Im Rausch der Geschwindigkeit: Foil Drive produziert Surf-Ausrüstung mit dem Form 3L und der Fuse-Serie
„Foil-Surfing“, „Surf-Foiling“ oder einfach nur „Foiling“ ist eine neue Variation des Surfens, bei der kurze Surfbretter auf einem Mast mit Unterwasserflügeln über die Wellen gehoben werden, ähnlich wie bei Tragflügelbooten.
Foil Drive ist ein Hersteller elektronischer Foiling-Ausrüstung, der sich gut mit der dritten Dimension auskennt. Das Team verwendet 3D-Druck in jedem Schritt des Entwicklungsprozesses und produziert Woche für Woche bis zu Eintausend Endverbrauchsteile mithilfe der Fuse-Serie und seiner Großformatdrucker vom Typ Form 3L. Foil-Surfing verbreitet sich wie ein Lauffeuer. Deshalb bietet 3D-Druck die ideale Lösung für die Fertigung, da er schnell und reaktiv ist. Nur so bleiben Hochleistungsprodukte erhältlich und erschwinglich für ein Publikum, das immer neue Nervenkitzel sucht.
„Es gibt unendlich viele Setups, die man ausprobieren kann. Es ist so dynamisch. Beim 3D-Surfing gibt es immer neue Sachen zu verbessern oder zu entwickeln“, berichtet uns Paul Martin, Gründer und Geschäftsführer von Foil Drive. Angefangen hat alles damit, dass Martin neue Setups ausprobieren wollte. Doch schon im zweiten Jahr hat sich das Projekt zu einem weltumspannenden Multimillionen-Geschäft entwickelt. Dabei war von Anfang an der 3D-Druck der Motor des Erfolgs.
Aller Anfang ist schwer
Zwar müssen beim Foiling die Surferarme etwas weniger rudern, trotzdem ist es ein körperlich sehr anspruchsvoller Sport. Um die nötige Geschwindigkeit zu erreichen, damit sich das Brett aus dem Wasser hebt, müssen die Surfenden ganz schön paddeln.
Eine alte Schulterverletzung gab Martin dabei den Anstoß, seine Ingenieurkünste zu bemühen, um den Sport auf die nächste Stufe zu befördern. Er entwickelte einen kleinen, aber leistungsstarken Elektroantrieb für den Mast, der für die nötige Geschwindigkeit sorgt, damit sich die Boards problemlos aus dem Wasser heben. „Das war die offensichtliche nächste Evolutionsstufe. Seit 20 Jahren arbeite ich mit 3D-Druck. So konnte ich schnell ein paar funktionierende Prototypen anfertigen. Das Produkt gibt es überhaupt nur, weil ich Zugang zum 3D-Druck hatte“, erklärt Martin.
Bei seinen iterativen Tests verbrachte er viel Zeit im Wasser, wo das Design anderen Foilenden ins Auge fiel. Die Leute fragten, ob er auch für sie so ein Antriebssystem bauen könne. Und während Martin mit verschiedenen Designs herumexperimentierte, erkannte er, dass ihm nur die ernsthaften Produktionskapazitäten fehlten, um sein Produkt geschäftstauglich zu machen.
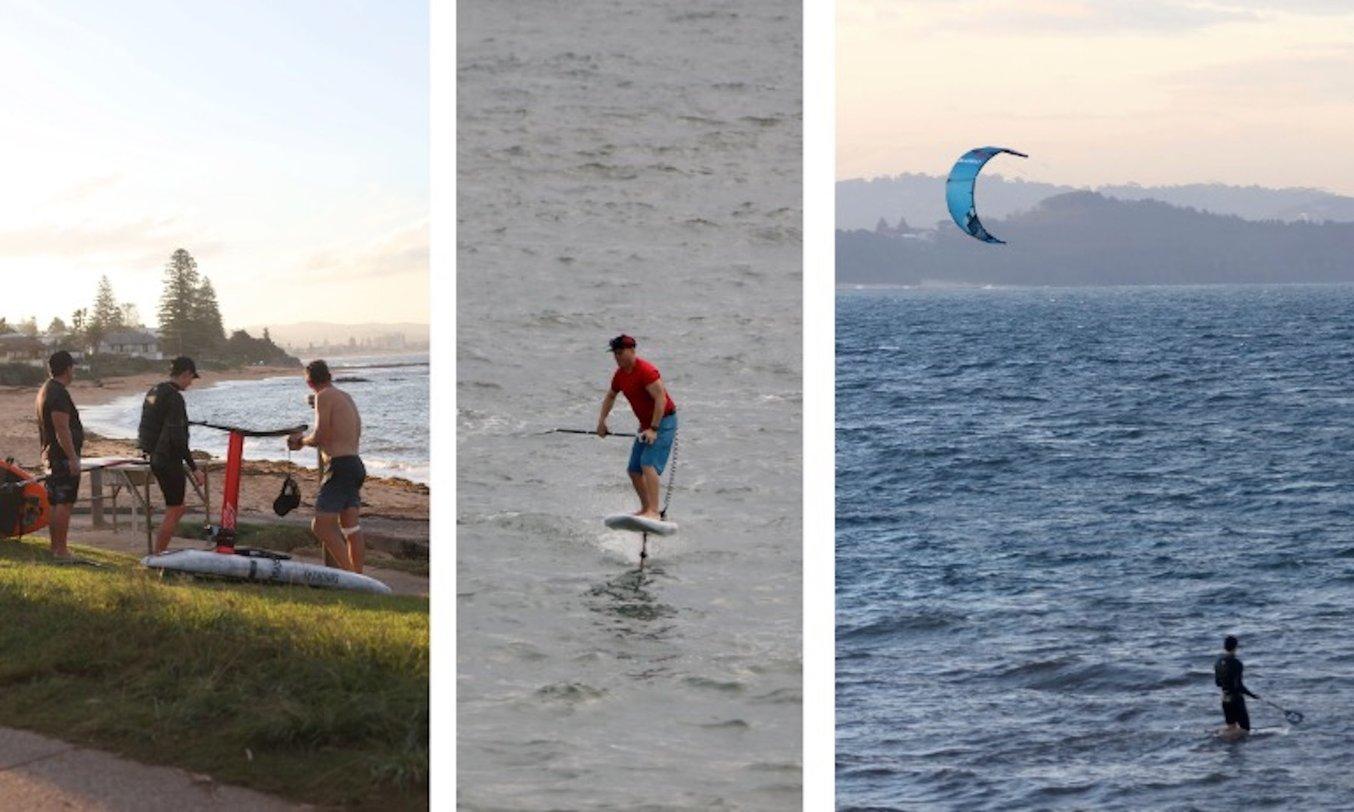
Foil-Surfen zählt zu den am schnellsten wachsenden Sportarten der Welt. Die Nachfrage nach der nächsten Generation anpassbarer Setups steigt exponentiell.
Das richtige Material für einen Endverwendungspropeller
Gewicht und Größe sind entscheidende Faktoren beim Foiling, wo es auf Dynamik und Schwung ankommt. Sind die Komponenten zu groß oder zu schwer, erreicht der Propeller nicht die nötige Geschwindigkeit, um das System aus dem Wasser zu heben. Die Designs mussten sehr viele Iterationsschritte durchlaufen, um das richtige Verhältnis von Größe zu Leistung auszuloten. Da kam der 3D-Druck goldrichtig. Martin hatte Schmelzschichtungsdrucker (FDM) und preiswerte SLA-Systeme zur Hand und konnte schnell neue Versionen entwickeln. „Man kann höchst komplexe Teile vor Ort fertigen, ohne Unsummen in die Entwicklung zu stecken“, sagt Martin.
Bei den Tests wurde jedoch klar, dass er eine 3D-Drucklösung mit besseren mechanischen Eigenschaften benötigte. Die Belastung der Rotorblätter ist eine besondere Herausforderung. Sie drehen sich mit 3000 U/min und tauchen dabei immer wieder ein und aus. Hinzu kommen Kraft und Drehmoment des Elektromotors. Mit einem Gewicht von gerade einmal neun Gramm müssen die Blätter extrem stark sein und all diese Kräfte bewältigen. „Da verlangt man dem Propeller Gewaltiges ab, mit solchen Kräften umzugehen“, kommentiert Martin.
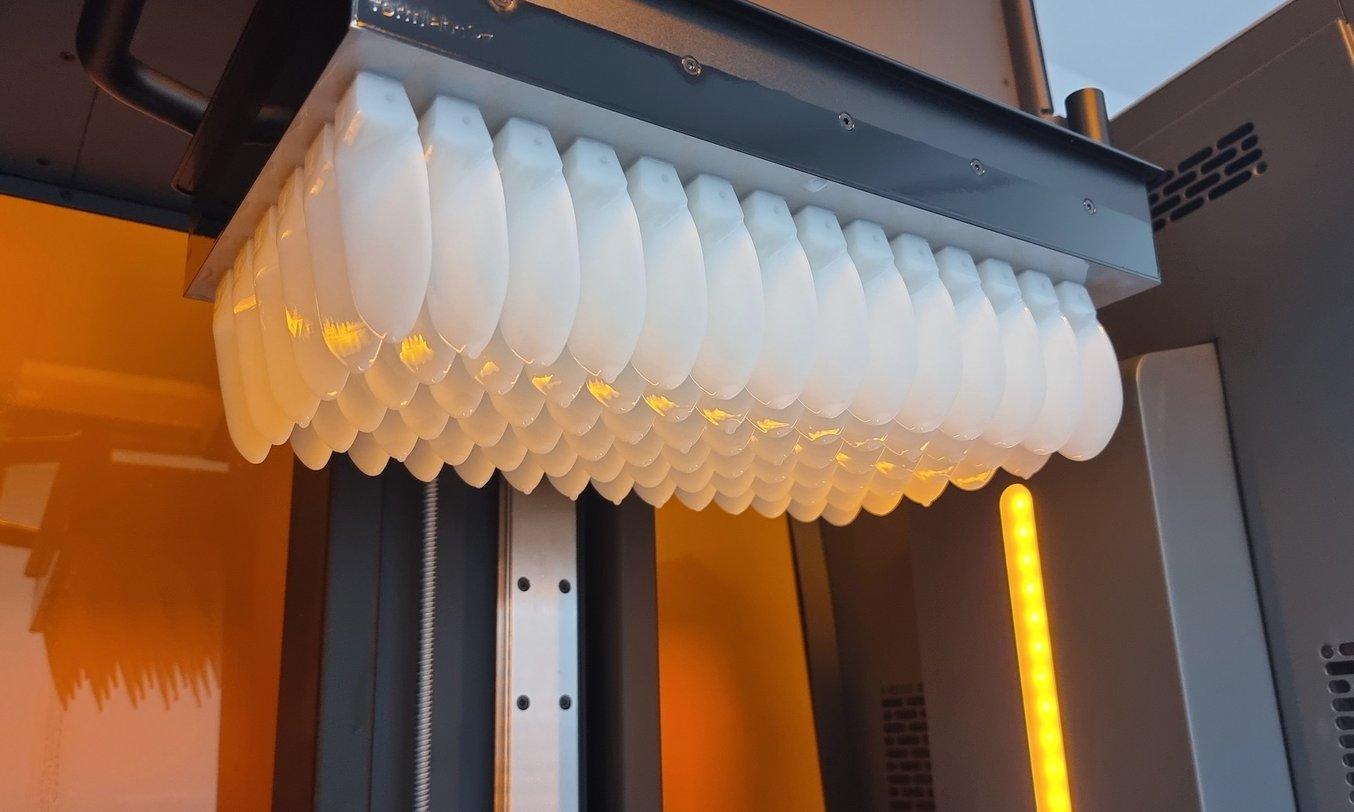
Das letztendliche Design der Propellerblätter, gedruckt aus Rigid 4000 Resin auf dem Form 3L
Werkzeuge für Blätter aus Metall würden Zehntausende kosten und eine Umgestaltung des Designs stark einschränken. „Ich muss diese winzigen Propeller in kleinen Stückzahlen herstellen, zu einem Preis, bei dem sich der Verkauf noch lohnt. Das geht nicht, außer eben mit 3D-Druck“, erläutert Martin.
Als er verschiedene Kunstharzdrucker ausprobierte, gab es für Martin Probleme bei der zuverlässigen Beschaffung von Materialien mit gleichbleibend verlässlichen mechanischen Eigenschaften. Verlässlichkeit ist der entscheidende Erfolgsfaktor für kleine Unternehmen wie Foil Drive. Einmal schlechtes Rohmaterial verwendet, und schon brechen die Teile im Wasser auseinander und die Kunden sitzen nicht nur sprichwörtlich auf dem Trockenen. Martin gewährt auf all seine Produkte wasserdichte Garantieansprüche, doch die Kosten für Service, Versand und Ersatzteile übertrafen bald den Wert der Güter. „Es musste ein Ende haben, dass die Teile auseinanderbrechen.“ Schlussendlich konnte er mithilfe des Melbourner Zulieferers Thinglab sein Design mit glasgefülltem Rigid 4000 Resin auf dem SLA-Drucker Form 3+ ausprobieren. Nach dem erfolgreichen Test der Teile kaufte er gleich mehrere Geräte.
Erst als wir Rigid 4000 Resin ausprobierten, lief alles glatt. Damit konnten wir Tausende herstellen und als Endverwendungspropeller an Leute auf der ganzen Welt versenden.
Paul Martin, Gründer und Geschäftsführer von Foil Drive
Keine kaputten Klemmen mehr
Das Team von Foil Drive verwendete größere, günstigere Kunstharzdrucker für die Teile abseits der Propeller, z. B. für die Steuerklemmen. Produziert und in die ganze Welt entsandt, zogen einige Kunden die Klemmen zu fest, wobei sie brachen. Martin entschied sich für die Produktion mit dem Form 3L und Tough 2000 Resin, welches mit der wiederholten Klemmbewegung fertig wurde. „Von da an hatten wir keinen einzigen Materialschaden mehr. Das hat sich sofort rentiert. Man bekommt wirklich das, wofür man bezahlt. Und beim Form 3L stellen wir einfach das Gerät ein und lassen es laufen“, so Martin.
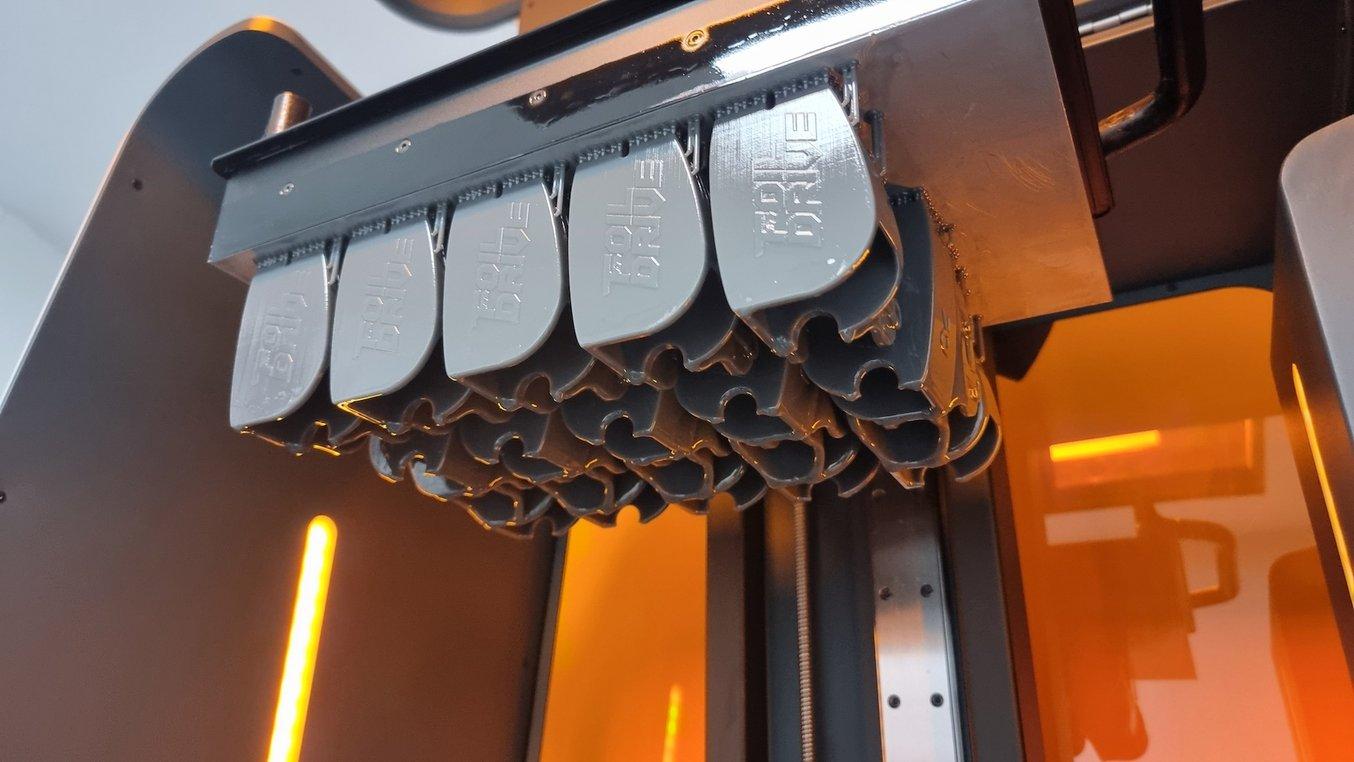
Tough 2000 Resin bietet Festigkeit und Haltbarkeit, auch noch nach Monaten im Meerwasser mit wiederholter Nutzung.
Der Form 3L zeigte deutlich, welchen Vorteil Zuverlässigkeit und fortgeschrittene mechanische Eigenschaften bedeuten. Doch als immer mehr Bestellungen hereinschwappten, musste Foil Drive noch größer denken. Um die hohen Stückzahlen zu produzieren und weiter mit neuen Geometrien zu experimentieren, bedurfte es einer Lösung mit Industrieleistung, die gleichzeitig die Reaktionsfähigkeit des 3D-Drucks gewährleistete. Leistungsstarker SLS-Druck im Betrieb war die passende Antwort.
Wir waren an einem Punkt angelangt, an dem wir massenweise Systeme verkauften. Und trotzdem wollten wir weiter unterschiedliche Formen entwerfen, und zwar ohne Stützstrukturen. Der Fuse hat uns dann höhere Stückzahlen bei niedrigeren Materialkosten ermöglicht.
Paul Martin, Gründer und Geschäftsführer von Foil Drive
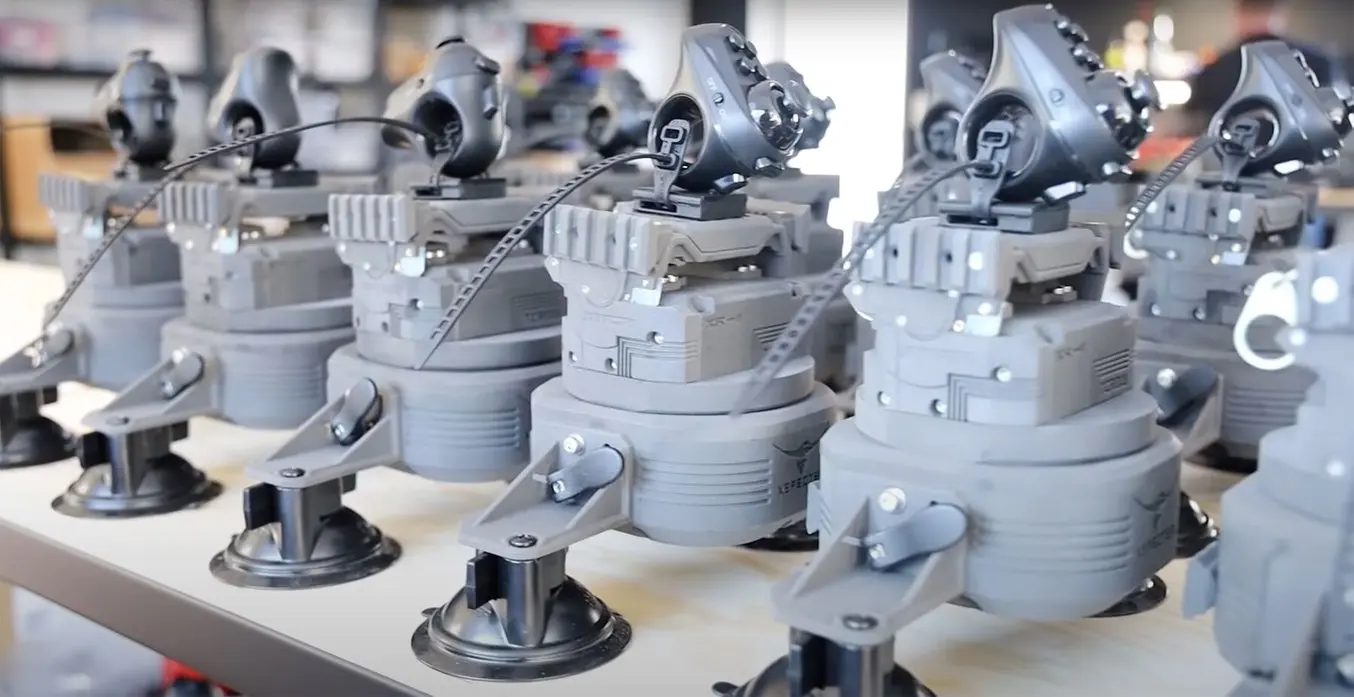
SLS-Produktion für die Endverwendung
3D-Druck für die Endverwendung ist nicht nur möglich, sondern dank des SLS-Ecosystems der Fuse-Serie auch noch erschwinglicher, agiler und leichter skalierbar denn je. Besuchen Sie unsere Seite zum Thema SLS für die Produktion und vergleichen Sie Produktionsverfahren, informieren Sie sich über unsere Mengenrabatte auf Pulver und entdecken Sie die Produktionsabläufe 15 verschiedener Hersteller, die derzeit die Fuse-Serie nutzen.
Flexibilität und Geschwindigkeit ausnutzen
Sobald die Fuse-Serie eingerichtet war, ging es los. Das Team begann mit 100 Teilen pro Woche, dann 200 und heute – mit einem zweiten Fuse 1+ 30W – entstehen wöchentlich etwa 650 Teile aus Nylon 12 Powder. Foil Drive konnte die Produktion an die wachsende Kundennachfrage anpassen, während die Popularität des Sports weiter sprunghaft ansteigt. „Die Fuse-Drucker haben wirklich für Produktionsvolumen und Skalierbarkeit gesorgt. Sie laufen 24 Stunden am Tag, sieben Tage die Woche“, berichtet Martin.
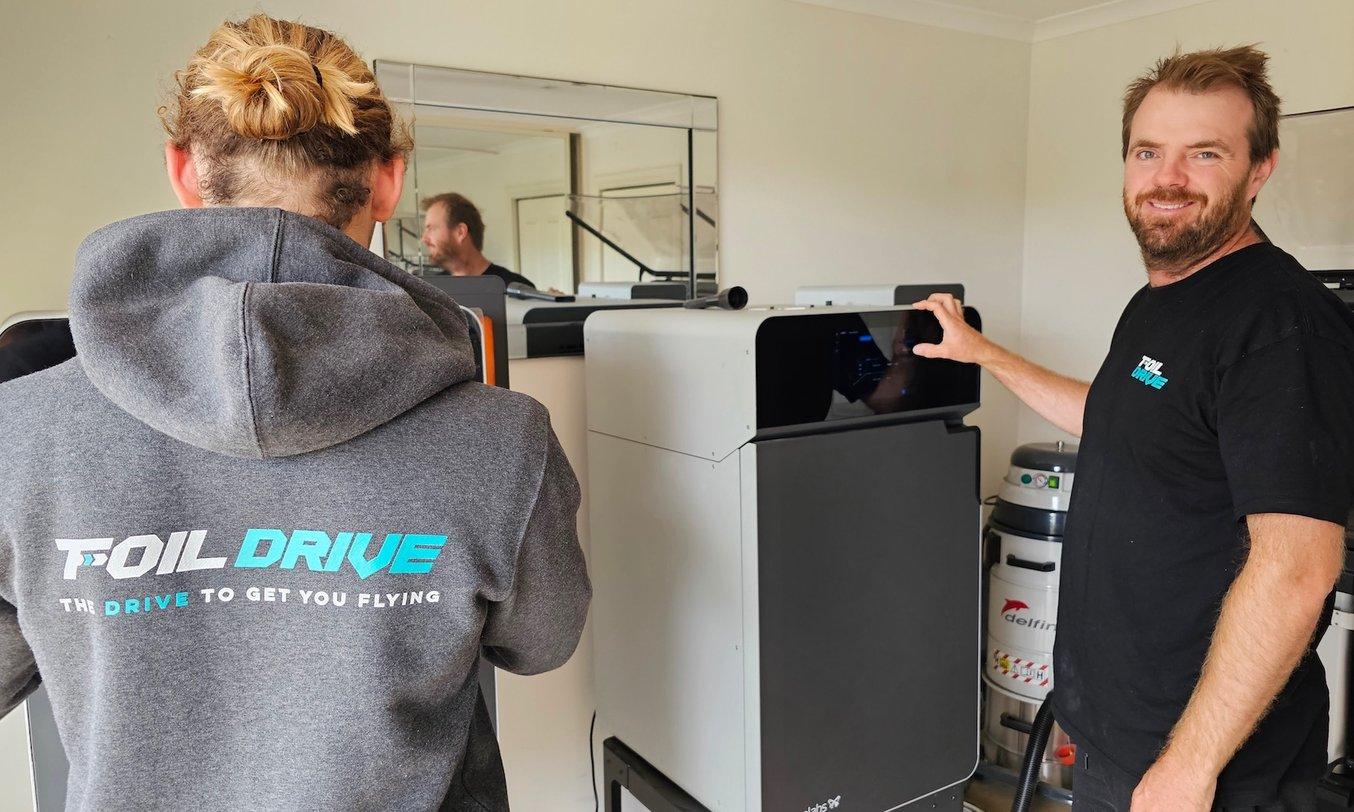
Paul Martin (rechts) und sein Team lassen die SLS-Drucker der Fuse-Serie sieben Tage die Woche rund um die Uhr laufen, um der hohen Nachfrage ihrer elektrischen Foil-Surfing-Systeme nachzukommen.
Bei solchen Schlagzahlen würden viele Hersteller zur traditionellen Fertigung mit Gussteilen wechseln, um die Kosten pro Teil zu senken. Doch Martin erfuhr die Vorteile der integrierten Fertigung persönlich in Anbetracht der Lieferkettenengpässe der letzten Jahre. Während der Knappheit von Silizium-Chips musste Foil Drive den Anbieter wechseln und das Bauteil, in den der Chip eingesetzt wird, passte nicht mehr korrekt. Hätte das Unternehmen zu diesem Zeitpunkt massengefertigte Komponenten genutzt – wie viele der Konkurrenten –, wäre die entstandene Verschwendung unermesslich gewesen. Stattdessen konnte Martin schnell umschwenken, das Design ändern und Verschwendung gänzlich vermeiden.
Für uns war es eine Kleinigkeit. Ein paar Dinge ändern, alles an PreForm senden, drucken und schon am nächsten Tag hatten wir die geänderten Teile, in die die Chips perfekt hinein passten. Die direkte Integrierung in den betriebsinternen Prozess gewährt uns vollständige Kontrolle. Wir konnten sofort reagieren.
Paul Martin, Gründer und Geschäftsführer von Foil Drive
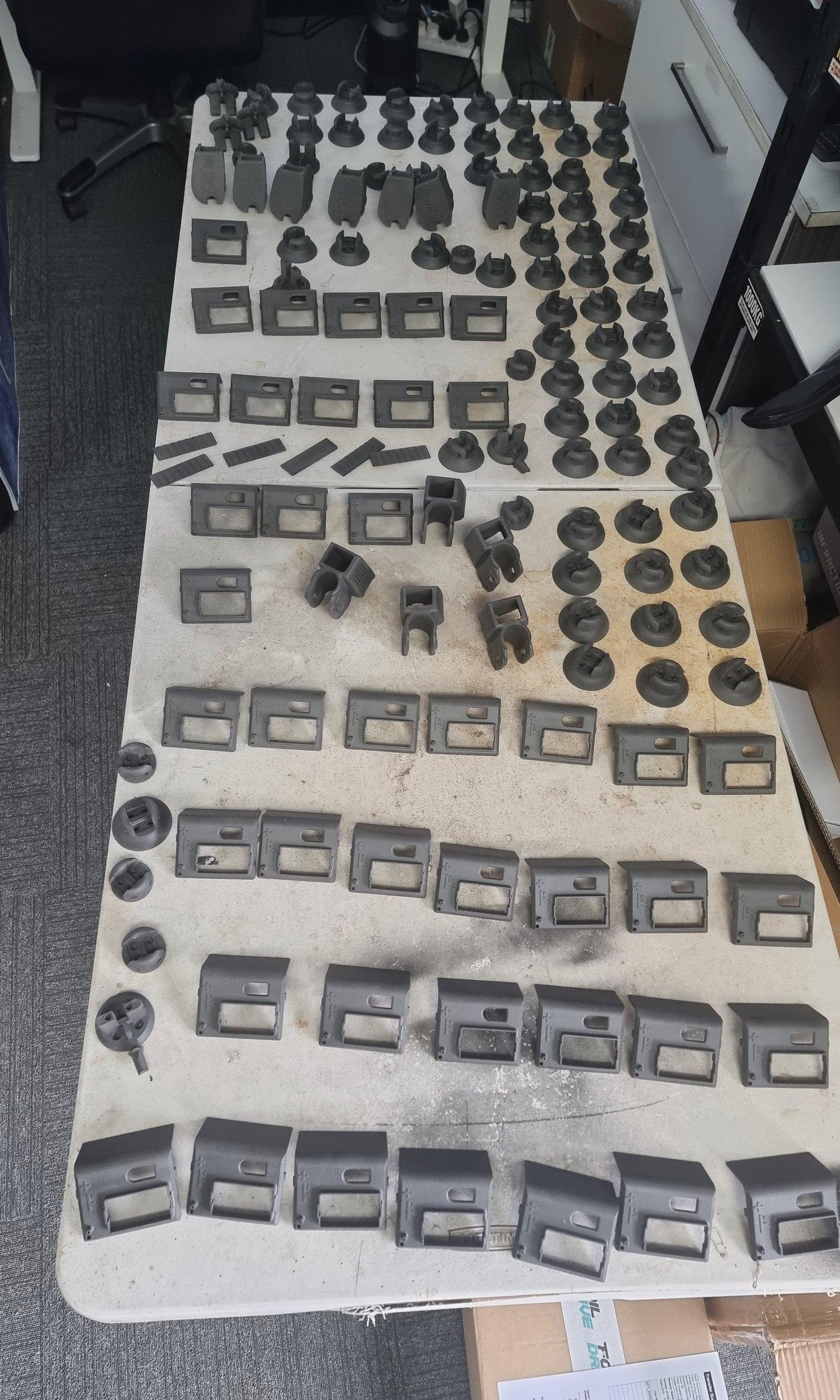
Foil Drive nutzt die SLS-Technologie der Drucker der Fuse-Serie, um mehrere Endverwendungsteile für das produzierte Surfbrett-Zubehör zu drucken.
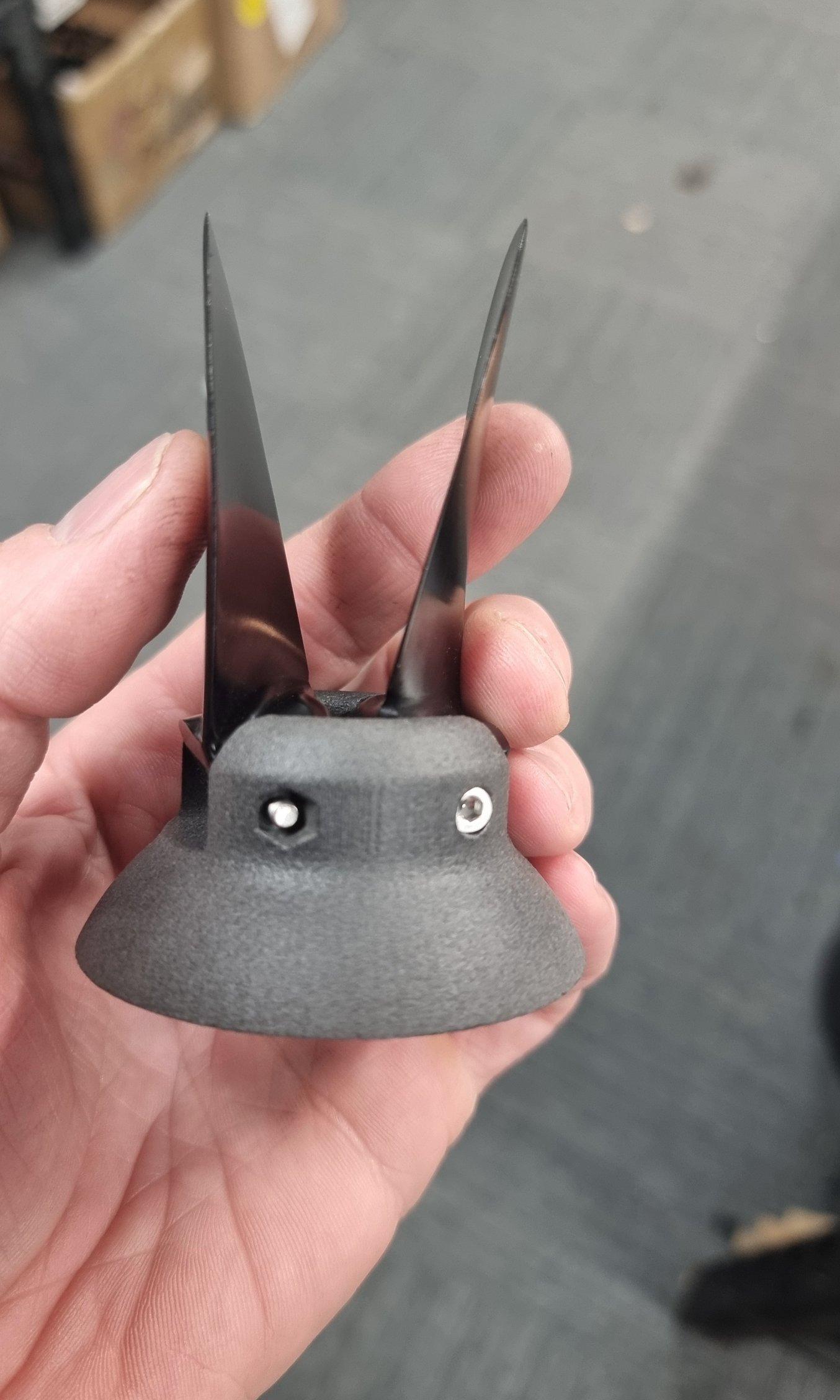
Das Bauteil des Faltpropellers nutzt die Festigkeit und maschinelle Bearbeitbarkeit von Nylon 12 Powder, um robuste Teile anzufertigen.
Produktionsvolumen mit der Fuse-Serie und dem Form 3L
Drucker/Material | Teile pro Druckvorgang | Teile pro Monat | Überlegungen | |
---|---|---|---|---|
Faltpropeller-Bauteil | Fuse 1+ 30W mit Nylon 12 Powder | ca. 60 | ca. 200 Bauteile | Integrierbare Gewinde, leicht flexibel, Produktionskapazität, Haltbarkeit, robust und für die Endverwendung geeignet |
Laufradblatt | Form 3L mit Rigid 4000 Resin | 84 | ca. 300–350 | Festigkeit, Iterationsfähigkeit, Steifigkeit, hält Unterwasserdruck bei 3000 U/min stand, scharfe/schmale Kanten |
Klemme | Form 3L mit Tough 2000 Resin | 15 | ca. 200 | |
Schwung aufbauen
Beim Foil-Surfing ist Schwung entscheidend für den Erfolg. Nur mit genug Geschwindigkeit hebt sich das Brett aus dem Wasser. Und genauso braucht es auch Schwung, um ein neues Produkt auf den Markt zu bringen. Dafür sorgt der 3D-Druck. Dank der Festigkeit von Materialien wie Rigid 4000 Resin oder Nylon 12 Powder ist die Herstellung robuster Endverwendungsteile ein Leichtes. Und mit ihrer reaktionsschnellen Produktion haben der Form 3+, Form 3L und die Fuse-Serie Foil Drive in nur drei Jahren zu einem millionenschweren Geschäft verholfen.
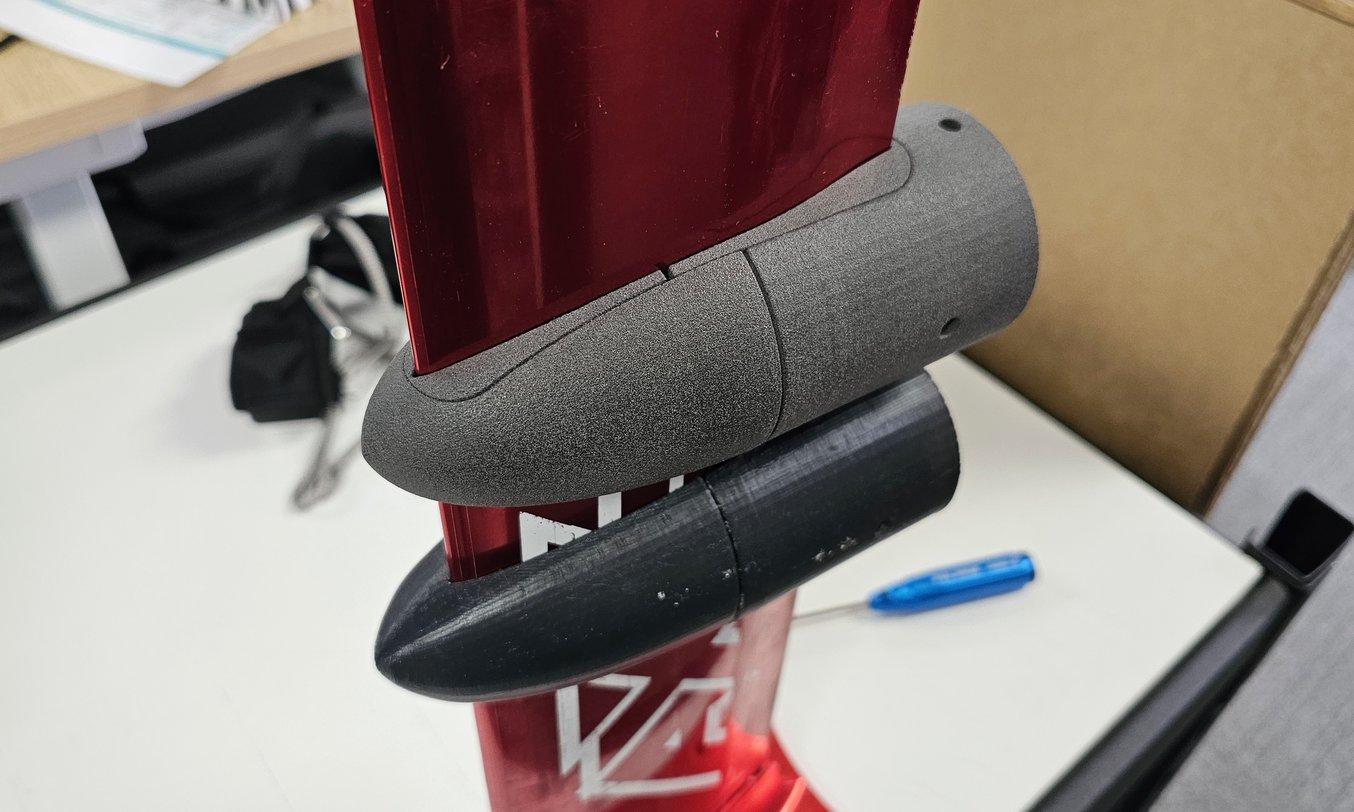
Oben ein Elektromotorgehäuse aus Nylon 12 Powder (gedruckt mit der Fuse-Serie) und unten aus Tough 1500 Resin
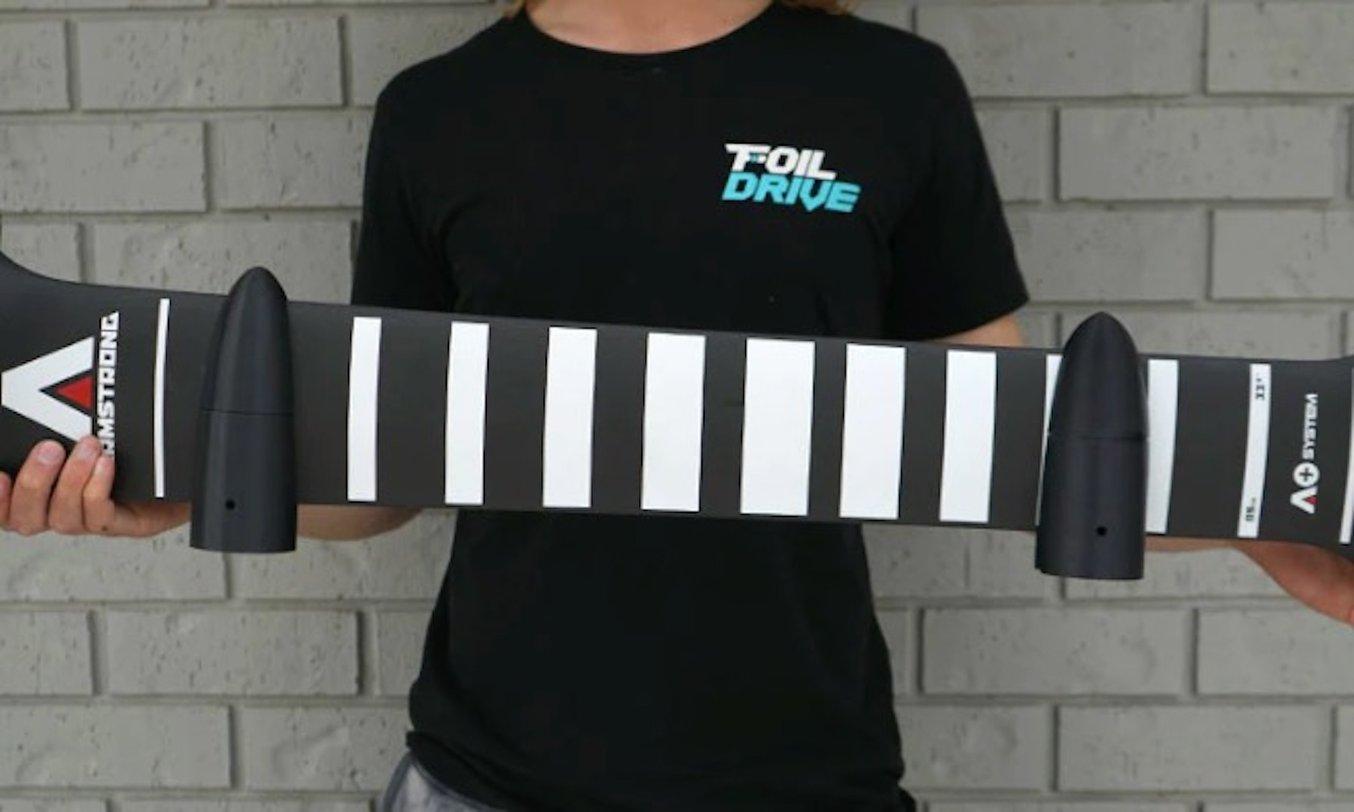
Die Motorengehäuse lassen sich an eine breite Palette von Masten unterschiedlicher Marken anpassen, selbst an kegelförmige Konstruktionen wie diese von Armstrong.
Bei unseren Produkten gibt es so viele Elemente, die von den Erwartungen traditioneller Fertigung abweichen: die Mengen, die verschiedenen Formen, die Größen und Geometrien, die Variationen – allein die Tatsache, dass auch nicht ein einziges unserer Einzelteile im Handel erhältlich war. Aber mit dieser Technologie lösen sich all diese Probleme schnell.
Paul Martin, Gründer und Geschäftsführer von Foil Drive
Die SLA- und SLS-Drucker von Formlabs eröffnen ganz neue Produktionswege, z. B. die Internalisierung der Lieferkette für eine reaktivere Fertigung oder die Entwicklung gänzlich neuer Produkte völlig ohne die Hindernisse traditioneller Formwerkzeuge. Um mehr über die Produktionsmöglichkeiten unserer Formlabs-Drucker zu erfahren, sprechen Sie noch heute mit unserem Spezialistenteam.