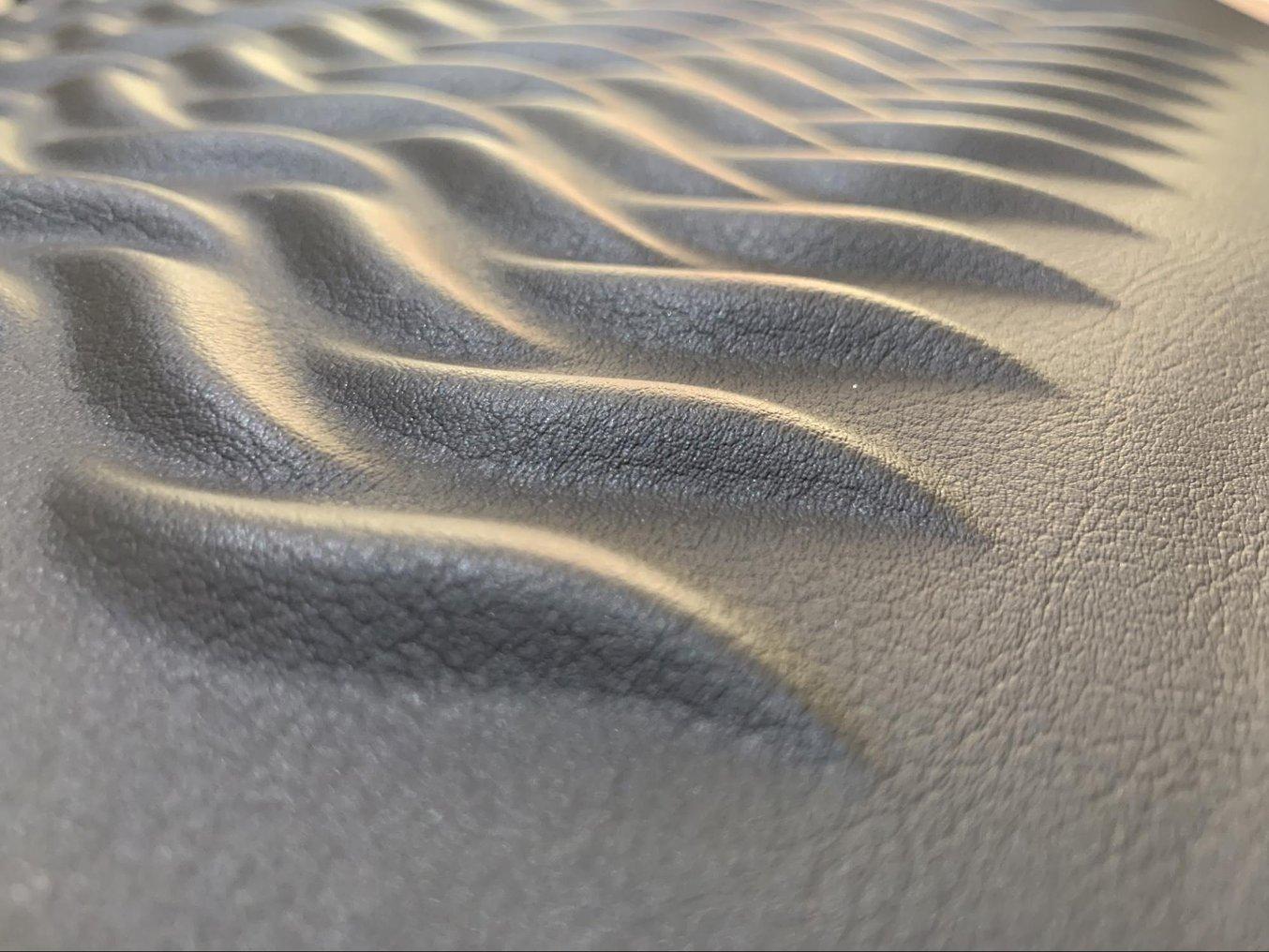
Makra Pro received an inquiry from a well-known motorcycle manufacturer on a Friday afternoon in June 2018. The motorcycle manufacturer promised a large order for the foam parts of motorcycle seats, but only if the plastic seat pans could be included. This piqued the interest of Matthias Krabel, Managing Director of Makra Pro, and opened the door new innovation.
Until then, Makra Pro had produced foam tools out of wood. In this project, however, Mr. Krabel wanted to experiment with using 3D printing for the first time. After some research on the internet, he decided to try the Form 2 with Durable Resin, as this material has similar properties to polypropylene (PP).
The Formlabs 3D printers were so convincing in the manipulation of the material that Makra didn't even consider looking at alternatives and their printer fleet was quickly expanded, which marked the beginning of a long success story.
From Prototyping to Tool Development, and Pre-Series Production
Today, Makra Pro has ten Form 2 and eight Form 3 printers in regular use. Depending on the orders, there are weeks when all 18 printers are running and parts are printed, washed, and post-cured around the clock. Makra Pro has become a significant innovator in the Middle Franconian region Markt Taschendorf. Matthias Krabel and his team have brought smart and rapid prototyping to the forefront.
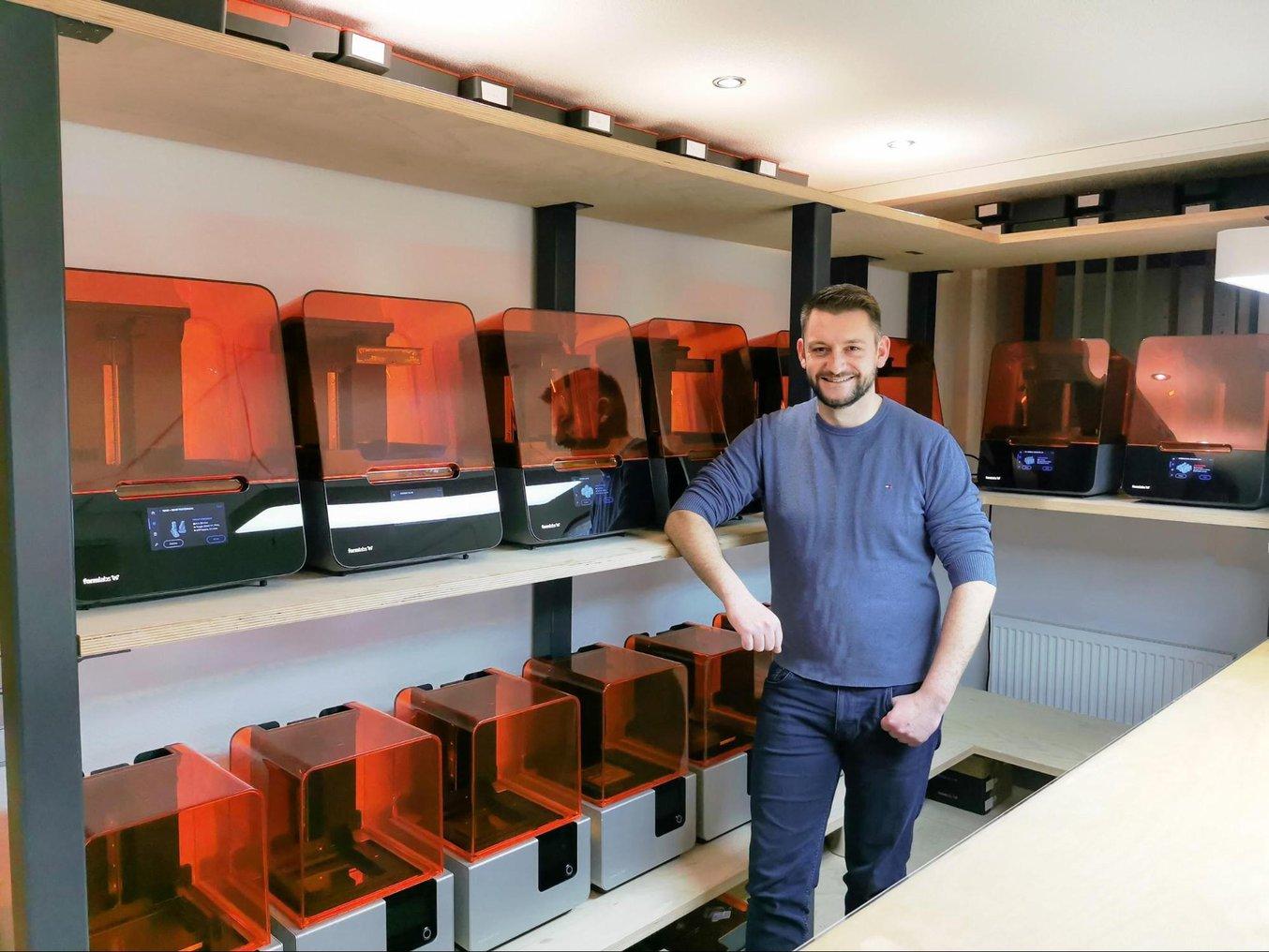
Matthias Krabel showcasing Makra Pro’s print fleet of 18 3D printers.
Makra Pro caters to customers from a wide variety of industries such as automotive, medical technology, and even agriculture. The focus of their work is on prototype and tool development as well as pre-series production—all of which can be improved with the help of 3D printing.
The greatest challenge in the day-to-day development of a project lies in the uncertainty as to whether the ideas evolving in the minds of the team can be implemented in reality. With desktop 3D printing, these can be quickly validated and adjusted if necessary.
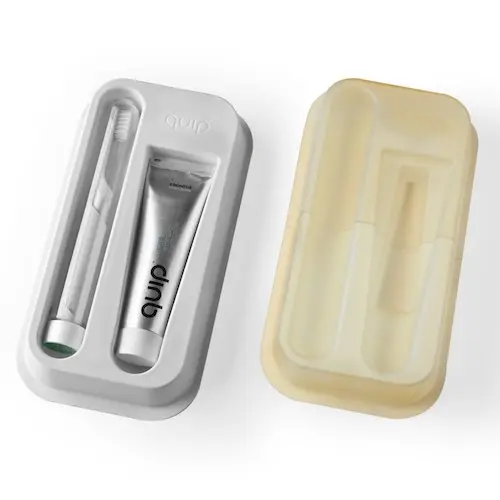
Moldmaking with 3D Prints
Interested in other applications of 3D printed molds? Download our white paper that also covers thermoforming and casting with elastomers.
A New Process for Foam Molding With 3D Printing
The latest innovation from Makra Pro, which was completed using the Formlabs 3D printers, has even led to the patenting of a process.
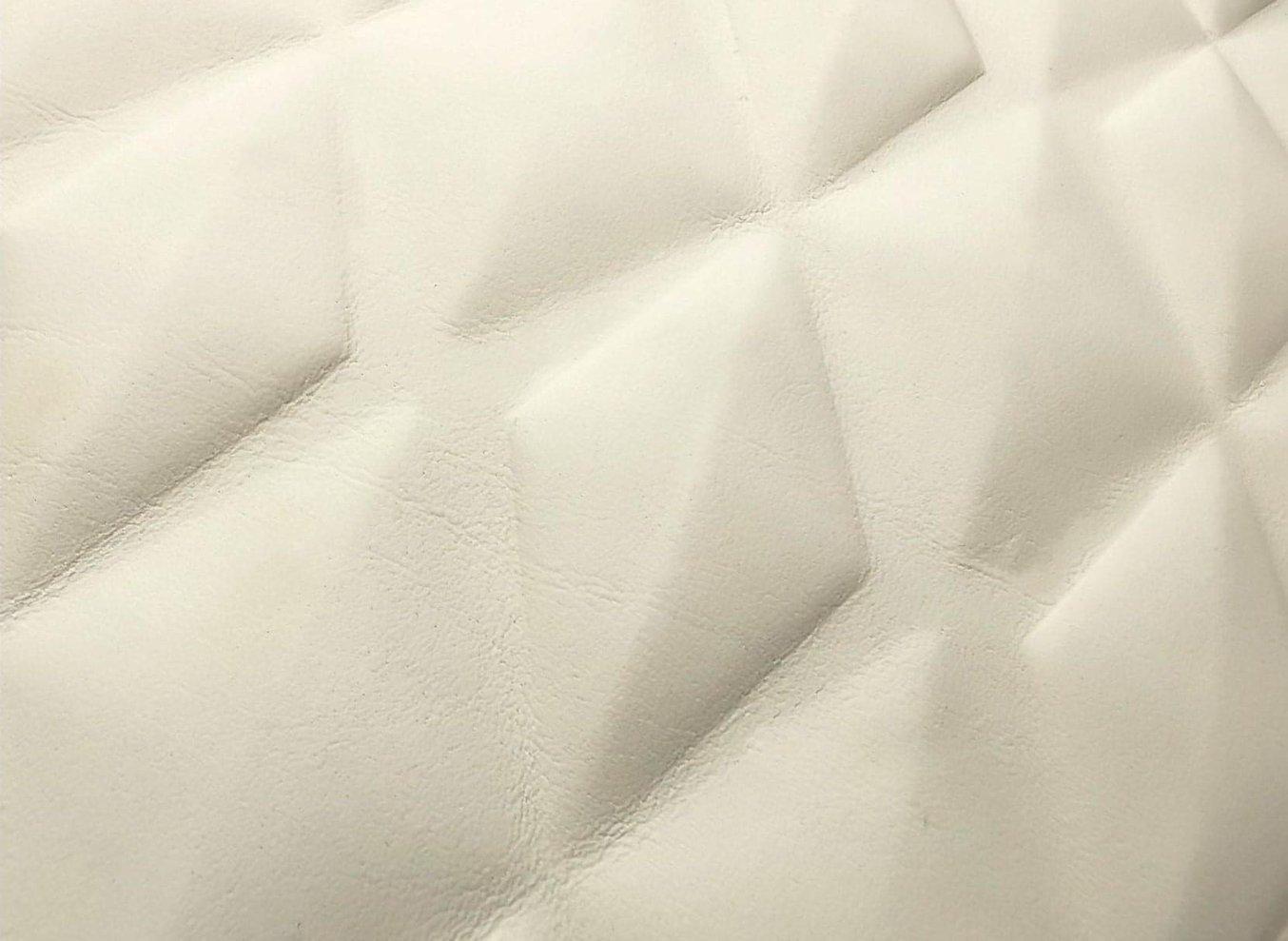
A close-up view of 3D leather.
Real leather is a material that is popular, among other applications, for the interior of vehicles or real estate properties. Leather is also often embossed, embroidered, or covered to achieve the desired pattern. The Makra Pro team wanted to achieve a 3D look for leather covers, which is a major challenge since real leather is difficult to stretch.
The groundbreaking idea came to Mr. Krabel while preparing waffles for his breakfast on a Sunday. He asked himself, “Could the leather be molded with the help of a foam, which spreads out in the same way as waffle batter?” This idea was finally put into practice and validated.
First, the molds for the tool are printed on the Form 3 printers with a specially developed material. These molds are inserted into the tool, covered with leather, and then injected with the foam for shaping. When the tool is then closed and the foam hardens and the leather takes its 3D look.
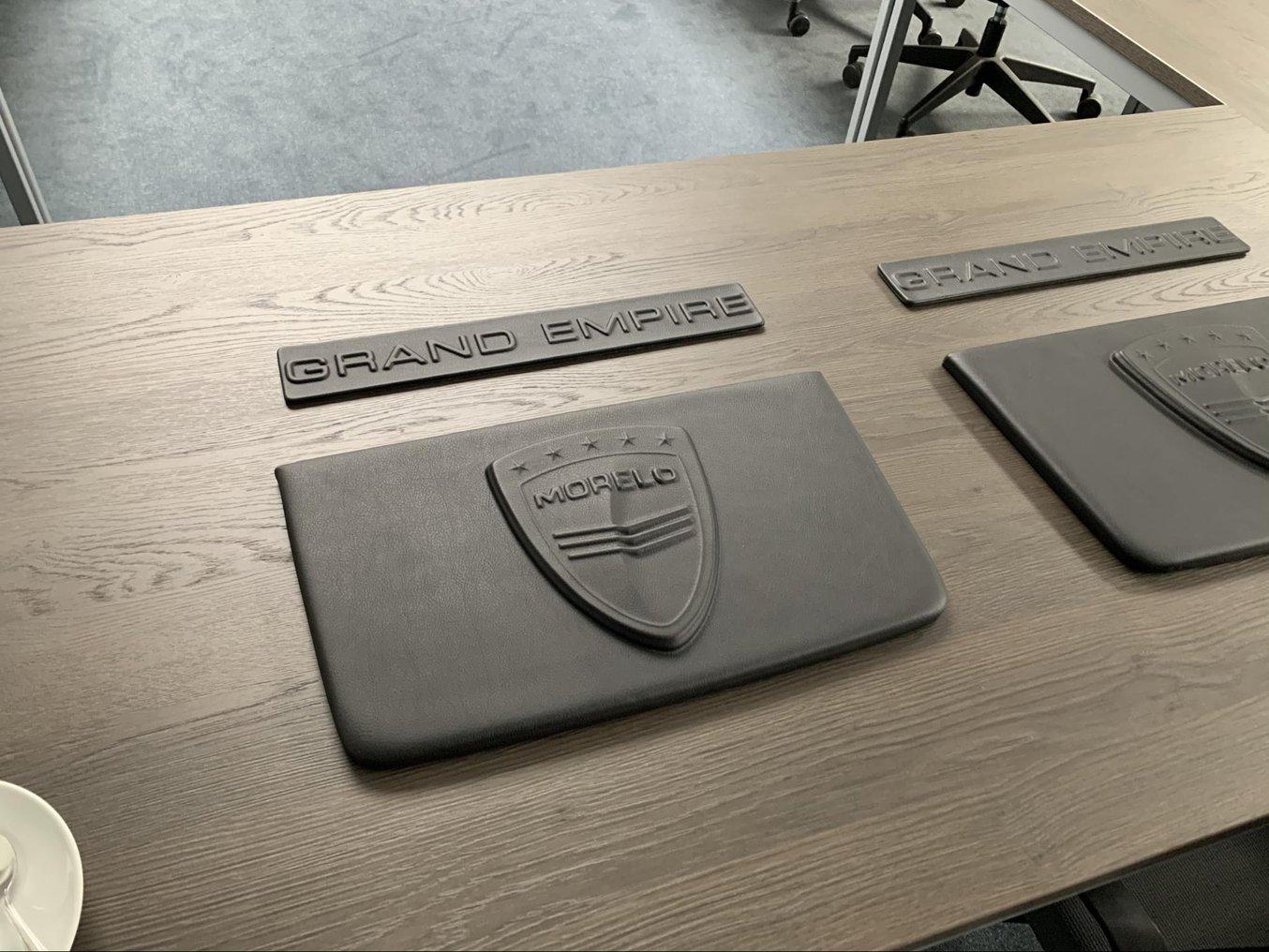
Custom 3D leather parts proceed for a luxury motorhome produced by Morelo.
The finished leather parts can then be, for example, stretched over the door panel in a car or attached to the seat cover in a vehicle. One well-known tuning company of limited-edition luxury automobiles uses these molded leather parts for wall or ceiling panels in vehicle enhancements.
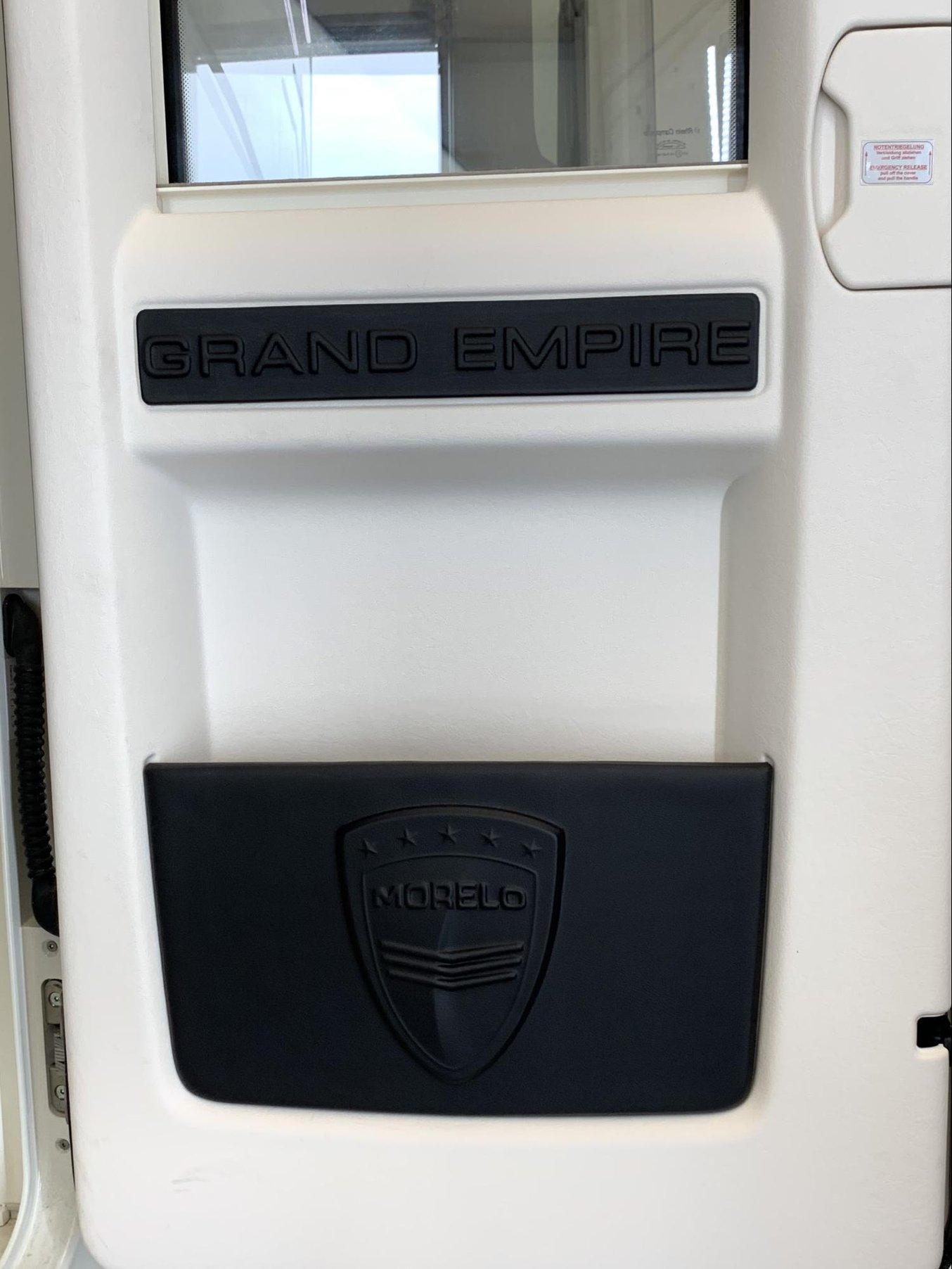
The custom 3D leather parts built into the door of a luxury motorhome.
Customers often request designs where the embossments of the leather are very delicate and can only be achieved using the 3D printed tool.
Since the end parts are usually larger than the build volume of the Form 3 printer, the molds are printed in several parts and then assembled in the tool. The largest mold Makra Pro produced consisted of 160 individual parts. These parts are often glued together in the tool or in other cases, the leather is processed using a loose mold in order to be able to change and personalize parts of the mold quickly and easily.
Thanks to the further development of Formlabs products, especially in the area of materials, Matthias Krabel expects to find new ideas, applications, and exciting projects that leverage 3D printing in the future.