Selective laser sintering (SLS) 3D printing is an ideal solution for creating affordable, on-demand consumable parts like these collet pads, which act as the bridge between always-changing products and the CNC turning machine.
Machining fixtures and jigs are tools used during subtractive processes like CNC machining to ensure accurate alignment and safety. While machining fixtures are work-holding devices that hold a piece of metal or other material steady during the CNC milling or CNC turning process, machining jigs provide a guide for the cutting or milling tool itself, and can move with the tool while keeping it accurately on its determined track. Jigs are often more commonly found in smaller machine shops that may not have a sophisticated CNC operation and are milling or turning manually — the milling jig acts as a failsafe and guards against any human error.
These tools, traditionally made from metal, wood, or plastic, are used every day for millions of parts that are made through subtractive processes like CNC milling or turning, and have a huge impact on the efficiency of the fabrication process. With new technologies like 3D printing and computer-aided design (CAD), machining jigs and fixtures can be improved in terms of cost, customization, material waste, and more.
Introduction to Machining Fixtures and Jigs
What Is Machining?
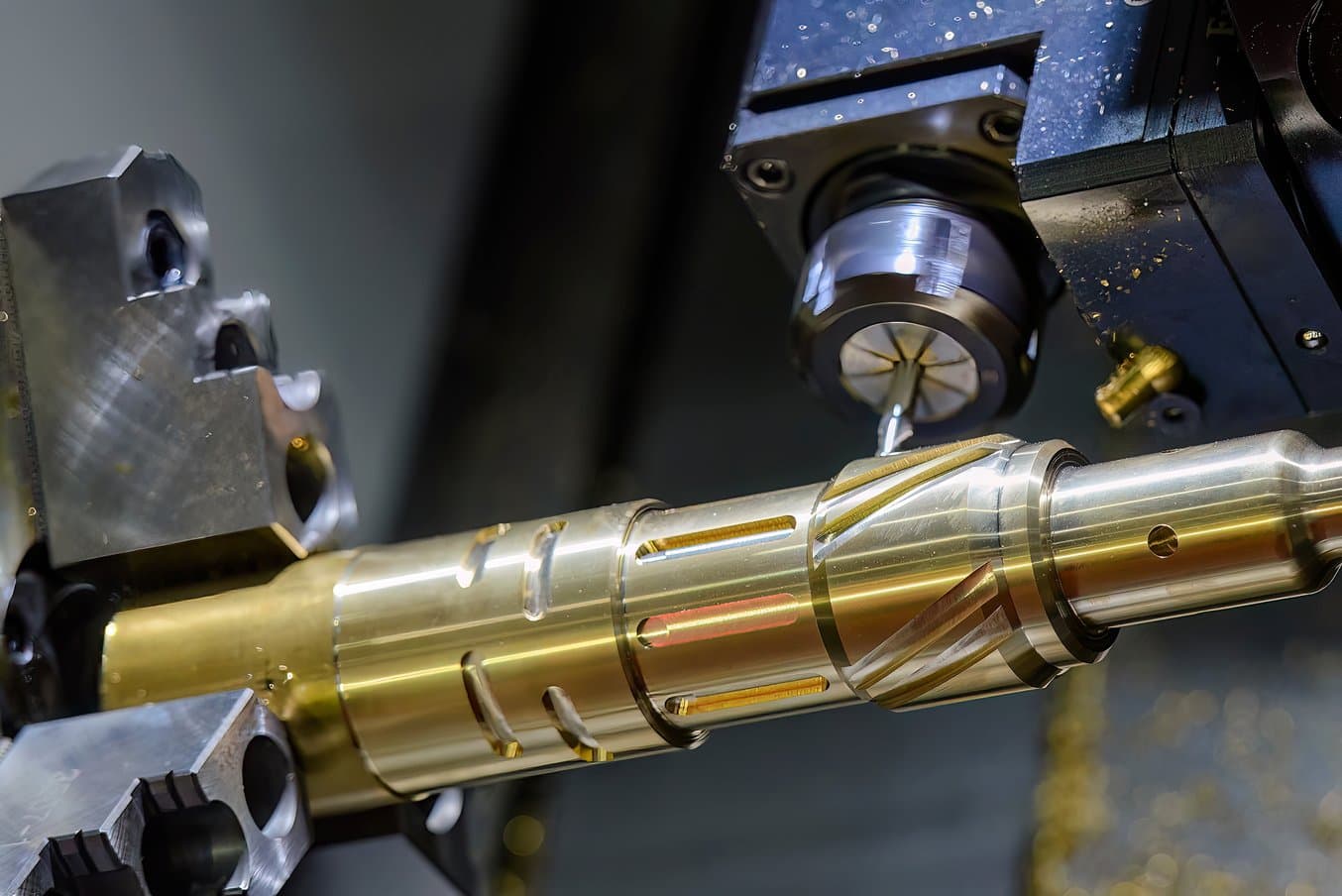
In the CNC turning process pictured above, a lathe is being used to rotate the brass cylindrical workpiece while the tool moves linearly. The machining fixtures being used are the silver blocks on the left functioning as workholding clamps.
Machining refers to any subtractive process where material is removed from a large part in order to create the desired shape. Machining has been the primary means of creating distinct designs out of raw materials like wood, metal, ceramic, and other materials for hundreds of years, though ‘machining’ typically refers to an industrialized version while earlier methods were mostly carving by hand. There are many different types of machining, as determined by how — and with what kind of tool — the material is removed.
Main Types of Machining Operations
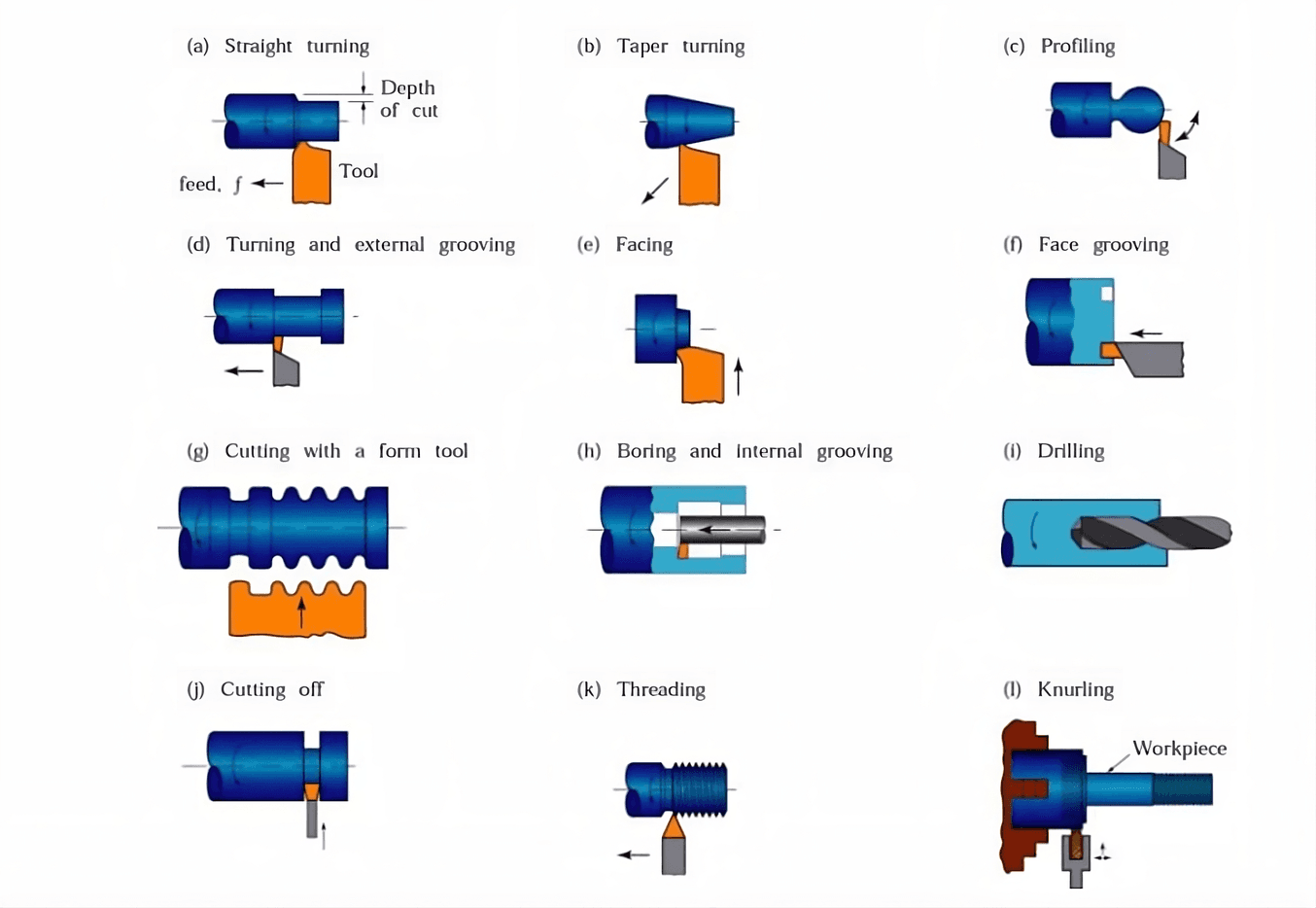
These are just some of the types and subcategories of machining operations — each type of machining can be defined by the way it removes material, the type of tool it uses, the way it rotates the part or tool, and so forth.
- Milling: Involves high-speed rotational cutting tools. During a milling operation, the product materials are kept still while a cutting tool moves around it, cutting material away to reveal the intended shape.
-
Turning: This method uses a stationary tool that removes material as it touches against a quickly rotating workpiece. CNC fixtures for turning need to be able to hold the workpiece very firmly and securely during this high-speed rotation.
-
Drilling: The most common machining method, drilling creates small holes (smaller than boring) and can be done with a machine or manually with a handheld drill found in everyday households.
-
Boring: Commonly thought of as the method to dig holes in the earth, boring is also the technique used to create hollow cylindrical parts like gun barrels.
-
Broaching: The broach, or broaching tool has a series of ‘teeth’ that remove material from the part in order to create the shape, and is the main machining method for creating gears. Linear broaching moves the broach through the material while rotary broaching rotates both the tool and the workpiece together — necessitating machining fixtures to hold the workpiece in place.
-
Grinding: This method is typically used as a finishing method rather than the primary way to remove large amounts of material, and is often employed as a secondary process to clean up the surface of a machined part.
-
Reaming: Used to enlarge holes made by drilling, reaming uses a multi-edge tool to remove material from drill holes.
-
Planing: Much like creating planks of wood, planing involves a stationary tool and a workpiece being moved across it to remove material in a desired geometry. Planing creates flat, smooth surfaces well, or can also be used to create dovetail joints, and curved or concave surfaces.
-
Sawing: Sawing is a well-understood method of machining, and involves using a teethed or serrated edge tool to split or separate a workpiece into multiple parts.
-
Waterjet cutting: Waterjet cutting is a type of machining that uses high-pressure water streams to split material or remove material from a workpiece.
-
Burning machining methods: These methods of machining (e.g. plasma cutter, laser cutter, oxy-fuel cutting) are used in highly precise applications to separate material using highly concentrated amounts of heat.
Machining Process Support: Fixtures and Jigs
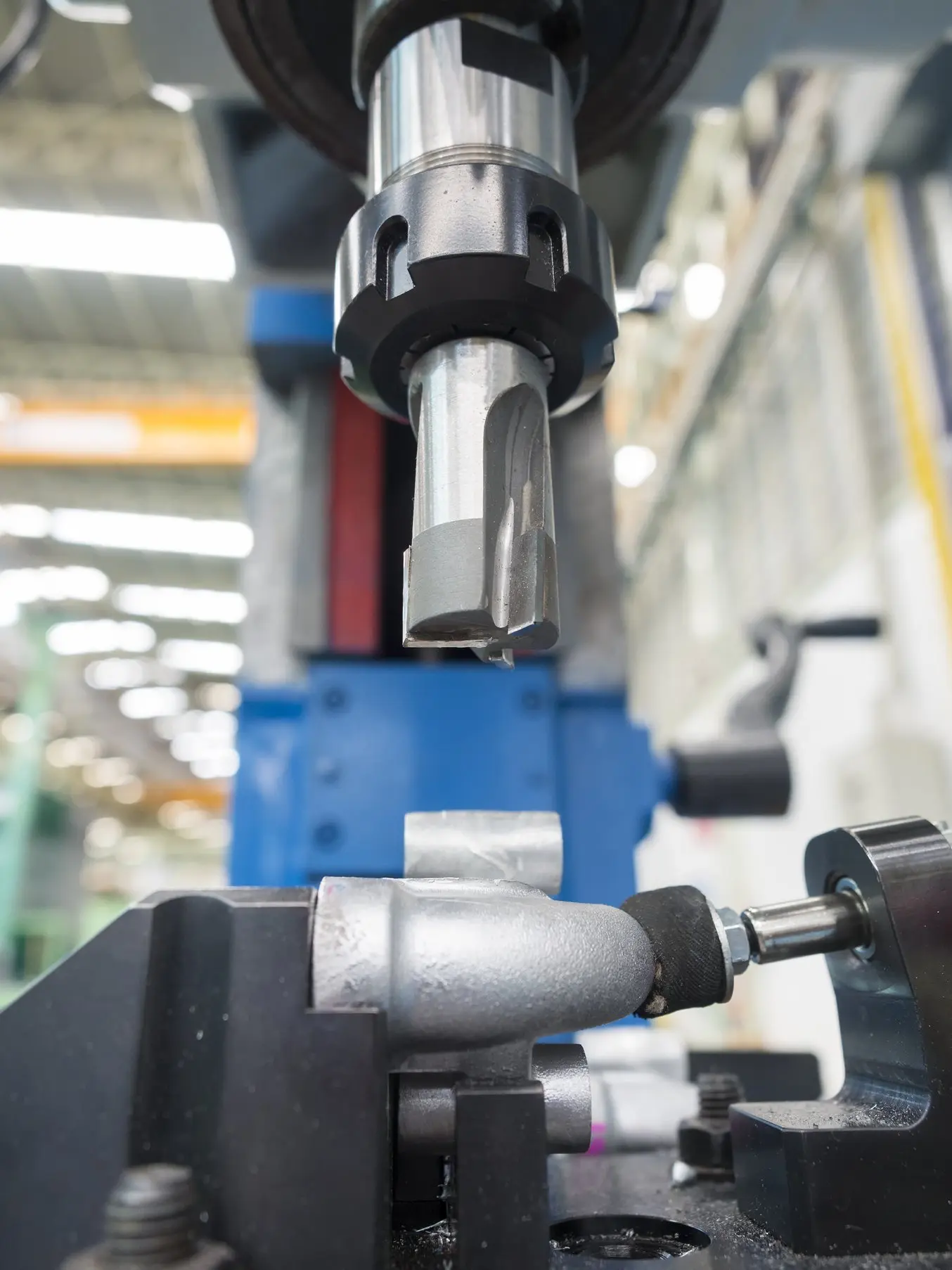
This automotive part (silver part, center) is being milled while it’s held in place by a two-part fixture (dark grey components, left and right).
In order to make precise, consistent removal of material possible, you need machining fixtures and jigs. These work-holding or guiding tools ensure stability during the machining process and create uniformity and interchangeability for the parts being manufactured. These machining fixtures reduce the effect of human error and help standardize a process that can be controlled, measured, and repeated.
Machining jigs and fixtures ensure that the workpieces and machining tools are fixed, angled, and guided correctly. These manufacturing aids have different names depending on the type of machining process and the way they apply force or hold parts, but their main function is to facilitate the machining process by either affecting the workpiece or the tool itself.
They can be mass-produced or custom-made, and they can be fabricated through manual or digital processes and out of many materials. Advances in the sophistication of machining jigs and fixtures can have an outsize impact on the success, accuracy, and consistency of machining processes.
The Importance of Precision in Machining
Machining is used to create highly precise parts used in industrial environments, and these parts are often made from materials, like metal, that are difficult or expensive to form precisely in other ways (like casting or molding).
Furthermore, machining produces parts individually and generates waste from the material removed during the process. These characteristics make it less suitable for mass production. Consequently, people choose machining due to specific and essential requirements for precision and accuracy.
This accuracy is partially ensured by the fixtures and jigs, like milling jigs, CNC workholding devices, or drilling fixtures, used during the process. These fixtures are extremely important to overall accuracy — they need to precise, hold their shape (no creep), and often customized to each product and each machine.
Different Types of Machining Jigs and Fixtures
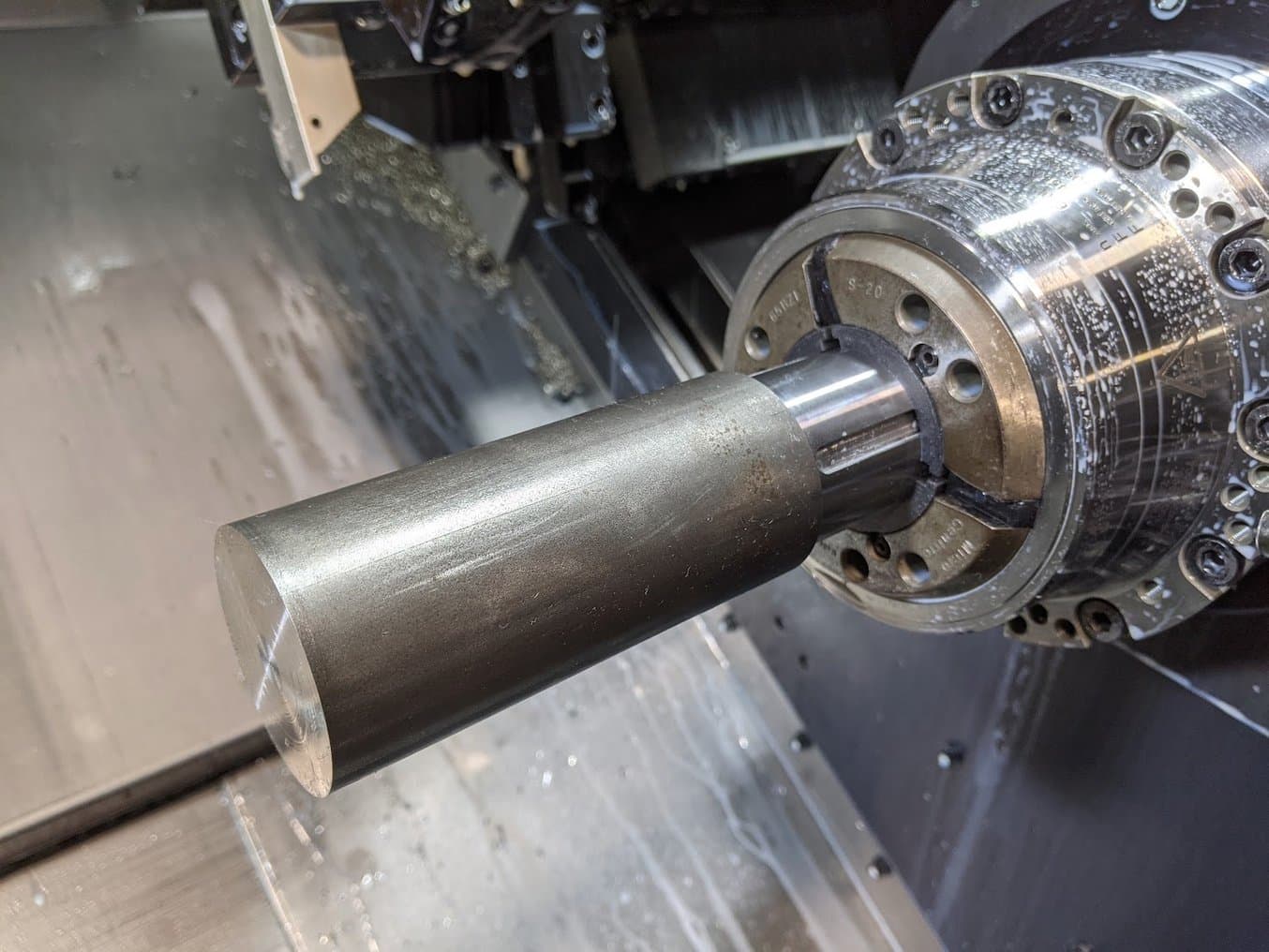
Customized collet pads are needed to hold the metal part securely inside the spindle for each part in the production run.
It’s a common adage in manufacturing that to make something you need to make four other ‘somethings’ just to get started, and this is true of machining fixtures and jigs.
Classification By Material or Fabrication Process
Machining fixtures are typically made of metal; they’re traditionally CMC machined or milled out of steel or aluminum and are incredibly precise and strong. Some are molded, but this requires a molding tool to be machined as well, and fixtures are often too low-volume to be cost-efficient for molding. Fabricating fixtures using these traditional manufacturing processes could add weeks of lead time before actual production can begin. On-demand fabrication of fixtures could be done with wood, but these were often bulky and easily damaged, leading to poor precision for the final part.
3D printing has become an alternative for the fabrication of a growing range of machining fixtures. The availability of strong, durable, and temperature-resistant materials, printers at different price points, and highly accurate 3D printing technologies has opened up new opportunities for machine shops to create customized, reliable fixtures that lead to highly precise machining operations. Polymer 3D printed fixtures can often replace metal fixtures and the technology allows for fixtures that can do more complicated actions with less material and greater precision.
Classification By Application or Function
Machining fixtures can be classified by the type of operation for which they are used, their power source, or their function and the way they apply pressure. The following types of machining fixtures are classified based on the machining process they’re used for.
-
Milling fixtures or milling jigs: Rotary table fixtures, vise fixtures, fixture plates, T-slot, and indexing fixtures are common types of milling fixtures — these components affix a block of material to the milling table so that the part will be held securely while a milling cutter moves around it, removing material from its surface.
-
Turning fixtures: During the turning process, turning fixtures hold the workpiece tightly to a high-speed rotating machine arm. The cutting tool remains steady, removing material where it comes in contact with the spinning workpiece. The machining fixtures used in turning processes are: the faceplate, collet, chuck, and mandrel fixtures.
-
Grinding fixtures: The components that hold a workpiece in place while its surface is being ground down are centerless, magnetic chuck, and sine bar fixtures.
-
Drilling fixtures: As with the drilling tool itself, drilling fixtures are commonly used in households for projects like cabinetry, and depending on their relation to the drill tool and the material, can be fixtures that secure the material or jigs that guide the drill in the right angle and direction.
-
Boring: During boring operations, either boring bars or boring head fixtures help angle the boring tool or bit in the right direction and with the correct amount of force.
Other classifications for machining fixtures might be their power source: hydraulic, pneumatic, electrical, manual, vacuum, or magnetic. Or, they could be classified by the way they secure parts: vise fixtures squeeze parts together from the outside, jig fixtures guide the cutting tool in a specific pattern, and angle fixtures are used in CNC milling operations to maintain a precise angle of force by the tool.
Fixtures and Jigs for Other Metal Working Applications
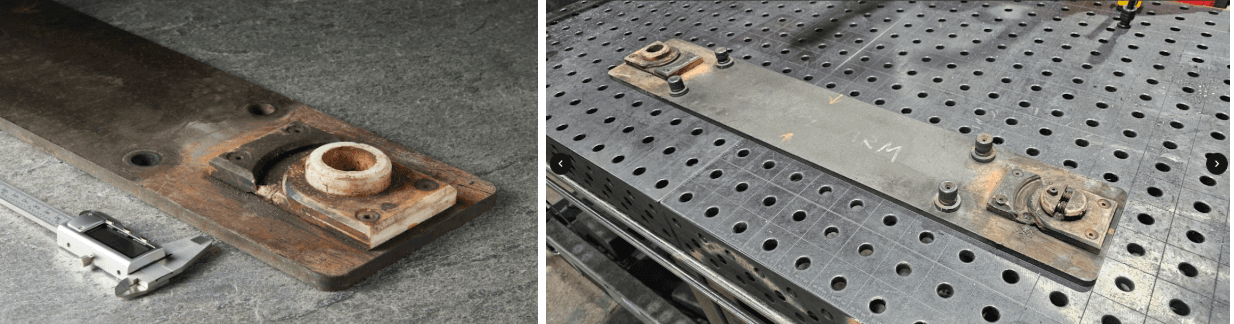
The straight arm jig is made of two small 3D printed parts mounted over a steel plate. The geometry is complex with organic shapes that would be challenging to machine and the team needed the tool in one day. After running about 2,000 welds on that jig it is still functional, even though some welds have dropped on the jigs by accident, causing some marks.
Though not a subtractive metal working process like CNC turning, milling, or machining, welding is another application in which fixtures and jigs, often 3D printed, have proven enormously useful in reducing waste, lowering costs, and streamlining operations. Welding jigs can be used for fit tests, to hold parts securely, to guide a welding robot, and for many other parts of the process. The benefits are the same as those of CNC fixtures, milling jigs, and more: more precise, repeatable, accurate metalworking processes are possible with good manufacturing aids.
3D Printing as an Alternative for Custom Fixture Design
As with so many industries and applications, 3D printing introduces possibilities for better, more affordable machining jigs and fixtures. 3D printing enables faster iteration, more thorough product development, superior design processes, and inexpensive fabrication methods for one-offs or low-volume jigs and fixtures. Better manufacturing aids not only improve the function of the aid itself, but they also have downstream effects, potentially improving the entire manufacturing process and function of the end-use products themselves.
Advantages of 3D Printing for Creating Machining Jigs and Fixtures
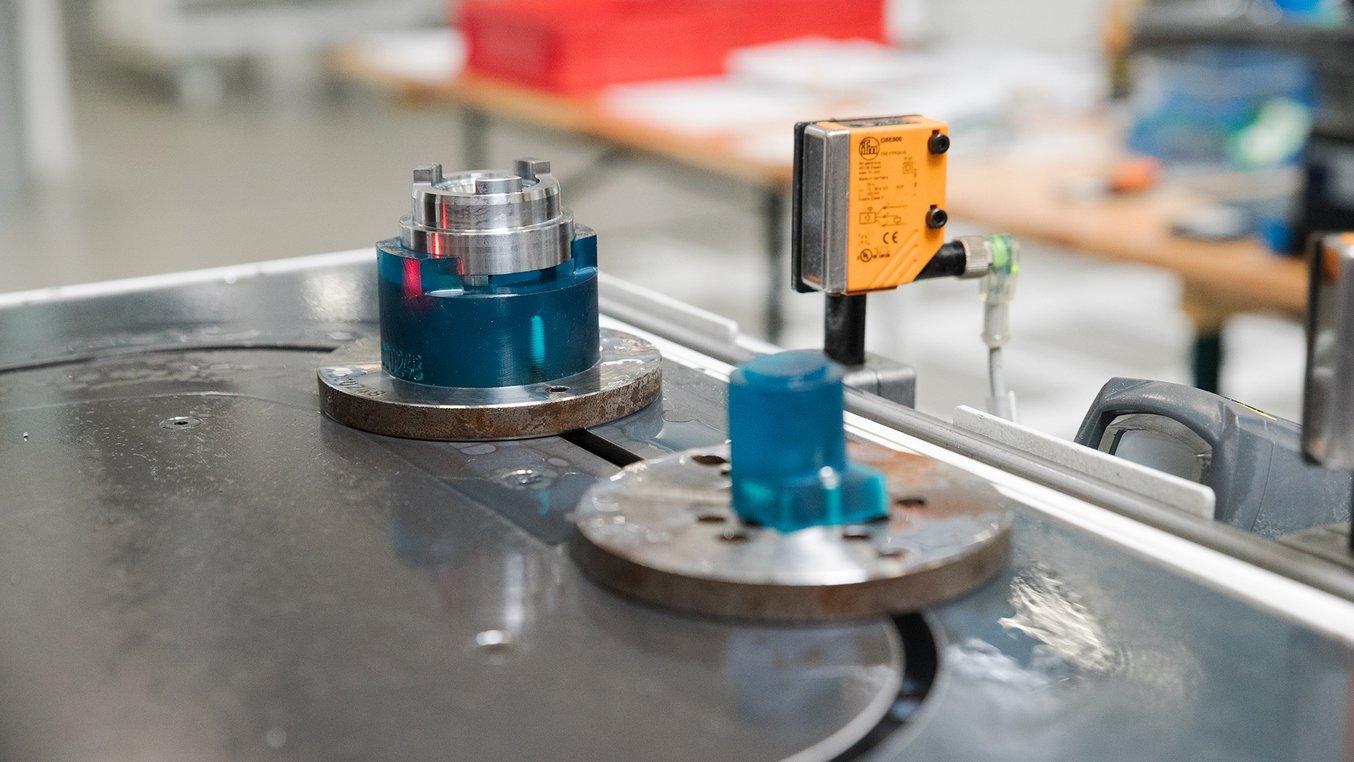
At Pankl Racing Systems' production line, each working stage in the automatic lathe requires a custom 3D printed CNC lathe jig. The jigs are attached to the conveyor belt using standard shuttles.
Perhaps the most well-understood benefit of in-house 3D printing is the improvement in speed: more iterations allow for a more thorough design and testing cycle, creating products (whether end-use or manufacturing aids) that have been more rigorously tested and developed.
The benefit of speed is perhaps especially impactful for manufacturing aids — which, if they’re not fabricated quickly, present an obstacle to any other prototyping or manufacturing even starting. Perhaps, considering the downstream impact of their efficiency and its effects on creating a better end use product, CNC fixtures, like CNC workholding clamps, should be given even more attention in the design phase. 3D printing prototypes of milling or machining jigs and fixtures would allow manufacturers to test their fit and efficacy — an ability often deemed unnecessary given the accessory nature of the part.
This can lead to better-designed parts with more efficient use of material — the operator may note that the part could be redesigned for ergonomics and ease of installation, removal, and replacement. It can also lead to opportunities for customization; machining tools like CNC turning tables are mass-produced while their programming and the products they shape are unique to the manufacturer. CNC jigs and fixtures can bridge that divide, with some simple streamlining of the CNC fixture design process.
The design flexibility of 3D printing — especially technologies that require no supports like selective laser sintering (SLS) — can open up new possibilities for fixtures and jigs to become more intricate, customized, and ergonomic.
The digital nature of 3D printing also allows for more efficient storage of files. With a 3D printer in multiple factories, one large manufacturer can affect change at each of their locations by sharing a CNC fixture design file that improves efficiency on a common machine. 3D printing makes the sharing of knowledge more effective and impactful and gives big companies a way to improve at each level of their network quickly and easily.
The range of materials available with different 3D printing technologies also makes 3D printing for machining jigs and fixtures much more powerful and useful in more situations. For example, 3D printed welding fixtures need to be heat-resistant, and certain stereolithography (SLA) materials, like Formlabs’ High Temp Resin or Rigid 10K Resin provide an affordable, on-demand, fast alternative to metal welding fixtures. 3D printed nylons, like Formlabs’ SLS Nylon 12 Powder or Nylon 11 Powder, are excellent for machining fixtures like chucks, which need a combination of durability and rigidity to hold parts tightly during a high-speed turning process.
3D Printing vs. CNC Machining for CNC Fixtures
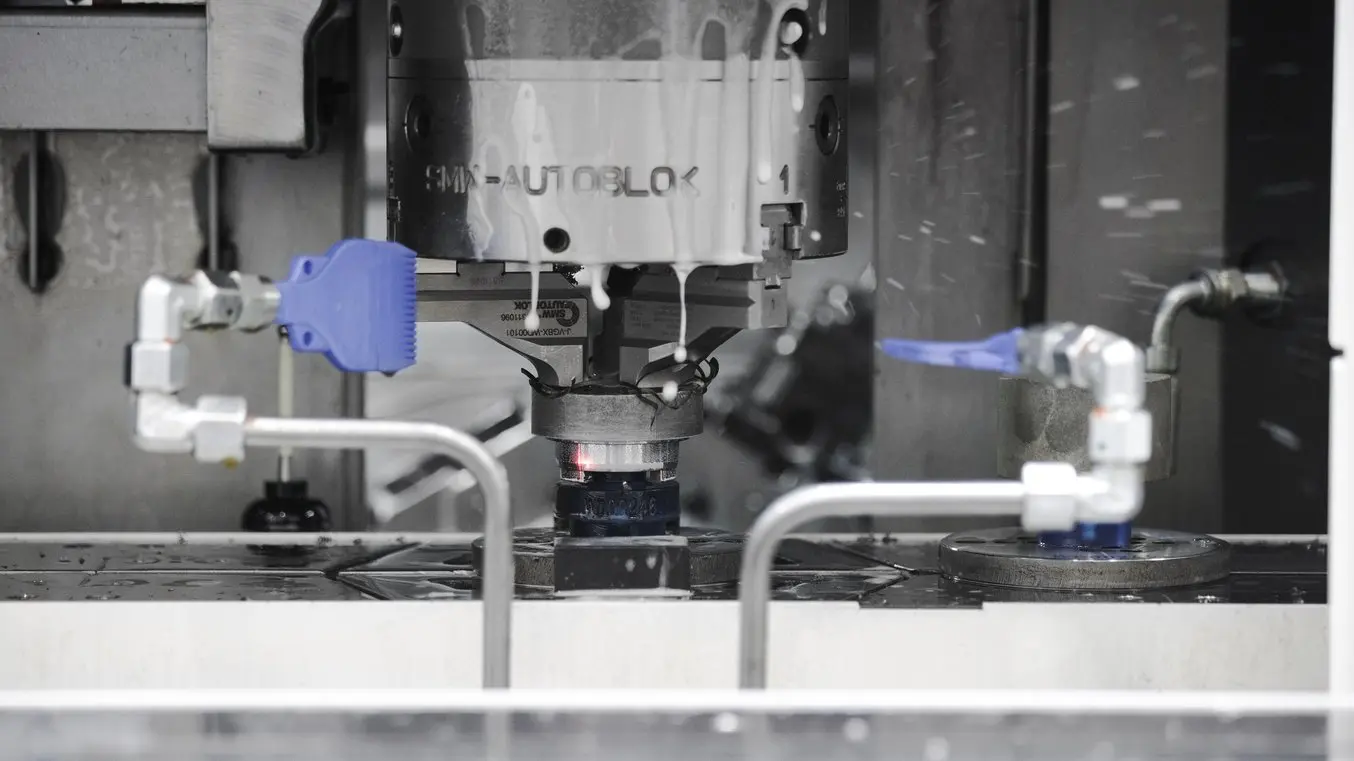
A machine gripper picks up the part from the first jig (dark green part, center) and places it on the second jig once the machining process is complete.
When choosing whether to 3D print or use CNC machining for fixtures, the main factors to consider are: material properties, the degree of complexity the part requires, and lead time.
In terms of material properties, machining fixtures and jigs don’t often need to be technically advanced beyond a certain level of strength and durability. Most industry-familiar plastics, like nylon, are sufficient. There are, of course, situations in which a specific material property, like conductivity, or heat-resistance are necessary, and at these times, a 3D printing technology like stereolithography (SLA) can offer the widest variety of advanced material properties purpose-built for different environments.
Once you’ve determined the base levels of force and friction these parts will undergo, you can consult 3D printing manufacturers’ data sheets to find a material that will work best. Machine shops like The Factory Amsterdam in New York have found that Nylon 12 Powder printed on the Fuse SLS Series can handle the high-speed CNC turning processes they perform.
Ultimate Tensile Strength (MPa) | Tensile Modulus (GPa) | HDT @ 0.45 MPa (°C) | Notched Izod (J/m) | |
---|---|---|---|---|
Nylon 12 Powder | 42 | 1.45 | 171 | 16 |
Rigid 10K Resin | 88 | 11 | 238 | 20 |
Tough 2000 Resin | 46 | 2.2 | 63 | 40 |
High Temp Resin | 49 | 2.8 | 238 | 17 |
Another consideration is the level of complexity the part requires. For certain machining fixtures, like collet pads, the pads themselves are simple shapes, and the manufacturer of the CNC turning machine often supplies original parts made out of steel. For applications where you’re making thousand or hundreds of thousand of the same thing, metal CNC machined fixtures will unquestionably stand the test of time. But when the fixtures and jigs start to become more complex, like a test fixture for a welding machine that needs to switch in between multiple programs, it becomes more costly and complicated to machine them.
The single biggest consideration for deciding whether or not to 3D print or machine your machining fixtures is time — how soon do you need these parts? In most manufacturing scenarios, the worst outcome is to have a production stoppage because of a missing fixture or jig. If you rely on machining for these parts — especially if you’re using metal to prototype them as well as produce the final design — you’ll add to your machine shop’s backlog and can cause a bottleneck that affects the entire output of the business. 3D printing machining fixtures instead can deliver them in a matter of hours, without taking attention away from other projects, as the machinists would be forced to do.
What is the Right 3D Printing Technology for Fixtures?
There is no one ‘best’ 3D printing technology for creating machining fixtures; the best tool for the job relies on multiple factors, and many businesses employ different types of 3D printers. The three most common 3D printing technologies are fused deposition modeling (FDM), stereolithography (SLA), and selective laser sintering (SLS) also sometimes referred to as powder bed fusion.
When considering which printer to choose for 3D printing your milling jig, CNC fixture, drilling fixture or other machining aid, consider the following.
Choose SLS for:
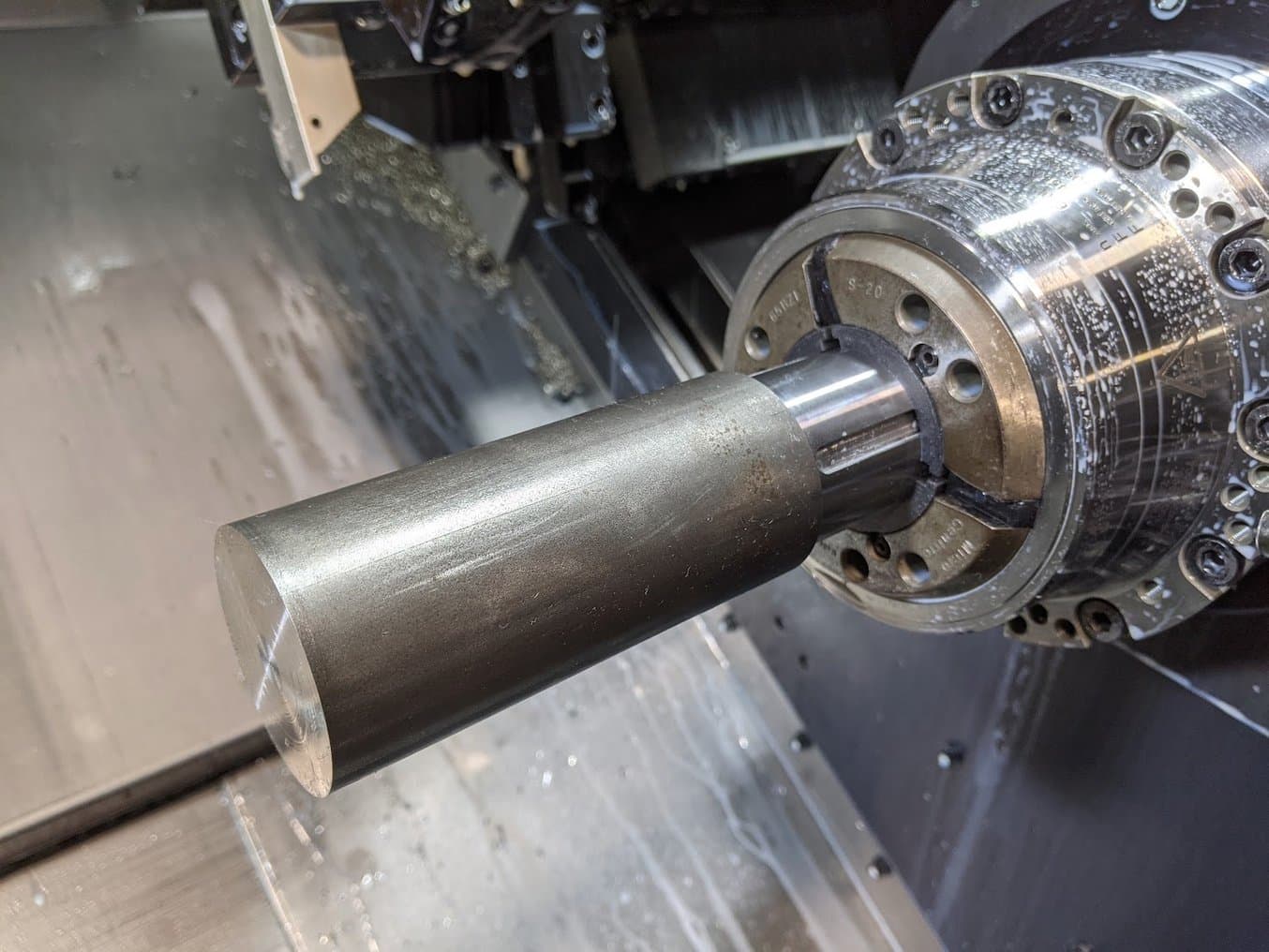
Customized collet pads are needed to hold the metal part securely inside the spindle for each part in the production run.
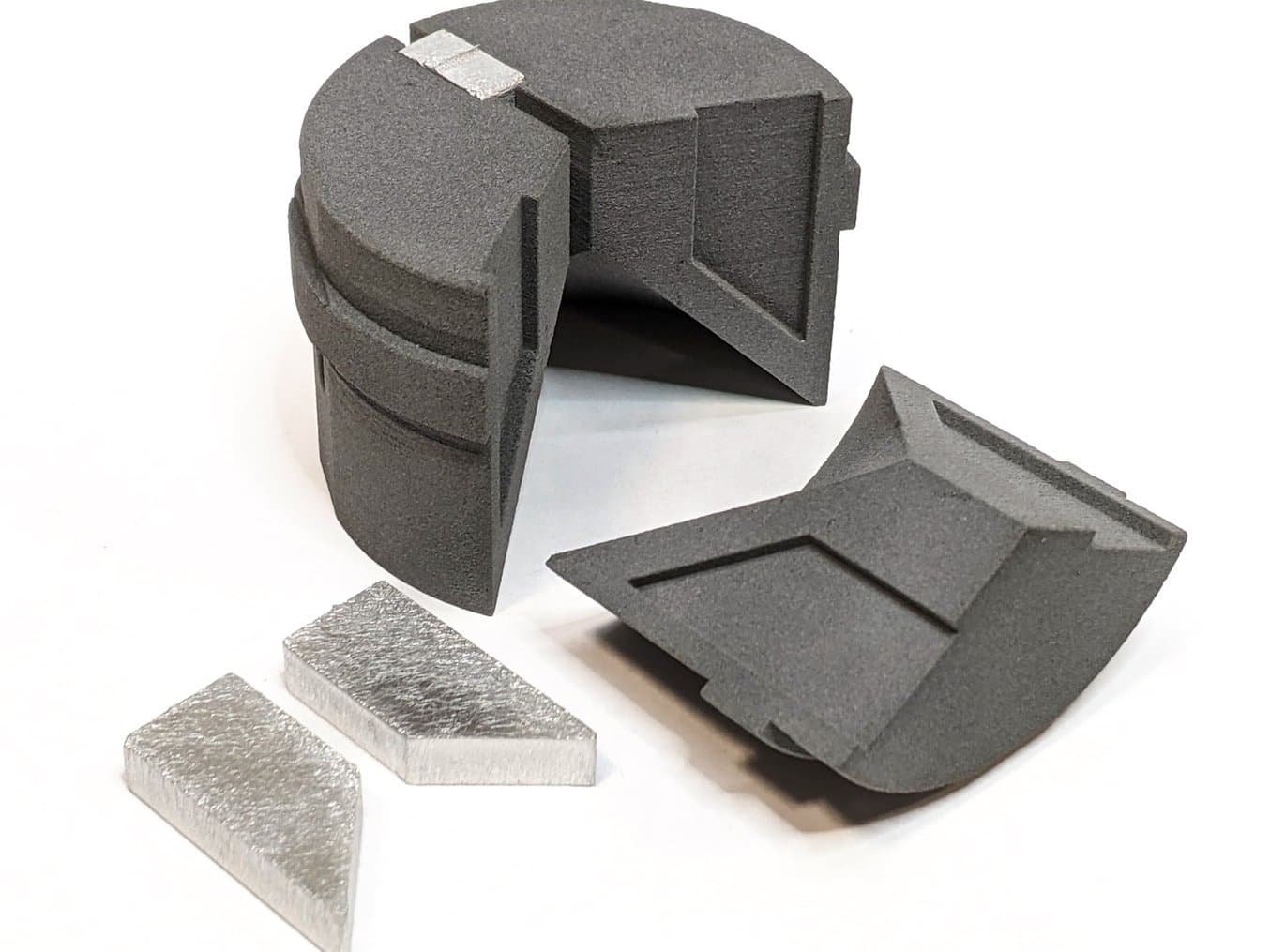
SLS 3D printing excels at producing small parts like these collet pads — consumable parts that nevertheless have to hold up through an entire production run of 3,000 to 4,000 parts and withstand radial forces generated from the lathe turning at 3,000 rpm.
- Strong, durable, heavy-duty tools: Parts that need to withstand high forces and repeated stress such as impact-resistant machining or milling fixtures.
-
Versatile, chemical-resistant, and environmentally stable materials: Nylon 12 Powder is a go-to material in 3D printing for general purposes. Nylon 3D printed parts absorb very little moisture and are resistant to light, heat, and chemicals. This is particularly important for machining tools as they are exposed to cooling solvents. Formlabs recommends choosing Nylon 12 Powder as the default material. For more specific use cases, consult the SLS materials catalog.
-
Complex design and lightweight features: SLS eliminates the need for support structures, offering more design freedom for creating intricate or hollow geometries. It enables designs with lattice structures that reduce material use while maintaining strength, which is excellent for large, lightweight jigs used in sheet metal forming or machine replacement parts.
-
High throughput: SLS is ideal for medium-volume production. The absence of supports allows operators to stack parts and reduce post-processing time. The Formlabs Fuse 1+ 30W build chamber enables operators to nest densely within the entire build volume, maximizing throughput and increasing efficiency. Formlabs' Fuse Sift and Fuse Blast simplify powder recovery and automate part cleaning and finishing.
Choose SLA for:
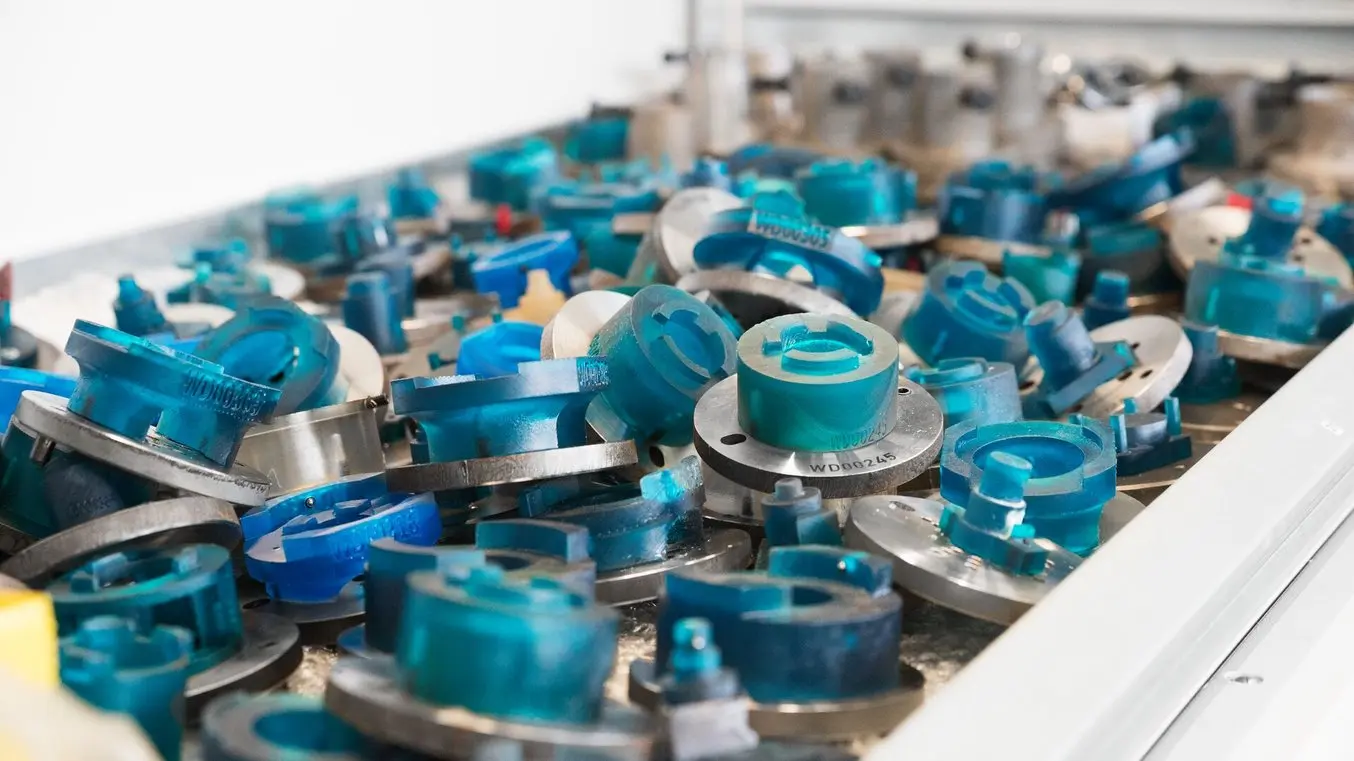
These 3D printed lathe jigs, printed in a legacy version of Formlabs’ Tough 2000 Resin, are strong and extremely accurate and can attach to the standard shuttles they’re fixed to, as well as create a secure connection with the workpiece.
- High precision, fine details, and smooth surface finish: Applications like machining alignment tools, location jigs, measurement devices, or ergonomic fixtures. Features such as custom grips for user comfort are easy to integrate.
-
Wide range of material properties with an easy switch between resins: Build tools with various specifications such as elastic, ESD-safe, or flame-retardant, to enable specialized applications. Rigid 10K Resin is frequently used in metalworking environments, particularly for welding fixtures; it is a stiff and temperature-resistant material with an HDT of 218 °C @ 0.45 MPa and a tensile modulus of 10,000 MPa.
-
Quick short-run production thanks to an accessible ecosystem: Formlabs’ SLA ecosystem comes at lower price points, requires minimal equipment, and can be seamlessly integrated into any production workflow. Go from design to ready-to-use part in less than a couple of hours with Form 4 and Form 4L.
Choose FDM for:
- Fast prototypes: FDM 3D printers excel at rapidly producing looks-like models that can be used to check fit quickly before moving to a different solution.
-
Affordable parts: FDM desktop 3D printers are some of the most recognizable and affordable on the market, with inexpensive materials that you can purchase easily from third-party vendors.
-
Multi-person teams or new users: FDM is the most widely known type of 3D printing, and new members of your team may feel comfortable with operating them due to their familiarity.
-
Familiar materials: FDM 3D printers use materials like ABS and PETG, most of which are commonly understood by the industry.
Creating Custom Jigs and Fixtures with 3D Printing
3D printing excels at producing custom or low-volume parts. CAD programs allow machinists to create optimized designs like CNC fixtures or workholding clamps that are precisely attuned to both the workpiece and the machine. 3D design can create overhangs, lattice structures, or other geometric features that are difficult to machine themselves, but are more efficient in terms of material and weight. 3D printing offers a combination of strength and efficiency that in many situations, eclipses the extra strength afforded by creating metal fixtures and jigs. To create an optimized machining fixture, such as a milling fixture, turning fixture, grinding fixture, or drilling fixture, there are simplified steps to follow to get the most out of your printer and material.
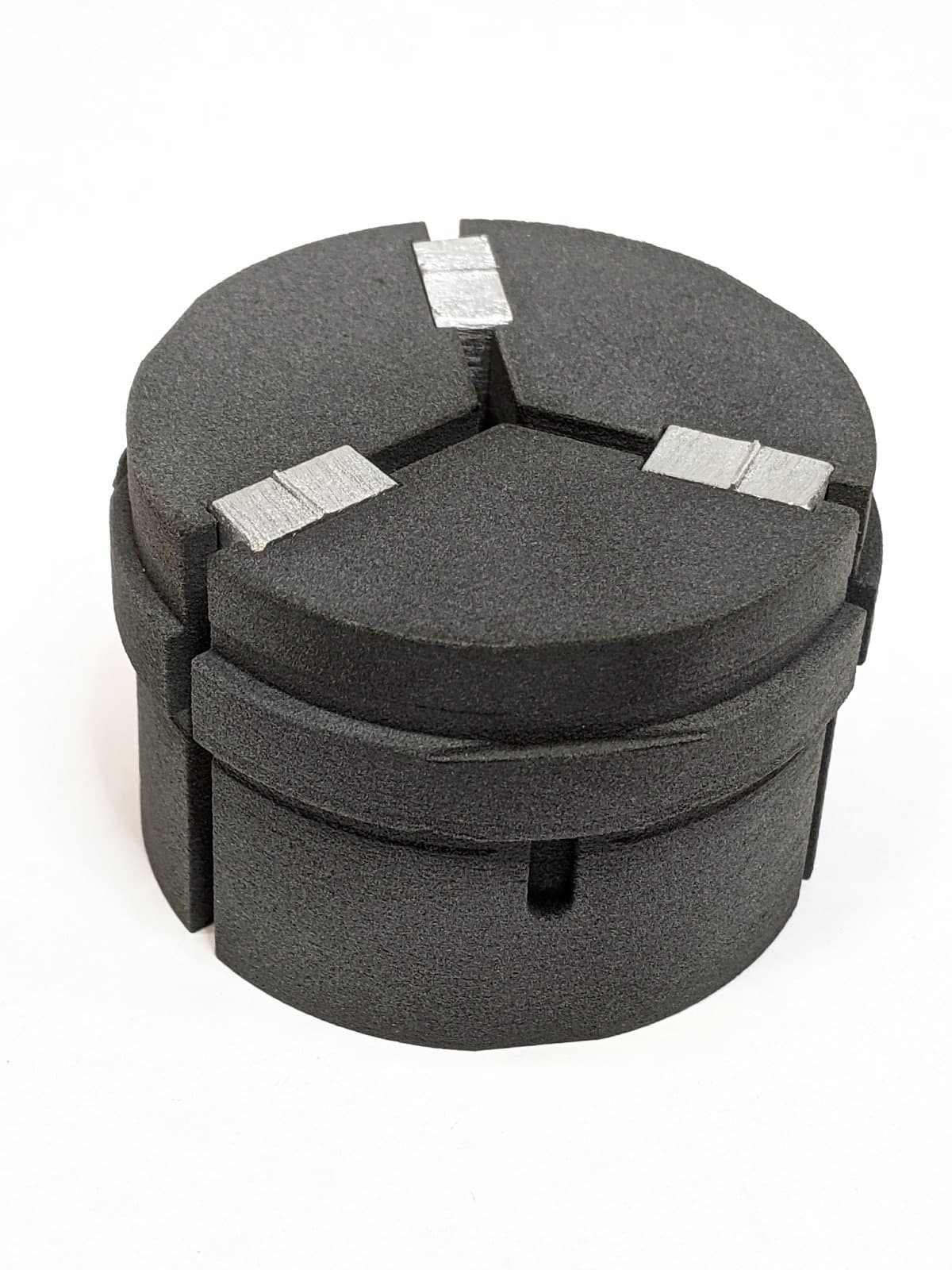
The SLS 3D printed collet pads need to be dimensionally accurate and highly precise in order to fit seamlessly together and integrate into the spindle. Any deviation could cause issues in the integrity of the turning process.
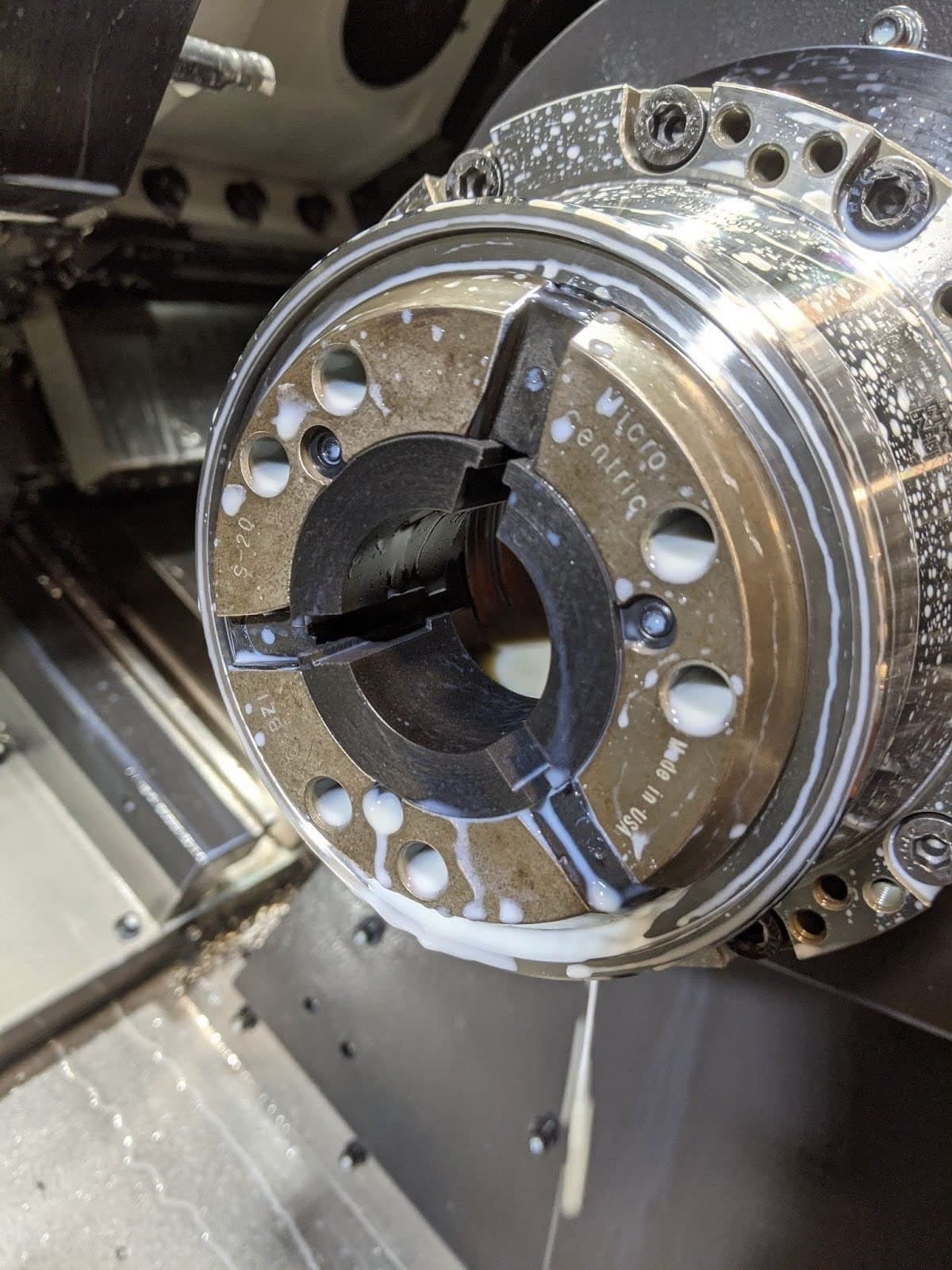
The tools are continuously in contact with the coolants inside the lathe. It is a semisynthetic oil that is aggressive on a lot of plastics and dissolves FDM materials. Nylon 12 Powder is chemically resistant and does not wear from it.
Digitize existing tooling designs with reverse engineering: Move to a digital inventory or identify tooling needs and design new tooling files. When designing a 3D printed jig or fixture, several key design considerations differ from traditional metal machined tools, allowing for unique features that are only possible with additive manufacturing.
Leverage complex geometries: Use 3D printing to create intricate internal features like channels, undercuts, and hollow structures, which are difficult and expensive to machine in metal. SLA is best for fine details and smooth surfaces, while SLS excels at durable, complex forms that can withstand mechanical stress.
Optimize for lightweight structures: Take advantage of SLS to create lightweight jigs with lattice or honeycomb structures. These reduce weight without sacrificing strength, which is hard to achieve with solid metal parts machined traditionally.
Design with precise wall thickness: SLA allows for precise, intricate designs with wall thicknesses around 2-3 mm. While not thinner than metal, SLA enables more complex shapes and smoother finishes without additional machining, which can improve performance and reduce costs.
Integrate multiple functionalities: 3D printing allows for the integration of features like clamps, locators, and guides into a single part. This simplifies design and reduces the need for multiple assembled components.
Incorporate smooth fillets for strength: Use SLA to add smooth fillets (1-2 mm radii) at stress points, reducing the risk of cracks and stress concentrations. While fillets are possible in machined metal, 3D printing enables more efficient, stress-resistant designs with fewer manufacturing steps.
Enhance ergonomics: Add ergonomic features such as custom grips or contoured edges directly into your SLA designs. These details improve usability and are easier and less costly to incorporate than in traditional machined metal tools.
Design for modularity and customization: Use SLS to create modular jigs and fixtures that can be easily customized or updated. This flexibility allows for faster adjustments and replacements compared to remanufacturing entire metal tools, saving time and cost.
Reduce assembly with single-part designs: Consolidate complex assemblies into a single 3D printed part, minimizing assembly time and reducing misalignment risks. SLA and SLS can streamline production workflows, offering fewer parts to manage and align compared to multi-part metal fixtures.
Consider additional finishing steps: Post-processing guidelines for 3D printing vary based on application. For machining fixtures and jigs, post-processing can be quite basic — there is no need for a painted, plated, coated, or extremely smooth part. For SLA 3D printed CNC fixtures and jigs: wash, dry, and remove supports. For SLS 3D printed machining fixtures and jigs, remove excess powder and media blast. For FDM 3D printed parts, remove supports and sand.
SLA and SLS 3D Printing: Powerful, Efficient Alternatives for Machining Fixtures and Jigs
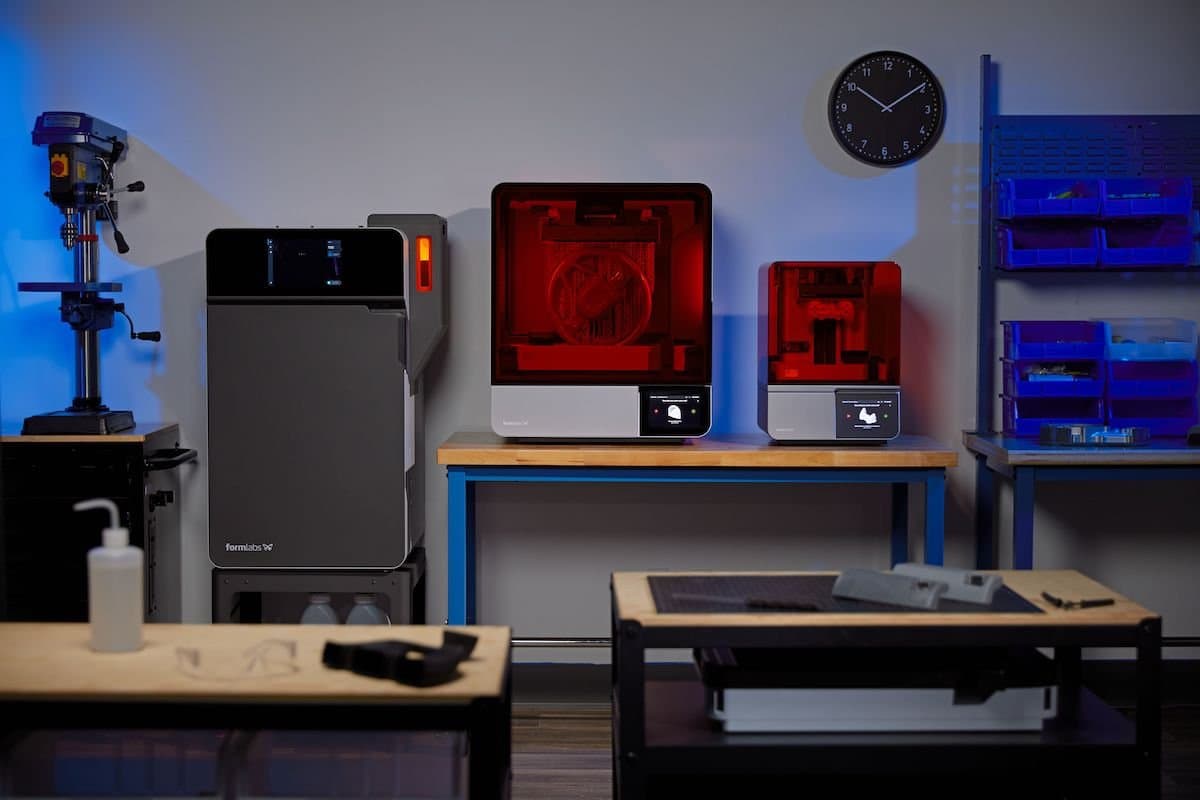
Formlabs printers Fuse 1+ 30W, Form 4L, and Form 4 are ideal tools for producing machining fixtures and jigs.
Machining fixtures are integral parts of the success of a machine shop’s operation. They bridge the gap between the mass-produced milling, turning, welding, cutting, drilling, boring, etc., equipment and the unique product the manufacturer is creating.
3D printing provides an alternative to traditional methods of fabrication for these machining fixtures and jigs. The range of materials and technologies available, the speed and efficiency of the printers themselves, and the degree of customization they make possible are reasons for manufacturers to bring 3D printing in-house. They can reduce their machinists’ workload while improving the efficiency of their process and even their bottom line.
To begin fabricating fixtures and jigs for turning, milling, or any type of machining operation, start by evaluating your needs: material type, mechanical properties, efficiencies you can find and improve upon, and build volume necessary. Formlabs’ sales team can help you decide if an SLA or SLS printer is the best fit for you. To learn more, request a free 3D printed sample part or contact our team to get your own file printed as a free custom sample.