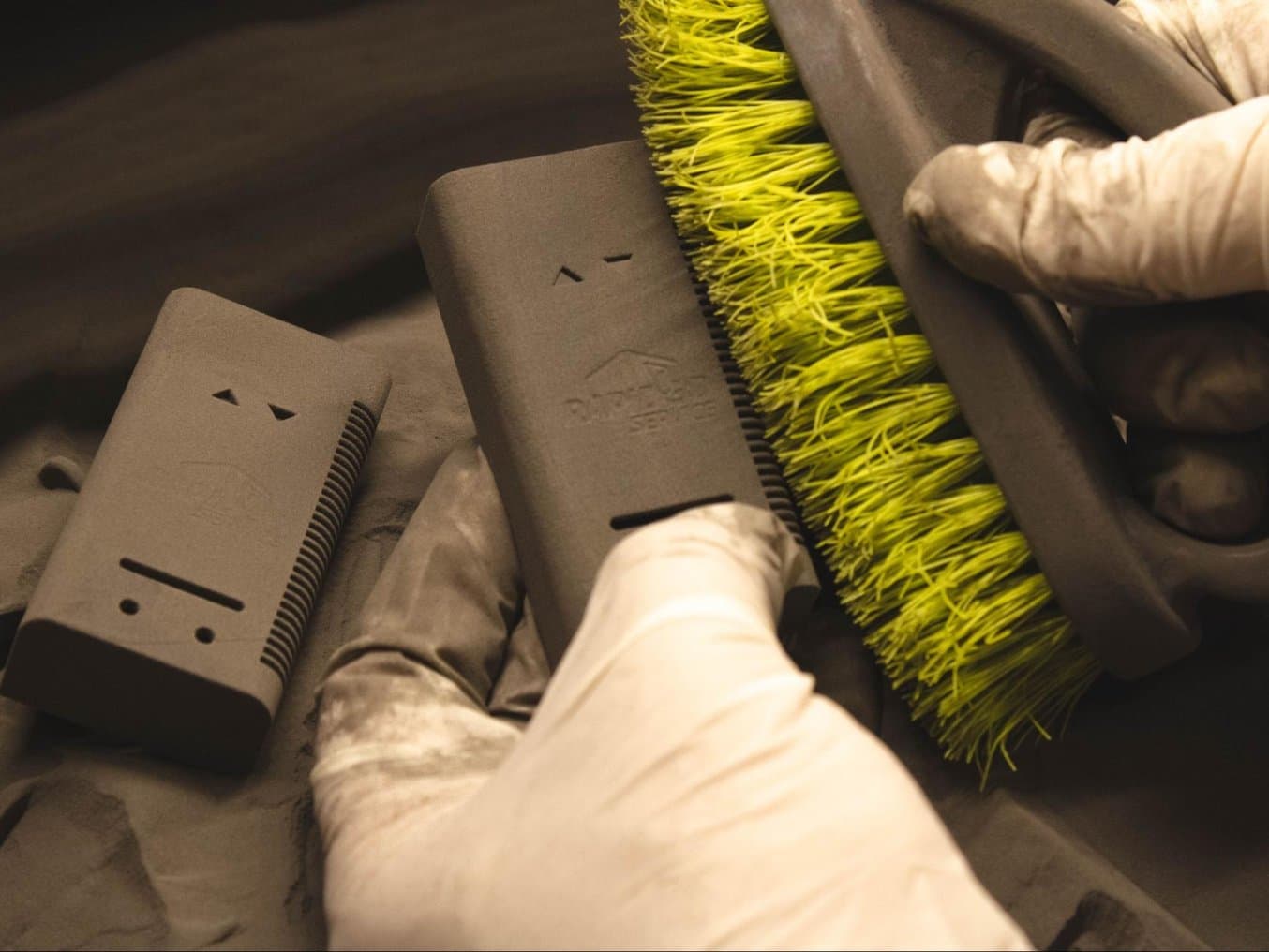
As a service provider in additive manufacturing, Rapid 3D Service helps its customers to convert their design ideas into tangible models and supports them all the way to series production and market launch.
The company is broadly positioned with FDM, SLA, and SLS 3D printing technologies to meet individual customer requests and prototyping requirements. At present, the Fuse 1 SLS 3D printer is their busiest employee with a 100% utilization.
In an interview, owner and managing director Rami Mizrahi and his business partner and wife Anke Mizrahi talk about their success factors, various customer applications and why Formlabs 3D printers appeal to them so much.
Founding a 3D Printing Service Bureau
Rami Mizrahi and Anke Mizrahi founded Rapid 3D Service in 2017 and the company quickly evolved into an all-rounder when it comes to 3D printing. Today, they offer prototyping and small series production using FDM, SLA, and SLS 3D printing. Furthermore, Rapid 3D Service uses SLA 3D printing to produce models for in-house silicone mold making.
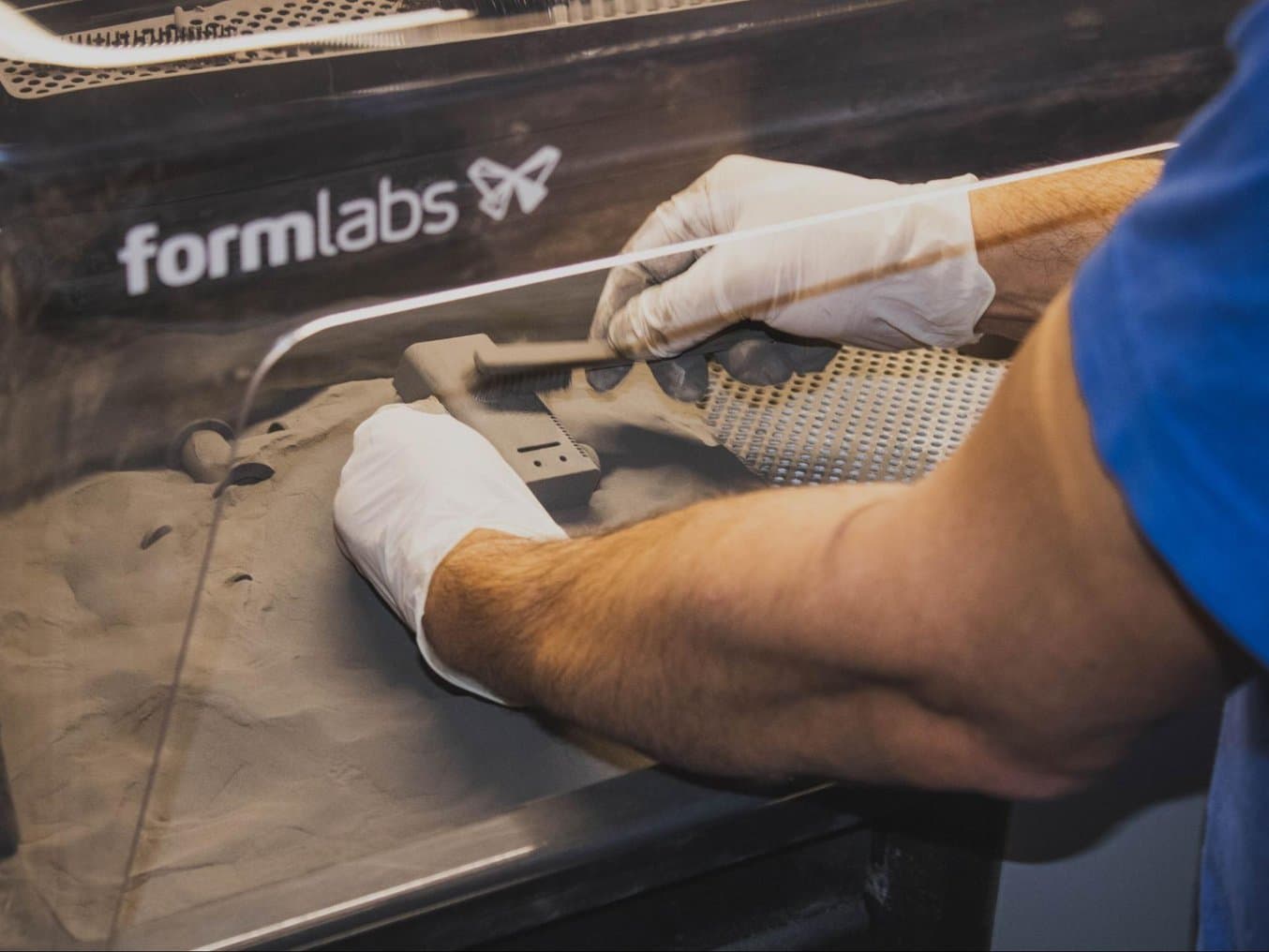
SLS 3D printing finishing process with Fuse Sift.
Rami Mizrahi brings over ten years of 3D printing experience and extensive technical expertise from before he started his own business, which helps him in advising customers and meeting their various requirements.
"We want to diversify to offer the customer the best possible options, since the different 3D printing processes naturally have different advantages and disadvantages," says Anke Mizrahi.
After purchasing their vacuum casting machine for casting silicone models, Rami Mizrahi decided to use a Formlabs SLA 3D printer to build the master models as well as individual directly 3D printed prototypes.
For the SLS 3D printing, they decided on a Fuse 1 from Formlabs, which was quickly supplemented with a second Fuse 1 due to the high demand for the laser sintering process. Due to the comparatively low entry price of the Formlabs Fuse 1 printer, even a young company such as Rapid 3D Service could afford to include SLS 3D printing technology in its portfolio and thus expand its customer base.
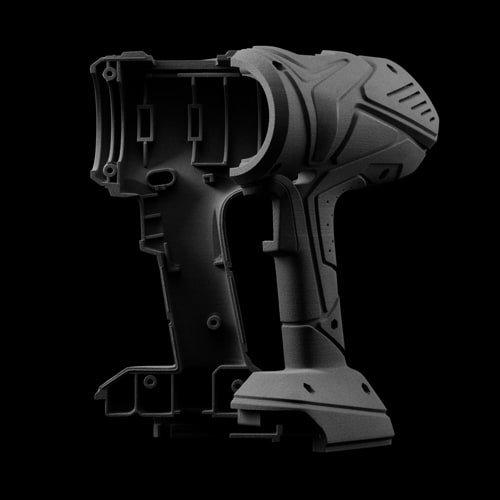
Introduction to Selective Laser Sintering (SLS) 3D Printing
Looking for a 3D printer to create strong, functional parts? Download our white paper to learn how SLS printing works and why it's a popular 3D printing process for functional prototyping and end-use production.
From Idea to Small Series Production
Rapid 3D Service works as an adviser during their customers' product development phase, whether they want to validate their product idea through individual prototypes in silicone molding or through a small series.
"From the inquiry to delivery, service and direct cooperation with the customer are very important to us," says Anke Mizrahi.
To provide detailed solutions to customers' requests, Rami Mizrahi offers technical advice on technologies, materials, and procedures for new requests.
For requests for parts with high load-bearing capacity, small series with large quantities, and high flexibility requirements, Rapid 3D Service generally uses SLS 3D printing.
However, other orders pose special requirements concerning the prototype's surface color or smoothness. In this case, SLA 3D printing or silicone molding is more likely to be used. Another advantage of this process is that filigree threading and similar design elements can be cast directly.
Rami Mizrahi also helps with quality control of STL files so that the radius, support structures, and wall thicknesses are correct for each print.
Fuse 1 Operates at Full Capacity
SLS 3D printing is the method used most often at Rapid 3D Service to produce prototypes and small series.
“Since their introduction in March 2020, our two Fuse 1 3D printers have never been switched off. They have been reliably running at capacity every day ever since."
Rami Mizrahi
SLS 3D printing convinces customers especially with the material properties of the nylon powder, as well as with the price and delivery times offered by Fuse 1. Thanks to laser sintering technology without support structures, the large build chamber of Fuse 1 can be completely filled by stacking components. Small series can be delivered in just a few days.
At the same time, the SLS 3D printing process allows flexibility to implement design customizations for customers just as quickly.
These were also the main reasons why they decided to use SLS 3D printing with one of their clients, Filono, a company that sells magnetic mobile phone mounts for vehicles. The company commissioned Rapid 3D Service to produce mount prototypes. The case was printed in Nylon 12 and Filono's magnetic strip is subsequently inserted into it. Several small series of the different mount variants have been iterated and thousands of them have already been delivered to Filono. These functional prototypes are currently already being sold, tested, and constantly adapted.
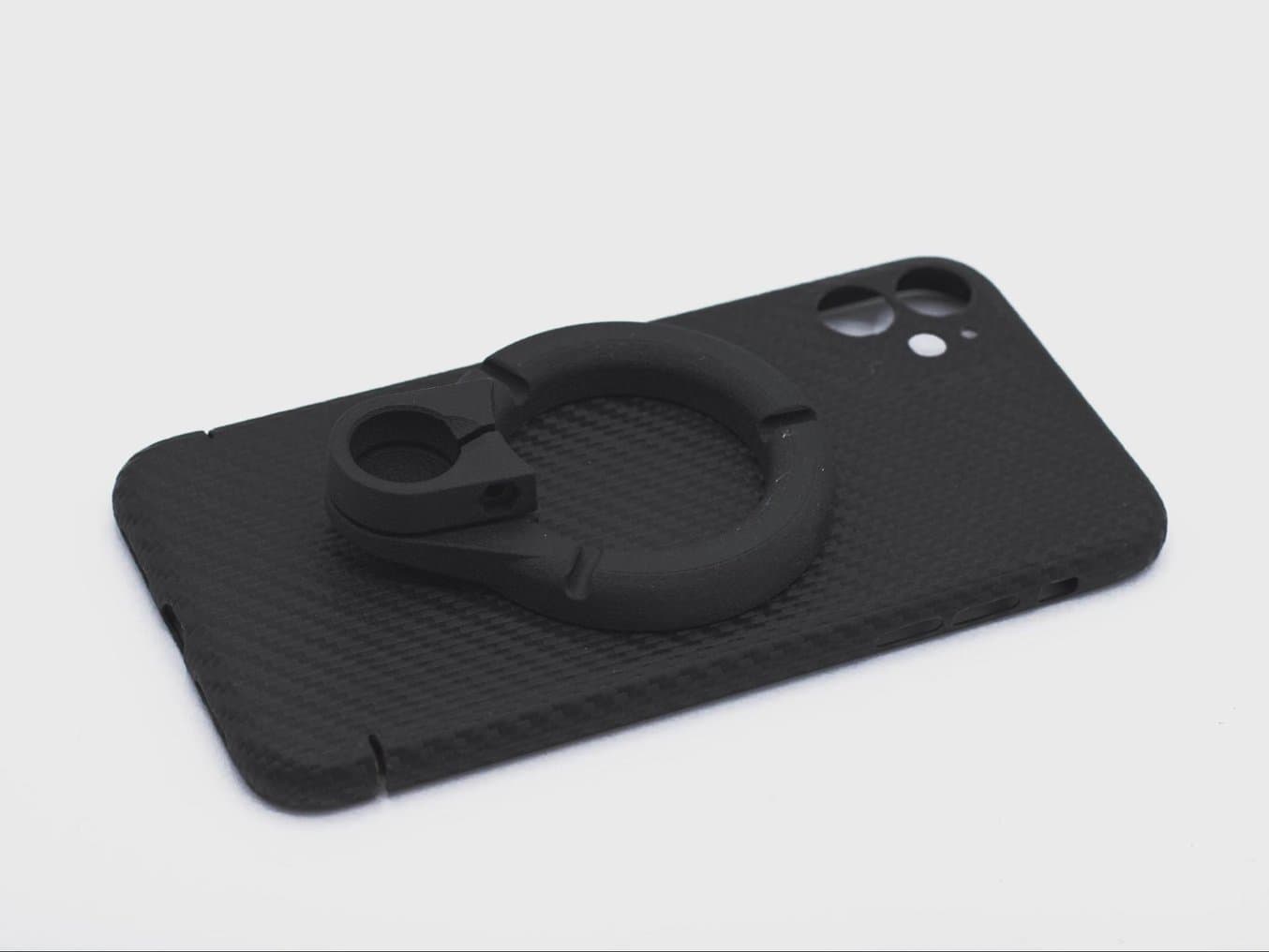
Ring-shaped mobile phone mount by Filono printed using Nylon 12 in small series.
"We usually deliver around a thousand parts per mobile phone mount variant to Filono. After the test phase, we often receive customization requests that we can immediately implement in the next print," explains Anke Mizrahi.
"Because we don't need new tools for each customization, we are much more flexible with iteration loops and quantities than with injection molding."
Anke Mizrahi
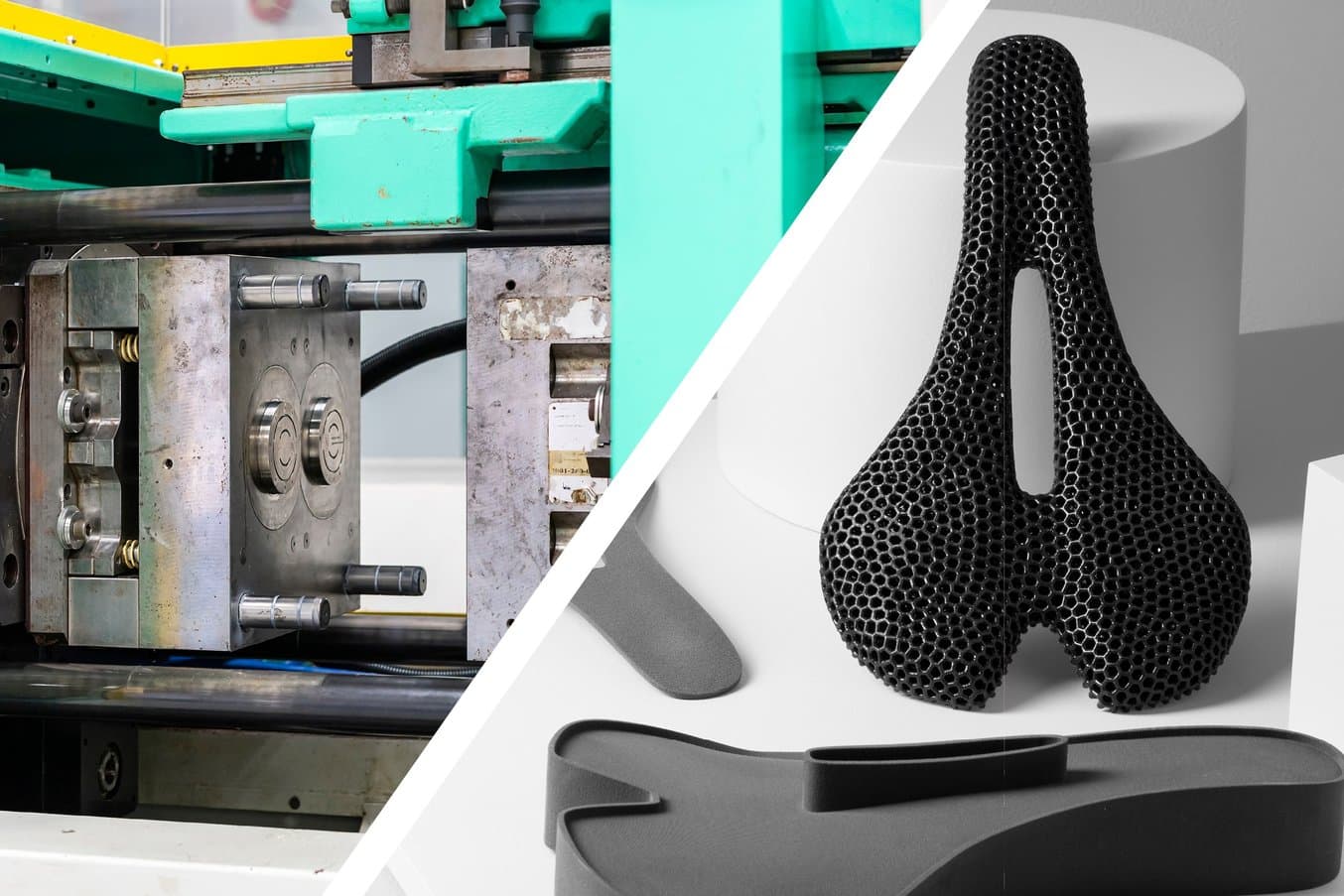
SLS 3D Printing vs. Injection Molding: When Should Injection Molding Be Replaced With 3D Printing?
This white paper discusses the advantages and disadvantages of injection molding and SLS 3D printing, and the applications where they can be used as complementary technologies.
Flexibility is essential for Filono for customizing mounts for cell phones of varying dimensions that have just come onto the market. This allows them to respond to fast-moving trends and rapidly launch new designs on the market.
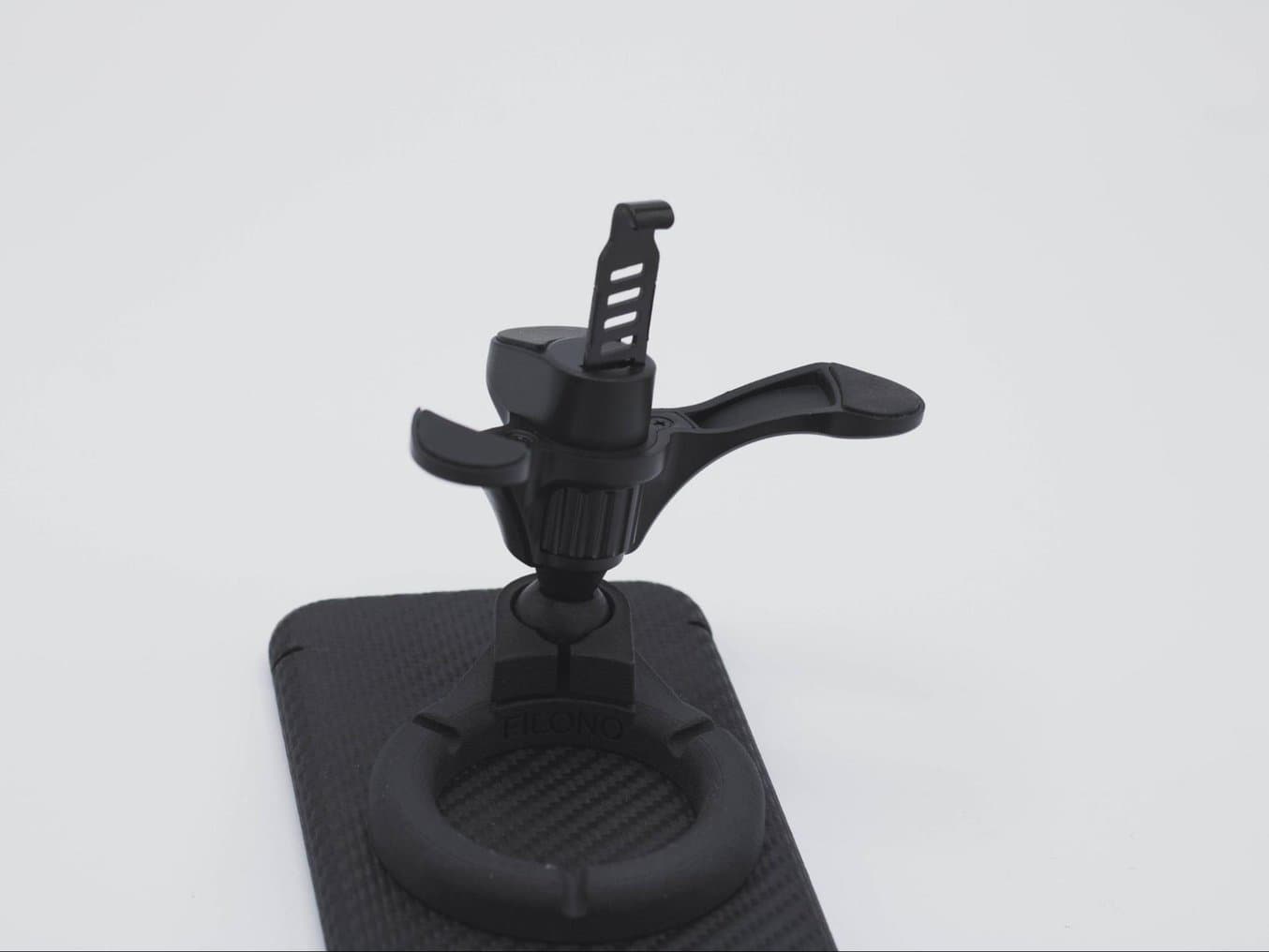
In this example application, Rami Mizrahi benefited above all from the size of the Fuse 1's build chamber.
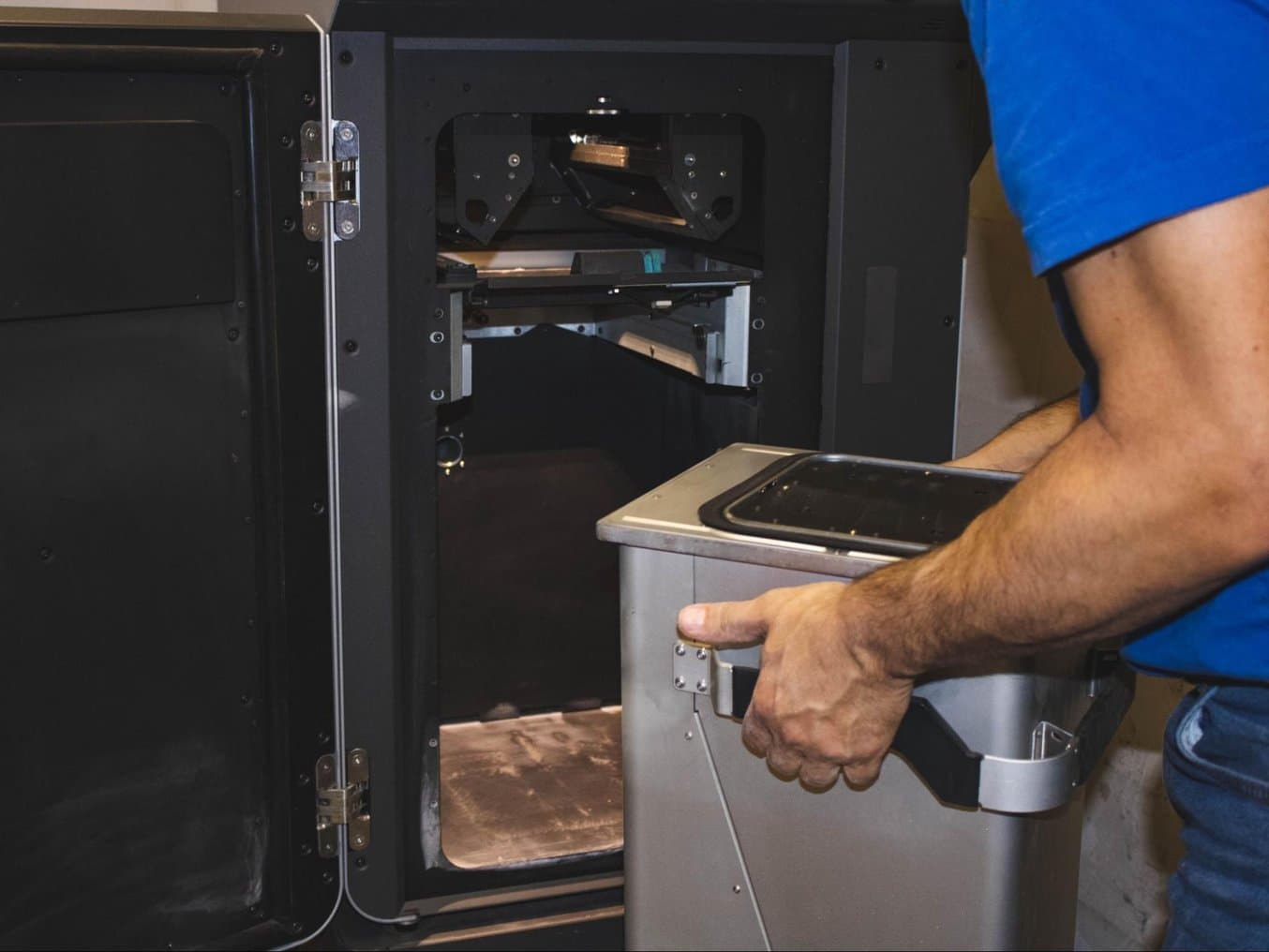
Inserting the Build Chamber into a Fuse 1.
“If I had done the whole thing with an FDM 3D printer, I could probably have delivered ten parts per build at most, because I can fill the platform, but I cannot build upwards. With SLS 3D printing, however, I am able to position the parts in such a way that, for example, I can print 100 cell phone holders in one build. Of course, this speeds up the process enormously, and I can deliver the 100 pieces to the customer within a few days instead of a few weeks,” explains Rami Mizrahi.
Silicone Molding Using SLA 3D Printing
A good example for silicone mold making using SLA 3D printed master models at Rapid 3D Service is a request from the company Witt-Gasetechnik. Prototypes for safety valve housings were needed before the customer switched to series production using injection molding.
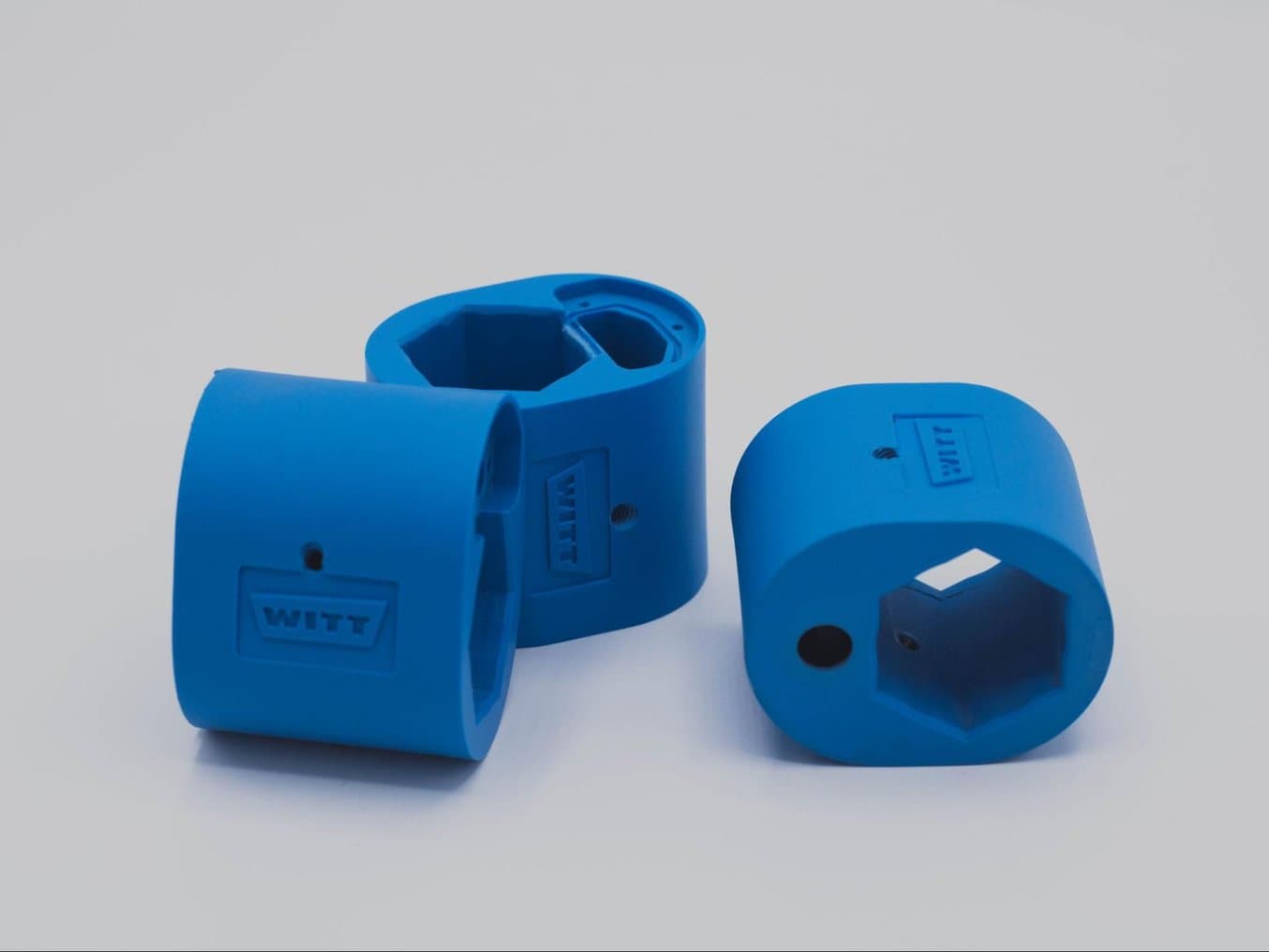
Housing for Witt Gasetechnik safety valves produced with silicone molding and SLA 3D printed master models.
Certain material requirements made silicone molding the most suitable option for these prototypes. Specifically, the material had to have a smooth surface, be UV and temperature resistant, and available in different colors. The housing also had to feature a transparent component to let through the light of a small infrared indicator on the safety valve. The housing, including the cast-in threading for the safety valve itself, were iterated in several versions, such as for a round and a hexagonal valve.
The service bureau printed the master models for this silicone molding using Formlabs Grey Pro Resin. The smooth surface and detail level of these SLA 3D printed parts is extremely important for the subsequent casting. An FDM 3D printed model would have a surface which is too rough due to the layer structure in the print, and it would not haven been detailed enough.
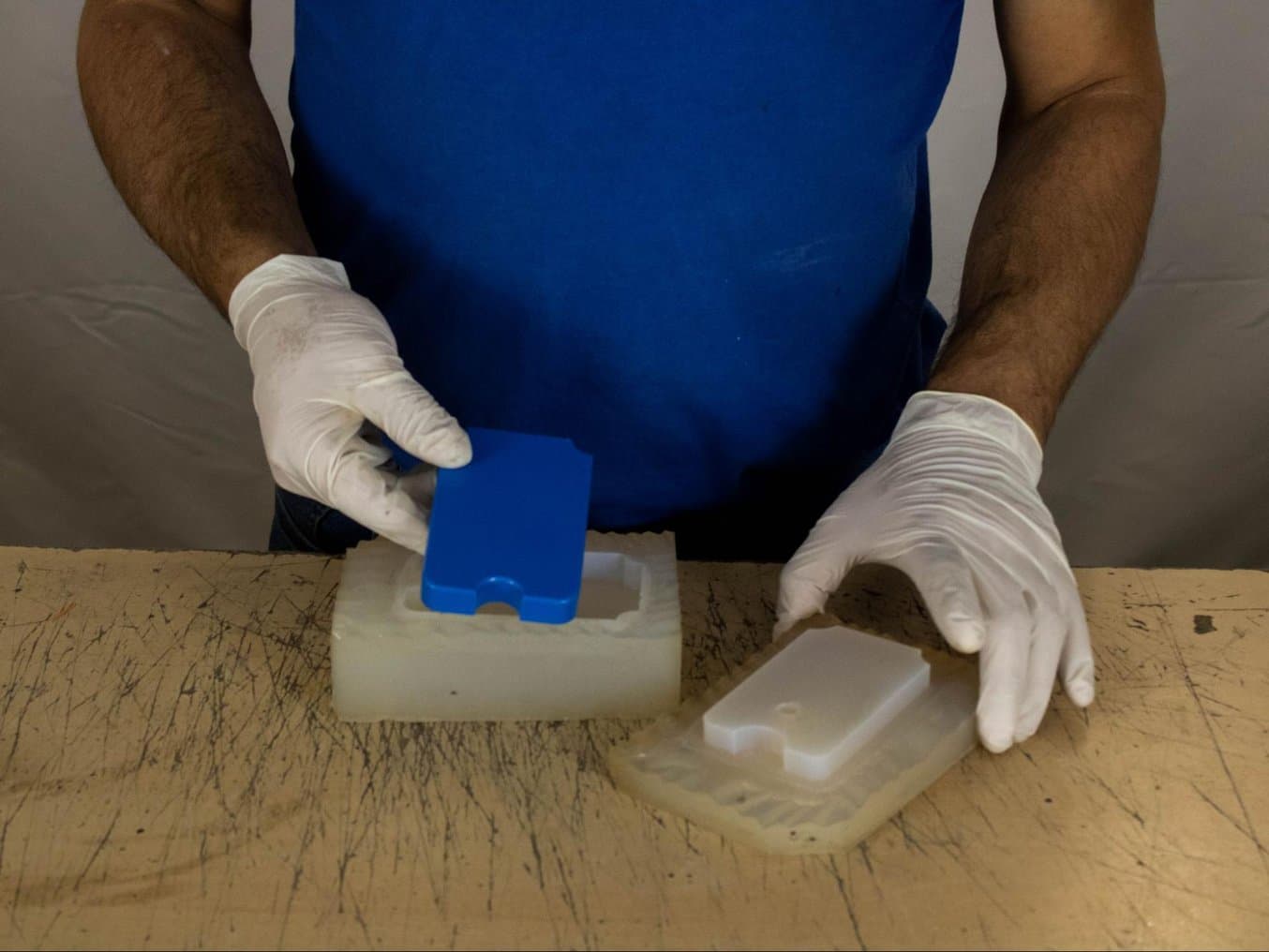
Silicone molding using an SLA 3D printed master model.
"When we prototyped housings for Witt Gasetechnik, we delivered a small series of several hundred parts in different versions. These were customized frequently, and reprinted and molded by us before completing testing and moving onto injection molding,” explains Mizrahi.
In addition to printing master models for silicone molding, Rapid 3D Service occasionally uses the SLA 3D printer for directly 3D printing prototypes.
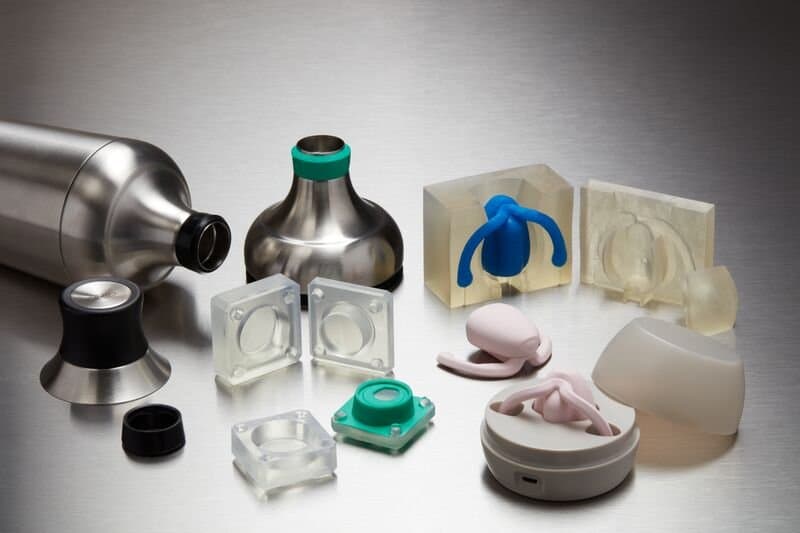
Silicone Molding for the Product Design
This whitepaper includes case studies from OXO, Tinta Crayons, and Dame Products, and presents three distinct implementations of silicone molding for product design and manufacturing.
Scalable 3D Printing
The price range and dimensions of Formlabs SLA and SLS 3D printers gives fledgling service bureaus such as Rapid 3D Service the opportunity to expand their technical capabilities, allowing them to grow and expand their business as demand increases.