Restor3d hat es sich zur Aufgabe gemacht, Chirurg*innen und Gesundheitsdienstleister dabei zu unterstützen, den menschlichen Körper zu reparieren und zu rekonstruieren. Der Lösungsansatz des Unternehmens liegt in der additiven Fertigung, die aufgrund ihrer Designfreiheit und Erschwinglichkeit das Potenzial hat, die herkömmlichen Märkte für Medizintechnik umzukrempeln.
Das Team von restor3d treibt Innovationen in der Präzisionschirurgie voran, denn es verändert die Art und Weise, wie Implantate, chirurgische Instrumente und Modelle für die Operationsplanung entwickelt und genutzt werden. Traditionell werden solche Instrumente nur schleppend weiterentwickelt, gehen mit erheblichen Vorabkosten einher und führen oft zu Komplikationen im chirurgischen Arbeitsprozess. Um die Bereitstellung chirurgischer Behandlungen drastisch zu verbessern, stützt sich restor3d auf die additive Fertigung und stellt operationsspezifische und häufig auch patientenspezifische Metallimplantate und Polymerinstrumente mithilfe von 3D-Druckern her.
Mit einer Produktionslinie bestehend aus über 25 3D-Druckern von Formlabs druckt restor3d bereits die nächste Generation chirurgischer Instrumente. Ihre Produkte bringen folgenden Nutzen:
- Sie ersetzen große, kostspielige OP-Trays durch operationsspezifische Einweginstrumente.
- Sie senken die Lieferketten- und Sterilisationskosten für Krankenhäuser drastisch.
- Sie verringern den Bedarf an intraoperativen Navigationssystemen durch patientenspezifische Instrumente.
Erfahren Sie im folgenden Beitrag vom Team von restor3d und den Chirurgen, die ihre Produkte nutzen, wie der 3D-Druck die Entwicklung erschwinglicher und voll personalisierter Medizinprodukte möglich macht.
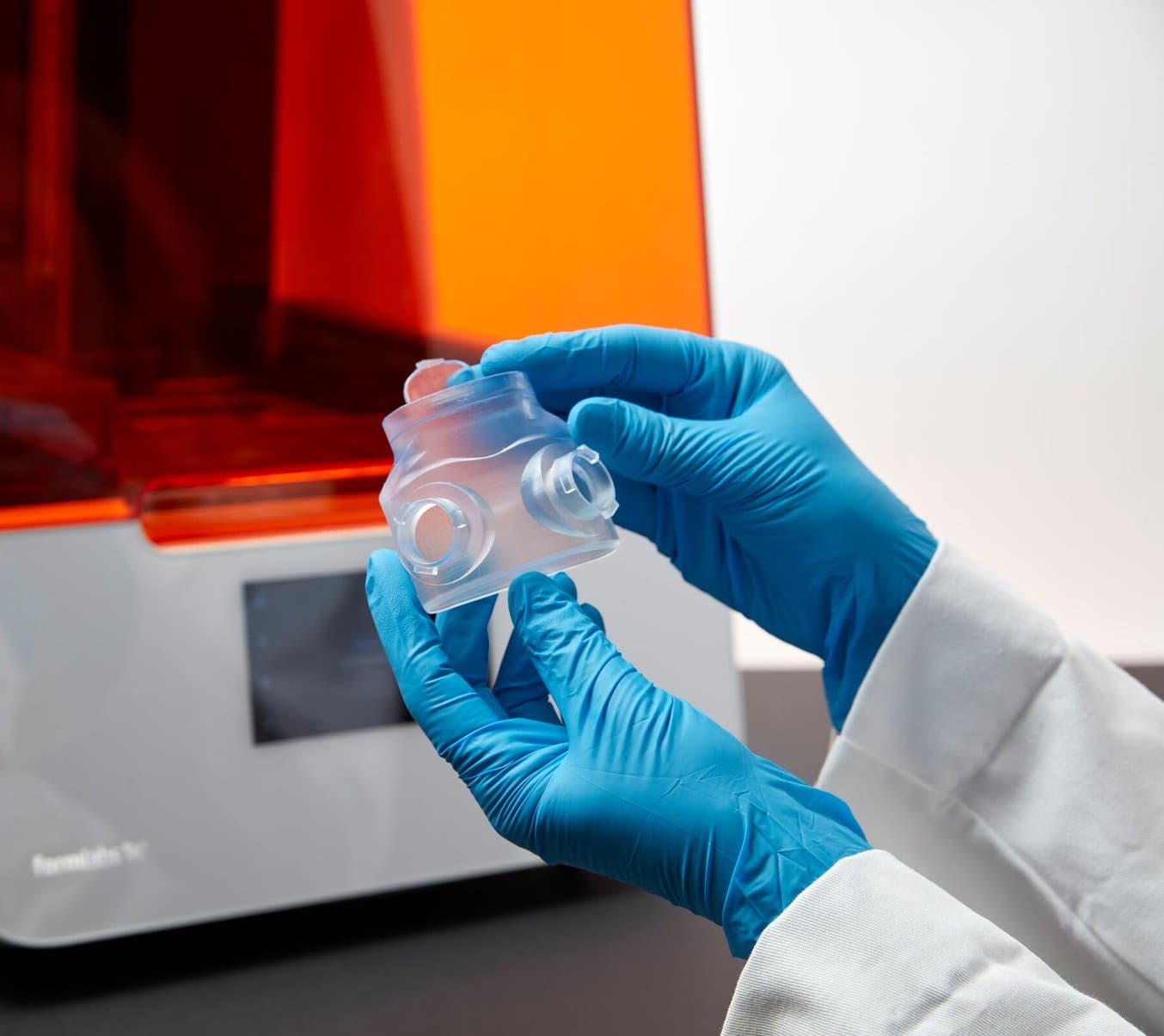
Nachgewiesene Vorteile der additiven Fertigung bei führenden Medizintechnikunternehmen
Erfahren Sie, wie Hersteller von Medizinprodukten die additive Fertigung statt konventioneller Prozesse einsetzen, in einer Podiumsdiskussion mit Enovis Surgical und restor3d.
Neue Horizonte auf dem Gebiet chirurgischer Instrumente
Restor3d besteht aus einem Team hochqualifizierter Fachleute der Bereiche Biomedizin und Materialwissenschaften, das sich zunächst auf 3D-gedruckte Implantate für Operationen an der Halswirbelsäule konzentrierte. Bei der Entwicklung dieser neuen Implantate war das Team mit einem immer wiederkehrenden Engpass konfrontiert: traditionell hergestellte Instrumentensysteme aus Edelstahl.
Cambre Kelly, Chief Technology Officer, erklärte die Situation folgendermaßen: „Wir waren dabei, ein innovatives Implantat zu entwickeln, dessen spezifische Merkmale sich nur mit 3D-Druck umsetzen lassen, aber wir erwarteten von Chirurgen, dieses Implantat mithilfe sehr konventioneller Instrumente einzusetzen. Uns wurde also schnell klar, dass es für uns ein entscheidendes Herausstellungsmerkmal werden würde, neben der Innovation von Implantaten auch das Angebot an Instrumenten weiterzuentwickeln.“
Allerdings machen die hohen Kosten herkömmlicher OP-Trays es für Krankenhäuser unattraktiv, Arbeitsprozesse zu individualisieren, ihren Ansatz zu überdenken oder neue Herangehensweisen zu testen.
„Traditionell werden Chirurgie-Kassetten normalerweise aus Edelstahl gefräst und kosten Beträge ab 50 000 € pro Kassette. Wenn man als Hersteller von Medizinprodukten in 10 Chirurgie-Kassetten für je 50 000 € investiert, ist man gezwungen, diese auch für eine sehr lange Zeit zu benutzen. Man wird nicht viel an den Designs iterieren, Kassetten entsorgen und von vorne beginnen oder vermeintlich kleine Details abändern wollen“, so Kelly.
Restor3d hat sich die Leistung der betriebsinternen additiven Fertigung zunutze gemacht und bietet jetzt Instrumente und dazu passende OP-Trays zu erschwinglichen Preisen an, damit Krankenhäuser agil handeln und Behandlungen kosteneffizient individualisieren können. Für die Herstellung operationsspezifischer Einweginstrumente brauchte es einen wahrhaft agilen Entwicklungsprozess, der auf noch nie dagewesene Weise eine Brücke zwischen chirurgischem Feedback und dem Produktentwicklungsteam schlug.
„Wir sind auf einzigartige Weise in der Lage, Produkte tatsächlich just-in-time zu liefern, da wir intern fertigen und Designs und Geometrien in kurzer Zeit anhand der Rückmeldungen von Praxistests justieren können. Durch den direkten 3D-Druck von Einweginstrumenten können wir unsere Designs sehr flexibel iterieren und überarbeiten“, berichtet Kelly.
Durch rekordschnelle Produktentwicklung den Weg für neue klinische Prozesse bereiten
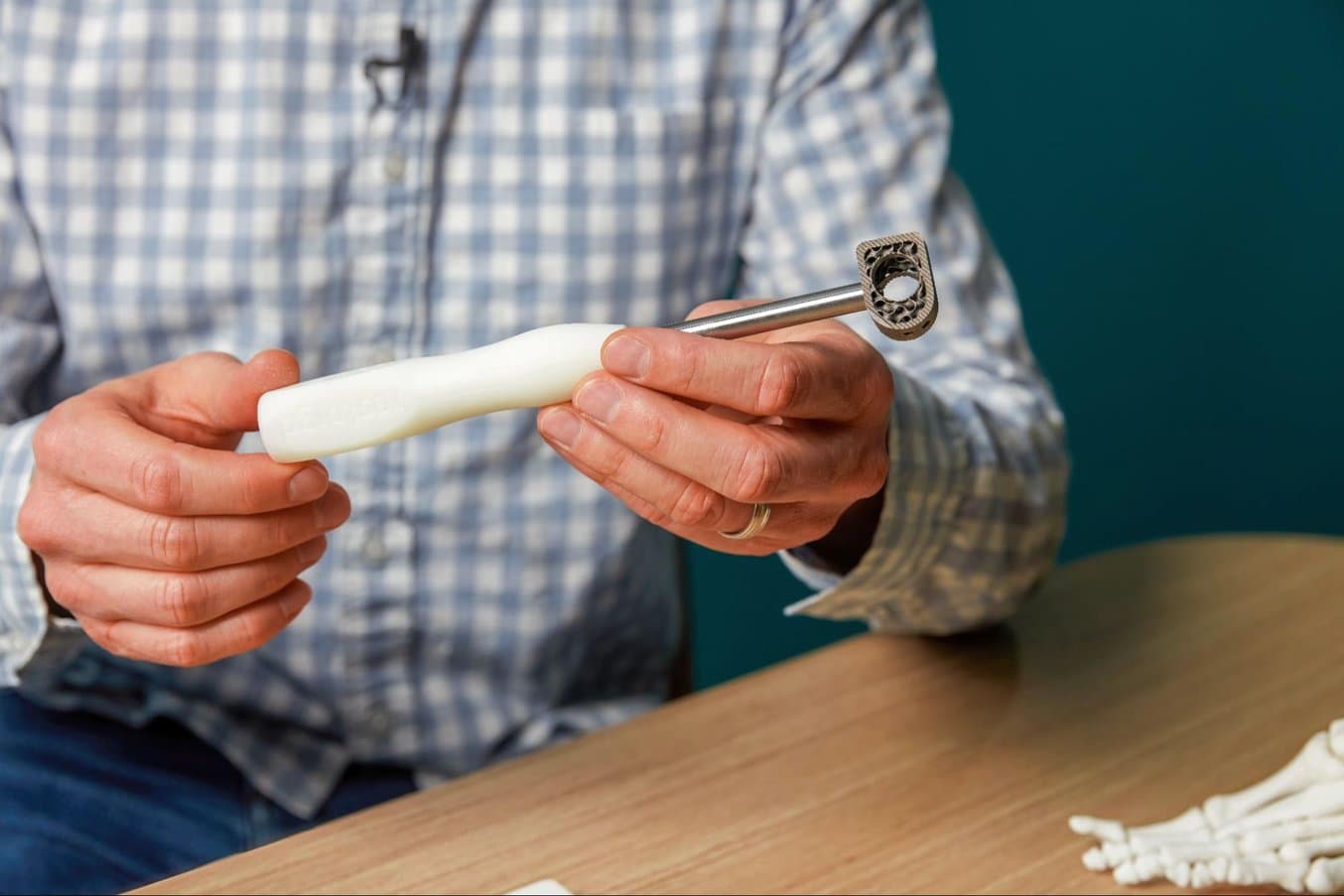
Die operationsspezifischen Einweginstrumente von restor3d kombinieren Metallkomponenten mit 3D-gedruckten Polymerteilen.
Nathan Evans, Senior Vice President der Produktentwicklung, erläutert uns: „Chirurgen arbeiten am liebsten mit der Ausrüstung, die sie aus ihrer Ausbildung kennen. Und wenn die 20 oder 30 Jahre zurückliegt, war diese Technologie damals womöglich nicht verfügbar. Wir beobachten einen echten Umschwung bei der Implementierung, wenn Chirurgen in Fallstudien von Kollegen die Ergebnisse sehen, die diese mit Technologien erzielen, die sie selbst noch nicht versucht haben, und entdecken, wie das einen Mehrwert, neue Ergebnisse, neue Ansätze oder klinische Prozesse möglich macht.“
Um die klinische Perspektive kennenzulernen, hat sich Formlabs mit Dr. Erik Westerlund unterhalten, einem orthopädischen Chirurgen und Fellowship-Teilnehmer, der auf die Wirbelsäule spezialisiert ist. Dr. Westerlund war von der ersten Generation von restor3d's System für die anteriore zervikale Diskektomie mit Fusion (ACDF) stark beeindruckt und erklärt: „Der bisherige Entwicklungsprozess ist seit 20 Jahren unverändert. Ein Unternehmen hat ein neues Implantat und/oder Instrumentensystem. Das Unternehmen taucht auf, erstellt Prototypen und ein paar Tage oder Wochen später gibt es etwas zum Anschauen. Mehrere Wochen später entsteht dann ein Beta-Instrument. Aber restor3d bringt nicht in ein paar Wochen einen Prototyp hervor, sondern das echte Instrument innerhalb von ein paar Tagen. Für mich verändert das die Grenzen des Möglichen vollkommen.“
Er führt weiter aus: „Nicht nur die Implantate selbst sind wichtig, sondern auch die Implantationstechnik. Das macht einen erfolgreichen Eingriff aus. Der neue Ansatz von restor3d ist ein systemischer Ansatz. Mit additiver Fertigung gibt es eine integrierte Parität von Implantat und Instrument – und die Möglichkeit, beide zu verändern, um den Patienten die besten Ergebnisse zu liefern.“
Die direkte Zusammenarbeit mit chirurgischen Fachleuten ist für restor3d ein unerlässlicher Bestandteil der Entwicklung seiner Medizinprodukte geworden. In Fachgebieten wir der orthopädischen Onkologie ist jede Operation ein ganz individueller Eingriff. Anders als bei herkömmlichen orthopädischen OPs, bei denen Patient*innen mit bestehenden Implantaten behandelt werden, verursacht der Krebs hier jeweils individuelle, spezifische Knochenschäden. Um spezialisierte Instrumente für den vollständigen Eingriff bereitzustellen, muss restor3d von Anfang bis Ende eng mit den Chirurgieteams zusammenarbeiten.
„Wir erhalten ständig Rückmeldungen von den Chirurgen. Durch den 3D-Druck ist es uns möglich, das Design schnell zu iterieren, um das Feedback der Chirurgen einzuarbeiten und in kurzer Zeit eine neue Lösung zu liefern.“
Nathan Evans, Senior Vice President der Produktentwicklung, restor3d
Ben Wesorick, Vice President der patientenspezifischen Entwicklung, fügt hinzu: „Wir fangen mit einem CT-Scan an, manchmal auch mit dem Röntgen, und gehen von den Scans über ein Planungsmeeting mit einem Arzt zum Design über und dann bis zur OP. Es ist also ein allumfassender Prozess, angefangen von der Erfassung der Patientenanatomie, und wir arbeiten durchgehend mit Chirurgen zusammen.“
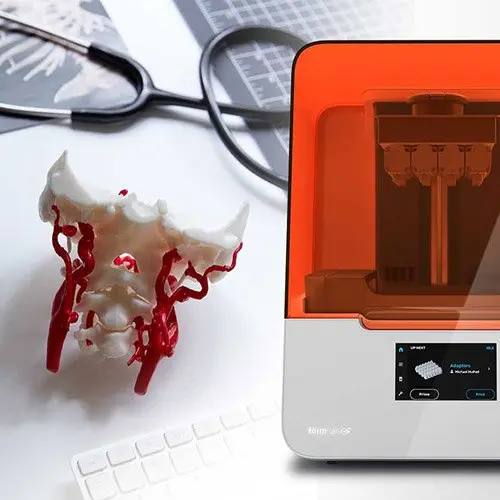
Einführung in den medizinischen 3D-Druck
Nehmen Sie an unserer Einführung teil, um bewährte Praktiken für den medizinischen 3D-Druck kennenzulernen. Außerdem stellen wir Ihnen das neueste Ecosystem von Formlabs Medical vor, einschließlich mehrerer neuer medizinisch geprüfter Produkte.
Planung und Hilfsmittel für die perfekte OP
Die Planungsphase ist bei komplizierten Operationen ein entscheidender Schritt. Sie macht einen bedeutenden Teil des Mehrwerts aus, den restor3d chirurgischem Fachpersonal liefert, und beinhaltet üblicherweise die Erstellung von Anatomiemodellen und patientenspezifischen Schneidführungen.
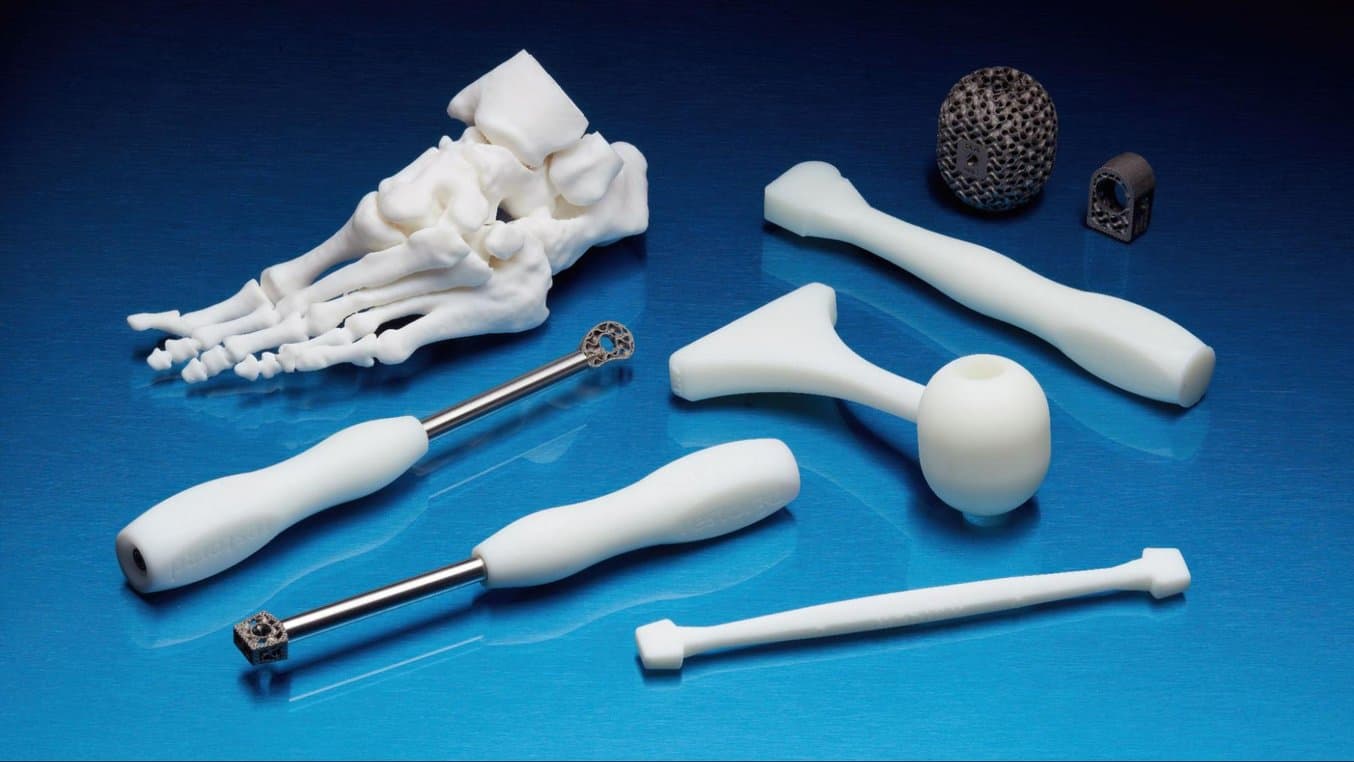
Abgesehen von Implantaten und operationsspezifischen Instrumenten bietet restor3d auch Anatomiemodelle und patientenspezifische Schneidführungen an, die die OP-Planung unterstützen.
Selbst für häufige Eingriffe, die das Behandlungsteam schon Tausende Male durchgeführt hat, ist die Planung essenziell. Jede Patientenanatomie ist einzigartig, und auch wenn das Implantat selbst perfekt entworfen ist, kann sich dessen Einsetzen in den Körper völlig individuell gestalten. Dies ist dem Team von restor3d bewusst. Deshalb bietet es zusätzliche Komponenten für die Planungsphase an, um eine erfolgreiche Operation zu gewährleisten. „Wir können schön konturierte Implantate fertigen, die dafür bestimmt sind, in bestimmte Löcher zu passen, aber wenn sich diese Löcher in der Praxis nicht an der richtigen Stelle befinden, dann haben wir das Endziel nicht erreicht und den Plan nicht umgesetzt. Deswegen sind die Schneidvorrichtungen und Instrumente, die wir anbieten, der Schlüssel dazu, dass alles funktioniert“, so Wesorick.
Um den Einfluss von restor3d auf den Planungsprozess zu überblicken, haben wir uns mit Will Edward unterhalten, MD, DVM und orthopädischer Onkologe bei Duke Health. Als wir ihn fragten, was das Besondere an der präoperativen Planung mit restor3d ist, erklärte er: „Das Schöne ist, dass restor3d uns nicht nur anatomische Modelle liefert, sondern auch das Implantat, die Schneidführungen, eigentlich alle Instrumenten, von Führungshülsen für unsere Bohraufsätze bis hin zu Schraubenlöchern.“
Dieses Komplettpaket an Planungshilfsmitteln macht es chirurgischen Teams möglich, sich auf einen Eingriff vorzubereiten und ihn sogar an anatomischen Modellen zu proben, bevor sie direkt am Patienten arbeiten. Eine derartige präoperative Vorbereitung verkürzt die Operationsdauer und steigert das Selbstvertrauen der Behandelnden, was bessere Ergebnisse und eine schnellere Genesung zur Folge hat.
„Seitdem ich mit restor3d arbeite, nutze ich unser intraoperatives Navigationssystem viel weniger. Das liegt daran, dass die Schneidführungen so gut sind. Computer-Navigation während der OP ist eine tolle Sache. Es ist faszinierend. Medizinstudenten lieben es, aber es verlängert auch die Dauer der Behandlung um einiges. Außerdem setzt es den Patienten erheblich mehr Strahlung aus. Wenn wir dasselbe Ergebnis also mit gut entwickelten Schneidführungen erzielen können, profitieren alle davon.“
Will Edward, MD, DVM und orthopädischer Onkologe bei Duke Health
Wie Formlabs den Ansatz von restor3d unterstützt
Bei der Herstellung derart detaillierter und individualisierter Sets von Hilfsmitteln für die präoperative Planung stützt sich restor3d auf seine betriebsinterne Flotte von 3D-Druckern. Die Vielfalt der verfügbaren Materialien, die Genauigkeit der Drucker und die Möglichkeit, nach Bedarf auf die Anforderungen von Chirurg*innen einzugehen, machen es möglich, ein so individuelles Produkt in so kurzer Zeit fertigzustellen.
„In den meisten unserer Fälle stellen wir ein bis drei Metallimplantate und sechs bis acht Formlabs-Komponenten bereit. Die mit Formlabs gefertigten Instrumente sind also ein wirklich zentraler Bestandteil zum Abschluss eines Falls und machen einen Großteil unserer Tätigkeit aus.“
Ben Wesorick, Vice President der patientenspezifischen Entwicklung, restor3d
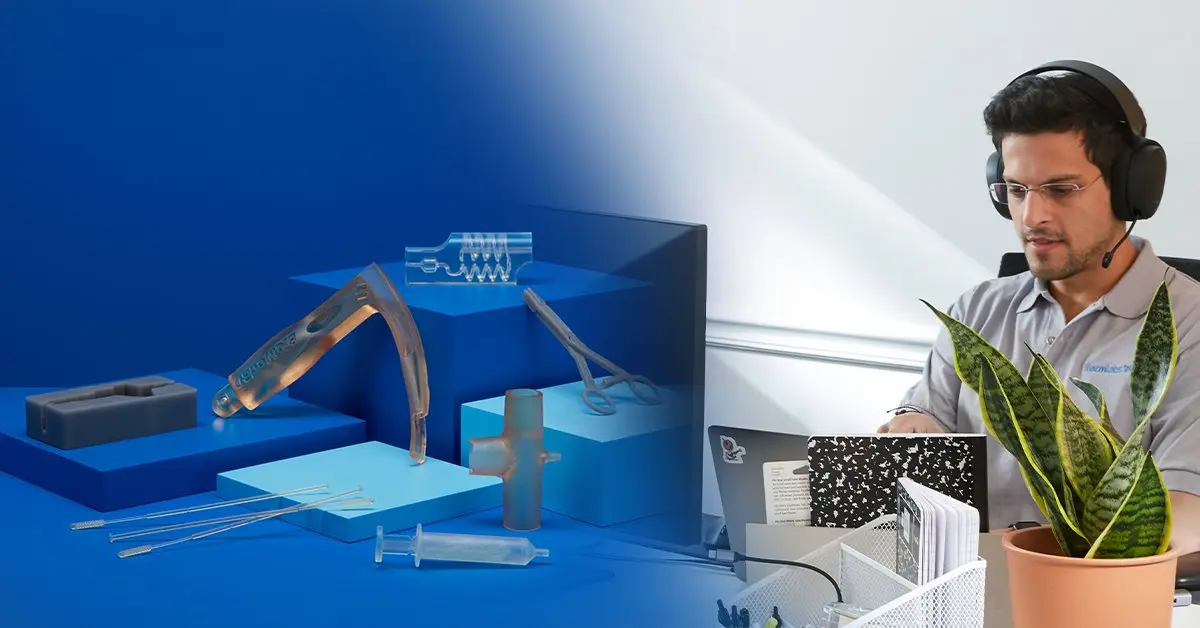
Kontakt zum Vertriebsteam von Formlabs Medical
Ob Sie patientenspezifische chirurgische Instrumente erstellen möchten oder Prototypen kardiologischer Medizinprodukte anfertigen: Wir stehen Ihnen zur Seite. Hinter Formlabs Medical steht ein engagiertes Spezialistenteam, das Sie und Ihr Unternehmen bei Bedarf mit professioneller Hilfe unterstützt.
Schnell, genau und leicht skalierbar
Restor3d verfügt über eine beeindruckende Flotte von Metall-3D-Druckern, die Werkzeug und Implantate aus Kobalt-, Chrom- und Titanlegierungen produzieren. Neben den Metall-Druckern, die ganze Räume einnehmen, beherbergt das Unternehmen auch eine Druckfarm mit Geräten der Form-Serie und anderen Polymer-Druckern.
Elena Tercheria, Leiterin der additiven Fertigung, ist auf die Produktion von Polymerteilen spezialisiert. Sie und ihr Team stützen sich bei 90 % ihrer Polymerteile auf ihre Flotte von Formlabs-Druckern, sowohl für Einweginstrumente als auch patientenspezifische, maßgefertigte Teile. Einige davon werden aus einem speziell formulierten Kunstharz gedruckt, dass für die OP-Teams auf Röntgenaufnahmen sichtbar ist.
Als Tercherias und ihr Team den Form 4B integrierten, erkannten sie sehr bald, dass der Drucker ihre Arbeitsabläufe umkrempeln würde, besonders in Bezug auf die Druckgeschwindigkeit. Tercheria erklärt: „Die Geschwindigkeit des Form 4B ist vergleichbar oder sogar schneller als industrielle DLP-Drucker.“
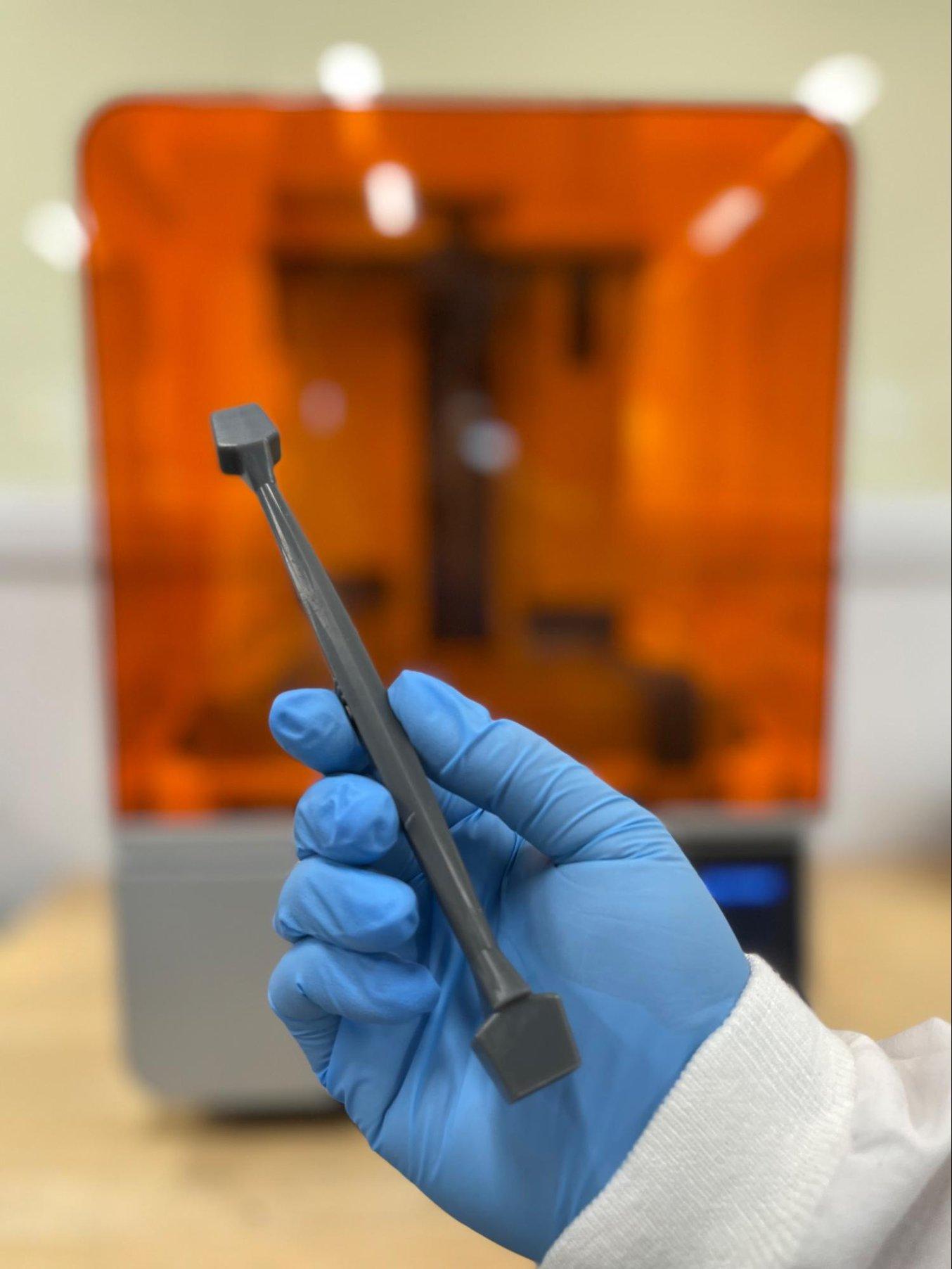
Tercherias Team stellte fest, dass auf dem Form 4B gedruckte Teile glatte Seitenwände aufweisen, sodass sie weniger nachbearbeitet werden müssen.
Bei der Zusammenarbeit mit chirurgischen Fachkräften, die sich auf eine OP vorbereiten, ist Agilität entscheidend. „Manchmal gehen Teile vor dem Versand kaputt. Manchmal muss man zusätzliche Teile versenden. Manchmal fordert ein Kunde einfach ein Neudesign des Teils. Die beschleunigte Druckzeit [des Form 4B] wird uns helfen, viel agiler auf solche Situationen zu reagieren.“ Dass einige Drucke um Stunden schneller fertig werden, kann den Unterschied zwischen Druck und Versand innerhalb eines Tages und Druckvorgängen über Nacht bedeuten. Indem Druckaufträge um bis zu 2 Stunden beschleunigt werden, werden zwei Druckaufträge in derselben Zeit gedruckt, die andere Drucker für einen benötigen, was die Kapazitäten letztendlich verdoppelt.
Tercherias Team ist begeistert von der verbesserten Genauigkeit der Zeitanzeige auf dem Form 4B. „Es mag nichtig erscheinen, aber zu wissen, wie lange ein Druck dauert, gibt Arbeitskräfte für höherwertige Aufgaben frei. Zu sehen, wie der Drucker jede Schicht mischt und trotzdem eine drastische Verkürzung der Druckzeit erreicht, ist beeindruckend. Das ist für uns eine große Sache, denn so können wir zuverlässig planen und die Verfügbarkeit der Geräte voraussehen.“
Im Hinblick auf Geschwindigkeit ist die Dauer der Nachbearbeitung einer der zentralen Faktoren, die in die Durchlaufzeit einfließen. Druckteile aus dem Form 4B haben eine glatte Oberfläche und erfordern weniger Stützstrukturen. Daher ist nur minimale Nachbearbeitung erforderlich, was Zeit spart und die Produktionsgenauigkeit erhöht.
Die Verringerung von Stützstrukturen bedeutet, dass weniger Teile durch die Nachbearbeitung müssen, was Zeit und Ressourcen spart.
Die 3D-Drucker von Formlabs sind eine optimale Lösung für den einzigartigen Arbeitsprozess von restor3d, denn sie sind schnell, genau, einfach zu benutzen und bieten eine Vielzahl an Materialoptionen. Eine weitere Stärke ist die Möglichkeit, nach eigenem Ermessen zu skalieren und mit der Zeit weitere 3D-Drucker in die Flotte aufzunehmen. Der Plug-and-Play-Charakter der Form-Serie ermöglicht es restor3d, seine Fertigungskapazitäten mit steigender Nachfrage zu erweitern, anstatt im Vorfeld eine große Menge an Kapital investieren zu müssen, das sich erst nach langer Zeit rechnet. Zweitens erlaubt die Flexibilität, die sich aus der Verwendung derselben Geräte und desselben Materials während des Entwicklungsprozesses ergibt, die Geräte bei Bedarf in die Produktion zu überführen.
„Es sind fast keine Schichtlinien zu sehen. Die Seitenwände sehen extrem glatt aus – fast als wären sie nicht 3D-gedruckt.“
Elena Tercheria, Leiterin Additive Fertigung, restor3d
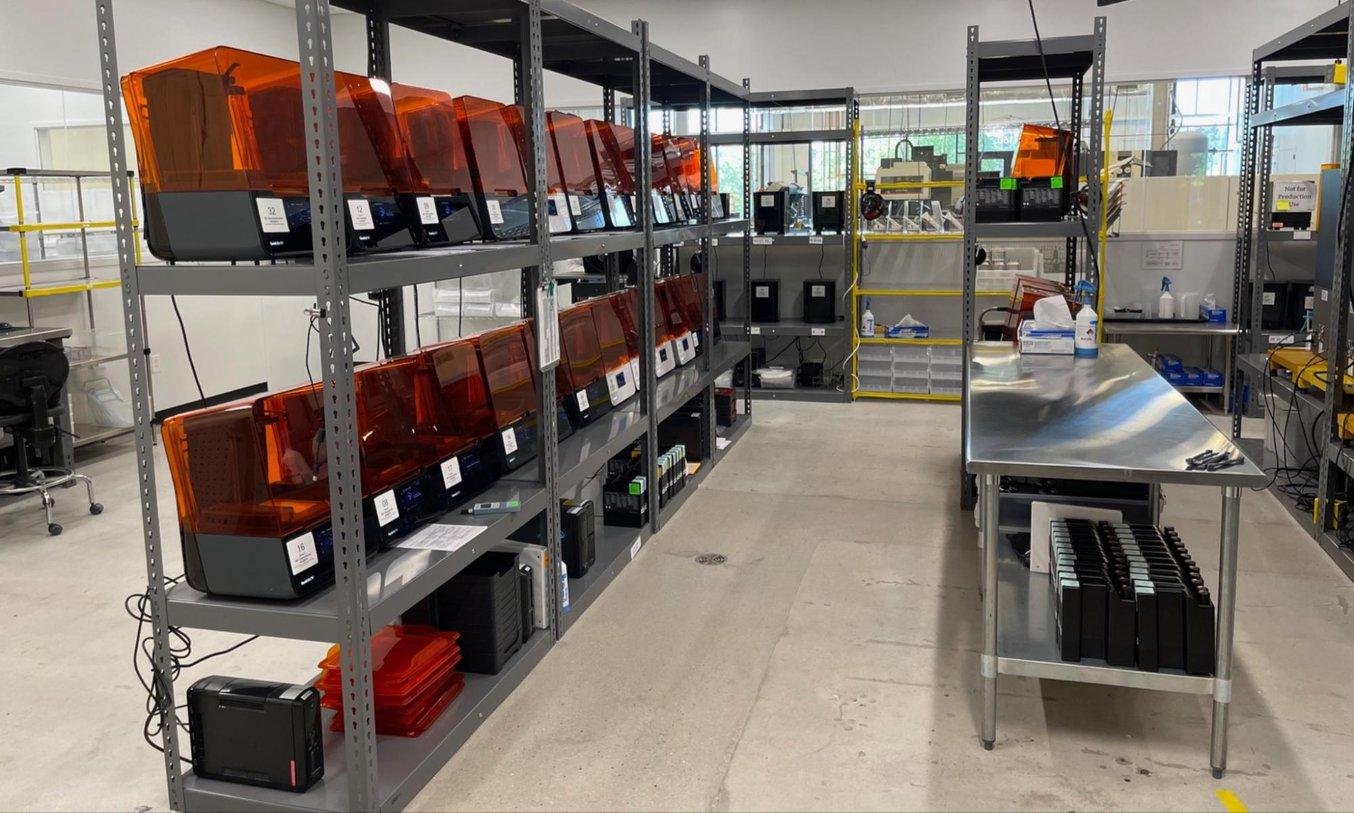
Restor3D betreibt eine Flotte von 28 3D-Druckern von Formlabs.
Kelly brachte es auf den Punkt: „Die beiden Gründe, warum wir bei Formlabs geblieben sind, sind die Produktionsflexibilität und die Möglichkeit der schrittweisen Skalierung. Die Investition in einen Formlabs-Drucker ist wesentlich geringer als die Investition einer halben Million Dollar für einen Metalldrucker. Somit können wir unsere Formlabs-Flotte im Laufe der Zeit schrittweise erweitern, und zwar auf eine nachhaltige Weise, die keine großen Vorabinvestitionen erfordert.“
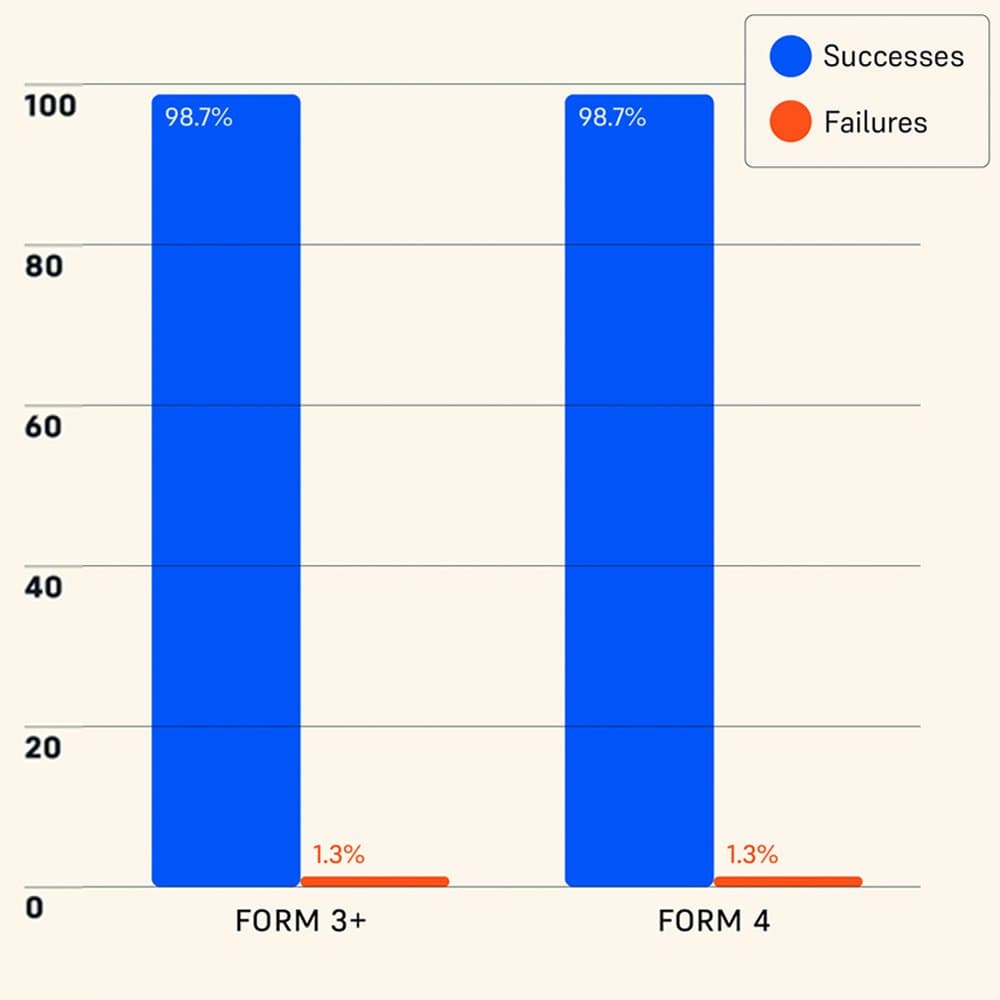
Zuverlässigkeit von Form 4 und anderen Kunstharz-3D-Druckern unabhängig getestet
Der Form 4 von Formlabs erreichte in einer Untersuchung eines unabhängigen, weltweit führenden Produkttesters eine Druckerfolgsrate von 98,7 %. Eine vollständige Beschreibung der Testmethode und die Ergebnisse finden Sie in unserem Whitepaper.
Leistungsstarke Materialien
Die chirurgischen Instrumente von restor3d kombinieren Metall- und Polymerteile und sollen die Instrumente aus Edelstahl ersetzen, die die Laufbahn zahlreicher Chirurg*innen bisher begleitet haben. Das Entwicklerteam wählt aus der verfügbaren Materialpalette ein passendes Polymer, das auch dem Gewindebohren standhält und im Anschluss an eine Sterilisierung durch Gammastrahlung oder Dampf in chirurgischen Eingriffen eingesetzt werden kann.
Formlabs bietet eine Bibliothek von über 30 Materialien, einschließlich zahlreicher biokompatibler Materialien für das Gesundheitswesen. Wesorick war von der Leistung der fortschrittlichen Kunstharze beeindruckt: „Dass wir die Resin-Materialien von Formlabs so gern mögen, liegt an ihren interoperativen Eigenschaften. Vor allem sind sie zäh. Wir können damit drucken, was wir wollen, ohne uns viele Gedanken um eine Verdünnung oder ein Brechen der Materialien zu machen. Tatsächlich haben wir die Erfahrung gemacht, dass sie bei Teilen wie Schlagkörpern, Schneidführungen und Bohrschablonen recht robust sind. Sie bieten Chirurgen also ein ziemlich gutes haptisches Feedback. Der andere Punkt, in dem diese Materialien sich für uns gut bewähren, ist ihre Flexibilität in Bezug auf das Design.“
Bei restor3d werden alle Instrumente und Implantate strengen Tests unterzogen, damit gewährleistet ist, dass die bereitgestellten Produkte der höchsten Qualität entsprechen und selbst in Umgebungen mit hoher Belastung verwendet werden können. Das Team führt Biege-, Stoß- und Drehmomentprüfungen und simulierte klinische Anwendungstests mit chirurgischen Fachleuten durch, um sicherzustellen, dass die Hilfsmittel den Anforderungen und Lasten im Operationssaal standhalten.
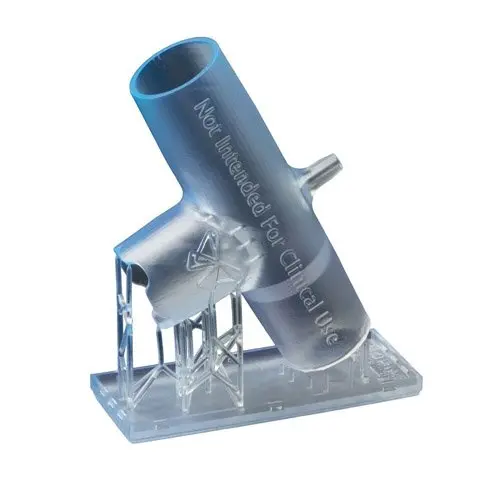
Kostenlosen Probedruck anfordern
Sehen und fühlen Sie die Qualität von Formlabs aus erster Hand. Wir senden Ihnen einen kostenlosen Probedruck an Ihren Arbeitsplatz.
Flexibles Design
Indem das Team von restor3d einige Komponenten aus Kunstharz (auch Resin genannt) 3D-druckt, kann es neue Ausrichtungen, Materialien und Designmerkmale ausprobieren.
„Was uns an den Formlabs-Druckern wirklich gefällt, ist die Flexibilität, die sie uns in Bezug auf das Design bieten. Unserer Erfahrung nach können wir die Anforderungen der Chirurgen mit Formlabs fast immer erfüllen, was bei einigen der anderen Drucksysteme, die wir nutzen, nicht der Fall ist“, so Wesorick.
Beim Design von Titan-Implantaten müssen zahlreiche Kriterien hinsichtlich Design for Additive Manufacturing (DfAM) beachtet werden, wie etwa die Ausrichtung der Platte und alle anderen Faktoren, die der 3D-Druck mit sich bringt.
„Verglichen mit dem Titan-3D-Druck ist Formlabs deutlich weniger eingeschränkt und lässt mehr Flexibilität zu. Ein Vorteil ist also: Wenn wir etwas nicht aus Metall herstellen können, dann ist die Wahrscheinlichkeit hoch, dass wir es aus Kunstharz bereitstellen und die geforderte Funktionalität erreichen können, dank der Flexibilität des Druckprozesses.“
Ben Wesorick, Vice President der patientenspezifischen Entwicklung
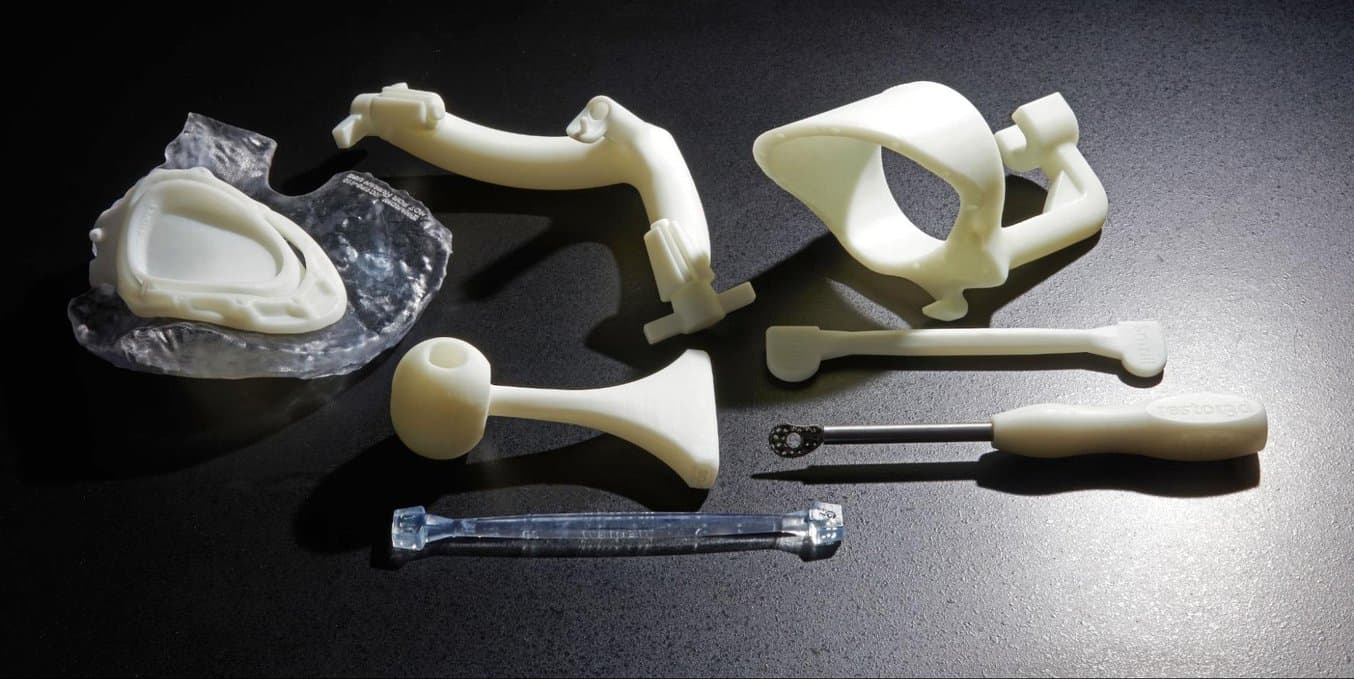
Dank der Gestaltungsfreiheit des Kunstharz-3D-Drucks ist restor3d in der Lage, komplexe neuartige Designs zu erstellen, wie etwa Rundschnitte oder sehr präzise geometrische Schnitte im Knochen, mit weniger Exposition und Dissektion.
Biokompatibel
Um die Kosten und die Markteinführungszeit weiter zu reduzieren, bietet Formlabs mehrere biokompatible SLA- und SLS-Materialien an, die sich für die Herstellung von Medizinprodukten eignen. Die BioMed-Kunstharze von Formlabs wurden für das Gesundheitswesen entwickelt als Materialien in medizinischer Qualität für eine breite Palette an Anwendungen, bei denen Leistung und Biokompatibilität entscheidend sind. Diese Materialien werden in unserer nach ISO 13485 zertifizierten Einrichtung hergestellt. Sie sind mit den gängigen Desinfektions- und Sterilisierungsmethoden kompatibel.
Evans erläutert die Vorteile der Kooperation mit einem Materialhersteller, der über ein robustes Qualitätssicherungssystem verfügt, folgendermaßen: „Wenn ein Zulieferer bereits Genehmigungs- und Prüfungsschritte für Biokompatibilität implementiert hat, zum Beispiel Prüfungen gemäß ISO 10993, ist das eine große Hilfe. Besonders für Startups in der Anfangsphase, die die extrem langen Durchlaufzeiten und Kosten vermeiden wollen, die mit diesen Prüfungen einhergehen. Dass die Prüfprozesse bereits vorhanden sind, ermöglicht uns einen schnelleren Markteintritt und rechtfertigt es für uns, dass wir nur bestimmte Tests durchführen und nicht die komplette Palette. Das ist das große Plus bei der Arbeit mit Formlabs.“
Das nächste Projekt: Probleme im gesamten Körper angehen
Restor3d hat sich beim Einsatz von 3D-Druck zur Innovation des OP-Saals als führendes Unternehmen etabliert. Ihre branchenführenden Sets für die präoperative Planung, die hochpräzisen und innovativen Implantate und die umfassenden Lösungen ihrer OP-Trays haben Krankenhäuser dabei unterstützt, Kosten zu senken und die Patientenerfahrung zu verbessern.
Doch nach Kellys Meinung steht das Unternehmen gerade erst am Anfang – das Team plant bereits die Expansion auf das Gebiet der Fuß- und Knöcheloperationen sowie verschiedene Wirbelsäulenoperationen. Weitere orthopädische Anwendungsbereiche wie die Traumatologie, die Behandlung der oberen Extremitäten und die Sportmedizin werden nicht lange auf sich warten lassen. „Wir positionieren uns bereits jetzt dafür, die richtige Infrastruktur und grundlegende Technologieplattformen bereit zu haben, um Probleme im gesamten Körper angehen zu können, und zwar über verschiedene Fachbereiche der Medizin.“
Das Unternehmen ist kürzlich in einen riesigen, brandneuen Bürokomplex umgezogen, um sein Geschäft und seine Produktion leichter auf die nächste Stufe skalieren zu können. Die neuen Räumlichkeiten unterstützen das Wachstum der derzeitigen Produktlinien und machen es dem Team möglich, neue Spezialprodukte zu entwickeln.
Wesorick zieht Resümee: „Es gibt eine Handvoll Firmen, die 3D-Druck und Orthopädie nutzen, aber davon agieren nur sehr, sehr wenige vollkommen intern. Das Insourcing erlaubt uns allerdings, uns stets zu verbessern und das schnellste Produkt auf dem Markt zu bieten. Das ist natürlich leichter gesagt als getan, aber der Umzug in die neue Einrichtung wird uns wirklich dabei helfen, unsere Vision zu verwirklichen, direkt hier in Durham, North Carolina, alle Produkte vom Kunstharz oder Pulver bis zum fertigen Teil zu umzusetzen.“
Erfahren Sie mehr darüber, wie der 3D-Druck in der Medizin Anwendung findet, und erkunden Sie Formlabs' breite Palette biokompatibler medizinischer Materialien.