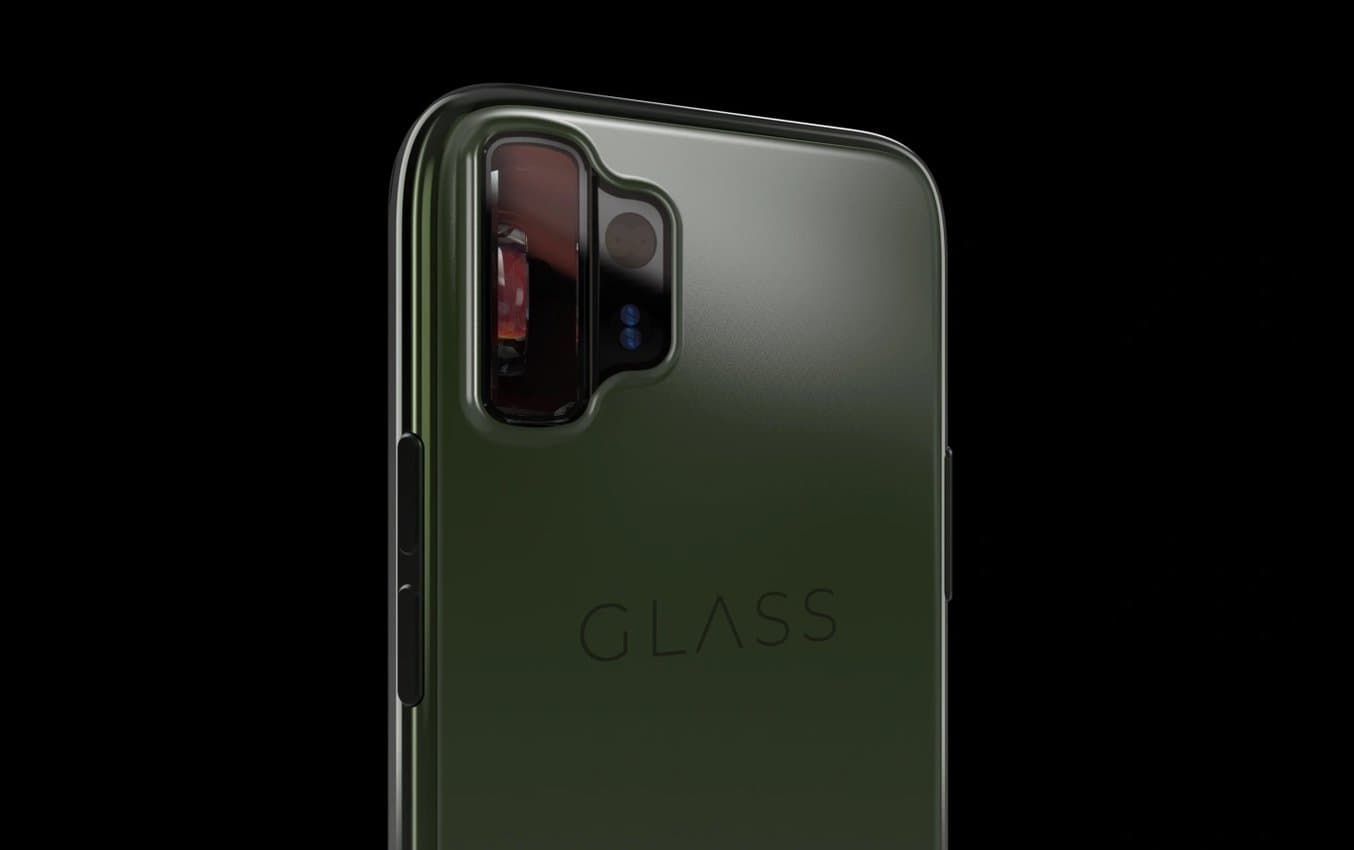
A Glass Inc. camera mockup. The company's camera technology is meant to fit inside a standard smartphone.
The Formlabs team recently spoke with Glass Imaging Inc. a start-up looking to disrupt the photography industry. Company Co-Founder Tom Bishop told us that, “fundamentally, nothing has changed since cameras were created. With the computational power in smartphones, we can make something better from the ground up.”
Glass Imaging Inc. was founded by Tom Bishop and Ziv Attar to address the future of image processing. The pair met while working on mobile imaging at Apple. After years of incremental improvements in smartphone cameras, the two set off to create Glass Imaging Inc. in order to fundamentally rethink how cameras work. The team sees a unique opportunity to design a camera that takes hardware — the lens and sensors — and the AI computing ability of modern smartphones to create the perfect photo. By fitting a wide anamorphic lens and extra-wide sensors inside a standard smartphone case, the team is aiming to bring DSLR quality photos to your pocket.
In order to convince phone makers to ditch decades old technology that, for the most part, is adequate, Glass Imaging Inc. is going to need a working, functional prototype. That’s where in-house stereolithography (SLA) 3D printing comes in. In recent years a wave of innovative startups have been turning to SLA to prototype parts, print end-use parts, creating molding, and more, in order to greatly reduce costs and better compete with existing companies. Glass Imaging Inc. is deploying both Black Resin and Rigid 4K Resin to create demo mounts, lens cases, and more. In this post, we hear from co-founders Tom Bishop and Ziv Attar, along with Mechanical Design Lead Cole Cogswell, on how they are changing mobile photography.
3D Printing Innovation
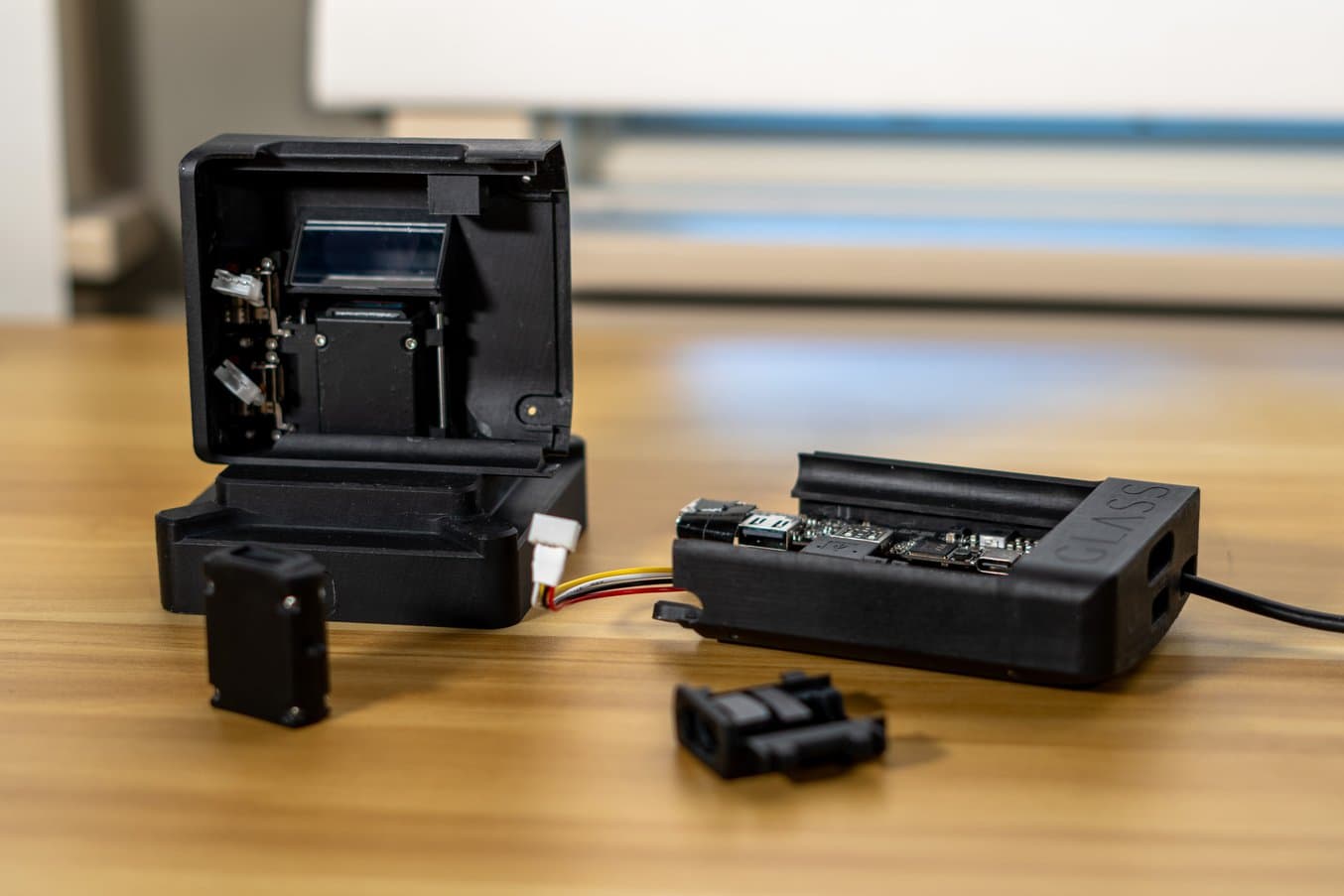
Components of a 3D printed Glass Imaging prototype camera case and lens housings.
When first getting started with 3D printing, Attar originally invested in an FDM 3D printer. While FDM has its benefits, especially its low price per print, the material properties often don’t hold up for many business applications.
When searching for something better, the company originally bought a cheap SLA printer on Amazon, with Attar saying “it was a pain in the neck, it did some big prints like phone cases, but the resin handling was a lot of work.” At this point the company invested in a Form 3+, due in part to its easier material handling.
Cogswell got to work, printing and testing different holders and lens cases. He said that, “it’s been super easy to go from your design concept to your physical print. You don't want to worry about design for manufacturing. There are some edge cases with custom supports, but it has been a super quick learning curve, I was printing modules for it in a couple days.” There’s been a major uptick in innovative startups bringing new products to market due in-part to in-house additive manufacturing. Lower barrier to entry is a huge boon to small businesses like Glass Images Inc., allowing them to challenge large incumbents even in highly technical fields such as mobile photography.
Cogswell said that prototyping on a small scale, “would be very difficult without 3D printing. When I first joined, we were getting parts machined and CNC machines, and the fastest you get those back is a few days to week, and then if you need adjustments, you have to send them back. With the 3D printing, we have been able to make small changes, and incorporate new features, that have made our demo much more compelling.”
He continued, “we basically print an entire phone case, if we were machining this, it would cost thousands and thousands of dollars, and take a week or more. Now, I start a print Friday afternoon, and when I come in Monday morning, the print is done.”
For early stage startups, prototypes are important to test designs, but also to show investors and businesses what they are working on. Bishop told us that the team’s “big vision is getting this technology into real smart phones. Most importantly, 3D printing is helping us continuously improve our product.”
Cogswell has deployed two resins to achieve this: Black Resin and Rigid 4K Resin. Black Resin has been a standout for larger parts, demo mounts, and devices that the team might show externally to the press or investors. According to Cogswell, Rigid 4K Resin has been “super reliable and given us much more consistent results for lens housings.”
The Future of Photography
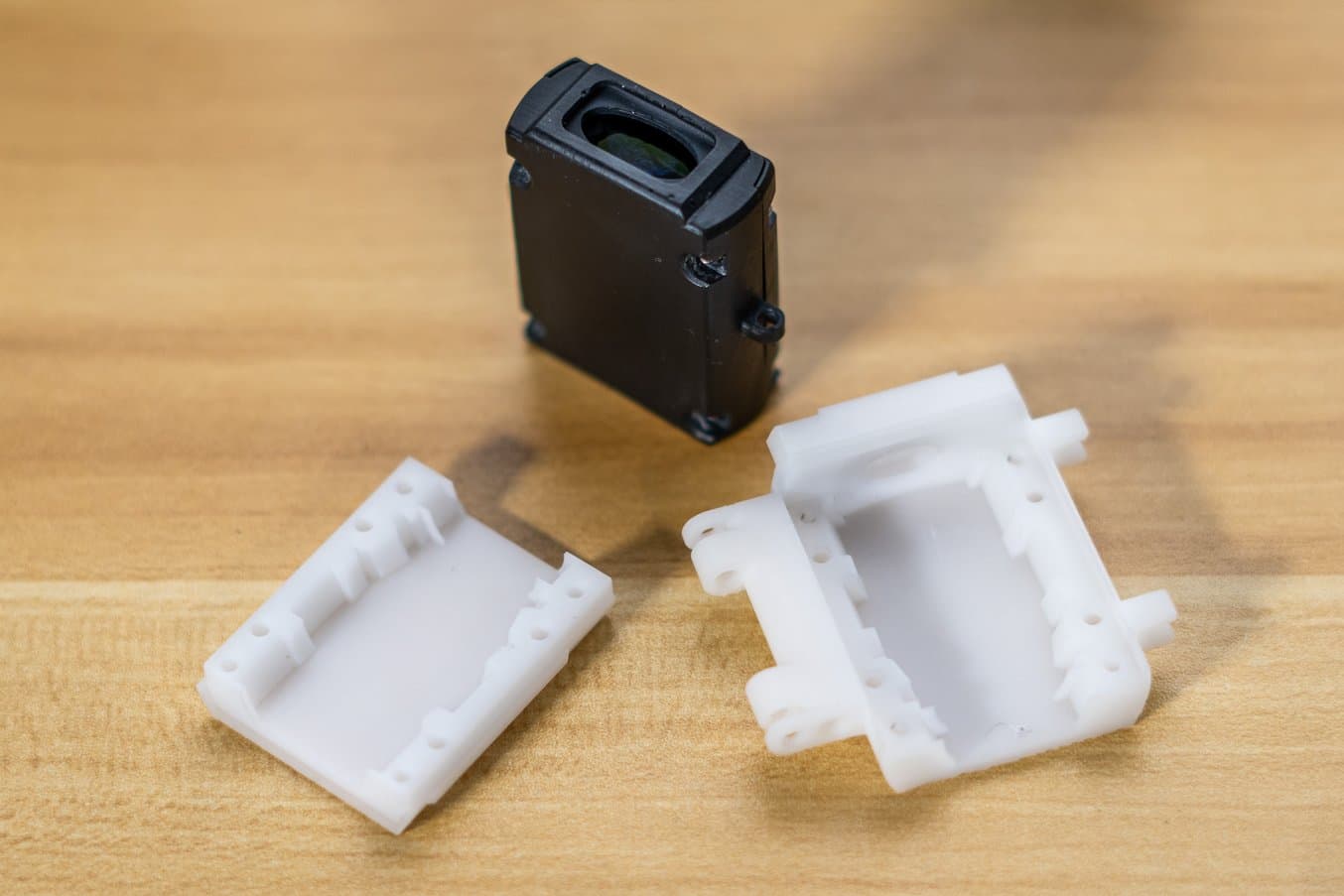
Right now, the team is printing lens housings in Black Resin and Rigid 4K Resin. For optical assemblies the precision and repeatability of alignment is important to obtain good quality images, and the team has been impressed with what has been possible with these materials.
Bishop told us that there has never been a better time to disrupt the smartphone camera market. “Our team has been working in this industry since the start of the smartphone camera era. It’s a really hard niche to break into, because you need the manufacturing, optics, and AI software background, as well as an understanding of international supply chains, but there is such demand for improvement and change, and we’re building an experienced team like no other,” he said.
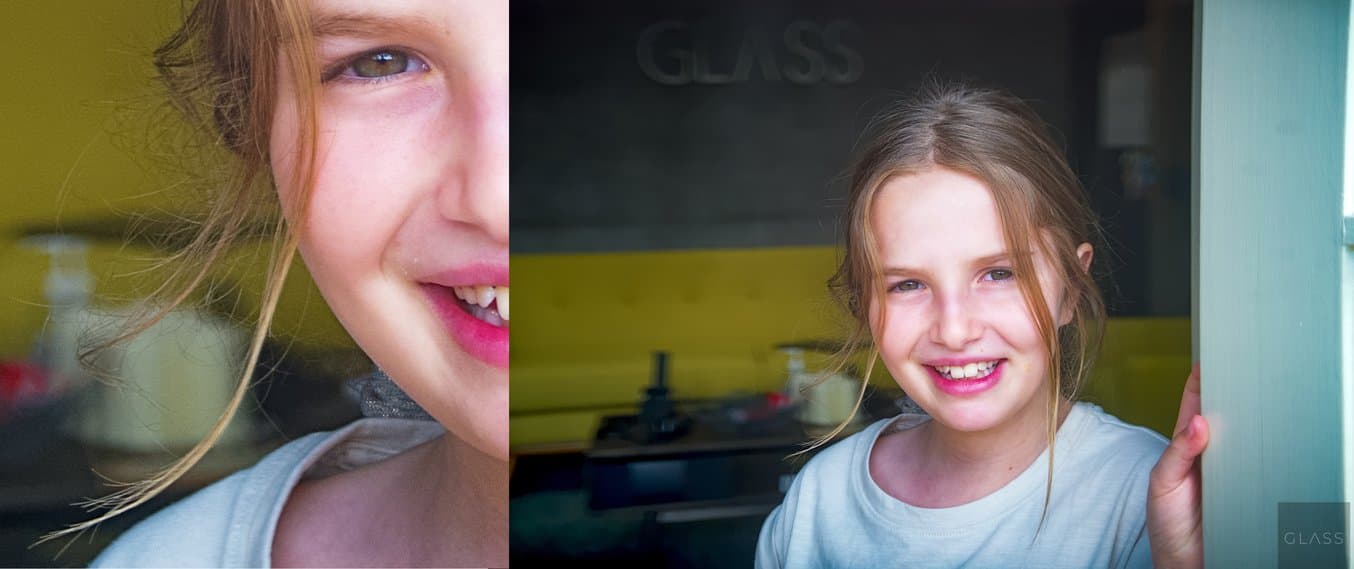
Sample images from a Glass Imaging prototype camera built with a 3D printed housing; enlarged regions demonstrate extreme detail and DSLR-like foreground/background separation.
By squeezing an extra-wide sensor into an ultra thin module that fits perfectly into a mobile device without the need for protruding bumps, the team believes that phone cameras can be as good as, if not surpass, DSLR devices. Doing this, and designing the entire device to perfectly sync with software algorithms, will generate the first true next-generation jump in smartphone camera quality.
When asked what advice Cogswell had for fellow designers considering in-house 3D printing, he told us that, “the only thing I would recommend is, just try it. Once you print your own part, you understand what goes into it, and it’s really fun. It’s fun to have your CAD part in your hand within a day. There is so much you can do with it, so many ways to think about design.”
To follow Glass Imaging Inc. on their journey to re-define the camera lens, visit their website.