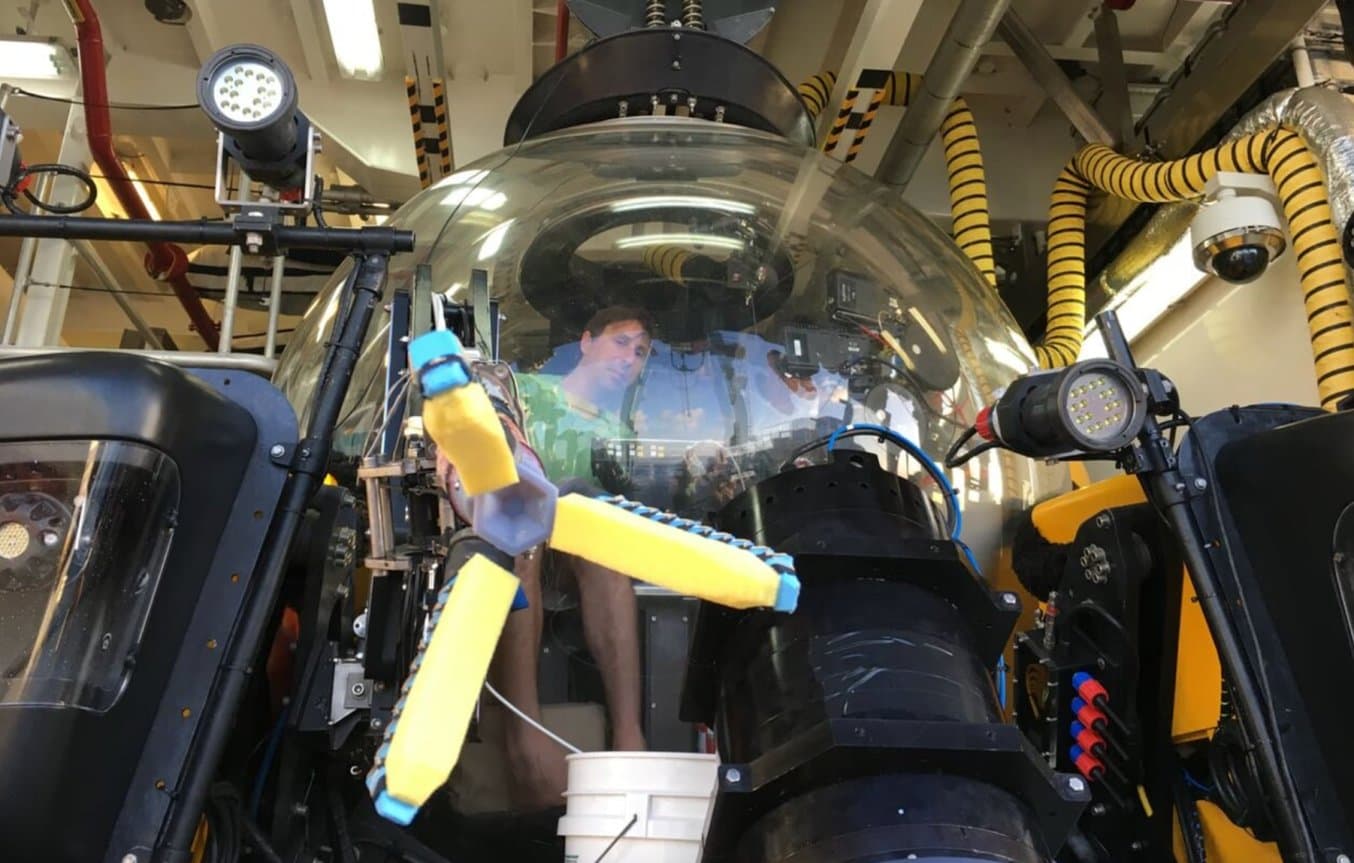
Brennan Phillips, Leiter der Forschung am Labor für Tiefsee-Robotik der URI. Bildrechte: David Gruber.
Während die internationale Gemeinschaft danach strebt, immer weiter ins All zu reisen, liegt eine wahrhaft unüberwindbare Barriere womöglich direkt auf unserem Heimatplaneten. Über 70 % unseres Planeten sind von Ozeanen bedeckt, doch nach Schätzungen der National Oceanic and Atmospheric Administration (NOAA) sind erst weniger als 20 % der Ozeane vollkommen erforscht.1 Im Gegensatz zur Weltraumforschung ist die Tiefseeforschung seit Langem unterfinanziert und vernachlässigt. Einige Forscher geben trotz zahlloser Herausforderungen nicht auf und nutzen erschwinglichen 3D-Druck, um in immer weitere Tiefen vorzudringen.
Am Labor für Unterwasser-Robotik und Bilderfassung, das zum Bay Campus der University of Rhode Island (URI) gehört, entwickeln Professor Brennan Phillips und ein Team aus Studierenden Hilfsmittel zur Erkundung der Ozeane in Tausenden Metern Tiefe. Mithilfe der Stereolithografie-3D-Drucker (SLA) Form 3+ und Form 3L druckt das Labor wasserdichte Kameragehäuse und eine Vielzahl von Forschungsinstrumenten.
Wasserdichte Teile unter Druck
Die Kartierung der Ozeane verlangt nach Hilfsmitteln, die nicht nur wasserdicht sind, sondern es auch unter dem enormen Druck weit unterhalb der Wasseroberfläche bleiben. Phillips und die Studierenden in seinem Labor entwarfen ein 3D-gedrucktes Gehäuse für eine Kamera, dank dessen diese auch unter Druck vollkommen trocken bleibt, aber dennoch leicht entnommen werden kann, um nach einem Einsatz die Daten abzurufen. Nach Dutzenden von Iterationen entschied sich das Team für ein zylindrisches Design, das in zwei Bauteilen aus Clear Resin auf dem Form 3+ gedruckt wird. In der internen Struktur des Gehäuses ist die Leiterplatine untergebracht und eine Epoxidharzfüllung sorgt dafür, dass die Kameralinse in der Schwebe gehalten wird. Unter der Linse befindet sich nur Epoxidharz, das durch in das Gehäuse integrierte Bullaugen eingespritzt wird.
„Wir standen vor der Herausforderung, eine Tiefseekamera in möglichst kleiner Größe möglichst günstig zu entwickeln. Mittlerweile haben wir Dutzende Modelle in verschiedenen Formen gedruckt, und dank des Druckprozesses sind uns bei der Form keine Grenzen gesetzt. Wir können Designs schnell erstellen, die Elektronik zusammenbauen, in das Gehäuse einsetzen, die Größe optimieren und dann das Epoxidharz eingießen“, berichtet Phillips.
Der 3D-Druck hat es dem Labor möglich gemacht, ausgiebig zu iterieren, ohne sich Sorgen über die Kosten zu machen, und erlaubt zudem eine größere Gestaltungsfreiheit als das Zerspanen.
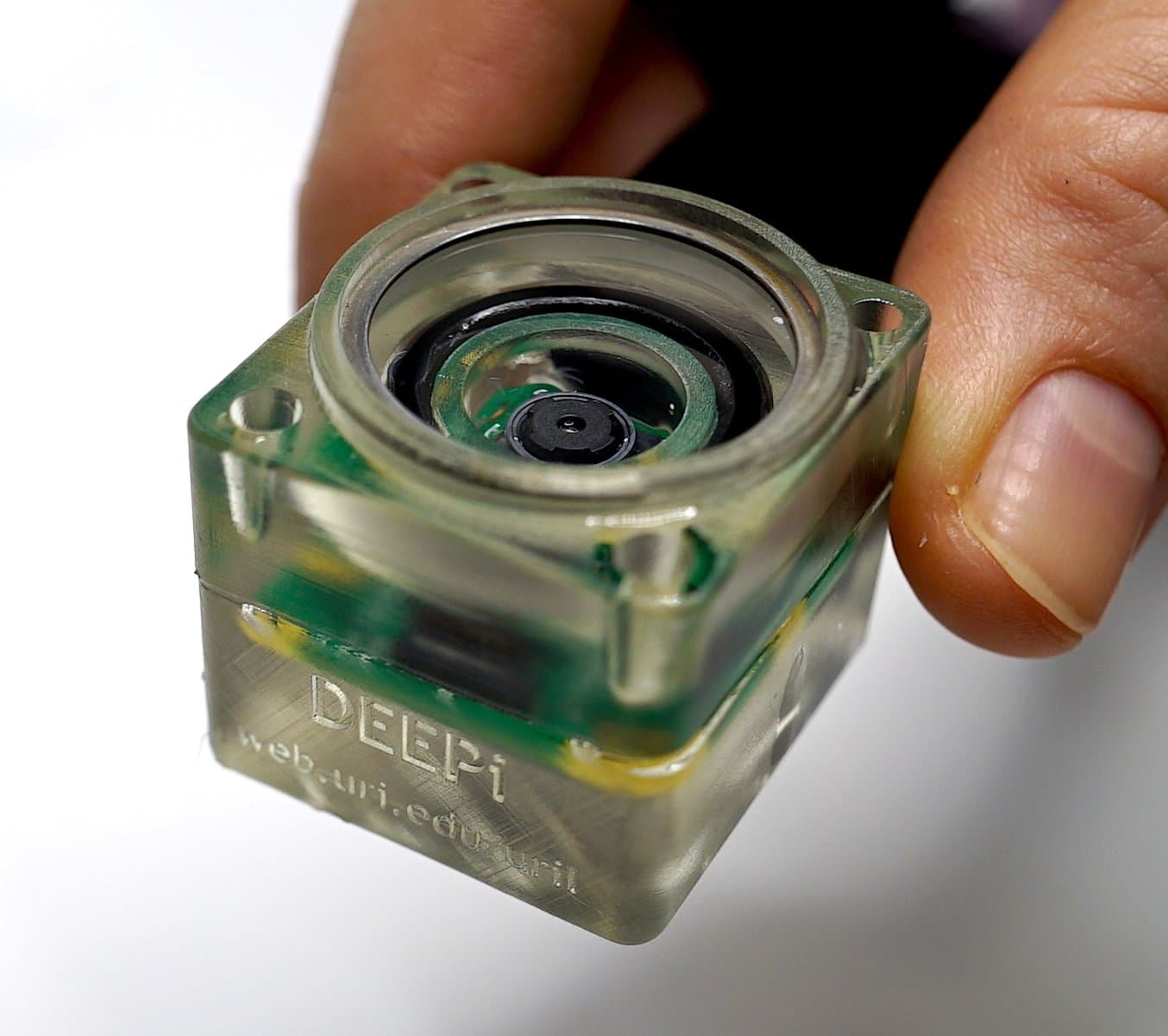
Das hybride Design der DEEPi-Kamera beinhaltet eine 3D-gedruckte Form und eine O-Ring-Dichtung sowie einen mit Epoxidharz gefüllten Hohlraum für die Komponenten der Leiterplatine und ein externes Ansichtsfenster aus klarem Glas (US-Patent #16/920 577). (Bildrechte: Brennan Phillips).
Im Labor wird die Tiefseeumgebung mithilfe eines Drucktanks simuliert. Sobald Phillips und sein Studierendenteam sich auf das zweiteilige Design mit Epoxidharz festgelegt hatte, legten sie die Teile in eine Druckkammer und erhöhten den Druck, um die Bedingungen der Tiefsee nachzuahmen. „Es war wirklich ein Experiment. Ich ging immer weiter runter, und zwar weiter als wir jemals erwartet hatten, sogar Tausende von Metern“, erzählt Phillips.
Warum SLA die perfekte Lösung für die Tiefseerobotik ist
Bei der Beurteilung verschiedener 3D-Drucker standen Genauigkeit und Materialeigenschaften für Phillips und sein Labor an erster Stelle. Aufgrund ihrer Isotropie sind Teile aus SLA-3D-Druckern nicht porös und lassen kein Wasser durchtreten, wie es bei Teilen aus FDM-Druckern (Schmelzschichtung) womöglich der Fall wäre. Die glatte Oberflächenbeschaffenheit von SLA-Teilen sorgt außerdem dafür, dass funktionale Baugruppen wie das zweiteilige zylindrische Gehäuse sich zusammenfügen, ohne dass raue Oberflächen Luftlöchern entstehen lassen. Auch die Maßgenauigkeit und hohe Auflösung der Druckteile tragen dazu bei, dass sie wasserdicht sind. Dank der unglaublich engen Toleranzen und kleinen Mindestgröße von Merkmalen lassen sich Schraubgewinde direkt in das Material drucken, was sich Phillips' Laborteam sowohl bei diesem zweiteiligen Gehäuse als auch bei den Schrauben zunutze macht, die die Verbindung zusätzlich absichern.
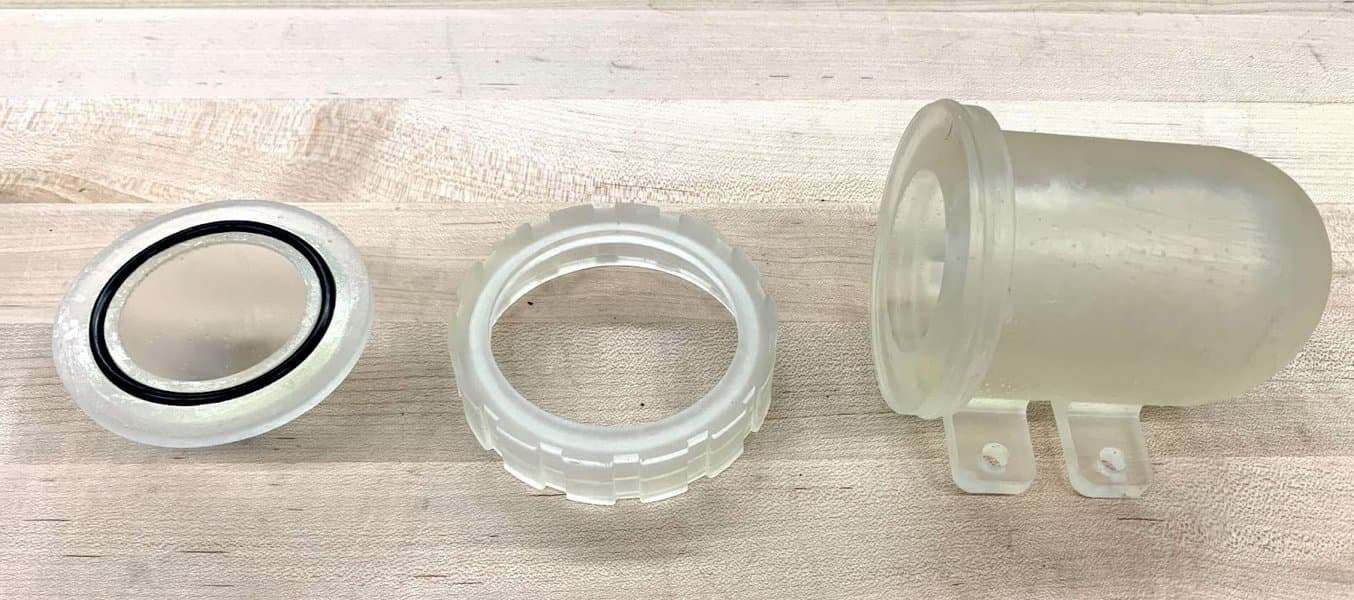
Eine vollständig 3D-gedruckte Baugruppe für ein Gehäuse, das Elektronikkomponenten auch in Tiefen von über 1000 Metern und unter hohem Druck vor Meerwasser schützt. Die O-Ringe werden direkt in die Bauteile eingedruckt und das Gehäuse wird mit einer handgeschraubten Lünette verschlossen. Foto und Design: Breanna Motsenbocker
„Man braucht die hundertprozentige Füllung von SLA-Teilen – mit FDM erreicht man vielleicht eine IP-Schutzklasse, aber die hält über mehr als ein paar Meter Druck hinaus nicht stand. Zweitens brauchen wir die hohe Auflösung, damit der O-Ring zwischen den zwei Teilen eine vollständige Abdichtung erzielt. Diese Teile kommen direkt aus dem Drucker, wir schleifen sie vielleicht etwas ab und richten sie so aus, dass alle kritischen Oberflächen glatt sind. So erhalten wir dann perfekte Dichtungen“, so Phillips. „Der dritte Grund ist, dass die Materialeigenschaften von SLA-Materialien weitaus besser sind – da gibt es im Grunde gar keinen Vergleich. Sie bringen eine viel höhere Leistung bei der Streckfestigkeit. Einfach alle Module sind besser als die aller anderen Materialien, die wir gefunden haben.“
Die Genauigkeit und das Materialangebot der Formlabs-Drucker haben die Kreation des Labors – die wasserfesten Gehäuse für den Tiefseeeinsatz – sowohl an Land als auch unter Wasser zum Erfolg gemacht. Im Januar 2020 veröffentlichten Phillips und sein Studierendenteam ihren Prozess zum 3D-Druck mit einer Stabilisierungsvorrichtung für den Form 2. Es gelang ihnen, die gleichen Gehäuse ohne messbare Unterschiede verglichen mit den an Land gedruckten Exemplaren zu drucken, was bedeutet, dass sich die Komponenten vor Ort auf Schiffen rund um den Globus drucken und sofort einsetzen lassen. Der Bericht belegt, dass sich diese essenziellen Hilfsmittel kostengünstig und lokal herstellen lassen und unterstützt damit die Mission des Labors, die Tiefseeforschung zu demokratisieren.
Die Implementierung des Form 3L
Als Formlabs die Einführung des Form 3L ankündigte, gehörten Phillips und sein Team zu den Ersten, die sofort einstiegen. „Wir waren einer der Erstanwender des Form 3L“, erzählt Phillips. Das Großformat des Form 3L hat es dem Team ermöglicht, mit größeren Designs für die Unterwasserforschung zu experimentieren und das Labor in zusätzlichen Funktionen durch innovative Forschungsinstrumente zu unterstützen.
Um die Gehäuse und andere Überwachungsgeräte unter Wasser in Gebrauch zu nehmen, muss das Labor Hunderte von Metern lange, dünne Glasfaserkabel einsetzen und warten. Zur Vermeidung von Knoten nutzte das Team zunächst umfunktionierte Fahrrad-Räder, die die Kabel über die Bootsreling leiteten. Ausgestattet mit einem großformatigen SLA-Drucker konnten sie jedoch Prototypen für diese Vorrichtung entwickeln, um ihre Größe zu verringern und den Vorgang effizienter zu machen.
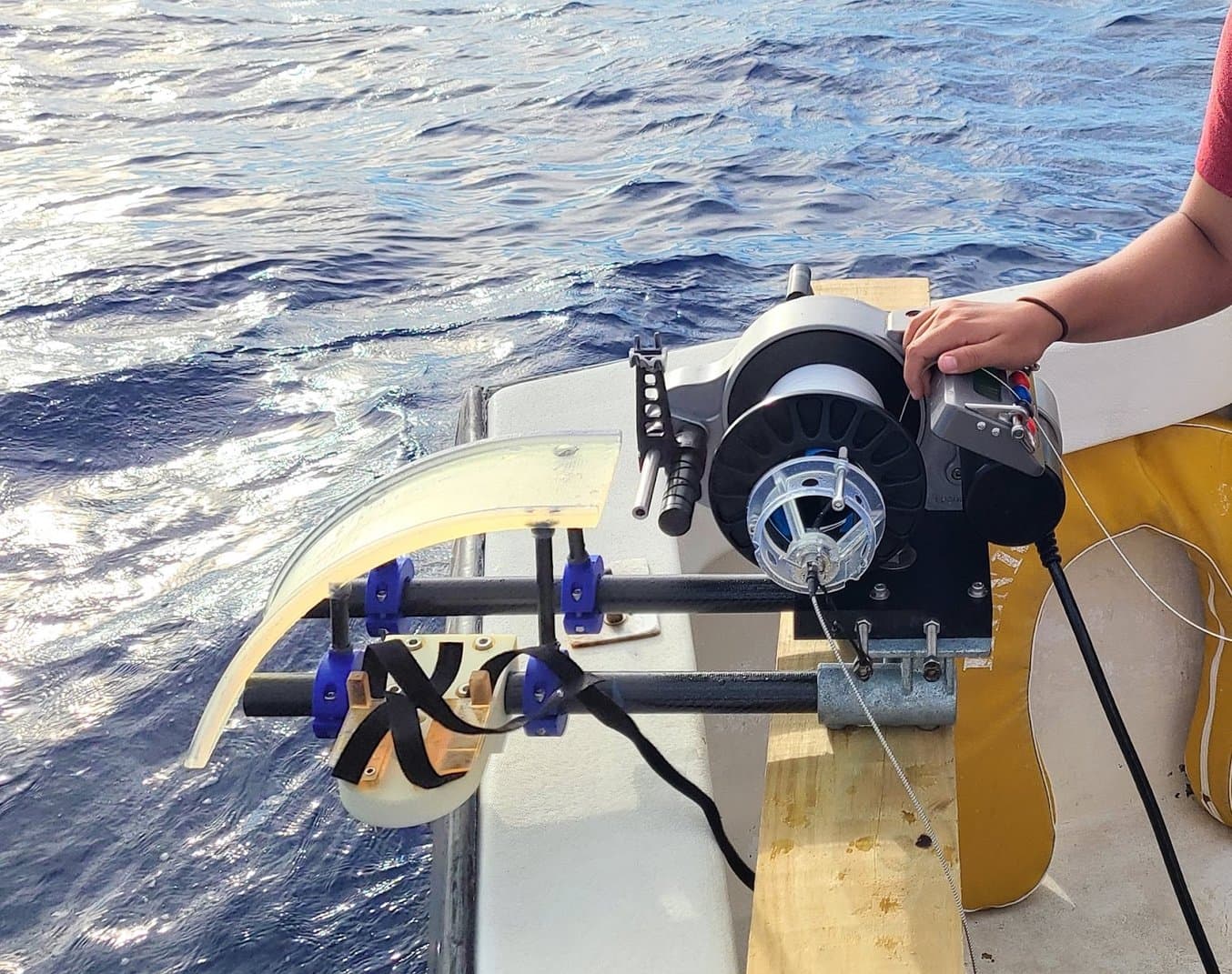
Mithilfe einer 3D-gedruckten rutschenartigen Schiene können die Glasfaserkabel reibungslos über die Reling geleitet werden, ohne dass sie verknoten oder brechen. (Bildrechte: Brennan Phillips)
„Für diese Angelsehne möchten wir keine Drehscheiben oder Räder benutzen. Wir brauchten eine Schiene. Also druckten wir drei oder vier Iterationen dieser Vorrichtung. Sie ist groß und schön glatt, und die Glätte ist bei dünneren Sehnen sehr hilfreich“, erklärt Phillips. Mit der auf dem Form 3L aus Clear Resin gedruckten Schiene kann die Angelschnur schneller sicher verstaut werden, sodass die Ausrüstung des Teams seltener ersetzt werden muss.
Innovationen mit Glasfaser
So umständlich es auch ist, sie aufzuwickeln: Angelschnur ist kein besonders empfindliches Material. Glasfaserkabel hingegen erfordern einen anderen Umgang und verursachen im Beschädigungsfall weitaus höhere Kosten. In Kooperation mit dem in Pawtucket, Rhode Island, USA, ansässigen Unternehmen Nautilus Defense LL erfand Phillips' Labor eine innovative neue Glasfaser-Angelsehne (FOFL, kurz für fiber optic fishing line, US-Patent angemeldet). „Glasfaser hat uns Ethernet, Live-Videoübertragung und all solche Dinge verschafft. Das lässt sich mit Kupferkabeln über große Entfernungen nur sehr schwer umsetzen. Jetzt gibt es also etwas, das es vorher nicht gab – die Glasfaser-Angelsehne“, erläutert Phillips.
Aber für sich genommen war die Angelsehne aus Glasfaser noch nicht nutzbar – sie brauchte einen mechanischen Endpunkt, damit man an ihr ziehen konnte, ohne den Glasfaserkern zu zerbrechen. Da sich Glasfaserkabel im Gegensatz zu anderen, robusteren Leinen nicht knoten oder bearbeiten lassen, musste das Team eine Halterung für das Ende des Kabels entwerfen.
Mit einem 3D-gedruckten Teil mit engen Toleranzen, wie Formlabs' hochauflösende SLA-Drucker sie ermöglichen, können die lastentragenden äußeren Stränge der Angelsehne vom zerbrechlichen Glasfaserkern getrennt werden. Mithilfe eingespritzten Epoxidharzes wird die geflochtene Leine an der 3D-gedruckten Halterung befestigt und die Glasfaser wird in eine metallenes Verzweigungsrohr geführt, das an den Computer angeschlossen werden kann, um auf die über die Glasfaser übertragenen Informationen zuzugreifen.
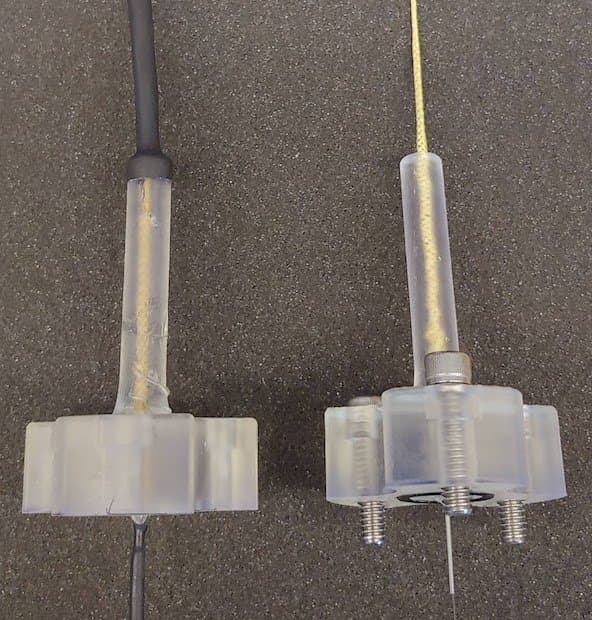
SLA-Druckteile werden als mechanische Endpunkte für die „Glasfaser-Angelsehne“ FOFL (US-Patent angemeldet) verwendet, die die lastentragende äußere Leine vom empfindlichen Glasfaserkern trennt. Bildrechte: Brennan Phillips
„Diese Art von Verbindung ist sehr stark, sie hält mindestens einhundert Pfund aus. Wir haben ein Patent angemeldet, haben das Design aber auch frei zugänglich gemacht“, so Phillips. „Ohne 3D-Druck, mit normalen Fertigungsprozessen, könnten diese Teile jedes Mal 3000 oder 4000 $ kosten, und wir haben mehrere Iterationen durchlaufen. Ich glaube, das hat niemand gemacht, weil der Weg bis zur Produktion so teuer war. Gerade die Kombination von Rapid Prototyping durch Methoden wie Formlabs-3D-Drucker und die neue Glasfaserleine macht neuartige Ideen wie diese greifbar“, meint Phillips.
3D-gedruckte Dichtungen zu reduzierten Kosten
Vor dem 3D-Druck war die Entwicklung dieser Hilfsmittel eine teure Angelegenheit, was Forschungsteams davor abschreckte, notwendige Designänderungen anzuwenden, und unterfinanzierten Programmen die Entwicklung gänzlich unmöglich machte. Das Labor für Unterwasser-Robotik und Bilderfassung ist Teil einer globalen Bewegung nach dem Leitsatz „deep and cheap“ – also Forschung in weiter Tiefe, aber zu niedrigen Kosten. Die Bewegung hat das Ziel, die Wissenschaft zu demokratisieren und Zugang zu Technologien zu verschaffen, sodass wir ein besseres Verständnis der uns umgebenden Ozeane erlangen. „Ich druckte Abschlusskappen, die bereits O-Ringe integriert hatten, und es funktionierte. Wenn man das über Zerspanung herstellt, kostet es Hunderte oder sogar Tausende Dollar, und die Zeichnungen müssen haargenau stimmen. Mit diesen Druckern kann ich drei oder vier Versionen ausdrucken und genau die richtige Passung erhalten, für gerade mal 50 $ Materialkosten“, so Phillips.
Das Laborteam beschränkt sich nicht nur auf den Druck von Teilen für die Endverwendung; mit Clear Resin hat es außerdem einen effizienten Arbeitsprozess zum 3D-Druck von Formen eingeführt. Das Endergebnis ist eine optimierte Lösung zum schnellen Spleißen von Unterwasserkabeln mit 3D-gedruckten Formen.
Vielfältige Anwendungsfälle
Im Labor von Phillips kommen Formlabs-3D-Drucker sowohl beim Prototyping zum Einsatz als auch zur Fertigung von Endprodukten, Rapid Tooling, Halterungen und Vorrichtungen und sogar Medizinprodukten. Selbst in einem so kleinen Forschungslabor dehnen der Innovationsgeist von Phillips und den Studierenden die Anwendungsbereiche und die Möglichkeiten der Technologie immer weiter aus.
Während der Covid-19-Pandemie erkannten Phillips und sein Studierendenteam, dass sie es in der Hand hatten, in Rhode Islands Reaktion auf die Pandemie wirklich etwas zu bewegen. Durch ausgiebige Tests und umfassende Forschungsarbeit gelang es dem Team, die Ergebnisse der chemischen Ausgasung von Formlabs' Surgical Guide Resin zur Nutzung in 3D-gedruckten Bauteilen für Beatmungsgeräte zu veröffentlichen. Damit erzielte das Team nicht nur eine wissenschaftliche Publikation, sondern meldete das Material auch zur Genehmigung einer Notfallzulassung (Emergency Use Authorization, EUA) durch die amerikanische Lebensmittel- und Arzneimittelbehörde FDA an.
„Während der Pandemie wurden riesige Anstrengungen unternommen, etwas zu schaffen, und da wollten wir dran teilhaben und dort helfen, wo wir die meiste Unterstützung bieten können. Aufgrund der Qualität der Drucker und dank Surgical Guide Resin konnten wir einen Beitrag auf höherer Ebene leisten“, berichtet Phillips.
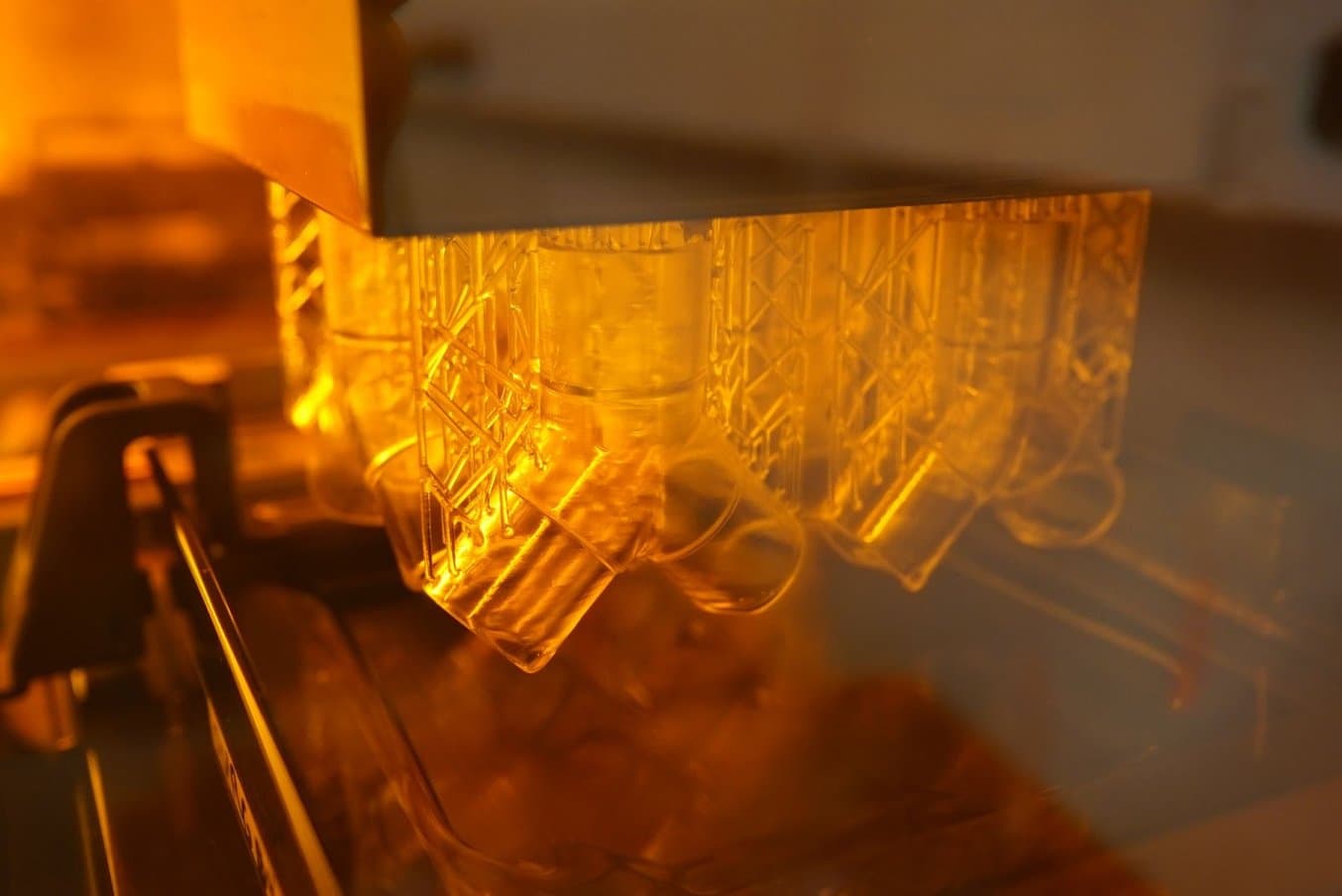
Y-Verteiler eines Beatmungsgeräts, die in einer Kooperation zwischen Forschenden an der Brown University und des Rhode Island Hospital entworfen wurden, werden in der Frühphase der Covid-19-Pandemie aus Surgical Guide Resin 3D-gedruckt. Bildrechte: Brennan Phillips
Die Demokratisierung der Tiefsee
Die niedrigen Fertigungskosten der Bauteile kommen nicht nur dem Budget des Labors zugute, sondern sorgen auch dafür, dass das Lernen (und die unvermeidlichen Fehlversuche beim Testen neuer Ideen) kein Grund ist, Studierenden den Zugang zu den Geräten zu verwehren. Studierende, die zum ersten Mal Teile entwerfen, können die Technologie selbst nutzen und das 3D-Drucken erlernen, ohne fürchten zu müssen, dass etwaige Fehler das Labor teure Ressourcen kosten.
Studierende im zweiten Studienjahr an der URI haben außerdem jedes Jahr die Möglichkeit, Druckgehäuse zu entwerfen und zu drucken, womit sie einerseits die Forschung unterstützen und zugleich wertvolle neue Fertigkeiten im 3D-Druck und CAD erwerben. „Vor diesen 3D-Druckern konnten Studenten erst im Aufbaustudium oder in der Berufswelt eigene Unterwasser-Gehäuse entwerfen und fertigen, denn das Budget und der Zugang zu Geräten waren sehr begrenzt. Diese Drucker öffnen jedoch viele Türen – es hat bei mir sogar schon ein Schüler ein Druckgehäuse gefertigt“, berichtet uns Phillips.
Nicht nur Studierenden in Amerika eröffnen die Drucker viele Möglichkeiten – Phillips gehört einer internationalen Gemeinschaft an, deren Ziel es ist, Hilfsmittel für die Tiefseeforschung in unterentwickelten Küstenstaaten auf der ganzen Welt erschwinglicher und zugänglicher zu machen. „Wir arbeiten daran, die Kapazitäten für Nationen zu erhöhen, die eigene Forschung in der Tiefsee betreiben möchten. Die Kosten sind ein Hindernis, die Ausbildung ebenso, aber diese Methoden haben das Potenzial, all das zu überwinden und die Erforschung der Ozeane zu demokratisieren“, meint Phillips.
1 https://oceanservice.noaa.gov/facts/exploration.html
2 Brennan T. Phillips, Josh Allder, Grady Bolan, R. Sean Nagle, Allison Redington, Tess Hellebrekers, John Borden, Nikolai Pawlenko, Stephen Licht,
Additive manufacturing aboard a moving vessel at sea using passively stabilized stereolithography (SLA) 3D printing, Additive Manufacturing, Volume 31, 2020, 100969, ISSN 2214-8604, https://doi.org/10.1016/j.addma.2019.100969.