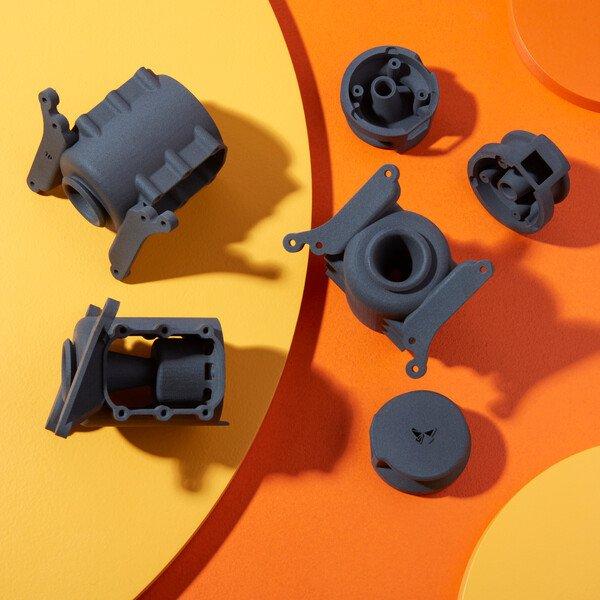
End-use parts printed on the Fuse 1
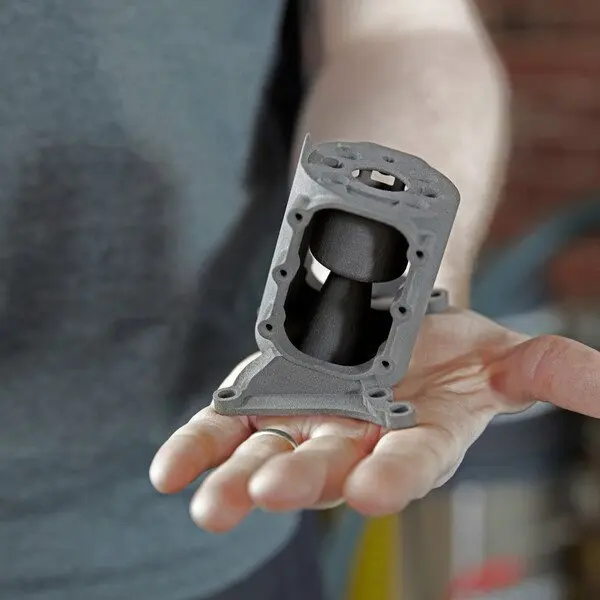
An IR sensor purge printed on the Fuse 1 in Nylon 12 Powder
Building the Fuse 1 was an engineering challenge. Packing industrial-grade performance into an affordable, sleek desktop selective laser sintering (SLS) 3D printer took years of engineering and design work.
One of the tools Formlabs engineers used to prototype parts was the Fuse 1 itself. But the use of 3D printing didn’t stop at prototyping. Today, every single Fuse 1 unit shipped to customers contains multiple production parts printed directly on a Fuse 1 using Nylon 12 Powder.
Using the Fuse 1 SLS printer to prototype and create end-use parts offered three main advantages, according to Seth Berg, the engineer program manager overseeing the Fuse 1:
- The design freedom to create complex parts without internal support structures.
- Reducing supply chains by prototyping and creating end-use parts in-house.
- Eliminating outsourcing to achieve an affordable solution for small-batch production with a proven, versatile Nylon 12 material.
SLS Prototyping and In-House Production: Printing an IR Sensor Purge
Seth Berg talks about printing end-use parts on the Fuse 1
When users install their new Fuse 1 printer and Fuse Sift post-processing unit, they may not know that five distinct parts were printed using a Fuse 1. Of those five parts, the IR sensor purge exemplifies the type of part that is perfect for small-batch production with in-house SLS 3D printing.
One of the biggest hurdles when creating the Fuse 1 was measuring and balancing the internal temperature inside the build chamber. Berg knew his team was facing one of its final hurdles before shipping the Fuse 1: they needed a custom IR sensor purge to properly regulate heat inside the print bay. Since temperature accuracy was so sensitive inside the print chamber, the team was expecting to make dozens of prototypes before finding the exact IR sensor purges that worked, and the prospect of outsourcing or using injection molding wasn’t ideal due to the number of prototypes required. So the team turned to their beta Fuse 1 units, powered by Nylon 12 Powder, to both prototype and produce the parts. “We needed a 3D printing technology that didn't constrain us in geometry or put support tips onto surfaces where we wanted smooth airflow. So, SLS was really the only 3D printing option that was gonna accomplish that for us,” said Berg.
So the team got to work using early Fuse 1 production units to design, test, and ultimately manufacture custom built parts at scale so we could get the Fuse 1 to market. Over time, they began creating more parts: door handles, IR handles, handles for the Fuse Sift, all in-house on their beta Fuse 1 units. Today, every single Fuse 1 unit shipped contains multiple production parts printed directly on a Fuse 1. “We tested these parts very rigorously. So we have nearly 50 printers at headquarters that we're running nonstop printing these parts. So we've tested these in a real printing application for thousands and thousands of hours,” said Berg.
After dozens of prototypes for the IR sensor purge, the team settled on a final design. They seamlessly moved from prototyping to small-batch production on the same Fuse 1 printers. With thousands of parts being printed each week, the Fuse 1 production line was further validation that the machine was ready to ship. Berg said, “At Formlabs, we think about accessibility of products both from a price standpoint, making it a product that you can afford to buy, but also accessible from a maintenance standpoint. The worst thing is when you come in the next morning and your print has failed. Seeing the Fuse 1 in action as both a prototyping powerhouse and full-time production machine was gratifying.”
Due to the dense packing capacity of the Fuse 1, the build chamber is able to hold 12 IR sensor purges per print cycle. For smaller parts such as the IR sensor handle, that number jumps to 60 parts per print cycle. While in-house 3D printing doesn’t yet make sense for mass production of millions of parts, multiple machines running in tandem is an excellent solution for small and medium batch sizes. The IR sensor handle requires 22g of powder to print, costing $2 per part. The main IR sensor purge uses 70g of powder, costing approximately $7 per part.
According to Berg, “having the Fuse 1 in house absolutely resulted in an IR sensor purge that worked more effectively, because we were able to iterate more quickly, and, and try more designs. Then we were able to move directly to production using the same material.” This means the team didn’t have to edit or tweak tolerances between prototyping and production.
Seth Berg
Having the Fuse 1 in house absolutely resulted in an IR sensor purge that worked more effectively, because we were able to iterate more quickly, and, and try more designs. Then we were able to move directly to production using the same material.
Without the Fuse 1, Berg said the team would have been stuck outsourcing SLS for these parts. Berg added, “if we did not have the Fuse 1 in house, we would have outsourced SLS parts to a service bureau, and we would've paid more money and it would've taken us longer to get those parts in house. The Fuse 1 prints industry quality end-use SLS parts in-house for a fraction of the price and time.”
Berg said that his team “is confident that these parts work in our application that every single Fuse 1 we ship has parts that are printed on the Fuse 1.” The IR sensor purge, the IR handle, the door handle, and the interlock magnet cover were all made possible with the help of the Fuse 1.
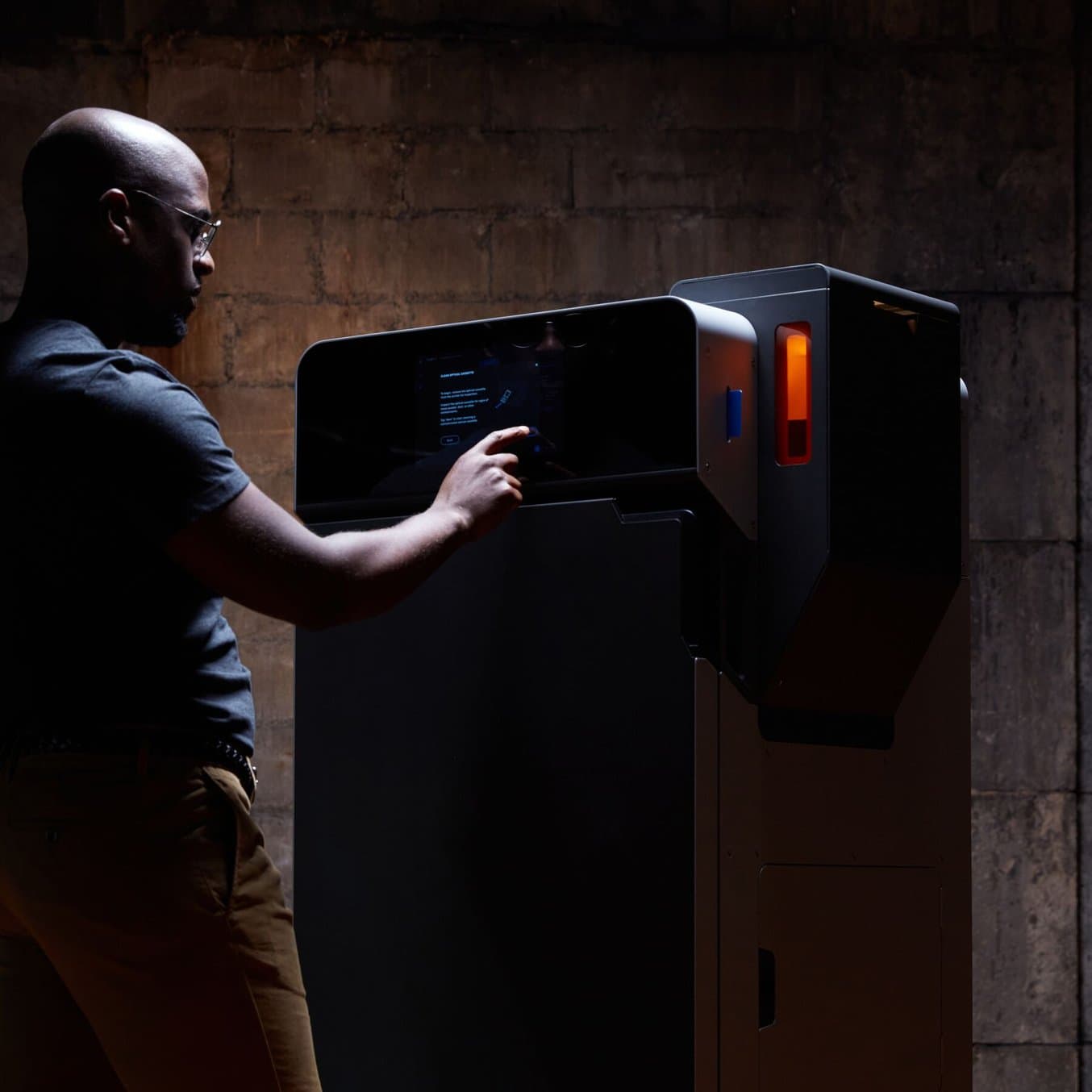
Outsourcing vs. In-House: When Does it Make Sense to Bring SLS 3D Printing In-House?
In this white paper, we evaluate the value proposition of bringing SLS 3D printers in-house, in comparison with outsourcing SLS parts from a service bureau.
Nylon 12 Powder for End-Use Parts
The first material Formlabs launched for the Fuse 1 is Nylon 12 Powder, a highly capable material for both functional prototyping and end-use production of complex assemblies and durable parts with high environmental stability.
While other 3D printing processes can be used for end-use parts, SLS printing offers a different set of properties which made printing parts for the Fuse 1 advantageous. First, SLS parts tend to last longer, especially when being handled or used every day. Compared to stereolithography materials, Nylon 12 prints offer a longer lifetime, low creep, and better wear, chemical, and UV resistance. “At the end of the day there are lots of different types of end-use parts, but almost all of them need to be tough, they need to be resistant to both temperature and impacts. Nylon is a material that's really in the sweet spot of all of those different material properties. So if you can think of an application where you want to print a part and, and use it, nylon is almost certainly a good option,” said Berg.
One feature of SLS powder printing that is especially salient for creating a custom IR sensor purge was the ability to print parts without internal supports. With other 3D printing processes, internal crevices and openings will require support structures, and parts have to be designed with this in mind. SLS printing eliminates this issue, allowing for complex parts to be created and used with drastically reduced post-production time.
Finally, Nylon 12 enables the Fuse 1 to print with up to 70% recycled powder. This is a huge advantage to both prototyping and production on the Fuse 1, allowing engineering teams to derive value from each gram of purchased powder. Berg’s team found this to be one of the core reasons the Fuse 1 was a competitive production option, stating that “all of the parts that are printed and installed onto the Fuse 1 are printed with 70% reused powder. That's one of the secrets that makes this a cost competitive manufacturing option for us to do in-house.” He continued, “and we didn’t only use recycled powder for prototypes. On the Fuse 1 manufacturing line, all of the parts that we print are using 70% recycled powder. That means the end-use parts as well.”
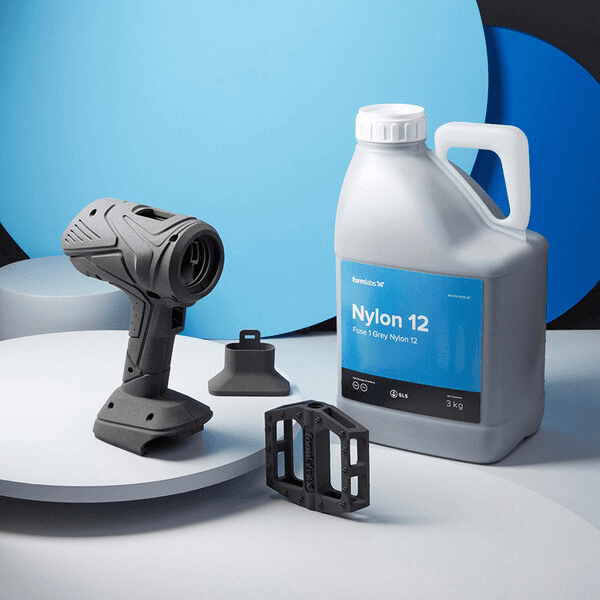
Nylon 12 Powder
Nylon 12 Powder is a highly capable material for both functional prototyping and end-use production of complex assemblies and durable parts with high environmental stability. We put together a post covering your most frequently asked questions.
The Fuse 1: Now Shipping
Formlabs is known for designing additive workflows that make industrial-quality 3D printing manageable for businesses of any size. The Fuse 1 and Fuse Sift empower businesses to take control of the design process, print production-ready nylon parts in-house, increase throughput, and bring industrial level SLS 3D printing to the benchtop at a truly entry-level price point. All of these concepts, the versatility of Nylon 12, and the unique benefits of SLS 3D printing, came together to help Berg and the Formlabs engineering team create a better Fuse 1.
Want to see how a part printed on the Fuse 1 looks like? Request a free sample part now.