How Diversified Metalsmiths Uses Clear Cast Resin for High-Accuracy and Clean Burnout Patterns

Though metal casting is still a $50 billion industry and directly provides 160,000 jobs in the United States alone, domestic foundry production is less than half the volume it was 10 years ago. The drop in production can be attributed to a multitude of factors, including cheaper offshore production, improved performance of metal alternatives, and the reality of fewer skilled technicians at each stage in the process. So, how do manufacturers in heavy industrial industries like aerospace, automotive, or energy source metal parts quickly and affordably?
The foundries that still supply these industries have thrived because they’ve adopted new methods of production and experimented with emerging technologies. We spoke with John Farr from Diversified Metalsmiths, Inc., to learn how Diversified has incorporated modern technologies into their metal casting workflow to reduce costs, improve lead times, and increase agility.
With the Form Series stereolithography (SLA) 3D printers and new Clear Cast Resin, Diversified has been able to print patterns in-house quickly and affordably, without changing up their casting workflow or relying on external providers.
“Our main reason for purchasing the 3L was pattern cost… Even amortizing the 3L and associated equipment, we will at a minimum break even on costs for our current order, and save over $200 per part on upcoming orders. There is very little difference in our process, both before and after casting, between the PMMA and Clear Cast Resin SLA patterns."
John Farr, VP of Technology, Diversified Metalsmiths
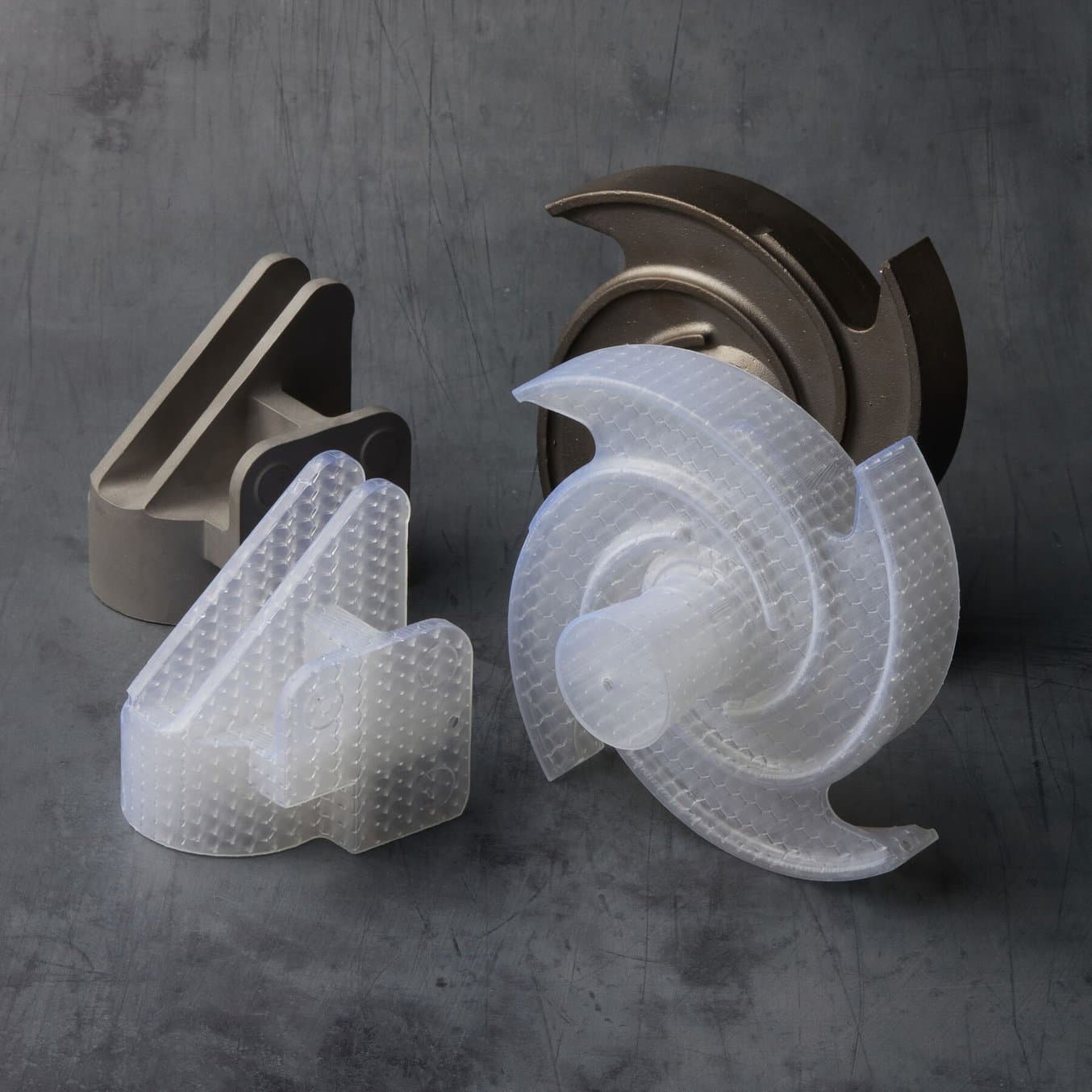
Precision and Cost-Efficiency in Casting: Leveraging 3D Printing for Metal Parts
This webinar will walk you through the methods by which several established foundries were able to cast metal parts using patterns 3D printed on Formlabs’ 3D printers. Learn how foundries are cutting costs, reducing lead times, and improving the quality of their metal parts by integrating Formlabs’ Clear Cast Resin and Materialise Magics’ Lattice with traditional casting methods.
Diversified’s Diverse Client Base
Diversified operates as a ‘job shop’ more than a high-volume facility, and they’re not alone. Many of the smaller foundries across the country are producing at similar volumes with a steady clientele who rely on them for high accuracy, quick turnaround parts. “Our customers don’t go out for quotes to anyone else, they know we can deliver exactly what they need,” says Farr.
When low- to mid-volumes of metal parts are necessary, with strict tolerances and short lead times, Diversified is the place to go. About 70% of their order volume is for fluid control applications — parts like impellers, pump housings, valves, drains, grates, and industrial fluid components. The other 30% of their work ranges from drone manufacturing to automotive components, medical devices, and even fine art.
Though volume can vary slightly, each month Diversified produces about three tons of castings. They operate several furnaces for different jobs; most are small enough to utilize their 400-pound furnace, but they have access to an 1100-pound furnace for larger parts.
One of Diversified’s consistent orders is a titanium impeller with an annual order volume of 100 parts. As titanium costs have risen, Diversified has had to look for alternative ways to reduce costs in other parts of the workflow. SLA 3D printing their patterns has been one of those methods to successfully offset the rising cost of titanium.
Merging the Traditional and the Modern
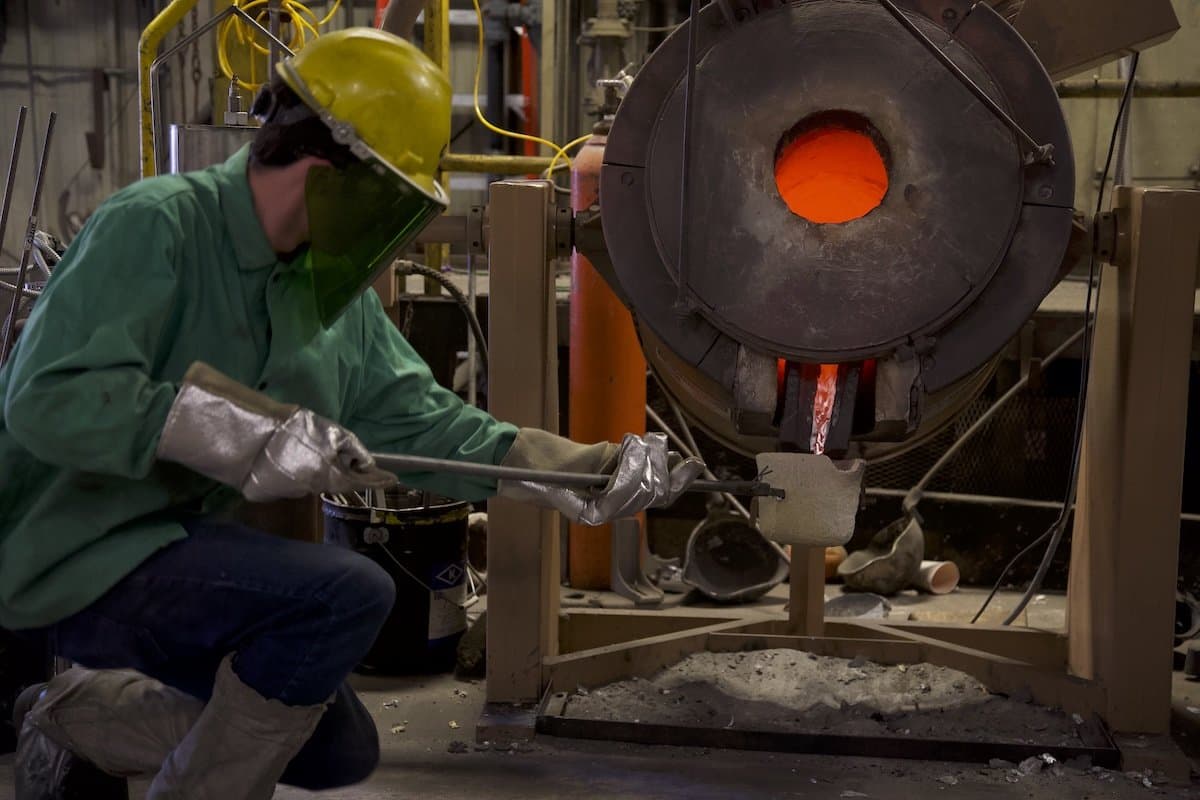
The industrial investment casting industry still relies on traditional processes for many parts of the workflow, like the pouring of molten aluminum into hollow investment, shown above.
Metal casting is a very traditional industry in some ways — at its core, the workflow has remained much the same for thousands of years. In other ways, foundries have been pioneers in modern manufacturing. At Diversified, Farr and his colleagues were some of the earliest adopters of 3D printing technology. “We’ve been involved in some form or another with 3D printed investment patterns since, I would say, the mid ‘90s,” Farr says.
Diversified first began to use wax 3D printers to create patterns when making traditional wax patterns (injecting liquid wax into hollow metal tooling) became prohibitively time-consuming and expensive. One particular project involved the use of four separate tools, including tools used to inject soluble wax cores, wax chills, soluble wax chills, and the fully assembled parts. All of the tooling had to be custom-made, shot with wax, assembled, and (frequently) reworked to eliminate any imperfections. “The man-hours it took to make a single wax investment pattern was prohibitive. It was taking the better part of a day, so from a labor standpoint, that was shortlived,” says Farr.
The Diversified team introduced wax printers from 3D Systems and thermojet 3D printers and integrated them into their workflow as a one-to-one replacement for the traditional injection workflow. Years later, a customer introduced them to a new product — 3D printed PMMA polymers on a VoxelJet binder jetting printer, which burned out cleanly and had more dimensional stability than the wax printers they had been using.
As costs began to rise everywhere in the industry, even outsourcing to another polymer 3D printer became too expensive — each pattern cost Diversified about $300, and to bring that machine in-house would cost them well over six figures.
“We had to start looking for something else as soon as those prices went up. We looked at FDM and SLA, and first went with five FDM printers because they had soluble support structures. We didn’t need anything different at the time,” says Farr.
But when a customer approached them about an annual 100-impeller order, Farr’s team needed a new solution, and they reached back out to Formlabs about the Form 3L large format SLA 3D printer.
Metal Casting With the Formlabs Ecosystem
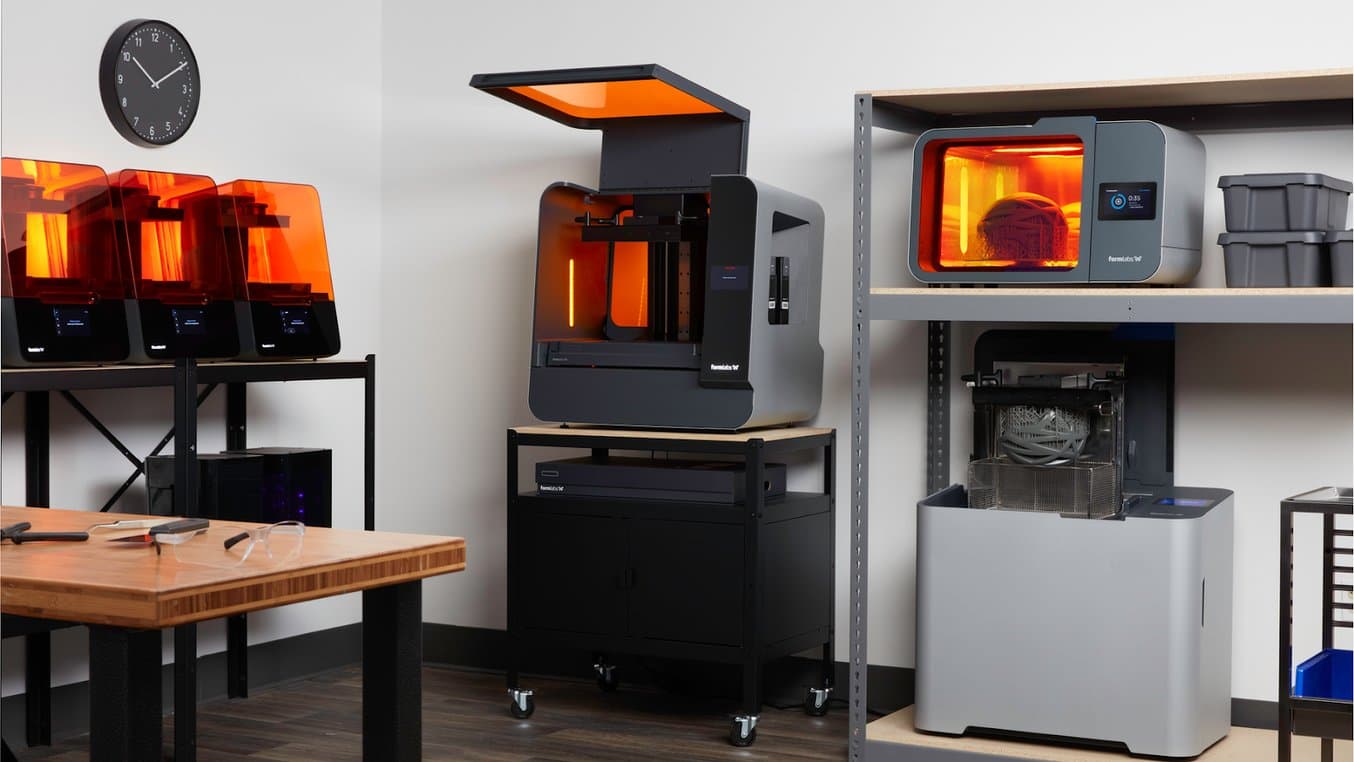
Form 3L, and post-processing solutions Form Wash L and Form Cure L, offer a larger form factor than many hobbyist-level desktop 3D printers, along with an accessible workflow and extremely high print quality.
There were several specs Diversified needed to hit in a new 3D printing solution — a material with a clean burnout, a reliable and easy-to-use ecosystem, and the size necessary for their impeller project. “The whole ecosystem and support system made sense to us. The fit and finish of the printers, the software, it seems better than everything else in the price point by a long shot,” says Farr. After having a test part printed by the Formlabs team, Farr found that Form 3L and Clear Cast Resin could slot immediately into their workflow — they didn’t need to change burnout temperatures, slurry formulation, or part design. The patterns made on Formlabs printers even allowed a slight process improvement because of the ability to add gating features directly into the parts.
“The Clear Cast parts slotted straight into the workflow. One nice thing, we can do the lineups for the gating printed right into the parts, which we couldn’t do with PMMA."
John Farr, VP of Technology, Diversified Metalsmiths
The workflow proved to be an easy switch, so the last thing to verify was the burnout process. Here too, Clear Cast Resin proved to be an effective replacement for their outsourced PMMA patterns — at a fraction of the cost. “The burnout is right in line with the PMMA — we treat it just like the PMMA, no issues there,” says Farr.
For a single impeller 3D printed pattern on Form 3L in Clear Cast Resin, Diversified is spending about $80 on materials and labor. Compared to their $300 of outsourcing costs, they’ve been able to make a fast ROI on the printer, while expanding their use cases and finding new applications. By printing just three times a week, they’ve paid off the printer in less than nine months.
Outsourced PMMA Pattern | Clear Cast Pattern In-House | |
---|---|---|
Cost | $300 | $80 |
Lead Time | 2 weeks | 24 hours |
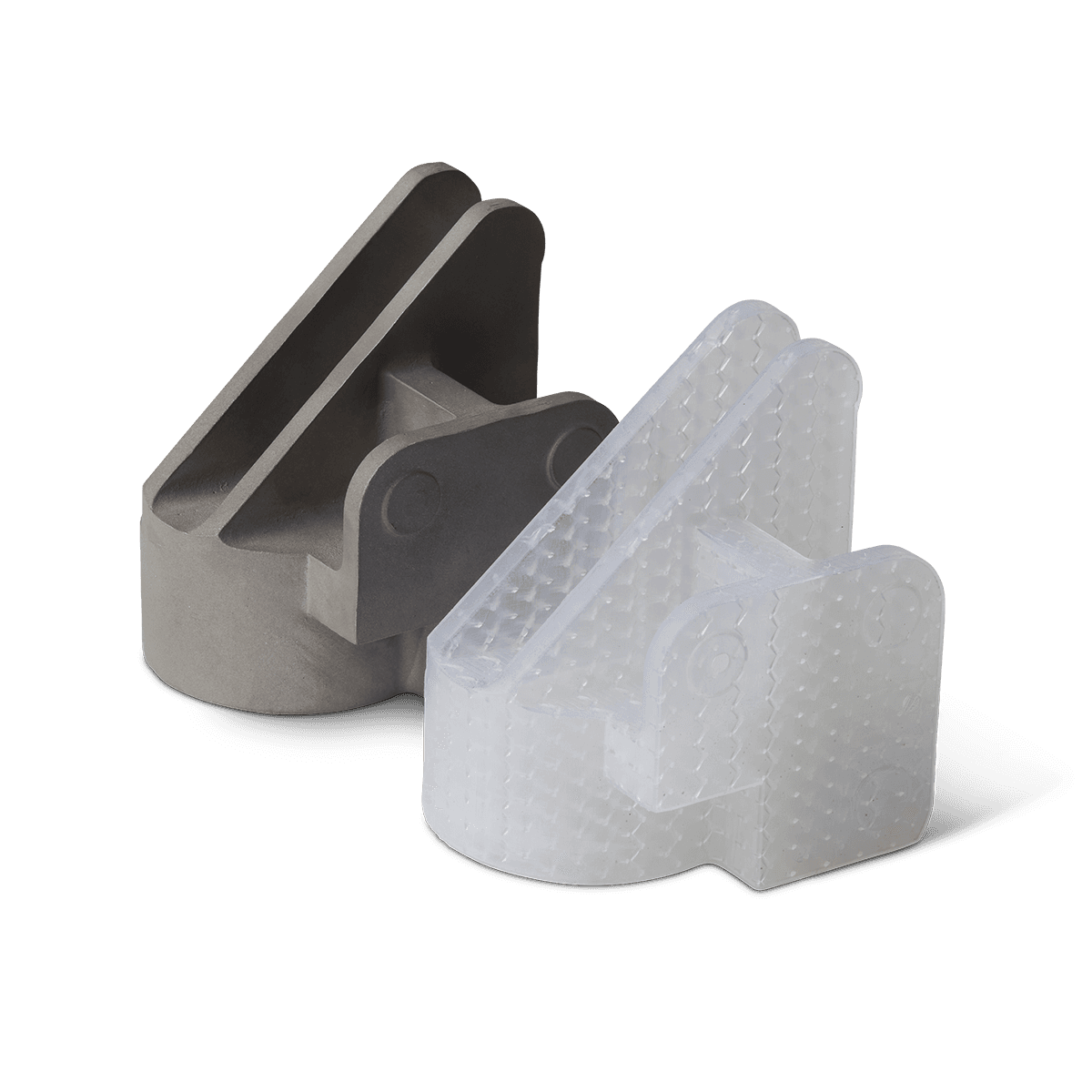
Industrial Investment Casting With 3D Printed Patterns Using Formlabs Clear Cast Resin
This white paper presents the methods by which several established foundries were able to cast metal parts using 3D printed patterns produced by Formlabs’ stereolithography (SLA) 3D printers.
The Perfect Tool for the Right Volume
Investment casting patterns are sacrificial, and 3D printing every pattern in a production run isn’t always the right solution when order volumes increase. There is, however, a ‘sweet spot,’ of volume where Form 3L and Clear Cast Resin are the ideal tools to leverage. “If a customer called and requested a thousand of these parts, then at that point we do tooling. But tooling for something like this could be $30,000 so you need to make a lot of them to justify that cost,” says Farr.
Having a printer and material in-house like Form 3L and Clear Cast Resin makes it possible to reduce overall labor time, and get the complex geometries and dimensions right the first time.
“Sand patterns aren’t nearly as accurate as investment casting, you want the almost perfect geometry of the 3D printed investment cast process because it saves time in the pre-print and the post-processing labor, where you might have to grind something else down. The amount of time saved with 3D printing where I push a button and go off to do something else, then skip the machining and hand-work after the cast, will make up for the cost of 3D printed patterns,” says Farr.
Getting Started With Clear Cast Resin
3D printing has been used for investment casting workflows for decades. Though it’s not right for every situation, advances in material science and print accuracy have made it a more effective tool for certain jobs.
The Form Series SLA 3D printers and Clear Cast Resin offer a ‘set it and forget it’ workflow as well as industry-leading accuracy and clean burnout. By reducing labor in the pre-print process as well as mitigating grinding or hand machining parts after the fact, these 3D printed patterns lower your overall cost per part and introduce new capabilities without requiring any change in workflow.
To get started with Clear Cast Resin, order now. To learn how you can start producing metal parts with 3D printed investment casting patterns, download our white paper.