Creating Patient-Specific Cutting Guides With ISO Certified Biocompatible Materials
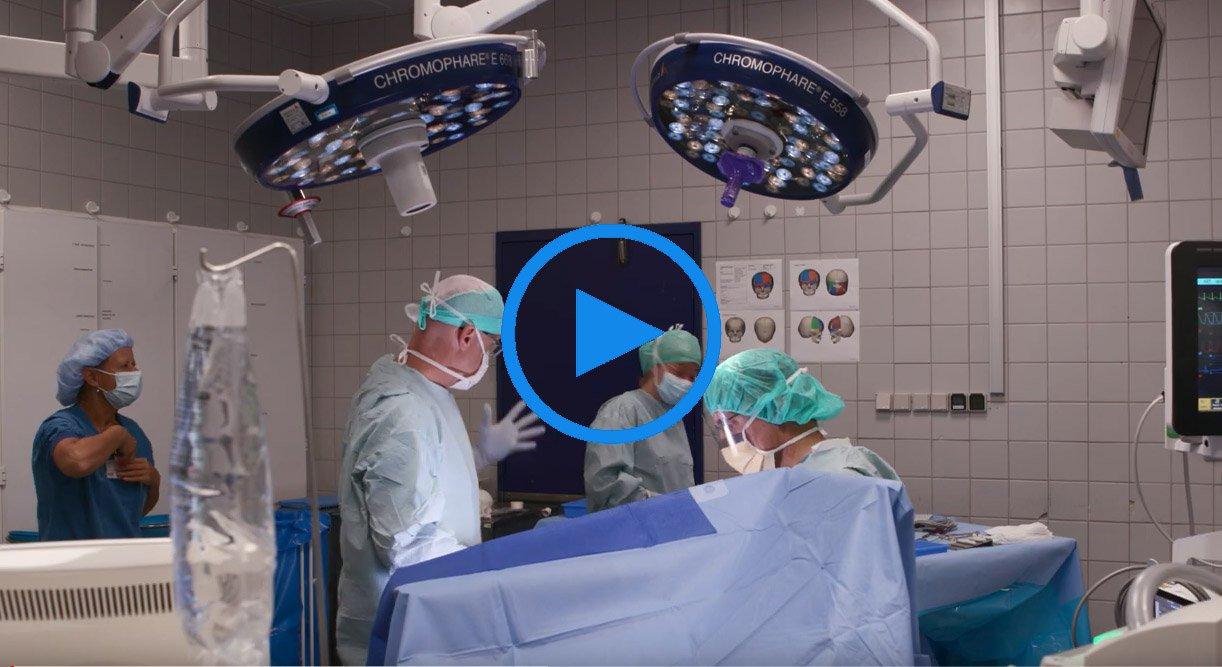
Around the world, hospitals are rapidly turning toward in-house 3D printing to improve preoperative planning, operation times, and patient outcomes. Joakim Lundtoft Lindhardt, from the 3D Innovation Center at Aarhus University Hospital in Denmark, is a leading engineer implementing 3D printing across the hospital. His lab serves a diverse set of needs, with a special focus on patient-specific cutting guides to help improve patient and surgical outcomes.
The lab assists in the treatment of these patients on a regular basis. Last year, an infant arrived at Aarhus University Hospital with a cranial deformity. Thus began a process to assist in the highly-skilled procedure that was to follow; the team generated digital scans of the skull, and sent them to Lindhardt. He went to work analyzing the skull, and turned to BioMed Clear Resin to create cutting guides to help the surgeons during surgery. BioMed Clear Resin is a rigid, transparent material for biocompatible applications requiring long-term skin or mucosal membrane contact as well as bone, tissue, and dentin contact. The material is also validated in accordance with ISO 18562, allowing for gas pathway applications in healthcare and is one of the most validated biocompatible SLA resin on the market today. This makes it appropriate not only for cutting guides, but a host of different medical applications in healthcare. The 3D scans are originally made for diagnostic purposes; the team is able to re-purpose them for 3D work. This means less scans, and a reduction of radiation exposure.
Lindhardt, referring to the case, said that, “from my perspective, using 3D printing is a win for both the patients and the health care system. Now, we have an exact copy of the patient’s cranium [skull] before the patient’s surgery. It improves planning and helps us create predictable results during surgery.”
In this post, we hear about why Lindhardt thinks in-house 3D printing is vital for hospitals, how he approaches creating surgical guides, and what’s next for his printing division.
Manufacturing Medical Devices the Hospital Simplified With (ISO) Certified Biocompatible 3D Printing Materials
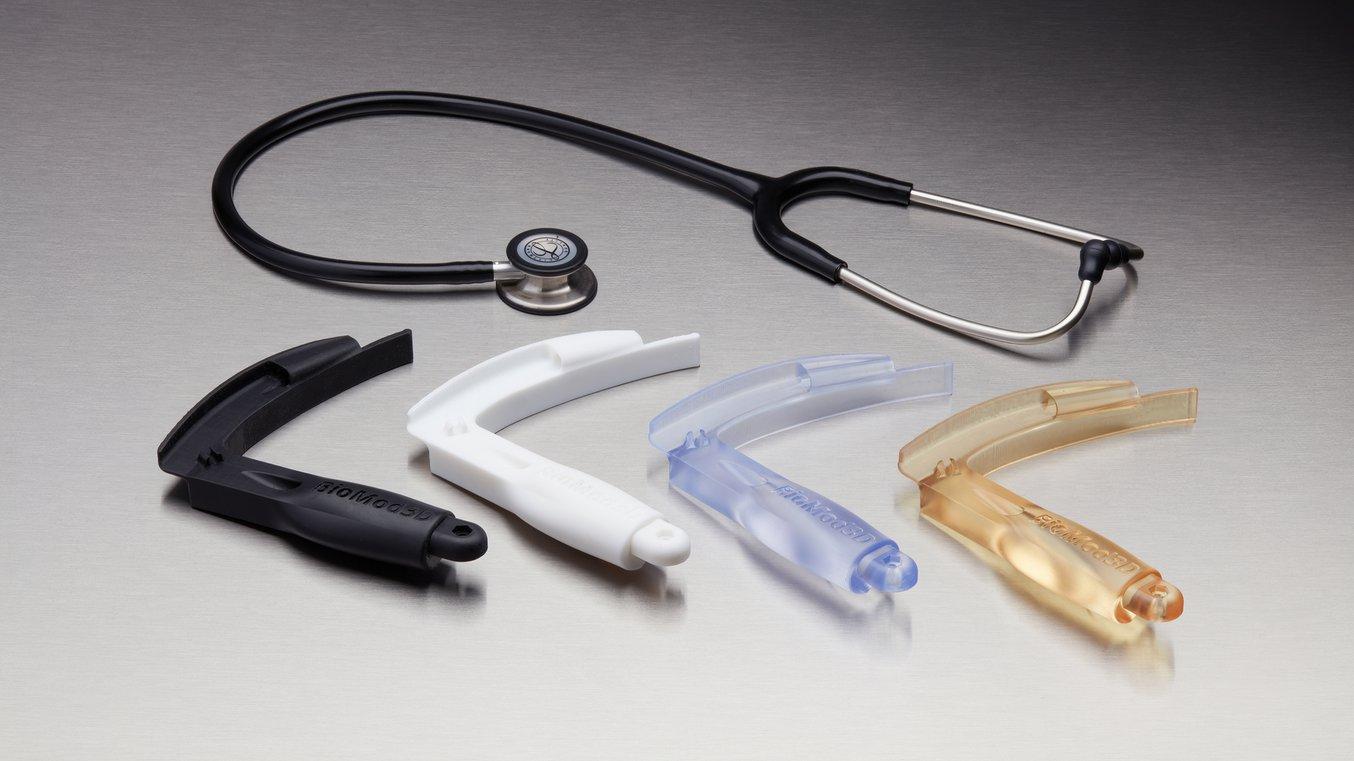
BioMed Resins from Formlabs are designed for healthcare professionals seeking medical-grade materials.
Aarhus University Hospital started with a simple investment in 3D printing, hiring Lindhardt for a one-year position. He was instructed to set up the basic infrastructure for the in-house printing of cutting guides with a focus on mandible and skull reconstruction. According to Lindhardt, “We very quickly realized that the potential for having an in-house unit was quite vast. And also that it required some kind of speciality knowledge that wouldn't be found elsewhere at the hospital. We realized that we saw a knock on the door effect where other surgical specialties or surgeons would ask, ‘hey if you can do that for them, can you do this for me?’ We started out having the Formlabs Form 2 that carried out all our printing needs on that one machine. Then we obviously stayed with [Formlabs] SLA printers now, with Form 3Bs for cutting guides.”
Formlabs medical materials, like our BioMed Resins, are designed for healthcare professionals who are seeking medical-grade materials for a wide range of applications where performance and biocompatibility are critical. Materials in our BioMed Resin family are developed and manufactured in an ISO 13485-certified facility and are compatible with common disinfection and sterilization methods.
The release of additional BioMed Resins in 2022 led to an acceleration in use of SLA printers at Aarhus University Hospital, and ISO biocompatibility certifications were the driving factor. Lindhardt told us that, “the ISO certificates make it so much easier to implement into our QMS system. And really makes it a no-brainer to say we use these materials that fulfill ISO requirements.”
BioMed White Resin | BioMed Black Resin | BioMed Clear Resin | BioMed Amber Resin | Tough 1500 Resin | |
---|---|---|---|---|---|
USP <88> Class VI | ✓ | ✓ | ✓ | ||
USP <151> Pyrogen and ISO 10993-11 | ✓ | ✓ | |||
ISO 10993 | ✓ | ✓ | ✓ | ✓ | ✓ |
ISO 18562-1,-2,-3,-4 | ✓ | ||||
ISO 13485 | ✓ | ✓ | ✓ | ✓ | |
ISO 14971 | ✓ | ✓ | ✓ | ✓ |
He continued, “Over time, we have changed materials quite a few times. We started with the LT Clear Resin and then moved over to Surgical Guide Resin. But currently, we are using BioMed Clear Resin for our cutting guides, which is our most frequently used material.”
Lindhardt added that, “One thing that I think is sort of unique about us is that we are a hospital-wide unit and so we apply our services throughout the hospital. We see other printing solutions that sit within a specific department and are not shared. What we've done is that we've expanded the potential use cases, which allows us to have a much broader impact at the hospital.”
One of the easiest ways to justify investment in an in-house 3D printing unit for hospitals is to make the case for a shared hospital-wide unit serving multiple functions. The versatility of 3D printing lends itself to an easily provable return on investment — from cutting guides to preoperative planning models, fixing broken or missing machine parts, and more.
“What’s great about 3D printing is the ability to generate patient-specific models and patient matched tools. We can produce complex geometries, which is what the body consists of,” added Lindhardt.
Solving Complex Cases With Patient-Specific 3D Printed Models and Surgical Guides?
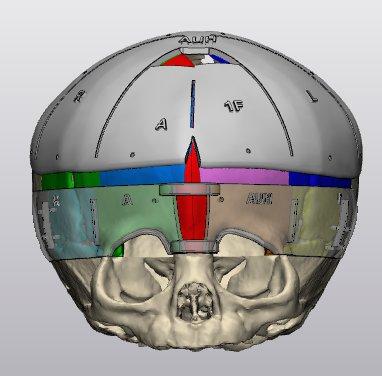
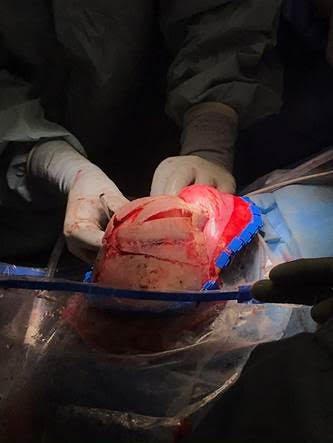
At the beginning of this article, we mentioned the case of an infant who was suffering from a cranial deformity. 3D printing with Formlabs technology allowed Lindhardt and his team to better understand and respond to the patient’s specific needs, and the surgery was a resounding success. This surgery is one more example of how 3D printing is enabling medical professionals to confidently address surgical cases with positive outcomes that, in the past, were seen as too difficult or risky.
Lindhardt told us that, “[predictable results] are definitely a part of the benefits of 3D printing. Going back to the infant skull case, another benefit of visualizing the 3D print was the eight fragments floating around. Without the use of 3D printing, you would never have the audacity as a surgeon to move forward with an eight-fragment surgery, you simply wouldn't be able to put it together and have symmetry and functionality. So having the use of 3D printed [cutting guides], you're able to have a much more refined surgery, ultimately leading to better patient outcomes.”
Lindhardt continued, “that's the main benefit. Obviously, we also see a reduction in surgery time overall. When we move tissue from one place of the body to another place, and reconnect the blood supply, the shorter amount of time that the tissue is without blood, the better for healing and final outcomes. With the use of cutting guides, everything is identified in minutes.”
Lindhardt has seen repeated examples of risky cases the hospital felt confident taking on, due to their ability to print patient-specific cutting guides with BioMed Clear Resins. He said that, “the patient may have been offered surgery anyway, but now we can just carry out the surgery, in a much better position. Actually, I'm currently working with a child, he’s 14 years old, and he broke his forearm, and it has stopped growing. I'm unsure that the patient would have been offered surgery simply because the surgeons would be hesitant as they risk doing more harm than good. But with patient-specific 3D printed guides, the surgeons have a higher chance of actually aligning things the way they intend to.”
Johan Blomlof, Associate professor, Consultant Craniomaxillofacial Surgeon, said that, “during the past five years, we haven’t had to redo surgery on any children when using this [3D printed guides] method.”
Looking to Learn More About Medical 3D Printing?
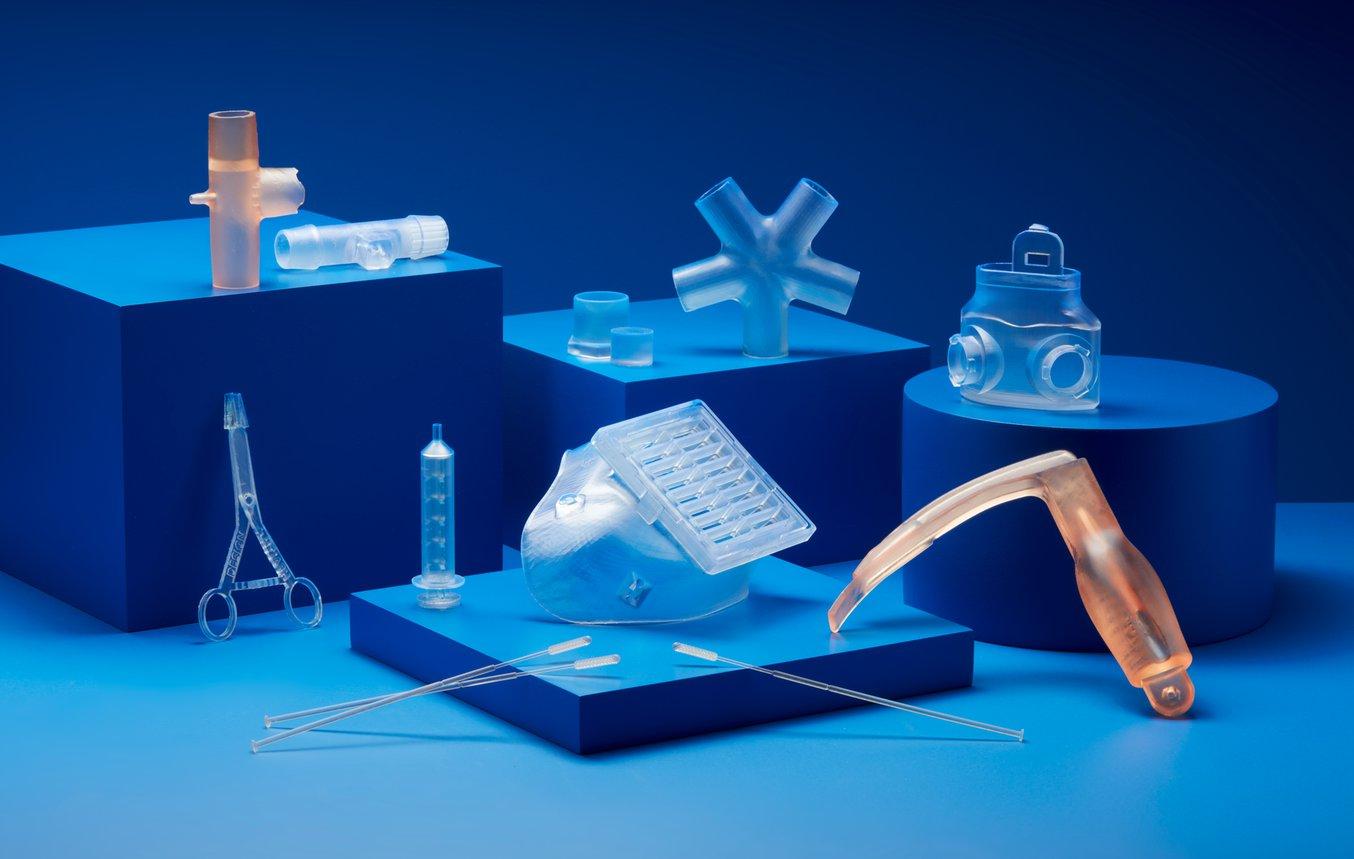
Lindhardt and the team at Aarhus University Hospital have established themselves as a leader in the point-of-care use of 3D printing to bring innovation and consistency to the surgical room.
Hospitals around the world are experiencing a major uptick in the adoption of 3D printing in just the past few years. Many, like Aarhus University Hospital, are starting with teams of one or two before expanding 3D printing to be a hospital-wide service to reduce surgery times, increase patient outcomes, and more. “We are constantly seeking to explore and develop 3D printing and 3D technologies in the healthcare system,” Lindhardt said.
To learn more about how 3D printing can be used for medical applications and hospitals, visit our medical page. Or, reach out now to talk to a Formlabs medical specialist.