Silikon-3D-Druck von Dichtungen für Kfz-Steckverbinder für die Endverwendung
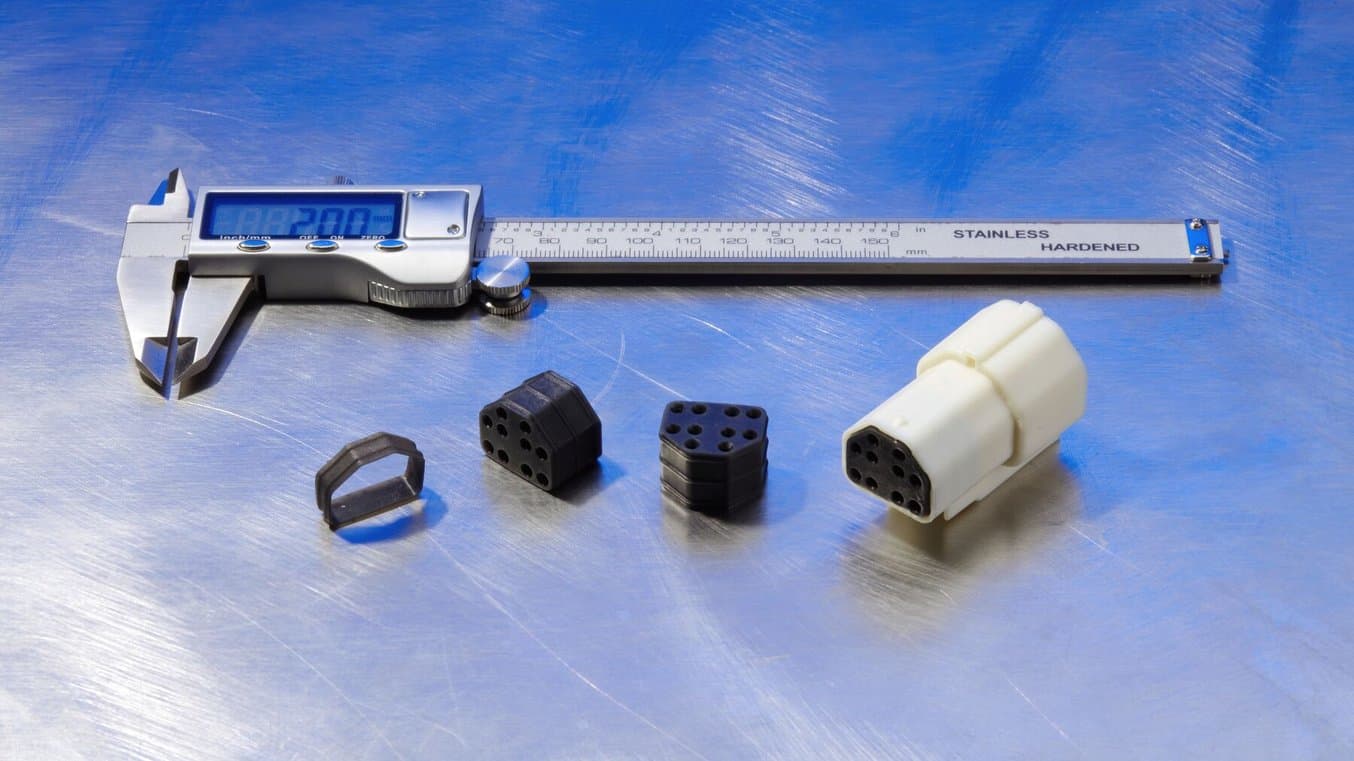
Verbinderdichtungen von HGM Automotive Electronics, die aus Silicone 40A Resin 3D-gedruckt wurden.
HGM Automotive Electronics ist ein spezialisierter Hersteller, der hochmoderne Elektroniksysteme für den Aftermarket der Automobilbranche entwirft und vertreibt.
Laut Guy Cardwell, Leiter der Forschung und Entwicklung bei HGM Automotive Electronics, ist eine der großen Herausforderungen des Unternehmens die Schwierigkeit, Bauteile für die Wartung oder Reparatur seiner Motoren zu finden, denn das Team beschäftigt sich zum großen Teil mit Oldtimern. Steckverbinder und andere elektronische Komponenten sind immer schwerer auffindbar, vor allem da die Originalproduktion dieser Bauteile bereits eingestellt wurde.
Das Team ist für die Prototypenentwicklung und Kleinserienfertigung auf 3D-Druck umgestiegen, da dieser zur Fertigung von Teilen auf Abruf und im eigenen Betrieb die beste Lösung darstellt. Weil der Industriezweig jedoch stark reguliert ist und bestimmte Anforderungen wie etwa die IP-Schutzart und Chemikalienbeständigkeit einhalten muss, spielt die Wahl des Materials eine entscheidende Rolle. Das am meisten verwendete Material für Dichtungen von Kfz-Steckverbindern ist weiches Silikon, doch für dessen Fertigung gibt es nur äußerst wenige Optionen. Spritzguss ist bei der Produktion kleiner Stückzahlen nicht kosteneffizient, während der traditionelle Silikonguss ein langwieriges Verfahren ist.
Mit der Veröffentlichung von Silicone 40A Resin, dem ersten erschwinglichen 3D-Druckmaterial aus 100 % Silikon für weiche, biegsame und robuste Teile, hat das Team Cardwell zufolge „genau den richtigen Stoff“ gefunden. Mittels ausgiebiger chemischer und mechanischer Tests hat es belegt, dass das neue Material über die hervorragenden mechanischen Eigenschaften und die Chemikalienbeständigkeit verfügt, die Automobilbauteile für die Endverwendung verlangen. Das Unternehmen war Teil der Beta-Tests des neuen Materials und setzte es für die Prototypenfertigung ein, doch ihr vordergründiges Ziel ist es nun, es auch für die Kleinserienproduktion von Endverbrauchsteilen zu nutzen.
„Silicone 40A Resin ist einfach perfekt. Es hat eine ausgesprochen große Ähnlichkeit zum Originalmaterial, das wir vom Zulieferer erhalten hätten.“
Guy Cardwell, Leiter der Forschung und Entwicklung bei HGM Automotive Electronics
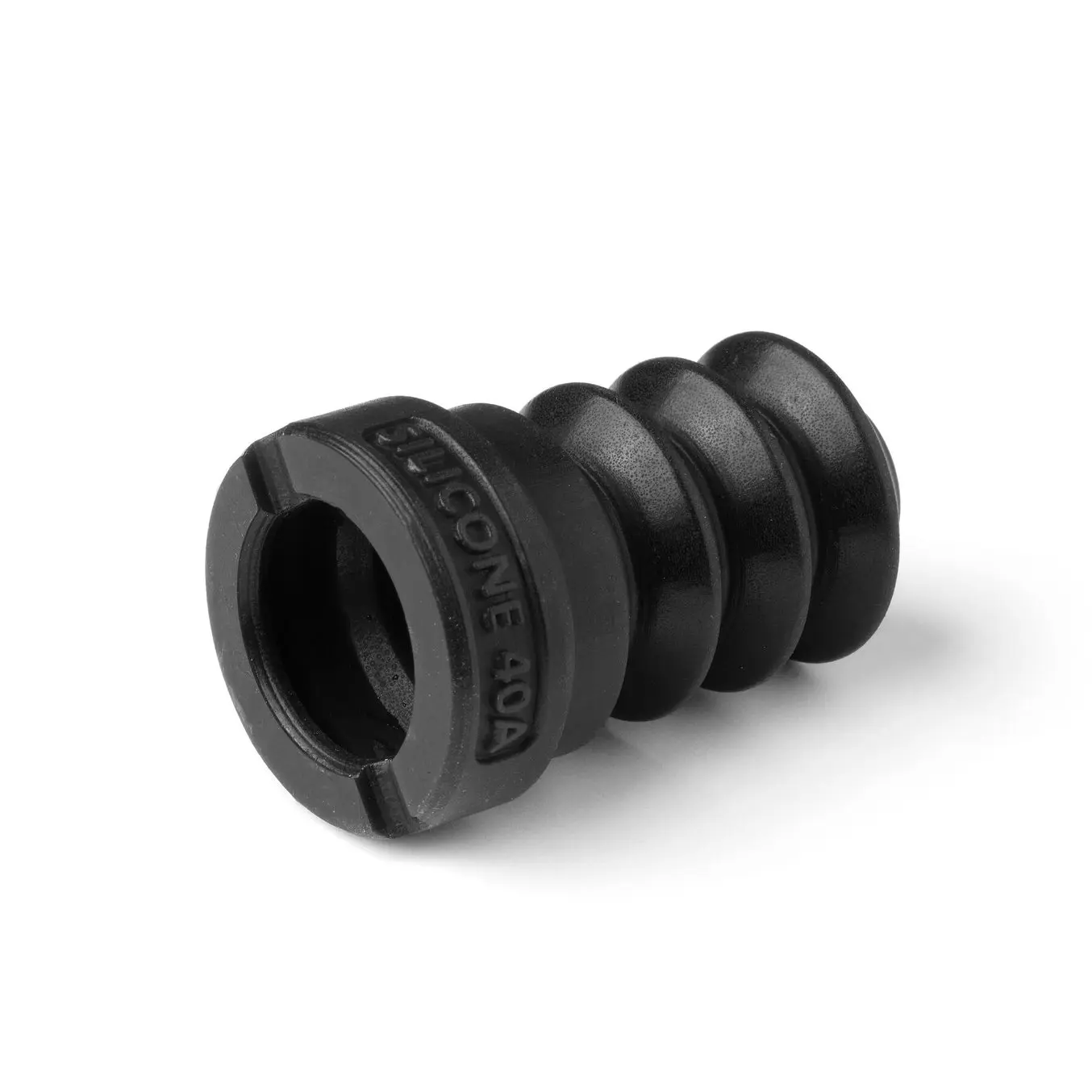
Kostenlosen Probedruck anfordern
Sehen und fühlen Sie selbst die Qualität von Formlabs. Wir senden Ihnen einen kostenlosen Probedruck aus Silicone 40A Resin an Ihren Arbeitsplatz.
Verbesserung des Designs von Verbinderdichtungen mit Silicone 40A Resin
Gegenübergestellte Methode | Vorteile des 3D-Drucks mit Silicone 40A Resin |
---|---|
Ausgelagerter Spritzguss | Durchlaufzeit um 90 % verkürzt Kosten um 98 % gesenkt |
Betriebsinterner Silikonguss | Schwierige, komplexe Geometrie mit detaillierter Auflösung umgesetzt Arbeitsaufwand, Fehlerrisiko und Durchlaufzeit verringert Reproduzierbar und skalierbar von 10 bis 1000 Einheiten |
Aufgrund des Erfolges seiner elektrischen Steckverbinder begann HGM Automotive mit individuellen Dichtungen zu experimentieren. Dabei handelt es sich um schwer zu beschaffende Komponenten, die auf dem Markt kaum erhältlich sind, oder wenn doch, dann meist in minderwertiger Qualität. Die Herausforderung, individuelle Dichtungen für die Verbinder zu entwickeln, ergab sich aus dem Mangel eines geeigneten, biegsamen Elastomermaterials. Das Team hätte eine Spritzgussform fertigen und das Teil damit aus sehr weichem Urethan herstellen können. Das birgt jedoch den Nachteil, dass so eine Form eingangs zwischen 6000 € und 10 000 € gekostet hätte. Solch hohe Ausgaben wären gerechtfertigt, wenn das Unternehmen 10 000 dieser Komponenten benötigen würde – realistisch ist jedoch eine Stückzahl von 100 bis 1000 Teilen pro Jahr. Darüber hinaus ist es nahezu unmöglich, das Design zu verändern, sobald die Gussform einmal erstellt wurde. Gerade bei Verbinderdichtungen, die häufig komplizierte Geometrien haben, ist das ein ernsthaftes Hindernis. „Es läuft alles auf die Frage der Kosten und Flexibilität hinaus“, so Cardwell.
Durchlaufzeit | Kosten | |
---|---|---|
Ausgelagerter Spritzguss | 3–4 Wochen | 10 000 € Werkzeugkosten 0,50 € pro Teil |
Betriebsinterner 3D-Druck mit Silicone 40A Resin | 6 Stunden für 25 Teile | 1–2 € pro Teil |
Bei einem Produktionsvolumen von 100 Einheiten der Verbinderdichtungen konnte HGM Automotive seine Kosten um 98 % und seine Durchlaufzeit um 90 % reduzieren.
Ursprünglich hatte das Unternehmen die Dichtungen aus Formlabs' weichem und flexiblem Material Elastic 50A Resin gedruckt, doch selbst das war noch nicht flexibel genug. Wie Cardwell hinzufügt, benötigen Kabelbaumhersteller aufgrund der manuellen Montage der Steckverbinder vermutlich zwei- bis dreimal länger dafür, einen Steckverbinder mit einem härteren Material wie Urethan zu montieren, als mit einer Silikondichtung, „einfach, weil sie gegen das Material arbeiten müssen.“
Eine andere Option war, auf herkömmlichen Silikonguss zurückzugreifen, wie es das Team schon bei anderen Bauteilen getan hat. Da dieser spezifische Steckverbinder darauf ausgelegt ist, dass neun Kabel die Dichtung passieren, handelt es sich jedoch um ein besonders filigranes Design. Es beinhaltet Löcher und eine Geometrie, die das Entformen erschweren würde – ein Grad an Detailliertheit, der auf die Präzision des 3D-Drucks angewiesen ist.
„Man kann das mit Guss umsetzen, aber man muss sehr, sehr vorsichtig [mit den filigranen Geometrien] sein und es ist zeitintensiv. Dass wir es also einfach chargenweise 3D-drucken können, ist ein Luxus im Vergleich zu allen anderen Prozessen.“
Guy Cardwell, Leiter der Forschung und Entwicklung bei HGM Automotive Electronics
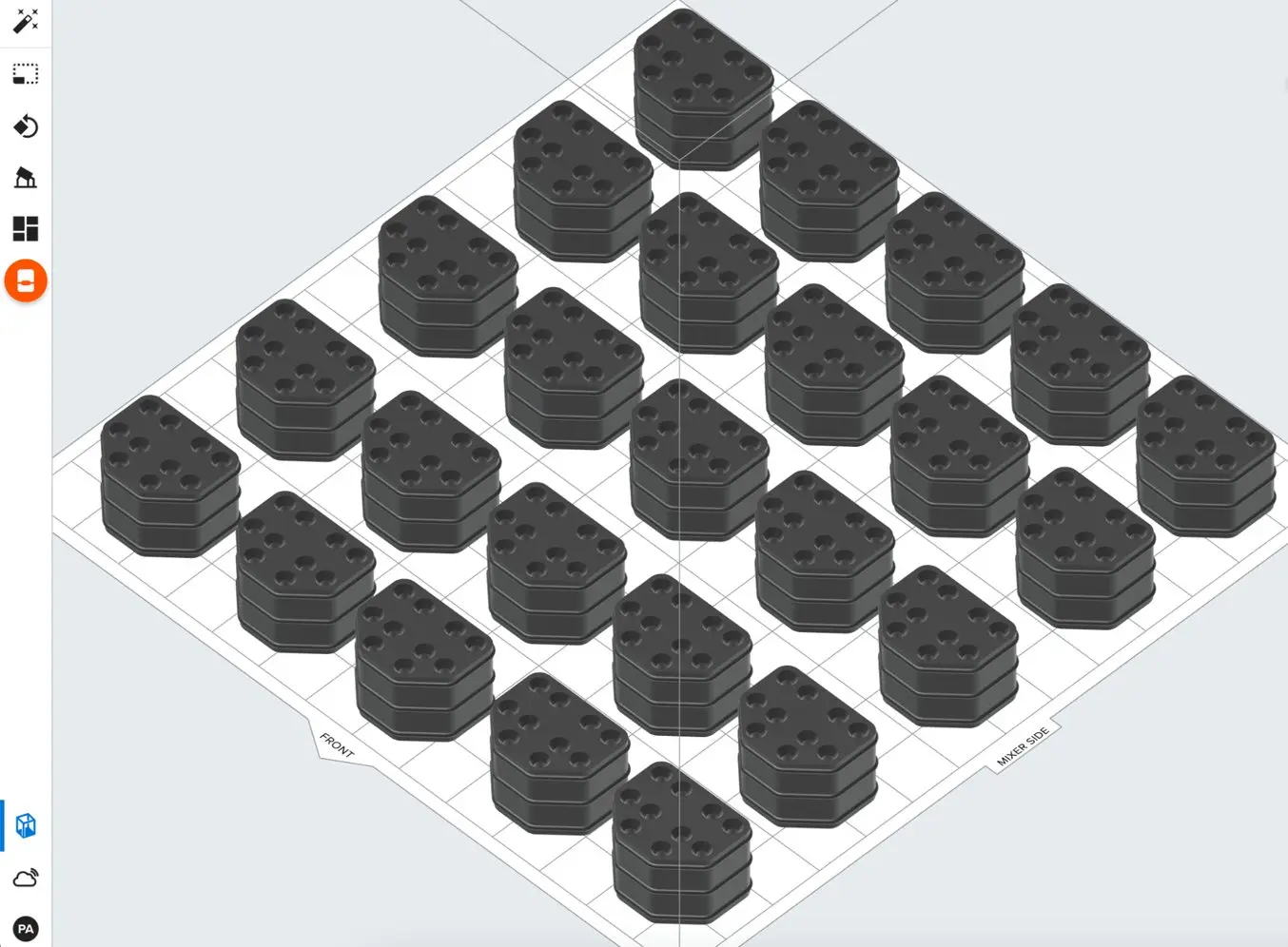
CAD-Datei der Verbinderdichtungen von HGM Automotive Electronics in der Software PreForm. Neun Kabel führen durch die ca. einen Zentimeter dicke Dichtung. Aufgrund der komplizierten Geometrie mit feinen Details ist der Werkzeugbau für den Spritzguss oder das Gießen von Flüssigsilikon schwierig. Die 25 Verbinderdichtungen können auf dem Form 3+ in 4 Stunden und 30 Minuten gedruckt werden.
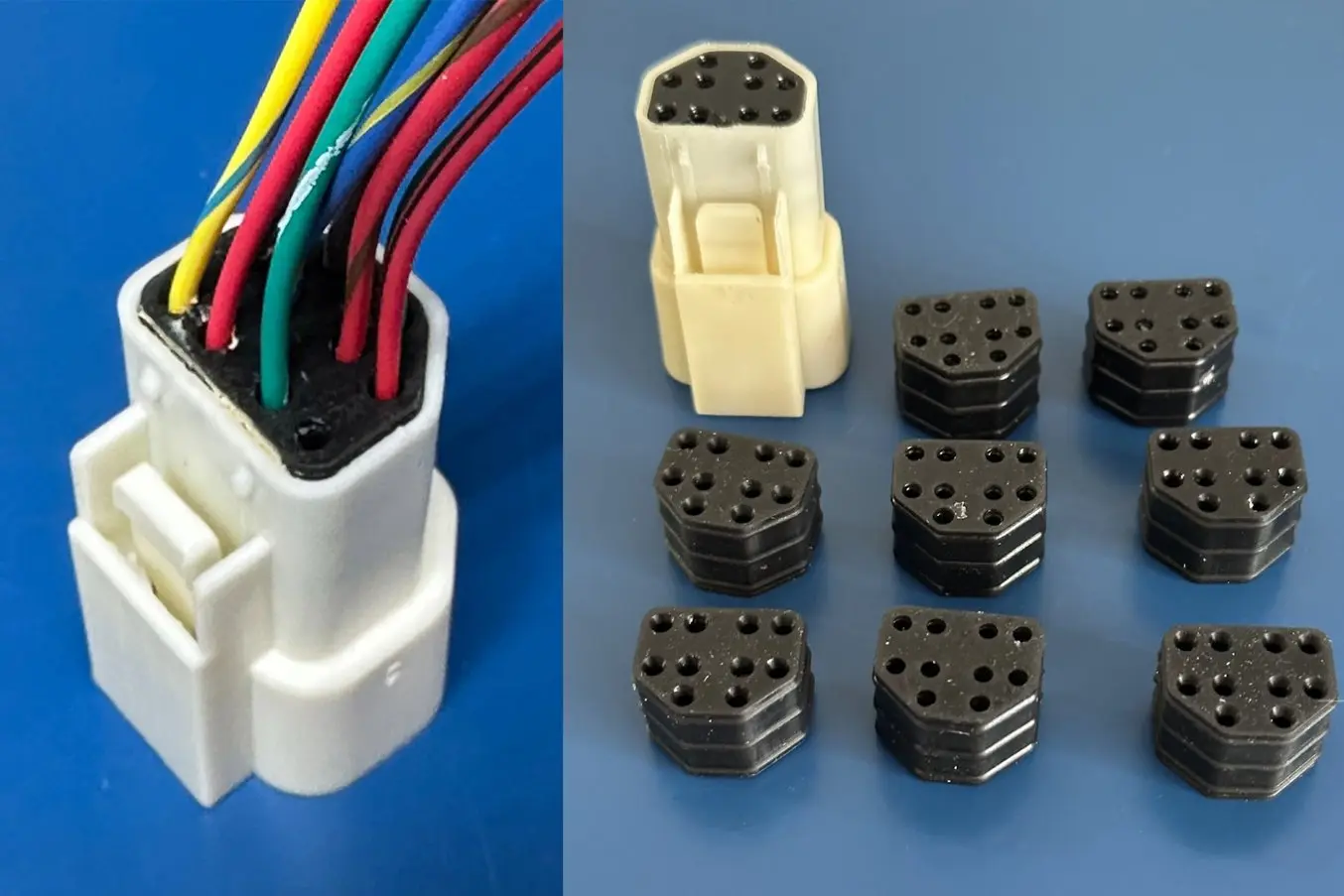
3D-gedruckte Verbinderdichtungen, mit Gehäuse und Elektronik zusammengebaut.
„Es ist eigentlich das perfekte Material, weil es dem Produktionsmaterial so sehr ähnelt.“
Guy Cardwell, Leiter der Forschung und Entwicklung bei HGM Automotive Electronics
Dank Silicone 40A Resin kann HGM den Fertigungsprozess für Kleinserien im eigenen Haus behalten, und auch die vielfältigen Einsatzmöglichkeiten des Materials sind für das Unternehmen attraktiv. Schon jetzt hat das Team weitere Anwendungen außer der Verbinderdichtungen ins Auge gefasst. Der Hauptvorteil des neuen Materials ist seine starke Ähnlichkeit zum Produktionsmaterial, durch die es für die Anwendungen von HGM Automotive Electronics ideale Eigenschaften bietet, vor allem hinsichtlich Elastizität, Reißfestigkeit und Flexibilität.
„Silicone 40A Resin verleiht mir die Flexibilität, Designs zu verwirklichen, die vorher nur mit einem sehr teuren und zeitaufwendigen Formprozess möglich waren. Das erlaubt uns, neue Märkte zu erschließen und Produkte herzustellen, deren Fertigung bisher unbezahlbar teuer oder kompliziert gewesen wäre. Es gibt zwar andere 3D-Drucklösungen, die eine Art elastisches Material drucken können, aber nur die SLA-Drucker von Formlabs mit Silicone 40A Resin konnten weiche Verbinderdichtungen fertigen, die der Qualität und Haltbarkeit von Formteilen aus Silikon oder TPU entsprechen.“
Guy Cardwell, Leiter der Forschung und Entwicklung bei HGM Automotive Electronics
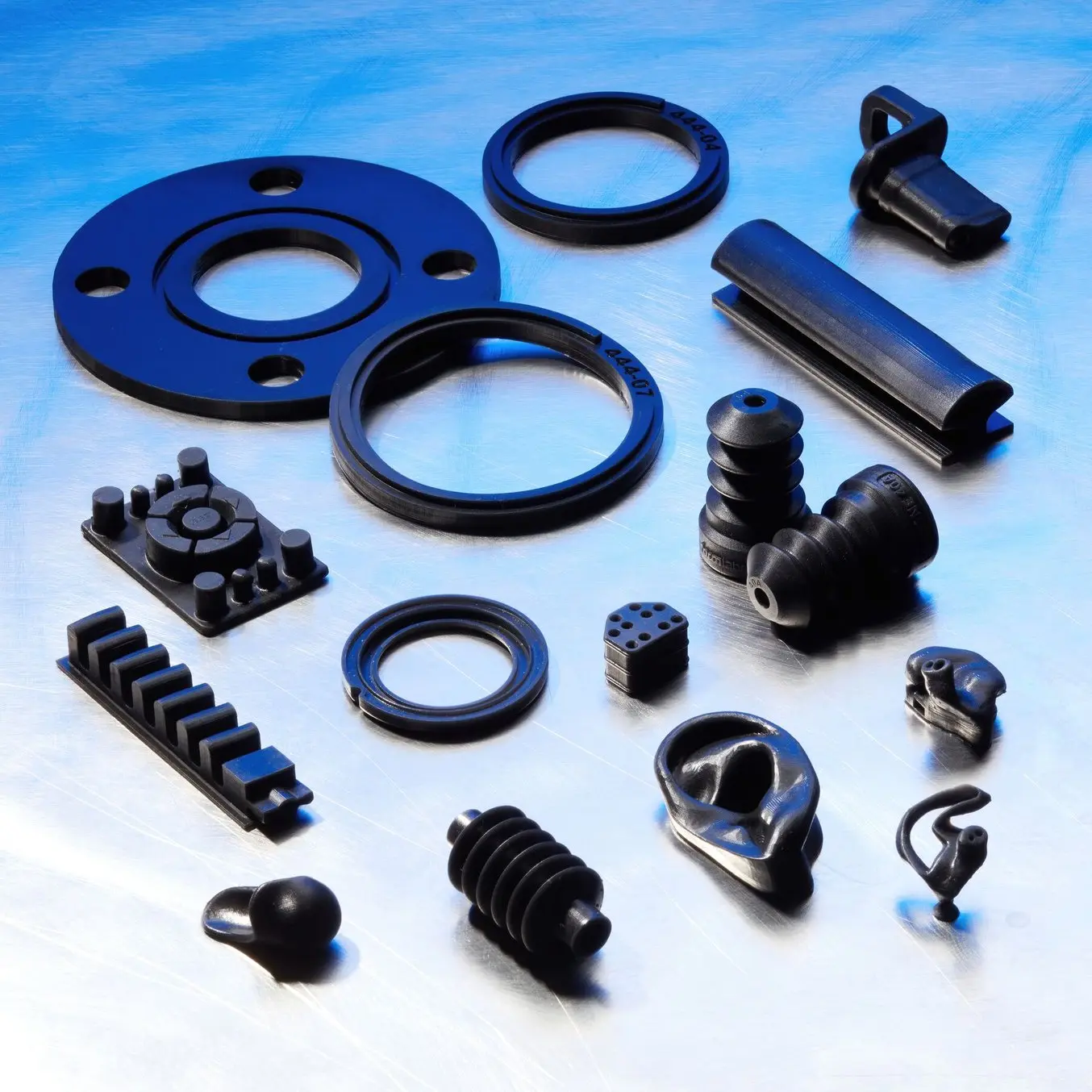
Einführung in Silicone 40A Resin
In diesem Webinar führt Sie unser Expertenteam für 3D-Druck durch die zentralen Vorteile und Anwendungsbereiche von Silicone 40A Resin und stellt die Materialeigenschaften und den Arbeitsprozess dieses Kunstharzes vor.
Vom Test zum Triumph: Silicone 40A Resin erfüllt die Branchenanforderungen an thermische und chemische Beständigkeit
„Silicone 40A Resin weist in Bezug auf Biegsamkeit und Verarbeitbarkeit genau die Eigenschaften auf, die wir für diese Anwendung brauchen. In unseren bisherigen Tests entsprach seine chemische Beständigkeit dem, was wir von einem gegossenen oder spritzgegossenen Silikon für diese Anwendung erwartet hätten.“
Guy Cardwell, Leiter der Forschung und Entwicklung bei HGM Automotive Electronics
In der Automobilindustrie sind häufig wasserdichte Versiegelungen gefragt, die eine Tiefenbewertung von einem bis zu zwei oder drei Metern bestehen, je nach Anwendungsfall. Zusätzlich gibt es Anforderungen an die chemische Beständigkeit gegenüber allen standardmäßigen Automobilflüssigkeiten, in erster Linie Wasser, Öl und Getriebeflüssigkeit. Um die Bauteile zu testen, druckte Cardwell mehrere Proben und führte im Motorraum seines Autos Funktionstests an ihnen durch. Die 3D-gedruckten Silikonteile wurden unter normalen Betriebsbedingungen im Motorraum gelassen, um ihre Temperatur- und Chemikalienbeständigkeit über mehr als sechs Wochen zu prüfen.
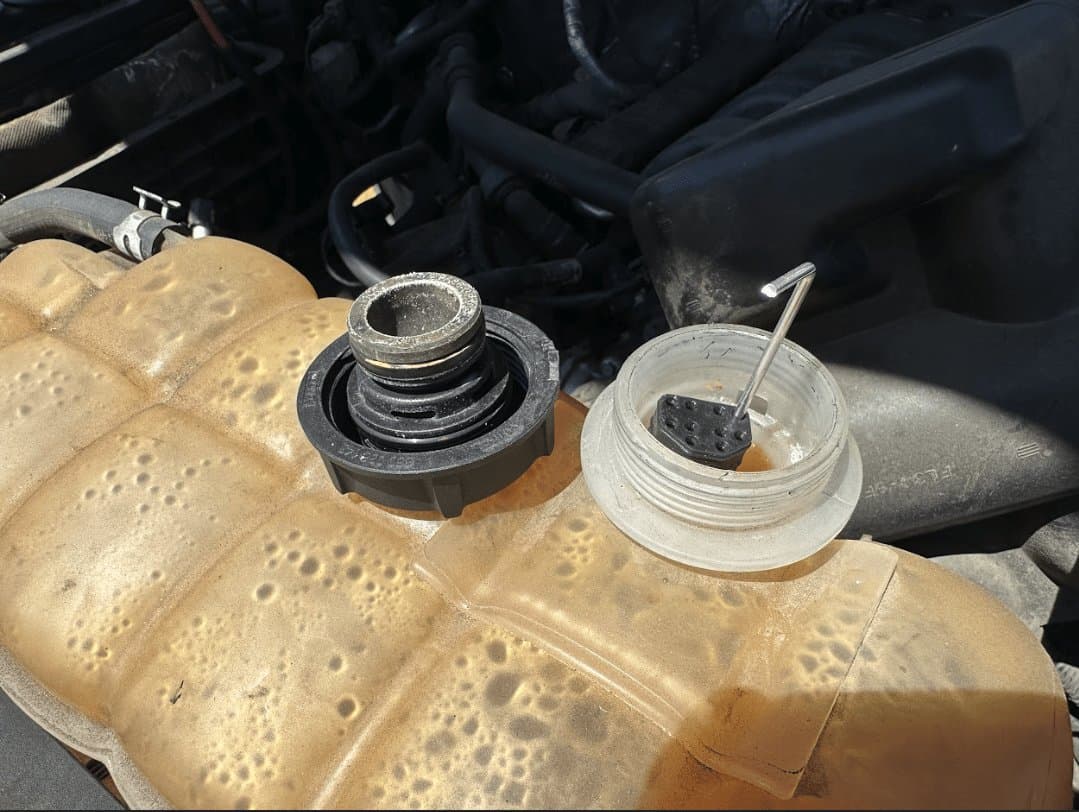
3D-gedruckte Verbinderdichtungen aus Silicone 40A Resin im Feldtest durch HGM Automotive Electronics in einem Kühlmittelbehälter eines Automotors.
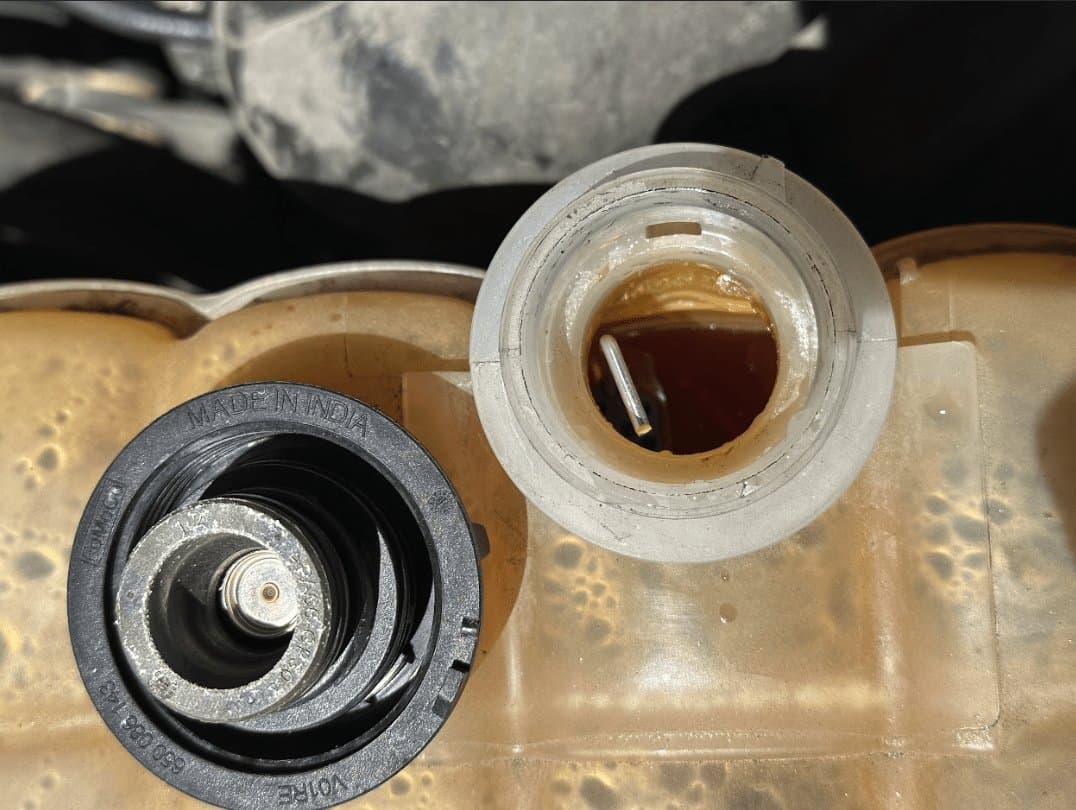
„Wir haben sie bei Temperaturwechseln in verschiedenen Flüssigkeiten im Motorraum gelassen. Getestet haben wir mit Wasser, statisch mit Getriebeflüssigkeit und mit Frostschutzmittel“, berichtet Cardwell. Er fügt hinzu: „Wo diese Dichtungen hauptsächlich das Eindringen verhindern, das ist typischerweise Wasser.“ Nach sechs Wochen der thermischen Zyklen und Tests in verschiedenen Flüssigkeiten hebt Cardwell die Wasserdichtigkeit und die Temperaturbeständigkeit von Silicone 40A Resin hervor. Bei Automobilelektronik treten Temperaturen zwischen -40 °C und 105 °C auf.+ Mit seiner Glasübergangstemperatur (Tg) von -107 °C und thermischer Beständigkeit zwischen -25 °C und 125 °C entsprach Silicone 40A Resin den Anforderungen des Teams an die Temperaturbeständigkeit vollkommen. „Ich bin bei den Tests, die wir mit dem Material durchgeführt haben, davon ausgegangen, dass es sich ähnlich verhält wie ein vergleichbares spritzgegossenes Silikon seiner Art“ – und das war auch der Fall. Die Materialeigenschaften von Silicone 40A Resin stimmten vollkommen mit den Ansprüchen an ein Material für die Endverwendung überein, was dieses Material zur perfekten Ergänzung für das Portfolio des Unternehmens machte.
Nach der Durchführung ausgiebiger Praxistests ist das Team von HGM höchst zufrieden mit dem neuen Kunstharz aus 100 % Silikon und seiner Eignung für seine Anforderungen. Das Team plant, das Material für Verbinderdichtungen für die Endverwendung einzusetzen, für voraussichtlich 500 bis 1000 Einheiten pro Jahr. Cardwell möchte die Verwendung des Kunstharzes sogar noch weiter ausdehnen und fügt hinzu: „Es gibt mindestens vier Produkte, die sich sofort anbieten, allein im Bereich der Verbinder.“
Zukünftige Innovationen von HGM Automotive Electronics möglich gemacht
Silicone 40A Resin hat HGM Automotive die Flexibilität verliehen, Designs zu verwirklichen, die sonst nur mit teuren und zeitintensiven Prozessen möglich wären, und somit neue Märkte zu erkunden.
„Ich kann mich erinnern, wie ich verschiedenen Mitarbeitern in der Firma [ein paar Probeteile] gezeigt habe, und allen ist die Kinnlade runtergefallen und sie fragten, ‚Wow, wie hast du das gemacht?‘ Es ist also ein sehr spannendes Material für uns. Man weiß nicht, was die zukünftigen Anwendungen sein werden, bis man es tatsächlich verwendet, erst dann bekommt man ein echtes Verständnis davon. Ich gehe nicht davon aus, dass wir bei den Verbindern aufhören werden. Wir werden damit eine Menge anderer Sachen verwirklichen. Das steht für mich außer Frage.“
Guy Cardwell, Leiter der Forschung und Entwicklung bei HGM Automotive Electronics
Für die Zukunft freut sich Cardwell darauf, seiner Kundschaft verkünden zu können, das er problemlos individuelle Teile aus einem weichen Gummimaterial herstellen kann. Zu seinen Plänen gehört die Entwicklung verschiedener Arten individueller Dichtungen und neuartiger Silikonisolatoren für Hochspannung wie dem unten abgebildeten.

3D-gedruckte Zündkerzenisolatoren aus Silicone 40A Resin.
“Kann ich sagen, was ich morgen mit 3D-gedrucktem Silikon anstellen werde? Nein, aber ich bin gespannt, es herauszufinden.“
Guy Cardwell, Leiter der Forschung und Entwicklung bei HGM Automotive Electronics