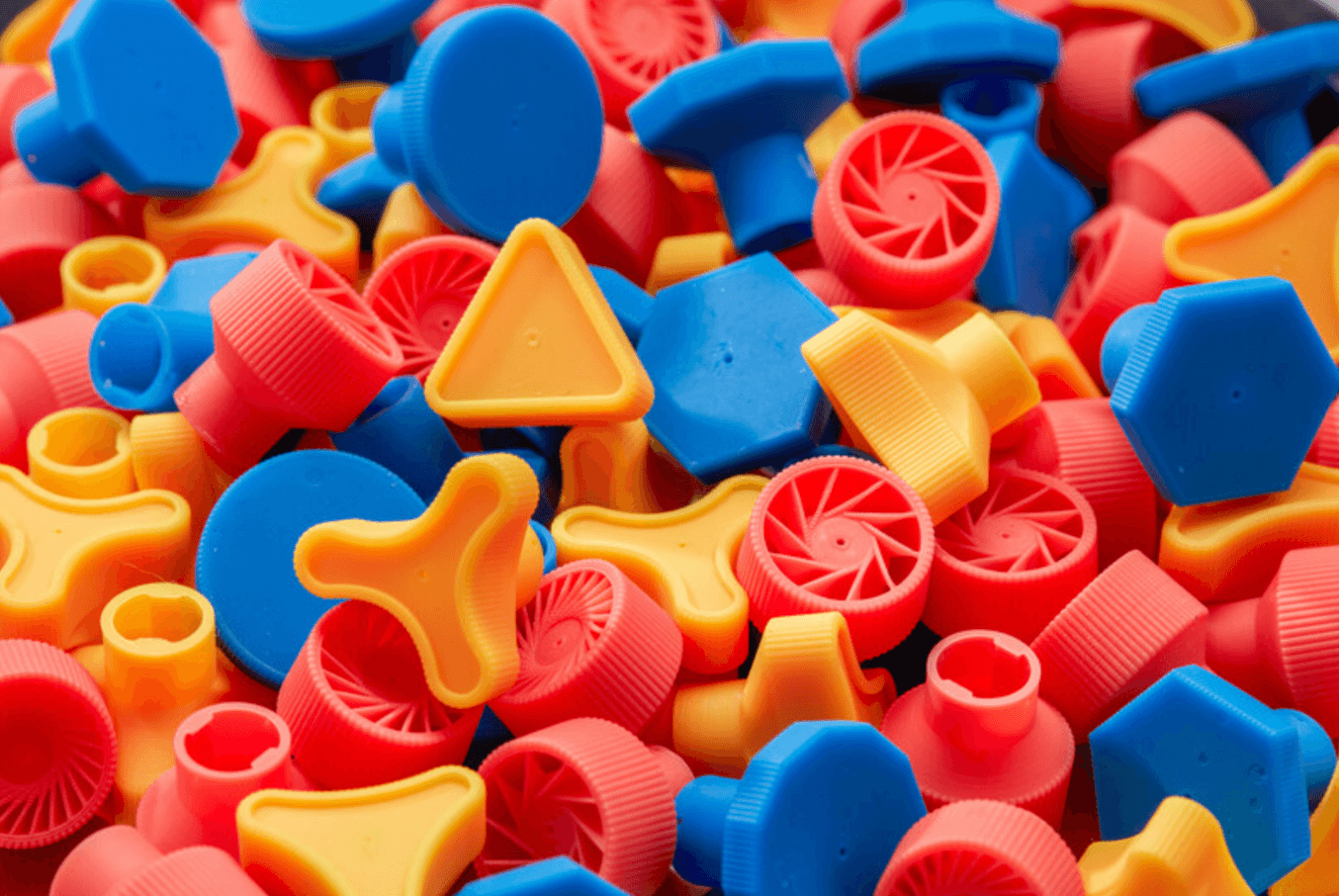
The Digital Factory ist eine Konferenz zu fortgeschrittener Fertigung: Sie behandelt, wie Unternehmen moderne Technologieinnovationen nutzen, um neue Standards in Sachen Effizienz zu setzen und neue bewährte Praktiken zu entwickeln. Häufig laufen diese von High-Tech getriebenen Initiativen irgendwo versteckt in großen Organisationen ab, beispielsweise in F+E-Teams oder Sonderprojektgruppen. The Digital Factory ist eine Gelegenheit, bei der Experten aus der Praxis und Führungskräfte zusammenkommen, Ideen vorschlagen und austauschen und erfahren, wo Industrie-4.0-Projekte in anderen Bereichen erfolgreich waren.
Auf der 2019er Konferenz in Boston wollten wir zeigen, wie einige dieser Innovationen und bewährten Praktiken zusammenkommen. Dazu veranstalteten wir eine interaktive Demo, bei der die Teilnehmer einen modernen Montageprozess mitmachten, wobei Technologien von Amazon Web Services, Tulip, Vention, RightHand Robotics und natürlich auch von Formlabs zum Einsatz kamen.
Die Teilnehmer wurden eingeladen, eine Sonderedition von The Public Radio zu bauen und zu konfigurieren. Es handelt sich dabei um ein Radio für nur einen einzigen Sender, das von Spencer Wright und Zach Dunham entwickelt wurde. Dieser Beitrag erklärt, wie wir die Materialeigenschaften von Stereolithografie-Kunstharzen (SLA) und die Skalierbarkeit des 3D-Druckers Form 3 genutzt haben, um Kunststoffteile und -baugruppen bedarfssynchron zu fertigen. Außerdem wurden weitere Smart-Factory-Technologien wie maßgefertigte Werkbänke von Vention und Sensoren und Software von Tulip und AWS eingesetzt. Wir berichten auch etwas von unserem Design for Manufacturing beim Designprozess von SLA-Teilen und wie diese Schritte Ihnen dabei helfen können, den Durchsatz zu optimieren und die Nachbearbeitungszeit zu verringern.
Der Arbeitsablauf in der Pop-Up-Fabrik
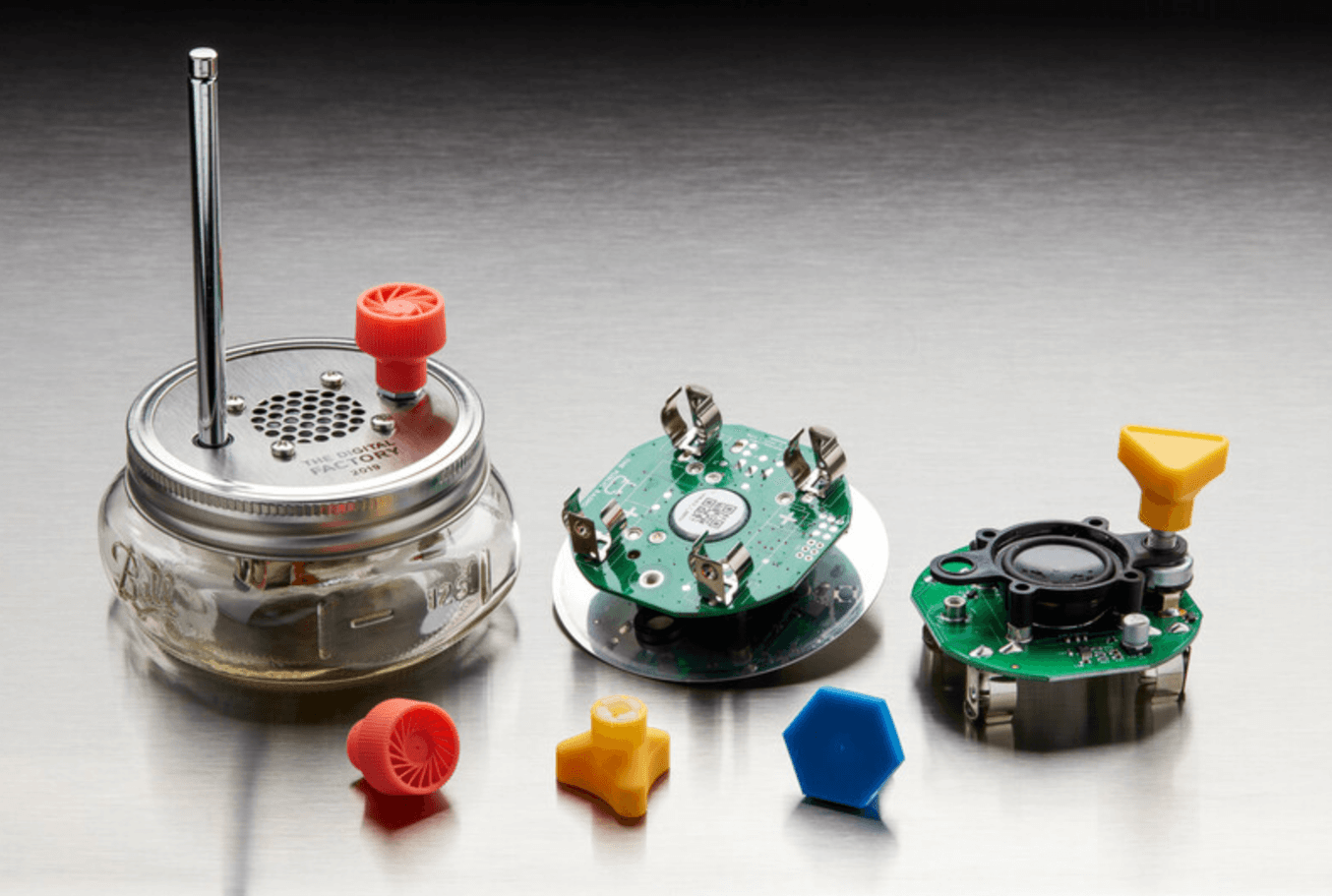
Der Prozess beginnt an einem Tulip-gestützten Terminal, wo man einen Radiosender und den gewünschten Drehknopf aussucht. Ein Etikettendrucker am Terminal gibt einen angepassten QR-Code-Aufkleber aus, der dann an den Tulip-Werkbänken gescannt wird.
Jede Werkbank bietet 3D-gedruckte Drehknopfbaugruppen, Batterien, Antennen und Radio-Unterbaugruppen. Hinzu kommen bekannte Fertigungswerkzeuge wie eine Programmiervorrichtung aus Laserschnitt- und 3D-Druckteilen. Das Display an der Arbeitsstation führt Sie durch die einzelnen Schritte und Sensoren protokollieren Ihre Handlungen, um sicherzustellen, dass nichts übersehen wurde. Die Inventaränderungen werden auf die Minute genau erfasst.
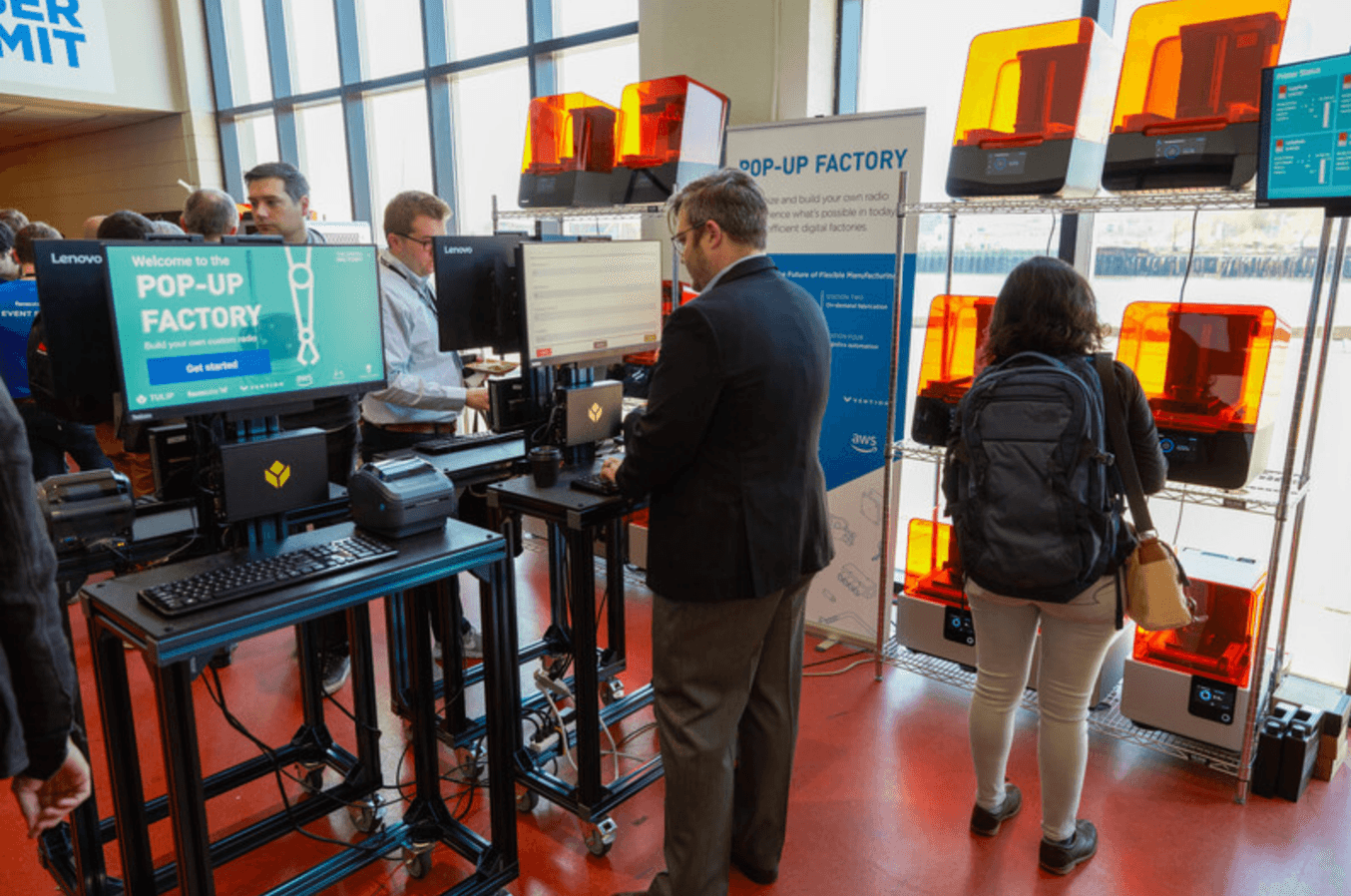
Teilnehmer konfigurieren ihre Radios an Tulip-Terminals und erstellen ihren Arbeitsauftrag, während Drucker der Typen Form 2 und Form 3 im Hintergrund laufend neue Drehknöpfe produzieren.
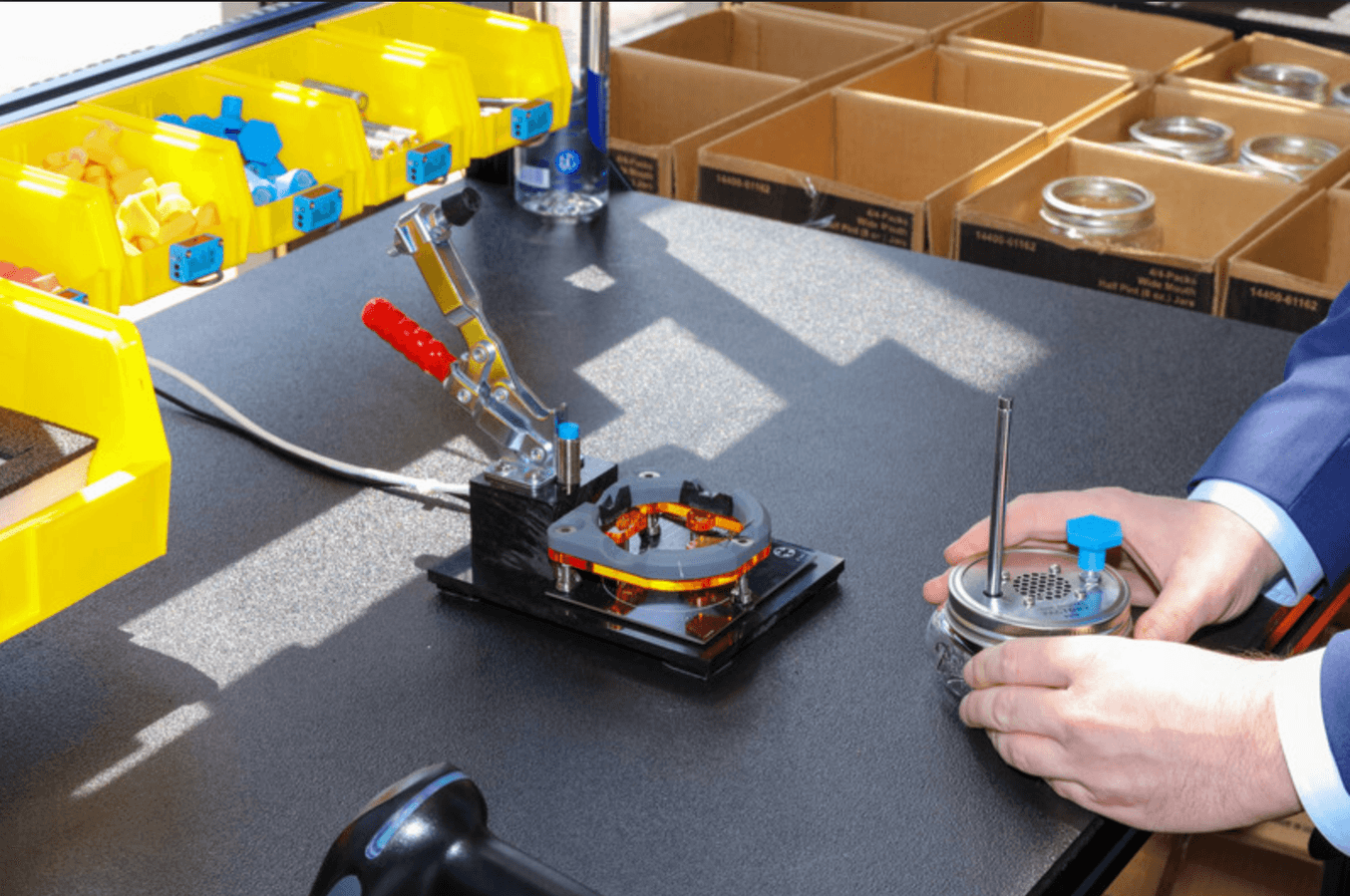
Teilnehmer montieren und programmieren Radios an Werkbänken von Vention, die mit Hardware von Tulip ausgerüstet sind. Ein großer Bildschirm zeigt schrittweise Anweisungen an und Sensoren erfassen Inventar, Zyklen und andere wichtige Fertigungsdaten.
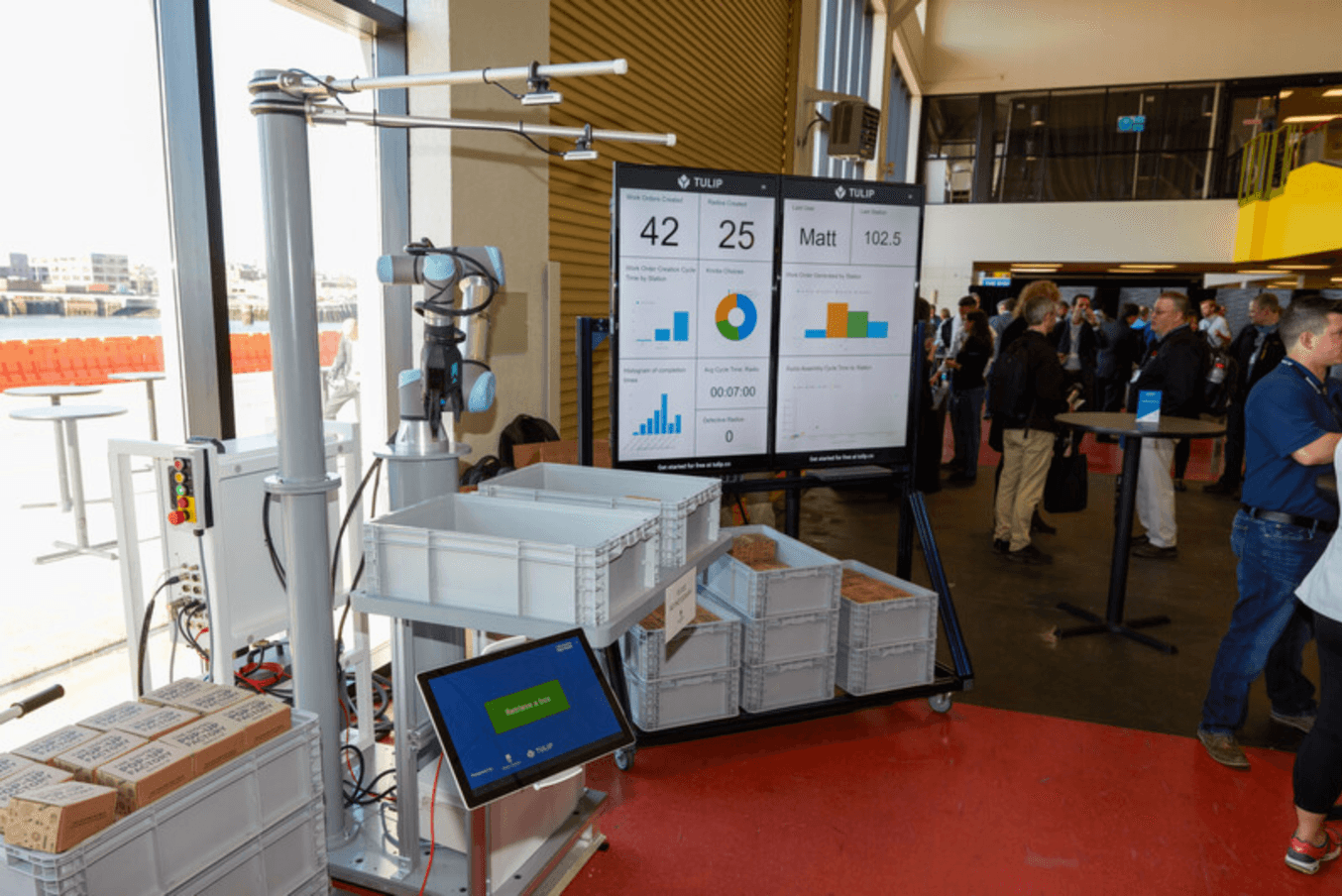
Eine Zelle von RightHand Robotics übergibt einen Karton.
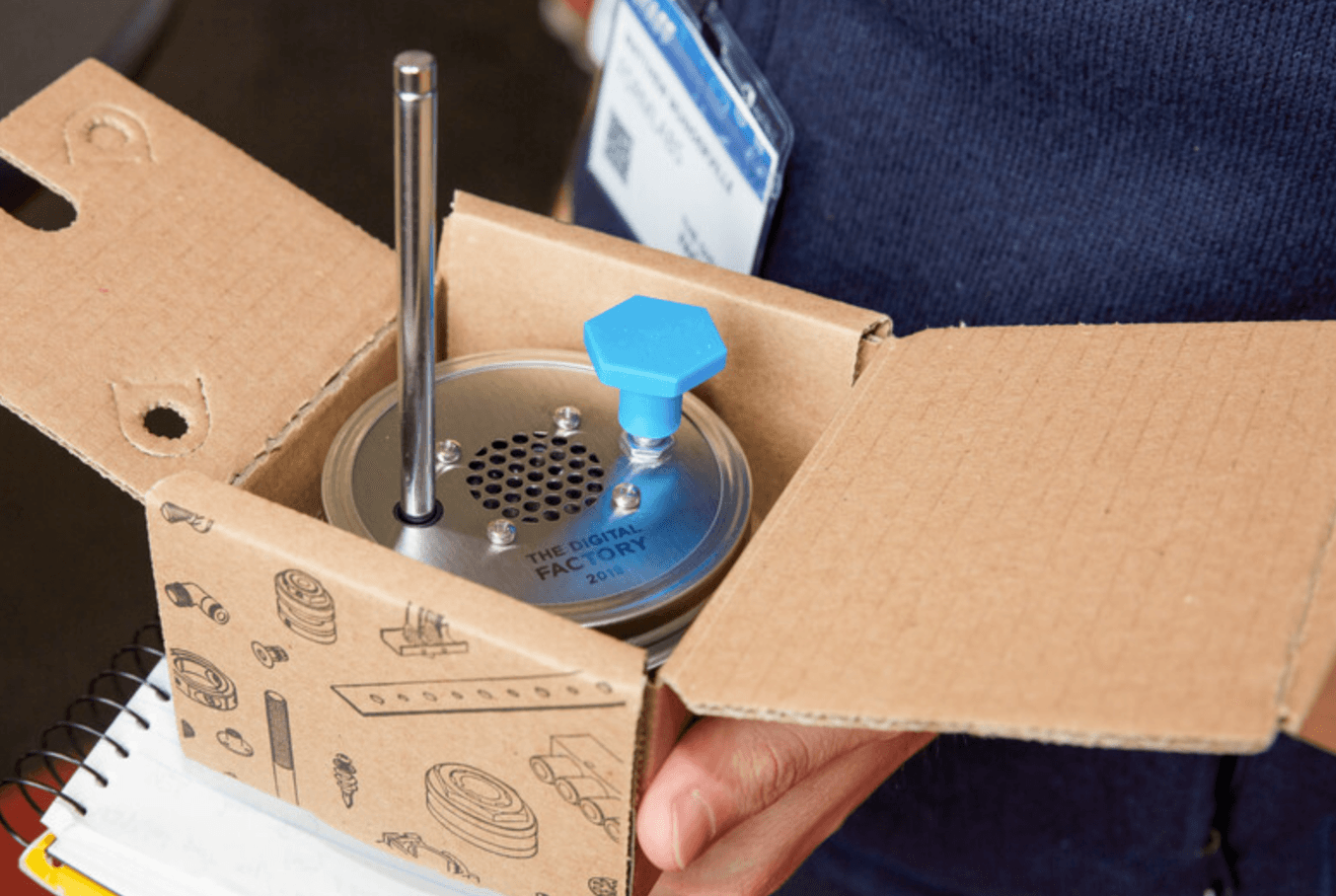
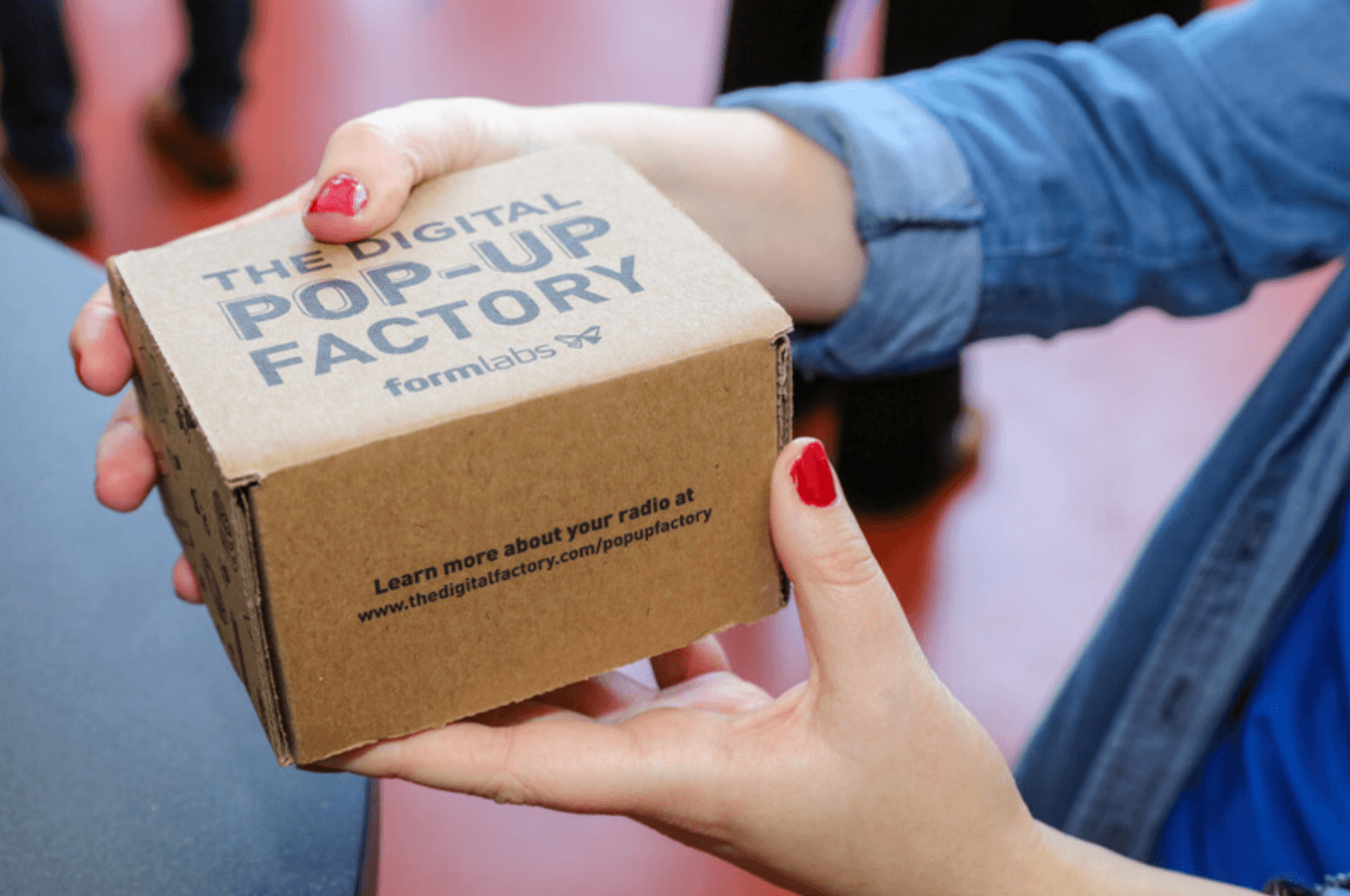
Eine fertige Digital-Factory-Edition von The Public Radio in ihrer Verpackung.
Design für additive Fertigung und Montage
Die 3D-gedruckten Drehknöpfe mussten bestimmte ästhetische und funktionale Anforderungen erfüllen:
-
Wir wollten The Public Radio farbenfrohe Akzente verleihen, darum haben wir Optionen in mehreren Farben bereitgestellt.
-
Wir wollten die Flexibilität des Drucks auf Abruf veranschaulichen und boten 12 einzigartige Formen an. Die roten Drehknöpfe, die am Morgen in der Fertigung eingesetzt wurden, hatten also ein anderes Design als ihre Gegenstücke am Nachmittag.
-
Wir benötigten ein Design, das einen guten Formschluss mit dem D-förmigen Stift von The Public Radio eingeht und sich auch bei groberer Behandlung nicht löst.
-
Die Druckkraft, mit der der Drehknopf bei der Montage aufgesteckt werden sollte, musste im Allgemeinen mit der Hand aufgewendet werden können, damit der Montageprozess nicht verlangsamt wurde und keine zusätzlichen Werkzeuge notwendig waren.
Um diesen Anforderungen zu erfüllen, haben wir zwei Kunstharze kombiniert: unser Color Kit, mit dem wir eine große Bandbreite an Farben anbieten konnten, und Durable Resin, ein besonders schlagfestes technisches Material mit guter Dehnung.
Die Dehnung war bei den Rippen im Teiledesign erforderlich, damit der D-förmige Stift von The Public Radio wirksam umschlossen wird, das Teil beim Aufstecken aber genug nachgibt, um keinen zu großen Kraftaufwand zu erfordern.
Der Einsatz aus Durable Resin musste außerdem das Außenteil aus Color Kit fixieren und eine freie Rotation verhindern.
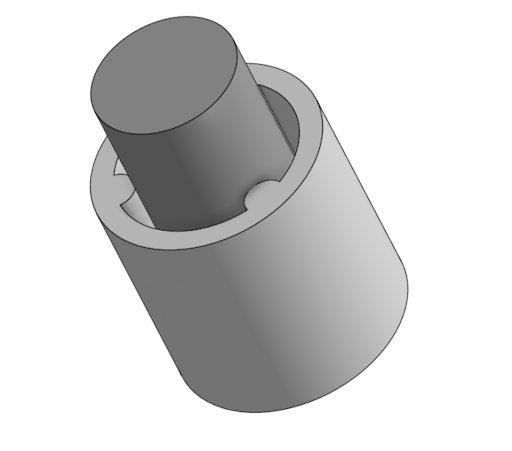
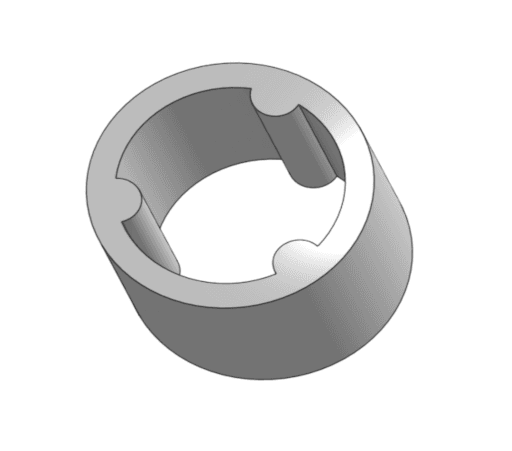
Beispiel einer typischen Eindrückrippengeometrie bei Kunststoffteilen
Die Produktion
Nachdem die Designs funktionell validiert wurden, haben wir kleinere Anpassungen vorgenommen und sie für die Produktion vorbereitet. Alle Teile der gedruckten Drehknopf-Baugruppen mussten selbsttragend sein, sich leicht von der Konstruktionsplattform entfernen lassen und platzoptimiert beieinander stehen, um die Anzahl der erforderlichen Druckvorgänge zu verringern. Da die Drehknopfgeometrien prinzipiell ein geschlossenes Rohr sind, wurden außerdem winzige Belüftungsöffnungen hinzugefügt, um eine Hohlkörperbildung zu verhindern.
In ähnlicher Weise wurden die Einsätze aus Durable Resin an der Basis gekerbt, um die Hohlkörperbildung zu verhindern und die Entfernung des Teils zu erleichtern.
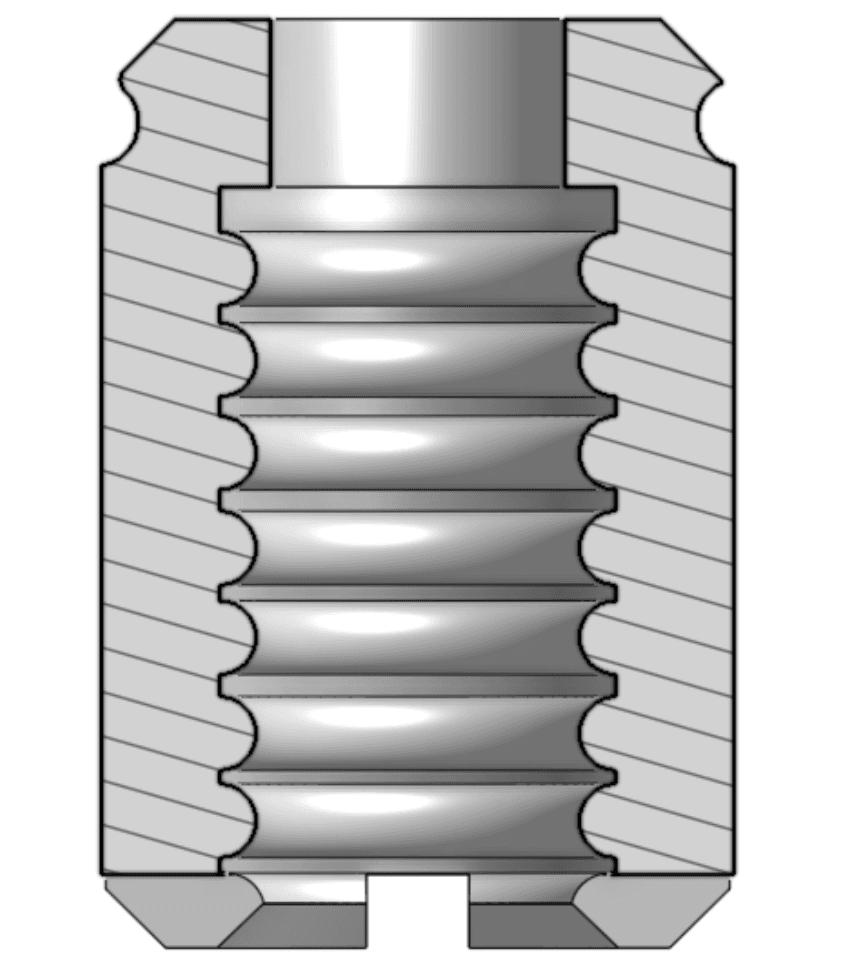
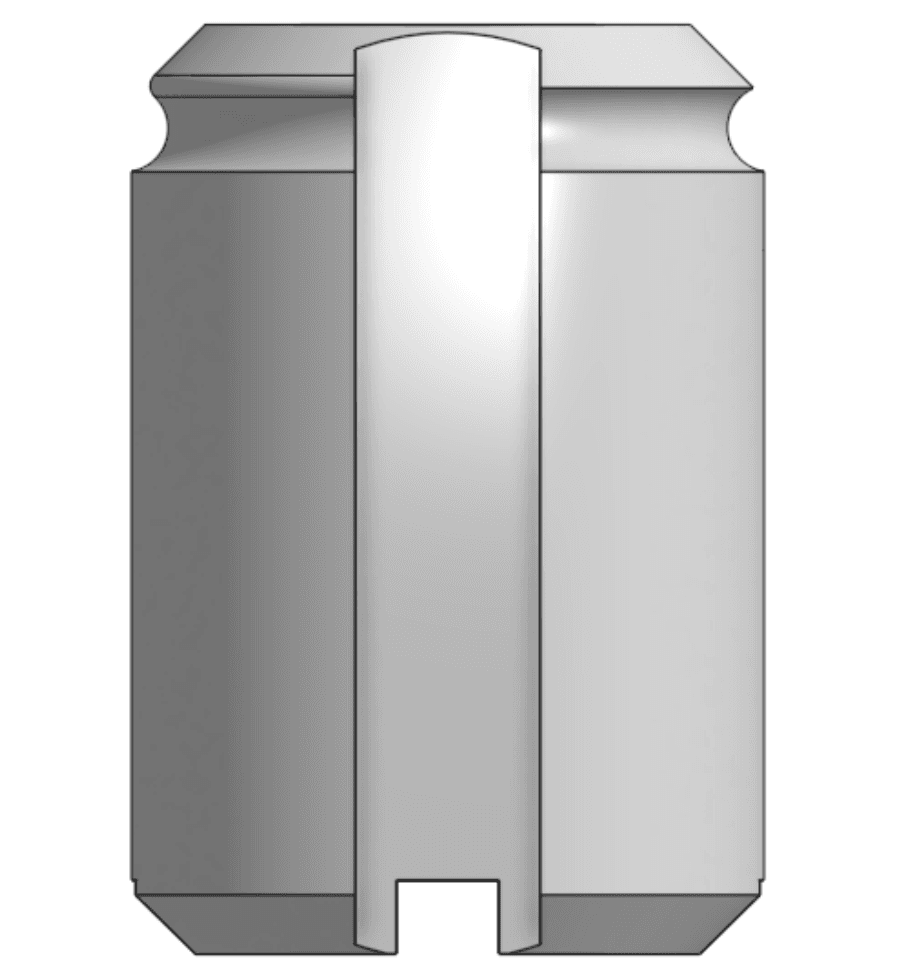
Design for Manufacturing des Einsatzes aus Durable Resin und Baugruppendetails: Die gekerbte und gefaste Basis erleichtert die Entfernung des Teils. Ein Schnappring oben und Nute dienen dazu, den Drehknopf anzubringen und ein Durchdrehen zu verhindern.
Die Einsätze aus Durable Resin wurden ziemlich eng auf die Konstruktionsplattform gepackt: insgesamt 81 pro Druckvorgang. Color Kit mit größerem Durchschnittsdurchmesser ergab weniger Teile pro Druckvorgang: abhängig vom Design 30 bis 40.
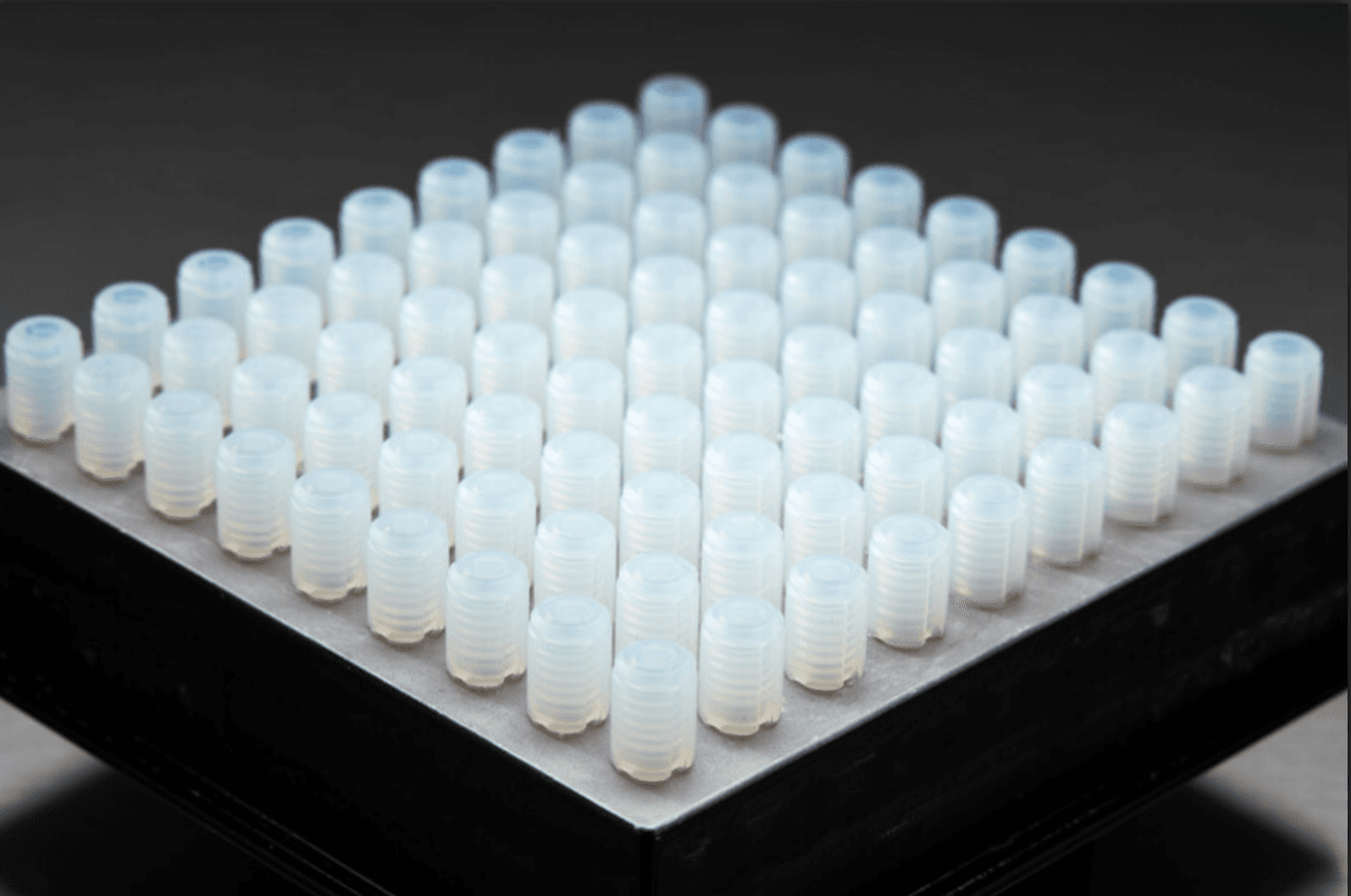
Einsätze aus Durable Resin auf der Konstruktionsplattform.
Bei 600 montagebereiten Radiosätzen wollten wir wenigstens 400 Stück von jeder Farboption auf Lager haben. Mit 400 roten Drehknöpfen, 400 blauen Drehknöpfen und 400 gelben Drehknöpfen brauchten wir auch einen Einsatz aus Durable Resin pro Drehkopf, wodurch die Anzahl der Teile für die zweitägige Demo auf 2400 Druckteile stieg.
Insgesamt waren 55 Druckdurchgänge nötig, um 2400 Teile für 1200 zusammengesetzte Drehknöpfe zu fertigen. Wir haben die Arbeitslast auf betriebsinterne Drucker und unsere Vorführungsgeräte vor Ort verteilt, damit am ersten Morgen von The Digital Factory gleich genug Drehknopf-Baugruppen an den Arbeitsstationen auf Lager waren.
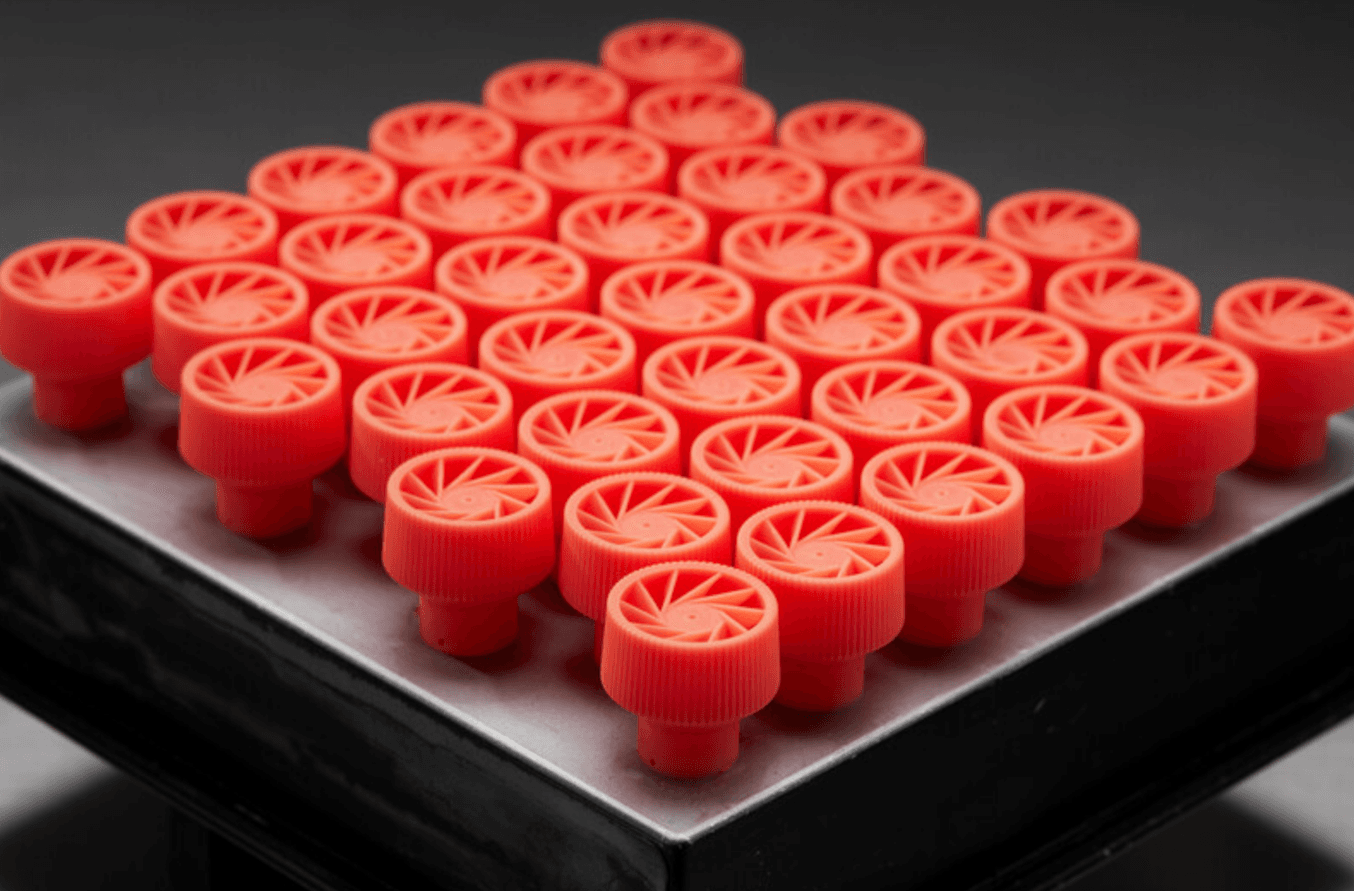
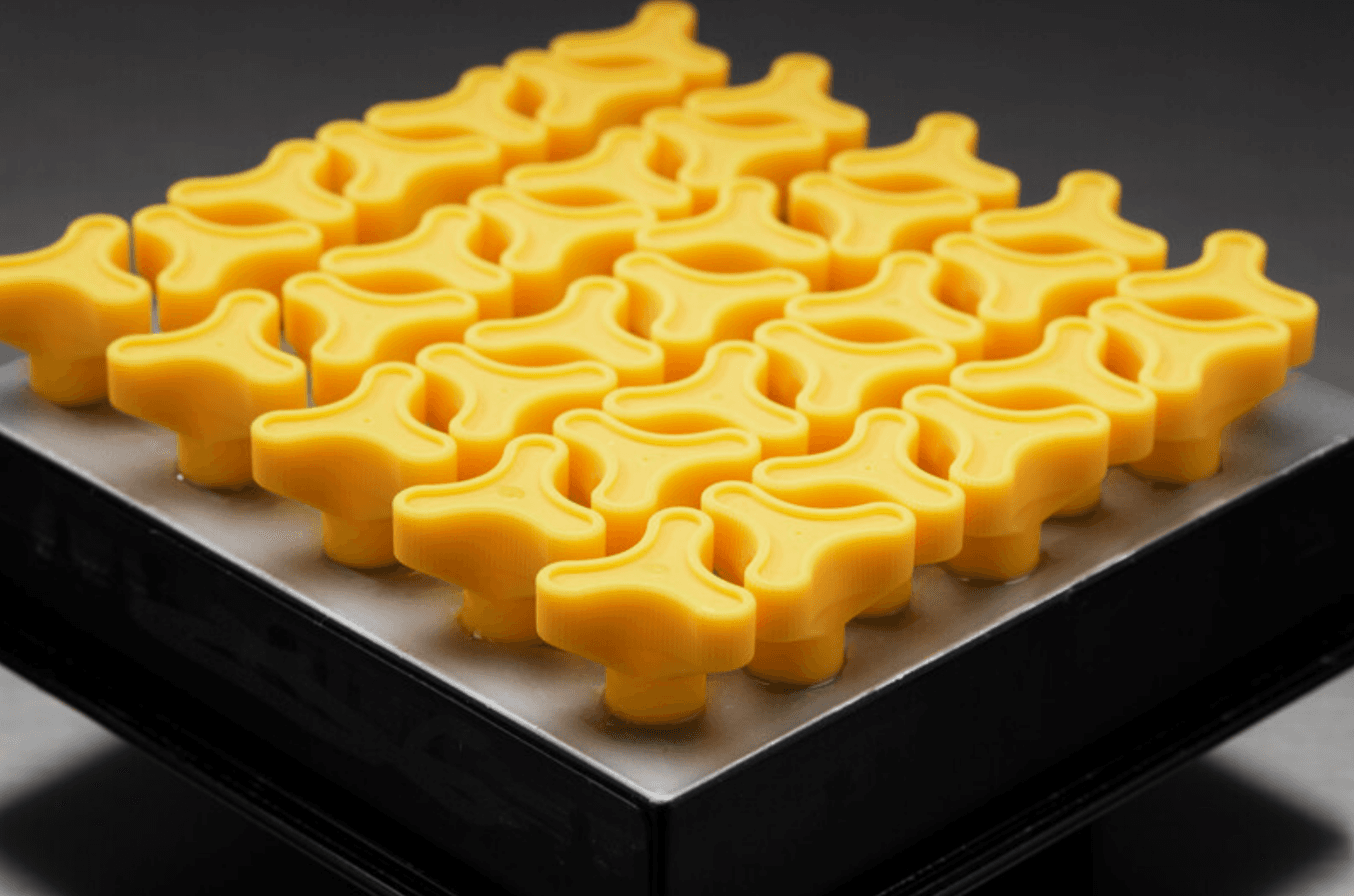
Von der Nachfrage lernen und reaktive Arbeitsprozesse schaffen
Echtzeitinformationen zur Produktnachfrage, etwa die Erfassung der beliebtesten Farboption, kombiniert mit den Werkzeugen zur Herstellung der Teile vor Ort schafft die Möglichkeit eines eng integrierten Kreislaufs aus Angebot und Nachfrage. So werden ein Überangebot und unnötige Lagerbestände verhindert. Es ist hinlänglich bekannt, dass es sehr schwer ist, die bevorzugten Farben bei Konsumgütern vorauszusagen. Viele Unternehmen betreiben einen beträchtlichen Aufwand, um Programme und Techniken zu entwickeln, mit denen die Genauigkeit der Vorhersage verbessert werden kann..
Während unserer zweitägigen Pop-Up-Fabrik war Sonic Red mit Abstand die beliebteste Farbe, etwa zweimal so beliebt wie die Optionen Blue oder Mellow Yellow. Bei zukünftigen Pop-Up-Fabriken könnten wir den Produktionsplan entsprechend anpassen oder ein weiteres Experiment durchführen, z. B. dieselbe Drehknopfgeometrie bei allen drei Farben verwenden, um das Kundenverhalten besser zu verstehen.
Die Hersteller von heute sind mehr denn je dem Druck ausgesetzt, flexibel und gleichzeitig ultraeffizient zu sein. Die Pop-Up-Fabrik-Demo zeigt, wie Smart-Factory-Technologien wie Sensoren und Software sich perfekt mit agilen Fertigungsmethoden wie 3D-Druck kombinieren lassen.
Um mehr darüber zu erfahren, wie die führenden Hersteller von heute den 3D-Druck zur Innovation nutzen, lesen Sie einige unserer Fallstudien und erfahren Sie, wie Google, New Balance und Ashley Furniture 3D-Drucker und Kunstharze von Formlabs nutzen, um ihre Fertigungsprozesse umzustellen.