Formlabs is proud to announce the Fuse Blast — the first affordable, industrial-quality cleaning and polishing solution for selective laser sintering (SLS) 3D printing — to complete the Fuse Series ecosystem with powerful, automated post-processing.
Adding Fuse Blast as a complement to Fuse Sift in the post-processing workflow reduces cleaning time to as little as 15 minutes overall — an 80% reduction in average hands-on labor time. The automated system blasts parts with media as they revolve in a tumbler, efficiently removing loose and semi-sintered powder from the surface to produce a smooth part with no powder residue. Fuse Blast also features an optional polishing system for customer-grade parts that present a smooth, semi-gloss, and dye-ready surface finish.
Starting at only $10,999, Fuse Blast packs a long list of powerful features for a fraction of the cost of comparable cleaning and polishing solutions, and aligns perfectly with our mission to bring reliable, industrial-quality tools to professionals at an accessible price point.
The Fuse Blast is not the only improvement to Formlabs’ SLS workflow — a series of new software features make SLS 3D printing with the Fuse Series ecosystem even faster and more efficient. The updates include an improved packing algorithm for 42% less waste, 30% faster print speed with Nylon 12 Powder, and fine feature preservation for robust intricate designs, so that your workflow includes less time spent waiting and more time on value-added tasks.
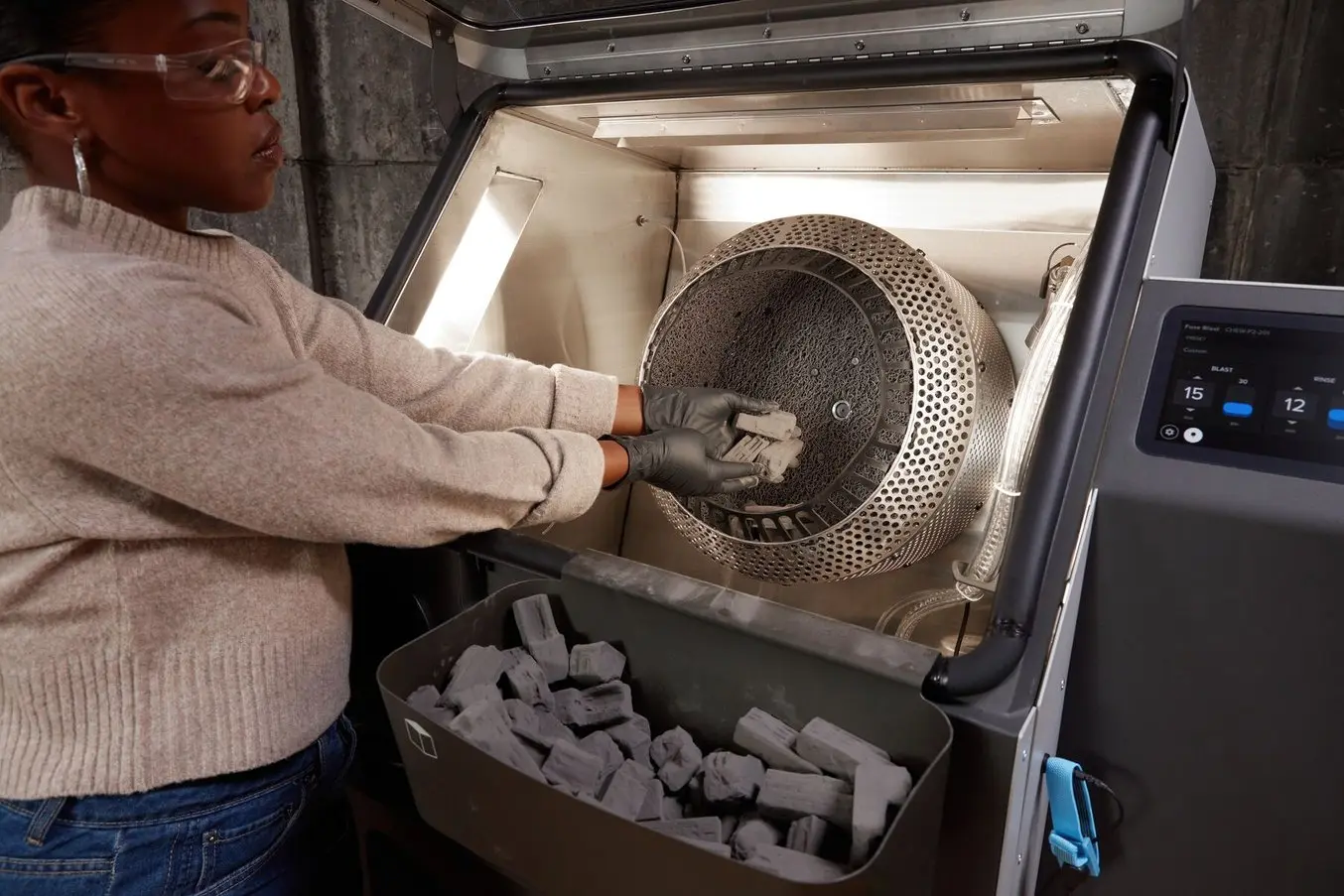
New Automated Post-Processing And Speed Improvement For The Fuse Series SLS 3D Printers
Discover the latest innovations at Formlabs: SLS software improvements for the Fuse Series and the new Fuse Blast, an automated solution that enables hands-free SLS part cleaning and polishing in as little as 15 minutes. Register to watch a 15 minute introduction and product demo.
Reinventing SLS Post-Processing
SLS 3D printing is rapidly becoming the go-to technology for those looking to fabricate rugged, industrial-quality parts cost-effectively. This technology offers almost unlimited design freedom, industry-standard high-performance materials that can function in place of traditionally manufactured parts, and extremely high accuracy and resolution. SLS 3D printers like the Fuse 1+ 30W enable new workflows for rapid prototyping, manufacturing aids, tooling, and end-use goods for mass customization or stopgap production.
However, as the technology expands in popularity across every industry, from consumer goods to end-use aerospace components, post-processing options have not increased at the same pace. Powder management tools like the Fuse Sift provide an easy, affordable solution for powder recovery and recycling, but for the next step of meticulously cleaning and polishing SLS prints, there haven’t been many accessible machine options.
Before the Fuse Blast, users were faced with two options: inexpensive machines that required the user to manually process the part, or very expensive automated solutions. Some machines are available for only cleaning but do not offer a polishing option, while those that do offer a complete solution are often priced around $100,000. Along with higher prices, expensive SLS cleaning systems often require complex infrastructure to support them, like three-phase power supply and separate, enclosed areas.
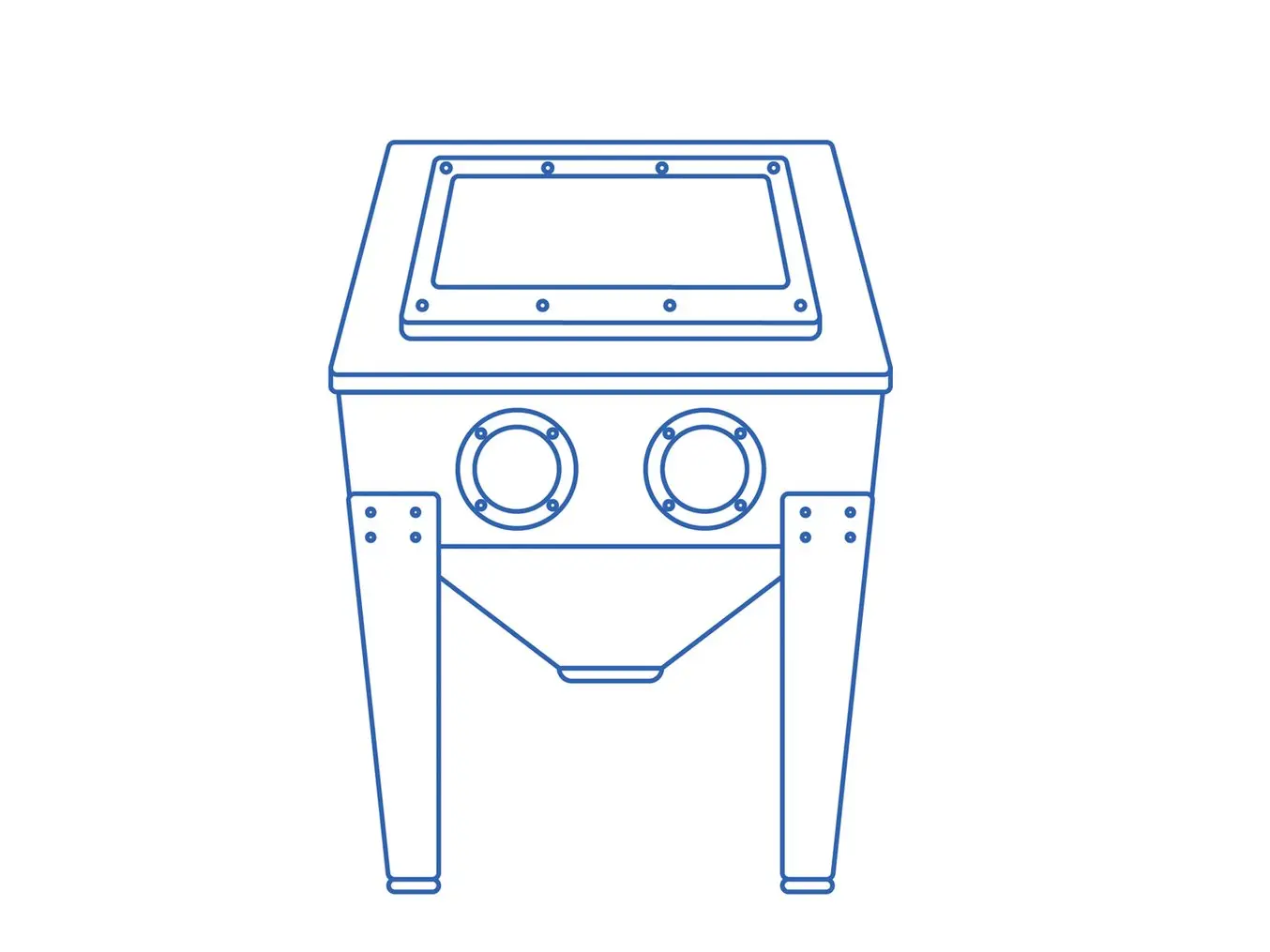
Manual media blasting cabinets are often accessibly priced, but require hands-on labor and make it harder to achieve a consistent finish.
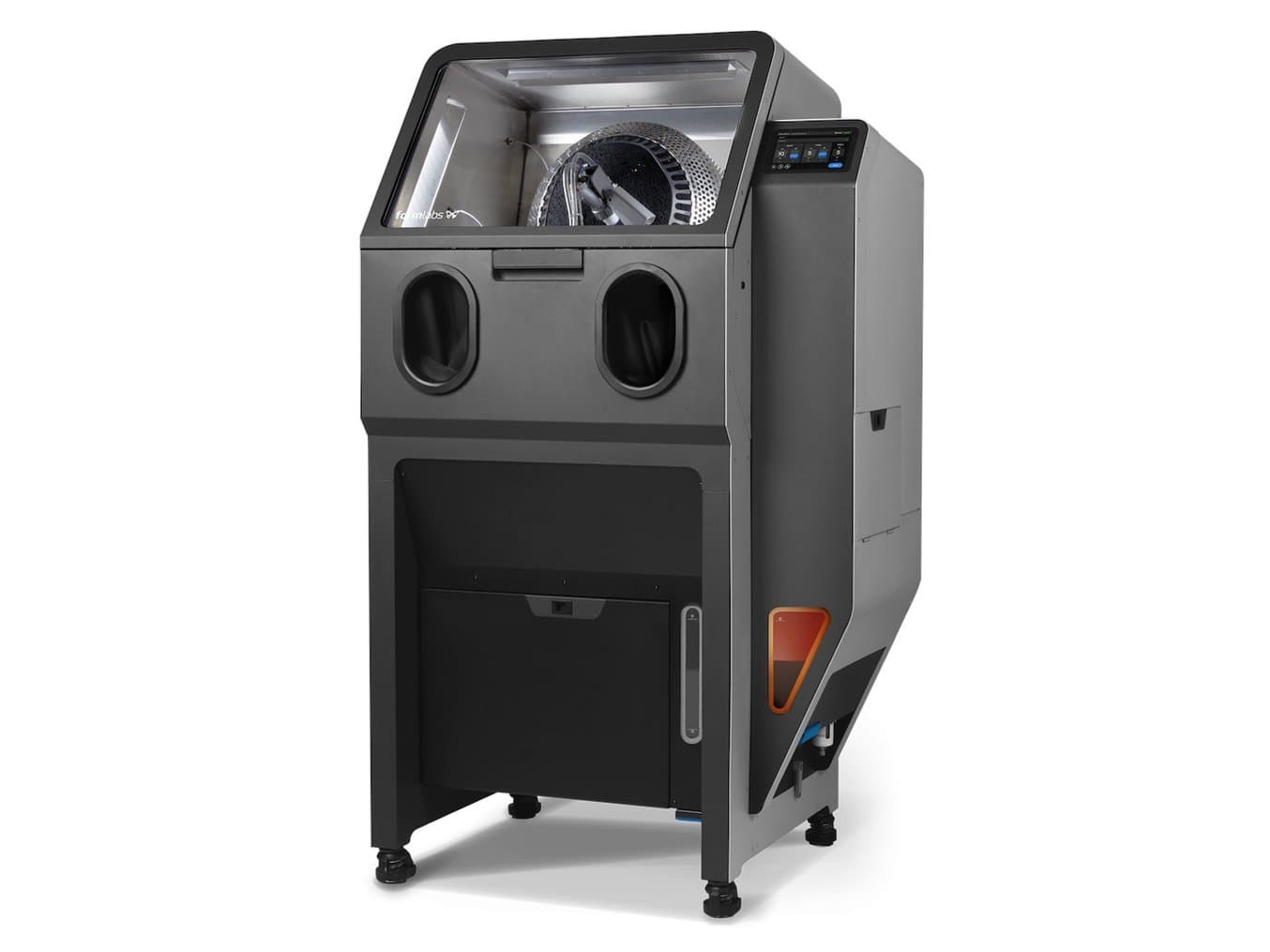
Fuse Blast delivers hands-free, automated, professional-grade SLS part cleaning at an accessible price and size.
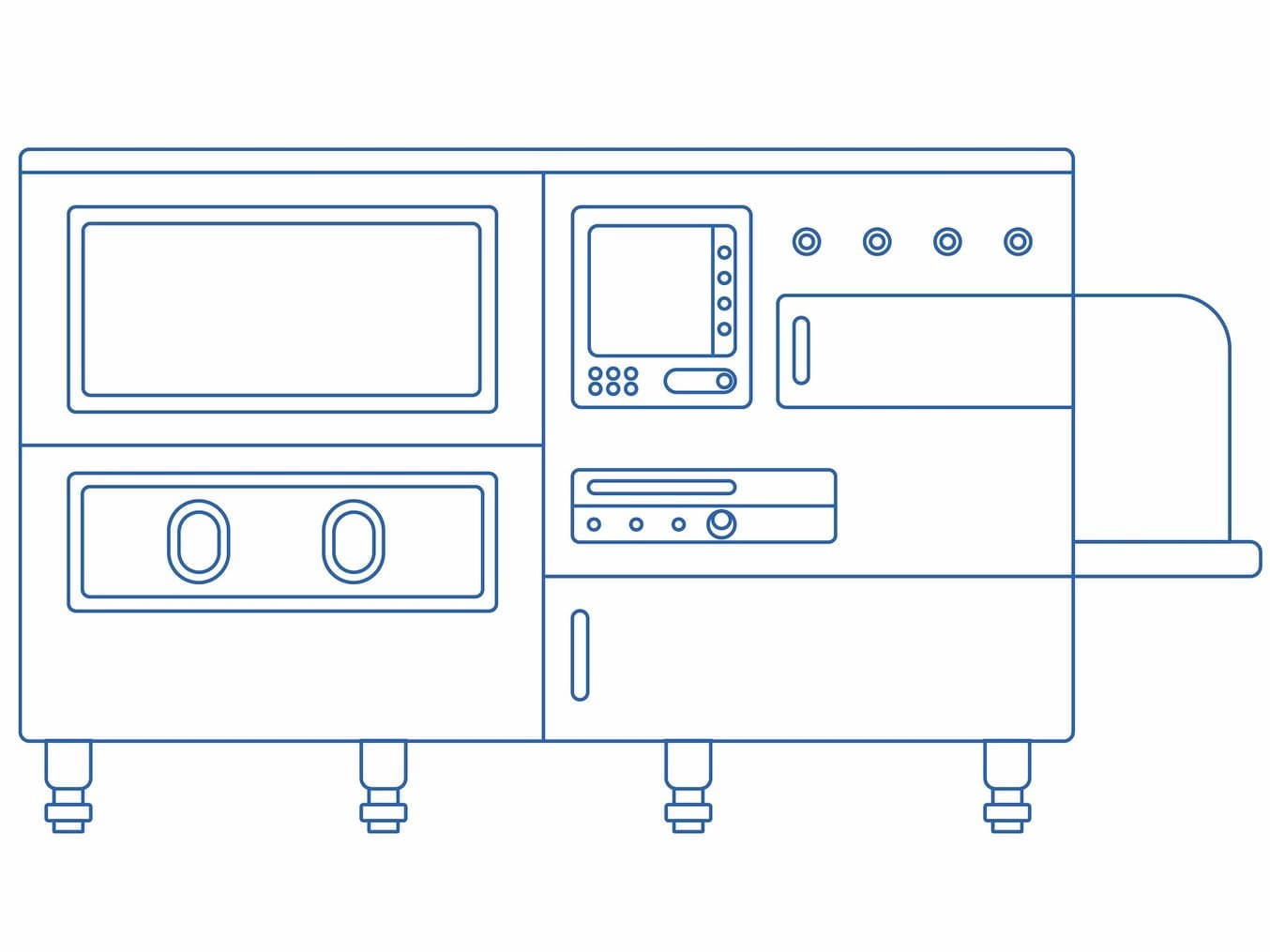
Traditional automated blasting solutions are very expensive, large, and often require complex infrastructure.
The Fuse Blast can also be compatible with other SLS workflows — for those operating a traditional large-format SLS machine who need to streamline their post-processing capabilities, the affordably priced Fuse Blast can add cleaning and polishing capacity while keeping costs low.
Complete options that are compact, consistent, and affordably priced haven’t been available, until now. The Fuse Blast combines the accessibility of the Fuse Series with the ease of use that you expect from traditional, industrial machines.
From Print to Professional Final Product in as Little As 15 Minutes
The Fuse Blast takes on the work of post-processing SLS parts and makes it easier for users to devote their time to other higher-value tasks. Less time spent on post-processing also opens up opportunities to scale production and increase Fuse Series output, without adding staff.
Automated Tumbling for Hands-Free Powder Removal
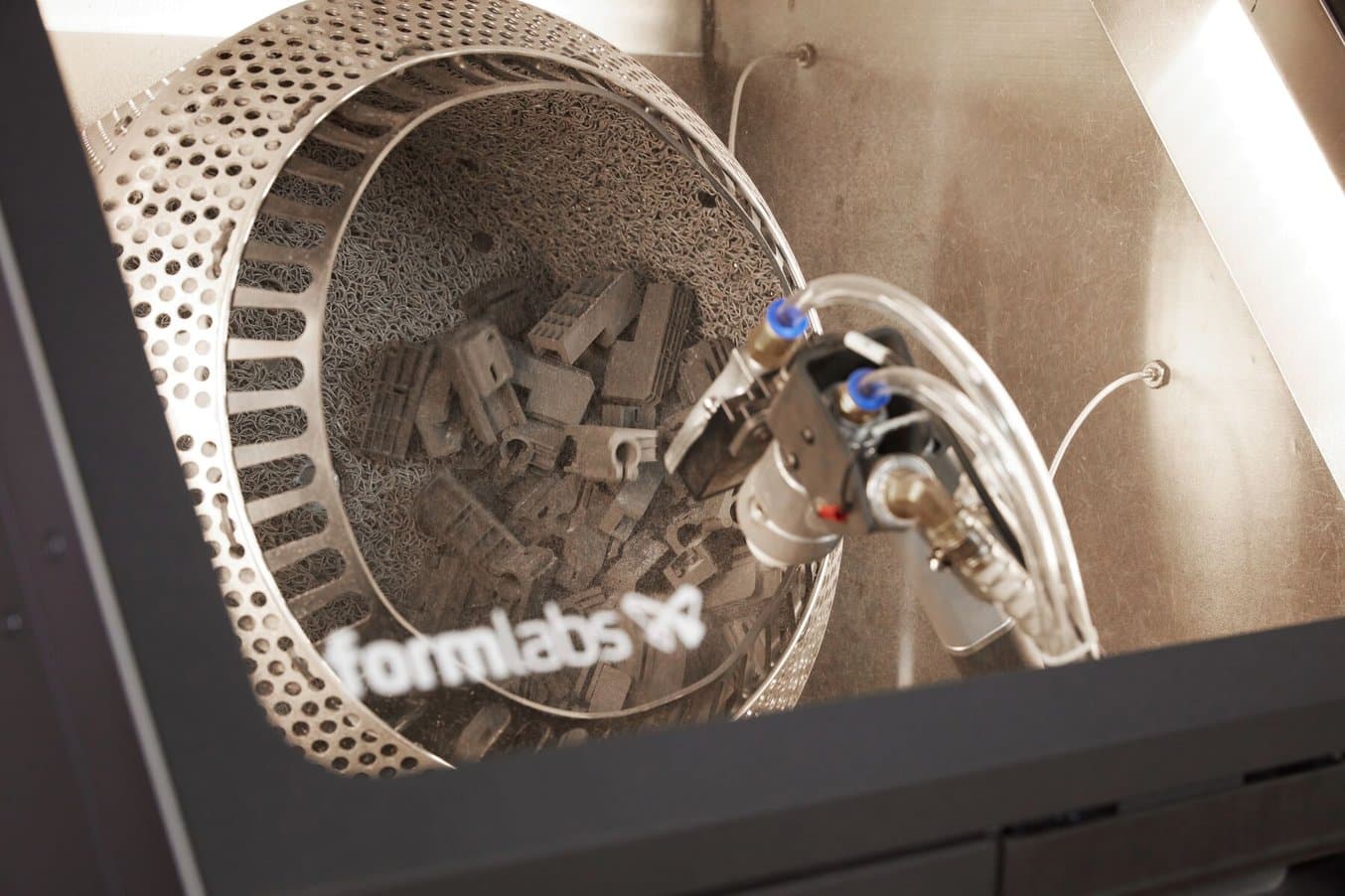
The hands-free tumbling basket uses a combination of basket rotation, compressed air, and abrasive media — it can also be removed easily in situations where manually cleaning larger parts requires more room to move within the Fuse Blast.
The tumbling basket inside the Fuse Blast efficiently removes semi-sintered and loose powder from the parts’ surface using a combination of basket rotation, compressed air, and abrasive media. The tumbling basket is completely hands-free; users only need to take their parts from the Fuse Sift to the tumbling basket using the transfer container and choose a cycle.
Manually cleaning SLS 3D printed parts is the most time-consuming and physically demanding part of the SLS workflow and traditional glovebox systems can be hard on workers’ bodies. Automating the powder removal and cleaning process not only frees up their time for high-value tasks, it reduces wear and tear on their bodies as well as the ventilation systems in their workspace.
Media blasting is a crucial step in the SLS workflow — SLS users need a blasting solution that can consistently clean parts that vary in shape and size, without spending hours of manual labor to clear each groove or feature. The option to add Fuse Blast’s additional polishing capability streamlines a manual workflow that used to take multiple machines and hours of physically demanding labor.
Clean Parts, Clean Workshop
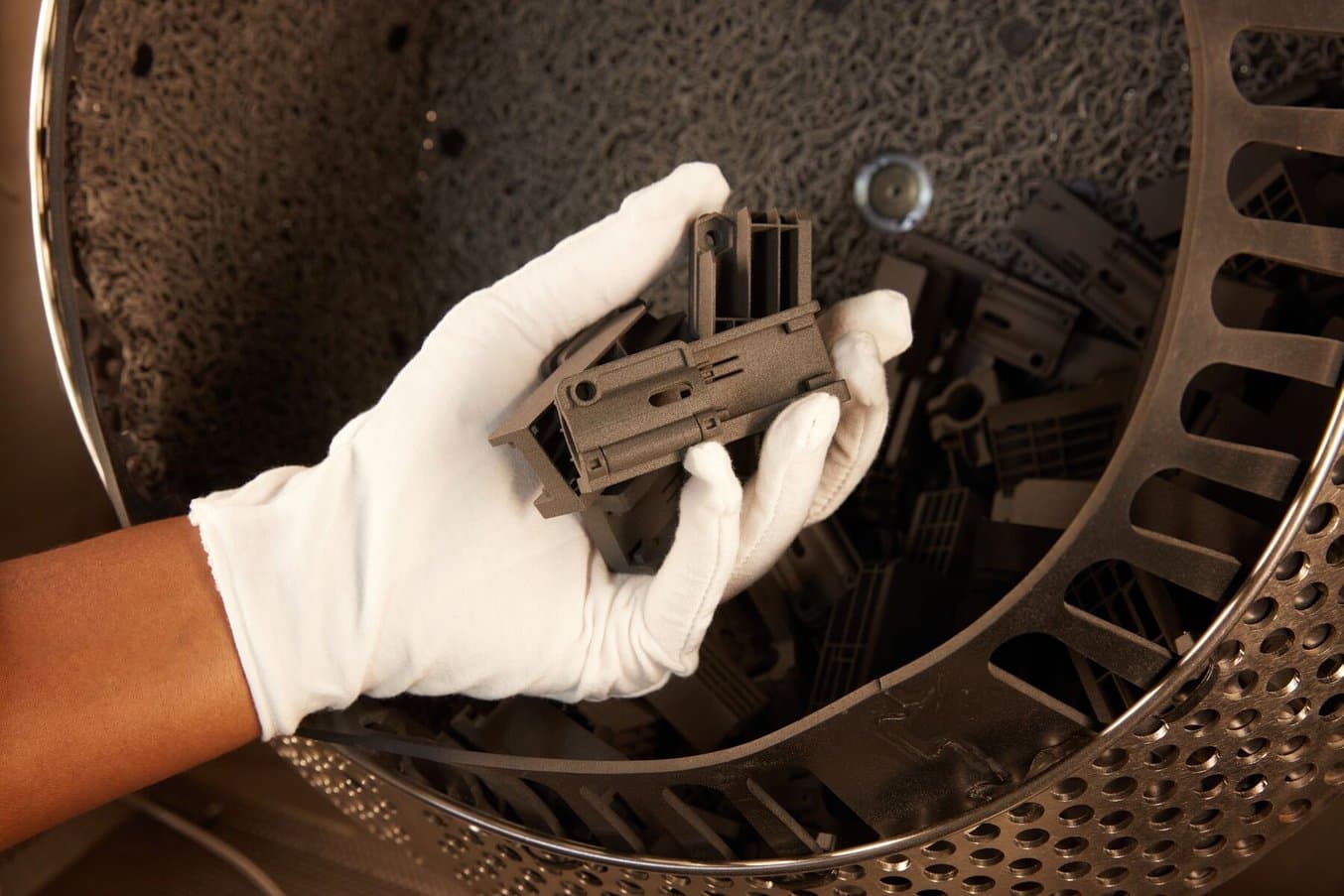
Fuse Blast's in-line ionizer removes static charges from parts, ensuring that each part is clean to the touch, with no powdery residue.
Fuse Blast uses an in-line ionizer to remove static charges from parts, releasing surface dust and media residue during processing. Combining the mechanical effects of the tumbler with a directed stream of ionized air ensures powder-free parts that are clean to the touch, by preventing dust from re-settling after processing is complete. This advanced feature lets users take a part from powder cake to final product in 15 minutes with minimal hands-on labor.
Fuse Blast also features a rinse function that cleans the interior of the cabinet from powder and media to ensure a mess-free environment. In combination with the dust-free parts, this prevents additional dust from being released into the workshop and contaminating the workspace during part transfer and handling.
Passive Media Separation
During many currently available blasting workflows, media becomes ineffective when saturated with powder after just a few cycles — forcing workers to spend extra pre-blasting time in the Fuse Sift to remove powder first. The saturated mix of used powder and media becomes waste and new media must constantly be purchased and refilled into the blaster.
The Fuse Blast’s passive media separation makes it economical to use the Fuse Sift for only a quick de-caking step — users will take the build chamber, empty its contents into the Fuse Sift, and spend just five minutes extracting the parts. Those parts, covered in semi-sintered and some loose powder, can go into the Fuse Blast after only a few minutes in the Fuse Sift.
The passive media separation feature extends the lifespan of your media by more than 400% and enables users to spend only five minutes in the Fuse Sift, reducing overall time spent post-processing by 80%.
Pre-Set Routines and Adjustable Settings
The Fuse Blast offers multiple pre-programmed routines for optimized results, no matter what shape or quantity of parts you’re working on. Users can walk away with confidence, knowing that blasting settings have been tested thoroughly to ensure optimal results.
Delicate Mode is designed to gently treat parts that would otherwise be difficult to tumble, ensuring there is no damage to parts with very fine features, thin walls, or that are very small. For Nylon 12 GF Powder, which has a stronger semi-sintered shell, there is a designated setting that will remove Surface Armor and any loose powder while maintaining the integrity of the part. Most parts will perform ideally with Standard Mode, but users always have the option to tweak their settings for their own unique needs.
Options for Hands-On Attention to Detail
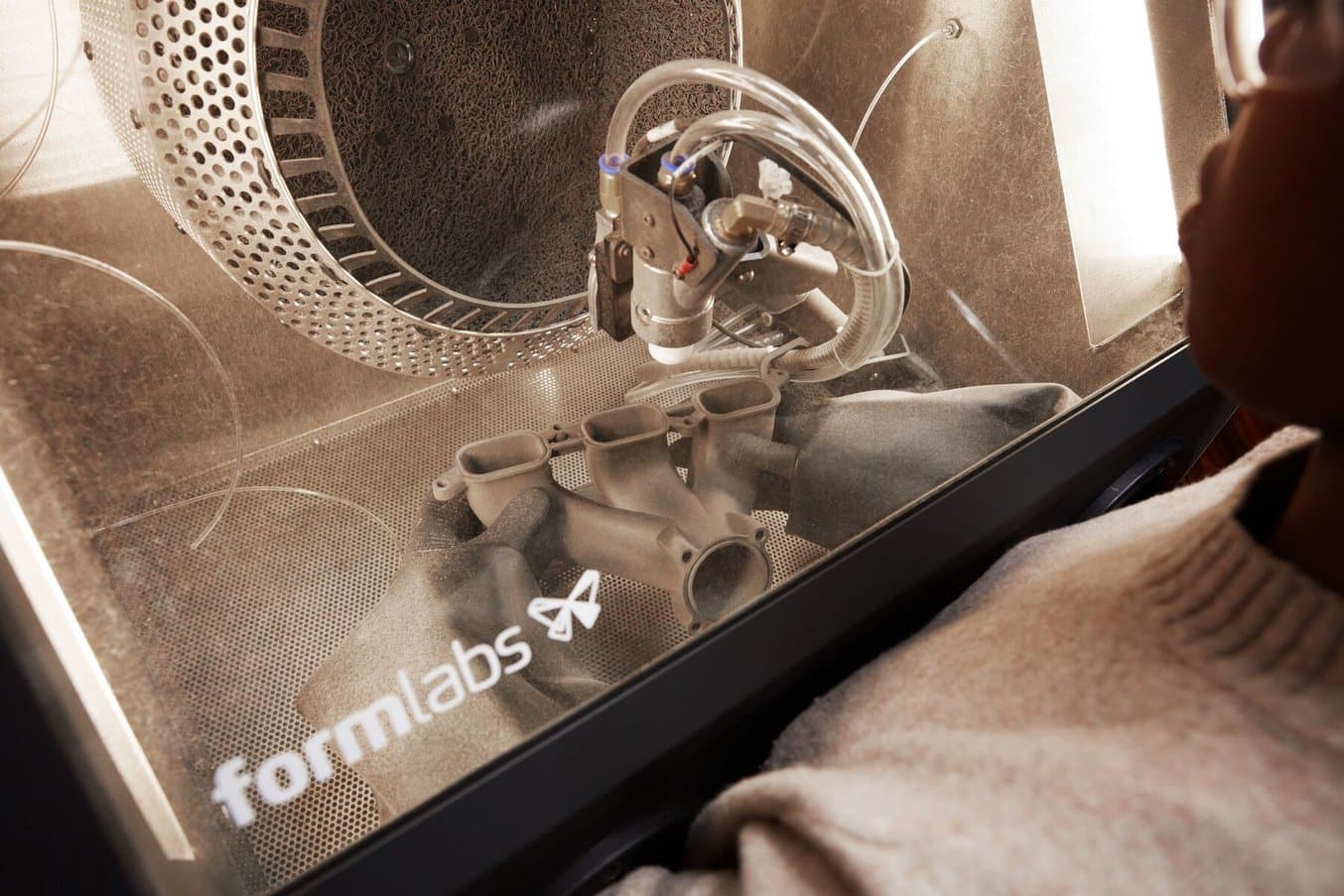
For large parts, users can opt to manually clean using the ergnomic blasting nozzle and foot pedals to precisely remove any excess powder from the surface of the parts.
In addition to pre-programmed, ‘set it and forget it’ cycles, users can also opt to add a manual step to their workflow. For very delicate parts, or large parts that don’t tumble as easily, users have the option to take matters into their own hands.
Manual blasting using the ergonomic blasting nozzle, completely sealed in by the glovebox cover lets you adjust the nozzle, operate the air and media streams using a foot pedal, and clean large or delicate parts easily in just a few minutes.
The orientation of the blasting nozzle arm makes it comfortable for the user even during manual cleaning. For targeted and precise blasting, users can handle parts with both hands and control the blast stream with foot pedals, ensuring every bit of powder is efficiently removed. The Fuse Blast presents solutions for any type of part, in a compact, all-in-one package, so that your cleaning and polishing equipment can be optimized for your own unique workflow.
Compact, Clean, Quiet Operation
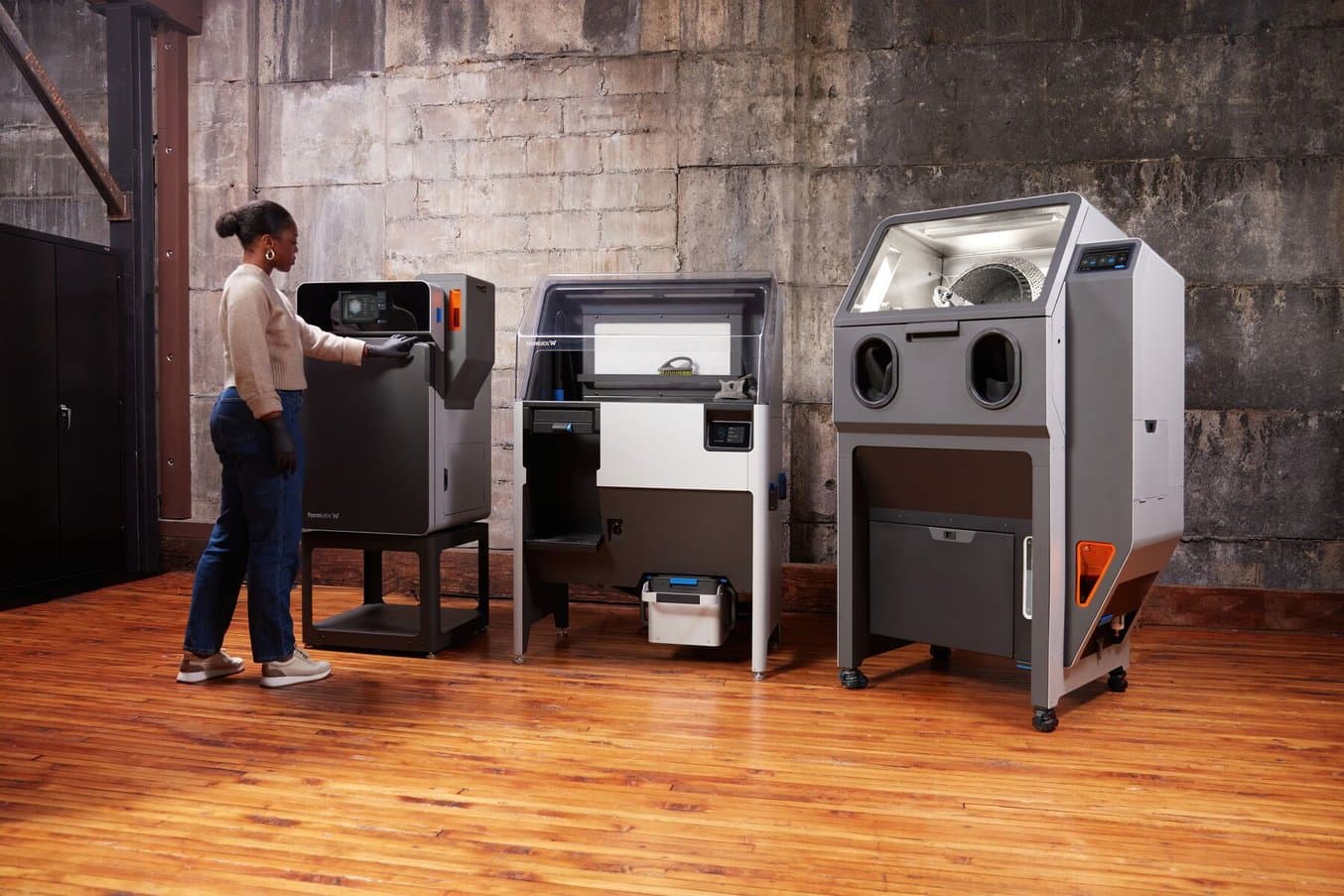
The Fuse Blast fits easily into existing workspaces. "If someone’s got space for a manual blasting system, which every company that has SLS should, you're gonna have space for a blasting without any issue,” says Brent Griffith, Product Engineer at Labconco.
The entire Fuse Series ecosystem has been designed so that anyone can have access to industrial-grade SLS parts — whether they’re in a small office or large warehouse. The Fuse Blast is no different and can be placed directly next to the Fuse Series printer and Fuse Sift for a simple, contained workflow. Manual blasting cabinets on the market today often present a tangle of infrastructure issues; personal protective equipment, ventilation, separate rooms, or ad-hoc sealant solutions are commonly required. The Fuse Blast is sealed, clean, and keeps powder inside, not on your clothes or equipment.
The Fuse Blast uses negative air pressure and a HEPA filter to help maintain a clean, powder-free environment, and the sealed chamber even keeps noise below 70 decibels — quiet enough for a conversation directly next to the unit.
Optional Polishing for Professional Parts
Though manual blasting options are affordable, they lack the ability to go one step beyond blasting for a truly smooth, end-use quality product. Fuse Blast’s polishing function is an optional drop-in upgrade that can go beyond cleaning to surface finishing, enabling parts that are not only powder-free but smooth, scuff-resistant, and dye-ready with a professional, semi-gloss finish.
The Polishing System can be easily integrated into existing Fuse Blast machines for workflows where a consumer-grade finish is integral to success. The polishing step elevates SLS parts from functional and rugged to polished end-use parts ready for customers, providing a solution for stop-gap or bridge production comparable to machined or molded parts.
Case Studies
Fuse Blast Automates SLS Post-Processing at Labconco
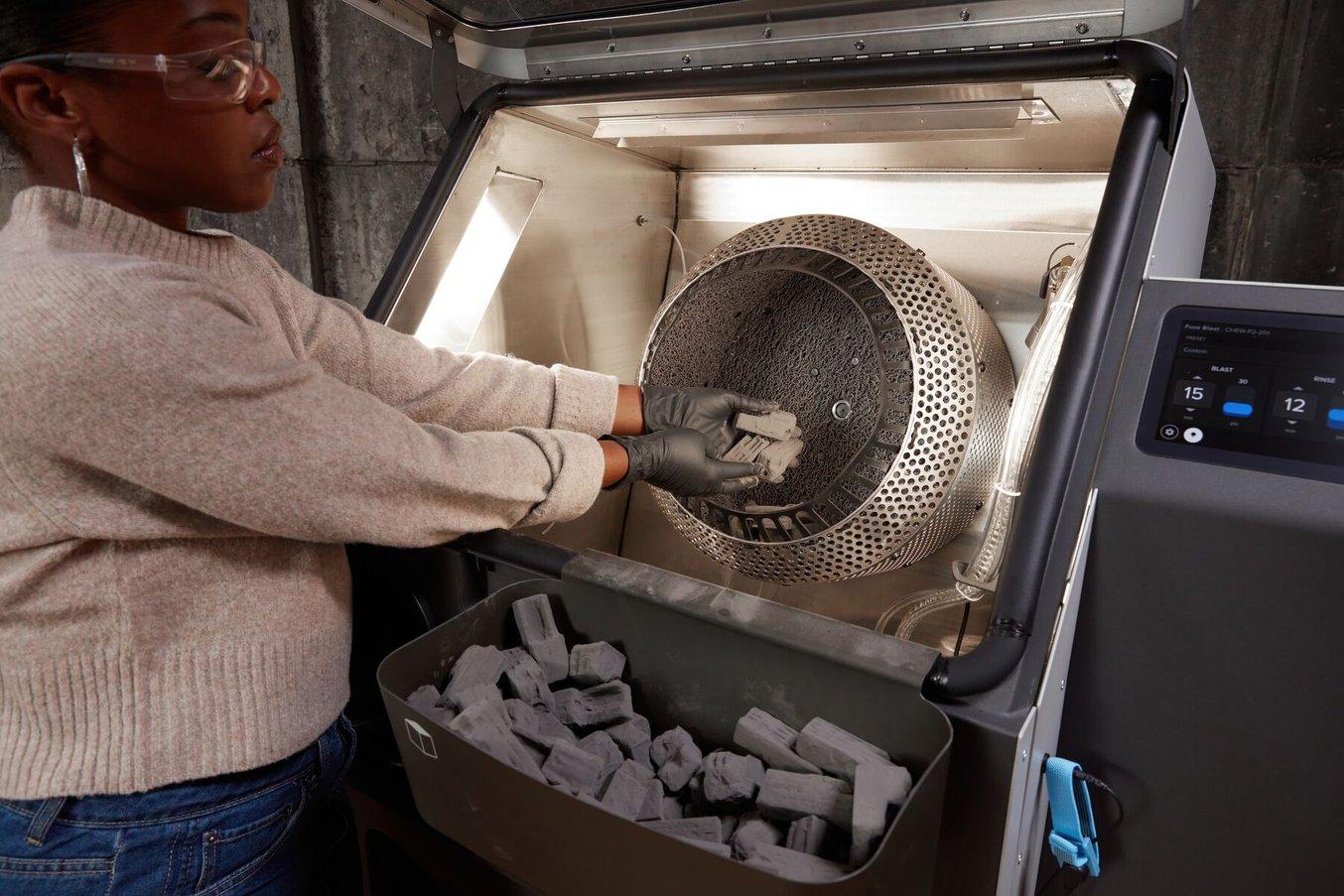
The Fuse Blast can complete the Formlabs Fuse Series SLS system or integrate into an another manufacturer's SLS or MJF printer workflow, at an accessible price and with a streamlined workflow.
Labconco, a manufacturer of laboratory equipment for a range of industries has completely overhauled their design and manufacturing process with SLS 3D printing. As more parts in their catalog are being optimized for additive manufacturing, they needed a solution for automated post-processing — manual post-processing steps like media blasting and cleaning were requiring hours of hands-on labor — time better spent on higher-value design and engineering tasks.
“The company wants us focused on finding new opportunities, redesigning components, and cutting down on costs rather than sitting there, manually cleaning all these parts off,” says Brent Griffith, Product Engineer at Labconco.
Along with a high-cost automated blasting system, Labconco added the Fuse Blast to complete their Fuse SLS ecosystem. After a ten-minute set-up, Griffith could automate the cleaning and media blasting of two full Fuse Series build chambers. “Set-up was a breeze… it's almost the same size as our manual blasting system. So if someone’s got space for a manual blasting system, which every company that has SLS should, you're gonna have space for Fuse Blast without any issue,” says Griffith.
Better Part Quality and Performance
Right away, the requesting teams around Labconco noticed a difference in surface smoothness and part quality.
“The Blast immediately made a huge difference, and the engineers, every single one that I started handing parts to on the prototyping side, started to recognize that the parts had changed — even without me having to tell them that we'd automated the post-processing. They immediately noticed that there was less residual powder on the parts, they felt smoother, they felt nicer, they looked better. It made a noticeable difference in the quality of parts.”
Brent Griffith, Product Engineer at Labconco
The smooth surfaces and lack of any powder residue had an unexpected effect on part performance — machines were functioning more smoothly when their SLS printed components had been cleaned in the Fuse Blast. “We actually gained slightly better performance on some of the components that we were manufacturing because they were so much cleaner, especially on the initial, commissioning runs for one of our products. We're noticing immediately that we weren't drawing as much power and motors weren't stalling out as much because the parts were smoother and there was no powdery residue,” says Griffith.
The results were virtually identical to those cleaned in their other high-cost automated blasting system. “I can’t say I notice much of a difference between the two. [The Blast] is punching way outside of its weight class,” Griffith continued.
Less Time Post-Processing, More Time For Design Optimization
The Fuse Blast’s automation does more than just eliminate time spent hands-on manually blasting parts — it reduces the amount of time Griffith and the team have to spend with the Fuse Sift. Spending more time in the Fuse Sift used to pay dividends by shortening blasting time. Now, the Fuse Blast runs through automated cycles and produces clean parts, even if parts begin buried in powder. “I care a lot less about how much powder I'm getting off [in the Fuse Sift] because I know what the Blast is capable of. Cleaning parts in the Sift doesn't translate to time savings anymore,” says Griffith.
For one part that has a steady production rate of about 50 parts per week, Griffith was manually blasting and having to clean out three holes per part with a pipe cleaner. With the Fuse Blast, he can set an automated cycle and walk away, coming back after 20 minutes to a set of perfectly clean parts. “The Blast is a phenomenal unit. It does a fantastic job on clearing out holes, which is probably one of the bigger time savers for me,” says Griffith.
Integration Into An Existing SLS Ecosystem at Autotiv
Autotiv is a contract manufacturer specializing in 3D printed production runs and rapid prototypes for customers in industries like robotics, automotive, consumer goods, and more. For rush orders, the team at Autotiv can turn parts around in just one day by leveraging a large-format industrial SLS 3D printer that runs around the clock.
Autotiv’s business has grown rapidly, but as orders increase for small- and medium-volume production runs, post-processing has begun to take up more and more of the team’s time. For one recent order, team members had to clean parts in shifts to avoid the fatigue that comes from hours of hands-on powder removal and cleaning. They considered investing in an industrial-sized automated solution for media blasting, but couldn’t justify the high cost.
The Fuse Blast came in at just the right time — the Autotiv team received an order for several thousand small SLS components, but didn’t have the bandwidth to clean them all by hand. “It was easy to set up and worked right out of the box, all we had to do was add media and power. The unit itself is sleek and looks great, plus the addition of a touchscreen makes it very easy to use,” said Chris Haak, Operations Lead at Autotiv.
The Fuse Blast fits easily into the Autotiv workspace near their large-format SLS printer and directly across from the printer’s accompanying powder management system. Though they were initially unsure about using the Fuse Blast with another OEM’s printer, the part quality and the relief to the team’s workload proved the effectiveness of the solution.
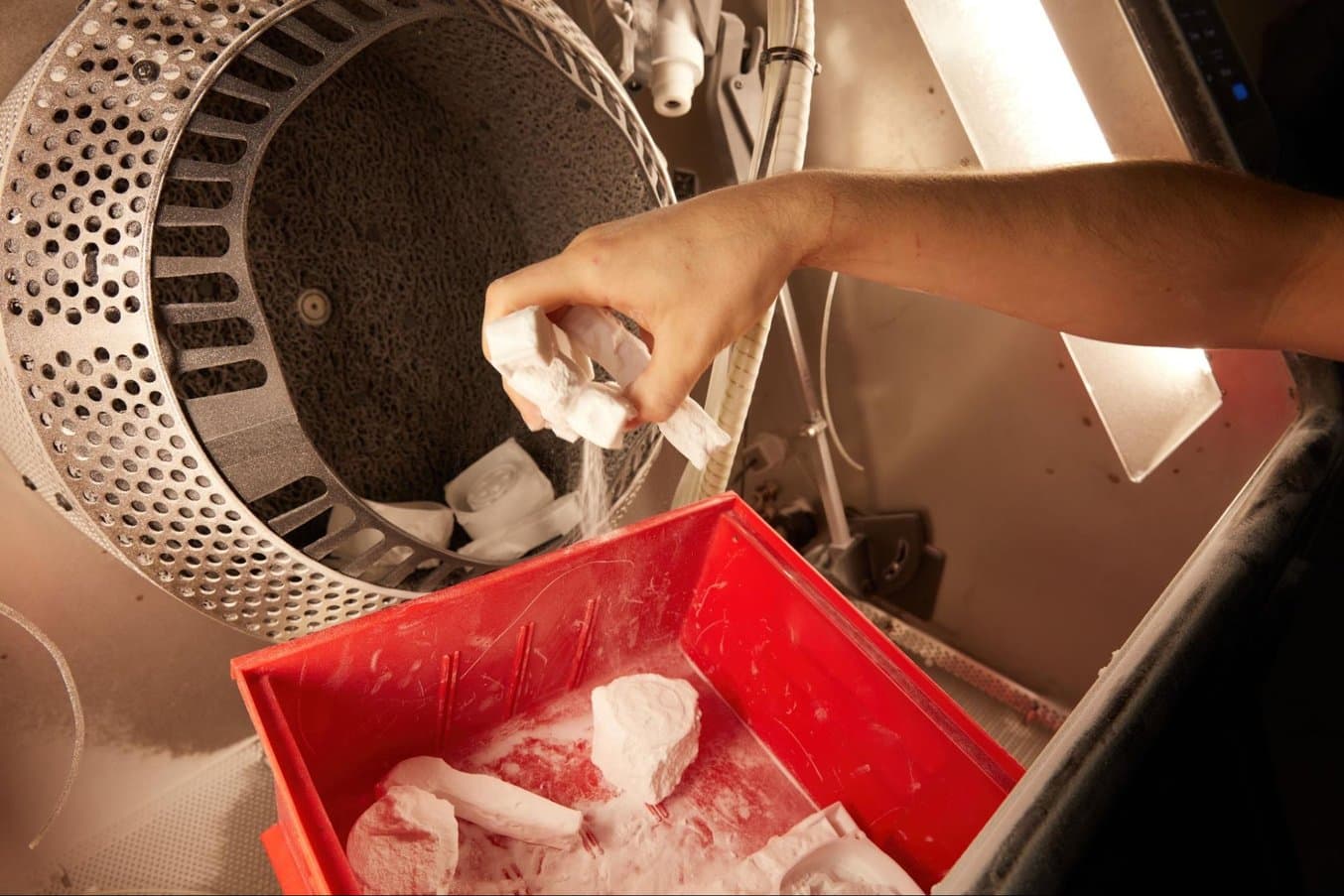
Most of Autotiv’s business comes from SLS production of nylon 12 parts from their large-format SLS printer. Cleaning many small parts like these used to take up a significant portion of Haak’s day.
“Adding this system to any new or existing SLS workflow is a massive improvement over a manual cleaning and post-processing workflow. The Blast also takes stress off of our bodies due to removing the repetitive movement of manual cleaning.”
Chris Haak, Operations Lead at Autotiv
Autotiv has grown its customer base steadily since its inception less than a decade ago by focusing on reliability and consistency, superior part quality, and top-tier customer service. SLS post-processing was a major obstacle to further growth due to the high labor cost involved. With Fuse Blast, the team can focus on high-value tasks, like design consultations, print optimization, and advanced post-processing techniques like coating, vapor smoothing, dyeing, painting, and assembly.
“Since getting the Blast, Autotiv has been able to take on more work due to the time savings the Blast provides, time savings are easily hours per day.”
Chris Haak, Operations Lead at Autotiv
Software Improvements for a Faster, More Powerful Fuse 1+ 30W
In addition to the addition of new hardware for a complete SLS workflow, Formlabs is introducing a suite of software improvements.
- Users will now be able to print parts in Nylon 12 Powder up to 30% faster with better fine feature resolution for detailed, robust parts, and produce parts with enhanced ductility with the "Default Print Mode".
- The new Fuse Series part nesting algorithm improves pack densities, allowing users to reduce print time and minimize wasted powder by 42% on average.
- Users who print back-to-back cycles benefit from a streamlined workflow by limiting the need to vacuum between prints.
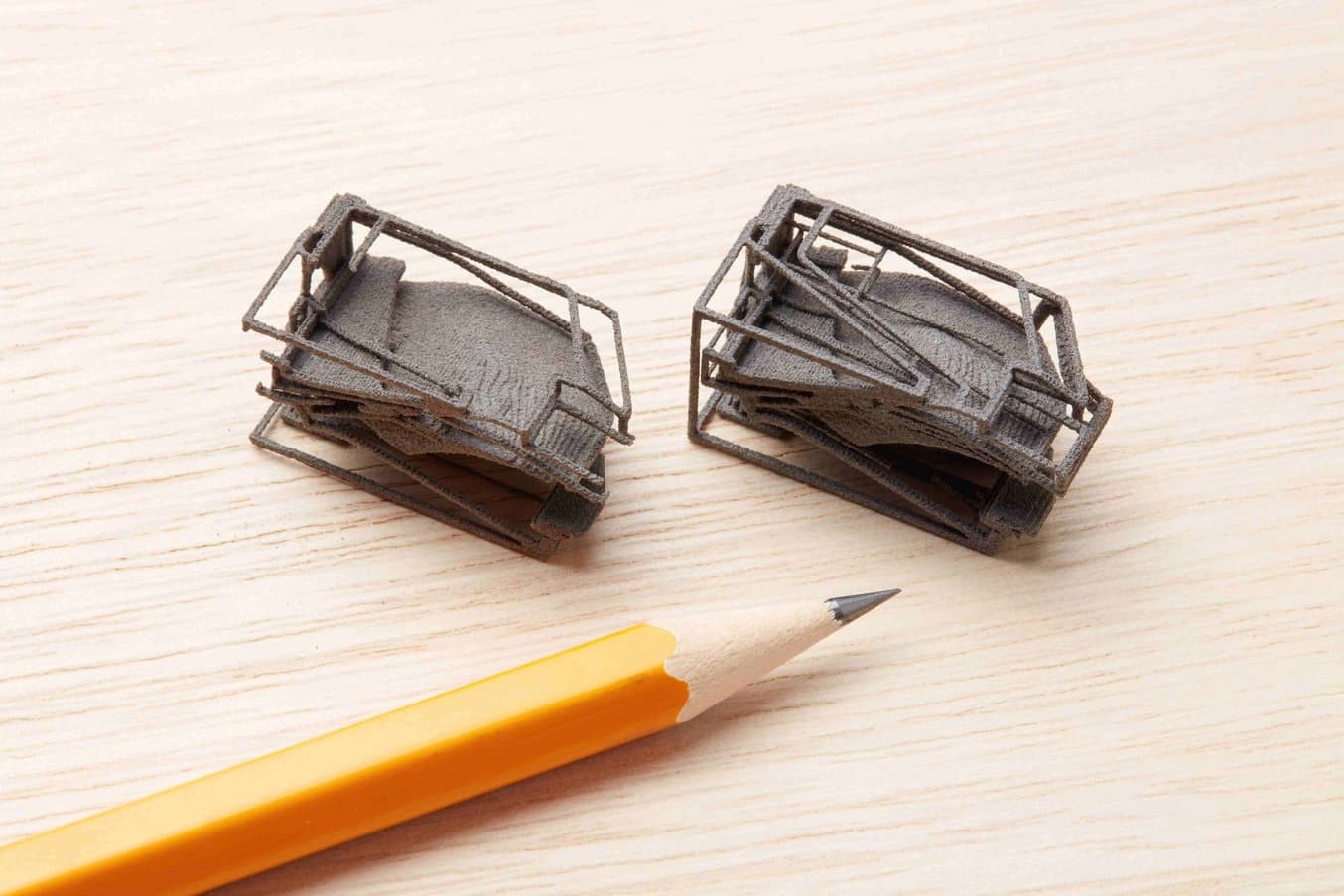
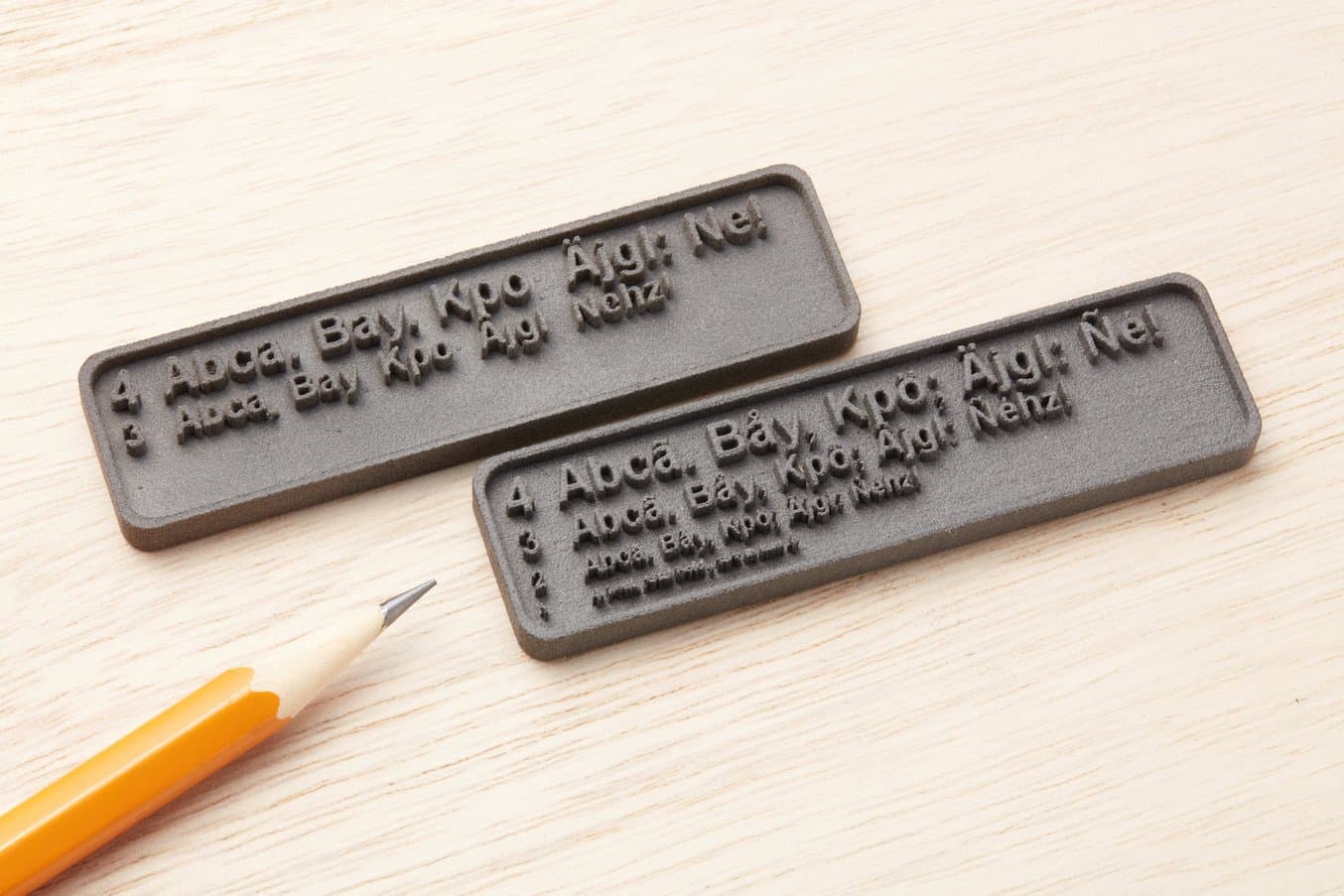
Part printed on the Fuse 1+ 30W with legacy settings (left) and with the improved fine feature resolution (right).
New software features will also be rolled out in 2024 to enable:
- Up to 50% faster print generation time
- Up to 50% faster print upload time
- Up to 15% faster pre-print wait time for Nylon 12 Powder
Reduce Labor, Streamline Operations
The Fuse Blast enables the entire post-processing timeline to be reduced to as little as 15 minutes, from finished print to professional final part, with minimal manual labor. Users can now spend as little as five minutes removing the powder cake from the build chamber in the Fuse Sift before transferring the parts to the Fuse Blast for an automated cleaning routine. Overall, hands-on time spent in the Fuse Sift is reduced by an average of 80%, allowing that time can be reallocated to high-value tasks.
Media blasting parts adds extra value by elevating their end appearance without adding hands-on labor time and cost. The Fuse Blast’s pre-programmed settings, passive media separation, and optional manual cleaning and polishing options create a complete yet compact solution for SLS parts that present a photo-ready finish and function seamlessly as part of multi-part assemblies.
With the Fuse Blast, Formlabs introduces the final step to a complete, industrial, and affordable SLS workflow. For the price of many of the automated media blasters currently on the market, you can now purchase an entire Fuse Series ecosystem — Fuse 1+ 30W printer, Fuse Sift, and Fuse Blast.
Upgrade To An All-In-One SLS Solution
SLS 3D printing doesn’t have to be expensive and slow, or require complex infrastructure. With enhanced software features and the complete post-processing workflow with Fuse Blast, you can now create high-performance SLS parts easily, without a big price tag.
Watch our webinar to learn more about the Fuse Blast or contact us to speak to a member of the SLS team.