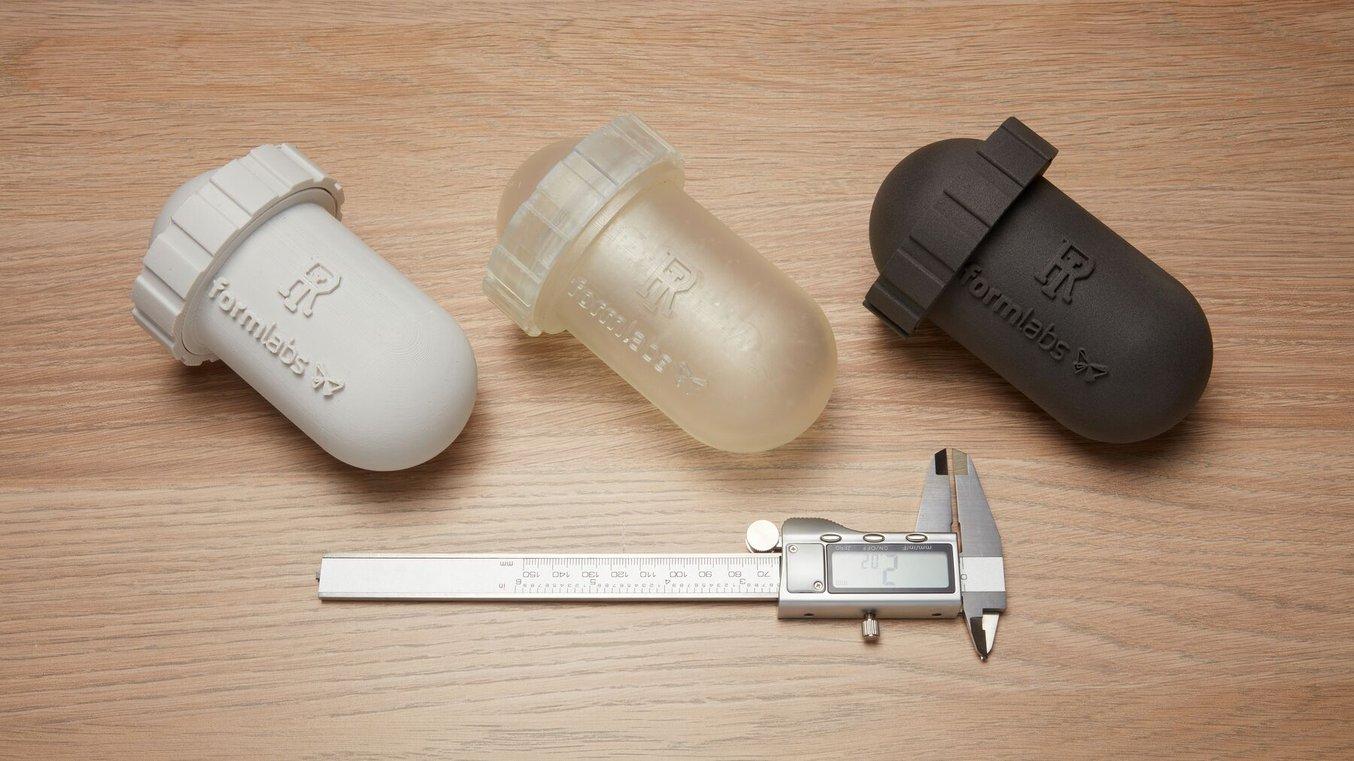
Hay una gran demanda de piezas personalizadas y pequeñas cantidades de piezas estancas al agua y al gas en diversos sectores, como el de la investigación marina, la robótica submarina, la ingeniería de tecnologías sostenibles, la industria del petróleo y el gas y la industria militar. Aunque algunas tecnologías de impresión 3D ofrecen una solución ideal para estas piezas, la percepción común de las piezas fabricadas de forma aditiva es que son porosas y no se pueden utilizar en entornos presurizados.
Gracias a una colaboración entre Formlabs y el Laboratorio de Robótica y Procesamiento de Imágenes Submarinas (URIL) de la Universidad de Rhode Island, se imprimieron conjuntos de varias piezas mediante modelado por deposición fundida (FDM), estereolitografía (SLA) y sinterizado selectivo por láser (SLS) y se sometieron a ensayo en una cámara de simulación de presión subacuática. Los resultados de ese ensayo, así como los diagramas, las recomendaciones sobre juntas tóricas y las directrices de diseño, están disponibles en el libro blanco.
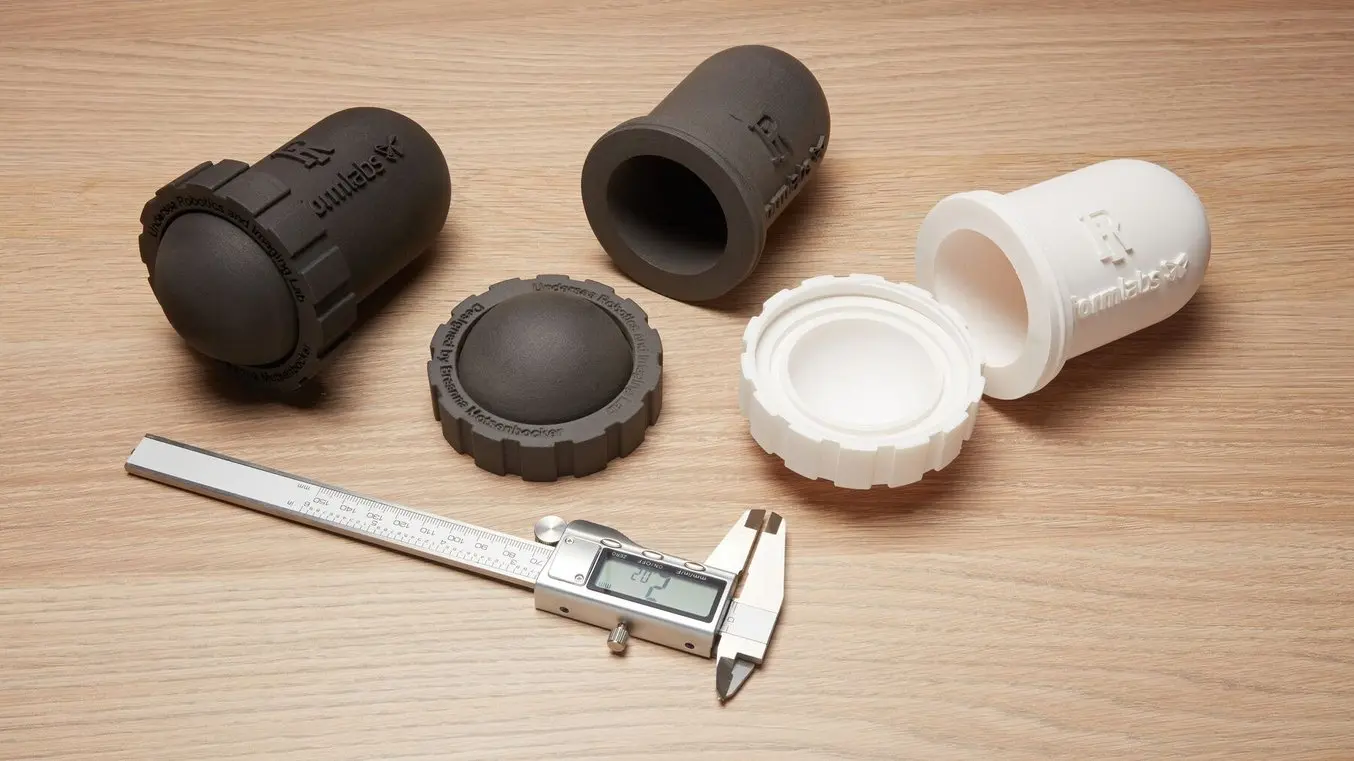
Impresión 3D de carcasas estancas y resultados de los ensayos de presión
En este libro blanco, ofreceremos los resultados de los ensayos y recomendaciones claras para imprimir en 3D de forma económica carcasas estancas personalizadas.
Diseño y fabricación de piezas estancas personalizadas
La estanqueidad es la capacidad que tiene un objeto de evitar que el agua entre o salga de una carcasa y está muy relacionada con la construcción de dicha carcasa o conjunto, en vez de basarse en la naturaleza fundamental del material de sus componentes. Sin embargo, si se tiene en cuenta la presión a la que se verán sometidas estas piezas al descender bajo la superficie, las propiedades inherentes de los materiales cobran mayor importancia. El experimento de la URIL aborda el diseño, el método de sellado y las propiedades de los materiales.
Aplicaciones para piezas estancas
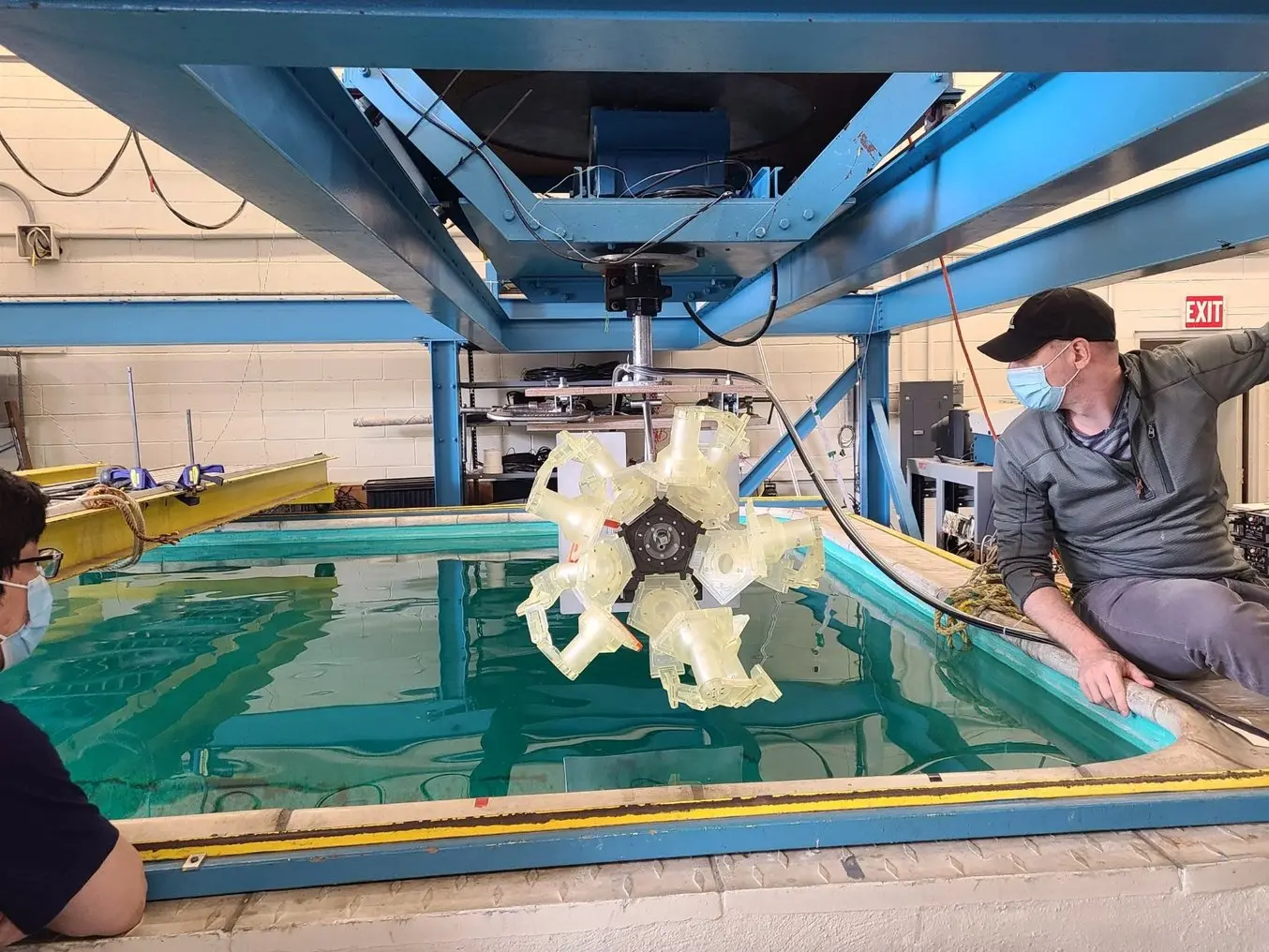
La impresión 3D permite probar formas nuevas y complicadas para equipamiento de ensayo y recolección de muestras, como esta herramienta con componentes impresos con la Clear Resin.
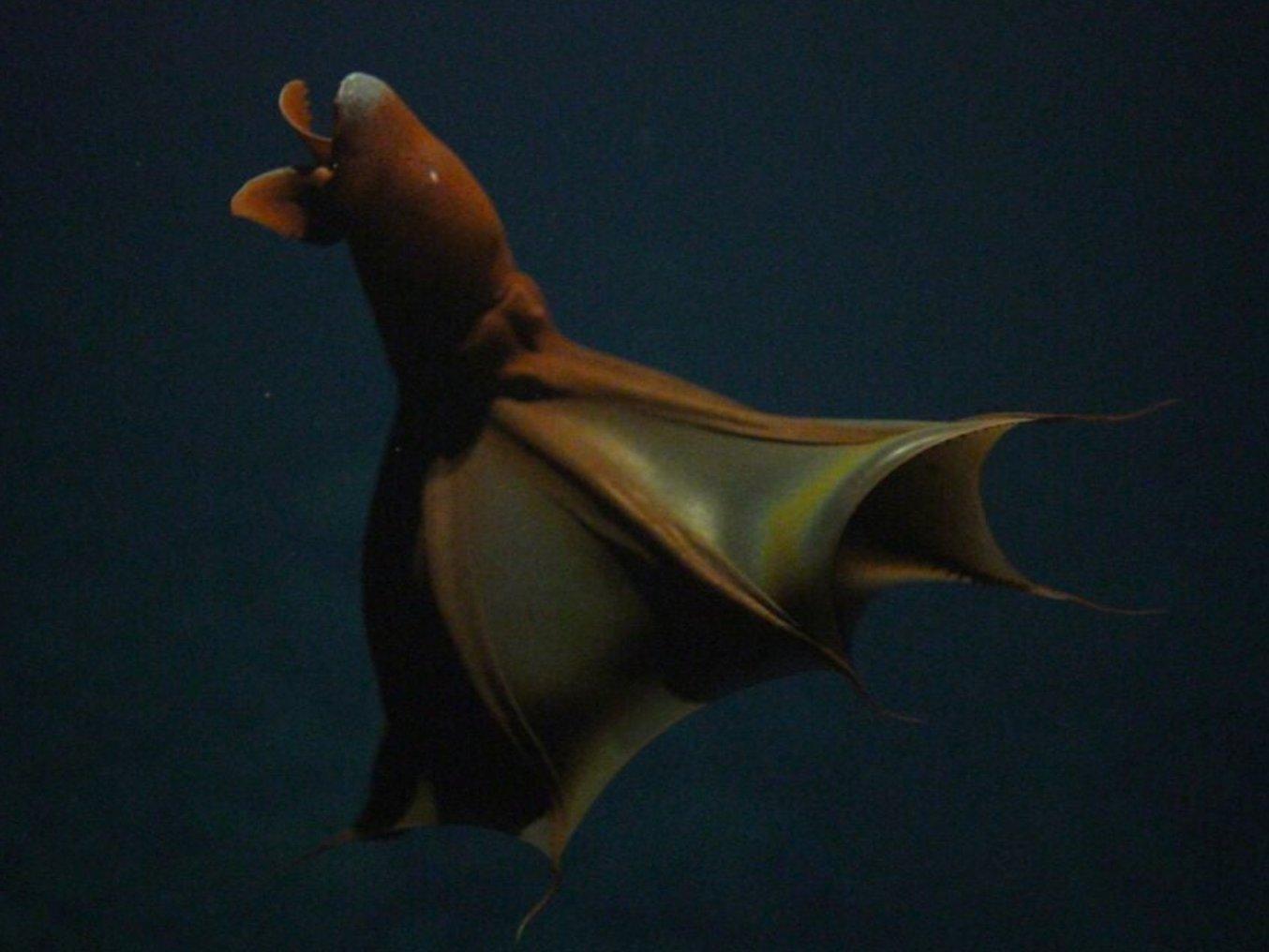
Las carcasas estancas permiten tomar imágenes de las profundidades marinas, como esta foto de un vampyroteuthis, incluso sin un costoso equipamiento de cámara submarina.
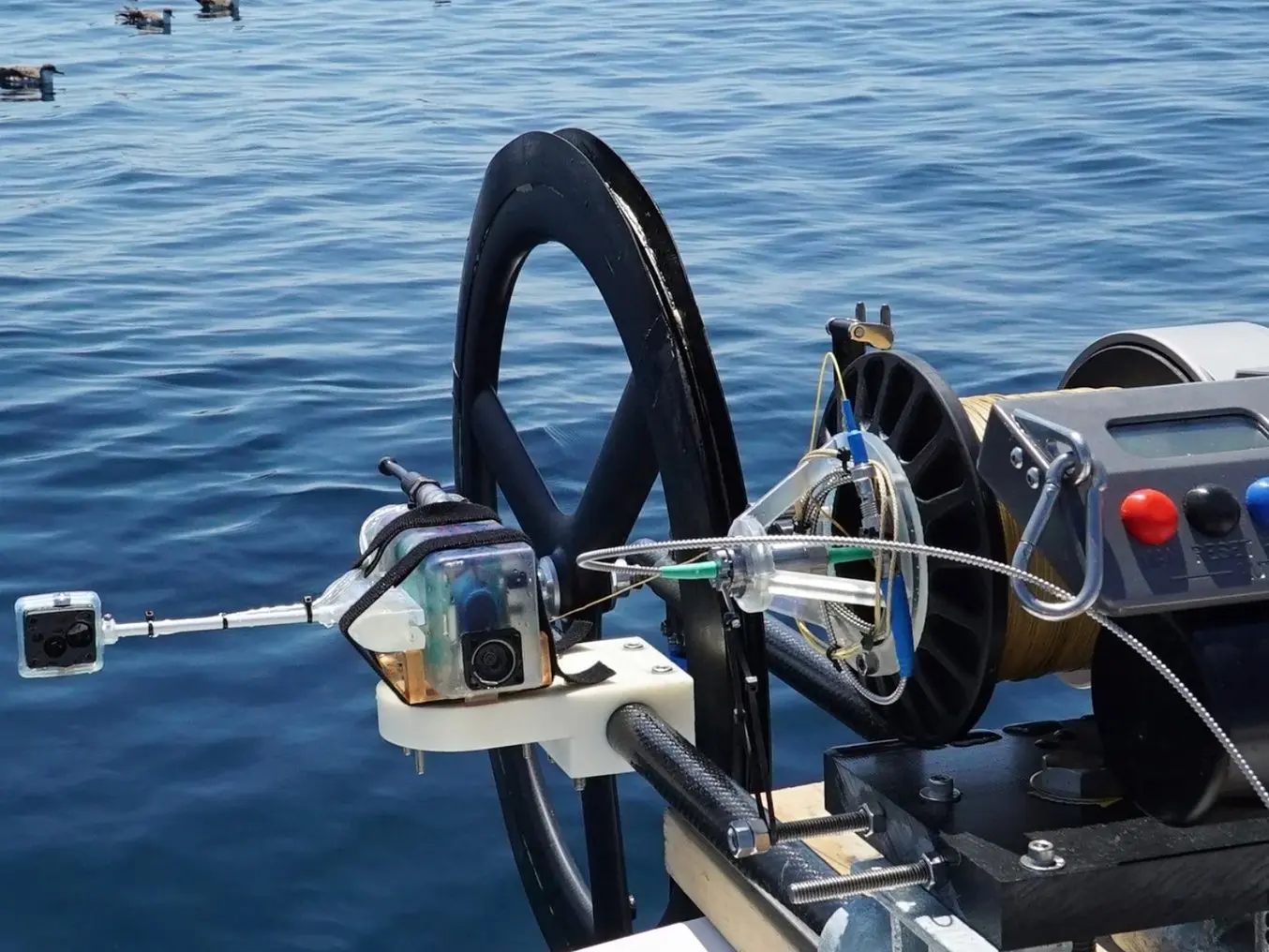
El carácter ágil de la impresión 3D bajo demanda hace que sea posible usar sujeciones con guía y fijaciones hechas a medida para la investigación en el mar, de forma rentable.
Las impresiones estancas se emplean en situaciones tan diversos como los motores fuera borda para navegación y ocio, la exploración robótica en aguas profundas, la fotografía submarina, etc. Cuando las piezas son estancas, también pueden contener otros líquidos. Por tanto, son extremadamente útiles para aplicaciones en las que hay tubos que transportan líquidos entre componentes, como la automoción, la investigación química, los servicios públicos de gas, agua y electricidad, la construcción, etc.
Para aplicaciones de investigación en los campos de la ecología, la geología o la climatología, crear equipamiento personalizado para el estudio y el muestreo a menudo resulta excesivamente caro, Dado que cada aplicación es única y que los entornos en los que se utilizan están en constante cambio y son difíciles de gestionar desde la superficie, los componentes subacuáticos o que transportan fluidos con frecuencia deben tener algún grado de personalización.
Impresión 3D de piezas estancas en la NOAA
Para combatir la pérdida de arrecifes de coral, los científicos e investigadores del Laboratorio Oceanográfico y Meteorológico del Atlántico (AOML) de la NOAA y sus instituciones asociadas están utilizando métodos innovadores para estudiar los corales en la naturaleza, reproducir ciertas condiciones en entornos controlados de laboratorios y después cultivar nuevas especies de coral que puedan resistir mejor las condiciones extremas de los entornos actuales.
El AOML ha recurrido a la impresión 3D para facilitar sus investigaciones de campo y de laboratorio. El uso de impresoras de Formlabs ha ayudado a estandarizar y mejorar la precisión y la comparabilidad de sus experimentos, y ha facilitado el desarrollo de nuevas tecnologías. La gama de materiales disponibles para las impresoras de Formlabs facilita el diseño, la iteración y el uso de las piezas estancas impresas en 3D.
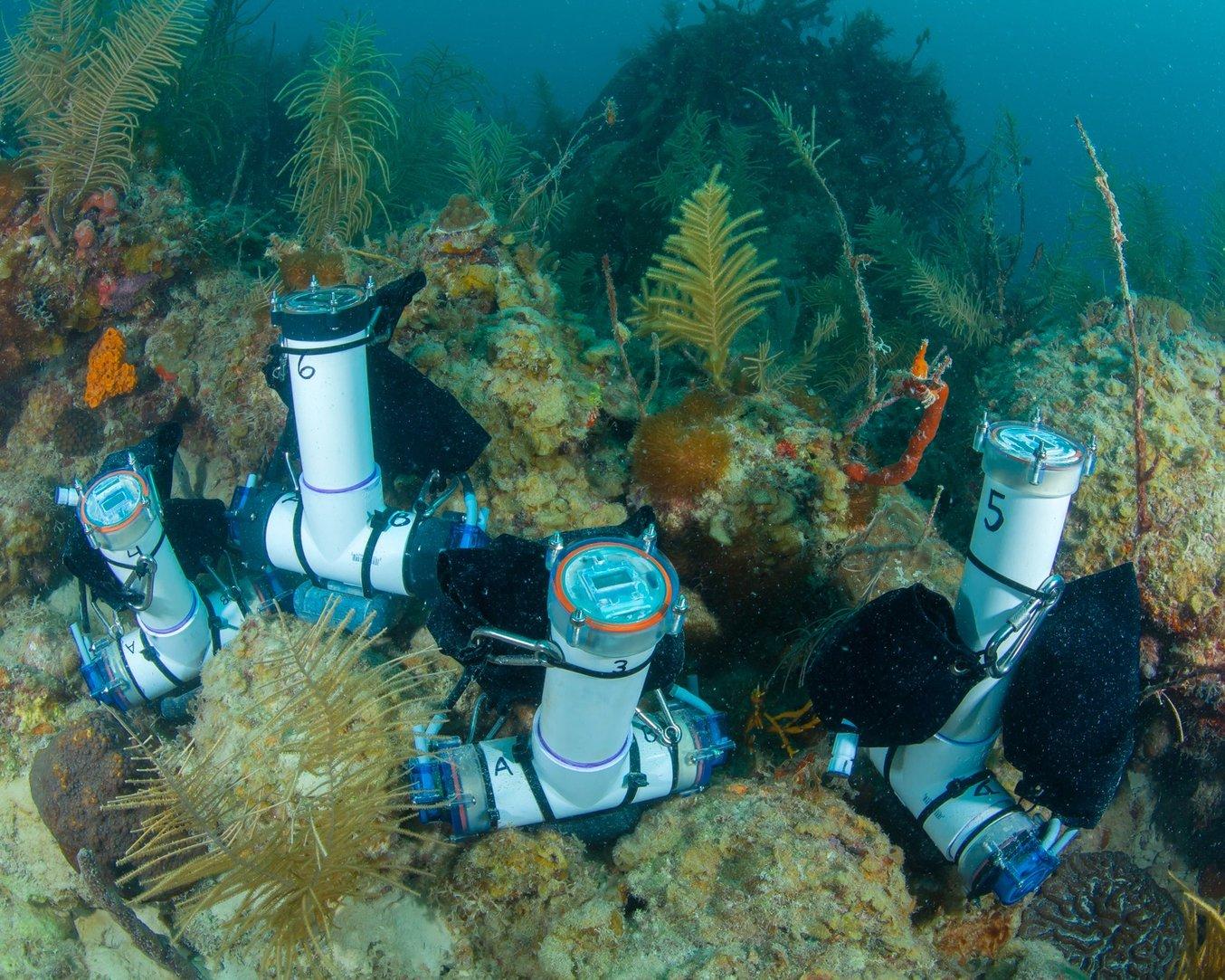
La investigación del AOML requiere equipamiento sofisticado y a menudo personalizado para vigilar los hábitats de los corales salvajes. (Imágenes cortesía de la NOAA)
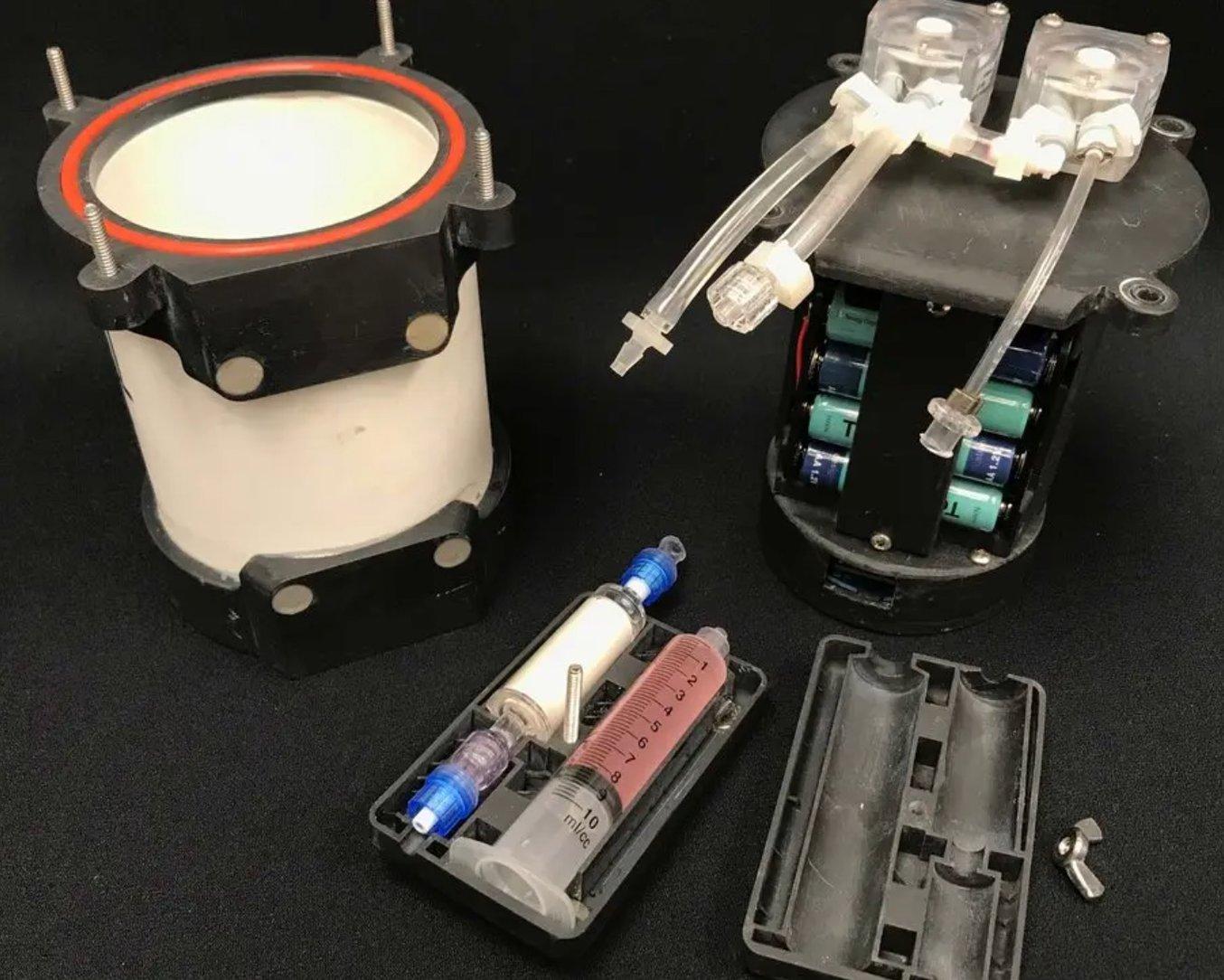
El laboratorio del AOML diseñó y fabricó este muestreador automatizado de profundidad para ADN ambiental utilizando impresoras de Formlabs SLA para los topes, el cartucho de muestras y el armazón interno.
Valiéndose de cuatro impresoras de resina de Formlabs, así como de la impresora de sinterizado selectivo por láser (SLS) Fuse 1, Nate Formel y sus compañeros del AOML imprimen carcasas de muestreadores de alta resistencia, sujeciones con guía para sensores y equipamientos experimentales y componentes personalizados para sus acuarios internos. Son estructuras construidas para estudiar la salud de los corales y los métodos para mejorar la resistencia de los corales frente al aumento de la temperatura del agua y las condiciones extremas de un clima cambiante.
"Ahora tenemos estos componentes impresos en 3D muy personalizados que tienen los puntos de conexión y los agujeros pasantes necesarios para permitirnos recolectar muestras de agua. En cuanto al diseño original del muestreador que motivó todo esto, dejamos de fabricarlo con un coste de 1000 $ y empezamos a hacerlo por solo 220 $. Eso significa que ahora puedo sacar cinco muestreadores por el precio que antes me costaba hacer uno", dice Formel.
Los métodos actuales de fabricación para piezas estancas
Los métodos actuales para fabricar estos componentes estancos suelen usar materiales conocidos de fabricación tradicional, como metal, plásticos moldeados por inyección o goma. Los componentes producidos en masa son asequibles, pero configurarlos después de forma que satisfagan las necesidades específicas del uso que se les quiere dar puede ser difícil y requiere conectores, fijaciones o carcasas hechos a medida. En los conjuntos de piezas con múltiples encajes, estas piezas se sellan entre sí mediante una combinación de elementos con roscas, elementos con enclavamientos o de acoplamiento y juntas de diversos tipos, como juntas tóricas.
Elegir juntas tóricas puede ser extremadamente difícil y configurar los parámetros adecuados para tu carcasa puede llevar mucho tiempo. El manual de juntas tóricas de Parker tiene miles de recomendaciones en función de la compresión, el diámetro, el grosor, el material, la presurización, etc. El proceso de elegir una junta tórica de tamaño personalizado es tan difícil que muchos recurren a la estandarización y a los componentes producidos en masa, lo que limita la capacidad de innovar y de encontrar nuevas aplicaciones.
Impresión 3D estanca: Cómo elegir la tecnología de impresión 3D adecuada
Anteriormente, el trabajo subacuático se limitaba a proyectos con gran financiación que pudieran construir costosas máquinas y componentes hechos a medida. Es una situación que la impresión 3D ha podido cambiar, permitiendo fabricar productos personalizados para la investigación y el desarrollo por un coste inferior al de los métodos tradicionales. Si se quiere usar una solución impresa en 3D bajo el agua, hay que considerar detenidamente cuál es la tecnología de impresión 3D y el material que mejor se ajustan a la situación.
Tanto la tecnología SLA como el SLS se utilizan en ámbitos de ingeniería e investigación, pero destacan en situaciones diferentes. La tecnología SLS es excelente para producir piezas de uso final en volúmenes bajos, tiene un catálogo de materiales conocidos como el nylon y el TPU y crea piezas resistentes de calidad industrial. Las impresoras SLA destacan en situaciones que requieren un acabado de la superficie liso y propiedades de los materiales muy específicas. En este ensayo, tanto el acabado de la superficie liso de las piezas de SLA como su densidad fueron beneficiosas para su rendimiento en un entorno presurizado. Las impresoras de modelado por deposición fundida (FDM) se utilizan a menudo para el prototipado rápido, pero no crean piezas estancas y, por lo tanto, no se utilizan en aplicaciones estancas.
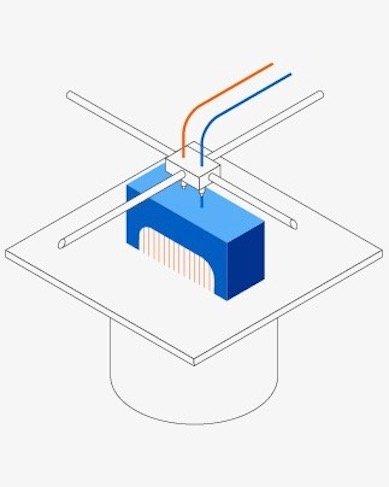
Tecnología de impresión 3D de modelado por deposición fundida (FDM).
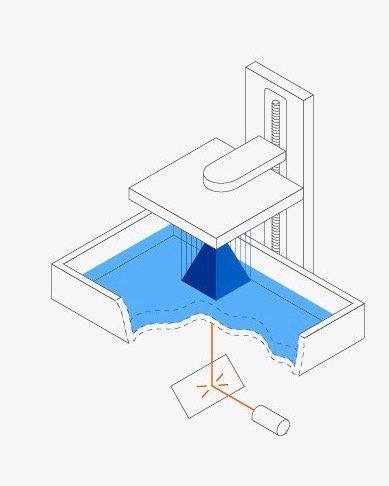
Tecnología de impresión 3D por estereolitografía (SLA).
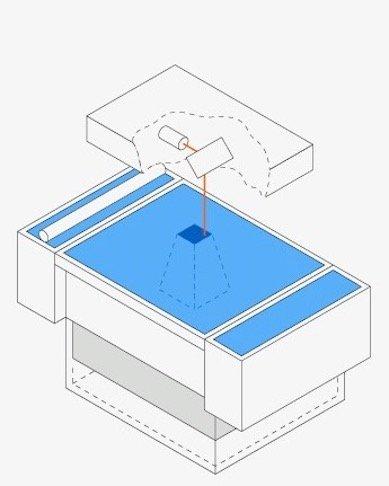
Tecnología de impresión 3D por sinterizado selectivo por láser (SLS).
Modelado por deposición fundida (FDM)
La forma de tecnología de impresión 3D más conocida, el modelado por deposición fundida (FDM), no crea piezas estancas. De esta incapacidad surgió la idea errónea generalizada de que las piezas impresas en 3D en general no pueden utilizarse en situaciones que requieran componentes estancos. La tecnología FDM extruye plástico fundido a través de una boquilla, depositándolo capa a capa, pero sin unir dichas capas de forma química.
Las piezas impresas mediante FDM son anisotrópicas, lo que quiere decir que poseen propiedades mecánicas distintas en función de la dirección en la que actúa sobre ellas el esfuerzo mecánico y son menos densas que un objeto similar producido mediante otros métodos. Como las capas no están unidas químicamente entre sí, los líquidos se pueden filtrar hasta la superficie de la pieza a través de los espacios microscópicos que hay entre las capas. Por consiguiente, las carcasas impresas en impresoras FDM no son estancas, a menos que las piezas estén muy posacabadas y se hayan sellado mediante algún paso adicional, como el alisado con vapor o un revestimiento. Estas piezas implosionarán bajo presión y se agrietarán a lo largo de las líneas de capa.
Si los usuarios necesitan crear piezas estancas con las impresoras 3D FDM, diseñar la pieza sin huecos, puertos u otras aberturas; "sobreextruir" y utilizar capas más gruesas son algunas de las técnicas que puedes utilizar para intentar mejorar la estanqueidad, junto con el posacabado adicional necesario (alisado, lijado, revestimiento). Elegir un filamento como el PETG o el polipropileno es otra buena forma de intentar mejorar la estanqueidad, aunque estos métodos no servirán para piezas que se usan en entornos presurizados.
Estereolitografía (SLA)
En cambio, las piezas impresas en 3D mediante estereolitografía (SLA) son estancas, porque cada capa está unida químicamente a las capas contiguas. Las piezas impresas mediante SLA se forman en un proceso en el que un láser cura resina líquida capa a capa, estableciendo enlaces entrecruzados entre las cadenas poliméricas de cada capa y entre ellas y las capas contiguas. Este proceso crea superficies con un acabado liso prácticamente sin líneas de capa y que no son porosas, por lo que el agua no las puede penetrar. Las piezas tienen tolerancias muy buenas, por lo que los ensamblajes de múltiples piezas, como las carcasas que se usan en los ensayos de este libro blanco, se pueden unir mediante conexiones roscadas sin que quede apenas huecos que dejen pasar el aire entre ellos. Cuando se combinan con un sello o una junta, las carcasas son totalmente estancas y pueden soportar una presión inmensa.
Sinterizado selectivo por láser (SLS)
La tecnología de sinterizado selectivo por láser (SLS) crea piezas sinterizando una sección transversal de la pieza encima de un lecho de polvo, cubriéndola con polvo nuevo y volviendo a empezar. Las piezas impresas son un tanto isotrópicas, pero pueden presentar diferencias en sus propiedades mecánicas en función de la dirección desde la que se aplica la fuerza. Las impresiones SLS son estancas cuando se diseñan con las tolerancias y las técnicas de sellado apropiadas.
Consejos de diseño para imprimir en 3D piezas estancas
Como se ha dicho anteriormente, la estanqueidad de una carcasa depende tanto de las cualidades impermeables de los propios componentes como del diseño de la carcasa, es decir, de cómo encajan esos componentes entre sí. Las tecnologías de impresión 3D SLA y SLS pueden crear componentes con tolerancias tan ajustadas que las carcasas con elementos de enclavamiento o las que tienen roscas para tornillos pueden ser completamente estancas sin pasos adicionales. Sin embargo, en entornos extremadamente presurizados, como en los que se prueban en este experimento, medidas adicionales como el uso de juntas tóricas pueden aumentar la eficacia de las carcasas.
Diseño de la carcasa
El Laboratorio de Robótica y Procesamiento de Imágenes Submarinas de la Universidad de Rhode Island (URIL) se ha propuesto democratizar la investigación de las profundidades marinas. Impresoras 3D con precios accesibles como la Form 3+ y su versión de gran formato, la Form 3L, han hecho posible diseñar y fabricar herramientas sofisticadas de exploración submarina y compartir esos diseños con la comunidad científica.
El URIL ha publicado varios artículos sobre sus investigaciones submarinas, entre los que se cuentan una guía para el novedoso diseño de DEEPi (un sistema de procesamiento de imágenes y control para las profundidades marinas), una investigación sobre el uso de la estabilización pasiva para ayudar en la impresión SLA en un barco en movimiento en el mar y una consulta sobre el uso de la biomimética en el diseño de carcasas, basándose en formas nautiloides.
El investigador principal Brennan Philips y la candidata a doctorado Breanna Motsenbocker llevan años realizando iteraciones de las carcasas de su cámara y sus robots submarinos, y han publicado varios artículos que detallan sus conclusiones. El laboratorio ha publicado su diseño de código abierto con la intención de hacer que el proceso de fabricación sea accesible para comunidades que anteriormente carecían de la financiación para llevar a cabo una recopilación de datos o investigaciones bajo el agua.
El Laboratorio de Robótica y Procesamiento de Imágenes Submarinas ha hecho que ambos diseños (uno para los ensayos, con paredes delgadas, y otro con paredes más gruesas, no sometido a ensayo) sean de código abierto y estén disponibles públicamente para reproducirlos. Para acceder a estos diseños, descarga el libro blanco completo.
Diseños de biomimética
En colaboración con otros investigadores, Philips y Motsenbocker también han estudiado cómo los diseños biomiméticos pueden mejorar la funcionalidad de sus carcasas estancas. En un artículo publicado en octubre de 2023, los investigadores estudiaron cómo la concha de los nautilos perlados (un miembro de la familia de los moluscos) impide que el agua entre en su interior, incluso a profundidades extremas. Los resultados podrían arrojar luz sobre cómo las complejas morfologías de esas conchas pueden revelar geometrías resistentes a la presión que sean comparables a las "ideales" utilizadas actualmente en la robótica marina de aguas profundas: esferas y cilindros simples, que tienen una relación superficie/volumen mínima y una fabricabilidad más fácil. Para leer los resultados completos de su investigación, visita el artículo publicado en la revista.
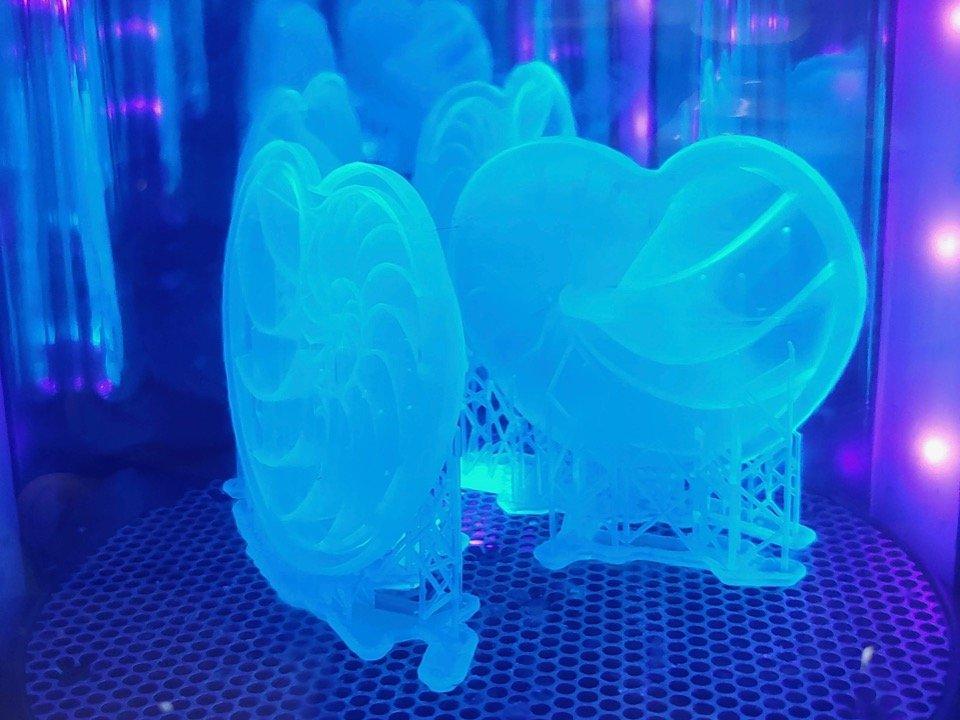
Estos componentes impresos en 3D siguen el modelo del nautilo perlado, un miembro de la familia de los moluscos que puede soportar una enorme presión bajo el agua sin que su concha sufra daños.
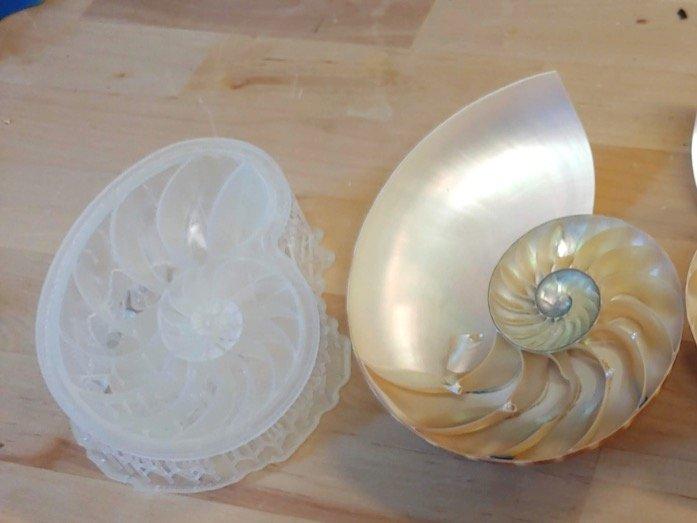
Escanear moluscos (derecha) y utilizar el diseño digital para recrear su geometría para la impresión 3D (izquierda, con la Clear Resin) puede ayudar a los investigadores a comprender cómo han evolucionado estos animales para prosperar en su inhóspito entorno.
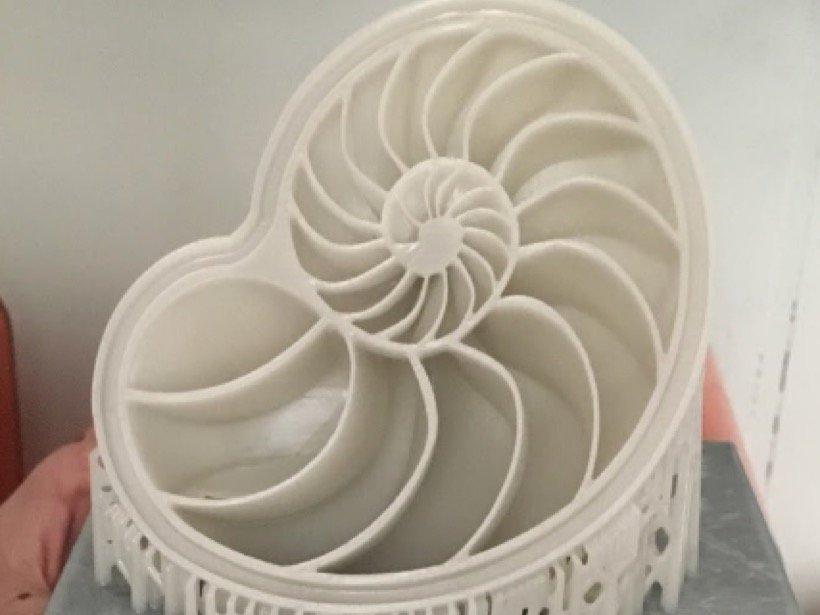
Esta pieza de gran tamaño, impresa con la White Resin, se podría utilizar para proteger cámaras de tamaño reducido para la investigación en aguas profundas.
Cómo elegir una junta tórica para una carcasa estanca impresa en 3D
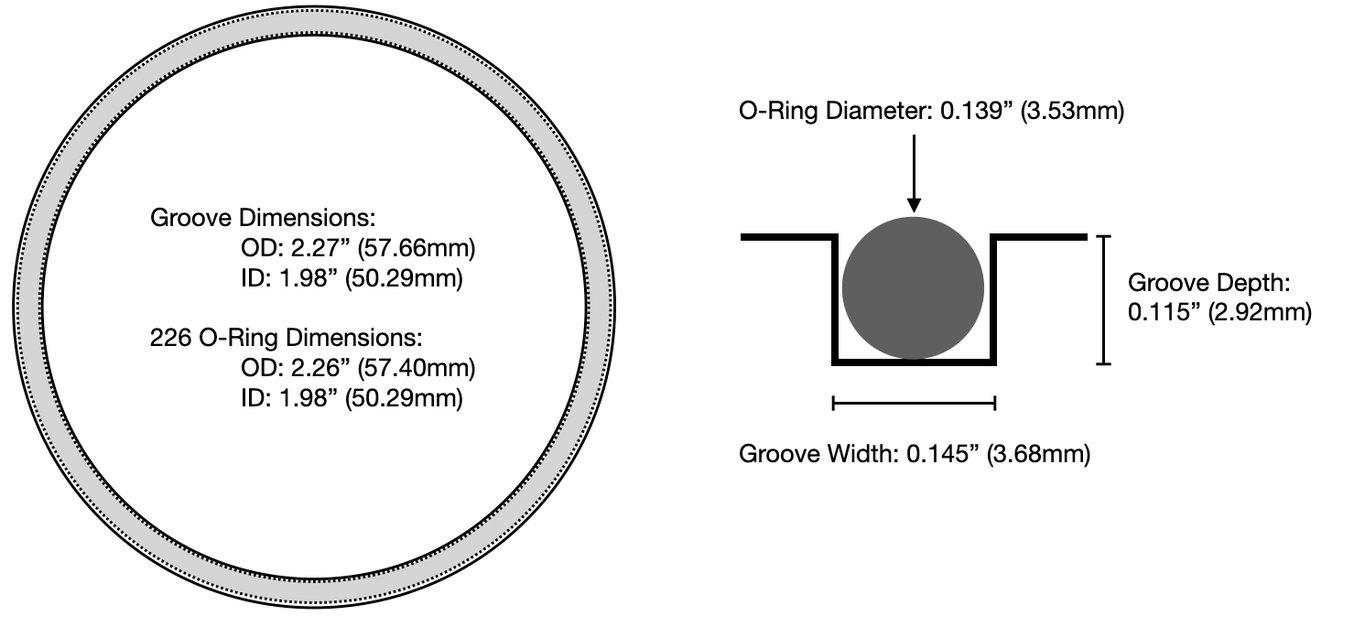
El Laboratorio de Robótica y Procesamiento de Imágenes Submarinas experimentó con éxito tanto con las juntas tóricas superficiales como con las internas, pero prefiere las juntas tóricas superficiales.
Cuando se hayan elegido los diámetros interno y externo para la carcasa, se puede seleccionar una junta tórica superficial basada en el diámetro interno. La junta tórica debería ajustarse apropiadamente entre el tope y el cuerpo. Las juntas tóricas de 35 mm crean el sellado más fiable para las piezas impresas mediante SLA. Para conocer las recomendaciones y conclusiones específicas del URIL, descarga el libro blanco completo.
Impresión 3D estanca: Ensayos y resultados
Para crear las carcasas se usaron las tecnologías de impresión 3D FDM, SLA y SLS. El Nylon 12 GF Powder se imprimió en la impresora SLS Fuse 1+ 30W, mientras que los demás materiales (la Grey Resin, la Clear Resin, la BioMed Amber Resin y la Rigid 10K Resin) se imprimieron en la impresora SLA Form 3+. Las piezas impresas en una máquina Craftbot con filamento de ácido poliláctico (PLA) absorbían agua en el mismo momento en el que sumergían, de modo que se eliminaron de los ensayos.
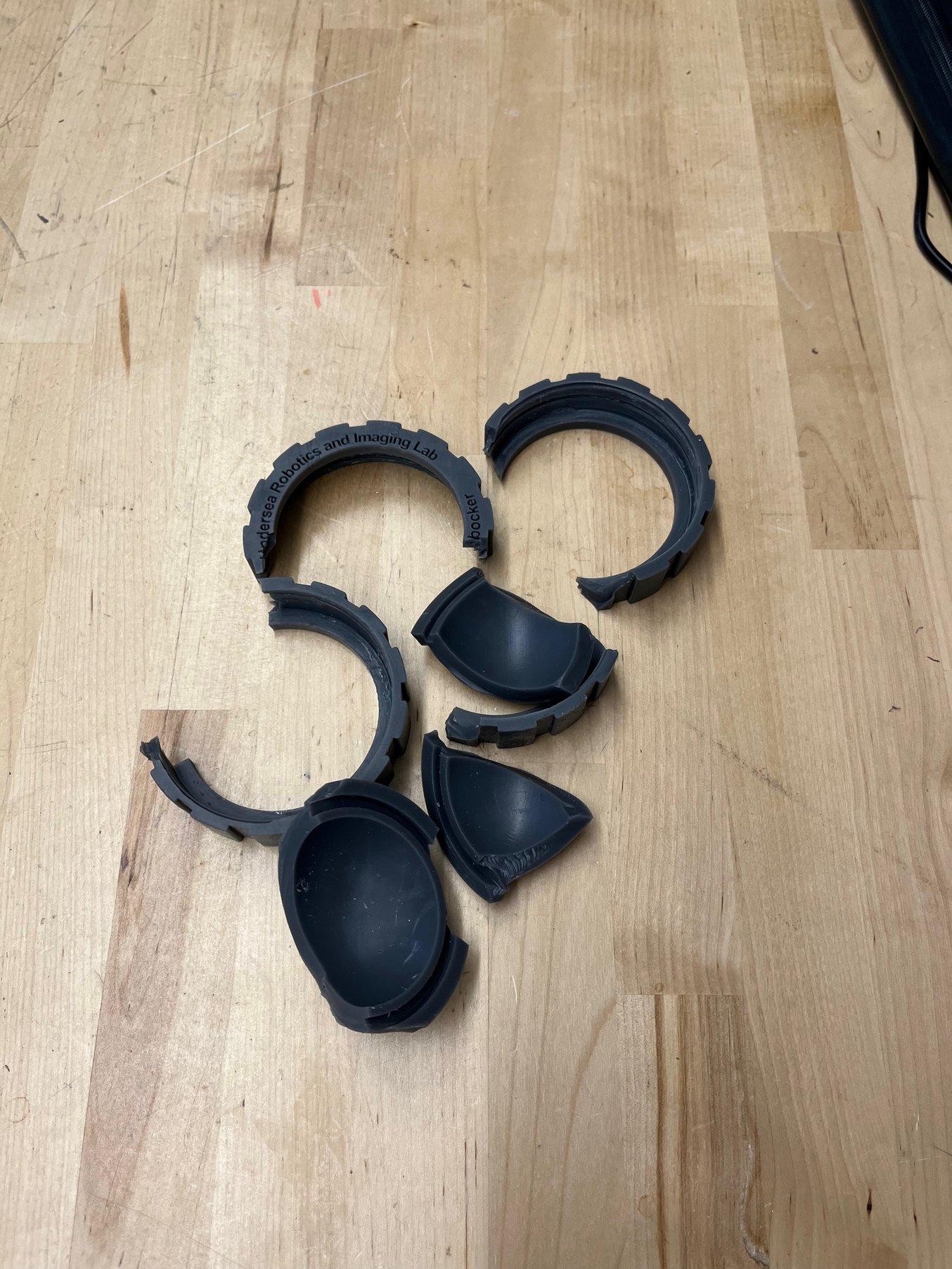
El Nylon 12 GF Powder implosionó a la presión más baja, una media de 1304 psi o 90 bar.
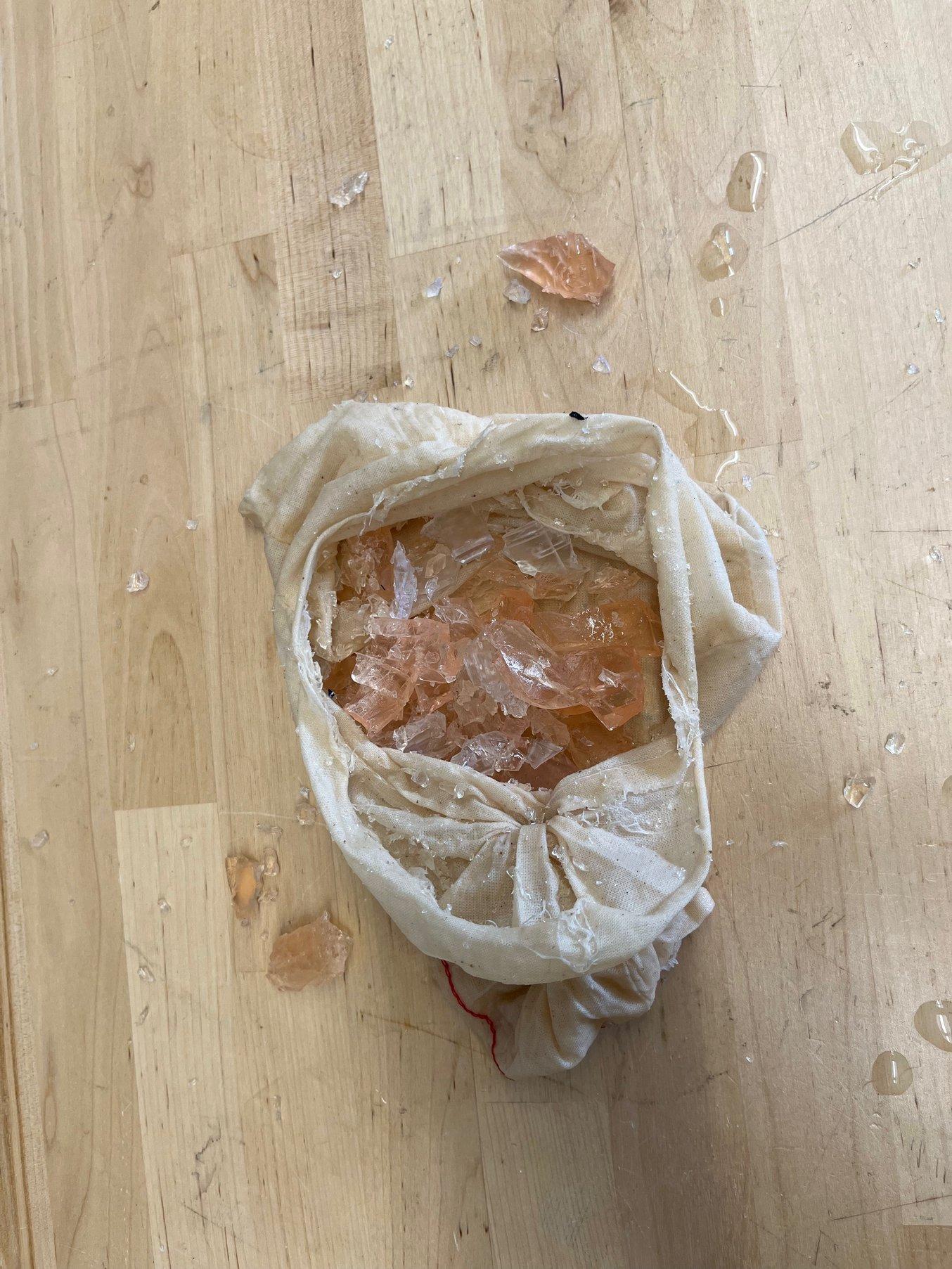
La BioMed Amber Resin resistió una presión mucho mayor, implosionando a una media de 2907 psi o 200 bar.
Los resultados demostraron que la impresión 3D SLA y SLS son métodos eficaces para crear carcasas estancas cuando se combinan con juntas tóricas, con la impresión 3D SLA como clara ganadora, ya que algunas de las piezas que produjo sobrevivieron a una presión extrema equivalente a profundidades de 4000 m bajo el nivel del mar. Las piezas impresas mediante FDM resultaron inadecuadas para esta aplicación, ya que entraba agua en ellas inmediatamente después de sumergirlas y no podían soportar ningún tipo de presurización.
Los materiales para SLA más rígidos tuvieron el mejor rendimiento bajo presión y los métodos de posacabado como el granallado pueden mejorar todavía más su comportamiento reduciendo la porosidad de la superficie. Para acceder a los resultados completos y ver el rendimiento de cada material, descarga nuestro libro blanco.
Para saber más acerca de la robótica submarina y de cómo aprovechar las impresoras 3D y los materiales para fabricar carcasas completamente estancas y resistentes a la presión, contacta con nuestro equipo, que puede ponerte en contacto con expertos de la red de Formlabs que trabajan actualmente en estas aplicaciones.