Wie Hayco Ultraschall-Zahnbürsten für die renommiertesten Weltmarken entwickelt
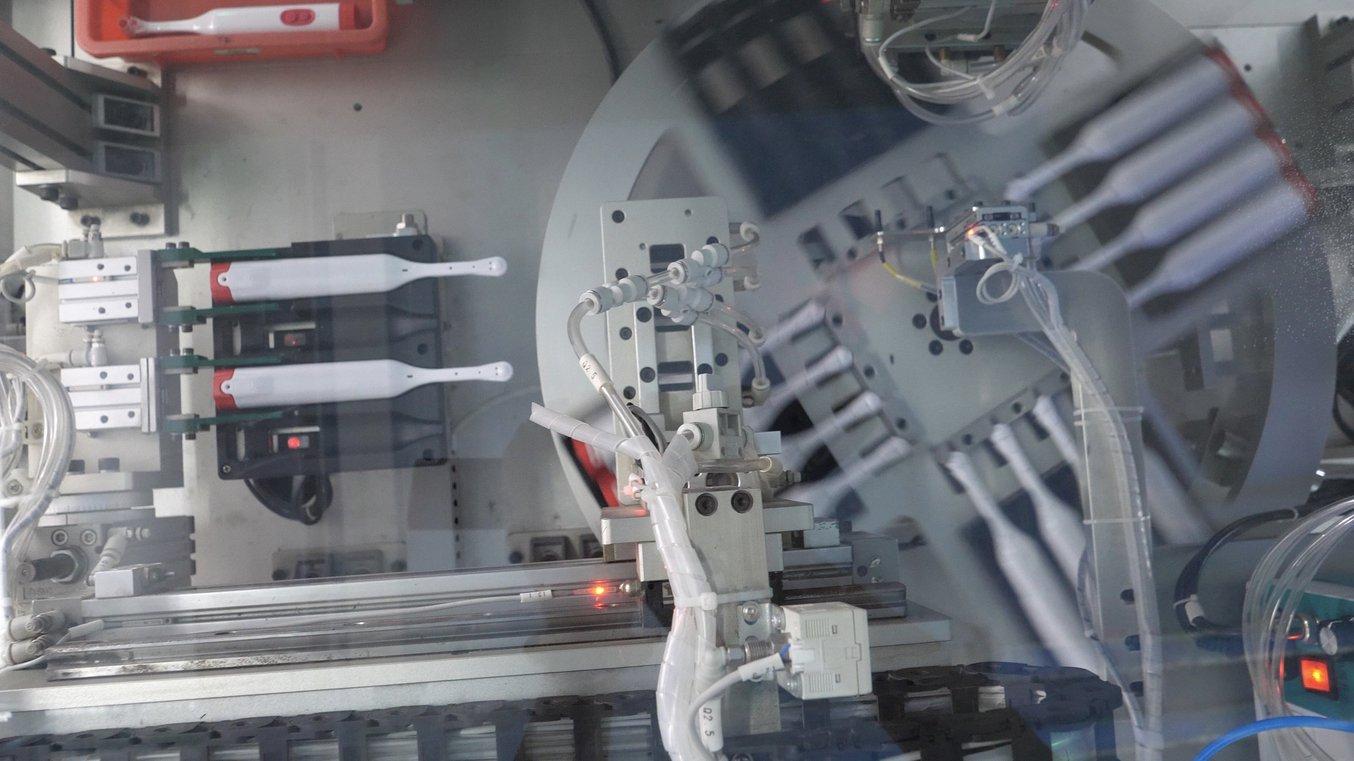
Im Jahr 1892 gründete der australische Unternehmer William E. Hay die South Australian Brush Company, die sich bald in ganz Südaustralien einen Namen mit Besen und Bürsten machte. Als Williams Enkel Donald Hay 1983 Asiens Aufstieg als globales Fertigungszentrum beobachtete, entschied er sich, in Hong Kong ein neues Unternehmen unter dem Namen Hayco zu gründen.
Mit Augenmerk auf die Familienspezialität, das Herstellen von Bürsten, eröffnete Hayco ein Spritzgusswerk im chinesischen Shenzhen. Das Unternehmen ist schnell gewachsen und verfügt mittlerweile über 6000 Mitarbeiter und mehrere Werke in China und der Dominikanischen Republik.
Seit seiner Gründung hat Hayco mit zahlreichen namhaften Marken bei der Herstellung von Haushaltsreinigungsprodukten aus Kunststoff zusammengearbeitet. Auf der Grundlage der Unternehmenstradition, der Herstellung von Bürsten, entwickelt und fertigt Hayco seit 18 Jahren hochwertige elektrische Zahnbürsten für Marktführer in der Mundhygiene, wie Philips and Church & Dwight. Aktuell werden über 20 Millionen elektrische Zahnbürsten auf den Weltmarkt gebracht.
Erfahren Sie in diesem Beitrag, wie das Engineering-Team von Hayco additive Fertigung einsetzte, um neue Produkte zu entwickeln und genaue, biokompatible Prototypen zu fertigen, bevor sie in die Serienfertigung gehen.
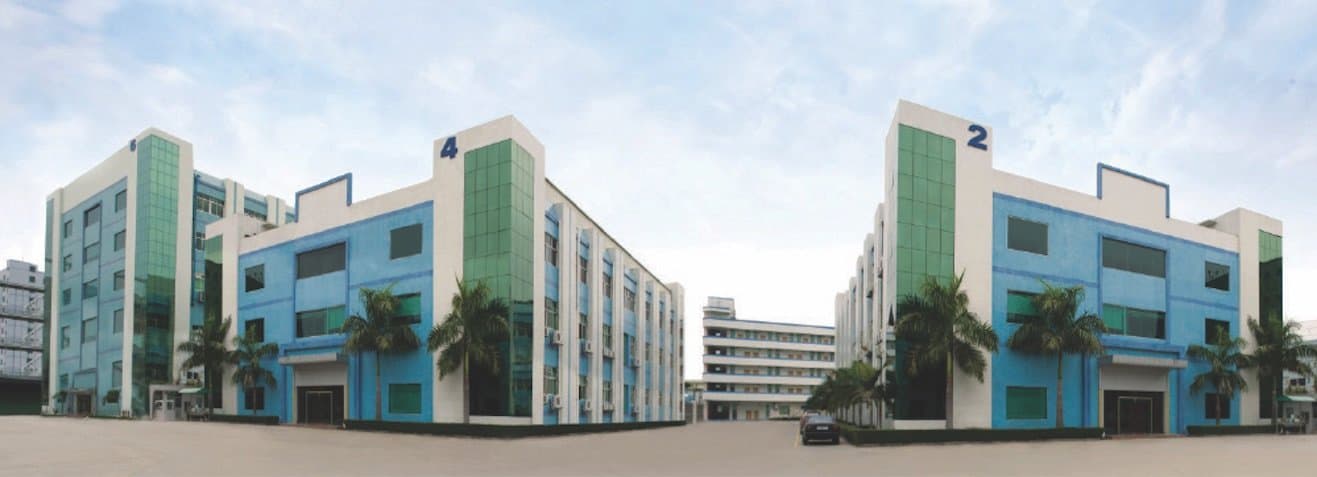
Hayco’s manufacturing plant in Shenzhen, China
Frühe Anwender additiver Fertigung
Aufgrund seiner langjährigen Erfahrung in der Fertigung und der Designinnovation war Hayco ein früher Anwender von 3D-Druck und verwendet seit den frühen 1990er Jahren industrielle Schmelzschichtungs-(FDM)- und SLS 3D-Drucker. Als Hoss Vong, der aktuelle Senior Manager für Front End Innovation, im Jahr 2000 zu Hayco kam, begann er, 3D-Druck für die Prototypenfertigung vieler Kunststoffprodukte einzusetzen, darunter auch Ultra-Schallzahnbürsten.
„Damals lief Rapid Prototyping mit 3D-Druck noch ganz anders als heute. Wir hatten Industriedrucker. Sie waren groß, erforderten umfassende Schulungen und waren in Anschaffung und Wartung sehr, sehr kostspielig“, so Vong.
Das richtige Material für unterschiedliche Komponenten
Beim Design einer neuen Zahnbürste gibt es bei jeder Komponente andere Anforderungen, die sich auf die Wahl der Methoden und Materialien zur Prototypenfertigung auswirken. Beispielsweise muss das Gehäuse glatt und robust sein, das Chassis muss belastbar sein und gleichzeitig hochgenau, um die gesamte Elektronik aufnehmen zu können. Und was am wichtigsten ist: Der Bürstenkopf muss aus einem biokompatiblem Material bestehen, um Verbrauchertests zu ermöglichen.
Die Materialauswahl ist besonders wichtig bei der Bewertung der dynamischen und schwingungstechnischen Eigenschaften des Produkts. Steifigkeit und Dichte müssen so nah wie möglich am Endprodukt liegen.
„Wir hatten bislang großen Erfolg mit dem Materialangebot von Formlabs, mit der wir die Leistung des Endprodukts möglichst genau abbilden konnten“, erklärt Vong.
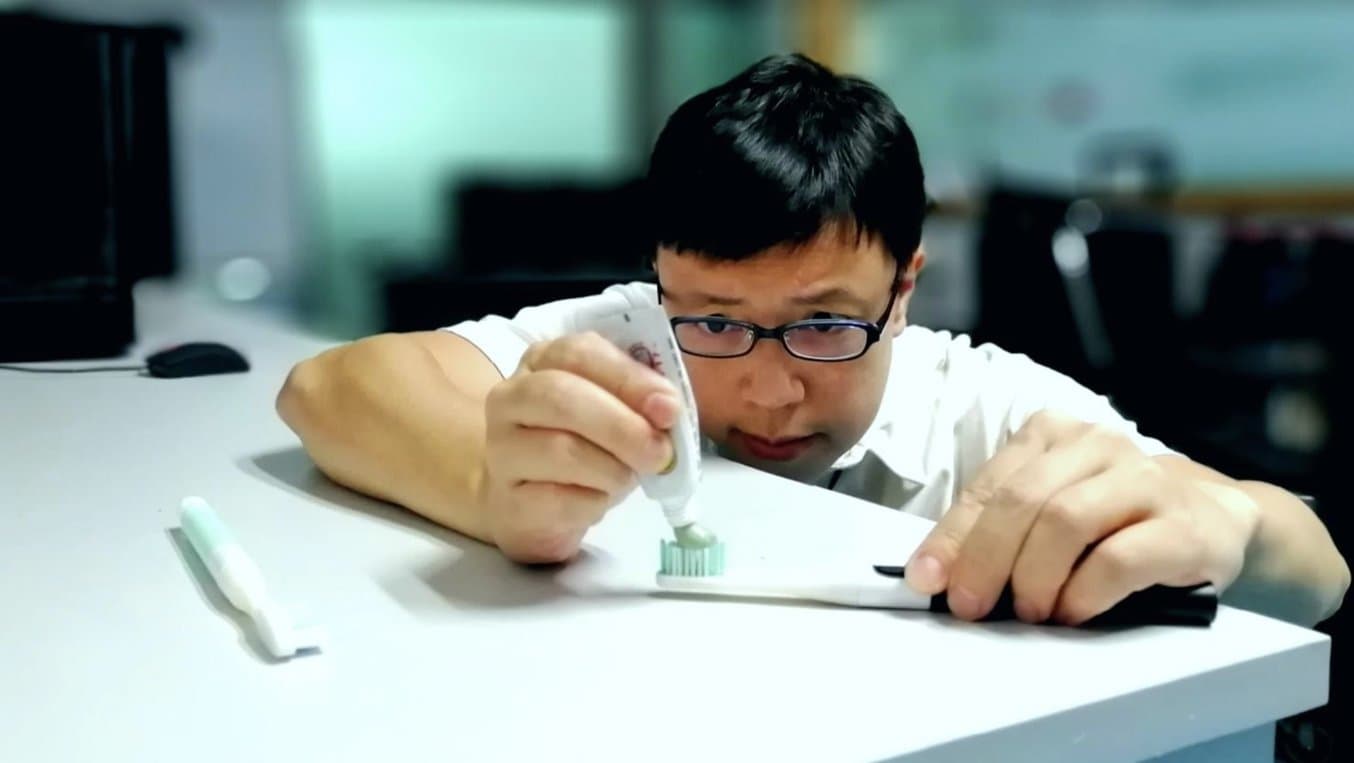
Hoss Vong testet einen Zahnbürsten-Prototyp. Der Bürstenkopf besteht aus einem biokompatiblem Material, damit Funktionstests möglich sind.
Aus Erfahrung wusste Vong, dass Stereolithografie die geeignetste 3D-Drucktechnologie für diese Anwendung war. Allerdings war es nicht leicht, einen Drucker zu finden, der das erforderliche Materialangebot lieferte. „Man findet selbstverständlich immer recht günstige Kunstharze von Drittanbietern auf dem Markt, doch aus Sicherheits- und Qualitätsgründen setzen wir sie nie ein“, erläutert Vong.
Nachdem er recherchiert hatte, entschied sich Vong für einen 3D-Drucker von Formlabs, der eine große Auswahl an Materialien für die Prototypenfertigung und für Anwendungen mit Biokompatibilitätsanforderungen liefert.
„Wir verwenden viele Formlabs Standard-Kunstharze und wenn wir die Verbrauchertests durchführen müssen, nutzen wir Dental SG Resin, das biokompatibel ist und feine Details liefert“, so Vong.
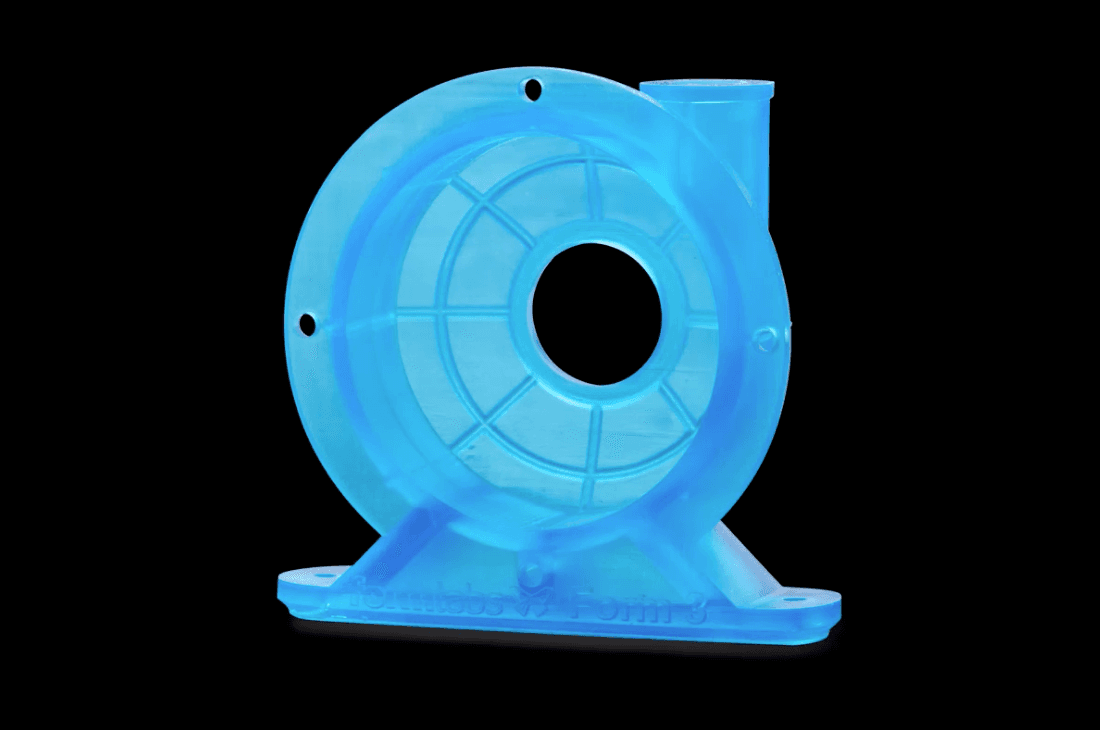
Kostenlosen Probedruck anfordern
Sehen und fühlen Sie die Qualität des SLA 3D-Drucks persönlich. Wir schicken Ihnen einen kostenlosen Probedruck an Ihren Arbeitsplatz.
3D-Druck für alle Ingenieure
„Der Form 2 hat gehalten, was die positiven Bewertungen versprachen, die ich vor dem Kauf unserer ersten Formlabs-Drucker gelesen hatte. Sie haben sich als sehr zuverlässige Geräte erwiesen, und Formlabs hat mir eine Materialauswahl für Tests angeboten. Im Gegensatz zu vielen anderen industriellen Druckern ist er außerdem sehr intuitiv in der Bedienung. Unsere 3D-Drucker konnten nicht mehr nur von einigen wenigen geschulten Ingenieuren eingesetzt werden – alle Mitarbeiter können sie für ihre Projekte einsetzen, was wir sehr fördern. Als der Form 3 auf den Markt kam, bestellten wir sofort zwei Drucker vor, um unseren wachsenden Bedarf für Kapazitäten in der Prototypenfertigung zu decken. Wir haben jetzt insgesamt sechs Formlabs-SLA-Drucker“, berichtet Vong.
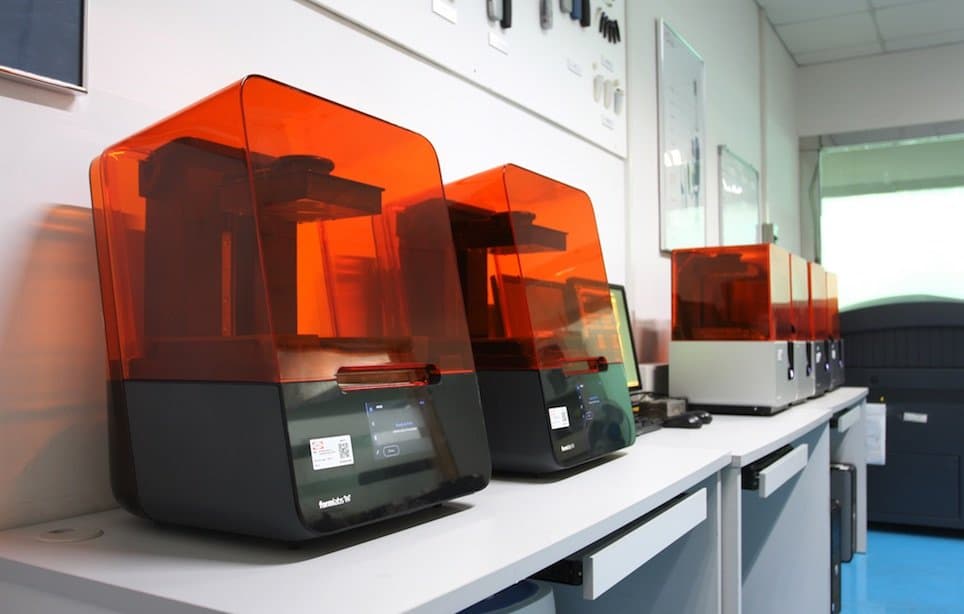
Hayco nutzt aktuell sechs Formlabs-SLA-Drucker in seinen 3D-Werkstätten. Dank der Benutzerfreundlichkeit ist der 3D-Druck jetzt nicht mehr nur für einige wenige geschulte Ingenieure zugänglich. Alle Mitarbeiter werden dazu ermutigt, sie in Projekten einzusetzen.
Laut Vong belaufen sich die Kosteneinsparungen mit Formlabs-3D-Druckern auf ca. 35 % im Vergleich zu anderen Drucktechnologien. Besonders macht sich die Low Force Stereolithography (LFS) Technologie des Form 3 bemerkbar.
„Der Form 3 druckt weniger Stützstrukturen pro Druck, während bei anderen Drucktechnologien deutlich mehr Stützmaterial verwendet wird, zum Teil bis zu 60 % mehr, was sich bei vielen Iterationen für viele Produkte schnell summiert“, sagt Vong.
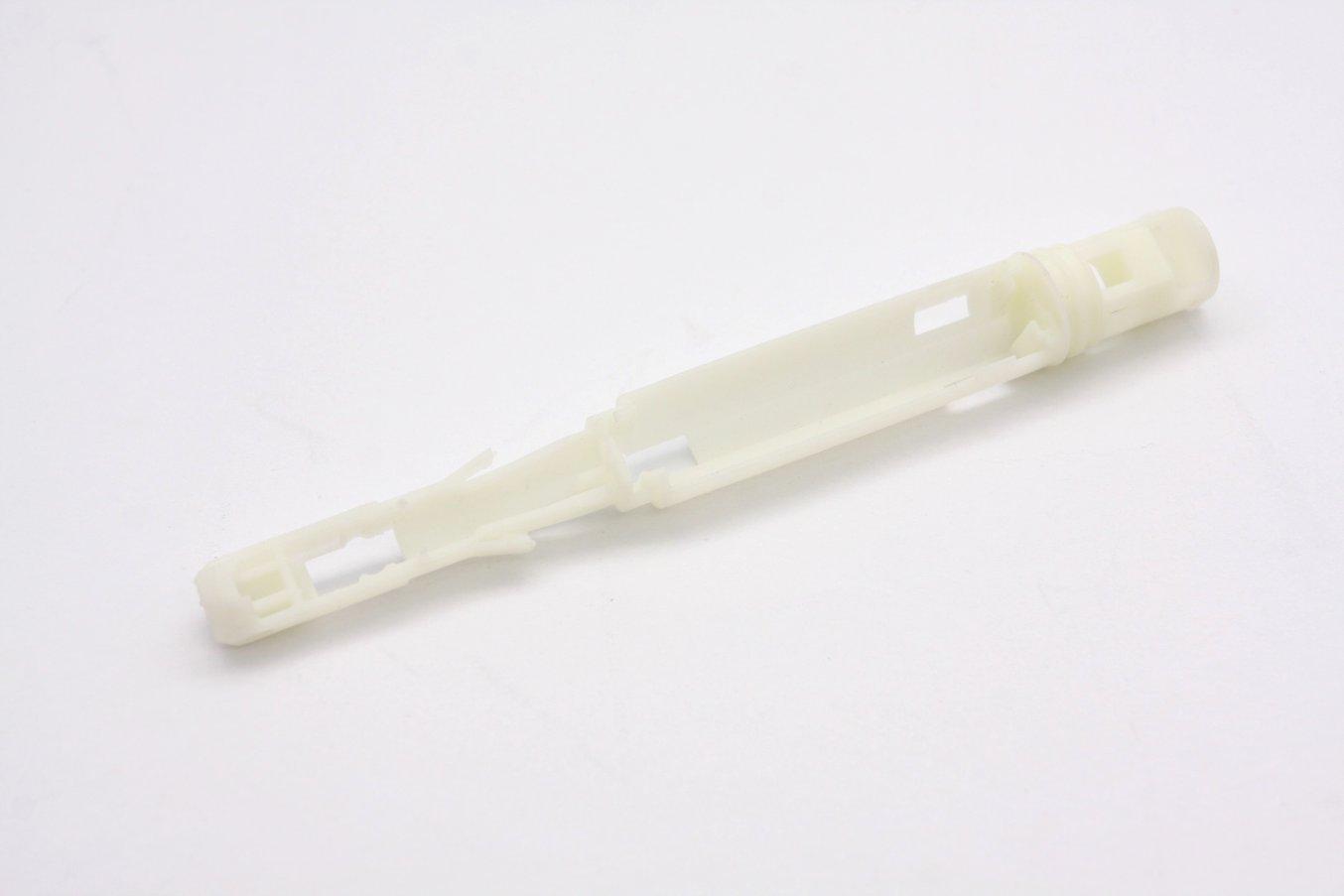
Ein Chassis einer elektrischen Zahnbürste, das mit White Resin auf dem Form 3 gedruckt wurde.
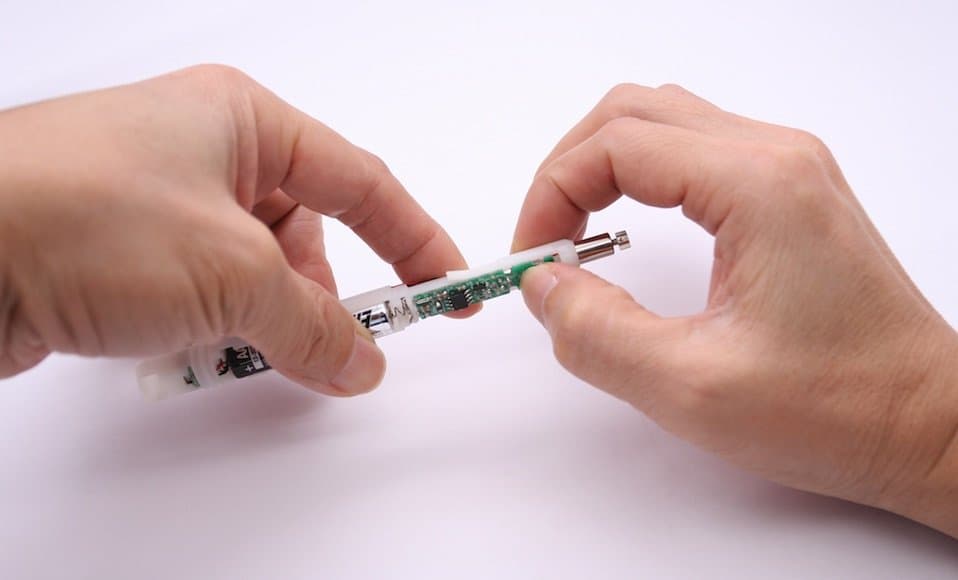
Die Chassis-Prototypen von elektrischen Zahnbürsten müssen zäh und gleichzeitig sehr genau sein, um die gesamte Elektronik aufnehmen zu können.
Prototypentests ohne Werkzeuge für Rapid Injection Molding
„Nehmen wir einmal das Beispiel der Knöpfe an der elektrischen Zahnbürste. Vor einigen Jahren konnten wir ohne ein Spritzgusswerkzeug für echte spritzgegossene Kunststoffteile nie absolut sicher sein, wie die Kunststofffeder funktionieren würde“, schildert Vong.
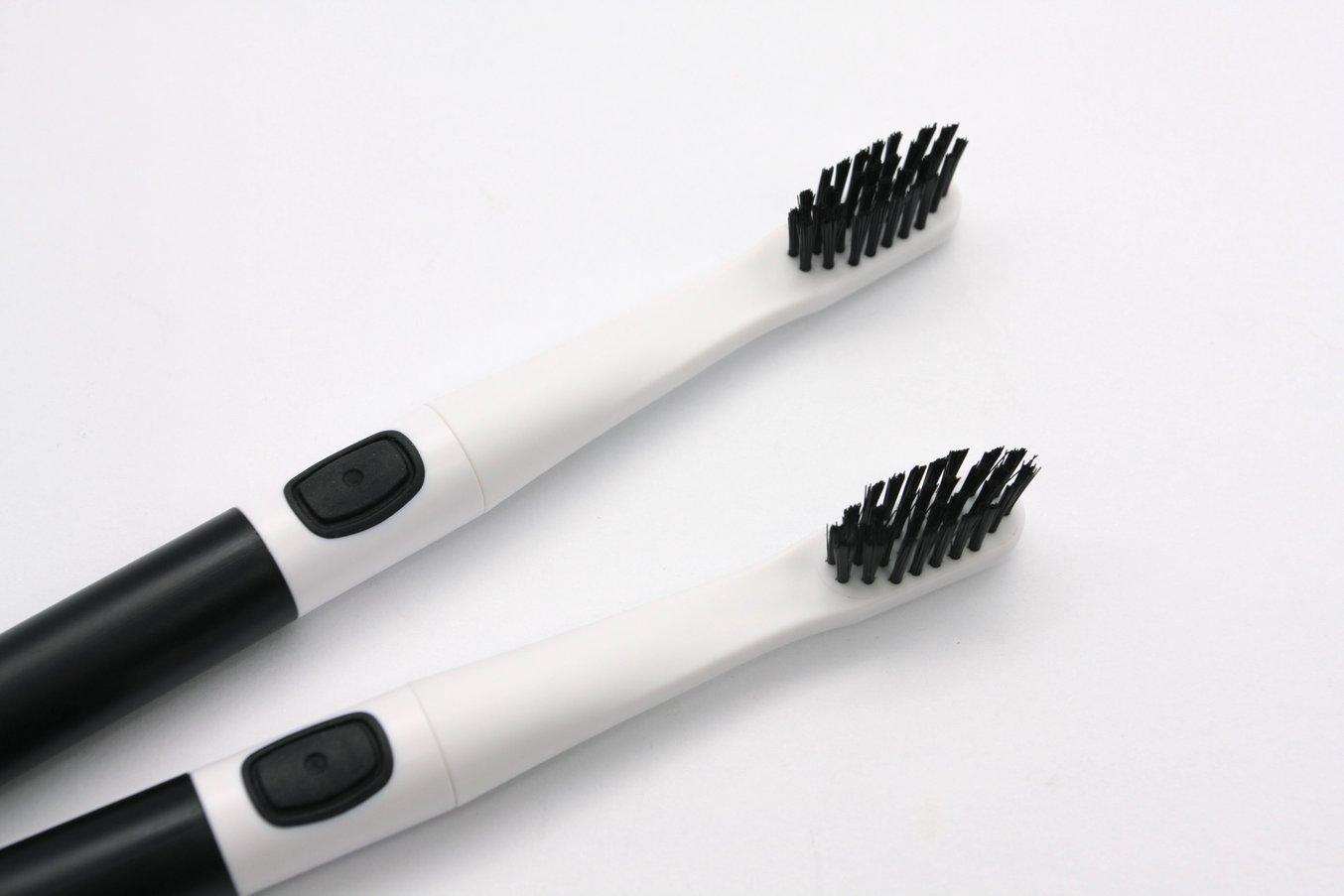
Ein Prototyp einer elektrischen Zahnbürste, der auf dem Form 3 mit White Resin gedruckt wurde (unten), und das endgültige Kunststoffprodukt, das spritzgegossen wurde (oben).
„Wir verwenden jetzt den Form 3 Drucker und Tough 2000 Resin für einige unserer Prototypen. Die Drucke ähneln spritzgegossenem Polyoxymethylen stark. Damit können wir nicht nur einen Prototyp zu Vorführungszwecken herstellen, sondern auch unterschiedliche Designs testen, um deren Funktionalität zu vergleichen und bei Bedarf innerhalb von Stunden die Abmessungen zu optimieren“, so Vong.
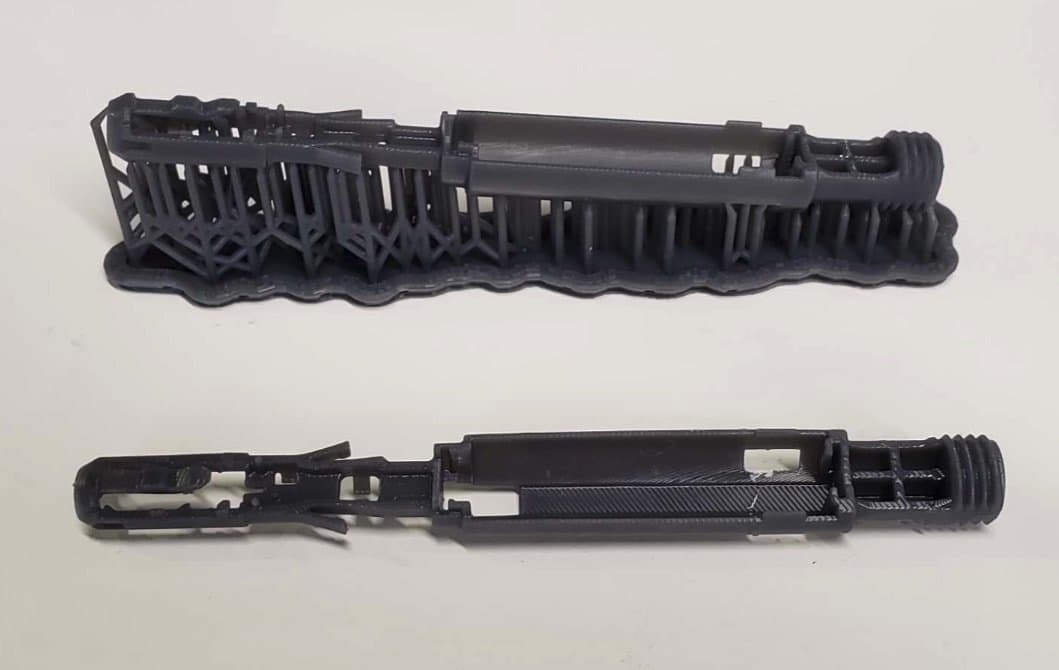
Der Chassis-Prototyp einer elektrischen Zahnbürste, der mit Tough 2000 Resin von Formlabs gedruckt wurde.
Die nächsten Schritte für Hayco
Mundhygiene ist eine Wachstumssegment für Hayco, von der das Unternehmen dank seiner Kernkompetenzen in den Bereichen Tuften, Formenbau und elektronischen und mechanischen Baugruppen sowie durch seine hochentwickelten Testverfahren profitieren kann. Die 3D-Drucktechnologie von Formlabs erlaubt es Hayco, mit der Entwicklung von Geräten für den schnell wachsenden Markt Asien-Pazifik zu beginnen und dabei auf seine Tradition in der Bürstenherstellung aufzubauen.
„Wir werden weiter in 3D-Drucktechnologien investieren, wie das bereits in den letzten 20 Jahren der Fall war. Aktuelle Forschungsbereiche sind lasergesinterte Metallformeinsätze für unsere Formenbau-Abteilung. Wir stellen bereits Teile her, die auf eine andere Weise kaum gefertigt werden könnten“, sagt Vong.
„Formlabs ist für uns ein großartiger Partner und wir freuen uns auf die nächsten Entwicklungen, die das Angebot der verfügbaren Materialeigenschaften noch erweitern“, so Vong.
Möchten Sie unsere Materialien für den Maschinenbau ausprobieren? Sehen und fühlen Sie die Qualität von Formlabs. Lernen Sie unsere Materialien kennen und finden Sie das richtige für Ihre Bedürfnisse.