proporcionar piezas de recambio. Antes, esto suponía calcular cuantos recambios serían necesarios, moldearlos todos por inyección y almacenarlos.
"Eso es un gran desperdicio de recursos, de espacio y de dinero. Si imprimimos en 3D, no necesitamos conservar los moldes de inyección y las piezas durante los próximos 15 años. Hay mucha demanda de recambios y piezas de fin de vida útil, porque los productos siempre se acaban y tenemos muchas piezas de plástico moldeadas por inyección. Si las apilamos bien y nos aseguramos de que las impresiones tengan una densidad de piezas muy alta, el proceso pasa a ser rentable", dijo Kleylein.
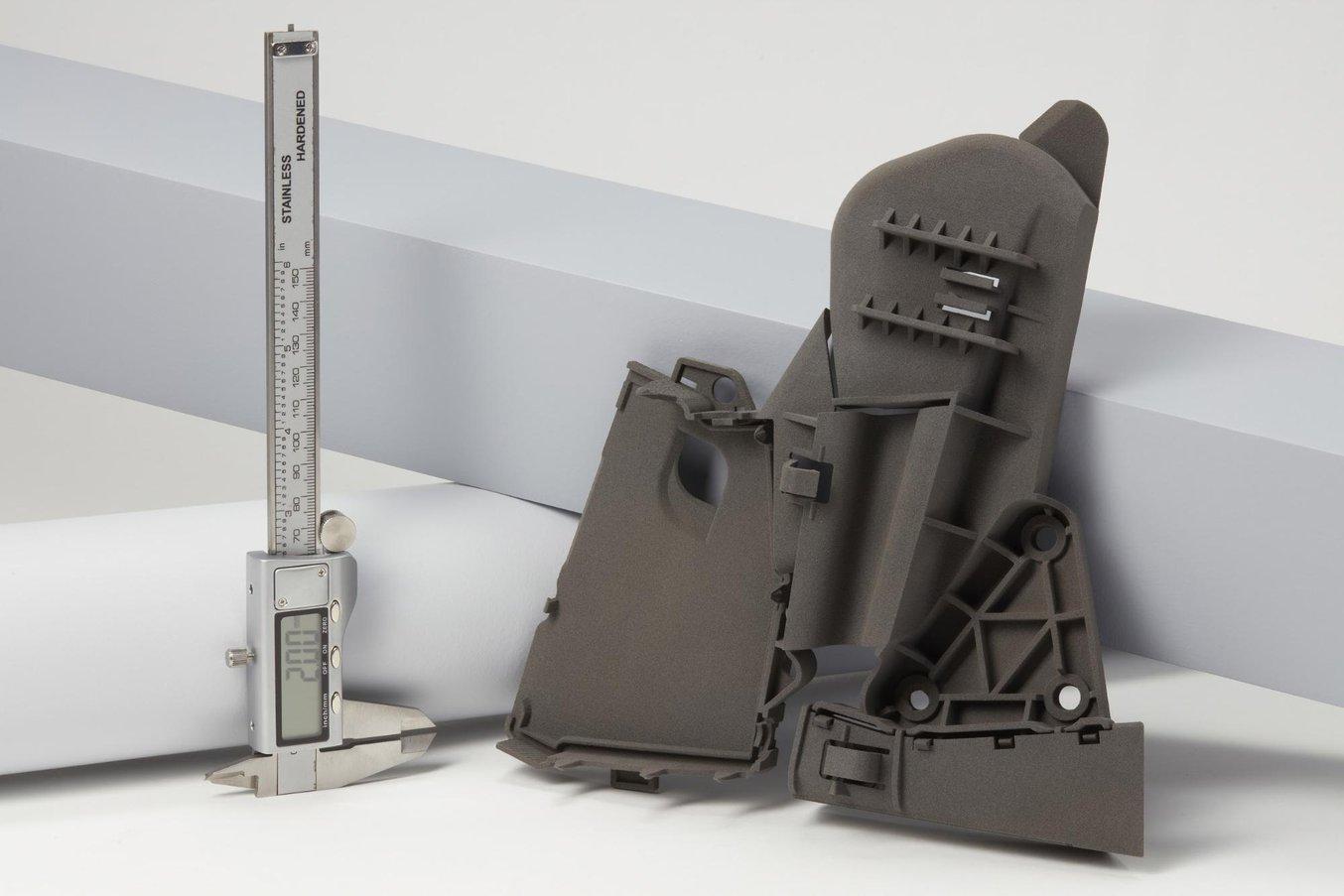
Un recambio de módulo de la manija de una puerta que tradicionalmente se moldea por inyección.
"En el sector de la automoción es importante ofrecer la máxima calidad posible al mejor precio posible. Actualmente, cualquier número de piezas inferior a 10 000 al año se podría imprimir mediante SLS".
Christian Kleylein
El SLS es una tecnología ideal para la producción en varios aspectos:
-
Puede crear piezas de alta calidad con propiedades similares a las de las piezas moldeadas por inyección.
-
Se puede incorporar en un entorno de producción.
-
Se trata de uno de los procesos de fabricación aditiva menos derrochadores y el más limpio, algo cada vez más importante para la fabricación.
"Se pueden usar polímeros técnicos, de modo que se pueden imprimir piezas técnicas y no se necesitan soportes. Además, el posacabado es muy limpio, porque la mayoría del polvo se quita de la pieza antes de aplicar el aire comprimido o el granallado", dijo Kleylein.
"Algunos de los clientes de Brose se muestran muy receptivos y la idea les gusta, porque intentamos imprimir sin que haya prácticamente derroche. Podemos reutilizar el polvo y no hay que tirarlo. Tampoco hay otras sustancias químicas que haya que reciclar. Para finales del año que viene, esperamos que todas nuestras máquinas funcionen con cero desperdicios", dijo Kleylein.
El futuro del SLS en la producción en serie
Por supuesto, la meta definitiva es usar el SLS para fabricar piezas de producción en serie para la próxima generación de productos automovilísticos, que Christian cree que llegarán en un futuro próximo.
"Ahora se pueden crear prototipos y recambios. Actualmente, si tenemos en cuenta los avances técnicos, veo factible la producción en serie en cuatro o cinco años".
Christian Kleylein
Para llegar a ese punto, deben producirse dos cambios clave: considerar la fabricación aditiva durante el desarrollo de productos desde la fase de diseño y reducir más el coste de los materiales y las máquinas.
"El mayor obstáculo es que el diseñador de productos sepa lo que puede hacer con la impresión 3D y tome la decisión de imprimir en 3D la pieza. Esto nunca va a ser rentable con componentes que se han diseñado para el moldeo por inyección. Hay que diseñar expresamente para el proceso", afirmó Kleylein.
"En el fondo, depende de cuántas piezas se planee imprimir y de la eficiencia de los sistemas de fabricación tradicionales. Cuando la propuesta de valor sea adecuada, produciremos una pieza con el sistema de producción más eficiente que haya. No vamos a hacer que la impresión 3D sea obligatoria para un producto, pero si es la mejor forma de producir la pieza, la imprimiremos", dijo Kleylein.
Al facilitar el acceso a la impresión 3D SLS, la Fuse 1 tendrá un papel clave para potenciar este paso hacia la producción. Brose ya tiene planes para seguir expandiendo rápidamente sus capacidades de impresión 3D. Su segundo taller de fabricación aditiva de plásticos se está construyendo en EE. UU. y también recibirá pronto su primera Fuse 1.
"Todavía tenemos muchos grandes desafíos por delante, pero en lo que respecta a la Fuse 1, sabemos que contamos con un producto muy potente y con un precio muy competitivo".
Christian Kleylein