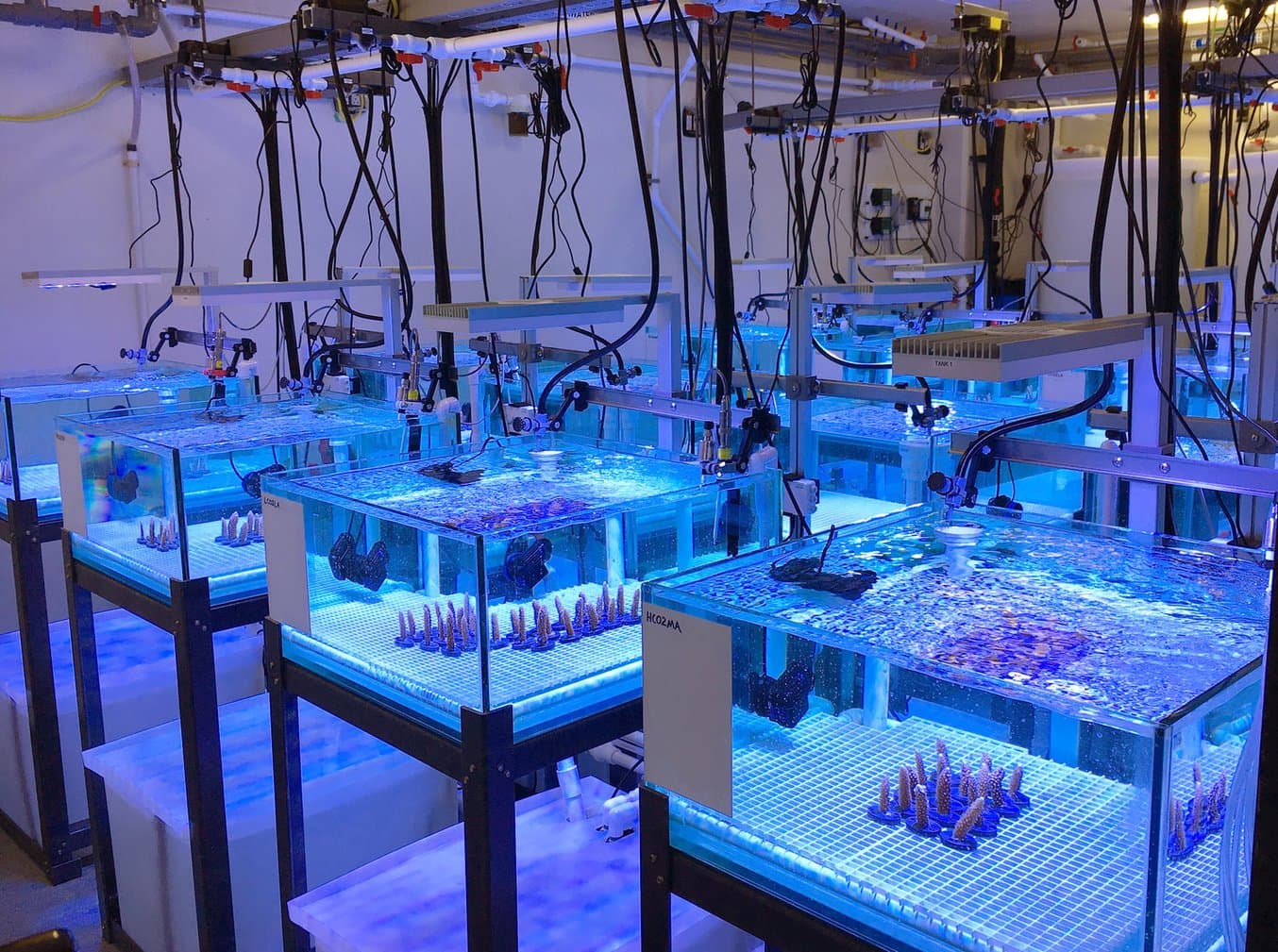
The Experimental Reef Lab at NOAA's Atlantic Oceanographic and Meteorological Laboratory (AOML) (image courtesy of NOAA)
More evidence of climate change comes across news channels faster every day—photos of melting polar landscapes, lush tropics reduced to charred wastelands, and desiccated coral reefs. To fight the effects of climate change, researchers across the world are employing novel and innovative techniques. A team of researchers at the National Oceanic and Atmospheric Administration (NOAA) relies on 3D printing to help them achieve repeatable, customized parts for coral reef research and monitoring.
Utilizing two Form 2 and two Form 3 stereolithography (SLA) printers as well as the Fuse 1 selective laser sintering (SLS) printer, Nate Formel and his colleagues at NOAA’s Atlantic Oceanographic and Meteorological Laboratory (AOML) print heavy-duty sampler housings, jigs for experimental sensors and equipment, and customized components for their in-house aquaria—structures built to study coral fitness and methods to enhance coral resilience in the face of rising water temperatures and extreme conditions of a changing climate.
An Integral Part of the Global Ecosystem
Corals are colonial organisms, typically made up of thousands or hundreds of thousands of individual polyps, each with a complex consortium of microorganisms that contribute to their health and nutrition. Reef-building corals secrete calcium carbonate, a hard rock-like material that comprises structures we commonly call reef framework or habitat. This habitat and the entire reef ecosystem it supports is extremely valuable, hosting the single highest concentration of biodiversity in the marine realm; often termed the “rainforests of the sea.” From an anthropocentric perspective, they provide billions of dollars of value to the US economy, supporting fisheries, tourism, and protecting shorelines from wave energy and storms.
Coral are vital to the health of the global ecosystem and the global economy, but their own health is failing rapidly. A study published in One Earth found that since 1950, over half the global population of coral has been wiped out. Anthropogenic, or human-caused, factors like water pollution, habitat destruction, and global warming from the use of fossil fuels, industrial farming, and deforestation, are the primary cause of the massive loss in coral population.
To fight coral reef loss, scientists and researchers at NOAA and their partner institutions are utilizing innovative methods to survey coral in the wild, reproduce certain conditions under controlled settings in labs, and then cultivate new species of coral that can better withstand the extreme environments of today. The AOML Coral Program where Formel works, in partnership with the University of Miami's Cooperative Institute for Marine and Atmospheric Studies (CIMAS) has turned to 3D printing to facilitate their field and lab research. Using Formlabs printers has helped standardize, as well as improve the accuracy and comparability of, their experiments, and facilitated the development of new technologies.
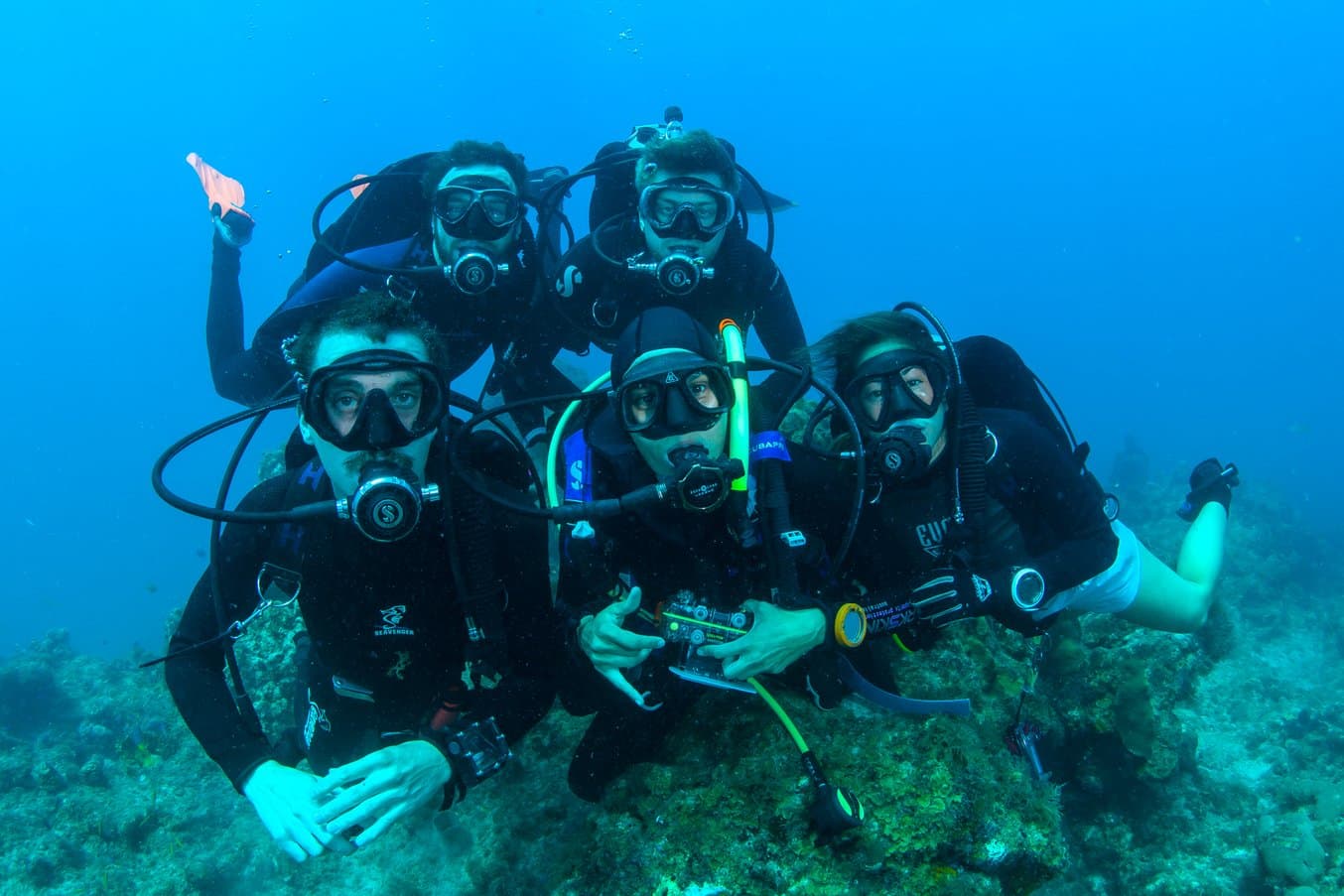
Members of the NOAA’s Atlantic Oceanographic and Meteorological Laboratory (AOML) on duty. (image courtesy of NOAA)
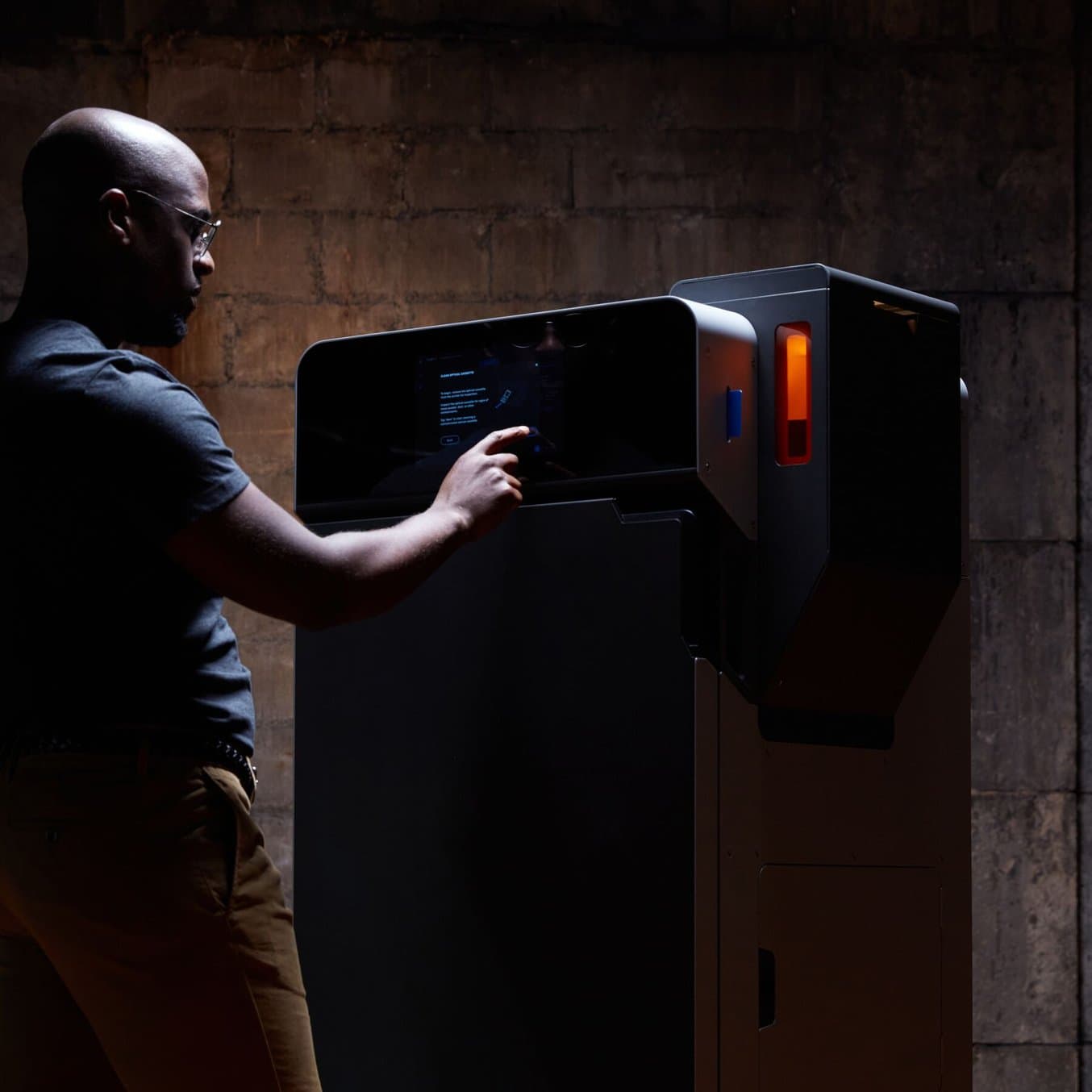
Outsourcing vs. In-House: When Does it Make Sense to Bring SLS 3D Printing In-House?
In this white paper, we evaluate the value proposition of bringing SLS 3D printers in-house, in comparison with outsourcing SLS parts from a service bureau.
Field Research: Controlled Conditions on the High Seas
To identify characteristics of coral that will thrive in a new, more extreme marine environment, Formel and his colleagues look for coral that are currently thriving under conditions expected in a more acidified ocean, like those near volcanic vents. The team created a subsurface automated sampler (SAS) to collect water samples on coral reefs to help understand the intensity and variability of the conditions in which these coral are living. They made the design of these samplers open source so other groups across the world could use this tool. Utilizing 3D printing helped keep the cost of the sampler low, to allow the construction and deployment of many samplers without large funding budgets. The automation allows for synchronized sampling to give researchers an idea of exactly what’s happening in the water at different times or at multiple locations.
“The automation of sampling was an appealing idea to improve our science and improve the ease of carrying out that science,” says Formel. “You can have a synchronized sampling time that shows exactly what’s happening in the water chemistry at different sites.”
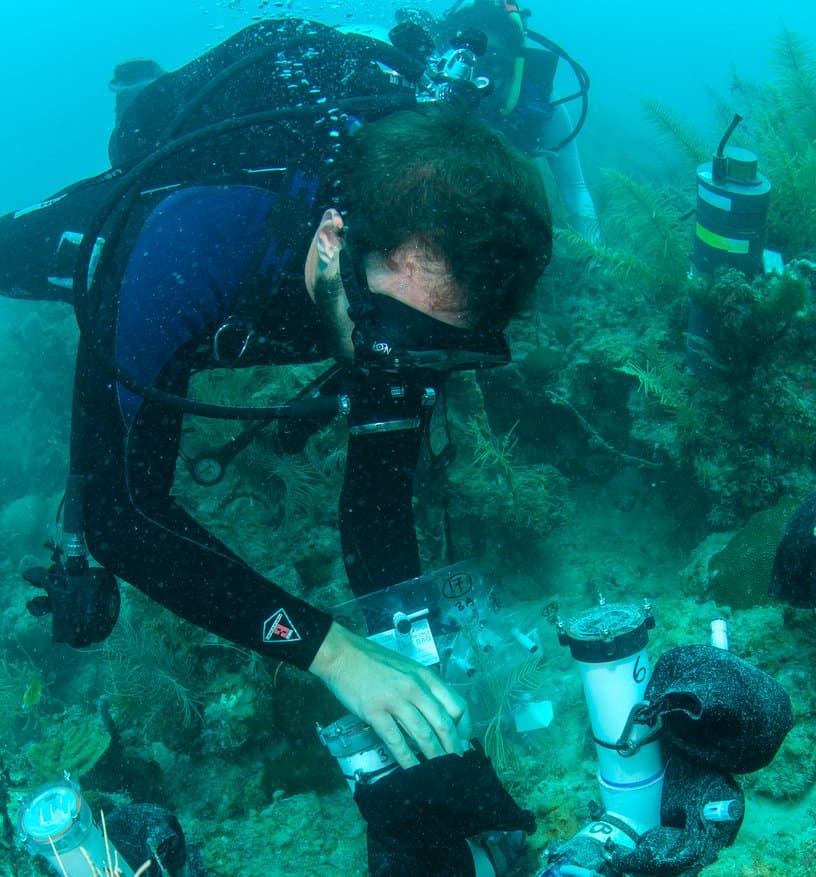
Subsurface Automated water Samplers (SAS) Deployment at Dry Tortugas (image courtesy of NOAA)
The lead of the AOML Coral Program, Dr. Ian Enochs, began this effort to build a low-cost open-source water sampler using enclosures built from clear waterproof acrylic with stainless steel hardware, with materials adding up to almost $1,000. Research labs have limited budgets and, with such a high cost of materials, it was unrealistic to expect the first version of the sampler to be used widely. However, without automation, all samples had to be collected by hand, increasing field time and costs. Manual collection also made it extremely difficult to collect high frequency, synchronized, or night-time samples. Enochs and Formel turned to 3D printing to bring that cost down and expand the types of datasets they could collect. “3D printing allowed us to maintain the complexity of the research we wanted to carry out, and do it for a fraction of the cost,” said Formel.
The AOML Coral Program started with the most ubiquitous 3D printing technology, a desktop fused deposition modeling (FDM) unit, but quickly ran into a roadblock. FDM prints aren’t watertight—the way in which an FDM print nozzle lays down material creates small gaps in between layers, and would allow water to seep in, damaging the delicate internal electronics and sampling motors. Upon hearing about SLA technology, the team got started with a Form 2, and later Form 3, to create watertight samplers from PVC pipe and 3D printed parts to replace the original expensive acrylic housings.
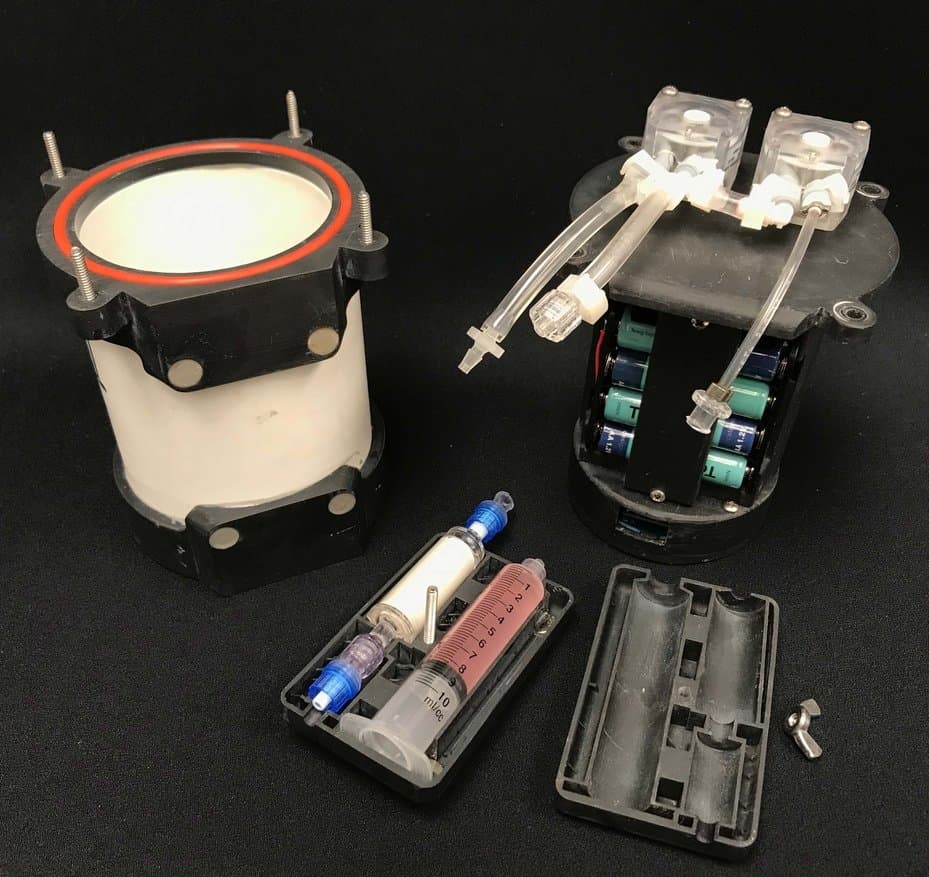
Subsurface Automated Sampler for eDNA (SASe) with SLA end-caps, sample cartridge, and internal armature. (image courtesy of NOAA)
“We now have these very customized 3D printed components that have the necessary connection points and through-holes to allow us to collect water samples. The original sampler design that motivated all of this, we stopped making it for $1,000 and started making it for $220. That means I can now put out five samplers when I used to only be able to put out one.”
Nate Formel
In-House Aquaria: Testing Extreme Conditions
Inside the Experimental Reef Lab (ERL) at the University of Miami’s marine campus, Formel and scientists in the AOML Coral Program maintain multiple identical aquarium systems meant to simulate different conditions in reef environments. Each of these aquariums maintain control of a suite of environmental variables, including water acidity, temperature, light, and flow rate, among others.
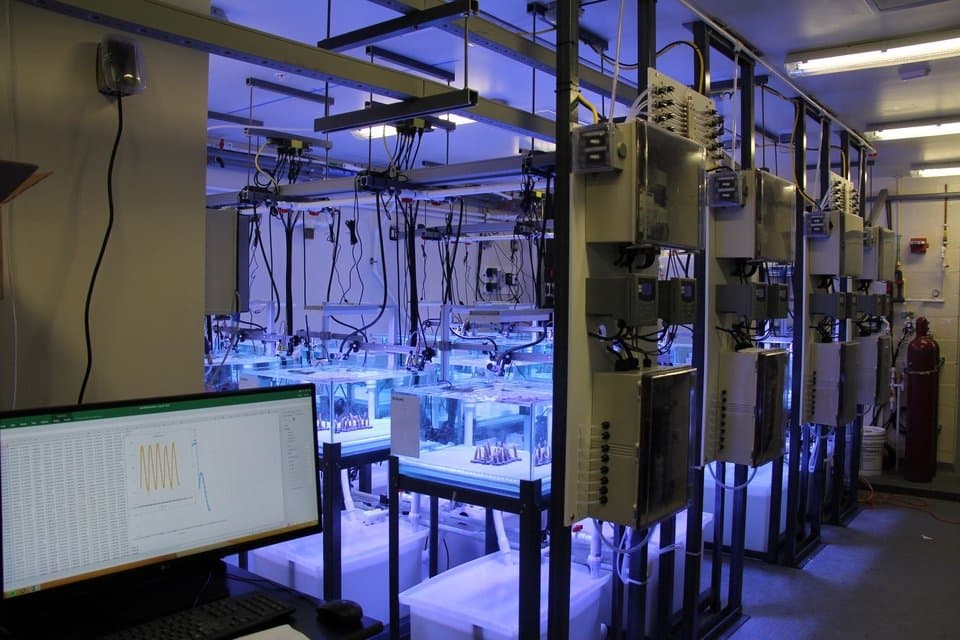
The Experimental Reef Lab; each tank has specific controls and requires a customized electronics casing. SLS 3D printing them allowed the team to reduce costs and increase the efficacy of their data collection process. (image courtesy of NOAA)
Scientific sensors and equipment in a saltwater aquarium environment require waterproof housings and robust and reliable mounts to avoid being damaged by splashed water and the corrosive salt air.
Being able to 3D print watertight housings and assemblies allowed them to introduce automation into husbandry of the experimental aquariums as well. By creating a 3D printed housing for splash proof feeders, they automated the feeding of corals throughout the night, eliminating hours of labor and improving and standardizing the timing of feeding events for coral.
Another 3D printed creation was a waterproof stir-plate housing. They wanted to be able to control water mixing in a closed chamber within their tanks. Stir plates are common enough, but waterproof stir plates are expensive. Instead of purchasing them, the team used a computer fan motor, connected that to a wire that was enclosed within a Formlabs printed housing, secured the lid with an O-ring and an acrylic faceplate, sealed the wire with epoxy, and created their own waterproof stir plate for $30 of materials. The submersible stirplate was incorporated into a novel open-source incubation chamber system for rapid assessment of coral fitness, keeping costs low and the technology accessible, while standardizing and streamlining the research being done.
“That’s one of the awesome powers of 3D printing. We could control water in an identical manner for a bunch of “sub-tanks” within our original tank. Replication is such an important part of science, to test and retest things. When you can replicate [your] experiment many times over, you have a statistically robust way to do your science.”
Nate Formel
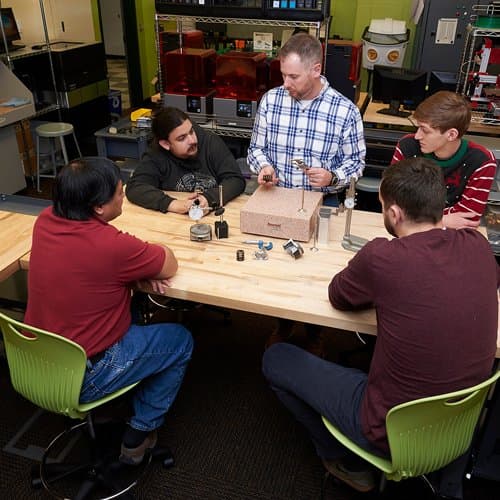
Guide to 3D Printing In Education
In this guide, we’ll discuss the benefits of 3D printing in education, from improved student collaboration to workforce development and empowered creativity.
Rugged Parts for Repeatable Science
Though ideal for creating waterproof housings, SLA printed parts were still not as sturdy as the AOML Coral Program was looking for. Further, they require time intensive post-curing to make them suitable for use with marine organisms. Sintered nylon, however, was a familiar material used to make many off the shelf components, since nylon removes any concerns for impacts to their study organisms while also creating incredibly tough components.
Their first nylon print was a simple housing for the experimental aquariums to protect metal switches from corrosion. To test the strength of the prints Formel took a sledgehammer and a chisel to the Fuse 1 printed part and found, impressively, that he couldn’t easily break it.
Formel told us that, “It’s about us becoming as effective and efficient as possible. We’re trying to simplify science and using [more robust tools] makes it easy to practice controlled, repeatable science.”
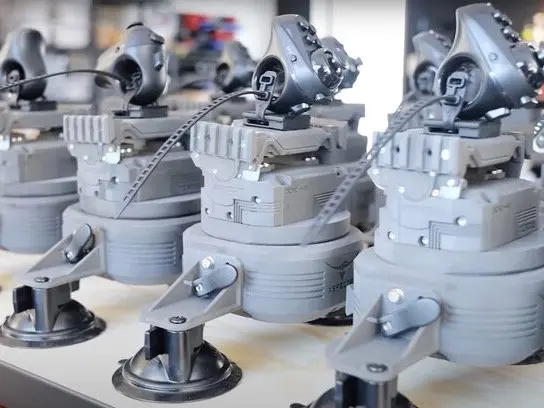
Stress Testing 3D Printed Parts for End-Use Applications
This white paper presents Formlabs 3D printing hardware and material solutions for end-use part production. It documents various users' case studies and includes stress testing results to verify the suitability of 3D printing materials for end-use applications.
The Right Price Point for Research
Formel had to justify the cost of the equipment to the division leadership team. The Fuse 1 had a small enough footprint with a big enough print area, as well as an accessible price point, that it checked all the boxes.
The continued cost savings through print bed optimization and powder refresh rate also contribute to the overall affordability of printing with the Fuse 1. Formel packs build chambers as tightly as possible to align the packing density with the Nylon 12 Powder optimal refresh rate of 30%, meaning only 30% of the build chamber is brand new, unused powder, while 70% is recycled powder from previous prints.
“We haven’t had to get more material since purchasing the machine. The recycle rate is so helpful, and we shoot for optimal packing density. It translates directly into a low cost per part,” says Formel.
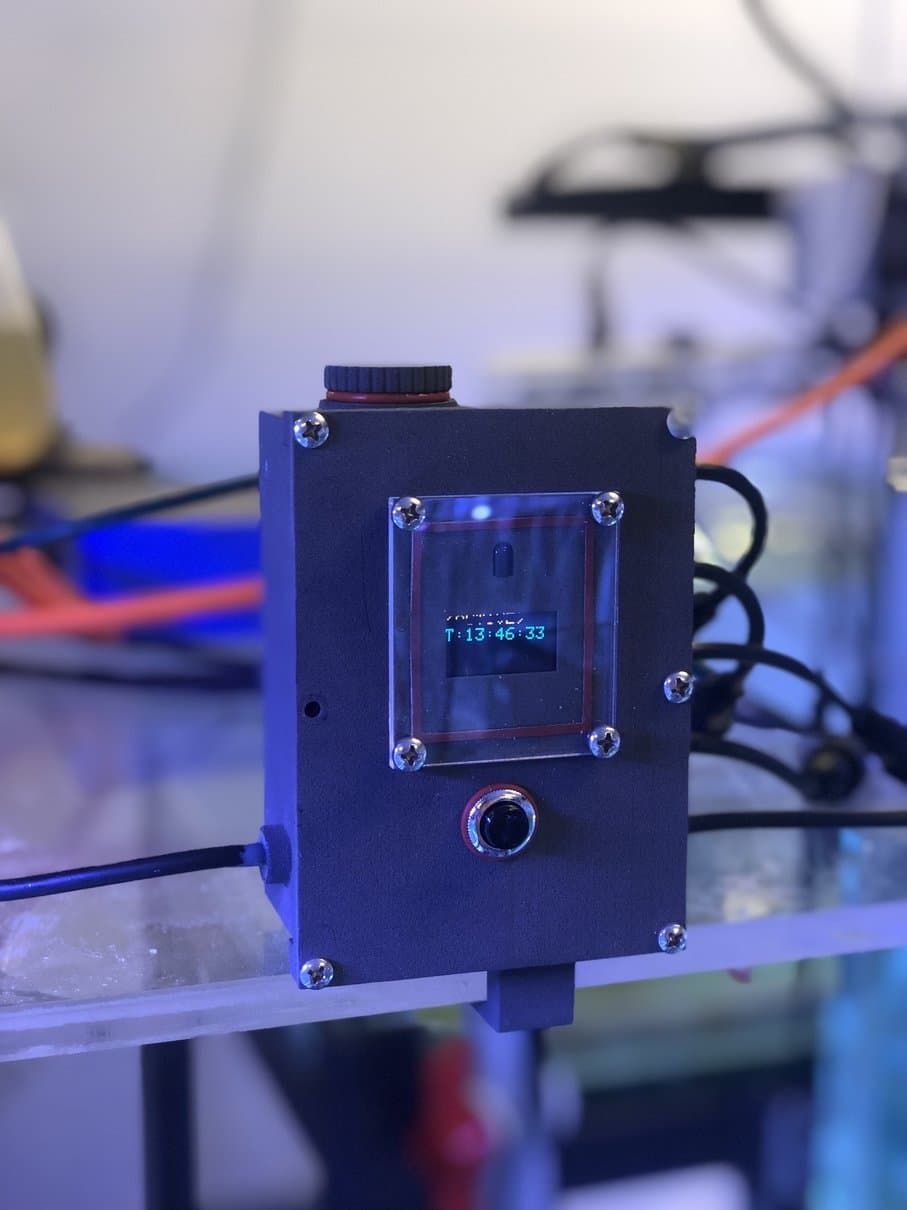
Fuse 1 printed electronics housing (left) and sensor mount (right). (images courtesy of NOAA)
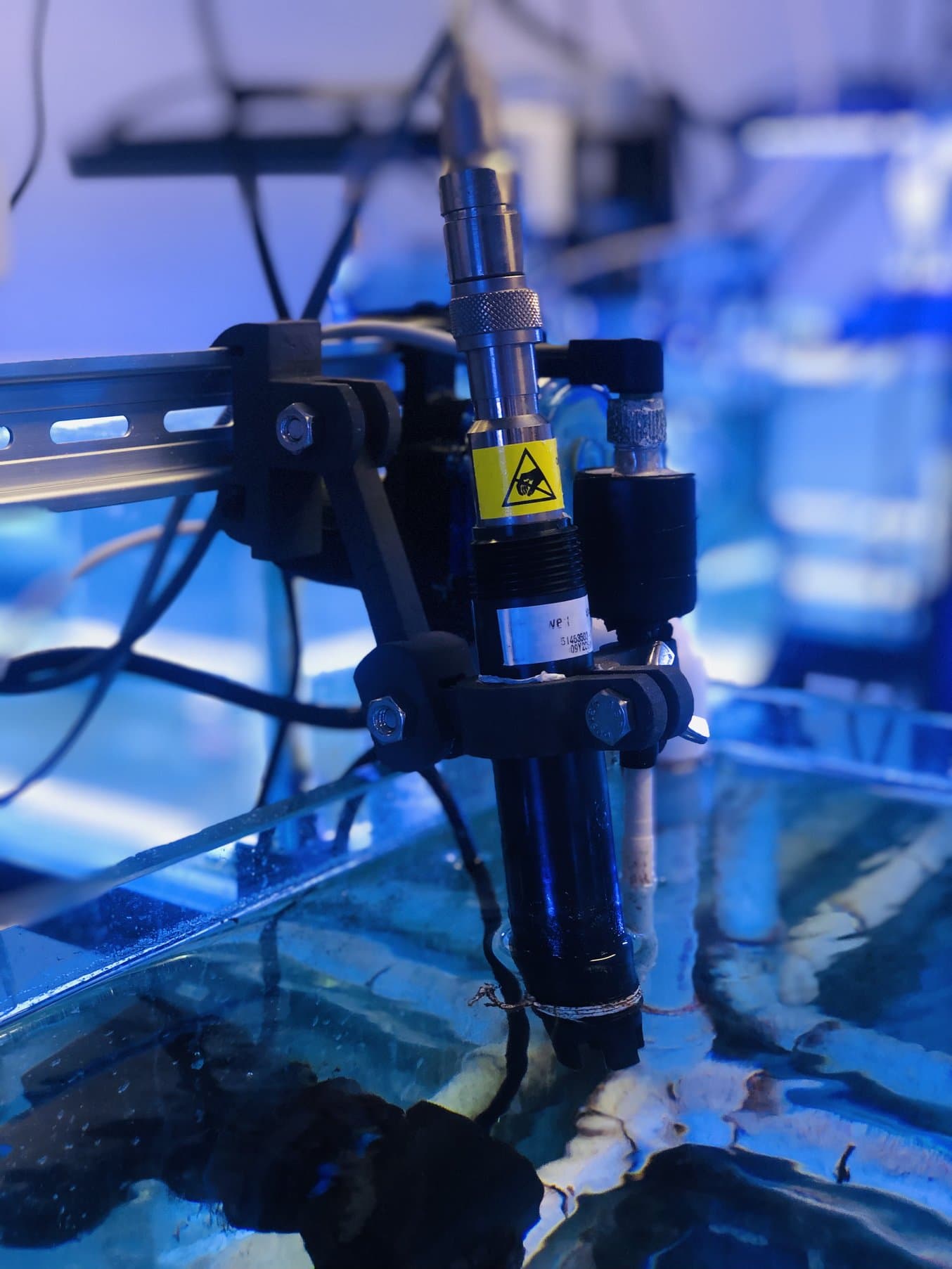
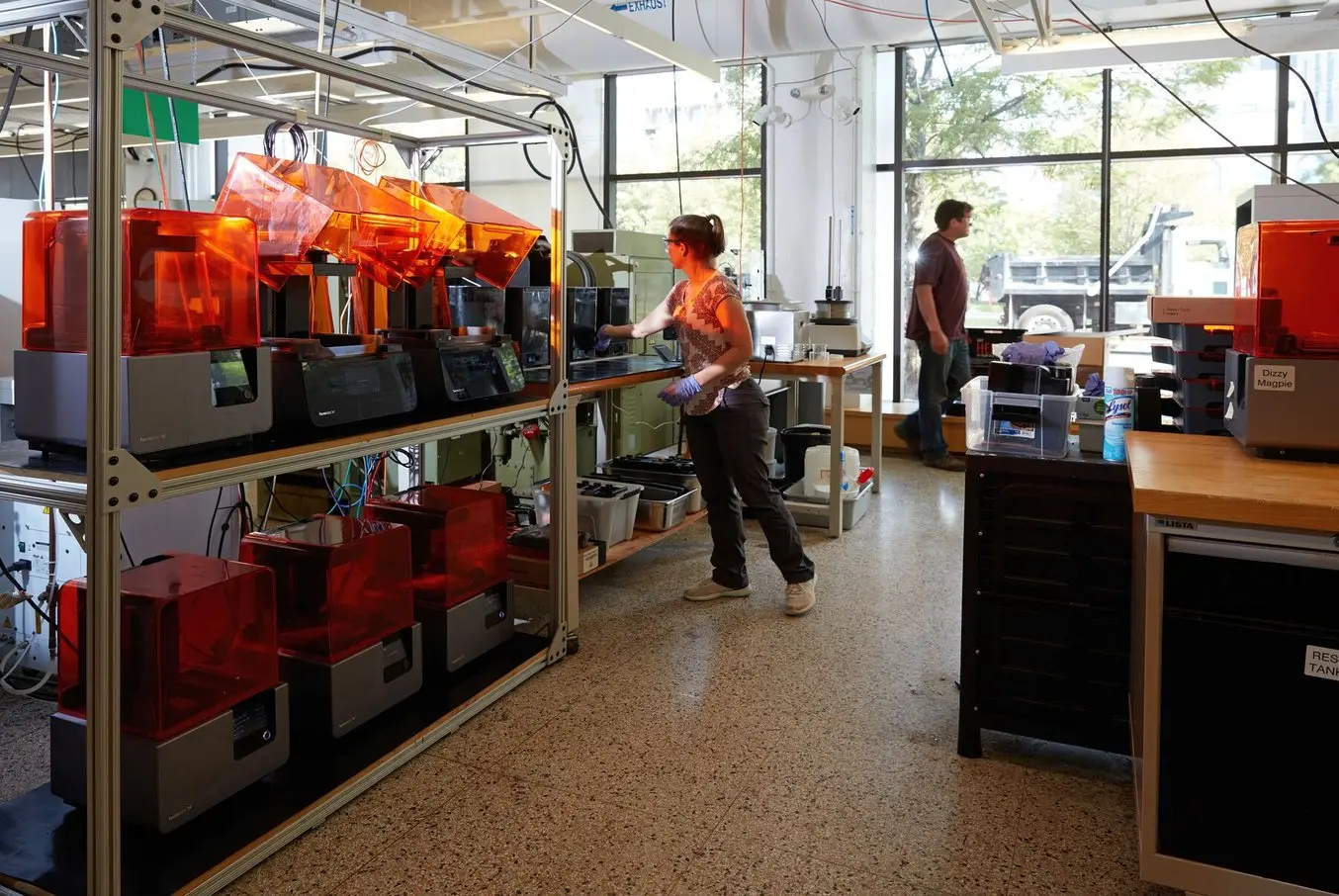
Special Pricing for Educational Institutions
Accredited educational institutions are eligible for special pricing, including a 10% discount on printers, hardware, and select accessories, and free Open Material Mode. Contact Formlabs or an Authorized Reseller to verify your eligibility.
Democratizing Science to Face a Global Threat
Both the field sampling and the in-house aquarium results provide a wealth of data to help researchers understand how coral could survive in harsh conditions. Through funding from NOAA’s Coral Reef Conservation Program, the AOML Coral program is working to identify more resilient corals, and their mechanisms of resilience, to help regrow the coral reefs that are such an important part of the marine ecosystem and the global economy. But one lab can’t do it alone, so Formel and his team make their tools, including their 3D designs and parts, totally open-source, to spread knowledge and awareness about their methods and results.
“One term we use is ‘democratize science’. We want to make it easier for everyone to use the same tools, and these printers have really helped us step up that effort. The potential for new things to get created that no one has thought of before has increased with 3D printing because of the accessibility. Prior to this job, I’d never invented a part, and now I do it all the time.” says Formel.
To encourage that same spirit of invention in younger generations, NOAA AOML and the University of Miami bring students from middle school through graduate school to the lab for educational sessions and tours. These future scientists, engineers, and innovators are able to get exposure to 3D printing technology as well as witness first-hand how the science of climate protection and restoration works.
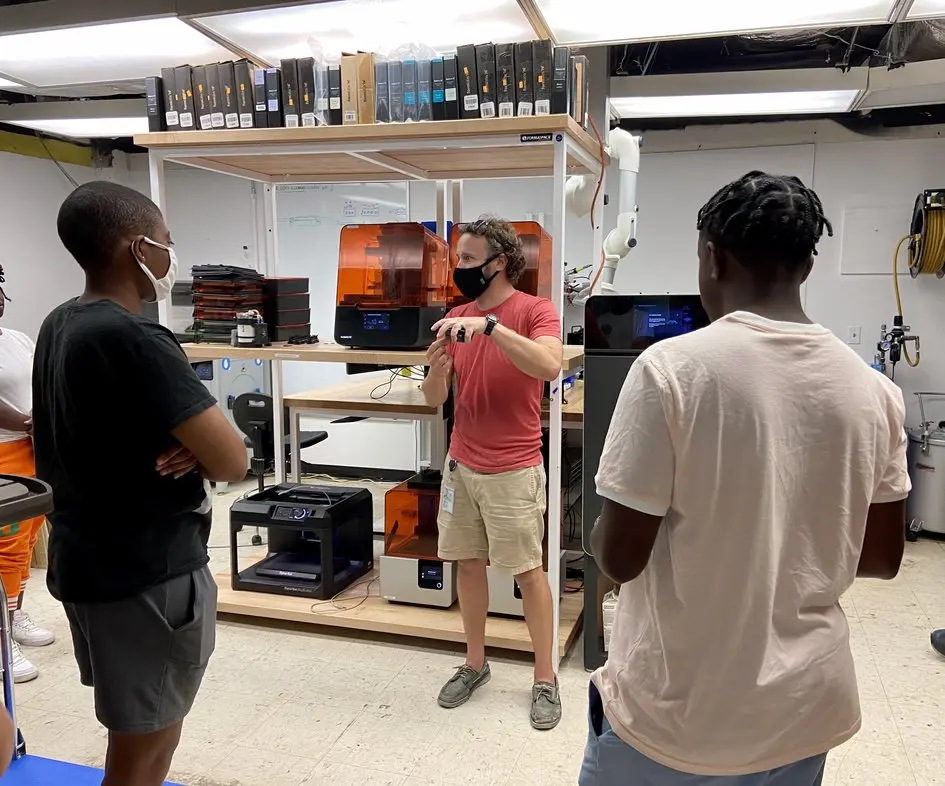
Formel hosting a group of students visiting the lab, with several 3D printing technologies represented, including Formlabs SLA and SLS printers. (image courtesy of NOAA)
As climate change worsens, new strategies and techniques for fighting its effects will be developed by this younger generation. Just as Formel has become accustomed to inventing new tools with his Formlabs printers, the engineers of the future will have to create things that no one has thought of before. Exposure to accessible, affordable, and easy-to-use 3D printers is integral to helping them do that, and NOAA and the AOML are committed to helping make that happen through events like these educational sessions.