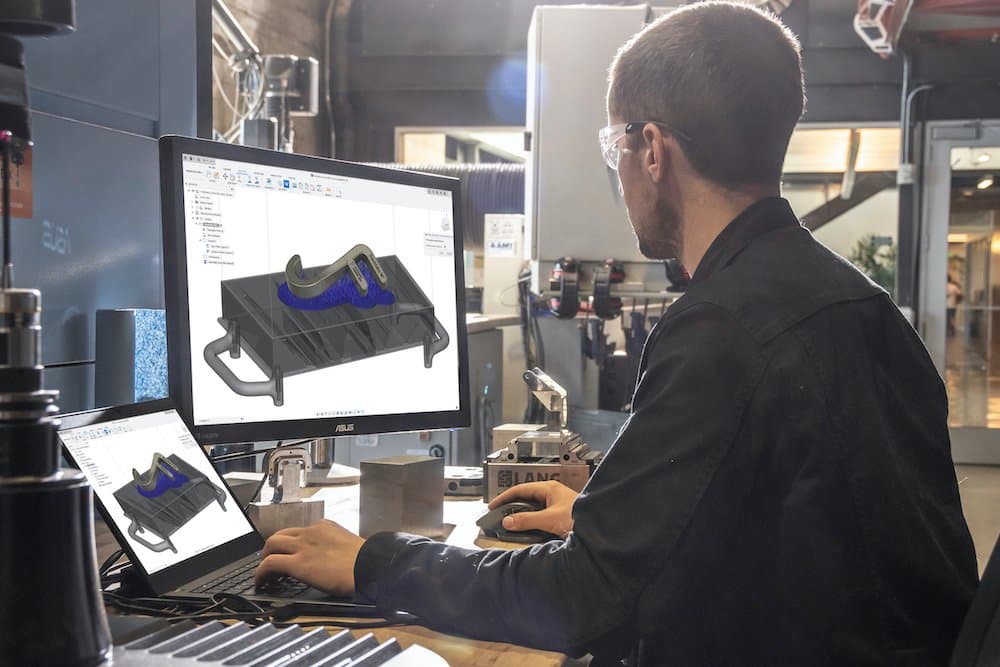
Formlabs und Autodesk Fusion 360 arbeiten zusammen, um Ihren digitalen Arbeitsablauf zu optimieren ― mit neuen CAD-Tools für den 3D-Druck. Unser Form 3 und Form 3L sind die ersten SLA-Geräte in diesem brandneuen Tool, das die perfekte Kombination aus Autodesks vielseitigem CAD-Paket und professionellen 3D-Druckergebnissen bietet. Dank dieser neuen Funktionen iterieren Formlabs-Nutzer ihre Ideen nun in nur wenigen Schritten; darüber freuen wir uns sehr.
Im Rahmen dieser Softwareintegration lässt sich über eine brandneue grafische Benutzeroberfläche direkt in Fusion 360 visualisieren und kommunizieren, inwieweit die Teile in das Druckvolumen des Form 3 und Form 3L passen. Designer können Ihr Design-Dashboard individuell anpassen, so wie es am besten zu ihren am häufigsten genutzten 3D-Druckabläufen passt. Außerdem optimieren Teams damit ihre Dateiverwaltung, indem Sie FORM-Dateien direkt aus Fusion 360 exportieren. (Und direktes Senden an PreForm folgt in Kürze.) So müssen keine individuellen STL-Dateien mehr heruntergeladen werden, was den Designern und Herstellern zuverlässigere Versionskontrolle ermöglicht.
„Die Integration der Drucker von Formlabs in Autodesk Fusion 360 ist ein wichtiger Schritt bei der Optimierung additiver Arbeitsprozesse. Dies vereint sowohl Design- als auch Herstellungsaufgaben in einer einzigen Plattform.“
Sualp Ozel, Autodesk
Formlabs stand in enger Zusammenarbeit mit den Entwicklern bei Autodesk, um diese Integration Wirklichkeit werden zu lassen. Senior Product Manager Sualp Ozel sagt dazu: „Die Integration der Drucker von Formlabs in Autodesk Fusion 360 ist ein wichtiger Schritt bei der Optimierung additiver Arbeitsprozesse. Dies vereint sowohl Design- als auch Herstellungsaufgaben in einer einzigen Plattform. Das spart Geld und liefert bessere, gleichmäßige und professionelle Ergebnisse, ohne Zeit zu verschwenden.“
Die Inspiration dazu fanden wir bei unserer bunt gemischten und teilfreudigen Community auf der ganzen Welt, die bereits Fusion 360 zusammen mit dem Form 3 nutzt. Jetzt werden die digitalen Arbeitsabläufe noch präziser auf die jeweiligen Absichten abgestimmt. Untenstehend finden Sie einige dieser Geschichten. Und schauen Sie auch in Zukunft wieder rein, da noch mehr Fallstudien folgen.
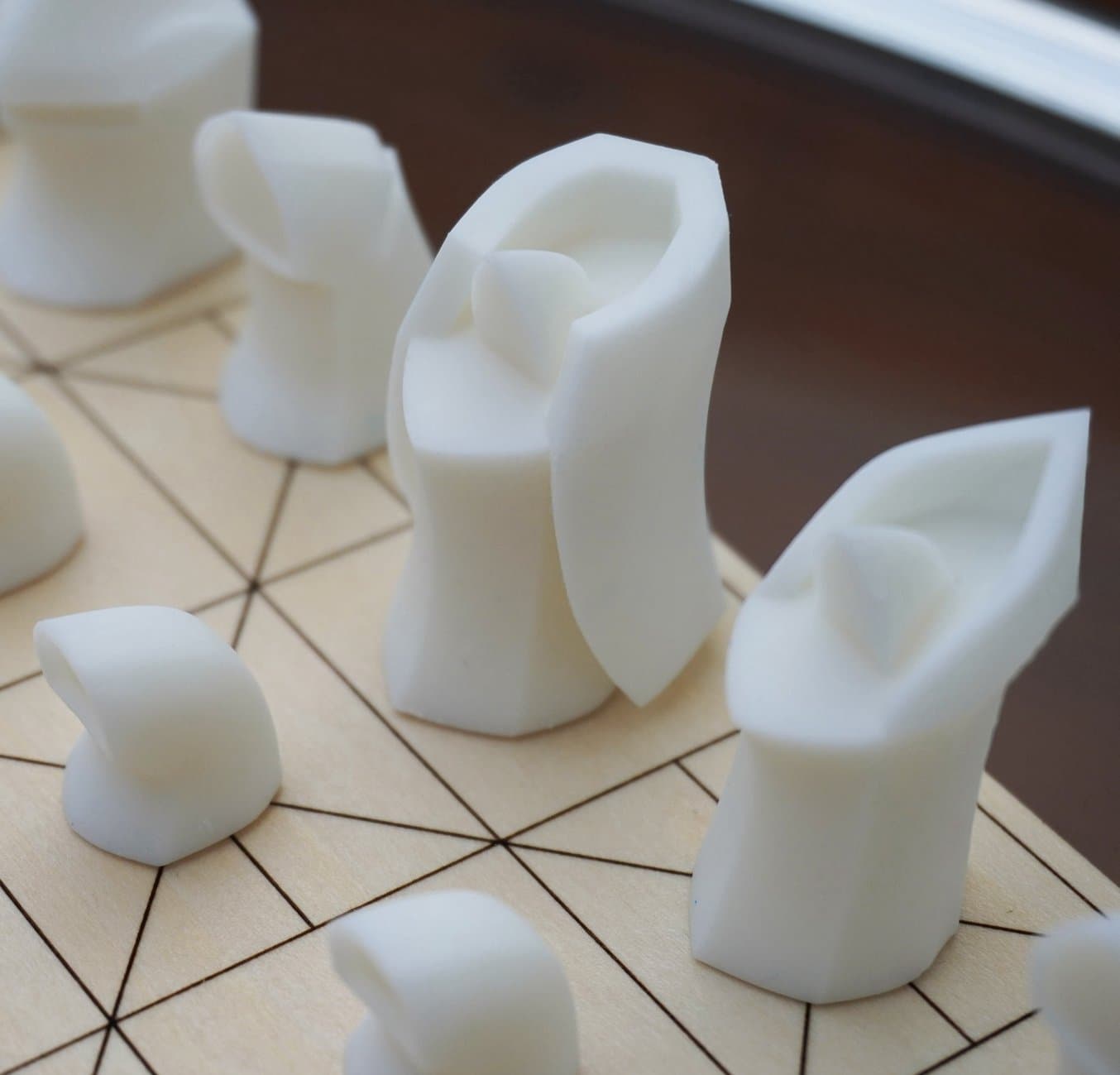
Integration von Formlabs und Fusion 360
Formlabs und Autodesk Fusion 360 arbeiten zusammen, um Ihren digitalen Arbeitsablauf zu optimieren ― mit einer neuen CAD-Software für 3D-Druck-Integration. Besuchen Sie unseren Integration Hub, um mehr über die neuesten SLA-Funktionen von Fusion 360 zu erfahren, weitere Geschichten unserer Nutzer zu lesen und unseren Design-Leitfaden herunterzuladen. (Bild: Schachspiel von Will Qiu)
Fallstudie: Cosm
Geschäftsführer Derek Sham gründete das Medizinprodukt-Unternehmen Cosm im Jahre 2018, um eine sehr weit verbreitetes, aber selten angesprochenes Leiden zu bekämpfen: Uterusprolaps. Dieser Krankheitszustand, dessen Ursache eine Schwächung des Beckenbodens ist, tritt weltweit bei fast 25 % aller Frauen auf. Als Behandlung ohne operativen Eingriff wird meist ein Pessar in die Vagina eingesetzt oder eine stützende Prothese. Leider geben jedoch viele Patienten die Behandlung auf, da die wenigen Standardgrößen und -formen zu Frustration führen. Cosm bekämpft dieses Problem nun mit einem brandneuen Ansatz der Individualisierung auf die Patientin.
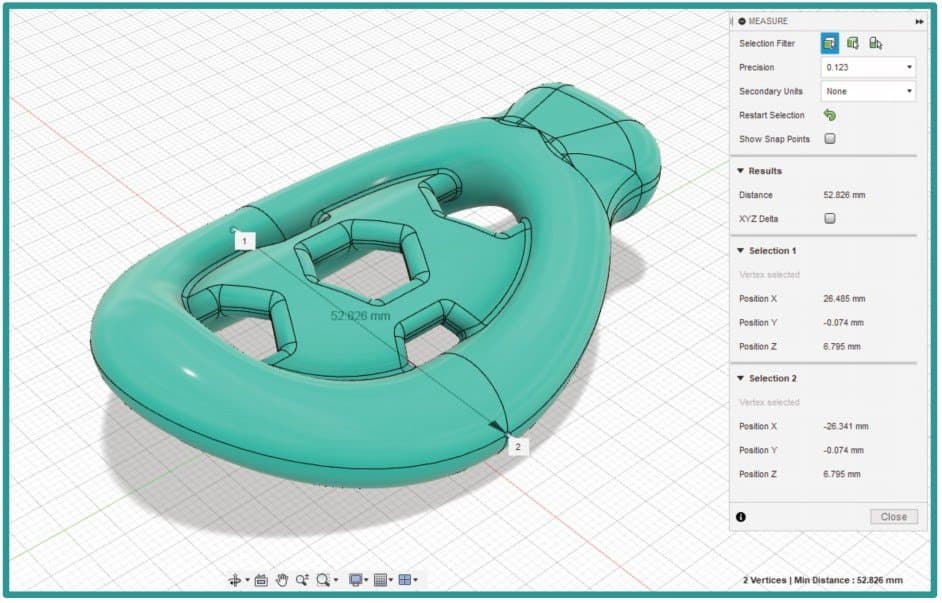
„Mit der Auflösung des Form 3B können wir unsere Abmessungen in Fusion 360 um den Bruchteil eines Millimeters variieren, um die Eigenschaften zu erhalten, die wir von unseren Formen und finalen Silikonteilen fordern.“
Robert Lancefield, Mechanical Design Engineering Lead
Cosms CTO Aye Nyein San berichtet: „Da sind datenbasierte Wissenschaft, maschinelles Lernen und KI miteinbezogen. Und damit hoffen wir, Frauen bei der Behandlung aufgrund eines Prolapses eine bessere Erfahrung zu bieten.“ Danach erklärte sie uns, dass der Arbeitsablauf mit einer neuen Ultraschalltechnik beginnt. Die Scandaten werden in Fusion 360 importiert, um ein konformes Gussgehäuse zu entwerfen, welches dann auf dem Form 3B gedruckt wird. Diese Gussform wird dann mit biokompatiblen Silikon gefüllt, um ein auf die Patientin zugeschnittenes Pessar zu fertigen.
Sowohl Fusion 360 als auch der Form 3B bieten Cosm die exakte Maßgenauigkeit, die man für erstklassige Behandlungen benötigt.
Fallstudie: Vertiball
Curtis Kennedy, Gründer und Geschäftsführer von Vertiball, möchte Sportlern eine Möglichkeit bieten, Ihre Muskelschmerzen selbst zu lindern, sich von Strapazen zu erholen und Verletzungen vorzubeugen. Und da kommt der Vertiball ins Spiel: ein frei drehbarer Massageball, der an einer vertikalen Fläche befestigt werden kann, was die gezielte Massagetherapie der betroffenen Stelle erleichtert. Die Schlüsselinnovation des Vertiballs ist der patentierte Saugnapf und Industriestärke, der sich an glatten, porenfreien Flächen befestigen lässt, wie z. B. an gestrichenen Gipswänden, an Metall oder auch an Holz. Die Vorderseite des Geräts enthält einen sich drehenden Ball, der am Basismechanismus befestigt ist.
Bei so vielen beweglichen Teilen, war ein präziser Prototyp eine Grundvoraussetzung. Curtis fand die nötige Zuverlässigkeit sowohl bei Fusion 360 als auch beim Form 3. Während der Designphase jedes Bauteils führte das Vertiball-Team Belastungsanalysen in der Simulationsumgebung von Fusion 360 durch, noch bevor ein Gramm Material mit dem Form 3 in einen Prototypen verwandelt wurde.
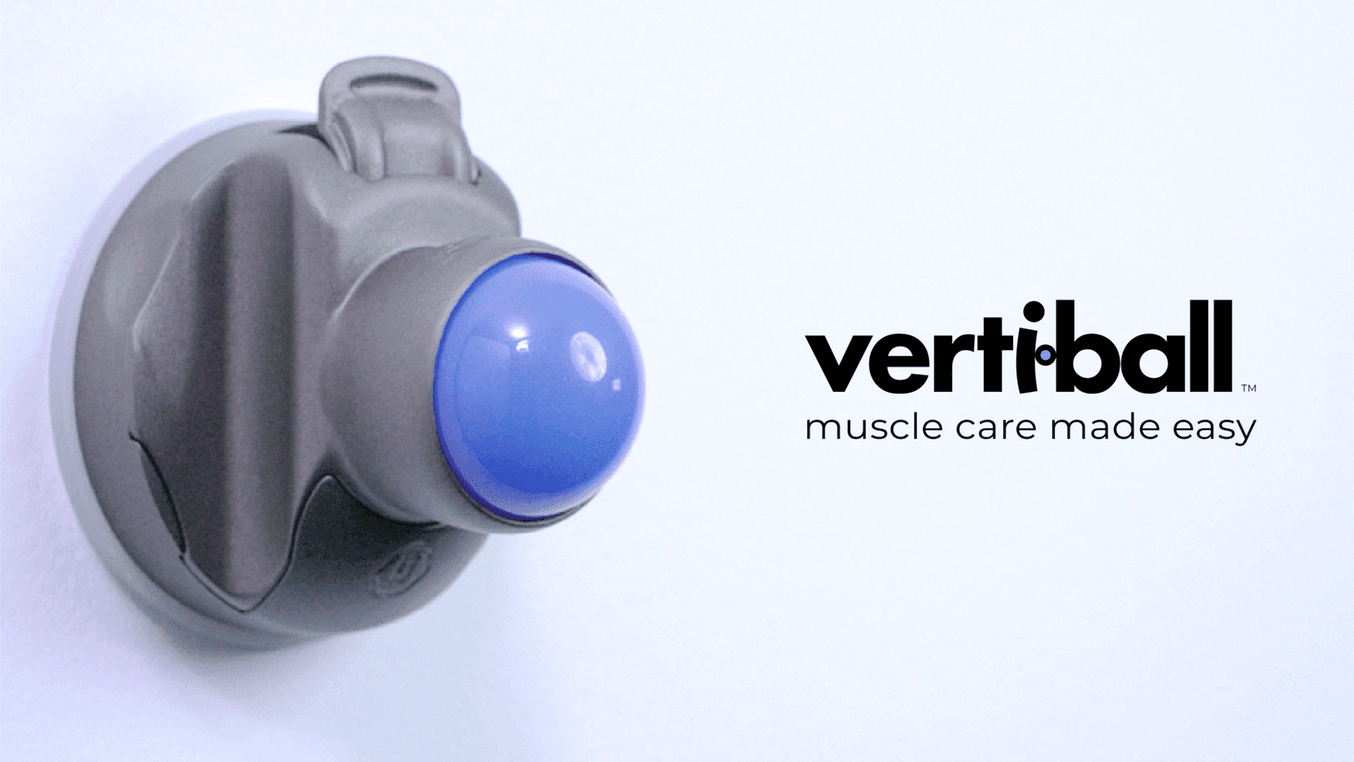
„Ein neues Design kann am Computer fantastisch aussehen, aber ohne einen Test ist das nichts wert. Erst validieren wir die Funktionalität des Designs durch Simulation in der Theorie und dann gehen wir zur Prototypenfertigung mit dem Form 3 über.“
Curtis Kennedy, CEO von Vertiball
Für den Entwicklungsprozess benötigte Curtis außerdem ein Material, das die niedrige Reibung und den Widerstand gegenüber Rissen von Polyamid 6 simulieren konnte, welches als Fertigungsmaterial für das Endprodukt geplant war. Dafür wählte er Formlabs' Materialfamilie der Kunstharze Tough und Durable.
Fallstudie: PrintCity
Mark Chester ist Product Development Specialist bei der 3D-Druckwerkstatt PrintCity an der Manchester Metropolitan University. Mit einer Flotte an FDM-, SLA- und Metall-3D-Druckern von Additive-X, Formlabs' größtem Vertriebspartner im Vereinigten Königreich, berät Mark Unternehmen mit Machbarkeitsstudien zu neuen Digitaltechnologien.
Der größte Wasserversorger des Landes, United Utilities, erkundigte sich bei ihm bezüglich optischer Scans und 3D-Druck zur Herstellung kleiner Ersatzteile nach Bedarf. Dies sollte die tage- und wochenlagen Lieferzeiten dieser Teile aus dem Weg räumen, wenn einmal etwas im Einsatz kaputt geht.
Mark schlug einen Laserscan eines abgenutzten Teils als ersten Schritt im Arbeitsprozess vor. Die Rohdaten wurden in Fusion 360 importiert und im Gittermodell repariert. Die leistungsfähigen Modellierungsoptionen von Fusion 360 machten dann das Reverse Engineering des Ersatzteils möglich. Zum Schluss werden die Teile dann direkt von Fusion 360 an PreForm übermittelt, bevor man sie auf dem Form 3 druckt. Dank der Integration von Fusion 360 und PreForm kann die Wartungsmannschaft von United Utilities Scans importieren, reparieren und Teile drucken, alles direkt vor Ort, ohne Dutzende STL-Dateien für ein einzelnes Teil zu speichern.
„Fusion 360 hat eine flache Lernkurve, wenn der Kunde noch keine Erfahrung mit CAD hat. Außerdem ist es kostengünstig.“
Mark Chester, Product Development Specialist bei PrintCity
Mit Autodesk Fusion 360 und dem Form 3 kann Marks Team schnell umsetzbare Arbeitsabläufe identifizieren und sie den Kunden vorstellen, ganz gleich, wie groß die Organisation sein mag.