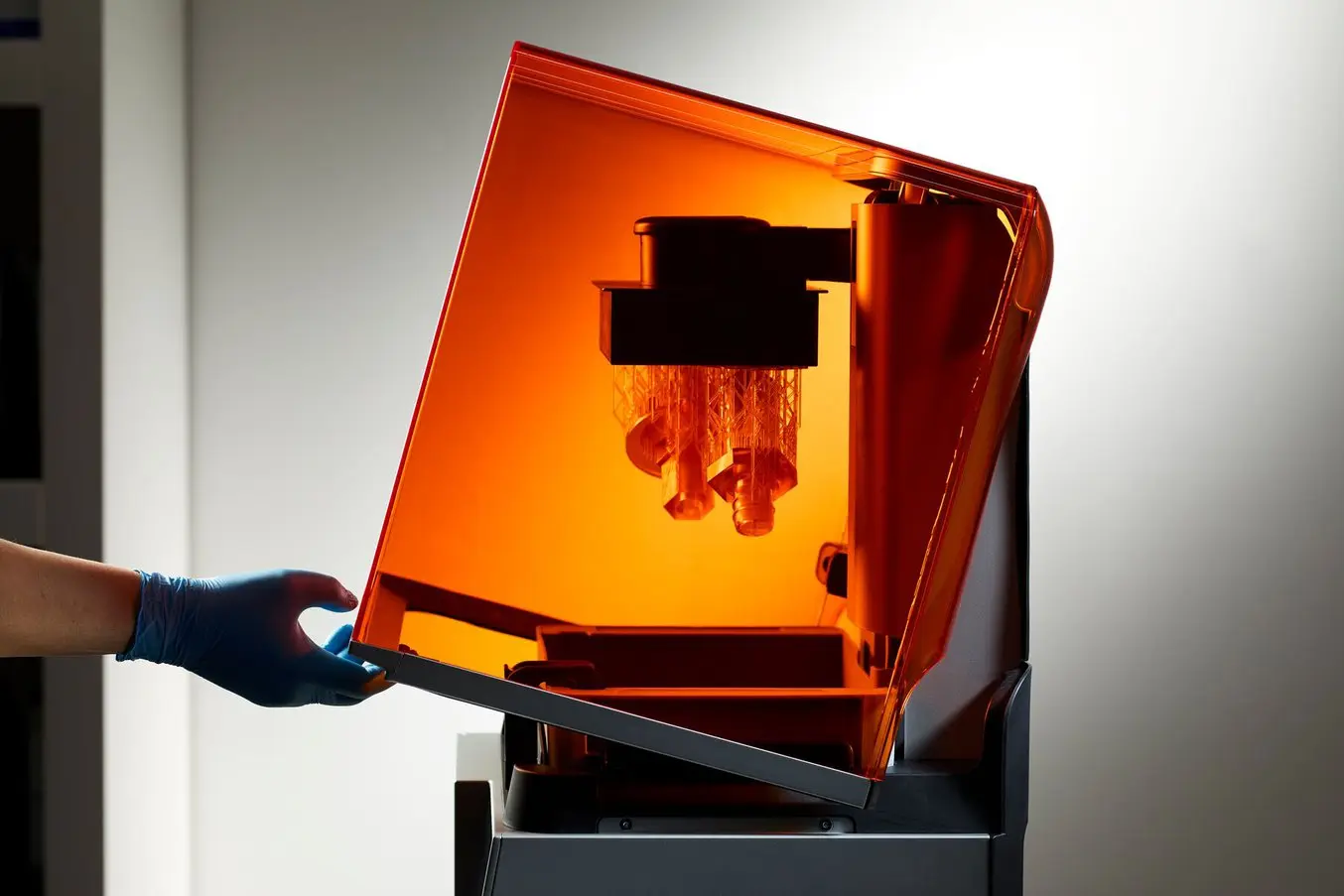
Stereolithography (SLA) 3D printing is the most common resin 3D printing process and has become vastly popular for its ability to produce high-accuracy, isotropic, and watertight prototypes and end-use parts. SLA 3D printers produce parts with a range of advanced material properties, superior surface finishes, and fine features.
In this comprehensive guide, learn how SLA resin 3D printers work, why thousands of professionals use this process today, and how SLA printers can benefit your work.
What Is Stereolithography (SLA) 3D Printing?
Stereolithography, also known as vat photopolymerization or resin 3D printing, is an additive manufacturing process where a light source cures liquid resin into hardened plastic.
SLA 3D printing offers the fastest speed, highest resolution and accuracy, sharpest details, and smoothest surface finishes of all 3D printing technologies. Another key benefit of resin 3D printing is the versatile range of materials available. Material manufacturers have created innovative SLA resin formulations with a wide range of optical, mechanical, and thermal properties to match those of standard, engineering, and industrial thermoplastics.
Advances in 3D printing hardware, software, and materials science have made SLA technology more affordable and accessible, enabling businesses to change the way they approach prototyping, testing, and production.
SLA 3D printed parts are being deployed in every industry as end-use products, industrial replacement parts, manufacturing aids, tooling, and more. Their smooth surface finish and tight tolerances make them ideal for use in multi-part assemblies, consumer grade products, or final design review parts.
The introduction of affordable and accessible workflows made it possible for businesses of every size to bring high-quality 3D printing in-house. The utilization of this technology has helped hundreds of thousands of professionals reduce operating costs, improve efficiency, and unlock entirely new business models.
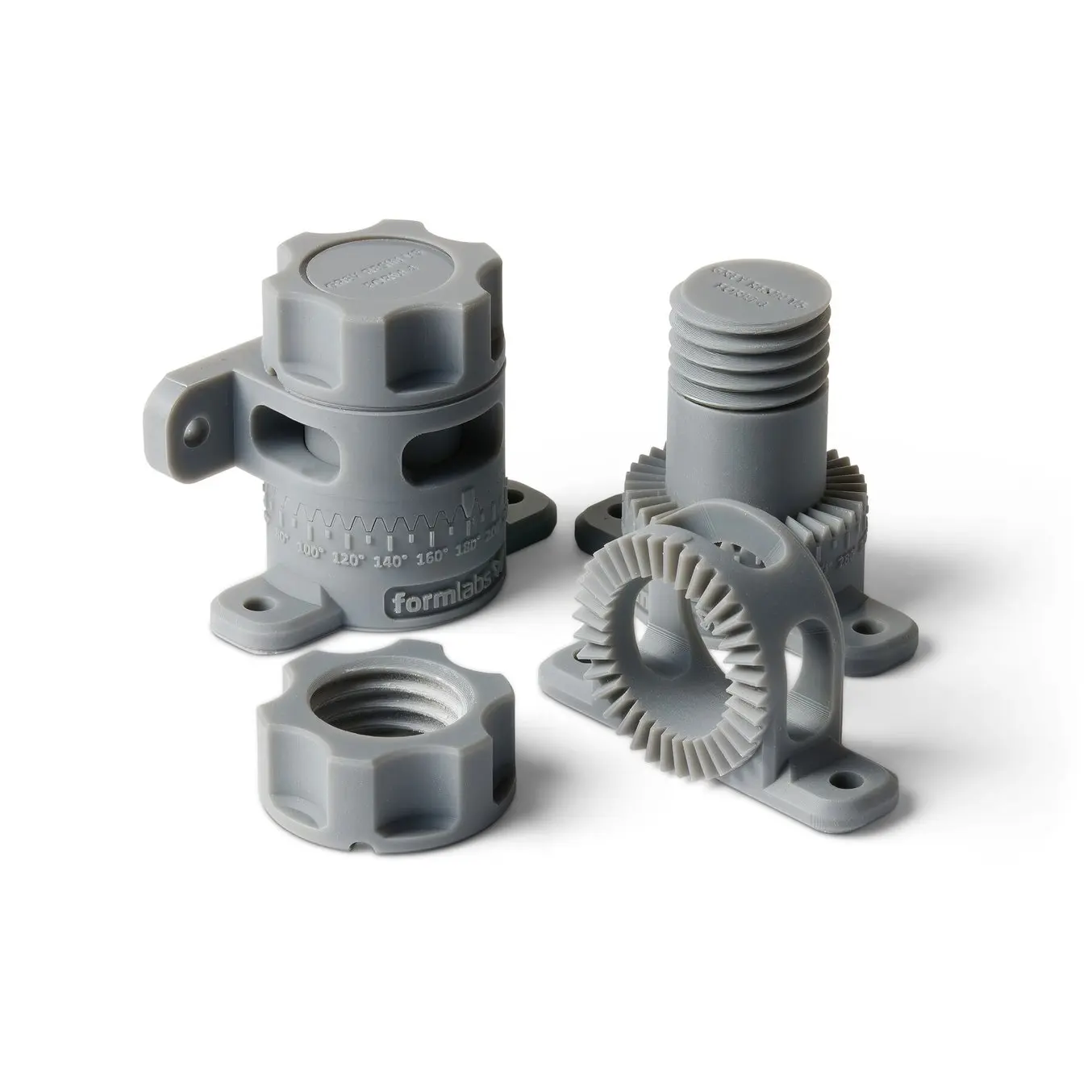
Request a Free Sample Part
See and feel Formlabs quality firsthand. We’ll ship a free 3D printed sample part to your office.
How Does SLA 3D Printing Work?
SLA 3D printing uses a light source to cure liquid resin into three-dimensional objects by exposing a vat or tank of resin to a light source, which hardens it. Traditional, top-down SLA 3D printers had that light source positioned above the vat of liquid resin. Inverted stereolithography, first introduced in 2011 by Formlabs co-founders Max Lobovsky, David Cranor, and Natan Linder, positions the light source below the vat of resin; the cross-section is traced on the bottom-most layer of resin, which is backfilled as the build platform lifts up and allows liquid resin to flow underneath the previously cured layer.
There were several important innovations that led to the invention of inverted stereolithography, including the transparent (and eventually flexible) bottomed resin tank. This new tank design enabled the creation of larger inverted SLA 3D printers because peel forces were mitigated by the flexible surface.
SLA 3D printers use light to cure light-reactive thermoset materials called “resin.” When SLA resins are exposed to certain wavelengths of light, short molecular chains join together, polymerizing monomers and oligomers into solidified rigid or flexible geometries.
In the last decade, several new types of resin 3D printing processes have been developed, primarily differentiated by the type of light source they use. These include: laser-powered stereolithography (SLA), digital light processing (DLP), or masked stereolithography (MSLA, also often used interchangeably with LCD 3D printing).
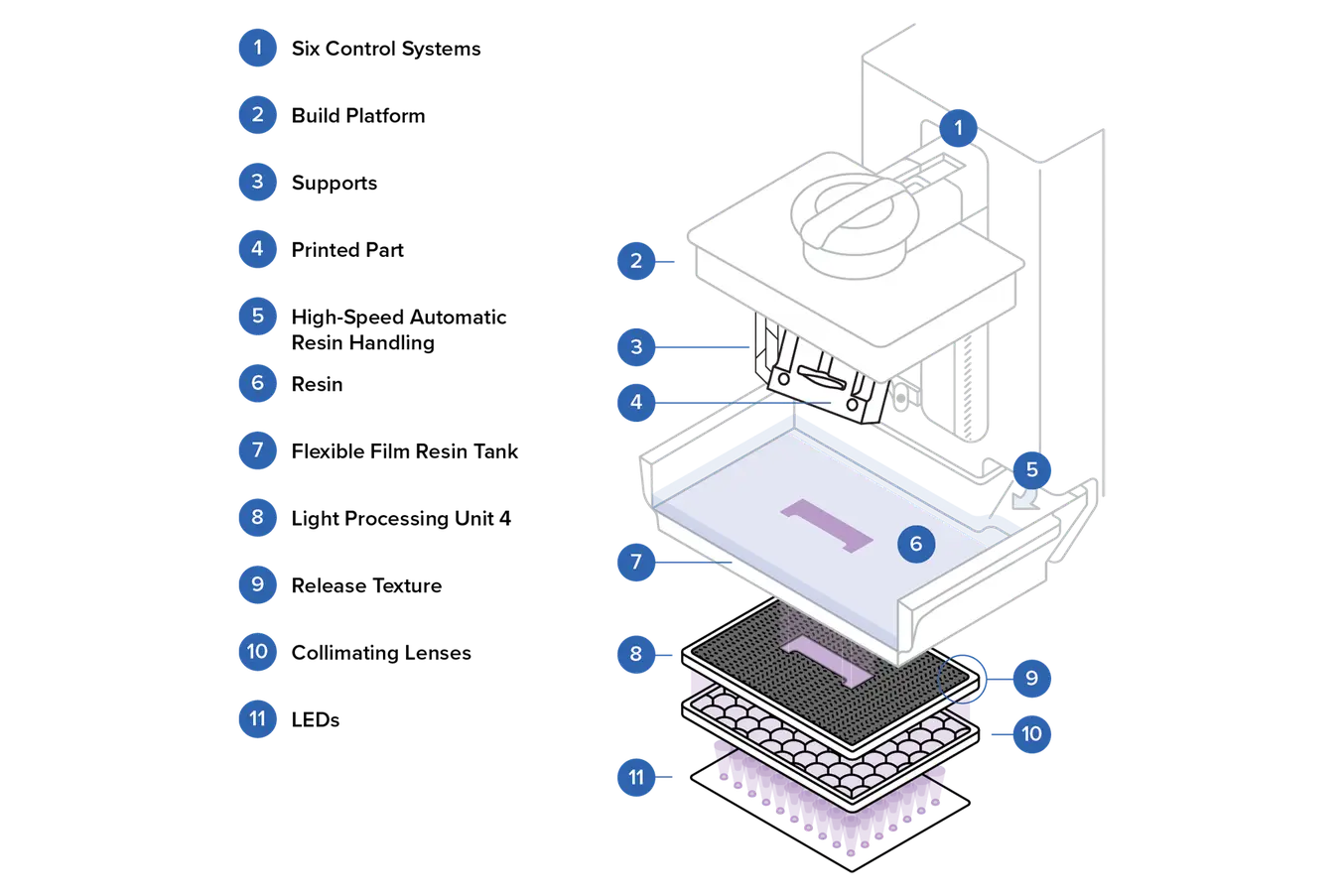
A graphic representation of Formlabs’ Low Force Display™ (LFD) print engine, an advanced form of MSLA 3D printing.
Regardless of the direction from which the light source shines or the type of light source, the SLA 3D printing workflow is straightforward. When the part has finished printing, there is a necessary alcohol or ether wash step to remove excess liquid resin from the surface of the part. Then, depending on the material, a post-cure step may be necessary to complete the polymerization of the part, helping it reach its optimal material properties. Further post-processing methods like coloring, coating, or plating may be used for specific applications or aesthetics.
A Brief History of Stereolithography
The SLA 3D printing process first appeared in the early 1980s, when Japanese researcher Dr. Hideo Kodama invented the modern layered approach to stereolithography, using ultraviolet light to cure photosensitive polymers. The term stereolithography was coined by Charles (Chuck) W. Hull, who patented the technology in 1986 and founded 3D Systems to commercialize it. Hull described the method as creating 3D objects by successively “printing” thin layers of material curable by ultraviolet light. These first SLA 3D printers were large, industrial systems, often priced above $100,000, that required complex infrastructure and maintenance.
SLA 3D printing, however, was not the first 3D printing technology to gain widespread popularity. As patents for different types of 3D printing technologies began to expire at the end of the 2000s, the introduction of small-format fused deposition modeling (FDM) 3D printers widened access to additive manufacturing. While this affordable extrusion-based technology sparked the first wave of wide adoption and awareness of 3D printing, FDM 3D printers did not satisfy the spectrum of professional needs.
Desktop SLA 3D Printers Disrupt the Market
Small-format desktop SLA printers brought the promise of high-resolution 3D printing — previously limited to monolithic industrial systems — to those looking for a much smaller and more affordable setup. Form 1, the first inverted stereolithography solution available, made it possible for customers of all backgrounds and budgets to use this advanced technology.
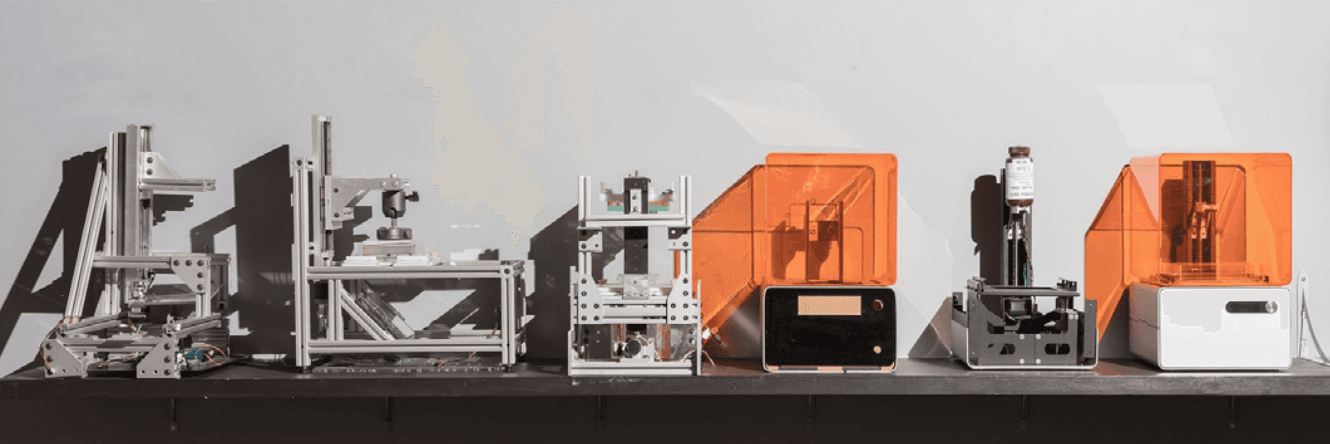
Prototypes of the Form 1, the first desktop SLA 3D printer.
Formlabs released Form 2 in 2015 and, with the subsequent release of a wider range of materials, SLA 3D printing became much more accessible for professionals in a range of different environments. In 2019, Formlabs introduced Low Force Stereolithography™ (LFS) with the Form 3 and Form 3L SLA 3D printers, which use flexible-bottomed resin tanks to drastically reduce the forces exerted on parts when peeling the cured part away from the bottom of the tank.
These capabilities expanded access to 3D printing for a variety of custom and high-precision applications across disciplines including engineering, product design, and manufacturing, as well as dental, jewelry, and other industries.
As applications grew, the technology became more popular and widely accepted. Today, stereolithography is one of the three most established plastic 3D printing processes, the other two being fused deposition modeling (FDM) and selective laser sintering (SLS). Successive iterations have made the Form Series the world’s leading professional resin 3D printers with 140,000 units sold and over 400 million parts printed as of 2024.
The Next Chapter: LFD Print Engine
In 2024, Formlabs took powerful, accessible resin 3D printing a step further, releasing desktop-sized Form 4 and its biocompatible version, Form 4B, as well as Form 4L and Form 4BL large-format resin 3D printers. The newest iterations of Formlabs’ Form Series resin 3D printers are powered by a next-generation MSLA print engine, called Low Force Display™ (LFD).
The accessibility and affordability of high-powered desktop and benchtop units have made new modes of production possible. Companies can scale 3D printing output incrementally, bring their supply chain in-house, and increase flexibility and adaptability in the face of uncertain market conditions. By adding new materials, companies can unlock new applications.
At the core of the LFD Print Engine is the Backlight Unit. The ultra-high power light source uses LEDs and collimating lenses to emit a uniform area projection of light. The light passes through the lens array, making it more collimated (parallel) and uniform, eliminating dark or bright spots.
From here, the light passes through the Light Processing Unit (LPU) 4, where filters and masks form the light into the shape of the printed layer. Once the light reaches the liquid resin inside the tank, the full area turns into a solid layer. The Build Platform then rises out of the resin and a precision Z-axis peels away the layer from the bottom of the resin tank.
In the past, peel forces have been a major hurdle for resin 3D printing, forcing users to sacrifice either part quality, reliability, or printing speed when selecting a printer. With Form 4 and Form 4L, peel forces are minimized using a redesigned Flexible Film Resin Tank and a new Release Texture, a proprietary, microtextured optical film that introduces airflow to prevent the resin tank from suctioning to the LPU.
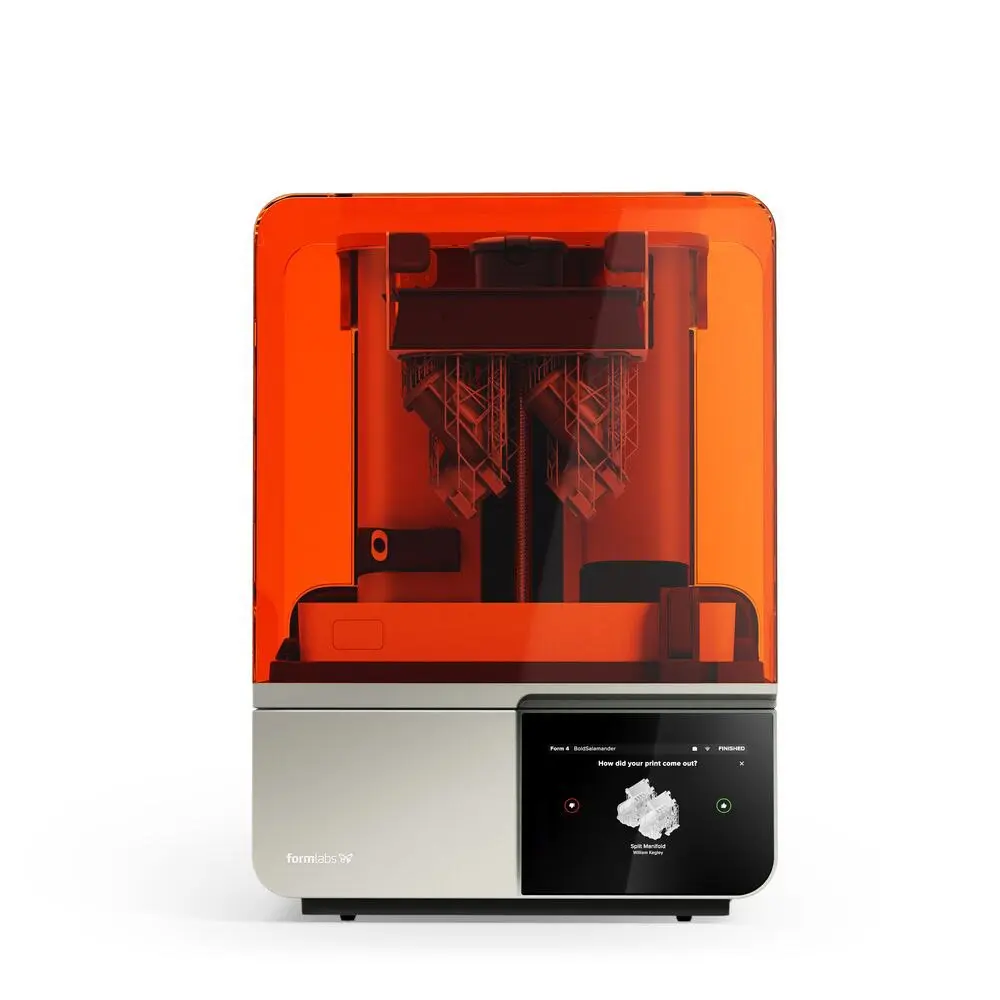
Product Demo: Form 4
See how Form 4 can enable new levels of productivity and innovation through its unmatched speed, accuracy, and reliability.
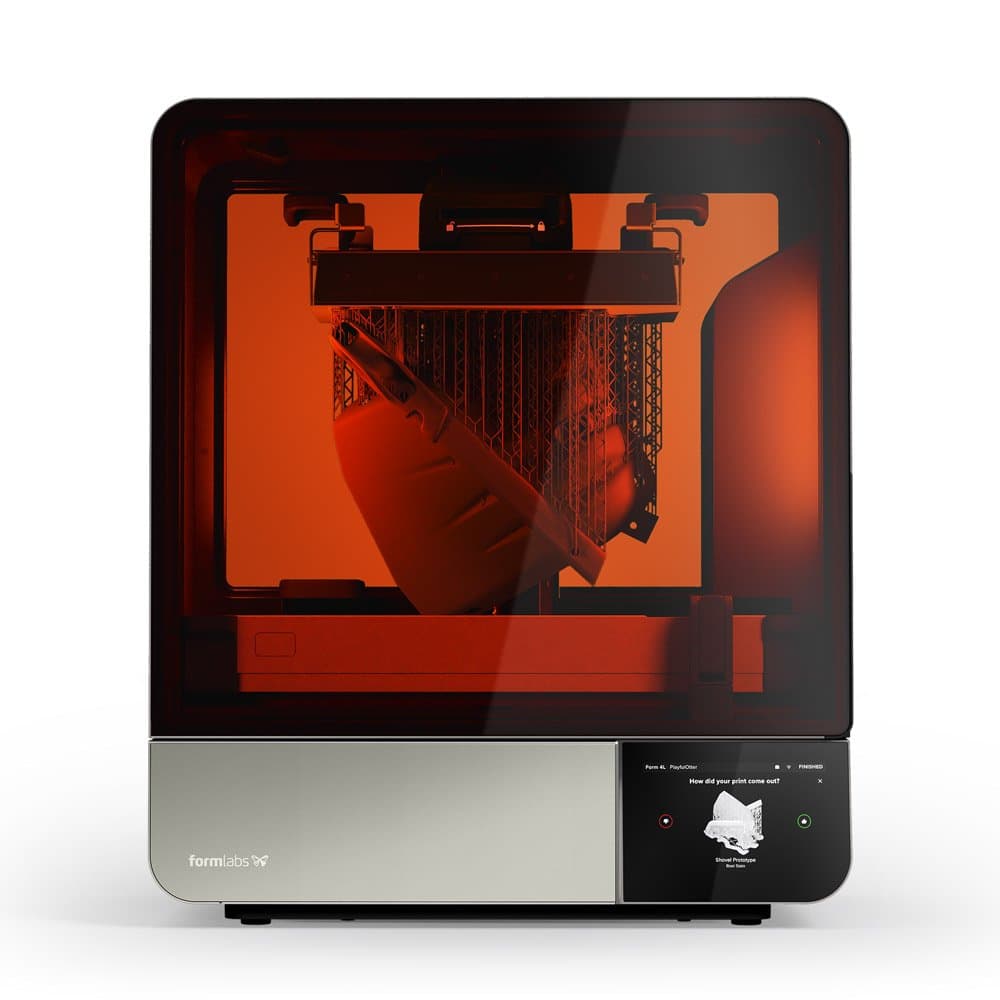
Product Demo: Form 4L
See how Form 4L, our next-generation large-format resin 3D printer, takes the speed, accuracy, and reliability of Form 4 to a completely new scale.
SLA 3D Printing Workflow
1. Design
Use any CAD software or 3D scan data to design your model, and export it in a 3D printable file format (STL or OBJ). Then, import the digital design into print preparation software to specify printing settings and slice the digital model into layers for printing. Formlabs’ print preparation software, PreForm, is free to download and can create automated supports and print orientations.
More advanced users may consider specifically designing for SLA, or taking steps like hollowing parts to conserve material.
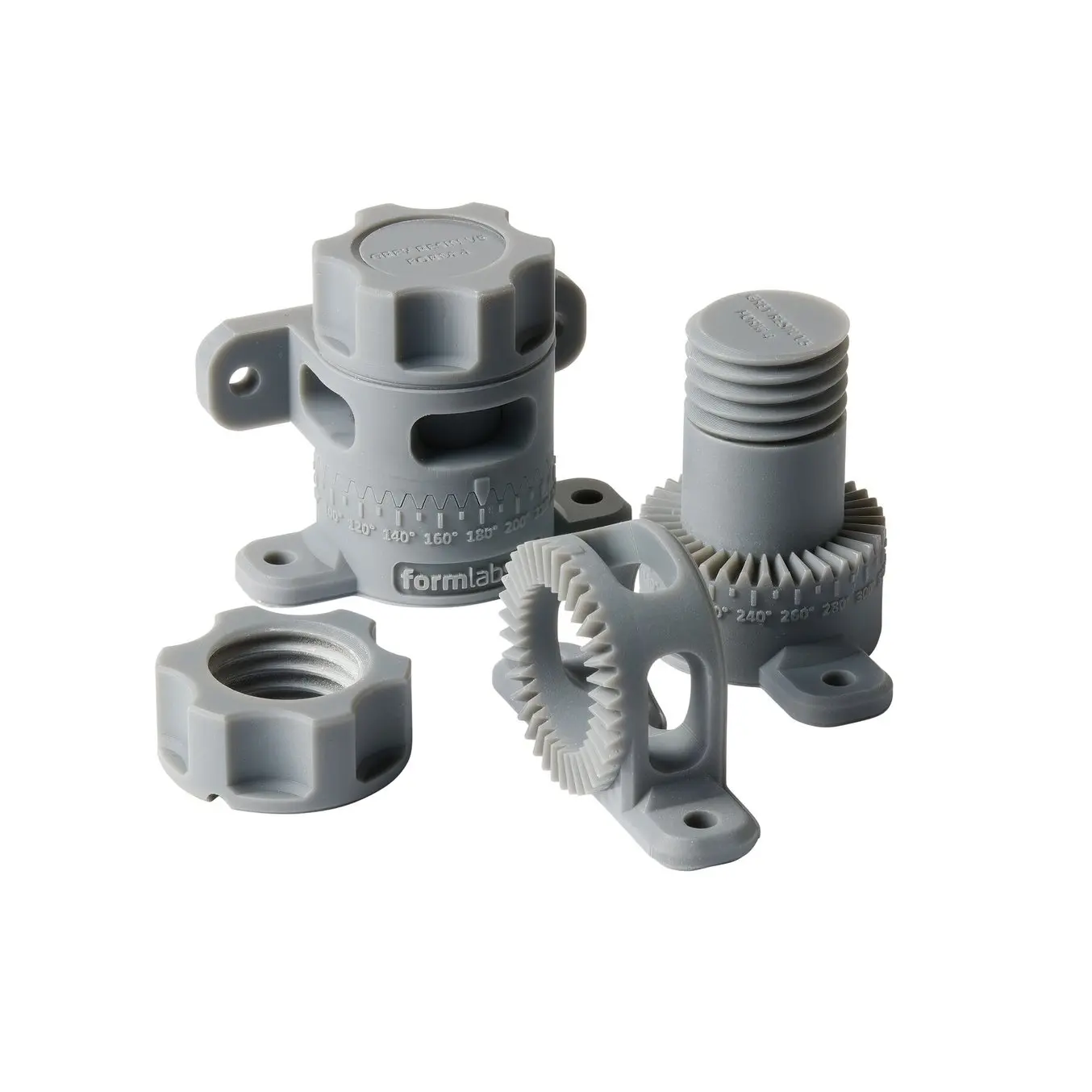
Form 4 Series Design Guide
A successful 3D print starts with a well-designed model. Follow our best practices to optimize designs and reduce failures.
2. Print
The print preparation software will send the part to the printer, typically over a wireless internet connection, USB, or ethernet.
Inverted SLA printers use removable tanks and build platforms that make it easy to change materials and start a new print. More advanced SLA printers like Formlabs’ Form Series printers also use a cartridge system that automatically refills the material during printing. This means that after a quick confirmation of the correct setup, the printing process begins and the machine can run unattended until the print is complete.
For Formlabs SLA 3D printers, an online Dashboard also allows you to remotely manage printers, materials, and teams.
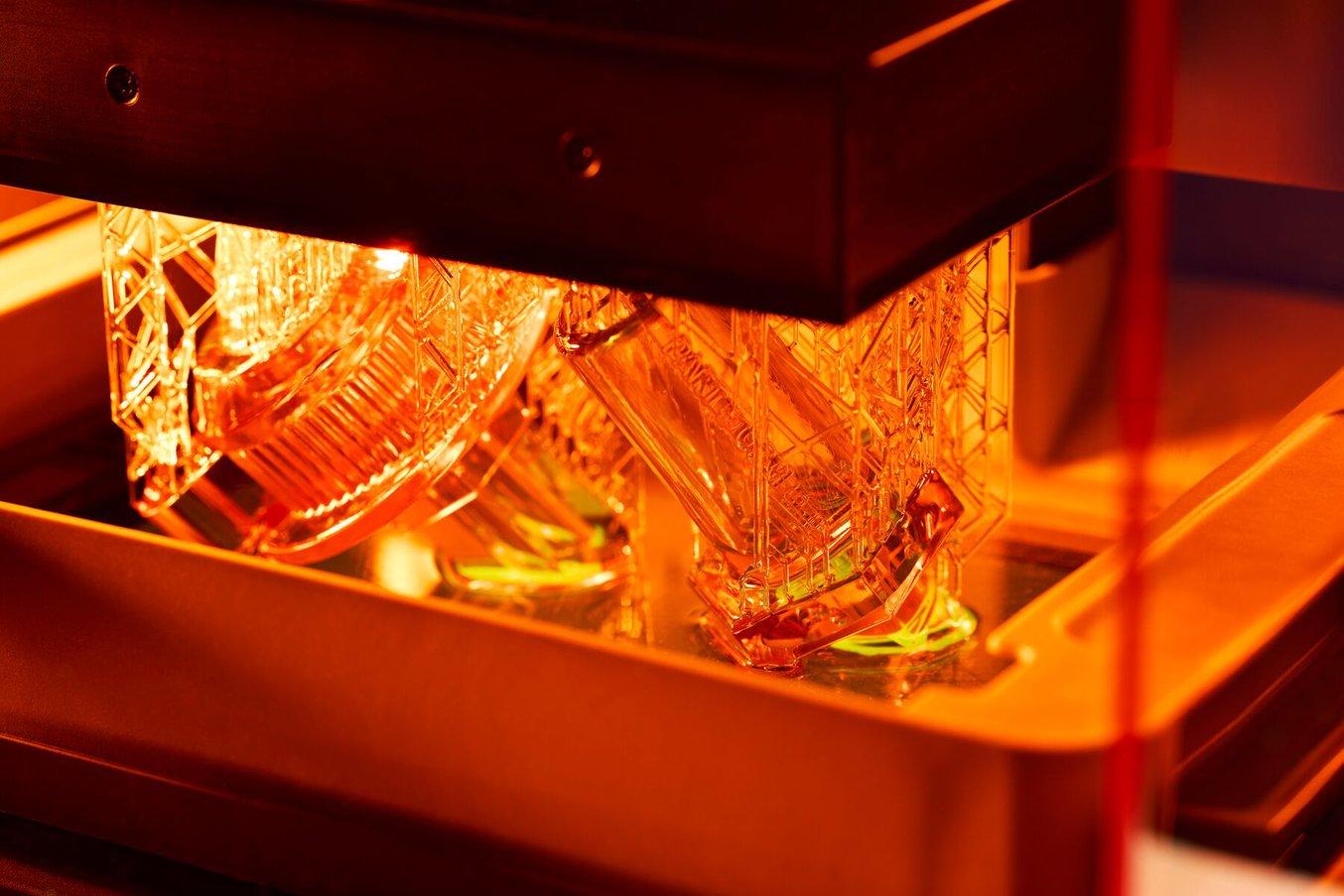
3. Post-Process
To remove parts from the build platform, different SLA 3D printers have various methods; most are manual and require scraping parts off. Formlabs’ Build Platform Flex and Build Platform Flex L enable the quick and easy removal of parts from the build platform while cutting down on hands-on labor and improving the quality of your parts by avoiding any chips or scratches.
After removing parts from the build platform, parts require rinsing in isopropyl alcohol (IPA) or ether wash to remove any uncured resin from their surface. Formlabs’ Form Wash and large-format Form Wash L have been engineered to streamline the wash process, easily removing excess resin and shortening overall post-processing time.
After rinsed parts are dry, some materials require post-curing, a process that helps improve parts' strength and performance, and reach their optimal material properties. Formlabs’ Form Cure and large-format Form Cure L precisely control temperature and light to provide a consistent, high-intensity cure.
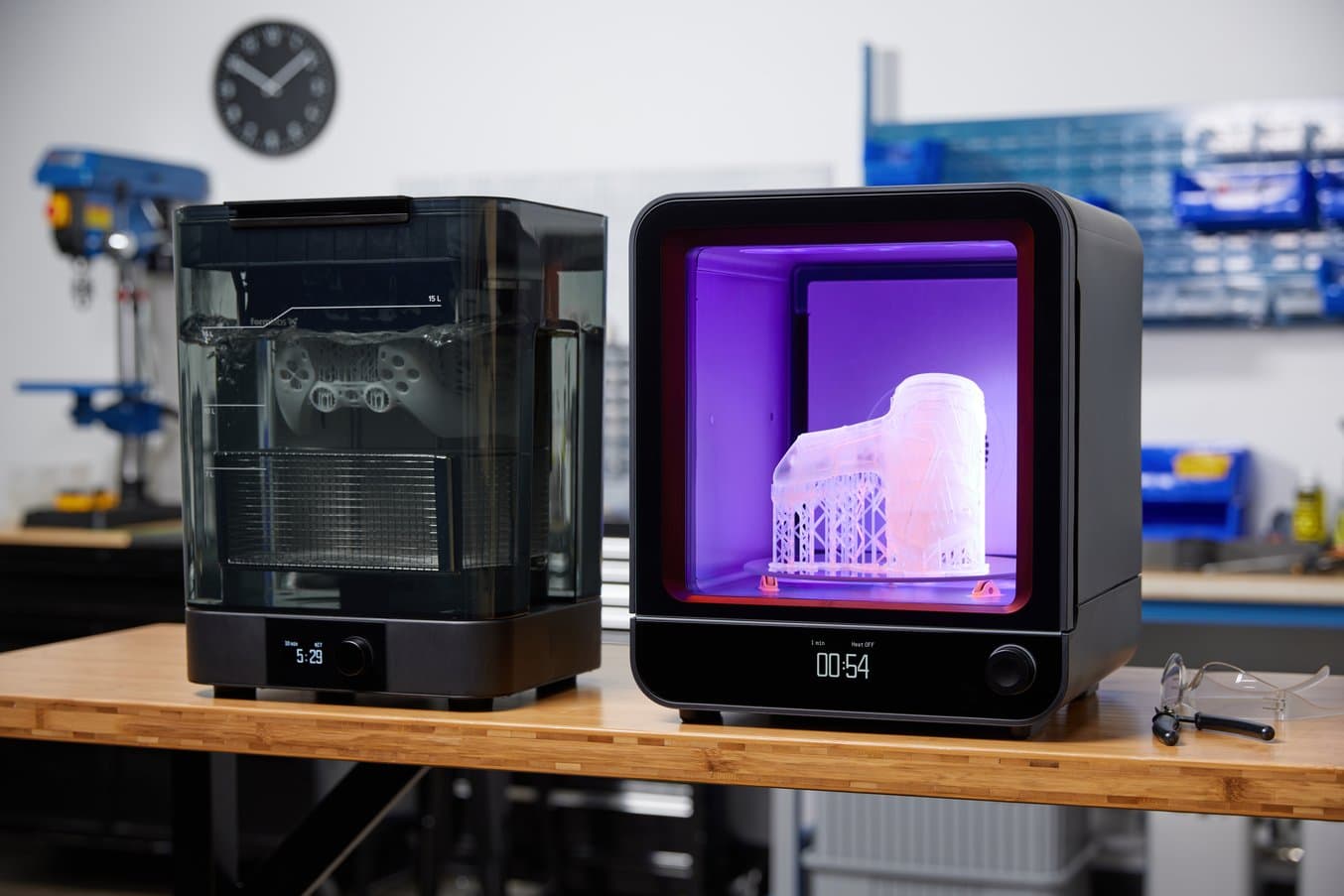
Form Wash (left) cleans resin 3D printed parts automatically and thoroughly thanks to its improved agitation. Form Cure (right) can post-cure resin 3D printed parts with unprecedented speed and consistency in as little as 60 seconds.
Finally, remove supports from the parts and sand the remaining support marks for a clean finish. SLA parts can be easily machined, primed, painted, and assembled for specific applications or finishes.
Some parts could also benefit from further steps like sanding, coating, plating, or media blasting. These advanced resin 3D print post-processing methods can achieve a wide range of results, such as making parts better suited for outdoor applications through UV protection, or increasing the mechanical strength of a part by electroplating it in metal or a ceramic coating solution like Cerakote.
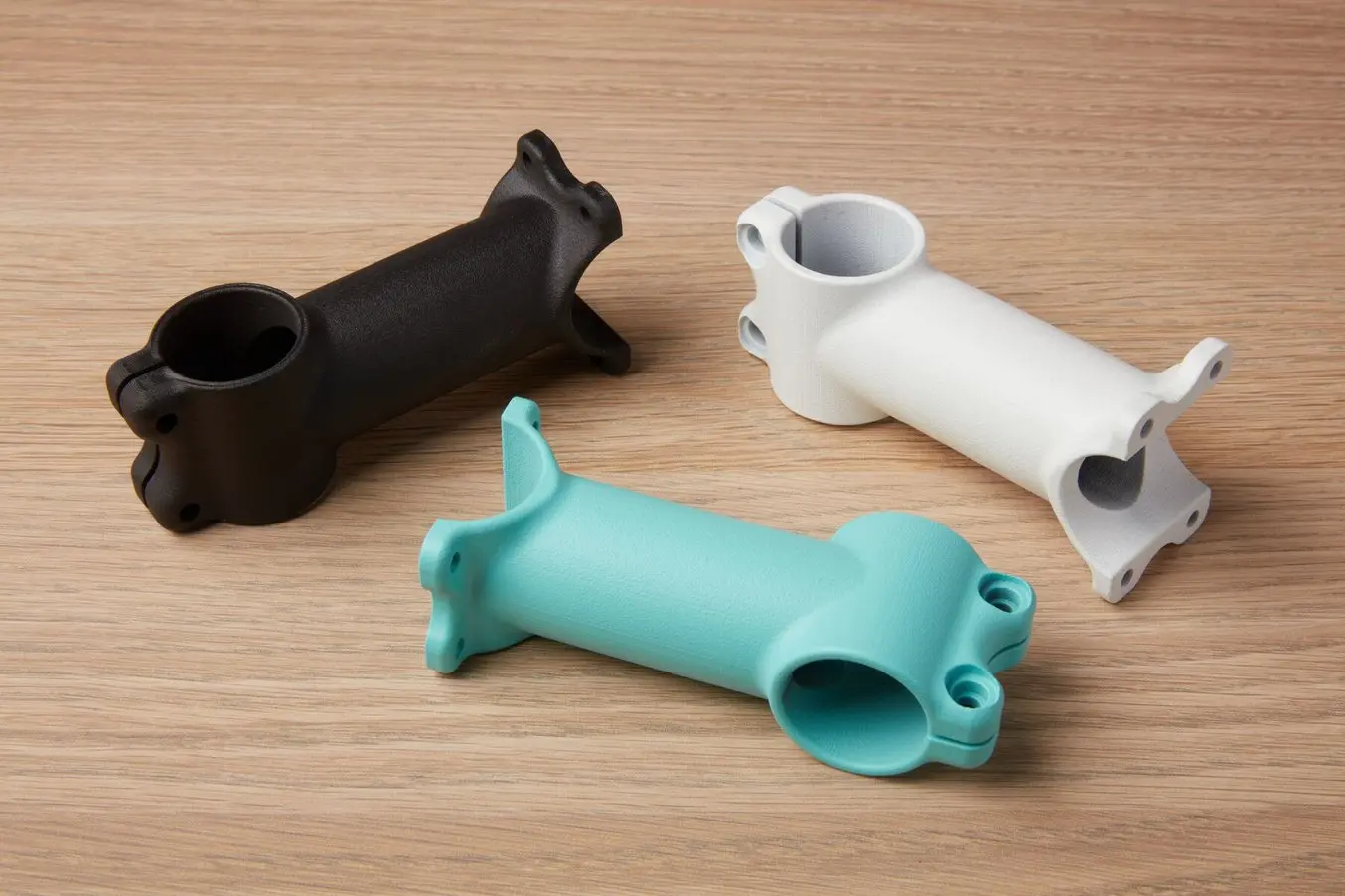
Coatings like Cerakote can reinforce SLA 3D printed parts and make them stronger, more durable, and more aesthetically pleasing.
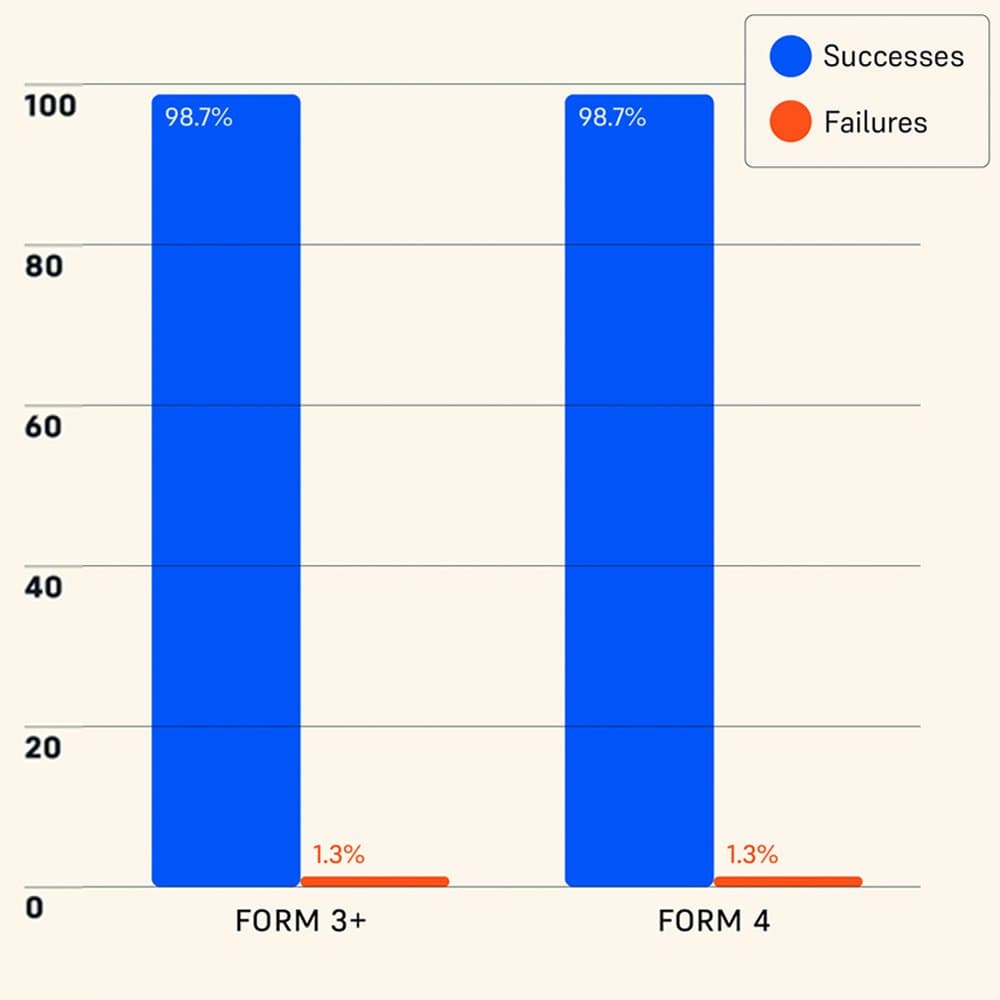
Independently Tested Reliability of Form 4 and Other Resin 3D Printers
Formlabs Form 4 was measured to have a 98.7% print success rate by an independent global leader in product testing. Read a complete description of the test methodology and see the results in our white paper.
Why Choose SLA 3D Printing?
Professionals choose SLA 3D printing for its ability to quickly produce parts with fine features, smooth surface finishes, excellent precision, high accuracy, superior mechanical attributes, isotropy, watertightness, and material versatility.
Speed and Throughput
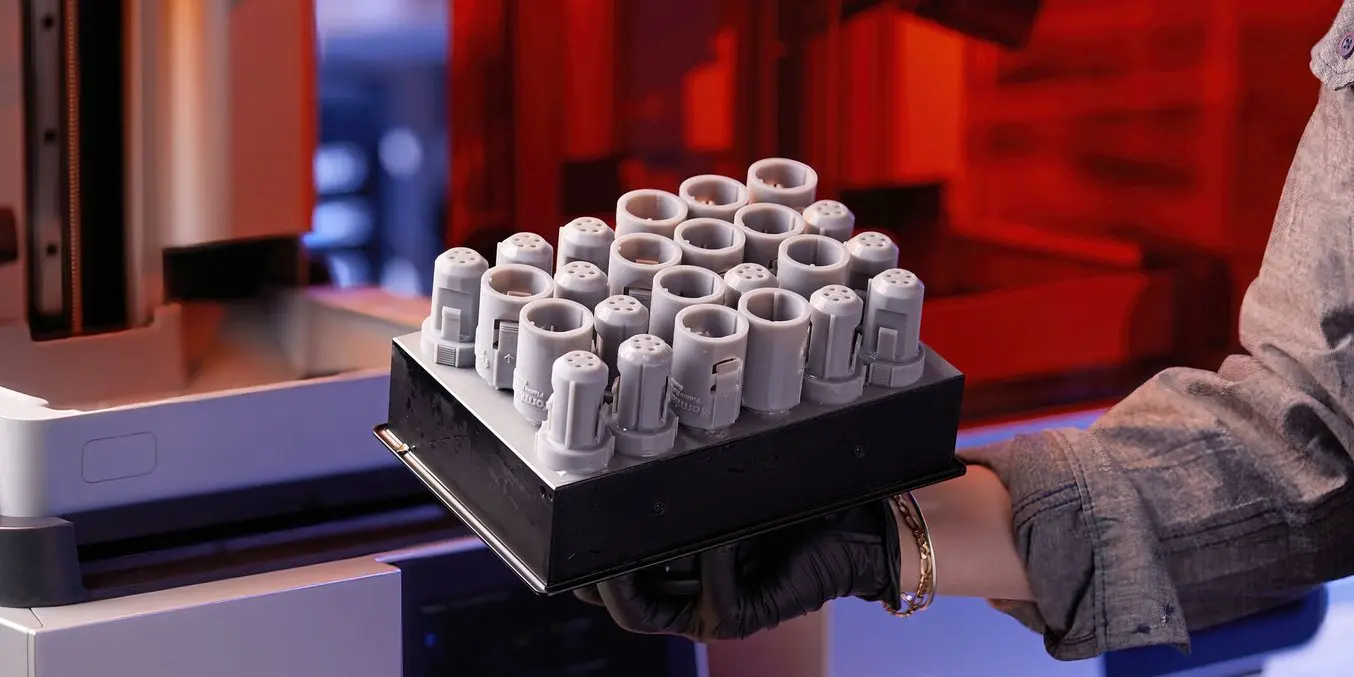
Print Speed Comparison: Electrical Connector
FDM 3D Printing | SLA 3D Printing | SLS 3D Printing | |
---|---|---|---|
1 assembly (2 parts) | 2 h 38 min | 1 h 3 min | 3 h 30 min printing (6 h 27 min cooling) |
50 assemblies (100 parts) | 84 h | 13 h 2 min | 12 h 59 min printing (13 h 49 min cooling) |
Compared printers and printing parameters:
- FDM 3D printer: Bambu Lab X1, PLA Basic, 120 microns layer height, 15% infill density
- SLA 3D printer: Form 4, Grey Resin, 100 microns layer height
- SLS 3D printer: Fuse 1+ 30W, Nylon 12 Powder, 110 microns layer height
As more businesses turn to 3D printing for production as well as rapid iteration, 3D printing speed becomes a greater consideration when choosing a technology. Though advances have been made in 3D printing speed across all technologies, SLA 3D printing has established itself as the clear frontrunner for the fastest 3D printing process available.
Some resin 3D printing processes are faster than others; laser-powered SLA generally cures each layer more slowly than DLP or MSLA (LCD) technologies that can cure an entire cross-section with one quick exposure of the light source.
Formlabs has made industry-leading print speeds a priority; Form 4 and Form 4L have been engineered to build parts as fast as 100 mm per hour using specifically designed materials like Fast Model Resin. Most Form 4 builds finish in under two hours using any material, enabling multiple design iterations per day.
Large-format SLA 3D printing enables human-scale design and engineering, and now with Form 4L, that means no more compromising on speed. Most Form 4L builds finish in under six hours. Even builds that are the full height of the printer, or higher-volume production runs with multiple pieces covering the entire build platform, can print in less than a day, making same-day iterations of large parts or production at higher volumes possible.
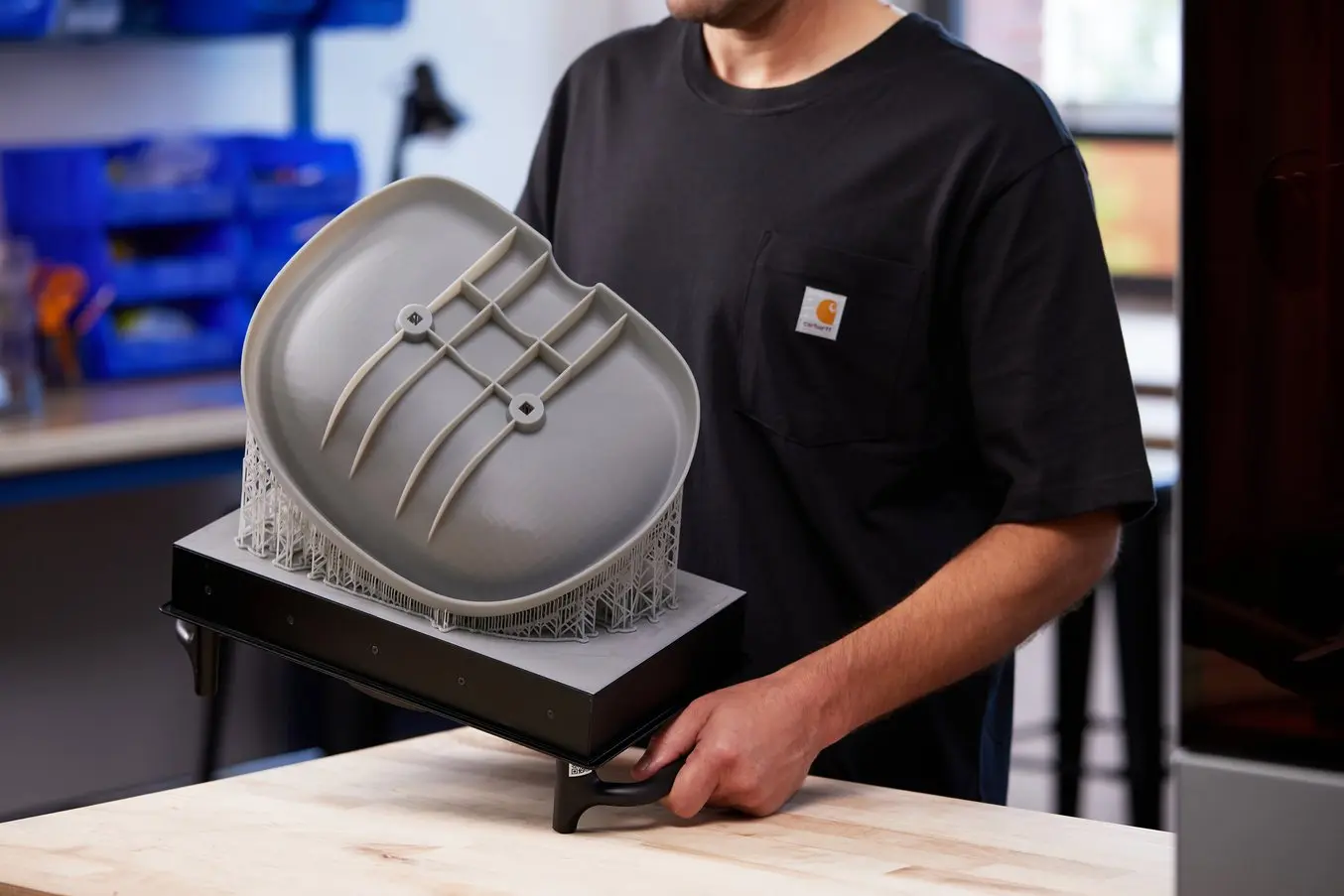
Print Speed Comparison: Radio Flyer Seat Prototype
FDM 3D Printing | SLA 3D Printing | |
---|---|---|
Print Time | 42 hr 3 min | 2 hr 37 min |
Compared printers and printing parameters:
- FDM 3D printer: Ultimaker S7, PLA, 100 microns layer height, 20% infill density
- SLA 3D printer: Form 4, Fast Model Resin, 200 microns layer height
When that speed is compounded day by day and week by week, the throughput benefits are extraordinary. Form 4 and Form 4L can now match the speed of high-throughput technologies such as injection molding. Printing full build chambers over the course of a few hours, multiple times a day, can rival the output of a medium-volume injection molding machine, without the high up-front cost of tooling.
Material Versatility
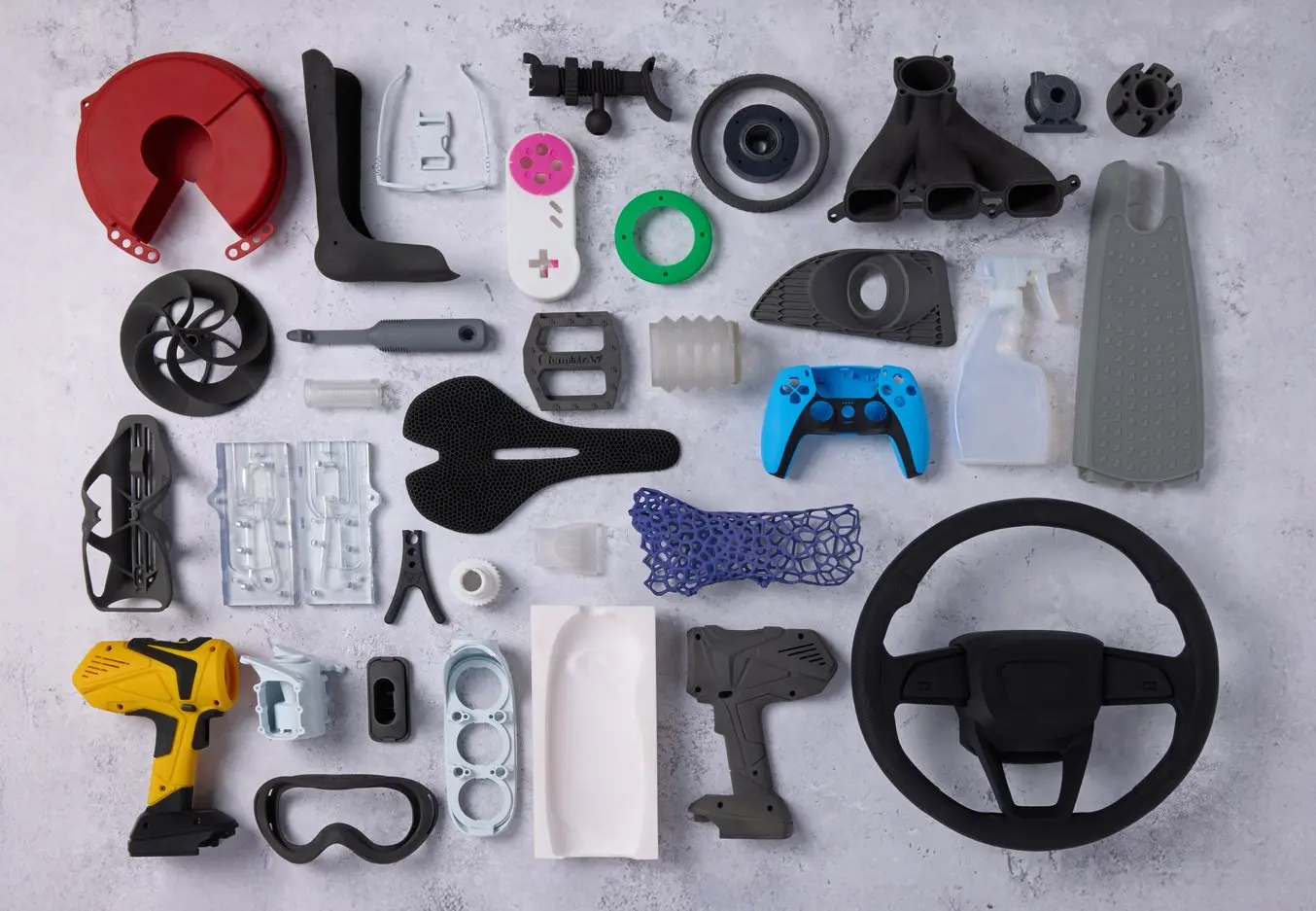
SLA offers the widest range of material options for plastic 3D printing.
SLA resins are incredibly versatile, and there are hundreds of different formulations available. They can be can be soft or hard, heavily filled with secondary materials like glass and ceramic, or imbued with mechanical properties like high heat deflection temperature or impact resistance. Materials range from industry-specific, like dentures, to those that closely match final materials for prototyping, formulated to withstand extensive testing and perform under stress.
Many manufacturers of SLA printers also formulate and manufacture their own resins for use in a closed system, though some offer an open platform for any resin to be used, and others white-label other companies’ resins.
Because these resins are formulated specifically for SLA 3D printers, they are not completely analogous to the familiar thermoplastics like nylon or ABS used in traditional plastic manufacturing methods like injection molding. Though learning which resin is best for a specific application may take testing and consideration of data sheets and application guides, there is an SLA resin for almost every application possible — the enormous variety of mechanical and aesthetic properties available make it easy to create an optimized and efficient workflow.
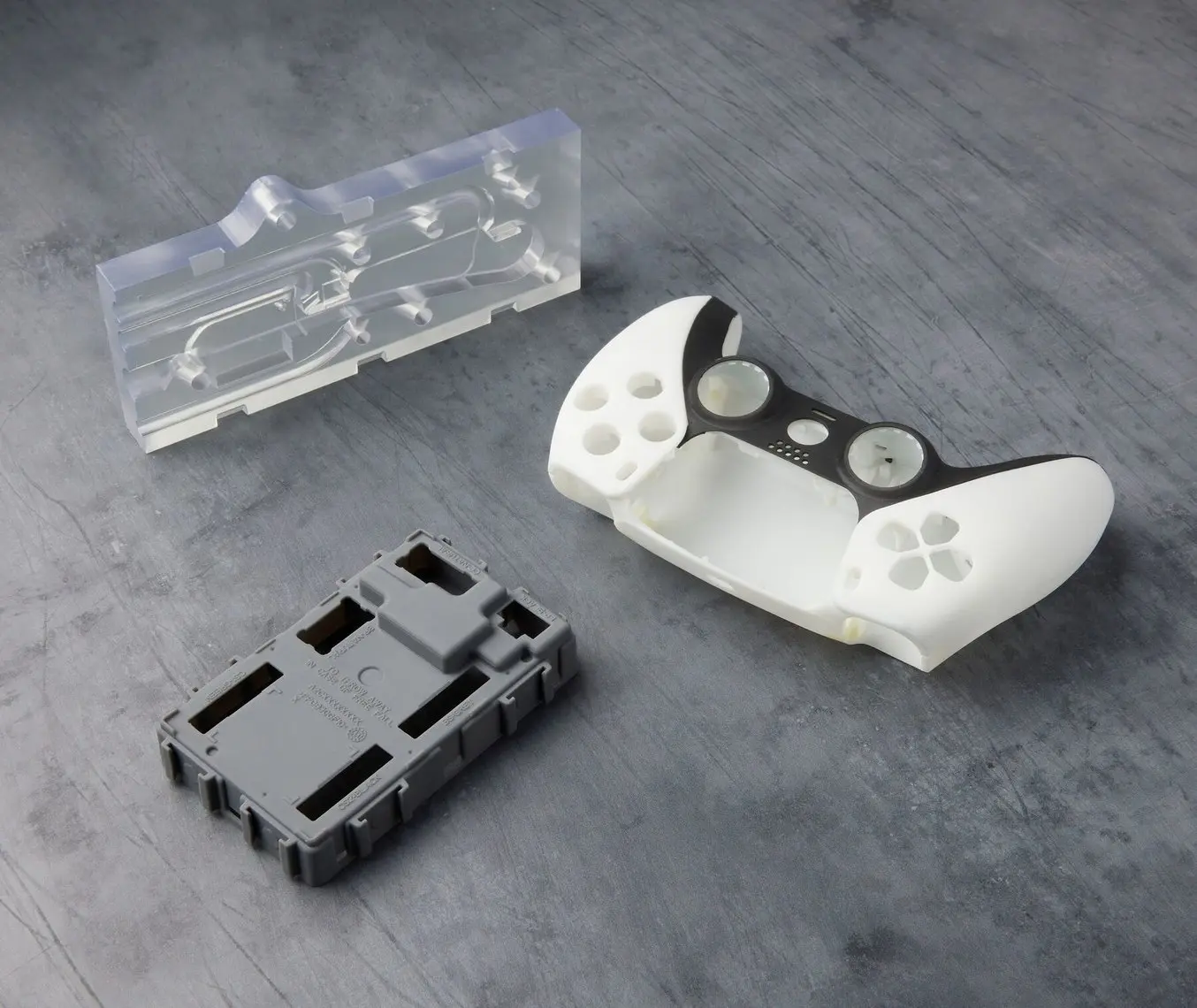
Form 4 Materials Guide
Learn more about all the high performance materials available on Form 4 and how to leverage the right material for your application.
Accuracy and Precision
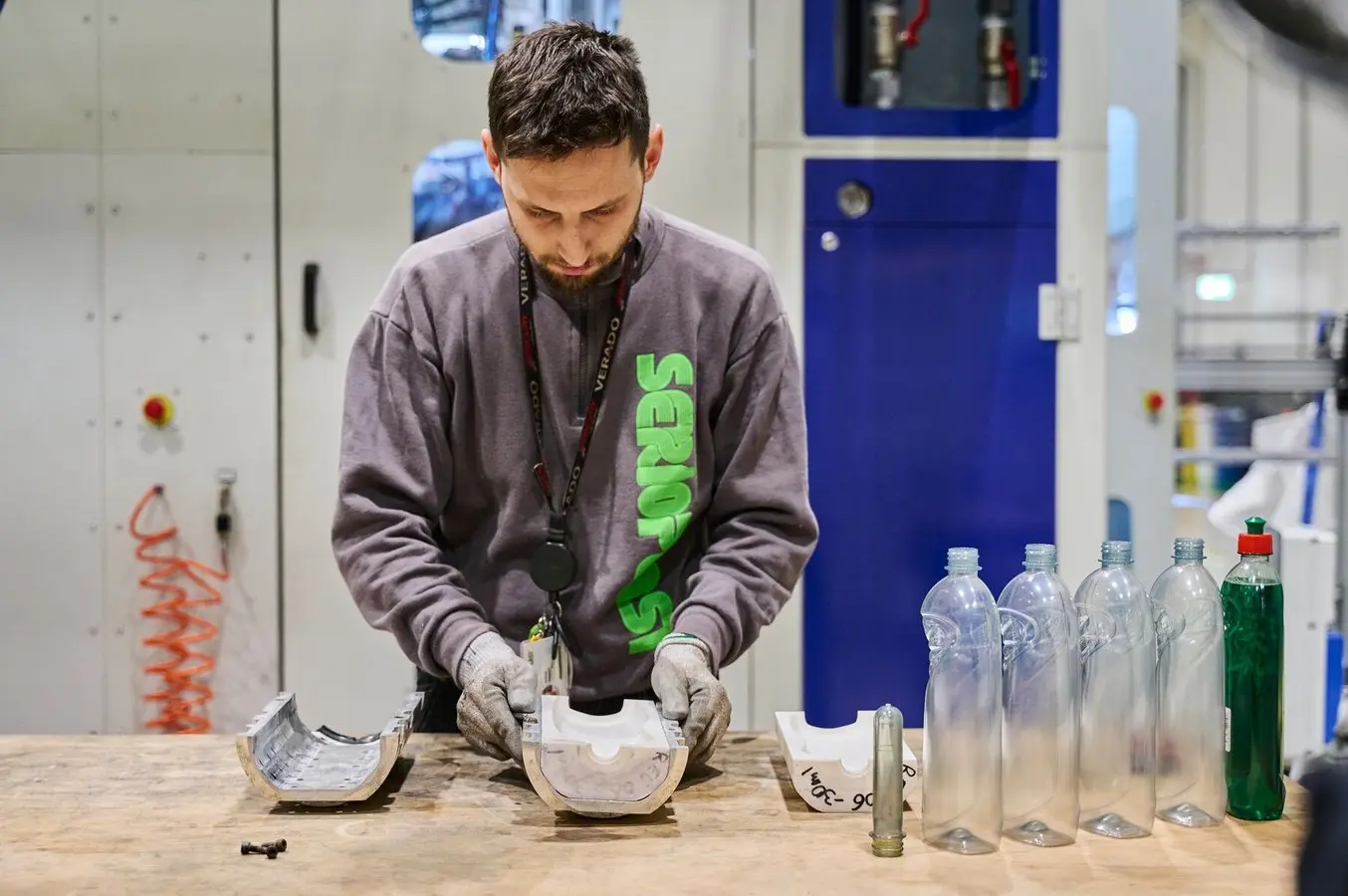
3D printed molds for stretch blow molding (SBM) produced in Rigid 10K Resin have such smooth surfaces and high dimensional accuracy that they can create bottles that are nearly indistinguishable from those made by traditional steel molds.
Accuracy and precision are paramount for all industries from manufacturing to dentistry, and SLA printing is one of most accurate 3D printing solutions on the market currently.
Accuracy refers to how closely you match the dimensions of the CAD model, and precision is defined as how repeatedly you can produce the same dimension. Compared to machined accuracy, professional SLA 3D printers are somewhere between standard machining and fine machining. However, accuracy does vary between resin 3D printer manufacturers and can be dependent on the type of light source used to cure the resin, the quality of the components, and the engineering and calibration that go into making those components function together. Accuracy is also dependent on the material — rigid materials are more accurate and easier to print with than flexible materials.
For example, Form 4/B and Form 4L/4BL can print Precision Model Resin — a high-accuracy material for creating restorative models — with >99% of the printed surface area within 100 μm of the digital model. For larger models (81-150 mm features) the XY dimensional tolerance is typically ±0.3% (lower limit: ±0.15 mm) when using Grey Resin.
The heated and enclosed build environment of Formlabs SLA 3D printers provides almost identical conditions for each print. Better accuracy is also a function of lower printing temperature compared to thermoplastic-based technologies that melt the raw material. Because stereolithography uses light instead of heat, the printing process takes place close to room temperature, and printed parts don't suffer from thermal expansion and contraction artifacts.
Form 4 and Form 4L's LFD Print Engine, especially the high-resolution liquid crystal display and collimating lenses included in the LPU 4, create hyper-accurate cross-sections of each part. The low peel forces made possible by the Release Texture and Flexible Film Resin Tank make accuracy repeatable, leading to highly precise parts.
Fine Features and Smooth Surface Finish
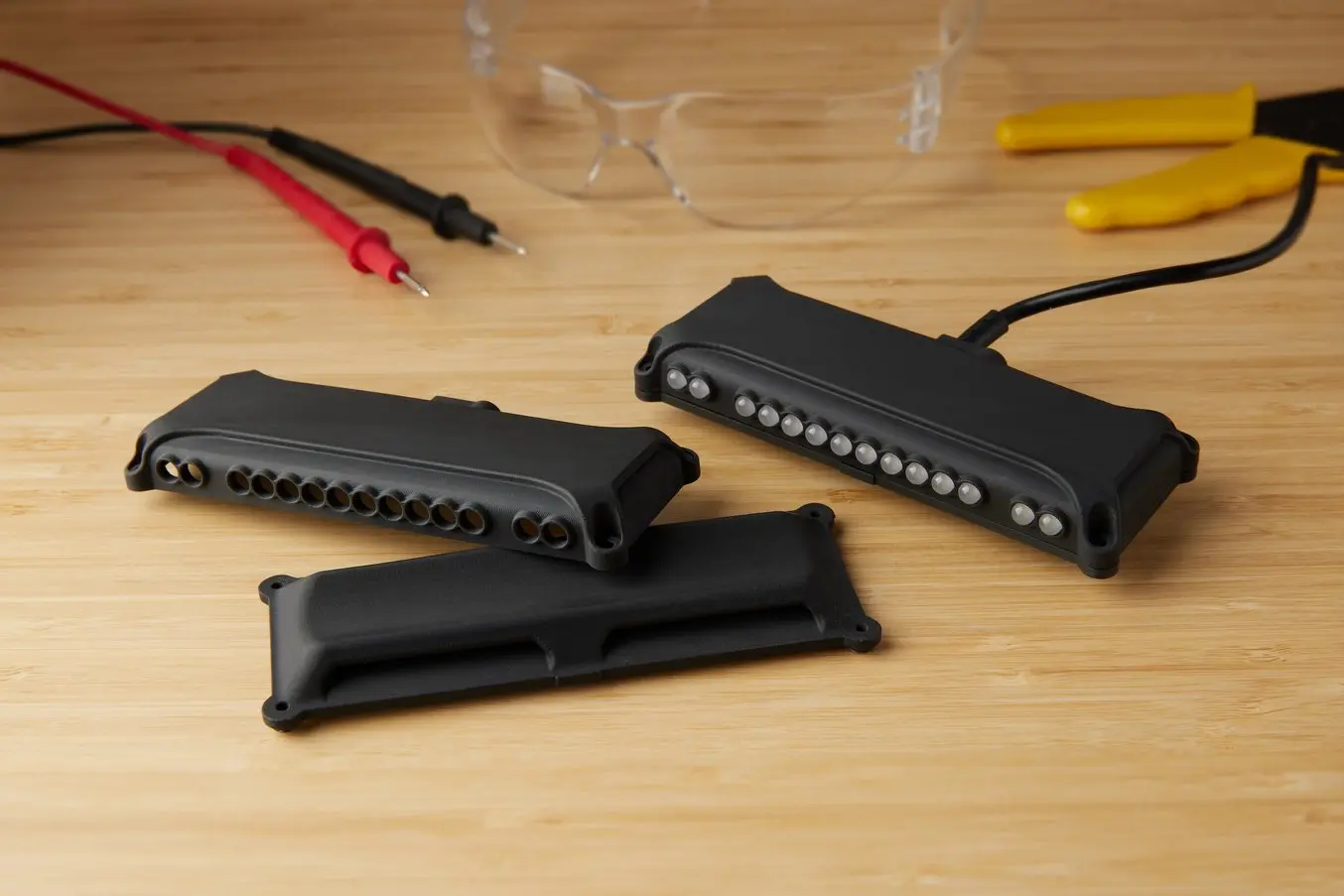
Resin 3D printers create parts with a smooth surface finish, which translates to barely any visible layer lines even on complex features, like curved edges.
SLA 3D printers are considered the gold standard for creating parts with smooth surface finishes and fine features. Resin 3D printed parts can easily have appearances comparable to traditional manufacturing methods like injection molding with barely any post-processing. Conversely, FDM 3D printed parts often have visible layer lines, and SLS 3D printed parts often exhibit a grainy, slightly rough texture on the surface.
The surface quality of SLA 3D printed parts lends itself to the creation of end-use products that look and feel like mass-produced consumer goods. It also makes secondary processes like rapid tooling possible.
SLA 3D printers also can achieve finer features and smaller minimum feature sizes than FDM 3D printers, comparable to SLS 3D printers. The light in resin 3D printers can be controlled in much more precise shapes than a filament extruder and therefore create smaller features or thinner walls. And, because SLA light sources can be lower power than the lasers required to melt powder in SLS 3D printers, they can cure with greater precision, leading to smaller features.
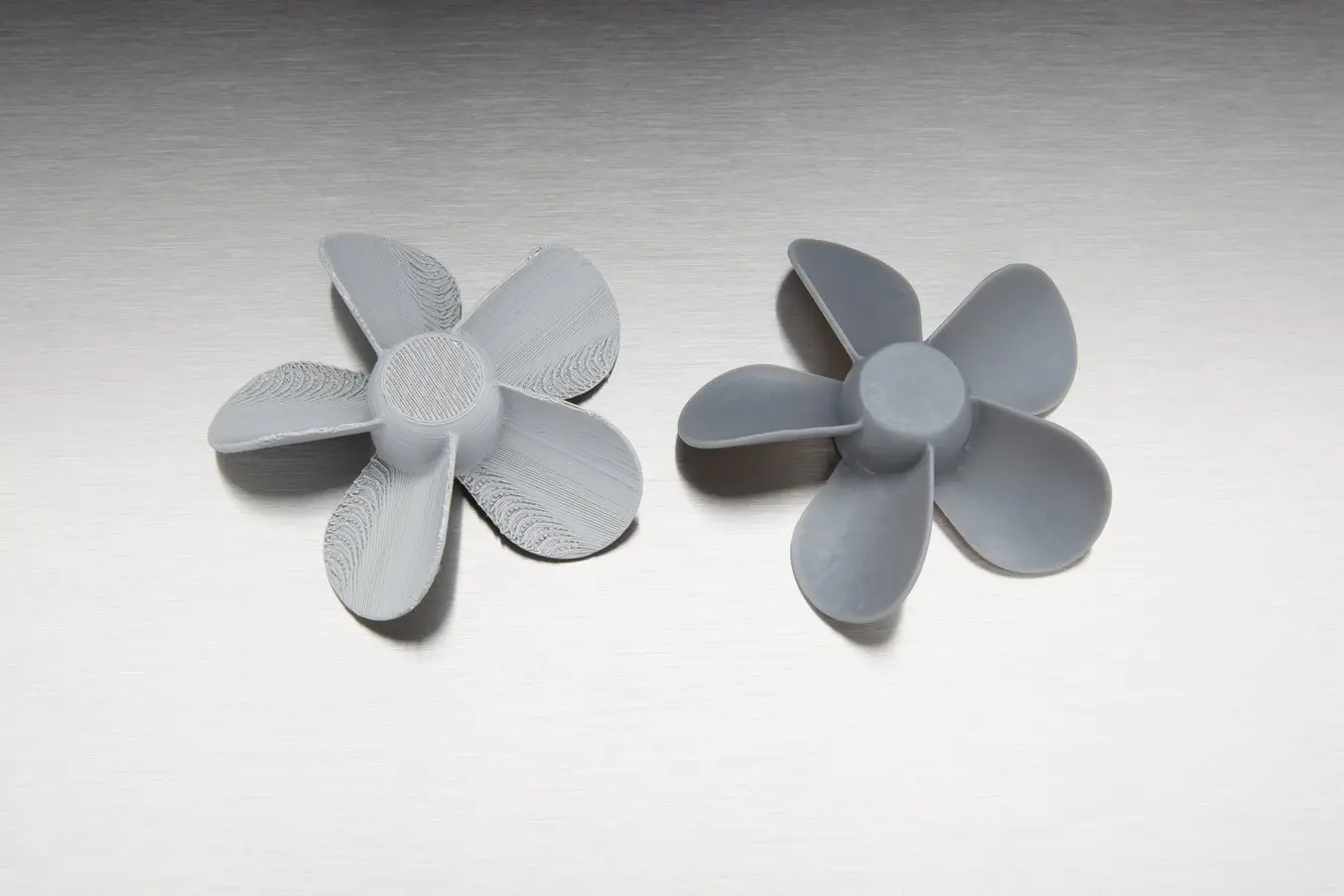
While FDM 3D printed parts tend to have visible layer lines and might show inaccuracies around complex features, parts printed on SLA machines have sharp edges, a smooth surface finish, and minimal visible layer lines.
Isotropy
Because 3D printing creates parts one layer at a time, completed prints may have variations in strength based on the orientation of the part relative to the printing process, with different properties in X, Y, and Z axes.
Extrusion-based 3D printing processes like fused deposition modeling (FDM) are known for being anisotropic due to layer-to-layer differences created by the print process. This anisotropy limits the usefulness of FDM for certain applications or requires more adjustments on the part geometry side to compensate for it.
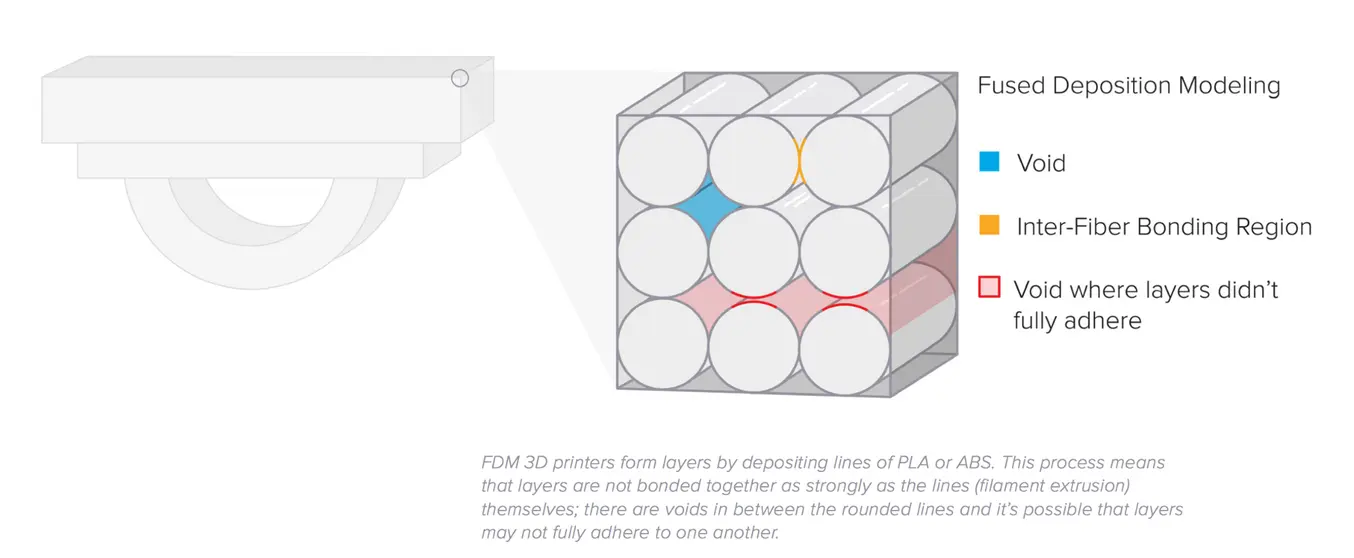
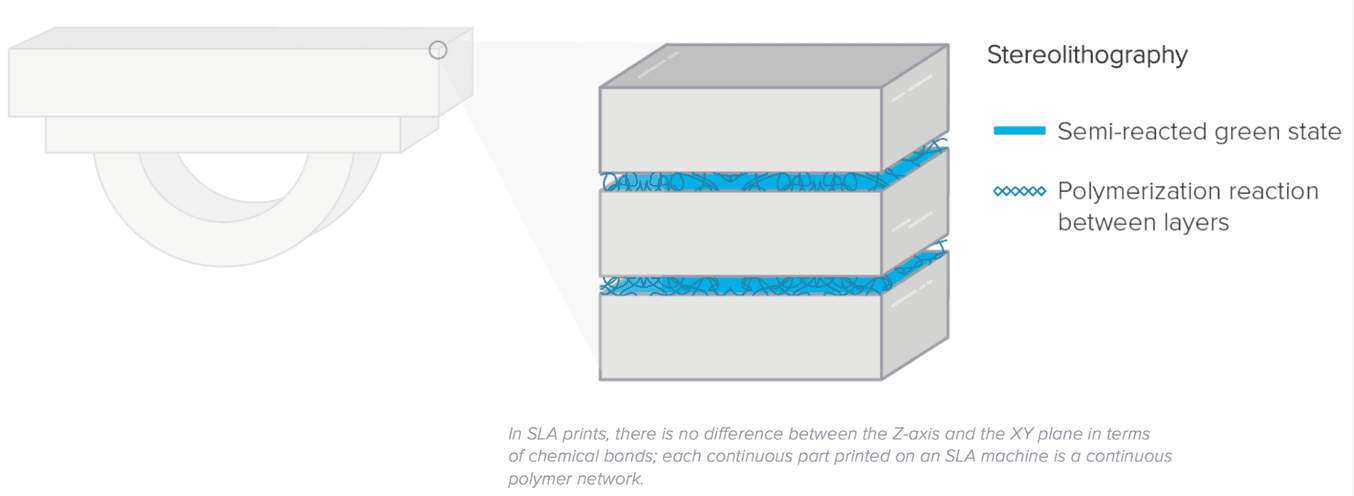
In contrast, SLA resin 3D printers create highly isotropic parts. Achieving part isotropy is based on a number of factors that can be tightly controlled by integrating material chemistry with the print process. During printing, resin components form covalent bonds, but layer to layer, the part remains in a semi-reacted “green state.”
While in the green state, the resin retains polymerizable groups that can form bonds across layers, imparting isotropy and watertightness to the part upon final cure. On the molecular level, there is no difference between X, Y, or Z planes. This results in parts with predictable mechanical performance critical for applications like jigs and fixtures, end-use parts, and functional prototyping.
Watertightness
SLA printed objects are continuous, whether producing geometries with solid features or internal channels. This watertightness is important for engineering and manufacturing applications where air or fluid flow must be controlled and predictable. Engineers and designers use the watertightness of SLA printers to solve air and fluid flow challenges for automotive uses, biomedical research, and to validate part designs for consumer products like kitchen appliances.
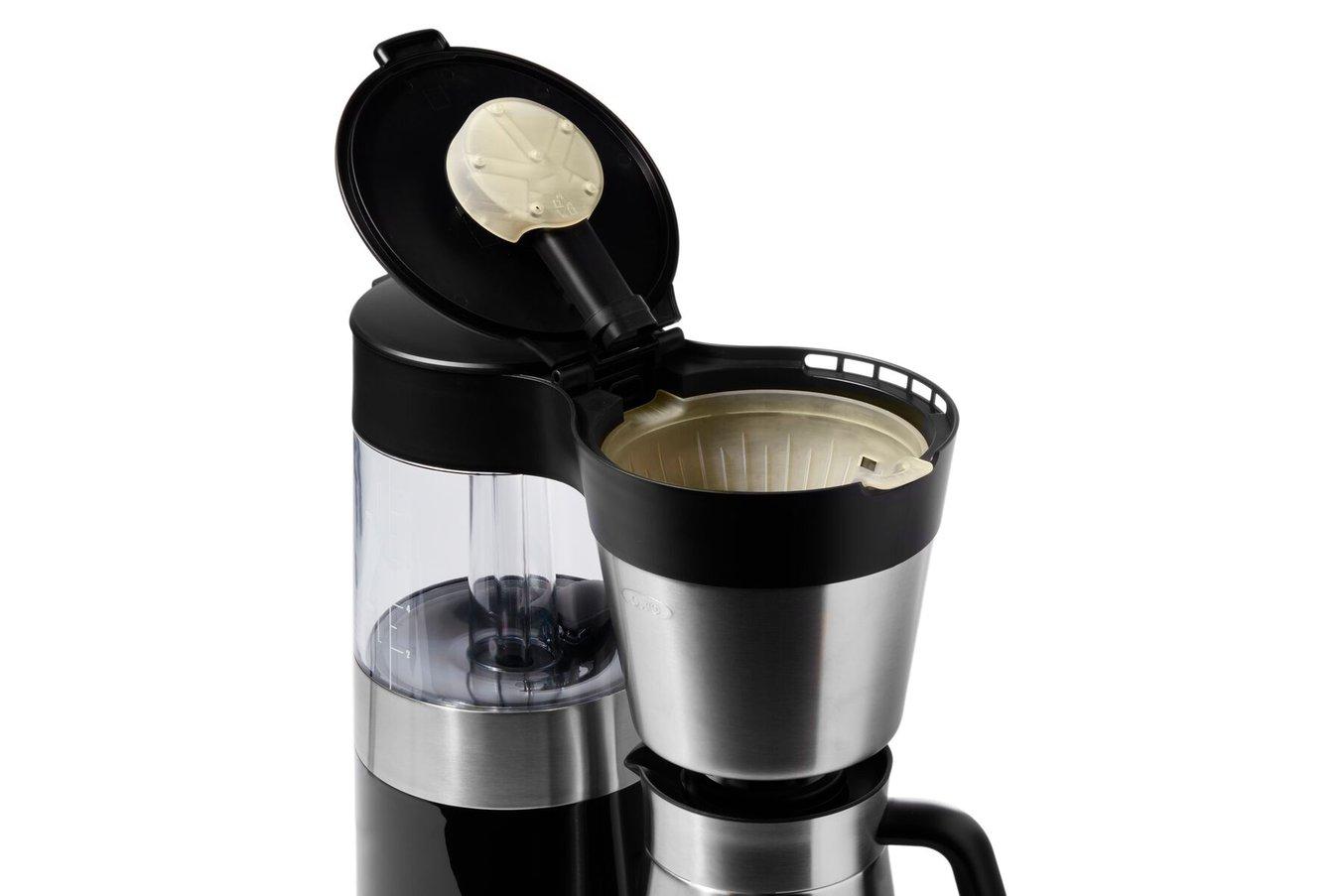
OXO relies on the watertightness of SLA 3D printing to create robust functional prototypes for products with air or fluid flow, like this coffee maker.
Custom or low-volume watertight and gas-tight parts are also sought after across several industries, such as marine research, underwater robotics, sustainable technologies engineering, oil and gas industries, and defense. Though some 3D printing technologies present an ideal solution for these parts, the common perception of additively manufactured parts is that they are porous and cannot be deployed in pressurized environments.
In recent years, however, this assumption has been thoroughly disproven. SLA printers can create watertight enclosures and completely waterproof parts. Institutions like National Oceanic and Atmospheric Administration (NOAA) and the University of Rhode Island have made incredible strides in marine research by implementing low-cost, high-quality SLA 3D printed testing and research equipment.
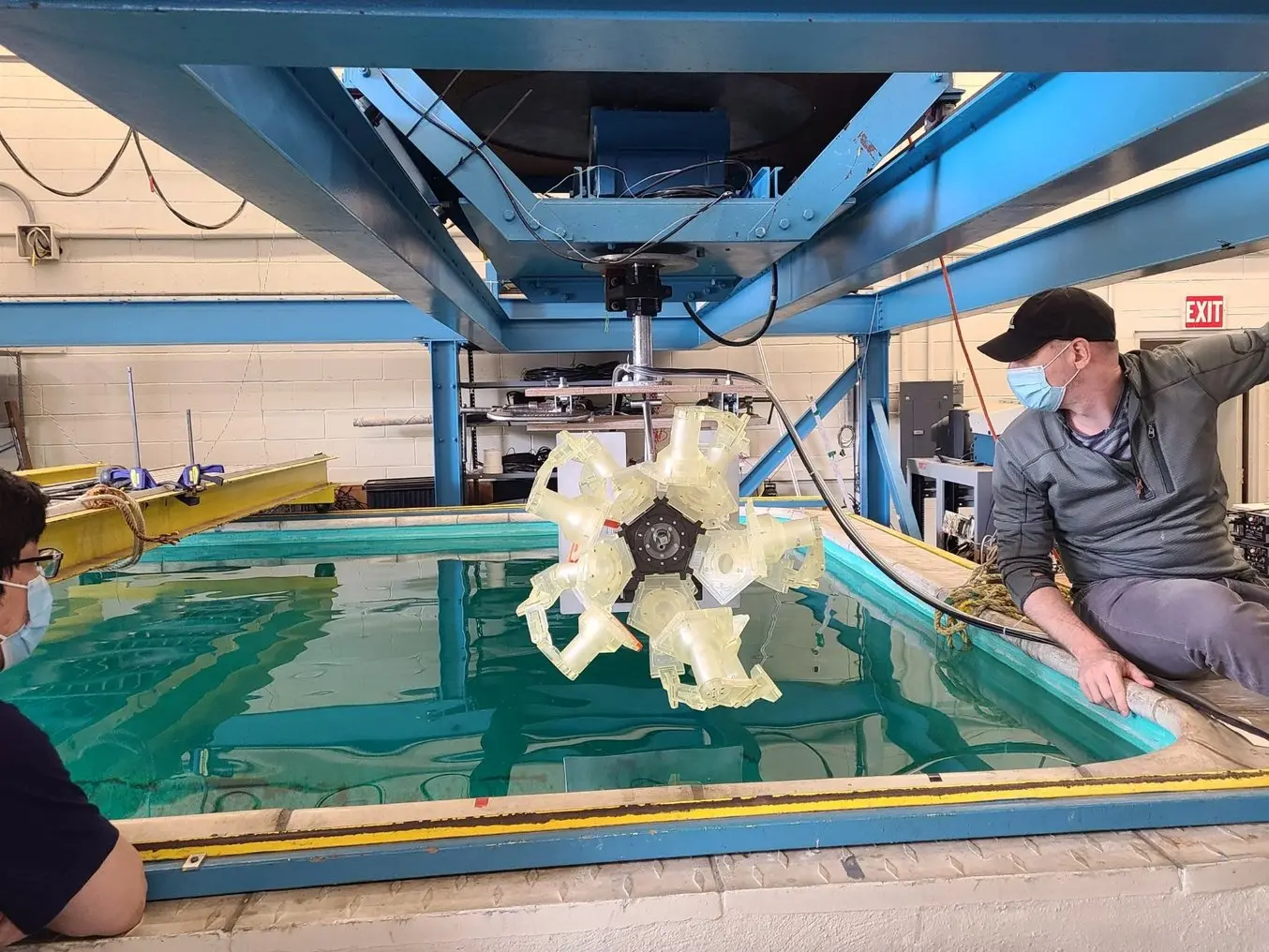
3D printing makes it possible to try out new and complex shapes for testing and sample-gathering equipment, like this tool with components printed in Clear Resin.
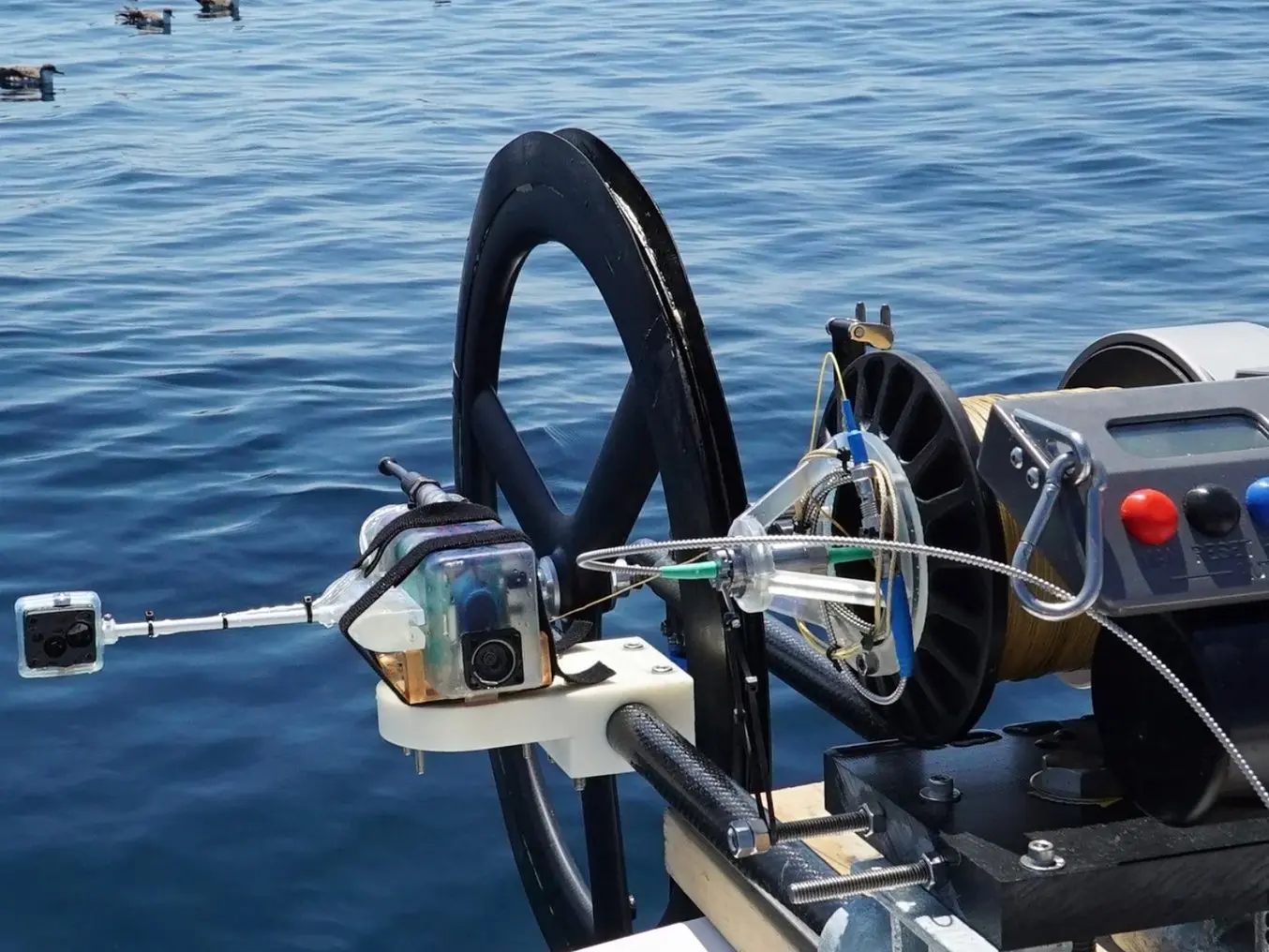
The agile nature of on-demand 3D printing makes custom jigs and fixtures for research at sea possible and cost-effective.
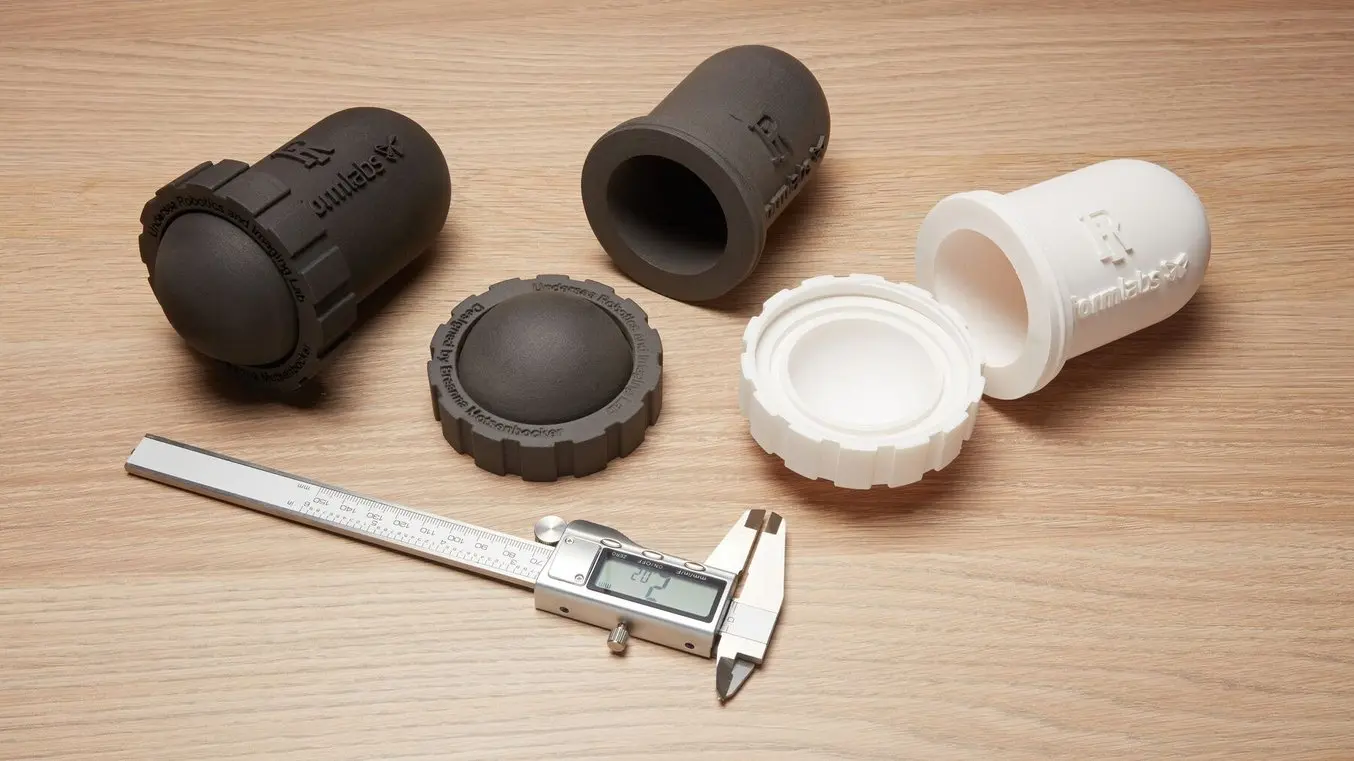
3D Printing Watertight Enclosures and Pressure Testing Results
In this white paper, we will provide the testing results and clear guidelines on how to affordably 3D print customized watertight enclosures.
SLA 3D Printing Applications
Resin 3D printed parts accelerate innovation and supports businesses in a wide range of industries and applications. Advanced materials, incredible dimensional accuracy, and accessible workflows make parts at every stage, from prototyping to production, possible. As costs have come down at the same time that the technology has become more affordable and scalable, end-use applications and mass-customization are becoming the norm, not the exception.
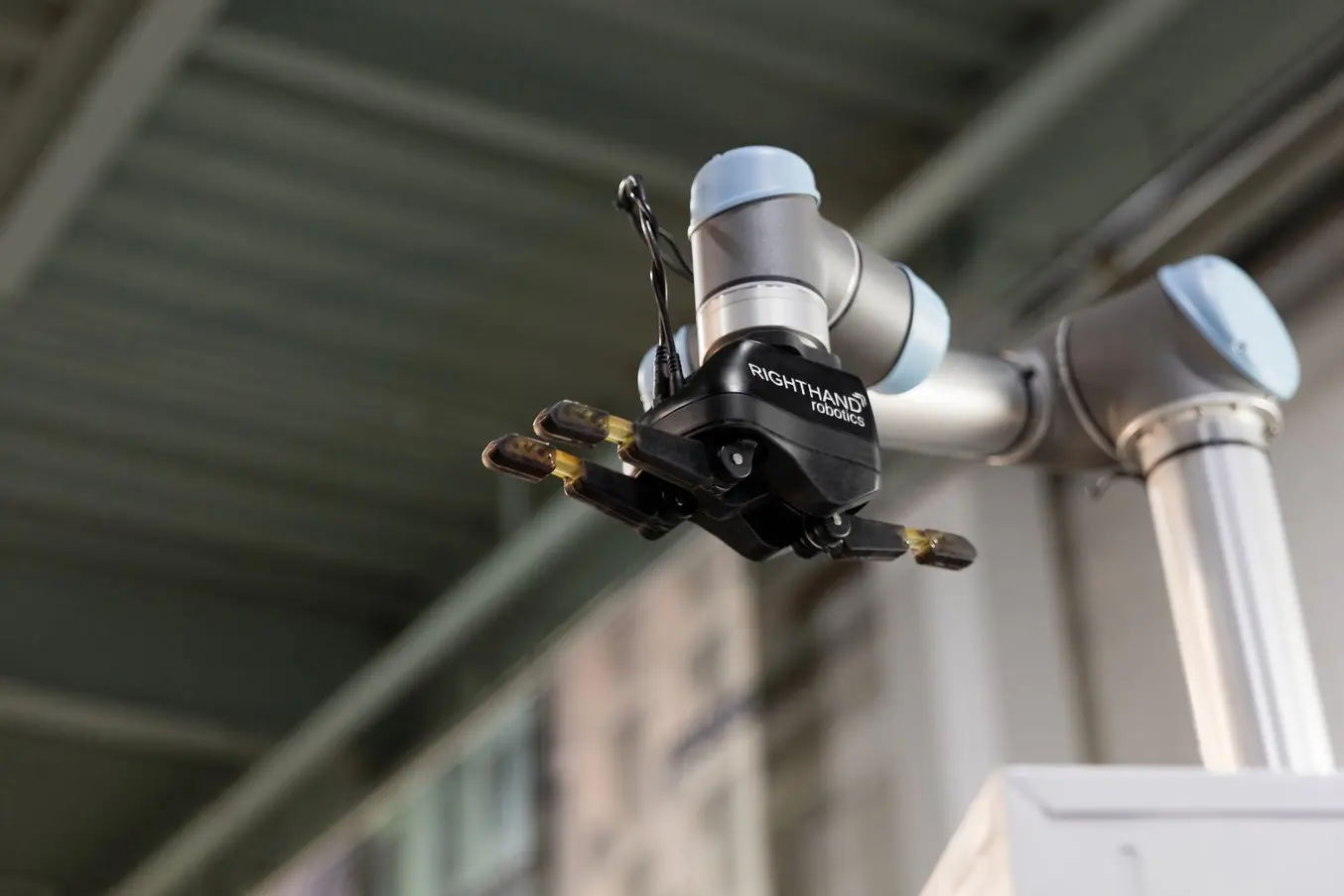
Engineering and Product Design
Rapid prototyping with 3D printing empowers engineers and product designers to turn ideas into realistic proofs of concept, advance these concepts to high-fidelity prototypes that look and work like final products, and guide products through a series of validation stages toward mass production.
Applications:
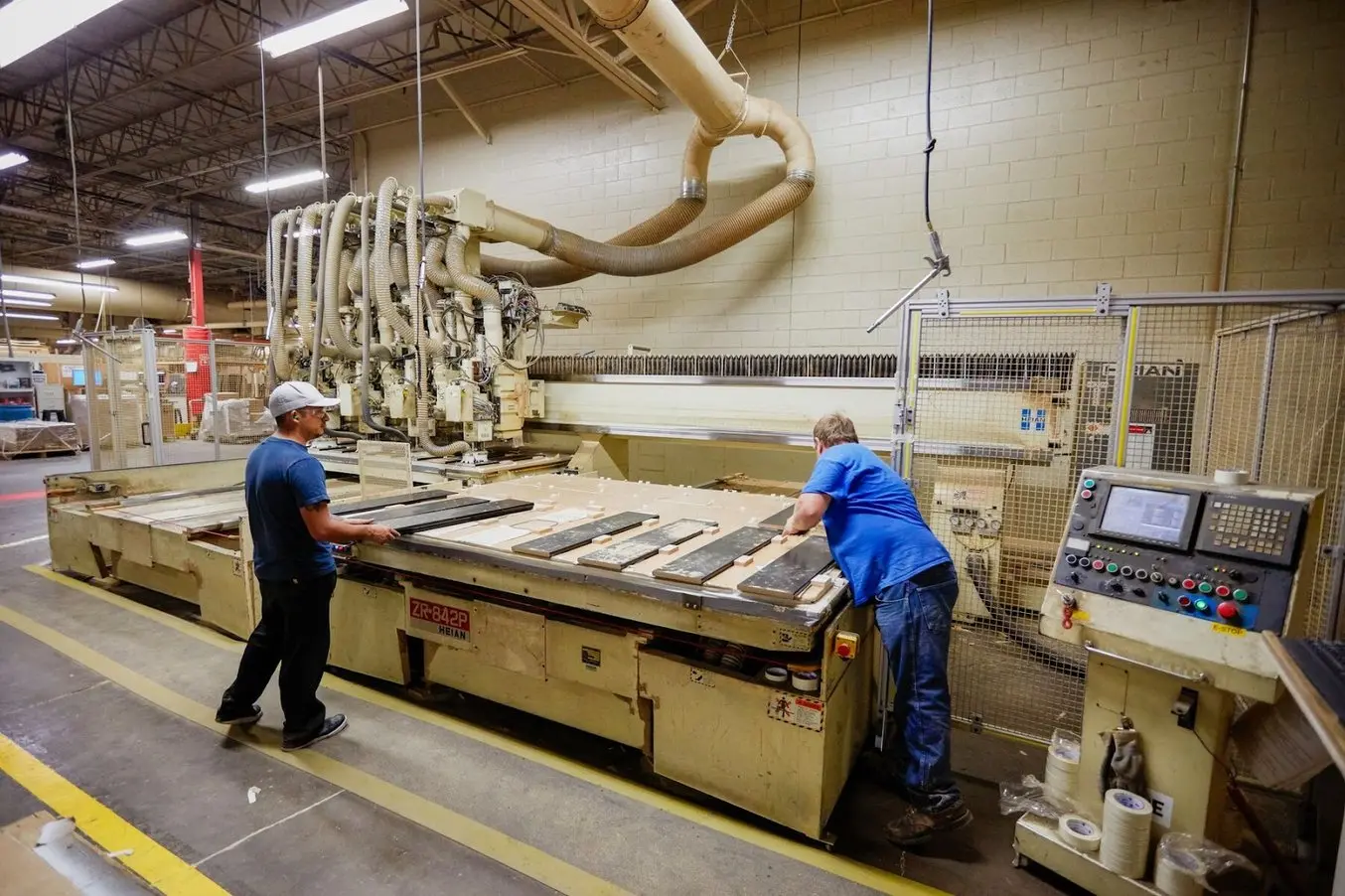
Manufacturing
Manufacturers automate production processes and streamline workflows by prototyping tooling and directly 3D printing custom tools, molds, and manufacturing aids at far lower costs and lead times than with traditional manufacturing. This reduces manufacturing costs and defects, increases quality, speeds up assembly, and maximizes labor effectiveness.
Applications:
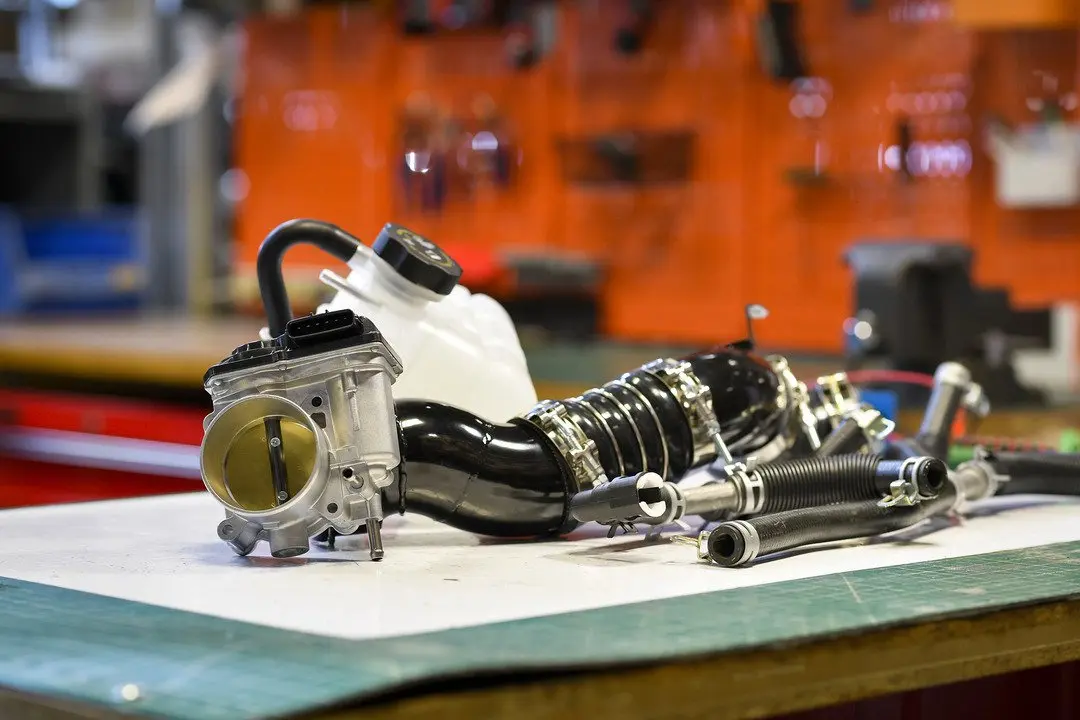
Automotive
Automotive designers, manufacturers, and engineers use SLA 3D printing for a variety of parts throughout their process. From concept models to aftermarket parts, SLA 3D printing is everywhere, and touches the development or production of every car on the road.
- Rapid prototyping (concept models, functional prototyping, validation testing)
- Rapid tooling
- Manufacturing aids
- End-use, aftermarket, and custom parts
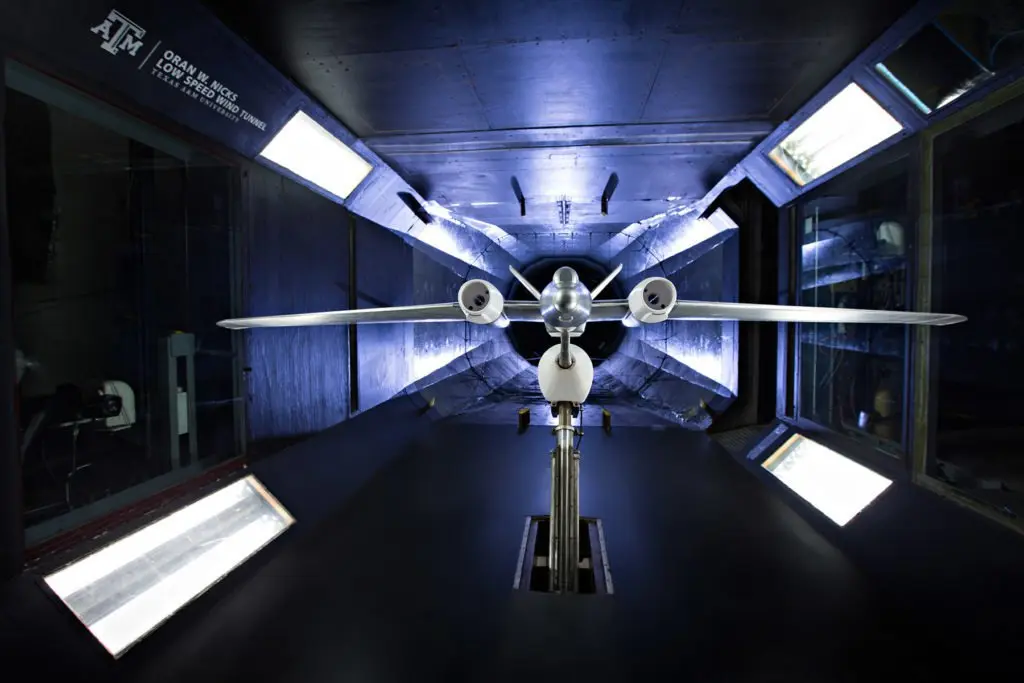
Aerospace
SLA 3D printed parts have been sent to space for testing on the International Space Station, used in manufacturing for commercial airlines, and are used across the world for testing, prototyping, and manufacturing in both the private and federal aerospace industry. From fixtures that help build space mission lasers to ceramics that are used in testing for jet-fuel applications, SLA parts are helping us reach the final frontier.
- Rapid prototyping (wind tunnel testing)
- Rapid tooling
- Manufacturing aids
- End-use, replacement, and custom parts
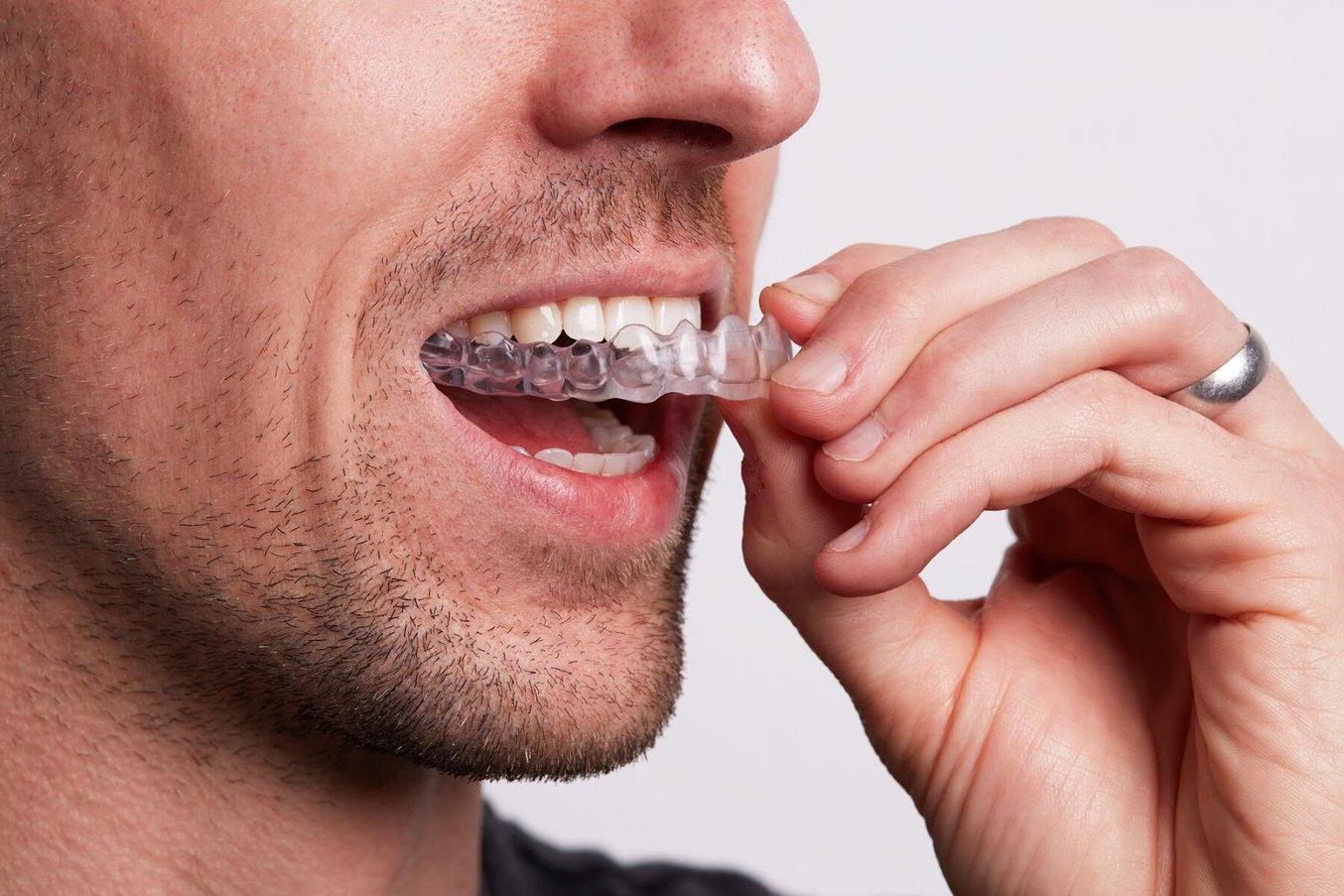
Dental
Digital dentistry reduces the risks and uncertainties introduced by human factors, providing higher consistency, accuracy, and precision at every stage of the workflow to improve patient care. 3D printers can produce a range of high-quality custom products and appliances at low unit costs with superior fit and repeatable results.
Applications:
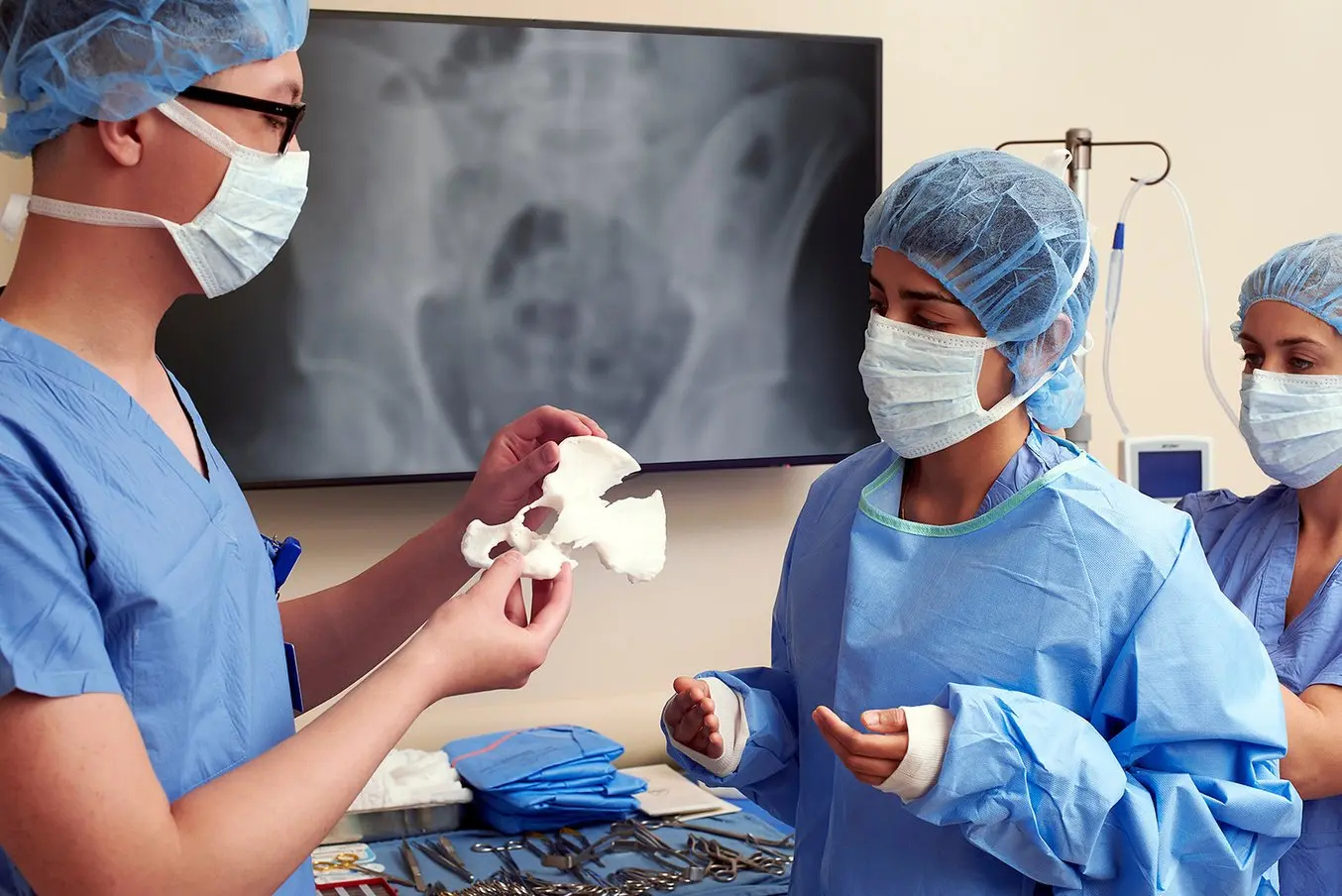
Medical
Affordable, professional-grade desktop 3D printing helps doctors deliver treatments and devices with a high level of customization to better serve each unique individual, opening the door to high-impact medical applications while saving organizations significant time and costs.
Applications:
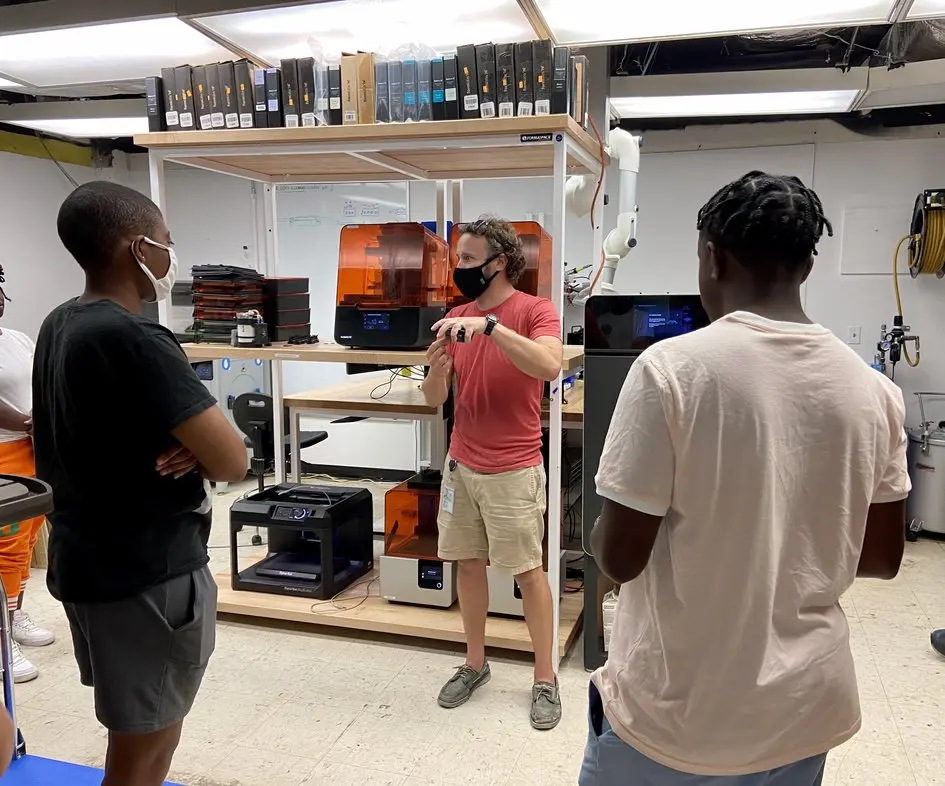
Education
Resin 3D printers are multifunctional tools for immersive learning and advanced research. They can encourage creativity and expose students to professional-level technology while supporting STEAM curricula across science, engineering, art, and design.
Applications:
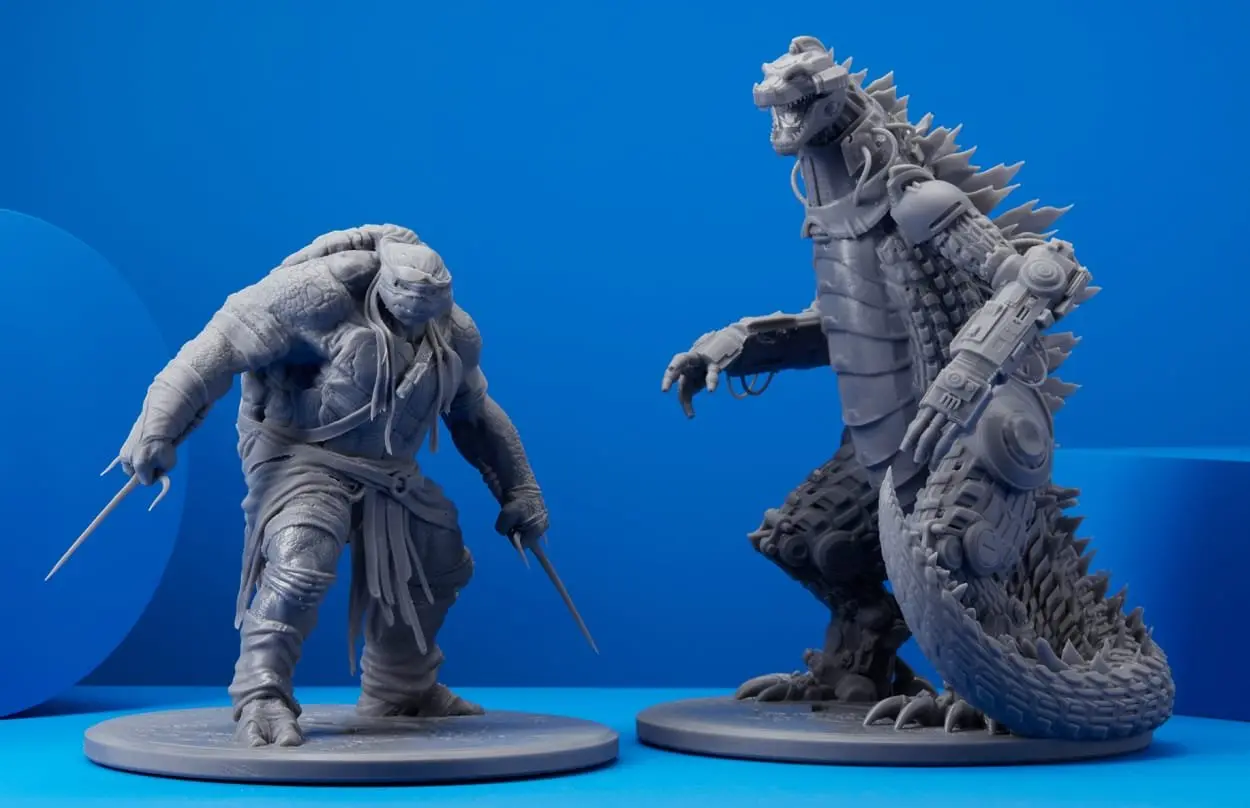
Entertainment
High-definition physical models are widely used in sculpting, character modeling, and prop making. 3D printed parts have starred in stop-motion films, video games, bespoke costumes, and even special effects for blockbuster movies.
Applications:
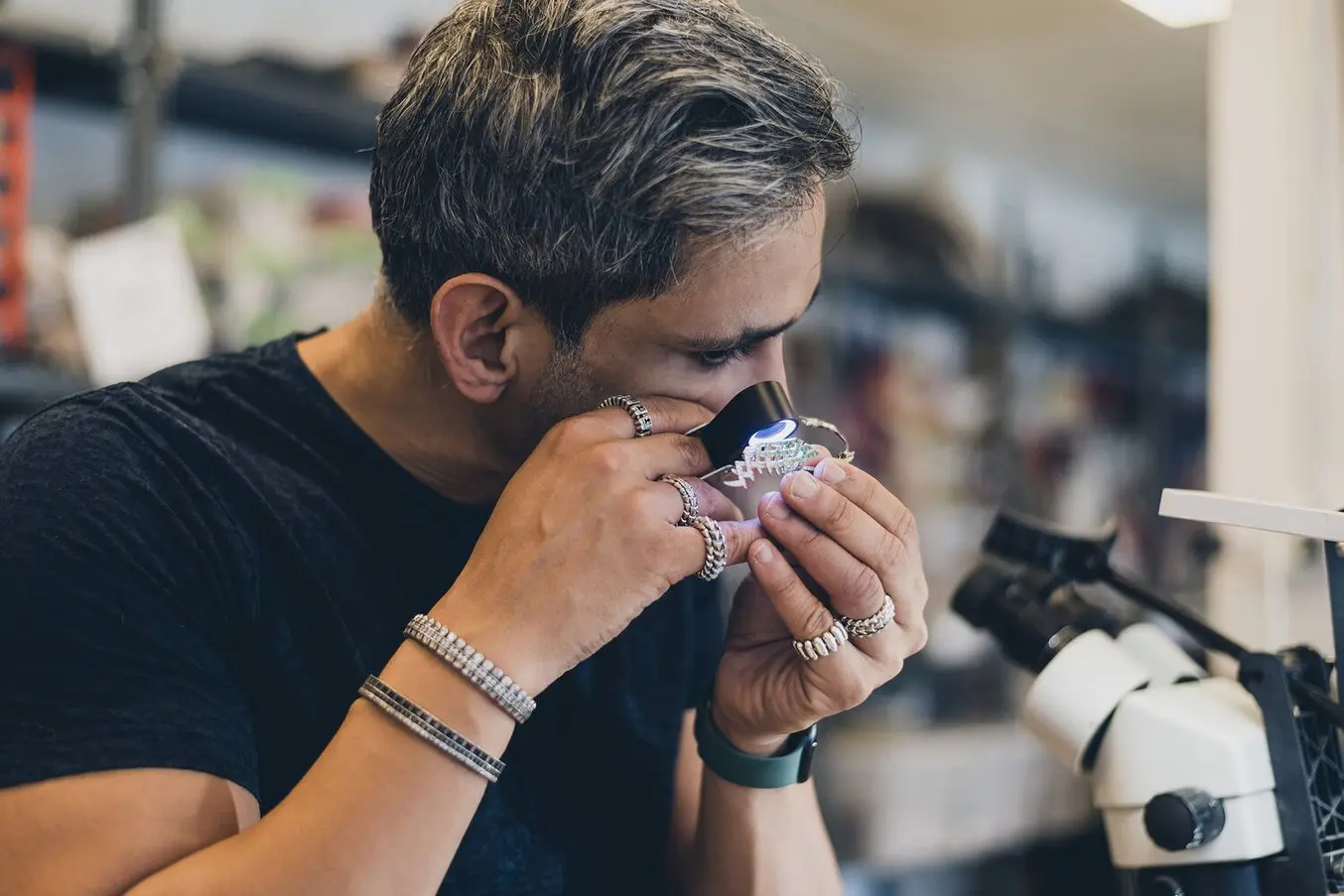
Jewelry
Jewelry professionals use CAD and 3D printing to rapidly prototype designs, fit clients, and produce large batches of ready-to-cast pieces. Digital tools allow for the creation of consistent, sharply detailed pieces without the tediousness and variability of wax carving.
Applications:
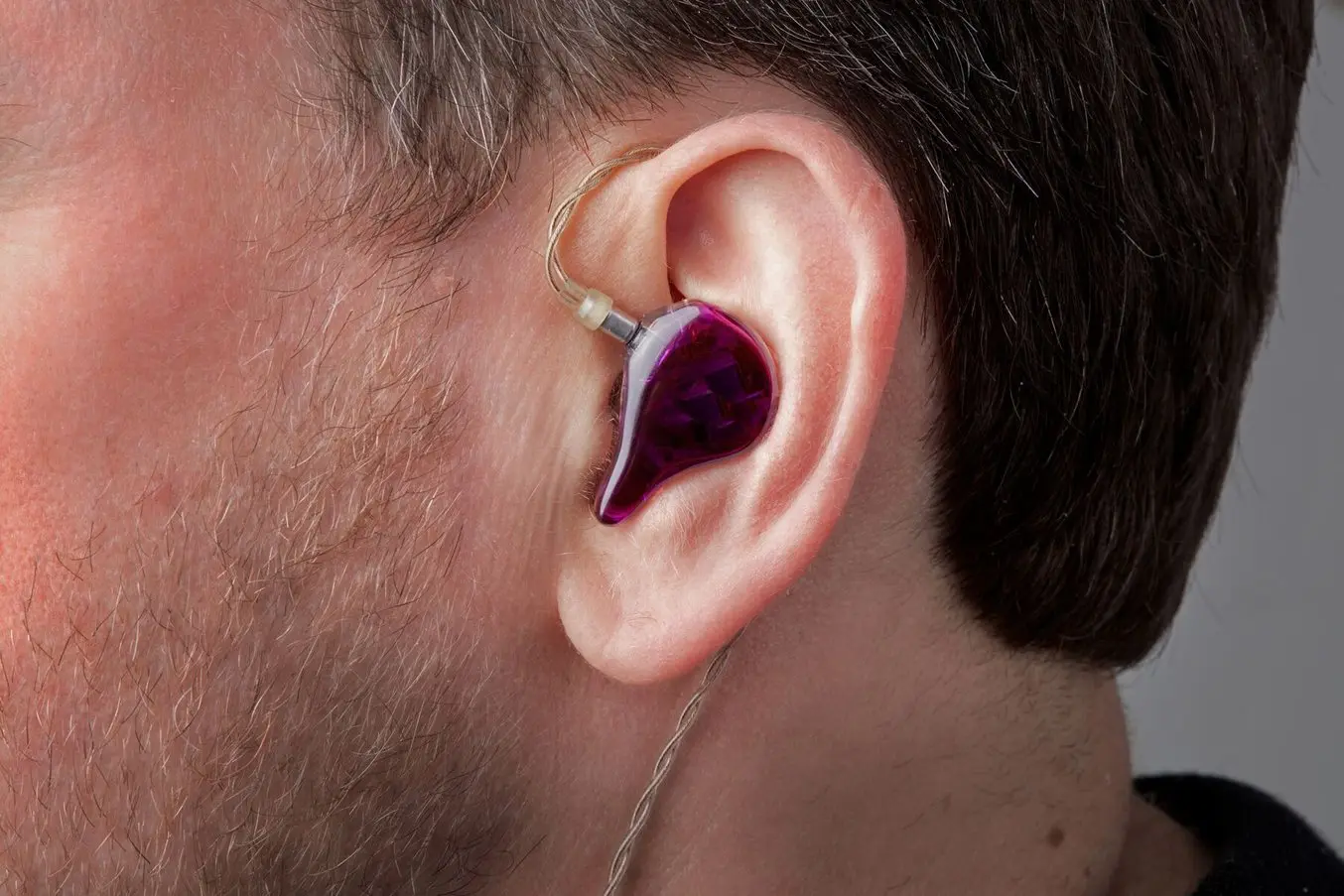
Audiology
Hearing specialists and ear mold labs use digital workflows and 3D printing to manufacture higher quality custom ear products more consistently, and at higher volumes, for applications like behind-the-ear hearing aids, hearing protection, and custom earplugs and earbuds.
Applications:
- Hearing aids
- Noise protection
- Consumer audio
SLA 3D Printing Materials
SLA 3D printing materials are highly versatile, offering resin formulations with a wide range of optical, mechanical, and thermal properties to match those of standard, engineering, and industrial thermoplastics. There are resins formulated specifically for manufacturing concerns like electrostatic discharge or flame retardancy, and resins formulated to mimic the mechanical properties of industry-familiar plastics. Depending on the formulation and chemistry, some resins can also be leveraged to produce pure silicone, polyurethane, or ceramic parts. Resin 3D printing also offers the broadest spectrum of biocompatible materials, opening up doors in end-use products, medical equipment, 3D printing at the point of care, and medical procedure innovation.
The specific material availability is highly dependent on the manufacturer and printer. Formlabs offers the most comprehensive resin library with 40+ uniquely formulated resins.
3D printing’s ability to create cost-effective parts with complex geometries makes innovation possible, and, with the right material, those innovative ideas can be tested, validated, and put into practice. Formlabs’ materials enable applications like mass-customized consumer goods, surgical tools, dental implants and appliances, manufacturing aids, rapid tooling, and more. Formlabs’ resin 3D printers make accessing these powerful workflows possible.
General Purpose Resins
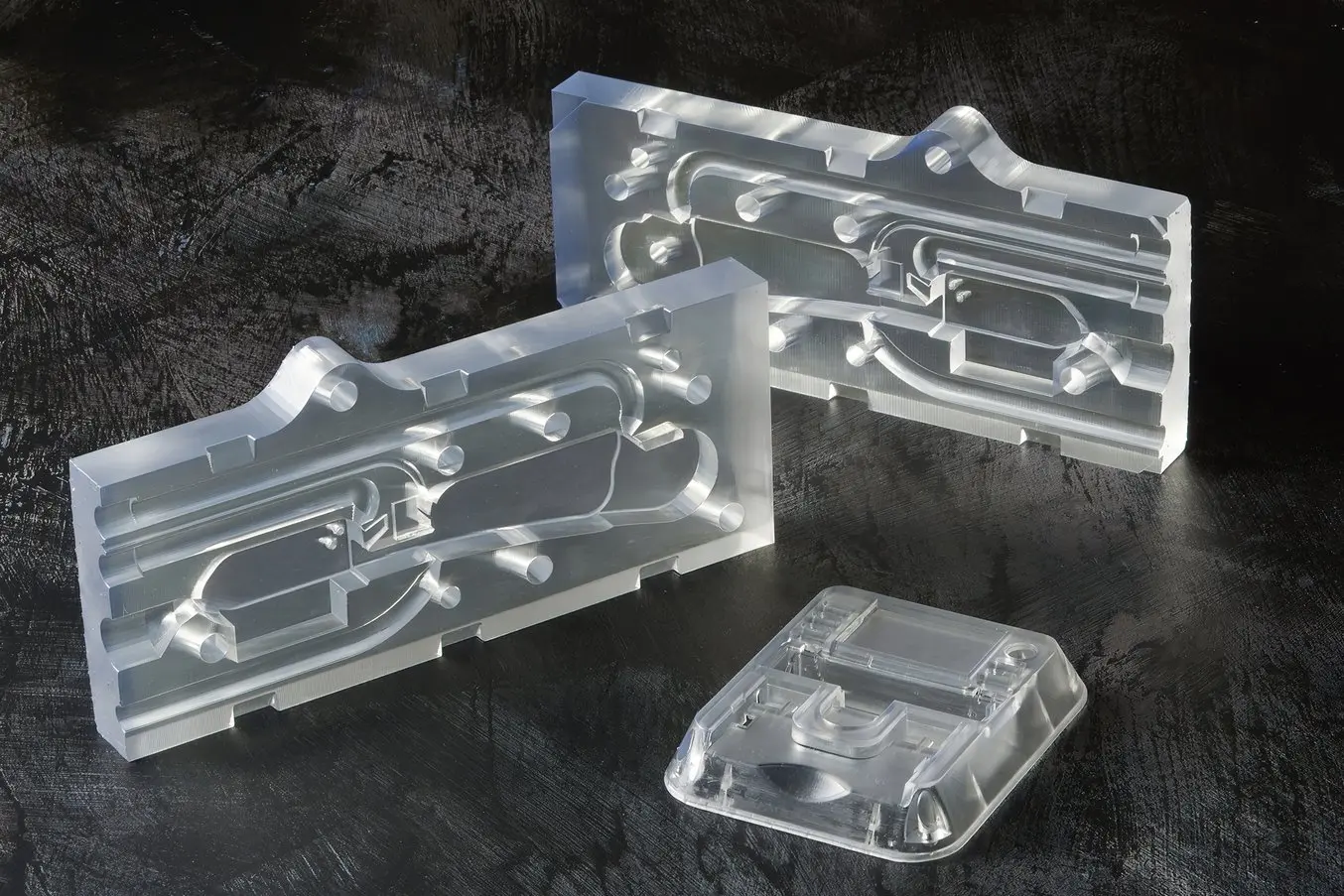
Clear Resin creates highly transparent and colorless parts that can be polished to near optical transparency. For two-part molds, this transparency makes it easy to observe and troubleshoot the molding process as it happens within the part.
Formlabs’ General Purpose Resins are formulated for speed and consistency to create parts in a range of applications and industries. From matte greyscale parts for design review prototypes to transparent parts printed in Clear Resin for see-through models and molds, General Purpose Resins are the workhorses of SLA 3D printing. Formlabs latest General Purpose Resins developed for Form 4 allow new heights to be reached in speed, mechanical properties, and resolution — Fast Model Resin can print at speeds of 100 mm per hour and Grey Resin has 30% higher impact strength.
Material | Description | Applications |
---|---|---|
Fast Model Resin | Print speeds of up to 100 mm/hour | Concept models Rapid prototyping |
Clear Resin | Polishes to near optical transparency | Parts requiring optical transparency Rapid prototyping Transparent molds Millifluidics |
Greyscale Resins (Grey, Black, White) | Smooth, matte finish High resolution | Concept models Rapid prototyping Jigs and fixtures Masking tools |
Color Resin | Custom colors Bright, colorful parts | Rapid prototyping with matching color, material, and finish (CMF) Color-coded jigs and fixtures Custom-colored end-use parts |
Engineering and Manufacturing Resins
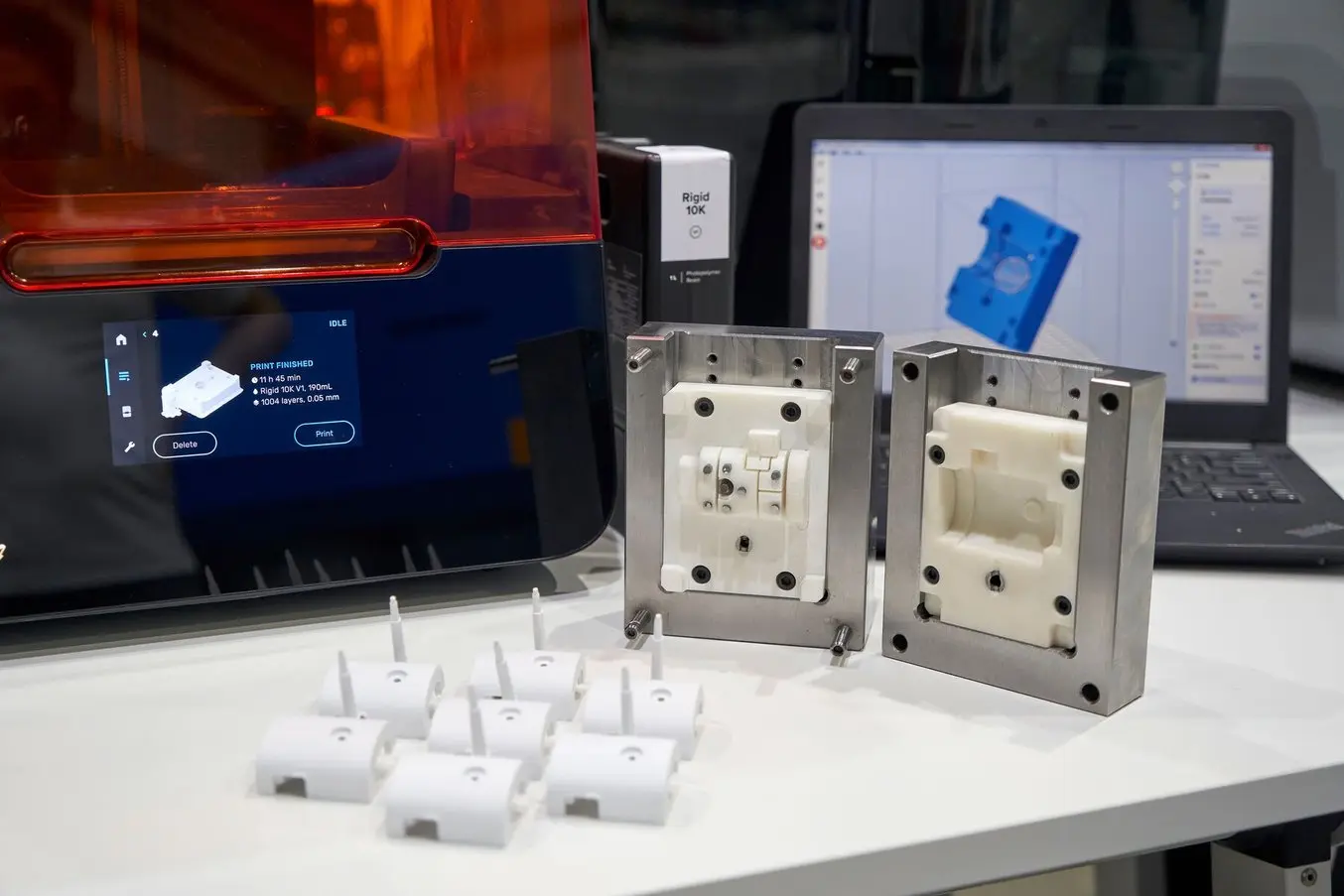
Rigid 10K Resin is a highly glass-filled material for industrial parts that need to withstand significant load without bending, including applications like injection molding.
Formlabs Engineering Resins have been formulated to answer specific needs in engineering and manufacturing workflows, and enable new applications, streamline operations, and simplify field testing. These materials are designed to match or exceed the capabilities of industry-familiar materials like ABS, silicone, or PEEK. From extremely stiff, rigid materials, to robust materials that can handle impacts, to soft and flexible materials that can handle bending and flexing through repeated cycles. Unique specialty materials include ESD-safe or flame-retardant resins, as well as technical materials that haven’t been accessible in desktop 3D printing before, such as true ceramic and silicone 3D printing.
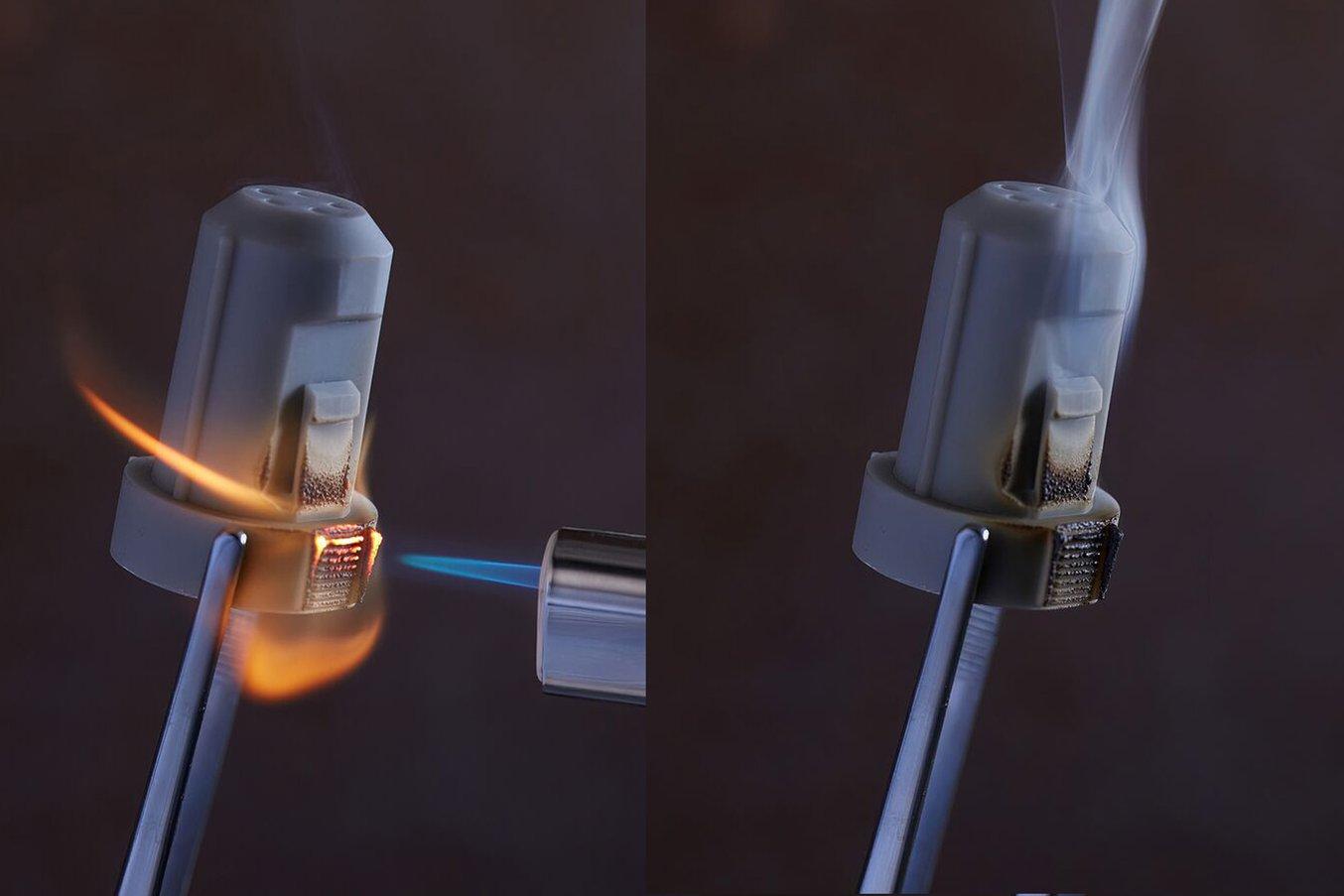
Formlabs' Flame Retardant Resin is a specialty UL 94 Blue Card certified material for creating self-extinguishing and halogen-free parts.
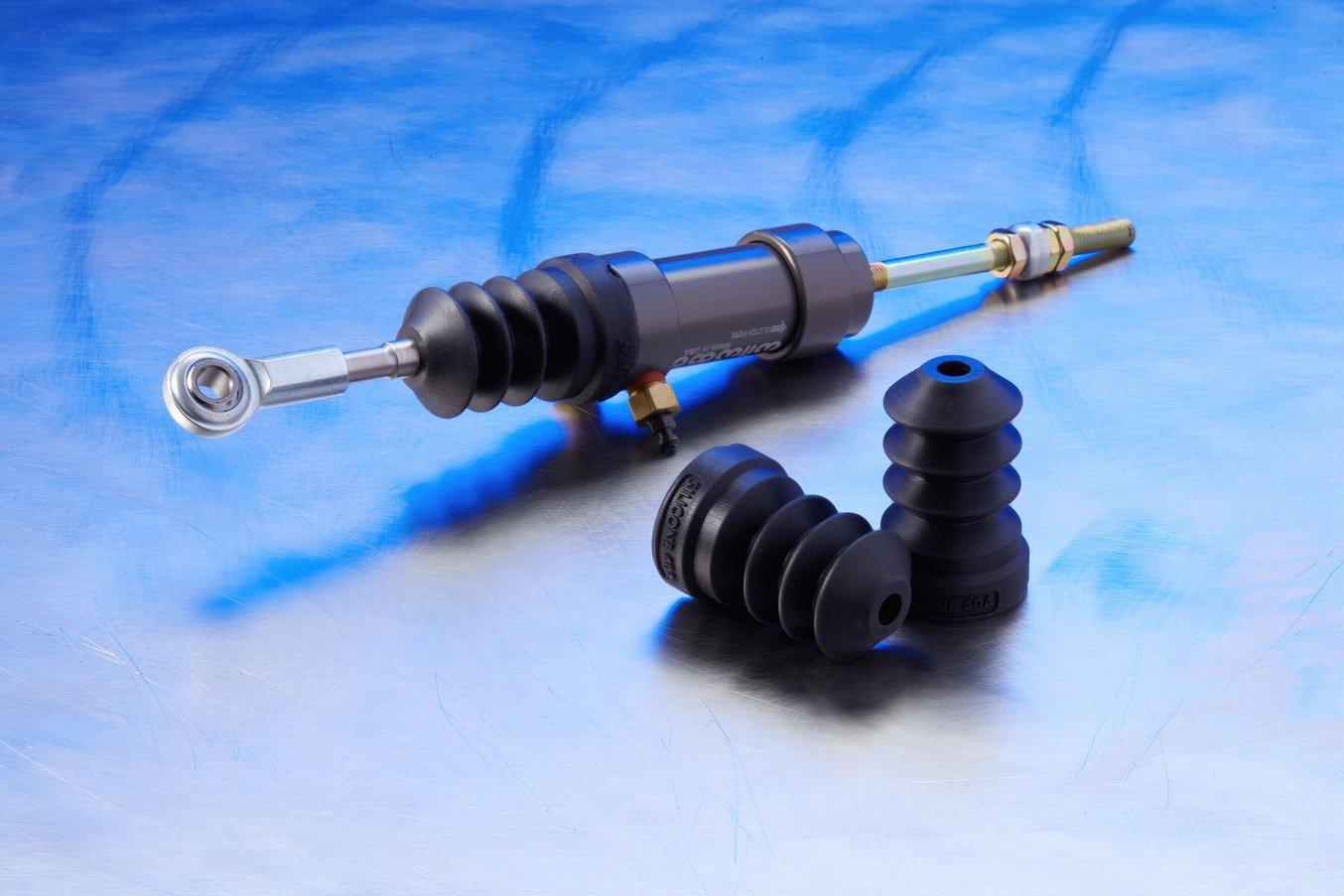
Silicone 40A Resin is a true silicone, with mechanical properties that are familiar to engineers and product designers.
Material | Description | Applications |
---|---|---|
Tough and Durable Resins | Strong, robust, functional, and dynamic materials Can handle compression, stretching, bending, and impacts without breaking Various materials with properties similar to ABS, PP, or PE | Housings and enclosures Jigs and fixtures Connectors Wear-and-tear prototypes |
Rigid Resins | Highly filled, strong and stiff materials that resist bending Thermally and chemically resistant Dimensionally stable under load Simulates stiffness of PEEK or glass and fiber-filled thermoplastics | Jigs, fixtures, and tooling Turbines and fan blades Fluid and airflow components Electrical casings and automotive housings |
Flexible and Elastic Resins | Flexibility of rubber, TPU, or silicone Can withstand bending, flexing, and compression Holds up to repeated cycles without tearing | Consumer goods prototyping Compliant features for robotics Medical devices and anatomical models Special effects props and models |
Silicone 40A Resin | The first accessible 100% silicone 3D printing material Superior material properties of cast silicone | Functional prototypes, validation units, and small batches of silicone parts Customized medical devices Flexible fixtures, masking tools, and soft molds for casting urethane or resin |
High Temp Resin | High temperature resistance High precision | Hot air, gas, and fluid flow Heat resistant mounts, housings, and fixtures Molds and inserts |
Flame Retardant (FR) Resin | Flame retardant, heat-resistant, stiff, and creep-resistant material for indoor and industrial environments with high temperatures or ignition sources | Interior aerospace and automotive parts Protective and internal consumer products or medical electronics components Custom jigs, fixtures, and replacement parts |
ESD Resin | ESD-safe material to improve electronics manufacturing workflows | Tooling & fixturing for electronics manufacturing Anti-static prototype and end-use components Custom trays for component handling and storage |
Polyurethane Resins | Excellent long-term durability UV, temperature, and humidity stable Flame retardancy, sterilizability, and chemical and abrasion resistance | High performance automotive, aerospace, and machinery components Robust and rugged end-use parts Tough, longer-lasting functional prototypes |
Alumina 4N Resin | 99.99% pure alumina technical ceramic Exceptional thermal, mechanical, and conductive properties | Heat and electrical insulators Heavy-duty tools Chemically resistant and wear-resistant components |
Clear Cast Resin | Clean burnout Low thermal expansion Highly accurate | In-house production of industrial investment casting patterns for end-use metal parts |
Dental Resins
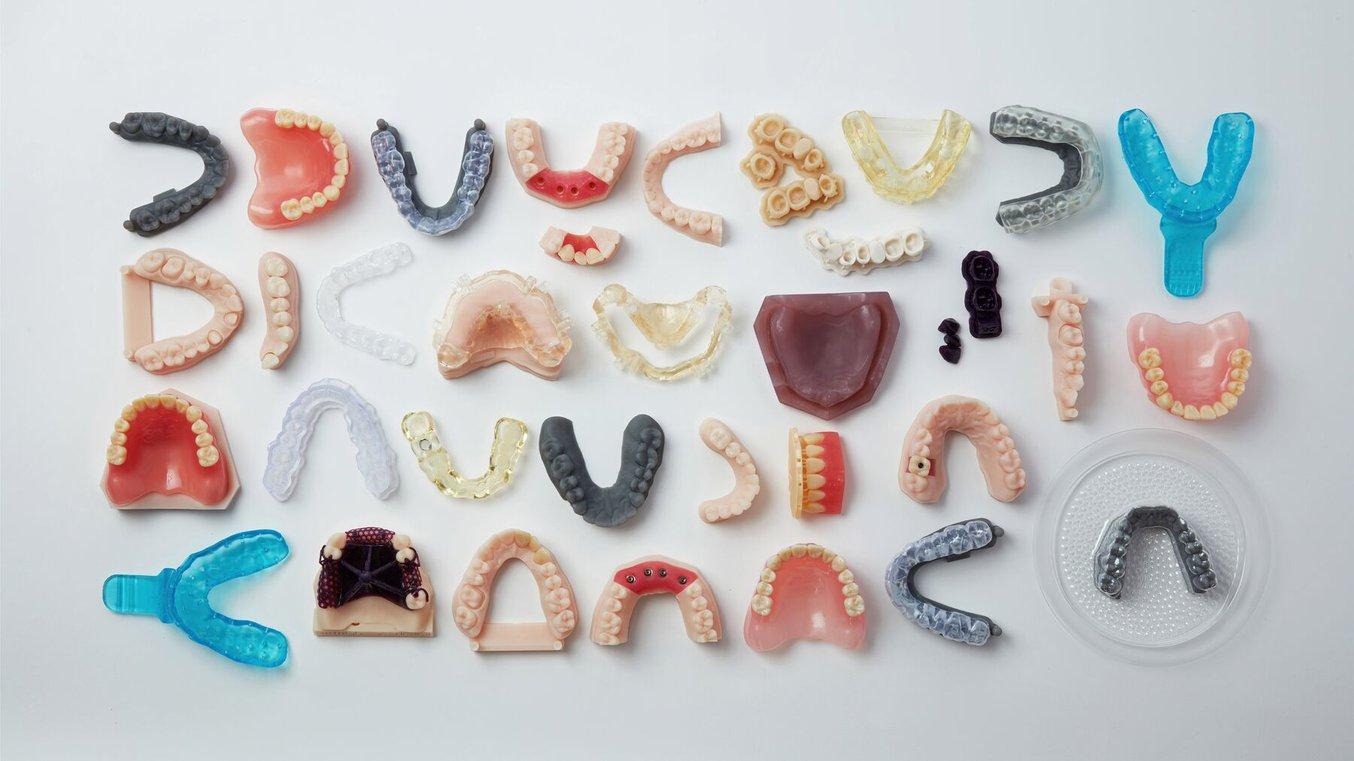
Formlabs Dental Resins empower dental labs and practices to rapidly manufacture clear aligners, biocompatible appliances like surgical guides or splints, and even advanced intraoral applications such as full dentures or permanent restorations.
For dental professionals, the Formlabs ecosystems offers a simplified, all-in-one workflow that promises accurate parts, every time — no adjustment or calibration necessary. From large labs and practices with multiple types of appliances to smaller operations that specialize in certain indications, the Form 4B and library of Dental Resins provide solutions for everyone.
Material | Description | Applications |
---|---|---|
Precision Model Resin | High-accuracy material for creating restorative models with >99% of printed surface area within 100 μm of the digital model | Removable die models Crown and bridge models Implant analog models Diagnostic models |
Fast Model Resin | Formlabs' fastest dental material capable of printing a dental model every 49 seconds | Thermoforming models Orthodontic appliance models |
Grey Resin | Offers a balance of speed and accuracy along with excellent aesthetics | Diagnostic models Fit test models |
Surgical Guide Resin | Next-generation 3D printing material that is autoclavable and biocompatible for implant placement surgical guides | Surgical guides Pilot drill guides Drilling templates Device sizing templates |
Dental LT Clear Resin | Long-term biocompatible material for hard occlusal splints and night guards | Hard occlusal splints Hard night guards |
Dental LT Comfort Resin | Long-term biocompatible material easily polished to high optical transparency | Flexible occlusal splints Flexible night guards |
Digital Dentures | Accessible, affordable digital denture material for Class II long-term biocompatible dentures | Final dentures Try-in dentures |
Premium Teeth Resin | Nano-ceramic Class II biocompatible material with enhanced aesthetics and superior intraoral mechanical properties | Denture teeth Try-in dentures Full-arch implant-supported restorations |
Custom Tray Resin | Fast printing, biocompatible resin for custom impression trays | Custom impression trays |
Temporary CB Resin | Tooth-colored resin available in five shades with excellent marginal adaptation, strength, and aesthetics | Crowns Bridges Inlays Veneers Onlays |
Permanent Crown Resin | Tooth-colored, ceramic-filled resin for high strength, long term restorations available in four VITA Classical shades | Single crowns Inlays Onlays Veneers |
IBT Flex Resin | Flexible and biocompatible material for highly accurate indirect bonding trays and direct composite restoration guides | Indirect bonding trays Direct composite restoration guides |
Soft Tissue Starter Pack | Flexible material for removable soft tissue components | Soft tissue for implant models Gingiva masks |
Medical Resins
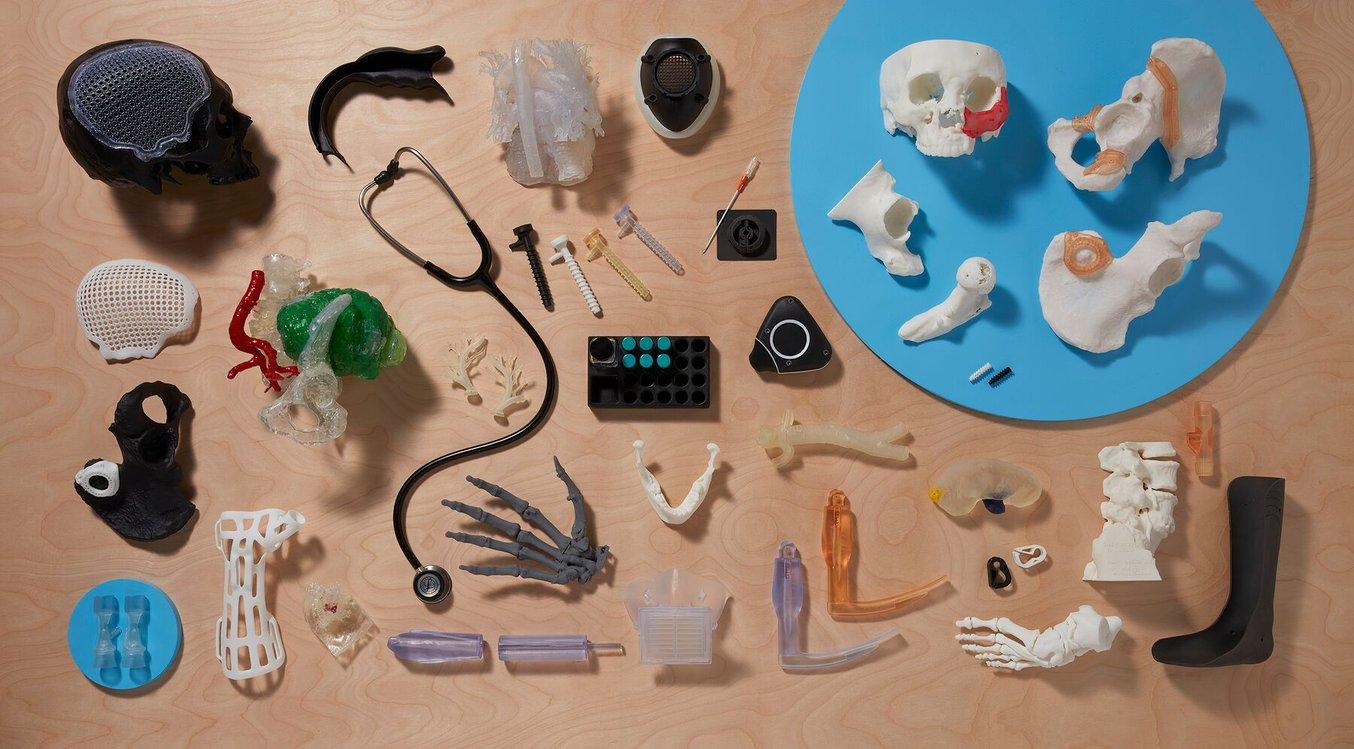
Formlabs BioMed Resins enable healthcare professionals to create accurate, biocompatible, and personalized anatomical models, surgical instrumentation, and medical devices that improve patient care.
For healthcare professionals, Formlabs BioMed Resins are medical-grade materials for a wide range of applications where performance and biocompatibility are critical. Materials in the BioMed Resin family are developed and manufactured in an ISO 13485 certified facility and are compatible with common disinfection and sterilization methods.
Material | Description | Applications |
---|---|---|
BioMed White Resin | Rigid and opaque white. Approved for long-term skin (>30 days) or short-term bone, tissue, dentin, and mucosal membrane contact (<24 hours). | End-use medical devices and device components; patient-specific implant sizing models and molds; cutting and drilling guides; surgical tools and templates; biocompatible molds, jigs, and fixtures; anatomical models that can be used in the OR. |
BioMed Black Resin | Rigid and matte black. Approved for long-term skin (>30 days) and short-term mucosal membrane contact (<24 hours). | Medical devices and device components; biocompatible molds, jigs, and fixtures; end-use parts requiring patient contact; consumer goods. |
BioMed Amber Resin | Rigid and semi-transparent. Approved for long-term skin (>30 days) or short-term bone, tissue, dentin, and mucosal membrane contact (<24 hours). | End-use medical devices; implant sizing models; cutting and drilling guides. |
BioMed Clear Resin | Rigid and transparent. Approved for long-term skin (>30 days), breathing gas pathways, and mucosal membrane contact (>30 hours) or short-term bone, tissue, and dentin (<24 hours). | End-use devices, including gas pathway devices; biocompatible prototypes, molds, jigs and fixtures; models for visualization and implant sizing; cell culture and bioprocess devices. |
BioMed Durable Resin | Impact, shatter, and abrasion resistant. Transparent. Approved for long-term skin (>30 days) and mucosal membrane (>30 hours) or short-term tissue, bone, and dentin contact (<24 hours). | Patient-specific instruments; single-use instruments; end-use devices and components requiring biocompatibility and impact resistance. |
BioMed Elastic 50A Resin | Soft and silicone-like. Translucent. Approved forlong-term skin (>30 days) or short-term mucosal membrane contact (<24 hours). | Comfortable medical devices requiring long-term skin contact; biocompatible soft tissue models surgeons can reference in the operating room. |
BioMed Flex 80A Resin | Hard rubber-like. Translucent. Approved for long-term skin (>30 days) or short-term mucosal membrane contact (<24 hours). | Flexible biocompatible medical devices and components; medical devices requiring short-term mucosal membrane contact; firm tissue models to assist in surgeries. |
Jewelry Resins
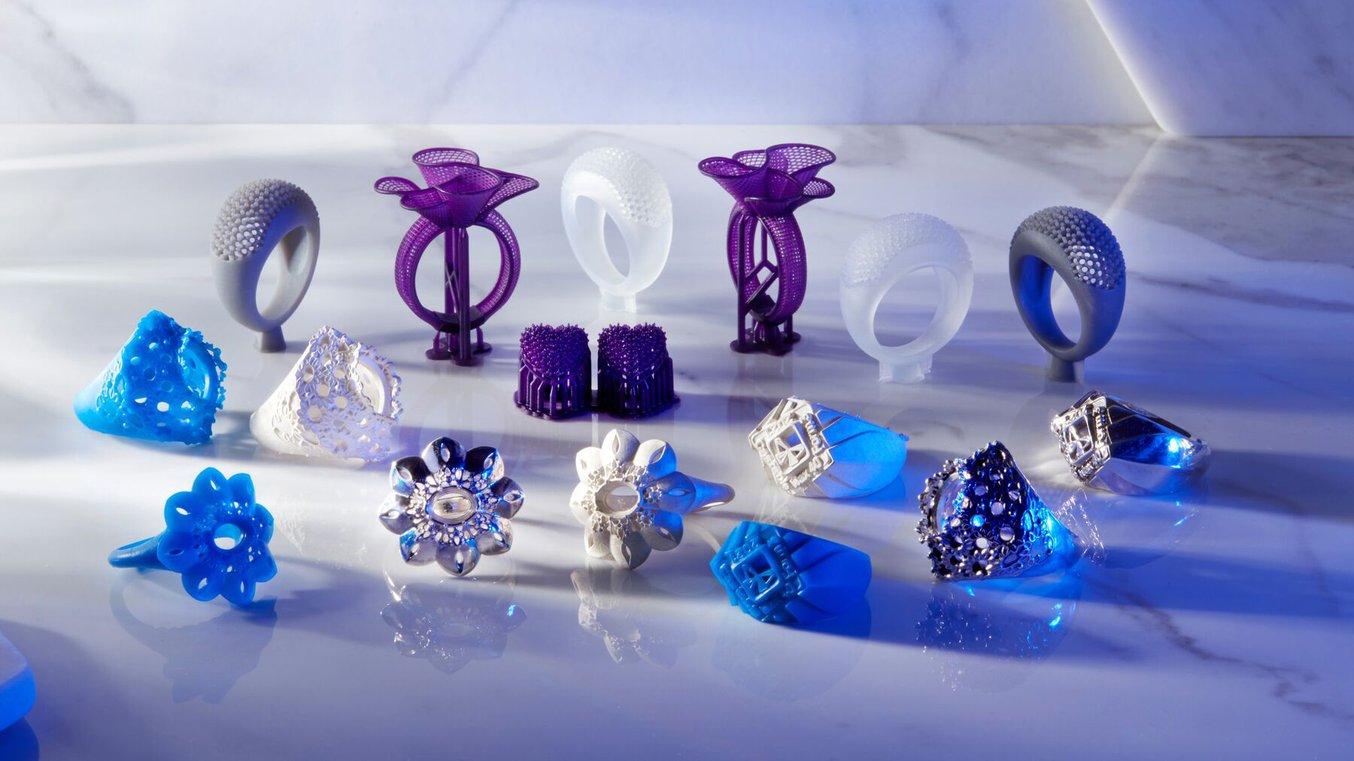
Jewelry Resins enable the prototyping and production of custom jewelry.
Formlabs Jewelry Resins are designed to reliably reproduce crisp settings, sharp prongs, smooth shanks, and fine surface details. They enable anyone from retailers and designers producing custom jewelry to large casting houses manufacturing at scale to produce try-on pieces for customers, ready-to-cast custom jewelry, or masters for reusable jewelry molds.
Material | Description | Applications |
---|---|---|
Castable Resins | Materials for investment casting Easy to cast, with intricate details and strong shape retention | Custom jewelry |
High Temp Resin | Strong and temperature resistant material for vulcanized rubber molding | Masters for reusable molds |
Grey Resin | General purpose material for high detail prototyping and custom fittings | Jewelry prototyping Try-on pieces |
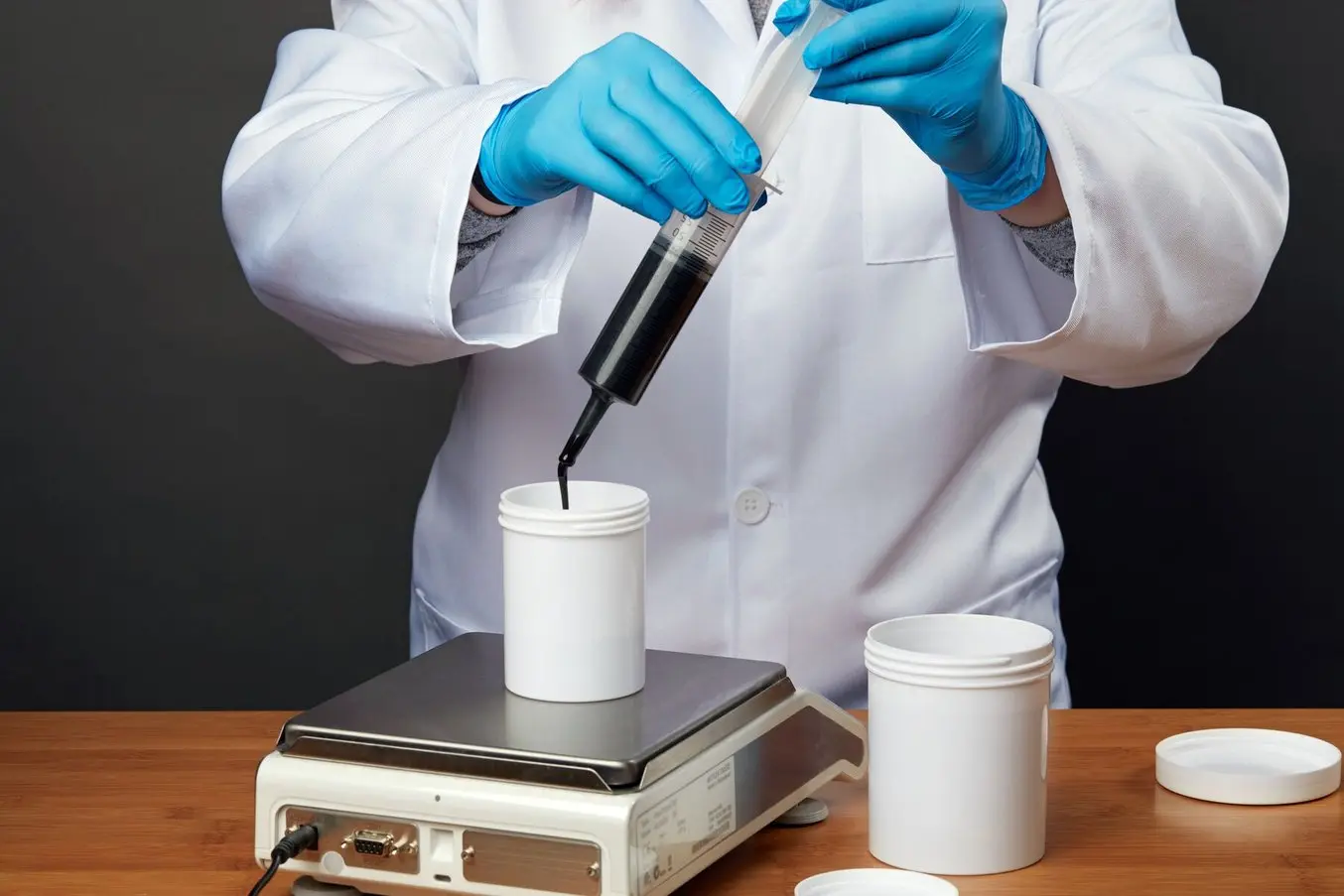
Formlabs is Open
Maximize your 3D printer’s potential with Formlabs Developer Platform. Unlock the possibility of printing with any 405 nm photopolymer resin or 1064 nm powder on Formlabs 3D printers, customize your print settings, or build software integrations.
Bringing SLA 3D Printing In-House
Several factors have influenced the surge in the number of businesses that are bringing SLA 3D printing in-house. High-quality SLA 3D printing has become more affordable, printers themselves have become reliable and easy to use, and as materials have become more advanced, new applications are opening up. Engineers, manufacturers, healthcare professionals, and businesses of all types can see the benefit of having resin 3D printing capacity in-house.
Though the benefits of this technology at your fingertips can stretch to every facet of an organization, the main advantages are that in-house SLA 3D printing reduces costs and shortens internal and customer lead times, helps control and insulate businesses' supply chains, and is a scalable technology that can grow with you.
Reduce Costs and Shorten Lead Times
SLA 3D printing can help businesses eliminate the high costs and long lead times associated with outsourcing or more complicated alternative methods like machining. With 3D printing, there’s no need for costly tooling and setup; the same equipment can be used to rapidly produce different geometries.
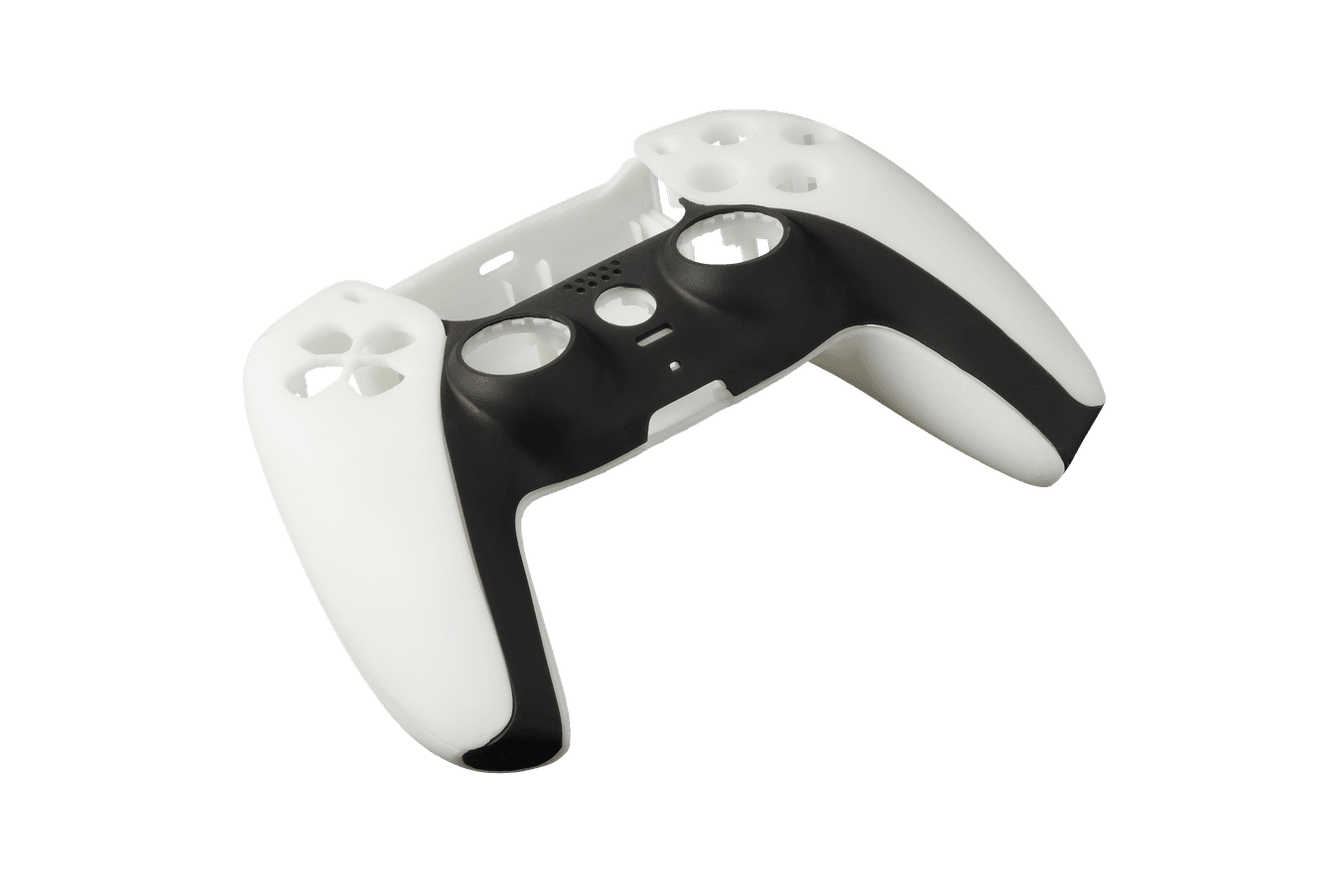
A three-piece gaming controller prototype assembly, 3D printed in two different materials for contrasting colors.
Rapid Prototyping: Battle Beaver Customs Gaming Controller
The rapid print speed of Form 4 enables same-day prototyping at Battle Beaver Customs, helping the company bring new products to the market faster and stay ahead of its competitors.
Prototype assembly | Outsourcing | 3D printing in house |
---|---|---|
Equipment | - | Form 4 White and Black Resins |
Lead time | 7 days | 5 hours |
Cost | $250 | $15 |
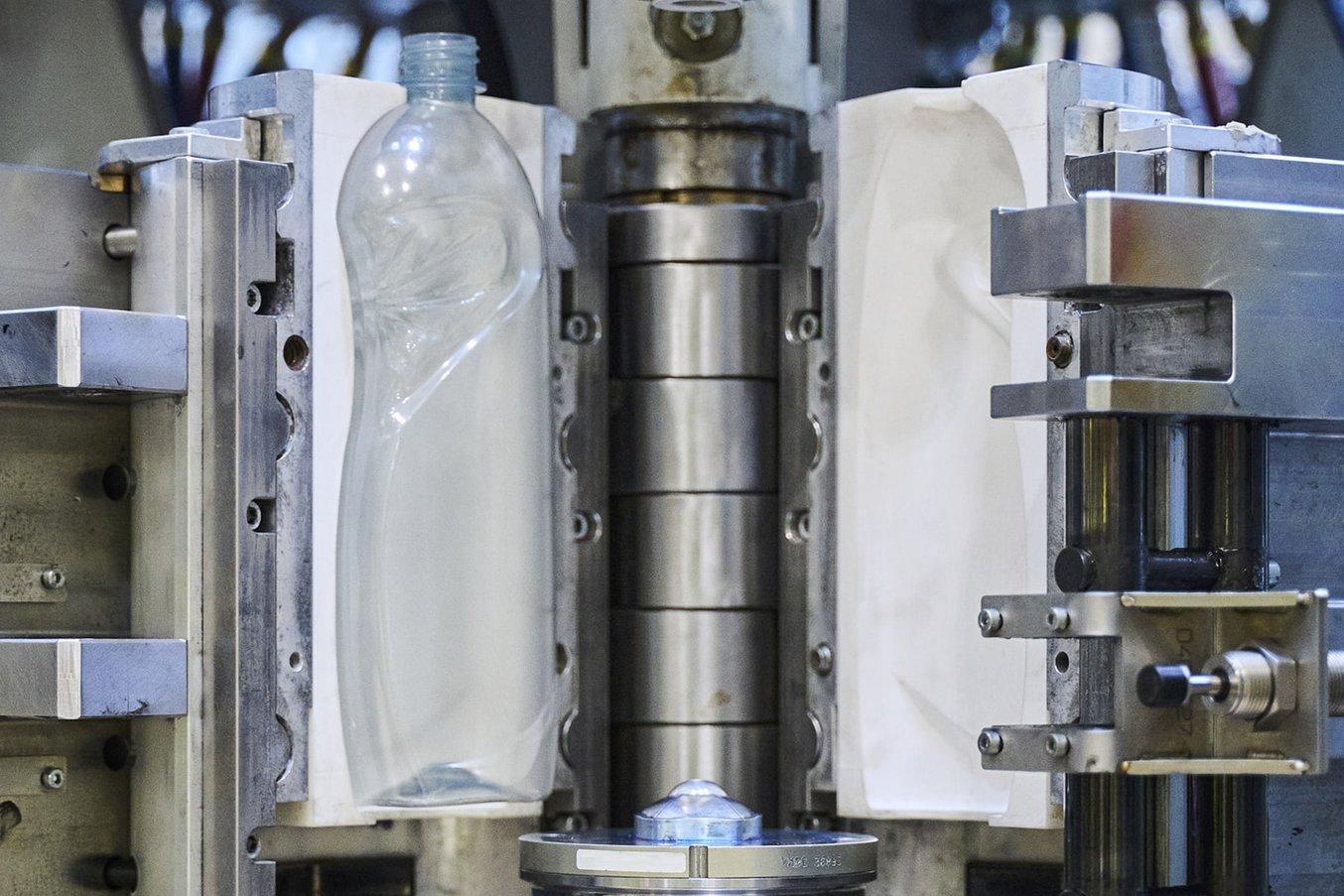
Mold 3D printed with Rigid 10K Resin for Unilever Slice 750 mL bottle installed onto the shell holder on the machine. The team can use the same process window as with a standard pilot mold, which allows them to reliably test the final process.
Rapid Tooling: Unilever Blow Molded Bottles
Unilever and Serioplast, use the Form 3L benchtop resin 3D printer and Rigid 10K Resin to quickly and efficiently produce molds for stretch blow molding (SBM) that can handle the pressure of traditional, industrial SBM machines.
Production Run of 200 units | Machined metal mold | 3D printed mold |
---|---|---|
Equipment | In-house CNC machine or outsourcing | Form 3L Rigid 10K Resin |
Pilot testing lead time | 6-8 weeks | 2 weeks |
Tooling cost | $2,500-$10,000 | $500-$1,000 |
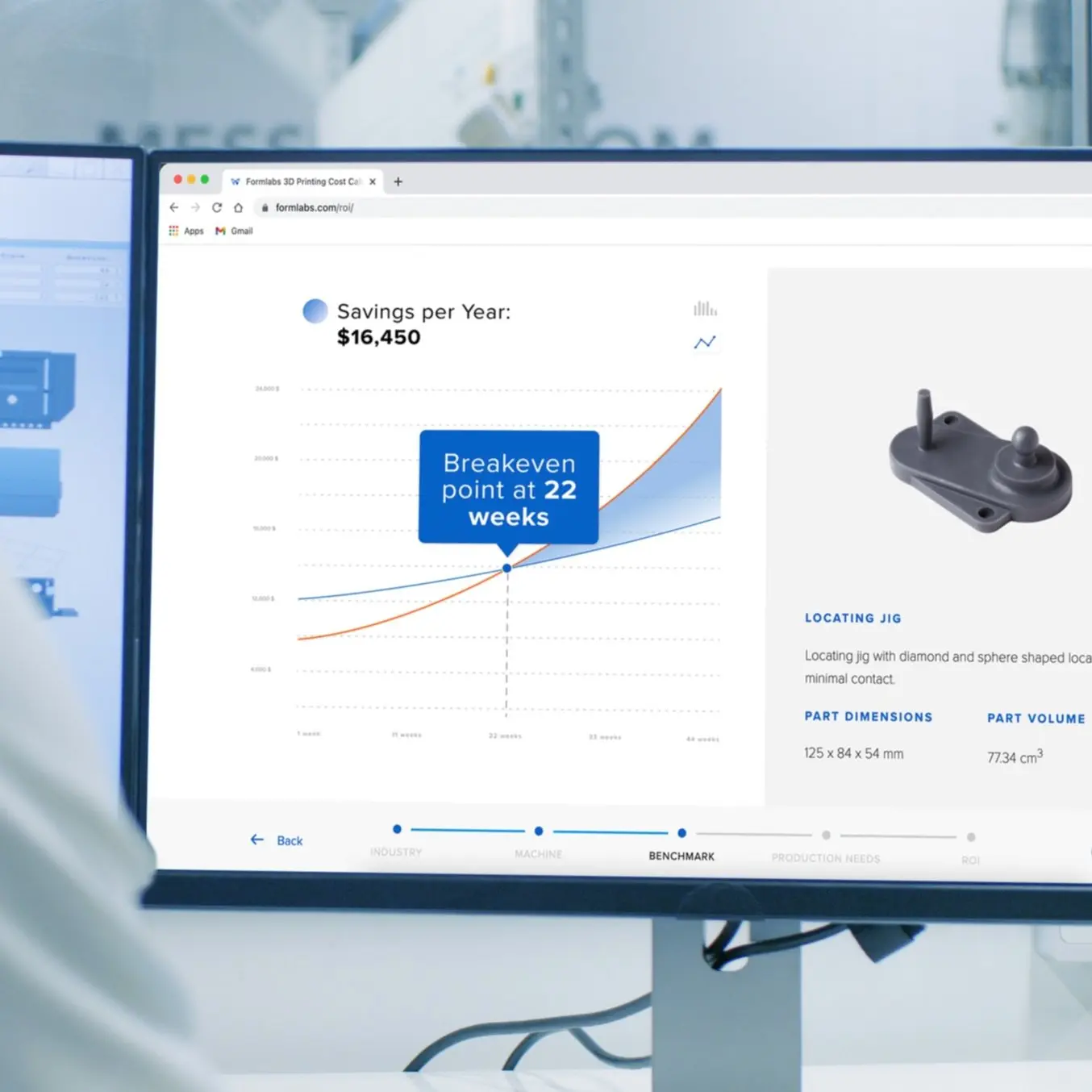
Calculate Your Time and Cost Savings
Try our interactive ROI tool to see how much time and cost you can save when 3D printing on Formlabs 3D printers.
Control Your Supply Chain
3D printing in-house can look different for different types of professionals. Many large businesses, such as Microsoft or Rivian, choose to operate internal service bureaus, where engineers, designers, and manufacturing teams request parts from a centralized lab. Other businesses, especially those that are design and iteration-focused with high degrees of CAD expertise in their workforce, prefer a decentralized approach with a printer on every designer’s desk. Accessible, affordable, desktop-sized machines like Form 4 make these types of workflows possible and can present agile solutions for a changing workforce and office environment.
Whether centralized or decentralized, 3D printing in-house gives employees greater control over their workflows, and reduces costs and uncertainties for the business as a whole.
Scale as Production Needs Increase
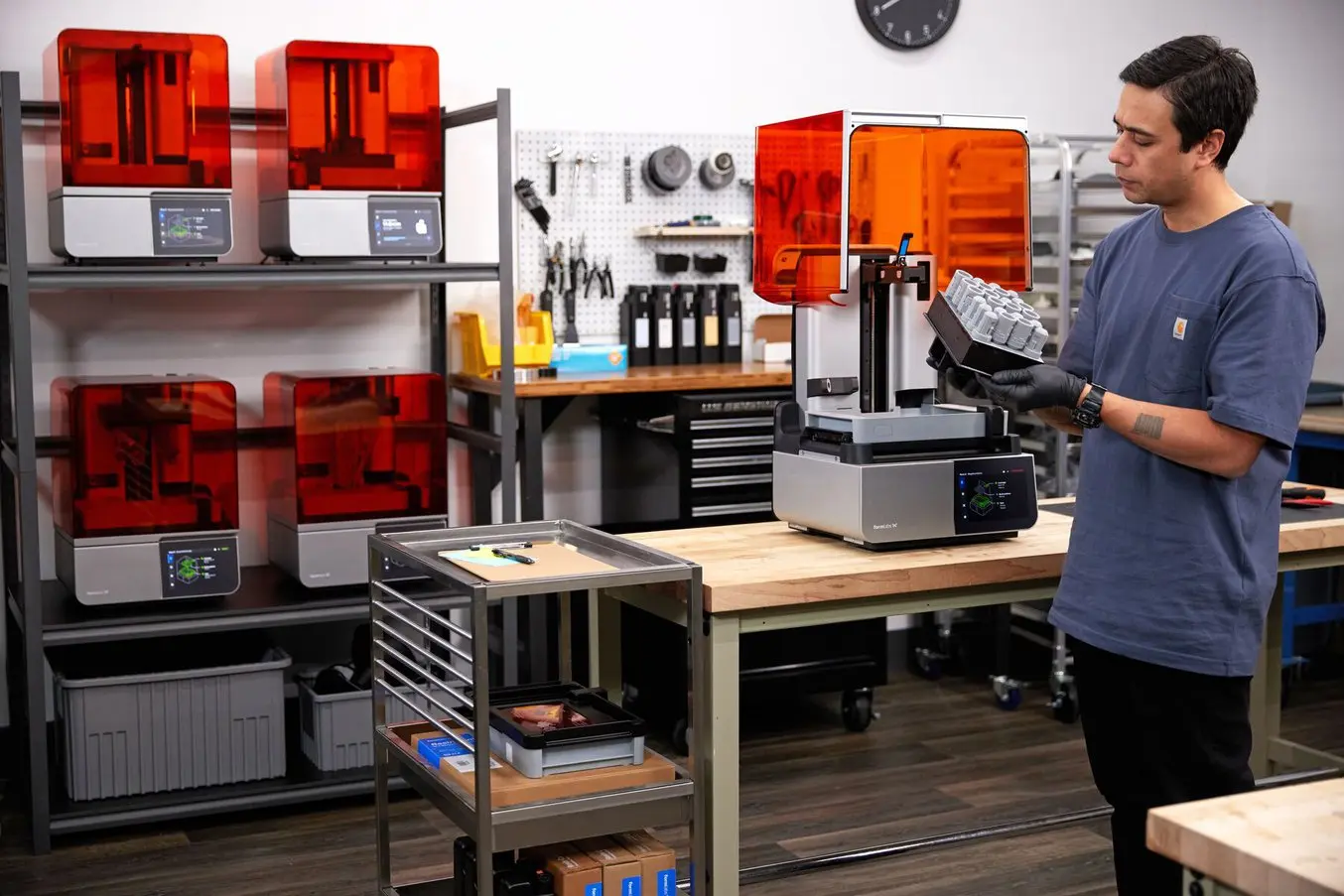
Desktop 3D printers like Form 4 are “plug and play”, so anyone can learn to use it in 15 minutes.
Depending on the number of parts and printing volume, investment into a small format 3D printer can break even within months. With small format machines, it’s possible to pay for just as much capacity as a business needs and scale production by adding extra units as demand grows. Using multiple 3D printers also creates the flexibility to print parts in different materials simultaneously.
To make managing multiple resin 3D printers easier, Formlabs customers have access to two software platforms. Dashboard is a free software platform that helps them monitor their printers and streamline management. For added capabilities and advanced management tools, Fleet Control leverages automation to automatically assign prints and make multi-printer management more efficient.
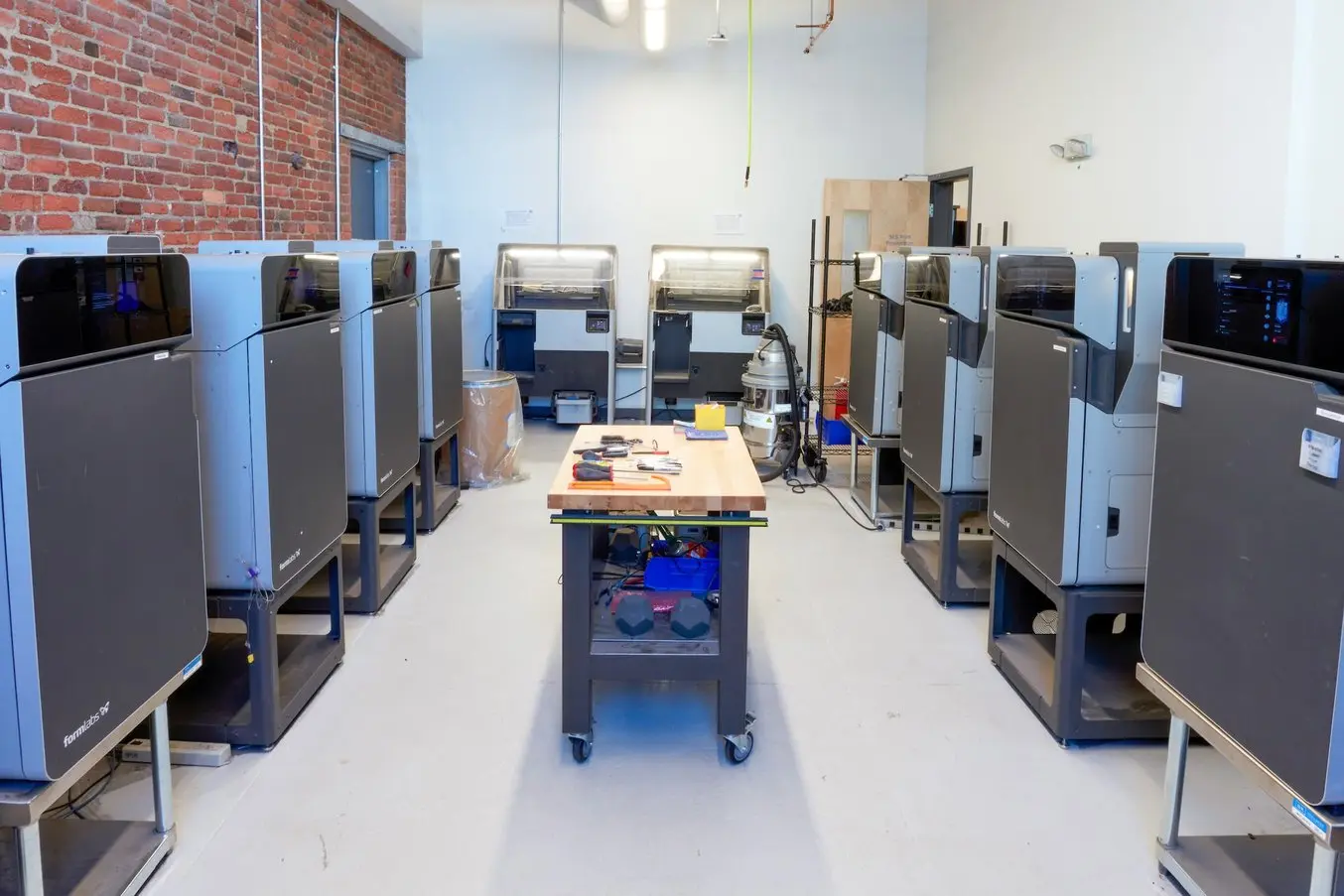
Managing 3D Printer Fleets
Managing multiple SLA and SLS printers doesn’t have to be complicated — any business can get a fleet of SLA and SLS printers up and running in just a day or two. By reviewing four different successful multi-printer scenarios, this guide will help you set up an efficient workflow for any volume or part type.
Get Started With In-House SLA 3D Printing
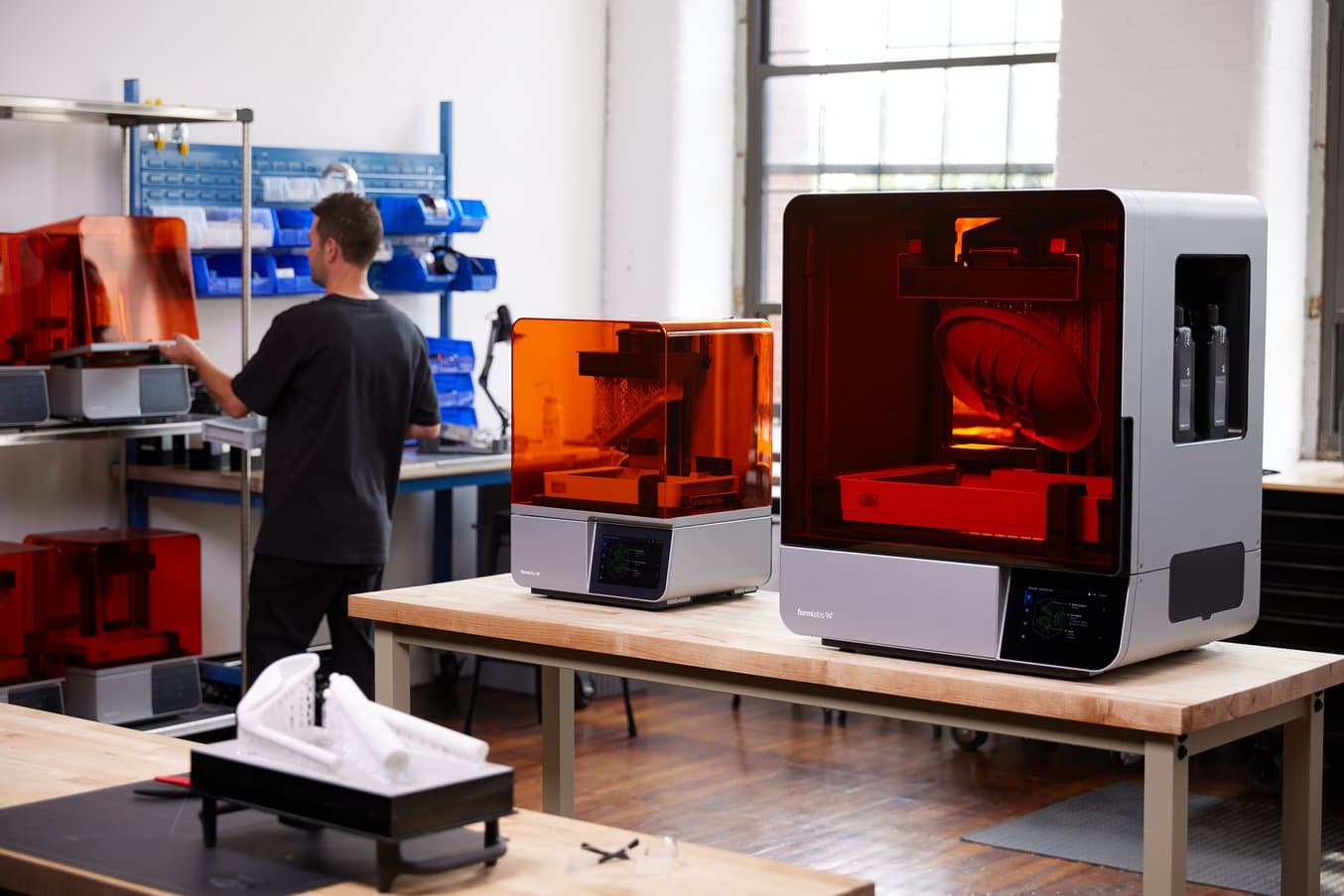
Form 4 and Form 4L are blazing fast masked SLA 3D printers that combine an industry-leading materials library, easy workflows, and a reliable, accurate print engine.
Formlabs offers desktop and benchtop SLA 3D printers that are fast and affordable and deliver high-quality parts with a wide range of material properties. The Formlabs resin 3D printing ecosystem is designed for ease of use and as few touchpoints as possible.
To continue exploring SLA 3D printing, start with feeling the quality of SLA for yourself: request a free sample 3D printed part in your choice of material to be mailed straight to your door.