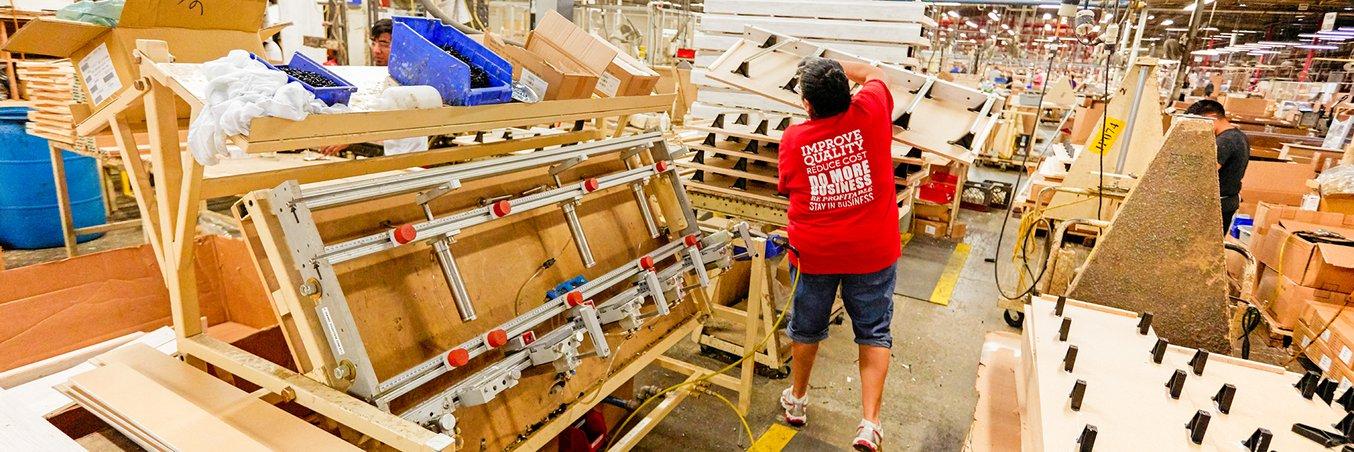
Trotz Jahrzehnten sich verändernder Märkte, unzähliger neuer Technologien und nie dagewesenem Arbeitskräftemangel ist Ashley Furniture immer weiter gewachsen. 2005 wurde das Unternehmen zum weltgrößten Möbelhersteller – ein Titel, den es noch heute trägt.
Ashley Furniture folgte einem steilen Erfolgskurs, von dem die meisten amerikanischen Unternehmen aus seiner Gründungszeit träumten. Das erste Werk wurde 1970 in Arcadia im US-Bundesstaat Wisconsin mit 35 Mitarbeitern eröffnet. Seitdem ist der Möbelhersteller zu einem weltweiten Unternehmen mit über 900 Geschäften auf dem ganzen Globus geworden. Die Werke von Ashley stellen wöchentlich mehr als 300 000 Möbelstücke her – das sind pro Jahr etwa 26 Millionen.
Ein aufmerksamer Blick in das Werk von Ashley in Arcadia enthüllt das Erfolgsrezept, und es ist tatsächlich ein Rezept. Wie bei den meisten modernen Herstellern findet man verschiedene Roboter, aber das Unternehmen hat noch keine Wunderlösung gefunden – und sucht auch nicht danach. Stattdessen konzentriert es sich auf ein Modell der ständigen Verbesserung. Es ist die Summe dieser Verbesserungen und eine Kultur, die sie fördert, die das Wachstum vorangetrieben und ihm zum unangefochtenen Spitzenplatz in der Möbelwelt verholfen haben.
Der 3D-Druck beispielsweise hat sich langsam in der Werkshalle durchgesetzt und zu einer schrittweisen Umorganisierung der Produktionsprozesse von der Fertigung bis zur Montage geführt.
Sehen Sie sich das Video an und erfahren Sie, wie Ashley Furniture von einer Idee zu 700 3D-gedruckten Teilen im Werk gelangt ist.
Eine Kultur der ständigen Verbesserung
Ständige Verbesserung ist die Hauptzutat beim Fertigungserfolg von Ashley Furniture. Die Fähigkeit, auf Veränderungen reagieren zu können, ist die einzige Konstante, wenn es darum geht, in der Fertigung konkurrenzfähig zu bleiben. Es bedarf aber mehr als nur einer Initiative oder eines Projekts, um neue Technologien und Praktiken zu integrieren, die einen fundamentalen Einfluss auf das Geschäft haben, und auch mehr als einer Anweisung aus der Führungsetage.
„Wenn wir diese Kultur der Veränderung nicht haben, wird das unser Wachstum einschränken. Wir müssen bereit sein, die Veränderung zu identifizieren und herauszufinden, wie wir sie am besten in unsere Prozesse und unsere Geschäftstätigkeit eingliedern können – und unseren Mitarbeitern nahebringen, wieso wir diese Veränderung vornehmen müssen, wie wir es tun können, und sie ermächtigen, uns dabei zu helfen“, so Vaughn Pieters, Senior Director of Casegood Operations von Ashley Furniture, der seit etwas über 25 Jahren im Unternehmen arbeitet.
3D-Druck ist ein klares Beispiel für das Engagement von Ashley gegenüber schlanker Produktion und Kaizen, mit von Mitarbeitern vorangetriebenen schrittweisen Änderungen, die zu bedeutenden Zeit- und Kosteneinsparungen bei der Markteinführung beigetragen haben. Sie haben zudem den Mitarbeitern dazu verholfen, produktiver zu sein und sich mehr auf kreative Arbeit zu konzentrieren.
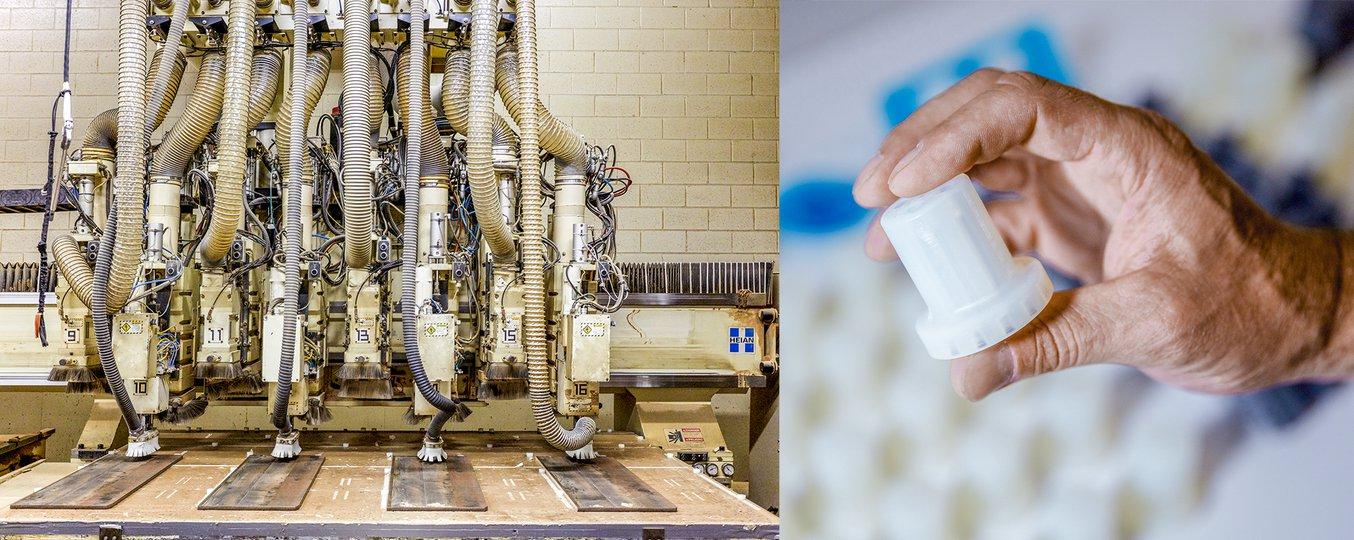
Hunderte von Führungsstiften aus Durable Resin werden auf den CNC-Oberfräsentischen im Werk von Ashley Furniture in Arcadia eingesetzt. Zuvor wurde für jede Platte eine eigene Vorrichtung hergestellt. Jetzt nutzen die Mitarbeiter ein Einrichteblatt, um die Stifte schnell auf einem einfachen Gittermuster zu versetzen.
„Wir haben mit einem einzigen einfachen Muster angefangen, da wir das Muster in wenigen Stunden fertigen konnten, anstatt es möglicherweise von einem internationalen Anbieter zu beziehen, was Wochen dauern würde. Wir konnten die 3D-Drucktechnologie nutzen, um einige unserer Fristen zu verkürzen und bessere und informiertere Entscheidungen mit unser Designabteilung zu treffen“, so Pieters
„Jetzt haben wir das bei der Art und Weise, wie wir 3D-Drucktechnologie zur Herstellung von Bauteilen nutzen, die uns dabei helfen, unsere täglichen Abläufe im Werk durchzuführen, noch ausgeweitet.“
Hartcodierung von Innovationskreisläufen
Die schlaue Frage eines Mitarbeiters war der Ausschlag für den Erfolg, den Ashley Furniture mit firmeninternem 3D-Druck hat. Die Technologie hat sich seitdem zu einem Problemlösungswerkzeug gewandelt, dessen Wert Mitarbeiter im ganzen Unternehmen vom CEO zum Fertigungsstraßenmitarbeiter verstehen und nutzen können, um Verbesserungsideen in die Tat umzusetzen.
„Einer der starken Aspekte des 3D-Drucks von Teilen ist, dass wir uns einigen Vorschlägen von Endbedienern anpassen können“, so Brian Konkel, Produktions- und Designingenieur bei Ashley Furniture. „Je mehr Bereiche wir mit 3D-Druckteilen haben, desto mehr sind die Mitarbeitern mit dem Prozess vertraut, und das hat neue Ideen und neuen Anfragen zur Produktionssteigerung mit sich gebracht.“
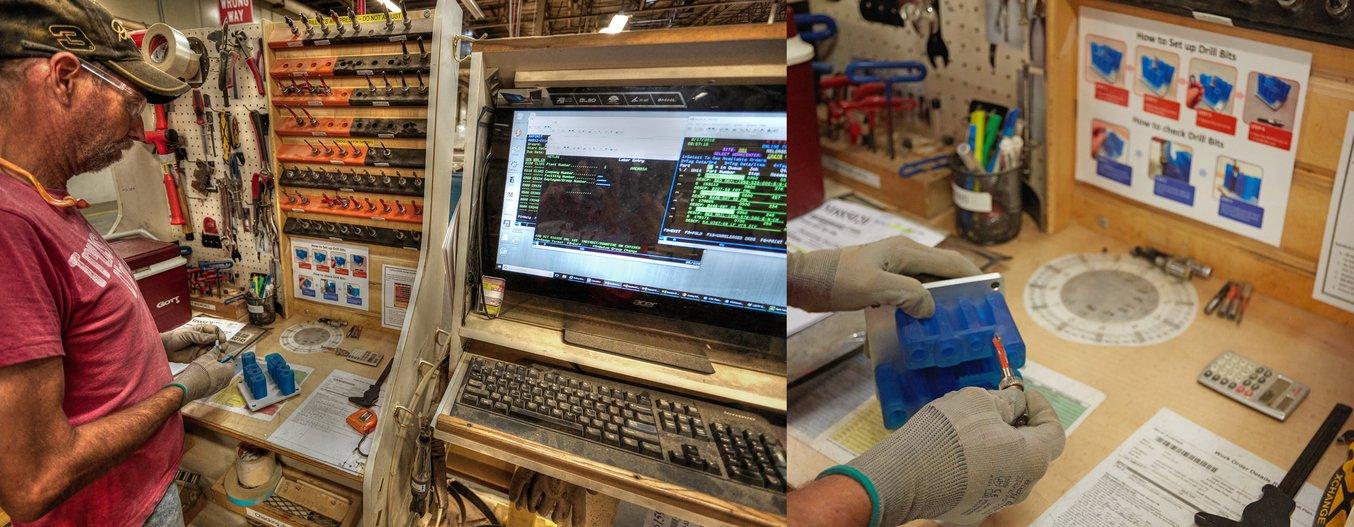
Eine Werkzeugführung aus Tough Resin mit einfachen Anweisungen, die einem Arbeiter dabei helfen, Bohrer zu überprüfen.
Die Idee dieser Feedback-Kreisläufe im ganzen Unternehmen ist nicht nur Ergebnis einer Kultur der ständigen Verbesserung, sondern ist eine „hartcodierte“ Praxis. Zusätzlich zu den internen Schulungsprogrammen verfügt das Unternehmen über das IDEA-Netzwerksystem, in dem jeder Mitarbeiter eine Idee zur Prozessverbesserung der Geschäftsführung vorschlagen kann. Wenn die Idee umgesetzt wird, erhalten sie dafür einen Bonus.
„Der Mitarbeiter hat tatsächlich die Möglichkeit zu sagen: ‚Hey, ich glaube, dass diese Idee uns dabei helfen würde, unseren Prozesse effizienter oder wirksamer zu machen.‘ Das hat mehrere Vorteile für uns: es hilft dem Unternehmen dabei, immer effizienter, immer effektiver zu werden und mehr Produkte in derselben Zeit fertigzustellen, und der Mitarbeiter erhält für seine Informationen einen Bonus“, erklärt Pieters.
„Wenn man diese Beteiligung des Mitarbeiters auf der untersten Ebene nicht hat, ist es um so schwerer, mit der Veränderung erfolgreich zu werden. Es ist eine Situation, bei der alle Beteiligten gewinnen, und sie hilft uns wirklich dabei, dass unsere Geschäftsführung und unsere Mitarbeiter viel mehr miteinander in Verbindung stehen. Ich denke, dass unser Geschäft unglaublich davon profitiert, dass wir eine großartige Beziehung im gesamten Unternehmen von unseren Eigentümern bis zu den Werksmitarbeitern haben und diese offene Kommunikation pflegen.“
Eine Herangehensweise an Automatisierung und neue Technologie, bei der der Mensch im Mittelpunkt steht
Diese Herangehensweise mit den Menschen im Mittelpunkt beeinflusst auch, wie das Unternehmen Investitionen und neue Technologien und deren Einsatz bewertet, besonders angesichts schrumpfender Arbeitsmärkte.
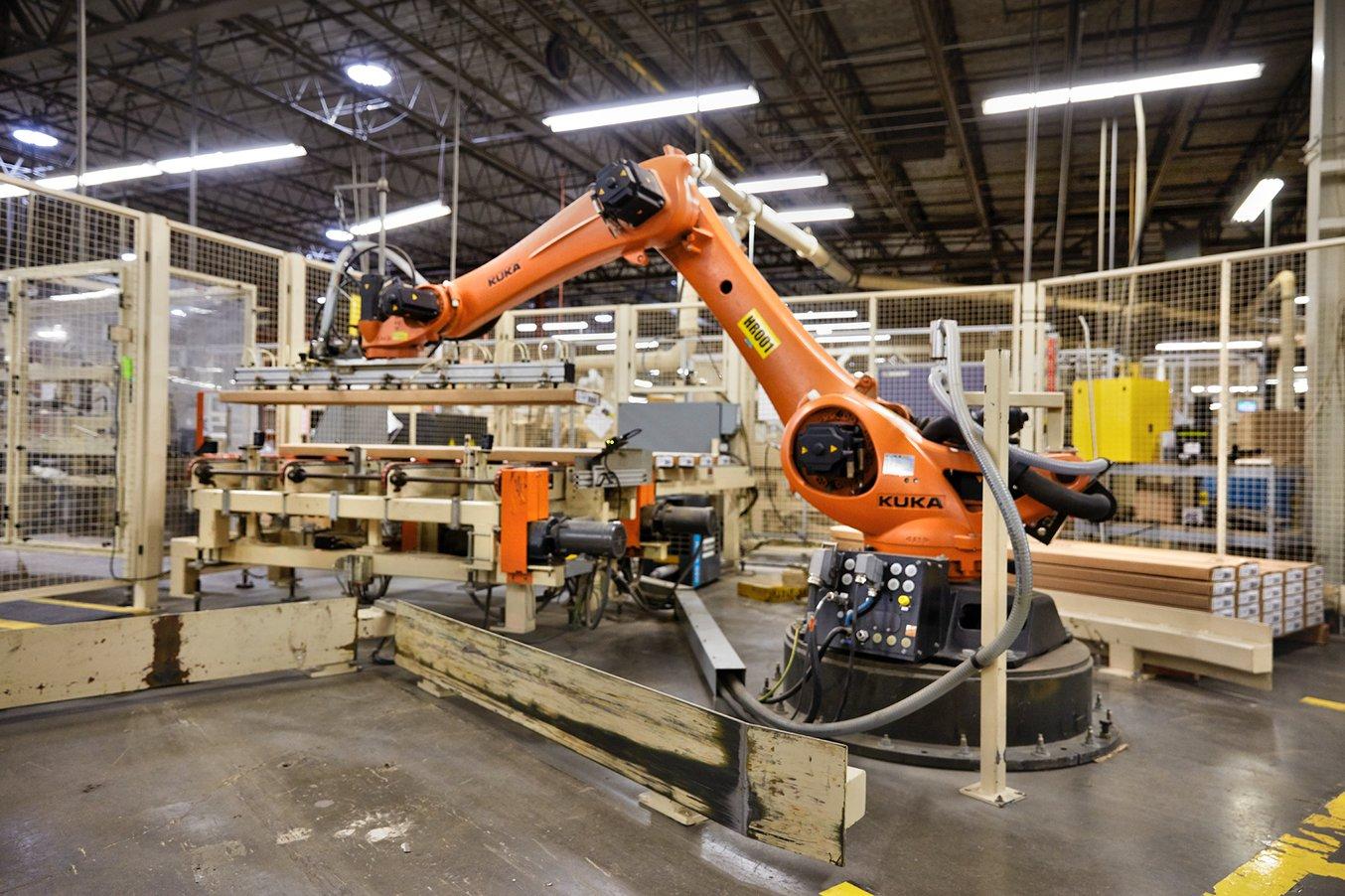
Ashley Furnitures erster Roboter, ein Palettierroboter, stapelt pro Stunde 200 Kisten perfekt aufeinander.
„Der Arbeitskräftemangel ist eine echte Herausforderung für uns. Wir müssen automatisieren. Unser Geschäft hier allein im Werk ist um 10 Prozent gewachsen, und das mit 15 Prozent weniger Arbeitskräften“, berichtet Pieters. „Wenn wir Automatisierungsprojekte betrachten – wo wir unsere Energie und unser Geld reinstecken sollten – [schauen wir,] wo die Arbeit am anstrengendsten ist, am monotonsten – wir beseitigen diese Arbeiten und lassen die Mitarbeiter ihren Verstand einsetzen, um zu sehen, wo wir unsere Prozesse weiter verbessern können“, erklärt Pieters.
„Wir haben unseren ersten Roboter vor fünf Jahren angeschafft, und jetzt können Sie bei der Besichtigung des Werks sehen, wo wir überall noch Automatisierung einsetzen. Beim 3D-Druck ist dasselbe Wachstumsmuster erkennbar.“
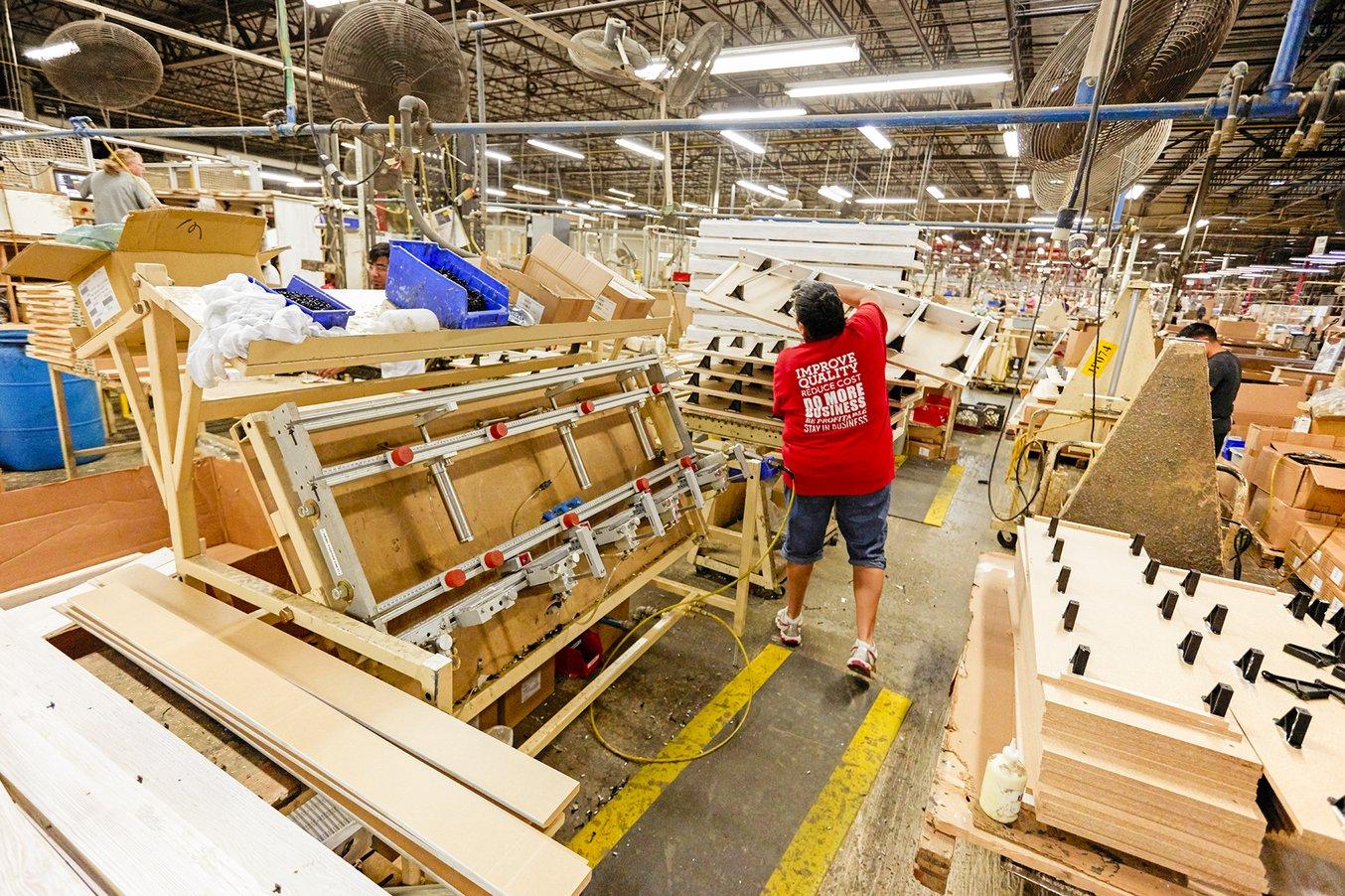
Ein universelles Montagevorrichtungssystem setzt 3D-gedruckte Teile ein, um die Anpassungen bei Produktwechseln zu erleichtern. So fallen die Kosten für den Bau ganz neuer Vorrichtungen in Metallwerkstätten vollständig weg.
Zusätzlich zu der Zeit- und Kostenersparnis gegenüber dem Outsourcing bestimmter Teile hat der 3D-Druck einige der traditionellen Prozesse im Werk verändert. Beispielsweise hat das Unternehmen ein universelles System für Montagevorrichtungen entwickelt. Wenn jetzt eine neue SKU eingeführt wird, müssen Fertigungsingenieure nur neue Teile drucken, um das System anzupassen, und Montagemitarbeiter befolgen die einfachen Anweisungen für jeden Wechsel. Das System hat die Einrichtungszeit im Montagebereich sowie den Lagerraum der ursprünglichen, bis zu 100 kg schweren Teile erheblich reduziert.
„Wir haben wirklich Vorrichtungen mit Abmessungen von 90 cm × 180 cm mit einem einfachen Behältersystem ersetzt; die Einrichtungszeit beträgt zwei Minuten.“ Konkel berichtet weiter: „Vorrichtungsbauer können sich jetzt anstelle von monotonen Arbeiten wichtigeren Problemen und größeren Herausforderungen zuwenden.“
„Dinge wie 3D-Druck und Automatisierung machen die Arbeit leichter für die Mitarbeiter, so dass sie nicht mehr so schwer und industriell ist“, sagt Pieters.
Raum für Experimente und Skalierung
Um neue Technologien voll ausschöpfen zu können, muss Hardware angeschafft werden, die mit Ihren Ideen wächst. Beim 3D-Druck ist die Hardware zwar wichtig, aber die Fähigkeiten der Maschine hängen auch stark von den eingesetzten Materialien ab. Ashley Furniture schöpft die technischen Kunstharze von Formlabs voll aus und probiert ständig neue Kunstharze aus, wenn diese auf den Markt kommen.
Diese Flexibilität bei der Lösungsfindung kann bearbeitete Teile ersetzen, und die Robustheit, den Schichten im Werk standzuhalten, hilft Ashley Furniture dabei, die Nutzung dieser Technologie zu skalieren. Und es ist kein Ende in Sicht.
Your Next Step Towards Continuous Improvement
This post covered just a few of the factors that help Ashley Furniture succeed. For more inspiration from companies leading the way in practical digital transformation, download the Digital Factory Report, or watch our executive briefing webinar.