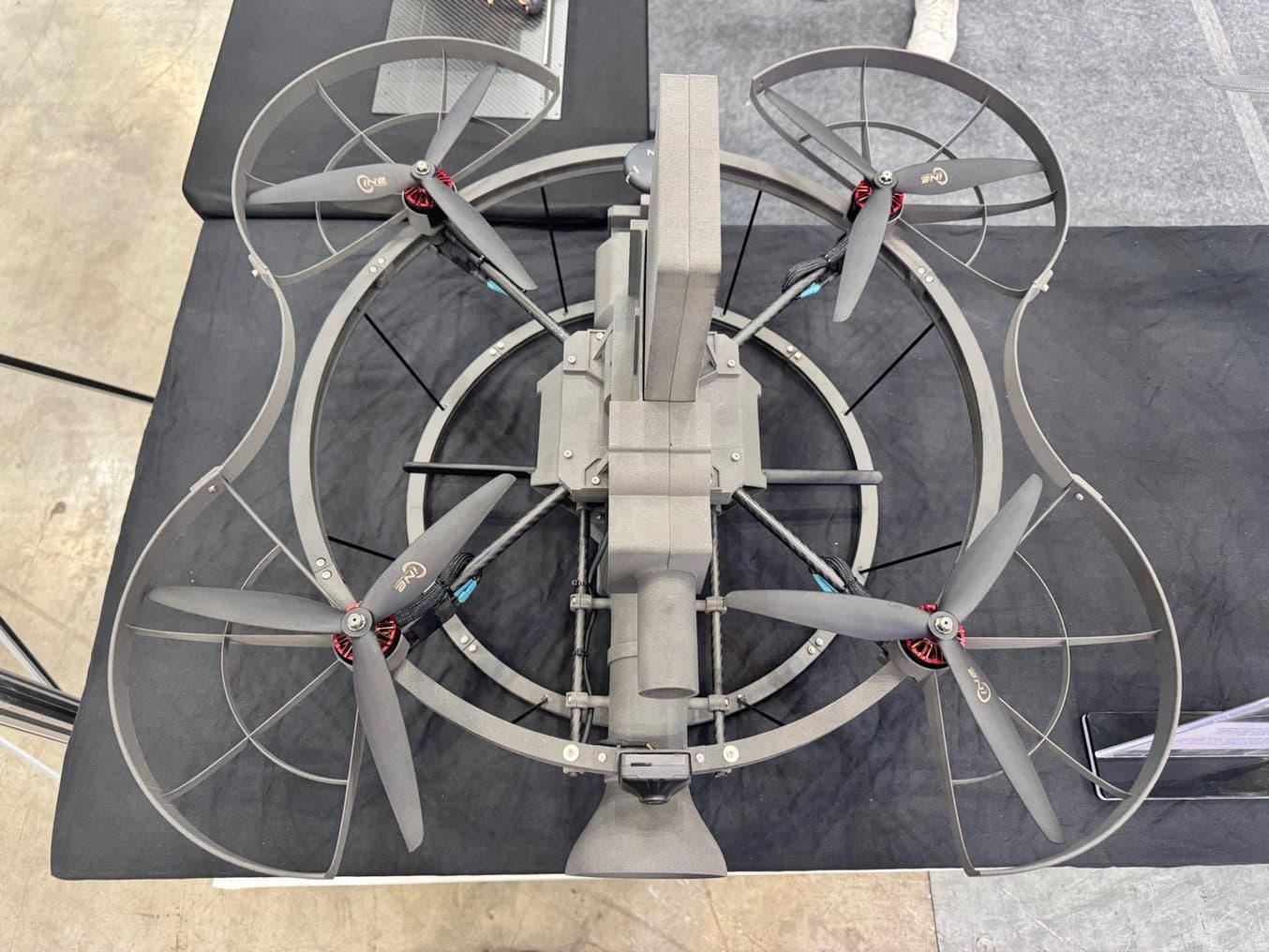
ION Mobility is a South Korea-based drone manufacturer that designs and builds advanced UAV systems tailored for public safety, defence, logistics, and industrial use. Their drones are deployed in real-world missions — ranging from surveillance to emergency response — equipped with HD cameras, thermal imaging, and secure communication systems. With the rise of urban air mobility (UAM), ION is also developing AI-powered autonomous flight systems, enabling reliable and efficient drone operations across complex environments.
Bringing these innovations to life, however, demands a manufacturing process that’s as fast and flexible as their technology. The ability to iterate quickly, produce high-performance components, and adapt to new design challenges is essential in this highly competitive industry.
Legacy Manufacturing Bottlenecks
Before adopting 3D printing, ION Mobility relied on outsourcing their drone parts to external suppliers using traditional machining methods. Producing components this way meant carving plastic blocks through subtractive manufacturing, which introduced a number of bottlenecks. Manufacturing cycles were slow, especially when design revisions were needed, and the cost of iteration quickly added up. Conventional techniques made sense for mass production but fell short when it came to low-volume, high-complexity parts — exactly the type needed for lightweight, mission-ready UAVs. ION needed a new solution — one that could cut production time and costs while delivering uncompromising performance.
From Bottleneck to Breakthrough With the Fuse 1+ 30W
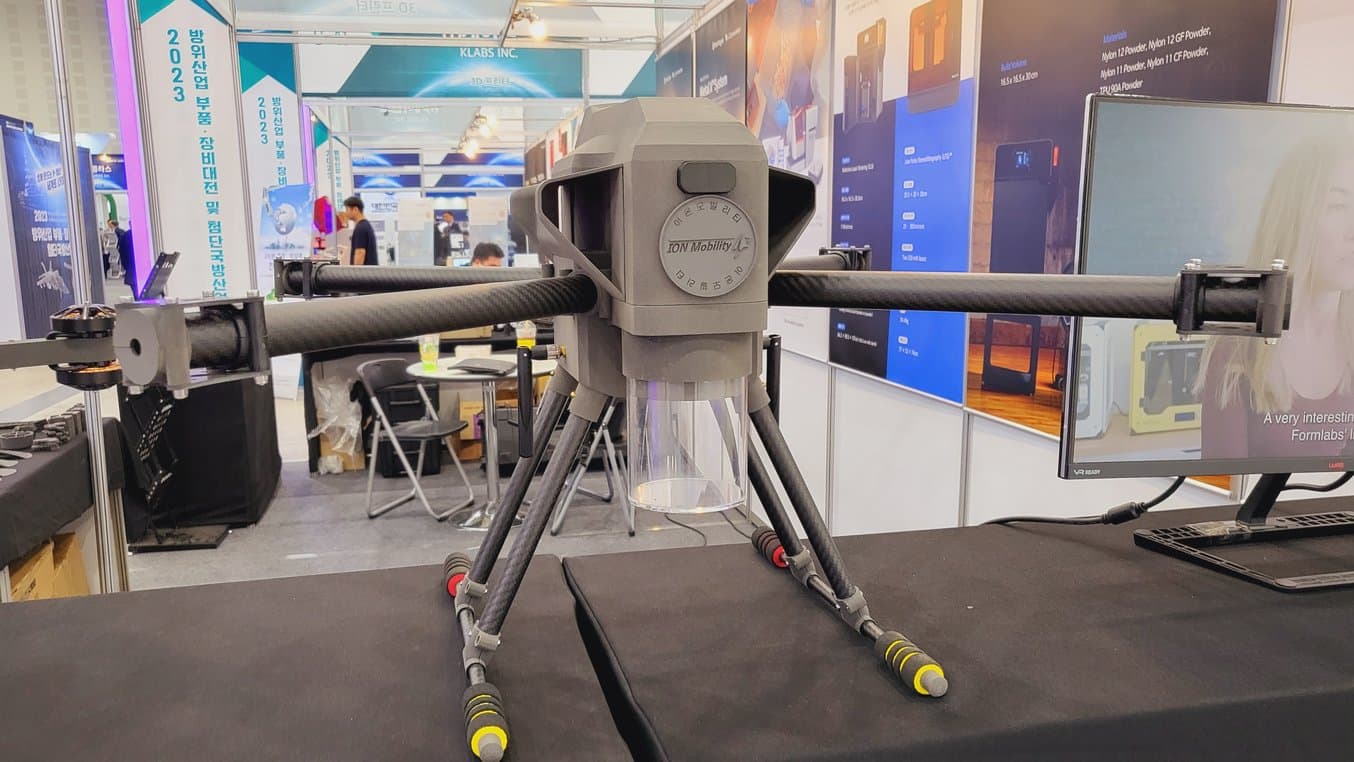
ION Mobility's drones are able to carry heavy payloads and their main body enclosures are strong, durable, and lightweight, all because of SLS 3D printing and Formlabs' advanced SLS powders like Nylon 12 GF Powder.
To overcome these challenges, ION Mobility brought SLS printing in-house with the Formlabs Fuse 1+ 30W. The team needed a system that could deliver end-use parts quickly, support complex geometries, and enable on-demand iteration. With the Fuse 1+ 30W, they found the right fit. The printer allowed ION’s engineers to complete standard jobs in as little as seven hours, while even high-density overnight builds could be completed in just fourteen. Thanks to selective laser sintering (SLS) 3D printing, there was no need for support structures, making it easy to print complex shapes without compromising strength or accuracy. Formlabs’ patented Surface Armor technology further ensured that each part came off the printer with a consistent, professional finish — ready to be tested or installed directly on the drone.
“With the Fuse 1+ 30W, we complete jobs in half a day, even with complex designs. What used to be time-consuming and expensive is now fast and cost-efficient.”
Sukchun Son, Senior Manager at ION Mobility
Optimising for Performance With Nylon 12 GF Powder
Drone design, however, is only half the equation. Material choice plays an equally crucial role in manufacturing reliable drone components. For ION, Formlabs’ Nylon 12 GF Powder offered the performance edge they needed. This glass-filled nylon delivers increased stiffness and thermal stability, making it ideal for UAV components that face extreme temperatures and structural loads. ION engineers were able to create lightweight, rugged drone frames, produce motor mounts with improved heat resistance, and fabricate mission equipment housings tailored to the precise tolerances needed for sensor integration. The result: flight-critical parts that perform reliably under pressure and in real-world conditions.
Real Results: Faster Development and Lower Costs
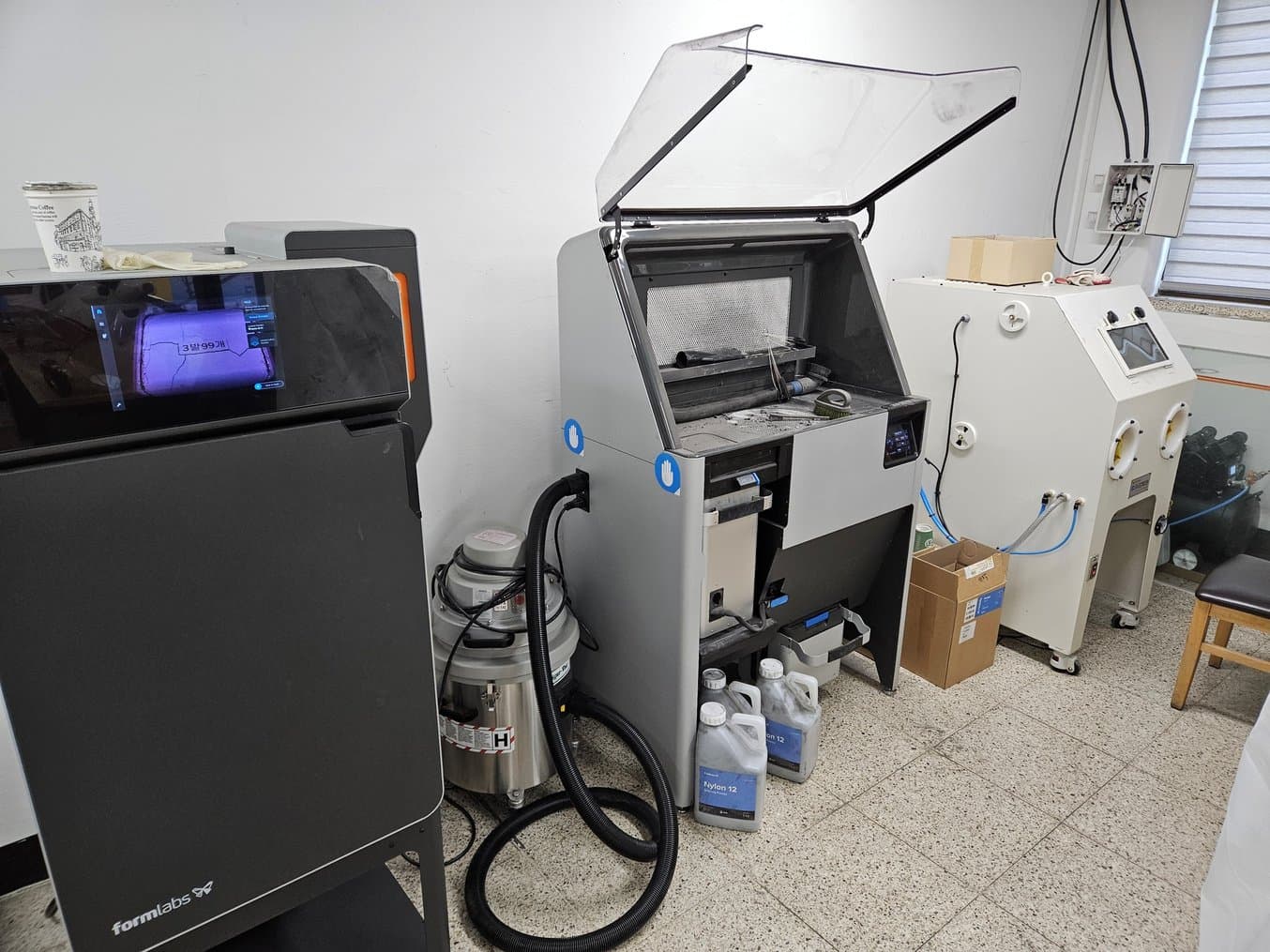
The Fuse Series SLS ecosystem is an accessible yet industrially powerful workflow that can produce high-quality parts without the cost, infrastructure, or footprint required for legacy powder bed technology systems.
Since implementing the Fuse 1+ 30W into their workflow, ION Mobility has reduced development costs by 60% and improved turnaround speed by 70%. Prototypes that once took weeks now take days — or even hours. Engineers can iterate freely without worrying about tooling costs, and parts that were previously too complex or expensive to manufacture are now printed on-demand. More than just a tool, the Fuse 1+ 30W has become a core part of the team’s innovation strategy.
According to the development team, the ability to fabricate custom, high-performance parts in-house has significantly elevated the capabilities of their tactical drone line. Where traditional manufacturing once set limits, in-house SLS printing is opening new design possibilities — and helping ION move faster than the competition.
Flying Beyond Limits
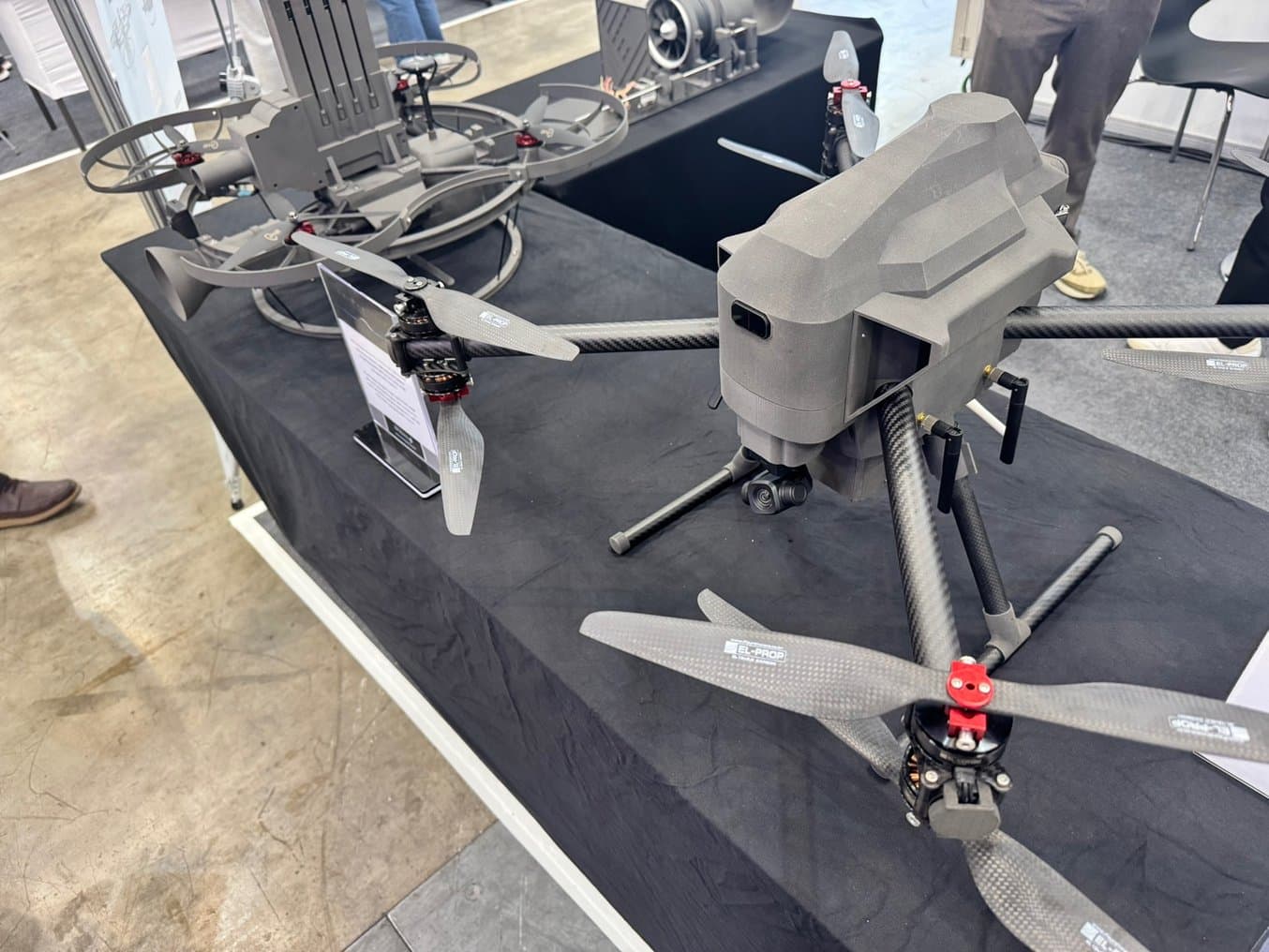
ION Mobility's drones are state of the art machines, so manufacturing them can be expensive. The Fuse Series has reduced R&D costs by 60% and increased their development speed by 70%, helping them reach market faster and stay ahead of their competition.
As demand for agile, rugged, and intelligent drones continues to grow, ION Mobility is poised to lead the way. Their investment in the Fuse 1+ 30W and Nylon 12 GF Powder has empowered the team to innovate without compromise and scale production with confidence. From prototype to production, they’ve gained full control over their development pipeline — delivering smarter, safer, and more effective drone solutions to the market faster than ever before.
“With traditional methods, production timelines were long and design changes came with high costs. Now, even the most complex parts are printed in half a day at a lower cost even.”
Sukchun Son, Senior Manager at ION Mobility
By pairing cutting-edge hardware with advanced materials and a forward-thinking approach, ION Mobility is redefining what’s possible in drone development — and showing what it means to build without limits. To learn more about building a drone with SLS, download our drone application guide.
To learn more about the Fuse Series, visit our page. To test the strength and durability of one of our SLS powders for yourself, request a free SLS 3D printed sample part.