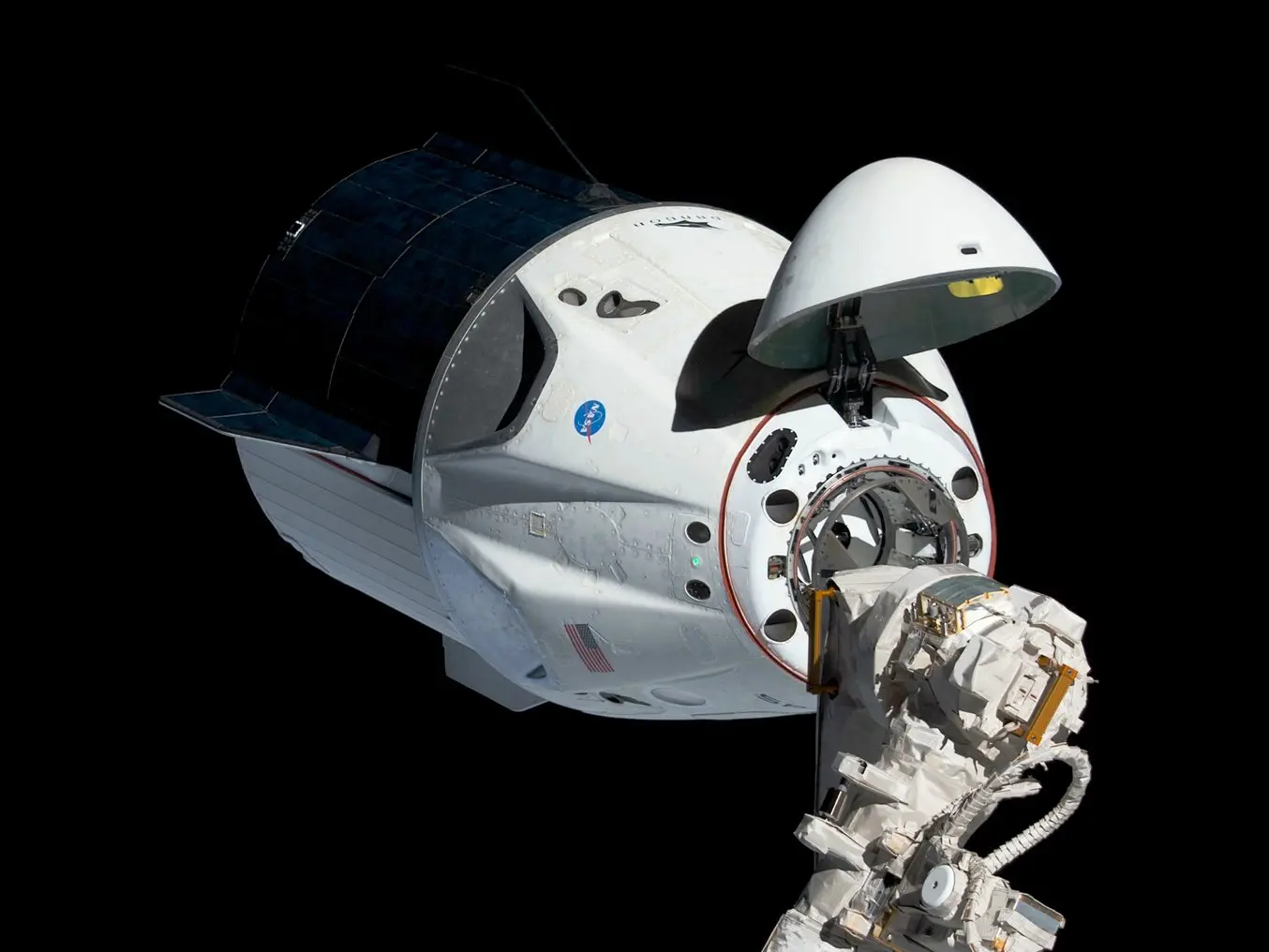
Eine „Dragon“-Kapsel der Firma SpaceX; Foto mit freundlicher Erlaubnis des Goddard Space Flight Center der NASA
Formlabs auf dem Weg zur ISS
Im Laufe des Sommers startet SpaceX die Mission zum 25. kommerziellen Versorgungsdienst (CRS-25) der Internationalen Raumstation ISS. An Bord der Frachtkapsel reisen über 2000 kg Nahrung und Ausrüstung zur Crew der ISS. Die Mission ist Teil des andauernden Frachtvertrags zwischen SpaceX und NASA und umfasst die Zusammenarbeit und Partnerschaft der beiden Organisationen.
Unter den Ausrüstungsteilen des Flugs CRS-25 befinden sich auch galvanisierte Muster aus dem Stereolithografie-3D-Drucker (SLA) Form 3. Mithilfe von Alpha Spaces ISS-Versuchsaufbau „Materials International Space Station Experiment“ (MISSE-16) werden die Musterdrucke der Außenumgebung der Raumstation ausgesetzt. Zu einem späteren Zeitpunkt werden sie dann für weiterführende Untersuchungen zur Erde zurückgebracht. In einer jüngeren Publikation berichtet die NASA über die Ziele eines anderen Experiments und über die Effizienz, die der 3D-Druck zu diesem Projekt beisteuert.
Die 3D-gedruckten und galvanisierten Teile werden den rauen Bedingungen des Alls ausgesetzt. Die Ergebnisse bieten der NASA und anderen Herstellern aus Luft- und Raumfahrt dann Aufschlüsse darüber, wie sich die additive Fertigung in zukünftige Produktpläne einfügt.
Ingenieurfachleute der NASA am Goddard Space Flight Center arbeiten schon länger mit Druckteilen von Formlabs, um das Design solcher Halterungen auf Festigkeit zu optimieren. Die Teile wurden aus Rigid 10K Resin gedruckt, einem glasgefüllten Material, das sich ideal für starre Teile eignet sowie temperatur- und chemikalienbeständige.
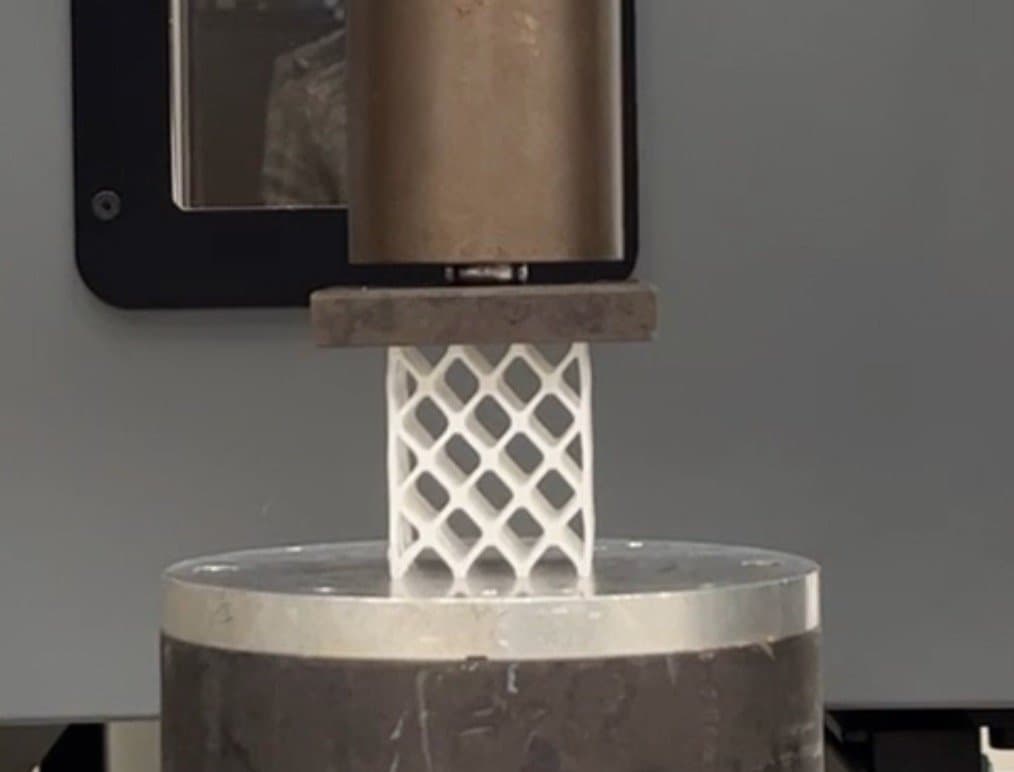
Gitterstruktur aus Rigid 10k Resin vor einem Test (links) und nach einem Test mit Belastung von oben (rechts)
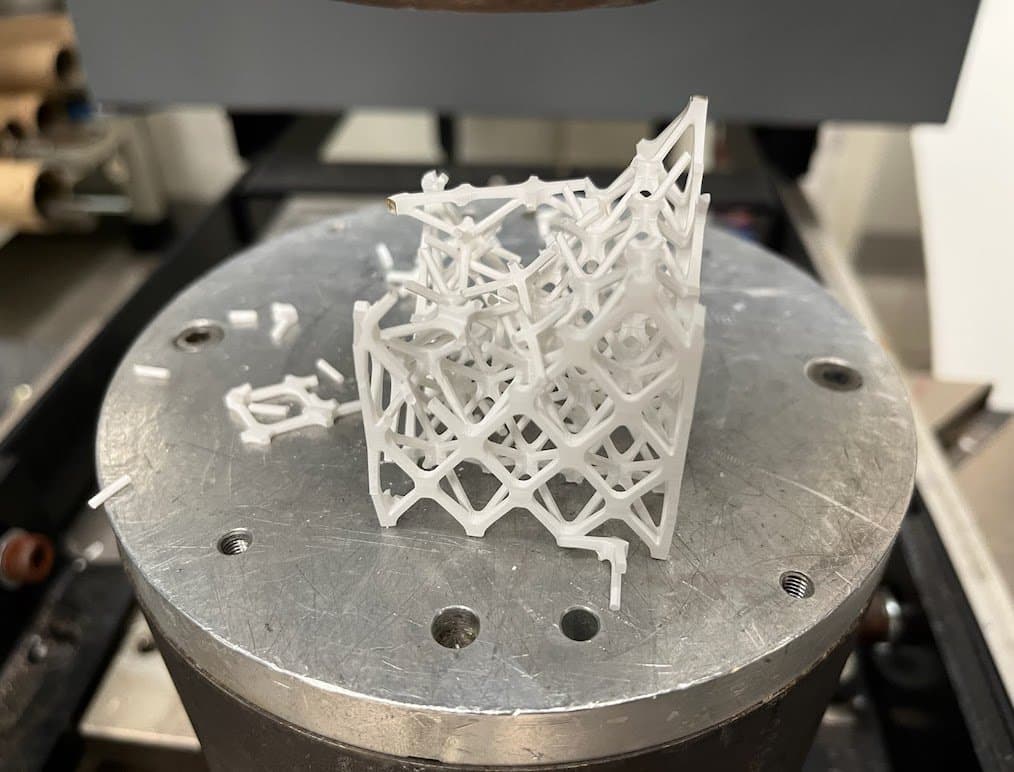
Galvanisierung von Druckteilen zwecks leichtgewichtiger Festigkeit und verringerter Abgase
Die Galvanisierung der Druckteile aus Rigid 10K Resin erhöht die Festigkeit der Teile und verringert die Menge der austretenden Abgase. Der Galvanisierungsprozess seitens des darauf spezialisierten Unternehmens RePliForm erstellt Teile, die wesentlich leichter sind als traditionell zerspante Komponenten für dieselbe Anwendung. Außerdem konnte das Goddard-Team so Design, Druck, Iteration und Neudesign weitaus schneller durchführen als mit CNC-Prozessen. Bei allen Komponenten und Prozessen muss auf den Preis geachtet werden – und so senkte das Team durch die verringerte Arbeitszeit, Vermeidung der Zerspanungskosten und die betriebsinterne Iteration seinen Gesamtanteil am Budget.
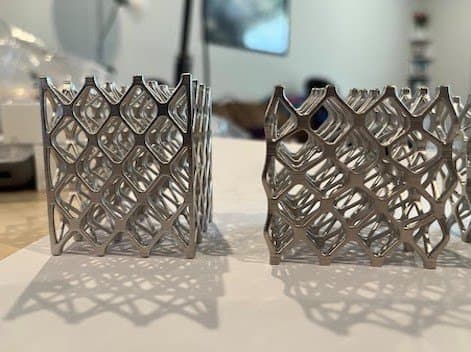
Gitterstruktur aus galvanisiertem Rigid 10k Resin vor einem Test (links) und nach einem Test mit Belastung von oben (rechts)
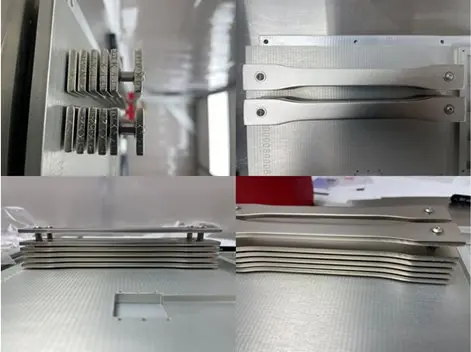
Galvanisierte 3D-Druckteile aus Rigid 10K Resin, die zur ISS gesandt werden
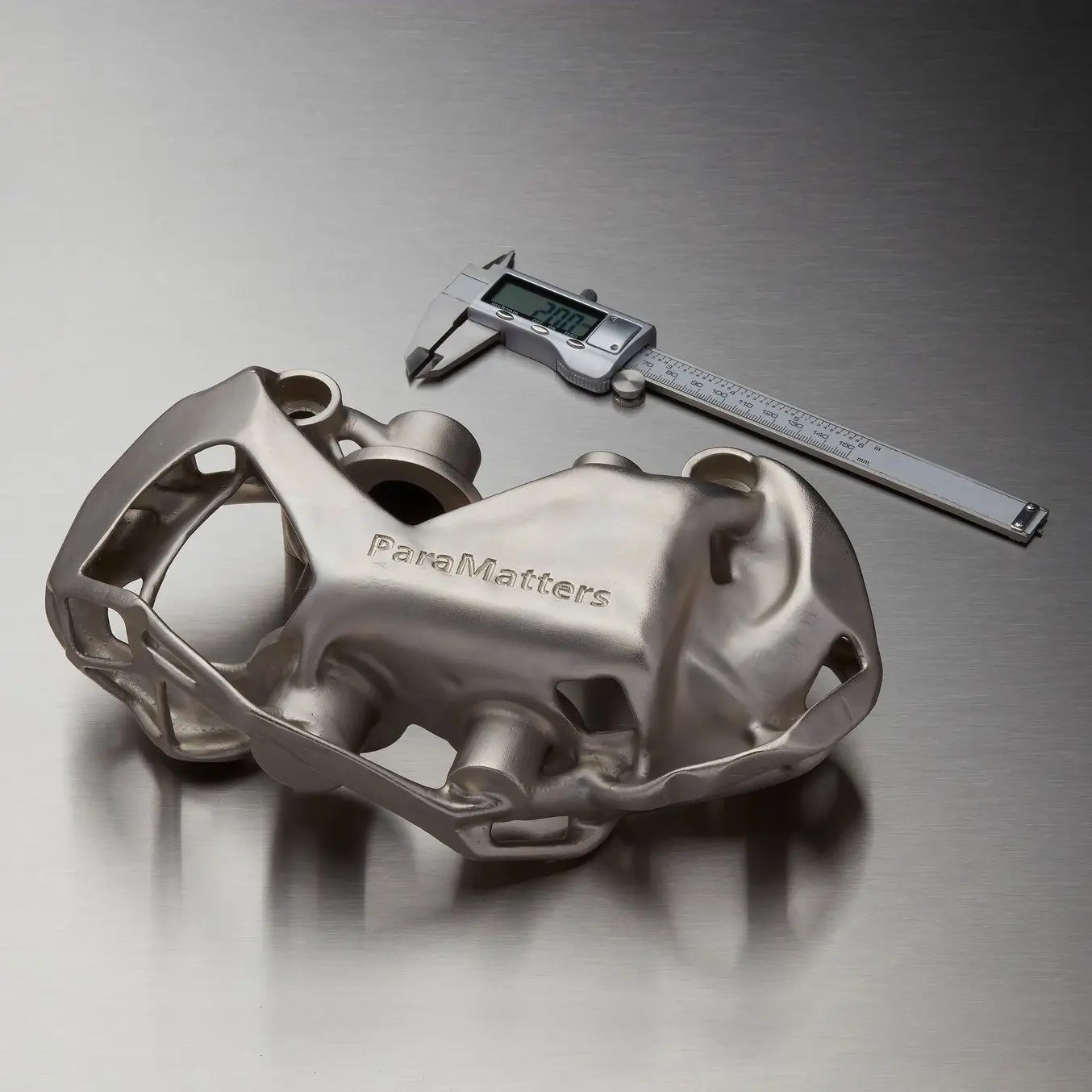
Metallische Festigkeit: Strategien und Anwendungsfälle zur Galvanisierung von SLA-Teilen
Im Folgenden erfahren Sie, wie Ingenieurteams Kunstharz-3D-Teile mit Metall überziehen und warum solche Hybridteile eine überraschend große Anzahl an Anwendungsbereichen eröffnen, z. B. durch mehr Festigkeit und Haltbarkeit in der Endverwendung.