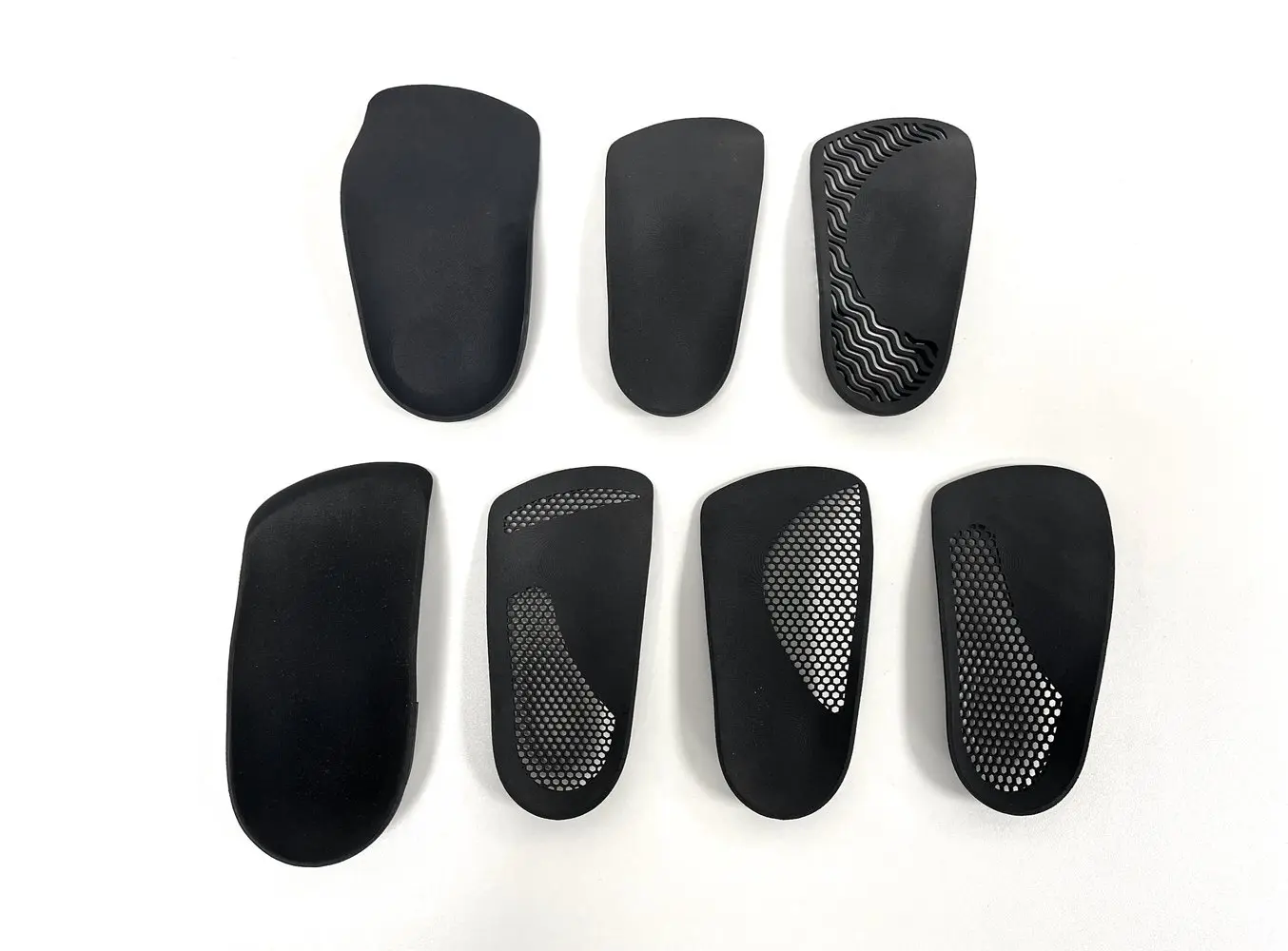
Das Orthopädiefachgeschäft MAG Orthotics Limited in Sheffield, Vereinigtes Königreich, bietet maßgeschneiderte Produkte und Reparaturen im Bereich Orthetik und Podologie an. Das Unternehmen befindet sich derzeit im Umbruch gen digitale Zukunft und führte vor kurzem den 3D-Druck ein, um Ressourcen, Zeit und Material zu sparen. Doch die Umstellung auf digitale Arbeitsabläufe betrifft nicht nur den eigenen Fertigungsprozess, sondern auch die Entscheidungen des gesamten Netzwerkes von Orthopädie- und Podologie-Fachleuten, mit denen MAG zusammenarbeitet.
Orthetikhersteller arbeiten in einem komplexen Ecosystem, das derzeit noch zwischen alten und neuen Fertigungsmethoden steckt. In Zusammenarbeit mit dem Vertriebspartner Additive-X, dem Software-Anbieter Fit360 und seinem Netzwerk in der Orthetik- und Podologie-Branche versucht MAG Orthotics, den Markt auf digitale Arbeitsabläufe umzustellen. Innerhalb dieses komplexen Netzwerks musste MAG Orthotics auf die Erfahrung seiner Partner zurückgreifen und gleichzeitig Händler und medizinische Fachleute über die Vorteile digitaler Prozesse und 3D-gedruckter Produkte aufklären.
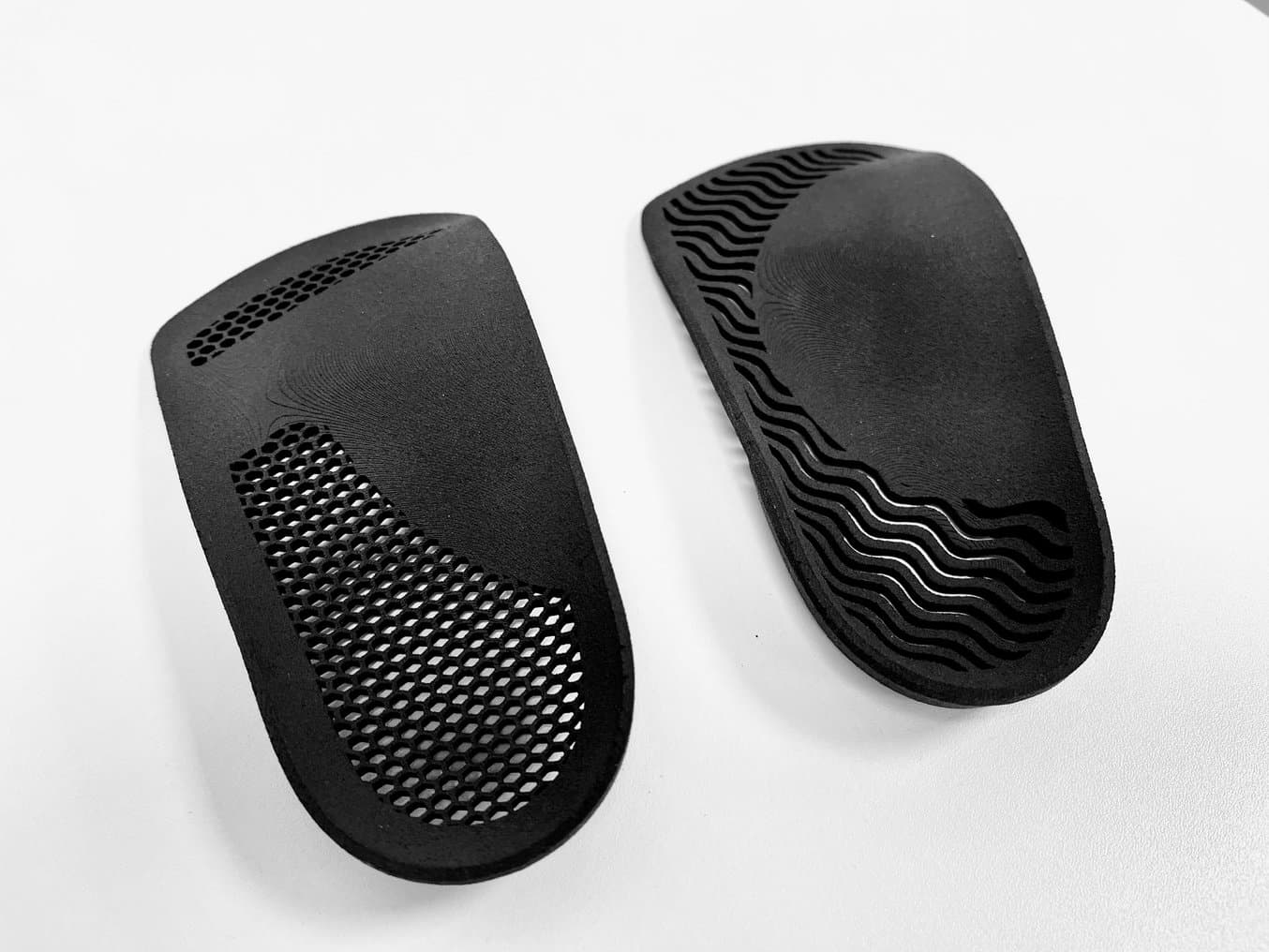
Die Zukunft der Einlagenfertigung und abfallfreie Produktion mit MAG Orthotics: Umgestaltung der Prozesse mit Formlabs und FIT360
Entdecken Sie die Möglichkeiten der Digitalisierung im Bereich der Einlagenfertigung, einschließlich Design und 3D-Druck. Erfahren Sie von MAG Orthotics aus erster Hand alles über den Umstieg auf 3D-Druck und ihr Engagement für Nachhaltigkeit.
Das komplexe Ecosystem
MAG Orthotics arbeitet mit Fachleuten der Orthetik und Podologie im britischen Gesundheitssystem National Health Service (NHS) sowie mit Krankenhäusern und in Privatkliniken im gesamten Vereinigten Königreich zusammen. Lee Lingard ist Spezialist für CAD und 3D-Entwicklung bei MAG Orthotics und leitet den gesamten 3D-Druck des Unternehmens. Von Fachleuten für Podologie und Orthopädietechnik erhält MAG Orthotics entweder einen Scan per E-Mail oder einen physischen Schaumstoffabdruck, den MAG dann einscannt. Das Ergebnis wird dann an Lingard gesendet, der das beste Design und die beste Fertigungsweise für die Orthese bestimmt.
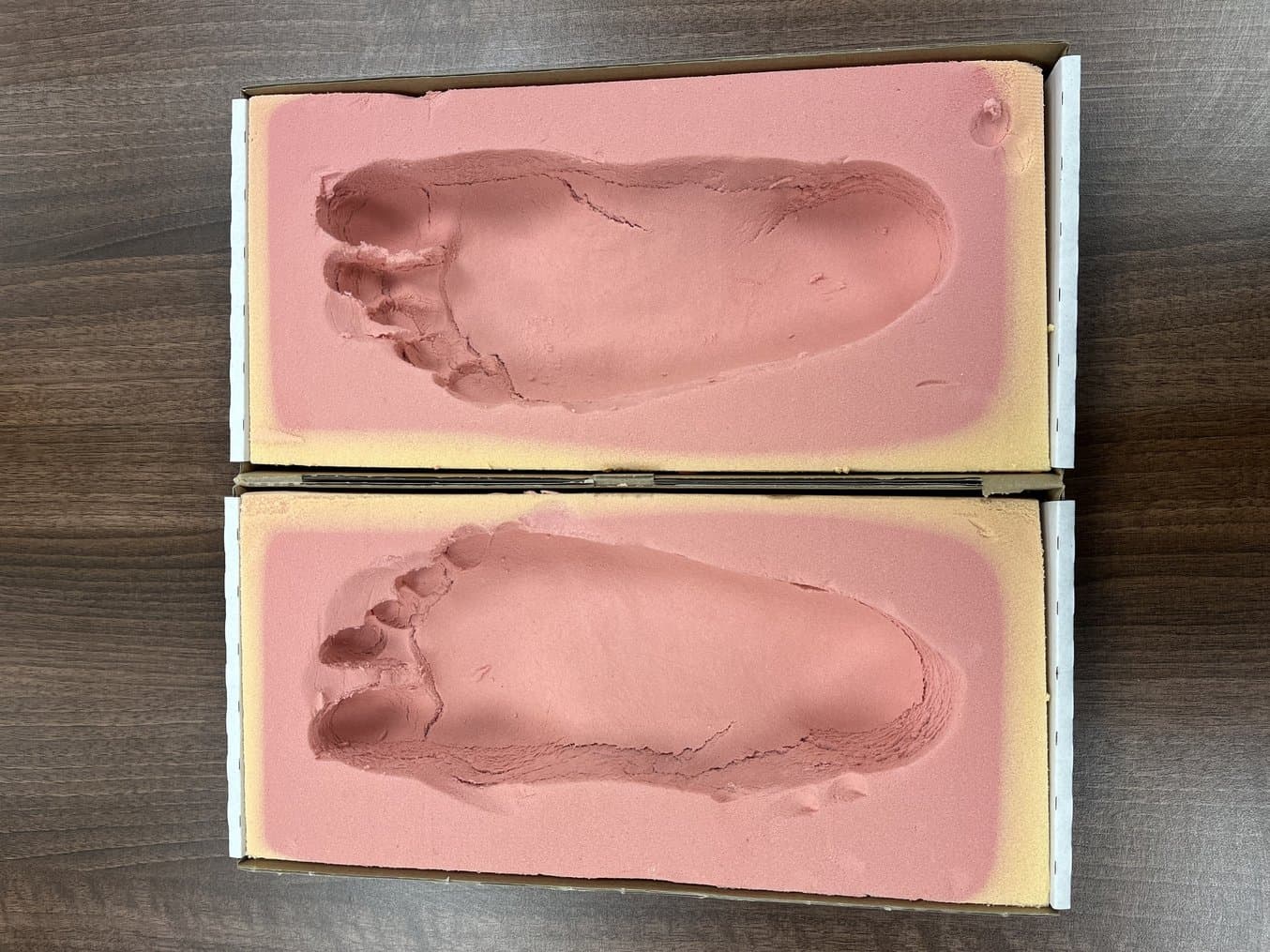
Einige Orthopädietechniker*innen und Podolog*innen senden immer noch physische Schaumstoffabdrücke an MAG Orthotics.

Schaumstoffabdrücke müssen zunächst gescannt werden, was im Vergleich zu einem rein digitalen Arbeitsablauf mehr Zeit erfordert.
Das Design wird bei MAG Orthotics in Fit360 erledigt, einer CAM-Software für das Design individueller Orthetik zum Fräsen, Zerspanen und 3D-Drucken. Die Wahl des Fertigungsverfahrens hängt in erster Linie vom gewünschten Material ab. Bei MAG Orthotics werden Orthesen auf CNC-Maschinen, einem FDM-Drucker und zwei SLS-3D-Druckern des Typs Fuse 1+ 30W von Formlabs hergestellt.
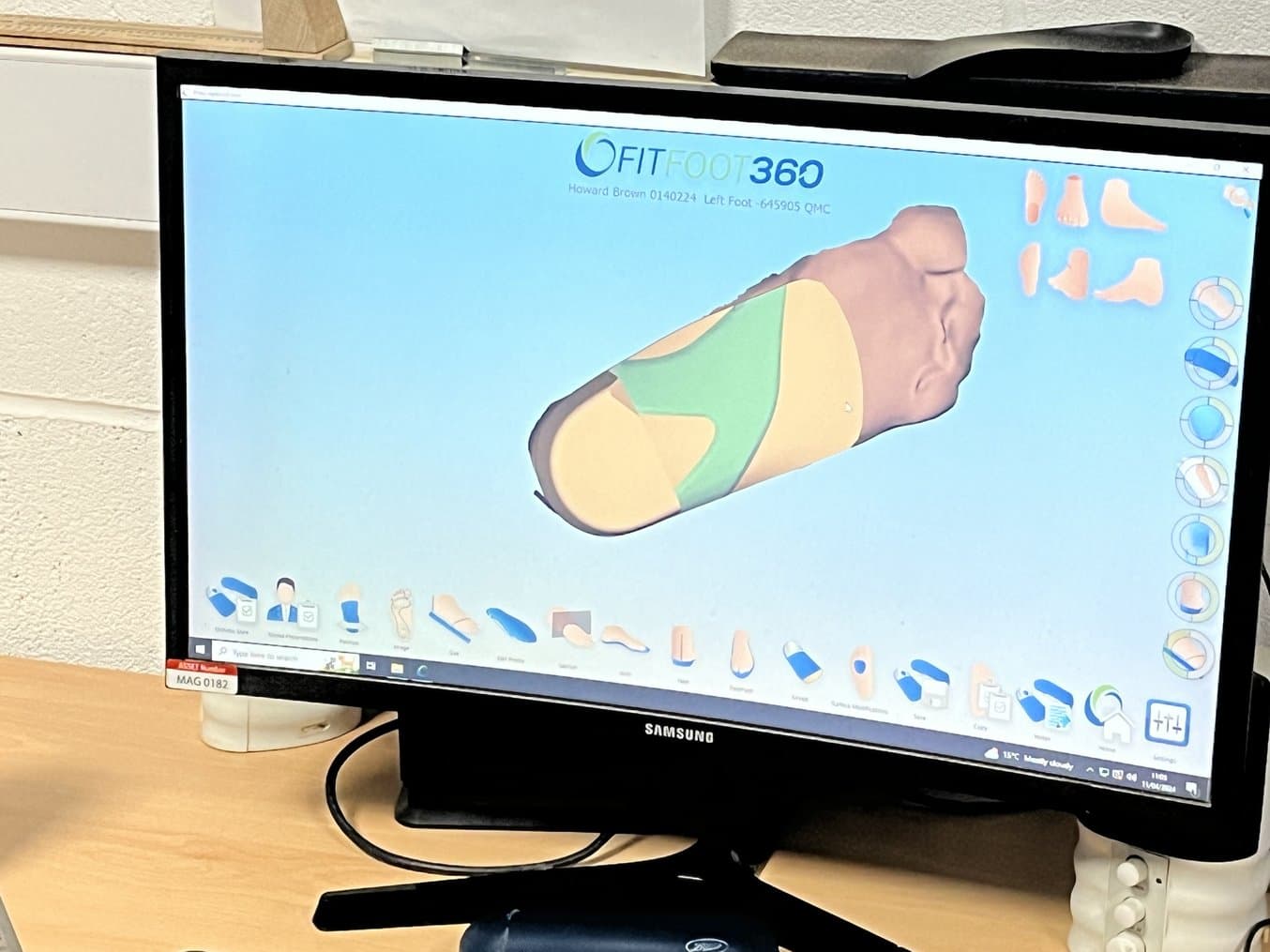
MAG Orthotics verwendet die Software Fit360 für das Design von Einlegsohlen.
Chris Lawrie, Inhaber und Geschäftsführer von Fit360, sagt: „Das Tolle an unserer Zusammenarbeit mit MAG ist, dass sie in der Software wählen können, ob das Material gefräst, aus einem festen Material gedruckt oder mit einer anderen Methode aus weichem Material gedruckt werden soll.“ In einer Zeit, in der die Orthesenfertigung sich an der Schwelle zwischen verschiedenen Fertigungstechnologien und Materialien befindet, erlauben diese Optionen es MAG, die angeforderte Orthese zu liefern und gleichzeitig einen konsistenten Designprozess zu gewährleisten.
Abkehr von traditionellen Methoden
Der Übergang von einem konventionellen, gefrästen Produkt zu einem 3D-gedruckten Produkt ist schwierig, da neue Technologien und die damit verbundenen Arbeitsabläufe erst erlernt werden müssen. Lingard sagt: „Wenn etwas Neues auf den Markt kommt, bin ich ganz wild darauf, es zu lernen, also war es für mich aufregend. Ich liebe Technik.“
Doch während Lingard der digitalen Zukunft freudig begegnet, muss sich die Branche als Ganzes dem Wandel erst noch stellen. „Ich mache jetzt schon seit 15 Jahren CAD-Design“, erzählt Lingard, „aber es gibt immer noch den einen oder anderen Orthopädietechniker, der nach der traditionellen Methode fragt. Da entsteht für uns also eine große Lücke.“
Diese Lücke ist ein Grund dafür, dass MAG immer noch einige traditionelle Fertigungsmethoden einsetzt. Als Fertigungslabor haben sie die Aufgabe, die verschriebenen Orthesen Gestalt annehmen zu lassen. Im Moment schließt dies den Einsatz einiger alter Fräsen mit ein, während die Fertigung auf digitale, umweltfreundlichere Prozesse umgestellt wird.
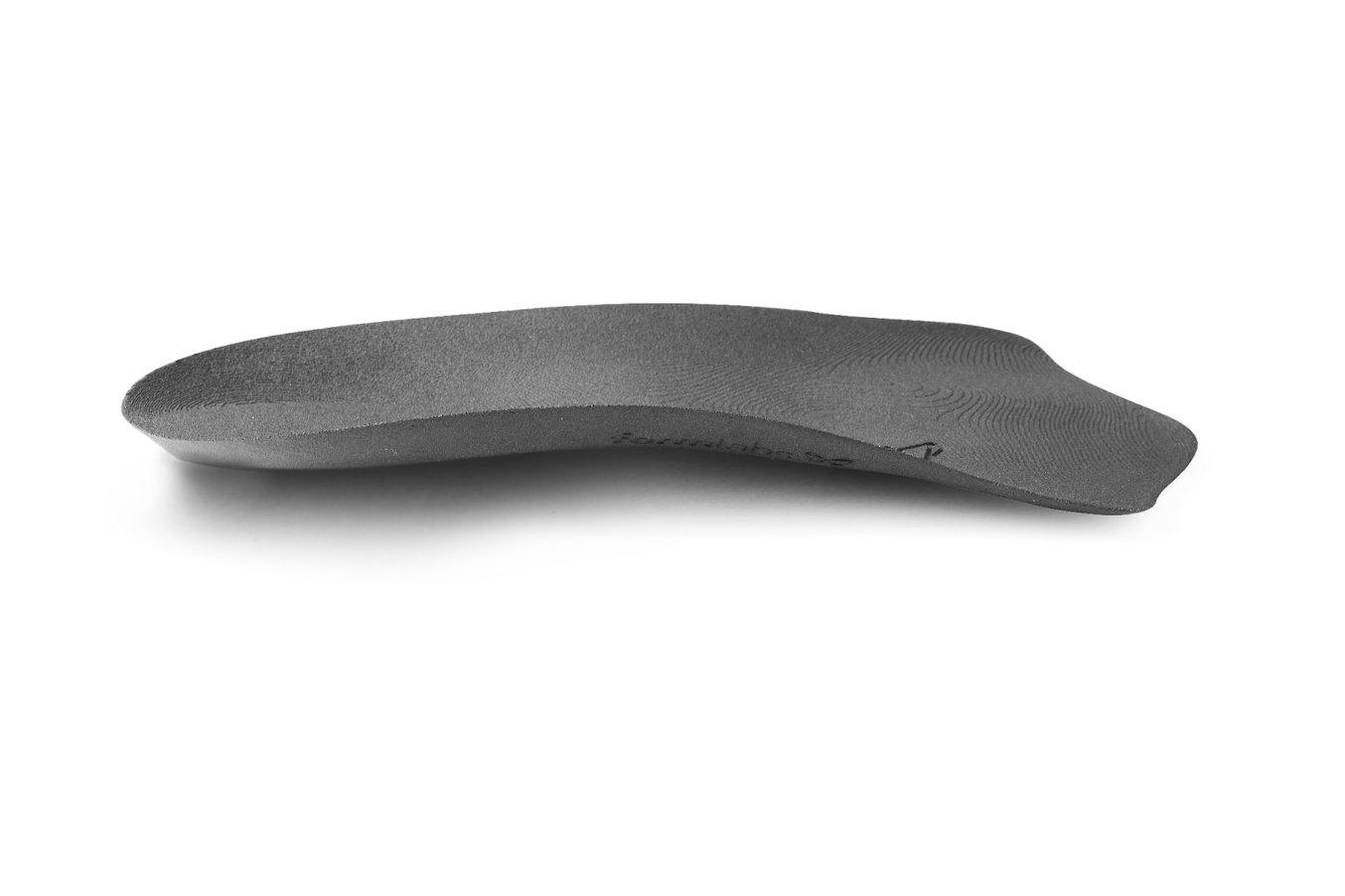
Fordern Sie einen Probedruck einer Einlage an
Entdecken Sie die überragenden Eigenschaften von Nylon 11 Powder und revolutionieren Sie Ihre Einlagenfertigung. Erleben Sie die exzellente Energierückgabe und Haltbarkeit, die in unabhängigen Tests mehr als vier Millionen Schritte überstanden.
Der Umstieg auf SLS-3D-Druck
Mark Joyce, Werksleiter bei MAG Orthotics, sieht im 3D-Druck einen großen Schritt auf dem Weg zu nachhaltigeren Prozessen. Anfangs lagerte MAG den 3D-Druck aus, um erste Versuche mit der Technologie zu machen. Die Auslagerung war kostspielig und zeitaufwändig, da die Orthesen an MAG Orthotics zurückgesandt werden mussten. Zu diesem Zeitpunkt, so Joyce, „dachten wir, dass wir selbst in die Branche einsteigen müssten.“
Joyce arbeitete mit Additive-X zusammen, um den Drucker zu finden, der sich am besten für ihren Betrieb eignet. Die wichtigsten Faktoren bei der Bewertung der Optionen waren Kosten, Langlebigkeit und Zuverlässigkeit. Bei seiner Recherche von SLS-Druckern stellte Joyce fest, dass die meisten Lösungen zu komplex und zu teuer waren, und entschied sich daher für den Fuse 1+ 30W als einen Drucker, der in Bezug auf Materialien, Hardware und Preis allen Anforderungen entsprach.
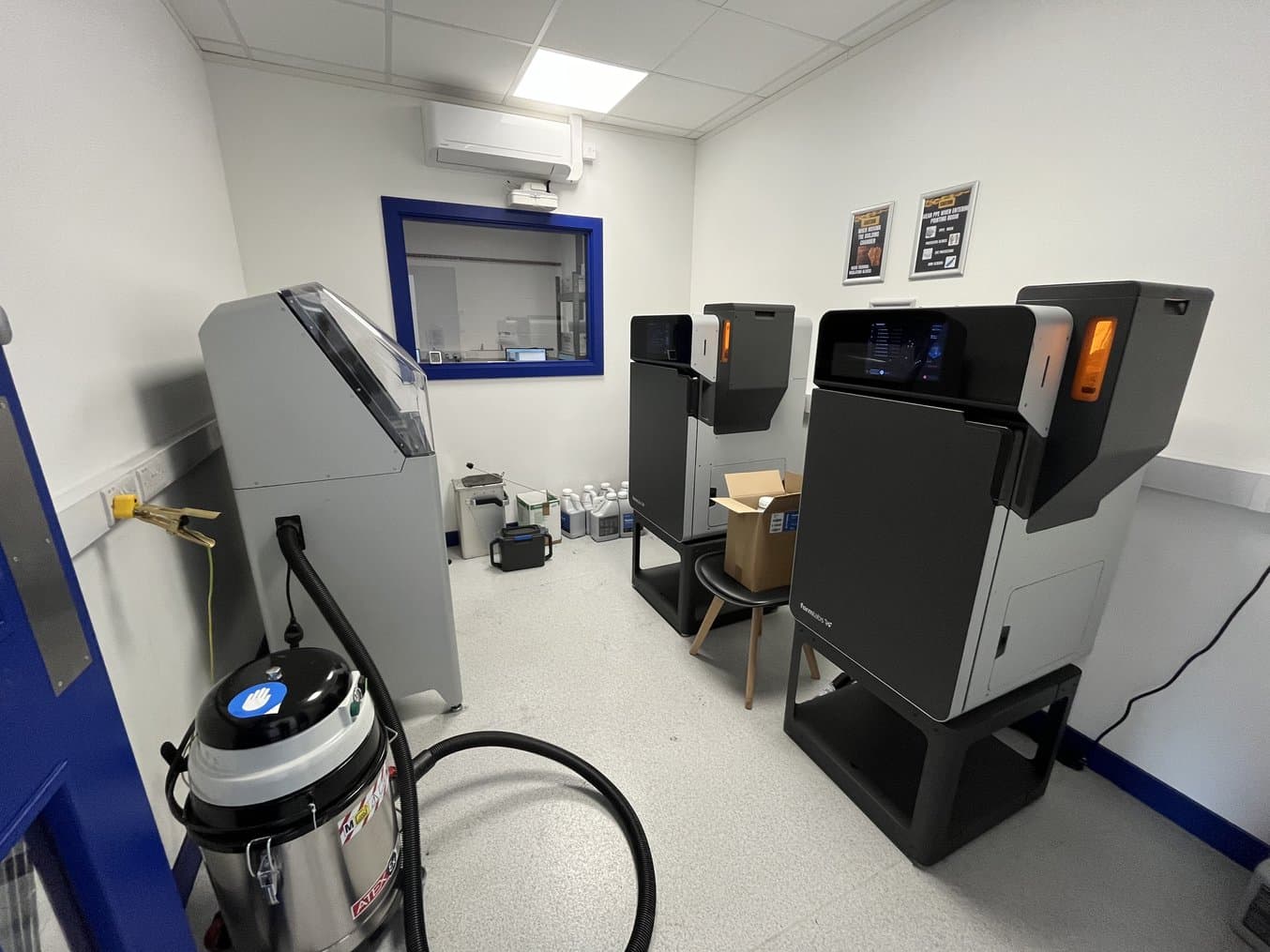
MAG Orthotics druckt betriebsintern mit zwei 3D-Druckern vom Typ Fuse 1+ 30W (rechts), was für Redundanz in den Fertigungskapazitäten sorgt.
Jetzt druckt das Team jeden Tag mit dem Fuse. Lingard berichtet: „Wir verwenden auch noch CNC-Fräsen, aber wir versuchen, wo immer möglich die Drucker einzuführen.“ Eine der größten Hürden bei der Einführung digitaler Arbeitsabläufe war jedoch nicht interner Natur.
„Unsere größte Herausforderung sind die Orthopädietechniker, denn sie hängen an den alten Methoden, und es ist schwer, sie für neue Technologien zu gewinnen“, beklagt sich Lingard. Um dieses Problem zu lösen, hat Lingard damit begonnen, Orthopädietechniker*innen ein Paar 3D-gedruckte Einlagen und EVA-Einlagen zum Vergleich anzubieten. Eine Orthopädietechnikerin, die selbst Läuferin und Wanderin ist, war von den 3D-gedruckten Einlagen überzeugt, nachdem sie sie eine Woche lang ausprobiert hatte.
„Es ist ein Kostenfaktor für uns, denn es geht um Zeit, Durchlaufzeit, Materialien und so weiter. Wir versuchen, die Menschen für diese neuen Technologien zu begeistern“, erklärt Lingard. Indem MAG Orthotics jetzt investiert, ebnet das Unternehmen den Weg für eine sauberere und schnellere Fertigung in der Zukunft.
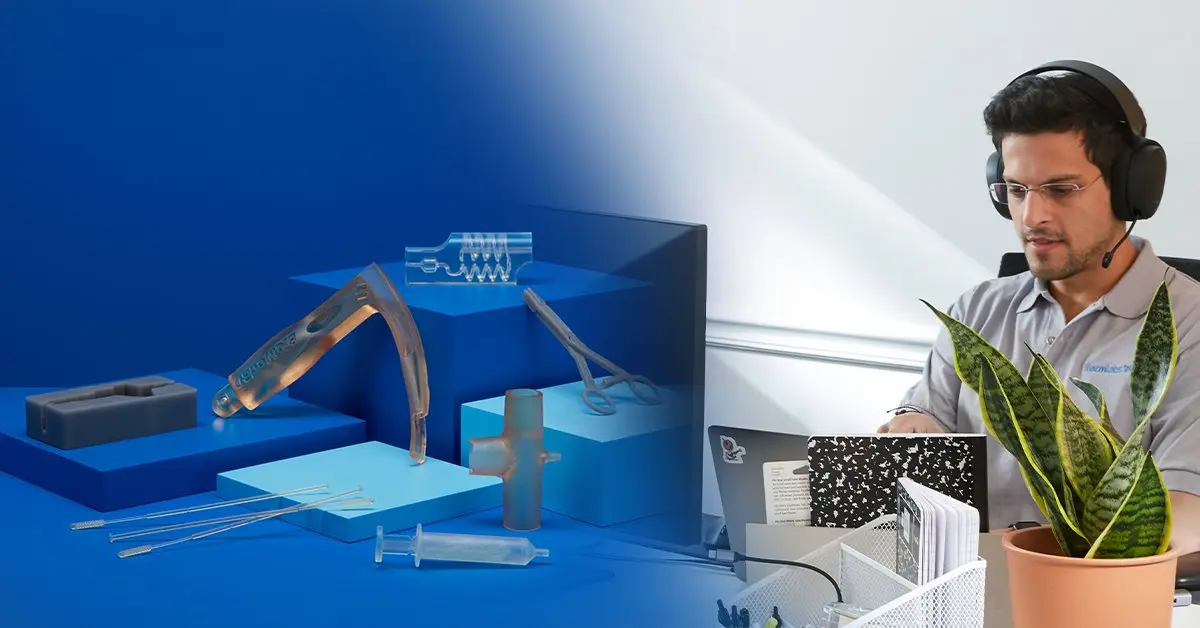
Kontakt zum Vertriebsteam von Formlabs Medical
Ob Sie patientenspezifische chirurgische Instrumente erstellen möchten oder Prototypen kardiologischer Medizinprodukte anfertigen: Wir stehen Ihnen zur Seite. Hinter Formlabs Medical steht ein engagiertes Spezialistenteam, das Sie und Ihr Unternehmen bei Bedarf mit professioneller Hilfe unterstützt.
Abfallfreie Fertigung
Im Vereinigten Königreich werden bei Ausschreibungen die „Zero to landfill“-Politik und die CO2-Bilanz berücksichtigt. Ein Teilziel von MAG Orthesis bei der Umstellung auf digitale Arbeitsabläufe und 3D-Druck ist auch die Minimierung des Abfalls in der Fertigung.
„Früher haben wir viel Gips verwendet, es wurde also von Hand mit Gips geformt und dann mit EVA oder Polypropylen um den Gips herum modelliert. Wir gingen dann einen Schritt weiter und starteten mit CAD-Design, das mittels CNC-Fräsen umgesetzt wurde, aber es gab immer noch viel Abfall. Doch mit dem Pulverdruck mit TPU haben wir ein sehr, sehr geringes Abfallaufkommen, und das ist der ökologische Weg nach vorn.“
Mark Joyce, Geschäftsführer, MAG Orthotics
Als SLS-Drucker druckt der Fuse 1+ 30W mit Pulver. Anders als bei der CNC-Bearbeitung, bei der Material, das nicht Teil der fertigen Einlage ist, entsorgt wird, kann das nicht gesinterte Pulver für den Druck folgender Einlagen wiederverwendet werden.
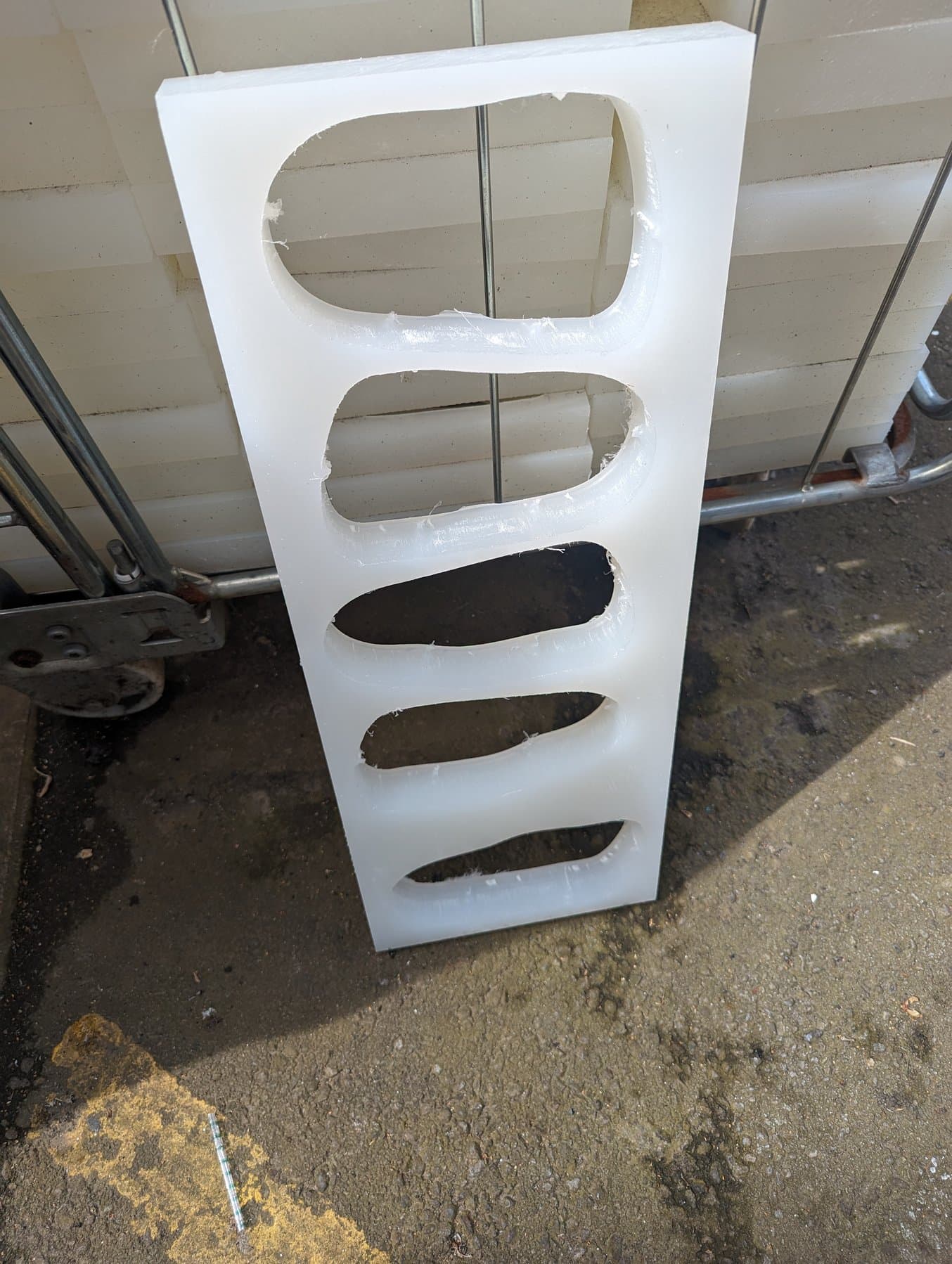
Der Materialabfall bei der CNC-Fertigung mit Polypropylen summiert sich schnell.
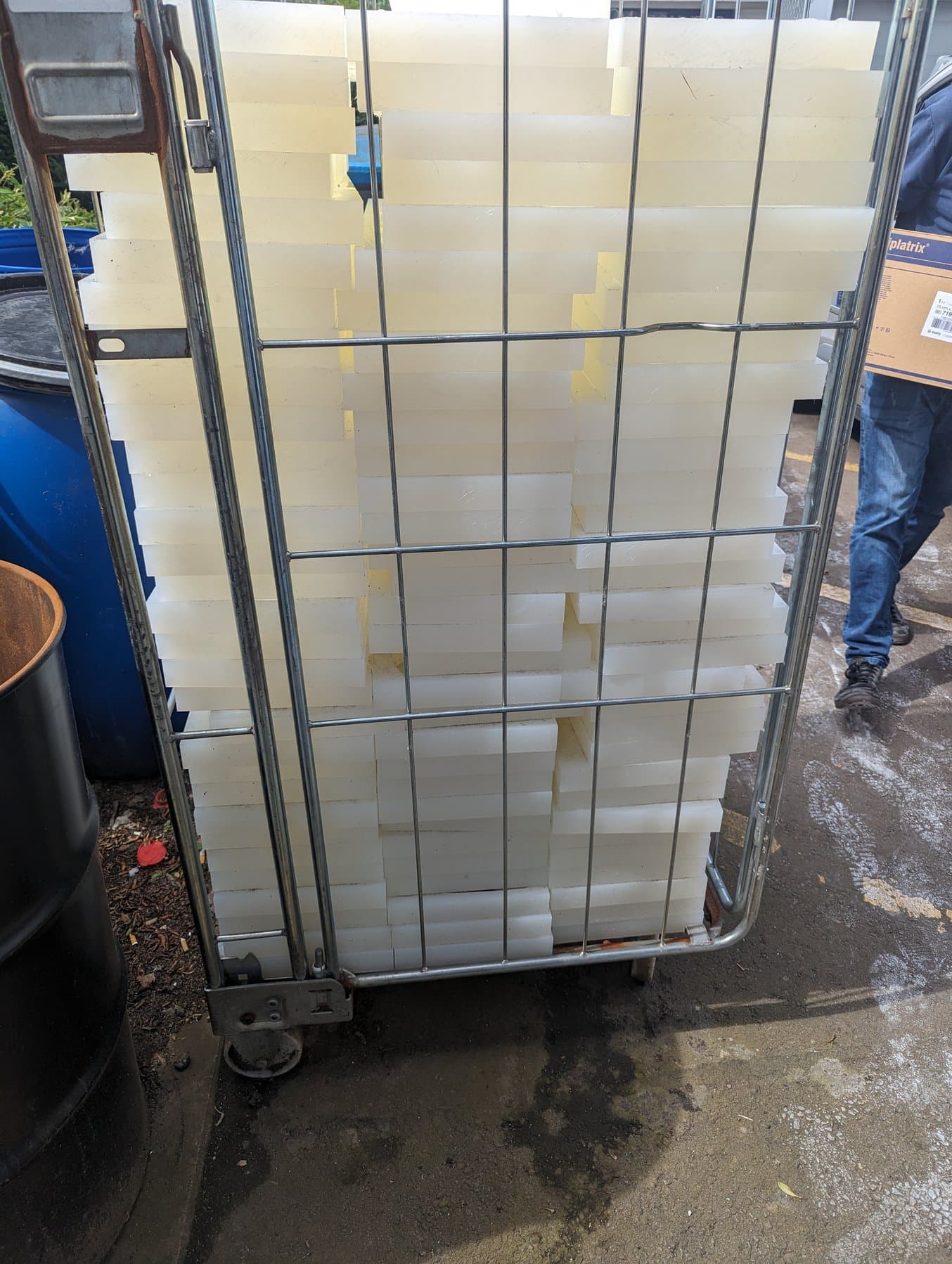
Die Verringerung des anfallenden Abfalls ist einer der Hauptgründe, warum MAG Orthotics den 3D-Druck eingeführt hat.
MAG druckt Einlagen aus Nylon 11 Powder, einem starken und hochduktilen Material, das für den Hautkontakt zugelassen ist. Druckteile aus Nylon 11 Powder nehmen nur sehr wenig Feuchtigkeit auf und sind licht-, hitze- und chemikalienbeständig, was sie zu einem idealen Material für die Fertigung von Einlagen macht. Das Drucken von Nylon 11 Powder in Inertgasatmosphäre, in diesem Fall Stickstoff, bedeutet eine geringere Oxidation des Pulvers, was zu höheren Neuzuführungsraten und damit noch weniger Abfall führt.
Da das Team keine physischen Abdrücke einholen muss, verbraucht es außerdem weniger Kraftstoff und verringert den Fahrzeugverschleiß, sodass der Prozess von Anfang bis Ende umweltfreundlicher ist.
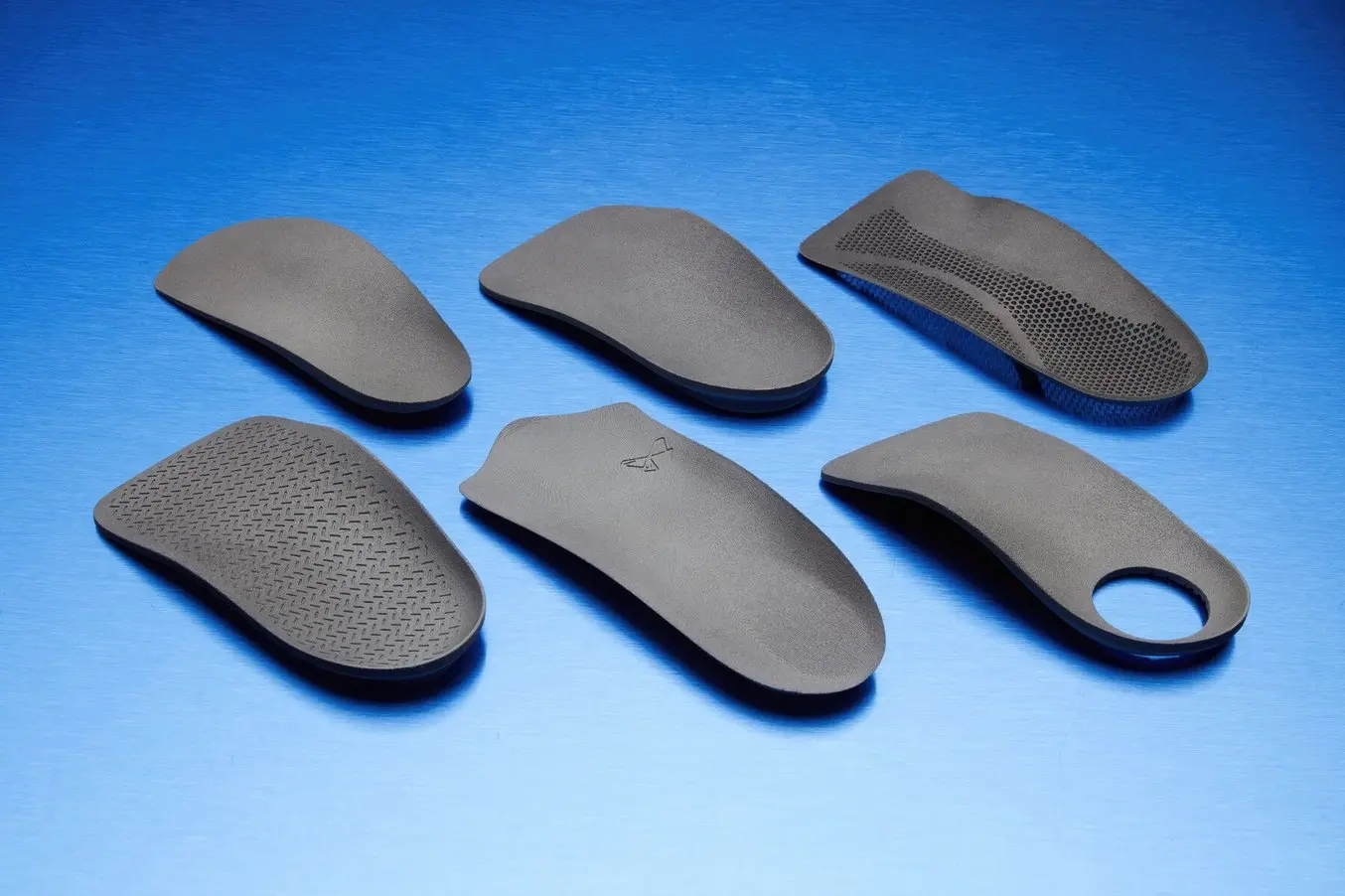
Revolutionieren Sie Ihre Einlagenproduktion mit dem Fuse 1+ 30W von Formlabs
Bringen Sie Ihre Einlagenproduktion auf Touren und sparen Sie zugleich Zeit und Geld. In diesem Webinar erfahren Sie, was den Fuse 1+ 30W von Formlabs zur perfekten Lösung für den Einstieg in die digitale Fertigung macht oder wie Sie Ihre Produktion damit kostengünstig und effizient skalieren.
Zeitersparnis
Digitale Arbeitsabläufe haben ein enormes Potenzial, die Fertigungsdauer zu verkürzen. Bei herkömmlichen Verfahren musste man in eine Klinik fahren, um Abformungen abzuholen. MAG arbeitet daran, „Unternehmen und Kliniken davon zu überzeugen, in einen Handscanner zu investieren, mit dem sie den Fuß scannen können“, sagt Joyce. Wenn ein Scan und ein Rezept „einfach über einen Link per E-Mail kommen, sind das drei Tage, die man sofort spart“, erläutert Joyce.
„Bei gefrästem EVA-Schaumstoff hat man den ganzen Grat und Verschnitt, den man abschneiden muss, und man muss die Schablonen anbringen, um all das herum schneiden, dann alles glätten, alles in Form bringen – es dauert alles viel länger. Deshalb mögen wir 3D-gedruckte Einlagen, weil sie viel schneller und mit weniger Aufwand hergestellt werden können.“
Lee Lingard, Spezialist für CAD und 3D-Entwicklung, MAG Orthotics
Dank digitaler Arbeitsabläufe können Podologie-Fachleute am Montagmorgen einen digitalen Scan und eine Bestellung senden. Eine Stunde später wird die Bestellung bearbeitet und innerhalb einer Stunde kann Lingard die orthopädischen Einlagen entwerfen. Dann werden die Einlagen am Montagnachmittag gedruckt, wobei der Druck über Nacht abgeschlossen wird. Am nächsten Tag können die Einlagen gereinigt und fertiggestellt werden, sodass die Durchlaufzeit nur etwas mehr als einen Tag beträgt.
Im Vergleich dazu dauert die Verwendung von Schaumstoffabdrücken etwa 72 Stunden länger, da die Abholzeit und die administrative Bearbeitung der Bestellung hinzukommen. Auch wenn die tatsächliche Druckdauer länger sein kann als die Zeit, die an der CNC-Maschine verbracht wird, erfordert eine CNC-Maschine eine manuelle Bedienung und eine umfangreiche Nachbearbeitung. Sobald ein 3D-Drucker vorbereitet ist, ist der eigentliche Druck völlig automatisch, sodass Mitarbeitende für höherwertige Aufgaben frei sind oder Drucke über Nacht durchgeführt werden können. Einlagen aus einem SLS-Drucker müssen zwar gereinigt werden, erfordern aber nur wenig Nachbearbeitung. Daher beansprucht der digitale Arbeitsablauf insgesamt weniger Zeit und Arbeit. Insgesamt sagt Joyce, dass sein Team die Durchlaufzeiten für Bestellungen durch den 3D-Druck von Einlagen minimiert – zusätzlich zur Verringerung seiner CO2-Bilanz.
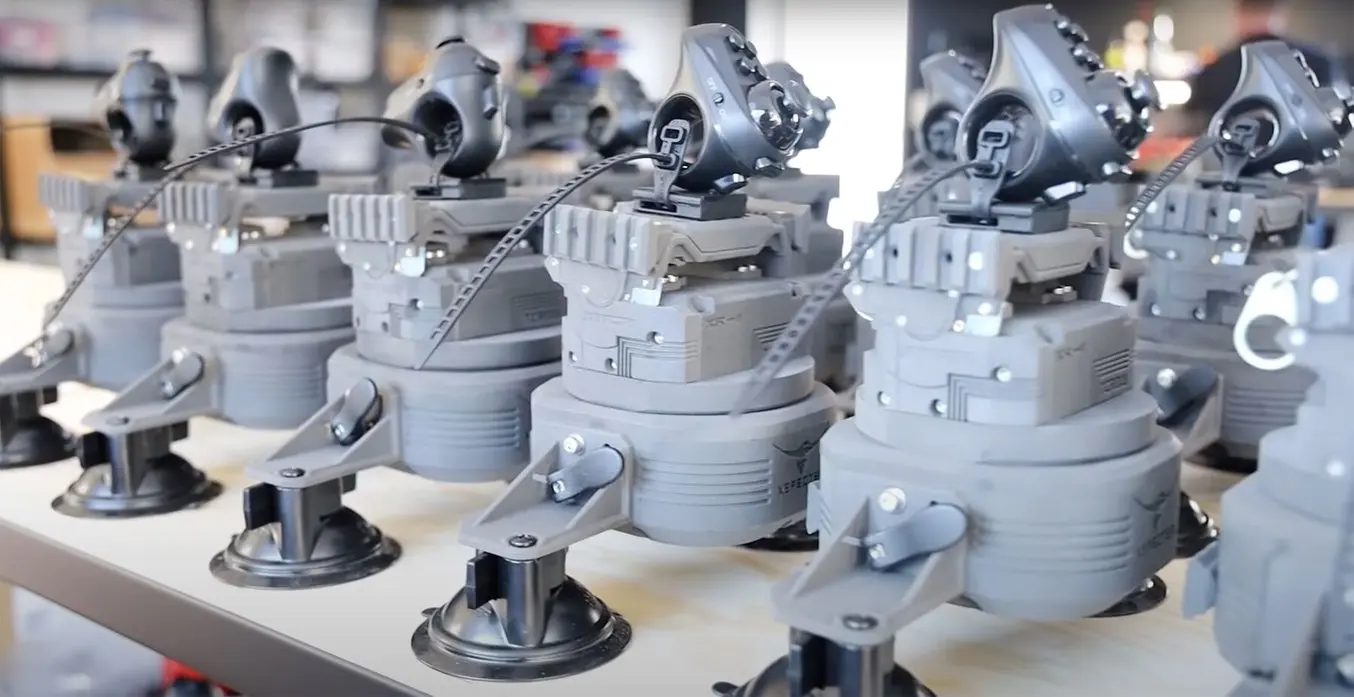
SLS-Produktion für die Endverwendung
3D-Druck für die Endverwendung ist nicht nur möglich, sondern dank des SLS-Ecosystems der Fuse-Serie auch noch erschwinglicher, agiler und leichter skalierbar denn je. Besuchen Sie unsere Seite zum Thema SLS für die Produktion und vergleichen Sie Produktionsverfahren, informieren Sie sich über unsere Mengenrabatte auf Pulver und entdecken Sie die Produktionsabläufe 15 verschiedener Hersteller, die derzeit die Fuse-Serie nutzen.
Auf dem Weg in die Zukunft
MAG Orthotics arbeitet weiterhin daran, die Orthetik-Branche auf digitale Arbeitsabläufe umzustellen, und skaliert daher seine SLS-Fertigung. Die zwei 3D-Drucker des Typs Fuse 1+ 30W sorgen für Redundanz beim Drucken, sodass immer mindestens ein Drucker in Betrieb sein kann. MAG Orthotics prüft auch die Möglichkeit der chemischen Dampfglättung (Vapor Smoothing), ein üblicher Nachbearbeitungsschritt, der bei SLS-3D-Druckteilen durchgeführt wird, um die Porosität und die Rauheit zu verringern und so eine glattere und glänzendere Textur zu schaffen.
In Zusammenarbeit mit Fit360, Additive-X, Formlabs und ihrem Netzwerk von Orthopäd*innen und Podolog*innen arbeitet das Team von MAG Orthotics an der Umstellung auf digitale Prozesse – und der Eliminierung von Abfällen. Neue 3D-Drucktechnologien wie der Fuse 1+ 30W helfen ihnen dabei.
Erfahren Sie mehr über den 3D-Druck von orthopädischen Einlagen oder sprechen Sie mit unserem Expertenteam, um die richtige Lösung für Ihr Unternehmen zu finden.
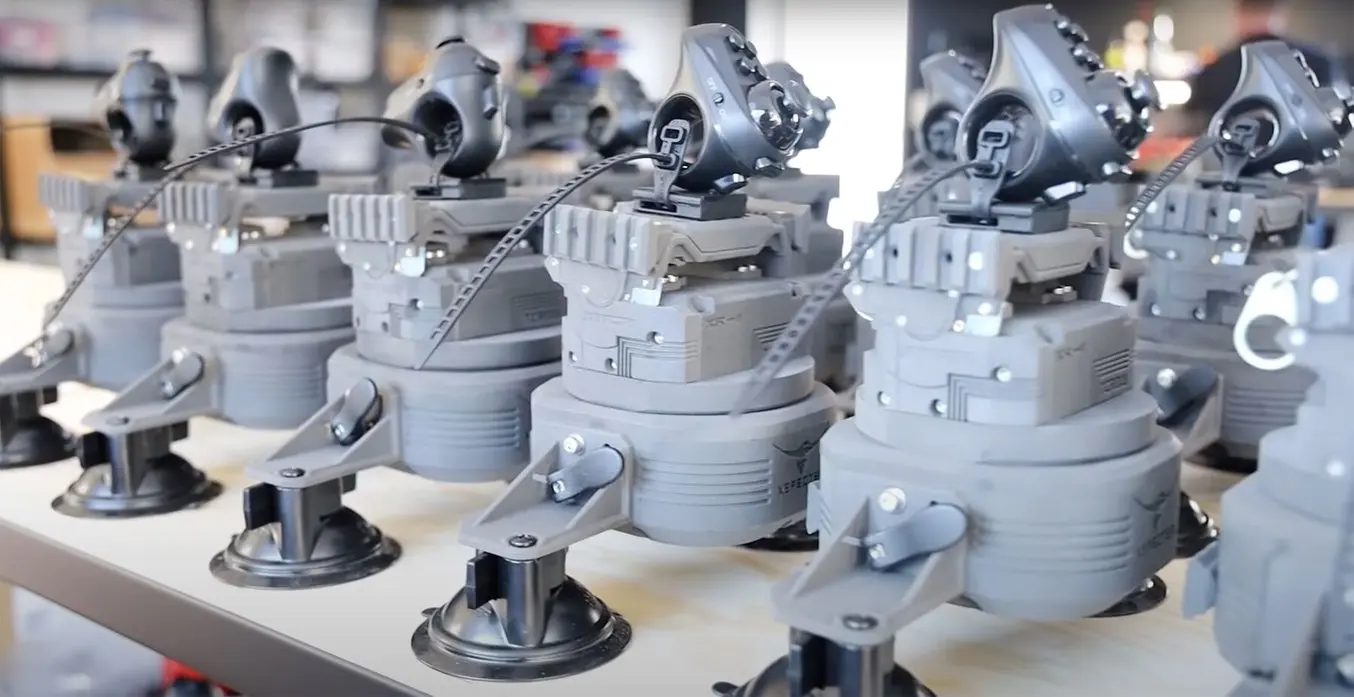
SLS-Produktion für die Endverwendung
3D-Druck für die Endverwendung ist nicht nur möglich, sondern dank des SLS-Ecosystems der Fuse-Serie auch noch erschwinglicher, agiler und leichter skalierbar denn je. Besuchen Sie unsere Seite zum Thema SLS für die Produktion und vergleichen Sie Produktionsverfahren, informieren Sie sich über unsere Mengenrabatte auf Pulver und entdecken Sie die Produktionsabläufe 15 verschiedener Hersteller, die derzeit die Fuse-Serie nutzen.