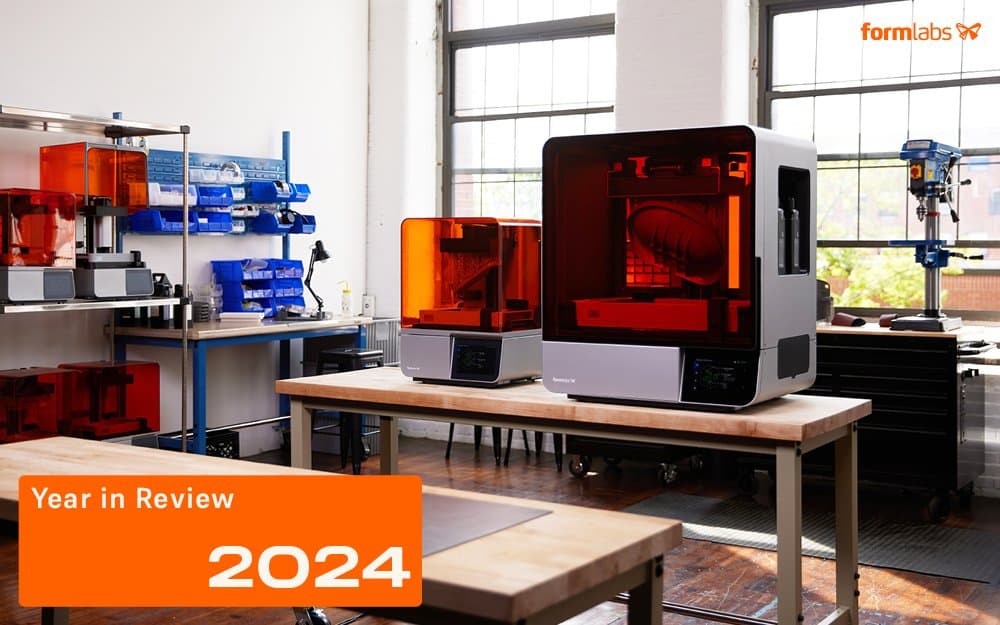
2024 was a groundbreaking year at Formlabs as we continue to push the boundaries of what it’s possible to 3D print. This year brought the release of our blazing fast masked stereolithography (MSLA) Form 4 Series 3D printers, the opening of our ecosystem, and much more. From bringing together innovative users at User Summit, to celebrating our users’ unique stories, we’re closing out the year with just a few of our (and your) highlights from 2024.
Need for Speed
Form 4 and Form 4B
In April, we announced our Form 4 masked stereolithography (MSLA) 3D printer and Form 4B for biocompatible printing. Delivering 4x the speed and 30% more build volume than Form 3/B+, Form 4/B redefines the industry standard for speed, accuracy, reliability, and material versatility and received glowing reviews from the likes of Tested and TechRadar.
“The Form 4 impresses with some of the speediest, most accurate, and detailed prints we've seen from any 3D printer yet.”
Alastair Jennings, TechRadar
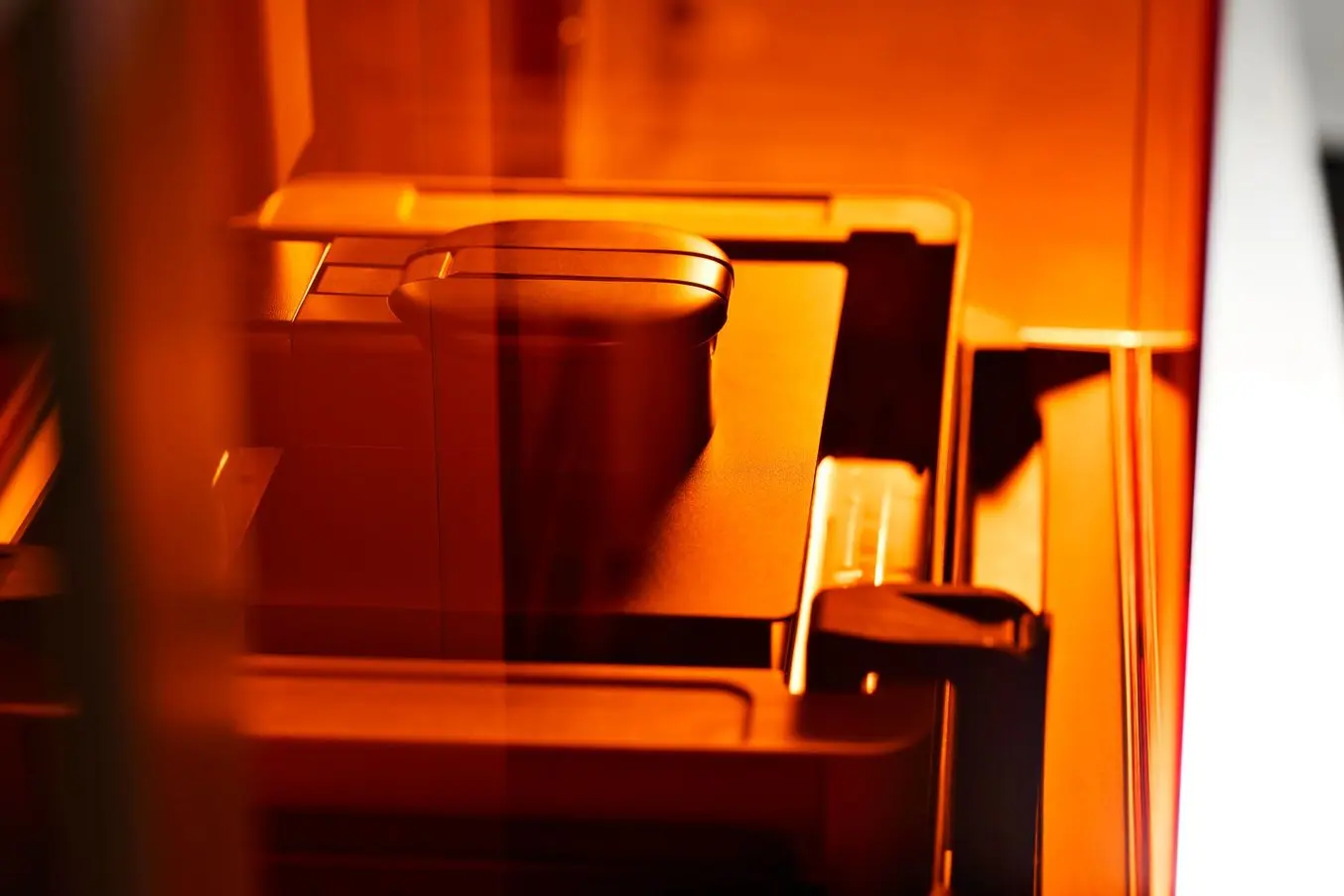
Product Demo: Form 4
See how Form 4 can enable new levels of productivity and innovation through its unmatched speed, accuracy, and reliability.
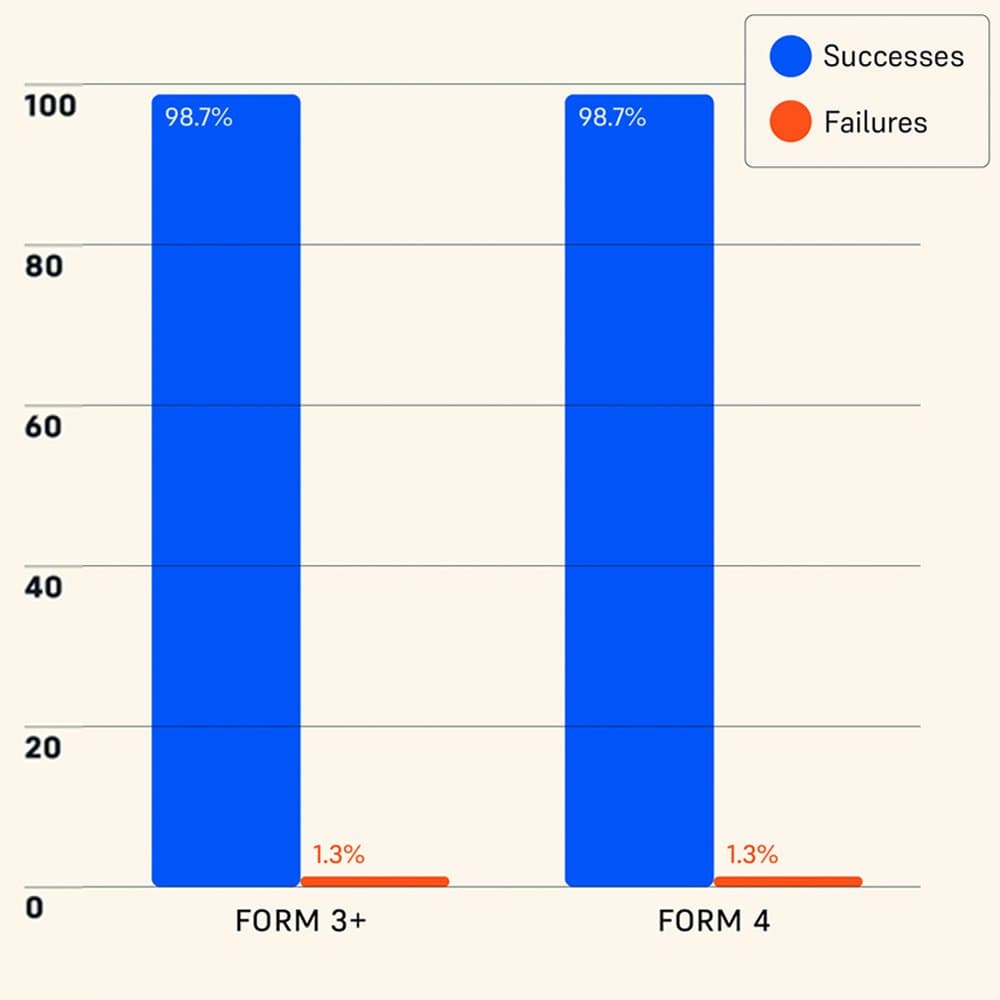
Independently Tested Reliability of Form 4 and Other Resin 3D Printers
Formlabs Form 4 was measured to have a 98.7% print success rate by an independent global leader in product testing. Read a complete description of the test methodology and see the results in our white paper.
Form 4L and Form 4BL
Six months after releasing Form 4/B, we announced Form 4L and Form 4BL, large-format MSLA 3D printers. Built on the same groundbreaking Low Force Display™ (LFD) technology as Form 4/B, Form 4L/BL delivers most large parts in under six hours without compromising on accuracy or reliability.
Empowering scalable production of medical devices, or large prototypes before lunch, Form 4L/BL’s reliability, precision, speed, and ease of use is garnering rave reviews from the likes of Norm Chan at Tested, and users like Brose, Archer Aviation, and St. Louis Children’s Hospital.
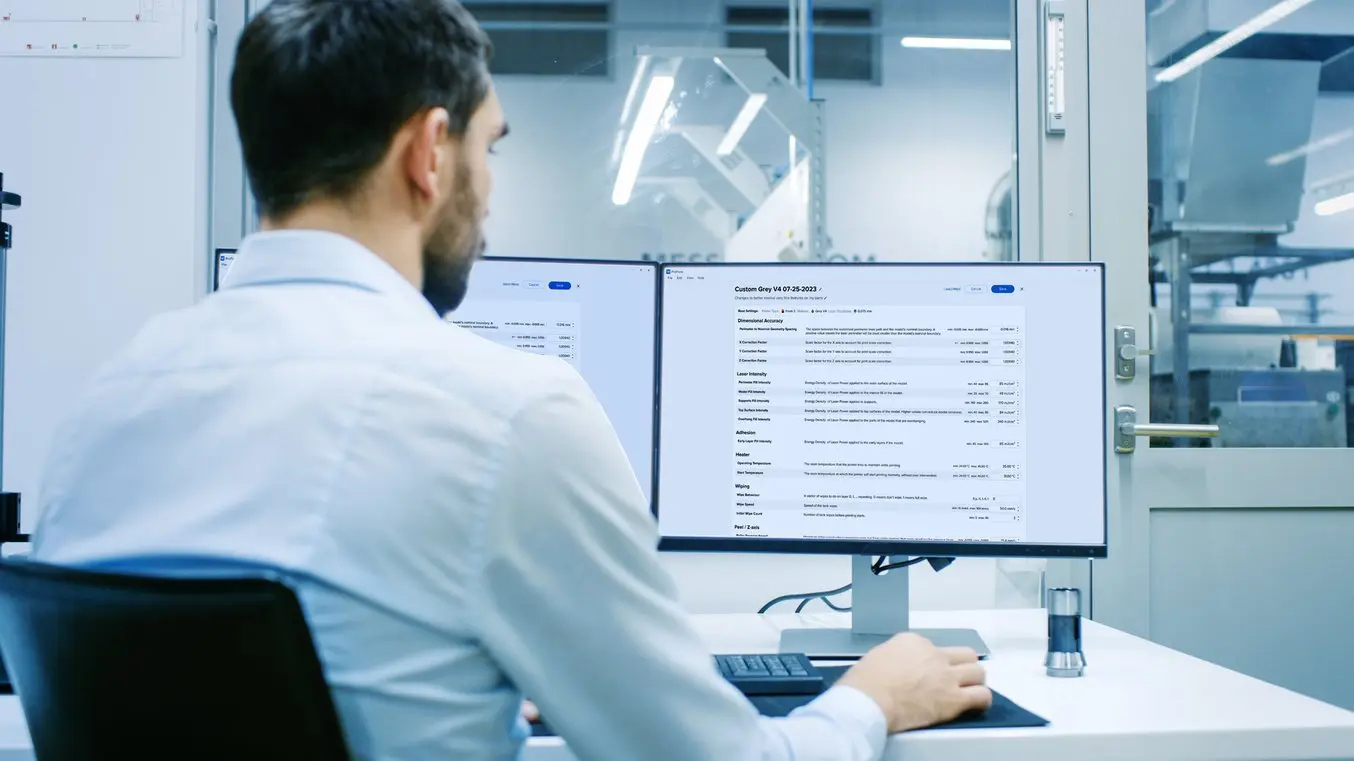
Talk to Our Sales Team
Whether you need to prototype at speed, or are producing end-use parts, we’re here to help. The Formlabs Sales team is composed of dedicated specialists who know exactly how to support you and your company's needs.
Expanding Possibilities With New Materials and Open Material Mode
We pride ourselves on our expansive material library and the versatile materials that, with our ecosystems, consistently deliver exceptional parts. But we also know that there are challenges beyond those we have materials and workflows for and users pushing the boundaries of material science. As of this fall, Formlabs is open! Open Material Mode enables expert users to print with third-party materials and custom resins, and opens the Formlabs SLA and SLS ecosystems.
Our material scientists took advantage of the groundbreaking hardware of Form 4 Series printers to develop new resins such as Fast Model Resin, Formlabs’ fastest printing resin. Our new General Purpose Resins, Grey Resin V5, Clear Resin V5, White Resin V5, and Black Resin V5 offer enhanced aesthetics, improved mechanical properties, and faster print speeds. Fast Model Resin can reach print speeds of 100 mm per hour at a 200 μm layer height, accelerating design and production timelines.
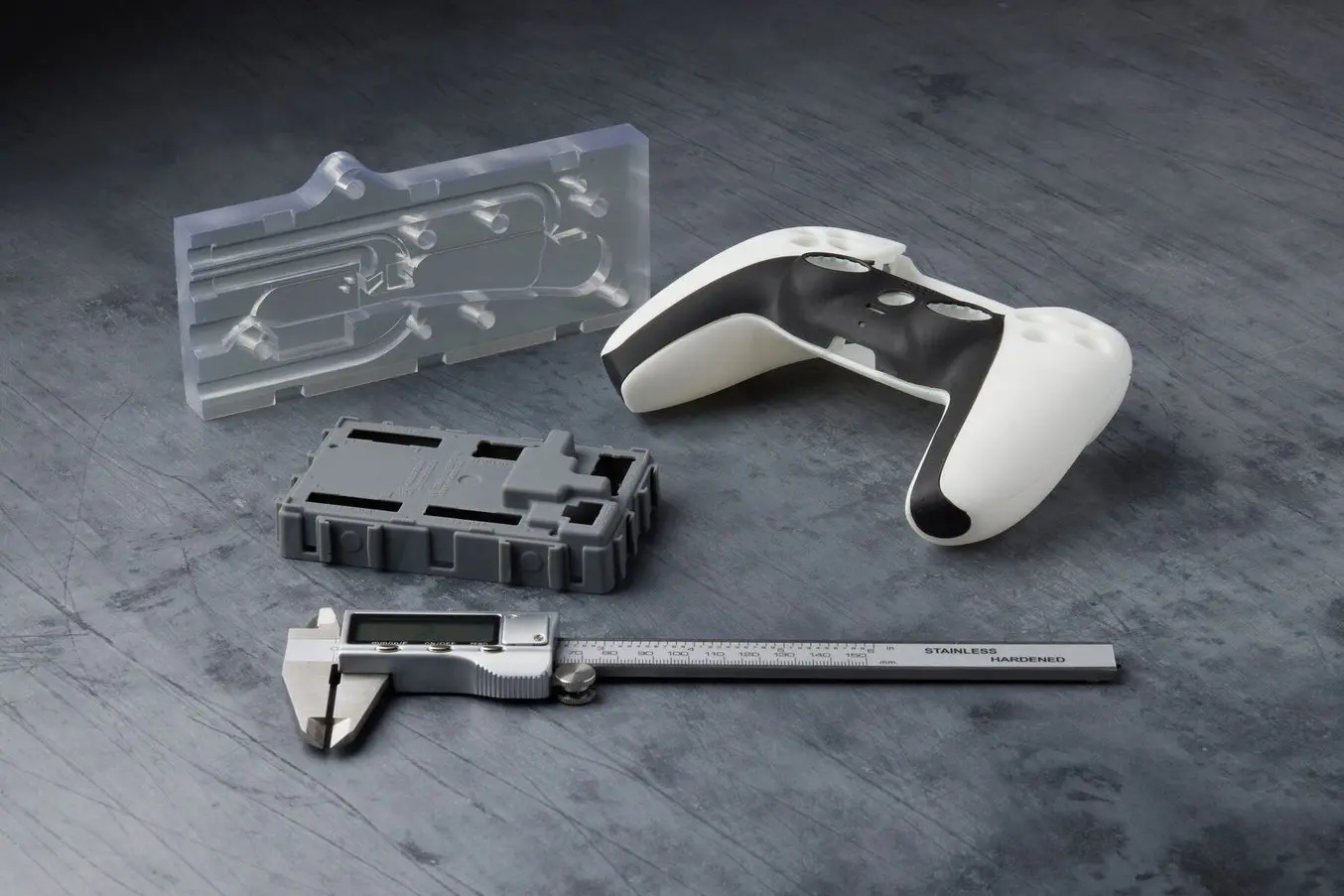
General Purpose Resins for Form 4 Series 3D printers have enhanced aesthetics, improved mechanical properties, and faster print speeds, all at a lower cost per liter.
Released in September, Clear Cast Resin was developed specifically for industrial investment casting foundries for the direct production of casting patterns in-house at reduced costs, decreased turnaround times, and improved flexibility in iteration and production.
Nylon 12 White Powder and Nylon 12 Tough Powder are materials that empower Fuse Series customers to expand their in-house capabilities. Nylon 12 White Powder makes advanced post-processing workflows easier than ever, for dyed, painted, and coated photo-ready parts that match your brand’s aesthetic and are ideal for medical applications where color contrast is necessary. Nylon 12 Tough Powder’s high ductility and low refresh rate make rugged, end-use parts more affordable than ever.
To learn more about Formlabs materials, explore our material library or request a free sample part to evaluate materials for yourself.
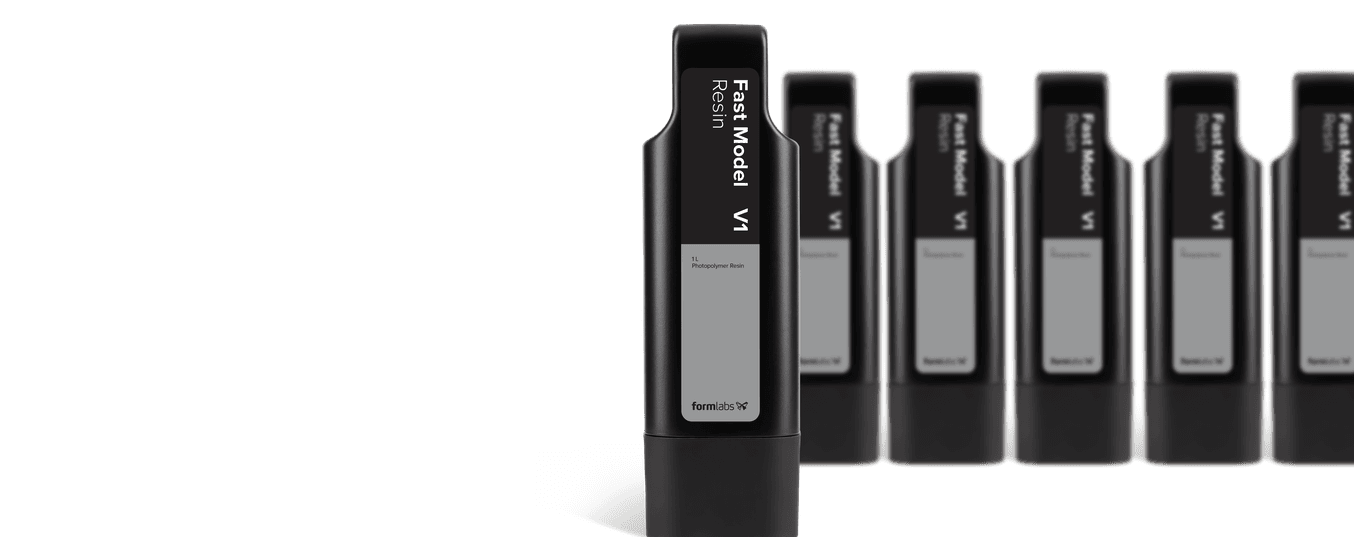
Form 4 Materials Guide
Learn more about all the high performance materials available on Form 4 and how to leverage the right material for your application.
Not In Theatres: Thought-Provoking Videos
User Summit
This fall we livestreamed our 2024 Formlabs User Summit, a full day of application talks, SLS and SLA deep drive, and conversations with industry trailblazers like Youtuber @TomStantonEngineering.
Form 4 Breakdown Video With Shane Wighton of Stuff Made Here
In a detailed, hour-long video, Shane Wighton of the YouTube channel Stuff Made Here visited Formlabs and, in front of the lead engineer for Form 4 (who used to work under Shane), breaks down an entire printer. Watch the detailed deep dive into the technology and hardware of Form 4 that’s fascinated so many.
Can 3D Printing Compete With Injection Molding?
With the blazing speeds and fine finishes of Form 4, we set out to show how 3D printing can compete with traditional injection molding — and the comments went wild with questions. So intense was the debate that we released a second video pitting two Form 4Ls against injection molding as both rushed to produce an actual part used in our printers. Let the debates commence!
Saving Charlotte
Charlotte the green sea turtle suffers from Bubble Butt, where air gets trapped under a turtle’s shell, crowding their organs and making it difficult to swim. Together, Mystic Aquarium, Adia, New Balance, and Formlabs developed a 3D scanning, design, and printing solution to create a customized weighted harness that helps Charlotte swim again.
10 Innovative Applications From Formlabs Users
Ford Developed the New Explorer Using Formlabs SLA and SLS 3D Printers
Ford Motor Company is the sixth largest automaker in the world, producing over 4 million vehicles a year and employing over 175,000 staff worldwide. At the heart of Ford's European operations is Ford Cologne, including PD Merkenich’s Rapid Technology Center, which is instrumental in creating rapid prototypes for product development and responsible for designing all passenger vehicles for the European market from the ground up.
Brose: Leveraging SLA and SLS Technology to Bolster Automotive Production
“We decided to jump onto the Formlabs boat here. We did that because the material availability and the consistency of the prints were so much improved that the technology is now ready to be helpful in the automotive industry. The issue for us is that safety and durability concerns exist, especially with the OEMs. We’re trying to rule this out. And in collaboration with Formlabs, we have proven that we can implement parts like we do on the current BMW X7.”
Matthias Schulz, Manager, Seat Prototyping, Brose North America
One in every three new vehicles coming off the assembly line today has at least one component manufactured by Brose — one of the five largest family-owned automotive suppliers in the world. Brose’s commitment to continuous improvement has led them to invest in new technologies like additive manufacturing and automation to streamline their processes and deliver innovative solutions for each of their customers.
3D printing is at the core of multiple initiatives in Brose’s design and end-use manufacturing processes and has helped Brose adapt and respond to all the changes in the fast-paced automotive industry.
Arbutus Medical Went From Concept to Commercialization in Four Months for Rapid Medical Device Development
“We did all the testing, all the verification, with 3D printed parts. It was basically a four-month project from idea to sellable part.”
Radu Postole, Product Design Lead, Arbutus Medical
Arbutus Medical creates specialized procedure kits with high-performance single-use instruments so patients can receive treatment faster and doctors can spend their time treating instead of tracking down tools.
Formlabs resin 3D printers are used to not only prototype medical devices, but to manufacture devices for human factors testing and pilot production. For the latest device, a Kirschner Bow, Postole worked with Phil Tsao, a Formlabs ambassador and founder of Ember Prototypes, a rapid prototyping, consulting, and product design firm, to leverage 3D printing to sprint from idea to commercialization in one year, even utilizing 3D printing for stopgap production, producing over 800 parts a month.
“I still have the Rigid 10K prototype and the injection molded T1. Every time somebody comes to my shop, I show them as an example of what we can do. People are always blown away by how good the Rigid 10K assembly looks. They can't tell the difference between that and the injection mold, other than the color.”
Phil Tsao, Founder of Ember Prototypes
MOSOLF: How Police and Special Vehicles Are Produced With SLS 3D Printing
MOSOLF Special Vehicles GmbH is a leading special vehicle manufacturer based in Kippenheim, Germany. Their clients require a diverse range of custom and low-volume parts, where tooling costs render traditional manufacturing methods economically unfeasible. For MOSOLF, 3D printing presents an ideal solution.
“I estimate that every third police van [in Germany] now contains additively manufactured parts. At MOSOLF, we are now so far advanced with 3D printing that there is no vehicle that leaves our yard without an additively manufactured part in it. We now 3D print around 5,000 parts per year, but we are on an upward trend, which means that we have at least three parts in every vehicle if not more.”
Carsten Busam, Head of Project Planning, MOSOLF Special Vehicles GmbH
Archer Aviation Develops Next-Generation Air Taxis
“Form 4L allows us to print big parts of super high-quality, barely any hand finishing on them, and readily usable. The machine has been flawless for the entire time we have had it.”
Julien Thiebaud, Design Manager, Advanced Technologies, Archer
Archer Aviation, Inc. a leader in electric vertical takeoff and landing (eVTOL) aircraft, is reimagining air travel with the development of the next generation of air taxis. When the advanced technologies division, a full design studio doing interior design for aircraft, tested Form 4L, they found that it increased the number of iterations the team could do in a week, putting their best FDM to shame and producing functional prototypes that required 80% less sanding and finishing.
Rosenberger: Optimizing Traditional Manufacturing and Lead Times With 3D Printed Tooling and End-Use Parts
The Rosenberger Group is one of the biggest global players in internet connectivity, manufacturing the high-frequency fiber optic and high-voltage connectivity solutions that power our global network. To maintain their success in a constantly changing industry (and to be a key driver of that change), Rosenberger has worked with Formlabs since 2017, leveraging both SLA and SLS technology at every stage of production.
"Our colleagues, but also the industry in general, have come to realize that we can be faster and more agile with 3D printing than with machining in order to develop solutions."
Manuel Kapsreiter, Equipment Designer, Rosenberger
Heidelberg: 3D Printing Robotics Applications and Replacement Parts for Printing Presses
Heidelberger Druckmaschinen AG is the leading global manufacturer of offset printing presses and produces a wide range of tools and automation solutions for the entire printing value chain, from some of the largest and fastest state-of-the-art printing presses to cutting and folding machines. They originally added SLS 3D printing to optimize prototyping and product development, but today the company uses 3D printed parts in series production, producing thousands of parts per year for around 15 different applications.
“The most essential point for us is the speed of 3D printing. We have a swift response time to customer requirements, which are constantly changing. We can develop and produce new parts within one or two days, whereas it used to take us several weeks in some cases. That's why 3D printing is perfect for us.”
Joachim Krumma, Management, CTS-3 GmbH
Prime Inspections Digitalizes Pipeline Operations and Maintenance With SLS 3D Printed Tools
“The SLS process and the Fuse printers have changed the way we do business, especially as we look to expand.”
Craig Burke, Prime Inspections
Prime Inspections helps oil and gas companies construct, monitor, and maintain pipeline systems by providing nondestructive testing (NDT) and field-joint coating (FJC) services. SLS 3D printing has significantly enhanced their ability to complete this work faster, safer, and more efficiently. “I don’t think we could have done it without having the Fuse printers. Going metal, the cost would outweigh the benefit. Not only are these printers fast, but as soon as I can dream up a part, 10 hours later it’s in my hands,” Burke says.
Unilever & Serioplast Develop New Bottle Designs With 3D Printed Molds
“A consumer goods company like Unilever must be on the market as soon as possible or before your competitors. You need to offer the best product at the best price in the shortest time possible to the consumers. 3D printing helps us speed up this process.“
Stefano Cademartiri, CAD & Prototyping Owner, Unilever
Unilever is constantly developing new products for everyday use, from personal care to home care, nutrition, and more. Packaging, including the design of a bottle, can sometimes affect customer perception as much as what’s inside. But for a “simple” plastic bottle, getting from a design on the computer screen to filling it on the manufacturing line has traditionally taken many months. With Formlabs SLA printers and Rigid 10K Resin, Unilever and Serioplast were able to reduce lead times by up to 70% and tooling costs by up to 90% to produce pilot runs of 200 units in only two weeks.
Deutsche Bahn Uses 3D Printed Manufacturing Aids to Streamline Vehicle Maintenance
“We started with 3D printing in 2015, and since then we have already produced over 100,000 parts at Deutsche Bahn that have resulted in millions of Euros in savings.”
Susanne Tost, Marketing Specialist at DB Group Project 3D Printing
As one of the largest railway companies in the world, Deutsche Bahn is responsible for the mobility of more than 10 million passengers per day. With over 40 plants throughout Germany that service its fleet of passenger and freight trains, 3D printing is a key tool for producing manufacturing aids that simplify workflows, reduce costs, and help get trains back on the rails faster.
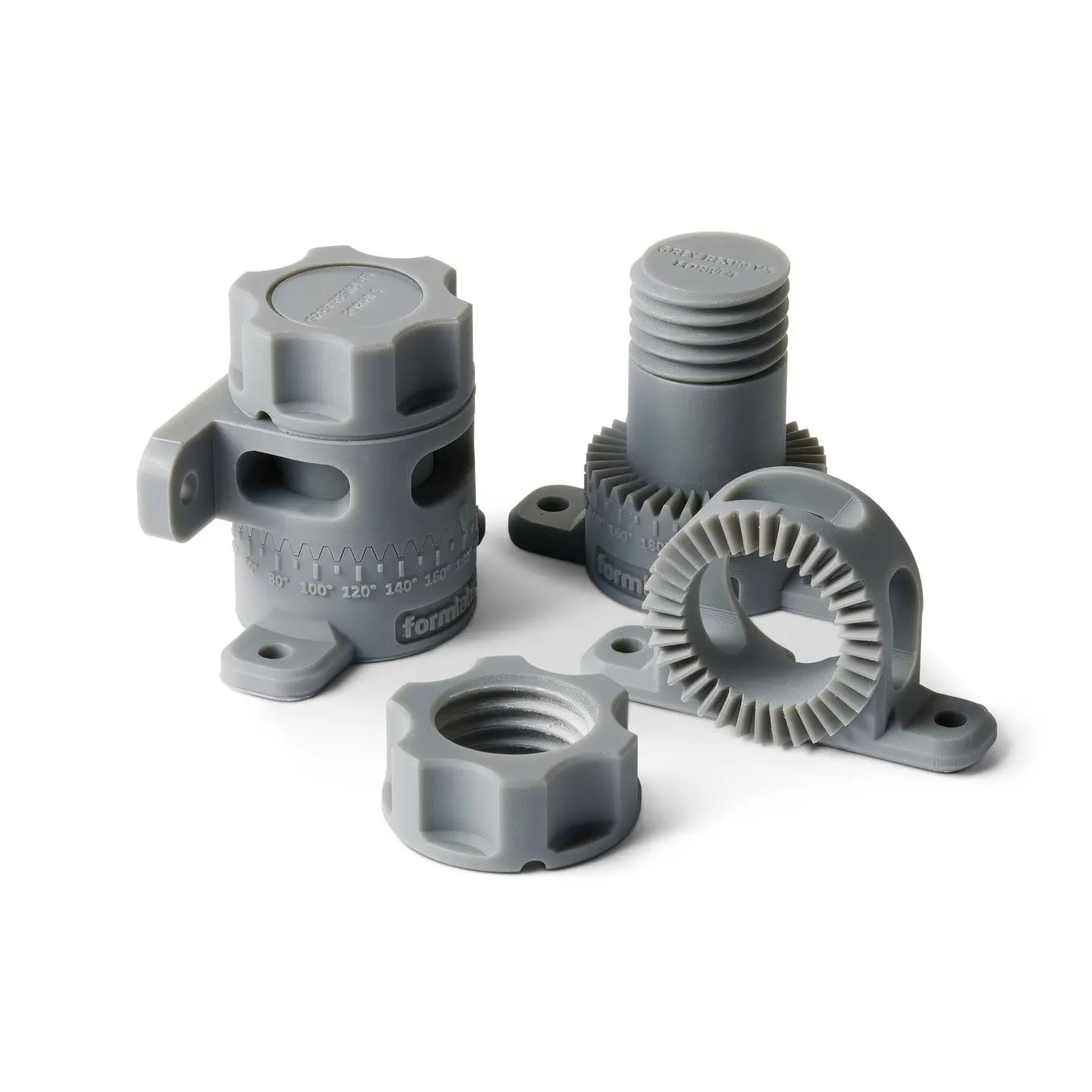
Request a Free Sample Part
See and feel Formlabs quality firsthand. We’ll ship a free 3D printed sample part to your office.
Looking to 2025
2024 was one of the biggest years in the history of Formlabs with groundbreaking new printers and materials, the opening of our platform, and so many inspirational stories of the innovative work being done by our users. But for every story we share there are more that go untold; for every product we announce, there’s a team working to bring it to our users.
We’re hard at work pushing the boundaries of just what it’s possible to print. To receive the latest news in 2025, join our mailing list for new product announcements, stories, and educational content. To start printing, explore our printers or contact sales to learn more.