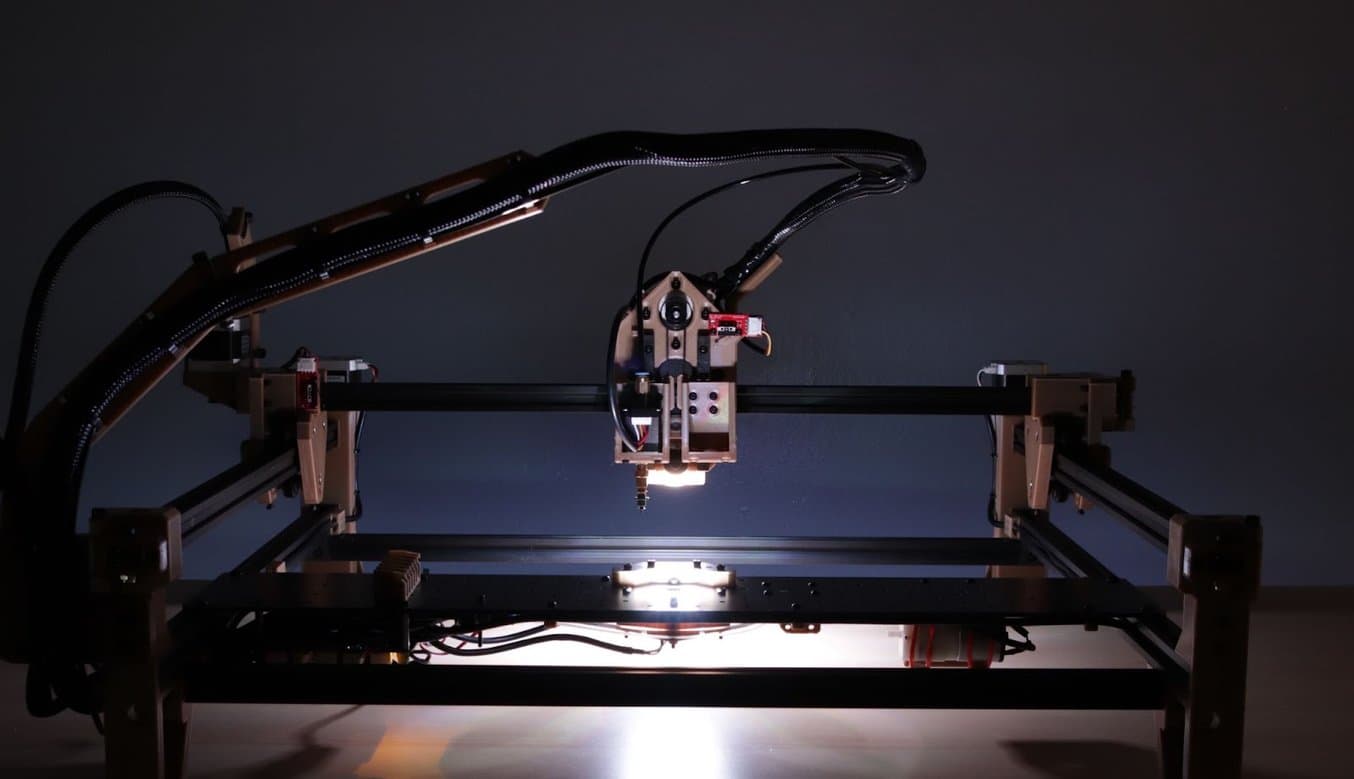
Als junges Unternehmen ist der Einstieg in die Herstellung, Konzipierung und Fertigung handfester Produkte an sich schon schwierig genug. Was könnte da noch herausfordernder sein? Die Produktion der Ausrüstung, die eben diese Produkte herstellt. Stephen Hawes’ Unternehmen Opulo tut genau das – es baut „Pick-&-Place“-Maschinen für mittelgroße Elektronikhersteller. Opulos Maschine nimmt eine elektrische Komponente und platziert sie auf einer Leiterplatte. So entsteht die Hauptplatine, also das Gehirn einer Maschine.
Um die zahlreichen Hindernisse beim Einstieg in die Fertigungsbranche zu überwinden (die von der globalen Krise der Lieferketten nur noch verstärkt wurden), verließ sich Hawes auf zwei entscheidende Faktoren: Alles wurde als Open Source und als Crowd-Development entwickelt und mittels 3D-Druck produziert, um die Kosten zu senken, die Lieferkette robust zu machen sowie die Reaktionsfähigkeit und Gestaltungsfreiheit zu verbessern. Er verwendet den SLA-3D-Drucker (Stereolithographie) Form 3 und ESD Resin, um sich gegen Probleme in der Lieferkette zu wappnen. So stellt er sicher, dass die Mikrochips der Geräte nicht durch elektrostatische Entladungen beschädigt werden. Das spart Tausende Dollar.
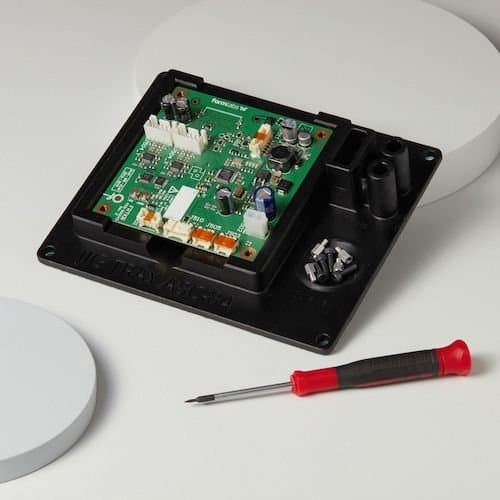
Wir stellen vor: ESD Resin
ESD Resin ist ein kostengünstiges 3D-Druckmaterial zur Herstellung statisch resistenter Teile, die zur Verwendung im Werk gedacht sind.
Das Produkt
2018 arbeitete Hawes am Wachstum eines kleinen Elektrogeräteherstellers mit einer fanatischen YouTube-Gefolgschaft. Doch als die Nachfrage stieg, stieß er in die altbekannten Fertigungsprobleme: Der Zusammenbau der Leiterplatten als Herzstücke der Geräte war extrem arbeitsaufwändig; die Mengen waren jedoch noch zu klein für traditionelle Fertigungsautomatisierung.
Als eingefleischter Problemlöser gründete Hawes also das Unternehmen Opulo und arbeitete an einer Platzierungsmaschine, die kleine Elektronikkomponenten aufhebt und auf einer grünen Leiterplatte positioniert, welche wir als das „Gehirn“ einer Maschine verstehen können. Opulos geistiges Eigentum ist komplett quelloffen, so hat er einen enthusiastischen Kundenstamm aufgebaut sowie eine Experten-Community, die bei der Weiterentwicklung der Technologie mit Rat und Tat zur Seite steht.
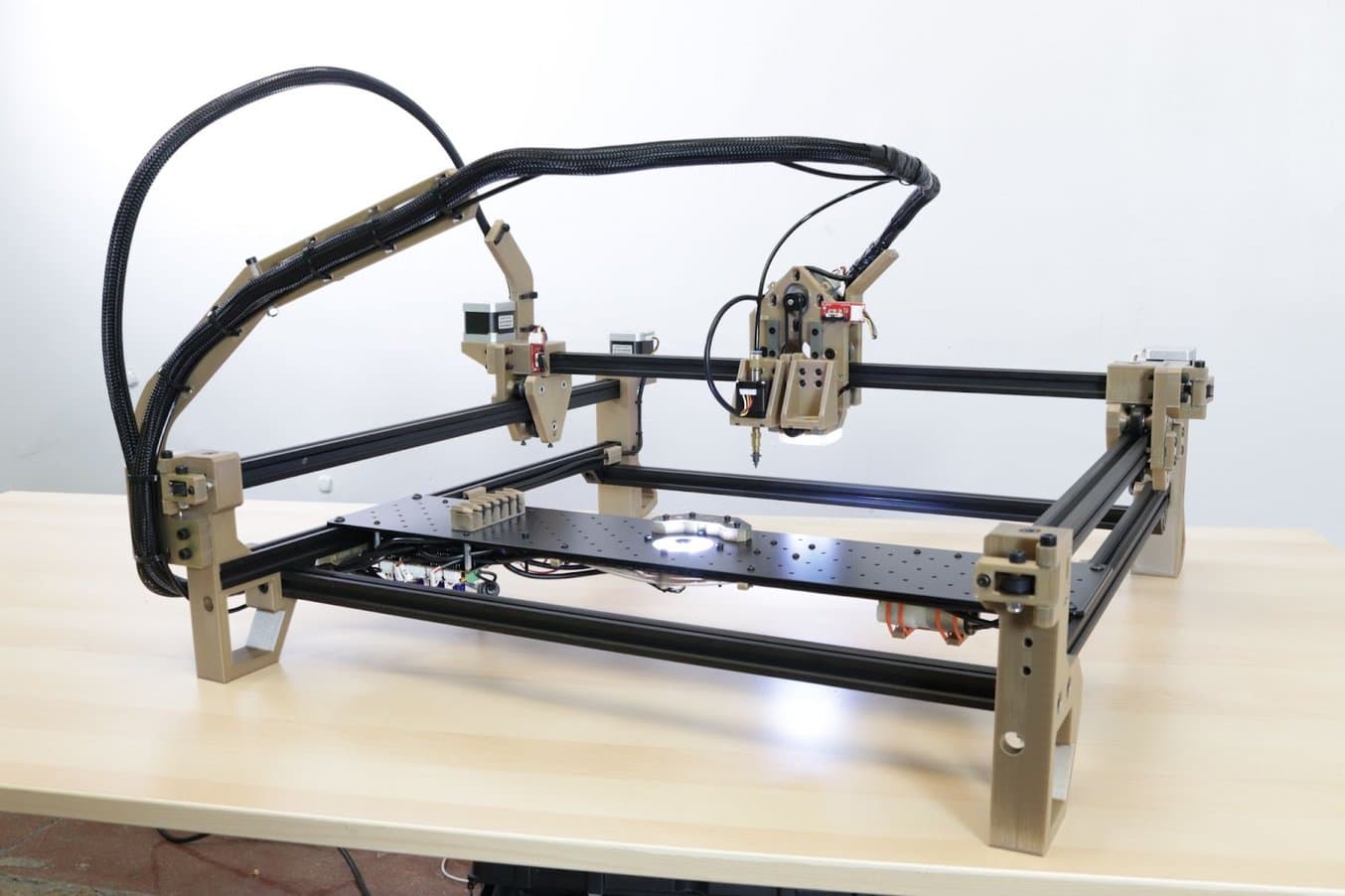
„Ich bin ein Allrounder. Ich kann von allem etwas, aber ich bin nicht der beste Elektrotechniker oder Maschinenbauingenieur. Dank Open Source habe ich Studierte zur Seite, die mir dann sagen ‚Hier, mach das so‘. Es geht um den Aufbau einer Community, um Enthusiasmus, darum, Leuten zu helfen und es dir Community zurückzuzahlen, die mir so viel geholfen hat. Und es geht auch darum, Hilfe zu bekommen.“
Mithilfe der Community hat Opulo den LumenPnP entwickelt und liefert nun Geräte an kleine und mittelständische Unternehmen. Hunderte von Geräten sind im Einsatz. Dabei gibt es hauptsächlich drei Kundenkategorien:
-
Auftragswerkstätten: kleine Dienstleister, die auf Auftrag Kleinserien produzieren
-
Hobbybastler*innen: Leute mit kleinen Elektronikprojekten, die keine Zeit für manuellen Zusammenbau haben
-
Kleinunternehmen: Firmen, die ihre Produkte im eigenen Betrieb herstellen und nicht die nötigen Mengen produzieren, um einen Vertragshersteller zu rechtfertigen. Auch Opulo fällt in diese dritte Kategorie und verwendet den LumenPnP, um neue LumenPnPs herzustellen.
800 % höhere Kosten bei Siliziumchips
In der Entwicklungsphase trat ein großes Problem auf, das von der Open-Source-Community nicht behoben werden konnte. Die Leiterplatinen versagten erschreckend oft. Anhand von Tests stellte das Team fest, dass die Siliziumchips, aus welchen die Leiterplatinen bestehen, elektrostatisch beschädigt waren. Weiterhin fiel den Teammitgliedern auf, dass ihre Stühle ihnen Stromschläge versetzten. So kombinierten sie, dass die beim Zusammenbau entstehende Reibung die empfindlichen Chips elektrisch beschädigte.
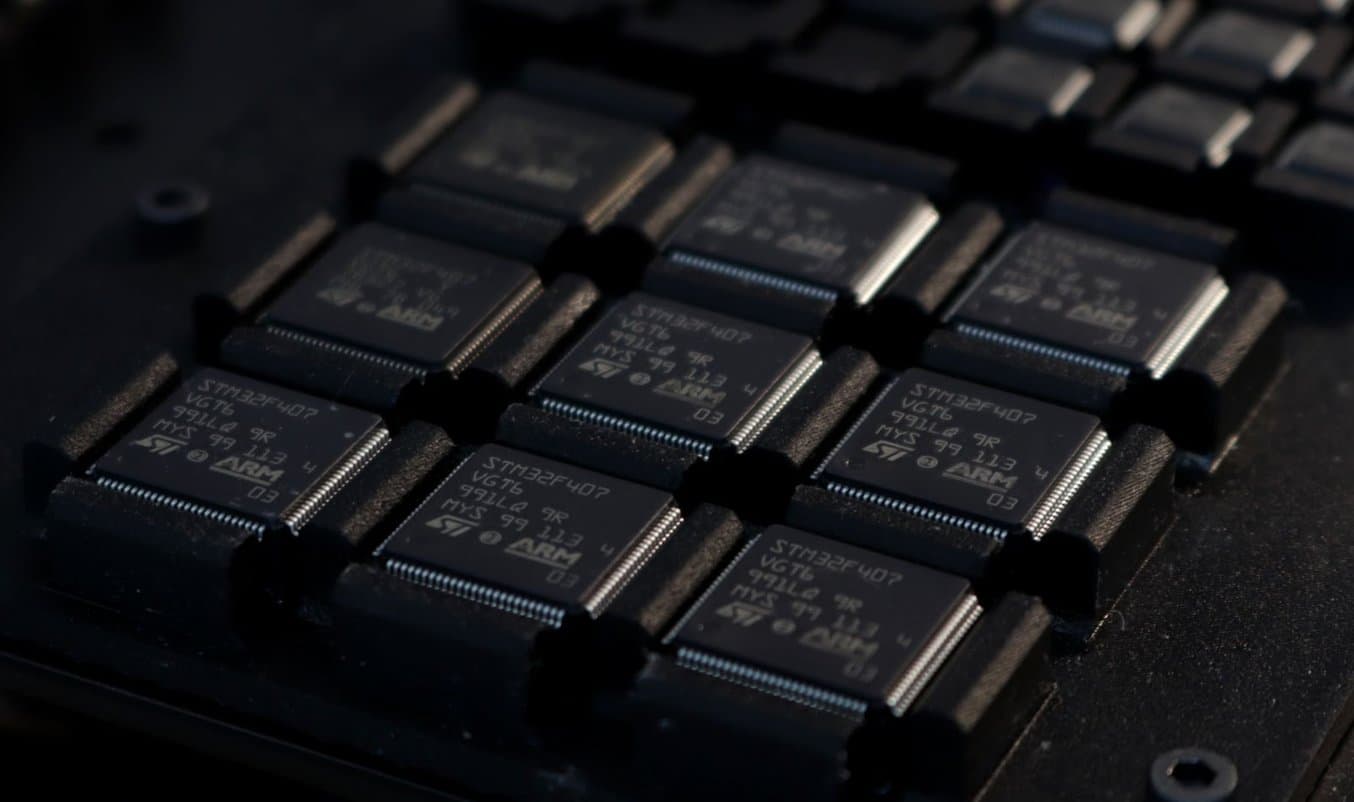
Eine fertige Leiterplatine, deren Siliziumchips durch ESD Resin vor elektrostatischen Entladungen geschützt werden
„Diese Chips sind teuer, da wollen wir nicht, dass sie kaputtgehen. Wir haben die Lötpunkte eine Million mal untersucht. Daran lag es nicht. Wir trugen ESD-ableitfähige Armbänder (die die elektrischen Entladungen sicher in den Boden ableiten), also waren wir nicht der Auslöser. Letztendlich kamen wir auf die Tabletts, die die Chips festhalten.“
Je weiter der Entwicklungsprozess fortschritt, desto gravierender wirkten sich die Kosten der kaputten Chips aus. Im Jahr 2021 litt auch Opulo unter der Krise der Lieferkette und der oft diskutierten Knappheit an Chips. Der Preis einzelner Chips stieg von vorher 3,60 USD auf 60 USD pro Chip. Da fiel jeder kaputte Chip ins Gewicht.
„Es ist niederschmetternd, furchtbar, wenn ein Chip kaputtgeht. Sie sind für uns wie Gold. Wir können sie nicht einfach zerstören. Jetzt, mehr denn je, ist es Zeit, in ESD-Schutz zu investieren. Wenn das Produkt im Betrieb ankommt, müssen wir unbedingt sicherstellen, dass es vor Elektrostatik geschützt ist.“
Um einen komplett ESD-geschützten Arbeitsablauf einzuführen, wandte sich Hawes dem Form 3 und ESD Resin zu. Der Druck der maßgefertigten Chip-Tabletts eliminiert das Risiko von ESD-Beschädigungen an den äußerst teuren und wichtigen Chips. Er erzählte uns: „ESD Resin ist fantastisch. Es ist einfach nur toll, zu wissen, dass den Chips nichts mehr passiert. Ich wüsste nicht, was wir ohne es anfangen sollten.“
Optionen für ESD-ableitfähige Teile in der Fertigung
Hawes hat Recht. Es gibt in der Fertigung nicht viele kosteneffiziente Alternativen zu 3D-gedrucktem ESD Resin. Ein Spritzgussteil bedeutet keine Änderungen des Designs und hohe Kosten zur Produktion der Form. Ähnlich sieht es beim Fräsen aus. Auch da gibt es ESD-ableitfähige Materialien, doch gelten dieselben Einschränkungen. Passende Filamente existieren für andere Druckertypen, doch die geringere Auflösung kann sich für die hochpräzisen Platzierungsroboter als schwierig erweisen, wenn die Liegefläche der Chips nicht perfekt glatt ist. Und Metall, welches zwar ableitfähig und ESD-geschützt ist, ist in der Werkzeugproduktion extrem teuer. Und auch hier müsste man sich auf ein spezifisches Design für die vielen unterschiedlichen Produktionsserien festlegen.
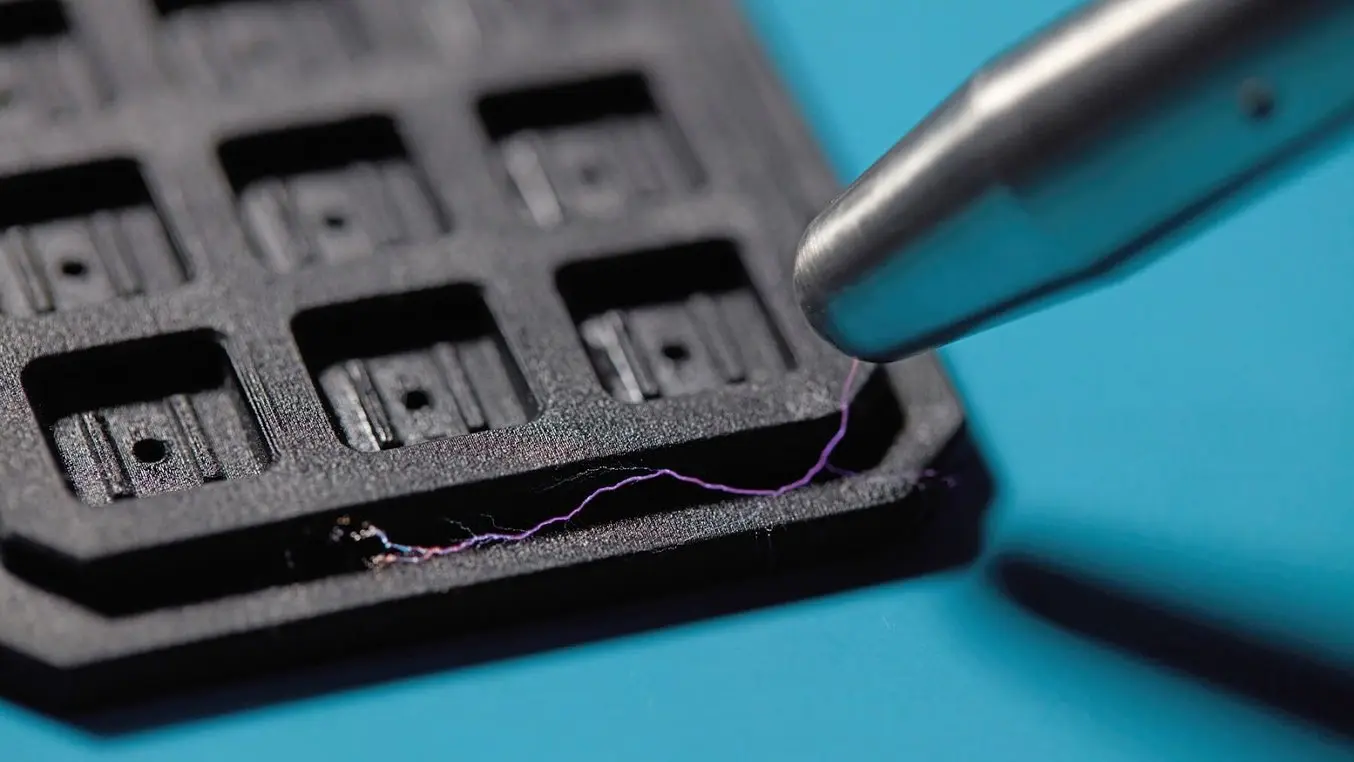
Elektrostatische Entladungen (ESD) können empfindliche Elektronik beschädigen, wie z. B. Computerchips aus Silizium.
„Man kann sich ESD-ableitfähige Spritzgussteile besorgen, doch die Erstanschaffungskosten dafür sind astronomisch ... insbesondere, wenn sich das Design noch ändert ... man könnte es fräsen ... aber selbst das ist es nicht wert oder besonders schnell. Außerdem haben wir keinen Platz für eine Fräsmaschine. Es ist leicht, einen Form 3 in die Ecke zu stellen, mit Form Wash und Form Cure darunter. Ich will das Gerät nicht die ganze Zeit im Auge behalten müssen.“
Eine skalierbare Lösung
In einem jungen Unternehmen, das gerade die ersten Produkte verkauft und noch wächst, ist Platz ein entscheidender Faktor. Viele Systeme, die die Präzision und die Materialvielfalt des Form 3 bieten, haben große Ansprüche an die Infrastruktur vor Ort. „Die Tatsache, dass wir keinen speziellen Platz dafür brauchen, ist ein riesiger Vorteil. Die Stellfläche ist klein, deshalb können wir richtig hochauflösende Teile in unserem Büro herstellen. Wir können ganz verrückte Präzisionsteile betriebsintern anfertigen“, berichtet Hawes.
Vielleicht ist der wichtigste Faktor bei der Auswahl eines 3D-Druckers für den LumenPnP die Genauigkeit. Der Roboter platziert winzige Chips in ebenso winzigen Ecken der Platine. Dabei können ein paar Mikrometer Abweichung bereits den Chip zerbrechen, was das Unternehmen 60 USD kostet und die Fertigstellung des Produkts behindert.
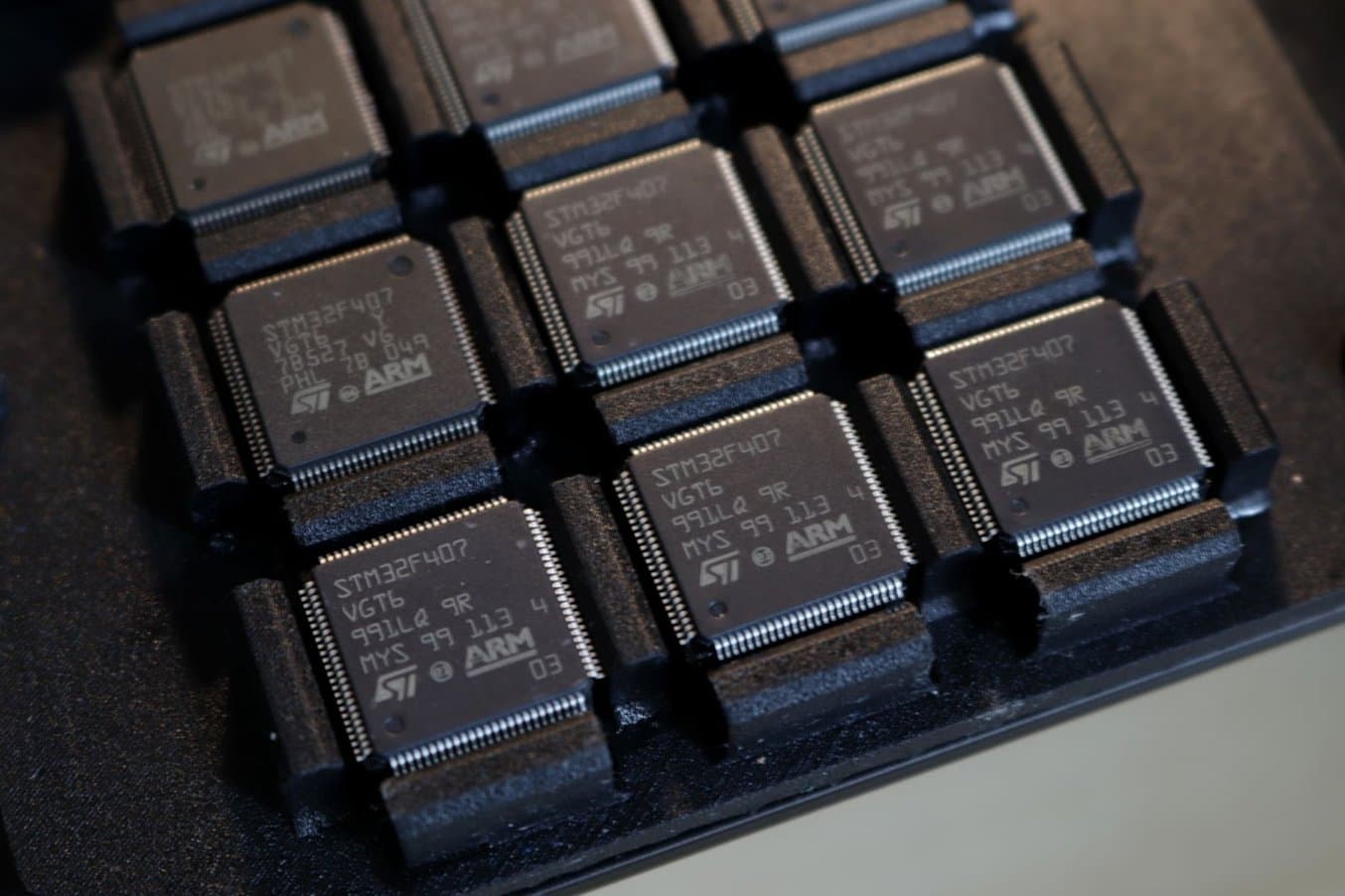
Computerchips aus Silizium sind ein integraler Bestandteil in der Fertigung vieler Produkte. Ihr Preis ist seit 2019 um 800 % gestiegen.
„Diese Teile sind höchst empfindlich, zerbrechlich und präzise. Um einen solchen Chip aufzunehmen, ist ein präziser 3D-Drucker eine fantastische Lösung.“
Auch die Materialvielfalt macht den Form 3 für Opulo zu einem Allzweckgerät. Neben ESD Resin nutzt das Team auch die Kunstharzfamilie Tough & Durable für verschiedenste Anwendungen. Beim Druck bestimmter Komponentenhalterungen ermöglicht Clear Resin die Überwachung der Chipposition aus jedem Winkel, dank der durchsichtigen Oberfläche. Für die Halterungen und Vorrichtungen, die die Leiterplatten festhalten, nutzt Opulo Tough 2000 Resin, ebenso wie für den Druck tragender Teile wie Klemmen oder auch für Prototypenteile des Roboters.
„Wir verwenden Clear Resin und Tough 2000 Resin. Clear Resin ist toll, da es sich schnell und gut drucken lässt. Und man kann gut durch die Geometrien hindurchsehen. Tough 2000 Resin ist mein Lieblingskurzharz, einfach das beste. Das nehmen wir für alles, was fest sein muss.“
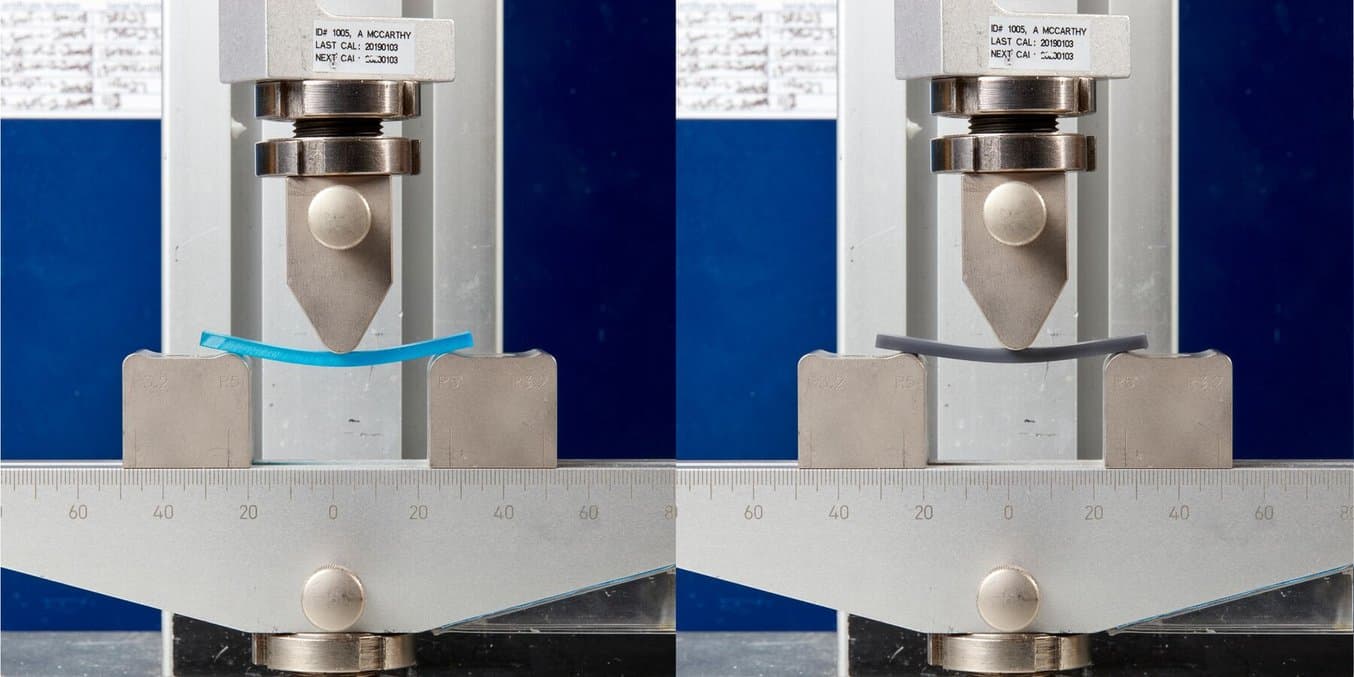
Die Neuformulierung als Tough 2000 Resin (früher blau, heute grau) bietet verbesserte Festigkeit und Haltbarkeit unter Last.
Ein Blick auf die Zukunft mit dem Form 3
Blickt Opulo in die Zukunft der eigenen Fertigung, muss sich das Unternehmen absichern gegen weitere Preisexplosionen in der Lieferkette und gegen Materialknappheit. Jüngste internationale Ereignisse haben einige der größten Siliziumchipfabrikanten aus dem Verkehr gezogen und Hersteller wie Opulo können sich elektrostatische Beschädigungen nicht leisten. Dank Form 3 und ESD Resin schützen sie ihre Komponenten und bereiten sich auf eine wachsende Produktion vor.
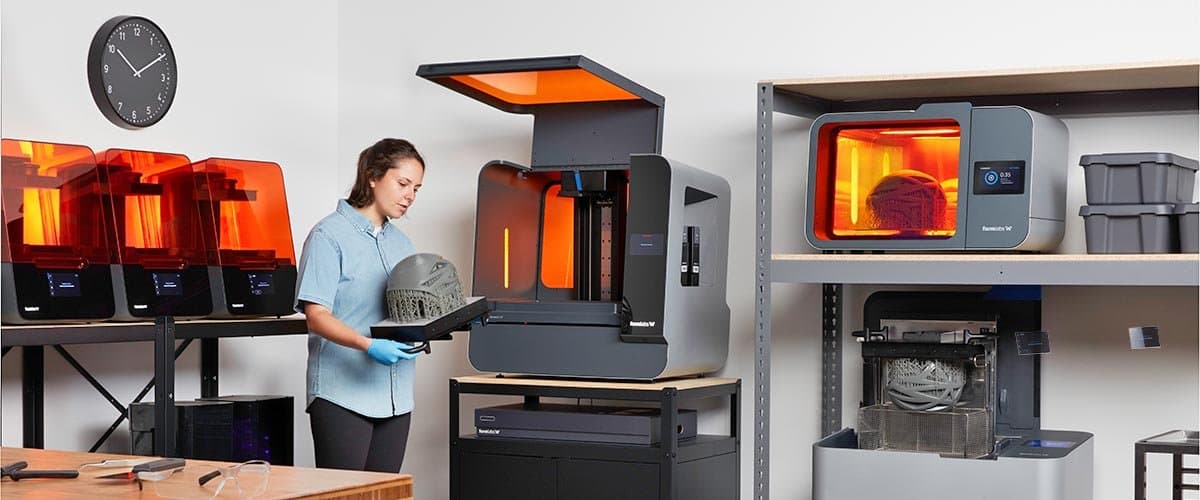
Nach Hunderten verkaufter Geräte und einer langen Warteliste wirft Opulo einen Blick auf den Spritzguss, entwickelt den Prototyp aber fertig mit dem Form 3, damit das abschließende Teil so perfekt wie möglich ausfällt. Dabei berät die Entwicklercommunity das Unternehmen in der Iteration; und Opulo freut sich auf die Zukunft mit dem Form 3 und dem LumenPnP.
„Das Wissen, dass wir gleich zu Anfang die passende Geometrie haben, ist enorm wichtig. Es schließt die Lücke auf wunderbare Art und Weise.“